第7章(2)金属加工设备.
《金属结构制造与安装》第七章 平板钢闸门的安装

图7-1 平面闸门门槽埋件结构布置 1-主轨;2-护角;3-底坎;4-侧轨;5-反轨;6-止水座板 -主轨; -护角; -底坎; -侧轨; -反轨; -
Байду номын сангаас
7 平面钢闸门的安装
7.1.1安装埋件前的准备工作 安装埋件前的准备工作 ⑴准备场地 要考虑:起重机械、埋件处理(堆放、检查、调整及除锈刷漆工作) 要考虑:起重机械、埋件处理(堆放、检查、调整及除锈刷漆工作)、不受 土建施工干扰、门叶的组装等。 土建施工干扰、门叶的组装等。 不便使用机械或无吊装机械时,要设法利用地形地物采用土法吊装( 2)。 不便使用机械或无吊装机械时,要设法利用地形地物采用土法吊装(图7-2)。
图7-2 土法吊装埋件
7 平面钢闸门的安装
7.1.1安装埋件前的准备工作(续1) 安装埋件前的准备工作( 安装埋件前的准备工作 ⑵检查埋件和校正变形 埋件运到工地后,应按图纸清点数量并检查构件质量。 埋件运到工地后,应按图纸清点数量并检查构件质量。构件变形不能超过 的允许偏差,超出时必须进行处理。 表7-l的允许偏差,超出时必须进行处理。
主轨、反轨、 图7-10 主轨、反轨、侧轨控制点布置图
焊不锈钢工作面的铸铁轨道; 埋焊不锈 (a)焊不锈钢工作面的铸铁轨道;(b)埋焊不锈 焊不锈钢工作面的铸铁轨道 钢工作面的铸铁轨道;(c)焊不锈钢工作面的 钢工作面的铸铁轨道;(c)焊不锈钢工作面的 焊接轨道;(d)埋焊不锈钢工作面的焊接轨道 焊接轨道;(d)埋焊不锈钢工作面的焊接轨道
表7 - 1
序号 变形和偏差名 工作范围内 1 2 3 工作面弯曲度 侧面弯曲度 工作面局部凸凹不平 度 扭 曲 相邻构件组合处的错 位 构件长度的1/1500且不超 过 构件长度的1/1000且不超 过4 每米范围内不大于1,且 不超过2处 长度不大于3 m的构件, 不应大于1,每增加1m, 递增0.5,且最大不超过2 不大于2,且应平缓过渡 非工作范围内 构件长度的1/1500且不 超过4 构件长度的1/1000且不 超过5 每米范围内不超过4 长度不大于3m的构件, 不应大于2,每增加1m, 递增0.5,且最大不超过3 应平缓过渡 构件长度的1/2000 且不超过1 构件长度的1/1000 且不超过2 每米范围内不大于 0.5,且不超过2处 0.5 不应大于0.5
第7章机械加工工艺规程制订

二、定位基准的选择
粗基准:毛坯上未加工的表面作定位基 准的为粗基准 。 精基准:经过机械加工的表面作定位基 准的为精基准。 选择顺序:先选择精基准定位把工件加 工到设计要求,然后考虑选择粗基准定 位,把用作精密基准的表面加工出来。
1.粗基准的选择原则
1)对于有不加工表面的工件,为保证 不加工表面与加工表面之间的相对位置 要求,一般应选择不加工表面为粗基准。
外圆表面加工方案
