莱钢1500可逆轧机工作辊、中间辊轴承座油气润滑改造
油气润滑技术在热连轧上的应用
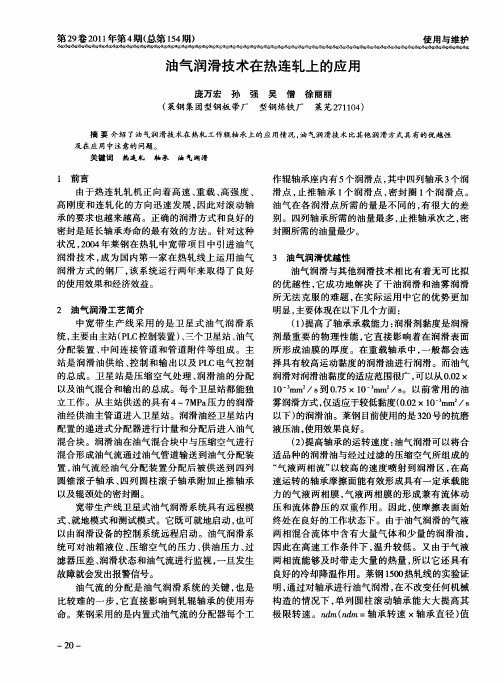
式中: —_ 单个轴所需要的润滑油量/ L h ; ( /) m C 一 系数 , 润滑 C=0 0 3 .0 5 - 油气 . 0 —0000 , 0 0 油雾润滑C 0 0 , = . 0 对于油脂润滑 C 0 5 =
[ 接第 1 页】 上 9 这样 的分 析方 法 对两 种 电 动机 的闭环 系统是 完 全
2 油气 润 滑工 艺简 介 中 宽 带 生 产 线 采 用 的 是 卫 星 式 油 气 润 滑 系 统, 主要 由主站 (L 控 制 装置 )三 个 卫星 站 、 PC 、 油气
作辊轴承座 内有 5 个润滑点 , 其中四列轴承3 个润 滑点 , 推轴 承 1 润滑点 , 封 圈 1 润 滑点 。 止 个 密 个 油气 在各 润 滑 点 所 需 的量 是 不 同 的 , 很 大 的 差 有 别 。 四列轴 承 所需 的油 量最 多 , 推轴 承 次 之 , 止 密 封 圈所 需 的油 量最 少 。
关 键 词 热 连 轧 轴承 油 气 润滑
1 前 言
由于 热 连 轧 轧 机 正 向 着 高 速 、 载 、 强 度 、 重 高 高 刚度 和 连 轧 化 的方 向迅 速 发 展 , 因此 对 滚 动 轴 承 的要 求 也 越来 越 高 。正确 的润 滑方 式 和 良好 的
密封是延长轴承寿命的最有效的方法 。针对这种 状况 ,04 20 年莱钢在热轧 中宽带项 目中引进油气 润滑技术 , 成为 国内第一家在热轧线上运用油气 润 滑 方 式 的钢 厂 , 系 统 运 行 两 年 来 取 得 了 良好 该 的使用 效果 和经 济效 益 。
低速时 , 测速反馈也不能使其特性得到改善 , 因而 可能 出现下降溜钩现象 。维护工作 中, 速度反馈 的脉 冲编 码 器 出现 故 障 不 能 轻 易 取 消 , 否则 影 响 行 车正 常使 用 。
轧制润滑工艺在莱钢1500mm热连轧精轧机组中的应用

轧制润滑工艺在莱钢1500mm热连轧精轧机组中的应用热轧时采用轧制工艺润滑能明显起到降低轧机负荷,减少轧辊消耗、改善成品表面质量的作用,本文系统介绍轧制工艺润滑在莱钢1500mm热连轧精轧机组中的应用。
标签:轧制润滑;轧制力;轧辊磨损。
1、概述莱钢1500mm热轧生产线于2005年投产,经过近两年多的运行,设备状况、工艺过程基本稳定,随着产量的逐步提高,产品厚度逐渐向薄规格延伸,轧辊工作负荷明显增加,加速了轧辊的剥落和磨损,频换的换辊又造成轧制作业率的降低。
为此在该生产线增设轧制润滑装置: 精轧机组采用油-水混合喷射润滑系统对工作辊进行润滑的轧制方式。
