液态成型技术基础A
第一章 金属液态成形理论基础

第一节 液态金属充型能力与流动性
0、什么是液态金属的充型能力
1)定义:
液体金属充满铸型型腔,获得尺寸精确、轮廓清晰的 成型件的能力,称为充型能力。
2)充型能力对成型的影响
充型能力不足时,会产生浇不足、冷隔、夹渣、气孔 等缺陷。
3)影响充型能力的因素
充型能力首先取决于金属本身的流动性(流动能力),同 时又受铸型性质、浇注条件和铸件结构等因素影响。
一、铸件的凝固方式
在铸件凝固过程中,其断面上一般存在三个区 域:固相区、凝固区和液相区。
1、分类
依据对铸件质量影响较大的凝固区的宽窄划分 铸件的凝固方式为如下三类:
(1)逐层凝固
纯金属和共晶成分的合金在凝固过程中不存在液、固并 存的凝固区,随着温度下降,固体层不断加厚,液体不 断减少,直达铸件中心,这种凝固方式称为逐层凝固。
机械应力
二、铸件的变形及其防止
1、变形的原因:
铸件内部残余内应力。 只有原来受拉伸部分产生压缩 变形、受压缩部分产生拉伸变 形,才能使铸件中的残余内应 力减小或消除。
平板铸件的变形
杆件的变形
床身铸件的变形
粱形铸件的弯曲变形
2、防止措施:
减小应力; 将铸件设计成对称结构,使其内应力互相平衡; 采用反变形法; 设置拉肋; 时效处理。
2、冷裂纹的特征
裂纹细小,呈连续直线状,裂缝内有金属光泽或轻 微氧化色。
3、防止措施
凡是能减少铸件内应力和降低合金脆性的因素 均能防止冷裂。 设置防裂肋亦可有效地防止铸件裂纹。
防裂肋
三、合金的吸气性
液态合金中吸入的气体,若在冷凝过程中不能溢 出,滞留在金属中,将在铸件内形成气孔。
一)气孔的危害
气孔破坏了金属的连续性,减少了其承载的有效 截面积,并在气孔附近引起应力集中,从而降低 了铸件的力学性能。 弥散性气孔还可促使显微缩松的形成,降低铸件 的气密性。
材料成型基础

1、金属液态成形技术:熔炼金属,制造铸型,并将熔融金属浇入铸型,凝固后获得一定形状和性能铸件的成形方法称为液态成形。
简称铸造。
2、充型能力:液态合金充满铸型型腔,获得形状完整,轮廓清晰铸件的能力。
衡量充型能力可用所能形成的铸件最小壁厚。
充型能力的好与差,首先取决于铸造合金的流动性;同时又受到外界条件,如铸型性质、浇注条件、铸件结构等因素的影响,是各种因素的综合反映。
3、流动性:液态金属本身的流动能力。
衡量流动性一般采用螺旋试样长度。
金属的种类、成分、结晶特征及其它物理性能,决定了流动性4、收缩:金属液态、凝固及固态冷却过程中发生体积减少的现象。
5、铸件在冷却和凝固过程中,由于合金的液态收缩和凝固收缩,往往在铸件最后凝固的地方出现孔洞。
容积大而比较集中的孔洞称为缩孔;细小而分散的孔洞称为缩松。
6、缩孔形成条件:金属在恒温或较窄的温度范围内结晶,铸件由表及里逐层凝固。
缩松形成条件:金属结晶温度范围较宽,呈体积凝固方式(糊状凝固)。
7、铸件在凝固和随后的冷却过程中,固态收缩受到阻碍而引起的内应力,称为铸造应力。
热应力、相变应力、机械阻碍应力8、偏析:铸件(尤其是厚壁铸件)凝固后截面上不同部位,以至晶粒内部,产生化学成分不均匀的现象。
偏析产生的原因是由于各种铸造合金在结晶过程中发生了溶质再分配的结果。
9、熔炼:固态炉料按比例装入熔炉加热熔化,通过一系列冶金反应,转化成具有一定化学成分和温度符合铸造成形要求的液态金属。
10、金属熔化后,液态金属通过浇注系统充填铸型型腔的过程称为浇注过程。
