活塞杆机械加工工艺
液压缸的结构及机械加工工艺分析
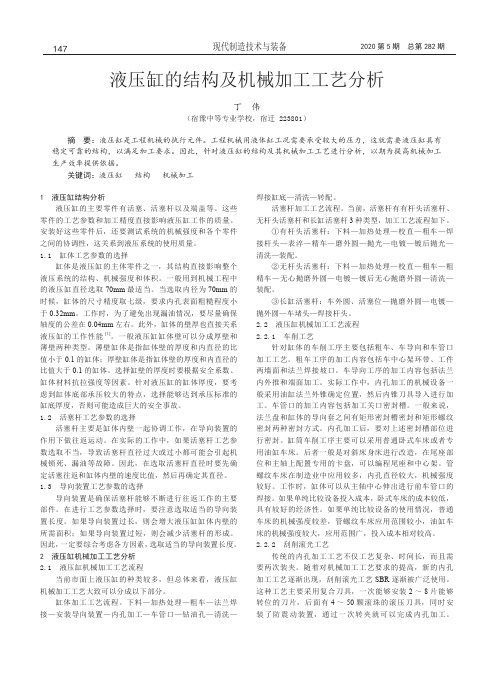
1 液压缸结构分析液压缸的主要零件有活塞、活塞杆以及端盖等。
这些零件的工艺参数和加工精度直接影响液压缸工作的质量。
安装好这些零件后,还要测试系统的机械强度和各个零件之间的协调性,这关系到液压系统的使用质量。
1.1 缸体工艺参数的选择缸体是液压缸的主体零件之一,其结构直接影响整个液压系统的结构、机械强度和体积。
一般用到机械工程中的液压缸直径选取70mm最适当。
当选取内径为70mm的时候,缸体的尺寸精度取七级,要求内孔表面粗糙程度小于0.32mm。
工作时,为了避免出现漏油情况,要尽量确保轴度的公差在0.04mm左右。
此外,缸体的壁厚也直接关系液压缸的工作性能[1]。
一般液压缸缸体壁可以分成厚壁和薄壁两种类型。
薄壁缸体是指缸体壁的厚度和内直径的比值小于0.1的缸体;厚壁缸体是指缸体壁的厚度和内直径的比值大于0.1的缸体。
选择缸壁的厚度时要根据安全系数、缸体材料抗拉强度等因素。
针对液压缸的缸体厚度,要考虑到缸体底部承压较大的特点,选择能够达到承压标准的缸底厚度,否则可能造成巨大的安全事故。
1.2 活塞杆工艺参数的选择活塞杆主要是缸体内壁一起协调工作,在导向装置的作用下做往返运动。
在实际的工作中,如果活塞杆工艺参数选取不当,导致活塞杆直径过大或过小都可能会引起机械锁死、漏油等故障。
因此,在选取活塞杆直径时要先确定活塞往返和缸体内壁的速度比值,然后再确定其直径。
1.3 导向装置工艺参数的选择导向装置是确保活塞杆能够不断进行往返工作的主要部件。
在进行工艺参数选择时,要注意选取适当的导向装置长度。
如果导向装置过长,则会增大液压缸缸体内壁的所需面积;如果导向装置过短,则会减少活塞杆的形成。
因此,一定要综合考虑各方因素,选取适当的导向装置长度。
2 液压缸机械加工工艺分析2.1 液压缸机械加工工艺流程当前市面上液压缸的种类较多,但总体来看,液压缸机械加工工艺大致可以分成以下部分。
缸体加工工艺流程。
下料—加热处理—粗车—法兰焊接—安装导向装置—内孔加工—车管口—钻油孔—清洗—焊接缸底—清洗—转配。
活塞杆说明书

机械制造工艺综合实训论文题目活塞杆夹具工艺设计学生姓名学号学院机电学院专业机械工程班级指导教师陈本德2020年12月南京工业大学浦江学院目录第一部分工艺设计说明书 31.零件图工艺性分析 31.1零件结构功用分析 31.2零件技术条件分析 31.3零件结构工艺性分析 32.毛坯选择 32.1毛坯类型 32.2毛坯余量确定 32.3零件图 43.机加工工艺路线确定 44.设备及其工艺装备确定 54.1选择机床和夹具 54.2选择刀具 55.切削用量及工时定额确定 6 第二部分第30号工序夹具设计说明书81.工序尺寸精度分析82.定位方案确定83.定位误差分析计算84.夹紧方案及元件确定85.夹具总装图9 参考资料9第一部分工艺设计说明书1.零件图工艺性分析1.1零件结构功用分析从活塞杆的受力分析可知,它受扭转一弯曲复合作用力,由于其承受中等载荷,工作又较平稳,冲击力很小,所以可采用优质碳素结构钢的45号钢,坯料用热轧圆钢。
为了改善组织、提高力学性能,坯料要经过正火热处理1.2零件技术条件分析外圆尺寸精度:φ22,φ70,φ35.7,φ27.8,φ30,φ26外圆;外圆形状位置精度:要求为φ22两轴节相对φ70外圆相互位置精度外圆表面质量:φ70 0.8um,的表面质量要求其它面Ra为12.5um1.3零件结构工艺性分析轴的锻件强度较高,形状比较简单,外轮廓尺寸不大,在轴径φ42,φ27.8两节阶梯轴,可用三爪卡盘结论:轴的结构较规则,在加工键槽和B型中心孔时,采用专用夹具定位和夹紧2.毛坯选择2.1毛坯类型在传递力矩过程时要承受很强的冲击力和很大的交变载荷, 要求材料应有较高的强度、冲击韧度、疲劳强度和耐磨性,而且其轮廓形状不复杂,零件尺寸不大,而且零件属于批量生产,故采用45。
2.2毛坯余量确定毛坯的形状和尺寸越接近成品零件,即毛坯精度越高,则零件的机械加工劳动量越少,材料消耗越少,可充分提高劳动生产率,降低成本,但是毛坯制造费用会提高,在确定毛坯时,应根据机械加工和毛坯制造两方面考虑。
活塞杆
