Simulation on the Dynamic Pressure and Flow of the
仿真建模实践和理论 英文文献
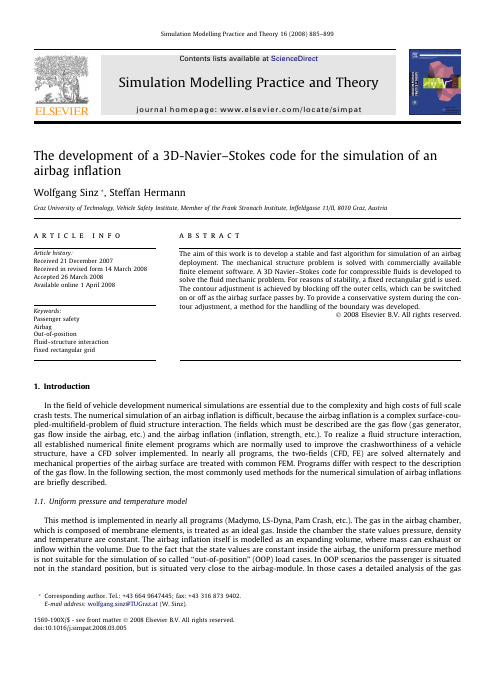
properties is decisive to get a simulation model with the required accuracy [10]. But the assumption that the values are constant has only a marginal influence on the overall shape of the airbag at the end of the inflation.
article info
Article history: Received 21 December 2007 Received in revised form 14 March 2008 Accepted 26 March 2008 Available online 1 April 2008
Keywords: Passenger safety Airbag Out-of-position Fluid–structure interaction Fixed rectangular grid
1.2. Finite pointset method (FPM)
The FPM method was originally developed by Kuhnert [11] and is a grid free method which is based on the Lagrange approach. The values which describe the gas flow (velocity, density and temperature) are stored on freely positioned particles. These particles move with the local flow velocity. Due to the fact that the FPM needs no grid the FPM method is suitable for applications in which the geometry of the flow area changes strongly over time. A lot of integration points (smoothing length of about 15 mm [6]) are required for adequate results, thus the calculation time is considerably greater.
基于绕组分布函数理论和动态磁网络的两种内置式永磁牵引电机解析建模方法
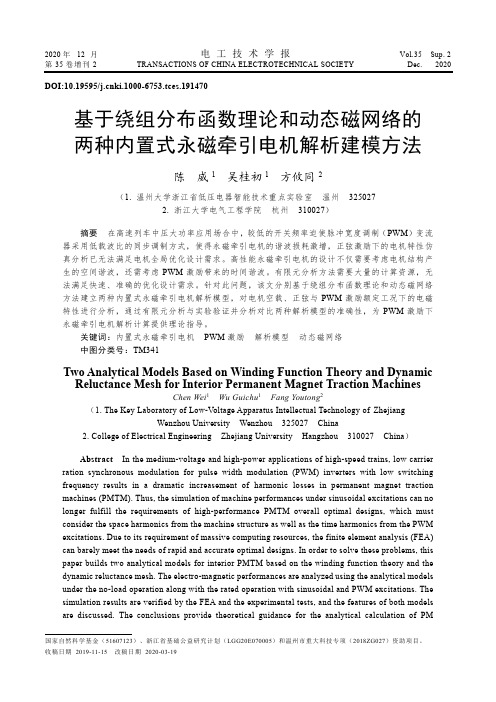
2020年12月电工技术学报Vol.35 Sup. 2 第35卷增刊2 TRANSACTIONS OF CHINA ELECTROTECHNICAL SOCIETY Dec. 2020 DOI:10.19595/ki.1000-6753.tces.191470基于绕组分布函数理论和动态磁网络的两种内置式永磁牵引电机解析建模方法陈威1吴桂初1方攸同2(1. 温州大学浙江省低压电器智能技术重点实验室温州 3250272. 浙江大学电气工程学院杭州 310027)摘要在高速列车中压大功率应用场合中,较低的开关频率迫使脉冲宽度调制(PWM)变流器采用低载波比的同步调制方式,使得永磁牵引电机的谐波损耗激增,正弦激励下的电机特性仿真分析已无法满足电机全局优化设计需求。
高性能永磁牵引电机的设计不仅需要考虑电机结构产生的空间谐波,还需考虑PWM激励带来的时间谐波。
有限元分析方法需要大量的计算资源,无法满足快速、准确的优化设计需求。
针对此问题,该文分别基于绕组分布函数理论和动态磁网络方法建立两种内置式永磁牵引电机解析模型,对电机空载、正弦与PWM激励额定工况下的电磁特性进行分析,通过有限元分析与实验验证并分析对比两种解析模型的准确性,为PWM激励下永磁牵引电机解析计算提供理论指导。
关键词:内置式永磁牵引电机PWM激励解析模型动态磁网络中图分类号:TM341Two Analytical Models Based on Winding Function Theory and DynamicReluctance Mesh for Interior Permanent Magnet Traction MachinesChen Wei1Wu Guichu1 Fang Youtong2(1. The Key Laboratory of Low-Voltage Apparatus Intellectual Technology of ZhejiangWenzhou University Wenzhou 325027 China2. College of Electrical Engineering Zhejiang University Hangzhou 310027 China)Abstract In the medium-voltage and high-power applications of high-speed trains, low carrier ration synchronous modulation for pulse width modulation (PWM) inverters with low switching frequency results in a dramatic increasement of harmonic losses in permanent magnet traction machines (PMTM). Thus, the simulation of machine performances under sinusoidal excitations can no longer fulfill the requirements of high-performance PMTM overall optimal designs, which must consider the space harmonics from the machine structure as well as the time harmonics from the PWM excitations. Due to its requirement of massive computing resources, the finite element analysis (FEA) can barely meet the needs of rapid and accurate optimal designs. In order to solve these problems, this paper builds two analytical models for interior PMTM based on the winding function theory and the dynamic reluctance mesh. The electro-magnetic performances are analyzed using the analytical models under the no-load operation along with the rated operation with sinusoidal and PWM excitations. The simulation results are verified by the FEA and the experimental tests, and the features of both models are discussed. The conclusions provide theoretical guidance for the analytical calculation of PM国家自然科学基金(51607123)、浙江省基础公益研究计划(LGG20E070005)和温州市重大科技专项(2018ZG027)资助项目。
Modeling the Spatial Dynamics of Regional Land Use_The CLUE-S Model

Modeling the Spatial Dynamics of Regional Land Use:The CLUE-S ModelPETER H.VERBURG*Department of Environmental Sciences Wageningen UniversityP.O.Box376700AA Wageningen,The NetherlandsandFaculty of Geographical SciencesUtrecht UniversityP.O.Box801153508TC Utrecht,The NetherlandsWELMOED SOEPBOERA.VELDKAMPDepartment of Environmental Sciences Wageningen UniversityP.O.Box376700AA Wageningen,The NetherlandsRAMIL LIMPIADAVICTORIA ESPALDONSchool of Environmental Science and Management University of the Philippines Los Ban˜osCollege,Laguna4031,Philippines SHARIFAH S.A.MASTURADepartment of GeographyUniversiti Kebangsaan Malaysia43600BangiSelangor,MalaysiaABSTRACT/Land-use change models are important tools for integrated environmental management.Through scenario analysis they can help to identify near-future critical locations in the face of environmental change.A dynamic,spatially ex-plicit,land-use change model is presented for the regional scale:CLUE-S.The model is specifically developed for the analysis of land use in small regions(e.g.,a watershed or province)at afine spatial resolution.The model structure is based on systems theory to allow the integrated analysis of land-use change in relation to socio-economic and biophysi-cal driving factors.The model explicitly addresses the hierar-chical organization of land use systems,spatial connectivity between locations and stability.Stability is incorporated by a set of variables that define the relative elasticity of the actual land-use type to conversion.The user can specify these set-tings based on expert knowledge or survey data.Two appli-cations of the model in the Philippines and Malaysia are used to illustrate the functioning of the model and its validation.Land-use change is central to environmental man-agement through its influence on biodiversity,water and radiation budgets,trace gas emissions,carbon cy-cling,and livelihoods(Lambin and others2000a, Turner1994).Land-use planning attempts to influence the land-use change dynamics so that land-use config-urations are achieved that balance environmental and stakeholder needs.Environmental management and land-use planning therefore need information about the dynamics of land use.Models can help to understand these dynamics and project near future land-use trajectories in order to target management decisions(Schoonenboom1995).Environmental management,and land-use planning specifically,take place at different spatial and organisa-tional levels,often corresponding with either eco-re-gional or administrative units,such as the national or provincial level.The information needed and the man-agement decisions made are different for the different levels of analysis.At the national level it is often suffi-cient to identify regions that qualify as“hot-spots”of land-use change,i.e.,areas that are likely to be faced with rapid land use conversions.Once these hot-spots are identified a more detailed land use change analysis is often needed at the regional level.At the regional level,the effects of land-use change on natural resources can be determined by a combina-tion of land use change analysis and specific models to assess the impact on natural resources.Examples of this type of model are water balance models(Schulze 2000),nutrient balance models(Priess and Koning 2001,Smaling and Fresco1993)and erosion/sedimen-tation models(Schoorl and Veldkamp2000).Most of-KEY WORDS:Land-use change;Modeling;Systems approach;Sce-nario analysis;Natural resources management*Author to whom correspondence should be addressed;email:pverburg@gissrv.iend.wau.nlDOI:10.1007/s00267-002-2630-x Environmental Management Vol.30,No.3,pp.391–405©2002Springer-Verlag New York Inc.ten these models need high-resolution data for land use to appropriately simulate the processes involved.Land-Use Change ModelsThe rising awareness of the need for spatially-ex-plicit land-use models within the Land-Use and Land-Cover Change research community(LUCC;Lambin and others2000a,Turner and others1995)has led to the development of a wide range of land-use change models.Whereas most models were originally devel-oped for deforestation(reviews by Kaimowitz and An-gelsen1998,Lambin1997)more recent efforts also address other land use conversions such as urbaniza-tion and agricultural intensification(Brown and others 2000,Engelen and others1995,Hilferink and Rietveld 1999,Lambin and others2000b).Spatially explicit ap-proaches are often based on cellular automata that simulate land use change as a function of land use in the neighborhood and a set of user-specified relations with driving factors(Balzter and others1998,Candau 2000,Engelen and others1995,Wu1998).The speci-fication of the neighborhood functions and transition rules is done either based on the user’s expert knowl-edge,which can be a problematic process due to a lack of quantitative understanding,or on empirical rela-tions between land use and driving factors(e.g.,Pi-janowski and others2000,Pontius and others2000).A probability surface,based on either logistic regression or neural network analysis of historic conversions,is made for future conversions.Projections of change are based on applying a cut-off value to this probability sur-face.Although appropriate for short-term projections,if the trend in land-use change continues,this methodology is incapable of projecting changes when the demands for different land-use types change,leading to a discontinua-tion of the trends.Moreover,these models are usually capable of simulating the conversion of one land-use type only(e.g.deforestation)because they do not address competition between land-use types explicitly.The CLUE Modeling FrameworkThe Conversion of Land Use and its Effects(CLUE) modeling framework(Veldkamp and Fresco1996,Ver-burg and others1999a)was developed to simulate land-use change using empirically quantified relations be-tween land use and its driving factors in combination with dynamic modeling.In contrast to most empirical models,it is possible to simulate multiple land-use types simultaneously through the dynamic simulation of competition between land-use types.This model was developed for the national and con-tinental level,applications are available for Central America(Kok and Winograd2001),Ecuador(de Kon-ing and others1999),China(Verburg and others 2000),and Java,Indonesia(Verburg and others 1999b).For study areas with such a large extent the spatial resolution of analysis was coarse(pixel size vary-ing between7ϫ7and32ϫ32km).This is a conse-quence of the impossibility to acquire data for land use and all driving factors atfiner spatial resolutions.A coarse spatial resolution requires a different data rep-resentation than the common representation for data with afine spatial resolution.Infine resolution grid-based approaches land use is defined by the most dom-inant land-use type within the pixel.However,such a data representation would lead to large biases in the land-use distribution as some class proportions will di-minish and other will increase with scale depending on the spatial and probability distributions of the cover types(Moody and Woodcock1994).In the applications of the CLUE model at the national or continental level we have,therefore,represented land