11、浇注系统:铸型中液态金属流入铸型型腔的通道。
12、砂型铸造:以粘土砂为主要造型材料13、特种铸造:通过改变铸型材料、浇注方法、充型形式、凝固条件等形成的铸造技术14、金属固态塑性成形:在外力作用下,使金属材料产生预期的塑性变形,以获得所需的形状、尺寸和力学性能的毛坯或零件的加工方法。
15、金属塑性变形的能力又称为金属的可锻性,它指金属材料在塑性成形加工时获得优质毛坯或零件的难易程度。
材料成型原理及工艺第一章液态成型工艺基础理论
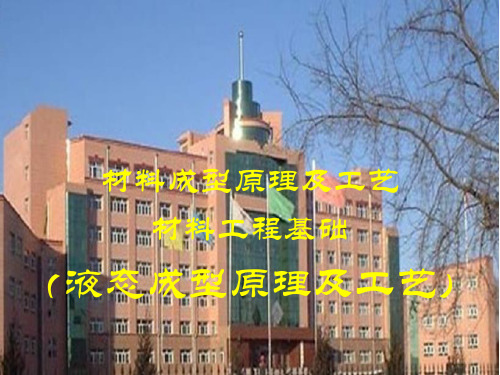
态 陷产生,导致成型件力学性能,
成 特别是冲击性能较低。
型 2. 涉及的工序很多,难以精确控
的 制,成型件质量不稳定。
缺 3.由于目前仍以砂型铸造为主,
点:
自动化程度还不很高,且属于热 加工行业,因而工作环境较差。
4.大多数成型件只是毛坯件,需 经过切削加工才能成为零件。
液态成型原理及工艺
冲天炉出铁
缸体等。
液态成型原理及工艺
液 (3) 成本较低
态
所用原料大都来源广泛,价格
成
低廉,一般不需要昂贵的设备。
型
的 (4)成型件尺寸精度高
优
成型件与最终零件的形状相似、
点:
尺寸相近,因而切削加工余量可 减少到最小,从而减少了金属材
料消耗,节省了切削加工工时。
液态成型原理及工艺
液
1. 组织疏松,晶粒粗大,成型件 内部常有缩孔、缩松、气孔等缺
液态成型原理及工艺
一、液态合金的流动性
1、合金流动性:是指液态合金本身的
流动能力。
合金的流动性用浇注 流动性试样的方法来 衡量。流动性试样的 种类很多,如螺旋形、 球形、α形、真空试 样等等,应用最多的 是螺旋形试样,如图11所示。
图1-1 液态成型原理及工艺
合金流动性主要取决于合金化学成分。对应着纯 金属、共晶点和形成金属间化合物的成分,流动 性出现最大值;而有结晶温度范围的合金,流动 性下降。这是因为纯金属和共晶成分的合金是在 恒温下结晶的,凝固层表面光滑,对尚未凝固的 金属液流动阻力小,因此流动性好;如图1-2a。
液态成型原理及工艺
绪 论 复习题
1、什么是液态成型?优缺点有哪些?
液态成型原理及工艺
第一章液态成型工艺基础理论
三种液态成形方法
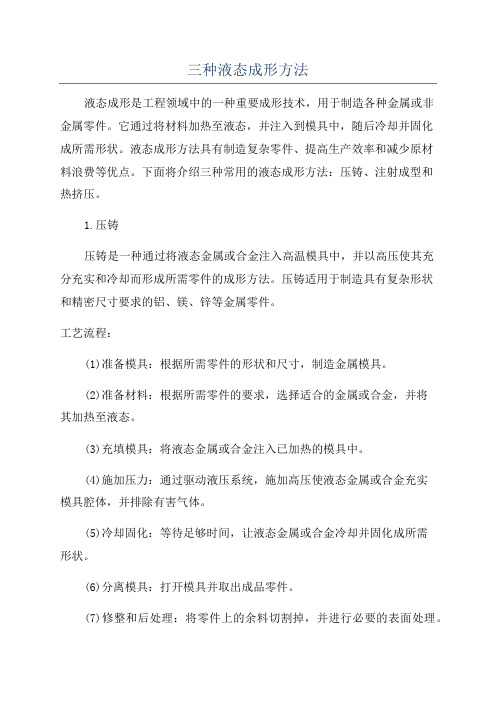
三种液态成形方法液态成形是工程领域中的一种重要成形技术,用于制造各种金属或非金属零件。
它通过将材料加热至液态,并注入到模具中,随后冷却并固化成所需形状。
液态成形方法具有制造复杂零件、提高生产效率和减少原材料浪费等优点。
下面将介绍三种常用的液态成形方法:压铸、注射成型和热挤压。
1.压铸压铸是一种通过将液态金属或合金注入高温模具中,并以高压使其充分充实和冷却而形成所需零件的成形方法。
压铸适用于制造具有复杂形状和精密尺寸要求的铝、镁、锌等金属零件。
工艺流程:(1)准备模具:根据所需零件的形状和尺寸,制造金属模具。
(2)准备材料:根据所需零件的要求,选择适合的金属或合金,并将其加热至液态。
(3)充填模具:将液态金属或合金注入已加热的模具中。
(4)施加压力:通过驱动液压系统,施加高压使液态金属或合金充实模具腔体,并排除有害气体。
(5)冷却固化:等待足够时间,让液态金属或合金冷却并固化成所需形状。
(6)分离模具:打开模具并取出成品零件。
(7)修整和后处理:将零件上的余料切割掉,并进行必要的表面处理。