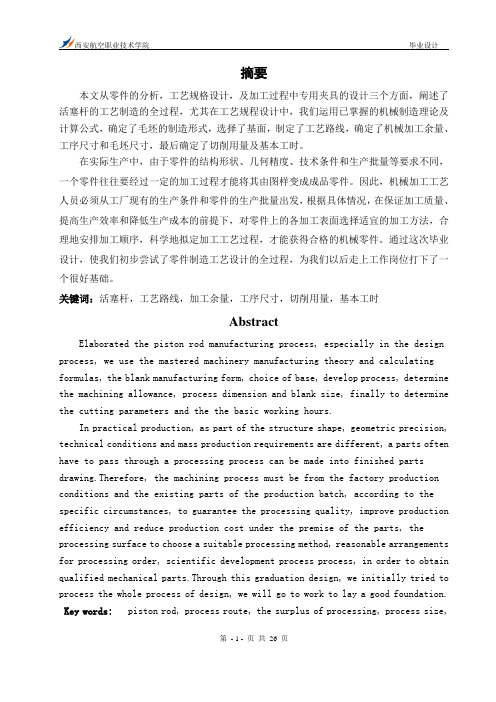
摘要本文从零件的分析,工艺规格设计,及加工过程中专用夹具的设计三个方面,阐述了活塞杆的工艺制造的全过程,尤其在工艺规程设计中,我们运用已掌握的机械制造理论及计算公式,确定了毛坯的制造形式,选择了基面,制定了工艺路线,确定了机械加工余量、工序尺寸和毛坯尺寸,最后确定了切削用量及基本工时。
在实际生产中,由于零件的结构形状、几何精度、技术条件和生产批量等要求不同,一个零件往往要经过一定的加工过程才能将其由图样变成成品零件。
因此,机械加工工艺人员必须从工厂现有的生产条件和零件的生产批量出发,根据具体情况,在保证加工质量、提高生产效率和降低生产成本的前提下,对零件上的各加工表面选择适宜的加工方法,合理地安排加工顺序,科学地拟定加工工艺过程,才能获得合格的机械零件。
通过这次毕业设计,使我们初步尝试了零件制造工艺设计的全过程,为我们以后走上工作岗位打下了一个很好基础。
关键词:活塞杆,工艺路线,加工余量,工序尺寸,切削用量,基本工时AbstractElaborated the piston rod manufacturing process, especially in the design process, we use the mastered machinery manufacturing theory and calculating formulas, the blank manufacturing form, choice of base, develop process, determine the machining allowance, process dimension and blank size, finally to determine the cutting parameters and the the basic working hours.In practical production, as part of the structure shape, geometric precision, technical conditions and mass production requirements are different, a parts often have to pass through a processing process can be made into finished parts drawing.Therefore, the machining process must be from the factory production conditions and the existing parts of the production batch, according to the specific circumstances, to guarantee the processing quality, improve production efficiency and reduce production cost under the premise of the parts, the processing surface to choose a suitable processing method, reasonable arrangements for processing order, scientific development process process, in order to obtain qualified mechanical parts.Through this graduation design, we initially tried to process the whole process of design, we will go to work to lay a good foundation. Key words: piston rod, process route, the surplus of processing, process size,cutting parameters, the basic working hours目录1.