Vehicle Applications of Controller Area Network
FSAC赛车整车控制器硬件设计

AUTOMOBILE DESIGN | 汽车设计FSAC 赛车整车控制器硬件设计廖兴华 甘桦福柳州铁道职业技术学院 广西柳州市 545000摘 要: 本文针对FSAC(中国大学生无人驾驶方程式大赛)赛车在赛场等特定场景下比赛设计了一款整车控制器。
旨在保障赛车能圆满完成比赛任务。
通过对控制需求分析设计了电源电路、输入输出接口、驱动芯片电路等,设计的整车控制器最后进行实车验证。
结果表明,所设计的控制器具有良好的稳定性,可靠性,满足比赛要求。
关键词:FSAC 无人车 整车控制器1 引言在疫情期间,以无人车开展无人快递、无人配送发挥了重要的作用。
加上今年政府工作报告明确提出2030年实现碳达峰,2060年实现碳中和的具体时间要求[1]。
无人车的研发越来越受到相关企业和研究机构的重视,无人车大多是在新能源汽车基础上改造而来,对减少环境污染带来积极促进作用。
作为无人车中核心关键零部件的整车控制器的开发也成为关注的重点。
2 FSAC 赛车架构FSAC(中国大学生无人驾驶方程式大赛)由中国汽车工程学会从2017年开始举办,由于疫情影响至今举办了3届。
FSAC 赛车是由各高校大学生自行设计、制造、开发完成需满足大赛规则的赛车。
[2]-[3]。
目的是让学生理论联系实际,全方位锻炼学生能力。
2.1 FSAC 赛车系统组成FSAC 赛车包括感知系统、决策控制系统、底层控制系统三部分组成,如图1所示。
感知系统包括摄像头、激光雷达、GPS。
感知系统和决策系统之间通过串口通信。
决策系统与底层控制系统之间通过CAN 总线通讯[3]。
底层控制系统实现车辆线控转向、线控驱动和线控制动。
2.2 FSAC 赛车整车控制器设计赛车整车控制器的硬件设计根据大赛规则和控制需求包括电源模块设计、输入输出接口设计、驱动电路设计、CAN 总线通讯设计等。
设计的目标是能实现车辆的数据采集,对数据进行处理,输出控制信号实现车辆线控驱动、线控制动和线控转向[4]-[5]。
城市轨道交通术语翻译

The following section is a collection of terms used in the manual手册,说明书. Sources and references are identified for those terms with multiple definitions多重定义.Accident modification factorsA means of quantifying crash reductions associated with safety improvements.Actuated开动,驱使Signal ControlPhase time based on detection data.Adaptive Signal Control A signal control concept where vehicular traffic in a network is detected at a point upstream and/or downstream and an algorithm is used to predict when and where traffic will be and to make signal adjustments at downstream intersections based on those predictions.Added Initial An interval that times concurrently with the minimum green interval and increases by each vehicle actuation received during the initial period. This time cannot exceed the maximum initial.Analysis period A single time period during which capacity analysis is performed on a transportation facility. If the demand exceeds capacity during an analysis period, consecutive analysis periods can be selected to account for initial queue from the previous analysis period. Also referred to as time interval.Analytical Model A model that relates system components using theoretical理论considerations tempered调节的、缓和的、适中的, validated证实、生效, and calibrated标刻度by field data.Annual average daily traffic The total volume of traffic passing a point or segment of a highway facility in both directions for one year divided by the number of days in the year.Approach A set of lanes at an intersection横断、交叉、十字that accommodates容纳、调节all left-turn, through, and right-turn movements from a given direction.Approach grade引导坡度The grade of an intersection approach, expressed as a percentage, with positive values for upgrade and negative for downgrade.Area type A geographic parameter因素、参数reflecting the variation of saturation浸湿,饱和flows in different areas.Arrival rate The mean of a statistical统计的distribution of vehicles arriving at a point or uniform 校服、一律、一致、统一segment of a lane or roadway.Arrival type Six assigned categories生物类别for determining the quality of progression发展、一系列at a signalized intersection.Arterial动脉的A signalized street that primarily主要、首要serves through traffic and that secondarily provides access to abutting邻接、毗连properties, with signal spacing间隔、间距of 2.0 miles or less.Arterial LOS An arterial- and network-level performance measure associated with the class of arterial and the travel speed of arterial under study.Automatic Vehicle Location (AVL) System An intelligent transportation system (ITS) technology to track vehicle location, speed and other measures within a system. Most applications are found on transit vehicles and systems.Average Speed The average distance a vehicle travels within a measured amount of time.Average travel speed The length of the highway segment divided by the average travel time of all vehicles traversing the segment, including all stopped delay times.Back of queue The distance between the stop line of a signalized intersection and the farthest reach of an upstream queue, expressed as a number of vehicles. The vehicles previously stopped at the front of the queue are counted even if they begin moving.Bandwidth The maximum amount of green time for a designated direction as it passes through a corridor at an assumed constant speed, typically measured in seconds.Bandwidth attainability A measure of how well the bandwidth makes use of the available green time for the coordinated movements at the most critical intersection in the corridor.Bandwidth efficiency A measure that normalizes bandwidth against the cycle length for the arterial under study.Barnes’ Dance A common term for an exclusive pedestrian phase where pedestrians may cross all intersections legs and sometimes diagonally.Barrier A separation of intersecting movements in separate rings to prevent operating conflicting phases at the same time.Base condition The best possible characteristic in terms of capacity for a given type of transportation facility; that is, further improvements would not increase capacity; a condition without hindrances or delays.Base saturation flow rate The maximum steady flow rate—expressed in passenger cars per hour per lane—at which previously stopped passenger cars can cross the stop line of a signalizedintersection under base conditions, assuming that the green signal is available and no lost times are experienced.Call A term used to describe the presence of vehicle, bicycle, or pedestrian demand in an actuated detection controller system.Capacity The maximum rate at which vehicles can pass through the intersection under prevailing conditions. It is also the ratio of time during which vehicles may enter the intersection.Carryover A term commonly used for the “extend” setting in controller manuals. It is another way to describe the time provided for a vehicle to traverse from