2.注射成型注射成型是一种通过将液态或半液态塑料材料注入模具中,并在成型温度下固化成所需形状的成形方法。
注射成型适用于制造塑料零件,广泛应用于电子、汽车、日用品等领域。
工艺流程:(1)准备模具:根据所需零件的形状和尺寸,制造塑料模具。
(2)准备材料:选择适合注射成型的塑料树脂,并将其加热至液态或半液态。
(3)充填模具:将液态或半液态塑料注入已加热的模具中。
(4)冷却固化:等待足够时间,让塑料在模具中冷却并固化成所需形状。
(5)分离模具:打开模具并取出成品零件。
(6)修整和后处理:将零件上的余料切割掉,并进行必要的表面处理。
3.热挤压热挤压是一种通过将液态金属在高温和高压下通过模孔挤压成型的成形方法。
热挤压适用于制造具有长直形截面或复杂截面的杆、管和型材等零件。
工艺流程:(1)准备模具:根据所需零件的形状和尺寸,制造高温合金模具。
1-材料成形理论基础

材料成形工艺基础1第一章 材料成形理论基础液态成形--铸造 固态成形--锻造 固态连接--焊接21第一节 液态成形基础1、液态金属的结构液态金属在结构上更象固态而不是汽态,原子之间 仍然具有很高的结合能。
液态金属的结构特征 液态金属内存在近程有序的原子集团。
这种原子集团是不稳定 的,瞬时出现又瞬时消失。
所以,液态金属结构具有如下特 点: l)液态金属是由游动的原子团构成。
2)液态金属中的原子热运动强烈,原子所具有的能量各不相 同,且瞬息万变,这种原子间能量的不均匀性,称为能量起 伏。
3)由于液态原子处于能量起伏之中,原子团是时聚时散,时 大时小,此起彼伏的,称为结构起伏。
3第一节 液态成形基础1、液态金属的性质液态金属是有粘性的流体。
粘度的物理本质是原子间作 相对运动时产生的阻力。
表面张力:在液体表面内产生的平行于液体表面、且各 向均等的张力421.2铸件的凝固组织合金从液态转变成固态的过程,称为一次结晶 或凝固。
当液态金属冷却至熔点以下,经过一定时间的孕 育,就会涌现一批小晶核,随后这些晶核按原子规则 排列的各自取向长大,与此同时又有另一批小晶核生 成和长大,直至液体全部耗尽为止。
51.2铸件的凝固组织合金从液态转变成固态的过程,称为一次结晶 或凝固。
一次结晶从物理化学观点出发,研究液态金属的 生核Formation of stable nuclei 、长大Growth of crystals、结晶组织的形成规律。
凝固从传热学观点出发,研究铸件和铸型的传热过 程、铸件断面上凝固区域的变化规律、凝固方式与 铸件质量的关系、凝固缺陷形成机制等。
631.2铸件的凝固组织凝固组织分宏观和微观。
宏观组织:铸态晶粒的形态、大小、取向、分布 微观组织:晶粒内部的亚结构的形状/大小/相 对分布/缺陷等 晶粒越细小均匀,金属材料的强度和硬度越高,塑 性和韧性越好。
71.3铸件的凝固方式和控制铸件的工艺原则铸件的凝固方式逐层凝固方式(skin-forming solidification) 糊状凝固方式(mushy solidification) 中间凝固方式(middle solidification)。
材料成型技术基础第一章第五节与液态成形相关的新工艺、新技术简介

第五节与液态成形相关的新工艺、新技术简介一、模具快速成形技术快速成形(Rapid Prototyping,简称RP):利用材料堆积法制造实物产品的一项高新技术。
