精益管理专业术语-M系列
精益生产管理常用术语
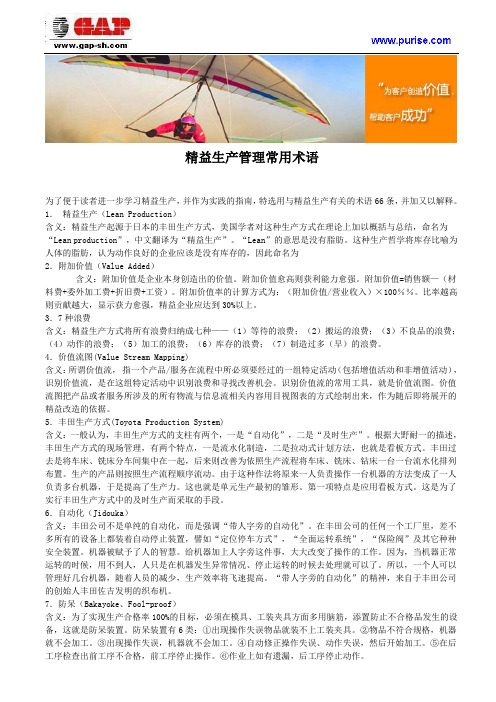
精益生产管理常用术语为了便于读者进一步学习精益生产,并作为实践的指南,特选用与精益生产有关的术语66条,并加又以解释。
1.精益生产(Lean Production)含义:精益生产起源于日本的丰田生产方式,美国学者对这种生产方式在理论上加以概括与总结,命名为“Lean production”,中文翻译为“精益生产”。
“Lean”的意思是没有脂肪。
这种生产哲学将库存比喻为人体的脂肪,认为动作良好的企业应该是没有库存的,因此命名为2.附加价值(Value Added)含义:附加价值是企业本身创造出的价值。
附加价值愈高则获利能力愈强。
附加价值=销售额—(材料费+委外加工费+折旧费+工资)。
附加价值率的计算方式为:(附加价值/营业收入)×100%%。
比率越高则贡献越大,显示获力愈强,精益企业应达到30%以上。
3.7种浪费含义:精益生产方式将所有浪费归纳成七种——(1)等待的浪费;(2)搬运的浪费;(3)不良品的浪费;(4)动作的浪费;(5)加工的浪费;(6)库存的浪费;(7)制造过多(早)的浪费。
4.价值流图(Value Stream Mapping)含义:所谓价值流,指一个产品/服务在流程中所必须要经过的一组特定活动(包括增值活动和非增值活动),识别价值流,是在这组特定活动中识别浪费和寻找改善机会。
识别价值流的常用工具,就是价值流图。
价值流图把产品或者服务所涉及的所有物流与信息流相关内容用目视图表的方式绘制出来,作为随后即将展开的精益改造的依据。
5.丰田生产方式(Toyota Production System)含义:一般认为,丰田生产方式的支柱有两个,一是“自动化”,二是“及时生产”。
根据大野耐一的描述,丰田生产方式的现场管理,有两个特点,一是流水化制造,二是拉动式计划方法,也就是看板方式。
丰田过去是将车床、铣床分车间集中在一起,后来则改善为依照生产流程将车床、铣床、钻床一台一台流水化排列布置。
39个精益管理术语,都在这里了...
