Diagnostics Used in Commissioning the IUCF Cooler Injector Synchrotron
PNOZ m EF 8DI4DO操作手册说明书

PNOZ m EF 8DI4DO}Configurable control systems PNOZmulti 2This document is a translation of the original document.All rights to this documentation are reserved by Pilz GmbH & Co. KG. Copies may be made for internal purposes. Suggestions and comments for improving this documentation will be gratefully received.Pilz®, PIT®, PMI®, PNOZ®, Primo®, PSEN®, PSS®, PVIS®, SafetyBUS p®,SafetyEYE®, SafetyNET p®, the spirit of safety® are registered and protected trademarks of Pilz GmbH & Co. KG in some countries.SD means Secure Digital1.2Using the documentation4 1.3Definition of symbols42.2Unit features6 2.3Front view73.2System requirements8 3.3Safety regulations8 3.3.1Use of qualified personnel8 3.3.2Warranty and liability9 3.3.3Disposal9 3.3.4For your safety94.2Functions10 4.3System reaction time10 4.4Block diagram105.2Dimensions in mm11 5.3Connecting the base unit and expansion modules116.2Connection13 6.3Download modified project to the PNOZmulti system1410.2Accessories221Introduction1.1Validity of documentationThis documentation is valid for the product PNOZ m EF 8DI4DO. It is valid until new docu-mentation is published.This operating manual explains the function and operation, describes the installation andprovides guidelines on how to connect the product.1.2Using the documentationThis document is intended for instruction. Only install and commission the product if youhave read and understood this document. The document should be retained for future ref-erence.1.3Definition of symbolsInformation that is particularly important is identified as follows:NOTICEThis describes a situation in which the product or devices could be dam-aged and also provides information on preventive measures that can betaken. It also highlights areas within the text that are of particular import-ance.INFORMATIONThis gives advice on applications and provides information on special fea-tures.2Overview2.1Scope of supply}Expansion module PNOZ m EF 8DI4DO}Jumper2.2Unit featuresUsing the product PNOZ m EF 8DI4DO:Expansion module for connection to a base unit from the configurable control systemPNOZmulti 2 .The product has the following features:}Can be configured in the PNOZmulti Configurator}Semiconductor outputs:4 safety outputsDepending on the application, up to PL e of EN ISO 13849-1 and up to SIL CL 3 of ENIEC 62061}8 inputs for connecting, for example:–E-STOP pushbutton–Two-hand button–Safety gate limit switch–Start button–Light beam devices–Scanner–Enabling switch–PSEN–Operating mode selector switch}LED for:–Error messages–Diagnostics–Supply voltage–Output circuits–Input circuits}Test pulse outputs used to monitor shorts across the inputs}Monitoring of shorts between the safety outputs}Plug-in connection terminals:Either spring-loaded terminal or screw terminal available as an accessory (see orderreference)}Please refer to the document "PNOZmulti System Expansion" for the PNOZmulti base units that can be connected.2.3Front viewKey:}0 V, 24 V: Supply connections}Inputs I0 – I7}Outputs O0 – O3}LEDs:–POWER–Run–Diag–Fault–I Fault–O Fault3Safety3.1Intended useThe expansion module may only be connected to a base unit from the configurable systemPNOZmulti 2 (please refer to the document "PNOZmulti System Expansion" for details ofthe base units that can be connected).The configurable system PNOZmulti 2 is used for the safety-related interruption of safetycircuits and is designed for use in:}Emergency stop equipment}Safety circuits in accordance with VDE 0113 Part 1 and EN 60204-1The following is deemed improper use in particular:}Any component, technical or electrical modification to the product}Use of the product outside the areas described in this manual}Use of the product outside the technical details (see Technical details [ 17]).NOTICEEMC-compliant electrical installationThe product is designed for use in an industrial environment. The productmay cause interference if installed in other environments. If installed in otherenvironments, measures should be taken to comply with the applicablestandards and directives for the respective installation site with regard to in-terference.3.2System requirementsPlease refer to the "Product Modifications PNOZmulti" document in the "Version overview"section for details of which versions of the base unit and PNOZmulti Configurator can beused for this product.3.3Safety regulations3.3.1Use of qualified personnelThe products may only be assembled, installed, programmed, commissioned, operated,maintained and decommissioned by competent persons.A competent person is someone who, because of their training, experience and current pro-fessional activity, has the specialist knowledge required to test, assess and operate thework equipment, devices, systems, plant and machinery in accordance with the generalstandards and guidelines for safety technology.It is the company’s responsibility only to employ personnel who:}Are familiar with the basic regulations concerning health and safety / accident preven-tion}Have read and understood the information provided in this description under "Safety"}And have a good knowledge of the generic and specialist standards applicable to the specific application.3.3.2Warranty and liabilityAll claims to warranty and liability will be rendered invalid if}The product was used contrary to the purpose for which it is intended}Damage can be attributed to not having followed the guidelines in the manual}Operating personnel are not suitably qualified}Any type of modification has been made (e.g. exchanging components on the PCB boards, soldering work etc.).3.3.3Disposal}When decommissioning, please comply with local regulations regarding the disposal of electronic devices (e.g. Electrical and Electronic Equipment Act).3.3.4For your safetyThe unit meets all the necessary conditions for safe operation. However, you should alwaysensure that the following safety requirements are met:}This operating manual only describes the basic functions of the unit. The expanded functions are described in the PNOZmulti Configurator's online help. Only use thesefunctions once you have read and understood the documentations.}Do not open the housing or make any unauthorised modifications.}Please make sure you shut down the supply voltage when performing maintenance work (e.g. exchanging contactors).Function description4Function description4.1Integrated protection mechanismsThe relay conforms to the following safety criteria:}The circuit is redundant with built-in self-monitoring.}The safety function remains effective in the case of a component failure.}The safety outputs are tested periodically using a disconnection test.4.2FunctionsThe expansion module provides additional inputs and additional semiconductor outputs.The function of the inputs and outputs on the control system depends on the safety circuitcreated using the PNOZmulti Configurator. A chip card is used to download the safety cir-cuit to the base unit. The base unit has 2 microcontrollers that monitor each other. Theyevaluate the input circuits on the base unit and expansion modules and switch the outputson the base unit and expansion modules accordingly.The online help on the PNOZmulti Configurator contains descriptions of the operatingmodes and all the functions of the PNOZmulti control system, plus connection examples.4.3System reaction timeCalculation of the maximum reaction time between an input switching off and a linked out-put in the system switching off is described in the document "PNOZmulti System Expan-sion".4.4Block diagram5Installation5.1General installation guidelines}The unit should be installed in a control cabinet with a protection type of at least IP54.}Fit the safety system to a horizontal mounting rail. The venting slots must face upward and downward. Other mounting positions could damage the safety system.}Use the locking elements on the rear of the unit to attach it to a mounting rail.}In environments exposed to heavy vibration, the unit should be secured using a fixing element (e.g. retaining bracket or end angle).}Open the locking slide before lifting the unit from the mounting rail.}To comply with EMC requirements, the mounting rail must have a low impedance con-nection to the control cabinet housing.}The ambient temperature of the PNOZmulti units in the control cabinet must not exceed the figure stated in the technical details, otherwise air conditioning will be required.NOTICEDamage due to electrostatic discharge!Electrostatic discharge can damage components. Ensure against dischargebefore touching the product, e.g. by touching an earthed, conductive sur-face or by wearing an earthed armband.5.2Dimensions in mm5.3Connecting the base unit and expansion modulesConnect the base unit and the expansion modules as described in the operating manualsfor the base modules.}The terminator must be fitted to the last expansion module}Install the expansion module in the position configured in the PNOZmulti Configurator.The position of the expansion modules is defined in the PNOZmulti Configurator. The ex-pansion modules are connected to the left or right of the base unit, depending on the type.Please refer to the document "PNOZmulti System Expansion" for details of the number of modules that can be connected to the base unit and the module types.6Commissioning6.1General wiring guidelinesThe wiring is defined in the circuit diagram of the PNOZmulti Configurator.Please note:}Information given in the Technical details [ 17] must be followed.}Use copper wire that can withstand 75° C.6.2ConnectionSupply voltageConnection examples for the input circuitConnection examples for semiconductor outputs*Two loads may be connected to each safety output with advanced fault detection, even onapplications in accordance with EN IEC 62061, SIL CL 3. Prerequisite: Feedback loop isconnected, shorts across contacts and external power sources are excluded (e.g. throughseparate multicore cables). Please note that, in the event of an error in the feedback loop,the safety system switches to a safe condition and shuts down all the outputs.Connection examples for feedback loop6.3Download modified project to the PNOZmulti systemAs soon as an additional expansion module has been connected to the system, the projectmust be amended using the PNOZmulti Configurator. Proceed as described in the operat-ing instructions for the base unit.NOTICEFor the commissioning and after every program change, you must checkwhether the safety devices are functioning correctly.Operation7OperationWhen the supply voltage is switched on, the PNOZmulti safety system copies the configur-ation from the chip card.The LEDs “POWER”, “DIAG”, “FAULT”, “IFAULT” and “OFAULT” will light up on the baseunit.7.1MessagesLegendLED onLED flashesLED off8Technical detailsApprovals BG, CCC, CE, GOST, TÜV, cULus Listed Application range Failsafefor Supply to the SC outputsVoltage24 VKind DCVoltage tolerance-20 %/+25 %Current load capacity at UB8,0 APotential isolation yesSupply voltagefor Module supplyinternal Via base unitVoltage24,0 VKind DCCurrent consumption39 mAPower consumption1,0 WMax. power dissipation of module4,50 WStatus indicator LEDInput voltage in accordance with EN 61131-2 Type 124 V DCInput current at rated voltage 5 mAInput current range2,5 - 5,3 mAPulse suppression0,5 msMaximum input delay8 msductor outputs4Switching capabilityVoltage24 VTyp. output current at "1" signal and rated voltage ofsemiconductor output2,00 APermitted current range0,00 - 2,50 AResidual current at "0" signal0,05 mAMax. transient pulsed current12 AMax. capacitive load 1 µFMax. internal voltage drop500 mVMax. duration of off time during self test330 µsSwitch-off delay 3 msIn accordance with the standard EN 60068-2-14Temperature range0 - 60 °CForced convection in control cabinet off55 °CStorage temperatureIn accordance with the standard EN 60068-2-1/-2Temperature range-25 - 70 °CClimatic suitabilityIn accordance with the standard EN 60068-2-30, EN 60068-2-78 Condensation during operation Not permittedEMC EN 61131-2VibrationIn accordance with the standard EN 60068-2-6Frequency5,0 - 150,0 HzAcceleration1gShock stressIn accordance with the standard EN 60068-2-27Acceleration15gDuration11 msMax. operating height above sea level2000 mAirgap creepageIn accordance with the standard EN 61131-2Overvoltage category IIPollution degree2Rated insulation voltage30 VProtection typeIn accordance with the standard EN 60529Mounting area (e.g. control cabinet)IP54Housing IP20Potential isolation between SC output and system voltage Type of potential isolation Basic insulationDIN railTop hat rail35 x 7,5 EN 50022Recess width27 mmMax. cable lengthMax. cable length per input1,0 kmBottom PC Front PC TopPCConnection type Spring-loaded terminal, screw terminal Mounting typeplug-inConductor cross section with screw terminals 1 core flexible0,25 - 2,50 mm², 24 - 12 AWG 2 core with the same cross section, flexible without crimp connectors or with TWIN crimp connectors 0,20 - 1,50 mm², 24 - 16 AWG Torque setting with screw terminals0,50 NmConductor cross section with spring-loaded terminals:Flexible with/without crimp connector0,20 - 2,50 mm², 24 - 12 AWG Spring-loaded terminals: Terminal points per connec-tion2Stripping length with spring-loaded terminals 9 mm Dimensions Height 101,4 mm Width 22,5 mm Depth 120,0 mm Weight105 gWhere standards are undated, the 2012-04 latest editions shall apply.8.1Safety characteristic dataNOTICEYou must comply with the safety-related characteristic data in order to achieve the required safety level for your plant/machine.SC inputs 2-channel PL e Cat. 4SIL CL 34,27E-1120SC inputs1-ch., pulsedlight barrier PL eCat. 4SIL CL 32,10E-1020with ad-vanced faultdetection PL e Cat. 4SIL CL 32,12E-1120SC outputs1-channel PL d Cat. 2SIL CL 22,29E-1020SC outputs2-channel PL e Cat. 4SIL CL 31,64E-1020All the units used within a safety function must be considered when calculating the safetycharacteristic data.INFORMATIONA safety function's SIL/PL values are not identical to the SIL/PL values ofthe units that are used and may be different. We recommend that you usethe PAScal software tool to calculate the safety function's SIL/PL values.Supplementary data9Supplementary data9.1Permitted ambient temperature Tamb dependent on the totalcurrent IsumOrder reference10Order reference 10.1Product10.2AccessoriesConnection terminalsTerminator, jumperSupportTechnical support is available from Pilz round the clock. Americas Brazil+55 11 97569-2804Canada+1 888-315-PILZ (315-7459)Mexico+52 55 5572 1300USA (toll-free)+1 877-PILZUSA (745-9872)Asia China+86 21 60880878-216 Japan+81 45 471-2281South Korea +82 31 450 0680Australia +61 3 95446300Europe Austria+43 1 7986263-0Belgium, Luxembourg +32 9 3217575France+33 3 88104000Germany+49 711 3409-444Ireland+353 21 4804983Italy+39 0362 1826711Scandinavia +45 74436332Spain+34 938497433Switzerland +41 62 88979-30The Netherlands +31 347 320477Turkey+90 216 5775552United Kingdom +44 1536 462203You can reach our international hotline on: +49 711 3409-444 ****************C M S E ®, I n d u r a N E T p ®, P A S 4000®, P A S c a l ®, P A S c o n fi g ®, P i l z ®, P I T ®, P L ID ®, P M C p r i m o ®, P M C p r o t e g o ®, P M C t e n d o ®, P M D ®, P M I ®, P N O Z ®, P r i m o ®, P SE N ®, P S S ®, P V I S ®, S a f e t y B U S p ®, S a f e t y E Y E ®, S a f e t y N E T p ®, T h E S P I r I T O f S A f E T Y ® a r e r e g i s t e r e d a n d p r o t e c t e d t r a d e m a r k s o f P i l z G m b h & C o . K G i n s o m e c o u n t r i e s . W e w o u l d p o i n t o u t t h a t p r o d u c t f e a t u r e s m a y v a r y f r o m t h e d e t a i l s s t a t e d i n t h i s d o c u m e n t , d e p e n d i n g o n t h e s t a t u s a t t h e t i m e o f p u b l i c a t i o n a n d t h e s c o p e o f t h e e q u i p m e n t . W e a c c e p t n o r e s p o n s i b i l i t y f o r t h e v a l i d i t y , a c c u r a c y a n d e n t i r e t y o f t h e t e x t a n d g r a p h i c s p r e s e n t e d i n t h i s i n f o r m a t i o n . P l e a s e c o n t a c t o u r T e c h n i c a l S u p p o r t i f y o u h a v e a n y q u e s t i o n s .Pilz develops environmentally-friendly products using ecological materials and energy-saving technologies. Offices and production facilities are ecologically designed, environmentally-aware and energy-saving. So Pilz offers sustainability, plus the security of using energy-efficient products and environmentally-friendly solutions.Pilz Gmbh & Co. KG felix-Wankel-Straße 2 73760 Ostfildern, Germany Tel.: +49 711 3409-0 fax: +49 711 3409-133 100X X X X -D E -0X 0-0-1-3-000, 2015-00 P r i n t e d i n G e r m a n y © P i l z G m b h & C o . K G , 20151002661-E N -03, 2016-02 P r i n t e d i n G e r m a n y © P i l z G m b H & C o . K G , 2015。
西门子重量测量技术:综合式重量测量组件和解决方案说明书
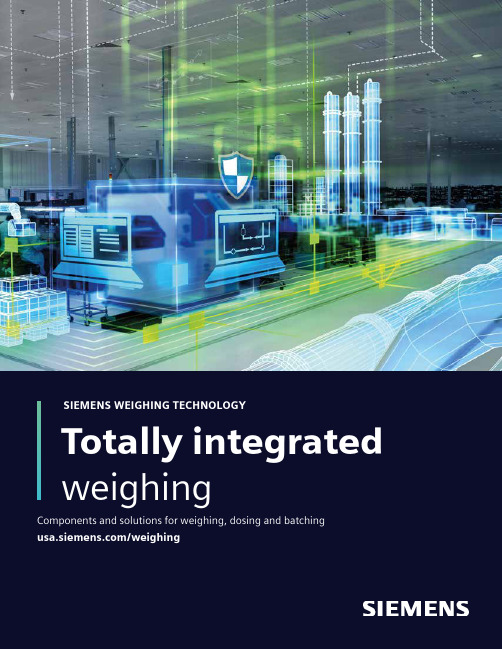
SIEMENS WEIGHING TECHNOLOGY Totally integrated weighingComponents and solutions for weighing, dosing and batching/weighingTotally integrated weighingSo, what do youneed measured?Weighing and dosing processes are of great significance inmany areas of industrial production.Whether for filling food and beverage containers or preparingrecipes for chemicals and pharmaceutical products: With oursolutions, you can count on absolute reliability and highestprecision.2So, what do you need measured? 21SIWAREX DB – your connectionto the digital world 8 2SIWAREX weighing modules –available for all requirements 6 Our SIWAREX weighing electronics at a glance 7 SIWAREX DB – your connectionto the digital world 8 Load cells and accessories – an overview 9 Non-automatic weighing 10 Check weighing 11Dosing, filling and batching applications 12 Loss-in-weight applications 13 Belt scales 14 Product overview 15 Solids flowmeters 16 Weighfeeder 17 Integrators – stand-alone 18 Integrators – SIMATIC-integrated 19 Process protection 20 3Sales and support 21 Siemens weighing trainings –on-site and online223Totally integrated weighingSeamless integrated weighing technology in the SIMATIC environmentSIMATIC PLCThe free standard example projects and function blocks offer full access to all parameter and data of the weighing electronics and allow a fast integration of the scales into existing automation programs and visualizations. In case of alarms, integrated hardware interrupts provide full transparency from the sensor to the controller. Following SIMATIC standards, a long term availability of all electronics and components is guaranteed.Based on a continuous handling concept across all different weighing electronics, a quick and easy integration of new types of scales is ensured.Userfriendly HMIThe HMI panel offers completely editable user interfaces. All relevant workflow processes, such as operating, monitoring and maintenance can be done directly from the central HMI, means there is no struggle with any additional black box on the machine.Besides that, the HMI offers a customer-friendly error handling: due to the detailed error message system, the errors will be shown in a clear text which leaves no ques t ions un-answered. You need more than one language to be displayed? No problem, foreign languages can easily be added via simple EXCEL ex- and import. But the HMIdoes not only offer comfort regarding the handling during daily business.The SIMATIC Comfort HMI, for instance can also be used as legal-for-trade main display.Continuous hardware conceptThe hardware concept considers the SIMATIC standards, which makes the wiring easy and guarantees a clear structure in the cabinet.By using SIMATIC standard controllers and I/O cards, you will achieve highest flexibility and scalability in your weighing environment. Besides that you can decide whether to install your components centrally or as d istributed system.1234Totally integrated weighingTotally integrated weighing2315SIWAREX weighing modules – available for all requirementsWhether central or distributed: our electronic weighing systems set standards. We offer i ntegrated solutions for seamless integration into the SIMATIC automation system underthe name SIWAREX. The weighing system can be easily adapted to meet your individual requirements with the SIMATIC standard components. Moreover, standardized interfaces, i ntegrated functions, and uniform tools allow for cost-effective configuration.Whatever your choice, you can count on a high degree of precision with SIWAREX and benefit from certifications according to OIML as well as a finely graded range of functions.Whether you need to produce accurate mixtures, ensure precise filling and loading, or perform tasks like legal-for-trade bagging, checking and dosing: SIWAREX WP351 is always the right choice. It’s the perfect fit for all auto -matic and non-automatic weighing applications.6Totally integrated weighingOur SIWAREX weighingelectronics at a glanceTotally integrated weighingSIWAREX DB – your connection to the digital worldAnalog limitations are left behind with SIWAREX DB. Instead of doing a parallel connection of the analog load cells and having no information about the single load cell, digitalization of each load cell offers full transpar-ency.SIWAREX DB makes the digitalization of the proven, most common and cost-effective strain gauge t echnology possible. For direct connection to a SIMATIC S7 or PCS7 PLC the SIWAREX WP weighing e lectronics are ideal.Seamless communication between SIWAREX and SIMATIC ensures less time and effort duringcommissioning. During operation the single channel monitoring, allowing wire break, impedance, and the current utilization of each load cell to be detected and corrected in the event of an error.SIWAREX DB supplies diagnostics data that are fully integrated in the SIMATIC environment. Error messages are displayed centrally on the SIMATIC controller and the HMI.Whether it’s the specific monitoring of weighing processes or extended diagnostics – in environments that have already been automated, the benefits of digitalization can be exploited to ever better effect.In the field of weight measurement, seamless integration from the field to the control levels ensures that data is record -ed and evaluated more comprehensively than previously possible. With SIWAREX DB, this level ofconnectivity now also covers the individual analog load cell.8Totally integrated weighingLoad cells and accessories – an overview9Totally integrated weighingNon-automatic weighingWeighing air cargo shipments reliablyCargologic AG is a leader in air cargo handling and has been operating at Zurich Airport for more than 50 years. To weigh individual freight units and complete unit load devices (ULDs), a floor model of a platform scale is used. The solution was a combi -nation comprised of four SIWAREX WL280 RN-S SA load cells and the SIWAREX WP231 weighing module.10Totally integrated weighingDosing, batching and bagging scaleA predefined set-point is completely automatically batchedby the SIWAREX electronic – typically by coarse and fine flow control.Dosing, batching and high-speed bagging (bagging m achines, multi component batching)The optimal choiceSIWAREX WP351 (SIMATIC ET 200SP)SIWAREX WP251 (SIMATIC S7-1200/stand-alone) SIWAREX FTA (SIMATIC S7-300/400/ET 200M) SIWAREX load cells and installation accessoriesExact weighing for fruit and vegetable packagingThe end customer of the plant builder RMA techniek was not able to conduct final check weighing at the end of the packaging process. A custom weighing solution in an integrated control environment had to change all that. The core element of the solution is the SIWAREX S7-1215C controller.Check weighingsolutions for tea, coffee, beverages, foods such as dairy and convenience products. A new machine for filling coffee capsules shall be projected and put in operation.Loss-in-weight applicationsFilling processes in washing powder productionMifa AG is Switzerland’s largest detergent and cooking oil manu-facturer and also produces detergents and householdcleaning products in liquid and powder form. A solution with Siemens weighing products has been found for the company’s outdated washing powder filling system that has done more than just positively affect productivity.Weighing and controlling the rate of materials on a conveyor belt is one of the most common procedures in process automation. Siemens has more than 35 years of experience weighing bulk materials on conveyors. You will find ourMilltronics belt scales from Siemens combine simple drop-in installation and low maintenance (no moving parts) withAccurate measuring for aRussian phosphate mineApatit Mining in Russia is the world’s largest producer of highgrade phosphate ore which is used as a raw material base for theproduction of phosphate-based fertilizers. The company waslooking to modernize and expand production and needed anaccurate and reliable system to weigh the ore to determine themine’s production rates. The picture shows MSI belt scale withMWL calibration system.Product overviewFlowguide sizes to fit any ASME or DIN flangeMeasuring accuracy is not affected by product buildup on the sensing plateDust-tight enclosure to prevent contamination or spillingQuick-release latches formaintenance and samplingSolids flowmetersSolids flowmeters in a fertilizer plantIn a fertilizer plant, crushed dolomite and crushed limestone are mixed in a reactor, whereby the mixing ratio of 1:3 must be maintained. The materials are conveyed from silos via screw conveyors into the solids flowmeters and brought t ogether in a bucket elevator for conveying into the reactor. The exact mixing ratio is ensured by the speed of the screw conveyors, which is controlled by a PLC, on the basis of the respective throughput rates of the solids flowmeters.WeighfeederReliable pleasure thanksto Siemens weighingtechnologyThe cigar manufacturer J. Cortès has two production sites inBelgium and about 3600 employees around the world. At its sitein Handzame, the company was looking for a fail-proof weighingsystem to maintain the necessary balance in termsof flavor. Based in Torhout, the industrial weighing expert Bas-cules Robbe therefore turned to Siemens. Together, they offered acomplete and customized solution.Analog interfacesCommunication such asProfiBus DP, Modbus or EthernetIntegrators – stand-aloneStand-alone integratorsOur integrators display primary speed and load values, as well as derived values of rates as analog mA output, alarm relay, or remote totalizer or through several industrial communications protocols.Belt scale modules for S7-300, S7- and via ET200M to S7-400 or PCS7-1200Analog interfaces like stand-aloneSIMATIC-integrated integratorsBeltscale electronics for seamless integration into the SIMATIC S7-1200 automation system. Flowrate, belt speed, load and status info are easily adapted into PLC system. Parametrization and calibration can be done by PLC, HMI or SIWATOOL software for Notebooks.Integrators – SIMATIC-integratedProcess protectionCustom engineeringSiemens provides custom-engineered products to solve your special application needs. From material compatibility challenges to unique size requirements,Siemens’ custom engineering team can help. Service around the worldPlants must function reliably at all times. Efficient and effective process instrumentation and analytics are an indispensable require-ment to this end. You also need to be certain of fast and competent service from your supplier. Siemens is a global company that reacts locally. Whether you require consulting, quick delivery, or installation of new devices, the Siemens network ofspecialists is available to you around the world, wherever your location.Support around the worldOur online support system offers rapid, com-prehensive assistance regardless of time or location. From product support to service information, Siemens Industry online support is your first choice – around the clock, the fast way 365 days a year.The fast way to your experts:Sales Support: 1-800-365-8766 Technical Support:/pisupportSales andsupport21Totally integrated weighingSiemens weighing trainings – on-site and onlineThe training center in Karlsruhe provides a wide range of industrial scales across nearly 200 square meters. From conveyor belt scales to dosing and bagging, a wide variety of SIWAREX application possibilities can be seen in action. More-over, the training center has a spacious training room andnumerous training models.Individual training conceptThe weighing trainings can either take place in the weighing technology center in Karlsruhe, but also directly on the customer’s site.In the standard training portfolio we offer trainings for– basic trainings with the following content: mechanic and electronic,get to know the basic terms and applications regarding load cells, mounting units and SIWAREX electronics– static applications, such as platform or hopper scales – available in the levels basic, advance, expert– mass dynamics applications regarding belt scales and weighfeeders – available in the levels basic, advance, expertBesides that you are also able to plan your training individually tailored to your needs in agreement with our training experts.22Totally integrated weighingTotally integrated weighingAll trainings can be offeredin different languagesA complete overiew of the training portfolio you find here:English: In addition to our on-site trainings we also offer you various onlinetrainings in English and German.Please contact us, if you are interested: ****************Also have a look at our various online tutorials we offer you in Youtube.Under the following playlist link, you will find a range of filmsconcerning calibration, dosing, filter settings, integration in SIMATICand much more.23Legal Manufacturer Siemens Industry, Inc.100 Technology Drive Alpharetta, GA 30005 United States of America Telephone: +1 (800) 365-8766 /piOrder No. PIBR-B10259-1021Subject to changes and errors. The information provided in this bro-chure contains descriptions or performance characteristics which, in case of actual use, do not always apply as described or which may change as a result of further development of the products. The desired performance characteristics are only binding if expressly agreed in the contract. Availability and technical specifications are subject to change without notice.All product designations may be trademarks or product names of Siemens AG or supplier companies, the use of which by third parties for their own purposes may violate the rights of the owners./weighing。
医护英语考试题及答案

医护英语考试题及答案一、选择题(每题2分,共20分)1. What is the most common symptom of the common cold?A. FeverB. CoughC. Sore throatD. All of the above答案:D2. Which of the following is NOT a vital sign?A. Blood pressureB. PulseC. Respiratory rateD. Body temperature答案:D3. What does the acronym "ICU" stand for?A. Intensive Care UnitB. International Clinical UnitC. Immediate Care UnitD. Inpatient Clinical Unit答案:A4. The term "diabetes" refers to a condition characterized by:A. High blood sugar levelsB. Low blood sugar levelsC. High blood pressureD. High cholesterol levels答案:A5. A patient is said to be "anemic" if they have:A. Too much red blood cellsB. Too few red blood cellsC. Too much white blood cellsD. Too few platelets答案:B6. What is the medical term for a surgical incision?A. IncisionB. AmputationC. BiopsyD. Excision答案:A7. Which of the following is a method of sterilization?A. Washing with soap and waterB. BoilingC. Using alcohol swabsD. All of the above答案:D8. The abbreviation "MRI" stands for:A. Magnetic Resonance ImagingB. Medical Radioactive ImagingC. Multiple Radioactive IndicatorsD. Medical Radio Imaging答案:A9. What is the primary function of the liver?A. To filter bloodB. To produce bileC. To regulate blood sugar levelsD. To produce red blood cells答案:B10. A "thermometer" is used to measure:A. Blood pressureB. Body temperatureC. Respiratory rateD. Pulse答案:B二、填空题(每题1分,共10分)11. The medical term for a broken bone is ____________.答案:fracture12. A person with a severe allergy to penicillin would be given a warning to avoid contact with this medication, known as a(n) ____________.答案:allergy alert13. The abbreviation "HIV" stands for Human Immunodeficiency ____________.答案:Virus14. A healthcare professional who specializes in the diagnosis and treatment of diseases of the heart is called a ____________.答案:cardiologist15. The process of removing waste products from the body is known as ____________.答案:excretion16. A patient's medical history is recorded in their____________.答案:medical record17. The practice of washing hands with soap and water to prevent the spread of disease is called ____________.答案:hand hygiene18. A(n) ____________ is a healthcare professional trained to provide emergency medical services.答案:paramedic19. The abbreviation "OT" stands for Occupational____________.答案:Therapy20. A patient's condition is assessed and monitored throughregular ____________.答案:check-ups三、简答题(每题5分,共30分)21. What are the four stages of the nursing process?答案:The four stages of the nursing process are assessment, planning, implementation, and evaluation.22. Explain the difference between a virus and a bacterium.答案:A virus is a microscopic infectious agent that can only replicate inside the living cells of an organism, while a bacterium is a single-celled microorganism that can exist independently and can be beneficial, neutral, or harmful to humans.23. What is the purpose of a stethoscope in medical practice?答案:A stethoscope is used by healthcare professionals to listen to the sounds produced by the body, such as the heartbeat and breathing, to diagnose or monitor various conditions.24. Describe the role of a registered nurse in a hospital setting.答案:A registered nurse in a hospital setting providesdirect patient care, administers medications, monitors patients' conditions, collaborates with physicians and other healthcare professionals, and educates patients about theirhealth conditions and treatments.四、翻译题(每题5分,共20分)25. 请将以下句子翻译成英文:医生建议他每天服用阿司匹林以预防心脏病。
ABB 1900 Series Circular Chart Recorders用户操作手册说明书

Agents Manual Circular Chart RecordersAll VersionsLenno, Italy – Cert. No. 9/90AStonehouse, U.K.0255Clarification of an instruction or additional information.Further reference for more detailed information orhazards are associated with equipment or property damage, it must be understood that operation of damaged equipment could, under certain operational conditions, result in degraded process system performance leading to personal injury or death. Therefore, comply fully with all Warning andInformation in this manual is intended only to assist our customers in the efficient operation of our equipment. Use of this manual for any other purpose is specifically prohibited and its contents are not to be reproduced in full or part without prior approval ofInstallation, operation, maintenance and servicing must only be carried out by suitably trained personnel and in accordance with the Normal safety precautions must be taken to avoid the possibility of an accident occurring when operating in conditions of high pressure Chemicals must be stored away from heat, protected from temperature extremes and powders kept dry. Normal safe handling procedures Safety advice concerning the use of the equipment described in this manual or any relevant hazard data sheets (where applicable) may be1Section Page1INTRODUCTION (12)PREPARATION ............................................................22.1Agents Upgrade Kit Identification . (23)FITTING ADDITIONAL PEN(S)....................................53.1Fitting a Standard Input/Output Module.............53.2Fitting a Motor and Pen Assembly.....................73.3Fitting a Display Board ......................................83.4Changing the Software Configuration. (94)RECORDER TO CONTROLLER UPGRADE ............104.1Fitting a Controller Faceplate ..........................104.2Fitting a Software Key .....................................114.3Changing the Software Configuration.. (125)FITTING A TRUE TIME EVENT MARKER ................135.1Fitting a Motor andTrue Time Event Marker (13)5.2Changing the Software Configuration (146)FITTING ADDITIONAL MODULES ............................156.1Fitting an Input and Relay Module. (157)ADDING ADVANCED SOFTWARE OPTIONS ..........177.1Software Key Identification ..............................177.2Fitting a Software Key . (188)COMMISSIONING LEVEL .........................................198.1Set Up Instrument Type Page(All Models Except C1950 SeriesPasteurizer Versions) (20)8.2Set Up Instrument Type Page(C1950 Series Pasteurizer Versions Only) (22)8.3Company Standard Page ................................238.4Input Assignment Page....................................248.5Pen Assignment Page .....................................258.6Input Calibration Page .....................................268.7Output Calibration Page ..................................288.8Pen Calibration Page.......................................298.9Display Set Up Page .......................................308.10Relay Test Page...............................................308.11Digital Input Test Page.....................................318.12Output Test Page.............................................318.13Diagnostics Page (329)INSTRUMENT REPAIR ..............................................339.1Non-volatile Memory ICs .................................339.2Microprocessor Board Replacement (33)CONTENTS1INTRODUCTIONThe COMMANDER 1900 Series of documentation is shown inFig. 1.1.The COMMANDER 1900 instrument can be configured for specific applications using different combinations of front panels and modules. The COMMISSIONING LEVEL is used in the setting up and calibration of the instrument.2PREPARATION2.1Agents Upgrade Kit Identification – Figs. 2.1 to 2.622PREPARATION……2.1Upgrade Kit Identification3…2PREPARATION…2.1Upgrade Kit IdentificationIdentify the upgrade kit required and the relevent faceplate positions as detailed in Fig 2.643FITTING ADDITIONAL PEN(S)To fit additional pen(s) perform all the following procedures:a)Fit module in required position – see Section 3.1.b)Fit the required motor and pen assembly – see Section 3.2.c)Fit the required display board – see Section 3.3.d)Access the COMMISSIONING LEVEL to change the instrument type and re-configure instrument – see Section 3.4.5…3FITTING ADDITIONAL PEN(S)…3.1Fitting a Standard Input/Output Modulec)If necessary, remove and discard knockout(s) from instrument case.d)Carefully clean out hole(s) and ensure all debris is removed from inside the instrument.e)Route the leads and cables into the case.f)Identify the module position.g)Fit the required module as detailed in Fig. 3.2.On completion proceed to Section 3.2.63FITTING ADDITIONAL PEN(S)…3.2Fitting a Motor and Pen Assembly – Fig. 3.3a)Fit the required motor and pen assembly as detailed in Fig. 3.3.On completion proceed to Section 3.3.7…3FITTING ADDITIONAL PEN(S)3.3Fitting a Display Board – Fig. 3.4a)Fit the required display board as detailed in Fig. 3.4. On completion proceed to Section 3.4.83FITTING ADDITIONAL PEN(S)…3.4Changing the Software Configuration – Fig. 3.5To enable the use of the additional pen(s), it is necessary to change a number of parameters in the COMMISSIONING LEVEL:a)Access the COMMISSIONING LEVEL– see Fig. 3.5.b)Select the Instrument Type frame and set the instrument type required – see Section 8.1.c)Assign the new inputs to a process variable, remote set point or position feedback in the Input Assignment P age– seeSection 8.4.d)Assign the new pen(s) to a process variable, remote set point or position feedback in the P en Assignment P age– seeSection 8.5.e)Calibrate the new pen(s) in the Pen Calibration Page– see Section 8.8.4RECORDER TO CONTROLLER UPGRADETo upgrade a recorder instrument to a controller instrument perform all the following procedures:a)Replace recorder faceplate(s) with controller faceplate(s) – see Section 4.1.b)Fit correct software key to allow access to control parameters – see Section 4.2.c)Access the COMMISSIONING LEVEL to change the instrument type and re-configure instrument – see Section 4.3.4.1Fitting a Controller Faceplatea)Fit a controller faceplate as shown in Fig. 4.1.On completion proceed to Section 4.2.4RECORDER TO CONTROLLER UPGRADE…4.2Fitting a Software Keya)Fit the required software key as shown in Fig. 4.2.b)Switch on and configure the instrument using the Advanced Software Options manual.On completion proceed to Section 4.3.…4 RECORDER TO CONTROLLER UPGRADE4.3Changing the Software Configuration – Fig. 4.3To use the instrument as a controller, it is necessary to change a number of parameters in the COMMISSIONING LEVEL:5FITTING A TRUE TIME EVENT MARKERTo fit a true time event marker perform all the following procedures:a)Fit pen motor in position 4 and special pen arm assembly to pen bracket 4 – see Section 5.1.b)Access the COMMISSIONING LEVEL to select event pen option – see Section 5.2.c)Set up pen 4 event marker sources in Set Up Range Page, BASIC CONFIGURATION LEVEL.5.1Fitting a Motor and True Time Event Markera)Fit a new motor in position 4 on the motor plate and a true time event pen arm assembly to pen bracket 4 (black identificationband) – see Fig 5.1.On completion proceed to Section 5.2.…5FITTING A TRUE TIME EVENT MARKER5.2Changing the Software Configuration – Fig. 5.2a)Switch on the instrument.b)Access the COMMISSIONING LEVEL – see Fig. 5.2.c)Set the Event Option Enable frame to Yes – see Section 8.1.d)Set up pen 4 event marker sources in the Set Up Pen Range Page, BASIC CONFIGURATION LEVEL.6FITTING ADDITIONAL MODULES…6FITTING ADDITIONAL MODULES…6.1Fitting an Input and Relay Modulec)If necessary, remove and discard knockout(s) from instrument case.d)Carefully clean out hole(s) and ensure all debris is removed from inside the instrument.e)Route the leads and cables into the case.f)Identify the module position.g)Fit the required module as shown in Fig. 6.2.7ADDING ADVANCED SOFTWARE OPTIONSre b m u N t r a P ye K e r a w tf o S ep y T n o i t p O n o i s r e V r e d r o c e R no i s r e V r e l l o r t n o C 1•s r e d r o c e R d n a s r e l l o r t n o C d r a d n a t S r e z i l a t o T 36330/0091C 1330/0091C k a o S /p m a R 5–2330/0091C re m i T &h t a M A 7330/0091C 3330/0091C r e m i T &h t a M ,r e z i l a t o T B 8330/0091C 4330/0091C ,k a o S /p m a R ,r e z i l a t o T re m i T &s h t a M C –5330/0091C 2•s n o i s r e V r e z i r u e t s a P re d r o c e R t c u d o r P t o H J 1591G 3530/0091C r e l l o r t n o C /r e d r o c e R t c u d o r P t o H R 2591H –4530/0091C t c u d o r P d l o C &t o H R 3591r e l l o r t n o C /r e d r o c e R J –5530/0091C 3•s r e l l o r t n o C t r o t e R K0691K –6530/0091C L 0691L–7530/0091C n o i t a m r o f n i g n i t a r e p o d n a g n i m m a r g o r p l a n o i t i d d a r o f V D A –0091C /M I o t r e f e R 1•n o i t a m r o f n i g n i t a r e p o d n a g n i m m a r g o r p l a n o i t i d d a r o f S A P –0091C /M I o t r e f e R 2•no i t a m r o f n i g n i t a r e p o d n a g n i m m a r g o r p l a n o i t i d d a r o f C P M –0091C /M I o t r e f e R 3•To add additional software options perform all the following procedures:a)Fit correct software key to allow access to control parameters.b)Configure the instrument using the Advanced Software Options Manual , IM/C1900–ADV7.1Software Key Identification – Fig. 7.1The software key is a p.c.b. assembly which must be fitted to the main processor board to enable access to the additional programming pages required to configure the instrument.Table 7.1 Software Key Identification…7ADDING ADVANCED SOFTWARE OPTIONS8COMMISSIONING LEVEL19…8COMMISSIONING LEVEL8.1Set Up Instrument Type Page (All Models Except C1950 Series Pasteurizer Versions)20218COMMISSIONING LEVEL …Display OptionThis frame allows the second and third faceplates on specific instruments to be enabled or disabled:YES –enable NO –disable The dIS.O Pt frame is only displayed on the following versions :recorder versions –1913 and 1914controller version –1914.Note.The display option is set automatically according to the instrument type and must Update DoneThe ACtIVE frame is displayed momentarily as any changes are stored in the non-volatile memory. dONE is displayed on completion.Return to Instrument Type frame.Note.The parameters changed in this Page are updated during the start-up sequence.ON again.22…8COMMISIONING LEVEL8.2Set Up Instrument Type Page (C1950 Series Pasteurizer Versions Only)Page Header – Instrument TypeTo advance to the Company Standard Page Chart TypeSelect the controller/recorder chart type required.1951.xcontroller/recorder chart type:J ER/C type chart –recorder K PX105 and PXR105 type chart –recorder C Special chart–recorder1952.x1953.xcontroller/recorder chart type:R ER/C type chart –controller S PX105 and PXR105 type chart –controller D Special chart–controller Single or Dual RTD.Select either single or dual (second divert) RTD.See User Guide (Pasteurizer Versions) Section 7 for further information on the use of a second divert RTD.Update DoneThe ACtIVE frame is displayed momentarily as any changes are stored in the non-volatile memory. dONE is displayed on completion.Return to Instrument Type frame.Note.The parameters changed in this Page are updated during the start-up sequence.ON again.238COMMISSIONING LEVEL …8.3Company Standard PagePage Header – Company Standard Page To advance to the Input Assignment PageSet Company StandardSelect YES to reconfigure the instrument to the company standard settings.The ACtIVE frame is displayed momentarily as any changes are stored in the non-volatile memory. dONE is displayed on completion.Note.If the software in use is earlier than version 5, reconfiguring the instrument to the frequency must be re-set in the Crystal Type frame below.Note.If the software in use is version 2101 issue 1 or later, the crystal frequency is fixed Mains FilterSelect the mains filter of the supply used to ensure maximum noise rejection on analog inputs.Security TypeSelect type of security required in OPERATOR LEVEL :A –access to control and program settings with correct security code–no access to control or program settings even with correct security code.Note.The security system can be overridden and the COMMISSIONING LEVEL accessed,Crystal TypeSelect crystal type fitted on main processor board:8MEG –8 Megahertz crystal –12 Megahertz crystalNote.The parameter selected in this frame is dependent on the type of crystal fitted on the AD-FAIL message.Note.If the software in use is version 2101 issue 1 or later, the crystal frequency is fixed Return to Company Standard frame.Note.The crystal frequency is read during the start up procedure. If the frequency has a) Return to the Company Standard frame.b) Switch the instrument OFF then ON.…8COMMISSIONING LEVEL 8.4Input Assignment Page24258COMMISSIONING LEVEL …Page Header – Pen AssignmentTo advance to the Input Calibration PagePen 1 TypeSelect pen function required:trENd –trend pen –event penNote.The event pen and the true time event marker are separate functions and only the Event Pen can be selected in this page. The T rue Time Line Event Pen Option allows marking on the same time line as the red pen and requires a special pen arm and motor assembly – see Section 5.Pen 1 SourceSelect the signal to be recorded on pen 1 – the selections in this frame relate to instrument type.Pen 2 TypeRepeat as for Pen 1 Type , if applicable.Pen 2 SourceRepeat as for Pen 1 Source , if applicable.Pen 3 TypeRepeat as for Pen 1 Type , if applicable.Pen 3 SourceRepeat as for Pen 1 Source , if applicable.Pen 4 TypeRepeat as for Pen 1 Type , if applicable.Pen 4 SourceRepeat as for Pen 1 Source , if applicable.Return to Pen Assignment frame.8.5Pen Assignment Page26…8COMMISSIONING LEVEL8.6Input Calibration PagePage Header – Input CalibrationTo advance to the Output Calibration Page Select InputSelect input required.Calibrate 100mV EnableIf 100mV calibration is required, set the input links to mV – see Section 4 of Installation Guide .Connect a d.c. voltage calibrator to the selected input and apply 100mV.Select CAL-Y to enable 100mV calibration.If 100mV calibration is not required select CAL–N .Calibrate 100mVIf calibrate 100mV is enabled, (–) is displayed in the lower display during calibration. dONE is displayed on completion.Calibration PassIf calibration is successful, the selected input displayed on the upper display and the input value displayed on the lower display.Calibration FailCalibration failure may be due to the following:incorrect input link setting incorrect input signal applied faulty non-volatile memory.Re-calibration EnableEnable or disable 100mV re-calibration:YES –repeat 100mV calibration NO –advance to the next frame.Continued on next page.278COMMISSIONING LEVEL ……8.6Input Calibration PageCalibrate 1V EnableIf 1V calibration is required, set the input links to V – see Section 4 of Installation Guide .Connect a d.c. voltage calibrator to the selected input and apply 1V.Select CAL-Y to enable 1V calibration.If 1V calibration is not required select CAL–N .Calibrate 1VIf calibrate 1V is enabled, (–) is displayed in lower display during calibration. dONE is displayed on completion.Calibration PassIf calibration is successful, the selected input is displayed on the upper display and input value is displayed on the lower display.Calibration FailCalibration failure may be due to the following:incorrect input link setting incorrect input signal applied faulty non-volatile memory.Re-calibration EnableEnable or disable 1V re-calibration:YES –repeat 1V calibrationNO –advance to the next frame.Calibrate Cold JunctionAn automatic cold junction (ACJC) transistor (TR10) is fitted on the main p.c.b. adjacent to module position 1.If cold junction calibration is required, set the input links to mV – see Section 4 of Installation Guide .Select YES to enable cold junction calibration.If cold junction calibration is not required select NO .Set Cold Junction TemperatureMeasure the temperature adjacent to the automatic cold junction transistor (TR10). Set the measured temperature in °C.If the input links are set incorrectly Check Links flashes until the links are reset.Cold Junction TemperatureCheck cold junction temperature is the same as the value set in the SEt CJ frame above.Note.If the cold junction temperature is different from the value set in the SEt CJ frame Return to Select Input frame.Note.Reset the links to their original positions before proceeding to the next Page.28…8COMMISSIONING LEVEL8.7Output Calibration PagePage Header– Output CalibrationTo advance to the Pen Calibration PageSelect OutputSelect output required.Connect the 100Ω resistance standard across the output that requires calibration and connect the digital voltmeter across the resistor.Return to Select Output frame.298COMMISSIONING LEVEL …8.8Pen Calibration PagePage Header– Pen CalibrationTo advance to the Display Set Up Page Pen 1 Range High Calibrationon the 100% chart line.Pen 1 Range Low Calibrationon the 0% chart line.Pen 2 to 4 Range High CalibrationRepeat as for Pen 1 Range High Calibration , if applicable.Note.On instruments configured for true time event marker, the true time event pen Pen 4 High Calibration . Set the pen to the 100% position on the chart.Pen 2 to 4 Range Low CalibrationRepeat as for Pen 1 Range Low Calibration , if applicable.Note.P en 4 Low Calibration is omitted on instruments configured for true time event Pen Linearity CheckThe pens automatically draw the pen linearity check test pattern shown below.Return to Pen Calibration frame.30…8COMMISSIONING LEVEL8.9Display Set Up PagePage Header – Relay TestTo advance to the Digital Input Test Page Select Module PositionThe selections in this frame relate to modules fitted. Select module position required,Select Output StateSelect the relay output state for the module selected in the previous frame:Note.All relays on the selected module are turned ON or OFF together.Return to Select Module Position frame.318COMMISSIONING LEVEL …8.11Digital Input Test PagePage Header – Output TestTo advance to the Diagnostics Page Output Test EnableThe output test cycles each of the current outputs through a number of steps. The chart duration is automatically set to 24 hours.Select OP ON to enable the output test. OPtESt ACtIVE is displayed until the test is complete.To disable the output test select OP OFF .Note.To produce the correct test pattern, the current output of each module must be linked to its analog input and the plug-in links set for mA – see Section 4 of the Installation Guide .Return to Output Test frame.32…8COMMISSIONING LEVELOutput Test Pattern…8.12Output Test PageThe output test can be used to check the chart and pen movement and detect any linearity or hysteresis errors in pen positioning.8.13Diagnostics PagePage Header – Diagnostics PageTo advance to the COMMISSIONING LEVEL Error CodeThis frame is for factory use only.Instrument TimingThe display indicates the number of 8ms interrups used to process the enabled functions.The total executive cycle time is 240ms.Example – a display of 20 indicates 160ms of the executive cycle time have been used to processthe enabled functions.Return to Diagnostics Page frame.9INSTRUMENT REPAIR33I M /C 1900–A G N I s s u e 7The Company’s policy is one of continuous product improvement and the right is reserved to modify the information contained herein without notice.© ABB 2001Printed in UK (04.01)ABB Automation Ltd Howard Road, St. Neots Cambridgeshire, PE19 8EU UKTel: +44 (0)1480-475-321Fax: +44 (0)1480-217-948ABB Automation Inc.125 E. County Line Road Warminster, PA 18974USATel: +1 215-674-6000Fax: +1 215-674-7183ABB has Sales & Customer Support expertisein over 100 countries worldwide。
ABB驱动器用户手册Modbus适配器模块FMBA-01

Table of contents
8 Technical data and diagnostics . . . . . . . . . . . . . . . . . . . . . . . . . . . . . . . . . 19 FMBA-01 Modbus Adapter module . . . . . . . . . . . . . . . . . . . . . . . . . . . . . . . . 19 RS-485 link . . . . . . . . . . . . . . . . . . . . . . . . . . . . . . . . . . . . . . . . . . . . . . . . . . 20 LED indications . . . . . . . . . . . . . . . . . . . . . . . . . . . . . . . . . . . . . . . . . . . . . . . 20
QUANTA

QUANTA®QXXXXC AC VOLTAGE QXXXXD AC CURRENT DIGITAL PANEL METEROperator’s Manual/manuals®NEWPORT Electronics,Inc.CountersFrequency Meters PID Controllers Clock/Timers Printers Process Meters On/Off ControllersRecorders Relative Humidity Transmitters Thermocouples ThermistorsWireRate Meters Timers TotalizersStrain Gauge MetersVoltmeters MultimetersSoldering Iron TesterspH pens pH Controllers pH ElectrodesRTDs Thermowells Flow SensorsNEWPORT Electronics, Inc.®For Immediate AssistanceIn the U.S.A. and Canada: 1-800-NEWPORT®In Mexico: (95) 800-NEWPORT SMOr call your local NEWPORTOffice.Additional products fromIt is the policy of NEWPORT to comply with all worldwide safety and EMC/EMI regulations that apply.NEWPORT is constantly pursuing certification of its products to the European New Approach Directives. NEWPORT will add the CE mark to every appropriate device upon certification.The information contained in this document is believed to be correct but NEWPORT Electronics, Inc.accepts no liability for any errors it contains, and reserves the right to alter specifications without notice.WARNING: These products are not designed for use in, and should not be used for, patient connected applications.This device is marked with the international caution symbol. It is important to read the SetupGuide before installing or commissioning this device as it contains important information relating to safety and EMC.T A B L E O F C O N T E N T SSAFETY CONSIDERATIONS . . . . . . . . . . . . . . . . . . . . . . . . . . . . . . . . . . . . . . . . . . . . . . .ii Q2000 MAIN ASSEMBLY1.0Specifications . . . . . . . . . . . . . . . . . . . . . . . . . . . . . . . . . . . . . . . . . . . . . . . . . . . . . . .12.0Mechanical Assembly and Installation . . . . . . . . . . . . . . . . . . . . . . . . . . . . . . . . . . . . .43.0Power & Signal Input Connections . . . . . . . . . . . . . . . . . . . . . . . . . . . . . . . . . . . . . . .54.0Configuration Procedure . . . . . . . . . . . . . . . . . . . . . . . . . . . . . . . . . . . . . . . . . . . . . . .65.0Configuration Charts . . . . . . . . . . . . . . . . . . . . . . . . . . . . . . . . . . . . . . . . . . . . . . . . . .76.0Tests and Diagnostics . . . . . . . . . . . . . . . . . . . . . . . . . . . . . . . . . . . . . . . . . . . . . . . .97.0Main Board Connector Pin Assignments . . . . . . . . . . . . . . . . . . . . . . . . . . . . . . . . . .108.0Drawings . . . . . . . . . . . . . . . . . . . . . . . . . . . . . . . . . . . . . . . . . . . . . . . . . . . . . . . . . .11 Q9000 MAIN ASSEMBLY9.0Specifications . . . . . . . . . . . . . . . . . . . . . . . . . . . . . . . . . . . . . . . . . . . . . . . . . . . . . .1710.0Mechanical Assembly and Installation . . . . . . . . . . . . . . . . . . . . . . . . . . . . . . . . . . . .2011.0Power & Signal Input Connections . . . . . . . . . . . . . . . . . . . . . . . . . . . . . . . . . . . . . . .2112.0Configuration Procedure . . . . . . . . . . . . . . . . . . . . . . . . . . . . . . . . . . . . . . . . . . . . . .2213.0Configuration Charts . . . . . . . . . . . . . . . . . . . . . . . . . . . . . . . . . . . . . . . . . . . . . . . . . .2314.0Tests and Diagnostics . . . . . . . . . . . . . . . . . . . . . . . . . . . . . . . . . . . . . . . . . . . . . . .2615.0Main Board Connector Pin Assignments . . . . . . . . . . . . . . . . . . . . . . . . . . . . . . . . . .2716.0Drawings . . . . . . . . . . . . . . . . . . . . . . . . . . . . . . . . . . . . . . . . . . . . . . . . . . . . . . . . . .28 SIGNAL CONDITIONER BSCC, BSCC/D17.0Specifications . . . . . . . . . . . . . . . . . . . . . . . . . . . . . . . . . . . . . . . . . . . . . . . . . . . . . .3118.0Signal Input Requirements . . . . . . . . . . . . . . . . . . . . . . . . . . . . . . . . . . . . . . . . . . . .3519.0Test and Diagnostics . . . . . . . . . . . . . . . . . . . . . . . . . . . . . . . . . . . . . . . . . . . . . . . . .3620.0Configuration Procedure . . . . . . . . . . . . . . . . . . . . . . . . . . . . . . . . . . . . . . . . . . . . . .3721.0Configuration Charts . . . . . . . . . . . . . . . . . . . . . . . . . . . . . . . . . . . . . . . . . . . . . . . . .4022.0Calibration . . . . . . . . . . . . . . . . . . . . . . . . . . . . . . . . . . . . . . . . . . . . . . . . . . . . . . . . .4223.0Drawings . . . . . . . . . . . . . . . . . . . . . . . . . . . . . . . . . . . . . . . . . . . . . . . . . . . . . . . . . . .43 INSTALLATION INSTRUCTIONS24.0Digital Panel Meter Installation Instructions . . . . . . . . . . . . . . . . . . . . . . . . . . . . . . . .4525.0Signal Input Connections . . . . . . . . . . . . . . . . . . . . . . . . . . . . . . . . . . . . . . . . . . . . . .48i10280ML-0210280ML-02ii1.0MAIN ASSEMBLY Q2000 SPECIFICATIONS1.1GENERALThe Q2000 main assemblies are identified by an initial designator (BQ2)plus a power/display option numeral, zero thru nine (0-9).The following table identifies the main assembly types:DisplayType120 V ac240 V ac9-32 V dc 5 V ac24 V acLED BQ20BQ22BQ24BQ26BQ28LCD BQ21BQ23BQ25BQ27BQ29The QUANTA Digital Panel Meter/Controller consists of a main assembly,signal conditioner and interface options (if ordered) all housed in a 1/8DIN case.The main assembly consists of a main board and a display board which ispermanently attached to it at a 90 degree angle.The main board provides mounting for the power supply, circuitcomponents, and connectors for plugging in the signal conditioner,optional analog card, and optional controller/communications interfacecard (requires removal of a bypass push-on jumper).The display board includes the analog-to-digital converter, the LED orLCD display and the push-on jumper for programming the decimal points.Decimal point programming may also be done from the main boardconnector (J1).110280ML-021.2POWERAC Models:24/120/240 V +10/-15%47-63 HzCommon Mode Voltage:1500 Vp test(354 Vp per IEC spacing),(150 Vp per CE)DC Models: 5 V ±5% (5 V return common to signal LO)9-32 V(300 V isolation from 9-32 V return to signal LO)(100 Vp per CE)Source Impedance: 3 ohmsRipple:250 mV maximumPower Consumption: 5 watts maximum1.3DISPLAYLED:14.2 mm (0.56 in), 7-segment light emitting diodeLens color:RedLCD:12.7 mm (0.50 in), 7-segment liquid crystalLens color:ClearRange:0 to ±1999Overload Indication:Three least significant digits blanked, "1" or "-1" displayed 1.4CONVERSIONTechnique:auto-zero, dual slope, average valueSignal Integration Period:100 ms, nominalReading Rate: 2.5/s, nominal1.5ENVIRONMENTALOperating Temperature(Ambient):0 to 60°CStorage Temperature:-40 to 85°CHumidity:To 95% RH, non-condensing, 0-40°C1.6MECHANICALCase Material:UL-rated 94V-0, polycarbonateWeight:0.57 kg (with interface board)10280ML-022310268ML-021110280ML-02Notes: Dimensions are in inches ±0.01"with millimeters in [ ] ±0.25 mm.MAX8.0DRAWINGS8.1DIMENSIONSNOTES1310280ML-021510280ML-0210280ML-02169.0MAIN ASSEMBLY Q9000 SPECIFICATIONS9.1GENERALThe Q9000 main assemblies are identified by an initial designator (BQ9)plus a power/display option number: 0, 2, 4, 6, or 8.The following table identifies the main assembly types:DisplayType120 V ac240 V ac9-32 V dc 5 V ac24 V acLED BQ90BQ92BQ94BQ96BQ98The QUANTA Digital Panel Meter/Controller consists of a main assembly,signal conditioner and interface options (if ordered) all housed in a 1/8DIN case.The main assembly consists of a main board and a display board which ispermanently attached to it at a 90 degree angle.The main board provides mounting for the power supply, circuitcomponents, and connectors for plugging in the signal conditioner,optional analog card, and optional controller/communications interfacecard (requires removal of a bypass push-on jumper).The display board includes the analog-to-digital converter, the LED andthe push-on jumper for programming the decimal points.Decimal pointprogramming may also be done from the main board connector (J1).1710280ML-029.2POWERAC Models:24/120/240 V +10/-15%47-63 HzCommon Mode Voltage:1500 Vp test(354 Vp per IEC spacing),DC Models: 5 V ±5% (5 V return common to signal LO)9-32 V(300 V isolation from 9-32 V return to signal LO)(100 Vp per CE)Source Impedance: 3 ohmsRipple:250 mV maximumPower Consumption: 5 watts maximum9.3DISPLAYLED:14.2 mm (0.56 in), 7-segment light emitting diodeLens color:RedRange:0 to ±9999, digits flash from 10K to 20K counts Overload Indication:Four digits flash zero at 20K and above9.4CONVERSIONTechnique:auto-zero, dual slope, average valueSignal Integration Period:100 ms, nominalReading Rate: 2.5/s, nominal9.5ENVIRONMENTALOperating Temperature(Ambient):0 to 60°CStorage Temperature:-40 to 85°CHumidity:To 95% RH, non-condensing, 0-40°C9.6MECHANICALCase Material:UL-rated 94V-0, polycarbonateWeight:0.57 kg (with interface board)10280ML-02181910280ML-0216.0DRAWINGS16.1DIMENSIONSNotes: Dimensions are in inches ±0.01"with millimeters in [ ] ±0.25 mm.10280ML-0228NOTES 10280ML-023017.0SPECIFICATIONS17.1GENERALThe basic signal conditioner board is identified as a BSCC (Q2000C orQ9000C) for ac voltage input. The Q2000 and Q9000 prefix is determinedby the main assembly baord used with the BSCC option board. When theBSCC board is configured differently, it is identified as a BSCC/D(Q2000D or Q9000D), used for ac current input.17.2BSCC: AC VOLTA E SI NAL CONDITIONERFive full-scale ranges are provided in the Q2000C and Q9000C series.The reading is computed from the rectified ac signal, calibrated forsinusoidal input. See AC VOLTAGE INPUT tables on pages 33 and 34.17.3BSCC/D: AC CURRENT SIGNAL CONDITIONERTen full-scale ranges are provided in this series. The reading is computedfrom the rectified ac signal, calibrated for sinusoidal input. See ACCURRENT INPUT tables on pages 35.17.4Q2000C & Q9000C: AC VOLTAGE INPUT SPECIFICATIONSConfiguration:Single-ended, meter ground common to signal LOZero:AutomaticQ2000C AC VOLTAGE INPUTSRANGE INPUT RESOLUTION FREQUENCYIMPEDANCE RANGE 199.9 mV 1.1 M ohm0.1 mV47-1000 Hz1.999 V 1.1 M ohm 1 mV47-1000 Hz19.99 V 1 M ohm10 mV47-1000 Hz199.9V 1 M ohm100 mV47-1000 Hz150.0 V for CE750 V10 M ohm1V47-1000 Hz150 V for CEFull-wave rectified ac signal, calibrated for sinusoidal input.31 10280ML-0220.0CONFIGURATION PROCEDURE20.1GENERALUse this procedure to determine the configuration of the BSCC or BSCC/D.Configure the meter using the push-on jumpers provided separately oralready positioned on the pin forests. Pin forests designations are shownwith each configuration chart.20.2GLOSSARYThe chart below explains various terms which appear throughout thefollowing procedure:Definition DefinitionTerm Voltage Input Range Term Current Input RangeCVR10 / 50 mV ac DCR10 / 20 uA acCVR20 / 200 mV ac DCR20 / 200 uA acCVR30 / 2 V ac DCR30 / 2 mA acCVR40 / 20 V ac DCR40 / 20 mA acCVR50 / 200 V ac DCR50 / 200 mA ac0 / 150 V for CECVR60 / 750 V ac DCR60 / 2 A ac0 / 150 for CEDCR70 / 5 A acTerm DefinitionV1Largest input voltageI1Largest input current20.3SELECTIONIf the Input is:Voltage, proceed to Section 20.3.1Current, proceed to Section 20.3.237 10280ML-02NOTES 10280ML-024410280ML-0246。
萨费伊 夸萨 900 系列开路气体检测仪 产品手册说明书
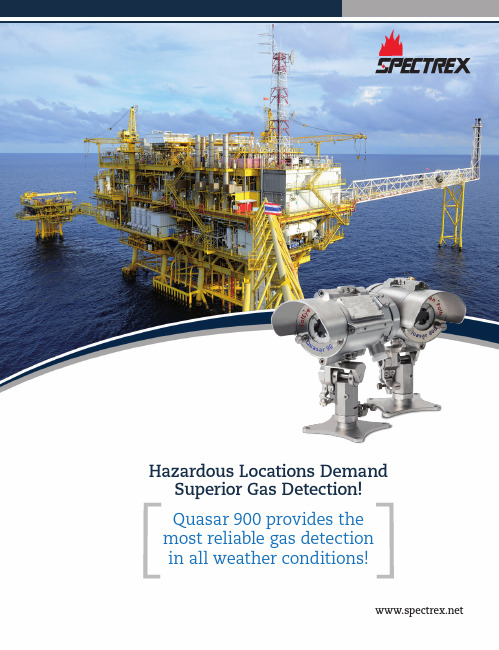
Hazardous Locations DemandSuperior Gas Detection!Quasar 900 provides themost reliable gas detectionin all weather conditions!2SafEye Quasar 900 Series Open Path Gas DetectorWhy Open Path Gas Detectors?Spectrex invented the xenon flash lamp design that revolutionized the open-path gas detection market, which, until then, was plagued by false alarms due to the drawbacks of the previous designs. Now, Open path detectors complement the use of individual point detectors, take executive action and offer many significant benefits including:• Wider area coverage• Most likely method to pick up any leak • Very high speed of response • No unrevealed failure modes • Beam block warning• Detector location is less critical • Size of gas hazard indicatedApplications include:• Offshore platforms & FPSOs • Petrochemical plants• Chemical processing plants• Gas filling and distribution terminals • Gas transport and pipelines • Large storage areas & buildings • Perimeter monitoringFrom the Arctic Circle to Middle EasternDeserts40-meter path 70% LEL40% LEL20% LEL 7m wide cloudSafEye Source This scenario shows how the matrix of point type detectors can miss a leak or eventually only see diluted gas levels whereas SafEye 900 Open-Path will, in this case, measure 20% LEL x 7m = 1.4 LEL.m - well above 1 LEL.m alarm level1 LEL meter (1 LEL.m) = a cloud of 5% LEL methane gas that is20 meter wide1 LEL meter (1 LEL.m) = a cloud of 100% LEL methane gas that is1 meter wide Gas leak can be picked up by Open Path Detectors that point detectors miss!SafEye SourceSafEye Source1 LEL Meter1 LEL Meter Gas Cloud 100% LELGas Cloud 5% LEL1m 20m 100m 100m SafEye DetectorSafEye DetectorSafEye DetectorPoint type detectorThe SafEye Quasar 900 Series is the very latest open path IR technology and detects a wide range of hydrocarbon gases – including alkanes (methane to hexane) and ethylene.Path lengths can be up to 660ft (200m). Quasar 900 models can be tailored to protect your high-risk installation.Reliability and performance is key and is assured with SIL2 approval and successful 3rd party FM performance / function testing to FM and EN standards3SafEye Quasar 900 Series Open Path Gas DetectorWe had Factory Mutual (FM) independently test Quasar 900 to recognized worldwide Function and Performance standards for open-path gas detectors (FM6325 andEN60079-29-4). Guess what – we passed with flying colors!(apart from anything else, it costs a lot). Well, its to give you the assurance that what we say about Quasar 900 is true – and in safety, that’s important!IMMUNITY TO FALSE ALARMSQuasar 900 is totally immune to interference from sunlight or any other sources of radiation such as flare stacks, arc welding or lightning.PERFORMANCE IN ALL WEATHERSThe Quasars 900’s high power xenon lamp will compensate for changing weather conditions, including rain, fog, mist, snow and makes it immune to influences from solar radiation, arc-welding, stack flares or vibration from machinery.The optical lenses are thermostacically heated to preventthe formation of ice and build up of snow on the optics even under severe weather conditions. It also eliminates build up of condensation on the lenses.Quasar is rated for operation over a very wide temperature range from -67°F to + 149ºF (-55ºC to + 65ºC) - a truly worldwide productRELIABILITYQuasar 900 is approved to SIL2 (IEC61508), equipped with heated optics and tolerates a very wide temperature range to provide reliable detectionFAILSAFENo unrevealed failures. In normal operation, the output signal is 4 to 20 mA, depending on the measured gas concentration. Sub-4mA signals includes indications for beam blockage(2mA), a fault (1mA). In addition, a continuous self-test of the Quasar 900 will issue a pre-warning signal (3mA) where the detector is still operational but requires some attention – for example when the transmitter or receiver is misaligned or if there is a deposit build-up on the optics. Maintenance without downtime!BUILT-IN DATA LOGGERAn internal data-logger keeps a detailed record of the previous 100 events.GAS LIBRARYThe detectors can be calibrated to methane, propane or ethylene. The calibration selection must be determined when ordering.MINIMUM DETECTABLE LEVELDue to Quasar 900's inherent stability and sensitivity, the minimum detectable level is 0.15 LEL.mSIMPLE TO ALIGN AND COMMISSIONOne person can easily align and commission the system without the need for special training or skills. After an initial coarse adjustment by eye, a telescope is fitted allowing fine adjustment to optimized the adjustment for maximum signal strength.Don’t just take our word for it!Why do we do this?5SafEye Quasar 900 Series Open Path Gas DetectorComplete Access in the Field or Safe AreaThe unique, intrinsically safe approved connection port on the Quasar 900 receiver allows simple connection of various types of handheld unit that will communicate with Quasar 900 in the hazardous event log, perform diagnostic functions, in conjunction with Spectrex software.Two options are available, both able to connect to the intrinsically safe approved connection port on the Quasar 900 receiver.- HART handheld- RS485 handheldFor work in a safe area / workshop, other options are available, still connected via the I.S. port. for your convenience.These take the form of cable harnesses to connect with your own6SafEye Quasar 900 Series Open Path Gas DetectorGENERAL SPECIFICATIONSDetection Range Model 901 902 903 904Feet 23-6650-132 115-330265-660Meters 7-2015-4035-10080-200 Detected Gas C1-C8Response Time 3 sec.0-8 LEL.m ethyleneSpectral Response 2.0 - 3.0µmDisplacement/Misalignment ±0.5°ToleranceDrift ±7.5% of the reading or ±4% of the full scale (whichever is greater)Minimum Detectable Level 0.15 LEL.mTemperature Range –67°F (–55°C) to 149°F (65°C)Humidity Up to 95% non-condensing (withstands up to 100% RH for short periods)Heated Optics To eliminate condensation and icing on the windowWarranty Safety system – 3 yearsELECTRICAL SPECIFICATIONSPower Supply24VDC nominal (18-32 VDC)Power Consumption Detector: 250mA (300mA Peak)(peak includes heated optics)Source: 250mA (300mA Peak)Warm Up Time30 sec for transmitter and receiverElectrical Connection (specify) 2 x 3/4" – 14NPT conduitsor 2 x M25 x 1.5mm ISOElectrical Input Protection per MIL-STD-1275BElectromagnetic Compatibility EMI/RFI protected per EN50270OUTPUTS – INTERFACES0-20mA Current OutputGas reading 4-20mA Obscuration/beam block 2mANormal, zero reading 4mA Zero calibration mode 1mAMaintenance call 3mA Fault 0mAMisalignment 2.5mARS-485 Interface – Modbus The RS-485 input/output provides complete data information to a PC and receives control Compatible commands from the PC or handheld unitHART HART communications on 0-20mA analog current (FSK) – used for maintenance and assetmanagementVisual Status Indicator 3 color LED: Green – Power on, Yellow – Fault, Red – AlarmMECHANICAL SPECIFICATIONSHazardous Area Approval ATEX&IECEx Ex II 2(2)G DEx db eb ib [ib Gb] IIB + H2 T4 GbEx tb IIIC T135°C DbTa = –55°C to +65°CFM/FMC Class I Div 1 Groups B, C and DClass II,III Div 1 Groups E, F and GTR CU/EAC 1Ex d e ib [ib Gb] IIB + H2 T4 Gb XEx tb IIIC T135°C Db XInmetro Ex db eb ib [ib Gb] IIB_H2 T4 GbEx tb IIIC T135°C DbPerformance Approved per FM6325 and tested by FM per EN60079-29-4Reliability SIL2 per IEC61508 (TUV)stainless steel 316L.Dimensions Detector/Source 10.5 x 5.1 x 5.1 inch (267 x 130 x 130mm)Tilt Mount 4.7 x 4.7 x 5.5 inch (120 x 120 x 158mm)Weight Detector/Source 11lb (5kg)Tilt Mount 4.2lb (1.9kg)Water and Dust Tight IP66 and IP68NEMA 250 6PEnvironmental Meets MIL-STD-810C for Humidity, Salt and Fog, Vibration, Mechanical Shock, High and LowTemperatureACCESSORIESTilt Mount P/N 888270 HART Hand-Held Diagnostic Unit P/N 888810Wall Mount P/N 799255 HART Harness Kit P/N 888815U-Bolt/Pole Mount (4-5 inch)P/N 799225 USB/RS485 Harness Converter Kit P/N 794079Weather Cover P/N 888263 U-Bolt/Pole Mount (2-3 inch)P/N 888140Commissioning Kit P/N 8882477SafEye Quasar 900 Series Open Path Gas Detector AccessoriesCommunication, Diagnostics, Set-upCommissioning, maintenance and diagnostics tools for the Quasar 900 Series, which providesIf, instead, user wishes to use their own HART handheld or PC / laptop in safe area, we offer:HART HARNESS KIT P/N 888815For standard HART Hand-Held (I.S.) to connect between the Hand-Held and the I.S. Port on 900, including a harness.USB RS485 HARNESS CONVERTER KIT P/N 794079With RS485/USB converter, kit is used with Spectrex Host software, enables the user to connect to any available PC or laptop. For use in safe area only. Connects, for convenience, to connection port on 900 or RS485 terminals COMMISSIONING KIT P/N 888247P/N 888355-2The Commissioning/Alignment Kit is required forcommissioning and maintenance checks.Only one kit is required per site, Includes: AlignmentTelescope, Magnetic Mode Selector, Function CheckThe Duct Mount allows gas detection in areas wherethe monitored area does not allow installation of thegas detection system inside the area.Filters (2) and set of Socket keys for access to unitsWEATHER COVER, STAINLESS STEEL P/N 888263TILT MOUNT P/N 888270POLE MOUNT (U-Bolt, 4–5 inch) P/N 799225HART HAND-HELD DIAGNOSTIC UNIT P/N 888810and connects to I.S. port on 900.Duct Mount8How to choose your newQuasar 900SafEye Quasar 900 Series Open Path Gas DetectorModel =Receiver + Transmitter Installation Distance 901QR-X-11X + QT-X-11X 23-66 ft / 7-20m 902QR-X-11X + QT-X-21X 50-132 ft / 15-40m 903QR-X-11X + QT-X-31X 115-330 ft / 35-100m 904QR-X-11X+QT-X-41X265-660 ft / 80-200mQuasar 900 Part numbersQR - X -C: ATEX F: FMB: Inmetro R: TR CUC: ATEX F: FMB: Inmetro R: TR CUC: ATEX F: FMB: Inmetro R: TR CURECEIVERX1: M252: ¾" NPT11QT - X -- X -TRANSMITTERXXX1: M252: ¾" NPT1: M252: ¾" NPTO: No G: Yes1: M e thane 2: Propane 3: Ethylene1XX90X1: 7-20m: Short Range2: 15-40m: Medium Range 13: 35-100m: Medium Range 24: 80-200m: Long Range1: 7÷20m: (23÷66ft)2: 15÷40m: (50÷132ft)3: 35÷100m: (115÷330ft)4:80÷200m: (256÷660ft)Q -900, F e b r u a r y 2020 (A c )Headquarters: 6021 Innovation Blvd , Shakopee , MN 55379, USA Tel: 973 239-8398E-mail:******************************|。
SINUMERIK SINUMERIK ONE 机器人控制系统操作手册说明书

SINUMERIKSINUMERIK ONEMillingOperating ManualValid for:SINUMERIK ONESoftware versionCNC system software for SINUMERIK ONE V6.20 SINUMERIK Operate for PCU/PC V6.2007/2022A5E48384797B ADLegal information Warning notice systemThis manual contains notices you have to observe in order to ensure your personal safety, as well as to prevent damage to property. The notices referring to your personal safety are highlighted in the manual by a safety alert symbol, notices referring only to property damage have no safety alert symbol. These notices shown below are graded according tothe degree of danger.DANGERindicates that death or severe personal injury will result if proper precautions are not taken.WARNINGindicates that death or severe personal injury may result if proper precautions are not taken.CAUTIONindicates that minor personal injury can result if proper precautions are not taken.NOTICEindicates that property damage can result if proper precautions are not taken.If more than one degree of danger is present, the warning notice representing the highest degree of danger will be used. A notice warning of injury to persons with a safety alert symbol may also include a warning relating to property damage.Qualified PersonnelThe product/system described in this documentation may be operated only bypersonnel qualified for the specific task in accordance with the relevant documentation, in particular its warning notices and safety instructions. Qualified personnel are those who, based on their training and experience, are capable of identifying risks and avoiding potential hazards when working with these products/systems.Proper use of Siemens productsNote the following:WARNINGSiemens products may only be used for the applications described in the catalog and in the relevant technical documentation. If products and components from other manufacturers are used, these must be recommended or approved by Siemens. Proper transport, storage, installation, assembly, commissioning, operation and maintenance are required to ensure that the products operate safely and without any problems. The permissible ambient conditions must be complied with. The information in the relevant documentation must be observed.TrademarksAll names identified by ® are registered trademarks of Siemens AG. The remaining trademarks in this publication may be trademarks whose use by third parties for their own purposes could violate the rights of the owner.Disclaimer of LiabilityWe have reviewed the contents of this publication to ensure consistency with the hardware and software described. Since variance cannot be precluded entirely, we cannot guarantee full consistency. However, the information in this publication is reviewed regularly and any necessary corrections are included in subsequent editions.Siemens AGDigital Industries Postfach 48 4890026 NÜRNBERG GERMANYA5E48384797B ADⓅ 06/2022 Subject to change Copyright © Siemens AG 2019 - 2022.All rights reservedTable of contents1Introduction (17)1.1About SINUMERIK (17)1.2About this documentation (18)1.3Documentation on the internet (20)1.3.1Documentation overview SINUMERIK ONE (20)1.3.2Documentation overview SINUMERIK operator components (20)1.4Feedback on the technical documentation (22)1.5mySupport documentation (23)1.6Service and Support (24)1.7Important product information (26)2Fundamental safety instructions (27)2.1General safety instructions (27)2.2Warranty and liability for application examples (28)2.3Security information (29)3Fundamentals (31)3.1Product overview (31)3.2Operator panel fronts (32)3.2.1Overview (32)3.2.2Keys of the operator panel (34)3.3Machine control panels (42)3.3.1Overview (42)3.3.2Controls on the machine control panel (42)3.4User interface (46)3.4.1Screen layout (46)3.4.2Status display (47)3.4.3Actual value window (49)3.4.4T,F,S window (51)3.4.5Operation via softkeys and buttons (53)3.4.6Entering or selecting parameters (54)3.4.7Pocket calculator (56)3.4.8Pocket calculator functions (57)3.4.9Context menu (59)3.4.10Changing the user interface language (59)3.4.11Entering Chinese characters (60)3.4.11.1Function - input editor (60)3.4.11.2Entering Asian characters (62)3.4.12Entering Korean characters (63)3.4.13Protection levels (65)MillingOperating Manual, 07/2022, A5E48384797B AD3Table of contents3.4.14Work station safety (67)3.4.15Cleaning mode (67)3.4.16Display live image from a camera (68)3.4.17Online help in SINUMERIK Operate (69)4Multitouch operation with SINUMERIK Operate (73)4.1Multitouch panels (73)4.2Touch-sensitive user interface (74)4.3Finger gestures (75)4.4Multitouch user interface (78)4.4.1Screen layout (78)4.4.2Function key block (79)4.4.3Further operator touch controls (80)4.4.4Virtual keyboard (80)4.4.5Special "tilde" character (81)4.5Expansion with side screen (82)4.5.1Overview (82)4.5.2Sidescreen with standard windows (82)4.5.3Standard widgets (84)4.5.4"Actual value" widget (84)4.5.5"Zero point" widget (85)4.5.6"Alarms" widget (85)4.5.7"NC/PLC variables" widget (85)4.5.8"Axle load" widget (86)4.5.9"Tool" widget (86)4.5.10"Service life" widget (87)4.5.11"Program runtime" widget (87)4.5.12Widget "Camera 1" and "Camera 2" (87)4.5.13Sidescreen with pages for the ABC keyboard and/or machine control panel (88)4.5.14Example 1: ABC keyboard in the sidescreen (89)4.5.15Example 2: Machine control panel in the sidescreen (90)4.6SINUMERIK Operate Display Manager (91)4.6.1Overview (91)4.6.2Screen layout (92)4.6.3Operator controls (92)5Setting up the machine (97)5.1Switching on and switching off (97)5.2Approaching a reference point (98)5.2.1Referencing axes (98)5.2.2User agreement (99)5.3Operating modes (101)5.3.1General (101)5.3.2Modes groups and channels (103)5.3.3Channel switchover (103)5.4Settings for the machine (105)5.4.1Switching over the coordinate system (MCS/WCS) (105)5.4.2Switching the unit of measurement (105)Milling 4Operating Manual, 07/2022, A5E48384797B ADTable of contents5.4.3Setting the zero offset (107)5.5Measure tool (109)5.5.1Overview (109)5.5.2Manually measuring drilling and milling tools (109)5.5.3Measuring drilling and milling tools with the workpiece reference point (110)5.5.4Measuring drilling and milling tools with fixed reference point (111)5.5.5Measuring radius or diameter (112)5.5.6Fixed point calibration (113)5.5.7Measuring the drilling and milling tool length with electrical tool probe (113)5.5.8Calibrating the electrical tool probe (116)5.5.9Manually measuring a turning tool (for milling/turning machine) (117)5.5.10Manually measuring a turning tool using a tool probe (for milling/turning machine) (118)5.5.11Logging tool measurement results (120)5.6Measuring the workpiece zero (122)5.6.1Overview (122)5.6.2Sequence of operations (126)5.6.3Examples with manual swiveling (swiveling in JOG mode) (127)5.6.4Setting the edge (128)5.6.5Edge measurement (129)5.6.6Measuring a corner (134)5.6.7Measuring a pocket and hole (137)5.6.8Measuring a spigot (140)5.6.9Aligning the plane (145)5.6.10Defining the measurement function selection (147)5.6.11Logging measurement results for the workpiece zero (148)5.6.12Calibrating the electronic workpiece probe (149)5.6.12.1Calibration of length and radius or diameter (149)5.6.12.2Calibrate on sphere (151)5.7Settings for the measurement result log (153)5.8Zero offsets (155)5.8.1Display active zero offset (156)5.8.2Displaying the zero offset "overview" (157)5.8.3Displaying and editing base zero offset (158)5.8.4Displaying and editing settable zero offset (159)5.8.5Displaying and editing details of the zero offsets (160)5.8.6Deleting a zero offset (161)5.8.7Measuring the workpiece zero (162)5.9Monitoring axis and spindle data (164)5.9.1Specify working area limitations (164)5.9.2Editing spindle data (164)5.10Displaying setting data lists (166)5.11Handwheel assignment (167)5.12MDA (169)5.12.1Saving an MDA program (169)5.12.2Editing/executing a MDI program (170)5.12.3Deleting an MDA program (171)MillingOperating Manual, 07/2022, A5E48384797B AD5Table of contents6Execution in manual mode (173)6.1General (173)6.2Selecting a tool and spindle (174)6.2.1T, S, M windows (174)6.2.2Selecting a tool (176)6.2.3Starting and stopping a spindle manually (176)6.2.4Position spindle (177)6.3Traversing axes (179)6.3.1Traverse axes by a defined increment (179)6.3.2Traversing axes by a variable increment (180)6.4Positioning axes (181)6.5Swiveling (182)6.6Manual retraction (187)6.7Simple face milling of the workpiece (188)6.8Simple workpiece machining operations with milling/turning machines (191)6.8.1Simple workpiece face milling (milling/turning machine) (191)6.8.2Simple stock removal of workpiece (for milling/turning machine) (193)6.9Default settings for manual mode (197)7Machining the workpiece (199)7.1Starting and stopping machining (199)7.2Selecting a program (201)7.3Testing a program (202)7.4Displaying the current program block (203)7.4.1Displaying a basic block (203)7.4.2Display program level (203)7.5Correcting a program (205)7.6Repositioning axes (206)7.7Starting machining at a specific point (207)7.7.1Use block search (207)7.7.2Continuing program from search target (209)7.7.3Simple search target definition (210)7.7.4Defining an interruption point as search target (210)7.7.5Entering the search target via search pointer (211)7.7.6Parameters for block search in the search pointer (212)7.7.7Block search mode (212)7.7.8Block search for position pattern (215)7.8Controlling the program run (217)7.8.1Program control (217)7.8.2Use Powerride for program control (219)7.8.3Skip blocks (219)7.9Overstore (221)7.10Editing a program (223)Milling 6Operating Manual, 07/2022, A5E48384797B ADTable of contents7.10.1Searching in programs (223)7.10.2Replacing program text (225)7.10.3Copying/pasting/deleting a program block (226)7.10.4Renumbering a program (228)7.10.5Creating a program block (229)7.10.6Opening additional programs (230)7.10.7Editor settings (231)7.11Working with DXF files (235)7.11.1Overview (235)7.11.2Displaying CAD drawings (236)7.11.2.1Open a DXF file (236)7.11.2.2Cleaning a DXF file (236)7.11.2.3Enlarging or reducing the CAD drawing (237)7.11.2.4Changing the section (238)7.11.2.5Rotating the view (238)7.11.2.6Displaying/editing information for the geometric data (239)7.11.3Importing and editing a DXF file in the editor (240)7.11.3.1General procedure (240)7.11.3.2Specifying a reference point (240)7.11.3.3Assigning the machining plane (241)7.11.3.4Setting the tolerance (241)7.11.3.5Selecting the machining range / deleting the range and element (242)7.11.3.6Saving the DXF file (243)7.11.3.7Transferring the drilling positions (244)7.11.3.8Accepting contours (246)7.12Importing shapes from CAD programs (250)7.12.1Reading in CAD data into an editor and processing (252)7.12.1.1General procedure (252)7.12.1.2Import from CAD (252)7.12.1.3Defining reference points (253)7.12.1.4Viewing point information (256)7.12.1.5Creating a new contour (257)7.12.1.6Accepting the machining steps (258)7.13Display and edit user variables (260)7.13.1Overview (260)7.13.2Global R parameters (261)7.13.3R parameters (262)7.13.4Displaying global user data (GUD) (264)7.13.5Displaying channel GUDs (265)7.13.6Displaying local user data (LUD) (266)7.13.7Displaying program user data (PUD) (267)7.13.8Searching for user variables (267)7.14Displaying G Functions and Auxiliary Functions (270)7.14.1Selected G functions (270)7.14.2All G functions (272)7.14.3G functions for mold making (272)7.14.4Auxiliary functions (273)7.15Displaying superimpositions (275)7.16Mold making view (278)MillingOperating Manual, 07/2022, A5E48384797B AD7Table of contents7.16.1Overview (278)7.16.2Starting the mold making view (280)7.16.3Adapting the mold making view (280)7.16.4Specifically jump to the program block (281)7.16.5Searching for program blocks (282)7.16.6Changing the view (283)7.16.6.1Enlarging or reducing the graphical representation (283)7.16.6.2Moving and rotating the graphic (284)7.16.6.3Modifying the viewport (284)7.17Displaying the program runtime and counting workpieces (286)7.18Setting for automatic mode (288)8Simulating machining (291)8.1Overview (291)8.2Simulation before machining of the workpiece (299)8.3Simultaneous recording before machining of the workpiece (300)8.4Simultaneous recording during machining of the workpiece (301)8.5Setting the model quality (302)8.6Different views of the workpiece (303)8.6.1Plan view (303)8.6.23D view (304)8.6.3Side view (304)8.6.4Turning view (305)8.6.5Half section (305)8.7Editing the simulation display (307)8.7.1Blank display (307)8.7.2Showing and hiding the tool path (307)8.8Program control during the simulation (308)8.8.1Changing the feedrate (308)8.8.2Simulating the program block by block (309)8.9Changing and adapting a simulation graphic (310)8.9.1Enlarging or reducing the graphical representation (310)8.9.2Panning a graphical representation (311)8.9.3Rotating the graphical representation (311)8.9.4Modifying the viewport (312)8.9.5Defining cutting planes (312)8.10Displaying simulation alarms (314)9Generating a G code program (315)9.1Graphical programming (315)9.2Program views (316)9.3Program structure (320)9.4Fundamentals (321)9.4.1Machining planes (321)9.4.2Current planes in cycles and input screens (321)Milling 8Operating Manual, 07/2022, A5E48384797B ADTable of contents9.4.3Programming a tool (T) (322)9.5Generating a G code program (323)9.6Blank input (324)9.7Machining plane, milling direction, retraction plane, safe clearance and feedrate (PL, RP,SC, F) (326)9.8Selection of the cycles via softkey (327)9.9Calling technology functions (331)9.9.1Hiding cycle parameters (331)9.9.2Setting data for cycles (331)9.9.3Checking cycle parameters (331)9.9.4Programming variables (332)9.9.5Changing a cycle call (332)9.9.6 Compatibility for cycle support (333)9.9.7Additional functions in the input screens (333)9.10Measuring cycle support (334)10Creating a ShopMill program (335)10.1Program views (336)10.2Program structure (341)10.3Fundamentals (342)10.3.1Machining planes (342)10.3.2Polar coordinates (342)10.3.3Absolute and incremental dimensions (343)10.4Creating a ShopMill program (346)10.5Program header (347)10.6Program header (for milling/turning machine) (349)10.7Generating program blocks (352)10.8Tool, offset value, feed and spindle speed (T, D, F, S, V) (353)10.9Defining machine functions (355)10.10Call work offsets (357)10.11Repeating program blocks (358)10.12Specifying the number of workpieces (360)10.13Changing program blocks (361)10.14Changing program settings (362)10.15Selection of the cycles via softkey (364)10.16Calling technology functions (369)10.16.1Additional functions in the input screens (369)10.16.2Checking input parameters (369)10.16.3Setting data for technological functions (369)10.16.4Changing a cycle call (370)10.16.5Programming variables (370)10.16.6 Compatibility for cycle support (371)MillingOperating Manual, 07/2022, A5E48384797B AD9Table of contents10.17Measuring cycle support (372)10.18Example, standard machining (373)10.18.1Workpiece drawing (374)10.18.2Programming (374)10.18.3Results/simulation test (386)10.18.4G code machining program (388)11Programming technological functions (cycles) (391)11.1Know-how protection (391)11.2Drilling (392)11.2.1General (392)11.2.2Centering (CYCLE81) (393)11.2.3Drilling (CYCLE82) (394)11.2.4Reaming (CYCLE85) (398)11.2.5Deep-hole drilling 1 (CYCLE83) (399)11.2.6Deep-hole drilling 2 (CYCLE830) (405)11.2.7Boring (CYCLE86) (415)11.2.8Tapping (CYCLE84, 840) (417)11.2.9Drill and thread milling (CYCLE78) (424)11.2.10Positioning and position patterns (428)11.2.11Arbitrary positions (CYCLE802) (430)11.2.12Row position pattern (HOLES1) (433)11.2.13Grid or frame position pattern (CYCLE801) (434)11.2.14Circle or pitch circle position pattern (HOLES2) (436)11.2.15Displaying and hiding positions (438)11.2.16Repeating positions (440)11.3Milling (441)11.3.1Face milling (CYCLE61) (441)11.3.2Rectangular pocket (POCKET3) (443)11.3.3Circular pocket (POCKET4) (450)11.3.4Rectangular spigot (CYCLE76) (457)11.3.5Circular spigot (CYCLE77) (462)11.3.6Multi-edge (CYCLE79) (466)11.3.7Longitudinal groove (SLOT1) (470)11.3.8Circumferential groove (SLOT2) (476)11.3.9Open groove (CYCLE899) (482)11.3.10Long hole (LONGHOLE) - only for G code programs (491)11.3.11Thread milling (CYCLE70) (493)11.3.12Engraving (CYCLE60) (497)11.4Contour milling (504)11.4.1General (504)11.4.2Representation of the contour (504)11.4.3Creating a new contour (506)11.4.4Creating contour elements (507)11.4.5Changing the contour (512)11.4.6Contour call (CYCLE62) - only for G code program (513)11.4.7Path milling (CYCLE72) (514)11.4.8Contour pocket/contour spigot (CYCLE63/64) (519)11.4.9Predrilling contour pocket (CYCLE64) (521)11.4.10Milling contour pocket (CYCLE63) (524)Milling 10Operating Manual, 07/2022, A5E48384797B ADTable of contents 11.4.11Residual material contour pocket (CYCLE63) (529)11.4.12Milling contour spigot (CYCLE63) (530)11.4.13Residual material contour spigot (CYCLE63) (534)11.5Turning - milling/turning machine (537)11.5.1General (537)11.5.2Stock removal (CYCLE951) (537)11.5.3Groove (CYCLE930) (541)11.5.4Undercut form E and F (CYCLE940) (545)11.5.5Thread undercut (CYCLE940) (551)11.5.6Thread turning (CYCLE99), only for G code (557)11.5.6.1Special aspects of the selection alternatives for infeed depths (584)11.5.7Thread chain (CYCLE98) (585)11.5.7.1Special aspects of the selection alternatives for infeed depths (594)11.5.8Cut-off (CYCLE92) (595)11.6Contour turning - Milling/turning machine (599)11.6.1General information (599)11.6.2Representation of the contour (600)11.6.3Creating a new contour (601)11.6.4Creating contour elements (603)11.6.5Changing the contour (610)11.6.6Contour call (CYCLE62) (611)11.6.7Stock removal (CYCLE952) (612)11.6.8Stock removal residual (CYCLE952) (627)11.6.9Grooving (CYCLE952) (630)11.6.10Grooving residual material (CYCLE952) (641)11.6.11Plunge turning (CYCLE952) (645)11.6.12Plunge turning residual material (CYCLE952) (655)11.7Further cycles and functions (660)11.7.1Swivel plane (CYCLE800) (660)11.7.1.1Cylinder surface transformation with swivel plane (667)11.7.2Swiveling tool (CYCLE800) (671)11.7.2.1Swiveling tool/preloading milling tools - only for G code program (CYCLE800) (671)11.7.2.2Aligning turning tools (CYCLE800) - millling/turning machine (672)11.7.3High-speed settings (CYCLE832) (677)11.7.4Subroutines (681)11.7.5Adapt to load (CYCLE782) (683)11.7.6Interpolation turning (CYCLE806) (685)11.7.6.1Function (685)11.7.6.2Selecting/deselecting interpolation turning - CYCLE806 (686)11.7.6.3Calling the cycle (687)11.7.6.4Parameter (687)11.8Additional cycles and functions in ShopMill (688)11.8.1Transformations (688)11.8.2Translation (689)11.8.3Rotation (689)11.8.4Scaling (690)11.8.5Mirroring (691)11.8.6Cylinder surface transformation (691)11.8.7Straight or circular machining (694)11.8.8Programming a straight line (696)Table of contents11.8.9Programming a circle with known center point (697)11.8.10Programming a circle with known radius (698)11.8.11Helix (699)11.8.12Polar coordinates (700)11.8.13Straight polar (701)11.8.14Circle polar (701)11.8.15Obstacle (702)12Multi-channel view (705)12.1Multi-channel view (705)12.2Multi-channel view in the "Machine" operating area (706)12.3Multi-channel view for large operator panels (709)12.4Setting the multi-channel view (711)13Collision avoidance (713)13.1Activate collision avoidance (715)13.2Set collision avoidance (716)14Tool management (719)14.1Lists for the tool management (719)14.2Magazine management (721)14.3Tool types (722)14.4Tool dimensioning (725)14.5Tool list (732)14.5.1Additional data (735)14.5.2Creating a new tool (736)14.5.3Measuring the tool (738)14.5.4Managing several cutting edges (738)14.5.5Delete tool (739)14.5.6Loading and unloading tools (739)14.5.7Selecting a magazine (741)14.5.8Code carrier connection (742)14.5.9Managing a tool in a file (744)14.6Tool wear (747)14.6.1Reactivating a tool (749)14.7Tool data OEM (751)14.8Magazine (752)14.8.1Positioning a magazine (754)14.8.2Relocating a tool (754)14.8.3Deleting / unloading / loading / relocating all tools (755)14.9Tool details (757)14.9.1Displaying tool details (757)14.9.2Tool data (757)14.9.3Cutting edge data (758)14.9.4Monitoring data (760)14.10Changing a tool type (761)Table of contents14.11Graphic display (762)14.12Sorting tool management lists (764)14.13Filtering the tool management lists (765)14.14Specific search in the tool management lists (767)14.15Multiple selection in the tool management lists (769)14.16Settings for tool lists (770)14.17Working with Multitool (771)14.17.1Tool list for multitool (771)14.17.2Create multitool (772)14.17.3Equipping multitool with tools (774)14.17.4Removing a tool from multitool (775)14.17.5Deleting multitool (776)14.17.6Loading and unloading multitool (776)14.17.7Reactivating the multitool (777)14.17.8Relocating a multitool (778)14.17.9Positioning a multitool (779)15Managing programs (781)15.1Overview (781)15.1.1NC memory (784)15.1.2Local drive (784)15.1.3USB drives (786)15.1.4FTP drive (786)15.2Opening and closing the program (788)15.3Executing a program (790)15.4Creating a directory / program / job list / program list (792)15.4.1File and directory names (792)15.4.2Creating a new directory (792)15.4.3Creating a new workpiece (793)15.4.4Creating a new G code program (794)15.4.5Creating a new ShopMill program (794)15.4.6Storing any new file (795)15.4.7Creating a job list (796)15.4.8Creating a program list (798)15.5Creating templates (799)15.6Searching directories and files (800)15.7Displaying the program in the Preview (802)15.8Selecting several directories/programs (803)15.9Copying and pasting a directory/program (805)15.10Deleting a program/directory (807)15.10.1Deleting a program/directory (807)15.11Changing file and directory properties (808)15.12Set up drives (810)Table of contents15.12.1Overview (810)15.12.2Setting up drives (810)15.13Viewing PDF documents (816)15.14EXTCALL (819)15.15Execution from external memory (EES) (821)15.16Backing up data (822)15.16.1Generating an archive in the Program Manager (822)15.16.2Generating an archive via the system data (823)15.16.3Reading in an archive in the Program Manager (825)15.16.4Read in archive from system data (826)15.17Setup data (828)15.17.1Backing up setup data (828)15.17.2Reading-in set-up data (830)15.18Recording tools and determining the demand (832)15.18.1Overview (832)15.18.2Opening tool data (833)15.18.3Checking the loading (833)15.19Backing up parameters (835)15.20RS-232-C (838)15.20.1Reading-in and reading-out archives via a serial interface (838)15.20.2Setting V24 in the program manager (839)15.21Multiple clamping (841)15.21.1Multiple clamping (841)15.21.2Program header setting, "Clamping" (842)15.21.3Creating a multiple clamping program (843)16Service and diagnostics (845)16.1Alarm, error, and system messages (845)16.1.1Displaying alarms (845)16.1.2Displaying an alarm log (847)16.1.3Displaying messages (848)16.1.4Sorting, alarms, faults and messages (848)16.1.5Deactivating system alarms (849)16.2PLC and NC variables (851)16.2.1Displaying and editing PLC and NC variables (851)16.2.2Saving and loading screen forms (855)16.3Creating screenshots (856)16.4Version (857)16.4.1Displaying version data (857)16.4.2Save information (858)16.5Logbook (860)16.5.1Displaying and editing the logbook (860)16.5.2Making a logbook entry (861)16.6Remote diagnostics (863)16.6.1Setting remote access (863)Table of contents16.6.2Permit modem (864)16.6.3Request remote diagnostics (865)16.6.4Exit remote diagnostics (866)17Working with Manual Machine (867)17.1Manual Machine (867)17.2Measuring the tool (869)17.3Measuring the workpiece zero (870)17.4Setting the zero offset (871)17.5Set limit stop (872)17.6Simple workpiece machining (873)17.6.1Traversing axes (873)17.6.2Angular milling (874)17.6.3Straight and circular machining (875)17.6.3.1Straight milling (875)17.6.3.2Circular milling (876)17.7More complex machining (878)17.7.1Drilling with Manual Machine (879)17.7.2Milling with Manual Machine (880)17.7.3Contour milling with manual machine (881)17.7.4Turning with manual machine - milling/turning machine (881)17.8Simulation and simultaneous recording (883)18Teaching in a program (885)18.1Overview (885)18.2Select teach in mode (887)18.3Processing a program (888)18.3.1Inserting a block (888)18.3.2Editing a block (888)18.3.3Selecting a block (889)18.3.4Deleting a block (889)18.4Teach sets (891)18.4.1Input parameters for teach-in blocks (892)18.5Settings for teach-in (894)19Handheld terminals for multi-touch operation (895)19.1HT 8 (895)19.1.1HT 8 overview (895)19.1.2Traversing keys (897)19.1.3Machine control panel menu (898)19.1.4Virtual keyboard (900)19.2HT 10 (902)19.2.1HT 10: Overview (902)19.2.2Machine control panel menu (904)19.2.3Virtual keyboard (906)19.3Calibrating the touch panel (907)Table of contents20Ctrl-Energy (909)20.1Functions (909)20.2Ctrl-E analysis (910)20.2.1Displaying energy consumption (910)20.2.2Displaying the energy analyses (911)20.2.3Measuring and saving the energy consumption (912)20.2.4Tracking measurements (913)20.2.5Tracking usage values (913)20.2.6Comparing usage values (914)20.2.7Long-term measurement of the energy consumption (915)20.3Ctrl-E profiles (916)20.3.1Creating and editing energy-saving profiles (916)20.3.2Using the energy-saving profile (919)Index (921)。
- 1、下载文档前请自行甄别文档内容的完整性,平台不提供额外的编辑、内容补充、找答案等附加服务。
- 2、"仅部分预览"的文档,不可在线预览部分如存在完整性等问题,可反馈申请退款(可完整预览的文档不适用该条件!)。
- 3、如文档侵犯您的权益,请联系客服反馈,我们会尽快为您处理(人工客服工作时间:9:00-18:30)。
Diagnostics Used in Commissioning the IUCF Cooler Injector SynchrotronMark S. Ball, Dennis L. Friesel, Brett J. HamiltonIndiana University Cyclotron Facility2401 Milo Sampson Ln., Bloomington, IN 47408Abstract. Several new diagnostics systems were designed to aid in the commissioning of the IUCF Cooler Injection Synchrotron (CIS). Among them are a time of flight measurement system (ToF), a multi-wire profile monitor system (Harp) and a beam position monitor system (BPM).Pulsed beam from the 7 MeV linear accelerator is monitored using the ToF system. Several removable Harps are mounted in the injection beamline and ring which are instrumental f or tuning ring injection and accumulation. BPMs are placed at the entrance and exit of the four ring dipole magnets to facilitate beam centering during injection and ramping. Fast and slow BPM displays are available to the operator for these functions. These diagnostics and their uses for CIS ring commissioning will be discussed.ENERGY MEASUREMENTA time of flight system (ToF) is being used in the 7 MeV injection beamline to detect changes in the beam energy from the RFQ/DTL. The system is similar to the one used at TRIUMF (1), where a change in energy is measured as a change in phase between two pickups of a fixed, known distance apart.The 200 µs pulsed beam is accelerated through the RFQ/DTL using a 425 MHz, 300 kW rf amp. The non-interceptive, resonant, beam pickups are immediately down-stream of the accelerator, 2.5 meters apart. A beam signal is detected, buffered and sent to the ToF electronics. An Analog Device AD607 (2) is used as an rf to if, 10.7 MHz, converter.The AD607 is normally used in wireless communications as a down-converter amplifier. It has a mixer and log amp with AGC, as well as, an I & Q demodulator, all in a 20-pin surface-mount chip. It has been tested in the lab as an AGC beam position d etector with a 75 dB range. The output of the AD607 is a constant 300 mV signal, which is fed into limiting amps and then a type II phase detector. The output is filtered to a DC level, amplified, and displayed on a scope.In order to achieve an energy of 7 MeV, the DTL amplifier must be operated in an unregulated mode, relying on a large capacitance to hold the charge over the 200 µs pulseperiod. The resultant output energy can sag by as much as 500 keV over the span of the pulse period. Using the ToF monitor, the amplifier can be adjusted to minimize the sag (Fig. 1), flattening the output energy to the acceptance of the CIS injection aperture, 180 keV. The monitor also provides a good comparison b etween beam intensity o n the stop in the CIS ring and the energy.FIGURE 1. T op display is the ToF. The average energy is 7 MeV. The bottom display is the CIS stop located downstream of the first dipole. The energy sag at the end of the ToF pulse corresponds with the sag in intensity on the stop.BEAM PROFILE MONITORSMechanically, the CIS Harps are very similar to those used in other labs. They are secondary emission multi-wire chambers using high-voltage cathode grids and multi-pin vacuum connectors. E ach detector b oard uses 24 wire grids with 1 mm spacing. The circuit board is also a familiar design, using a large RC time constant at the input of the detector. The 48 signals are multiplexed through a single integrator. One interesting aspect of the Harp electronics design is the timing electronics, which are incorporated on the printed circuit board using a programmable array logic chip (PAL). A trigger from the devices on the board provides the ADC clock. The data acquisition parameters can be changed by reprogramming the PAL. This permits data acquisition and display of Harp signals to occur in two ways. For operations, the signal goes to a fast ADC with FIFO memory allowing the user to acquire data at a fast rate and display it whenever desired on the operations monitor.During commissioning and troubleshooting, a stand-alone display system is used, incorporating a PC and graphical programming package from Hewlett-Packard, HP VEE, (3). The Harp has been the primary diagnostic during commissioning of the CIS ring. Two Harps have been placed in the ring injection beamline and one in the ring. The first Harp is mounted in front of a stop, allowing one to monitor intensity and shape of the beam over 200 µs pulse length while adjusting the profile. The Harps are moved in and out of the beam path using air actuated insertion devices. The flexibility of this setup, allows an operator to observe a Harp display of first-turn beam in the CIS ring along with multi-turns (Fig. 2) and also accumulate maximum intensity with the Harp out of the beam path. Plans have been made to remove the Harp presently used in CIS and replace it with a new low-profile design. There will also be five Harps in the beamline connecting CIS to the Cooler.FIGURE 2. T he CIS Harp as seen using HP-VEE. The small traces are first-turn beam in the ring. The large traces are multiple turns.BEAM POSITION MONITORSThere are eight BPMs (4) in the CIS ring, positioned at the entrance and exit of each of four dipole magnets. All signal conversion is done at the pickup and the DC signals are multiplexed to different areas. The wide bandwidth of the position signals is useful for observing and changing ramp vectors, which are spaced every 11 ms (Fig 3). For the moment, vectors are changed by hand, but plans have been made to implement a feed forward loop to automatically a djust the vectors to keep the beam centered in the ring during ramping.FIGURE 3. T he upper display is the beam position (2 mm/Div.) in the CIS ring during a 7 MeV ramp. The bottom display is the intensity during the same ramp.W ALL GAP MONITORA wall gap monitor (WGM) is used to provide bunched beam information such as bunching factor measurements, and to observe beam intensity losses during the ramp (Fig. 4). A digital oscilloscope is used to capture the signal and display it for the operator. During ramping, losses are easily detected by comparing amplitude losses with BPM position distortions.FIGURE 4. T he top display is the WGM output during a 225 MeV ramp. The bottom display is the output from a logarithmic amplifier of the same ramp.REFERENCES[1]Yin, Y., R. E. Laxdal, A. Zelenski, P. Ostroumov, “A Very Sensitive N on-InterceptingBeam Average Velocity Monitoring System for the TRIUMF 300-keV Injection Line,”Beam Instrumentation Workshop, Argonne, IL, May, 1996.[2]Hewlett-Packard “Test and Measurement Catalog,” pp. 47–49, 1996.[3]Analog Devices “Linear Products Data Book,” pp. 7.7–22, 1990/91.[4]Ball, M., V. Derenchuk, B. J. Hamilton, “Beam Diagnostics in the Indiana UniversityCooler Injector Synchrotron” in Beam Instrumentation Workshop (Argonne, IL, May 1996), pp. 544–548.。