焦化脱硫催化剂
焦化厂焦炉烟气脱硫脱硝技术的应用

焦化厂焦炉烟气脱硫脱硝技术的应用摘要:炼焦生产期间排放的烟气内部包含氮氧化物、二氧化硫等污染物,由此转变而言的PM2.5占据空气总量的50%左右,同时也会形成酸雨,诱发严重的环境问题。
在脱硫脱硝技术不断发展和进步的影响下,其为炼焦烟气污染物治理提供方向指导,尤其是氮氧化更为相关工作的顺利进行提供保障。
本文就针对当前相对成熟的脱硝工艺技术方法进行分析,并未今后焦化厂脱硫脱硝工作顺利进行提供保障。
关键词:焦化厂;焦炉烟气;脱硫脱硝技术;应用分析随着工业生产的应用热度逐渐升高,人们对工业排放污染的关注度也越来越高。
在工业生产的过程中由于工艺的需要导致大量污染物排放到生态环境中,严重威胁着人们的生命安全。
其中,焦化厂作为焦化生产的主要场所,每时每刻都在排放着大量的烟气,其成分中所包含SO2会导致酸雨的形成,进而给空气环境带来严重的威胁。
针对这种情况,焦化厂采用了脱硫脱硝技术对烟气中的污染物进行科学处理,有效减轻焦化烟气对生态环境造成的压力。
1焦化厂焦炉烟气的特点分析焦化厂的焦化生产过程非常复杂,中间需要经过多道处理程序。
洗精煤储存在焦化厂的备煤车间,而在后续的生产操作中,洗精煤需要经过煤塔的漏嘴装入到运输车中,因此在车间和煤塔之间需要经过封闭的通廊,来保证洗精煤的运送安全。
运输车将洗精煤按照顺序输送到炭化室进行干馏产生焦炭,干馏温度设置在960~1040℃。
焦炉的燃烧过程会产生大量的烟气,烟气会通过设置好的通道从烟囱排放到大气中。
焦炉的工作过程非常复杂,工艺也具有一定的特殊性。
对烟气的成分进行分析可知,烟气中主要含有SO2、粉尘以及氮氧化物,且氮氧化物所占的比例较高。
其中,SO2是一种非常常见的硫氧化物,会对大气造成非常严重的危害。
一旦将SO2与水相溶,便会发生化学反应进而产生亚硫酸,而亚硫酸在PM2.5的基础上会进一步氧化成硫酸,导致酸雨的形成,对环境造成不可挽回的影响。
氮氧化物所包含的化合物较多,除了NO2,其他的氮氧化物具有非常不稳定的特性。
焦化脱硫及提盐工艺的描述

December 08, 2020
谢谢大家!
5 提盐
• 焦炉煤气含有硫化氢、氢化氰等有害酸性物质, 当采用湿式催化氧化脱硫工艺时,脱硫液中生成 硫氰酸铵(钠)、硫代硫酸铵(钠)、硫酸铵( 钠)等副产盐类物质,并产生脱硫废液。它们存 在于溶液中不利于脱硫效率的提高,而且增加了 对设备的腐蚀作用。另一方面,硫氰酸铵(钠) 、硫代硫酸铵(钠)在工业上是很有市场价值的 产品。因此,废液的工业处理对焦化煤气系统的 安全防腐,对环境保护,对企业的经济效益都有 重要意义。
• 真空蒸发蒸汽冷凝液是冷凝氨水,返回工艺系统。
• 废活性炭经热风氧化可再生使用,一般可再生利用 2~3次。
• 本工艺装置包括:原废液脱色;一次真空蒸发浓缩,冷 却结晶、过滤提取粗硫代硫酸铵;二次真空蒸发浓缩, 冷却结晶、水洗涤过滤提取硫氰酸铵等三次加热蒸发浓 缩过程。粗制产品再结晶得到合格产品,另外还包括真空 泵系统。
• 再生段发生的基本反应如下:
•
NH4HS+1/2O2→NH4OH+S
•
(NH4)2S+1/2O2+H2O→2NH4OH+S
•
(NH4)2SX+1/2O2+H2O→2NH4OH+SX
• 除以上反应外,还进行以下副反应:
•
2NH4HS+2O2→(NH4)2S2O3+H2O
•
2(NH4)2S2O3+O2→2(NH4)2SO4+2S
3 工艺特点