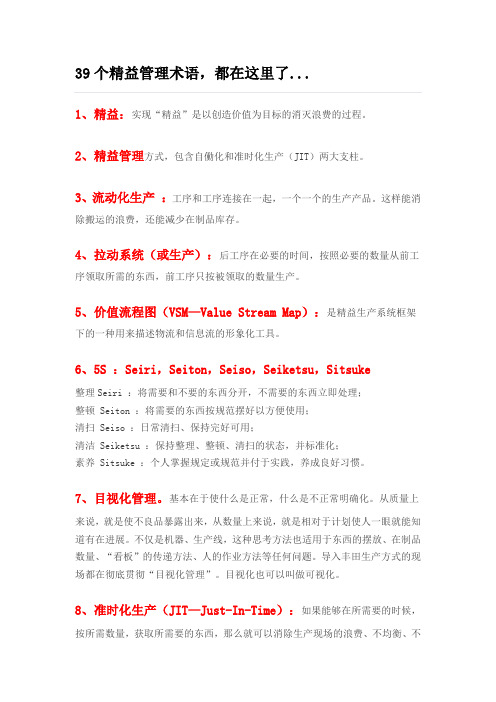
39个精益管理术语,都在这里了...1、精益:实现“精益”是以创造价值为目标的消灭浪费的过程。
2、精益管理方式,包含自働化和准时化生产(JIT)两大支柱。
3、流动化生产:工序和工序连接在一起,一个一个的生产产品。
这样能消除搬运的浪费,还能减少在制品库存。
4、拉动系统(或生产):后工序在必要的时间,按照必要的数量从前工序领取所需的东西,前工序只按被领取的数量生产。
5、价值流程图(VSM—Value Stream Map):是精益生产系统框架下的一种用来描述物流和信息流的形象化工具。
6、5S :Seiri,Seiton,Seiso,Seiketsu,Sitsuke整理Seiri :将需要和不要的东西分开,不需要的东西立即处理;整顿 Seiton :将需要的东西按规范摆好以方便使用;清扫 Seiso :日常清扫、保持完好可用;清洁 Seiketsu :保持整理、整顿、清扫的状态,并标准化;素养 Sitsuke :个人掌握规定或规范并付于实践,养成良好习惯。
7、目视化管理。
基本在于使什么是正常,什么是不正常明确化。
从质量上来说,就是使不良品暴露出来,从数量上来说,就是相对于计划使人一眼就能知道有在进展。
不仅是机器、生产线,这种思考方法也适用于东西的摆放、在制品数量、“看板”的传递方法、人的作业方法等任何问题。
导入丰田生产方式的现场都在彻底贯彻“目视化管理”。
目视化也可以叫做可视化。
8、准时化生产(JIT—Just-In-Time):如果能够在所需要的时候,按所需数量,获取所需要的东西,那么就可以消除生产现场的浪费、不均衡、不合理,提高生产效率。
该思想的开山鼻祖是丰田汽车的创始人-丰田喜一郎,其后继者将此思想展开,概括成为了一个生产体系。
不单是in time, 而是just in time,这是一个重要的关键。
“Just-In-Time”和“自働化”共同形成丰田生产方式的两大支柱。
9、自働化(Jidoka):在丰田的生产方式当中,必须完全是带人字旁的“自働化”。
100个精益名词解释(全)
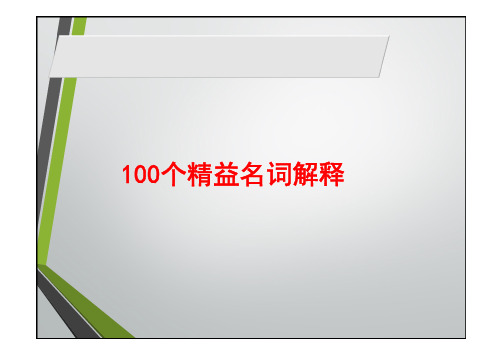
100个精益名词解释A3 Report (A3报告)一种由丰田公司开创的方法,通常用图形把问题、分析、改正措施、以及执行计划囊括在一张大的(A3)纸上。
在丰田公司,A3报告已经成为一个标准方法,用来总结解决问题的方案,进行状态报告,以及绘制价值流图。
国际通用的A3纸是指宽297毫米,长420毫米的纸张。
A-B Control (A-B控制)一种控制两台机器或是两个工位之间生产关系的方法,用于避免过量生产,确保资源的平衡使用。
图示中,除非满足下面三个条件,否则任何一台机器或是传送带都不准运行:A机器已装满零件;传送带上有标准数量的在制品(本例中为一件);B机器上没有零件。
只有当这三个条件都满足的时候,才可以进行一个生产周期,然后等再次满足这些条件时,再进行下一个周期。
Andon (信号灯)一个可视化的管理工具,让人们一眼就能够看出工作的运转状况,并且在任何有异常状况时发出信号。
Andon可以用来指示生产状态(例如,哪一台机器在运转),异常情况(例如,机器停机,出现质量问题,工装故障,操作员的延误,以及材料短缺等),以及需要采取的措施,如换模等。
此外,Andon同样也可以通过计划与实际产量的比值来反映生产状态。
Automatic Line Stop (自动停止生产线)出现任何生产问题或质量缺陷的时候都会自动停止生产。
对于自动生产线而言,这通常包括安装传感器及相应开关,用来探测异常情况,并且自动停止生产线。
