钻模设计
随动式钻模的设计

。
2 00 3
针对 不 同品种 的工 件 与钻孔 尺 寸只 需 更换 钻 套 与调 节 钻模行程 即 可 起移动
, ,
使用 十分方 便
。
由于 钻 模 是 随着 主 轴箱
,
一
作者简介
:
曹鹏杰
:
,
男
,
19 7 4
。
年生
,
江 苏邳 县 人
。
,
硕士
,
工 程
因此 完 全 不 影 响 工 件 的装 卸
实现 了 设 计 意 图
,
定 扭矩 的特性
可 以保 证 主轴继 续 进 给时钻模 板上 的
一
参考文献
王 光
:
钻套与 主轴 的同心 度并且 具有
精度
。
定 的刚性
,
,
确 保 了钻孔 的
,
斗
,
王
春福
.
.
机 床 夹具 设 计 手 册
[M ]
.
上 海
:
上
海科技
加 工 完成后
,
主轴箱 抬起
,
钻 头 与工 件脱 离
钻模
出版 社
.
200 3
。
师
。
研究领域
机械设计
已 发表论文 1 篇
(编 辑 : 向
飞)
(上 接 第 4 9 页 )
收线装 置 的工 作原 理 如 图 9 所 示
。
收 线 电机 接 收 P L C
l 和齿
在
一
些 问题
,
,
但 它 的 开 发 为 国 内微 细 扁 线 材 的 研 究 做 出 了
,
翻转式钻模课程设计
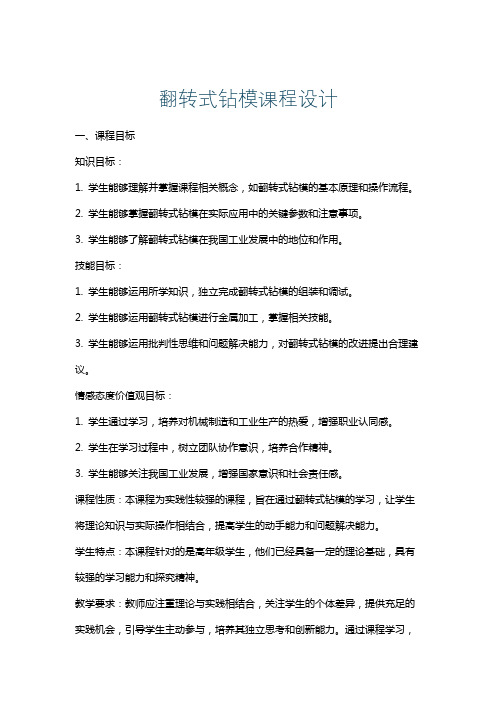
翻转式钻模课程设计一、课程目标知识目标:1. 学生能够理解并掌握课程相关概念,如翻转式钻模的基本原理和操作流程。
2. 学生能够掌握翻转式钻模在实际应用中的关键参数和注意事项。
3. 学生能够了解翻转式钻模在我国工业发展中的地位和作用。
技能目标:1. 学生能够运用所学知识,独立完成翻转式钻模的组装和调试。
2. 学生能够运用翻转式钻模进行金属加工,掌握相关技能。
3. 学生能够运用批判性思维和问题解决能力,对翻转式钻模的改进提出合理建议。
情感态度价值观目标:1. 学生通过学习,培养对机械制造和工业生产的热爱,增强职业认同感。
2. 学生在学习过程中,树立团队协作意识,培养合作精神。
3. 学生能够关注我国工业发展,增强国家意识和社会责任感。
课程性质:本课程为实践性较强的课程,旨在通过翻转式钻模的学习,让学生将理论知识与实际操作相结合,提高学生的动手能力和问题解决能力。
学生特点:本课程针对的是高年级学生,他们已经具备一定的理论基础,具有较强的学习能力和探究精神。
教学要求:教师应注重理论与实践相结合,关注学生的个体差异,提供充足的实践机会,引导学生主动参与,培养其独立思考和创新能力。
通过课程学习,使学生达到上述课程目标,为今后的学习和工作打下坚实基础。
二、教学内容1. 翻转式钻模概述- 了解翻转式钻模的发展历程、分类及特点。
- 理解翻转式钻模的工作原理及其在机械加工中的应用。
2. 翻转式钻模的组成与结构- 掌握翻转式钻模的主要部件及其功能。
- 学习翻转式钻模的组装与拆卸方法。
3. 翻转式钻模的操作与调试- 学习翻转式钻模的操作流程及安全注意事项。
- 掌握翻转式钻模的调试方法,确保加工精度。
4. 翻转式钻模在实际应用中的案例分析- 分析典型翻转式钻模在实际生产中的应用案例。
- 学习翻转式钻模的优化与改进方法。
