液相催化加氢搅拌器形式_原理及其发展趋势
化学化工中的催化加氢反应

化学化工中的催化加氢反应在今天的化学化工领域,催化加氢反应是一种非常重要的工业生产技术,尤其是石油化工和化学品生产。
这种反应可以将不饱和化合物或硫化物转化为饱和化合物,从而提高其稳定性和可用性。
本文将介绍催化加氢反应的基本原理、反应类型、工业应用以及目前的发展趋势。
一、催化加氢反应的基本原理催化加氢反应是一种加氢还原的反应,它是指在催化剂存在的情况下,将不饱和化合物或硫化物与氢气作用,将氢原子加入分子中,形成饱和化合物的过程。
该过程将不饱和化合物的双键或三键断裂,产生新的碳氢键。
这种反应需要催化剂的存在,使不饱和化合物或硫化物分子中可反应的化学键与氢原子之间的活化能降低,从而提高反应速率和转化率。
二、催化加氢反应的种类在催化加氢反应中,根据不同的反应物和反应条件,可以分为饱和脂肪酸及其衍生物、芳香烃和杂环化合物等不同类型。
1、饱和脂肪酸及其衍生物的催化加氢反应饱和脂肪酸及其衍生物是一种重要的化学品,其在医药、食品、化妆品等行业中有着广泛的应用,因此饱和脂肪酸及其衍生物的催化加氢反应也是一项极为重要的工业生产技术。
该反应通常采用贵金属催化剂,如铂和钯等。
2、芳香烃的催化加氢反应芳香烃是一种典型的不饱和化合物,其催化加氢反应可以将芳香环上的双键和三键加氢,形成饱和环烷化合物。
这种反应常采用铝烷或钯催化剂,反应条件较为温和,常温下就能使芳香烃发生氢化反应。
3、杂环化合物的催化加氢反应杂环化合物是一种具有广泛用途的化学品,如吲哚、噻嗪等,其催化加氢反应可以使其产生稳定性更强的饱和杂环化合物。
这种反应的催化剂多采用贵金属催化剂,如铂、钯等。
三、催化加氢反应的工业应用催化加氢反应已经广泛应用于石油化工、化学品生产、环保以及新能源等领域,其中最重要的是石油化工中的加氢处理、醇或羧酸的催化加氢和生物质转化等过程。
1、石油化工中的加氢处理加氢处理是石油化工中广泛应用的一种反应,其主要目的是降低原油性质中的硫、氮、氧等有害元素,从而提高油品的质量和价值。
加氢反应器的工作原理是什么
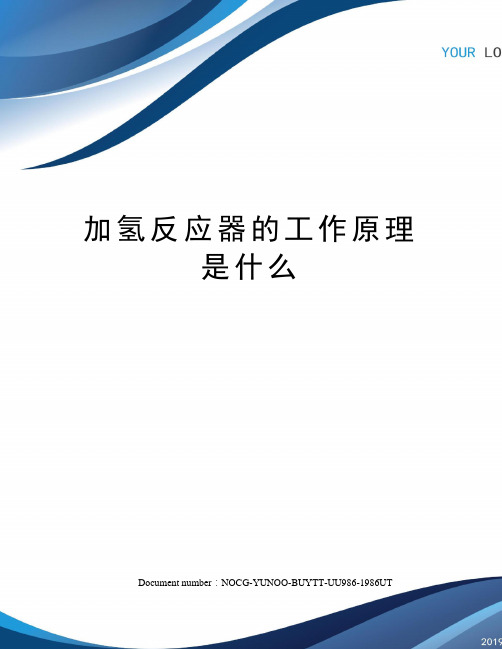
加氢反应器的工作原理是什么Document number:NOCG-YUNOO-BUYTT-UU986-1986UT加氢反应器的工作原理是什么.工艺原理1、加氢精制的反应原理加氢精制的主要反应有以下几种:一、烯烃饱和:是不饱的单烯、双烯通过加氢后,变成饱和的烷烃。
如:1、R-C=C-R+H2→R-C-C-R....+Q2、R-C=C-C=C-R'+H2→R-C=C-C-C-R'+H2→R-C-C-C-C-R'二、脱硫反应在反应条件下,原料中含硫化合物进行氢解,转化成相应的烃和硫化氢,从而硫原子被脱除。
如:硫醇:R-S-H+H2→R-H2+SH2?硫醚:R-S-R'+H2→R-S-H+R'-H+H2→R-H+R'-H+SH2二硫化物:R-S-S-R'+H2→R-S-H+R'-S-H+2H2→R-H+R'-H+2SH2?二硫化物加氢转化为烃和硫化氢需经过生成硫醇的中间阶段,即首先在s-s键上断裂,生成硫醇,再进一步加氢生成烃和硫化氢,中间生成的硫醇也转化成硫醚。
而噻吩环状含硫物,在加氢脱硫时首先定环中双键,发生饱和,然后再发生断环脱硫,脱硫反应速度因分子结构按以下顺序递减:RSH>RSSR>RSR'>噻吩三、加氢脱氮反应石油馏分中的含氮化合物可分为三类:1、脂肪胺及芳香胺类;2、吡啶、喹啉类型的碱性杂环化合物;3、吡咯、茚入咔唑型的非碱性氮化物,氮化物加氢发生氢解反应生成NH3和烃如:胺类:R-NH2+H2→RH+NH3(1)吡啶(2)喹啉?由此可见:所有的含氮化合物氢解时都要向胺转化,再进一步氢解生成烃和氨。
