基于传热传质的氧化铝溶解过程分析和建模
化学工程中的传质过程优化与模拟

化学工程中的传质过程优化与模拟传质过程是化学工程中的重要环节,它涉及物质在不同相之间的传递和分布。
优化传质过程可以提高反应效率、降低能源消耗,进而改善产品质量和降低生产成本。
而模拟传质过程则可以帮助工程师更好地理解和预测实际系统的行为,为工艺设计和操作提供指导。
传质过程中最常见的一种现象是扩散。
扩散是指物质由高浓度区域向低浓度区域的自发移动。
在化学工程中,我们经常需要将反应物输送到反应器中,或者将产物从反应器中分离出来。
因此,了解和控制扩散过程对于化学工程师来说至关重要。
优化传质过程的方法有很多种,其中一种常用的方法是通过改变传质介质的性质来提高传质速率。
传质介质的选择可以根据具体的应用需求进行优化。
例如,在某些情况下,选择具有较大表面积的填料可以增加传质界面的面积,从而提高传质速率。
另外,改变传质介质的物理性质,如粒径、孔隙度等,也可以改善传质过程。
此外,还可以通过在传质介质中添加助剂或表面活性剂来改变传质过程的性质,提高传质速率。
除了优化传质介质的性质外,改变传质条件也是优化传质过程的重要手段之一。
传质速率与温度、压力、浓度等因素密切相关。
通过调节这些因素,可以改变传质速率,实现传质过程的优化。
例如,在某些情况下,提高温度可以增加物质的扩散速率,从而加快传质过程。
另外,通过改变传质过程中的压力差或浓度差,也可以改变传质速率。
因此,在实际工程中,我们可以根据具体情况调整传质条件,以达到最佳的传质效果。
传质过程的模拟是化学工程中的重要工具之一。
通过模拟传质过程,我们可以更好地理解和预测实际系统的行为。
在过去,传质过程的模拟主要依靠实验方法,但是实验方法通常费时费力且成本较高。
而借助计算机模拟技术,我们可以更快速、更经济地进行传质过程的模拟。
通过建立数学模型,我们可以模拟传质过程中的物质传递和分布,从而预测系统的行为。
这对于工艺设计、操作优化和故障诊断都具有重要意义。
传质过程的模拟需要考虑多个因素,如传质介质的性质、传质条件、反应动力学等。
氧化铝浓相输送过程的两相流建模及参数测量问题的研究的开题报告

氧化铝浓相输送过程的两相流建模及参数测量问题的研究的开题报告一、选题的背景与意义氧化铝是一种广泛应用于工业生产中的重要材料,其生产过程中需要进行浓相输送,将浓缩后的氧化铝浆料输送至下一道工艺流程。
但是,在氧化铝浓相输送的过程中,会出现颗粒的堵塞、腐蚀等问题,导致输送效率和设备寿命的降低,因此需要对氧化铝浓相输送过程进行深入研究,提高其效率和可靠性。
基于此,本课题将研究氧化铝浓相输送过程的两相流建模及参数测量问题,以实现对氧化铝浓相输送过程的科学控制和优化设计,从而提高生产效率和产品质量。
二、研究内容与方案本课题的研究内容主要包括以下几个方面:1. 氧化铝浓相输送过程的流体力学性质分析通过对氧化铝浓相输送过程中的液相和固相进行流体力学性质的分析,得到氧化铝浆料的携带速度、浓度和颗粒分布等信息,为后面的两相流建模提供理论依据。
2. 氧化铝浓相输送过程的两相流建模基于流体力学性质的分析结果,建立氧化铝浓相输送过程的两相流动模型,探究其漂移速度、颗粒浓度分布、颗粒堆积及颗粒堵塞等问题。
3. 氧化铝浓相输送过程中参数的测量方法由于氧化铝浓相输送过程是一种非常复杂的多相流动过程,因此需要选择合适的测量方法,对其各项参数进行准确的测量。
本课题将研究不同的测试手段,并通过对比实验和模拟结果,选取最适合氧化铝浓相输送过程的测量方式。
三、研究的意义和目的本课题的研究意义主要包括以下几个方面:1. 提高氧化铝浓相输送过程的效率与可靠性通过对氧化铝浓相输送过程的两相流建模及参数测量的研究,使得生产工作者能够更好地控制和优化输送过程,实现在保证产品质量的前提下提高生产效率。
2. 探究两相流在工业场景中的特性本课题的研究还可深入探究两相流在工业场景中的特性,对于相关行业的发展以及资源的合理利用都有着重要的参考意义。
3. 为未来的研究提供理论和技术支持本课题的研究将为未来相关领域的研究提供理论和技术支持,如氧化铝浓相输送过程的机器学习优化、氧化铝浆料特性的研究等。
晶种分解过程中氧化铝浓度及晶体粒度动力学模型的数值模拟的开题报告