• 1)改良一塔式焦化煤气脱硫工艺装置特点 • 对喷射再生槽流程,本工艺装置可不再设有独立的喷射再
生槽、液封槽、反应槽、富液泵、贫液中间槽等设备。 • 对再生塔流程,本工艺装置可不再设有独立的再生塔、脱
焦化厂烟气脱硝脱硫一体化解决方案1

110万吨/年焦炉烟气脱硝脱硫一体化技术方案110万吨/年焦炉烟道气与脱硝脱硫一体化设计方案廊坊市晋盛节能技术服务有限公司目录1. 项目概述 (2)1.1. 项目概况 (2)2. 设计依据 (2)2.1. 设计原则 (2)2.2. 设计标准 (3)2.3. 设计原始参数 (3)2.3.1 烟气参数 (3)2.3.2 气候条件 (4)2.4. 设计要求 (4)2.5. 工程范围 (4)3. 烟气脱硫脱硝一体化工艺 (5)3.1. 总工艺流程 (5)3.2. 脱硝工艺 (5)3.3. 脱硫工艺 (7)4. 烟气脱硫脱硝一体化技术说明 (8)4.1. 脱硝技术 (8)4.1.1脱硝系统的构成 (8)4.1.2脱硝系统主要设备 (9)4.2. 脱硫技术 (11)4.2.1脱硫工艺描述 (11)4.2.2脱硫主要设备 (11)5. 经济及环境效益分析 (13)5.1脱硫脱硝环境效益及节约费用 (13)5.2脱硫脱硝运行费用 (13)5.3脱硫脱硝投资费用 (14)5.4设备清单 (13)1.项目概述1.1.项目概况焦化厂是专门从事冶金焦炭生产及冶炼焦化产品、加工、回收的专业工厂。
焦、NOx及烟尘炉烟囱排放的大气污染物为焦炉煤气燃烧后产生的废气,主要有SO2等,污染物呈有组织高架点源连续性排放,是污染最为严重的行业之一。
2012年6月,环境保护部及国家质量监督检验检疫局联合发布了《炼焦化学工业污染物排放标准》,明确规定了焦化工业的大气污染物排放标准。
廊坊市晋盛节能技术服务有限公司一体化烟气治理技术,就是将烟气烟气除尘技术,烟气脱硫、脱硝技术捆绑在一起,形成一套集成创新的装置,这套装置既能除尘、脱硫、脱硝,从而达到烟气资源化利用的目的。
从此改变烟气治理只有投入,没有产出的困境。
2.设计依据2.1.设计原则2.1.1脱硫脱硝➢对尾气同时进行脱硝及脱硫治理。
➢采用高效、先进、运行稳定、管理方便的治理工艺及技术,保证废气的达标排放;➢烟气净化治理不影响焦化厂生产工艺的正常运行。
焦化脱硫废液及硫泥干化焚烧制酸的技术研究

焦化脱硫废液及硫泥干化焚烧制酸的技术研究何龙;李金山;刘自凤;王光华;吴木之;王晴东;陈哲;胡林;马志勇【摘要】针对目前国内外湿式氧化法脱硫工艺中存在的脱硫废液、硫泥污染问题,提出了焦化脱硫废液、硫泥一体干化焚烧,制取浓硫酸的新工艺.该工艺以硫泡沫与脱硫废液共同提质干化、所得粗盐硫磺为原料直接焚烧,采用"3+2"ⅢⅠ-ⅤⅣⅡ二转二吸制酸工艺流程.该技术不仅提高了硫的资源利用率,使SO2总转化率大于或等于99.7%,且工艺废水均可回收利用,无二次污染产生.%The pollution problem of desulfurization waste liquid and sulphur sludge in desulfurization process at home and abroad,A new process for producing concentrated sulphuric acid from the waste liquid of coking desulfurization and slime dry