催化重整预加氢进料加热炉事故分析
重整装置反应加热炉操作的危害分析及对策
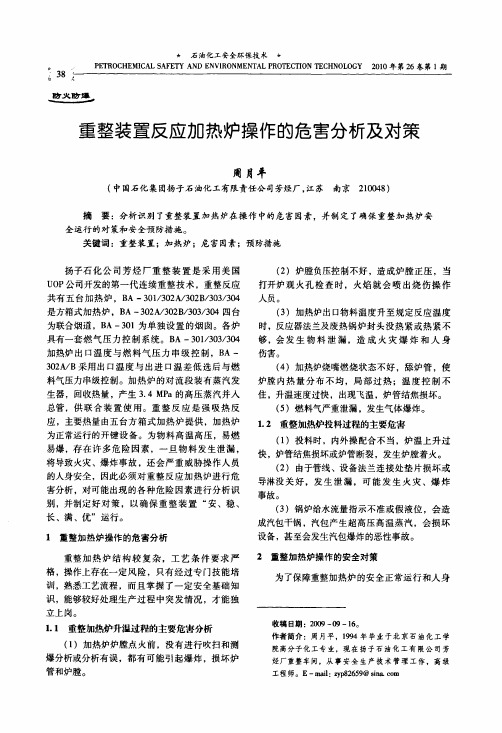
专石油化工安全环保技术夯PE T R O C H E M I C A L S A F E TY A N DE N V I R O N M E N T A L P R O T EC T I O N TE C H N O LO G Y2010年第26卷第1期重整装置反应加热炉操作的危害分析及对策周月平(中国石化集团扬子石油化工有限责任公司芳烃厂,江苏南京210048)摘要:分析识别了重整装置加热炉在操作中的危害因素,并制定了确保重整加热炉安全运行的对策和安全预防措施。
关键词:重整装置;加热炉;危害因素;预防措施扬子石化公司芳烃厂重整装置是采用美国U O P公司开发的第一代连续重整技术,重整反应共有五台加热炉,BA一301/302A/302B/303/304是方箱式加热炉,BA一302A/302B/303/304四台为联合烟道,B A一301为单独设置的烟囱。
各炉具有一套燃气压力控制系统。
BA一301/303/304加热炉出口温度与燃料气压力串级控制,B A一302A/B采用出口温度与出进口温差低选后与燃料气压力串级控制。
加热炉的对流段装有蒸汽发生器,回收热量,产生3.4M Pa的高压蒸汽并人总管,供联合装置使用。
重整反应是强吸热反应,主要热量由五台方箱式加热炉提供,加热炉为正常运行的开键设备。
为物料高温高压,易燃易爆,存在许多危险因素,一旦物料发生泄漏,将导致火灾、爆炸事故,还会严重威胁操作人员的人身安全,因此必须对重整反应加热炉进行危害分析,对可能出现的各种危险因素进行分析识别,并制定好对策,以确保重整装置“安、稳、长、满、优”运行。
l重整加热炉操作的危害分析重整加热炉结构较复杂,工艺条件要求严格,操作上存在一定风险,只有经过专门技能培训,熟悉工艺流程,而且掌握了一定安全基础知识,能够较好处理生产过程中突发情况,才能独立上岗。
1.1重整加热炉升温过程的主要危害分析(1)加热炉炉膛点火前,没有进行吹扫和测爆分析或分析有误,都有可能引起爆炸,损坏炉管和炉膛。
炼油厂事故案例分析

炼油车间事故案例分析目录1 同类装置事故汇编 11.1 重整催化剂水中毒事故 11.2 重整催化剂硫中毒事故 11.3 重整反应器结焦事故 11.4 催化剂跑损事故 21.5 催化剂提升管弯头破裂事故 31.6 重整第一反应器堵塞事故 31.7 容器严重憋压事故 41.8 锅炉干锅事故 41.9 装置进水事故 51.10 塔内瓦斯外泄事故 51.11 压控阀冻结设备超压事故 51.12 预分馏塔超压事故 61.13 重整临氢换热器出口管线弯头破裂事故 6 1.14 重整高压分离罐出口线堵塞事故 61.15 盲目进罐油气中毒事故71.16 盲板管理混乱造成紧急停工事故71.17 瓦斯罐超压险些爆炸事故71.18 重整反应器出口法兰焊口断裂事故81.19 氢压机出口补氮气阀阀芯碎裂事故81.20 某厂重整车间炉管堵塞事故81.21 氮气窒息事故之一81.22 氮气窒息事故之二91.23 氮气窒息事故之三91.24 氢气压缩机缸套冻裂101.25 氢气装瓶机抱轴事故101.26 预加氢压缩机玻璃看窗破裂事故101.27 往复式压缩机缸盖紧固螺栓断裂事故11 1.28 氢压机机身及进出口管线震动大事故11 1.29 加氢进料泵机械密封泄漏事故111.30 判断失误严重损坏氢压机事故121.31 重整压缩机曲轴箱爆炸事故121.32 九江石化铂重整装置F101闪爆事故之一13 1.33 九江石化铂重整装置F101闪爆事故之二13 1.34 九江石化铂重整装置F101闪爆事故之三14 