对于非自动生产线而言,通常设置一个固定工位,用来停止生产线的运转。
如果无法在生产周期中解决问题,这个工位的操作员可以在周期结束的时候,通过绳子或是按钮来停止生产。
这个例子解释了自动化(Jidoka)的精益原则,它能够防止缺陷进入到下一个生产工序,并且能够避免制造出一系列的缺陷产品。
与之形成对比的是,有些大批量的生产厂家,即便是发现缺陷重复出现,不得不返工时,仍维持生产线的运转,为了是获得较高的设备利用率。
精益生产术语中英文对照_20150227

序号中文英文1山积图stack diagram2线平衡line balancing3标准作业程序standard operation procedure(SOP) 4客户节拍customer takt time(TT)5节拍cycle time(CT)6换型change over (CO)7前置期lead time8有价值的时间value added time9缓冲buffer10设备综合效率overall equipment efficiency (OEE) 11标准作业票standard work sheet(SWS)12价值流程图value stream mapping (VSM)13价值流设计value stream design(VSD)14批量大小lot size15操作工operator (OP)16多技能工multi-skilled operator17技能矩阵skill metrix18班shift19零件计划plan for every part (PFEP)20防呆poka yoke21牛奶线milkrun22均衡生产leveling23看板Kanban24安灯andon25物料上线点point of use provider (POUP)26先进先出first in first out (FIFO)27在制品库存work in process (WIP)28生产效率productivity29一分钟换模single minute exchange die(SMED) 30持续改善continue improvement(CI)31改善KAIZEN32浪费waste根本原因root cause临时措施temperary action长期措施Long-term action截止日期due date序号No.责任人PIC(person in charge)。
我说精益管理之M阶段
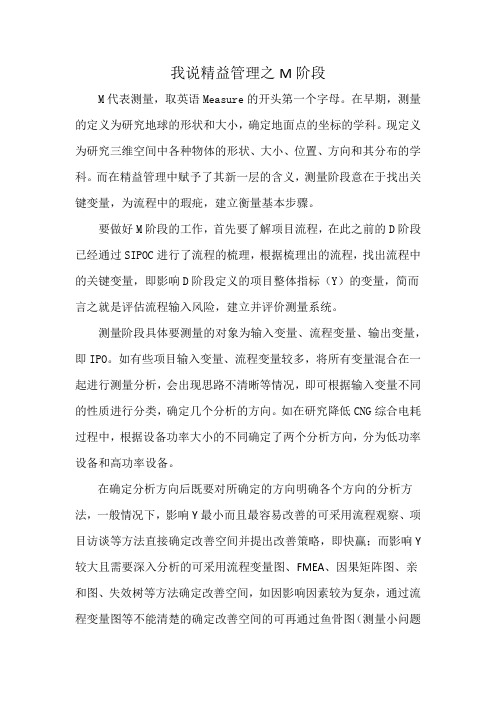
我说精益管理之M阶段M代表测量,取英语Measure的开头第一个字母。
在早期,测量的定义为研究地球的形状和大小,确定地面点的坐标的学科。
现定义为研究三维空间中各种物体的形状、大小、位置、方向和其分布的学科。
而在精益管理中赋予了其新一层的含义,测量阶段意在于找出关键变量,为流程中的瑕疪,建立衡量基本步骤。
要做好M阶段的工作,首先要了解项目流程,在此之前的D阶段已经通过SIPOC进行了流程的梳理,根据梳理出的流程,找出流程中的关键变量,即影响D阶段定义的项目整体指标(Y)的变量,简而言之就是评估流程输入风险,建立并评价测量系统。
测量阶段具体要测量的对象为输入变量、流程变量、输出变量,即IPO。
如有些项目输入变量、流程变量较多,将所有变量混合在一起进行测量分析,会出现思路不清晰等情况,即可根据输入变量不同的性质进行分类,确定几个分析的方向。
如在研究降低CNG综合电耗过程中,根据设备功率大小的不同确定了两个分析方向,分为低功率设备和高功率设备。