incineration is put ing the process of sulfur foam desulfurization wastewater and common quality and drying,the direct burning of sulfur salt the use of advanced"3 + 2"ⅢⅠ-ⅤⅣⅡtwo RPM two suction process,improve the sulphur resource utilization rate,the total conversion rate of SO2 more than 99.7%;In the process of production,the wastewater from the process is recycled,and no two pollution is produced.【期刊名称】《硫酸工业》【年(卷),期】2018(000)002【总页数】4页(P13-15,18)【关键词】湿式氧化法;脱硫;焦化;硫泥;硫酸生产;技术【作者】何龙;李金山;刘自凤;王光华;吴木之;王晴东;陈哲;胡林;马志勇【作者单位】武汉科技大学化学与化工学院,湖北武汉430081;萍乡市新安工业有限责任公司,江西萍乡337000;杭州蓝光建设工程咨询有限公司,浙江杭州310000;武汉科技大学化学与化工学院,湖北武汉430081;中国宝武钢铁集团广西钢铁集团有限公司,广西防城港538000;武汉科技大学化学与化工学院,湖北武汉430081;武汉科技大学化学与化工学院,湖北武汉430081;武汉科技大学化学与化工学院,湖北武汉430081;武汉科技大学化学与化工学院,湖北武汉430081【正文语种】中文【中图分类】TQ111.16;X781目前,众多焦化企业采用湿式氧化法(HPF法)脱除焦炉煤气中硫化氢和氰化氢。
湿式氧化法脱硫催化剂的合理应用

1 3
湿 式 化 法 脱 硫 催 化 剂 的 合 理 应 用 氧
张 彤
( 吉林长春 东狮科贸实业有限公司 10 1 ) 3 15 脱硫系统进 口气体中硫化氢质量浓度达 5gm / 左右 , 运行不久 , 便出现了脱硫效率低 、 副盐生成 量大 、 硫磺 产 量低 等 问题 。其 原 因是 在 原 料煤 种 发生变化 、 口气体中硫含量较高的情况下 , 进 没有 以酞 菁钴类 催化 剂 为 主 , 挥 不 了酞 菁 钴类 催 化 发 剂脱高硫及有机硫的能力 。在笔者的建议下 , 增 加了酞菁钴类脱硫催化剂的用量 , 并对副盐进行 了处理 , 工况有所好转 。
下 简称 东狮 公 司 ) 产 的 “ 8 ” 硫 催 化 剂 还 有 生 88 脱
说 。笔者认为 : 在栲胶与酞菁钴这两大类脱硫催 化剂 中, 如果进 口气体 中硫化氢含量不高 、 脱硫负 荷不大 , 且工艺管理较为严格 , 可以选择栲胶 ; 如 果进 口气体中硫含量较高或有机硫含量较高 、 脱 硫负荷较大、 系统阻力较大, 可以选择使用酞菁钴 类 催 化剂 。东狮 公 司在 2 1 研 制 开发 的 D T 00年 S. 1 型与 D T2型脱硫催化剂 , S- 综合 了栲脱 与酞菁 钴类催化剂的优点 , 实现了优势互补 , 具有脱硫效 率高 、 降低系统阻力 、 抑制副盐生成 、 提高硫磺产 量等特点 , 并已在河南晋开化肥厂与 山东荣信焦