热轧时采用工艺润滑后,轧辊与轧件之间被一层边界润滑膜隔开,可以起到如下作用:1) 降低热轧时轧辊与轧件间的摩擦系数,从而降低轧制力,容易轧制薄规格带钢。
2) 减少轧辊消耗和储备,提高作业率。
3) 减少氧化皮压入,改善轧辊表面状态和轧后成品表面质量4) 改善制品内部组织性能,提高深冲钢的深冲性能。
2、系统组成及控制原理2.1系统组成:本系统设备主要由贮油箱、工作油箱、工作水箱、加油泵、计量泵站、水泵站、上下集水管、喷嘴和电控系统等组成。
2.2系统原理储油箱中加热至一定温度的油经供油泵送至工作油箱中;并由计量泵经供油电磁阀送至各架轧机的油水混合器。
水箱中加热至一定温度的水由供水泵送至各架轧机旁的混合器与油混合后送至各架轧机的上下工作辊面上进行润滑。
如图1所示。
图1:轧制润滑示意图2.3系统控制:2.3.1系统配置本系统由PLC一套。
其主要配置有:电源、CPU、通讯摸板、开关量输入、开关量输出、模拟量输入、研华工控机、变频器。
系统见图2:控制系统用PLC实施自动控制。
本系统在地下室配有两面柜子,一个PLC 柜子,一个变频器柜。
在控制室操作台上放置计算机作为监控使用。
有网线连接柜子和计算机完成通讯;另外,由DP网连接S7-400与变频器完成通讯。
2.3.2控制过程润滑轧制时喷油水混合液程序的控制如下:轧钢时,在轧机前的热金属检测器首先检测到来钢的信号,当钢咬入F6架后(可根据需要设定延时),同时控制F1、F2、F3、F4、F5和F6架喷水、喷油。
莱钢1500mm六辊可逆式冷轧机的板形控制技术

1前言莱钢板带厂冷轧生产线始建于2006年1月,同年6月份投产,该生产线主要是1台单机架六辊可逆式冷轧机,年设计能力20万t。
为了减少断带,提高产品质量,对主要板形控制技术进行了分析。
2主要板形控制技术2.1液压弯辊技术液压弯辊技术分为工作辊液压弯辊和中间辊液压弯辊,工作辊弯辊有液压正弯和液压负弯,弯辊力为-360~+720kN;中间辊只有液压正弯,弯辊力为0~+360kN。
在轧辊凸度不足或磨损情况下可以采用正弯,增大轧辊凸度,防止带钢边浪,而负弯可以减少轧辊有效凸度,防止带钢中间浪。
2.2轧辊分段冷却控制技术分段冷却控制技术通过调整冷却液的分段流量,改变轧辊的局部热膨胀变形,是轧制薄带材最有效的板形控制手段。
高速冷轧带钢生产中轧辊的温度较高,生产中必然出现热凸度,而在轧辊辊身上的温度分布极不均匀,故辊身上的热凸度也必然出现不均现象,从而造成带钢的局部缺陷,如复合波、二次谐波等缺陷。
轧件进入辊缝之前,在轧件表面喷涂冷却物质,可起到减轻热凸度的作用[1]。
轧辊分段冷却控制就是根据每个测量段上与带钢应力相对应的轧辊分段冷却分量,按数学模型计算出每个冷却区的冷却设定值,来推动相应的冷却控制阀门,即决定哪些阀门应打开,打开多大,哪些阀门应关闭等,同时在轧制过程中轧辊在任何时候都有一个基本冷却量,该基本冷却量约为最大冷却量的1/3。