use by designating the relative cover of each land-use type in each pixel, e.g.a pixel can contain30%cultivated land,40%grass-land,and30%forest.This data representation is di-rectly related to the information contained in the cen-sus data that underlie the applications.For each administrative unit,census data denote the number of hectares devoted to different land-use types.When studying areas with a relatively small spatial ex-tent,we often base our land-use data on land-use maps or remote sensing images that denote land-use types respec-tively by homogeneous polygons or classified pixels. When converted to a raster format this results in only one, dominant,land-use type occupying one unit of analysis. The validity of this data representation depends on the patchiness of the landscape and the pixel size chosen. Most sub-national land use studies use this representation of land use with pixel sizes varying between a few meters up to about1ϫ1km.The two different data represen-tations are shown in Figure1.Because of the differences in data representation and other features that are typical for regional appli-cations,the CLUE model can not directly be applied at the regional scale.This paper describes the mod-ified modeling approach for regional applications of the model,now called CLUE-S(the Conversion of Land Use and its Effects at Small regional extent). The next section describes the theories underlying the development of the model after which it is de-scribed how these concepts are incorporated in the simulation model.The functioning of the model is illustrated for two case-studies and is followed by a general discussion.392P.H.Verburg and othersCharacteristics of Land-Use SystemsThis section lists the main concepts and theories that are prevalent for describing the dynamics of land-use change being relevant for the development of land-use change models.Land-use systems are complex and operate at the interface of multiple social and ecological systems.The similarities between land use,social,and ecological systems allow us to use concepts that have proven to be useful for studying and simulating ecological systems in our analysis of land-use change (Loucks 1977,Adger 1999,Holling and Sanderson 1996).Among those con-cepts,connectivity is important.The concept of con-nectivity acknowledges that locations that are at a cer-tain distance are related to each other (Green 1994).Connectivity can be a direct result of biophysical pro-cesses,e.g.,sedimentation in the lowlands is a direct result of erosion in the uplands,but more often it is due to the movement of species or humans through the nd degradation at a certain location will trigger farmers to clear land at a new location.Thus,changes in land use at this new location are related to the land-use conditions in the other location.In other instances more complex relations exist that are rooted in the social and economic organization of the system.The hierarchical structure of social organization causes some lower level processes to be constrained by higher level dynamics,e.g.,the establishments of a new fruit-tree plantation in an area near to the market might in fluence prices in such a way that it is no longer pro fitable for farmers to produce fruits in more distant areas.For studying this situation an-other concept from ecology,hierarchy theory,is use-ful (Allen and Starr 1982,O ’Neill and others 1986).This theory states that higher level processes con-strain lower level processes whereas the higher level processes might emerge from lower level dynamics.This makes the analysis of the land-use system at different levels of analysis necessary.Connectivity implies that we cannot understand land use at a certain location by solely studying the site characteristics of that location.The situation atneigh-Figure 1.Data representation and land-use model used for respectively case-studies with a national/continental extent and local/regional extent.Modeling Regional Land-Use Change393boring or even more distant locations can be as impor-tant as the conditions at the location itself.Land-use and land-cover change are the result of many interacting processes.Each of these processes operates over a range of scales in space and time.These processes are driven by one or more of these variables that influence the actions of the agents of land-use and cover change involved.These variables are often re-ferred to as underlying driving forces which underpin the proximate causes of land-use change,such as wood extraction or agricultural expansion(Geist and Lambin 2001).These driving factors include demographic fac-tors(e.g.,population pressure),economic factors(e.g., economic growth),technological factors,policy and institutional factors,cultural factors,and biophysical factors(Turner and others1995,Kaimowitz and An-gelsen1998).These factors influence land-use change in different ways.Some of these factors directly influ-ence the rate and quantity of land-use change,e.g.the amount of forest cleared by new incoming migrants. Other factors determine the location of land-use change,e.g.the suitability of the soils for agricultural land use.Especially the biophysical factors do pose constraints to land-use change at certain locations, leading to spatially differentiated pathways of change.It is not possible to classify all factors in groups that either influence the rate or location of land-use change.In some cases the same driving factor has both an influ-ence on the quantity of land-use change as well as on the location of land-use change.Population pressure is often an important driving factor of land-use conver-sions(Rudel and Roper1997).At the same time it is the relative population pressure that determines which land-use changes are taking place at a certain location. Intensively cultivated arable lands are commonly situ-ated at a limited distance from the villages while more extensively managed grasslands are often found at a larger distance from population concentrations,a rela-tion that can be explained by labor intensity,transport costs,and the quality of the products(Von Thu¨nen 1966).The determination of the driving factors of land use changes is often problematic and an issue of dis-cussion(Lambin and others2001).There is no unify-ing theory that includes all processes relevant to land-use change.Reviews of case studies show that it is not possible to simply relate land-use change to population growth,poverty,and infrastructure.Rather,the inter-play of several proximate as well as underlying factors drive land-use change in a synergetic way with large variations caused by location specific conditions (Lambin and others2001,Geist and Lambin2001).In regional modeling we often need to rely on poor data describing this complexity.Instead of using the under-lying driving factors it is needed to use proximate vari-ables that can represent the underlying driving factors. Especially for factors that are important in determining the location of change it is essential that the factor can be mapped quantitatively,representing its spatial vari-ation.The causality between the underlying driving factors and the(proximate)factors used in modeling (in this paper,also referred to as“driving factors”) should be certified.Other system properties that are relevant for land-use systems are stability and resilience,concepts often used to describe ecological systems and,to some extent, social systems(Adger2000,Holling1973,Levin and others1998).Resilience refers to the buffer capacity or the ability of the ecosystem or society to absorb pertur-bations,or the magnitude of disturbance that can be absorbed before a system changes its structure by changing the variables and processes that control be-havior(Holling1992).Stability and resilience are con-cepts that can also be used to describe the dynamics of land-use systems,that inherit these characteristics from both ecological and social systems.Due to stability and resilience of the system disturbances and external in-fluences will,mostly,not directly change the landscape structure(Conway1985).After a natural disaster lands might be abandoned and the population might tempo-rally migrate.However,people will in most cases return after some time and continue land-use management practices as before,recovering the land-use structure (Kok and others2002).Stability in the land-use struc-ture is also a result of the social,economic,and insti-tutional structure.Instead of a direct change in the land-use structure upon a fall in prices of a certain product,farmers will wait a few years,depending on the investments made,before they change their cropping system.These characteristics of land-use systems provide a number requirements for the modelling of land-use change that have been used in the development of the CLUE-S model,including:●Models should not analyze land use at a single scale,but rather include multiple,interconnected spatial scales because of the hierarchical organization of land-use systems.●Special attention should be given to the drivingfactors of land-use change,distinguishing drivers that determine the quantity of change from drivers of the location of change.●Sudden changes in driving factors should not di-rectly change the structure of the land-use system asa consequence of the resilience and stability of theland-use system.394P.H.Verburg and others●The model structure should allow spatial interac-tions between locations and feedbacks from higher levels of organization.Model DescriptionModel StructureThe model is sub-divided into two distinct modules,namely a non-spatial demand module and a spatially explicit allocation procedure (Figure 2).The non-spa-tial module calculates the area change for all land-use types at the aggregate level.Within the second part of the model these demands are translated into land-use changes at different locations within the study region using a raster-based system.For the land-use demand module,different alterna-tive model speci fications are possible,ranging from simple trend extrapolations to complex economic mod-els.The choice for a speci fic model is very much de-pendent on the nature of the most important land-use conversions taking place within the study area and the scenarios that need to be considered.Therefore,the demand calculations will differ between applications and scenarios and need to be decided by the user for the speci fic situation.The results from the demandmodule need to specify,on a yearly basis,the area covered by the different land-use types,which is a direct input for the allocation module.The rest of this paper focuses on the procedure to allocate these demands to land-use conversions at speci fic locations within the study area.The allocation is based upon a combination of em-pirical,spatial analysis,and dynamic modelling.Figure 3gives an overview of the