1.35 九江石化铂重整装置F101闪爆事故之四14 1.36 加热炉回火伤人事故之一151.37 加热炉回火伤人事故之二151.38 加热炉回火伤人事故之三151.39 加热炉回火事故之四161.40 加热炉回火伤人事故之五161.41 重整炉出口法兰着火事故161.42 处理堵塞管线引起人烧伤事故171.43 预加氢催化剂自燃事故171.44 炉膛气体未分析点火爆炸伤人事故171.45 加热炉炉膛爆炸事故171.46 扫线动火互不联系造成爆塔事故181.47 违章操作造成氢气爆炸着火烧伤人员事故181.48 装置吹扫中着火致使2人被烧死事故181.49 高温汽油烫伤人事故191.50 1993年金陵石化铂重整车间氢贮瓶爆炸事故报告192 镇海炼化公司部分事故汇编212.1 1980年11月6日炼油厂成品油码头冒罐跑油事故212.2 1981年3月7日炼油厂热电站重大停电事故212.3 1981年4月7日炼油厂热电站锅炉严重缺水造成炉管胀接口泄漏事故212.4 1982年7月23日炼油厂油品车间油罐爆炸事故222.5 1982年8月14日炼油厂催化车间跑润滑油事故222.6 1983年9月17日化肥厂合成车间2#渣油贮罐冒罐事故232.7 1984年6月18日炼油厂油品车间油罐抽瘪事故232.8 1985年1月11日化肥厂火炬倾斜事故232.9 1987年6月30日化肥厂4118-K1T烧瓦事故242.10 1988年1月30日炼油厂油品车间碱液严重烧伤事故242.11 1988年11月5日化肥厂仪表工误操作造成全厂停车事故24 2.12 1989年9月5日炼油厂排水车间重伤事故252.13 1990年1月5日化肥厂合成车间现场着火伤人事故252.14 1990年5月22日炼油厂油品车间氢氟酸灼伤事故252.15 1991年1月21日机修厂铆焊车间检修工硫化氢中毒事故26 2.16 1991年4月25日化肥厂合成车间现场着火伤人事故262.17 1992年10月16日化肥厂常明火炬管线水击落架事故262.18 1993年7月16日炼油厂丙烷压缩机开关带负荷合闸事故27 2.19 1994年4月1日炼油厂一套常减压串跑油事故272.20 1994年10月6日炼油厂催化车间着火烧伤检修工事故272.21 1995年3月31日炼油厂Ⅰ套常减压着火事故282.22 1995年5月28日化肥厂合成车间误操作引起停车事故282.23 1995年6月22日仓储公司贮运车间串油事故282.24 1995年9月10日化肥厂0101-V1-3渣油罐憋压损坏事故29 2.25 1995年9月19日炼油厂焦化行车工违章作业致人重伤事故29 2.26 1996年1月23日炼油厂加氢装置润滑油泵轴瓦损坏事故30 2.27 1997年1月10日化肥厂合成车间1#气化炉闪爆伤人事故30 2.28 1997年3月13日炼油厂聚丙烯车间三名职工违章抽烟引起闪燃事故302.29 1997年6月22日仓储公司贮运车间跑油事故312.30 1997年7月10日炼油厂加氢裂化F-304爆炸事故312.31 1998年1月22日炼油厂焦化车间火灾伤人事故312.32 1998年2月13日炼油厂一车间着火伤人事故322.33 1999年1月29日仓储公司贮运车间串油事故322.34 1999年3月21日炼油厂油品车间泵房火灾事故332.35 1999年11月22日炼油厂重油催化检修现场跑油事故332.36 1999年11月26日炼油厂油品车间丙烯栈台火灾事故332.37 1999年12月15日炼油厂重油催化检修现场瓦斯外泄事故33 2.38 2000年3月30日炼油厂一车间火灾事故342.39 2000年4月20日炼油厂二电站CFB锅炉设备损坏的事故35 