这两个冷却量迭加后作为每个冷却区实际的冷却输出给下级控制轧制装置,并由控制装置打开和关闭相应的控制阀,达到对板形控制的目的。
可逆式冷轧机的分段冷却示意图见图1。
2.3轧辊轴向横移技术莱钢1500mm六辊可逆式冷轧机属于HC轧机,是六个轧辊垂直排列、中间辊可轴向移动的高精度板形控制轧机。
中间辊移动距离与弯辊力的最佳配合,一定程度上减少了普通四辊轧机板宽范围外支承辊与工作辊间的接触压力形成的有害弯矩,具有很强的板形控制能力;可实现轧机横向刚度无限大,使轧辊辊型不受轧制力变化的影响,减少带钢边部减薄量和裂边,保证带材有良好的板形;可以轧制高精度的薄带钢,并具有大压下量、提高生产率、节约能源、减少辊耗、提高成材率等优点。
莱钢1500mm六辊可逆冷轧机的板形控制技术

高的板形 精度 的要 求 ,现 以莱钢 10 l六 辊 50f i m 可 逆 式 冷 轧 机 为 例 ,介 绍 一 下 板 形 控 制 的 新 技
术
复合波 、二次谐波等,利用弯辊较难解决。 在 轧制 过 程 中轧辊 有 一个 基本 冷 却量 ,约为
22 轧辊 分段冷 却控 制技 术 . 分段 冷却 控 制技 术 就是 通过 调 整冷却 液 的分
1 影响板形 凸度 和平坦度 的 因素
带 钢 的 凸度 由原 料 的形 状 、轧 辊 的空 载辊 形
( 原始凸度 、热凸度和磨损 曲线) 、轧辊 的弹性变 形( 即弯曲挠度和压扁) 等决定 。在普通 四辊轧机 上所 使 用 的变压 下量 法 、总轧 制压 力 控制 法 、以
受 轧制 力 变化 的 影 响 ,减少 带 钢 边部 减 薄量 和 裂
边 ,保证带材有 良好 的板形 。可轧制高精度薄带 钢 ,并 具 有大 压 下量 、提 高生 产 率 、节 约 能源 、
个冷却 区实际的冷却输 出给控制装置 ,由其打开
和关 闭 相 应 的 控制 阀 ,对 板 形 进 行 控 制 。 图 1 为 轧 机 的分段 冷却 示意 图。
Pr f eCo t o c n l g 5 0 m - v r i l l i t i t e o l n r l i Te h o o y i 1 0 m n 6 h Re e sb eCo d M l a wu S e l l La
S n a y n, MaJn o gXio u ig
莱钢 10 E 5 0 六辊单机架冷轧机 的弯辊技术 m 分为工作辊液压弯辊和中间辊液压弯辊 ,工作辊 液压弯辊有液压正弯和液压负弯 ;中间辊 只有液 压 正弯 。在轧 辊 凸度 不足 或磨 损 情况 下可 以采用 正弯,增大轧辊凸度 ,防止带钢边浪 ,而负弯可
可逆冷轧机乳化液系统改造与优化

参考文献 [1] 李玉功.冷轧带钢表面清洁度影响因素分析与对策[J].山西冶
金,2017(3):91- 93.