反应速度:脂肪胺〉芳香胺〉吡啶类型碱性杂环化合物〉吡咯类型的非碱性氮化物。
由于氮化物的分子结构都比较复杂,且都很稳定,故而氢解反应需要的条件比较苛刻,要求氢分压在15Mpa,温度在400℃,能脱除96%左右的氮,故此加氢裂化设计压力为16Mpa,而且精制的空速不能过高。
液相加氢技术现状及发展前景

Ke y wo r d s :Li q u i d p h a s e h y d r o g e n a t i n ; Di e s e l h y d r o t r e a t i n g u n i t ; I s o T h e r mi n g t e c no h l o y; g E n e r y g c o n s u mp t i o n ;
W ANG M e n g L , J I N Y u e — c h a n g z
,
W ANG T i e — g a n g z
,
L1Gu o - pi n g ̄
n. L i a o n i n g S h i h u a Un i v e r s i t y , Li a o n i n g F u s h u n 1 1 3 0 0 1 ,Ch i n a ;
De v e l o om e nt Pr o s oe c t a nd Pr e s e n t
S i t u a t i o n o f t he Li q ui d Ph a s e Hy dr O g e n a t i 0 n Te c h no l o g y
Ab s t r a c t :P r e s e n t s i t u a t i o n o f t h e l i q u i d p h a s e h y d r o g e n a t i o n t e c h n o l o g y wa s i n t r o d u c e d . T h e b r e a k t h r o u g h o f I s o T h e r mi n g l i q u i d p h a s e h y d r o g e n a t i o n t e c h n o l o g y a n d S RH l i q u i d c i r c u l a t i o n h y d r o g e n a t i o n t e c h n o l o g y wa s d i s c u s s e d . T h e p r o c e s s lo f w a n d t e c h n i c a l c h a r a c t e r i s t i c s o f t wo k i n d s o f t e c h n o l o g y we r e a n a l y z e d . An d t h e y we r e c o mp a r e d wi t h c o n v e n t i o n a l h y d r o g e n a t i o n t e c h n o l o g i e s . Th e r e s u l t s s h o w t h a t t h e l i q u i d p h a s e h y ro d g e n a t i o n t e c h n o l o y g h a s