零件的工艺分析及生产类型的确定....................... - 2 -1.1零件的功用、结构及特点 ......................... - 5 -1.2零件的技术要求 ................................. - 5 -1.3零件的工艺性 ................................... - 5 -1.4确定零件的生产类型 ............................. - 6 -2.毛坯的选择........................................... - 6 -2.1确定毛坯的类型 ................................. - 6 -2.2确定毛坯的制造方法和尺寸及其公差................ - 6 -2.3确定毛坯的技术要求 ............................. - 7 -3.基准的选择.......................................... - 7 -3.1粗基准的选择 ................................... - 7 -3.2 精基准的选择................................... - 8 -4.拟定机械加工工艺路线................................. - 8 -4.1确定各表面的加工方法 ........................... - 8 -4.2拟定加工工艺路线 ................................ - 8 -5.确定机械加工余量、工序尺寸........................... - 9 -6.选择机床工艺设备.................................... - 12 -6.1选择机床...................................... - 12 -6.2选择刀具...................................... - 12 -6.3选择夹具...................................... - 12 -6.4选择量具...................................... - 12 -7.填写切削用量及基本工时.............................. - 13 - 7.1切端面........................................ - 13 - 7.2车端面........................................ - 14 - 7.3粗车外圆...................................... - 15 - 7.4精车螺纹...................................... - 15 - 7.5精车外圆...................................... - 16 - 7.6倒角.......................................... - 17 - 7.7粗磨外圆...................................... - 18 -7.8精磨外圆...................................... - 18 -8.夹具的设计.......................................... - 19 - 8.1 机床夹具的功用................................ - 19 - 8.2问题的提出.................................... - 19 - 8.3定位方案...................................... - 20 - 8.3.1定位基准的选择 .......................... - 20 - 8.3.2定位元件的设计 .......................... - 20 - 8.4定位误差分析 .................................. - 20 - 8.4.1夹具设计及简要操作说明 .................. - 20 - 8.5夹紧装置的设计 ................................ - 21 - 8.5.1夹紧装置的设计要求 ...................... - 21 - 8.5.2夹紧力的方向 ............................ - 21 - 8.5.3 夹紧力的作用点.......................... - 21 -8.6切削力和夹紧力的计算 .......................... - 21 -结束语............................................. - 21 - 致谢................................................ - 19 - 参考文献............................................. - 20 - 附录1.零件的工艺分析及生产类型的确定1.1零件的功用、结构及特点活塞杆是支持活塞做功的连接部件,大部分应用在油缸、汽缸等运动部件中,是一个运动频繁、技术要求高运动部件。
活塞杆的加工流程
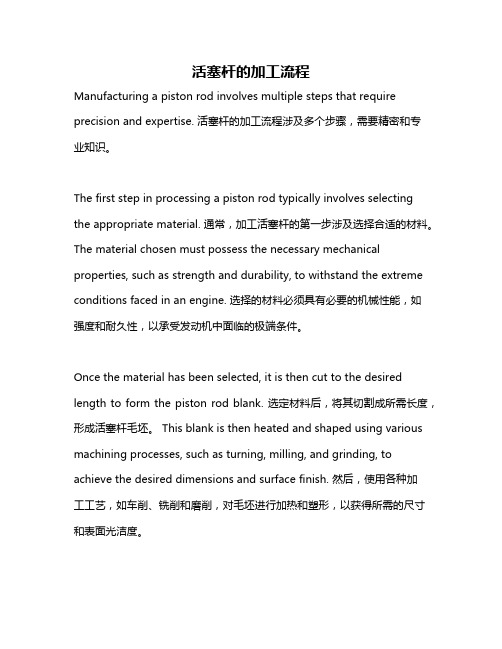
活塞杆的加工流程Manufacturing a piston rod involves multiple steps that require precision and expertise. 活塞杆的加工流程涉及多个步骤,需要精密和专业知识。
The first step in processing a piston rod typically involves selecting the appropriate material. 通常,加工活塞杆的第一步涉及选择合适的材料。
The material chosen must possess the necessary mechanical properties, such as strength and durability, to withstand the extreme conditions faced in an engine. 选择的材料必须具有必要的机械性能,如强度和耐久性,以承受发动机中面临的极端条件。
Once the material has been selected, it is then cut to the desired length to form the piston rod blank. 选定材料后,将其切割成所需长度,形成活塞杆毛坯。
This blank is then heated and shaped using various machining processes, such as turning, milling, and grinding, to achieve the desired dimensions and surface finish. 然后,使用各种加工工艺,如车削、铣削和磨削,对毛坯进行加热和塑形,以获得所需的尺寸和表面光洁度。
One critical aspect of processing a piston rod is the precision grinding of the final product. 加工活塞杆的一个关键方面是对最终产品进行精密磨削。
活塞杆是用什么材料制作
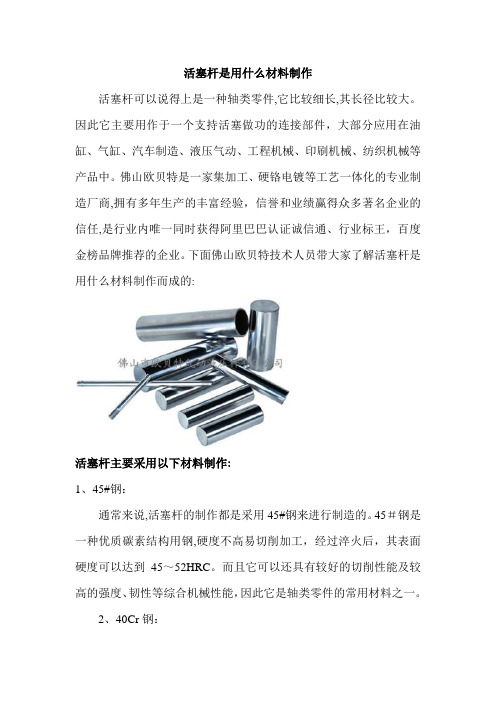
活塞杆是用什么材料制作活塞杆可以说得上是一种轴类零件,它比较细长,其长径比较大。
因此它主要用作于一个支持活塞做功的连接部件,大部分应用在油缸、气缸、汽车制造、液压气动、工程机械、印刷机械、纺织机械等产品中。
佛山欧贝特是一家集加工、硬铬电镀等工艺一体化的专业制造厂商,拥有多年生产的丰富经验,信誉和业绩赢得众多著名企业的信任,是行业内唯一同时获得阿里巴巴认证诚信通、行业标王,百度金榜品牌推荐的企业。
下面佛山欧贝特技术人员带大家了解活塞杆是用什么材料制作而成的:活塞杆主要采用以下材料制作:1、45#钢:通常来说,活塞杆的制作都是采用45#钢来进行制造的。
