玻璃熔制 玻璃熔制
3 玻璃的熔制及熔(1)讲解

(5)玻璃液冷却阶段 将清澄和均化了的玻璃液均匀降温,使玻璃 液具有成型所需的黏度; 在冷却阶段应不破坏玻璃液的质量; 浮法玻璃冷却阶段结束的温度在1100~ 1050℃左右。
3.1.1 配合料的熔化
(1)配合料的加热及初熔 (2)各种反应简介 多晶转变 盐类分解 水分的逸出 (3)成分的挥发 R2O的挥发 由纯碱引入时:引入量×0.032% 由芒硝引入时:引入量×0.06%
3.1.3 澄清
(1)目的 消除玻璃液中的气泡 (2)玻璃液中的气泡形态和种类 形态:可见气泡、溶解气泡、化学结合的气 体。还有熔体表面上的气体。 种类: CO2、SO2、SO3、N2、O2、H2O、H2
(3) 排泡与去气 澄清是排出玻璃液中的可见气泡; 去气是全部排除玻璃液中的气体,包括化学 结合的气体。
B.二次气泡(灰泡,直径小于0.1mm) ①硫酸盐和其他盐类的继续分解; ②溶解气体的析出; ③耐火材料气泡 ④玻璃液流股间的化学反应; ⑤电化学反应
r=1mm时, 2σ/r =0.6kPa; r<0.01mm时, 2σ/r > 0.06MPa; R= 0.001mm时, 2σ/r= 0.6MPa。 可以看出,表面张力对大气泡的影响可以忽 略,对小气泡的影响则是巨大的。 玻璃液中存在的微小气泡,在温度降低时, 内部的压力急剧增大,使气泡内的气体分压 明显大于玻璃液中气体的分压,从而溶解于 玻璃液中;温度升高时,气泡又会析出。
B.新气泡的产生 澄清好的玻璃液一般不能再次产生气泡。 原因是: 新生气泡的半径r≈0,需要克服的
2σ/r≈∞。
(8)影响澄清的因素
A.配合料中的气体率 一般15~20% B.澄清温度 温度高,黏度小,有利于澄清;熔窑温度受 耐火材料的限制。 C.窑压 微正延长澄清时间 B.提高澄清温度 C.搅拌 D.鼓泡 E .加澄清剂(最常用)
玻璃的熔制过程
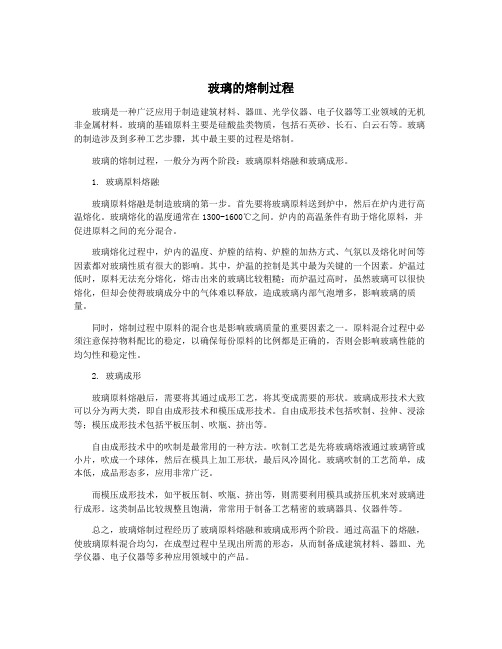
玻璃的熔制过程玻璃是一种广泛应用于制造建筑材料、器皿、光学仪器、电子仪器等工业领域的无机非金属材料。
玻璃的基础原料主要是硅酸盐类物质,包括石英砂、长石、白云石等。
玻璃的制造涉及到多种工艺步骤,其中最主要的过程是熔制。
玻璃的熔制过程,一般分为两个阶段:玻璃原料熔融和玻璃成形。
1. 玻璃原料熔融玻璃原料熔融是制造玻璃的第一步。
首先要将玻璃原料送到炉中,然后在炉内进行高温熔化。
玻璃熔化的温度通常在1300-1600℃之间。
炉内的高温条件有助于熔化原料,并促进原料之间的充分混合。
玻璃熔化过程中,炉内的温度、炉膛的结构、炉膛的加热方式、气氛以及熔化时间等因素都对玻璃性质有很大的影响。
其中,炉温的控制是其中最为关键的一个因素。
炉温过低时,原料无法充分熔化,熔击出来的玻璃比较粗糙;而炉温过高时,虽然玻璃可以很快熔化,但却会使得玻璃成分中的气体难以释放,造成玻璃内部气泡增多,影响玻璃的质量。