用增加数百元 , 考虑到副产的硫磺 , 增加 的费用更 少 ; 每天减 少原 料煤 费用支 出约 3万 元 , 济效 但 经
益显著。 企 业在 催化 剂 的用 量 方 面 出 现 问题 , 了对 除
催 化 剂性能 掌握 不准 确之外 , 也有 2点 客观 因素 :
焦炉煤气脱硫及硫回收工艺分析
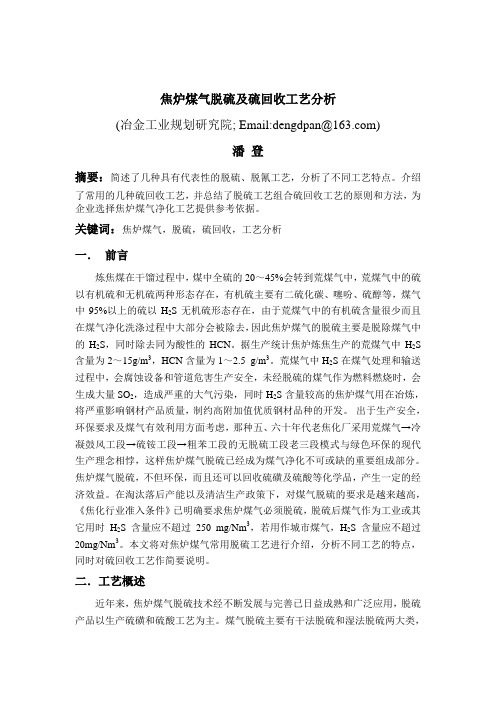
焦炉煤气脱硫及硫回收工艺分析(冶金工业规划研究院; Email:dengdpan@)潘登摘要:简述了几种具有代表性的脱硫、脱氰工艺,分析了不同工艺特点。
介绍了常用的几种硫回收工艺,并总结了脱硫工艺组合硫回收工艺的原则和方法,为企业选择焦炉煤气净化工艺提供参考依据。
关键词:焦炉煤气,脱硫,硫回收,工艺分析一.前言炼焦煤在干馏过程中,煤中全硫的20~45%会转到荒煤气中,荒煤气中的硫以有机硫和无机硫两种形态存在,有机硫主要有二硫化碳、噻吩、硫醇等,煤气中95%以上的硫以H2S无机硫形态存在,由于荒煤气中的有机硫含量很少而且在煤气净化洗涤过程中大部分会被除去,因此焦炉煤气的脱硫主要是脱除煤气中的H2S,同时除去同为酸性的HCN。
据生产统计焦炉炼焦生产的荒煤气中H2S 含量为2~15g/m3,HCN含量为1~2.5 g/m3。
荒煤气中H2S在煤气处理和输送过程中,会腐蚀设备和管道危害生产安全,未经脱硫的煤气作为燃料燃烧时,会生成大量SO2,造成严重的大气污染,同时H2S含量较高的焦炉煤气用在冶炼,将严重影响钢材产品质量,制约高附加值优质钢材品种的开发。
出于生产安全,环保要求及煤气有效利用方面考虑,那种五、六十年代老焦化厂采用荒煤气→冷凝鼓风工段→硫铵工段→粗苯工段的无脱硫工段老三段模式与绿色环保的现代生产理念相悖,这样焦炉煤气脱硫已经成为煤气净化不可或缺的重要组成部分。
焦炉煤气脱硫,不但环保,而且还可以回收硫磺及硫酸等化学品,产生一定的经济效益。
在淘汰落后产能以及清洁生产政策下,对煤气脱硫的要求是越来越高,《焦化行业准入条件》已明确要求焦炉煤气必须脱硫,脱硫后煤气作为工业或其它用时H2S含量应不超过250 mg/Nm3,若用作城市煤气,H2S含量应不超过20mg/Nm3。
本文将对焦炉煤气常用脱硫工艺进行介绍,分析不同工艺的特点,同时对硫回收工艺作简要说明。
二.工艺概述近年来,焦炉煤气脱硫技术经不断发展与完善已日益成熟和广泛应用,脱硫产品以生产硫磺和硫酸工艺为主。
焦化企业脱硫废液提盐工艺优化

关键词:焦化企业;脱硫废液;提盐工艺;优化炼焦过程中的煤会转化为焦炭和荒煤气,在高温烧焦条件下将部分硫元素转化为H2S,容易出现催化剂中毒的现象,为此要预先进行脱除H2S的处理,针对NH4SCN和(NH4)2SO4的溶解度差异性较小、市场对(NH4)2S2O3需求量少的状态,本文提出脱硫废液资源化治理项目,进行脱硫废液的回收和利用,解决脱硫废液造成的环境污染问题,提升焦化企业的经济效益。
1焦炉煤气脱硫概述焦炉煤气脱硫废液具有强烈的刺激性气味和毒性,引发碱溶液或脱硫催化剂消耗增加,提高脱硫液成本,造成资源浪费的现象,无法体现循环利用和清洁生产的环保理念。
当前焦炉煤气脱硫方法主要以湿式催化氧化法为主,并根据脱硫液组成的不同,湿式催化氧化脱硫工艺主要有以下几种方法:1)PDS法。
这是一种新型的脱硫方法,整个反应过程为:溶解氧在碱性溶液中吸附活化;煤气与脱硫液接触并生成HS-;其他物质在催化剂体系中进行化学反应并生成单质硫;催化剂吸附氧再生。
2)HPF法脱硫。