45#钢是一种优质碳素结构用钢,硬度不高易切削加工,经过淬火后,其表面硬度可以达到45~52HRC。
而且它可以还具有较好的切削性能及较高的强度、韧性等综合机械性能,因此它是轴类零件的常用材料之一。
2、40Cr钢:40Cr钢也是活塞杆制作中比较常用的一种材料,它不仅是一种中碳调质钢,也是一种冷镦模具钢。
它具有比较好的综合机械性能,一般适用于中等精度、转速较高的轴类零件的制造。
因此它在活塞杆中就常被应用于一些较大冲击力、重载荷传动要求大的活塞杆中,因为它可以有效地保证活塞杆拥有足够的工作强度。
3、不锈钢材质:不锈钢是用于活塞杆制作中一种材料,耐空气、蒸汽、水等弱腐蚀介质的特点,常用的有304、316、402这几种材质.这几种材质的焊接性、抛光性、耐热性、耐腐蚀性、耐腐蚀性都是比较好的,通过精密冷拔、精磨、高精度抛光等工艺处,其制造出来的活塞杆的各项技术指标均符合并超过国家标准,因此常用于油缸、气缸、减震器中。
佛山欧贝特活塞杆是经过特殊研磨及硬铬电镀技术外理,再经镜面抛光而成,耐磨擦、抗腐蚀性特性,适用于各种气缸、油缸、活塞杆、包装、木工、纺织、印染机械、压铸机、注塑机、及其它机械用导杆、顶杆等。
材质:优质不锈钢外径公差:f7—f8(其它公差可订造)表面粗糙度:Ra0.2—0.4硬铬厚度:0.015-0。
活塞杆锻造工艺
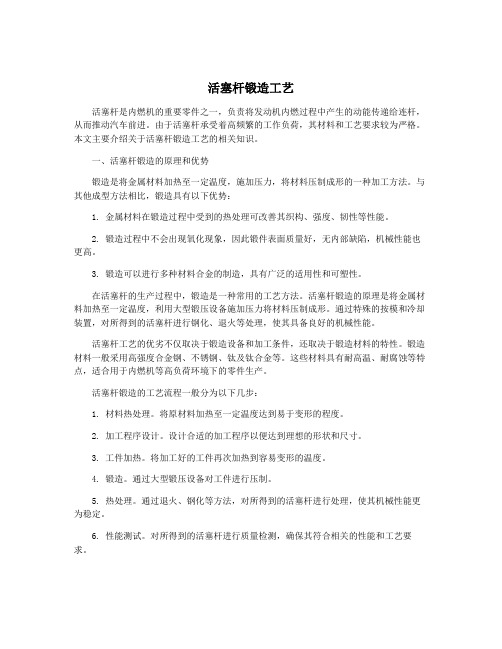
活塞杆锻造工艺活塞杆是内燃机的重要零件之一,负责将发动机内燃过程中产生的动能传递给连杆,从而推动汽车前进。
由于活塞杆承受着高频繁的工作负荷,其材料和工艺要求较为严格。
本文主要介绍关于活塞杆锻造工艺的相关知识。
一、活塞杆锻造的原理和优势锻造是将金属材料加热至一定温度,施加压力,将材料压制成形的一种加工方法。
与其他成型方法相比,锻造具有以下优势:1. 金属材料在锻造过程中受到的热处理可改善其织构、强度、韧性等性能。
2. 锻造过程中不会出现氧化现象,因此锻件表面质量好,无内部缺陷,机械性能也更高。
3. 锻造可以进行多种材料合金的制造,具有广泛的适用性和可塑性。
在活塞杆的生产过程中,锻造是一种常用的工艺方法。
活塞杆锻造的原理是将金属材料加热至一定温度,利用大型锻压设备施加压力将材料压制成形。
通过特殊的按模和冷却装置,对所得到的活塞杆进行钢化、退火等处理,使其具备良好的机械性能。
活塞杆工艺的优劣不仅取决于锻造设备和加工条件,还取决于锻造材料的特性。
锻造材料一般采用高强度合金钢、不锈钢、钛及钛合金等。
这些材料具有耐高温、耐腐蚀等特点,适合用于内燃机等高负荷环境下的零件生产。
活塞杆锻造的工艺流程一般分为以下几步:1. 材料热处理。
将原材料加热至一定温度达到易于变形的程度。
2. 加工程序设计。
设计合适的加工程序以便达到理想的形状和尺寸。
3. 工件加热。
将加工好的工件再次加热到容易变形的温度。
4. 锻造。
通过大型锻压设备对工件进行压制。
5. 热处理。
通过退火、钢化等方法,对所得到的活塞杆进行处理,使其机械性能更为稳定。
6. 性能测试。
对所得到的活塞杆进行质量检测,确保其符合相关的性能和工艺要求。
活塞杆锻造技术具有重要的应用和发展前景。
通过不断提升加工装备和工艺技术的水平,锻造工艺不断地向着高精度、高稳定性、低能耗、低成本等方向发展。
活塞杆锻造技术在汽车工业、石油化工、航空航天等高负荷环境下的关键领域有着广泛的应用。
旋转摩擦焊在液压油缸活塞杆制造中的工艺应用研究[1]
旋转摩擦焊在液压油缸活塞杆制造中的工艺应用研究[1]摘要:我国的液压工业经过近50年的发展,液压行业已形成了门类比较齐全,有一定生产能力和技术水平的工业体系。
本文中主要就针对液压油缸活塞杆焊接使用的高性能旋转摩擦焊工艺。
擦焊接是一种在固相中进行焊接的方法,其中一个部件相对于配合部件移动并与配合部件压力接触,以在结合表面产生热量,在相对运动停止期间或之后通过施力完成焊接。
有几种形式的能量供应和各种形式的相对运动。
摩擦加热的产生导致界面处的连接温度相对较低。
这在很大程度上是摩擦焊接适用于其他难以焊接的材料和材料组合的原因。
焊接区域通常很窄,通常具有精细的微观结构。
