Alignment of the Central D-Zero Detector
墨盒问题(Cartridgeproblem)

墨盒问题(Cartridge problem)Continuous ink printer utility fault solutionThe reason why the use of continuous ink are all for one reason - to save money. The fact is not false, the use of continuous ink can reduce the cost of supplies. But the use of continuous ink system also brings a lot of trouble for the users. The author will solve some CISS fault experience out to share with you, so that in the event of failure after timely treatment.To construct a continuous ink supply systemUse the principle of continuous ink is through the catheter to the ink bottle and the ink tank, the pressure will Everfount ink poured into the cartridge and printing. In accordance with the classification structure, mainly composed of three parts of continuous ink supply system, respectively is the print cartridge, the ink bottle and the ink conduit. The print cartridge is the original cartridge. In order to ensure the printing quality and reduce the failure, usually continuous ink will be converted into the original cartridge carrier print.The print cartridge: the original cartridge containing a sponge, can get good filtering effect of impurities contained in the ink, the ink absorbent sponge fault but also easy to cause the breakage of print. Now the market also appeared in the non sponge cartridge modification. This type of ink cartridge although no sponge, not prone to fault disconnection, but the filter filter area is small, the filtration of impurity is poor, easily lead to blockage of the nozzle.The ink bottle, ink bottle is provided for the device for ink. Through the catheter from the ink bottle to the print cartridge ink delivery. The ink bottle usually adopts the bottle shaped appearance, and the constant pressure structure. This is mainly because the ink bottle of this design is easy to use and low cost and repeated filling.Ink: ink conduit is connected with catheter print cartridge and ink bottle pipeline. Including cable accessories, such as pipeline plate, wire etc.. Walk the line assembly is to facilitate the alignment and fixed wiring in the pipeline, usually without damaging the printer itself under the condition of construction.Said structure is mainly for readers have an intuitive feeling of continuous ink, thus the fault itself will have a more clear understanding. Below, the author aimed at using continuous for several fault often appear in the ink case analysis.One case: unable to identify the cartridgeThe use of continuous ink users may often encounter such a situation: in the machine after a period of time, not in print, because the printer cannot identify the black cartridge.The fault reason and solution: this situation is mainly because the waste ink printer is full. In fact, each kind of ink-jet printer has set a fixed parts life. When certain parts reach the service life, the printer will prompt to print. The waste ink is easy to form a continuous ink system in use process, so it is easy to lead to the waste ink full storehouse. This canbe done in two aspects: processing or use this printer motherboard software reset reset, thereby eliminating the printer settings; or to repair the waste ink in the sponge replace. The author recommends that users use the latter. Because just cleared easily lead to missing burned waste ink printer.Case two: print head car swing speed is slow, resulting in low speed printingContinuous ink supply system reform tend to transform the original cartridge, this transformation will inevitably cause the burden of carriage. In the heavy load situation, the word car will slow. But the heavy load will lead to accelerated aging and increase the belt printer carriage and connecting rod friction. All these will lead to slow print speed. Severe cases can lead to the word car can not be reset, and cannot be used.Causes and solutions: 1, to replace the motor. The hose and the printer continuous ink supply system of wall friction, resulting in electric motor load increased, the long-term use of electric motor loss, try changing; 2, lubricating rod. The use of time for a long time, the word car friction inside the machine and the connecting rod becomes large, resulting in increasing the resistance of the electric motor is running slow.When the connecting rod lubrication fault can be solved; 3, printer belt aging. The friction drive gear connected with the motor assembly variable belt printer accelerated aging, then cleaning and lubrication can reduce fault belt aging.Case three: printer nozzle cloggingThis is after the ink supply system for printer installed on one of the most common fault. Because the ink is easy to cause heavy impurity precipitation, so the printer head will thus blocked.Failure causes and solutions: clogging is almost as impurity precipitate, also partly because the ink is too acidic caused spray corrosion. If it is because the printer for unused or add non original ink ink delivery system caused by the obstacle or the print head plug, it is best to carry out the washing operation of nozzle. If the water washing can not solve the problem, only the head removed, soaked in about 50-60 DEG C with pure water, cleaning, washing to dry after use. If there is still no significant effect of repeated cleaning, that spray nozzle aperture has been blocked, the failure of the replacement of the nozzle only.In addition to note is the printer head service life limit, such as inkjet printer head of EPSON's life is about 20 - 30 cartridges, therefore, does not use the continuous ink can always guarantee low cost.In addition, the mouth cleaning pump fault is the main cause of inkjet printer head. The printer cleaning pump mouth protection to play a decisive role in the printer head. The carriage return, to head for weak gas treatment by cleaning pump nozzle, nozzle for sealing protection. A break in the printer or install a new cartridge nozzle, a suction pump at the lowerend of the machine to the nozzle of suction, suction pump working accuracy is good. But in the actual operation, performance and air tightness of the suction pump will be decreased due to the increase of residual concretion time, dust and ink in the mouth. If the user does not carry out regular inspection or cleaning, it will make the printer nozzle continuous failure similar plug. So often maintain a suction pump. The specific method is to use the printer cover down unloading car, using a needle aspiration of pure water for irrigation, in particular to mouth embedded in the porous pad fully cleaned. Note that this part of the cleaning, cleaning must not use ethanol or methanol, this will cause a microporous gasket dissolved in this component deformation mosaic. At the same time can come into contact with the lubricating oil pump mouth, oil pump will make the mouth parts of the rubber sealing ring to seal protection nozzle deformation.Case four: the replacement of the new panel will display "ink cartridges"Usually only in the normal ink consumption under the condition of late, the control panel on the "ink" light will be bright. If the replacement ink cartridges, printer panel on the "ink" light is on, then the fault of printer.The fault reason and solution: this kind of failure which might be a cartridge not installed or cartridge itself and detection circuit problem. Another possibility is in the off state to remove the old cartridge and replace the new cartridge. To replace the cartridge, printer of ink delivery system for filling ink, and this process will not be carried out in theoff state, the printer cannot detect cartridge re installed on. At the same time, some of the printer ink volume measurement is the electronic counter using the printer inside for counting, especially in usage statistics of color ink, when the counter reaches a certain value, the printer determines ink exhausted.In the process of starting replacement cartridges, electronic counter of the internal reset will confirm the installation of a new printer cartridge and began to identify. While in the off state to replace the new ink cartridges, printer failed to counter reset, so still report "ink".Failure causes and solutions: reinstall the cartridge in the boot state. But if the fault is still,You must try to use a normal cartridge to replace the cartridge or verify whether the detection circuit problem. If the problem is detecting circuit of electrical contacts mounted on the ink cartridge is ink contamination or corrosion, resulting in poor contact with the cartridge, the cartridge is not detected. The solution is to use alcohol to clean the contact or replace the cartridge.Case five: after the printer cannot print inkThe use of continuous ink supply system will often go to the container to add ink, sometimes add ink after the printer cannot print normally.The fault reason and solution: this failure is mostly due to too much ink filling times, brought serious burden to theprinter and eventually lead to print. There are many reasons for failure to print, such as the waste ink pad is full, print or word car mobile nozzle clogging problems. In this regard, users should regularly carry out maintenance and maintenance of the printer, avoid the faults happening.。
ALIGNMENT

专利名称:ALIGNMENT发明人:ISHIBASHI YORIYUKI,HIRANORYOICHI,YAMASHITA KYOJI,UCHIDANORIO,TABATA MITSUO申请号:JP22981788申请日:19880916公开号:JPH0279418A公开日:19900320专利内容由知识产权出版社提供摘要:PURPOSE:To enable highly precise alignment between a reticle and a wafer by illuminating a standard mark provided on a wafer and a transcribed mark for compensation so as to detect a diffracted light, and getting the slippage information on the relative position between the reticle and the wafer based on this detection results so as to align them. CONSTITUTION:A standard mark 20 and a mark 8 for compensation are illuminated in order by a light source 23, and the image of its reflected diffraction light transmits a slit 21 provided in a wafer off axis system 5. And its transmitted light quantity is received by a photoelectric sensor 22, and the position coordinate of a wafer chuck table 11 when the output becomes maximum (or zero) is measured by a laser interferometer 25. Next, based on the above detection signal the amount of relative position slippage between reticle 1 and a wafer 3 for position compensation is calculated by CPU 26, and based on it a TTL alignment system 4 or wafer off axis alignment optical system 5 is compensated. And the wafer 3 for position compensation is replaced with an actual wafer for LSI manufacturing, and a circuit pattern drawn in the reticle 1 is transcribed.申请人:TOSHIBA CORP 更多信息请下载全文后查看。
高分三号雷达卫星数据预处理流程

高分三号雷达卫星数据预处理流程1.首先,我们需要导入高分三号雷达卫星数据。
First, we need to import the data from the GF-3 radar satellite.2.然后,对数据进行质量控制,包括去除异常值和填补缺失值。
Then, perform quality control on the data, including removing outliers and filling in missing values.3.接下来,对数据进行预处理,如去噪、辐射校正和地理坐标转换。
Next, preprocess the data, such as denoising, radiometric correction, and georeferencing.4.在数据预处理过程中,需要考虑雷达影像的波长和极化特性。
Consider the wavelength and polarization characteristics of the radar images during data preprocessing.5.对数据进行辐射定标,确保数据在不同时间和地点具有一致的无量纲化单位。
Radiometric calibration of the data is performed toensure consistent dimensionless units at different times and locations.6.在地理坐标转换时,需要将雷达影像数据投影到统一的坐标系中。
During georeferencing, the radar image data needs to be projected onto a unified coordinate system.7.数据的辐射校正有助于减小不同时间和天气条件下影像的差异。
Radiometric correction of the data helps reducedifferences in images under different times and weather conditions.8.在预处理过程中,还需要考虑雷达影像的分辨率和几何精度。
船舶专业英语单词

船舶专业英语单词3-roller bending machine 三弯机Abandon v. 弃船Abolish v. 消除ABS 美国船级社Acceleration n. 加速度Accelerometer n. 加速度表Accommodate v. 容纳Accommodation deck起居(住舱)甲板Accuracy n. 精度Accurate synchrony device准同步装置acetylene cutter 气割机Acid-pickling n. 酸洗Acoustics n. 音响效果Adhesiveness n. 粘附力adjacent a.相邻的Adjust v. 调节Administration n. 行政管理Admit v. 接纳Adopt v. 采纳,采用affiliated factory 分厂,附属工厂aforementioned a.前述Aft a. adv. n. (在)船艉aft peak 艉尖舱after service 售后服务Ahead n. 正车air bottle 空气瓶air compressor 空压机air reservoir 气瓶air siren 汽笛air-tight test 气密实验alarm bell 警铃Alignment n. 找中all waves 全波Allowance n. 允值all position 全方位alternating current ( A.C.) 交流电Ammonia n. 氨Amplify v. 放大An automatic production line自动生产线analogous output 模拟输出analogue computer 模拟计算机Anchor n. 锚anchor chain (cable chain)锚链anchor handling 锚操纵Anchor windlass (chain windlass)起锚机anchorage buoy 系泊浮筒Angular n. 角度Antenna n. 天线anticorrosion precaution 防腐措施Apparatus n. (pl. apparatus orapparatuses) 仪器,器械,装置Appearance n. 外观Approval n. 批准,认可Approve vat. 认可Arbitrate v. 仲裁Arc n. 弧度arduous a.艰难的Arrange v. 布置,安排Asbestos n. 石棉Assemble v. 装配Assemble Language 汇编语言Assembly n. 装配Astern n. 倒车atmospheric survey 大气环流调查atomic power 原子能Atomize v. 雾化Authority n. 当局Automatic control device自动控制装置Automatic production line自动生产线automatic steering 自动操舵Automatic submerged arc welding自动埋弧焊automatic telephone 自动电话Aux. boiler 副锅炉Aux. engine 辅机Aux. engine room 辅机舱Aux. machinery 辅机auxiliary means 辅助手段auxiliary system 辅助系统axial push 轴向推力Backing n. 衬垫ballast piping 压载水管系ballast pump 压载泵ballast system 压载系统ballast water 压载水Base n. 基准Base point n. 基准点basic design 基本(方案)设计basic metal 母材battery unit 蓄电池组Beam n. 波束Beam n. 横梁Bearing n. 轴承bearing hole n. 轴承孔bedplate n. 机座bell set 铃组bending machine 冷弯机berth n. (水平)船台,(船上)床铺berth or slipway fabrication船台装配bilge n. 舱底水bilge keel 舭龙骨bilge plate 舭板bilge pump 舱底水泵bilge system 舱底水系统binary system 二进位制blank n. 毛胚block n. 分段block or section fabrication分段或总段装配blood vessel 血管blower 风机blue collar worker 蓝领,工人boat deck 艇甲板bollard n. 带缆桩bolt n. 螺栓bolthead n. 螺栓头bottom n. 船底bottom plate 底板bottom structure 底板结构bow n. 船艏bow &stern structure 艏艉结构bow section 艏段branch company 分公司,子公司branch system 分系统bridge n. 桥楼bridge control 桥楼控制broadcast n. v. 广播broadcast station 广播站bronze sleeve 青铜套筒bulbous bow 球鼻艏bulk cargo 散装货物bulk-cargo carrier 散装货船bulkhead n. 隔舱壁bulkhead structure 隔舱壁结构bushing n. 衬垫butt joint 对接接头cabin n. 舱室cable fixture 电缆夹具calculation n. 计算calculator n. 计算器calibrate v. 校正calibration n. 校正cam n. 凸轮cam follower 凸轮附件camber n. 梁拱camshaft n. 凸轮轴capstan windlass锚绞盘cargo n. 船货cargo oil 货油cargo –hold n. 货舱cargo-lifting n. 起货casing n. 罩壳cast iron piece 铸铁件casting n. 铸造cathode-ray type 阴极射线式CCS 中国船级社central control 集控centreline n. 中心线centrifugal a.离心的certificate n. 证书chain drive 链传动chain locker 锚链舱chain pipe 锚链管chain reaction 连锁反应chain stopper 制链器challenge n. v. 挑战chamfer v. 在边缘切斜面changeover switch 转换开关characteristics n.性能,特性,特征charge v. 充(电,气)check n. v. 检验chemical medium 化学介质China Classification Society(CCS)中国船级社China Ocean Shipping Company(COSCO) 中国远洋公司chip n. 芯片circle n. 圈子,团体class n. 船级classification n. 船级classification society 船级社cleanness n. 清洁度closed circulation 闭式循环clutch n. 离合器CO2 shielded arc welding 二氧化碳气体保护焊Coating n. 图层code n. 法典code display circuit 编码显示电路coefficients of ship form 船型系数cold processing 冷加工collision n. (船只)碰撞combustibility n. 可燃性combustion n. 燃烧combustion chamber 燃烧室combustion gas 燃气commanding telephone 指挥电话communication n. 通讯compartment n. 分隔舱compartment stuffing box隔舱填料函compass n. 罗经compass deck 罗经甲板compensate vt. 补偿competition n. 竞争completion drawing 完工图component n. 组成部分composition n. 成分组成compound excitation 复励comprehensive productivity综合生产能力compressed air 压缩空气compression (power)stroke n.压缩冲程computer control console计算机控制台conceptual a. 概念的condensation n. 冷凝conductor n. 导体connecting rod 连杆connection n. 接头constant voltage 恒压constitute v. 构成consumables n. 消耗品consumption n. 消耗contact v. 触发container n. 集装箱continuous deck 连续甲板contract n. 合同contradiction n. 矛盾control component 控制元件control console 控制台control unit 控制装置converse method 反装法convertor n. 转换器conveyor n. 传送带coolant n. 致冷剂coolant(cooling agent)n. 制冷剂cooler n. 冷却器cooling system 冷却系统cooperation n. 合作coordinate n. 坐标core enterprise 核心企业corrosion n. 腐蚀corrugated a. 波纹状的course n. 航向cover n. 药皮CPP drive 可调浆传动crank cheek 曲柄夹板crankcase n. 曲柄箱crankpin n. 曲柄臂crankshaft n. 曲轴crankweb n. 曲柄臂crew n. (全体)船员cross section 截面crosshead n. 十字头cultivate v. 培养,培育current n. 电流current n. 洋流,水流current-impulse frequencyconvertor 电流-脉冲频率变换器curve n. 曲线cutting n. 切割cylinder n. 气缸cylinder block 气缸体cylinder cover (cylinder head) 缸盖cylinder liner 气缸衬套cylinder oil 气缸油cylinder wall 缸壁data impulse 数据脉冲davit n. 吊艇架deadweight ton(DWT) n.载重量,吨载量Decca receiver 台卡定位仪deck n. 甲板deck girder 甲板材deck longitudinal 甲板纵骨deck machinery 甲板机deck plate 甲板板deck structure 甲板结构deckhouse 甲板室deform v. 形变deliver v. 交货,交船delivery n. 交船,交货delivery ceremony 交船典礼derrick n. 吊杆design stage 设计阶段designation n. 名称,牌号designation n. 目的地detail design 详细(施工)设计detect v. 探测detect v. 侦察detection n. 探测deviation n. 位移dial n. 刻度盘diameter n. 直径differentia n. 差异digital computer 数字计算机digital output 数字输出direct current(D.C.)直流电direct drive 直接传动direct telephone对讲电话,直线电话directional finder 测向仪directional instrument 指向仪器directional stability 航向稳定性disc n. 圆盘discharge n. v. 排水dispensable a. 非必要的dispute n. v. 争端,争执distribute v. 分布distribute v. 分配,配电distribution n. 配电distribution box 分电箱distribution panel 区配电板distribution switch 配电开关distribution system n. 配电系统division n. 划分DNV 挪威船级社Dock n. 船坞dock trial 码头试验docking winch 带缆绞车Doppler effect 多普勒效应Doppler frequency offset多普勒频移Doppler sonar log多普勒声纳计程仪double bottom 双层底double-action a.双作用down-vertical welding 下行焊draft(draught)n. 吃水drainage n. 疏水,泄水drawing n. 图纸drawing instrument 绘图仪drift v. 漂移drinking water 饮用水drip-proof type 防滴式drive n. 传动drive mechanism 传动机构drive mechanism 传动装置drive unit 传动装置driven shaft 从动轴dry v. 烘干drydock n. 干船坞dynamic –pressure type 水压式echo signal 返回信号echo sounder 回声测深仪economic effect 经济效益edge preparation 边缘加工edge processing 边缘加工edger n. 刨边机eject v. 喷射elapse v. (时光)消逝electric brain 电脑electric load 负荷electrical arc 电弧electrical compass 电罗经electrical drive 电力托动electrical energy 电能electrical impulse 电脉冲electrical power 电力electrical shedding 放电electrical signal 电器信号electrical slag welding 电焊渣electrical unit 电器装置electrical user 电器设备electrical-driven a. 电动的electrician n. 电工electricity outfitting 电舾electrode n. 焊条electromagnetic contactor电磁接触器electromagnetic induction 电磁感应electromagnetic log 电磁计程仪electromagnetic sensor 电磁传感器electronic computer 电子计算机electronics n. 电子(学)element n. 机械零件element n. 要素emerge v. 崛起,兴起emergency control 应急控制emergency network 应急电网emergency power station 应急电站emergency radio transmitter应急无线电发信机emergency steering 应急操舵emergency switchboard 应急配电板emergency telegraph 应急传令钟emergent discharge 应急排放emergent service 应急使用enclose v. 封闭encounter v. 遭遇energy convertor 换能器engine foundation (engine seat )机座engine frame 机架engine oil 机油engine outfitting 机舾engine space 机舱engineer n. 轮机员engineer n. 工程师engineering and technical team工程技术队伍engineer vessel 工程船engine-room 机舱ensure v. 确保enterprise n. 企业EO 无人机舱equipment n. 设备error n. 误差essence n. 实质,本质evolve v. 渐进,进化,演变excessive a. 过量的,极度的excitation n. 励磁excite v. 激励exhaust port 排气口exhaust stroke 排气冲程exhaust valve 排气阀expand v. 扩张,扩建expansion n. 展开图expansion stroke 膨胀(作工)冲程expansion tank 膨胀箱experiment n. 实验exterior force 外力extinguish v. 灭火F.O.meter 燃油流量计F.O.tank 燃油舱Fabricate v. 装配,制作fabrication n. 装配facile adaptability 灵活的适应性facsimile transmission(fax)传真fairing n. 光顺体,流线体fair-lead n. 导缆孔fashioned steel 型钢fast speed (rapidity)快速性fathometer n. 侧深仪feed v. 馈给feed circuit 馈电线路fillet seam 角焊缝fillet welding 角焊filter n. 过滤器. 过滤fine a. 纤细的finished product 成品fire alarm 火警fire hazard 火灾fire pump 消防泵fire-fighting system 消防系统fire-resistant a.耐火的fixed part 固定件flash signal light 闪光信号灯flat fillet seam 平角焊缝flexibility n. 挠性flexible coupling 挠性联轴节float launching 漂浮下水floatability n. 漂浮性floating positively 正浮floating production storageunit(FPSU)浮式生产储油轮flood v. 进水floodability n. 不沉性floor plate 肋板fluctuate v. 波动fluctuation n. 波动flush v. 清洗flushing agent 清洗剂flux n. 焊剂flywheel n 飞轮foam n. 泡沫folding machine 折边机for home use 国内用forced lubrication 强制润滑forced ventilation 机械通风fore perpendicular 艏垂线forecastle n. 艏楼foreign trade 外贸forging n. 锻造formation n. 构成,结构frame n. 肋骨framework n. 框架framing block 肋骨框架分段free end 自由端freeboard n. 干舷freighter n. 货船Freon n. 氟利昂frequency n. 频率frequency difference latching频率锁定frequency regulation 调频fresh water (F.W.)淡水fresh water production plant造水装置friction resistance 摩擦阻力fuel n. 燃料fuel nozzle 喷油嘴fuel oil 燃油fuel oil (F.O.)燃油fuel pipeline 燃油管系full-load a. 满载的full-load displacement 满载排水量funnel n. 烟囱galley n. 厨房gantry n. 龙门架gas cutting 气割gas tight seal 气密密封gas turbine engine 燃气轮机gas welding 气焊gear n. 齿轮gear drive 齿轮转动geo-physical propecting vessel地球物理探测船GL 西德劳氏船级社grant v. 给予……的权利gravity centre 重心gravity welding 重力焊groove v. 开坡口ground v. 接地group n. (企业)集团growth n. 生长,发育guarantee n. v. 保证general description 概述general-purpose a.通用的generating set 发电机组geometrical characteristics 几何特征geometrical principle 几何原理gravity launching 重力下水guided-missile frigate 导弹护卫舰gyro n. 陀螺仪gyro compass 陀螺罗经,回转罗经H.D.Heavy Machinery Co. Ltd.H.D.重机股份有限公司Halogen n. 卤素hand control手控hand level 手柄hand steering 手动操作hand wheel 手轮handle v. 操纵harbour n. 港口,停泊harbour generator 停泊发电机hardware n. 硬件hatch trunk 舱口围壁hawsepipe n. 锚链筒he water pressure system 水压系统headquarters n. 总部,厂部headroom n. 甲板间高度heat exchanger 热交换器heating n. 供暖heavy current n. 强电heavy oil 重油heel n. 横倾hereinbelow adv. 在下文high frequency 高频high-speed boat 高速艇horizontal a.水平的,卧式的horsepower(hp) n. 马力hose n. 软管hot processing 热加工hot work 火工hull n. 船体hull cleanness 船体光顺性hull construction 船体结构hull form 船型hull line 船体线型hull structure 船体结构human brain 人脑humidify v. 增湿hydraulic a. 液压的hydraulic fluid 液压流体hydraulic machine 液压机hyperbolic curve receive 双曲线定位仪identify vt.识别ignite v. 点火ignition n. 点火illumination n. 照明illustration n. 生动的说image display system 图象显示系统IMCO 政府间海事协商组织impact n. 冲击implication n. 含义impulsator n. 推动器,脉冲发生器impulse-type a.脉冲式的impurity n. 杂质inclination n. 倾斜inclination test 倾斜试验incline v. 倾斜index n. 索引indication n. 显示indicator n. 显示仪indicator n. 指示器indicator light 指示灯indicator valve示功阀inert gas 惰性气体inertia n. 惯性inertia platform 惯性平台inevitable a.不可避免的initial metacentric height 初稳心高inject n. 喷射injecting system 喷油系统injector n. 喷油器inner bottom longitudinal 内底纵骨inner bottom plate 内底板inner ring 内环input n. v. 输入inspector n. 质检员installation n. (船上)安装installation error 安装误差instancy speed 瞬时速度instrument n. 仪表,仪器insulating material 绝缘材料insulation n. 绝缘intake n. 吸入intake port 汲气口intake valve 进气阀integral casting 整体浇铸intention n. 意向intercommunication (intercom)n.内通,内部通讯interfering moment 干扰力矩intermediate bearing 中间轴承intermediate shaft 中间轴internal combustion engine 内燃机international authorities 国际当局Internet 因特网(国际互连网)introduce v. 引进,引入,介绍iron powder electrode 铁粉焊条jig n. 胎架joint design 联合设计journal n. 轴颈keel n. 龙骨keel plate 龙骨板keep station 定位kerosene test 煤油实验key enterprise 骨干企业kilohertz 千赫kinetic energy 动能knot n. 节labyrinth n. 迷宫,曲径land-based a. 路基的landing-place n. 码头lap joint 搭接接头large-computer(mainframecomputer) n. 大型(计算)机,主机lay v. 敷设length n. (一)节,(一)段level n. 液位level gauge 液位计level relay 液位继电器license n. 许可证life line 生命线life-belt n. 救生圈life-boat n. 救生艇life-jacket n. 救生衣life-or-death a.生死攸关的life-raft n. 救生筏life-saving n. 救生lifting capacity 起重能力light current 弱电lighting n. 照明light-ship displacement (light-load displacement)轻载排水量lines lofting 线型放样lines offsets 型值lines plan 线型图lining n. 衬垫load distribution 负荷分配load line mark 载重线标志load transfer 负荷转移local strengthening 局部加强locate v. 定位lock washer 锁紧垫片lofting n. 放样log n. 计程仪logical a.逻辑的long bridge 长桥楼longitudinal a.纵向的longitudinal (uniflow)scavenge直流扫气longitudinal bulkhead 纵隔舱壁longitudinal framing 纵向构架loop n. 回路loop antenna 环状天线Loran receiver 劳兰定位仪Loudspeaker n. 扬声器low speed 低速lower deck 下甲板LR 英国劳氏船级社lube oil 润滑油lube oil(L.O.)滑油lube oil pump 滑油泵lubricant n. 润滑剂lubricant film 润滑油膜lubricating oil 滑油lubrication system 滑油系统M.E.engine room 主机舱Machine v. 机加工machinery n. 机械machinery set 机组machinery workshop 机电车间machining n. 机加工machining workshop 机加工车间magnetic compass 磁罗经magnetic field 磁场magnetic needle 磁针magnetic object 磁性物体magnifier n. 放大器magnify v. 放大magnitude n. 大小main bearing 主轴承main engine (ME) 主机main generating set 主发电机组Main Group 1 第一大部分main hull 主船体main network 主电网main power station 主电站main switchboard 主配电板maintenance n. v. 维护,保养marker n. 厂商man power resource 人力资源management n. 生产管理maneuver v. n. 操纵maneuverability n. 操纵性maneuvering console 操纵台maneuvering system 操纵系统manual work 手工劳动manufacture n. &v. 生产,制造marine crane 船用起重机marine diesel engine 船用柴油机marine engineer 机电工程师marine engineering researchinstitute造机研究所marine geological research vessel海洋地质调查船mark v. 标出mast lightmaster controller 主令控制器Master degree 硕士学位material n. 材料material marking 下料mathematical a.数学的mathematical lofting skill数学放样技术maximum(max.)n. 最大means n. 手段,工具measurement laboratory 计量实验室measuring meter 测量仪表measuring point 测量点mechanical energy 机械能mechanical launching 机械下水mechanical processing 机加工mechanical unit 机械装置medium speed 中速medium wave 中波medium-computer n.中型(计算)机member n. 构件memory n. 储存器,内存memory and storage system储存系统merchant ship 民用船mercury n,水银meridian n. 子午线metacentre n. 稳心metal recovery 金属回收率metallic equipment 冶金设备microclimate n. 小气候microcomputer n. 微机microprocessor n. 微处理器midship n. a. adv. 舯部military ship 军用船miller n. 铣床minicomputer n. 小型计算机minimize v. 降至最低minus push 负推力minus value 负值miscellaneous a. 杂项的mobilize v. 动员model case 样箱model plate 样板model rod 样棒moderate a. 中型的modern enterprise system现代企业制度modus n. 操纵法(pl. modi)monitor v. 监视monitoring device 监控装置moor v. 系泊motive power 原动力motor n. 电动机mould loft 放样台mouth n. 河口moving part 运动件multi-purpose a.多用途的,综合的multi-stage n. 多级mutual benefit 互惠互利nautical mile 海里naval architect 造船设计师navigating instrument 导航仪器navigating zone 航区navigation computer 导航计算机navigation equipment 导航设备navigational light 航行灯navy n. 海军navy underway replenishment ship海军航行补给船NC cutting machine 数控切割机nerve cell 神经细胞nesting n. 套料network n. 电网nil n. 零,无NK 日本海事协会non –ferrous metal 有色金属non-restrictive a.自由的,不受限制的non-standard product 非标产品non-transparent a. 不透明的normal displacement 正常排水量normal shipping 正常营运nozzle n. 喷嚏numbering system 计算系统numeral n. 数字numerical control (NC)数控numerical control cutter 数控切割机nut n. 螺母observation n. 观察occasion n. 盛事,盛举ocean-going vessel 远洋船oceanographic research vessel海洋调查船offshore service 近海作业oil charging piping 注油管系oil consumption 油耗oil filling port 注油口oil mist 油雾oil refinery 炼油厂oil tanker 油船oil-resistant a.耐油的oil-tight n. 油密Omega/satellite integratednavigation instrument 奥米加/卫星导航系统one-side welding单面焊接,双面成形one-way a.单向的open chamber 开放式燃烧室open circulation 开放循环opening n. 开口operating cycle 工作周期operation n. 施工operation n. 运行,运转operation surroundings 作业环境operator n. 操纵员opportunity n. 机遇optical projector 光学仪器optics n. 光学orbit n. 轨道order n. v. 订单,定购oscillation n. 振荡oscillation current 振荡电流outboard adv. 向舷外outer appearance 外观outer ring 外环outfitting n. 舾装output n. 输出overload v. 过载owner n. 船东owner’s representative船东代表oxide n. 氧化皮paint n. 油漆pain-taking a.艰巨的painting n. 涂装painting n. 涂装,油漆工艺palletizing management 托盘管理parallel n. 并联v. 并车parallel of generators 发电机并车parameter n. 参数part n. 部件,机械部件part fabrication 部装particle n. 颗粒party n. (谈判或合同之)一方passage n. 通道passageway n. 通道passenger-cargo vessel 客货船performance n. 性能permanently adv. 永久的perpendicular n. 垂线personnel n. 全体人员personnel n. 人员,人事phase angle 相角phase sequence 相序phase –sensitive rectifier相敏整流器physical quantity 物理量physical-chemical experiment理化实验physical-chemical experimentalcenter理化中心实验室pillar n. 支柱pilot n. 驾驶员,领航员,舵轮pipe connection 管子接头pipe flange 管子法兰piping system 管系piston pin 活塞环piston pin 活塞梢piston stroke 活塞冲程pitch n. 纵摇plan n. 图纸plane n. 平面plane v. 整平planing machine 校平机plant n. (成套机电)设备platform n. 平台pneumatic tool 气动工具pointing of direction 指向poisonous gas 有毒气体pollution n. 污染poop n. 艉楼port n. 左舷portable light 手提灯postdoctoral centre 博士后工作站potable water 饮用水pour v. 涌入,源源不断power amplifier 功率放大器power plant 动力装置,(火力)电厂power station 电站power supply 电源,供电power system 电力系统,动力系统practice n. 习惯做法preamplifier n. 前置放大器pre-combustion chamber预燃燃烧室pre-heat v. 预热pressure container 压力容器pressure relay 压力继电器pressure sensor 压力传感器pressure tank 压力柜pretreat v. 预处理primary radio transmitter主无线电发信机prime mover 原动机primer n. 底漆primer painting 涂底漆principle dimensions 主尺度process n. 工艺,流程v. 加工,处理production efficiency 生产效率production line 生产线production procedure 生产程序program n. 程序projection plane 投影面prolong v. 延长promote v. 促进,晋升propeller n. 螺旋桨proportion n. 比例propulsion efficiency 推进效力propulsion plant 推进装置protection type 保护式provision n. 食品pump n. 汞purity v. 净化push rod 顶杆push-pull magnetic amplifier推挽磁放大器pyramid method 正装法quality assurance 质量保证quality control 质量控制quality management 质量管理quality policy 质量方针quay n. (顺岸式)码头quiescent a.安静的radar n. 雷达radio beacon station 导航台radio communication equipment无线电通讯设备radio directional finder 无线电测向仪radio message 无线电报radio receive 无线电接收机radio room 报房radio station 电台radio transmitter 无线电发信机radio wave 无线电波range n. 航程range v. 测距range display 航程显示器range unit 航程装置rated power 额定功率rated value 额定值reaction n. 反作用力reading n. 读数receiver n. 接收器reciprocating movement 往复运动rectification n. 矫正,整顿rectify v. 整流,滤波reduction gear 减速齿轮reduction gearbox 减速齿轮箱reduction unit 减速装置reduction with an astern clutch带到车离合器的减速reefer n. (俗)冷藏船,冰箱reflect v. 反射refrigerating plant 制冷装置register n. (机)验船师register vt. 登记,注册regulation n. 登记regulator n. 调整器relative humidity 相对湿度relative motion 相对运动relay contactor 继电器remains n. 残余remote control 遥控remote control station 遥控站rescue v. n. 救援rescue frequency 救援频率rescue transmitter 救援发信机resemble v. 相似reserve buoyancy 储备浮力reservoir n. 容器resistance n. 阻力resistance heat 电热阻rest v. 靠左retaining washer 保护垫片retake v. 回收,取回reversal n. 换向reverse v. 反向逆转reverse power 逆功率reversing system 换向机构revolution n. 旋转rigid a. 刚性的ring seam 环缝rock arm 摇臂roll n. 横摇roller machine 滚床room n. 余地rope n. 缆索rotary movement 旋转运动rotate v. 旋转rotating direction 旋转方向rotation n. 旋转度rotor n. 转子rough sea 波涛汹涌roughness n. 粗糙度routine n. 例行公事rpm 转速rudder n. 舵rudder angle indicator 舵角指示器rudder carrier 舵承,舵托rudder stock 舵轴,舵杆rudder stopper 舵角限制器rules n. 规范,规则running n. 经营管理rust preventative 防锈剂rust prevention 防锈rust removal 除锈rust-proof a.防锈的safeguard v. 捍卫safety valve 安全阀salt content 含盐量sanitary water 卫生水saturated steam 饱和蒸汽scavenge v. n. 扫气scavenge box 扫气箱scavenge flow 扫气气流scavenge pattern 扫气型式screen n. 荧光屏screw shaft 螺旋桨轴sea damage 海损sea trial 试航sea water (SW)海水sea-chart room 海图室seakeeping performances航海性能,试航性seal n. v. 密封sealing agent 密封剂sealing gasket 密封垫片sealing ring 密封圈search light 探照灯seasick a.晕船seat n. 座seating n. 基座section n. 总段self excitation 自励self-designed a.自行设计的self-regulated device 自我调节机构semi-conductor n. 半导体SEMT of France 法国热机协会senior engineer 高级工程师sensibility n. 灵敏度separation n. 分离separator n. 分离器serialize vt.使……成系列service n. 公共基础设施service engineer 服务工程师service life 使用寿命service tank 日用柜servo motor 伺服电动机settle v. 沉淀settling tank 沉淀柜shaft bracket 艉轴架,人字架shaft system 轴系shape processing 成形加工shear machine 剪切机shed v. 放射,散发sheer n. 脊弧sheet plate 薄板shell n. 壳板shell plating 外壳列板shell structure 外板结构ship equipment 船舶结构ship general 总体ship outfitting 船舾ship system 船舶系统shipbuilding n. 造船shipbuilding industry 造船工业shipbuilding technology researchinstitute 造船工艺研究所shipping n. 航运shipyard(yard)n. 船厂shop trial 车间实验shore electricity box 岸电箱short circuit 短路short wave 短波short-range a.短途的shot-blast v. 喷丸shot-blasting 喷丸处理side n. 船侧side girderside light 舷灯side plate 弦侧板side structure 船侧结构signal n. 信号signal light 信号灯signal processor 信号处理器silicon n. 硅silicon control rectifier(SCR)可控硅single bottom 单底single-action a.单作用single-rudder n. 单舵single-stage n. 单级single-screw n. 单桨site architect 现场造船师site supervisor 现场监控师sketch n. 草图slide-block n. 滑板,导块sliding distance 滑行距离slipway n. (倾斜)船台slipway taper 船台斜面small metacentric angle 小倾角socialist market economy社会主义市场经济software n. 软件soil n. 土壤SOLAS 国际海上人命安全公约SOS 遇难信号sound energy 声能sound insulation 隔音sound power telephone 声力电话sound speed 声速sound wave 声波sounder n. 测深仪sources of power supply 能源space n. 舱室space n. 空间spare gears 备品spare parts(spares)备件special power supply 特种电源speed indicator 航速指示器speed reduction 减速speed servo system 速度随动系统spring n. 弹簧squeeze n. v. 挤压stability n. 稳性stabilizer n. 减摇鳍stabilizing unit 减摇装置staff member 职员stage n. 级stainless steel 不锈钢stand v. 经受standard n. 标准standard displacement 标准排水量stand-by n. 备用stand-by generating set 备用发电机starboard n. 右舷start v. 动身,出发starting system 起动系统starting valve 启动阀state v. 说明state-specified a.部颁的station v. 驻扎steadiness n. 稳定性steam &aux. boiler system蒸汽与副锅炉系统steel plate pretreatment 钢板预处理steel structure 钢结构steel wire 钢丝steering gear 操舵装置steering gear 舵机steering gear room 舵机房steering mechanism 操舵机构steering wheel 舵轮stem n. 艏柱stern n. 船艉,艉柱stern tube 艉轴管stiffener n. 扶强,加强筋storage tank 贮存柜store-room n. 储藏室straight line 直线straight seam 直焊缝strength test 强度试验stringer n. 纵通材structural material 结构材料structure n. 结构,构件stud n. 螺柱stuffing box 填料函subway shield 地铁盾构suck v. 吸入suction (induction) stroke 汲气冲程suction port 吸入口sufficient a.足够的,充足的sum n. (数)二树之和supercomputer n. 巨型(计算)机superstructure n. 上层建筑supervision n. 监督,监造supply vessel 补给,工作船support n. 支撑物surface treatment 表面处理surveyor n. (船)验船师survive v. 幸存,死里逃生sustain v. 支撑,支持swirl chamber 涡流式燃烧室swirl resistance 涡流式阻力switch n. 开关symbol n. 符号symmetrical a.对称的synchro (selsyn)n. 自整角机synchro signal transmitter 自整角机讯号发送器synchronous device 同步装置synchronous follower 同步随动件talent n. 人才,有才能的technical staff 全体技术人员technical force 技术力量technical service 技术服务technical specification技术规格书technical term 技术术语telegraph n. 传令钟teleprinter n. 电传打字机teleperature relay 温度继电器temporarily adv. 临时地temporary emergency powersupply临时应急电源terminal n. 终端testing n. 调试testing facilities 测试设备testing instrument 测试仪器test & trials 试验与试航TEU reefer container ship 冷风集装箱船the ambient air 大气the application software 应用软件the block coefficient 方型系数the brake horse power (BHP)轴马力,制动马力the breath moulded 型宽the central processing unit (CPU)中央处理单元the centralized control room (thecontrol room)集控室the controllable pitch propeller(CPP)可调螺距桨the critical path method (CPM)各种计划节点配合the data base management system(DBMS)数据库管理系统the depth moulded 型深the design water plane 设计水线面the design water plane coefficient设计水面线系数the displacement coefficient 排水量系数the earth magnetic field 地球磁场the effective horsepower 有效马力the fire main 消防总管the fixed pitch propeller 固定螺距桨the future type 未来型the graphic processing software图像处理软件the intertia navigation system惯性导航系统the integral stud anchor chain 整体锚链the language system 语言系统the length B.P.两柱间长the length overall 全长the length W.L.水线长the living quarters 生活区the longitudinal prismaticcoefficient纵向菱形系数the metacentre of transversalinclination 横倾稳心the middle longitudinal crosssection舯横剖面the midship transversal crosssection coefficient 舯横截面系数the net registered tonnage 净登记吨位the North Pole 北极the office automation (OA)办公自动化the operating system (OS)操作系统the painting outfitting 涂装the parties concerned 有关方面the propulsion plant 推进装置the rated frequency 额定功率the rated horsepower 额定马力the roll period 横摇周期the satellite navigation system卫星导航系统the system software 系统软件the total longitudinal bend 总纵弯曲the total longitudinal strength 总纵强度the total tonnage 总吨位thermal mechanism 热力机械thermal stress 热应力thermometer n. 温度计thread v. 攻螺纹thrust bearing 推力轴承thrust end 推力端thrust ring 推力环thrust shaft 推力轴thyristor n. 硅可控整流器,可控硅tier n. (船)层TIG钨极惰性气体焊tightness test 密性试验time vt. 确定……的时间timing gear 准时机构title n. 职称,头衔tonnage n. 吨位top people 上层人物top side plate 弦侧顶板torsional vibration 扭振torsional moment 扭距TQC全面质量管理transceiver n. 收发报机transfer pump 输送泵transistor amplifier 晶体管放大器transistor controller 晶体控制器transistor loop 晶体管回路transmitter n. 发射机,发送器transportation n. 输送transversal a. 横向的transversal bulkhead 横隔舱壁transversal scavenge 横流扫气transversal stability 横稳性treatment plant 处理装置trend n. 趋势trial-and-error a.反复的通过试验找出错误的trim n. 纵倾trunk-piston n. 筒形活塞T-type joint T型接头tuition n. 学费turbine oil 透平油turbocharger n. 涡轮废气增压器turning ability 回转性turning circle 回转半径turning gear 盘车机构turning motion 回转twenty-foot equivalent unit (TEU)20英尺国际标准集装箱twin-engine incoporation 双机并车twinkle v. 闪烁twin-rudder n. 双舵twin-screw n. 双桨two-way a. 双向的ultra short wave 超短波UMS 无人机舱under voltage 欠电压uneven a. 不均匀uniform a. 均匀的unload v. 卸载upper deck 上甲板upset v. (船只)倾覆vacuum n. 真空validate vt. (使)生效valve mechanism 阀机构vaporize v. 汽化velocity n. 速度ventilating pipe 通风管ventilation &air-conditioningsystem通风与空调系统ventilator n. 通风机vertical a. 垂直的,直立式的vertical seam 垂直焊缝vertical welding 立焊vibration n. 振动viscosity n. 粘度visible range 视距visual telegraph 灯光传令钟visual-acoustical signal 灯光音响信号voltage n. 电压voltage latching 电压锁定voyage n. 航行waste heat 余热water head 压头water inlet pipe 进水管water jacket 水套water pressure test 水压试验water supply 水源,自来水water supply system 供水系统water vapour 水蒸气waterline 水线watertight a. 水密的water-tight test 水密试验wave impact 波浪冲击力resistance 兴波阻力wear n. v. 磨损weather post 露天部位weight calculation 重量计算welder n. 焊工,焊机welding n. 焊接welding laboratory(lab)焊接试验室welding machine 焊机welding procedure 焊接方法(工艺)welding seam 焊缝welding wire 焊丝well adv. 完全有理由wheel steering 随从操舵,舵轮操舵wheel house n. 驾驶室whereby adv. 靠那个wing buoyant tank 减摇水舱wire cable 钢索work n. 功working condition 工况working principle 工作原理working schedule 生产进度。
电阻率异常提取 英文
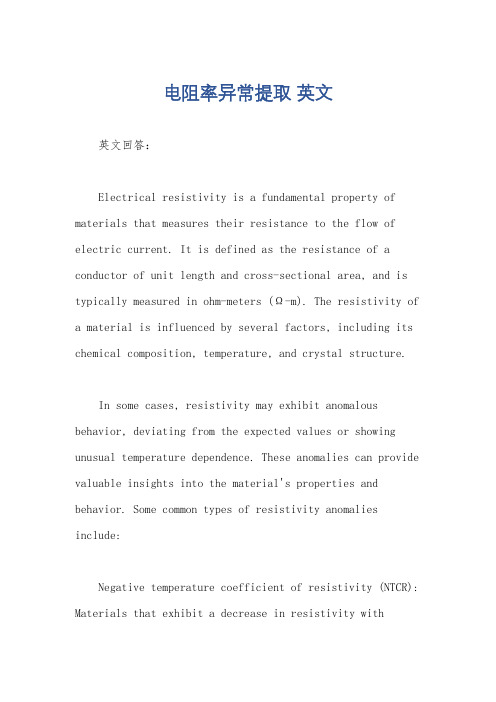
电阻率异常提取英文英文回答:Electrical resistivity is a fundamental property of materials that measures their resistance to the flow of electric current. It is defined as the resistance of a conductor of unit length and cross-sectional area, and is typically measured in ohm-meter s (Ω-m). The resistivity of a material is influenced by several factors, including its chemical composition, temperature, and crystal structure.In some cases, resistivity may exhibit anomalous behavior, deviating from the expected values or showing unusual temperature dependence. These anomalies can provide valuable insights into the material's properties and behavior. Some common types of resistivity anomalies include:Negative temperature coefficient of resistivity (NTCR): Materials that exhibit a decrease in resistivity withincreasing temperature. This behavior is typically observed in semiconductors and metallic alloys.Positive temperature coefficient of resistivity (PTCR): Materials that exhibit an increase in resistivity with increasing temperature. This behavior is commonly found in metals and insulators.Metal-insulator transition (MIT): Some materials undergo a transition from a metallic state with low resistivity to an insulating state with high resistivity at a critical temperature.Resistivity anomalies can be caused by various physical mechanisms, such as:Structural defects: Impurities, vacancies, and dislocations can disrupt the regular arrangement of atomsin a material, increasing its resistivity.Phase transitions: Changes in the material's crystal structure or electronic properties can lead to abruptchanges in resistivity.Magnetic ordering: In magnetic materials, the alignment of magnetic moments can affect the flow of electric current, resulting in resistivity anomalies.The study of resistivity anomalies has applications in various fields of science and engineering, including:Materials characterization: Resistivity measurementscan provide information about the chemical composition, crystal structure, and defect density of materials.Semiconductor device design: The temperature dependence of resistivity is crucial for designing semiconductor devices, such as transistors and solar cells.Geophysics: Resistivity surveys are used to explore the Earth's interior and detect underground structures.Medical diagnostics: Bioimpedance spectroscopy, which measures the electrical impedance of biological tissues,can provide insights into physiological conditions and disease states.In summary, resistivity anomalies refer to deviations from the expected resistivity behavior of materials. These anomalies can provide valuable information about the material's properties and behavior, and have applications in various fields of science and engineering.中文回答:电阻率是材料的一个基本特性,用来衡量它们对电流流动的阻力。
Combustible Gas Leak Detector R9300 操作手册说明书

DetectorInstructionTable of ContentsSafety ......................................................................................................2-3 Features . (3)Instrument Description (3)Specifications (4)Operating Instructions (5)Battery Replacement (6)Sensor Replacement (6)SafetyBefore using this instrument, read all safety information carefully. In this manual the word “WARNING” is used to indicate conditions or actions that may pose physical hazards to the user. The word “CAUTION” is used to indicate conditions or actions that may damage this instrument.If you are using your Combustible Gas Leak Detector as a result of a service call, chances are someone has either smelled a combustible gas leak or someone has reason to believe gas may be leaking. While your Combustible Gas Leak Detector is designed to function without producing sparks or otherwise igniting the gases it detects, the environment you are responding to probably has no such safeguards. Most combustible gas leaks are noticed long before concentration levels build up to the point that explosion hazards exist.If you feel an explosion hazard exists:• Arrange for evacuation of people in the areaAs a matter of routine, ventilate the area you plan to work in. Ventilation will help ensure the gas does not accumulate in large volume where it can attain its Lower Explosive Limit (LEL).Lower Explosive Limit (LEL): The point at which a combustible gas, when mixed with air, has developed the minimum concentration to combust when exposed to a source of ignition. The LEL is usually stated as a per-centage of gas in air, as a fuel-air-ratio, or as parts-per-million (PPM). Features• Detects a wide range of combustible gases including; gasoline, pro-pane, natural gas and fuel oil• High sensitivity detects small leaks• Designed for one-handed operation• 16” (406mm) gooseneck for hard to reach areas• User adjustable sensitivity wheel• Alarm set at 10% LEL for methane• Earphone jack for loud environments (earphones sold seperately)• Tricolor visual indicator• Audible (variable tick rate) and visual (LED) alarm indicators• User replaceable sensorInstrument Description1. Sensor Tip Guard & Sensor (internal)2. Gooseneck Probe3. Alarm Light4. Ready Light (Power-On)5. Power ON/OFF Slide SwitchSpecificationsDetected Gases: Methane, Natural Gas, Benzene,Ethane, Propane, Butane,Acetone, Alcohol, Ammonia,Gasoline, Jet Fuel, IndustrialSolvents, Lacquer, Paint Thinner,NapthaSensitivity 50 ppm methaneSensor Type Heated semiconductor gas sensorAlarm Audible (buzzer) and Visual (LED indicator) Alarm Limit Set @ 10% LEL for Methane (Can becalibrated for other concentrations orgases up to 40% LEL)Sensitivity Settings Adjustable WheelWarm-up Time Approx. 5 minsResponse Time Less than 2 secondsEarphone Jack YesPower Supply 3 “C” batteriesBattery Life Approx. 8 hoursProduct Certifications CEProbe Length 16” (406mm)Operating Temperature 32 to 122°F (0 to 50°C)Storage Temperature 4 to 140°F (-10 to 60°C)Operating Humidity Range 10-90%Dimensions 8.7 x 2.8 x 1.8” (221 x 72 x 46mm) Weight 18.4 oz (520g)Operating InstructionsSwitch on the Combustible Gas Leak Detector by sliding the ON/OFF but-ton and the READY light is glowing. The gas leak detector runs through a one-minute warm-up and self-zeroing sequence when it is first turned on in fresh air. The alarm of the instrument may be very loud without contact with any gas, that is caused the initial preset sensitivity.Rate (Sensitivity) AdjustmentEach time the instrument is put into service, you should conduct a quick functional test. Adjust the tick rate to non-alarm level. Then, simply ex-pose the sensor to a known leak, like a cigarette lighter, or pass the probe over a drop of combustible fluid. After the initial warm-up, the instrument can be used to detect combustible gases. When the sensor in the probe tip detects a combustible gas, the tick rate will increase and the instru-ment sounds a warbling tone while the ALARM light. As the concentration of gas increases, so does the tick rate.If the situation calls for quiet operation, or if background noise makes it difficult to hear the built-in speaker, you can use an earphone. The jackis at the top of the instrument. Note that listening to the alarm or tick through the earphone is very loud.If the READY light is off, the batteries are low. They should be replaced immediately. Low batteries will adversely affect the instrument’s reliability. See battery replacement procedures.Adjusting the Tick Rate (Sensitivity)The tick rate tells you when the sensor (in the tip of the instrument) is getting close to a gas leak. You can control the tick rate using the rotary wheel in the center of the instrument.• Move the wheel clockwise to increase the frequency• Move the wheel counter-clockwise to decrease the frequencyBattery Replacement1. Before replacing the batteries make sure to turn off your instrument.2. To remove the battery cover apply pressure and push away from the meter. Slide the cover out of the tracks.3. Replace all three batteries with new ones.4. Replace the battery cover by sliding it into place.Sensor ReplacementAlthough the sensor is designed to offer many years of reliable service, it may become inoperable if it is submerged in liquid or otherwise physically damaged.To replace sensor:1. Turn the instrument off2. Remove the upper tip guard by pressing straight up from the alignment notch that separates the two halves of the tip guard.3. This is a sturdy component, but use caution bending its leads.4. Pull the sensor straight up from its tip housing.5. Replace the sensor, pressing it straight in.6. Reassemble in reverse order.________________________________________________ ________________________________________________ ________________________________________________ ________________________________________________ ________________________________________________ ________________________________________________ ________________________________________________ ________________________________________________ ________________________________________________ ________________________________________________ ________________________________________________ ________________________________________________ ________________________________________________ ________________________________________________________________________________________________ ________________________________________________ ________________________________________________ ________________________________________________ ________________________________________________ ________________________________________________ ________________________________________________ ________________________________________________ ________________________________________________ ________________________________________________ ________________________________________________ ________________________________________________ ________________________________________________ ________________________________________________。
ngs测序原理

ngs测序原理Next-generation sequencing (NGS) is a high-throughput DNA sequencing technology that has revolutionized the field of genomics. It allows for the rapid and cost-effective analysis of the entire genome, transcriptome, or epigenome of an organism. In this document, we will explore the principles behind NGS sequencing and the key steps involved in the process.The NGS sequencing process begins with the isolation of DNA or RNA from the sample of interest. This nucleic acid is then fragmented into smaller pieces, which are subsequently sequenced using a variety of NGS platforms. The sequencing platforms use different methods to detect the sequence of each fragment, resulting in the generation of millions of short DNA sequences, known as reads.The next step in the NGS process involves the alignment of these short reads to a reference genome or transcriptome. This is done to determine the original sequence of the DNA or RNA fragments. Once the reads have been aligned, the next step is to assemble them into longer contiguous sequences, known as contigs. This process is particularly important for de novo sequencing, where no reference genome is available.After the assembly step, the contigs are further analyzed to identify genetic variations, such as single nucleotide polymorphisms (SNPs) and insertions/deletions (indels). These variations can provide valuable insights into the genetic diversity and evolutionary history of the organism being studied. Additionally, the NGS data can be used to quantify gene expression levels and identify differentially expressed genes in various biological conditions.One of the key advantages of NGS technology is its ability to generate massive amounts of sequencing data in a relatively short period of time. This high-throughput nature of NGS has enabled researchers to undertake large-scale genomic projects, such as the 1000 Genomes Project and The Cancer Genome Atlas (TCGA), which have significantly advanced our understanding of human genetics and disease.In conclusion, NGS sequencing has revolutionized the field of genomics by enabling the rapid and cost-effective analysis of the entire genome, transcriptome, or epigenome of an organism. The principles behind NGS sequencing involve the fragmentation, sequencing, alignment, assembly, and analysis of DNA or RNA fragments. The high-throughput nature of NGS technology has paved the way for large-scale genomic projects and has significantly advanced our understanding of genetics and disease.。
双频激光干涉仪设计要点概要

3System Design ConsiderationsChapter 3 System Design ConsiderationsIntroductionIntroductionAlthough there are many possible configurations of the laser and optics, all Agilent laser measurement systems have these basic parts in common:• A laser sourc e, to produce the two optical frequencies f1 and f2 and generate the reference signal. In discussions in this manual, f1 is the lower frequency and f2 is the higher.•Beam-directing optics, to direct all or part of the laser beam to each measurement axis of the system, using right-angle bends.•Measurement optics, to separate the two optical frequencies, direct them over the reference and measurement paths, and recombine them.•One receiver per measurement axis, to detect the difference in optical frequencie s and produce the measurement signal for that axis.•Electronics to convert the measurement and reference signals into displacement data.Two important characteristics of Agilent interferometers must be emphasized:•Only the change in relative position of the optics is detected.•Either optical component may move, as long as optical alignment is maintained. If the interferometer is fixed and the retroreflector is the moving component (toward or away from theinterferometer, motion with respect to its original position is detected. Conversely, if the retroreflector is fixed, the interferometer can be the moving component.Agilent laser position transducers can detect and measure all linear motions; that is, 3 degrees of the 18 degrees of freedom defined in the Glossary. Small angle measurements may be made by multiple measurements on the same axis.The measurement system is relatively insensitive to all other motions, as briefly described below. See Figure3-1.3-2User’s ManualChapter 3 System Design ConsiderationsIntroductionFigure 3-1. Possible component motions1.Motion of the receiver or laser head along the beam path (X has noeffect on the measurement since both f1 and f2 would exhibitDoppler shift.2.Small motions of the laser head, receiver, interferometer, orretroreflector in a direction perpendicular to the beam path (Y or Z have no effect on the measurement. The only restriction is thatsufficient light returns to the receiver.3.Angular motion (pitch or yaw of the laser head about the Z or Yaxis has the effects described below:a.It introduces a measurement error (cosine error.b.It may displace the laser beam so that insufficient light returnsto operate the receiver.4.Although the laser head or the receiver may be rotated in 90°increments about the beam axis (roll, other roll deviations from the four optimum positions degrade the measurement signal. If either the laser head or receiver is rotated 45° about the beam axis, all position information will be lost because the receiver will not be able to distinguish between the two frequencies.5.Angular motion of the receiver about the Y or Z axis has no effect onthe measurement, within alignment limits specified for thereceiver. (Receiver specifications are given in Chapter8,“Receivers,” of th is manual.6.Angular motions of the interferometer and retroreflector depend onthe particular components for limitations.User’s Manual3-3Chapter 3 System Design ConsiderationsAccuracy ConsiderationsAccuracy ConsiderationsSeveral factors outside the laser measurement system can affect system accuracy. These factors (the measurement environment, machine and material temperature, and the optics installation and their interrelationships must be understood in order to predict the performance of the system. Detailed descriptions and methods of compensation are given in Chapter15, “Accuracy and Repeatability,”of this manual.Generally, Agilent laser measurement systems offer automatic compensation for air environments and also for temperature changes of the work material. For a temperature-controlled environment(20±0.5° C, typical system accuracy using air sensor automatic compensation is 1.5ppm. Using the Agilent10717A Wavelength Tracker for compensation, the measurement repeatability is on the order of ±0.2ppm, depending on the environment. Determining What Equipment is NeededFirst, sketch out your optical configuration. Remember:•Each measurement axis (except for the Agilent10717A Wavelength Tracker requires an interferometer and associated retroreflector.•Each measurement axis after the first one requires a beam splitter.The number of beam splitters required is n-1, where n is thenumber of measurement axes.•If an Agilent10717A Wavelength Tracker is used, it counts as a measurement axis.•If a multiaxis interferometer, such as the Agilent10721A, Agilent10735A,Agilent10736A, or Agilent10737L,R is used, be sure the beam-directing optics you select will provide enough laser beam power to drive the receivers through the multiplemeasurement paths of the interferometer.•Beam benders should be arranged so their exiting beams are perpendicular to one polarization plane of the incoming laser beam. •Rotation of the beam during bending can result in problems due to the effects of polarization.•Beam splitters sho uld be arranged so:3-4User’s ManualChapter 3 System Design Considerations Determining What Equipment is NeededUser ’s Manual 3-5–one exiting beam is along the axis of the incoming beam, and the second beam is perpendicular to one polarization of theincoming beam, as described above for beam benders.–Each measurement axis requires an interferometer. The natureof the measurement(s to be made influences the interferometer choice.–Each measurement axis (including the Agilent 10717AWavelength Tracker requires a receiver. The interferometer used can influence the receiver choice. Note that theAgilent 5519A and Agilent 5519B laser heads include a built-in receiver .Then, from your layout, determine your optics needs. Choose the Agilent laser head, optical and electronic components accordingly. Decide on a compensation scheme and, finally, select cables. Table 3-1 summarizes the equipment choices. For advice and help, contact Agilent Technologies.Table 3-1. Equipment choices ComponentComment(sLaserOne required per system Agilent 5517ALowest velocity, largest size, 6mm beam Agilent 5517B25% higher velocity than Agilent 5517A, small size, 6mm beam Agilent 5517CStd5517C-0035517C-009Higher velocity than Agilent 5517A and 5517B, small size 6 mm beam diameter 3 mm beam diameter 9 mm beam diameter Agilent 5517DHighest velocity, small size, 6mm beam Agilent 5519A Largest size, built-in receiver and power supply used in theAgilent 5529A Dynamic Calibrator System and Metrologyapplications.Agilent 5519B Largest size, built-in receiver and power supply, higher velocity thanAgilent 5519A; used in the Agilent 5529A Dynamic CalibratorSystem and Metrology applications.Beam-Directing Optics Order as required to manipulate beam path to your configurationAgilent 10567A Dual-Beam Beam Splitter, useful in vacuum applications Agilent 10700A 33% Beam SplitterAgilent 10701A 50% Beam SplitterAgilent 10707A Beam BenderAgilent 10725A 50% Beam Splitter, no housingAgilent 10726A Beam Bender, no housingAgilent N1203C Agilent N1204CPrecision Beam TranslatorPrecision Horizontal Beam BenderDetermining What Equipment is NeededTable 3-1. Equipment choices(ContinuedComponent Comment(sBeam-Directing Optics (ContinuedAgilent N1207C Precision Vertical Beam BenderMeasurement Optics One Interferometer-plus-Reflector pair required per axis Agilent 10702A Linear InterferometerAgilent 10702A-001Same as above, but with wedge windows — required ifinterferometer is the moving component.Agilent 10703A Reflector — paired with Agilent10702AAgilent 10704A Reflector — paired with Agilent 10705AAgilent 10705A Single Beam InterferometerAgilent 10706A Plane Mirror InterferometerAgilent 10706B High Stability Plane Mirror InterferometerAgilent 10715A Differential InterferometerAgilent 10715A-001Differential Interferometer, turned configurationAgilent 10716A High Resolution InterferometerAgilent 10716A-001High Resolution Interferometer, turned configurationAgilent 10717A Wavelength Tracker (requires measurement receiver and cable Agilent 10719A One-axis Differential Interferometer, requires 3mm beam fromAgilent 5517C-003Agilent 10721A Two-axis Differential Interferometer, requires 3mm beam fromAgilent 5517C-003Agilent 10724A Plane Mirror ReflectorAgilent 10735A Three-axis InterferometerAgilent 10736A Three-axis InterferometerAgilent 10736A-001Three-axis Interferometer with Beam Bender Agilent 10737L Compact three-axis Interferometer, leftAgilent 10737R Compact three-axis Interferometer, rightAgilent 10766A Linear InterferometerAgilent 10767A Linear Retroreflector — paired with Agilent 10766A Agilent 10767B Lightweight RetroreflectorAgilent 10770A Angular InterferometerAgilent 10771A Angular Retroreflector — paired with Agilent 10770A Agilent 10774A Short Range Straightness Optics (matched set Agilent 10775A Long Range Straightness Optics (matched set3-6User’s ManualDetermining What Equipment is NeededTable 3-1. Equipment choices(ContinuedComponent Comment(sOptic Mounts Adjustable mounts simplify installation and alignment Agilent 10710B Use with Agilent 10700A, 10701A, 10705A, 10707AAgilent 10711A Use with Agilent 10702A, 10706A, 10706B, 10715A, 10716A Measurement Receivers One required per axis; one required with Agilent 10717AWavelength Tracker (if usedAgilent 10780C ReceiverAgilent 10780F Remote ReceiverAgilent E1708A Remote Dynamic ReceiverAgilent E1709A Remote High-Performance ReceiverReceiver Cables for use with Agilent10895A VME Axis board — one cable per system Agilent 10790A 5 meters longAgilent 10790B10 meters longAgilent 10790C20 meters longReceiver Cables for use with Agilent10885A PC Axis Board or Agilent N1231A PCIThree-Axis Board — one cable per receiverAgilent 10880A 5 meters longAgilent 10880B10 meters longAgilent 10880C20 meters longLaser Head Cables for Agilent5517A/B/C/D Laser Head used with Agilent10885A, 10889B, or N1231A axis boards (cable has a DIN connector for connecting to the Agilent10884A Power Supply to provide power to the laser head — one cable per systemAgilent 10881A 3 meters longAgilent 10881B7 meters longAgilent 10881C20 meters longLaser Head Cables for Agilent5517A/B/C/D Laser Head used with Agilent10885A, 10889B, or N1231A axis boards (cable has spade lugs for connection to a power supply to provide power to the laser head— one cable per systemAgilent 10881D 3 meters longAgilent 10881E7 meters longAgilent 10881F20 meters longLaser Head Cables for Agilent5519A/B Laser Head used with Agilent10887P Programmable PC Calibrator Board in the Agilent5529A system— one cable per system Agilent 10882A 3 meters longAgilent 10882B7 meters longAgilent 10882C20 meters longUser’s Manual3-7Determining What Equipment is NeededTable 3-1. Equipment choices(ContinuedComponent Comment(sAccessory Reflectors Order as required for your applicationAgilent 10728A Plane MirrorAgilent 10769A Beam Steering MirrorAgilent 10772A Turning MirrorAgilent 10773A Flatness MirrorHigh Performance Laser Head Cable for Agilent5517B/C/D Laser Head used with the Agilent10897B and 10898A VME Axis boards, and N1231A PCI Axis board (cable has a DIN connector for connecting to the Agilent10884A Power Supply to provide power to the laser head — one cable per systemAgilent N1251A 3 meters (9.8 feetAgilent N1251B7 meters (23.0 feetHigh Performance Receiver Cables for use with Agilent10897B and 10898A VME Axis boards, and N1231A PCI Axis board — one cable per receiverAgilent N1250A 5 meters (16.4 feetAgilent N1250B10 meters (32.8 feet3-8User’s ManualElectronic ComponentsElectronic ComponentsTransducer SystemsThere are three different types of electronics for Agilent laser transducer systems. These electronics use different backplanes and have different performance and outputs. Full details are given in the appropriate electronics system manuals.PC-Based ElectronicsThe Agilent10885A PC Axis Board is compatible with PC (ISA backplanes.Up to six Agilent10885As may be used in a single system.VME Compatible ElectronicsThe Agilent10898A High Resolution VMEbus Dual Laser Axis Board,Agilent10897B High Resolution VMEbus Laser Axis Board, and Agilent 10895A VMEbus Laser Axis Board are compatible with VME backplanes.The Agilent 10896B VME Laser Compensation Board is also compatible with VME backplanes and works with the Agilent 10895A. Up to six Agilent10895As and several Agilent10896As (up to one for each Agilent 10895A may be used in a single system.PC-Based PCI ElectronicsThe Agilent N1231A PCI Three-Axis Board is optimized for connection to a PMAC motion control system from Delta Tau®. It is a full size, Universal (3.3V and 5.0V signaling compatibility, 32-bit, 33MHz, PCI Rev. 2.2 compliant card for use in PC-compatible controllers as part of an Agilent laser interferometry position measurement system.User’s Manual3-9Electronic ComponentsCalibrator System ElectronicsAgilent5529A Dynamic CalibratorThe Agilent5529A Dynamic Calibrator is a laser system used to ensure the accuracy of a machine’s motion and positioning. Controlled through your PC (with Microsoft® Windows installed, the system is able to collect and analyze measurement data for anumber of measurements. The Agilent5529A Dynamic Calibrator typically includes the following electronic components:•Agilent5519A/B Laser Head•Agilent10886A PC Compensation board (optional, for automatic compe nsation•Agilent10887B PC Calibrator Board•Agilent10751C,D Air sensor and Agilent10757D,E,F Material Temperature sensor(s (optional, as required•Agilent10888A Remote Control units (optionalThe PC compensation boards provide the interfaces between the air and material temperature sensors and your PC. The boards convert the analog electrical voltages from the sensors to digital forms that the PC uses to calculate the compensation factors. These factors adjust for changes in the systems’ operating environme nts. Typical sensors used with each Agilent10886A PC Compensation board are theAgilent10751C,D Air Sensor and one to three Agilent10757D,E,F Material Temperature sensors.The Agilent10887B PC Calibrator Board enable the PC to perform laser calibrator-related functions with the Agilent5529A calibrator software.An Agilent Two-Axis 5529A/5529A Dynamic Calibrator and an Agilent55292A USB Expansion Module are also available. The USB software hosts up to five axes on one computer.3-10User’s ManualAdjustment ConsiderationsAdjustment ConsiderationsIn general, when aligning the Agilent optics, it will be necessary to adjust most or all of the optical components. Most optics are not referenced to their housings since simple adjustments by the user can usually provide optimum alignment. The Agilent10710B andAgilent10711A Adjustable Mounts should be used to provide the adjustment capability for most optical components.There are a few exceptions, however. Certain optics designed for multiaxis systems provide referenced housings. Installation and alignment of these optics depends on the optic; refer to specific instructions for these optics (Agilent10719A, Agilent10721A,Agilent10735A, Agilent10736A elsewhere in this manual.Other optics require you to fabricate your own mounts.In general, the alignment procedures are performed with all optical components in place. Your measurement system design should allow for adjustment of the laser, optics, and receivers during alignment. Laser beam and optics protectionThe laser measurement system requires protection against unintentional laser beam blockage and air turbulence problems. In some applications, such as machine tools, protection should be provided to prevent metal chips or cutting fluid from interfering with the measurements. Also, the optical components usually require protection to prevent contamination of the optical surfaces by oil or cutting fluid. In applications which are considered “clean”, protection may not be needed.If protection of the laser beam and optical components is required, there are two general types: moving-component protection and stationary component protection.In many applications, the only moving component is the interferometer or the reflector. Many of the beam benders are stationary and only direct the laser beam to themeasurement axis. In these cases, it is only necessary to provide fixed tubing for the laser beam and some type of sealed enclosure for the optics. Since only one laser beam of approximately 6mm (0.24inch in diameter is involved, relatively small diameter tubing can be used. Since either the interferometer or the reflector is moving during the measurement, protecting the laser beam and the moving components requires a telescoping cover or a cover that is self-sealing. A wide variety of commercially available protective covers are suitable for this purpose.User’s Manual3-11Adjustment ConsiderationsFigure3-2 illustrates techniques for protecting the laser beam and optical components with different types of protective covering. Note that the cover for the retroreflector allows the retroreflector to be moved very close to the interferometer. This helps minimize the deadpath errors. Chapter15, “Accuracy and Repeatability,” in this manual has more details on minimizing deadpath.Figure 3-2. Protective covers for optics and laser beam3-12User’s ManualAdjustment ConsiderationsFigure 3-3 shows a different type of protective cover. Again, the mechanical arrangement allows the retroreflector to be close to the interferometer at the closest point of travel, even though the telescoping cover is not entirely collapsible. Another type of protective cover is the flexible bellows. This is generally used for short travel distances.Figure 3-3. Collapsible spiral cover for movable retroreflectorUser’s Manual3-13System GroundingSystem GroundingBe sure to consider electrical grounding requirements as you plan and install your Agilent laser measurement. Grounding is important for safety reasons, but your grounding arrangement can also affect your laser system’s performance.Best practice requires that all system components that are connected to electrical ground should be connected to ground at a common point, not at separate points. Your electrical ground connections should radiate from a single point. Using more than one grounding point could create a ground loop, which could introduce an unacceptable level of electrical noise into the electronics.Signal grounds on each Agilent laser head, each Agilent receiver and the Agilent laser measurement system electronics are all connected to their respective chassis. To prevent ground loops they all should be grounded through one common point.The Agilent 10780C or Agilent 10780F receiver mounting is isolated from ground by using the nylon screws supplied.A system using VME electronics (Agilent10898A, Agilent10897B, and Agilent 10895A axis boards, PC electronics (Agilent 10885A axis board or PCI electronics(N1231A axis board should be grounded through the electronics power line.3-14User’s M anualLaser HeadLaser HeadOrientationAn Agilent laser head may be mounted in any orientation as long as it is positioned to direct the beam into the optical system parallel to or orthogonal with the machine axes being measured. See Chapter5, “Laser Heads,” in of this manual for more information about laser head orientation.Mounting plane toleranceThe plane defined by the three mounting feet on the laser head must be parallel to either the bottom or sides of the beam-splitters and of the beam-bender housings to within ±3°, and to the bottom or sides interferometers to within ±11°. This ensures that the polarization axes of the interferometers are oriented properly relative to the polarization vectors of the laser beam (Figure3-4. The laser head can be rotated in 90° increments about the beam axis (roll without affecting the system performance, but the measurement direction sense will change with each 90° rotation.Allow 50 mm (2 inches clearance around the laser head for easy servicing.Allow at least 100 mm (4 inches clearance at the back of the laser head for cable connections.User’s Manual3-15Laser HeadFigure 3-4. Laser position transducer mountingPointing stabilityTo maintain good pointing stability, it is good practice to use kinematic mounting principles. Refer to Chapter5, “Laser Heads,” in this manual for more information about laser head pointing stability.Thermal isolationBecause there is some heat dissipation from the laser heads, you should choose the mounting method and location with care. Where possible, mount the laser head away from the measuring area, to avoid any thermal effects.Vibration isolationSince the system measures only the relative motion between the interferometer and reflector, measurements are not affected by vibration along the beam axis of the laser source or the receiver.3-16User’s ManualOpticsWhen vibration of the laser head causes displacement of the beam (perpendicular to beam axis at an interferometer or receiver, the beam signal power can fluctuate. If this fluctuation is too great, insufficient beam signal will arrive at the receiver, causing a “measurement signal error.”Magnetic shieldingAgilent laser heads contain a permanent magnet. When installing an Agilent laser measurement system in an application sensitive to magnetic fields, shielding around the laser head may be required. MountingSee Chapter5, “Laser Heads,” in this manual for laser head installation and mounting instructions.The laser source in Agilent5517C-009 9-mm Laser Head is referenced to locations on the outside of the laser head, allowing the laser head to be installed in a predefined mounting location, minimizing the need for laser head alignment. A diagram of the mounting location for this laser head is presented in Figure 3-16.OpticsPlane of orientation with respect to laser headThe mounting plane tolerance of the optics to the laser head is the same as discussed in the paragraph titled “Mounting plane tolerance,”above. That is, the bottom or sides of the interferometers should be parallel to within ±l° of the plane defined by the laser head’s three mounting feet.Effect of optics on measurement direction senseThe orientation and configuration of the interferometers affects the measurement direction sense. The direction sense depends on which frequency is in the measurement path of the interferometer. For example, if f1 (lower frequency is in the measurement path and f2 (higher frequency is in the reference path and the optics are moving away from each other, the fringe counts will be INCREASING. This corresponds to using an Agilent5517A, Agilent5517B, orAgilent5517C Laser Head (mounting feet in horizontal plane with anAgilent10702A Linear Interferometer mounted with labels facing up and down (see Figure3-5. Interchanging f1 and f2 (e.g., rotating interferometer 90° in this example will result in the fringe counts DECREASING.User’s Manual3-17OpticsThe optical schematics for the interferometers, in Chapter7 “Measurement Optics,” show which frequency polarizations are in the measurement path.measurement direction sense will change. This rotation causes switching of frequencies in the measurement path.Configuration effectsMany of the distance-measuring interferometers can be configured to turn the beam at right angles. When configuring the linear,single-beam, and plane mirror interferometers to turn the beam, the measurement direction sense will be changed. This is because the measurement and reference paths are switched on the interferometers, therefore changing the direction sense. For more information, see the Chapter7, “Measurement Optics,” in this manual.3-18User’s ManualOpticsVibration isolation for opticsVibration of the optics along the beam can cause the fringe count in the laser measurement system electronics to fluctuate rapidly. Vibrations along this axis constitute real, measurable, displacements; you will have to decide if these fluctuating measurements are acceptable in your application. In extreme cases, however, the velocity of the optics may momentarily exceed the velocity limitation of the laser system, causing an error.When vibration occurs perpendicular to the beam, the beam signal power can fluctuate. If this fluctuation is too great, insufficient beam signal will arrive at the receivers, causing a “measurement signal error”.Loose mounting can cause the optics to move inappropriately during a measurement, causing a measurement error or loss of beam power.Elastic mounting can have the same effect as loose mounting. It can also be responsible for a “sag” offset in the optics’ positions. If there is vibration in the machine, an elastic mounting can transmit and amplify the vibration to the attached optic, possibly causing more errors. You should anticipate these effects and minimize them, if necessary, during the laser measurement system design process.Certain interferometers are inherently less susceptible to vibration effects than others. This is particularly true of differential-style interferometers such as the Agilent10715A, Agilent10719A, and Agilent10721A. The stability of these interferometers is due to the fact that both their reference beams and their measurement beams travel to external mirrors. Any motion of the interferometer itself that is common to both beams will not appear as a measurement. Of course, any vibration between the reference and measurement mirrors will constitute real, measurable, displacements.Adjustable mounts for opticsThe optical elements inside several of the Agilent laser measurement system optics are not precisely referenced to their housings. In most applications involving these optics, a few simple alignments during system installation can usually provide equal or better alignment than referencing the optics to their housings. Therefore, slight positioning adjustments of the unreferenced interferometers, beam splitters, and beam benders are needed for proper system alignment.User’s Manual3-19OpticsPositioning adjustments for most optics can be provided by using Agilent10710B or Agilent10711A Adjustable Mounts, as appropriate. These mounts allow adjustment of pitch and yaw of any attached optic. (Roll adjustment is typically not required, and can usually be avoided by careful optical system layout.For a listing of which Adjustable Mount supports which optic, see the Chapter9, “Accessories,” in this manual.In some applications, referenced housings can provide significant advantages. For example, the alignment requirements for certain multiaxis applications can be difficult or impossible to achieve without referenced housings. In those cases, interferometers such as the Agilent10719A, Agilent10721A, Agilent10735A, and Agilent10736A should be considered. These products have referenced housings and prealigned optical elements. Because they have individual mounting requirements, these products are not intended for use with the adjustable mounts described above. For more information about these optics, refer to Chapter7, “Measurement Optics,” in this manual. Fasteners for opticsAny optical component that fits an adjustable mount is supplied with mounting screws to mount it on the appropriate adjustable mount. Vacuum applications。
- 1、下载文档前请自行甄别文档内容的完整性,平台不提供额外的编辑、内容补充、找答案等附加服务。
- 2、"仅部分预览"的文档,不可在线预览部分如存在完整性等问题,可反馈申请退款(可完整预览的文档不适用该条件!)。
- 3、如文档侵犯您的权益,请联系客服反馈,我们会尽快为您处理(人工客服工作时间:9:00-18:30)。
a r X i v :p h y s i c s /0604199v 1 [p h y s i c s .i n s -d e t ] 25 A p r 2006physics/0604199D0Note CONF-5085(2006)Alignment of the Central DØDetector ∗Andr´e Sopczakon behalf of the DØCollaborationLancaster UniversityAbstractThe alignment procedure of the Silicon Microstrip Tracker,SMT,and the Central Fiber Tracker,CFT,is described.Alignment uncertainties and resulting systematic errors in physics analyses are addressed.1.IntroductionThe alignment of the DØtracking detectors is crucial for many physics analyses.The precision determination of the detector element positions improves the track reconstruction and the pre-cision measurements at the interaction point.This is particularly important for Higgs,top and B-physics,and for an impact parameter trigger.A general overview of the DØdetector[1]and operation[2]has recently been given.Figure1shows the central DØdetector,Fig.2gives the positions of the barrel wafers and F-disk wedges,and Fig.3displays a side-view of the SMT with barrels,F-disks and H-disks.Fig.1:Central DØdetector.The Silicon Microstrip Tracker(SMT)and the Central Fiber Tracker(CFT)are used for the central tracking.2.Method and alignment procedureThe basic method to align the wafers is to minimize axial-residuals and z-residuals(Fig.4).In the SMT,there are432barrel wafers,144F-disk wedges,and96H-disk wedges.The CFT encompasses304ribbons(each with256parallel scintillatingfibers,1.6or2.5m long).In total976elements require alignment.The initial position of the sensitive barrel elements were determined from metrology measurements.The alignment procedure is as follows:a track isfitted with all hits,except the hit from the sensitive element to be aligned.Then,axial-residuals and z-residuals of the hit on the wafer to be aligned,are determined.The pull(residual/error)is calculated and the corresponding χ2as a sum of pulls from all tracks on the wafer are determined.Theχ2is minimized as a function of the wafer position(three space coordinates and three angles).All wafer positions are determined and these positions serve as input geometry for the next iterative step.The iterative process continues until a convergence criterion is reached.A wafer is considered aligned if the shift divided by its uncertainty of a sensitive element between two iterations is less than a certain value.This value is called the‘shift limit’.Fig.2:Left:Barrel wafer positions.Right:F-disk wedges.Fig.3:SMT:Side-view of barrels,F-disks and H-disks.ZXYY waferaxial residualz residualFig.4:Definition of axial-and z-residuals for the SMT barrel wafers as the deviations of the fitted track (curved line)from the true hit position (marked by ×).For the barrel,Fig.5shows a histogram of the number of hits per wafer for 50,000events,and shows the shifts of each wafer between two consecutive iterations for the first and last iteration,illustrating the convergence.The corresponding plots for the F-disk and CFT are shown in Figs.6and 7.The number of tracks per event and the χ2per degree of freedom for the track reconstruction show an improvement after alignment (Fig.8).A shift limit of 0.07is applied.Entries432hits per wafer n u m b e r o f w a f e r s204060050001000015000Entries432 160.9 / 74Constant 13.39Mean -0.3100Sigma3.090shift x (µm)n u m b e r o f w a f e r s255075-20-1001020Entries432 83.03 / 32Constant 39.25Mean -0.2422E-01Sigma0.1419shift x (µm)n u m b e r o f w a f e r s50100-2-1012Fig.5:Left:number of hits per wafer for 50,000data events in the SMT barrel.Center:shifts of the 432wafers for the first iteration.Right:shifts for the last iteration.Entries 144hits per disk n u m b e r o f d i s k s510152002000400060008000Entries144 43.49 / 49Constant 2.061Mean -0.7239Sigma12.21shift x (µm)n u m b e r o f d i s k s1020-20-1001020Entries 144 48.66 / 30Constant 10.53Mean -0.4684E-01Sigma0.1446shift x (µm)n u m b e r o f d i s k s102030-2-1012Fig.6:Left:hits per disk for 50,000data events for the F-disks.Center:shifts of the 144wedges for the first iteration.Right:shifts for the last iteration.Entries 152hits per ribbon n u m b e r o f r i b b o n s510150250005000075000Entries304 72.29 / 68Constant 6.916Mean -3.587Sigma25.95shift x (µm)n u m b e r o f r i b b o n s51015-100-50050100Entries 304 71.30 / 75Constant 5.052Mean 0.1200Sigma0.7427shift x (µm)n u m b e r o f r i b b o n s510-2-1012Fig.7:Left:hits per ribbon for 50,000data events for the CFT.Center:shifts of the 304ribbons for the first iteration.Right:shifts for the last iteration.unalignedmean=16/eventnumber of tracks per eventnumber of tracks per evente v e n t se v e n t salignedmean=19/event020004000020406002000400060000204060chi2 / degree of freedom e v e n t sunaligned mean=34chi2 / degree of freedome v e n t saligned mean=22100020003000050100150250050007500050100150Fig.8:Left:number of tracks per event.Right:χ2per degree of freedom.Both,before and after alignment.3.ResidualsFor the barrel,the axial residuals before and after alignment are shown for all wafers,and for each individual wafer (Fig.9).Figure 10shows the corresponding plots for the F-disks.The residuals in the z-direction are given in Figs.11and 12.m e a n a x i a l r e s i d u a l (µm )m e a n a x i a l r e s i d u a l (µm )-40-202040Fig.9:Barrel axial residuals.Upper left:unaligned for all wafers.Upper right:aligned for all wafers.Lower left:unaligned for individual wafers.Lower right:aligned for individual wafers.wedge numberm e a n a x i a l r e s i d u a l (µm )m e a n a x i a l r e s i d u a l (µm )-40-202040Fig.10:F-disk axial residuals.Upper left:unaligned for all left:unaligned for individual wedges.Lower right:aligned for contain 12wedges.m e a n z r e s i d u a l (µm )m e a n z r e s i d u a l (µm )-500500Fig.11:left:all wafers.right:wedge numberm e a n z r e s i d u a l (µm )m e a n z r e s i d u a l (µm )-10001000Fig.12:F-disk residuals in z-direction.Upper left:unaligned for all wedges.Upper right:unaligned for individual wedges.Lower left:unaligned for all wedges.Lower right:aligned for individual wedges.Each of the 12indicated disks contain 12wedges.4.Optimization of convergenceIn order to improve the alignment process,the convergence speed,the accuracy and the depen-dence on the number of input events have been studied.Figure 13shows the number of wafers to be aligned as a function of the iteration number for a shift limit of 0.05.For this shift limit value no convergence is obtained.The required numbers of iterations for convergence with larger shift limits is also shown.The variation between two aligned geometries for the same data and two different shift limits has been studied.The differences in x and y-directions between two barrel geometries for one geometry produced for shift limit 0.07,and the second one for 0.08are shown in Figs.14and 15.The differences in x-direction between geometries produced with different shift limits are also shown in Fig.14as a function of the shift limit.For small shift limits the variation isbelow 3µm.While a very good precision of the relative wafer positions is obtained,a larger shift of the entire SMT position is possible even for a small variation of the shift limit parameter.The example inFig.15shows a relative shift in y-direction of the SMT wafers with σ=2.3µm,a very similar value as in the x-direction.However,the entire SMT is shifted between the two geometries by about 9µm.This corresponds to an oscillating behaviour of the axial shift as a function of the wafer id.iterations n u m b e r o f w a f e r s t o b e a l i g n e d50010005001000shift limitn u m b e r o f i t e r a t i o n s f o r c o n v e r g e n c eFig.13:Convergence of iterative process.Left:number of wafers to be aligned for shift limit 0.05as a function of the number of iterations.The alignment process does not converge.Right:number of iterations required for convergence as a function of the shift limit in the range 0.07-1.2.0.07/0.08dx (µm)n u m b e r o f w a f e r s50100150020shift limits i g m a o f d x (µm ) w .r .t s h i f t l i m i t 0.07Fig.14:Barrel difference in x-direction between aligned geometries produced with different shift-limits.Left:all wafers combined between shift limit 0.07and 0.08.Right:as a function of the shift limit w.r.t.0.07.0.07/0.08dy (µm)n u m b e r o f w a f e r s25507501020a x i a l s h i f t (µm )wafer id-10010-10010Fig.15:Left:barrel difference in y-direction between aligned geometries produced with different shift-limits.Right:corresponding axial shift.There are 6wafers per inner layers,and 12per outer layers beyond wafer id 144.In addition,the dependence of the wafer positions on the number of input events has been studied (Fig.16).Variations of the wafer positions in the aligned geometries below 5µm are expected for more than 30,000data input events.In a first step the shift limit has been reduced from 0.07to 0.05,and in a further step it has been reduced from 0.05to 0.04.Convergence was achieved by using the aligned 0.05geometry as starting geometry for the 0.04run.The convergence is illustrated in Fig.17.40k/50kdy (µm)n u m b e r o f w a f e r s255075-20020number of events useds i g m a o f d y (µm ) w .r .t 50k e v e n t sFig.16:Barrel difference in y-direction between aligned geometries produced with different shift-limits.Left:all wafers combined between 40,000and 50,000data input events.Right:as a function of the number of input events w.r.t.50,000events.iterations n u m b e r o f a l i g n e d w a f e r ssl=0.05sl=0.04500100050100150200iterations% o f a l i g n e d w a f e r s50100255075100125Fig.17:Convergence of iterative process for two additional alignment steps,starting with the aligned geometry for shift limit 0.07.Left:number of aligned wafers for shift limit 0.05and 0.04.Vertical lines correspond to 72h CPU time.Right:number of iterations required for shift limit 0.04(in %)w.r.t.the converged 0.05alignment.5.Uncertainties from procedure variationsIn order to determine the uncertainty in the alignment procedure the CFT geometries are com-pared for two cases a)when SMT and CFT were aligned simultaneously,and b)when the SMT was aligned first,and then the CFT was aligned.No significant effect on the alignment was observed (Fig.18).43.12 / 20Constant 29.59Mean -0.2754Sigma2.730∆axial (µm)n u m b e r o f r i b b o n s102030-100100204060-10-5051052.11 / 17Constant 52.25Mean 0.1480E-01Sigma1.526∆rad (µm)n u m b e r o f r i b b o n s2040-10-5051050100-10-50510Fig.18:Differences between geometries as explained in the text.Furthermore,in order to test the re-alignability and the corresponding systematic uncertainty,one wafer was misaligned by 50µm w.r.t.the original aligned geometry,and subsequently re-aligned.Remarkably,in the first iteration of the re-alignment 432elements were shifted.After re-alignment all elements were within 1µm of the original position.The geometries before and after re-alignment are compared to the original geometry(Fig.19).∆x (µm)n u m b e r o f w a f e r s∆y (µm)2004000500200400-101255075-0.90.90255075-1-0.10.8Fig.19:Upper:one wafer is shifted 50µm in x-direction.The other 431wafers remain at ∆x =∆y =0.Lower:all wafers are re-aligned within 1µm.7.Longevity /variation of active elementsFigure 20shows the variation of the number of disabled elements with time.During each data-taking shutdown several disabled elements were repaired.Fig.20:Fraction of disabled elements as a function of time.After data-taking shutdowns some additional wafers become operational and require alignment. Figure21shows an example of residuals for a single wafer(mean value of thefitted Gaussian) before and after alignment.lowP trackt16.03.6datesB1827B2827A813C794A+B1+B2+C84310.Time stability of detector alignmentThe detector alignment has been performed for different time periods.In order to determine the alignment precision two aligned geometries from different time periods are compared.An example is given in Fig.22for period1and5.The time stability of the detector for various time periods between April2002and December2004has been studied and no significant variation is observed(Fig.23).Period1(B1,B2)April20,20033(C)Jan.18,2004 5(E)Dec.18,200462.30 / 16Constant 57.89Mean-0.9177E-01Sigma 1.003∆axial (µm) numberofwafers50100150-1001050100150-4-2024Fig.22:Left:list of data sets and their date of data taking.Right:axial differences between wafers of the aligned geometries for time period1and5.No significant variation between the aligned geometries is observed.time periodsigma(µm)∆radwrtperiod124time periodmean(µm)∆radwrtperiod1-0.50.51Fig.23:Radial differences between wafers of the aligned geometries for time periods2to6w.r.t.period1(see Fig.22).No significant variation between the aligned geometries is observed.11.Local alignment:metrologyIn addition to the previously described global alignment,where wafers are considered ideal planes with no structure,the local alignment has been investigated.Local alignment refers to the alignment on a given sensitive element.As an example,the wafer geometry and the separation in z-direction is shown in Fig.25.Figure24illustrates the positions of thefiducial points on the wafers.This is particulary interesting as some wafers are made of two independent silicon plates.The precision in the distance∆z of twofiducial points for detector elements made of the two sensors is given in Fig.26from metrology.No indication of a shift in the survey between these plates is observed and variations are within±10µm.Fig.24:Positions offiducial points on the silicon wafers.Fig.25:Left:sensitive silicon area,HDI readout with SVX chips.Right:joining two silicon plates in support structure.P t values.Thefigure shows also the b-quark tagging efficiency versus the light quark mistag rate.The alignment uncertainty contributes to the systematic errors in several physics analyses. The effect of the alignment uncertainty has been studied,for example,by assuming a constant shift of10µm in radial direction outward(Fig.30)in order to estimate the impact on B-meson lifetime measurements.Only a small contribution to the systematic uncertainty from alignment in B-meson lifetime measurements is observed(Table3).phi (rad)DCA(µm)phi (rad)DCA(µm)unalignedbarrelσ=133µmDCA (µm)eventsalignedbarrelσ=82µmDCA (µm)events200400600-1000-5000500100020004000-1000-50005001000wafer numberDCA(µm)wafer numberDCA(µm)Fig.27:Upper left:displaced beamspot position in the r-φplane as a function ofφtrack.Lower left:corrected beamspot position.Center:DCA resolution for unaligned and aligned detector after beamspot correction.Right:Fig.28:Impact parameter resolution for the online Silicon Track Trigger(STT).Fig.29:Left:impact parameter resolution after alignment as a function of the transverse momentum.The beamspot size has been taken into account.Right:b-quark tagging performance using a neural network algorithm.∆rad (µm)n u m b e r o f w a f e r s20409.99951010.000520040099.51010.511∆axial (µm)n u m b e r o f w a f e r s204060-0.50.5x 10-30250500750-1-0.50.51Fig.30:For systematic error studies:comparison of geometries,10µm radial shift outwards.Table 3:Systematic uncertainties B s →J /ψφlifetime measurement.Alignment3Model for resolution46As examples of physics analyses where the detector alignment is crucial,results from lifetime measurements are shown in Figs.31and32.The signal(shaded region)is clearly visible over the background(dotted line).Fig.31:B-meson lifetime measurements.Left:B s→J/ψφ.Right:B s→D sµνX.0.250.30.35visible proper decay length (cm)N(µD*X)/N(µDX)Fig.32:Lifetime measurements.Left:B d.Right:Λb→J/ψΛ.13.Conclusions and outlookAbout850sensitive elements have been aligned.The alignment precision is close to design value(e.g.residuals:data20µm,simulation16µm).Some alignment parameters have been optimized.Systematic uncertainties of the alignment procedure are less than about10µm.The monitoring of the detector stability showed no significant movement.The alignment ensures excellent on-line and off-line b-tagging,and lifetime measurements,and is therefore crucial for Higgs,top,and B-physics.In spring2006,a new inner layer[3],Layer-0,at1.6cm from the interaction point will be installed inside the current vertex detector,which will significantly improve the impact parameter resolution,as illustrated in Fig.33.σ(IP)(µm)Fig.33:Expected layer-0(L0)improvement for the impact parameter(IP)resolution.Simulation and data(2a) overlap.Also shown is the impact parameter resolution without layer-1.References[1]DØCollaboration,physics/0507191,submitted to Nucl.Inst.Methods A,“The UpgradedDØDetector”.[2]R.Lipton,“DØTracking–From the Inside Looking Out”,these proceedings.[3]M.Weber,“A New Inner Layer Silicon Strip Detector for DØ”,these proceedings.AcknowledgementsI would like to thank the organizers of the TIME’05conference for their kind hospitality,and Tim Brodbeck,Aran Garcia-Bellido,Mike Hildreth,Alex Melnitchouk,Ulrich Straumann, Mike Strauss and Rick van Kooten for comments on the manuscript.Contributions from Guen-nadi Borrisov and Brian Davies are particularly acknowledged.20。