1)粗车-半精车-精车 ——软 2)粗车-半精车-粗磨-精磨 ——软、硬 3)粗车-半精车-精车-精细车(金刚车) ——有色金属
孔加工方案
1)钻-(扩)-粗铰-精铰:非旋转体上小孔 2)钻-(扩)-拉 :大批量 3)粗镗-半精镗-精镗 : 箱体上孔 4)粗镗-半精镗-粗磨-精磨:淬硬
3、机械加工工艺过程卡
3、机械加工工序卡
五、制定工艺规程的原则与步骤
1.原则 :保质、高效、低耗。 2.步骤: 1)分析零件图和产品装配图。 2)选择毛坯。 3)选择定位基准。 4)拟定工艺路线。 5)确定加工余量和工序尺寸。
五、制定工艺规程的原则与步骤
1.原则 :保质、高效、低耗。 2.步骤: 6)确定切削用量和工时定额。 7)确定个工序的设备及刀具、夹具、量具 和辅助工具。 8)填写个工序的技术要求及检验方法。 9)填写工艺文件。
1.粗基准的选择原则
(2)如果要保证某加工表面(相对重要 表面)切除的余量均匀,应选该表面作 粗基准 。
1.粗基准的选择原则
(3)为保证各加工表面都有足够的加工 余量,应选择毛坯余量小的表面作粗基 准。
1.粗基准的选择原则
(4)选作粗基准的表面,应尽可能平整, 不能有飞边、浇注系统、冒口或其它缺 陷,以便使工件定位可靠,夹紧方便。 (5)同一尺寸方向上的粗基准表面只能 使用一次。
金属材料学第7-11章课后习题答案
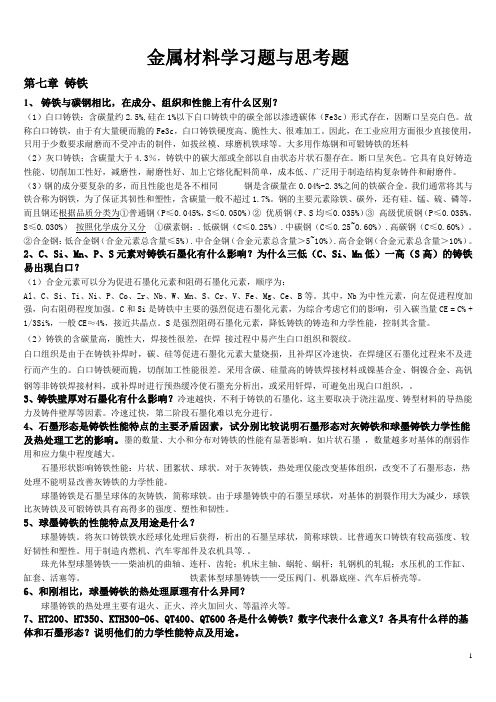
金属材料学习题与思考题第七章铸铁1、铸铁与碳钢相比,在成分、组织和性能上有什么区别?(1)白口铸铁:含碳量约2.5%,硅在1%以下白口铸铁中的碳全部以渗透碳体(Fe3c)形式存在,因断口呈亮白色。
故称白口铸铁,由于有大量硬而脆的Fe3c,白口铸铁硬度高、脆性大、很难加工。
因此,在工业应用方面很少直接使用,只用于少数要求耐磨而不受冲击的制件,如拔丝模、球磨机铁球等。
大多用作炼钢和可锻铸铁的坯料(2)灰口铸铁;含碳量大于4.3%,铸铁中的碳大部或全部以自由状态片状石墨存在。
断口呈灰色。
它具有良好铸造性能、切削加工性好,减磨性,耐磨性好、加上它熔化配料简单,成本低、广泛用于制造结构复杂铸件和耐磨件。
(3)钢的成分要复杂的多,而且性能也是各不相同钢是含碳量在0.04%-2.3%之间的铁碳合金。
我们通常将其与铁合称为钢铁,为了保证其韧性和塑性,含碳量一般不超过1.7%。
钢的主要元素除铁、碳外,还有硅、锰、硫、磷等,而且钢还根据品质分类为①普通钢(P≤0.045%,S≤0.050%)②优质钢(P、S均≤0.035%)③高级优质钢(P≤0.035%,S≤0.030%)按照化学成分又分①碳素钢:.低碳钢(C≤0.25%).中碳钢(C≤0.25~0.60%).高碳钢(C≤0.60%)。
②合金钢:低合金钢(合金元素总含量≤5%).中合金钢(合金元素总含量>5~10%).高合金钢(合金元素总含量>10%)。