2.40 2000年9月29日炼油厂油品车间重伤事故352.41 2001年3月15日一车间“3.15”火灾事故352.42 2001年3月31日重一F-501闪爆362.43 2001年7月24日炼油厂化验职工李一平死亡事故363 重整装置长期稳定运转中常见问题与相关事故383.1 重整装置预处理单元腐蚀问题及相关事故383.2 重整装置的积碳问题与相关事故413.3 重整催化剂氮中毒问题443.4 重整原料油的切割与保护问题453.5 原料中硫的控制问题与催化剂硫中毒事故463.6 重整反应系统水环境控制问题与相关事故473.7 催化剂氯失调问题与相关事故483.8 对突发事故的处理原则和方法501 同类装置事故汇编1.1 重整催化剂水中毒事故1.1.1 原料带水现象91年12月14日下午,九江石化铂重整装置预分馏塔操作出现异常,塔顶回流罐液面上升,拔头油量增大,随后出现重整产氢量逐渐下降,由4500Nm3/h下降到2000Nm3/h,循环氢纯度由83%上升到96%。
09重整催化剂与事故分析(0912)

5,顶部金属颗粒的大小与线状丝状炭的生成 速率有关,如下图所示,金属颗粒越小, 线状丝状炭的生成速率越快;
60 50 40 30 20 10 0 0 40 80 120
线状丝 状炭生成速 率,n m / s
颗粒宽度,n m
图< 2 0 > 金属颗粒大小与炭生 长速率的关系
6,脱离了金属母体的丝状炭仍然具有化学活 泼性。
附。
2,催化剂粉尘
催化剂的磨损率是CCR催化剂的重要指 标之一。 正常情况下,催化剂磨损为1-3Kg/天, 一年约耗剂1吨左右。 不正常情况下,磨损可达10-30 Kg/天,
或更高。
造成装置粉尘量大有多种原因,从 收集到的材料可以归纳出以下原因:
1,催化剂磨损率高; 2,还原区料位失控;
3,闭锁料斗损坏;
金属表面生炭机理示意图
丝状炭的特征
1. 所有丝状炭的顶部多有一个金属颗粒;
2. 丝状炭的直径受顶部金属颗粒大小的控制。
在大部分情况下,金属颗粒是比较小的, 因此丝状炭的直径通常在500-1000 Å左右; 3. 丝状炭的生长速率与温度有关,在铁、镍 和钴-乙炔系统中,温度升高320℃,丝状 炭的生长速率加快20倍; 4. 丝状炭顶部的金属颗粒如果被沉积物全部 包裹,丝状炭将会停止生长;生长中的丝 状炭,顶部的金属颗粒未被沉积物包裹;
检修时可以将放射源关闭或移走,但是最
好不要移动测定头;
上述分析说明,在还原区的料位指
示上有两点需要引起我们的注意,一
是料位计的标定指示范围(满量程指
示值),要尽可能接近设计值;二是
点位计具有最后判别权。
事故处理:
处理这类事故的最好办法是反应系统停 工卸剂,催化剂过筛,然后装剂运转; 上述办法是最快捷,最彻底的处理办法, 但是需要无计划停车,并取得总公司同意。 另一种办法是不停工处理,让系统慢慢 的将大量催化剂粉尘带出,但是处理时间 长,工作量大,装置在处理期间需要适当 降低苛刻度,并有一些风险。 经验:在淘析器气体到过滤器的管线上 加装一个截流阀是十分有用的。
重整装置预加氢进料换热器管束失效分析

( )E 1 1 1 10/ C换热 器 管 束 内表 面 的腐 蚀 主 要是 H s HC一 H 引起 的轻 微 均 匀腐 蚀 ,且 局 部 存在 2— 1N 3 轻微 点蚀 。 ( ) E 1 2 1 0 / 热器 管束 外表 面 的腐蚀 主 要是 1 C换 H2 S等腐蚀 性 介质 引起 的较严 重 的 均匀腐 蚀 . 局 且 部结垢 形成 垢下 腐蚀 , 因活性 阴离子 的存 在而 导致 局 部发 生腐 蚀穿 孔 。
2 腐 蚀 检 测 21 宏 观 腐 蚀 形 貌 .