5. 翻转式钻模的维护与保养- 了解翻转式钻模的常见故障及其排除方法。
- 掌握翻转式钻模的日常维护与保养技巧。
钻模板 设计
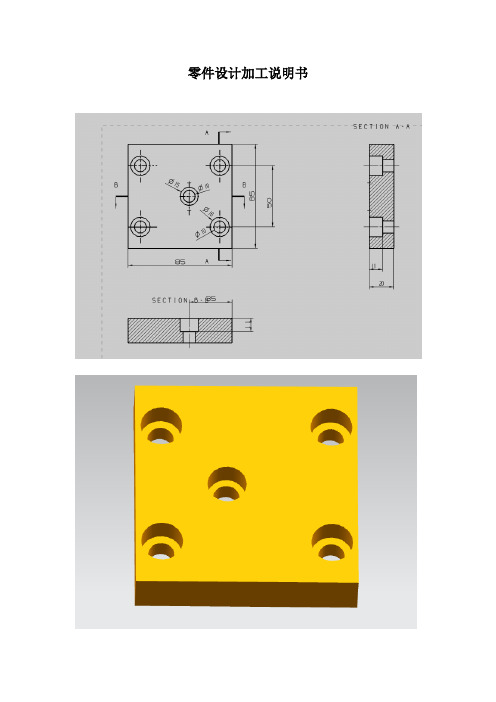
零件设计加工说明书(零件图)一、零件的分析1)钻模板的作用:用于安放钻套,并确保钻套在钻模上的固定位置。
2)钻模板的工艺分析由于钻模板的上下表面及四周在装配时有配合要求,故加工时应该合理的选择机床加工,在加工过程中选择合理装夹方法用于合理限制工件的自由度,防止欠定位过定位的发生。
同时由于4Xφ10的阶梯孔是是用螺纹与夹具体固定的,没有公差要求,故加工要求困难度较低。
对于与钻套相配合的孔有尺寸公差的要求为保证达到加工要求可用数控铣床加工二、工艺规程设计1) 确定毛坯的规格100X100X28的钢板,材料为45钢。
2)基面的选择①粗基准的选择:在加工四周时以毛坯的上下两个大平面作为加工的粗基准,这样可以防止欠定位的出现,同时用定位棒可防止过定位的出现。
②精基准的选择:精基准的选择主要应该考虑基准重合的问题,当设计基准与工序基准不重合时,应该进行尺寸换算。
3)制定工艺路线工序1:下料100X100X28的钢板,材料为45钢。
工序2:热处理表面硬度为28~32HRC。
工序3:在牛头刨床上粗加工钻模板的四周,以除去硬皮层。
工序4:①在X5132铣床上粗铣已经去过硬皮的工件,保证四周的垂直度及85X90的尺寸②在加工钻模板的上下表面保证尺寸及上下表面的平行度同时留下磨削余量。
工序5:①画线在正确的位置上钻4Xφ10的孔。
②在已经钻的孔上加工4Xφ16深度为11的忽孔。
③再加工与钻套相配的阶梯孔,保证加工尺寸要求。
工序6:在磨床上磨工件的上下两面以保证上下表面之间的尺寸20及表面粗糙度Ra0.8.工序7:冲箭头。
工序6:终检。
三、刀具的选择端面铣刀,刨床刀具,麻花钻:φ10.6 φ16 φ9. 8φ14.5,立铣刀:φ10 φ15。
钻模板班级:姓名:学号:。
钻模设计示例
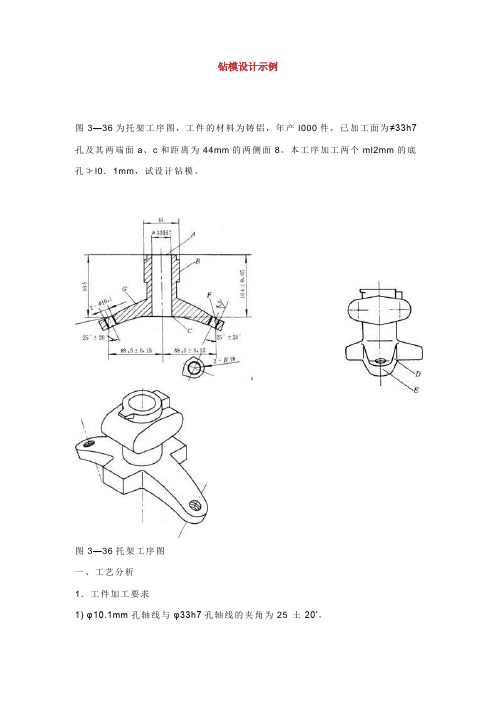
钻模设计示例图3—36为托架工序图,工件的材料为铸铝,年产l000件,已加工面为≠33h7孔及其两端面a、c和距离为44mm的两侧面8。
本工序加工两个ml2mm的底孔≯l0.1mm,试设计钻模。
图3—36托架工序图一、工艺分析1.工件加工要求1) φ10.1mm孔轴线与φ33h7孔轴线的夹角为25°土20′。
2) φ10.1mm孔到φ33h7孔轴线的距离为88.55土0.15mm。
3)两加工孔对两个rl8mm轴线组成的中心面对称(未注公差)。
此外,105mm的尺寸是为了方便斜孔钻模的设计和计算而必须标注的工艺尺寸。
2.工序基准根据以上要求,工序基准为φ33h7孔、a面及两个rl8mm的中间平面。
3.其它一些需要考虑的问题为保证钻套及加工孔轴线垂直于钻床工作台面,主要限位基准必须倾斜,主要限位基准相对钻套轴线倾斜的钻模称为斜孔钻模;设计斜孔钻模时,需设置工艺孔;两个410.1mm孔应在一次装夹中加工,因此钻模应设置分度装置;工件加工部位刚度较差,设计时应考虑加强。