2、C、Si、Mn、P、S元素对铸铁石墨化有什么影响?为什么三低(C、Si、Mn低)一高(S高)的铸铁易出现白口?(1)合金元素可以分为促进石墨化元素和阻碍石墨化元素,顺序为:Al、C、Si、Ti、Ni、P、Co、Zr、Nb、W、Mn、S、Cr、V、Fe、Mg、Ce、B等。
其中,Nb为中性元素,向左促进程度加强,向右阻碍程度加强。
C和Si是铸铁中主要的强烈促进石墨化元素,为综合考虑它们的影响,引入碳当量CE = C% + 1/3Si%,一般CE≈4%,接近共晶点。
金属学与热处理课后习题答案第七章
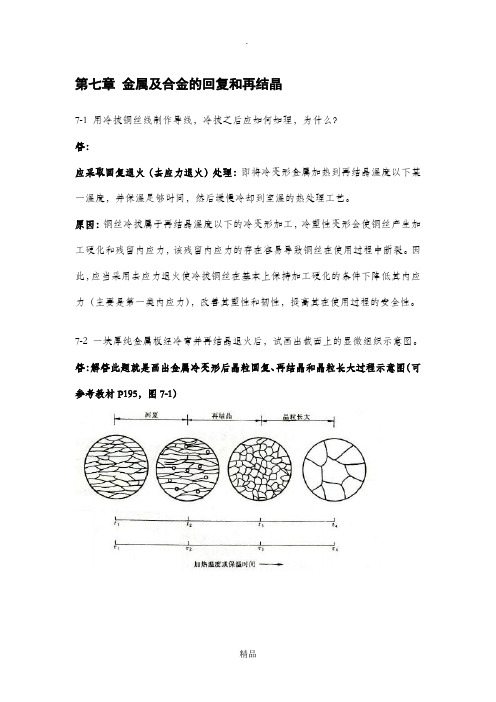
第七章金属及合金的回复和再结晶7-1 用冷拔铜丝线制作导线,冷拔之后应如何如理,为什么?答:应采取回复退火(去应力退火)处理:即将冷变形金属加热到再结晶温度以下某一温度,并保温足够时间,然后缓慢冷却到室温的热处理工艺。
原因:铜丝冷拔属于再结晶温度以下的冷变形加工,冷塑性变形会使铜丝产生加工硬化和残留内应力,该残留内应力的存在容易导致铜丝在使用过程中断裂。
因此,应当采用去应力退火使冷拔铜丝在基本上保持加工硬化的条件下降低其内应力(主要是第一类内应力),改善其塑性和韧性,提高其在使用过程的安全性。
7-2 一块厚纯金属板经冷弯并再结晶退火后,试画出截面上的显微组织示意图。
答:解答此题就是画出金属冷变形后晶粒回复、再结晶和晶粒长大过程示意图(可参考教材P195,图7-1)7-3 已知W、Fe、Cu的熔点分别为3399℃、1538℃和1083℃,试估算其再结晶温度。
答:再结晶温度:通常把经过严重冷变形(变形度在70%以上)的金属,在约1h的保温时间内能够完成超过95%再结晶转变量的温度作为再结晶温度。
1、金属的最低再结晶温度与其熔点之间存在一经验关系式:T再≈δTm,对于工业纯金属来说:δ值为0.35-0.4,取0.4计算。
2、应当指出,为了消除冷塑性变形加工硬化现象,再结晶退火温度通常要比其最低再结晶温度高出100-200℃。
如上所述取T再=0.4Tm,可得:W再=3399×0.4=1359.6℃Fe再=1538×0.4=615.2℃Cu再=1083×0.4=433.2℃7-4 说明以下概念的本质区别:1、一次再结晶和二次在结晶。
2、再结晶时晶核长大和再结晶后的晶粒长大。
答:1、一次再结晶和二次在结晶。
定义一次再结晶:冷变形后的金属加热到一定温度,保温足够时间后,在原来的变形组织中产生了无畸变的新的等轴晶粒,位错密度显著下降,性能发生显著变化恢复到冷变形前的水平,称为(一次)再结晶。
《金属材料与热处理》教材习题答案:第七章 有色金属及硬质合金
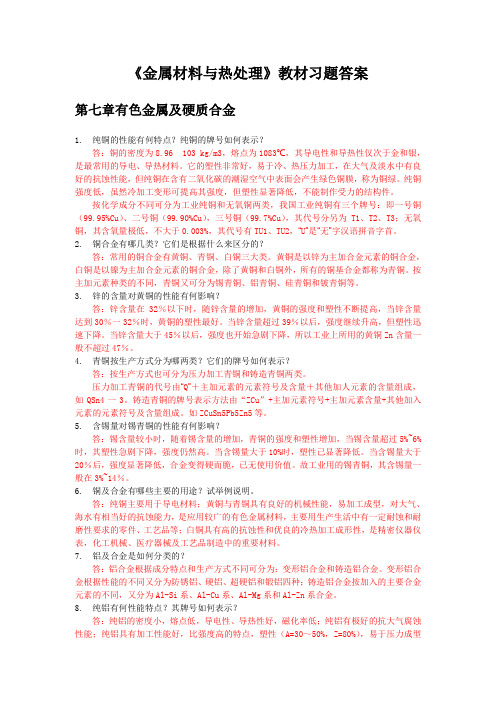
《金属材料与热处理》教材习题答案第七章有色金属及硬质合金1.纯铜的性能有何特点?纯铜的牌号如何表示?答:铜的密度为8.96 ×103 kg/m3,熔点为1083℃,其导电性和导热性仅次于金和银,是最常用的导电、导热材料。