从 图 1中可 以看 出 , 管束 外表 面红 棕 色浮 锈较
多, 局部 存在 许 多溃疡 状腐 蚀坑 , 出现 腐 蚀穿 孔 。 并
管 束穿 孔 部位 位 于 管 程 出 口附近 ( 出 口约 l ~ 离 _ 3 201 处 ) . " 3 1 。穿 孔部 位 附近 基 体外 表 面 存 在许 多 大 小 不 一 和 深 度 不一 的腐 蚀 凹坑 ,凹坑 最 深可 达 到
f) 观 形 貌 a宏
。
管束 成分 与 1C Mo低 合金 钢 的化 学组 成 ( 表 3 5r 见 )
基 本相 同。
表 2 管 束基 体 的化 学成 分 , %
() 束 内 外 壁 示 意 ( 位 :m b管 单 () 3
收 稿 日期 :0 0 0 — 6 修 稿 日期 : 0 — 2 0 。 2 1— 9 0 ; 2 1 1 — 7
图 1 管束 外 表 面 宏 观 腐 蚀 形 貌
・
6 4・
加氢处理装置安全特点和常见事故分析(汪加海)
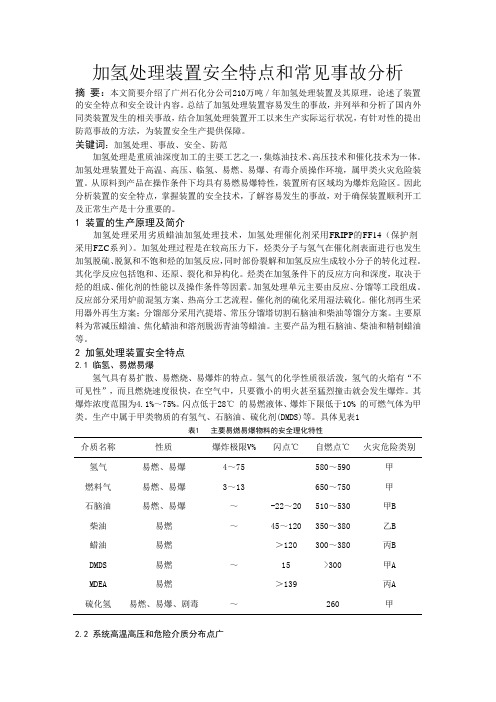
加氢处理装置安全特点和常见事故分析摘要:本文简要介绍了广州石化分公司210万吨/年加氢处理装置及其原理,论述了装置的安全特点和安全设计内容。
总结了加氢处理装置容易发生的事故,并列举和分析了国内外同类装置发生的相关事故,结合加氢处理装置开工以来生产实际运行状况,有针对性的提出防范事故的方法,为装置安全生产提供保障。
关键词:加氢处理、事故、安全、防范加氢处理是重质油深度加工的主要工艺之一,集炼油技术、高压技术和催化技术为一体。
加氢处理装置处于高温、高压、临氢、易燃、易爆、有毒介质操作环境,属甲类火灾危险装置。
从原料到产品在操作条件下均具有易燃易爆特性,装置所有区域均为爆炸危险区。
因此分析装置的安全特点,掌握装置的安全技术,了解容易发生的事故,对于确保装置顺利开工及正常生产是十分重要的。
1 装置的生产原理及简介加氢处理采用劣质蜡油加氢处理技术,加氢处理催化剂采用FRIPP的FF14(保护剂采用FZC系列)。
加氢处理过程是在较高压力下,烃类分子与氢气在催化剂表面进行也发生加氢脱硫、脱氮和不饱和烃的加氢反应,同时部份裂解和加氢反应生成较小分子的转化过程。
其化学反应包括饱和、还原、裂化和异构化。
烃类在加氢条件下的反应方向和深度,取决于烃的组成、催化剂的性能以及操作条件等因素。
加氢处理单元主要由反应、分馏等工段组成。
反应部分采用炉前混氢方案、热高分工艺流程。
催化剂的硫化采用湿法硫化。
催化剂再生采用器外再生方案;分馏部分采用汽提塔、常压分馏塔切割石脑油和柴油等馏分方案。
主要原料为常减压蜡油、焦化蜡油和溶剂脱沥青油等蜡油。
主要产品为粗石脑油、柴油和精制蜡油等。
2 加氢处理装置安全特点2.1 临氢、易燃易爆氢气具有易扩散、易燃烧、易爆炸的特点。
氢气的化学性质很活泼,氢气的火焰有“不可见性”,而且燃烧速度很快,在空气中,只要微小的明火甚至猛烈撞击就会发生爆炸。
其爆炸浓度范围为4.1%~75%。
闪点低于28℃的易燃液体、爆炸下限低于10% 的可燃气体为甲类。