液相加氢技术的应用现状

C-NUM 液相加氢技术的应用对象也是航煤原料,这种原 料本身的性质和状态比常规的柴油等油料更好,加氢效果更 佳,整个精制过程的对循环系统、反应环境的要求比较小。在面 对航煤原料时,C-NUM 技术应用装置取消了循环油系统,有效 降低了循环泵可能带来的安全风险和成本、动力消耗;反应温 度为 245 ℃,压力为 3.5 MPa,氢油比在 12~13 范围内,属于较 为理想的反应过程。但如果面对的是原料性质、状态更差一些 的焦化柴油等柴油种类时,C-NUM 技术装置能否顺利加氢,能 否顺利完成精制反应获得符合标准的产品油,还需要进一步的 实践和验证分析。
目前来看,液相加氢技术始终存在氢气消耗量高、循环加 氢能耗较高、循环泵安全风险较高、催化剂使用寿命较低等问 题。想要改善这些问题需要通过特殊的设备装置,提高氢气与 原料油的混合程度,实现原料油中的氢气饱和状态[3]。想要达 到氢气饱和的理想状态,可能需要超重力、微米气泡等类型的 装置,使原料油中的氢气溶解量远超于实际需求量。如果能够 解决溶氢过程中的氢气饱和问题,就能够真正节约掉循环加氢 的装置和能耗,并且规避掉循环泵可能带来的安全风险和泄露 风险。这是液相加氢技术未来发展的主要方向,突破这一难题 就能够促进液相加氢技术的有效发展,扩大液相加氢技术的应 用范围。目前的液相加氢技术还不能代替气相滴流等技术的应 用,在原料油精制反应中还不能占据更大的主动性[4]。
LI Nong, LI Hai-feng, ZHAO Xin-quan, LI Guo-qi (Sinochem Changhe Technology Co., Ltd., Dongying 257335, China)
Abstract: Liquid phase hydrogenation technology is a process to maintain high hydrogen-oil ratio, which can effectively improve the heat transfer effect between phases, can improve the reaction eff iciency of oil, reduce the power consumption in the application process of diesel oil, kerosene and other feedstock oils, and produce more environmentally friendly clean oil. In the process of liquid phase hydrogenation, the amount of hydrogen dissolved in oil is the key problem, which affects the energy consumption and production eff iciency of the technology. This paper mainly analyzes the application status and application prospect of this technology.
加氢设备的化工原理及应用

加氢设备的化工原理及应用1. 加氢设备的概述•加氢设备是一种将氢气加入化学反应中的工业设备,它可以广泛应用于石油化工、精细化工、制药等领域。