它的塑性非常好,易于冷、热压力加工,在大气及淡水中有良好的抗蚀性能,但纯铜在含有二氧化碳的潮湿空气中表面会产生绿色铜膜,称为铜绿。
纯铜强度低,虽然冷加工变形可提高其强度,但塑性显著降低,不能制作受力的结构件。
按化学成分不同可分为工业纯铜和无氧铜两类,我国工业纯铜有三个牌号:即一号铜(99.95%Cu)、二号铜(99.90%Cu),三号铜(99.7%Cu),其代号分另为T1、T2、T3;无氧铜,其含氧量极低,不大于0.003%,其代号有TU1、TU2,“U”是“无”字汉语拼音字首。
2.铜合金有哪几类?它们是根据什么来区分的?答:常用的铜合金有黄铜、青铜、白铜三大类。
黄铜是以锌为主加合金元素的铜合金,白铜是以镍为主加合金元素的铜合金,除了黄铜和白铜外,所有的铜基合金都称为青铜。
按主加元素种类的不同,青铜又可分为锡青铜、铝青铜、硅青铜和铍青铜等。
3.锌的含量对黄铜的性能有何影响?答:锌含量在32%以下时,随锌含量的增加,黄铜的强度和塑性不断提高,当锌含量达到30%一32%时,黄铜的塑性最好。
当锌含量超过39%以后,强度继续升高,但塑性迅速下降。
当锌含量大于45%以后,强度也开始急剧下降,所以工业上所用的黄铜Zn含量一般不超过47%。
4.青铜按生产方式分为哪两类?它们的牌号如何表示?答:按生产方式也可分为压力加工青铜和铸造青铜两类。
压力加工青铜的代号由“Q”+主加元素的元素符号及含量+其他加人元素的含量组成,如QSn4一3。
铸造青铜的牌号表示方法由“ZCu”+主加元素符号+主加元素含量+其他加入元素的元素符号及含量组成。
如ZCuSn5Pb5Zn5等。
5.含锡量对锡青铜的性能有何影响?答:锡含量较小时,随着锡含量的增加,青铜的强度和塑性增加,当锡含量超过5%~6%时,其塑性急剧下降,强度仍然高。
7.3 电解加工

增液孔 Φ1mm
零件尺寸精
度由阴极片 内腔口保证,
偶尔短路烧
伤时,只需 更换阴极片。
5. 叶片加工
叶片型面复杂,精度要求较高, 加工批量大,电解加工效果好。 加工方式有单面加工和双面加工。 机床有立式和卧式两种。 多用NaCl电解液混气加工。
机械加工设备——第7章
电解加工整体叶轮已普遍应
用,直接在轮坯上套料加工叶
精度控制在±0.1~0.2mm。
也采用端面进给法。
阴极设计制造是关键。用成型
精度高的电解液或混气加工时,阴
极设计较易。为使流场均匀,阴极 对应处加开增液孔。 近年发展用简单形状电极的数 控电解加工,柔性好,减少准备时
间,电源容量小,但加工速度降低
机械加工设备——第7章
4. 套料加工
用于等截面的大面积异 型孔或异型零件的加工,端 面进给加工方式。
图7-9 电解加工示意图 1-直流电源 2-工具电极 3-工件阳极 4-电解液泵 5-电解液
机械加工设备——第7章
7.3.2 电解加工特点:
1、优点:
1)可加工任何硬度的金属材料 2)加工叶片、锻模等型面,加工易变形或薄壁零 件 3)加工表面质量好,无毛刺、变质层、残余应力 4)生产率约为电火花加工的5~10倍 5)阴极工具无损耗可长期使用
机械加工设备——第7章
2.缺点:
1) 加工精度(±0.03 mm)及稳定性不易提高
2) 小孔、窄缝及棱角清晰零件难加工
3) 电极设计制造较麻烦,需多次修整 4) 附属设备多,一次性投资大 5) 防腐蚀及电解泥渣、废液处理问题
机械加工设备——第7章
7.3.3.电解加工工艺选用原则
1. 难加工材料的加工
机械加工设备——第7章
第7章 重金属及其它有机污染物
第7章重金属及其它有机污染物在食品安全领域中,重金属的概念和范围并不十分严格,一般是指对生物有显著毒性的一类元素,而其它有机污染物主要包括N-亚硝基化合物、多环芳烃化合物、杂环胺类化合物和二恶英等化合物。
7.1重金属从毒性角度出发,重金属既包括有毒元素如铅、镉、汞、铬、锡、镍、铜、锌、钡、锑、铊等金属,也包括铍、铝等轻金属和砷、硒等类金属,非金属元素氟通常也包括在内。
自从20世纪50年代日本出现水俣病和痛痛病,最终查明是由于食品遭到汞污染和镉污染所引起的,自此以后,重金属所造成的食源性危害问题开始引起人们极大的关注。
7.1.1重金属污染食品的途径重金属污染食品的途径除高本底的自然环境以外,主要是人类活动造成的环境污染。
其中造成食品污染的主要渠道是工业生产中三废的不合理排放,农业上施用含重金属的农药和化肥等;其次是原料、添加剂、加工机械、容器、包装、贮存和运输等环节可能对食品造成重金属污染。
7.1.2重金属的毒性作用特点人体摄入的重金属,不仅其本身表现出毒性,而且可在人体微生物作用下转化为毒性更大的金属化合物,如汞的甲基化作用。
另外其他生物还可以从环境中摄取重金属,经过食物链的生物放大作用,在体内千万倍地富集,并随食物进入人体而造成慢性中毒。
一般认为,重金属的中毒机理是:重金属离子与蛋白质分子中的巯基、羧基、氨基、咪唑基等形成重金属配合物,可产生使酶阻断或使膜变性等生理毒害作用。
重金属形成的化合物在体内不易分解,半衰期较长,有蓄积性,可引起急性或慢性中毒反应,还有可能产生致畸、致癌和致突变作用。
重金属在体内的毒性作用受许多因素影响,如与侵入途径、浓度、溶解性、存在状态、膳食成分、代谢特点及人体的健康状况等因素密切相关。
在众多有毒元素中,以铅、镉、汞、砷等元素对食品安全的影响最为严重,下面主要介绍它们的污染来源以及常用的国家标准检测方法。
7.1.3铅对食品的污染铅(lead,Pb)为灰白色金属。
铅的氧化态有0、+2和+4。
第七章 金属切削加工基础知识 1
2.进给运动:由机床或人力提供的运动,它使刀具
与工件间产生附加的相对运动,进给运动将使被切
削金属层不断地投入切削,以加工出具有所需几何 特性的已加工表面.(车削外圆时,进给运动是刀具 的纵向运动;牛头刨床刨削时,进给运动是工作台 的移运.)