one detector to the next.Change interval The yellow plus red clearance interval that occurs between phases of a traffic signal to provide for clearance of the intersection before conflicting movements are released. Also known as the clearance interval.Clearance lost time The time, in seconds, between signal phases during which an intersection is not used by any traffic.Clearance time The time loss at a transit stop, not including passenger dwell times. This parameter can be the minimum time between one transit vehicle leaving a stop and the following vehicle entering and can include any delay waiting for a sufficient gap in traffic to allow the transit vehicle to reenter the travel lane.Condition Diagram An illustration used to highlight the existing characteristics (i.e., number of lanes, signs, adjacent driveways, turn-bay lengths, traffic control, and land uses) of an intersection.Concurrent Phases Two or more phases in separate rings that are able to operate together without conflicting movements.Congested flow A traffic flow condition caused by a downstream bottleneck.Control Delay The amount of additional travel time experienced by a user attributable to a control device.Controller Memory A term that refers to the controller’s ability to “remember” (i.e., retain) a detector actuation and includes one of two modes (nonlocking or locking).Coordinated-Actuated Signal operations in coordination with other intersections, and using vehicle, bicycle, and/or pedestrian detection to define signal timing.Coordinated Phase(s) The phase (or phases) that is provided a fixed minimum amount of time each cycle under a coordinated timing plan. This phase is typically the major through phase on anarterial.Coordination The ability to synchronize multiple intersections to enhance the operation of one or more directional movements in a system.Corridor A set of essentially parallel transportation facilities designed for travel between two points. A corridor contains several subsystems, such as freeways, rural (or two-lane) highways, arterials, transit, and pedestrian and bicycle facilities.Critical lane group The lane groups that have the highest flow ratio for a given signal phase.Critical movement analysis A simplified technique for estimating phasing needs and signal timing parameters.Critical speed The speed at which capacity occurs for a facility, usually expressed as miles per hour.Critical volume-to-capacity ratio The proportion of available intersection capacity used by vehicles in critical lane groups.Crosswalk A marked area for pedestrians crossing the street at an intersection or designated midblock location.Cycle A complete sequence of signal indications.Cycle Length The time required for a complete sequence of signal indications.Cycle Failure Occasion where all queued vehicular demand cannot be served by a single green indication or signal phase.Dallas Display A type of signal display that attempts to avoid “yellow trap” problem by using louvers on the yellow and green ball indications to restrict visibility of the left-turn display to adjacent lanes while displaying indications based on the opposing through movement.Delay The additional travel time experienced by a driver, passenger, or pedestrian.A detector parameter typically used with stop-line, presence mode detection for turn movements from exclusive lanesDensity The number of vehicles on a roadway segment averaged over space, usually expressed as vehicles per mile or vehicles per mile per lane. (see also: volume-density, sometimes referred to as density timing)Demand The volume of traffic at an intersection, approach, or movement.Detector A device used to count and/or determine the presence of a vehicle, bicycle, or pedestrian.Dilemma Zone There are two types of dilemma zones.Type I occurs when yellow and red clearance times are too short for a driver to either stop or clear the intersection before the beginning of a conflicting phase.Type II, also known as an “Option Zone”, ore “Indecision Zone”. This occurs as the result of different drivers making different decision on whether to go or stop, upon the change from a green to yellow indication.Double Cycle A cycle length that allows phases to be serviced twice as often as the other intersections in the coordinated system.Downstream The direction of traffic flow.Early Return to Green A term used to describe the servicing of a coordinated phase in advance of its programmed begin time as a result of unused time from non-coordinated phases.Effective green time The time during which a given traffic movement or set of movements may proceed; it is equal to the cycle length minus the effective red time.Effective red time The time during which a given traffic movement or set of movements is directed to stop; it is equal to the cycle length minus the effective green time.Effective walkway width The width, in feet, of a walkway usable by pedestrians, or the total walkway width minus the width of unusable buffer zones along the curb and building line.Exclusive pedestrian phase An additional phase that is configured such that no vehicular movements are served concurrently with pedestrian traffic. See also, Barnes Dance.Exclusive turn laneA designated left- or right-turn lane or lanes used only by vehicles making those turns.Extend A detector parameter that extends a detector actuation by a setable fixed amount. It is typically used with detection designs that combine multiple advance detectors and stop-line detection for safe phase termination of high-speed intersection approaches.Field Implementation A term used to describe the installation of new signal timings in the controller and the review of traffic operations at the intersection.Fixed Force Off A force off mode where