二、托架斜孔分度钻模结构设计1.定位方案和定位装置的设计方案l:选工序基准φ33h7孔、a面及rl8mm作定位基面。
如图3-37a所示,以心轴和端面限制五个自由度,在r18mm处用活动v形块l限制一个角度自由度z。
加工部位设置两个辅助支承钉2,以提高工件的刚a)度。
此方案由于基准完全重合而定位误差小,但夹紧装置与导向装置易互相干扰,而且结构较大。
方案2:选φ33h7孔、c面及r18mm作定位基面。
其结构如图3-22b所示,心轴及其端面限制五个自由度,用活动v形块l限制z。
在加工孔下方用两个斜楔作辅助支承。
此方案虽然工序基准a与定位基准c不重合,但由于尺寸l05mm精度不高,故影响图3-37托架定位方案不大;此方案结构紧凑,1一活动v形块2一辅助支承钉3一斜楔辅助支承工件装夹方便。
为使结构设计方便,选甩第二方案更有利。
2.导向方案由于两个加工孔是螺纹底孔,装卸方便的情况下,尽可能选用固定式钻模板。
小孔钻模的设计

针对以上情况 , 考虑到既要保证产 品质量
还 要考虑 到方 便 工 人 装 夹 和操 作 加 工 , 提 高 为 加工 效 率 同 时 保 证 产 品 精 度 , 据 产 品 数 量 根 多 、 工 难 度 大 的特 点 , 过 反 复 思考 为 产 品 加 经 设计 了特 殊 的专用 模具 ,如 图 2所示 。
轴承 技术
21 00年第 1 期
・ 7・ 2
小 孔钻 模 的设 计
( 业务拓展 部 ) 崔 鑫 ( 工模 具制造有 限公 司) 穆敬巍 吕全英
摘
题。
要: 针对 油沟 上进 行小 孔加 工 、 料表 面 比较 硬 等 问题 , 材 设计 特 殊 结构 钻 模 解决 了技 术难
二是 由于小孔 直 径 仅 为 1 l, mn 而普 通 l钻 头
长 度较 短 , 长 钻 头 刚 性 差 易 折 断 , 计 成 多 加 设
图 1 产 品示 意 图
边形 可 以充分 利 用 空 问 , 用 标 准钻 头 相 对 提 使
高了刚性 。为保证模体 2 8 排 等分小孔的位置
2 确 定钻 模 结构
关 键词 : 小孔 ; 料硬 ; 材 定位 难 ; 量 大 批
1 概 述
我公司加工 几种型号 的专用轴 承 , 轴承 内圈 的生产工 艺流程 确 定先 加工 轴 承滚 道 和油 沟后 再钻加工 油孑 ; L在轴承 内圈滚道两 端油沟上 钻加
工6 等分 1 的小油孔 , 由于材料是高淬透性合
根据 标 准查 得钻 头 长 度 有些 短 , 头 与钻 模 干 钻 图 2 钻 模简 图
涉 ; 时 考 虑 到 产 品 批 量 大 数 量 多 , 普 通 分 同 用 度 头装夹 加工 存 在 分 度 累计 误差 、 率 低 等 的 效 缺点 。因此重 新 考 虑 钻模 结 构 形 状 , 后 将 外 最 形设 计 为六边 形 如 图 3所 示 : 种结 构 一 是 便 这 于装 夹 , 且 在 普 通 的小 钻 床 上 就 可 以 加 工 ; 并
SY型支架钻模的设计

SY型支架钻模的设计摘要:机械加工工艺是实现产品设计,保证产品质量,节约能源,降低消耗的重要手段,是企业进行生产准备,计划调度,加工操作,安全生产,技术检测和健全劳动的重要依据,为了在加工中提高税率,往往一些产品需要设计一些夹具。