procedure.The empirical analysis unravels the relations between the spatial dis-tribution of land use and a series of factors that are drivers and constraints of land use.The results of this empirical analysis are used within the model when sim-ulating the competition between land-use types for a speci fic location.In addition,a set of decision rules is speci fied by the user to restrict the conversions that can take place based on the actual land-use pattern.The different components of the procedure are now dis-cussed in more detail.Spatial AnalysisThe pattern of land use,as it can be observed from an airplane window or through remotely sensed im-ages,reveals the spatial organization of land use in relation to the underlying biophysical andsocio-eco-Figure 2.Overview of the modelingprocedure.Figure 3.Schematic represen-tation of the procedure to allo-cate changes in land use to a raster based map.Modeling Regional Land-Use Change395nomic conditions.These observations can be formal-ized by overlaying this land-use pattern with maps de-picting the variability in biophysical and socio-economic conditions.Geographical Information Systems(GIS)are used to process all spatial data and convert these into a regular grid.Apart from land use, data are gathered that represent the assumed driving forces of land use in the study area.The list of assumed driving forces is based on prevalent theories on driving factors of land-use change(Lambin and others2001, Kaimowitz and Angelsen1998,Turner and others 1993)and knowledge of the conditions in the study area.Data can originate from remote sensing(e.g., land use),secondary statistics(e.g.,population distri-bution),maps(e.g.,soil),and other sources.To allow a straightforward analysis,the data are converted into a grid based system with a cell size that depends on the resolution of the available data.This often involves the aggregation of one or more layers of thematic data,e.g. it does not make sense to use a30-m resolution if that is available for land-use data only,while the digital elevation model has a resolution of500m.Therefore, all data are aggregated to the same resolution that best represents the quality and resolution of the data.The relations between land use and its driving fac-tors are thereafter evaluated using stepwise logistic re-gression.Logistic regression is an often used method-ology in land-use change research(Geoghegan and others2001,Serneels and Lambin2001).In this study we use logistic regression to indicate the probability of a certain grid cell to be devoted to a land-use type given a set of driving factors following:LogͩP i1ϪP i ͪϭ0ϩ1X1,iϩ2X2,i......ϩn X n,iwhere P i is the probability of a grid cell for the occur-rence of the considered land-use type and the X’s are the driving factors.The stepwise procedure is used to help us select the relevant driving factors from a larger set of factors that are assumed to influence the land-use pattern.Variables that have no significant contribution to the explanation of the land-use pattern are excluded from thefinal regression equation.Where in ordinal least squares regression the R2 gives a measure of modelfit,there is no equivalent for logistic regression.Instead,the goodness offit can be evaluated with the ROC method(Pontius and Schnei-der2000,Swets1986)which evaluates the predicted probabilities by comparing them with the observed val-ues over the whole domain of predicted probabilities instead of only evaluating the percentage of correctly classified observations at afixed cut-off value.This is an appropriate methodology for our application,because we will use a wide range of probabilities within the model calculations.The influence of spatial autocorrelation on the re-gression results can be minimized by only performing the regression on a random sample of pixels at a certain minimum distance from one another.Such a selection method is adopted in order to maximize the distance between the selected pixels to attenuate the problem associated with spatial autocorrelation.For case-studies where autocorrelation has an important influence on the land-use structure it is possible to further exploit it by incorporating an autoregressive term in the regres-sion equation(Overmars and others2002).Based upon the regression results a probability map can be calculated for each land-use type.A new probabil-ity map is calculated every year with updated values for the driving factors that are projected to change in time,such as the population distribution or accessibility.Decision RulesLand-use type or location specific decision rules can be specified by the user.Location specific decision rules include the delineation of protected areas such as nature reserves.If a protected area is specified,no changes are allowed within this area.For each land-use type decision rules determine the conditions under which the land-use type is allowed to change in the next time step.These decision rules are implemented to give certain land-use types a certain resistance to change in order to generate the stability in the land-use structure that is typical for many landscapes.Three different situations can be distinguished and for each land-use type the user should specify which situation is most relevant for that land-use type:1.For some land-use types it is very unlikely that theyare converted into another land-use type after their first conversion;as soon as an agricultural area is urbanized it is not expected to return to agriculture or to be converted into forest cover.Unless a de-crease in area demand for this land-use type occurs the locations covered by this land use are no longer evaluated for potential land-use changes.If this situation is selected it also holds that if the demand for this land-use type decreases,there is no possi-bility for expansion in other areas.In other words, when this setting is applied to forest cover and deforestation needs to be allocated,it is impossible to reforest other areas at the same time.2.Other land-use types are converted more easily.Aswidden agriculture system is most likely to be con-verted into another land-use type soon after its396P.H.Verburg and othersinitial conversion.When this situation is selected for a land-use type no restrictions to change are considered in the allocation module.3.There is also a number of land-use types that oper-ate in between these two extremes.Permanent ag-riculture and plantations require an investment for their establishment.It is therefore not very likely that they will be converted very soon after into another land-use type.However,in the end,when another land-use type becomes more pro fitable,a conversion is possible.This situation is dealt with by de fining the relative elasticity for change (ELAS u )for the land-use type into any other land use type.The relative elasticity ranges between 0(similar to Situation 2)and 1(similar to Situation 1).The higher the de fined elasticity,the more dif ficult it gets to convert this land-use type.The elasticity should be de fined based on the user ’s knowledge of the situation,but can also be tuned during the calibration of the petition and Actual Allocation of Change Allocation of land-use change is made in an iterative procedure given the probability maps,the decision rules in combination with the actual land-use map,and the demand for the different land-use types (Figure 4).The following steps are followed in the calculation:1.The first step includes the determination of all grid cells that are allowed to change.Grid cells that are either part of a protected area or under a land-use type that is not allowed to change (Situation 1,above)are excluded from further calculation.2.For each grid cell i the total probability (TPROP i,u )is calculated for each of the land-use types u accord-ing to:TPROP i,u ϭP i,u ϩELAS u ϩITER u ,where ITER u is an iteration variable that is speci fic to the land use.ELAS u is the relative elasticity for change speci fied in the decision rules (Situation 3de-scribed above)and is only given a value if grid-cell i is already under land use type u in the year considered.ELAS u equals zero if all changes are allowed (Situation 2).3.A preliminary allocation is made with an equalvalue of the iteration variable (ITER u )for all land-use types by allocating the land-use type with the highest total probability for the considered grid cell.This will cause a number of grid cells to change land use.4.The total allocated area of each land use is nowcompared to the demand.For land-use types where the allocated area is smaller than the demanded area the value of the iteration variable is increased.For land-use types for which too much is allocated the value is decreased.5.Steps 2to 4are repeated as long as the demandsare not correctly allocated.When allocation equals demand the final map is saved and the calculations can continue for the next yearly timestep.Figure 5shows the development of the iteration parameter ITER u for different land-use types during asimulation.Figure 4.Representation of the iterative procedure for land-use changeallocation.Figure 5.Change in the iteration parameter (ITER u )during the simulation within one time-step.The different lines rep-resent the iteration parameter for different land-use types.The parameter is changed for all land-use types synchronously until the allocated land use equals the demand.Modeling Regional Land-Use Change397Multi-Scale CharacteristicsOne of the requirements for land-use change mod-els are multi-scale characteristics.The above described model structure incorporates different types of scale interactions.Within the iterative procedure there is a continuous interaction between macro-scale demands and local land-use suitability as determined by the re-gression equations.When the demand changes,the iterative procedure will cause the land-use types for which demand increased to have a higher competitive capacity (higher value for ITER u )to ensure enough allocation of this land-use type.Instead of only being determined by the local conditions,captured by the logistic regressions,it is also the regional demand that affects the actually allocated changes.This allows the model to “overrule ”the local suitability,it is not always the land-use type with the highest probability according to the logistic regression equation (P i,u )that the grid cell is allocated to.Apart from these two distinct levels of analysis there are also driving forces that operate over a certain dis-tance instead of being locally important.Applying a neighborhood function that is able to represent the regional in fluence of the data incorporates this type of variable.Population pressure is an example of such a variable:often the in fluence of population acts over a certain distance.Therefore,it is not the exact location of peoples houses that determines the land-use pattern.The average population density over a larger area is often a more appropriate variable.Such a population density surface can be created by a neighborhood func-tion using detailed spatial data.The data generated this way can be included in the spatial analysis as anotherindependent factor.In the application of the model in the Philippines,described hereafter,we applied a 5ϫ5focal filter to the population map to generate a map representing the general population pressure.Instead of using these variables,generated by neighborhood analysis,it is also possible to use the more advanced technique of multi-level statistics (Goldstein 1995),which enable a model to include higher-level variables in a straightforward manner within the regression equa-tion (Polsky and Easterling 2001).Application of the ModelIn this paper,two examples of applications of the model are provided to illustrate its function.TheseTable nd-use classes and driving factors evaluated for Sibuyan IslandLand-use classes Driving factors (location)Forest Altitude (m)GrasslandSlope Coconut plantation AspectRice fieldsDistance to town Others (incl.mangrove and settlements)Distance to stream Distance to road Distance to coast Distance to port Erosion vulnerability GeologyPopulation density(neighborhood 5ϫ5)Figure 6.Location of the case-study areas.398P.H.Verburg and others。