这是一种液相脱硫工艺,以煤气中的氨为碱源,中和焦炉煤气中的H2S,在反应中以酞菁钴磺酸盐为主催化剂、苯二酚和硫酸亚铁为助催化剂,达到98%的脱硫效率。
3)塔-希法。
主要涵括有塔克哈克斯工艺脱硫和希罗哈克斯脱硫废液处理两种工艺,选取混有1,4NQ(1,4-萘醌二磺酸钠)的氨水,将脱硫液脱硫温度控制在34-36℃,吸收液吸收焦炉煤气中的H2S,再转化为多硫化铵,氧化生成氨水及单质S。
4)改良ADA法。
这种脱硫方法是以ADA为主催化剂、NaVO3为助催化剂、稀Na2CO3为脱硫剂、酒石酸钾钠为分散剂,可以达到99%以上的脱硫效率。
5)栲胶法。
这是利用羟基进行氧化还原反应,栲胶内含诸多活泼羟基,具有防堵剂、防腐剂、钒离子配合剂的效用。
6)FRC法。
该法由Fumaks法脱硫、Rhodacs法脱氰、Compacs法废液净化制酸工艺组成,以三硝基苯酚为催化剂,在氨水与焦炉煤气逆向充分接触的条件下,进行酸碱中和反应,生成NH4HS和NH4CN,与脱硫液一同流出,再进入再生塔底部与空气预混,加压氧化再生为单质硫和再生液,泵送至脱硫塔循环利用[1]。
CoS高效脱硫剂在生产中的应用

有一定 的有效 期 , 间长产 品发生 了变 质 , 重 降 时 严 低 了有 效成份 的含量 。若是 绿色液 体或 溶解水 为
4 结论
使 用 C S高效 脱 硫 剂 的湿 法 脱 硫 , o 具有 净 化
天蓝 色溶 液 , 明产 品合 格 , 证 脱硫 效 率 高 , 以使 可
用。 32 投 入 方 法 .
杭州化 工
2 0 .8 3 0 8 () 3
2 1
CS 0 高效脱硫剂在生产中的应用
刘 丽 娟
( 山市征 楠 焦化 有 限公 司, 山市 0 0 ) 唐 唐 6 0
摘 要 : 据脱硫 工段 干法 脱硫 不能 满足城 市煤 气的指 标要 求 , 系统进 行 了改造 。选 用 湿法 脱硫 根 对 装置 , 用 C S高效脱硫 剂降低 煤 气 中硫 化 氢 的含 量 , 使 o 可提 高经 济效益 和社 会效 益 。
1 . 脱 硫原 理 2
1脱 硫 塔 ;. 环槽 ;. 环 泵 ;. 生塔 ;. . 2循 3循 4再 5 硫
泡沫槽 ; . 泡 沫泵 ;. 6硫 7 压滤 机 ; . 冲罐 8缓
2 . 设备情 况 2
脱硫塔 30 × 10 两 台 , 00 2 50 内装 D Q三角多
孔磁质 填料 D 一 0 10 ,再 生塔 3 0 x 9 1 Q 1 2 m’ 8o 49 4
1
炉 两座及 配套化 产 回收车 间 。为 保证外 供 煤气 的
硫 化 氢含 量 <2 m 。 0 ,公 司配 套 有 干 法脱 硫 装
置。
N 2x H O O 鱼 2 a H s a + 2+ s 21 N O + x上
脱 有机硫 的化 学 吸收反 应 :
- 1、下载文档前请自行甄别文档内容的完整性,平台不提供额外的编辑、内容补充、找答案等附加服务。
- 2、"仅部分预览"的文档,不可在线预览部分如存在完整性等问题,可反馈申请退款(可完整预览的文档不适用该条件!)。
- 3、如文档侵犯您的权益,请联系客服反馈,我们会尽快为您处理(人工客服工作时间:9:00-18:30)。
脱硫催化剂说明
目前,我国用于焦炉煤气的湿法脱硫工艺主要有湿式氧化和湿式吸收工艺两种,而用于
湿式氧化工艺的脱硫催化剂有十余种,概括起来可分为两大类:第一类是酚-醌转化(活性