•加氢设备主要由反应器、催化剂、加温装置和氢气供应系统等组成。
2. 加氢设备的化学反应原理•加氢反应是指将氢气作为反应物参与化学反应的过程。
常见的加氢反应包括饱和烃化反应、脱硫反应、脱氮反应等。
•加氢反应的基本原理是通过给予反应物足够的能量,使其与氢气发生反应进而实现化学变化。
•催化剂在加氢反应中起到关键作用,它可以提高反应速率、改善选择性,并降低反应温度。
3. 加氢设备的应用领域3.1 石油化工•加氢裂化是石油炼制过程中的关键环节。
通过加氢裂化可以将重质石油分子裂解成较轻的石油产品,如汽油、柴油等。
•加氢脱硫可去除石油中的硫,减少尾气中的二氧化硫排放,保护环境。
•加氢脱氮可去除石油中的氮,提高石油产品质量和市场竞争力。
3.2 精细化工•加氢还原反应可用于有机合成中,将含有双键或多键的有机化合物加氢转化为饱和化合物。
•加氢裂解反应可将高分子聚合物加氢分解为低分子产品,用于再生利用。
•加氢氧化反应可将有机化合物氧化为相应的羧酸或醛酮。
3.3 制药领域•加氢还原反应可用于合成各类药物中间体或药物,具有高效、高选择性的优点。
•加氢脱氧反应可对含有活性氧或氮的药物进行去除杂原子。
•加氢酰基化反应可对酮、醛等化合物进行功能化修饰。
4. 加氢设备的优势和发展趋势•加氢反应具有高效、高选择性、低能耗等优点,因此在化工领域得到广泛应用。
•加氢设备的发展趋势是提高反应活性,降低反应温度和压力,增加载体和催化剂的寿命。
•利用新型催化剂、改善反应器设计和优化氢气供应系统是提高加氢设备效率的关键。
5. 结论•加氢设备是一种重要的化工设备,通过加氢反应可以实现多种化学变化。
•在石油化工、精细化工和制药领域,加氢设备具有广泛的应用前景。
•加氢设备的发展将对化工工业的绿色可持续发展起到积极作用。
浅谈液相催化加氢反应器的形式
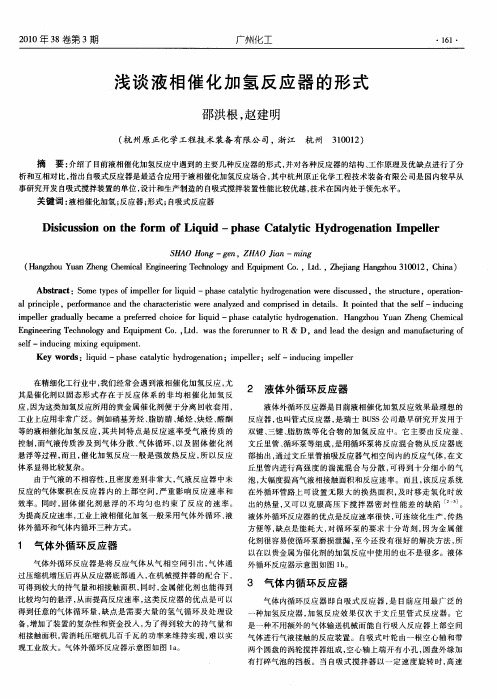
出的热量 , 又可 以 克服 高压下 搅拌 器 密封性 能 差 应速 率很快 , 可连续化 生产 , 热 传
方便等 , 缺点是能 耗大 , 对循 环泵 的要求 十分 苛刻 , 因为金属 催
2 液 体 外 循 环 反 应 器
液体外循环反应器是 目前液相催化 加氢反应效 果最理想 的
反应器 , 叫管式反应 器 , 也 是瑞士 B S U S公司最 早研究 开发用 于
应, 因为这类加氢反应所用 的贵金属催 化剂便 于分离 回收套用 ,
工业上应用 非常广泛 。例 如硝 基芳烃 、 脂肪腈 、 烯烃 、 炔烃 、 酮 醛
a r cpe,p r r n ea dtec aa tr t eea ay e n o r e eal.I p itdt a tesl —id cn lp n il ef ma c n h h rce si w r n zd a d c mp sd i d ti i o i c l i n s t one t h ef n u ig h
( aghuY a h n h mcl ni e n ehooyadE up e t o , t. Z e agH n zo 0 2 C i ) H nzo unZ egC e ia E g er gT cnl n q im n C . Ld , hj agh u30 1 , h a n i g i n 1 n
等的液相催 化加 氢反应 , 共 同特点是 反应 速率受 气液 传质 的 其 控制 , 而气液传质涉 及到气 体分 散 、 体循 环 、 气 以及 固体 催化 剂