它能根据产品的三维模样数据,不借助其它工具设备,迅速而精确地制造出该产品,集中体现在计算机辅助设计、数控、激光加工、新材料开发等多学科、多技术的综合应用。
传统的零件制造过程往往需要车、钳、铣、刨、磨等多种机加工设备和各种工装、模具,成本高又费时间。
一个比较复杂的零件,其加工周期甚至以月计,很难适应低成本、高效率生产的要求。
快速成形技术是现代制造技术的一次重大变革。
(一)快速成形工艺快速成形技术就是利用三维CAD的数据,通过快速成形机,将一层层的材料堆积成实体原型。
迄今为止,国内、外已开发成功了10多种成熟的快速成形工艺,其中比较常用的有以下几种:1.纸层叠法—薄形材料选择性切割(LOM法)计算机控制的CO2激光束按三维实体模样每个截面轮廓对薄形材料(如底面涂胶的卷状纸、或正在研制的金属薄形材料等)进行切割,逐步得到各个轮廓,并将其粘结快速形成原型。
用此法可以制作铸造母模或用于“失纸精密铸造”。
2.激光立体制模法—液态光敏树脂选择性固化(SLA法)液槽盛满液态光敏树脂,它在计算机控制的激光束照射下会很快固化形成一层轮廓,新固化的一层牢固地粘结在前一层上,如此重复直至成形完毕,即快速形成原型。
激光立体制模法可以用来制作消失模,在熔模精密铸造中替代蜡模。
3.烧结法—粉末材料选择性激光烧结(SLS法)粉末材料可以是塑料、蜡、陶瓷、金属或它们复合物的粉体、覆膜砂等。
粉末材料薄薄地铺一层在工作台上,按截面轮廓的信息,CO2激光束扫过之处,粉末烧结成一定厚度的实体片层,逐层扫描烧结最终形成快速原型。
用此法可以直接制作精铸蜡模、实型铸造用消失模、用陶瓷制作铸造型壳和型芯、用覆膜砂制作铸型、以及铸造用母模等。
4.熔化沉积法—丝状材料选择性熔覆(FDM法)加热喷头在计算机的控制下,根据截面轮廓信息作X-Y平面运动和高度Z方向的运动,塑料、石腊质等丝材由供丝机构送至喷头,在喷头中加热、熔化,然后选择性地涂覆在工作台上,快速冷却后形成一层截面轮廓,层层叠加最终成为快速原型。
r001铸造-液态成形基础知识
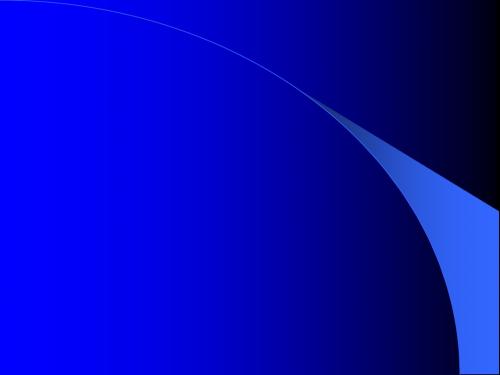
42
铸造过程质量控制(5)
铸件机械性能检测 1.硬度抽检 ---硬度计 2.抗拉强度(本体或单铸试棒)---万能试验机 3.延伸率、屈服强度(球铁) ---万能试验机 铸件金相检查 1.石墨形态 ---金相显微镜 2.基体组织 ---金相显微镜 铸件出厂前检查 1.尺寸检查 ---检具、测量、三坐标 2.外观缺陷检查 ---目视 3.抽样加工检查 ---切割、机械、X光
3. 铸件的凝固原则 solidification Principle
顺序凝固原则: Directional Solidification
在铸件上从远离冒口或 浇口到冒口或浇口之 间建立一个递增的温 度梯度,从而实现由 远离冒口的部分向冒 口的方向顺序地凝固。
同时凝固原则: Simultaneously Solidification 是采取工艺措施保 证铸件结构上各部 分之间没有温差或 温差尽量小,使各 部分同时凝固。如 图所示。
型砂混制过程中的质量控制 1.湿压强度 5.有效膨润土含量 2.水份 6.烧灼减量 3.紧实率 7.型砂温度 4.透气性
39
铸造过程质量控制(2)
铁水熔化过程中的质量控制 1.原材料进厂检验:生铁、废钢等 2.炉料配比:生铁+废钢+回炉料+铁合金 3.熔化后铁水的化学成分:碳、硅、锰、磷、 硫、铜、锡、钛、钒、铝、镁……. 4.熔化温度 5.出铁温度 6.球化反应