同时,熔制过程中原料的混合也是影响玻璃质量的重要因素之一。
原料混合过程中必须注意保持物料配比的稳定,以确保每份原料的比例都是正确的,否则会影响玻璃性能的均匀性和稳定性。
2. 玻璃成形玻璃原料熔融后,需要将其通过成形工艺,将其变成需要的形状。
玻璃成形技术大致可以分为两大类,即自由成形技术和模压成形技术。
自由成形技术包括吹制、拉伸、浸涂等;模压成形技术包括平板压制、吹瓶、挤出等。
自由成形技术中的吹制是最常用的一种方法。
吹制工艺是先将玻璃熔液通过玻璃管或小片,吹成一个球体,然后在模具上加工形状,最后风冷固化。
玻璃吹制的工艺简单,成本低,成品形态多,应用非常广泛。
而模压成形技术,如平板压制、吹瓶、挤出等,则需要利用模具或挤压机来对玻璃进行成形。
这类制品比较规整且饱满,常常用于制备工艺精密的玻璃器具、仪器件等。
总之,玻璃熔制过程经历了玻璃原料熔融和玻璃成形两个阶段。
通过高温下的熔融,使玻璃原料混合均匀,在成型过程中呈现出所需的形态,从而制备成建筑材料、器皿、光学仪器、电子仪器等多种应用领域中的产品。
玻璃窑炉的理论课

玻璃窑炉的理论课一、玻璃的熔制过程:玻璃的熔制过程分为五个阶段:(一)硅酸盐形成阶段:在高温(约800—1000℃)作用下发生变化:如粉料受热、水分蒸发、盐类分解、多晶转变等,变成不透明的烧结物;(二)玻璃形成阶段温度升高到1200℃时,各种硅酸盐开始为熔融,继续升高温度,未熔化的硅酸盐和石英砂完全熔解于熔融体中,形成大量可见气泡,这一阶段称为配合料熔化阶段;(三)玻璃液澄清阶段:当温度达到1400—1500℃时,玻璃液的黏度降低,使气泡大量逸出;(四)玻璃液均化阶段:达到玻璃液均化主要依靠扩散和对流作用。
高温是一个主要条件,因为它可以减少玻璃液黏度,使扩散作用加强,另外搅拌是提高均匀性的好方法;(五)玻璃液冷却阶段:澄清均化后的玻璃液黏度太小,不适于成型,必须通过冷却达到成形温度,成形温度比澄清温度低200—300℃。
以上各阶段不一定按顺序进行,各阶段没有明显的界线的二、对窑炉关键部位的了解和掌握以及作用1)加料口的作用:玻璃池窑将加料池发展为预熔池。
预熔池内的温度保持在1100—1300℃,配合料内各组分之间的硅酸盐反应在预熔池内开始,料堆表面已经开始熔融。
已初步熔化的料堆,当它进入熔化池后,其熔化速度可以加快。
在熔化池面积一定时,熔化速度加快了,相对来说,其澄清时间就延长了。
因此,加料口的作用就是能提高熔化率、改善玻璃质量、降低热耗的作用;池内粉料飞扬的情况大大减少,格子体堵塞情况大大改善。
2)窑坎:窑坎是放在窑池深层的挡墙,墙高为池深的1/2以上,有的可达到3/4;窑坎是控制玻璃液流,提高熔化率的技术措施。
窑坎作用是:迫使熔化部玻璃液呈一薄层全部流经窑池上层,经高温加热后再进入流液洞,这样提高了玻璃液的温度,有利于气泡的排除,加快澄清速度,从而改善玻璃液质量;设置窑坎后,玻璃液在窑坎处产生回旋,可延迟玻璃液在熔化部停留时间,可阻挡池底脏料流往澄清部。