悬浮等过程 , 而且 , 催化 加氢反 应一般 是强 放热 反应 , 以反 应 所 体系显得比较复杂。 由于气 液的不相 容性 , 且密度差别非 常大 , 气液反 应器 中未
液相加氢技术应用现状分析

液 相 加氢 技术 即在 反应 部 分不 设置 H : 循 环 系 统, 依靠 溶 解 足量 H 的液 相 产 品循 环 代 替 循 环 氢
来满足反应对 H : 的需要 , 从而大幅度 降低能耗 的 新 型加 氢工 艺 。 ’
1液相 加 氢技 术
液相加氢油中溶解 的H 量是关键问题 【 。宋
isotherming液相加氢技术中石化洛阳工程有限2液相加ቤተ መጻሕፍቲ ባይዱ技术的优点及其局限性公司和抚顺石油化工研究院共同开发的srh液相21优点循环加氢技术中国石化工程建设有限公司和北1液相加氢技术取消了循环氢系统在能耗京石油化工科学研究院共同开的slht连续液相方面具有明显优势
炼 油 与 化 工
2 0 1 5 年 第5 期
Co mbi n e d wi t h i n d u s t r i l a a p p l i c a t i o n s,i t a n ly a z e d t h e t e c h n i c a l f e a t u r e a n d d e v e l o p me n t p r o s p e c t o f t h r e e l i q u i d p ha s e
加氢技术、 S R H液相循环加氢技术和S L H T 连续液相加氢工艺 的技术特点及发展前景。 关键词 : 液相加氢 ; 技术特点; 工业应用; 发展前景
中 图分 类 号 : T E 6 2 4 . 4 3 文献标识码 : B 文章 编 号 : 1 6 7 1 — 4 9 6 2 ( 2 0 1 5 ) 0 5 . 0 0 0 5 — 0 3
永一等臼 用A s p e n — H Y S Y S 软件模拟计算在不同压 力、 温度 条件 下 H 和 H: S 在 柴油 中 的饱和 溶解 度 曲 线 。得 出结 论 , 随着 压 力 、 温度 的提 高 H: 饱 和 溶解
液相加氢技术进展
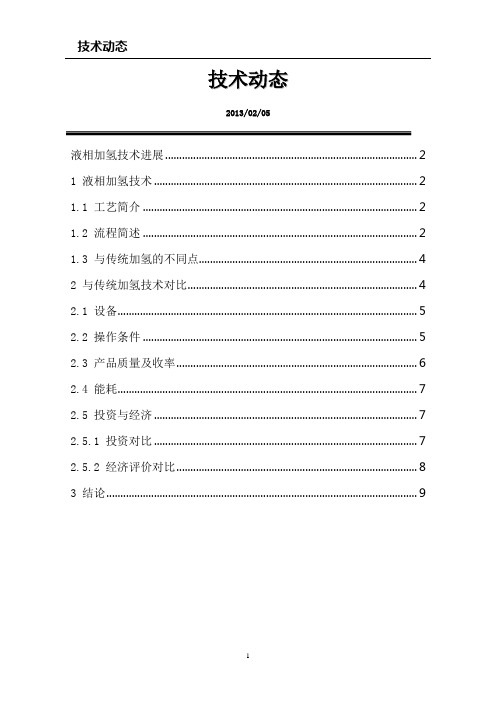
技术动态2013/02/05液相加氢技术进展 (2)1 液相加氢技术 (2)1.1 工艺简介 (2)1.2 流程简述 (2)1.3 与传统加氢的不同点 (4)2 与传统加氢技术对比 (4)2.1 设备 (5)2.2 操作条件 (5)2.3 产品质量及收率 (6)2.4 能耗 (7)2.5 投资与经济 (7)2.5.1 投资对比 (7)2.5.2 经济评价对比 (8)3 结论 (9)液相加氢技术进展在现代炼油行业,加氢处理装置往往由于操作条件较为苛刻,所以装置投资很大。
为此,为生产满足环保要求的清洁的石油产品,世界各国炼油技术人员开发了很多加氢技术,以降低装置的投资和能耗。
其中液相加氢技术是近几年发展起来的一种成熟的突破性加氢技术。
1 液相加氢技术1.1 工艺简介在加氢技术中,反应是以液相进行的。
传统加氢技术大量的富氢气循环气与进料一起进入反应器,以确保反应所要求的氢气被转换成液相。
液相加氢工艺技术反应部分不设置氢气循环系统,依靠液相产品循环以溶解足量的氢气,满足加氢反应的需要。
由于取消了氢气循环系统,节省了循环压缩机系统、高分系统及其相应设备,可以大大节约投资和能耗。
同时由于液相加氢工艺技术可以消除催化剂的润湿因子影响,而且循环油的比热容大,从而提高催化剂的利用效率,大大降低反应器的温升,降低裂化等副反应。