(编辑:张卓娅)
Modification and Optimization of Emulsification System for
Reversible Cold Rolling Mill
Ma Jing
输送到轧机入口处进行冷却以及润滑,最终实现循
环使用。
过滤精度 30~70μm
轧死 磁性过滤器
平床过滤器
撇油器
脏箱
净箱 机械搅拌
图 1 1 500 mm 冷轧机组乳化液循环系统图
2 莱钢 1 500 mm 乳化液循环系统存在的问题 1)乳化液箱采用老式的蒸汽盘管的加热方式,
里面铺设复杂的加热蒸汽管道,容易在蒸汽管道缝 隙 造 成 油 泥 沉 淀 和 板 结 ,清 理 困 难 ,蒸 汽 加 热 效 率低。
乳化液主要是由 1%~3%的轧制油和 97%~99% 的脱盐水经搅拌配比而成的乳浊液,在轧制过程中, 在一定的温度和压力条件下,分散于乳化液中的轧 制油以物理吸附和化学吸附两种方式吸附于钢板 和轧辊表面形成油膜,为轧制提供必要的润滑、冷却 和清洗作用。因此,乳化液的性能对带材表面清洁度 有着十分重要的关系,直接影响了冷轧产品的表面 质量。 1.2 乳化液系统工作流程
发生。 3.4 乳化液磁过器改造
改造地上污油箱的箱体结构,使地上污油箱的箱 体由一个单纯的收集槽成为一个粗过滤器,挡住了 大颗粒物质的泄漏;同时,将之前的水平气动式磁过 滤器进行了拆除改造为去磁能力更强、运行更稳定 的立式磁过滤器。经过改造,污油箱的去污能力更 强,溢流进入中间油箱的乳化液清洁性得到大幅度 提高。
莱钢冷轧1500液压辊缝控制系统 (1)
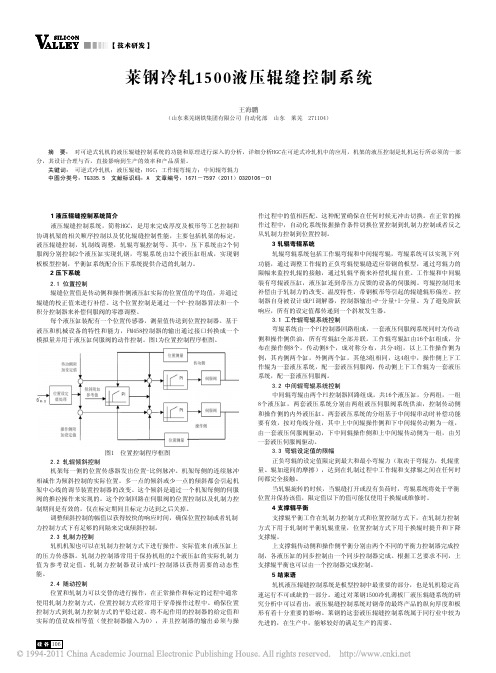
莱钢冷轧1500液压辊缝控制系统王海鹏(山东莱芜钢铁集团有限公司 自动化部 山东 莱芜 271104)摘 要: 对可逆式轧机的液压辊缝控制系统的功能和原理进行深入的分析,详细分析HGC 在可逆式冷轧机中的应用,机架的液压控制是轧机运行所必须的一部分,其设计合理与否,直接影响到生产的效率和产品质量。
关键词: 可逆式冷轧机;液压辊缝;HGC ;工作辊弯辊力;中间辊弯辊力中图分类号:TG335.5 文献标识码:A 文章编号:1671-7597(2011)0320106-011 液压辊缝控制系统简介作过程中的值相匹配。
这种配置确保在任何时候无冲击切换。
在正常的操作过程中,自动化系统依据操作条件切换位置控制到轧制力控制或者反之液压辊缝控制系统,简称HGC ,是用来完成厚度及板形等工艺控制和从轧制力控制到位置控制。
协调机架的相关顺序控制以及优化辊缝控制性能,主要包括机架的标定, 3 轧辊弯辊系统液压辊缝控制,轧制线调整,轧辊弯辊控制等。
其中,压下系统由2个伺服阀分别控制2个液压缸实现轧钢,弯辊系统由32个液压缸组成,实现钢轧辊弯辊系统包括工作辊弯辊和中间辊弯辊,弯辊系统可以实现下列板板型控制,平衡缸系统配合压下系统提供合适的轧制力。
功能,通过调整工作辊的正负弯辊使辊缝适应带钢的板型,通过弯辊力的2 压下系统限幅来监控轧辊的接触,通过轧辊平衡来补偿轧辊自重。
工作辊和中间辊装有弯辊液压缸,液压缸连到带压力反馈的设备的伺服阀。