在此零件上我们就对此简单的零件作一个孔的钻模设计,以此让读者对一般零件加工的钻模设计有个大致的了解。
关键词:定位夹紧机械夹具1 待加工零件此零件图如图1所示。
(1)零件图样分析①Φ9H7孔内的粗糙度Ra值为3.2mm。
②未注明倒角4×45°。
(2)工艺分析①在安排加工工序时,应将粗、精加工分开,以减少切削应力对加工精度的影响。
②在加工Φ9H7孔时,需要设计专用夹具。
③Φ9H7孔有一定的尺寸精度要求,其中心线距Φ10H7的中心平面的距离为40;与R16半圆同心。
利用钻模板保证这2个尺寸。
④根据图纸分析Φ9H7孔尺寸40的工序基准为Φ10H7的中心平面。
⑤加工孔时注意使用切削液保证转头不产生断裂和切削的排放。
2 设计钻模可换钻套(GB/T2268-91)如图2所示,支架是单一钻孔,大批量生产,为了更好的便于更换磨损的钻套,需要要可换钻套,钻套与套筒之间采用F7/m6或F7/k6配合,套筒与钻你、模板之间采用H7/n6配合。
当钻套磨损后,可卸下螺钉,更换新的钻套。
螺钉能防止钻套加工时的转动及退刀时的脱出。
一般钻套导向的基本尺寸取刀具的最大极限尺寸,钻孔时其公差取F7或F8。
若被加工孔维基准孔时,钻套导向孔的基本尺寸可取被加工孔的基本尺寸,钻孔时其公差取F7或F8。
若刀具用圆柱部分导向时,可采用H7/f7(g6)配合。
钻套的高度H增大,则导向性能好,刀具刚度提高,加工精度高,但钻套与刀具的磨损加剧。
取H=1~2.5d。
排屑空间h指钻套底部于工件表面之间的空间。
增大h值,排屑方便,但刀具的刚度和孔的加工精度都会降低。
钻削易排屑的铸铁时,取h=(0.3~0.7)d;钻屑较难排屑的刚件时,取h=(0.7~1.5)d。
穿越花键孔的细长孔钻模设计

影 响切屑形 状 的 因 素有 工 件 材料 、刀 片 、切 削速 度 、 给量 和切削液 。刀片和切削液前 面已经进行合理 进
的选择 ,而工件材料无法改变只有在切 削速度和进给 量
图4 喷吸钻系统
1 卡盘 2 工件 3 . . .中心 架 4 导 向套 . 5 钻管 .外
上考虑如何合理地断屑。根据实际加工 情况 的不 同,切
( )钻模板与夹具体合件的装配用找正心轴 ( 图 5 见 6 )从下部定位心轴 .m b 3 m钻头 ( )孔插入 , 插 套 再
入钻模板 4 . ml钻头 ( )孔 ,找正位置后 ,用螺 钉 ,2i 6 l 套 紧固。零件磨损更换 、定期检查 夹具精度 ,都 可 以用 找
正心轴调整检查 。
夹具 的具体结构和特点分 析如 下:
( )定位心轴 ( 图 3 与工 件 以渐 开线 花键 定 1 见 ) 位 ,同时起到间 隔孔 钻加 工 中常 用 的中间钻模 板作 用。
图 1 双联滑移齿轮
由于采用 了双层钻模板 ,钻削时有 了双 重导 向,能够有
1 零件加工工艺性分析 .
( )双联滑移齿轮 2个 ( m 1 h m、深 6 . 5l , 中 6 12 rm孔 l
由于喷吸钻是 内排屑深孔钻 ,因此在钻削 时最 主要 是如 何使切屑顺利地从内钻管排 出。切屑过长或过大都
2 1 年第 1 00 9期
WWW.7et wor i g 7 50 COr / al 1 k n 9 . n
参磊 工冷 工 加