催化重整预加氢进料加热炉事故分析
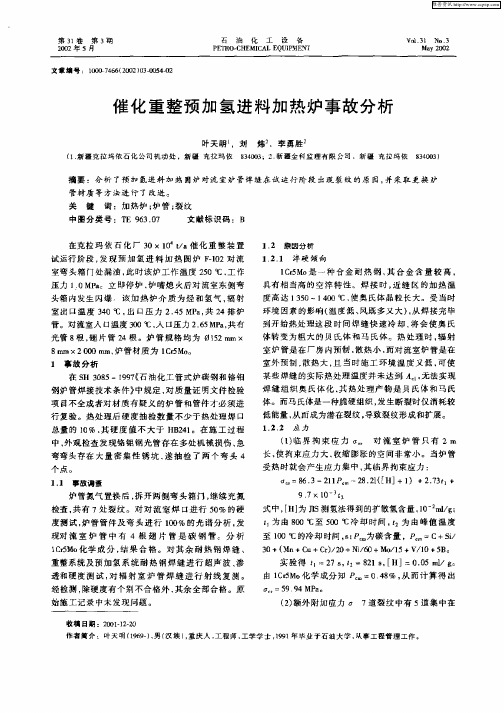
光管 8 , 片管 2 。炉 管 规格 均 为 12m 根 翅 4根 5 mx 8n. 0mn 炉管材 质为 1 rM 。 I x2 0 r, Ⅱ 0 C5 o
1 事 故 分 析 在 S 0 5—19 { 油 化 工 管 式 炉 碳 钢 和 铬 钼 H 38 97石
钢炉管 焊接技 术条件 》 中规定 , 对质 量证 明文 件检验 项 目不全或 者对 材质 有疑 义 的炉管 和管 件才必 须进
中, 外观 检查发 现铬钼 钢 光管 存在 多处 机械损 伤 , 急 弯弯头存 在 大 量密 集 性 锈 坑 , 抽 检 了两 个 弯 头 4 遂
个点。
1. 事 故 调 查 1
() 界 拘 束 应 力 a 1临
对 流 室 炉 管 只 有 2m
长, 使拘束 应 力大 , 收缩膨胀 的空 间非常小 。当炉管
始 施 工 记 录 中未 发 现 问 题 。
收 稿 日期 :2 0 一 2 0 0 I1— 2
() 2 额外 附 加应力
7道 裂纹 中有 5道集 中在
作 者简 介 :叶天 明 (9 9) 男 ( 族 )重 庆 人 . 程 师 , 学 学 士 19 年 毕 业 于石 油 大 学 , 事 工 程 管 理 工 作 。 16 一, 汉 , 工 工 91 从
Hale Waihona Puke 实 验得 I 7s :8 1s [ =00 l 。 :2 , 2 2 , H] .5m /g 由 1 rM 化 学 成分 知 P :0 4 % , 而 计 算得 出 C5 o .8 从
口 = 5 9 MPa 9 4 o
经检 测 , 除硬度 有个 别不合 格外 , 余全 部 合格 。原 其
叶 天 明 ,刘
( 1新 疆 克 拉 玛 依 石化 公 司机 动处 ,新 疆 克 拉 玛依
连续重整F202炉管损坏事故

连续重整F202炉管损坏事故一、事故经过2004年4月26日8:25,由于丙变3#、4#变压器故障,连续重整装置发生瞬间停电,预加氢循环机K101、重整装置循环机K201、增压机K202停机,加热炉F101、F201~204停炉联锁UC1001、UC2001发出声光报警,DCS画面上显示5台加热炉联锁切断阀变为红色。
当时,室外操作员正在室外采样。
室内操作员检查各加热炉瓦斯量,发现均迅速下降,DCS上的联锁模块也显示联锁阀已经关闭。
室内操作员立即转换画面,调整再接触系统操作,以防止高压串低压,对催化剂再生系统作紧急停工处理。
稍后室内操作员发现F202炉膛温度上升,立即赶到现场与采样刚刚回来的室外操作员一起关闭火嘴及长明灯手阀,并确认各加热炉已经全部熄火,炉膛给蒸汽迅速降温,系统进行撤压。
8:46装置发生大面积停电,室内操作员将四合一炉停车联锁硬开关打至“停车”位置,同时按照大面积停电事故处理方案进行处理,9:12左右将装置处理到安全状态。
岗位人员在加热炉火嘴加盲板时发现F202炉管有变形的异常现象,迅速报告车间。