force off points cannot move. Under this mode,non-coordinated phases can utilize unused time of previous phases.Fixed Time Signal Control A preset time is given to each movement every cycle regardless of changes in traffic conditions.Flashing Don’t Walk An indication warning pedestrians that the walk indication has ended and the don’t walk indication will begin at the end of the pedestrian clearance interval.Flashing Yellow Arrow A type of signal head display that attempts to avoid the “yellow trap” problem by providing a permissive indication to the driver that operates concurrent with the opposing through movement rather than the adjacent through movement.Floating Force Off A force off mode where force off points can move depending on the demand of previous phases. Under this mode, non-coordinated phase times are limited to their defined split amount of time and all unused time is dedicated to the coordinated phase. Essentially, the split time is treated as a maximum amount for the non-coordinated phases.Floating car method A commonly employed technique for travel time runs which requires the vehicle driver to “float” with the tra ffic stream while traveling at a speed that is representative of the other vehicles on the roadway and to pass as many vehicles as pass the floating car.Flow rate The equivalent hourly rate at which vehicles, bicycles, or persons pass a point on a lane, roadway, or other trafficway; computed as the number of vehicles, bicycles, or persons passing the point, divided by the time interval (usually less than 1 h) in which they pass; expressed as vehicles, bicycles, or persons per hour.Flow ratio The ratio of the actual flow rate to the saturation flow rate for a lane group at an intersection.Force Off A point within a cycle where a phase must end regardless of continued demand. These points in a coordinated cycle ensure that the coordinated phase returns in time to maintain its designated offset.Free flowA flow of traffic unaffected by upstream or downstream conditions.Fully actuated control A signal operation in which vehicle detectors at each approach to the intersection control the occurrence and length of every phase.Gap The time, in seconds, for the front bumper of the second of two successive vehicles to reach the starting point of the front bumper of the first.Gap ReductionThis is a feature that reduces the passage time to a smaller value while the phase is active.Green time The duration, in seconds, of the green indication for a given movement at a signalized intersection.Green time ratioThe ratio of the effective green time of a phase to the cycle length.Green Extension A signal priority treatment to extend a current green phase to give priority to a specific movement or vehicle, typically transit.Hardware The devices that physically operate the signal timing controls, including the controller, detectors, signal heads, and conflict monitor.Headway(1)The time, in seconds, between two successive vehicles as they pass a point on the roadway, measured from the same common feature of both vehicles (for example, the front axle or the front bumper);(2)The time, usually expressed in minutes, between the passing of the front ends of successive transit units (vehicles or trains) moving along the same lane or track (or other guideway) in the same direction.Hardware in the Loop (HITL) A means of providing a direct linkage between simulation models and actual signal controllers.Highway Capacity Manual A National Academies of Science/Transportation Research Board manual containing a collection of state-of-the-art techniques for estimating the capacity and determining the level-of-service for transportation facilities, including intersections and roadways as well as facilities for transit, bicycles, and pedestrians.Inhibit Max A basic timing parameter that removes the Maximum Green input as a phase parameter during coordination and allows the phase to extend beyond its normal maximum green values.Interval The duration of time where a traffic signal indications do not change state (red, yellow, green, flashing don’t walk). A traffic signal controller also has timi ng intervals (min green, passage time) that determine the length of the green interval.Intersection Delay - Average The total additional travel time experienced by users as a result ofcontrol measures and interactions with other users divided by the volume departing from the intersection.Intersection Level of Service A qualitative measure describing operational conditions based on average intersection delay.Isolated intersectionAn intersection at least one mile from the nearest upstream signalized intersection.Lagging pedestrian interval A pedestrian timing option that starts pedestrian walk interval several seconds after the adjacent through movement phase, thus allowing a waiting right-turn queue to clear before the pedestrian walk indication is presented and thereby reducing conflicts with right-turning vehicles.Lane group A set of lanes established at an intersection approach for separate capacity and level-ofservice analysis.Lane group delayThe control delay for a given lane group.Lane utilization The distribution of vehicles among lanes when two or more lanes are available for a movement; however, as demand approaches capacity, uniform lane utilization develops.Leading pedestrian interval A pedestrian interval option that starts a few seconds before the adjacent through movement phase, thus allowing pedestrians to establish a presence in the crosswalk and thereby reducing conflicts with turning vehicles.Lead-Lag Left-Turn Phasing A left-turn phase sequence where one left-turn movement begins with the adjacent through movement and the opposing left-turn movement begins at the end of the