3.主运动和进给运动的合成: 当主运动和进给运动 同时进行时,切削刃
互接触的表面上承受了很大的压力和强烈的摩
擦、刀具在高温下进行切削的同时,还承受着
切削力、冲击和振动,因此要求刀具切削部分
的材料应具备以下性能:
1.高硬度:刀具材料必须具有高于工件材料的硬
度,常温硬度应在HRC60以上。
2.耐磨性:耐磨性表示刀具抵抗磨损的能力,通
常刀具材料的硬度越高,耐磨性越好。
第七章 金属切削加工基础知识
要求目的:理解零件加工质量的概念、掌握切削
运动和金属切削刀具的基本知识、认识金属切削
过程的基本规律。
重点、难点:切削运动和切削刀具。
7.1 加工质量
金属切削加工(或冷加工)是指用切削工具从坯
料或工件上切除多余材料,以获得所要求的几何 形状、尺寸精度和表面质量的零件的加工方法。
公差、形状公差和位置公差来表示。
1.尺寸精度:是指加工表面本身的尺寸(如圆柱面
的直径)和表面间的尺寸(如孔间距离等)的精
确程度。尺寸精度的高低,用尺寸公差的大小来 表示。 为了实现互换性和满足各种使用要求,国家标准 GB1800-79规定,尺寸公差分为20个公差等级,即
IT01、IT0、IT1、IT2„„、IT18。从IT01 ~IT18,
Vc (m / min 或m / s)
式中:d——工件直径,㎜ n——工件或刀具每分钟(秒)转数(r/min或r/S)
第七章金属热处理原理复习题(已做完)
第七章⾦属热处理原理复习题(已做完)第七章《⾦属热处理原理》部分复习题⼀、名词解释:1.实际晶粒度:某⼀具体热处理或热加⼯条件下的奥⽒体的晶粒度叫实际晶粒度2.马⽒体、贝⽒体(上贝⽒体和下贝⽒体):过冷奥⽒体的等温转变中温转变时渗碳体分布在碳过饱和的铁素体基体上的两相混合物称为贝⽒体,上贝⽒体(B上):550℃~350℃,呈⽻⽑状,⼩⽚状的渗碳体分布在成排的铁素体⽚之间,下贝⽒体(B 下):350℃~Ms:在光学显微镜下为⿊⾊针状,在电⼦显微镜下可看到在铁素体针内沿⼀定⽅向分布着细⼩的碳化物(Fe2.4C)颗粒。
贝⽒体:过冷奥⽒体的连续冷却转变时碳在α-Fe 中的过饱和间隙固溶体。
⼆、填空题:1.钢加热时奥⽒体形成是由奥⽒体形核;晶核的长⼤;未溶碳化物(Fe3C)溶解;奥⽒体成分均匀化等四个基本过程所组成。
2.在过冷奥⽒体等温转变产物中,珠光体与屈⽒体的主要相同点是都是它们都是珠光体类型的组织,不同点是层间距不同,且珠光体层间距较⼤,屈似体层间距最⼩。
3.⽤光学显微镜观察,上贝⽒体的组织特征呈⽻⽑状状,⽽下贝⽒体则呈⿊⾊针状。
4.与共析钢相⽐,⾮共析钢C曲线的特征是多⼀条过冷A→F或(Fe3CⅡ)的转变开始线,亚共析钢左上部多⼀条过冷A转变为铁素体(F)的转变开始线,过共析钢多⼀条过冷A中析出⼆次渗碳体(Fe3CII) 开始线。
5.马⽒体的显微组织形态主要有板条状、针状两种。
其中板条状马⽒体的韧性较好。
6.⾼碳淬⽕马⽒体和回⽕马⽒体在形成条件上的区别是前者是在淬⽕中形成,后者在低温回⽕时形成,在⾦相显微镜下观察⼆者的区别是前者为⽵叶形,后者为⿊⾊针装。
7.⽬前较普遍采⽤的测定钢的淬透性的⽅法是“末端淬⽕法”即端淬试验。
三、判断题:1.所谓本质细晶粒钢就是⼀种在任何加热条件下晶粒均不发⽣粗化的钢。
(×)2.当把亚共析钢加热到A c1和A c3之间的温度时,将获得由铁素体和奥⽒体构成的两相组织,在平衡条件下,其中奥⽒体的碳含量总是⼤于钢的碳含量。
最新中职金属加工常识试卷库:第七章刨削、插削及拉削加工
第七章刨削、插削及拉削加工
一、填空题
l.刨削时,刨刀(或工件)的为主运动,工件(或刨刀)在垂直于方向的为进给运动。
2.按主运动方向有刨削和插削,刨、插削为切削,易受冲击,。
3.刨床应用最广泛,刨大型工件应选用床。
4.在刨床上可以加工、及等。
5.拉削的主运动为、进给运动由。
6.刨削较小的工件可用,较大的工件可用。
7.牛头刨床主要有、、、等部分组成。
8.刨削加工是刨刀相对工件作运动的切削加工方法。
二、判断题
1.因刨削过程有冲击和振动,故加工精度一般不高。
()
2.插削与刨削的共同点是刀具作直线往复切削运动。
()
3.一种拉刀可以加工各种不同形状和尺寸的工件。
()。
4.刨刀往往做成弯头形状,使刨刀在受力弯曲时刀尖能离开加工表面,防止扎刀。
() 5.斜面刨削的方法很多,一般是通过倾斜工作台而获得。
6.拉孔时,必须夹紧工件,拉刀作水平直线移动。
()。
7,因切削速度较低,刨削时一般不用切削液。
()
8.刨削与插削的主要区别是主运动的方向不同。
()
9.插刀与创刀相比,其前、后刀面的位置是相同的。
()
10.拉床一般不采用机械传动,而采用液压传动。
()
三、简答题
1、刨削加工的基本内容是什么?