3)流液洞:流液洞是熔化部和冷却部的玻璃液连通起来的位于池窑底部的涵洞,是由一套特制的优质耐火材料砌筑成的。
玻璃熔制过程的五个阶段
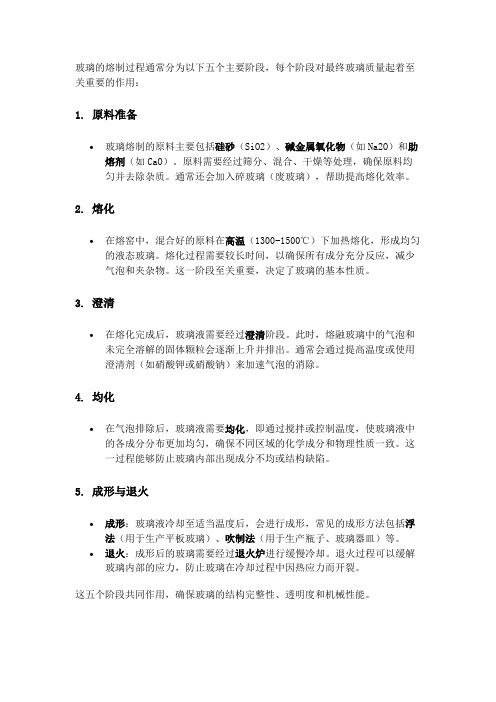
玻璃的熔制过程通常分为以下五个主要阶段,每个阶段对最终玻璃质量起着至关重要的作用:
1. 原料准备
•玻璃熔制的原料主要包括硅砂(SiO2)、碱金属氧化物(如Na2O)和助熔剂(如CaO)。
原料需要经过筛分、混合、干燥等处理,确保原料均
匀并去除杂质。
通常还会加入碎玻璃(废玻璃),帮助提高熔化效率。
2. 熔化
•在熔窑中,混合好的原料在高温(1300-1500℃)下加热熔化,形成均匀的液态玻璃。
熔化过程需要较长时间,以确保所有成分充分反应,减少
气泡和夹杂物。
这一阶段至关重要,决定了玻璃的基本性质。
3. 澄清
•在熔化完成后,玻璃液需要经过澄清阶段。
此时,熔融玻璃中的气泡和未完全溶解的固体颗粒会逐渐上升并排出。
通常会通过提高温度或使用
澄清剂(如硝酸钾或硝酸钠)来加速气泡的消除。
4. 均化
•在气泡排除后,玻璃液需要均化,即通过搅拌或控制温度,使玻璃液中的各成分分布更加均匀,确保不同区域的化学成分和物理性质一致。
这
一过程能够防止玻璃内部出现成分不均或结构缺陷。
5. 成形与退火
•成形:玻璃液冷却至适当温度后,会进行成形,常见的成形方法包括浮法(用于生产平板玻璃)、吹制法(用于生产瓶子、玻璃器皿)等。
•退火:成形后的玻璃需要经过退火炉进行缓慢冷却。
退火过程可以缓解玻璃内部的应力,防止玻璃在冷却过程中因热应力而开裂。
这五个阶段共同作用,确保玻璃的结构完整性、透明度和机械性能。
玻璃的熔制及成型
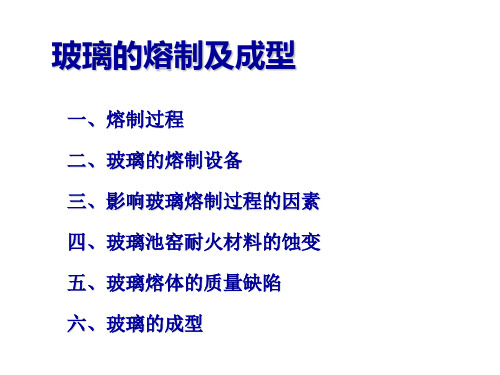
(3)搅拌与鼓泡
在池窑上增设搅拌与鼓泡装置可提高玻璃液的澄清和均化
速度。搅拌装置通常设置在池窑的卡脖、供料道等处,鼓泡通 常设在熔化池的料堆区和热点区。 (4)电助熔 (5)富氧燃烧 (6)高压与真空熔炼
1. 影响耐火材料蚀变的因素
(1)侵蚀介质的种类
(2)耐火材料的性能 (3)池窑作业的工艺制度
不变。 (1)硅质耐火材料的蚀变
(2)电熔锆刚玉(AZS)耐火材料的蚀变
(3)格子砖的蚀变
(1)硅质耐火材料的蚀变
硅质耐火材料在日用玻璃池窑上用做大碹及胸墙等的
耐火材料。因此主要承受碱性挥发物的侵蚀。在正常使用 情况下,窑温不高于1600oC时,硅质是很耐侵蚀的。
表面蚀变
内部蚀变 多晶蚀变
AZS砖的蚀变主要是: 玻璃相结合物被溶解;
刚玉与碱性氧化物发生变代反应,生成β-Al2O3和霞石。
(3)格子砖的蚀变
由于配合料及玻璃液的挥发物,燃料燃烧废气中某些
成分(如SO3)等随烟气进入蓄热室,在格子砖的表面侵 蚀形成腐蚀性冷凝液,形成对耐火材料的侵蚀。 此外,热作用也是格子砖易损的原因之一。对于下层