形位公差 ,具体要求见夹具体合件 图 ( 见图 5 。 )
≯. 1 6 f_5 38 0
8
() b
图 3 定位心轴
( )夹具体 ( 图 4 花键孔采用 线切割 加工 ,以 2 见 )
钻模套原设计

圆定钻模套 的外 圆直径配合 一般选用 以 H7 6或 / n H/ 7 6的配合直接压人钻模板 或夹具体 ; r 可换钻模套 的 外 圆直径 与衬 套常采用 F/6或 F/6而衬套与钻模 7 m T , k 板常采用 H / ; 7n 快换钻模套 的外 圆直径与衬 套常采用 6 F16 F/ , 7 或 7 6而衬套与钻模板常采用 H .6 m k Tn 的配合 。 t
2 钻模套 的主 要参数 钻模套 的主要参数包括钻模套 的外 圆直径 和配合
0 ), .d 加工钢件时 (. 1 )。 7 07 .a 材料越硬 , -5 系数取小值 ,
加工小孔 系数应取大值 。孔的位置精度要求高时 , 不论 钻削铸铁 、 钢或青 铜 , 可允许 h 0钻深孔 ( i> 时要 =; Ld5) 求排屑畅快 , ^一般取 1 ; .d 在斜 面上钻 孔时 h尽量取 5 小些 一般取 ^ .; ≤O5 也可根 据实际情况按 实物配磨钻
1 前 言
文献标识码 : B
文章编号 :0 2 2 3 ( 0 2) 3 0 5 - 2 10 - 3 3 2 0 0 — 0 5 0
在机床夹具设计过程 中 , 特别是钻床夹具设计 中 ,
以上 的孔或 加工 工件 孔 距精 度 要 求在 ± ~ n 5m n1 ± 1 m 时, 钻模 套 的高度 = 25 35) 。加 工孔距 精 度在 ( .~ . d
模套 。 3 钻模 套的结构型式 3 . 固定 钻 模 套 j 这种钻模套有两种 型式 , 即无肩 和带肩 , 一般常用
公差 、 钻模套的高度 、 钻模套至被加工件端面的距离等。
2 钻模 套 的 内径 尺 寸 及 公 差 . j
钻模套 内径的公称尺寸 d 应为所用刀具 的最大极 ,
- 1、下载文档前请自行甄别文档内容的完整性,平台不提供额外的编辑、内容补充、找答案等附加服务。
- 2、"仅部分预览"的文档,不可在线预览部分如存在完整性等问题,可反馈申请退款(可完整预览的文档不适用该条件!)。
- 3、如文档侵犯您的权益,请联系客服反馈,我们会尽快为您处理(人工客服工作时间:9:00-18:30)。
目录第一章实体建模 (2)1.1底座 (2)1.2钻模座 (4)1.3开口垫圈 (6)第二章创建钻模的装配 (8)2.1建模操作步骤 (8)第三章钻模的工程图 (12)第四章零件加工 (14)4.1使用CAM软件,加工零件“钻模座”: (14)4.2刀具参数和加工工艺: (17)4.3用手工编程,编制衬套: (18)第五章软件仿真 (20)结论 (23)致谢 (24)参考文献 (25)第一章实体建模1.1底座如图1-1所示:图1-1 底座实体图1.1.1方案分析:固定钳身整体是一种不规则结构,因此需要通过回转操作创建其主体特征。
主体结构上面的两处孔,可以通过打孔操作创建,中部的内腔是圆,可以通过拉伸作布尔求差运算得到。
在UG NX4设计过程中,可以按照以下设计思路创建固定底座:(1) 创建草图截面曲线,回转得到主体特征结构。
