生产流程-生产线平衡_图文
生产线平衡(line balance)
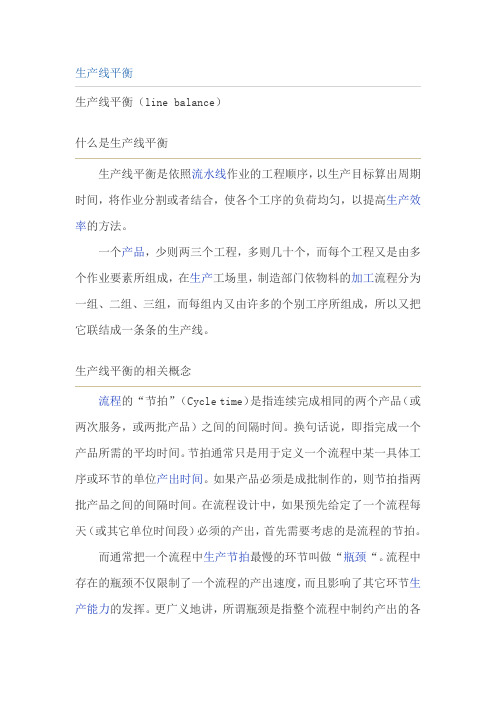
生产线平衡(line balance)什么是生产线平衡生产线平衡是依照流水线作业的工程顺序,以生产目标算出周期时间,将作业分割或者结合,使各个工序的负荷均匀,以提高生产效率的方法。
一个产品,少则两三个工程,多则几十个,而每个工程又是由多个作业要素所组成,在生产工场里,制造部门依物料的加工流程分为一组、二组、三组,而每组内又由许多的个别工序所组成,所以又把它联结成一条条的生产线。
生产线平衡的相关概念流程的“节拍”(Cycle time)是指连续完成相同的两个产品(或两次服务,或两批产品)之间的间隔时间。
换句话说,即指完成一个产品所需的平均时间。
节拍通常只是用于定义一个流程中某一具体工序或环节的单位产出时间。
如果产品必须是成批制作的,则节拍指两批产品之间的间隔时间。
在流程设计中,如果预先给定了一个流程每天(或其它单位时间段)必须的产出,首先需要考虑的是流程的节拍。
而通常把一个流程中生产节拍最慢的环节叫做“瓶颈“。
流程中存在的瓶颈不仅限制了一个流程的产出速度,而且影响了其它环节生产能力的发挥。
更广义地讲,所谓瓶颈是指整个流程中制约产出的各种因素。
例如,在有些情况下,可能利用的人力不足、原材料不能及时到位、某环节设备发生故障、信息流阻滞等,都有可能成为瓶颈。
正如“瓶颈”的字面含义,一个瓶子瓶口大小决定着液体从中流出的速度,生产运作流程中的瓶颈则制约着整个流程的产出速度。
瓶颈还有可能“漂移”,取决于在特定时间段内生产的产品或使用的人力和设备。
因此在流程设计中和日后的日常生产运作中都需要引起足够的重视。
与节拍和瓶颈相关联的另一个概念是流程中的“空闲时间”空闲时间是指工作时间内没有执行有效工作任务的那段时间,可以指设备或人的时间。
当一个流程中各个工序的节拍不一致时,瓶颈工序以外的其它工序就会产生空闲时间。
这就需要对生产工艺进行平衡。
制造业的生产线多半是在进行了细分之后的多工序流水化连续作业生产线,此时由于分工作业,简化了作业难度,使作业熟练度容易提高,从而提高了作业效率。
精益生产--生产线平衡(pdf 20页)
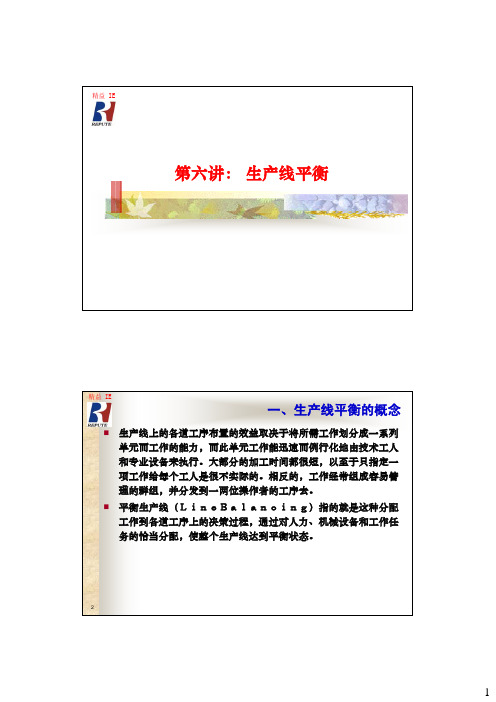
精益 IE
第六讲: 的概念
生产线上的各道工序布置的效益取决于将所需工作划分成一系列 单元而工作的能力,而此单元工作能迅速而例行化地由技术工人 和专业设备来执行。大部分的加工时间都很短,以至于只指定一 项工作给每个工人是很不实际的。相反的,工作经常组成容易管 理的群组,并分发到一两位操作者的工序去。
8
4
精益 IE
5.重排的方法
9
精益 IE
6.作业改善后合并的方法
10
5
精益 IE
案例
11
精益 IE
改善
分析这条生产线可以发现,瓶颈工序就是钻孔的工序。针对这八道工序的特 点,分解工序3(钻孔)的作业动作,提出以下的平衡改善措施:
改善瓶颈作业(即工序3钻孔),将工序3的定位动作(8秒)分担给工序2完 成。
Cell Line (目前Cell Line作业站并无一个统一的称呼,如NPS作 业站、流线化生产、一个流作业、摊贩式作业等)是指生产上的 一个组织单位。一个作业站配备有生产一类产品的全套设备,同 时还配有一名或若干名掌握多种技能、能熟练使用这些设备的全 能作业者。每个作业站独立完成整个产品的全部生产作业。整个 车间或工厂则由多个作业站组成。
因此希望朝多制程操作的作业方式安排
16
8
精益 IE
5、作业员的多能工化
具有能操作多制程作业能力的作业员,称为多能工。
生产线平衡分析图表

序号
1 2 3 4 5 6 7 8
工序名称
工序1 工序2 工序3 工序4 工序5 工序6 工序7 工序8
示意图
○ ○ ○ ● ○ ○ ○ ○
工序内容
标准要求
使用设备/工具 岗位人数
2 1 1 1 1 1 2 1
标准工时 (s)
9.0 4.5 4.0 6.0 5.0 4.5 10.0 5.0
标准产能 (pcs/h)
400 800 900 600 720 800 360 720
平衡工时 (s)
4.5 4.5 4.0 6.0 5.0 4.5 5.0 5.0
平衡产能 (pcs/h)
800 800 900 600 720 800 720 720
利用率 (%)
75% 75% 67% 100% 83% 75% 83% 83%
600
核准
总标准工时
人均产出(pcs/人 *h)
72.50 40 审核
平衡率 损失率
80.56% 19.44%
制表
9
工序9
○
10
工序10○Βιβλιοθήκη 11 工序11检验△
12 工序12装箱
◇
注:○表示一般生产作业工序,●为瓶颈工序,△表示检测工序,◇表示包装。
1
4.5
800
4.5
800
75%
1
4.0
900
4.0
900
67%
1
5.0
720
5.0
720
83%
2
11.0
327
5.5
655
92%
生产线总人力
15
生产线每小时产能 (pcs/h)
生产线平衡分析与改善PPT课件
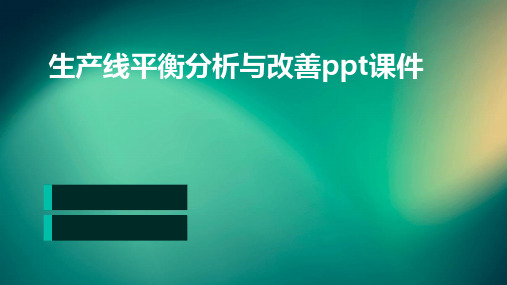
某汽车企业在生产过程中面临工艺复杂、生产流程长等问题,通过改进生产工 艺和引入智能制造技术,实现了生产线平衡的持续改进,提高了生产效率和产 品质量。
06 结论与展望
生产线平衡对企业的影响
提高生产效率
生产线平衡能够优化资源配置,减少生 产过程中的空闲时间,提高设备利用率,
从而提高生产效率。
持续改进与优化
定期检查
定期对生产线进行检查,发现潜在问题并及时解 决。
员工培训
加强员工培训,提高操作技能和生产意识,促进 持续改进。
ABCD
数据跟踪
建立数据跟踪机制,对生产线相关数据进行实时 监测和分析,以便及时调整和优化。
创新与改进
鼓励员工提出创新和改进意见,激发团队活力和 创造力,实现持续改进与优化。
设备利用率是指生产线设备在一段时间内 的有效工作时间与总工作时间的比值,反 映了设备的利用情况。
生产效率
在制品库存