在确定分析方向后既要对所确定的方向明确各个方向的分析方法,一般情况下,影响Y最小而且最容易改善的可采用流程观察、项目访谈等方法直接确定改善空间并提出改善策略,即快赢;而影响Y 较大且需要深入分析的可采用流程变量图、FMEA、因果矩阵图、亲和图、失效树等方法确定改善空间,如因影响因素较为复杂,通过流程变量图等不能清楚的确定改善空间的可再通过鱼骨图(测量小问题的方法)等方法手段进行分析,进而查找出改善空间。
在确定改善空间后,即确定了影响Y较大且需要深入分析的因素后,需对各个因素进行现状说明,说明可通过两种形式:一种为数据说明的形式,以数据为基础,采用时序图、流程能力图、残差图等进行说明;在无数据的情况下也可采用文字说明的形式对需要改善的因素进行表述。
精益管理中数据的来源非常重要,数据是从真实的情况下采集上来的,但为保证数据的真实性,容易使其他人信服,往往需要对数据进行真实性验证,如理清数据采集流程、方法、注意事项等等。
精益生产管理中的常见术语(一)
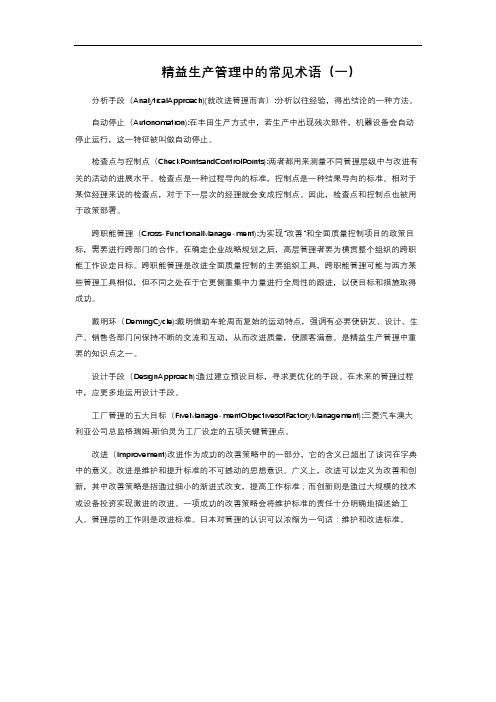
精益生产管理中的常见术语(一)分析手段(AnalyticalApproach)(就改进管理而言):分析以往经验,得出结论的一种方法。
自动停止(Autonomation):在丰田生产方式中,若生产中出现残次部件,机器设备会自动停止运行,这一特征被叫做自动停止。
检查点与控制点(CheckPointsandControlPoints):两者都用来测量不同管理层级中与改进有关的活动的进展水平。
检查点是一种过程导向的标准,控制点是一种结果导向的标准。
相对于某位经理来说的检查点,对于下一层次的经理就会变成控制点。
因此,检查点和控制点也被用于政策部署。
跨职能管理(Cross-FunctionalManage-ment):为实现“改善”和全面质量控制项目的政策目标,需要进行跨部门的合作。
在确定企业战略规划之后,高层管理者要为横贯整个组织的跨职能工作设定目标。
跨职能管理是改进全面质量控制的主要组织工具,跨职能管理可能与西方某些管理工具相似,但不同之处在于它更侧重集中力量进行全局性的跟进,以使目标和措施取得成功。
戴明环(DemingCycle):戴明借助车轮周而复始的运动特点,强调有必要使研发、设计、生产、销售各部门间保持不断的交流和互动,从而改进质量,使顾客满意。
是精益生产管理中重要的知识点之一。
设计手段(DesignApproach):通过建立预设目标,寻求更优化的手段。
在未来的管理过程中,应更多地运用设计手段。
工厂管理的五大目标(FiveManage-mentObjectivesofFactoryManagement):三菱汽车澳大利亚公司总监格瑞姆·斯伯灵为工厂设定的五项关键管理点。
改进(Improvement)改进作为成功的改善策略中的一部分,它的含义已超出了该词在字典中的意义。
改进是维护和提升标准的不可撼动的思想意识。
广义上,改进可以定义为改善和创新,其中改善策略是指通过细小的渐进式改变,提高工作标准;而创新则是通过大规模的技术或设备投资实现激进的改进。
精益六西格玛黑带课程-M阶段-数据收集与抽样
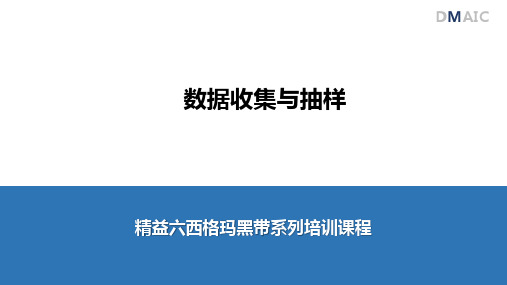
小结:有或无子组的系统抽样
DMAIC
无子组的
子组的
适于小批量流程 单元或测量值频繁地以‘每次一个 出现 频繁抽样 对于非时间序列的流程
(如. 服务,行政管理) 单值数据控制图
大规模生产 有合理的分组为基础
例如:电话服务中心每2小时抽 样5个(在 8.00,12.00,14.00等)
用组内变差的均值确定整体变差
DMAIC
表A
顾客总体的人口数据 (%)
年龄 30-45 45-60 M 10% 20% W 20% 50%