conflicting through movement. This option may create a “yellow trap” with some permissive signal displays.Level of service A qualitative measure describing operational conditions within a traffic stream, based on service measures such as speed and travel time, freedom to maneuver, traffic interruptions, comfort, and convenience.Local Controller The device used to operate and control the signal displays using signal timing provided by the user, master controller, or central signal system.Locking mode A controller memory mode used to trigger a call for service for the first actuation received by the controller on a specified channel during the red intervalLost Time The portion of time at the beginning of each green period and a portion of each yellow change plus red clearance period that is not usable by vehicles.Master Clock The background timing mechanism within the controller logic to which each controller is .referenced during coordinated operations.Master Controller An optional component of a signal system that facilitates coordination of a signal system with the local controller.Manual on Traffic Control Devices (MUTCD)The MUTCD, published by the Federal Highway Administration, provides the standards and guidance for installation and maintenance for traffic control devices on roadways.Maximum Allowable Headway (MAH) / Maximum Time Separation The maximum time separation between vehicle calls on an approach without gapping out the phase, typically defined by passage time or gap time. Maximum allowable headway refers to spacing between common points of vehicles in a single lane, but the term is commonly used to refer to maximum time separation in single or multi-lane approaches as well.Maximum Green The maximum length of time that a phase can be green in the presence of a conflicting call.Maximum Initial The maximum period of time for which the Added Initial can extend the initial green period. This cannot be less than the Minimum Green time.Maximum RecallA recall mode that places a continuous call on a phase.Measure of effectivenessA quantitative parameter indicating the performance of a transportation facility or service.Minimum Gap This volume density parameter that specifies the minimum green extension when gap reduction is used..Minimum Green The first timed portion of the green interval which may be set in consideration driver expectany and the storage of vehicles between the detectors and the stop line when volume density or presence detection is not used.Minimum Recall A recall parameter the phase is timed for its minimum green time regardless what the demand is for the movement.Movement A term used to describe the user type (vehicle or pedestrian) and action (turningmovement) taken at an intersection. Two different types of movements include those that have the right of way and those that must yield consistent with the rules of the road or the Uniform Vehicle Code.Non-locking mode A controller memory mode that does not retain an actuation received from a detector by the controller after the actuation is dropped by the detection unit.OccupancyThe percent of time that a detector indicates a vehicle is present over a total time period.Offset The time relationship between coordinated phases defined reference point and a defined master reference (master clock or sync pulse).Offset Reference Point (Coordination Point)The defined point that creates an association between a signalized intersection and the master clock.Overflow queueQueued vehicles left over from a green phase at a signalized intersection.OversaturationA traffic condition in which the arrival flow rate exceeds capacity.Passage Time (Vehicle Interval, Gap, Passage Gap, Unit Extension) A phase timer that ends a phase when the time from the last detector output exceeds the timer setting.Pattern Sync ReferenceThe set start of the master clock.Peak-hour factor The hourly volume during the maximum-volume hour of the day divided by four times the peak 15-min flow rate within the peak hour; a measure of traffic demand fluctuation within the peak hour.PedestrianAn individual traveling on foot.Pedestrian Recall A recall mode where there is a continuous call for pedestrian service resulting in the pedestrian walk and clearance phases to occur each time the phase times.Pedestrian Clearance Interval Also known as “Flash Don’t Walk”. The time prov ided for apedestrian to cross the entire width of the intersection.Pedestrian PhaseTime allocated to pedestrian traffic that may be concurrent with vehicular phases.Pedestrian scrambleSee Exclusive Pedestrian PhasePedestrian Walk IntervalAn indication to the pedestrian that it allows pedestrians to begin crossing the intersection.Pedestrian walking speedThe average walking speed of pedestrians, in feet per second.Percent Runs Stopped The percentage of the total number of travel time runs conducted during which a vehicle stops.Performance Index An arterial- and network-Level performance measure that allows several measures of effectiveness to be mathematically combined.Performance Measures Signal system related effects on stops, vehicle delay, arterial travel time, or existence of spill back queuing between closely spaced intersections.Permissive Movements A movement where it is allowed to proceed if there are available gaps in the conflicting flow.Permissive Period A period of time during the coordinated cycle in which calls on conflicting phases will be result in the coordinated phase transitioning to non-coordinated phase(s)..Permitted plus protected Compound left-turn protection that displays the permitted phase before the protected phase.Permitted turn Left or right turn at a signalized intersection that is made against an opposing or conflicting vehicular or pedestrian flow.Phase A controller timing unit associated with the control of one or more movements. The MUTCD defines a phase as the right-of-way, yellow change, and red clearance intervals in a cycle that are assigned to an independent traffic movement.Phasing Indication The current display for a given phase (green, yellow, red, walk, flashing don’twalk, or don’t walk).Phase Pair A combination of two phases allowed within the same ring and between the same barriers such as 1+2. 