生产效率是指生产线在一定时间内完成的 产品数量与总工作时间的比值,反映了生 产线的生产能力。
在制品库存是指生产线在制品的数量和存 储时间,反映了生产线的库存状况。
生产线平衡的优化目标
01
随着工业4.0和智能制造的兴起,未来生产 线平衡将更加注重智能化技术的应用,如
物联网、大数据、人工智能等。
绿色生产线的推广
随着环保意识的提高,未来生产线平衡将 更加注重环保和可持续发展,推广绿色生
产技术和设备。
柔性生产线的构建
为了更好地适应市场需求的变化,未来生 产线平衡将更加注重生产线的柔性和可重 构性。
绘制工艺流程图,直观展示工艺流程, 便于发现瓶颈环节。
引入自动化和智能化设备,减少人工 干预,提高生产效率。
生产流程生产线平衡
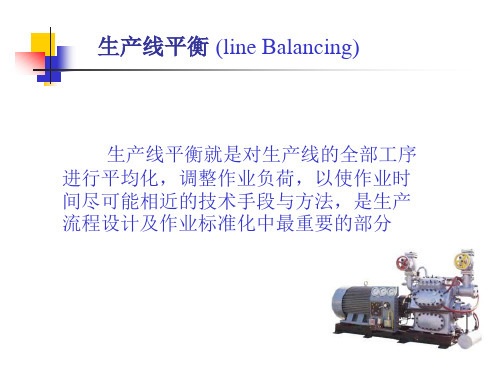
私事宽放率4% 疲劳宽放率8%
作业测定——模特法
生产线平衡措施
ECRS改善法
• 消除(Elimination):什么作业可以不做? • 合并(Combination):那些作业可以合并? • 重排(Rearrange):调整作业的順序是否会更有效率? • 简化(Simplification):是否能简化每一個作业,
生产线平衡意义:
保证生产连续性和均衡性
保证设备、人力的负荷平衡,从而能提高设备、工时 利用率,提高生产效率。
减少在制品,节约物资消耗,加速流动资金的周转, 从而降低生产成本;
生产线平衡概念
节拍(Cycle Time)
CT - 生产节拍 TW - 计划期内有效总工作时间 Q - 计划期内制品数量
生产线平衡概念
装配生产线平衡设计
3)按阶位由大到小排列,并表明各作业要素紧前作业要素
4)作业要素分配
生产线平衡措施
工序的分解和合并是工序同期化常用的方法。 受到机器限制,工序不能分解和合并时
.提高设备的生产效率 .改进工艺和操作方法
………
工作研究(work study)
程序分析 操作分析 动作分析 工作测定
位置约束
产品装配作业受到空间的限制。在大型的生产线上,如 汽车的装配线上,由于产品比作业人员可完成的装配作业 空间大,不能完成其周边的装配作业。
生产线平衡评价指标
生产线平衡率
平滑性系数(Smoothness Index)
生产线平衡概念
生产线平衡的一般数学表达:
给定一个无回路的有向图G=(E,P),节点E表示作 业要素集合,弧P表示生产作业元素之间的先后关系集合。 一个节点j∈E有一个值Tj(j=l,2,…,n)表示作业时间。 生产线平衡问题就是求节点集E的一个划分:
富士康《生产线平衡》

2019/12/16
34
例 : 產品A線時間損失分析 1. 基本數據:
實際產量 3017台 單件標准時間 340秒
投入時間 9小時 實測時間 377秒
工人數 40人
瓶頸時間 10秒
設定產量 3240台
2019/12/16
35
例 : 產品A線時間損失分析
31
平衡手法----程序改善
程序分析技巧