当时检查现场状态:F202瓦斯总阀关闭、瓦斯控制阀下游阀关闭、加热炉12个火嘴双阀关闭、12个长明灯双阀关闭、联锁切断阀UV2001/2关闭,同时检查UV2001/2手轮指针在50%位置,说明该切断阀自保处于投用状态。
二、事故损失本次停电时间之长,影响之大,属历史罕见。
整个事故处理未造成着火爆炸和人员伤亡。
F202炉管因变形失稳,继续使用风险较大,为保险起见,进行了更换。
但拆下的炉管仍可降低标准使用,在炉膛温度较低的炉子上使用应该说是可以的。
因此,炉管变形造成的损失应为:炉管原值—折旧—炉管残值=33.6—12.6—12.6=8.4万元(炉管原值:2.4万元/吨×14吨=33.6万元.折旧:该炉管的寿命为8年,已使用三年多,折旧为:33.6万元×3/8=12.6万元。
炉管残值为普通炉管的价格:0.9万元/吨×14吨=12.6万元)。
重整加热炉风道闪爆着火事故
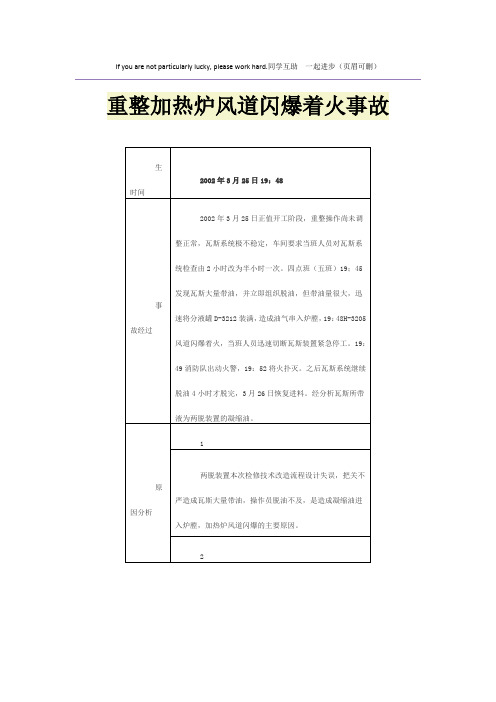
2002年3月25日正值开工阶段,重整操作尚未调整正常,瓦斯系统极不稳定,车间要求当班人员对瓦斯系统检查由2小时改为半小时一次。四点班(五班)19;45发现瓦斯大量带油,并立即组织脱油,但带油量很大,迅速将分液罐D-3212装满,造成油气串入炉膛,19:48H-3205风道闪爆着火,当班人员迅速切断瓦斯装置紧急停工。19:49消防队出动火警,19:52将火扑灭。之后瓦斯系统继续脱油4小时才脱完,3月26日恢复进料。经分析瓦斯所带液为两脱装置的凝缩油。
两脱装置本次检修技术改造流程设计失误把关不严造成瓦斯大量带油操作员脱油不及是造成凝缩油进入炉膛加热炉风道闪爆的主要原因
If you are not particularly lucky, please work hard.同学互助 一起进步(页眉可删)
重整加热炉风道闪爆着火事故
生时间
2002年3月25日19:48
原因分析
1
两脱装置本次检修技术改造流程设计失误,把关不严造成瓦斯大量带油,操作员脱油不及,是造成凝缩油进入炉膛,212脱液口较小,脱液不及也是一个方面的原因。
3
当班人员对瓦斯大量带油处理思路不清,未能及时切断瓦斯带油来源,也是一个原因。
防范措施
1
两脱装置立即整改瓦斯带液隐患,防止大量带液。
2
技术改造项目应层层把关,避免改造失误。
3
编制瓦斯大量带液处理预案,并进行办班讲课和演练。
4
报技改D-3212增加液位显示仪。
5
检修期间改造增加瓦斯脱液口。
- 1、下载文档前请自行甄别文档内容的完整性,平台不提供额外的编辑、内容补充、找答案等附加服务。
- 2、"仅部分预览"的文档,不可在线预览部分如存在完整性等问题,可反馈申请退款(可完整预览的文档不适用该条件!)。
- 3、如文档侵犯您的权益,请联系客服反馈,我们会尽快为您处理(人工客服工作时间:9:00-18:30)。
催化重整预加氢进料加热炉事故分析
叶天明1,刘 炜2,李勇胜2
(1.新疆克拉玛依石化公司机动处,新疆克拉玛依 834003; 2.新疆金科监理有限公司,新疆克拉玛依 834003)