5+6, 3+4, and 7+8.Phase Recall A call is placed for a specified phase each time the controller is servicing a conflicting phase. This will ensure that the specified phase will be serviced again. Types of recall include soft, minimum, and maximum. Soft recall only calls the phase back if there is an absence of conflicting calls.Phase SequenceThe order of a series of phases.Phasing DiagramA graphical representation of a sequence of phases.Platoon A group of vehicles or pedestrians traveling together as a group, either voluntarily or involuntarily because of signal control, geometrics, or other factors.Preemption Traffic signal preemption is the transfer of normal operation of a traffic control signal to a special control mode of operation.Preempt Trap A condition that can occur when a preemption call is serviced at a signalized intersection near an at-grade train-roadway crossing, where not enough clearance green time is provided to clear a queue of vehicles, and a vehicle could be trapped on the tracks with the railroad crossing lights and gates come down.Presence Mode A detection mode where a signal is sent to the controller for the duration of time a vehicle is inside the detection zone.Pretimed control A signal control in which the cycle length, phase plan, and phase times are preset to repeat continuously.Priority Traffic signal priority (TSP) is an operational strategy communicated between transit vehicles and traffic signals to alter signal timing for the benefit or priority of transit vehicle. Green extension, red truncation, and phase skipping are examples of signal timing alterations under TSP.Progression adjustment factor A factor used to account for the effect of signal progression on traffic flow; applied only to uniform delay.Protected Movements A movement where it has the right-of-way and there are no conflicting movements occurring.Protected plus permitted Compound left-turn protection at a signalized intersection that displays the protected phase before the permitted phase.Protected turn The left or right turns at a signalized intersection that are made with no opposing or conflicting vehicular or pedestrian flow allowed.Pulse Mode A detection mode where vehicle detection is represented by a single “on” pulse to the controller.Queue A line of vehicles, bicycles, or persons waiting to be served by the system in which the flow rate from the front of the queue determines the average speed within the queue. Slowly moving vehicles or people joining the rear of the queue are usually considered part of the queue. The internal queue dynamics can involve starts and stops. A faster-moving line of vehicles is often referred to as a moving queue or a platoon.Queue discharge A flow with high density and low speed, in which queued vehicles start to disperse. Usually denoted as Level of Service F.Queue spillback A term used to describe vehicles stopped at an intersection that exceed the available storage capacity for a particular movement.Queue storage ratio The parameter that uses three parameters (back of queue, queued vehicle spacing, and available storage space) to determine if blockage will occur.Quick-Estimation Method A method detined in Chapter 10 of the HCM 2000 that allows an analyst to identify the critical movements at an intersection, estimate whether the intersection is operating below, near, at, or over capacity, and approximate the amount of green time needed for each critical movement.Red Change Interval The period of time following a yellow period indicating the end of a phase and stopping the flow of traffic.Red time The period, expressed in seconds, in the signal cycle during which, for a given phase or lane group, the signal is red.Red Truncation A signal priority treatment to terminate non-priority approach green phasing early in order to more quickly return to green for the priority approach. This treatment is also known as early return to green.RingAn phases that operate in sequence.Ring Barrier Diagram A graphical representation of phases within a set of rings and phases within a set of barriers.Saturation Flow Rate The equivalent hourly rate at which vehicles can traverse an intersection approach under prevailing conditions, assuming a constant green indication at all time and no loss time, in vehicles per hour or vehicles per hour per lane.Saturation headway The average headway between vehicles occurring after the fourth vehicle in the queue and continuing until the last vehicle in the initial queue clears the intersection.Section A group of signalized intersections used to analyze traffic operations, develop new signal timings, and operate in the same control mode—manual, time of day, or traffic responsiveSegment A portion of a facility on which a capacity analysis is performed; it is the basic unit for the analysis, a one-directional distance. A segment is defined by two endpoints.Semi-Actuated Control A type of signal control where detection is provided for the minor movements only and the signal timing returns to the major movement because it has no detection and is placed in recall.Signal HeadAn assembly of one or more signal indications.Signal Coordination An operational mode that synchronizes a series of traffic signals to enhance the operation of one or more directional movements.Signal Warrant A threshold condition to determine whether a traffic signal is justified based on satisfaction of an engineering study. There are eight warrants provided in the MUTCD.Signalization condition A phase diagram illustrating the phase plan, cycle length, green time, change interval, and clearance time interval of a signalized intersection.Simple left turn protection A signal phasing scheme that provides a single protected phase in each cycle for a left turn.Simultaneous GapThis parameter requires all phases to concurrently “gap out” prior to crossing the barr ier.Software in the loop (SITL) A means of providing a direct linkage between simulation models and software emulations of controllers,Speed。