优质玻璃的重要前提之一,同时维持合理的作业制度也是 降低玻璃熔化过程的低耗、延长玻璃池窑窑龄的有效手段。 (1)温度制度 (2)压力制度 (3)泡界线 (4)液面
(5)气氛制度
6. 加速玻璃熔化的辅助手段
(1)助熔剂
助熔剂又称加速剂。 较低温度下先生成液相,然后与SiO2反应生成玻璃; 降低高温玻璃熔体的黏度,提高玻璃的透热性。 (2)澄清剂 常用的澄清剂有白砒、三氧化二锑、芒硝、食盐等。
保证玻璃液的热均匀性,并防止 出现温度波动,以免引起二次气 泡。
玻璃的熔制过程

五、玻璃液冷却阶段 为了使玻璃液的粘度增高到成形制度 所需的范围,需进行玻璃液的冷却℃, 冷却的玻璃液温度要求均匀一致,以有利 于成型。
玻璃熔制的各个阶段,各有其特点,同时它们又是彼 此互相密切联系和相互影响的。在实际熔制中,常常是同 时进行或交错进行的。这主要决定于熔制的工艺制度和玻 璃熔窑结构的特点。
第一节 玻璃的熔制过程 玻璃的熔制:按照料方混合好的配合料,经过高 温加热形成均匀的、纯净的、透明的、无气泡的 (即把气泡、条纹和结石等减少到容许限度),并 符合成型要求的玻璃液的过程,称为玻璃的熔制。 玻璃的熔制是一个非常复杂的过程,它包括一系 列物理的、化学的、物理化学的现象和反应。这些 现象和反应的结果,使各种原料的机械混合物变成 了复杂的熔融物即玻璃液。 各种配合料在加热形成玻璃过程中的物理的、化 学的和物理化学的现象,是基本相同的,它们在加 热时所发生的变化大致如下:
1)物理过程:包括配合料的加热,吸附水分 的蒸发、排除,某些单独组份的熔融,某 些组份的多晶转变,个别组份的挥发等; 2)化学过程:包括固相反应,各种盐类的分 解,水化物的分解、化学结合水的排除, 组份间的相互反应及硅酸盐的生成; 3)物理化学过程:包括低共熔物的生成,组 份或生成物间的相互溶解,玻璃和炉气介 质之间的相互作用,玻璃液和耐火材料的 相互作用及玻璃液和其中夹杂气体的相互 作用等。
二、玻璃液形成阶段 硅酸盐形成阶段生成的硅酸钠、硅酸钙、 硅酸铝等烧结物及反应剩余的大量SiO2在温 度继续升高时开始熔融,易熔的低共熔混合 物首先开始融化,同时,硅酸盐烧结物和剩 余的SiO2互相溶解和扩散,由不透明的半熔 融烧结物转变为透明的玻璃液,不再含有未 反应的配合料颗粒。但玻璃液中存在大量的 气泡,化学组成和性质也不均匀,有许多条 纹。平板玻璃形成大约在1200~1400 ℃完成。
第三节 玻璃的熔制
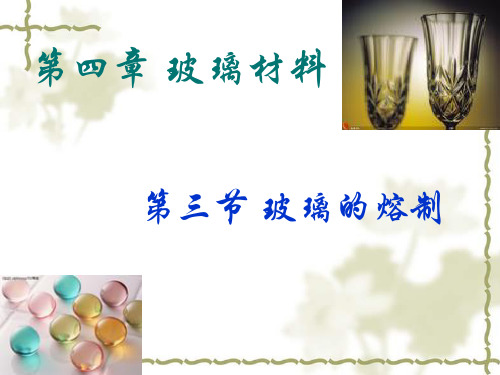
在熔制无色瓶罐玻璃的普通纯碱配合料时,必须保 持氧化气氛。 熔制以碳粉作还原剂的纯碱-芒硝配合料时,为保持碳 粉在加料口不被氧化,须还原气氛;最后又必须将碳粉完 全烧尽,须氧化气氛。
三、玻璃体的缺陷