摘要:分析了预加氢进料加热圆炉对流室炉管焊缝在试运行阶段出现裂纹的原因,并采取更换炉管材质等方法进行了改进。
关 键 词:加热炉;炉管;裂纹
中图分类号:TE963107 文献标识码:B
在克拉玛依石化厂30×104t/a催化重整装置试运行阶段,发现预加氢进料加热圆炉F2102对流室弯头箱门处漏油,此时该炉工作温度250℃,工作压力1.0MPa。
立即停炉,炉嘴熄火后对流室东侧弯头箱内发生闪爆。
该加热炉介质为烃和氢气,辐射室出口温度340℃,出口压力2.45MPa,共24排炉管。
对流室入口温度300℃,入口压力2.65MPa,共有光管8根,翅片管24根。
炉管规格均为 152mm×8mm×2000mm,炉管材质为1Cr5M o。
1 事故分析
在SH3085-1997《石油化工管式炉碳钢和铬钼钢炉管焊接技术条件》中规定,对质量证明文件检验项目不全或者对材质有疑义的炉管和管件才必须进行复验。
热处理后硬度抽检数量不少于热处理焊口总量的10%,其硬度值不大于H B241。
在施工过程中,外观检查发现铬钼钢光管存在多处机械损伤,急弯弯头存在大量密集性锈坑,遂抽检了两个弯头4个点。
1.1 事故调查
炉管氮气置换后,拆开两侧弯头箱门,继续充氮检查,共有7处裂纹。
对对流室焊口进行50%的硬度测试,炉管管件及弯头进行100%的光谱分析,发现对流室炉管中有4根翅片管是碳钢管。
分析1Cr5M o化学成分,结果合格。
对其余耐热钢焊缝、重整系统及预加氢系统耐热钢焊缝进行超声波、渗透和硬度测试,对辐射室炉管焊缝进行射线复测。
经检测,除硬度有个别不合格外,其余全部合格。
原始施工记录中未发现问题。
1.2 原因分析
1.2.1 淬硬倾向
1Cr5M o是一种合金耐热钢,其合金含量较高,
具有相当高的空淬特性。
焊接时,近缝区的加热温度高达1350~1400℃,使奥氏体晶粒长大。
受当时环境因素的影响(温度低、风既多又大),从焊接完毕到开始热处理这段时间焊缝快速冷却,将会使奥氏体转变为粗大的贝氏体和马氏体。
热处理时,辐射室炉管是在厂房内预制,散热小,而对流室炉管是在室外预制,散热大,且当时施工环境温度又低,可使某些焊缝的实际热处理温度并未达到A c1,无法实现焊缝组织奥氏体化,其热处理产物是贝氏体和马氏体。
而马氏体是一种脆硬组织,发生断裂时仅消耗较低能量,从而成为潜在裂纹,导致裂纹形成和扩展。
1.2.2 应力
(1)临界拘束应力σcr 对流室炉管只有2m 长,使拘束应力大,收缩膨胀的空间非常小。
当炉管受热时就会产生应力集中,其临界拘束应力:σ
cr
=86.3-211P cm-28.2l([H]+1)+2173t1+
9.7×10-3t2
式中,[H]为J IS测氢法得到的扩散氢含量,10-2ml/g; t1为由800℃至500℃冷却时间,t2为由峰值温度至100℃的冷却时间,s;P cm为碳含量,P cm=C+Si/ 30+(Mn+Cu+Cr)/20+Ni/60+M o/15+V/10+5B。
实验得t1=27s,t2=821s,[H]=0105ml/g。
由1Cr5M o化学成分知P cm=0.48%,从而计算得出