汽车专业英文

Spin control for carsStability control systems are the latest in a string of technologies focusing on improved diriving safety. Such systems detect the initial phases of a skid and restore directional control in 40 milliseconds, seven times faster than the reaction time of the average human. They correct vehicle paths by adjusting engine torque or applying the left- or-right-side brakes, or both, as needed. The technology has already been applied to the Mercedes-Benz S600 coupe.Automatic stability systems can detect the onset of a skid and bring a fishtailing vehicle back on course even before its driver can react.Safety glass, seat belts, crumple zones, air bags, antilock brakes, traction control, and now stability control. The continuing progression of safety systems for cars has yielded yet another device designed to keep occupants from injury. Automatic stability systems can detect the onset of a skid and bring a fishtailing vehicle back on course even before its driver can react. Stability control systems help drivers recover from uncontrolled skids in curves, thus avoiding spinouts and accidents.Using computers and an array of sensors, a stability control system detects the onset of a skid and restores directional control more quickly than a human driver can. Every microsecond, the system takes a "snapshot," calculating whether a car is going exactly in the direction it is being steered. If there is the slightest difference between where the driver is steering and where the vehicle is going, the system corrects its path in a split-second by adjusting engine torque and/or applying the cat's left- or right-side brakes as needed. Typical reaction time is 40 milliseconds - seven times faster than that of the average human.A stability control system senses the driver's desired motion from the steering angle, the accelerator pedal position, and the brake pressure while determining the vehicle's actual motion from the yaw rate (vehicle rotation about its vertical axis) and lateral acceleration, explained Anton van Zanten, project leader of the Robert Bosch engineering team. Van Zanten's group and a team of engineers from Mercedes-Benz, led by project manager Armin Muller, developed the first fully effective stability control system, which regulates engine torque and wheel brake pressures using traction control components to minimize the difference between the desired and actual motion.Automotive safety experts believe that stability control systems will reduce the number of accidents, or at least the severity of damage. Safety statistics say that most of the deadly accidents in which a single car spins out (accounting for four percent of all deadly collisions) could be avoided using the new technology. The additional cost of the new systems are on the order of the increasingly popular antilock brake/traction control units now available for cars.The debut of stability control technology took place in Europe on the Mercedes-Benz S600 coupe this spring. Developed jointly during the past few years by Robert Bosch GmbH and Mercedes-Benz AG, both of Stuttgart, Germany, Vehicle Dynamics Control (VDC). in Bosch terminology, or the Electronic Stability Program (ESP), as Mercedes calls it, maintains vehicle stability in most driving situations. Bosch developed the system, and Mercedes-Benz integrated it into the vehicle. Mercedes engineers used the state-of-the-art Daimler-Benz virtual-reality driving simulator in Berlin to evaluate the system under extreme conditions, such as strong crosswinds. They then put the system through its paces on the slick ice of Lake Hornavan near Arjeplog, Sweden. Work is currently under way to adapt the technology to buses and large trucks, to avoidjack-knifing, for example.Stability control systems will first appear in mid-1995 on some European S-Class models and will reach the U.S. market during the 1996 model year (November 1995 introduction). It will be available as a $750 option on Mercedes models with V8 engines, and the following year it will be a $2400 option on six-cylinder $1650 of the latter price is for the traction control system, a prerequisite for stability control.Bosch is not alone in developing such a safety system. ITT Automotive of Auburn Hills, Mich., introduced its Automotive Stability Management System (ASMS) in January at the 1995 North American International Auto Show in Detroit. "ASMS is a quantum leap in the evolution of antilock brake systems, combining the best attributes of ABS and traction control into a total vehicle dynamics management system," said Timothy D. Leuliette, ITT Automotive's president and chief executive officer."ASMS monitors what the vehicle controls indicate should be happening, compares that to what is actually happening, then works to compensate for the difference," said Johannes Graber, ASMS program manager at ITT Automotive Europe. ITT's system should begin appearing on vehicles worldwide near the end of the decade, according to Tom Mathues, director of engineering of