晶种分解过程中氧化铝浓度及晶体粒度动力学模型的数值模拟的开题报告1. 研究背景及意义晶种分解是一种常见的反应工艺,在工业生产中被广泛应用。
而氧化铝作为催化剂和材料方面的重要物质,在晶种分解反应过程中的浓度及晶体粒度变化对反应效果有着重要的影响。
因此,对氧化铝浓度及晶体粒度动力学模型的研究具有重要的理论和应用价值。
2. 研究内容及方法本文将采用数值模拟的方法研究晶种分解过程中氧化铝浓度及晶体粒度动力学模型。
具体研究内容包括:(1) 晶种分解反应的动力学模型建立;(2) 基于该动力学模型,确定氧化铝浓度及晶体粒度变化规律;(3) 基于数值模拟方法,模拟氧化铝浓度及晶体粒度随时间变化的过程,并分析模拟结果。
3. 预期研究结果及创新点预期研究结果为:对晶种分解过程中氧化铝浓度及晶体粒度动力学模型进行数值模拟,并得到氧化铝浓度及晶体粒度随时间变化的过程图示,同时分析其变化规律和影响因素。
本文的创新点在于:(1) 建立氧化铝浓度及晶体粒度动力学模型,对晶种分解反应过程进行深入分析;(2) 采用数值模拟方法研究氧化铝浓度及晶体粒度随时间变化的过程,更加直观地观察其变化规律。
4. 参考文献[1] Jia L. Modeling of the kinetics of crystal dissolution in lixiviation processes[J]. Chemical Engineering Science, 2005, 60(6):1605-1612.[2] Zha C, Wu M, Zhang Y, et al. Experimental study and mechanism analysis on modeling of crystal growth in gas-liquid bubble column reactor[J]. Chemical Engineering Science, 2016, 144:206-216.[3] Zhu X, Shen X, Zhang J, et al. Computational fluid dynamics simulation study on the fluid flow and heat transfer of a hot blast stove[J]. Applied Thermal Engineering, 2017, 111:1589-1597.。
模型辨识在氧化铝高压溶出温度控制中的应用
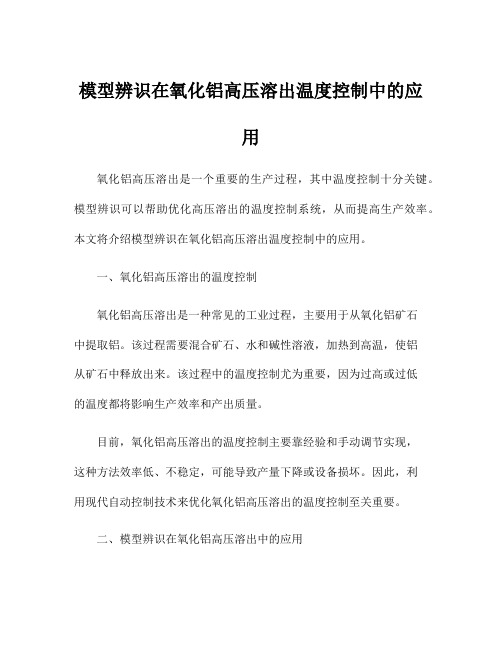
模型辨识在氧化铝高压溶出温度控制中的应用氧化铝高压溶出是一个重要的生产过程,其中温度控制十分关键。
模型辨识可以帮助优化高压溶出的温度控制系统,从而提高生产效率。
本文将介绍模型辨识在氧化铝高压溶出温度控制中的应用。
一、氧化铝高压溶出的温度控制氧化铝高压溶出是一种常见的工业过程,主要用于从氧化铝矿石中提取铝。
该过程需要混合矿石、水和碱性溶液,加热到高温,使铝从矿石中释放出来。
该过程中的温度控制尤为重要,因为过高或过低的温度都将影响生产效率和产出质量。
目前,氧化铝高压溶出的温度控制主要靠经验和手动调节实现,这种方法效率低、不稳定,可能导致产量下降或设备损坏。
因此,利用现代自动控制技术来优化氧化铝高压溶出的温度控制至关重要。
二、模型辨识在氧化铝高压溶出中的应用模型辨识是利用数学和统计方法,从观察数据中构建动态系统的数学模型的过程。
在氧化铝高压溶出的温度控制中,模型辨识可以通过分析观察数据确定合适的控制器参数,从而实现快速、准确的温度控制。
具体步骤如下:1.收集数据:收集氧化铝高压溶出过程中的温度数据,包括温度变化趋势、升温和降温速度、反应热等参数。
2.建立数学模型:根据收集到的数据,通过数学建模方法,建立氧化铝高压溶出的温度控制数学模型,包括反应速率方程、传热方程和物质平衡方程等。
3.模型求解:利用模型中的参数和方程,求解出温度控制器的响应函数,并根据模型的预测能力来确定控制器的最佳参数组合。
4.控制器设计:根据模型求解结果,设计出合适的温度控制器,实现温度的自动调节。
三、模型辨识的优势相比传统的手动控制方法,利用模型辨识技术优化氧化铝高压溶出的温度控制具有以下优势:1.提高控制精度:模型辨识技术可以通过精确的数据分析确定合适的温度控制器参数,提高温度控制的准确性和精度。
2.提高生产效率:减少人力调节,提高整个生产线的自动化程度,提高生产效率和产量。
3.降低能耗和成本:通过精确的温度控制,可以减少设备损坏和能源浪费,降低生产成本。
氧化铝在电解质中的溶解及其行为