表B
样本的人口数据 (数量)
年龄 30-45 45-60 合计 M 250 250 500
W 250 250 500 合计 500 500 1000
性别 性别
抽样案例3– 电信公司新服务(继续)
DMAIC
用Minitab练习采集随机样本(续)
1. 随机产生3000个数据 N( 10, 10) 2. 从3000中随机抽取100个数据 3. 计算这两列的均值和标准偏差
DMAIC
简单随机抽样:随机样本具有的代表性
DMAIC
. 即使对于小样本,也有要素的大量组合方式 例如: 从100个单元中随机抽出10个单元的可能方法有1.73E13 (173亿)
练习 1: 抽样方法的选择
DMAIC
案例 1
肯德基在中国地区又推出一种新的快餐, 高层领导想知道 顾客对此新款快餐的满意度如何, 应采用什么抽样方法?
案例 2
某家电卖场想调查顾客从决定购买到拿到商品的时间, 用什么抽样方法?
案例 3
某手机制造公司过去半年积压了很多某型号的产品, 需要降价处理, 在卖给消费者之前需要对产品进行抽样检验, 应如何抽样? 对于公司正在生产的新型号产品又如何抽样检验产品质量?
实验室管理学精益管理名词解释
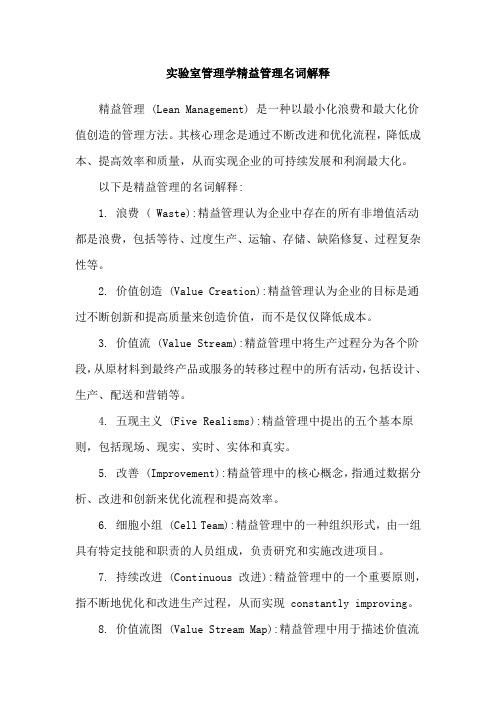
实验室管理学精益管理名词解释精益管理 (Lean Management) 是一种以最小化浪费和最大化价值创造的管理方法。
其核心理念是通过不断改进和优化流程,降低成本、提高效率和质量,从而实现企业的可持续发展和利润最大化。
以下是精益管理的名词解释:1. 浪费 ( Waste):精益管理认为企业中存在的所有非增值活动都是浪费,包括等待、过度生产、运输、存储、缺陷修复、过程复杂性等。
2. 价值创造 (Value Creation):精益管理认为企业的目标是通过不断创新和提高质量来创造价值,而不是仅仅降低成本。
3. 价值流 (Value Stream):精益管理中将生产过程分为各个阶段,从原材料到最终产品或服务的转移过程中的所有活动,包括设计、生产、配送和营销等。
4. 五现主义 (Five Realisms):精益管理中提出的五个基本原则,包括现场、现实、实时、实体和真实。
5. 改善 (Improvement):精益管理中的核心概念,指通过数据分析、改进和创新来优化流程和提高效率。
6. 细胞小组 (Cell Team):精益管理中的一种组织形式,由一组具有特定技能和职责的人员组成,负责研究和实施改进项目。
7. 持续改进 (Continuous 改进):精益管理中的一个重要原则,指不断地优化和改进生产过程,从而实现 constantly improving。
8. 价值流图 (Value Stream Map):精益管理中用于描述价值流的图形化工具,可以帮助企业分析和优化生产过程。
9. 浪费可视化 ( Waste Visualization):精益管理中的一种方法,通过可视化浪费,帮助企业更好地识别和消除浪费。
10. 拉动系统 (Pull System):精益管理中的一种生产组织形式,强调由客户需求来拉动生产,而不是通过堆积和过量生产来响应客户需求。
- 1、下载文档前请自行甄别文档内容的完整性,平台不提供额外的编辑、内容补充、找答案等附加服务。
- 2、"仅部分预览"的文档,不可在线预览部分如存在完整性等问题,可反馈申请退款(可完整预览的文档不适用该条件!)。
- 3、如文档侵犯您的权益,请联系客服反馈,我们会尽快为您处理(人工客服工作时间:9:00-18:30)。
精益管理专业术语-M系列
1.MachineCycleTime(机器周期时间)