43
1-1 液态成形基础知识
一、金属的凝固 Melt Solidification
1. 液态金属的结构与性质 液态金属由许多近程有序排列的“游动 的原子集团”所组成,瞬间存在、瞬间消 失。
– 原子的排列和原有的固体相似 – 存在很大的能量起伏,热运动很强 – 温度越高,原子集团越小,游动越快。
材料成形工艺-液态金属铸造成形工艺基础

5
第一章 液态金属铸造成形工艺基础
一、基本工艺要素及其控制
一、基本工艺要素及其控制
★ 铸造的基本工艺要素:
成分
温度
熔融金属液
结构
材质
温度
预先制备的铸型
6
第一章 液态金属铸造成形工艺基础
一、基本工艺要素及其控制
一、基本工艺要素及其控制
1、金属液应满足以下要求:
成分符合要求——各元素含量在标称范围内 合金液含气量、杂质含量在允许范围内
3、铸型与金属之间的相互作用
3.2、热作用: 冷却速度超出适当的工艺窗口 导致亚稳相的形成
型壁表面变形开裂 铸件表面质量差、夹砂结疤
金属液热量迅速导入铸型表层 热击——铸型破裂或表面龟裂
17
第一章 液态金属铸造成形工艺基础
一、基本工艺要素及其控制
3、铸型与金属之间的相互作用
3.2、热作用不良导致的缺陷:
应当注意气孔缺陷与疏松缺陷的差别和关联。
20
第一章 液态金属铸造成形工艺基础
一、基本工艺要素及其控制
3、铸型与金属之间的相互作用
铸件中气孔的形成:
卷入气孔的形成
气孔的一般分布区域
21
第一章 液态金属铸造成形工艺基础
一、基本工艺要素及其控制
一、基本工艺要素及其控制
4、常用铸造合金及其熔炼:
黑色金属——
14
第一章 液态金属铸造成形工艺基础
一、基本工艺要素及其控制
一、基本工艺要素及其控制
3、铸型与金属之间的相互作用:
机械作用: 金属液在进入型腔时对铸型的冲刷作用; 金属液充入型腔后对铸型壁面的压力作用; 铸型对金属凝固收缩而产生的阻碍作用。
热 作 用: 金属热量向铸型的换热传输作用。
- 1、下载文档前请自行甄别文档内容的完整性,平台不提供额外的编辑、内容补充、找答案等附加服务。
- 2、"仅部分预览"的文档,不可在线预览部分如存在完整性等问题,可反馈申请退款(可完整预览的文档不适用该条件!)。
- 3、如文档侵犯您的权益,请联系客服反馈,我们会尽快为您处理(人工客服工作时间:9:00-18:30)。
湖南大学课程考试试卷
以通过哪些工艺措施来改变或控制凝固速度?(10分)
2、论述缩孔的形成过程,并讨论分析缩孔与缩松的形成条件及形成原因的异
同点。
(12分)
四、计算题(共24分)
1、过共析钢液η=0.0049Pa﹒S,钢液的密度为7000kg/m3,表面张力为1500mN/m,
加铝脱氧,生成密度为5400 kg/m3 的Al
2O
3
,如能使Al
2
O
3
颗粒上浮到钢液表面
就能获得质量较好的钢。
假如脱氧产物在1524mm 深处生成,试确定钢液脱氧后
2min上浮到钢液表面的Al
2O
3
最小颗粒的尺寸。
(10分)
2、某二元合金相图如下所示。
合金液成分为C
B
=40%,置于长瓷舟中并从左端开始凝固。
温度梯度大到足以使固-液界面保持平面生长。
假设固相无扩散,液相均匀混合。
试求:
①α相与液相之间的平衡分配系数K0;
②凝固后共晶体的数量占试棒长度的百分之几?
③画出凝固后的试棒中溶质B 的浓度沿试棒长度的分布曲线,并注明各特征成分及其位置。
(14分)。