σ
cr
=59.94MPa。
(2)额外附加应力σ 7道裂纹中有5道集中在
碳钢翅片管附近,碳钢和耐热钢的线膨胀系数、弹性
模量不一样,因而受到额外的附加应力:
σ=E αl t 式中,E 为弹性模量,103MPa ;t 为温度,℃;αl 为线膨胀系数,K -1。
由此式算得250℃时1Cr5M o 炉管
因膨胀所受应力σ1=525MPa ,碳钢因膨胀所受的应力σ2=575MPa 。
可见碳钢比1Cr5M o 膨胀变形大,从而使碳钢翅片管附近的焊缝受到额外的附加应力σ=σ2-σ1=50MPa 。
(3)工作应力σ′ 当时炉管内的工作压力为110MPa 。
该压力的受力面积A 为急弯弯头表面积,
采用等效面积法可得A =0.029975m 2。
拉力F =110×106A =29.975kN ,当F 作用到焊缝时,所产生
的工作应力σ′=8.75MPa 。
由以上计算可得碳钢管附近焊缝受到的应力为σ+σ′=58.75MPa ,已经非常接近临界值σcr 。
若再考虑应力集中,则可以肯定这5道裂纹是由于所受拘束应力过大所致。
1.2.3 热处理
操作人员对环境因素的影响考虑不足,后冷及
热处理时使用的保温材料厚度和宽度不够,温控效果差。
热处理时热电偶插入位置不合理,不能真实反映实际情况,加上硬度未全检,从而留下隐患。
其余2道裂纹所受应力为8.75MPa ,远小于σcr ,主要是热处理使焊缝过于淬硬所致。
2 改进措施
将对流室炉管割除,4根碳钢翅片管更换为铬钼钢光管,使用奥302焊条重焊全部焊缝。
将硬度不合格的所有焊缝热处理后重新进行超声波、渗透和硬度复测,全部合格。
3 结语
应加强材料进场检验,对于耐热钢,按规范进行抽检是远不够的,应进行100%的材质复验,以有效地保证施工质量。
改进后的炉管经试运和投产检验,满足生产需要,达到了设计要求。
(张编)
催化装置压缩机振动分析及改进
郎礼民,吴剑锋
(上海炼油厂,上海 200137)
关 键 词:压缩机;振动;临界转速;悬臂端不平衡响应中图分类号:T Q 051121 文献标识码:B 某厂因催化装置的生产工艺改变,遂对富气压缩机组进行了改造,主要内容是富气压缩机的转子、隔板以及轴封,并将单向离合器与压缩机、压缩机与齿轮箱、齿轮箱与电机联接的三套联轴器由齿式更新为叠片式联轴器。
但改造以后试车发现该机组振动较大,已影响机组的正常运行。
机组布置见图1。
图1 机组布置示图
1 振动现象
该机组安装了Bently 的7200和3300系列传感器,径向振动探头分别布置在靠齿轮箱侧和汽轮机侧。
比较几次试车数据,发现机组的振动主要集中在压缩机上,特别是靠近压缩机转子悬臂端(压缩机轴靠近齿轮箱侧)位置振动幅值较大。
机组试车时,
压缩机振动幅值V375由80μ
m 上升至114μm ,V377由65μm 上升至95μm 。
振动以工频为主,工频相位大致有90°的变化,轴心轨迹为标准椭圆,具有临界转速共振的特征。
振动值的突然增大发生在临界转速的80%左右,并随转速的增大而上升。
在机组开机正常后,振动值会缓慢爬升,直至停机。
润滑油上。