其为对圆棒状母材进行旋转摩擦焊的工艺,通过该工艺方法相比于其他焊接工艺方法,本研究的旋转摩擦焊工艺接头力学性能良好、焊接效率高、并且该工艺稳定高效、在应用方面重复性、一致性生产提供高效率精益生产。
关键词:摩擦焊设备说明;工艺评定以及验收要求;过程控制;Research on the application of rotational friction welding in the manufacture of piston rod hydraulic cylinderBi Shu-ming(Zhejiang huachang hydraulic machinery Co., Ltd., Hangzhou, Zhejiang 311305, China)Abstract: After nearly 50 years of development, China's hydraulic industry has formed an industrial system with complete categories, certain production capacity and technical level. This paper mainly focuses on the high-performance rotational friction welding technology used for the welding of hydraulic cylinder piston rod. Frictionwelding is a method for making welds in the solid phase in which one component is moved relative to and in pressure contact with the mating component to produce heat at the faying surfaces, the weld being completed by the application of a force during or after the cessation of relative motion. There are several forms of supplying energy and various forms of relative movements. The generation of friction heating results in a comparatively low joining temperature at the interface. This is largely the reason why friction welding is suitable for materials and material combinations hich are otherwise difficult to weld. The weld region is generally narrow and normally has arefined microstructure. It is a process for rotational friction welding of round rod like base metal. Compared with other welding processes, the rotational friction welding process in this study has good mechanical properties, high welding efficiency, stable and efficient technology, and provides efficient and lean production with repeatability and consistency in application.Key words:Description of friction welding equipment, Process qualification and acceptance requirements, Pprocess control.0 引言近年来,国家相继发布《液压气动密封行业“十四五”发展规划》、《智能制造发展规划》和《中国制造2025》,重点突出中国集中优势、提高产品质量、加快替代高端进口产品步伐和智能化进程。