1.2 流程简述原料油自装置外来,通过原料油过滤器进行过滤,然后与精制柴油换热,进入滤后原料油缓冲罐,再经反应进料泵升压后,在流量控制下,与少量补充氢混合作为混合进料(图1)。
混合进料经过与一部分反应产物换热后,进入反应进料加热炉加热至所需温度,加热后的进料再与一定量的反应循环产物及一定量的补充新氢混合后进入加氢精制反应器第一催化剂床层,在催化剂作用下进行脱硫、脱氮、烯烃饱和、芳烃饱和等反应,加入到第一催化剂床层进料中的氢气量由进料液体的饱和限度决定,加入足够的氢气,直到第一催化剂床层有少量的尾气排出,这样可以确保氢气被完全饱和。
- 1、下载文档前请自行甄别文档内容的完整性,平台不提供额外的编辑、内容补充、找答案等附加服务。
- 2、"仅部分预览"的文档,不可在线预览部分如存在完整性等问题,可反馈申请退款(可完整预览的文档不适用该条件!)。
- 3、如文档侵犯您的权益,请联系客服反馈,我们会尽快为您处理(人工客服工作时间:9:00-18:30)。
Keyword s: liquid p ha se catalytic hydrogena tion; agita to r; app lica tion; deve lopm en t trend
引言
近年来 ,我国催化加氢技术在开发 、推广与使用上都 有了重大突破 。与传统的铁粉 、硫化碱 、水合阱等还原方法 相比 ,催化加氢具有副反应少 、效率高 、质量好 、能耗低 、三 废少等优点 ,在精细化工领域中得到了不断的开发和应 用 [1] 。
催化剂分散效果和减少其用量 ,是搅拌器设计需要进步一 研究的课题 ,液相催化加氢搅拌器的发展趋势首先是提高
自吸式搅拌器
气含率和气液相接触面积 ,形成均匀气液混合体系 ,实现 高效气液接触 ,强化气液传质过程 ,缩短气液反应时间 ;其
很多科研工作者将目光聚集在了自吸式搅拌器上 ,这 次是解决固体催化剂均匀悬浮问题 ,反应气体及固体催化
同样的悬浮程度时所需要的功率明显低于径流桨 。
的叶轮能使大量液体在叶轮
但是 ,在液相催化加氢反应中 ,当氢气从下方通入反 内外进行循环 , 根据文丘里
应釜后 ,如气量比较大 ,气泡因浮力而产生的上升流动使 喷射原理 , 液面上的气体通
得釜内液体的轴向流动型态被破坏 ,这时轴流式搅拌器对 过空心搅拌轴被高速运动的
均一 ,气含率的空间分布也较为均匀 ,且整体气含率较大 [2] 。 器组成 ,空心轴上端开有小
在不考虑氢气的情况下 , 轴流式搅拌器循环能力强 、 孔 ,圆盘外缘加有打碎气泡
排出量大 ,流体在釜内形成的整体循环流动对催化剂的悬 Байду номын сангаас挡板 。当自吸式搅拌器以
浮操作是十分有效的 。并且轴流式搅拌器在对催化剂达到 一定速度旋转时 , 高速运行
轴流式搅拌器
为了实现相间的充分混 合 ,提高传质效率 , 一些翼型轴 流桨 (图 2) 以其循环量大 、能 耗低 、气体分散能力强的优势在液相催化加氢中逐渐取代 了锚式桨 。这种搅拌器叶片面积率较大 ,即水平投影面上 叶片面积占由叶端画出的圆的面积的百分数较大 ,大面积
作者简介 :李洪涛 (1980 - ) ,男 ,硕士 。 收稿日期 : 2008 - 10 - 6
合 ,实现高效气液接触 ,强化气液传质过程 ,缩短气液反应 时间 ,获得了高的宏观反应速率 。
如果液位较深 ,自吸式搅拌器的吸气效果和对氢气的
层桨将上层桨有效分散的气体循环进入下部区域 ,在下部 分散效果会大大降低 ,同时 ,固液悬浮结构的不均匀也降