弯辊控制用来2.1 位置控制补偿由于轧制力的改变、温度特性,带钢板形等引起的辊缝辊形偏差。
控辊缝位置值是传动侧和操作侧液压缸实际的位置值的平均值,并通过制器自身被设计成PI 调解器,控制器输出=P-分量+I-分量。
为了避免阶跃辊缝的校正值来进行补偿。
这个位置控制是通过一个P-控制器算法和一个响应,所有的设定值都传递到一个斜坡发生器。
积分控制器来补偿伺服阀的零漂调整。
3.1 工作辊弯辊系统控制每个液压缸装配有一个位置传感器,测量值传送到位置控制器。
莱钢1500冷轧机组乳化液系统工艺技术改造
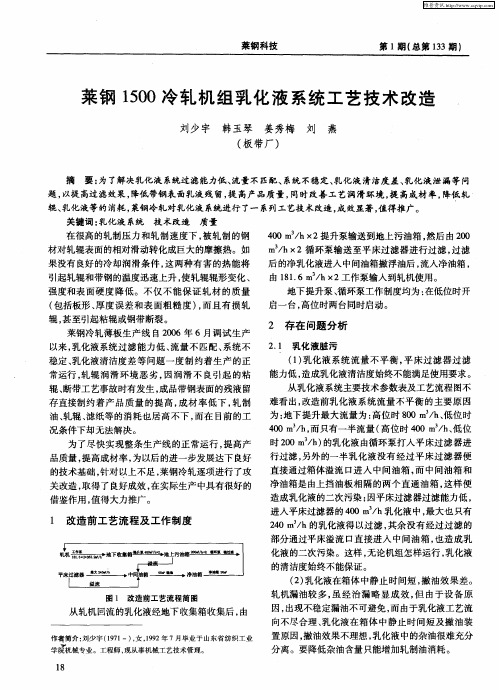
2 存在 问题分析
2 1 乳化液 脏 污 .
稳定 、 乳化液清洁度差等问题一度制约着生产 的正
常运行 , 轧辊 润滑环境恶 劣, 因润滑 不 良引起 的粘 辊、 断带工艺事故时有发生, 成品带钢表面的残液留
() 1 乳化液系统流量不平衡 , 床过滤器 过滤 平
能力低 , 造成乳化液清洁度始终不能满足使用要求 。 从乳化液系统主要技术参数表及工艺流程图不
难看 出 , 改造 前乳 化 液 系 统 流量 不 平 衡 的 主要 原 因
存直接制约着产 品质量 的提 高, 成材率 低下 , 轧制 油、 辊、 轧 滤纸 等 的消 耗 也 居高 不 下 , 在 目前 的 工 而 况条件下却无法解决 。
为: 地下提升最大流量为 : 高位时 80m / 、 0 。h 低位时
() 5 磁过滤器过滤能力低 , 导致系统铁粉含量高。 () 6 乳化液系统原装蝶阀阀座密封均 为橡胶密 封, 由于乳化液流量 大, 并且温度较高 , 加上管路震
症结所在是 : 系统流量不平衡 、 平床过滤器及磁过滤 器过滤能力低 、 工艺流 向不尽合理等 。为了彻底解
决这些问题 , 莱钢冷轧陆续进行了工艺技术改造 。
污染 ; 另一方面, 未过滤掉的较大的橡胶块堵塞了乳 化液喷嘴 , 使轧辊局部受热严重而受损 , 时常发生轧
维普资讯 http://wwຫໍສະໝຸດ
莱钢科技
第 1 总第 13 ) 期( 3期
莱 钢 10 0冷 轧 机 组 乳化 液 系统 工 艺技 术 改造 5
刘少 宇 韩玉琴 姜秀梅 刘 燕 ( 带厂 ) 板
摘 要: 为了解决乳化液系统过滤能力低、 流量不匹配、 系统不稳 定、 乳化液清洁度差、 乳化液泄漏等 问 题, 以提高过滤效果, 降低 带钢表面乳液残留, 高产 品质量 , 提 同时改善工艺润 滑环境 , 高成材率, 提 降低 轧 辊、 乳化液等的消耗 , 莱钢冷轧对乳化液系统进行 了一系列工艺技 术改造 , 成效显著, 值得推广。
莱钢1500mm宽带精除磷气动系统改造

从事轧钢设备管理与维修工作。
21 0 2年第 6期
液压 与气动
7 3
气 动 升 降辊 道 的设 计 与应 用
李君美
De i n a d Ap l a in o n u t i i g Ro lr sg n p i to f P e mai L f n l c c t e
理 时间较 长 , 响 正 五
换 向阀 通 电磁
产顺 行使 用 频次 的增 多 越加 严 重 , 渐 成 为 制约 生 产 逐
的大 问题 。