机器人英语翻译
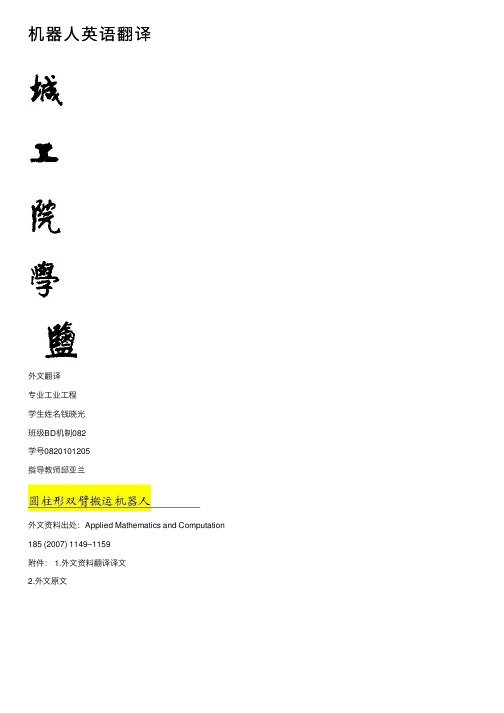
机器⼈英语翻译外⽂翻译专业⼯业⼯程学⽣姓名钱晓光班级BD机制082学号0820101205指导教师邱亚兰外⽂资料出处:Applied Mathematics and Computation 185 (2007) 1149–1159附件: 1.外⽂资料翻译译⽂2.外⽂原⽂灵活的双臂空间机器⼈捕捉物体的控制动⼒学译者:钱晓光⽂摘:在本⽂中,我们提出有效载荷的影响,来控制⼀个双臂空间机器⼈灵活的获取⼀个物体。
该拉格朗⽇公式动⼒学模型推导出了机器⼈系统原理。
源⾃初始条件的动⼒学模型模拟了整个系统的获取过程。
⼀个PD控制器设计,其⽬的是为了稳定机器⼈来捕捉对象,动态模拟执⾏例⼦:例:1.机器⼈系统不受控制发⽣撞击,仿真结果表明影响效果。
2.空间机器⼈捕获物体的成功是伟⼤的。
仿真结果表明,该机器⼈关节⾓和机械⼿的迅速程度已经达到稳定。
关键词:柔性臂;空间机器⼈;冲击;动⼒学;PD控制⽅案:圆柱型机器⼈;技能训练1.介绍空间机器⼈将成为⼈类未来在太空检验、装配和检索故障等⽇常⼯作的主要元素。
空间机器⼈满⾜宇航员额外的活动,对这些来说是很有价值的。
然⽽,⼈类⽣活配套设施的成本和时间对航员是有限制的,⾼度风险使空间机器⼈成为宇航员助⼿的选择。
增加设备的流动性, ⾃由飞⾏系统中⼀个或多个臂安装在⼀艘装有推进器⾥,然⽽,扩展推进器的使⽤却得到了极⼤的限制。
⼀个⾃由浮动的操作模式能增加系统的可操作性。
有很多的研究成果对刚性臂空间机器⼈做了研究。
考虑到空间机器⼈以下的特点:轻质量、长臂、重载荷、灵活、有效性等,切应考虑到良好的控制精度和性能。
与此同时,也存在着许多研究动态建模和单臂空间机器⼈灵活控制的成果。
作者描述了碰撞动⼒学建模⽅案的空间机器⼈和研究了多⼿臂灵活空间机器⼈。
吴中书使⽤假设模态⽅法描述了弹性变形,建⽴了动态模型,研究了拉格朗⽇公式和仿真的柔性双臂空间机械臂。
由两个特定操作阶段:影响阶段和撞击阶段。
影响阶段确定了初始条件的对象。
Proceedings of the Institution of Mechanical Engineers, Part D- Journal of Automobile Engineering
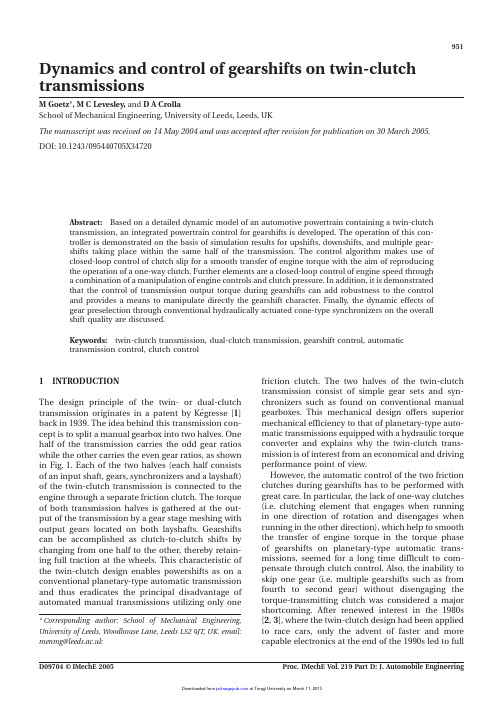
951 Dynamics and control of gearshifts on twin-clutch transmissionsM Goetz*,M C Levesley,and D A CrollaSchool of Mechanical Engineering,University of Leeds,Leeds,UKThe manuscript was received on14May2004and was accepted after revision for publication on30March2005.DOI:10.1243/095440705X34720Abstract:Based on a detailed dynamic model of an automotive powertrain containing a twin-clutchtransmission,an integrated powertrain control for gearshifts is developed.The operation of this con-troller is demonstrated on the basis of simulation results for upshifts,downshifts,and multiple gear-shifts taking place within the same half of the transmission.The control algorithm makes use ofclosed-loop control of clutch slip for a smooth transfer of engine torque with the aim of reproducingthe operation of a one-way clutch.Further elements are a closed-loop control of engine speed througha combination of a manipulation of engine controls and clutch pressure.In addition,it is demonstratedthat the control of transmission output torque during gearshifts can add robustness to the controland provides a means to manipulate directly the gearshift character.Finally,the dynamic effects ofgear preselection through conventional hydraulically actuated cone-type synchronizers on the overallshift quality are discussed.Keywords:twin-clutch transmission,dual-clutch transmission,gearshift control,automatictransmission control,clutch control1INTRODUCTION friction clutch.The two halves of the twin-clutchtransmission consist of simple gear sets and syn-chronizers such as found on conventional manual The design principle of the twin-or dual-clutchgearboxes.This mechanical design offers superior transmission originates in a patent by Ke´gresse[1]mechanical efficiency to that of planetary-type auto-back in1939.The idea behind this transmission con-matic transmissions equipped with a hydraulic torque cept is to split a manual gearbox into two halves.Oneconverter and explains why the twin-clutch trans-half of the transmission carries the odd gear ratiosmission is of interest from an economical and driving while the other carries the even gear ratios,as shownperformance point of view.in Fig.1.Each of the two halves(each half consistsHowever,the automatic control of the two friction of an input shaft,gears,synchronizers and a layshaft)clutches during gearshifts has to be performed with of the twin-clutch transmission is connected to thegreat care.In particular,the lack of one-way clutches engine through a separate friction clutch.The torque(i.e.clutching element that engages when running of both transmission halves is gathered at the out-in one direction of rotation and disengages when put of the transmission by a gear stage meshing withrunning in the other direction),which help to smooth output gears located on both layshafts.Gearshiftsthe transfer of engine torque in the torque phase can be accomplished as clutch-to-clutch shifts byof gearshifts on planetary-type automatic trans-changing from one half to the other,thereby retain-missions,seemed for a long time difficult to com-ing full traction at the wheels.This characteristic ofpensate through clutch control.Also,the inability to the twin-clutch design enables powershifts as on askip one gear(i.e.multiple gearshifts such as from conventional planetary-type automatic transmissionfourth to second gear)without disengaging the and thus eradicates the principal disadvantage oftorque-transmitting clutch was considered a major automated manual transmissions utilizing only oneshortcoming.After renewed interest in the1980s *Corresponding author:School of Mechanical Engineering,[2,3],where the twin-clutch design had been applied University of Leeds,Woodhouse Lane,Leeds LS29JT,UK.email:to race cars,only the advent of faster and morecapable electronics at the end of the1990s led to full menmg@952M Goetz,M C Levesley,and D A CrollaFig.1Twin-clutch transmission of two-layshaft typeinterest from all major car and transmission manu-for gearshifts,which produces high shift quality facturers.In2003,the twin-clutch transmission[4]comparable with that of planetary-type automatic wasfinally put into production for thefirst time.transmissions.Another important aim is to create a The problems of the control of both a singlegearshift control that is robust against changes in gearshift and multiple gearshifts on twin-clutch the clutch friction coefficient and allows the track-transmissions are addressed in this paper.Theing of transmission output torque trajectories,thus requirement for robust operation of the control of providing a basis for integration in torque-based gearshifts under a variety of operating points andpowertrain control schemes.conditions(e.g.changes in clutch friction)necessitatethe employment of closed-loop control techniques.For conventional automatic transmissions,closed-2DYNAMIC POWERTRAIN MODELloop control has been mainly applied to enginesynchronization[5],leaving the control of the engine For the simulation of gearshift performance,adynamic model of a vehicle powertrain was torque transfer to a combination of one-way clutchoperation and open-loop clutch pressure manipu-developed.lation.For twin-clutch transmissions the potentialsThe whole powertrain model is depicted in Fig.2 of various gearshift control concepts applied to up-and features a mean value torque production model shifts was compared in reference[6].The solutionof a spark ignition engine that was given in reference that offered the best gearshift performance was a[8]and that makes use of regression functions for closed-loop strategy,where the transmission outputairflow through throttle body and intake manifold torque was controlled throughout the whole gear-and for the torque generated in the combustion shift.The control of multiple gearshifts was addressedprocess.Also included in the engine model are the in reference[7]where a solution for so-called‘double rotational dynamics of the engine and accessory shifts’was proposed.The control described in thatloads.Inputs to the engine model are throttle angle article used the second clutch to provide somefill-and spark advance.The block representing the twin in torque for the time that the torque-transmittingclutch transmission in Fig.2consists of two parts: clutch has to be disengaged in order to be able to the rotational dynamics of clutches,synchronizers change the gear in that particular transmission half.and geartrain,and the dynamics of the hydraulic The control strategy presented in that paper,how-system.Inputs to the transmission block are pressure ever,made exclusive use of open-loop techniques.values for clutches and synchronizers,which are The objectives of this paper are to investigate the actually voltage inputs to the solenoid valves con-dynamics of gearshifts on twin-clutch transmissionstrolling the hydraulic actuation of clutches and and to develop an integrated powertrain control synchronizers.Dynamics and control of gearshifts on twin-clutch transmissions953Fig.2Model of a vehicle powertrain including a twin-clutch transmissionThe dynamic models of powertrain and hydraulic components of the transmission,while massless system were created in MATLAB/Simulink A,whichspring–damper elements are employed to model the was also used to generate the simulation results compliances of the shafts in the gearbox.To model presented in this paper.the drag that is created in the twin-clutch trans-mission,the inertias are‘connected’to the groundvia damper elements.2.1Rotational dynamics of the twin-clutchIn order to model the dynamics of a shift from transmissionsynchronizer to synchronizer where both gear ratios Figure3shows the dynamic model of the twin-clutch(i.e.synchronizers)are located within the same half transmission,which is based on the layout presented of the transmission,the dynamic model of the in Fig.1.twin-clutch transmission depicted in Fig.3had to Inputs to this part of the transmission model are be extended by an additional synchronizer model the clamp forces at clutches and synchronizers.Non-(indicated by the dashed rectangle in Fig.3).This compliant discs represent the inertias of the internalprovided the basis for realistic modelling of a changeFig.3Rotational dynamics of the twin-clutch transmission,depicted for the configuration of first and second gears.Extension is shown for third gear954M Goetz,M C Levesley,and D A Crollabetween synchronizers without producing discon-additional rules given bytinuities in the simulation results.This extension to IF {v in =v out }AND {x s Áx s,max }THENthe transmission model is used later in sections 3.3and 4.