2、插削加工的工艺特点是什么?。
- 1、下载文档前请自行甄别文档内容的完整性,平台不提供额外的编辑、内容补充、找答案等附加服务。
- 2、"仅部分预览"的文档,不可在线预览部分如存在完整性等问题,可反馈申请退款(可完整预览的文档不适用该条件!)。
- 3、如文档侵犯您的权益,请联系客服反馈,我们会尽快为您处理(人工客服工作时间:9:00-18:30)。
例1: CA6140
C:类别代号(床类) A:结构性代号(A结构) 6:组别代号(卧式车床组) 1:系别代号(普通车床系) 40:主参数代号(床身上最大回转直径400mm)
例2: M M 7 1 32 A
M:类别代号(磨床类) M:通用特性代号(精密) 7:组别代号(平面及端面磨床组) 1:系别代号(卧轴矩台平面磨床系) 32:主参数代号(工作台面宽度320mm)
1、通用机床的型号编制 2)机床的通用特性代号 :
通 用 特 性
高 精 度
精 密
M 密
自 动
Z 自
半 自 动
数 控
K 控加工中心 (自动换刀) Nhomakorabea彷型
F 彷
轻 型
Q 轻
加 重 型
简式 柔性 或经 加工 济型 单元
数显 高速
X 显 S 速
代 号 读 音
G 高
B 半
H 换
C 重
J 简
R 柔
二、机床的型号编制
一、机床的分类
机床主要是按加工方法和所用刀具进行分 类,根据国家制定的机床型号编制方法,机床 分为11大类: 车床,钻床,镗床,磨床,齿轮加工机床, 螺纹加工机床,铣床,刨插床,拉床,锯床和 其他机床。 在每一类机床中,又按工艺范围,布局型式 和结构性能分为若干组,每一组又分为若干个 系(系列)。
1/10
1/100 1/10
最大模数
工作台面长度 工作台面长度
龙门刨床
插床及牛头刨床 拉床
最大刨削宽度
最大插削及刨削长度 额定拉力(t)
1/100
1/10 1/1
最大刨削长度
- 最大行程
二、机床的型号编制
1、通用机床的型号编制 6)机床的重大改进顺序号 当机床性能和结构布局有重大改进时,在原机床型 号尾部,加重大改进顺序号A,B,C....等。
A:重大改进顺序号(第一次重大改进)
例3: T H M 6 3 50 /JCS
T:类别代号(镗床类) H:结构性代号(加工中心)
M:通用特性代号(精密)
6:组别代号(卧式铣镗床组)
3:系别代号(卧式铣镗床系)
50:主参数代号(工作台面宽度500mm) JCS:企业代号(北京机床研究所)
例 4:
Z 3 0 40 X46 /S2
摇臂钻床
卧式镗铣床 坐标镗床
最大钻孔直径
镗轴直径 工作台面宽度
1/1
1/10 1/10
最大跨距
- 工作台面长度
外圆磨床
内圆磨床 矩台平面磨床
最大磨削直径
最大磨削孔径 工作台面宽度
1/10
1/10 1/10
最大磨削长度
最大磨削深度 工作台面长度
齿轮加工机床
龙门铣床 升降台铣床
最大工件直径
工作台面宽度 工作台面宽度
1、通用机床的型号编制 3)结构特性代号: 为区别主参数相同而结构不同 的机床,在型号中用汉语拼音字分。 如:CA6140中的“A”。
。
二、机床的型号编制
1、通用机床的型号编制 4)机床的组别,系别代号: ①机床的组别和系别代号用两位数字表示; ②每类机床按其结构性能及使用范围划分为10组, 用数字0-9表示; ③系的划分原则是:主参数相同,并按一定公比 排列,工件和刀具本身的及相对的运动特点基本相同, 且基本结构及布局型式相同的机床,即划为同一系。 详见标准JB1838-85。