用机器加工,完成一件产品总共需要的时间。
2.Massproduction(大批量生产)
20世纪初出现的一种组织和管理产品开发、生产运作、采购和客户关系的制造方法。
典型特征:
·设计工序循序进行,非并行。
·材料以大批量、低频率方式运输。
3.MachineCycleTime(机器周期时间)
一台机器生产一个单位产品的时间。
4.MachineWork(机器工作)
由机器完成的工作。
5.ManualWork(手动工作)
由人完成的工作。
6.ManufacturingResourcesPlanning(MRPII)(物料需求计划MRP)
第二代物料需求计划增加了额外的控制联系,如采购订单自动生成,容量计划,以及应付账款业务。
7.MasterBlackBelt(黑带大师)
黑带大师是为组织实现战略负责的六西格玛质量专家。
8.MaterialsRequirementsPlanning(MRP)(物料需求计划)
计算机管理系统,计算主要生产计划中的物料需求。
9.MistakeProofing(错误预防)
帮助减少或消除行动中出现错误的任何改变。
10.MixedModelProduction(混合模式生产)
生产各种各样模型的能力,在同样的生产线上用不同的劳动力和材料内容。
11.Muda,Mura,Muri
在丰田生产系统中,常结合使用的三个术语,主要用来描述需要消除的浪费行为。
Muda
一切不为顾客创造价值但却消耗资源的活动。
在这个分类中,我们有必要把1型muda和2型muda区分开来。
1型muda指的是一系列不能立即消除的活动,一个例子是,由于无法达到顾客对喷漆要求,而进行返工操作的喷漆工序。
由于在此之前,制造商已经为提高喷漆工序的效率,努力了十几年,因此这种类型的浪费,不大可能被立即消除。
2型muda指的是可以通过改善,立即消除的浪费活动,一个例子是在制造装配工序中,多次无谓的搬运产品。
可以通过改善研习会,把生产设备和操作员安排到一个平顺流动的生产单元中,从而迅速消除这类浪费。
Mura
生产运作的不平衡。
例如,生产系统的进度安排不符合客户的需求,而是由生产系统本身决定;或者一个不均衡的工作节拍,导致操作员有时匆忙,有时空闲的现象。
这种不均衡的问题,通常可以通过管理涉外能够生产平衡,及改进工作节拍而消除。
Muri
超载的设备或是超负荷的工人,通常是工作的节拍比原设计的规格更高、更困难所致。
12.Multi-MachineHandling(多机操作)
或称多机床看管。
指在一个加工群布局中,为操作员分配的机器数量多于一台的做法。
在纺织行业,这种组织方式早就得到广泛应用。
特别是机械行业习惯上还是采取一机一人的组织方式。
随着生产技术的不断提高,设备的自动化程度越来越高,需要工人操作的作业内容日趋简单,所需操作时间日益减少,一人操作一台机器的话,会有很多空闲时间,造成劳动力的大量浪费。
实行多机床看管可以充分利用工人的工作时间,有利于节约劳动力,有利于降低生产成本。
13.Multi-ProcessHandling(多工序操作)
在一个以物料流为导向的布局中,为操作员分配多个生产工序的方法。
这需要对操作员做好培训。
在我们生产现场,既有多机操作,又有多工序操作。
对于大批量生产模式,一般是将操作员安排到一独立工位,只操作一种机器。
14.MultiMachineHandling(多机操作)
操作员能够操作两种以上的机器。
15.MultiProcessHandling(多流程操作)
操作员连续操作多个进程,能够促进材料的流动。
16.MultiTasking(多任务)
在一项活动完全回到原任务之前,将之分解为转换到另一任务之前的活动。