{dog clutch is engaged}(6)Both the synchronizer and the clutch models con-IF {x s <x s,max}THEN {dog clutch is disengaged}sist of a friction model that describes the torque transmitted in the slipping and in the sticking states.(7)It also contains the logic of the transitions between the two states.The synchronizer model incorporates These two equations essentially reflect the fact that a third state,which accounts for a mechanical lock-the dog clutch can be engaged once the two halves ing of its two halves via the dog-clutch-like part of of the synchronizer run with the same speed and the synchronizer.The friction behaviour of clutch thus the teeth can slide to their maximum axial dis-and synchronizer is given by the equations placement,thereby mechanically locking the syn-chronizer.If the teeth of the dog clutch are slid back T C =sgn(v in −v out )R m F N m k z (1)into their initial position,the mechanical coupling is neutralized.The information about the displacement with of the dog clutch comes from the actuator model of the synchronizer.m k=f (D v )(2)for the clutch,and 2.2Hydraulic actuation of clutches andsynchronizersTsyn =sgn(v in −v out )Rm sin a F N m kz (3)The hydraulic system of the transmission model gen-erates a clamp force at its output (i.e.input to the rotational dynamics described in the last section)withfrom a voltage input to the solenoid valves.The hydraulic actuation scheme is the most commonly m k=constant (4)used so far,particularly in conjunction with wet friction clutches.Electric actuation in conjunction for the synchronizer.If the clutch–synchronizer slips with dry friction clutches o ffers increased simplicity (v in ≠v out),the friction torque is given by equation and e fficiency but tends to show more compliance (1)for the clutch and equation (3)for the syn-in the actuation system and hence slower response chronizer.The friction coe fficient of the clutch is times.dependent on the sliding speed across the clutch and First,a detailed dynamic model of the hydraulic was represented by a higher-order polynomial as a actuation system was developed.The hydraulic clutch function of the sliding speed.This allowed modelling actuation consists of a proportional solenoid valve,of various friction materials of both wet and dry which controls oil flow to the hydraulic actuator.friction types.The friction coe fficient at the syn-Increasing the pressure in the hydraulic actuator chronizer has been assumed constant.extends the actuator piston,which acts on the clutch If both halves of the clutch–synchronizer stick pack,thus producing a clamp force.The model of together (v in =v out)the torque at the clutch–synch-the clutch pack essentially contained the equations ronizer is determined by the applied load torques of motion of the piston including the opposing forces and inertial torques and is limited by of the return spring and the clutch pack.This clutch pack model permits a simulation of the dynamic |T C,syn|∏m s R m F Nz(5)behaviour of the hydraulic clutch actuation at the A frictional lock-up of the clutch–synchronizer takes point where the clutch piston has ended its idle place if the di fferential speed across the clutch stroke and makes contact with the clutch pack,lead-vanishes and the criterion of equation (5)is fulfilled.ing to a sharp rise in clutch pressure.Based on The frictional contact of the clutch–synchronizer the detailed model,a simplified phenomenological breaks apart if the torque at the clutch–synchronizer model was generated for the development of the exceeds the limit given by equation (5).gearshift controller,since it was less complex and The additional state coming from a mechanical more flexible.The simplified model of the hydraulic locking of the synchronizer through engagement actuation is depicted in Fig.4and consists of two linear transfer functions and a feedback loop.of the dog clutch was accounted for by simpleDynamics and control of gearshifts on twin-clutch transmissions955Fig.4Simplified dynamic model of the hydraulic actuation and clutch pack in the s domain3INTEGRATED POWERTRAIN CONTROL OF of engine torque transfer without creating too much GEARSHIFTSvehicle jerk.If it is possible to mimic the operationof a one-way clutch by careful control of a friction Gearshifts on twin-clutch transmissions can beclutch,then the optimal transfer of engine torque accomplished as so-called clutch-to-clutch shifts could be accomplished even on a twin-clutch trans-by changing from one half of the transmission tomission.Such a control was suggested in references the other.However,before commencing the clutch-[9]and[10]and requires closed-loop control of to-clutch shift,the target gear needs to be engagedclutch slip.(preselected)on the opposite half of the trans-The problem of obtaining the torque signal and mission.Essentially,the gearshift on a twin-clutchthe advantages and disadvantages of each technique transmission consists of two parts:(sensor measurement versus mathematical observer)are not discussed here but are well covered in the (a)the preselection of the target gear on the torque-literature(see,for example,references[6],[11],and free half of the transmission;[12]).(b)the clutch-to-clutch shift.The clutch-to-clutch shift is the subject of this3.1Control of upshiftssection whereas the preselection(in particular,thedynamic effects of the gear change)is discussed in The control algorithm for power-on upshifts is section4.depicted in Fig.5.The control sequence is shown in The clutch-to-clutch shift consists of two distinctive the clutch pressure profiles of the simulation result parts:a‘torque phase’where engine torque is trans-(upshift fromfirst to second gear)in Fig.6.In step1 ferred from the offgoing clutch to the oncoming of the control algorithm,hydraulic pressure is reduced clutch and an‘inertia phase’where the speed of theat the offgoing clutch.The nearer the pressure is engine is synchronized to that of the target gear.decreased to the value where the clutch starts to The order of the two phases depends on the type ofslip,the smaller are the resulting torque vibrations shift(i.e.upshift or downshift)and the direction coming from the stick–slip transition.However,theactual transition from stick to slip at this clutch of the transmission of drive power(i.e.power-on orpower-off).is accomplished by the clutch slip control,which is The clutch-to-clutch shift can be controlled inactivated in step3.Prior to activation of the clutch principle in the same manner as on planetary-type slip controller,the oncoming clutch is prefilled in transmissions.However,because of differences instep2.This pressure needs to be selected on the the design(in particular,the absence of one-way basis of a compromise between fastfilling on one clutches on twin-clutch transmissions)the transferhand and little effect on driveline torque on the of engine torque in the torque phase becomes more other.The closed-loop control of clutch slip main-tains a small clutch slip reference value(5rad/s)by difficult to control.This is due to the difficulty incontrolling the timing of the application and release manipulating the pressure at the offgoing clutch.By of the two clutches.One-way clutches and theirramping up the pressure at the oncoming clutch ability to disengage automatically once the trans-(step4),the slip controller automatically reduces the mitted torque has become negative aid the controlpressure at the offgoing clutch,thus transferring956M Goetz,M C Levesley,and D A CrollaFig.5Algorithm for upshift controlFig.6Simulation result of an upshift fromfirst to second gear(BTDC,before top dead centre).The arrows and numbers indicate the steps of the control algorithm depicted in Fig.5engine torque without creating negative torque at In this phase,the engine speed is synchronized to this clutch.At the point where the pressure at thethat of the target gear while tracking a reference offgoing clutch has become zero,the slip controller speed profile.The closed-loop speed controller,whichis activated in step5,achieves this by manipulating is deactivated and the control can proceed to theinertia phase.both engine throttle angle and spark advance(SA),957 Dynamics and control of gearshifts on twin-clutch transmissionsthus uniting the advantages of large engine torque From the output torque profile in Fig.6,it can be variations and fast engine response.In the inertiaseen that the torque does not show any abrupt phase,transmission output torque control can be changes at the point of the transition from the torque activated(step6)in which closed-loop trackingto the inertia phase,thus verifying the smooth of a reference torque profile is achieved through control of the engine torque transfer by the clutch manipulation of pressure at the oncoming clutch byslip controller.the controller.The reference torque profile used heregoverns the transmission output torque to a level3.2Control of downshiftscorresponding to the change in gear ratio over thewhole gearshift.At the end of the inertia phase the The power-on downshift starts with the inertia phase clutch pressure is raised to the line pressure(step7),where the engine is synchronized to the target gear, which is the main pressure in the hydraulic system.followed by the torque phase where engine torque istransferred between the two clutches.The control It was observed that the torque vibrations createdat the end of the gearshift where the clutch locks up algorithm for downshifts is depicted in Fig.7.Again could be reduced by abruptly raising the sparkthe steps of the control algorithm are indicated in the advance to its original value at this point.Further simulation result depicted in Fig.8.At the beginning details of the upshift control including a discussionof the inertia phase(step1in Fig.7),the pressure at of robustness against changes in the clutch friction the offgoing clutch is reduced in a similar way as in material have been given in reference[13].the torque phase of the upshift control.Through-Figure6shows a simulation result for an upshift out the inertia phase of the downshift the engine from thefirst to second gear.The graph depicts theneeds to be accelerated in order to reach the syn-time profiles of transmission output torque T out,the chronous speed of the target gear.A combination rotational speeds v at both clutches including engineof an increase in throttle angle(step2)and clutch speed(denoted as input speed),the pressure pro-pressure modulation by the speed controller(step3)files p C at both clutches,the throttle angle and theallows tracking of a reference speed profile without spark advance(denoted Throttle and SA).In general,having to decrease the clutch pressure too much, good tracking of