基团转化),用变价离子催化,如ADA、对苯二酚、栲胶、F/R法中的苦味酸(PIA)和TAKAHAX
法中的1,4-萘醌2-磺酸钠等。上述脱硫催化剂虽能满足某些工艺要求,但也存在一些缺点,
如不能脱除有机硫,总脱硫效率低,硫泡沫不易分离,堵塞设备,适应H2S范围小,脱硫成
本较高等。第二类是近年来发展起来的磺化酞菁钴复合金属离子类脱硫催化剂,这类脱硫催
化剂与第一类不同的是脱硫催化剂本身是载氧体,通过本身携带的原子氧完成氧化再生作
用。
Z L脱硫催化剂属于第二类催化剂,但它吸收了第一类催化剂的优点,是一种新型的复
合型脱硫催化剂,已成功用于多家焦炉煤气的湿式氧化脱硫工艺,特别是在氨法HPF脱硫工
艺中的应用,显示了其优异的性能特点,取得了显著的社会效益。
1.Z L催化剂的性能特点和催化氧化原理
1.1性能特点
理论和生产实践都表明,Z L脱硫催化剂用于HPF脱硫工艺具有以下性能特点。
1) 该产品适合高、中、低含硫量的焦炉煤气,并且脱硫脱氰速度快、效率高,脱硫效
率可达98%以上;脱氰效率可达90%以上。
2) 在脱除无机硫的同时,可同时脱除有机硫。
3) 在同等工艺条件下,ZL催化剂和其他催化剂相比具有硫泡沫颗粒大,易分离、不
堵塞设备的特点,且用量少、运行成本低。
4) ZL催化剂对于硫磺的生成具有较好的选择性,所以付盐生长速度慢,废液排量小,
处理费用低,环境污染小。
1.2催化氧化反应原理
1)吸收反应
硫化氢(H2S)、硫醇(RHS)、羰基硫(COS)、 二硫化碳(CS2)等与碱性溶液反应生
成相应的化合物:
由上述吸收反应可知,在一定的工艺条件下,若使吸收反应进行彻底,需使体系中的
S2-被氧化成单质硫而分离。
2)脱硫反应
由于ZL催化剂的特殊分子结构具有携氧能力,在脱硫过程中,其不断释放出具有较高
氧化活性的原子氧,能迅速将体系中的S2-氧化成单质硫,大大强化了脱硫效果,主要反
应过程为:
3) 再生反应
脱硫反应中,催化剂所携带的氧被消耗,鼓入空气使其再生:
研究表明,ZL催化剂的作用机理如下。
a:ZL脱硫催化剂在碱性溶液中将溶解的O2吸附活化,形成高活性大离子;
b:当遇到H2S等含硫化合物时,将其吸附到高活性的大离子微观表面,在生产条件
下,使H2S等含硫化合物中的硫氧化成单质硫或多硫化物;
c:单质硫或多硫化物从ZL脱硫催化剂表面解吸而离去;
d:ZL脱硫催化剂经重新获得氧而再生.反应过程如下:
4) 副反应
1.3 ZL脱硫催化剂的性能指标
外观:蓝黑色粉末,粒度小于20目;水不溶物(﹪)≦3.00;催化活性≧0.06min-1。
2.ZL催化剂在焦炉煤气HPF脱硫工艺中的应用
从全国多家焦化厂对ZL脱硫催化剂的应用情况看,其应用范围十分广泛,既可单独用
于以Na2CO3为碱源的改良ADA工艺,也可与对苯二酚混合使用脱硫,还可用于以氨为碱源
的HPF焦炉煤气脱硫工艺。下面以HPF脱硫工艺为例对ZL脱硫催化剂的应用情况给以介绍。
2.1 ZL脱硫催化剂的工艺参数
根据脱硫生产工艺和设计要求不同,ZL脱硫催化剂的工艺参数有所差别,但基本工艺
参数如表1所示。
2.2 ZL脱硫催化剂的使用方法
ZL脱硫催化剂的使用,可采用冲击性投加或连续滴加方式。将ZL脱硫催化剂用容器溶
解直接加入反应槽或贫液槽中即可。一般来讲,开工初期,第一次投放量为每百立方米脱硫
液加入ZL脱硫催化剂3~5kg,系统运行稳定后,每天定时补加,使脱硫液中催化剂浓度
保持在30~50ppm。根据各厂使用经验,我们总结出每脱除一吨H2S大约消耗ZL催化剂0.8~