玻璃体内由于存在各种夹杂物,引起玻璃体均匀性 的破坏,称为玻璃的缺陷。 通常所说的缺陷主要是指气泡、条纹和结石三大缺 陷。他们分别是均匀玻璃中的气态、玻璃态和固态夹杂 物。 1、气泡 2、条纹、 线道、结瘤 3、结石
化学过程
1. 固相反应 2. 盐类分解 3. 水化物分解 4. 结晶水分解 5. 硅酸盐形成 与相互作用
物理化学过程
1. 低共熔物形成 2. 固态溶解,液态互溶
3. 玻璃液、炉气、气泡间
的相互作用 4. 玻璃液与耐火材料作用
2、玻璃的熔制过程
掌握
玻璃熔制
硅酸盐形 成阶段
玻璃形成 阶段
玻璃液澄 清阶段
D. 玻璃液的对流 玻璃液的对流有利于均化,但对耐火材料侵蚀加大; E. 气泡的上升 澄清过程,带动玻璃液均化。
玻璃液的冷却:1100 ~1200℃ 将玻璃液的温度降低200-300℃; 玻璃液具有成型必须的粘度。
定义
冷却是将玻璃液均匀冷却到 成型温度的过程。
注意!!
整个冷却过程应力求平稳 进行,以保证玻璃液的热均 匀性,并防止出现温度波动, 以免引起二次气泡。
澄清时间 通常延长澄清时间利于排除气泡。但硫 酸盐玻璃不然。 机械搅拌、超声波作用 使玻璃液沸腾搅拌。压力与气氛。窑内 必须保持微正压或微负压,负压过大,使冷 气吸入窑内,玻璃液产生大量气泡;相反正 压过大,不利于气体排除。
玻璃工艺学14玻璃的熔制

三.硅酸盐形成和玻璃形成阶段的中石英的溶解
溶 解100 的 的 50 含 量 1350℃ 1250 ℃
Na2O•2SiO2+CaSiO3+MgSiO3
Na2SiO3+CaSiO3+MgSiO3
SiO2 %
8
16
24
32
分钟
说明:1、玻璃形成阶段速度慢,玻璃形成阶段速度快; 2、温度的提高能加快硅酸盐形成和玻璃形成的反应 速度; 3、随时间延长,反应速度降低。
物 理 变 化 化 学 变 化 物 理 化 学 过 程
配合料加热升温 配合料脱水
固相反应 碳酸盐、硫酸盐、硝酸 盐的分解
共熔体的生成 固态的溶解与液态间互溶
各组分的熔化
晶相转变 个别组分的挥发
水化物的分解
化学结合水的分解 硅酸盐的形成与相互作 用
玻璃工艺学
玻璃液、炉气、气泡间的相互 作用
玻璃液与耐火材料间的作用
玻璃工艺学
1
第十四章
玻璃的熔制
主要内容: 玻璃的熔制过程及其影响因素,熔制制度,熔窑和耐火材 料的侵蚀过程等。
玻璃工艺学 2
第一节 玻璃熔制过程概述
玻璃的熔制过程就是将配合料经高温加热熔融成为均匀的、 无气泡的符合成型要求的玻璃液的过程。 玻璃熔制过程是一个很复杂的过程,它包括一系列的物理、 化学、物理化学反应。研究指出各种不同的配合料在加热时发生 如下所列的各种变化:
玻璃工艺学 21
说明: ①气泡内的压力 也是影响 澄清的动力 因素;
②气泡的半径r越大,总压力就越小,分压力也越小;
因此,溶解于玻璃液中的气体易于进入较大的气泡中而
使之增大,从而易于浮出玻璃液,而后破裂。 反之,对于小气泡,则总压力和分压力就越大,不易 增大,但气体组分会因此而易于扩散进入玻璃液中去。 根据: PV= n RT