别里亚耶夫的研究指出,许多添加剂都会延长氧化铝
的溶解时间 冰晶石熔体分别含有不同的添加剂时,随着
这些添加剂的增多,氧化铝的溶解时间增加,特别是摩尔
比降低时,氧化铝溶解时间延长。例如摩尔比由3降至
2.5,溶解时间增加1.5倍。
氧化铝在电解质中的溶解及其行为
铝电解的主要原料是氧化铝,它能否顺畅地溶解进入电解质关系 到铝电解槽的生产能否顺利进行,生产过程是否平稳,是否产生沉淀, 以及是否产生病槽等问题,相应地影响到电流效率、电能消耗和物料 消耗。
氧化铝的溶解同氧化铝的品种和性质、电解质的性质及状况以及 加料方式密切相关。
如果Al203的晶粒互相交联,形成一种结构上类似网络的结构,则能很快形成结壳。研究 证明,当Al203中的γ一Al203转变为α一Al203 ,则易于使Al203的晶粒形成网络结构,有利 于快速结壳。由于结壳中存在着这种网络结构,结构的强度增大,即使温度升高超过电解质 的融化温度也不致碎裂。
形成Al203网络结构的条件为:
温度一直在增加,结壳厚约5~10cm,下部的结壳温度需20h才达到暂时平衡,接近硬壳处的温度在
700℃左右。
(2)结壳的化学组成。大部分结壳w(Al203)<40%,,其余为电解质。结壳的摩尔比上下并不一样,
上部结壳的摩尔比要比液体电解质的摩尔比为低,下部结壳则接近于液态电解质的摩尔比。取样举例说明:
(2)炉帮。炉帮是熔融电解质沿槽膛内壁凝结成的一圈固 态电解质块体,它连续地以不同厚薄程度构成了槽膛空间, 在此空间内进行着铝电解的电化学及物理化学反应,实现 电解过程。这一层炉帮是良好的绝热和电绝缘材料,它既 能对炉膛保温,又能防止漏电,同时,良好髟状的炉膛可 使电流密度高而集中,电解质和铝液流动顺畅,气体排除 容易等,从而可获得较高的电流效率。它的形成和变化, 受电解槽热平衡情况支配。
氧化铝蒸发的动态过程建模与仿真

· 281·
[ 8 ]
( 11 )
根据饱和水蒸气热焓表 式:
关系回归成如下算
2. 2
系统热量平衡 根据传热速率方程
[7 ]
h = 2495 . 867 + 1 . 741 T + 2 . 653 × 10 - 3 T2 - 1 . 956 × 10 - 5 T3
, 新蒸汽在 Ⅰ 效汽室内 下:
C p = 4 . 186 - 2 . 923 x1 - 3 . 266 x2 - 0 . 071 x3 H = Cp T ( 13 )
dx i2 1 s = ( F i x i20 - F in, i x i2 - V i x i2 + V i x i2 ) dt M i in, dx i3 1 s = ( F i x i30 - F in, i x i3 - V i x i3 + V i x i3 ) dt M i in, ( 7) ( 8)
式中
F in, — —第 i 效蒸发单元的进料量; i— F out, — —第 i 效蒸发单元的出料量; i — Vi — — —第 i 效蒸发器出口乏汽量; V
s i
— — —第 i 级闪蒸器进第 i 效蒸发器乏
s
x210 = ( Fout, 其中, 4 x10 + Ffeed3 x11 ) / Fout, 4 + Ffeed3 ) 。 , 同理 由铝氧和苛碱质量平衡方程分别得出 铝氧和苛碱微分方程:
则蒸发器和闪蒸汽出口料液热焓分别为 : ( 17 ) , ( 21 ) , ( 22 ) 得各效蒸 由式( 6 ) ~ ( 8 ) , 发器出料温度微分方程:
dT e 1 i e e = [ Q + F in, i T i + 1 C p( i + 1 ) - F in, i T i C pi0 + dt M i C pi i
食品加工过程中的传质机制与建模研究