油缸活塞杆
油缸活塞杆本文由欧贝特提供定义油缸活塞杆顾名思义,是支持活塞做功的连接部件,大部分应用在油缸、气缸运动执行部件中,是一个运动频繁、技术要求高的运动部件。
以液压油缸为例,由:缸筒、活塞杆(油缸杆)、活塞、端盖几部分组成。
其加工质量的好坏直接影响整个产品的寿命和可靠性。
油缸活塞杆加工要求高,其表面粗糙度要求为Ra0.4~0.8um,对同轴度、耐磨性要求严格。
加工方法油缸活塞杆采用滚压加工,由于表面层留有表面残余压应力,有助于表面微小裂纹的封闭,阻碍侵蚀作用的扩展。
从而提高表面抗腐蚀能力,并能延缓疲劳裂纹的产生或扩大,因而提高油缸杆疲劳强度。
通过滚压成型,滚压表面形成一层冷作硬化层,减少了磨削副接触表面的弹性和塑性变形,从而提高了油缸杆表面的耐磨性,同时避免了因磨削引起的烧伤。
滚压后,表面粗糙度值的减小,可提高配合性质。
同时,降低了油缸杆活塞运动时对密封圈或密封件的摩擦损伤,提高了油缸的整体使用寿命。
滚压技术加工原理:它是一种压力光整加工,是利用金属在常温状态的冷塑性特点,利用滚压刀具对工件表面施加一定的压力,使工件表层金属产生塑性流动,填入到原始残留的低凹波谷中,而达到工件表面粗糙值降低。
由于被滚压的表层金属塑性变形,使表层组织冷硬化和晶粒变细,形成致密的纤维状,并形成残余应力层,硬度和强度提高,从而改善了工件表面的耐磨性、耐蚀性和配合性。
滚压是一种无切削的塑性加工方法。
应用油缸活塞杆的应用决定了它需要很好的耐磨,耐腐蚀以及防锈能力,因此通常油缸活塞杆的生产都会在表面镀一层铬。
镀铬泛指电镀铬,一般说的是工业机械上的镀硬铬。
铬是一种微带蓝色的银白色金属,相对原子质量51.99,密度6.98~7.21g /cm3,熔点为1857~1920℃,金属铬在空气中极易钝化,表面形成一层极薄的钝化膜,从而显示出贵金属的性质,同时由于隔绝了材料与外界的接触,因此,但镀铬层没有被磨损时,油缸活塞杆就不会生锈。
镀铬层具有很高的硬度,根据镀液成分和工艺条件不同,油缸活塞杆的镀铬层硬度一般可达HRC58~HRC62。
活塞杆加工工艺规范
xxxx有限公司文件名称:活塞杆加工工艺规范文件编号:GY03-14-2015文件签章有效/受控状态:编制 : 技术工艺科审核:审批:修改记录单版本时间简述A2015年2月活塞杆加工工艺规范1 引用标准GB/T1800.4-99孔、轴的极限偏差表 GB/T1801-99公差配合的选择 GB/T1184-96形位公差值 GB/T1031-95表面粗糙参数及其数值 厂标等效JB/Z307GB/T193-81GB/T196-81GB/T5786.2-86GB/T5796.3-86GB/T6403.5-86 金属切削加工工艺守则 普通螺纹直径与螺距系列 梯形螺纹基本尺寸 普通螺纹直径与螺距系列梯形螺纹基本尺寸 砂轮越程槽GB/T145-89 GB200-89 GB699-1999 GB908-87GB/T3-79JB/ZQ0138-80中心孔碳素结构钢优质碳素结构钢锻制圆钢和方钢规格 普通螺纹的收尾、兼距、退刀槽和倒角 单线梯形螺纹的收尾、退刀槽和倒角尺寸 2 需用设备(1)100t 开式油压机(2)校直用一组支承滚轮、划针盘、直尺(3)乙炔氧气加热器(4)卧式车床C6163,长8m(5)手工交流焊机(6) 热处理(回火)设备(7) 砂带磨头、外圆磨床、砂盘抛磨头(8)螺纹检验用环、塞规3 适用范围本工艺守则适用于加工液压启闭机活塞杆、柱塞杆及部分工业液压缸的活塞杆。
4 活塞杆类型基本有三种4.1 实心活塞杆,见图4.14.2中空型活塞杆由杆头、杆身(无缝管)、杆尾组焊而成,见图4.24.3中空带进油管的活塞杆,见图4.3由杆头、杆身、杆尾及内进油管组焊而成。
将4.2、4.3两种活塞杆称为组合活塞杆图4.1图4.2图4.35 备料及毛坯制作5.1 活塞杆常用材料有45#、35#及40Cr,通常情况下,45#、35#是正火态供货。
具体按设计要求。
5.2毛坯余量的确定选用确定活塞杆坯料余量,应根据其长径比、坯料状态(热轧圆钢,锻圆)通常情况热轧圆钢直径余量6~12mm,长度余量5~10mm。
活塞杆课程设计工序卡.