(2) 创建草图截面曲线,拉伸作布尔求差运算得到内腔结构。
(3) 利用孔操作,创建主体顶部特征结构。
(4) 进行边倒圆操作。
1.1.2建模操作步骤:1.利用草图功能,创建草图截面曲线,其操作如图1-1201所示:图1-1201 草图2.利用回转功能,创建底座主体特征结构,其操作如图1-1202所示:图1-12023.利用草图功能,创建腔体截面曲线(左图所示),再利用拉伸功能并进行布尔求差运算(右图所示),得到腔体结构,其操作如图1-1203所示:图1-12034.利用孔功能,对底座主体进行打孔(如下图所示),其操作如图1-1204所示:图1-12045.利用边圆角功能,对腔体进行倒角,倒角为R2,其操作如图1-1205所示:图1-12051.2钻模座如图1-2所示:图1-2 钻模座实体1.2.1方案分析:钻模座整体结构较为规则,因此可以通过曲线拉伸操作创建其主体特征。
主体结构上的其他孔结构,可以通过孔功能创建。
在UG NX4设计过程中可以按以下设计思路创建活动钳口:(1)创建草图截面曲线,拉伸得到主体特征结构。
(2)进行边倒圆操作。
(3)利用孔操作工能,创建孔结构。
1.2.2建模操作步骤:1.创建一个新文件,进入建模功能。
利用草图功能,创建草图截面曲线,其操作如图1-221所示:图1-221 草图2.利用拉伸功能,对草图曲线进行拉伸操作,其操作如图1-222所示:图1-2223.利用倒圆角功能,对模型进行倒角,半径为R3,并利用孔的功能,在模型上表面创建孔,并将其定位在圆边的中心位置,其操作如图1-225所示:图1-2231.3开口垫圈如图1-3所示:图1-3 开口垫圈实体1.3.1方案分析:开口垫圈整体结构较为规则,因此可以通过曲线拉伸操作创建其主体特征。
主体结构上的其他结构,可以通过草图和拉伸作布尔求差运算功能创建。
主体一圈的滚花可以利用沿导引线扫掠和关联复制功能创建。
在UG NX4设计过程中可以按以下设计思路创建开口垫片:(1)创建草图曲线,拉伸得到主体特征结构。
(2)利用倒斜角功能进行倒角。
(3)利用沿导引线扫掠和关联复制制作滚花。
(4)创建草图曲线,利用拉伸作布尔求差运算功能完成建模。
1.4.2建模操作步骤:1.创建一个新文件,进入建模功能。
利用草图功能,创建草图平面,在创建草图曲线,拉伸得到主体结构,其操作示意图如图1-321所示:图1-321 草图2. 利用倒斜角操作功能,对草图曲线进行倒角操作,倒角为2,其操作示意图如图1-322所示:图1-322 倒角3.利用沿导引线扫掠和关联复制制作滚花,其操作示意图如图1-323所示:图1-323 滚花效果4.利用草图功能,创建草图平面,在创建草图曲线,其操作示意图如图1-324所示:图1-324 草图5.利用拉伸作布尔求差运算功能,完成建模,操作示意图如图1-325所示:图1-325 拉伸第二章创建钻模的装配2.1 建模操作步骤2.1.1 固定钳身子装配1. 打开UG,新建一个装配文件,点击出现如图对话框按导入部件1,如图2-111所示。
添加组件对话框部件1图2-111 添加组件2. 导入部件4利用配对操作功能(如图),应用配对操作类型,将部件4装配到部件1上其操作示意图如图2-112所示。