六大步驟: 選擇—確定研究對象 記錄—用程序圖/路線圖等記錄工作 分析—用5W1H、ECRS分析改進 建立—建立新方法的模擬圖 實施—按模擬圖實施新方法 維持—將有效的方法標準化
2019/12/16
32
平衡手法----損失分析
目的:計算分析生產中的所發生的損失,並加以停止. 損失的種類:
拆解動作
將工站動作拆解成若幹個單一的操作內 容,並填入<<時間記錄表>>
時間測試
2019/12/16
分解動作時間量測,一般每個動作測量5 次為宜; 量測人員應站在作業員斜后面1米以外, 以能看清楚全部操作動作為准則; 測試中不能打擾作業員的正常操作,和 引起作業員的緊張;
22
時間測量流程
2019/12/16
37
平衡手法----作業條件改善
治工具改善
治具加工
說明: 在產線上完成一個動作 裝入治具完成另一個動作
治具加工
說明: 在治具上完成兩個動作
2019/12/16
38
平衡手法----打破平衡
平衡率﹕98% 動作分析,減少不增值動作
2019/12/16
39
平衡率﹕70% 打破平衡﹐打開了可平衡 局面
生产线平衡法
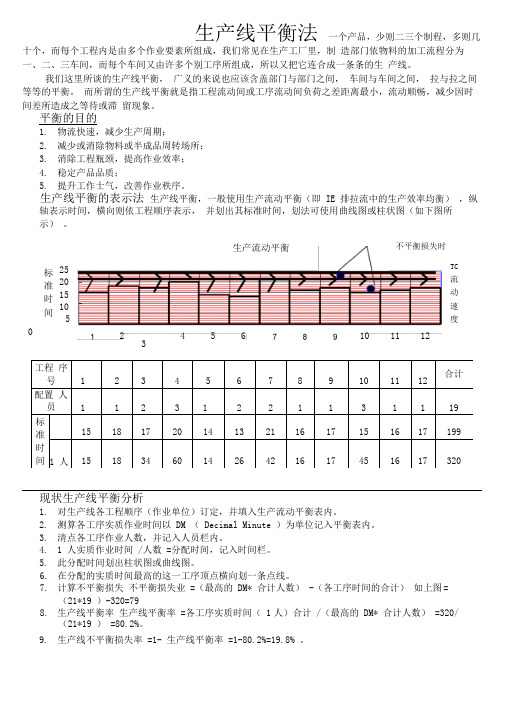
生产线平衡法 一个产品,少则二三个制程,多则几十个,而每个工程内是由多个作业要素所组成,我们常见在生产工厂里,制 造部门依物料的加工流程分为一、二、三车间,而每个车间又由许多个别工序所组成,所以又把它连合成一条条的生 产线。
我们这里所谈的生产线平衡, 广义的来说也应该含盖部门与部门之间, 车间与车间之间, 拉与拉之间等等的平衡。
而所谓的生产线平衡就是指工程流动间或工序流动间负荷之差距离最小,流动顺畅,减少因时间差所造成之等待或滞 留现象。
平衡的目的1. 物流快速,减少生产周期;2. 减少或消除物料或半成品周转场所;3. 消除工程瓶颈,提高作业效率;4. 稳定产品品质;5.提升工作士气,改善作业秩序。
生产线平衡的表示法 生产线平衡,一般使用生产流动平衡(即 IE 排拉流中的生产效率均衡) ,纵轴表示时间,横向则依工程顺序表示, 并划出其标准时间,划法可使用曲线图或柱状图(如下图所示) 。
25 2015 10 5现状生产线平衡分析1. 对生产线各工程顺序(作业单位)订定,并填入生产流动平衡表内。
2. 测算各工序实质作业时间以 DM ( Decimal Minute )为单位记入平衡表内。
3. 清点各工序作业人数,并记入人员栏内。
4. 1 人实质作业时间 /人数 =分配时间,记入时间栏。
5. 此分配时间划出柱状图或曲线图。
6. 在分配的实质时间最高的这一工序顶点横向划一条点线。
7.计算不平衡损失 不平衡损失业 =(最高的 DM* 合计人数) -(各工序时间的合计) 如上图 =(21*19 )-320=798. 生产线平衡率 生产线平衡率 =各工序实质时间( 1人)合计 /(最高的 DM* 合计人数) =320/(21*19 ) =80.2%。
9. 生产线不平衡损失率 =1- 生产线平衡率 =1-80.2%=19.8% 。