第2 页 共8页 材料牌号 38CrMoAlAn 每台件数 1 同时加工件数 1 工作液 工序工时 准终 单件
工位器具编号
工位器具名称
工步 号 1 2
工步内容 夹左端,中心架支承另一端,切下右端 6mm 做试片,进 行金相组织检查,端面车平,钻中心孔 B2. 5 倒头装夹工作,中心架支撑另一端,车端面,保证总长 1090mm,钻中心孔 B2.5
校对 (日期) 审核(日期)
批准(日期) 会签(日期)
7
工厂
机械加工工序卡
产品名称 零件名称 车间 毛坯种类 自由锻 设备名称 普通车床 夹具编号 设备型号 M1432 活塞杆 工序号 23 毛坯外形尺寸
产品图号 零件图号 工序名称 精磨外表面 每个毛坯可制件数 1 设备编号 夹具名称 双顶尖、跟刀架
工位器具编号
工位器具名称
工步 号 1 2 0.08-0.10mm
工步内容 两顶尖装夹工作,粗磨 50
0 0.0025 mm×770mm,留磨量
工艺装备
主轴转速 r/min 160
切削速度 m/min 25.64
进给量 mm/r 25
切削深度 mm 0.02
进给次数 1
粗磨 1:20 锥度部分,留磨量为 0.1mm
工艺装备
主轴转速 r/min 250
切削速度 m/min 78.5
进给量 mm/r 0.05
切削深度 mm 0.03
进给次数 1
250
78.5
0.05
0.03
1
编制(日期) 标记 处数 更改文件号 签字 日期 标记 处数 更改文件号 签字 日期
校对 (日期) 审核(日期)
批准(日期) 会签(日期)
- 1、下载文档前请自行甄别文档内容的完整性,平台不提供额外的编辑、内容补充、找答案等附加服务。
- 2、"仅部分预览"的文档,不可在线预览部分如存在完整性等问题,可反馈申请退款(可完整预览的文档不适用该条件!)。
- 3、如文档侵犯您的权益,请联系客服反馈,我们会尽快为您处理(人工客服工作时间:9:00-18:30)。
五、活塞杆
见图2-10
图2-10活塞杆
技术要求
1、1:20锥度接触面积不少于80%。
mm部分氮化层深度为0.2~0.3mm,硬度62~65HRC。
2、φ500
-
.0
025
3、材料38CrMoALA。
1、零件图样分析
mm×770mm自身圆度公差为0.005mm。
1)φ500
025
-
.0
mm中心线的同轴度公差为φ0.05mm。
2)左端M39×2-6g螺纹与活塞杆φ500
.0
025
-
mm中心线的同轴度公差为φ0.02mm。
3)1:20圆锥面轴心线与活塞杆φ500
025
-
.0
4)1:20圆锥面自身圆跳动公差为0.005mm。
5)1:20圆锥面涂色检查,接触面积不小于80%。
mm×770mm表面渗氮,渗氮层深度0.2~0.3mm,表面硬度62~65HRC。
6)φ500
-
.0
025
材料38CrMoALA是常用的渗氮处理用钢。
2、活塞杆机械加工工艺过程卡(表2-5)
表2-5 活塞杆机械加工工艺过程卡
3、工艺分析
mm×770mm处有密封装1)活塞杆在正常使用中,承受交变载荷作用,φ500
-
025
.0
置往复摩擦其表面,所以该处要求硬度高又耐磨。
mm×770mm部分经过调质处理和表面活塞杆采用38CrMoALA材料,φ500
-
.0
025
渗氮后,芯部硬度为28~32HRC,表面渗氮层深度0.2~0.3mm,表面硬度为62~65HRC。
这样使活塞杆既有一定的韧性,又具有较好的耐磨性。
2)活塞杆结构比较简单,但长径比很大,属于细长轴类零件,刚性较差,为了保证加工精度,在车削时要粗车、精车分开,而且粗、精车一律使用跟刀架,以减少加工时工件的变形,在加工两端螺纹时要使用中心架。
3)在选择定位基准时,为了保证零件同轴度公差及各部分的相互位置精度,所有的加工工序均采用两中心孔定位,符合基准统一原则。
4)磨削外圆表面时,工件易产生让刀、弹性变形,影响活塞杆的精度。
因此,在
加工时应修研中心孔,并保证中心孔的清洁,中心孔与顶尖间松紧程度要适宜,并保证良好的润滑。
砂轮一般选择:磨料白刚玉(WA),粒度60#,硬度中软或中、陶瓷结合剂,另外砂轮宽度应选窄些,以减小径向磨削力,加工时注意磨削用量的选择,尤其磨削深度要小。
5)在磨削φ500
mm×770mm外圆和1:20锥度时,两道工序必须分开进行。
.0
025
在磨削1:20锥度时,要先磨削试件,检查试件合格后才能正式磨削工件。
1:20圆锥面的检查,是用标准的1:20环规涂色检查,其接触面应不少于80%。
6)为了保证活塞杆加工精度的稳定性,在加工的全过程中不允许人工校直。
7)渗氮处理时,螺纹部分等应采取保护装置进行保护。