食品加工过程中的传质机制与建模研究食品加工过程是将农产品经过一系列处理和转化,最终制成适合人们食用和储存的食品的过程。
在这个过程中,传质机制起着重要的作用。
传质机制研究为提高食品加工的效率和品质提供了科学依据,对于食品工程领域的发展具有重要意义。
传质是指物质在空间上由高浓度区域向低浓度区域的传递过程,其目的在于实现物质的分离、纯化和转化。
在食品加工过程中,传质过程不仅包括物质的扩散、溶解和迁移等现象,还与传热、传质界面传质速率以及传质过程的动力学等因素紧密相关。
在传质机制的研究中,建立精确的数学模型是一种重要的手段。
传质机制主要涉及物质在食品中的扩散过程。
扩散是物质由高浓度向低浓度区域运动的过程,其速率与温度、浓度、物质性质以及界面因素等多种因素有关。
在食品加工过程中,传质速率对于保证食品质量和安全非常重要。
例如,高蛋白食品中的氨基酸和肽类物质容易在加工过程中产生不均匀分布,而且这些物质会引起食品中的腐败和质量变化。
因此,了解扩散机制以及相关因素对于避免这些问题具有重要意义。
建立传质机制的模型可以帮助预测和优化食品加工过程。
传质模型的建立通常基于物理化学定律以及实验数据,可以通过模拟和计算优化加工参数,以获得更好的产品质量和生产效益。
例如,在乳制品加工中,通过建立乳液中脂肪颗粒的扩散模型,可以预测不同温度和搅拌时间下脂肪颗粒的大小和分布情况,进而优化工艺条件,提高产品质量。
同时,传质模型的建立也为工程师提供了设计新食品加工设备的依据。
通过模拟和计算,可以预测不同设备参数对传质速率的影响,从而为设备设计和优化提供指导。
例如,在干燥过程中,传质模型可以用于预测食品中水分的迁移速率和干燥时间,以选择合适的干燥工艺和设备。
随着科技的发展,传质机制和模型研究也在不断深入。
传质机制的研究正在向多学科交叉的方向发展,涉及流体力学、热力学、分子化学等领域,以深入探索物质传递的规律。
同时,传质模型的建立也在融入计算机仿真、人工智能等技术,以提高模型的准确性和实用性。
氧化铝分解槽传热突变下的铝电解热态实验分析

铝 金属 制 品可通 过 氧化 分解 ,提高 铝金 属 制品 的抗 氧化 性 ,氧 化铝 分 解槽 是 进行 铝 金 属制 品 氧化 加 工 的重 要 设 备 ,
氧化 铝 分解槽 在 进行 铝 电解 中 ,当氧 化铝 分解槽 中的温度 每 升 高 10 ~ 2O℃ ,随 着烟 气 余热 回收 导 致沉 积率 下 降 ,产 生 氧化 铝 分解 槽传 热 突变 】,需要 分析 氧 化铝 分解 槽传 热 突变
图 2氧化铝 分解 槽的传热实 验管结构
氧化铝分解槽 的侧蒸发 产生的水 蒸气 ,在铝 电解 过程 中 , 以气态 方式扩 散吸 收跨膜 传质 通量 。氧化铝 分解槽 管壁 膜的
传质系数为 :
E =X 一 =[e , ,…,e
(1)
其中 ,e= 一 d=【el,e2,…, 】 表示 氧化铝 分解槽 传
铝 电解热 态 实验数 据 进行 技术参 数 分析和 拟 合处 理 .然 后进 行实验 结果分 析 ,得出有效 性结论 。
1 氧 化 铝 分解 槽 装 置 和 铝 电解 热 态 实验 系 统 结 构模 型
为 了 测试 氧化 铝 分解 槽 传热 突变 下 铝 电解 的热 态 性能 , 需要 构建 氧 化铝 分解槽 装 置结构 模 型 。氧 化铝 分解 槽装置 是 进行 铝 电解和 氧 化处 理的 主要设 备和 系统 ,主 要 由恒温冷 却 水系 统 、阀 门 、管道泵 及转 子组成 ,得到 氧化铝 分解槽 的铝 电解热 态实验系统 如 图 1所 示。
明 ,采 用该 方 法进 行 氧化 铝 分 解槽 传 热 突 变下 的 铝 电解 ,热 量 循环 利 用 性能 较好 ,加 工效 率 较 高。
关 键 词 :氧 化铝 ;分 解槽 ;加 工 ;热 态实验