Brake & Chassis Systems at ITT Automotive North America. Company engineers are now adapting the system to specific car models from six original equipment manufacturers. Company engineers are now adapting the system to specific car models from six original equipment manufacturers.A less-sophisticated and less-effective Bosch stability control system already appears on the 1995 750iL and 850Ci V-12 models from Munich-based BMW AG. The BMW Dynamic Stability Control (DSC) system uses the same wheel-speed sensors as traction control and standard anti-lock brake (ABS) systems to recognize conditions that can destabilize a vehicle in curves and corners. To detect such potentially dangerous cornering situations, DSC measures differences in rotational speed between the two front wheels. The DSC system also adds a sensor for steering angle, Utilizes an existing one for vehicle velocity, and introduces its own software control elements in the over allantilock-brake/traction-control/stability-control system.The new Bosch and ITT Automotive stability control systems benefit from advanced technology developed for the aerospace industry. Just as in a supersonic fighter, the automotive stability control units use a sensor-based computer system to mediate between the human controller and the environment - in this case, the interface between tire and road. In addition, the system is built around a gyroscopelike sensor design used for missile guidance.BEYOND ABS AND TRACTION CONTROLStability control is the logical extension of ABS and traction control, according to a Society of Automotive Engineers paper written by van Zanten and Bosch colleagues Rainer Erhardt and Georg Pfaff. Whereas ABS intervenes when wheel lock is imminent during braking, and traction control prevents wheel slippage when accelerating, stability control operates independently of the driver's actions even when the car is free-rolling. Depending on the particular driving situation, the system may activate an individual wheel brake or any combination of the four and adjust engine torque, stabilizing the car and severely reducing the danger of an uncontrolled skid. The new systems control the motion not only during full braking but also during partial braking, coasting, acceleration, and engine drag on the driven wheels, circumstances well beyond what ABS and traction control can handle.The idea behind the three active safety systems is the same: One wheel locking or slipping significantly decreases directional stability or makes steering a vehicle more difficult. If a car must brake on a low-friction surface, locking its wheels should be avoided to maintain stability and steerability.Whereas ABS and traction control prevent undesired longitudinal slip, stability control reduces loss of lateral stability. If the lateral forces of a moving vehicle are no longer adequate at one or more wheels, the vehicle may lose stability, particularly in curves. What the drive"fishtailing" is primarily a turning or spinning around the vehicle's axis. A separate sensor must recognize this spinning, because unlike ABS and traction control, a car's lateral movement cannot be calculated from its wheel speeds.SPIN HANDLERSThe new systems measure any tendency toward understeer (when a car responds slowly to steering changes), or over-steer (when the rear wheels try to swing around). If a car understeers and swerves off course when driven in a curve, the stability control system will correct the error by braking the inner (with respect to the curve) rear wheel. This enables the driver, as in the case of ABS, to approach the locking limit of the road-tire interface without losing control of the vehicle. The stability control system may reduce the vehicle's drive momentum by throttling back the engine and/or by braking on individual wheels. Conversely, if the hteral stabilizing force on the rear axle is insufficient, the danger of oversteering may result in rear-end breakaway or spin-out. Here, the system acts as a stabilizer by applying the outer-front wheel brake. The idea behind the three active safety systems is the same: One wheel locking or slipping significantly decreases directional stability or makes steering a vehicle more difficult. If a car must brake on a low-friction surface, locking its wheels should be avoided to maintain stability and steerability.The influence of side slip angle on maneuverability, the Bosch researchers explained, shows that the sensitivity of the yaw moment on the vehicle, with respect to changes in the steering angle, decreases rapidly as the slip angle of the vehicle increases. Once the slip angle grows beyond a certain limit, the driver has a much harder time recovering by steering. On dry surfaces, maneuverability is lost at slip-angle values larger than approximately 10 degrees, and on packed snow at approximately 4 degrees.Most drivers have little experience recovering from skids. They aren't aware of the coefficient of friction between the tires and the road and have no idea of their vehicle's lateral stability margin. When the limit of adhesion is reached, the driver is usually caught by surprise and very often reacts in the wrong way, steering too much. Oversteering, ITT's Graber explained, causes the car to fishtail, throwing the vehicle even further out of control. ASMS sensors, he said, can quickly detect the beginning of a skid and momentarily activate the brakes at individual wheels to help return the vehicle to a stable line.It is important that stability control systems be user-friendly at the limit of adhesion - that is, to act predictably in a way similar to normal driving.The biggest advantage of stability control is its speed - it can respond immediately not only to skids but also to shifting