the reference profiles for enginethus transmitting as much engine torque as possible. speed(second graph)and transmission output torque Prior to the end of the inertia phase,the oncoming (uppermost graph)can be observed.clutch is prefilled in step4(low pressure to suppressFig.7Algorithm for downshift control958M Goetz,M C Levesley,and D A CrollaFig.8Simulation result of a downshift from second tofirst gear(BTDC,before top dead centre).The arrows and numbers indicate the steps of the control algorithm depicted in Fig.7torque vibrations)and the throttle angle is decreased a downshift from second tofirst gear is depicted again in step5.in Fig.8.Once again,it can be seen that the track-In a similar way as previously explained for the ing performances of speed and torque reference upshift,clutch slip control is employed in the torquetrajectories are good.The output torque profile of phase for a smooth transfer of engine torque(step6).the downshift depicted in Fig.6looks reasonably In parallel with the clutch slip control,the optionalsmooth,owing to the relatively shallow gradient transmission output control can be activated(step7).of the reference torque trajectory selected in the Although the clutch slip controller takes care oftorque phase.the engine torque transfer,the transmission outputtorque profile can take different shapes depending3.3Control of multiple gearshiftson the operating point of engine and the gear ratio.To be able to manipulate the profile of the trans-As explained in the introduction,gearshifts thatchange between gears within the same half of the mission output torque,closed-loop torque controlcan be activated in the torque phase.To implement transmission(e.g.from fourth to second gear)cannot the output torque control without losing the functionbe accomplished as simple clutch-to-clutch shifts. of the clutch slip control,the pressure manipulation During the period of time where the original gear is at the oncoming clutch is split into two actions.Thedisengaged and the target gear engaged,the appro-first action requires ramping up the pressure,but at priate half of the transmission needs to be torque a lower rate than required in the torque phase of thefree.This means,however,that since both the upshift.This is necessary to force the slip controller original gear and the target gear are located within to transfer engine torque gradually.Then,the secondthe same half of the transmission,the torque-action comes from the closed-loop torque control,transmitting clutch has to be disengaged for the which adds its contributions in the pressure manipu-change in gears.The result would be a gearshift lation to the pressure ramp of thefirst control action.similar to a manual or automated manual trans-Further details of the downshift control havemission with interruption in traction,which is not been given in reference[14].A simulation result for acceptable for a powershift transmission.959 Dynamics and control of gearshifts on twin-clutch transmissionsTwo or more consecutive gearshifts would fulfil the transferred to the other clutch in steps5and6.The requirement of transmitting power to the wheelsremainder of engine torque is used for continuing during the gearshift,but these would result in un-the acceleration of the engine.The change of clutch acceptably long shift times and would be distinguish-in steps5and6is accomplished through conven-able as two separate gearshift events by the driver.tional open-loop pressure ramps.Owing to the small To solve the problem,it was proposed to use theamount of engine torque transferred,no significant second clutch during the gear change in order to improvement in clutch slip control over the open-provide somefill-in torque[7].This technique isloop controlled clutch change was noticed.A second adopted here and combined with the techniques reason why the clutch slip control was not aseffective here as it was in the normal torque phase of engine control,clutch slip,and torque controldeveloped in the previous sections.Since multiple is that,for its operation,the engine needs to be downshifts are,because of the importance ofdecelerated to the input shaft speed of the inter-response time,more critical than multiple upshifts,mediate gear,which would result in increased vehicle only multiple downshifts are discussed here.Thejerk.control algorithm for multiple downshifts is depicted While the gear is changed in the torque-free halfof the transmission through a change in synchronizer in Fig.9.The steps in the control algorithm that aredifferent from the control of single downshifts are in steps8and9,the engine speed controller is active indicated by arrows in the simulation result shownat the torque-carrying clutch(step7).The pressure in Fig.10.value at the engaging synchronizer is mainly deter-Up to step4,the control algorithm in Fig.9is themined by the time available for synchronization and same as for single downshifts.However,instead of the gear ratio.After synchronization of the input transferring the full amount of engine torque in theshaft to the target gear is completed,the syn-subsequent phase,only a part of engine torque is chronizer pressure is raised to line pressure(step10).Fig.9Control algorithm for multiple downshifts960M Goetz,M C Levesley,and D A CrollaFig.10Simulation result of a downshift from fourth to second gear(BTDC,before top dead centre).The arrows and numbers indicate the steps of the control algorithm depictedin Fig.9Subsequent to the prefilling of the original clutch In this section,the dynamic effects of preselection (step11)the actual torque phase begins,which ison the overall gearshift quality will be investigated. controlled in the same way as for single downshifts,A simple preselection strategy is employed thatrequires that a gear lower than the presently engaged again employing clutch slip control and transmissionoutput torque control.gear has to be selected on the torque-free half of the Figure10depicts a simulation result for a down-transmission.This has the advantage that the trans-shift from fourth to second gear.The speed trajectory mission is always prepared for a downshift without of the engine in Fig.10clearly indicates that thefirst having to change the target gear.engine accelerates constantly throughout the whole The engagement of the target gear ratio on the inertia phase,comparable with a single gearshift.torque-free half of the transmission requires syn-Thus,the driver experiences the multiple–gearshift chronization of the input shafts to the speed level event as a single gearshift event.Traction is inof the target gear.When changing to a target gear general maintained throughout the gearshift.In the lower than the gear currently engaged,the input torque phase the reference torque profile is trackedshaft needs to be accelerated.When changing to a accurately apart from an initial deviation.target gear higher than the gear currently engaged,the input shaft needs to be decelerated.If this syn-chronization process is carried out by use of conven-tional synchronizers,the energy for this speed change 4DYNAMIC EFFECTS OF GEAR PRESELECTIONis transferred from the output of the transmission.ON GEARSHIFT PERFORMANCE Other methods of synchronization include central syn-chronization with an external energy supply(external As mentioned at the beginning of section3,a gear-brake and electric motor)or synchronization via shift on a twin-clutch transmission consists of pre-engine control,both requiring only simple dog selection of the target gear on the torque-free halfclutches.The latter is only reasonably applicable of the transmission and a clutch-to-clutch shift.to automated manual transmissions featuring only。
基于动态地形模型的重大地质灾害仿真研究
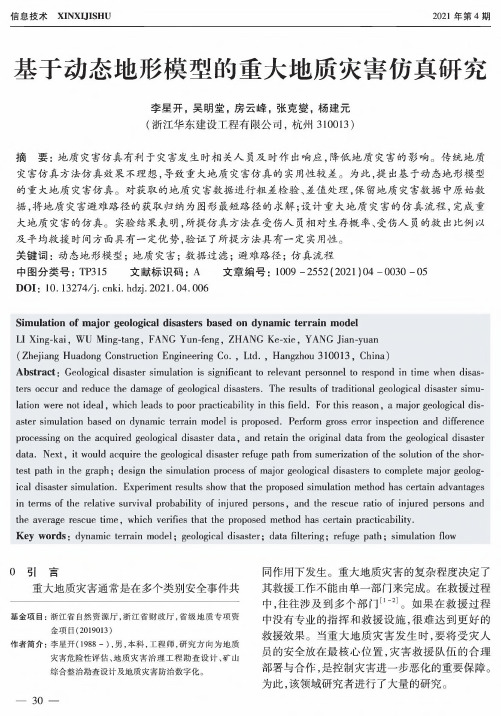
信息技术XINXUISHU2021年第4期基于动态地形模型的重大地质灾害仿真研究李星开,吴明堂,房云峰,张克燮,杨建元(浙江华东建设工程有限公司,杭州310013)摘要:地质灾害仿真有利于灾害发生时相关人员及时作出响应,降低地质灾害的影响。
传统地质灾害仿真方法仿真效果不理想,导致重大地质灾害仿真的实用性较差。
为此,提出基于动态地形模型的重大地质灾害仿真。
对获取的地质灾害数据进行粗差检验、差值处理,保留地质灾害数据中原始数据,将地质灾害避难路径的获取归纳为图形最短路径的求解;设计重大地质灾害的仿真流程,完成重大地质灾害的仿真。
实验结果表明,所提仿真方法在受伤人员相对生存概率、受伤人员的救出比例以及平均救援时间方面具有一定优势,验证了所提方法具有一定实用性。
关键词:动态地形模型;地质灾害;数据过滤;避难路径;仿真流程中图分类号:TP315文献标识码:A文章编号:1009-2552(2021)04-0030-05DOI:10.13274/ki.hdzj.2021.04.006Simulation of major geological disasters based on dynamic terrain modelLI Xing-kai,WU Ming-tang,FANG Yun-feng,ZHANG Ke-xie,YANG Jian-yuan(Zhejiang Huadong Construction Engineering Co.,Ltd.,Hangzhou310013,China)Abstract:Geological disaster simulation is significant to relevant personnel to respond in time when disasters occur and reduce the damage of geological disasters・The results of traditional geological disaster simulation were not ideal,which leads to poor practicability in this field.For this reason,a major geological disaster simulation based on dynamic terrain model is proposed・Perform gross error inspection and difference processing on the acquired geological disaster data,and retain the original data from the geological disaster data.Next,it would acquire the geological disaster refuge path from sumerization of the solution of the shortest path in the graph;design the simulation process of major geological disasters to complete major geological disaster simulation・Experiment results show that the proposed simulation method has certain advantages in terms of the relative survival probability of injured persons,and the rescue ratio of injured persons and the average rescue time,which verifies that the proposed method has certain practicability.Key words:dynamic terrain model;geological disaster;data filtering;refuge path;simulation flowo引言重大地质灾害通常是在多个类别安全事件共基金项目:浙江省自然资源厅,浙江省财政厅,省级地质专项资金项目(2019013)作者简介:李星开(1988-),男,本科,工程师,研究方向为地质灾害危险性评估、地质灾害治理工程勘查设计、矿山综合整治勘查设计及地质灾害防治数字化。
能耗模拟及相关软件介绍(英文ppt)

4. Introduction of simulation tools
(1)DOE(1)DOE-2 Hourly, whole-building energy analysis program wholecalculating energy performance and life-cycle cost of lifeoperation. Can be used to analyze energy efficiency of given designs or efficiency of new technologies. Other uses include utility demand-side management demandand rebate programs, development and implementation of energy efficiency standards and compliance certification, and training new corps of energyenergy-efficiency conscious building professionals in architecture and engineering schools.
(2) BLAST Performs hourly simulations of buildings, air handling systems, and central plant equipment in order to provide mechanical, energy and architectural engineers with accurate estimates of a building's energy needs. The zone models of BLAST (Building Loads Analysis and System Thermodynamics), which are based on the fundamental heat balance method, are the industry standard for heating and cooling load calculations. BLAST output may be utilized in conjunction with the LCCID (Life Cycle Cost in Design) program to perform an economic analysis of the building/system/plant design.