1.2kg。
2.3 在氨法HPF脱硫工艺中的应用结果
工艺简介
某厂焦炉煤气采用氨法HPF脱硫工艺,设计处理煤气量57000m3/h,入口煤气H2S含量5~
6g/m3,脱硫后煤气H2S含量≦0.5g/m3。目前效果更好脱硫焦炉煤气硫化氢小于100 mg/m3
该厂选用ZL脱硫催化剂,达到了预期的处理效果。工艺流程为:风机后煤气经预冷塔予冷
后,分别进入两台并联的脱硫塔,富液经循环泵进入各自的再生系统,再生后的贫液自流入
脱硫塔循环喷洒。再生空气从再生塔底部鼓入;为增加煤气中的氨含量,提高煤气的氨硫比,
把蒸氨塔顶的氨气经冷凝成氨水进入反应槽。
3. 副盐的增长与控制
众所周知,湿式氧化脱硫工艺的主要问题之一是废液的增长速度和废液的处理问题,HPF
脱硫工艺的含硫铵盐废液处理采取回兑配煤的方法,而对焦碳质量和煤气成分无显著影响,
可认为是一种简单经济的方法,较好地解决了废液的处理问题。但生产实践表明,该方法对
配煤环境、配煤设施的污染和腐蚀较重,因此如何最大限度地减少和控制付盐的增长,应成
为我们研究讨论的问题之一。
从1.2.4中的副反应(1)可以看出,该反应的发生主要和下列因素有关,一是脱硫液
温度,二是脱硫液的碱度,三是再生塔的鼓风强度(即氧密度)。控制好上述几个因素,可
使脱硫液中的(NH4)2S2O3含量几乎保持不变。
3.1 脱硫液温度
温度的控制主要考虑脱硫和再生两过程。前者是放热反应,较低的温度不仅利于脱硫操
作,也可减少副反应(1)的发生,温度太低不利于再生操作。综合考虑反应热及设备保温
情况,煤气温度控制为35℃,脱硫液温度38℃。
3.2脱硫液的碱度
1.2.1中的吸收反应要求,ZL脱硫催化剂必须在碱性(氨或纯碱)溶液中进行,要使吸
收反应完全,脱硫溶液的PH值必须控制得高一些。碱度的大小视煤气中的硫含量而有所波
动,实践证明:常压下的焦炉煤气脱硫,对于氨法,PH值控制在8.2~8.7为宜,脱硫液中
游离氨含量5.0~7.5;用碳酸钠做碱源时,PH在8.2~8.7之间,碱度0.2~0.3N。因而在
一定的硫氢化物的浓度下,副产物硫代硫酸盐的生成速度较快,在生产实践中,为减少副反
应的发生,根据生产中的进、出口煤气的H2S含量和实际的脱硫效率,应保持脱硫液的碱度
适当而不能过高。
3.3鼓风强度
足够高的氧密度是ZL催化剂再生的必要条件,同时也使副反应得以进行,因此,鼓风
强度的大小应根据脱硫液的实际再生效果来确定,在满足再生要求的前提下,适当低的鼓风
强度对减少副反应的发生和节约动力消耗都是有利的。再生塔的鼓风强度一般控制在95~
100m3/m2·h。
值得注意得是,1.2.4中的副反应(2)主要和煤气中的HCN的含量有关,也与单质硫
能否及时分离有关。使用ZL催化剂,及时地把单质硫分离出去,可减慢NH4SCN的增长速度;
另外,在ZL催化剂的作用下,NH4SCN还可以发生如下转化反应:
在氧化再生时,ZL将HS-催化氧化:
ZL
HS-+1/2O2→ OH-+S
由以上分析可以看出,在HPF脱硫工艺中应用ZL脱硫催化剂,副反应能够得到比较有效
地控制,因而副盐增长缓慢.最大限度地减少了废液处理量.
4 结论
ZL脱硫催化剂具有良好的性能特点,可用于焦炉煤气湿式氧化脱硫工艺,其在氨法H
PF脱硫工艺中应用,各项指标完全可以达到设计要求,具有脱硫效率高、硫磺颗粒大、硫
泡沫易分离和运行费用低等特点,而且副反应能得到较好地控制,废液量少。