一、机床的分类
③专用机床: 这类机床的工艺范围最窄,通常只能 完成某一特定零件的特定工序。如,加工机床主轴箱 体孔的专用镗床,加工机床导轨的专用导轨磨床等。 它是根据特定的工艺要求专门设计,制造的,生产率 和自动化程度较高,使用于大批量生产。组合机床也 属于专用机床。
一、机床的分类
2、按照机床的工作精度,可分为普通精度机床,精 密机床和高精度机床。 3、按照重量和尺寸,可分为仪表机床,中型机床 (一般机床),大型机床(质量大于10t),重型机床 (质量在30t以上)和超重型机床(质量在100t以上)。 4、按照机床主要器官的数目,可分为单轴,多轴, 单刀,多刀机床等。 5、按照自动化程度不同,可分为普通,半自动和自 动机床。
第二节 金属切削加工设备
金属切削机床是用刀具切削的方法将金属毛坯加工成机
器零件的机器,它是制造机器的机器,所以又称为“工 作母机”,习惯上简称为机床。机床是机械制造的基础 机械,其技术水平的高低,质量的好坏,对机械产品的 生产率和经济效益都有重要的影响。金属切削机床诞生 到现在已经有一百多年了,随着工业化的发展,机床品 种越来越多,技术也越来越复杂。我国第三次工业普查 的结果表明,截止到 1995 年底,我国机床拥有量为 383.52万台,其中金属切削机床为298.39万台,已占机 床总数的77.80%。
二、机床的型号编制
1、通用机床的型号编制 1)机床的类别代号 :
类 别
代 号 读 音
车 床
C
钻 床
Z
镗 床
T
磨 床
M 2M 3M
齿轮 加工 机床
螺纹 加工 机床
铣 床
X
刨 插 床
拉 床
L
锯 床
G
其他 机床
Y
S
B
Q
车
钻
镗
磨
二 磨
三 磨
牙
丝
铣
刨
拉
割
其
注意:分类代号用数字表示,只有磨床才有
二、机床的型号编制
Z:类别代号(钻床类) 3:组别代号(摇臂钻床组)
二、机床的型号编制
机床的型号是机床产品的代号,用以表明机床的 类型,通用和结构特性,主要技术参数等。 GB/T15375-94《金属切削机床型号编制方法》规定, 我国的机床型号由汉语拼音字母和阿拉伯数字按一定 规律组合而成。
二、机床的型号编制
1、通用机床的型号编制 通用机床型号的表示方法为:
二、机床的型号编制
。
二、机床的型号编制
1、通用机床的型号编制 5)机床的主参数和第二参数 机床主参数:代表机床规格的大小,在机床型号中, 用数字给出主参数的折算数值(1/10或1/150)。 第二参数:一般是主轴数,最大跨距,最大工作长度, 工作台工作面长度等,它也用折算值表示。
二、机床的型号编制
机床 卧式车床 立式车床 主参数名称 床身上最大回转直径 最大车削直径 主参数折算系数 1/10 1/100 第二主参数 最大工件长度 最大工件高度
一、机床的分类
1、按照万能性程度,机床可分为: ①通用机床:这类机床的工艺范围很宽,可以加工 一定尺寸范围内的多种类型零件,完成多种多样的工 序。如,卧式车床,万能升降台铣床,万能外圆磨床 等。 ②专门化机床:这类机床的工艺范围较窄,只能用 于加工不同尺寸的一类或几类零件的一种(或几种) 特定工序。如,丝杆车床,凸轮轴车床等。