工程 序号 1 2 3 4 5 6 7 8 9 10 11 12 合计配置 人员 1 1 2 3 1 2 2 1 1 3 1 1 19 标 准 时间15 18 17 20 14 13 21 16 17 15 16 17 199 1 人1518346014264216174516173203标 准 时间不平衡损失时生产流动平衡26 10 11 124 5 TC流 动 速 度。
精益生产系列培训--线平衡

线平衡
目录
线平衡的概念 线平衡的目的及相关
生产线平衡率 平衡率改善 改善四原则 线平衡的意义 总结
线平衡的概念
生产线平衡 是对生产的全部工序进行作业时间的平均化, 调整作业的负荷度,以便各作业时间可以最大化的接近, 最终消除各种等待浪费现象,提高生产线的整体效率
线平衡的目的
瓶颈工 序
ECRS四大原则
取消 作业动作是否有存在必要,(工序) 合并 作业动作或作业工序的再次组合 重排 作业动作的先后,多工序,多动作的重新分布 简化 简化人降低,提升成本优势 单件流,减少在制 以线平衡为基础,实现柔性生产系统 IE分析改善的基础
生产线中作业时间最长的工站的工时,称之为瓶颈时间 生产线的产出取决于瓶颈工序的产出 线平衡的目的...消除工序间的在制品,实现产品的一件一件的流动
生产线平衡率
LBR(线平衡率)是衡量生产线中,各工站节拍符合度的一个综合比值
平衡率=
单件标准时间总和 瓶颈工序×工站数
×100%
生产线平衡率改善
线平衡的改善,在于不断缩短瓶颈时间,提高节拍产出 瓶颈的时间会不断的降低,瓶颈工序也会转移,但瓶颈永远存在 线平衡的改善四原则ECRS
- 1、下载文档前请自行甄别文档内容的完整性,平台不提供额外的编辑、内容补充、找答案等附加服务。
- 2、"仅部分预览"的文档,不可在线预览部分如存在完整性等问题,可反馈申请退款(可完整预览的文档不适用该条件!)。
- 3、如文档侵犯您的权益,请联系客服反馈,我们会尽快为您处理(人工客服工作时间:9:00-18:30)。
生产线平衡评价指标
生产线平衡率
平滑性系数(Smoothness Index)
生产线平衡概念
生产线平衡的一般数学表达:
给定一个无回路的有向图G=(E,P),节点E表示作业 要素集合,弧P表示生产作业元素之间的先后关系集合。 一个节点j∈E有一个值Tj(j=l,2,…,n)表示作业时间 。生产线平衡问题就是求节点集E的一个划分:
程序分析(过程分析)
流程分析 线路图分析
程序分析(过程分析)
流程分析 线路图分析
程序分析(过程分析)
流程分析 线路图分析
物流方向
操作分析
动作分析
作业测定
运用各种技术来确定合格工人按照规定的 作业标准,完成某项工作所需要的时间
现场测时方法 经验估算法 工时计算法 模特法
……
作业测定——模特法
生产线平衡概念
优先约束
区域约束
与生产工位布置有关的限制,分为正区域约束和负区 域约束。正区域约束是指某些确定的作业要素应该彼此就 近设置;负区域约束是指作业要素之间相互干涉,在位置 上不应靠近的限制条件
位置约束
产品装配作业受到空间的限制。在大型的生产线上, 如汽车的装配线上,由于产品比作业人员可完成的装配作 业空间大,不能完成其周边的装配作业。