分散不良而凝并的气泡进入上部区域后又重新被高剪切 低了气固接触效率以及反应的速率 ,此时需要配以轴流桨
仅在上升过程中得到组合桨的分散而反应 ,大量未反应的 氢气聚积在反应器内的上部空间 ,严重影响了反应速率和
器等 ,对液相催化加氢反应的某一方面的性能起到很好的 改善效果 。在如何更进一步缩短搅拌时间 、解决放热 、改善
效率 。因此 ,很多科研人员开始考虑开发新的设备以提高 气液相的接触面积 ,从而提高反应的时空收率 。
遗憾的是 ,目前国内许多催化加氢厂家在生产过程中 采用的搅拌器不能达到很好的三相接触效果 ,导致了反应 时间过长 ,催化剂用量大 、反应不完全 ,严重影响了经济效 益 。本文结合杭州原正化学工程技术装备有限公司 2002 年以来的研究工作 ,重点介绍并分析了液相催化加氢过程 中用到的各种搅拌器 , 希望能 对国内化工领域的技术研究进 步产生一定的推动作用 。
与层间距在一定范围内变化不太敏感 ,这意味着多个叶轮 催化剂的用量 ,国内外科研机构和厂家开发了一系列的产
的设置在用来达到固体悬浮的同时可得到有效的气液传质 [8] 。品 ,诸如刮壁式搅拌器 、液压升降高速搅拌器 、集热式磁力
但是 ,由于气液的不相容性 ,且密度差别非常大 ,氢气 搅拌器 、恒温磁力搅拌器 、单片机混合搅拌器和永磁搅拌
在搅拌反应器中 ,机械搅拌的作用在于形成气液固三 相混合体系 ,促进氢气和固体催化剂的同时扩散 。为了达
到三相之间的充分接触 ,反应体系应满足以下要求 : 1) 要将反应釜底部的催化剂颗粒搅动起来 , 使之处
于悬浮状态 ,并且在其周围形成强烈的湍流 ,从而减小催 化剂颗粒和液体之间滞流层的厚度 ;
2) 使难溶解的氢气分散 , 形成微小的气泡分布于悬 浮液中 ,让液 、气相接触面积尽可能大 。因此 ,选择合适的 搅拌器以满足上述要求成了许多催化加氢厂家和搅拌器 设计生产企业共同面对的问题 。
摘要 :本文分别介绍了液相催化加氢中使用的各种搅拌器及其特点 ,轴流式搅拌器能在一定程度上达到催化剂悬浮与氢 气分散的效果 ;组合式搅拌器对催化剂悬浮与氢气分散具有明显的优势 ;自吸式搅拌器在所有搅拌器中能提供最大的气 液传质面积 ,得到最高的反应速率与氢气利用率 ,它将逐步成为新一代液相催化加氢装置的首选 。 关键词 :液相催化加氢 搅拌器 应用 发展趋势 中图分类号 : TQ050. 5 文献标识码 : A
种搅拌器将釜内液面上的氢气重新吸入并分散于液相 ,可 剂弥散于整个反应器内除气相空间外的每一个角落 ,类似
·94·
许多小反应器并联 ,能再现小试的选择性和转化率 ; 再次 是降低催化剂 ,反应气体用量 ,减少反应压力 ,提高生产安 全系数 ,同时也降低能耗 ,从而降低生产成本 。
结语
气液分散与催化剂悬浮问题是液相催化加氢中的核 心问题 ,其特点是反应速率受气液传质的控制 ,而气液传 质涉及到气体分散 、气体循环以及固体催化剂悬浮等过 程 。机械搅拌反应釜作为液相催化加氢中应用最广泛的设 备 ,选用合适的搅拌器可大幅提高反应的效率与时空收 率 ,对我国的精细化工行业影响巨大 。以往使用锚式桨 ,由 于气体分散及催化剂悬浮能力差已基本被淘汰 。大叶片式 翼型轴流桨目前也得到了较多应用 ,但是 ,氢气与催化剂 颗粒的共同作用破坏了这种桨的轴流型态 ,因此催化剂悬 浮能力与氢气分散能力均有所下降 。组合式搅拌器能够同 时满足气液传质与催化剂悬浮的过程 ,且对氢气有较长的 停留时间 ,因此是液相催化加氢中最优的常规搅拌器之 一 。自吸式搅拌器在所有搅拌器中能提供最大的气液传质 面积 ,得到最高的反应速率 ,对氢气的利用率也最高 ,已逐 步成为新一代液相催化加氢装置的首选 。