- 1、下载文档前请自行甄别文档内容的完整性,平台不提供额外的编辑、内容补充、找答案等附加服务。
- 2、"仅部分预览"的文档,不可在线预览部分如存在完整性等问题,可反馈申请退款(可完整预览的文档不适用该条件!)。
- 3、如文档侵犯您的权益,请联系客服反馈,我们会尽快为您处理(人工客服工作时间:9:00-18:30)。
5 玻璃熔制
5.1 实验目的意义
玻璃是无机材料的一个重要领域。
它所涉及的应用范围相当广泛,在现代高科技领域,特种玻璃制品有激光玻璃、零膨胀微晶玻璃、特种光纤、特种玻璃涂层…。
伴随着科技的高速发展,玻璃制备的方法也逐渐多样化,从传统的高温熔制方法到现在的低温液相法、气相沉积法。
但是传统的高温熔制法仍然占据着当前玻璃制品生产的绝大部分。
:
本实验的目的
本实验的目的:
(1)通过玻璃的高温熔制实验了解玻璃的制备工艺流程。
(2)了解影响玻璃制备的各种物理、化学因素。
(3)根据玻璃的性能要求能独立完成玻璃的制作配方、制定工艺流程图。
(4)了解玻璃的高温熔制设备。
5.2 实验基本原理
玻璃的基本概念::
(1) 玻璃的基本概念
按照现代玻璃的定义主要包含两个条件即A: 存在非晶态固体。
B: 表现出玻璃的转变现象。
根据上述条件玻璃的范围被拓展了,与此同时制备玻璃的方法也发生了变化,除了高温熔制以外出现了低温合成、气相沉积…。
(2) 玻璃的基本组成
玻璃的基本组成::
按照玻璃组成中的化合物主体分类可分为硅酸盐、磷酸盐、氟化物玻璃、硫系玻璃…。
通常在玻璃组成设计过程中都是根据所需的特定物理、化学性能指标进行单一或者多种化合物的组合。
(3) 熔融法玻璃制备过程(工艺流程图):
(A)玻璃配合料: 根据配方确定玻璃的主要原料(Si、Al、B、Ca、Na…),辅助原料(氧化
剂、还原剂、助熔剂、澄清剂、晶核剂、着色剂、脱色剂),玻璃熟料(同组成碎玻璃,起助熔和节能效果)。
(B)玻璃高温熔融过程:玻璃配合料加热→配合料熔化(主要是完成玻璃化反应)→残余原
料颗粒的熔解→澄清→均化→调节到玻璃的成形温度。
(C)玻璃制备工艺流程图:玻璃配合料→混合(控制粉体的颗粒度、均匀度、水分)→坩
埚(根据需要选择坩埚的种类和尺寸)→高温熔制设备(自动控温、定时,制定升温、保温、冷却曲线图)→玻璃成形设备(手工成形、自动成形)→退火设备(去除玻璃应力)→检验→包装入库。
5.3 实验仪器及装置
熔制玻璃的高温电炉有多种型号、规格。
常用玻璃的熔制温度范围在1250~1700℃之间,因此必须根据特定的配方合理地选择高温电炉。
高温电炉通常分为两类:(A) 硅碳棒型(1200~1450℃);(B) 硅钼棒型(1450~1700℃)。
上述两类高温电炉都能进行自动定时、自动控温。
实验高温电炉装置如图(13):
图8高温电炉装置
制备
实验样品的要求及制备
5.4 实验样品的要求及
(1)选择所要制备玻璃的配方。