生产线平衡问题研究方法
优化方法 启发式方法 仿真方法
装配生产线平衡设计
启发式方法——韩格逊-伯尼法 (位置加权法、阶位法)
例:某产品装配共需11个作业要素,其先后顺序及作业 时间如图,CT=10 min,试进行流水线的平衡。
装配生产线平衡设计
1)编制作业要素先后矩阵
装配生产线平衡设计
2)计算作业要素阶位
生产线平衡概念
节拍(Cycle Time)
CT - 生产节拍 TW - 计划期内有效总工作时间 Q - 计划期内制品数量
生产线平衡概念
优先约束 区域约束 位置约束
作业要素优先关系图 (作业要素示意图)
生产线平衡概念
优先约束 区域约束 位置约束
优先关系矩阵
Mij=l表示作业要素i是作业要素j的紧前 作业,在作业要素分配时必须将作业要 素i分配在j所在工位之前的工位上。
生产流程-生产线平衡_图文.ppt
生产线组织设计
主要内容
• 确定流水线的生产速度--节拍 • 工序同期化 • 计算设备数量和负荷系数 • 计算工人人数 • 选择运输装置 • 流水线平面设计 • 流水线技术经济评价
生产线平衡意义:
保证生产连续性和均衡性
保证设备、人力的负荷平衡,从而能提高设备、工时 利用率,提高生产效率。 减少在制品,节约物资消耗,加速流动资金的周转, 从而阶位由大到小排列,并表明各作业要素紧前作业要素
4)作业要素分配
生产线平衡措施
工序的分解和合并是工序同期化常用的方法。 受到机器限制,工序不能分解和合并时
.提高设备的生产效率 .改进工艺和操作方法
………
工作研究(work study)
程序分析 操作分析 动作分析 工作测定
作业测定——模特法
光学镜头组件装配
作业测定——模特法
装镜片工位 MOD 数分析表
作业测定——模特法
该工位的作业标准时间计算如下:
ST =∑MOD×0·129×1·3s=78×0·129×1·3s=13·08s
宽放量取30% 其中:作业和车间宽放率18%
私事宽放率4% 疲劳宽放率8%
作业测定——模特法
生产线平衡措施
ECRS改善法
• 消除(Elimination):什么作业可以不做? • 合并(Combination):那些作业可以合并? • 重排(Rearrange):调整作业的順序是否会更有效率? • 简化(Simplification):是否能简化每一個作业,
以縮短作业時間?
生产线平衡措施
流程重组
生产线平衡措施
动作经济原则—“工具物料应按最佳顺序排列”
生产线平衡问题研究
生产线平衡问题研究
生产线平衡问题研究
毛坯——切棒——粗车(外协)——划线 ——加工中心——钻——镗——磁探。
使一定的目标得到优化,满足一定的约束条件。
生产线平衡问题分类
(l) 确定了生产线的节拍cT,使生产平衡率最大化。 该类问题等价于CT一定求工位数目最少:
(2)确定了生产线上的工位数m,使生产平衡率最大化。 该类问题等价于m一定求生产线的最小生产节拍:
(3)己经确定了m和CT,目标函数为使平滑性指数最小化: