PCD刀具技术的新发展
2023年先进刀具技术与未来刀具的发展趋势模板

数控刀具
人工智能
500亿美元
机器学习
金刚石涂层
陶瓷材料
自适应刀具技术
年复合增长率
6%
刀具技术在未来制造业中的应用
刀具材料的优化与创新
1.刀具材料创新:从石器时代到现代切削技术时代
2.超硬材料:高速切削、高效加工的首选材料
3.纳米材料引领刀具材料未来发展
自动化与智能化刀具生产
智能刀具具备自动化加工功能,可根据加工要求实现自动化的刀具选择、夹持和更换操作。
Application of Tool Technology in the Cutting Era
2023/9/9 星期六
Lucy
刀具技术在切削时代的应用
Contents
先进刀具技术在未来制造业中的应用
Application of Advanced Tool Technology in Future Manufacturing Industry
1.切削加工技术:涂层刀具与高速钻头助力提升效率与质量
2.刀具环保节能趋势崛起,绿色制造成竞争关键
刀具技术的前沿研究与应用
Thanks
2023/9/9 星期六
分享人-Lucy
2. 智能刀具材料和涂层技术:研发更先进的刀具材料和涂层技术,以提高刀具的硬度、耐磨性和耐热性。通过智能材料的应用,刀具可以更好地抵抗高温、高速和大切削力环境的影响,延长刀具的使用寿命,提高切削效率,并减少生产过程中的停机时间和维护成本。
3. 刀具智能化管理系统:建立刀具智能化管理系统,实现对刀具的全生命周期管理。通过集成物联网技术、云计算和大数据分析,可以对刀具的采购、入库、出库、使用和维护等环节进行实时追踪和监控,提高刀具的利用率和管理效率。同时,通过分析和挖掘大数据,可以优化刀具的使用方式和维护策略,提高刀具的整体效益和生命周期成本控制。
高速切削刀具材料的进展和未来

高速切削刀具材料的进展和未来ΞProgre ss and Pro spect of H igh-speed Cutting T ool Material艾 兴 刘战强 赵 军 邓建新 宋世学(山东大学机械工程学院) 摘 要:文章结合高速切削技术和刀具材料的研究,综述了高速切削刀具材料的进展和应用,阐明了我国高速切削刀具材料面临的机遇和挑战,指出了高速切削刀具材料的未来。
关键词:高速切削 刀具材料1 概况 机械加工发展的总趋势是高效率、高精度、高柔性和强化环境意识。
在机械加工领域,切(磨)削加工是应用最广泛的加工方法。
高速切削是切削加工的发展方向,已成为切削加工的主流。
它是先进制造技术的重要共性关键技术。
推广应用高速切削技术将大幅度提高生产效率和加工质量并降低成本。
高速切削技术的发展和应用决定于机床和刀具技术的进步,其中刀具材料的进步起决定性的作用[1]。
研究表明[2、9],高速切削时,随着切削速度的提高,切削力减小,切削温度上升很高,达到一定值后上升逐渐趋缓[2]。
造成刀具损坏最主要的原因是切削力和切削温度作用下的机械摩擦、粘结、化学磨损、崩刃、破碎以及塑性变形等磨损和破损,因此高速切削刀具材料最主要的要求是高温时的力学性能、热物理性能、抗粘结性能、化学稳定性(氧化性、扩散性、溶解度等)和抗热震性能以及抗涂层破裂性能等。
基于这一要求,近20多年来,发展了一批适于高速切削的刀具材料,可在不同切削条件下,切削加工各种工件材料[3、4、7]。
目前,可以2500~5000m/min的高速切削铝合金(S i含量Φ12%,大于12%的为500~1500m/min);以500~1500m/min切削铸铁;300~1000m/min切削钢;100~400m/min切削淬硬钢;90~200m/min切削钛合金等。
当然人们还期待着以超高切削速度进行加工而获得更好的效果。
2 国外高速切削刀具材料的进展和应用 高速切削时,对不同的工件材料选用与其合理匹配的刀具材料和允许的切削条件,才能获得最佳的切削效果。
PCD刀具的应用与发展
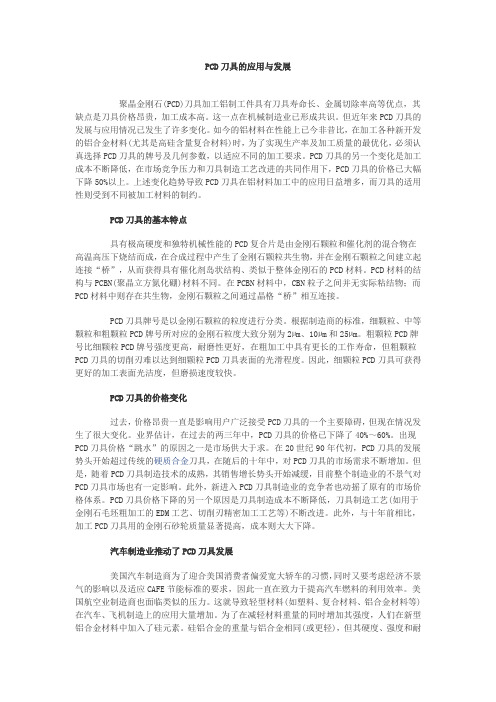
PCD刀具的应用与发展聚晶金刚石(PCD)刀具加工铝制工件具有刀具寿命长、金属切除率高等优点,其缺点是刀具价格昂贵,加工成本高。
这一点在机械制造业已形成共识。
但近年来PCD刀具的发展与应用情况已发生了许多变化。
如今的铝材料在性能上已今非昔比,在加工各种新开发的铝合金材料(尤其是高硅含量复合材料)时,为了实现生产率及加工质量的最优化,必须认真选择PCD刀具的牌号及几何参数,以适应不同的加工要求。
PCD刀具的另一个变化是加工成本不断降低,在市场竞争压力和刀具制造工艺改进的共同作用下,PCD刀具的价格已大幅下降50%以上。
上述变化趋势导致PCD刀具在铝材料加工中的应用日益增多,而刀具的适用性则受到不同被加工材料的制约。
PCD刀具的基本特点具有极高硬度和独特机械性能的PCD复合片是由金刚石颗粒和催化剂的混合物在高温高压下烧结而成,在合成过程中产生了金刚石颗粒共生物,并在金刚石颗粒之间建立起连接“桥”,从而获得具有催化剂岛状结构、类似于整体金刚石的PCD材料。
PCD材料的结构与PCBN(聚晶立方氮化硼)材料不同。
在PCBN材料中,CBN粒子之间并无实际粘结物;而PCD材料中则存在共生物,金刚石颗粒之间通过晶格“桥”相互连接。
PCD刀具牌号是以金刚石颗粒的粒度进行分类。
根据制造商的标准,细颗粒、中等颗粒和粗颗粒PCD牌号所对应的金刚石粒度大致分别为2µm、10µm和25µm。
粗颗粒PCD牌号比细颗粒PCD牌号强度更高,耐磨性更好,在粗加工中具有更长的工作寿命,但粗颗粒PCD刀具的切削刃难以达到细颗粒PCD刀具表面的光滑程度。
因此,细颗粒PCD刀具可获得更好的加工表面光洁度,但磨损速度较快。
PCD刀具的价格变化过去,价格昂贵一直是影响用户广泛接受PCD刀具的一个主要障碍,但现在情况发生了很大变化。
业界估计,在过去的两三年中,PCD刀具的价格已下降了40%~60%。
出现PCD刀具价格“跳水”的原因之一是市场供大于求。
PCBNPCD刀具的应用及发展趋势
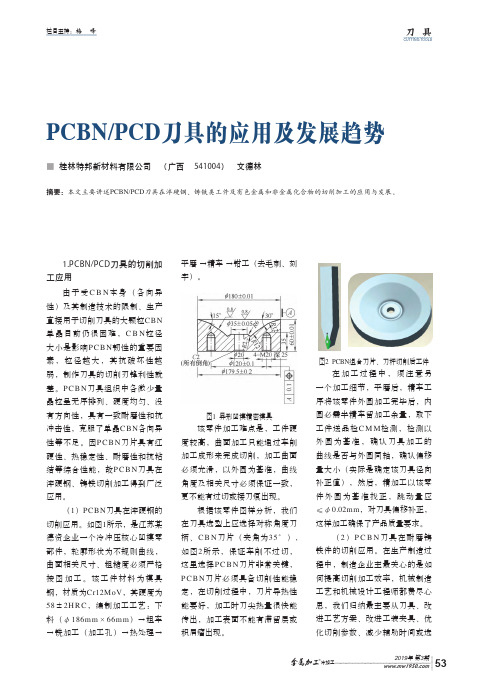
2019年 第3期冷加工53CUTTING TOOLS刀 具PCBN/PCD 刀具的应用及发展趋势■桂林特邦新材料有限公司 (广西 541004) 文德林摘要:本文主要讲述PCBN/PCD 刀具在淬硬钢、铸铁类工件及有色金属和非金属化合物的切削加工的应用与发展。
1.PCBN/PCD 刀具的切削加工应用由于受C B N 本身(各向异性)及其制造技术的限制、生产直接用于切削刀具的大颗粒CBN 单晶目前仍很困难,C B N 粒径大小是影响P C B N 韧性的重要因素,粒径越大,其抗破坏性越弱,制作刀具的切削刃锋利性就差。
P C B N 刀具组织中各微少量晶粒呈无序排列、硬度均匀、没有方向性,具有一致耐磨性和抗冲击性,克服了单晶CBN 各向异性等不足。
因P C B N 刀片具有红硬性、热稳定性、耐磨性和抗粘结等综合性能,故P C B N 刀具在淬硬钢、铸铁切削加工得到广泛应用。
(1)PCBN 刀具在淬硬钢的切削应用。
如图1所示,是江苏某德资企业一个冷冲压核心凹模零部件,轮廓形状为不规则曲线,曲面相关尺寸、粗糙度必须严格按图加工。
该工件材料为模具钢,材质为Cr12MoV ,其硬度为58±2H R C ,编制加工工艺:下料(φ186m m ×66m m )→粗车→铣加工(加工孔)→热处理→平磨 →精车 →钳工(去毛刺、刻字)。
图1 异形凹模精密模具该零件加工难点是,工件硬度较高,曲面加工只能通过车削加工成形来完成切削,加工曲面必须光滑,以外圆为基准,曲线角度及相关尺寸必须保证一致,更不能有过切或接刀痕出现。
根据该零件图样分析,我们在刀具选型上应选择对称角度刀柄、C B N 刀片(夹角为35°),如图2所示,保证车削不过切,这里选择P C B N 刀片非常关键,P C B N 刀片必须具备切削性能稳定,在切削过程中,刀片导热性能要好,加工时刀尖热量很快能传出,加工表面不能有滞留层或积屑瘤出现。
pcd工艺技术

pcd工艺技术PCD工艺技术(Polycrystalline Diamond)是一种综合利用钻石结晶技术制造的新材料。
它具有钻石硬度高、耐磨性好和热稳定性好等特点,被广泛应用于机械加工、矿山工具、石油勘探等领域。
PCD工艺技术的制造过程主要包括镀膜、压制和烧结三个步骤。
首先,在刀具表面镀上一层金属膜,以增加PCD与基体的结合力。
然后,将金属粉末与聚结剂混合均匀,填充在模具中,经过高温高压的条件下,金属粉末固化成坚硬的基体。
最后,将钻石晶粒均匀分布在基体中,再次进行高温高压的处理,使钻石晶粒与基体结合紧密,形成具有钻石硬度的PCD。
PCD工艺技术的优点主要体现在以下几个方面。
首先,PCD材料的硬度可达到钻石的六倍,因此具有极高的耐磨性。
在机械加工领域,使用PCD材料制造的刀具能够在高速切削和重负荷的工况下保持长时间的使用寿命。
其次,PCD材料具有极高的热稳定性,能够在高温和高速的加工环境下保持稳定的性能。
在石油勘探领域,使用PCD材料制造的特殊钻头能够快速、高效地穿透各种复杂的地层。
此外,PCD材料的导电性好,因此可以应用于电子器件的制造。
最后,PCD材料的结构稳定,不会轻易损坏,因此能够在恶劣的工作环境中长期使用。
然而,PCD工艺技术也存在一些挑战和局限性。
首先,PCD材料的制造工艺复杂,需要采用高温高压的处理,因此生产成本较高。
其次,由于钻石是一种贵重的材料,PCD材料的价格也相对较高,限制了其在一些领域的广泛应用。
此外,由于PCD材料的硬度高,加工和修复过程相对困难,也增加了维护和使用成本。
总之,PCD工艺技术是一种重要的先进材料制备技术。
它适用于各种领域,如机械加工、矿山工具和石油勘探等。
尽管制造工艺复杂,成本较高,但其优异的性能使其在特定领域有着广阔的应用前景。
未来,随着科技的不断发展,PCD工艺技术有望进一步完善,降低生产成本,提高材料性能,推动其在更多领域的应用。
ANCA整体PCD铣刀提高生产效率带来新的发展机遇

刀具应用ANCA 整体PCD 铣刀——提高生产效率带来新的发展机遇■文/ ANCA 对外交流与公共关系部经理Sepideh Zandieh金刚石(或PCD-聚晶金刚石)刀具在正 确的应用中,使用寿命是同等硬质合金刀具的20倍。
令人兴奋的是在ANCA 的EDGe 磨床上 制造的新一代整体PCD 螺旋立铣刀和钻头将进 —步扩大这一优势。
在3C (电子)和航空航天 制造业中,对于能够提供更高的生产率和质量的刀具,存在着巨大的需求。
硬质合金钎焊上PCD 顶尖,用来制造螺旋刀作为一台5轴数控机床,ANCA EDGe 带 有旋转电火花加工工艺,非常适合制造复杂的三 维切削刀具。
“ANCA 拥有软件开发的传统,使用ToolRoom 软件可以设计和制造旋转刀具上 的复杂几何图形。
除了螺旋钻头,我们最新发布的软件支持客户制造螺旋立铣刀(直角、圆角 和球头)。
” ANCA EDGe 和金刚石刀具产品经理Duncan Thompson 表示。
用EDGe 制造整体PCD 顶尖球头立铳刀和钻头实对于PCD 切削刀具制造商来说,此功能恰 逢其时,因为市场需求与技术发展携手共进,使带PCD 顶尖的刀具既经济又理想。
与传统PCD 刀具的剪切刃相比,用户想要更长的使用寿命和 更好的切割性能。
航空航天,尤其是3C 产业,正在推动这一发展进程。
此外,整体PCD 顶尖 的生产工艺已经成熟,变得更加经济实惠。
灵活性使PCD 顶尖刀具品质出众整体PCD 顶尖刀具具有许多优势。
最重要的是,刀具几何形状具有完全的灵活性。
EDGe 磨床的ToolRoom 软件使用户能够创建螺旋切削刀具(包括钻头和立铣刀),与具有钎焊PCD 刀 片的同等刀具相比,具有更优越的切削性能。
传统的PCD 旋转切削刀具通常将PCD 刀片钎焊到硬质合金刀具主体上。
虽然PCD 可以-84 -第io 期数控机床市场刀具应用延长切削刃的寿命,但根据设计,切削刃的几何形状是剪切(直)刃带直前角。
国外切削加工用PCD与PCBN的发展与应用
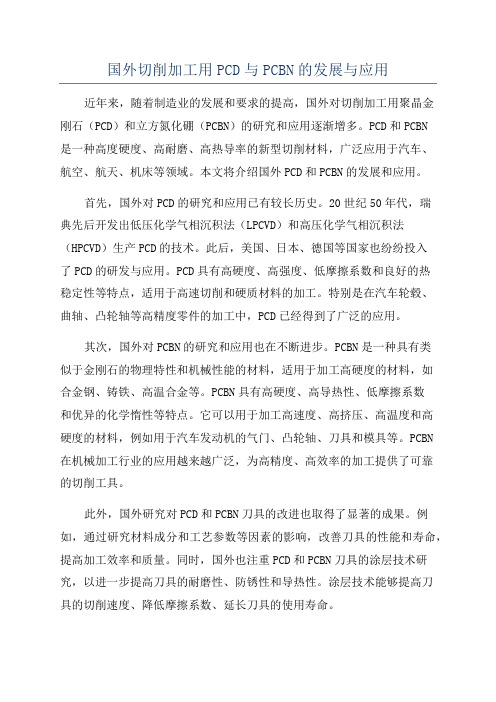
国外切削加工用PCD与PCBN的发展与应用近年来,随着制造业的发展和要求的提高,国外对切削加工用聚晶金刚石(PCD)和立方氮化硼(PCBN)的研究和应用逐渐增多。
PCD和PCBN是一种高度硬度、高耐磨、高热导率的新型切削材料,广泛应用于汽车、航空、航天、机床等领域。
本文将介绍国外PCD和PCBN的发展和应用。
首先,国外对PCD的研究和应用已有较长历史。
20世纪50年代,瑞典先后开发出低压化学气相沉积法(LPCVD)和高压化学气相沉积法(HPCVD)生产PCD的技术。
此后,美国、日本、德国等国家也纷纷投入了PCD的研发与应用。
PCD具有高硬度、高强度、低摩擦系数和良好的热稳定性等特点,适用于高速切削和硬质材料的加工。
特别是在汽车轮毂、曲轴、凸轮轴等高精度零件的加工中,PCD已经得到了广泛的应用。
其次,国外对PCBN的研究和应用也在不断进步。
PCBN是一种具有类似于金刚石的物理特性和机械性能的材料,适用于加工高硬度的材料,如合金钢、铸铁、高温合金等。
PCBN具有高硬度、高导热性、低摩擦系数和优异的化学惰性等特点。
它可以用于加工高速度、高挤压、高温度和高硬度的材料,例如用于汽车发动机的气门、凸轮轴、刀具和模具等。
PCBN在机械加工行业的应用越来越广泛,为高精度、高效率的加工提供了可靠的切削工具。
此外,国外研究对PCD和PCBN刀具的改进也取得了显著的成果。
例如,通过研究材料成分和工艺参数等因素的影响,改善刀具的性能和寿命,提高加工效率和质量。
同时,国外也注重PCD和PCBN刀具的涂层技术研究,以进一步提高刀具的耐磨性、防锈性和导热性。
涂层技术能够提高刀具的切削速度、降低摩擦系数、延长刀具的使用寿命。
综上所述,国外对切削加工用PCD和PCBN的研究和应用逐渐成熟。
PCD和PCBN的高硬度、高强度和优异的耐磨性使其在高精度、高效率的加工中具有广泛的应用前景。
未来,随着制造技术的不断发展和需求的不断增加,PCD和PCBN材料和刀具的研究与应用将会有更好的发展。
关于PCD刀具,最全的都在这了

关于PCD刀具,最全的都在这了PCD刀具介绍:PCD刀具是采用超硬材料PCD(聚晶金刚石)与刀具基体通过特殊工艺制成的刀具。
PCD刀具的特点:硬度高、抗压强度高、导热性好、耐磨性好。
PCD刀具主要指标:1、PCD的硬度可达8000HV,为硬质合金的8~12倍;2、PCD的导热系数为700W/mK,为硬质合金的1.5~9倍,甚至高于PCBN和铜,因此PCD刀具热量传递迅速;3、PCD的摩擦系数一般仅为0.1~0.3(硬质合金的摩擦系数为0.4~1),因此PCD刀具可显著减小切削力;4、PCD的热膨胀系数仅为0.9×10^-6~1.18×10^-6,仅相当于硬质合金的1/5,因此PCD刀具热变形小,加工精度高;5、PCD刀具与有色金属和非金属材料间的亲和力很小,在加工过程中切屑不易粘结在刀尖上形成积屑瘤。
PCD刀具制造技术:制造过程PCD刀具的制造过程主要包括两个阶段:1、PCD复合片的制造:PCD复合片是由天然或人工合成的金刚石粉末与结合剂(其中含钴、镍等金属)按一定比例在高温(1000~2000℃)、高压(5~10万个大气压)下烧结而成。
在烧结过程中,由于结合剂的加入,使金刚石晶体间形成以TiC、SiC、Fe、Co、Ni 等为主要成分的结合桥,金刚石晶体以共价键形式镶嵌于结合桥的骨架中。
通常将复合片制成固定直径和厚度的圆盘,还需对烧结成的复合片进行研磨抛光及其它相应的物理、化学处理。
2、PCD刀片的加工:PCD刀片的加工主要包括复合片的切割、刀片的焊接、刀片刃磨等步骤。
切割工艺由于PCD刀具具有很高的硬度及耐磨性,因此必须采用特殊的加工工艺。
目前,加工PCD复合片主要采用电火花线切割、激光加工、超声波加工、高压水射流等几种工艺方法,其工艺特点的比较见表1。
在上述加工方法中,电火花加工效果较佳。
PCD中结合桥的存在使电火花加工复合片成为可能。
在有工作液的条件下,利用脉冲电压使靠近电极金属处的工作液形成放电通道,并在局部产生放电火花,瞬间高温可使聚晶金刚石熔化、脱落,从而形成所要求的三角形、长方形或正方形的刀头毛坯。
- 1、下载文档前请自行甄别文档内容的完整性,平台不提供额外的编辑、内容补充、找答案等附加服务。
- 2、"仅部分预览"的文档,不可在线预览部分如存在完整性等问题,可反馈申请退款(可完整预览的文档不适用该条件!)。
- 3、如文档侵犯您的权益,请联系客服反馈,我们会尽快为您处理(人工客服工作时间:9:00-18:30)。
PCD刀具技术的新发展
为了满足用户对PCD刀具切削性能不断提高的要求,在竞争激烈的PCD刀具市场占有更大份额,刀具制造商正不断对PCD刀具技术进行与提高。
美国Diamond Abrasive公司通过优化PCD烧结工艺,促使金刚石颗粒之间生成的共生物增大,从而提高了粗颗粒PCD刀具的耐磨性。
该公司开发的CTH025牌号的耐磨性比同类型粗颗粒PCD牌号提高了25%~30%,该牌号被设计用于切削具有高耐磨性的铝合金属基复合材料(MMC).
Diamond Abrasive 公司还推出了一种称为“multimodal”的新型PCD牌号,这种牌号原来是为对刀具韧性要求极高的采矿业开发的,其特点是每片材料中都分布着各种不同粒度尺寸的金刚石颗粒,例如,mutimodal牌号CTM302的材料中包含了粒度尺寸从2µm到30µm的金刚石颗粒。
这种由大、小粒度混合构成的刀具切削刃性能相当于金刚石粒度为10µm的刀片性能,而刀具的寿命则超过了仅由单一粗颗粒金刚石制成的PCD刀具。
几年前,美国Sumi tomo Electric Carbide 公司曾推出一种称为DA2200的亚微细粒度(0.5µm)的PCD牌号,该牌号的PCD刀具可加工出极高的工件表面光洁度。
且具有几乎可与硬质合金媲美的高强度。
为了应对近来PCD刀具大幅降价的压力,该公司又开发了价格较低的DA2200牌号刀具以替代价格较贵的原型刀具。
由于采用了先进的PCD烧结工艺,从而可制备出PCD金刚石层厚度仅为标准的厚度1/3的DA2200复合片,用这种复合片制造的刀具与金刚石层较厚的PCD刀具强度相同,但所消耗的金刚石材料以及刀坯磨削工序中的材料去除量显著减少,从而降低了刀具的制造成本。
近来,采用PCD刀尖的多功能旋转刀具的开发与应用日渐增多。
这种刀具可在一次走刀中完成钻孔、扩孔、倒角、精修等多道孔加工工序,用于汽车制造业可有效降低加工成本,如一把多功能PCD刀具在需要重磨前可加工多达几千件汽车传动箱零件。
Clapp Dico 公司新开发了一种不需要重磨的超速(Super Speed)PCD铣刀。
该铣刀上装夹了多个不需重磨的小刀尖PCD刀片,刀片上的断屑槽可实现对切屑的有效控制;铣刀到本体采用轻型不锈钢制造,可避免耐磨铝合金切屑和冷却/冲洗液对刀体的损害。
该铣刀上还集成了一个由凸轮驱动的轴向调节装置,可对PCD刀片的轴向尺寸进行精确的微调,并实现了刀具硬件结构的最小化。
随着PCD刀具切削性能的不断提升和PCD刀具价格的不断下降,PCD刀具对于广大的用户具有了前所未有的吸引力,这将有助于推动数控刀具的普及应用以及数控刀具技术更快地
向前发展。