添加组件1放置定位添加组件4配对操作图2-112 装配3. 应用配对操作,完成固定的底座和轴的装配。
如图2-113所示:装配效果图2-113 装配4.导入部件2,利用配对操作功能,将部件3装配到部件2上,距离为3,如图2-114 所示。
部件2 装配效果图2-114 添加组件与装配5.导入部件3钻套,利用配对操作功能,分别利用和配对操作类型,对部件3进行装配操作。
如图2-115 所示:部件3 装配效果图2-115 添加组件与装配6. 导入部件6衬套。
利用配对操作功能,分别利用和配对操作类型,对部件6进行装配操作。
如图2-117所示:部件6 装配效果图2-116 添加组件与装配7. 导入部件7销,利用配对操作功能,分别利用和配对操作类型,对部件7进行装配操作,效果如图2-118所示。
部件7装配效果图2-117 添加组件与装配8. 导入部件3开口垫圈。
利用配对操作功能,分别利用和配对操作类型,对进行部件3装配操作,如图2-118所示:部件3 装配效果图2-118 添加组件与装配9. 导入部件8特制螺母。
利用配对操作功能,分别利用和配对操作类型,对进行部件3装配操作,效果如图2-119所示。
部件8装配效果图2-119 添加组件与装配10. 导入部件9螺母M16。
利用配对操作功能,分别利用和配对操作类型,对进行部件3装配操作,效果图2-120所示:部件9 装配效果图2-120 添加组件与装配钻模装配全部完成。
第三章钻模的工程图1.底座工程图如图3-1所示:图3-1 底座工程图2.钻模座工程图如图3-2所示:图3-2 钻模座工程图3.开口垫圈工程图如图3-3所示:4.装配图工程图如图3-4所示:第四章零件加工4.1使用MasterCam软件,加工零件“钻摸座”,其步骤如下:1.外形铣削,画实体图建立毛坯,毛坯大于工件尺寸,如图4-11所示:图4-11 草图生成实体2.在相对应的加工创建的菜单中(如图4-121),选择选择适合的菜单,创建刀具,设置参数,如图4-122所示;创建操作,如图4-123所示:图4-121 选择加工方式图4-122 选择刀具图4-123 设置参数3.进行刀路模拟,如图4-131所示:图4-131 刀路模拟4.挖槽加工,设置参数,刀路模拟,如图4-141 4-142所示:图4-141设置参数图4-142 刀路模拟5.进行打孔,注意打孔时应使用中心钻等刀具,具体如图4-151 4-152 4-153所示:图4-151 中心钻刀路模拟图4-152 钻孔刀路模拟图4-153 铰刀刀路模拟6.对曲面进行加工,创建刀具,设置参数,模拟刀路,如图4-161 4-162所示:图4-161 刀路模拟图4-162 设置参数7起初是粗加工,之后进行零件的半精加工和精加工,步骤与上面讲的类似,故不一一列出。
当所有的加工步骤全部完成后,可进行后处理的工作,导出程序,如图4-17:图4-17 导出程序8.出的程序,另存为记事本格式,见附录1.4.2刀具参数和加工工艺(如表4-21 4-22)表4-21刀具参数列表(如表4-3)表4-22加工工艺表4.3手动编程,编制“衬套”(如图4-3),程序如下。