(2)按配方的需求对各种化合物分别进行称量、清除原料中的杂质。
原料如受潮湿还必须
干燥处理。
(3)将已称量的各种化合物均匀混合(控制粉体的颗粒度、均匀度、水分)。
根据需要进行球
磨、过筛。
水分控制为3~5%。
(4)按配方的需求选择坩埚的种类和尺寸(由实验教师指导)。
5.5 实验步骤
(1)完成实验前的准备工作:手套(含石棉手套)、石棉板、护目镜、工作服装、口罩、坩埚
钳子(各种尺寸)、不锈钢水桶(含水)、石英砂、氧化铝粉末。
(2)准备玻璃成型模具(选择尺寸、预热处理),搅拌棒安装到位。
(3)保持实验环境整洁(清除易然物品、留存工作活动空间、灭火器)。
(4)检查实验高温电炉装置及配套设备的工作状态(由实验教师指导),确认安全、可操作。
(5)开启高温电炉装置及配套设备的工作电源,保持低温工作状态20分钟(由实验教师指
导)。
(6)将设定的升温、保温、冷却曲线方案输入高温电炉控制装置内的电脑并编程(确定升温
速率,由实验教师指导)。
(7)按照设定的升温、保温、冷却曲线方案及时、正确地将空坩埚放入高温电炉的炉膛中
间(炉膛中间铺展石英砂),随炉升温。
(8)按照设定的升温、保温、冷却曲线方案及时、正确地将玻璃配合料放入坩埚内(根据玻
璃配合料量及坩埚尺寸分批加入),注意玻璃配合料溢出坩埚(由实验教师指导)。
(9)按照设定的升温、保温、冷却曲线方案根据需要开启搅拌器工作电源,进行搅拌(由实
验教师指导)。
(10)在上述实验操作过程中必须及时观察高温电炉装置及配套设备的工作状态(硅碳棒、硅
钼棒可能发生断裂;实验坩埚开裂;断电以及其他突发事件),将情况通告实验教师。
(11)按照设定的升温、保温、冷却曲线方案将玻璃液体成型(浇注成型),在此操作过程中必
须由实验教师指导。
(12)将成型的玻璃坯体放入退火炉内进行退火处理,在此操作过程应防止玻璃坯体的突然
开裂(由实验教师指导,退火温度、时间应提前设定并使退火炉保持工作状态)。
(13)重新设定高温电炉装置及配套设备的工作状态(保持高温电炉的最小电流),由实验教师
指导清理实验工作现场,整理操作工具并上交实验教师。
(14)在整个实验过程中应密切观察高温电炉装置及配套设备的工作状态;实验坩埚及玻璃
配合料在高温电炉中的状态;玻璃液的熔制状态(气泡、条纹、澄清度、杂质…)。
将上述实验过程全部记录在案并结合已成型玻璃坯体的各项物理、化学性能指标进行分析和讨论。
(15)在整个实验过程中必须注意人身安全,严格按照操作程序进行实验,以免发生以外事
故。
5.6 实验结果与数据处理
(1)记录所要制备玻璃的配方及可能达到的物理、化学性能指标。
(2)记录玻璃配合料的换算表。
(3)记录玻璃制备工艺流程图及升温、保温、冷却曲线图。
5.7 实验结果与讨论
(1)影响玻璃制备的各种因素。
(2)探索玻璃配方中的元素、化合物与玻璃物理、化学性能之间的关系。
(3)改进与完善玻璃制备的途径。