加氢中的气液传质有重要影响 。排出流向上时 ,流体流动
由于自吸式搅拌器在空心轴上开设进气孔降低了轴
几乎为轴向流 ; 而排出流向下时则带有较多的径向流成 的强度 ,因此需要在开孔处进行补强处理 。另外 ,液相催化
分 ,有较强的分区倾向 , 且区间混合效果与径向流桨相 加氢中反应釜内普遍高温高压 ,搅拌器的高转速带来的密
的桨所分散而再一次循环 , 因此可有效延长气相停留时 以改善流型 、增加吸气及气体分散效果 [ 10] 。组合使用的高
间 ,提高气含率 ,有利于气液传质比表面积的增加 [4 ] 。
效轴流桨能将气体与固体催化剂均匀地弥散在反应器内 ,
在这种组合中 ,下层轴流桨的排出流方向对液相催化 包括反应釜底部 ,从而达到了快速反应的目的 。
催化剂悬浮和氢气的分散效果都显著降低了 [3 ] 。
液体夹带后从叶轮排出 ,在自吸式叶轮的两圆盘间形成负
组合式搅拌器
压 ,反应器内液面上方的气体由空心轴上端小孔处吸入 , 沿空心轴向下 ,并由下端圆盘间小孔鼓出 ,气泡从桨端逸
组合桨 (图 3) 被开发出来 后 ,催化剂悬浮与氢气分散的问 题同时得到了圆满的解决 ,在液 相催化加氢中逐渐得到应用 。其
A pplica tion and D eve lpom en t of Ag ita tor in L iqu id Pha se Ca ta lytic Hydrogena tion
L I Hon gtao, CHEN L un jun, ZHANG W en feng
A bstra ct: the p ap er in troduces va riou s agita to rs and the ir charac te ristics in liqu id p ha se ca ta lytic hyd rogena tion. The ancho r imp e lle r has been p hased ou t basica lly because of slow reac tion rate and less cycle. The axia l - flow stirrer can m ake ca ta lyst su sp end and m ake hyd rogen gas d isp erse in som e extent. The com b ined agita to r ha s obvious advan tages of ca ta lyst su sp end ing and hyd rogen ga s dispe rsing. The se lf - inducing agita to r can p rovide w ith m axim al m a ss tran sfer area of ga s - to - liqu id in a ll agita to rs and acqu ire s the highe st reaction ra te and the utiliza tion ra te of hyd rogen gas, wh ich w ill becom e the first cho ice of the new liqu id p hase catalytic hyd rogenation device s.