图4-3 衬套实体图手工编制程序:O0001M03 S800T0101GO0 X40 Z2G71 P1 Q2 U0.5 W0 F0.25 N1 G01 X38 F0.1Z0Z-20N2 GO1 X40G00 X100 Z100M01M03 S900T0101G00 X40 Z2G70 P1 Q2G00 X100 Z100M01M03 S800T0303G00 X13.5 Z2G71 U1 R0.5 G71 P3 Q4 U-0.4 W0 F0.1 N3 G01 X32Z0Z-20N4 X13.5G00 X100 Z100M01M03 S99T0303G00 X13.5 Z2G70 P3 Q4G00 X100 Z100M01MO3 S500T0404GOO X40 Z-22G01 X30 F0.1X42 F0.8G00 X100 Z100M30第五部分软件仿真1.选择机床,利用左上角菜单,选择所需的机床,如图5-1所示:图5-1 选择机床2.定义毛坯,利用左上角菜单,选择定义所需毛坯(毛坯尺寸:X130 Y130 Z30),如图5-2所示:3.选择夹具,利用左上角菜单,根据材料及工件所需选择加至的尺寸,及其他所需,如图5-3所示:图5-3 设置夹具4.选择好毛坯后,利用左上角菜单,选择零件后安装零件,如图5-4所示:图5-4 安装零件5.选择刀具,利用左上角菜单,选择加工所需刀具,可选择多把不同刀具放至刀库中,以便在半精加工和精加工时,快速换刀,如图5-5所示:图5-5 添加刀具6. 利用回零按钮使X,Y,Z轴回至零点,当出现时,说明回零完成,NC屏幕如图5-6所示:图5-6 回零7.更换所需的刀具,首先切换方式至MDI,后输入刀具号,后按执行按钮即可完成换刀动作,完成后如图5-7所示:图5-7 输入刀具号8.导入程序,在编辑状态下,程序显示下,在NC上翻页至,后打开所需程序(格式必须为记事本),后选择,输入程序号O0001,后按,即完成导程动作,NC屏幕如图5-8所示:图5-8 输入程序9.修改刀具补正,NC屏幕如图5-9所示:图5-9 修改刀具补正10.选择自动执行按钮及循环启动按钮,至此,完成所有仿真动作如图5-10所示。
图5-10 完成仿真结论实训马上就要结束了,说实话在这三周的综合实训中我们学到的东西要比一学期学到的东西还要多。
我们从拿到图纸加工零件到最后的答辩都付出了不少代价,有酸有甜。
我们各自都遇到了不同的问题,也由此看到了自己身上的许多不足和需要改进的地方。
当与他人合作完成工作时,要配合其他人的脚步一起行动。
这也告诉我们,不论我们目前的自身情况如何。
我们必须团结协作,共同进退,互相帮助。
实训设计也是对自己本身的一次考验,通过这次实训,我感觉自己的学习、处事能力得到了很大的提高。
完成设计的阶段也是值得永远留念的,这是我们学校生涯的最后一步,其中包含的不仅仅是一篇文章,更是我们这两年来学习的一次总结。
致谢经过三周的综合实训,论文设计已经接近尾声。
再次三周的综合实训中,仅凭我个人之力是很难完成平口钳的加工过程的编写的,所以在此要感谢三位老师的悉心教导,感谢同组一起工作的同学们的合作,正是由于大家的努力才使我成功完成了此次综合实训的内容,再次深表感谢。
由于经验的匮乏,学习知识的不足,实践能力的欠缺,本次实训的内容难免有许多考虑不周全的地方。