1 问题 分 析
三 大件 三 大件
精 除鳞 入 口夹送 辊与 出 口夹 送辊 分别 由两个 独立
前 言
精除磷 入 口夹 送辊气 缸 精 除磷 出口 口 夹送 辊气缸
莱钢 10 1 宽带精除鳞夹送辊为气压传动 系 5031 11 3 统, 主要用 于轧 钢 过 程 中封 闭 精 除鳞 高 压 水 。 自投 入
生 产 以来 , 制 阀组 故 障 , 件 故 障判 断 困难 , 障 处 控 元 故
7 2
液 压 与 气动
21 0 2年 第 6期
莱 钢 10 5 0mm 宽 带精 除磷 气 动 系统 改造
汪 洋。 武 强
P e ma i y t m f r o n h Rol rf r 1 0 n u t S se Re o m fPi c le o 0 mm ti c 5 S rp
移 至下 道工 序进 行收集 一 打捆一 码垛 。在 实 际生产 过 程 中, 由于坯 料尺 寸 以及 倍 尺分段 的精 确度 偏差 , 使得
钢 材在 定尺剪 切后 出现 一些 短 尺 材 , 由人 工 在 剪后 辊
要实 现冷 剪 的连 续剪 切 , 须 将 钢 材 全部 转 移 至 必 链 式 输送 机上 , 在输 送过 程 中进行分 离 。为此 , 步确 初 定从 链式 输送 机 中间 安装 一 组 横 移 辊 道 , 短 尺材 移 将 出输 送机 区 域 。如 图 1共 设 计 布 置 1 , 6只辊 子 , 中 其 位 于链 式 移钢 机 中的 1~ 8个辊 子设计 成 升降式 , 钢 移
- 1、下载文档前请自行甄别文档内容的完整性,平台不提供额外的编辑、内容补充、找答案等附加服务。
- 2、"仅部分预览"的文档,不可在线预览部分如存在完整性等问题,可反馈申请退款(可完整预览的文档不适用该条件!)。
- 3、如文档侵犯您的权益,请联系客服反馈,我们会尽快为您处理(人工客服工作时间:9:00-18:30)。
莱钢1500可逆轧机工作辊、中间辊轴承座油气润滑改造
提要:工作辊、中间辊换辊频率较高,原来轴承座油气润滑装置在更换轧辊和快插方式上效率低下同时给工作人员带来极大的安全隐患。
改造后的轴承座油气润滑装置效果良好。
关键词:油气润滑;工作辊轴承座;中间辊轴承座;传动侧;操作侧;变径接头;连接管
1.前言
莱钢冷轧薄板1#1500可逆轧机,由一重设计,2006年试生产,轧辊轴承座的润滑采用当今最先进的油气润滑技术。
但由于轧机传动侧及其牌坊内恶劣的环境,导致整个换辊效率比较低下,尤其随着1#轧机产能的全面释放,1#轧机轴承座油气润滑装置已严重影响了生产效率。
针对这些情况莱钢冷轧薄板对轧辊轴承座油气润滑装置和轧辊轴承座所在牌坊内的空间进行了系统分析,并对轧辊轴承座油气润滑装置进行了全面的改造。
2.存在问题
以下工作辊轴承座为例简介改造前轴承座油气润滑接口装置带来的系列问题。
如上图1,工作辊下辊装配由辊身、两个轴承做及其轴承座内的一些零部件组成,图1中:轴承座传动外侧、传动内侧、操作外侧、操作内侧分别对应下图2、图3、图4、图5。
其中传动外侧(图2)油气润滑接头处有一15cm长的导向杆(此装置主要起三个作用:1、导向作用;2、快速接头的载体;3、输送油气混合物,端面装有快速接头)。