铝带重卷机板带自动对中液压系统仿真研究
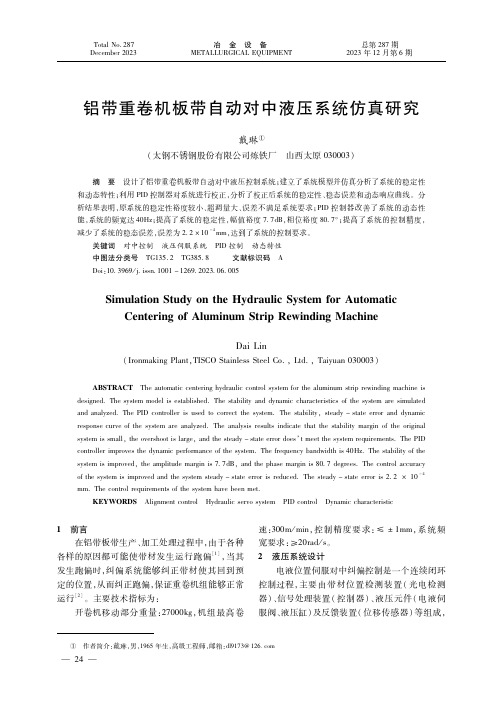
铝带重卷机板带自动对中液压系统仿真研究戴琳①(太钢不锈钢股份有限公司炼铁厂 山西太原030003)摘 要 设计了铝带重卷机板带自动对中液压控制系统;建立了系统模型并仿真分析了系统的稳定性和动态特性;利用PID控制器对系统进行校正,分析了校正后系统的稳定性、稳态误差和动态响应曲线。
分析结果表明,原系统的稳定性裕度较小、超调量大、误差不满足系统要求;PID控制器改善了系统的动态性能,系统的频宽达40Hz;提高了系统的稳定性,幅值裕度7 7dB,相位裕度80 7°;提高了系统的控制精度,减少了系统的稳态误差,误差为2 2×10-4mm,达到了系统的控制要求。
关键词 对中控制 液压伺服系统 PID控制 动态特性中图法分类号 TG135.2 TG385.8 文献标识码 ADoi:10 3969/j issn 1001-1269 2023 06 005SimulationStudyontheHydraulicSystemforAutomaticCenteringofAluminumStripRewindingMachineDaiLin(IronmakingPlant,TISCOStainlessSteelCo.,Ltd.,Taiyuan030003)ABSTRACT Theautomaticcenteringhydrauliccontrolsystemforthealuminumstriprewindingmachineisdesigned.Thesystemmodelisestablished.Thestabilityanddynamiccharacteristicsofthesystemaresimulatedandanalyzed.ThePIDcontrollerisusedtocorrectthesystem.Thestability,steady-stateerroranddynamicresponsecurveofthesystemareanalyzed.Theanalysisresultsindicatethatthestabilitymarginoftheoriginalsystemissmall,theovershootislarge,andthesteady-stateerrordoes’tmeetthesystemrequirements.ThePIDcontrollerimprovesthedynamicperformanceofthesystem.Thefrequencybandwidthis40Hz.Thestabilityofthesystemisimproved,theamplitudemarginis7 7dB,andthephasemarginis80 7degrees.Thecontrolaccuracyofthesystemisimprovedandthesystemsteady-stateerrorisreduced.Thesteady-stateerroris2 2×10-4mm.Thecontrolrequirementsofthesystemhavebeenmet.KEYWORDS Alignmentcontrol Hydraulicservosystem PIDcontrol Dynamiccharacteristic1 前言在铝带板带生产、加工处理过程中,由于各种各样的原因都可能使带材发生运行跑偏[1],当其发生跑偏时,纠偏系统能够纠正带材使其回到预定的位置,从而纠正跑偏,保证重卷机组能够正常运行[2]。
- 1、下载文档前请自行甄别文档内容的完整性,平台不提供额外的编辑、内容补充、找答案等附加服务。
- 2、"仅部分预览"的文档,不可在线预览部分如存在完整性等问题,可反馈申请退款(可完整预览的文档不适用该条件!)。
- 3、如文档侵犯您的权益,请联系客服反馈,我们会尽快为您处理(人工客服工作时间:9:00-18:30)。
Simulation on the Dynamic Pressure and Flow of theSeawater Desalination Axial Piston PumpZhai JiangState Key Lab of Fluid Power Transmission and ControlZhejiang University Hangzhou, P. R. China jiangzhai@Zhou HuaState Key Lab of Fluid Power Transmission and ControlZhejiang University Hangzhou, P. R. China hzhou@Abstract —The axial piston pump used as a high pr essur e pump is one of the most impor tant component in small and medium scale Sea Water Reverse Osmosis (SWRO) desalination pr ojects. The pr essur e and flow r ipple is an impor tant factor which impacts the noise level of the pump. The axial piston pump for SWRO desalination uses seawater as its wor king media and the fluid pr oper ties of seawater ar e obviously differ ent fr om mineral oil. In order to accurately simulate the dynamic pressure and flow of the pump, the special properties of seawater have to be considered. For this reason, the variational fluid properties of miner al oil and seawater wer e simulated and the r esults wer e compared. The model which describes the dynamic pressure and flow was presented. The pressure and flow characters of a single cylinder and a swash plate axial piston pump with five pistons were simulated using this model. From the simulation results, the deliver y pr essur e and flow r ipple when taking seawater as working medium are greater than the oil one if the geometry and boundar y conditions ar e same. In or der to r educe the pr essur e and flow r ipple, the over lap angle of the por tplate when taking seawater as working medium should be small.Keywords—seawate rdesalination, axial piston pump, pressure, flow, simulationI.I NTRODUCTIONIt is well known that seawater desalination is the technology and process for getting fresh water from sea. Compared to other methods, the Sea Water Reverse Osmosis process (SWRO) is an energy-saving technology in seawater desalination engineering. As the development of water hydraulic technology, axial piston pumps are widely used as power components in modern water hydraulic systems for their high specific power, efficiency and reliability [1]. So this type pumps can be developed as high pressure pumps for small andmedium scale SWRO desalination projects.But axial piston pumps for SWRO operation are affected by some disadvantages. In axial piston pumps, both the pumping mechanism and the fluid compressibility induce flow oscillations which can cause pressure pulsations and lead tovibrations and noise. When the pump is fed from a seawaterreservoir, the seawater can be in contact with atmospheric air that partially dissolves into the water. During the suction stroke the pressure reduction due to pressure losses and dynamic effects can cause the air to be released in bubbles. Besides of air-release, vapour cavitation can also arise if the pressure decreases more. Vapour cavitation induces the volumetric efficiency of the pump to drop and perhaps destroy some pump parts. So the accurately simulating the dynamic pressure and flow of the pump is very important for prediction of the vibration, cavitation and optimal design for the pump.Compared with hydraulic oil, the main physical parameters of sea water have their own characteristics. The dynamic viscosity of a type mineral oil is 5.1×10-2 Pa·s at 313K while the dynamic viscosity of water is 0.615×10-3 Pa·s at 288K. The dynamic viscosity of oil at operating temperatures is about 80 times that of seawater. So the gap leakage in water hydraulic elements is about 80 times larger than that for oil if the geometries of the leakage paths are the same. The vapour pressure for seawater is 1.22 ×10-2 MPa at 323K, which is higher by approximately 7 orders of magnitude that for mineral oil, which is only approximately 1.0×10-9 MPa at 323K. For this reason, the different properties of mineral oil and sea watershould be considered when simulate the dynamic pressure andflow of the pump.. Research on water axial piston pumps is being worldwide carried out; and the main topics are the development of someprototypes for different applications [2], the materials selection for key tribological pairs of the pump [3,4], the water lubrication character of the hydrostatic bearings and slippers of the pump [5]. The evaluation of the pumping flow and the reduction of noise and the avoidance of cavitation are mostly on axial piston pump for oil hydraulics [6,7], but the dynamic pressure and flow characters of the axial piston pump using water as working medium are rarely reported. In this paper, simulation processes and results for dynamic pressure and flow of an axial piston pump using differentworking medium such as mineral oil and sea water are presented. The factors of working medium which impact the dynamic characters are discussed. II. M ATHEMATICAL MODEL OF THE P UMPING PROCESS As seen in Fig. 1, the major components of an axial piston pump are the pistons, the cylinder block, valve plate, piston slippers, swash plate, and the drive shaft. In operation, the mainshaft drives the cylinder block, which rotates the pistons in turn. The swash plate is at some angle relative to the centerline of the drive shaft, which is also the axial center of rotation of the pistons. The pistons are held against the swash plate by springs and a retainer plate. The slippers slide on the surface of the swash plate and the angle will force the pistons to move in and out of the cylinder block. So the axial piston pump will produce a flow when the drive shaft is running.Figure 1. Schematic of an axial piston pumpThe main difference between the axial piston pump for SWRO and oil one are the tribological pairs. Because of the low dynamic viscosity of the seawater liquid lubrication is difficult to form at the main tribological pairs. For this reason, the materials selection for the SWRO pump is a key problem. Special engineering plastic and anticorrosion metal can be adopted as pairing materials.A. Dyanmic preesure and flow model of the pumpFig. 2 presents the principle adopted for the dynamic pressure and flow modelling for an axial piston pump. The cylinder block of the axial piston pump is divided in some chambers and the working medium is assigned in it. V Ci represents one of the variable volumes of the cylinder when the piston is moving and the pump is running. V PI and V PO represent the constant volume in the sum of dead volume at the suction and delivery side of the pump. The number of cylinders of the pump, N of variable cylinder volumes V Ci connected to the V Pi and V Po volumes respectively. A I represents the orifice area at the inlet of the pump and p i represents the pressure of the tank. The damping rate of A I can be omitted in general condition. A o represents the orifice area at the outlet of the pump. p o represents the output pressure of the pump and it can be determined by other parameters. From Fig. 2 we can see that the output pressure of the pump is determined by the orifice A o . Fig. 3 (b) presents two kidney ports at the portplate connected to the suction and delivery volumes and two silencing grooves that allow the cylinder to pass smoothly from inlet to delivery. Fig. 3 (a) presents the N slots at the cylinder which connected the two kidney ports successively when the cylinder run. So the areas of the variable orifices A i and A o (as showed in Fig. 2) depend on the position of the cylinder block with respect to the portplate.Figure 2. Principle of an axial piston pump modellingFigure 3. Cylinder slot and portplateBase on this principle, the mathematical model for the pressure and flow can be induced. Figure 4 presented the kinematic diagram of an axial piston pump.From the kinematic and geometrical character of the pump, the cylinder volume of a single cylinder chamber is given by:201sin tan 4Ci C i V V d R πθβ=+ (1)where V C0 is the dead volume of a single cylinder chamber, ȕ is the swash plate angle of the pump, R is the piston pitch radius and d is the diameter of the piston. If i represent the sequence number of the piston from the up dead point and the pump has N pistons, we can get2(1)i t i Nπθω=+− (2) Because of the low viscosity of the seawater, a high Reynolds number tends to characterize the flow in and out of the cylinder chamber. This flow may be modeled using aorifice pressure-flow equation, and this result is given by:,,)Ci i o I O Ci Q A C p p =− (3)where C d is throttling coefficient and its value is about 0.6. ȡ is the density of the working medium. The pressure of the cylinder chamber varies with time to account for the periodicity change from the output pressure, p o , to the intake pressure, p i . The discharge areas, A o , and suction area, A i , (as shower in Fig. 2) vary with time to model the transition regions on the port plate where the variable orifices provide a variable opening into each port. Considering the continuity equation, the dynamic pressure of each chamber is determined for the cylinder volume, so one obtains:d d d d Ci Ci Ci CLi Ci p V B Q Q t V t§·=−−¨¸©¹(4)where B is the bulk modulus of the working medium and Q CLi is the leakage flow from the clearance of the piston and the cylinder chamber.32,(1 1.5)()12CLiCi I O Cid Qe p p l πδ=+− (5) where į is the clearance in diameter between the piston and the cylinder bore, ȝ is the dynamic viscosity of the working medium, l Ci is the contact length between the piston and the cylinder bore, e is the eccentricity of the piston.The flow of the pump is the sum of N cylinder chambers, sothe flow of the pump:V Q A C = (7)where A V is area of a variable orifice to adjust the outlet pressure, p 0 is the environment pressure. The outlet pressure of the pump p O is:1d ()d NO CiCLi i POp BQQ t V ==−¦ (8)where N represents the number of cylinder chambers in pumping. V PO represents the dead volume between the outlet and the variable orifice to adjust the pressure. Based on Eq. (1) - Eq. (8) and corresponding software, the dynamic pressure and flow of the pump can be calculated as the geometry condition and other boundary condition are full.B. Properties model of mineral oil and sea waterFrom Eq. (1) – Eq. (8) we can find that the properties of working fluid such as density, bulk modulus and dynamic viscosity will impact the dynamic flow and pressure characters of the pump, so the model of the variable fluid properties should be considered. [8]In general condition, the fluid always contains some air or vapour and it can be dissolved or in the form of bubbles. The bulk modulus of the fluid gas mixuture is defined to be:d d p B ρ= (9) The density of the fluid gas mixture varies with pressure and air/vapour. Integrate the definition equation of bulk modulus (Eq. 9), we can obtain:000d (,)00(,)(,)pp pB p T p T p T eρρ³= (10)If one of the quantities density and bulk modulus is defined, the other is also defined through Eq. (10).The volume of the free air/vapor is assumed to vary with pressure in a way determined by a constant polytropic index Ȗ:1()GAS p Kp γρ= (11)1) Mineral oilBecause mineral oil has very low vapour pressure but air is more easily dissolved in it, it is assumed that the variable properties of mineral oil are main determined by the dissolved air.Suppose a sample of oil is taken. Separate the air including the dissolved air from the oil and store both at absolute atmospheric pressure p 0 and absolute temperature T 0. If the volumes of the oil and air are V OIL and V AIR respectively, the fractional air content x is defined to be:AIR AIR OILV x V V =+ (12) It is assumed that the air was all dissolved in the oil at p 0 and temperature T 0, and the air contained in unit volume of oil would occupy volume x / (1 - x) if separated. The quantity of unit volume oil mixture is constant on any state.00000(,)(,)1OIL AIR xm p T p T xρρ=+− (13) It is assumed that the saturation pressure of air in the fluid is p SAT . If the oil pressure p p SAT , all air is dissolved. Because the oil mixture volume is a unit, so quantities density of oil mixture at pressure p and temperature T :0000(,)(,)(,)(1)1(,)AIR OIL OIL p T x p T p T x p T ρρρρ=+− (14)All air is dissolved in the fluid, under these conditions the bulk modulus and dynamic viscosity of fluid mixture is assumed not to be influenced by the air content:(,)(,)OIL p T p T μμ= (15)If 0 p<p SAT , there is part of the air is dissolved and part is free. According to Henry’s law, the fraction air undissolved in oil is ș:()1SATp p p θ=−(16)It is assumed that the oil mixture volume is a unit at pressure p 0 and temperature T 0, so the volume of oil mixture and free air respective at pressure p and temperature T is:000d (,)(,)(1)pp p B p T OIL AIR V p T x e−+³=− (17)100(,)()AIR p x T V p T T pγθ=(18)The quantities density of oil mixture at pressure p and temperature T is:0000(1)(,)(,)(,)(1)()OIL AIR OIL AIR AIR x p T x p T p T x V V ρρρ+−+=−+ (19)If take a mean based on volumes, the dynamic viscosity of the mixture is:0000(,)(,)(,)OIL AIR OIL AIR AIR OIL AIR AIRV p T V p T p T V V μμμ+++=+ (20)2) Sea WaterSea water has high vapour pressure and air is difficultly dissolved in it, so it is assumed that the variable properties of sea water are main determined by the vapour ratio.It is assumed that the pressure at which vapour cavitation starts is p HVAP , the pressure at which cavitation is complete as p LVAP . If the pressure p p HVAP , there is no vapour. If p LVAP p<p HVAP , there is some vapor. For the seawater mixture we assume a fraction ij by mass is vapor, and ij is:()LVAP HVAP LVAPp p p p p ϕ−=− (21)It is assumed that the seawater mixture volume is a unit atpressure p 0 and temperature T 0, so the volume of seawater mixture, free air and vapour respective at pressure p and temperature T is:000d (,)(,)(1)pp pB p T SW V p T e ϕ−³=− (22)10000(,)()(,)SW HVAP VAP VAP HVAP p T T p V p T T p γρϕ=(23)The quantities density of seawater mixture at pressure p andtemperature T is:00(,)(,)SW SW VAPp T p T V V ρρ=+ (24)If take a mean based on volumes, the dynamic viscosity of the mixture is:0000(,)(,)(,)SW SW VAP VAP SW VAPV p T V p T p T V V μμμ+=+ (25)If p<p LVAP , there is vapor and no liquid. It is assumed that all seawater is on vapour state. So the fraction parameter ij = 1DŽThe volume of free air and all seawater vapour respective at pressure p and temperature T is:10000(,)()(,)SW HVAP VAP VAP HVAP p T Tp V p T T pγρρ=(26)So the quantities density of seawater mixture at pressure p and temperature T is:00(,)(,)SW VAPp T p T V ρρ=(27)If take a mean based on volumes, the dynamic viscosity of the mixture is:00(,)(,)VAP p T p T μμ= (28)Based on Eq. (9) – Eq. (28) and corresponding software, variable fluid properties at different pressure can be calculated.III. S IMULATION OF FLUID PROPERTIESThe variational properties such as quantities density, bulk modulus and dynamic viscosity can be simulated based on the above fluid properties model. Tab. 1 presents main constant parameters for the simulation.TABLE I.V ALUES OF MAIN PARAMETERS OF SEAWATER AND OILMain Constant Fluid ParametersMineral OilSeawaterT /K313 293ȡFLUID /(kg/m 3) 850 1025ȝFLUID /cP 51 0.615 ȡAIR /(kg/m 3) 1.2 - ȝAIR /cP 0.02 - x /% 0.1 - p SAT /bar 1 - p HVAP /bar - 0.012 p LVAP /bar--0.088Fig. 4 reports quantities density of oil and seawater versus absolute pressure: the curve of oil and the curve of seawater show a similar trend. Because seawater vapour is more easy than oil, the seawater cavitation is predicted to appear at a higher pressure comparatively with oil.Fig. 5 displays bulk modulus as a function of absolute pressure: both curves increase rapidly at about atmosphere pressure. The curve of oil is easy to change by the pressure, because modulus of pure seawater is greater than that of oil. Fig. 6 plots the dynamic viscosity of oil and seawater versus absolute pressure: the curve of seawater is below the curve of oil much more. The reason is that the viscosity of pure seawater is only about 1/80 of the one of oil, so the low viscosity of vapour fractions will not influence the seawater mixture viscosity more.Figure 4. Simulated quantities densityFigure 5. Simulated bulk modulusFigure 6. Simulated dynamic viscosityIV. S IMULATION OF PRESSURE AND FLOWThe development of the pump for SWRO is based on oil one, so its pumping characters impacted by different working fluid should be study. Tab. 2 shows the main parameters for the simulation of an axial piston pump for oil hydraulics.In order to study the influence of the fluid properties, two type fluids, mineral oil and seawater were taken as working medium in the pump respectively. The simulation of thecylinder pressure and flow over 2 pumping cycles is shown in Fig. 7 and Fig. 8.TABLE II.M AIN PARAMETERS FOR THE SIMULATIONNumber of pistons5 Radial Position of the piston /mm 30 Swash Plate Angle /deg 12.5 Piston diameter /mm 10 Piston length of contact /mm30 Piston clearance on diameter /mm0.005Dead volume of single cylinder /mm 3 1000 Dead volume of outlet /mm 3 1000 Rotate speed /rpm1000Figure 7. Simulated pressure of the cylinderFigure 8. Simulated volume flow of thecylinderFig. 7 shows the dynamic cylinder pressure at the inlet phase and outlet phase. At the start of the delivery phase the cylinder port connects with the delivery port silencing groove. Since the port plates exhibited some overlap in the dead centre region the cylinder pressure at the point of port opening was always significantly more than that in the delivery port. As a result a pulse flow occurs as shown on Fig. 8. As the delivery port flow area increases, the cylinder pressure rises. The oil andș /degQ /(L /m i n )0180360540720-4-224Outlet flow (Oil) Inlet flow (Oil)Outlet flow (Seawater) Inlet flow (Seawater)ș /degp /b a r0180360540720102030405060708090 OilSeawaterp /barȡ /(k g /m 3)101010101010101010p /barB /b a r1010101010101010104.0x108.0x101.2x101.6x102.0x102.4x10p /barȡ /(k g /m 3)seawater in the cylinder is compressed by the pressure, so reverse flow occurs. The cylinder pressure rise and eventually reaches the level of the delivery port. Fig.7 and Fig.8 also show that the cylinder pressure and flow when taking seawater as working medium are greater than the oil. Seawater's bulk modulus is greater than oil can explain this phenomenon. Fig.7 shows the pulse flow of seawater at the beginning of delivery phase is greater than the oil, so the overlap angle for SWRO axial piston pump should be optimized.Figure 9. Simulated pressure of the pumpFigure 10. Simulated volume flow of the pumpFig. 9 and Fig. 10 show the delivery pressure and volume flow of the pump. Several of the single-cylinder models are combined to form a complete pump model. From the results, It was found that the delivery flow ripple was of low amplitude and had little effect on the pressure within the cylinder at dead centres. Because seawater's bulk modulus is greater than oil, Fig. 9 and Fig.10 show that the pump's delivery pressure and flow when taking seawater as working medium are greater than the oil. The pressure and flow ripple pulse flow of seawater are greater than the oil.Figure 11 presents the pressure ripple using seawater at different overlap angle of the portplate. When the angle was kept as the value as the origin value of the oil pump, the dynamic pressure has obvious ripples. When the overlap angle is reduced to 9 deg, the pressure overshoot ripple is reduced. But when the angle is reduced to 8.5 deg, the reverse ripple occurred. So the overlap angle of the pump for SWRO should be small than the oil one and need to reduce properly.oil one, the dynamic pressure and flow characters of a swash plate axial piston pump was simulated. From the results, the delivery pressure and flow when taking seawater as working medium are greater than the oil one at the same geometry and boundary conditions. In order to reduce the pressure and flow ripple, the overlap angle of the portplate when taking seawater as working medium should be small than the oil one.A CKNOWLEDGMENTThe authors would like to thank the Ministry of Science and Technology of PRC for the National Key Technology R&D Program (No. 2006BAF01B03-02) and for providing the funding for this work.R EFERENCES[1] Ivantysyn, J., and Ivantysynova, M., Hydrostatics Pumps and Motors,Akademia Books International, New Delhi, India.[2] Vilenius 㧘 M. J.. Water and mobile hydraulic research in Finland. TheFifth International Conference on Fluid Power Transmission and Control 㧘Hangzhou, 2001.[3] Mens J W M, de G ee A W J. Friction and wear behaviour of 18polymers in contact with steel in environments of air and water. Wear. 1991, 149(1-2): 255-268.[4] Yang H, Yang J, Zhou H. Research on materials of piston and cylinderof water hydraulic pump. Industrial Lubrication and Tribology. 2003, 55(1): 38-43.[5] Rokala M, Calonius O, Koskinen K T, et al. Study of lubricationconditions in slipper-swashplate contact in water hydraulic axial piston pump test rig: Proceedings of the 7th JFPS International Symposium on Fluid Power. TOYAMA: 2008: 2008, 91-94.[6] A.M. Harrison, K.A. Edge, Reduction of axial piston pump pressureripple, In: Proceeding of IMechE, vol. 214, Pt I, 2000.[7] K.A. Edge, J. Darling, The pumping dynamics of swash plate pistonpumps, In: Journal of Dynamic Systems, Measurement and Control, Trans. of ASME, 1989, 111(6) 3: 07-312.[8] IMAG INE s.A., AMESim Standard fluid properties, – Indexedelementary fluid properties Report FP01, Roanne, France, 2000.ș /degQ /(L /m i n )18036054072002468OilSeawaterș /degp /b a r1803605407200102030405060708090 OilSeawaterp /b a r。