轧机处于工作状态时,油气混合物通过传动外侧(图2)和操作外侧(图4)的油气润滑接头进入轴承座内部。
在换辊过程中,抽辊前首先拔掉图2和图4中油气润滑接头上的快速接头。
装辊时,在轧机传动侧需观察油气润滑导向装置,主要是该装置容易因轨道轻微变形或轨道升降不到位而变形损坏。
换辊后操作人员需快速将其油气润滑软管与轴承座油气润滑接头连接并确认牢固到位。
综合以上,轧机工作状态和换辊过程中主要存在以下问题。
1.由于轧机传动侧油污多,地面滑,空间狭小,设备温度高,内部温度高达100度以上,环境极其恶劣,传动侧操作人员站位、工作时需把胳臂伸进轧辊抱
紧装置的缝隙内,存在极大的安全隐患。
2.轧机工作时,因振动或插装不到位导致油气润滑快速接头脱开,传动侧很难被发现。
3.装辊时传动侧油气润滑导向装置易变形损坏。
3.改造方案
针对上述问题,本着节能减排、备件通用、易点检操作、不破坏轴承座原有油气通道的原则,进行了系列改造,改造方向是把传动侧油气润滑接头引到操作侧。
以下工作辊为例介绍其具体改造内容。
以传动外侧为基准在原有油气润滑孔(图6标记1位置)对应一侧距水平中心线152.5和距垂直中心线为215的坐标位钻φ16的通孔(图6标记2位置),并攻丝M20*1.5,深32,加21*26的密封垫。
图6标记1,2位置中间通过加密封带直角弯头的橡胶软管相连。
传动内侧(图7标记3位置)同样攻丝M20*1.5,深32,加21*26的密封垫,此处加变径M20*1.5/M12*1.5,变径接头与φ16的管子通过螺纹连接,在操作内侧对应位置(图9标记5位置)钻φ22通孔,该孔对应操作外侧图8标记4位置。
两轴承座与轧辊装配后,用φ16一端攻内丝M12*1.5的连接管从操作外侧插入,并通过螺纹与变径接头相连,连接管拧紧后露出操作外侧5公分左右,末端安装快速接头。
此时再把传动侧机顶平台的油气润滑硬管移到操作侧即可。
此次改造需说明的几点:
1.图6中连接1、2位置的胶管,其对应空间小于牌坊内间隙15公分。
2.图6标记2的通孔,需具备如下条件
a其位置大于直径方向461mm【最大辊径φ425+16(φ16连接管)+20(半径方向10个间隙)=461】;
b该通孔属于细长孔,周边小厂具备其加工能力,且成本较低;
c该孔不能与图1装配耐磨板的固定螺栓和两轴承座四侧端盖相干涉;
d该孔壁厚不得小于5mm,以防钻孔崩裂及降低轴承座本身的抗疲劳能力。
e、φ16的连接管位置主要由轴承座与最大辊径决定,且φ16的管子在1.5m 长的范围内经得起轧机工作时轴承座的振动。
f、变径的主要作用是在轧机断带时,带钢对连接管冲击直接切断变径接头M12*1.5退刀槽位置,从而起到保护连接管的作用。
同时变径加工简单,成本较
低。
g、φ22通孔与φ16的连接管在半径方向有4mm间隙,在连接管受到冲击弯曲后简单矫直即可抽出,同样该间隙允许两轴承座钻孔位置可有2mm的加工误差,操作侧轴承座的通孔较长,采用φ22的孔径相对降低了加工难度,进一步节约成本。
综上,轧辊轴承座加钻传动侧油气润滑通孔位置是此次改造成功与否的关键。
结语
改进后的轴承座,解决了以上所有问题,效果良好,值得推广。