vehicle conditions (such as changes in weight or tire wear) and road quality. Thus, the systems achieve optimum driving stability by changing the lateral stabilizing forces.For a stability control system to recognize the difference between what the driver wants (desired course) and the actual movement of the vehicle (actual course), current cars require an efficient set of sensors and a greater computer capacity for processing information.The Bosch VDC/ESP electronic control unit contains a conventional circuit board with two partly redundant microcontrollers using 48 kilobytes of ROM each. The 48-kB memory capacity is representative of the large amount of "intelligence" required to perform the design task, van Zanten said. ABS alone, he wrote in the SAE paper, would require one-quarter of this capacity, while ABS and traction control together require only one half of this software capacity.In addition to ABS and traction control systems and related sensors, VDC/ESP uses sensors for yaw rate, lateral acceleration, steering angle, and braking pressure as well as information on whether the car is accelerating, freely rolling, or braking. It obtains the necessary information on the current load condition of the engine from the engine controller. The steering-wheel angle sensor is based on a set of LED and photodiodes mounted in the steering wheel. A silicon-micromachine pressure sensor indicates the master cylinder's braking pressure by measuring the brake fluid pressure in the brake circuit of the front wheels (and, therefore, the brake pressure induced by the driver).Determining the actual course of the vehicle is a more complicated task. Wheel speed signals, which are provided for antilock brakes/traction control by inductive wheel speed sensors, are required to derive longitudinal slip. For an exact analysis of possible movement, however, variables describing lateral motion are needed, so the system must be expanded with two additional sensors - yaw rate sensors and lateral acceleration sensors.A lateral accelerometer monitors the forces occurring in curves. This analog sensor operates according to a damped spring-mass mechanism, by which a linear Hall generator transforms the spring displacement into an electrical signal. The sensor must be very sensitive, with an operating range of plus or minus 1.4 g.YAW RATE GYROAt the heart of the latest stability control system type is the yaw rate sensor, which is similar in function to a gyroscope. The sensor measures the speed at which the car rotates about its vertical axis. This measuring principle originated in the aviation industry and was further developed by Bosch for large-scale vehicle production. The existing gyro market offers two widely different categories of devices: $6000 units for aerospace and navigation systems (supplied by firms such as GEC Marconi Avionics Ltd., of Rochester, Kent, U.K.) and $160 units for videocameras. Bosch chose a vibrating cylinder design that provides the highest performance at the lowest cost, according to the SAE paper. A large investment was necessary to develop this sensor so that it could withstand the extreme environmental conditions of automotive use. At the same time, the cost for the yaw rate sensor had to be reduced so that it would be sufficiently affordable for vehicle use.The yaw rate sensor has a complex internal structure centered around a small hollow steel cylinder that serves as the measuring element. The thin wall of the cylinder is excited with piezoelectric elements that vibrate at a frequency of 15 kilohertz. Four pairs of these piezo elements are arranged on the circumference of the cylinder, with paired elements positioned opposite each other. One of these pairs brings the open cylinder into resonance vibration by applying a sinusoidal voltage at its natural frequency to the transducers; another pair, which is displaced by 90 degrees, stabilizes the vibration. At both element pairs in between, so-called vibration nodes shift slightlydepending on the rotation of the car about its vertical axis. If there is no yaw input, the vibration forms a standing wave. With a rate input, the positions of the nodes and antinodes move around the cylinder wall in the opposite direction to the direction of rotation (Coriolis acceleration). This slight shift serves as a measure for the yaw rate (angular velocity) of the car.Several drivers who have had hands-on experience with the new systems in slippery cornering conditions speak of their cars being suddenly nudged back onto the right track just before it seems that their back ends might break away.Some observers warn that stability controls might lure some drivers into overconfidence in low-friction driving situations, though they are in the minority. It may, however, be necessary to instruct drivers as to how to use the new capability properly. Recall that drivers had to learn not to "pump" antilock brake systems.Although little detail has been reported regarding next-generation active safety systems for future cars (beyond various types of costly radar proximity scanners and other similar systems), it is clear that accident-avoidance is the theme for automotive safety engineers. "The most survivable accident is the one that never happens," said ITT's Graber. "Stability control technology dovetails nicely with the tremendous strides that have been made to the physical structure and overall capabilities of the automobile." The next such safety system is expected to do the same.。
汽车专业英语读译教程 (梁桂航 第3版 ) 习题与答案TEXT B
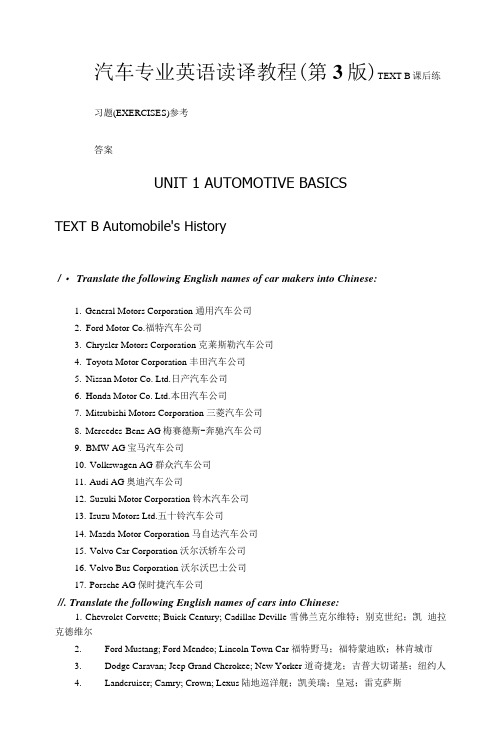
汽车专业英语读译教程(第3版)TEXT B课后练习题(EXERCISES)参考答案UNIT 1 AUTOMOTIVE BASICSTEXT B Automobile's History/ ・ Translate the following English names of car makers into Chinese:1.General Motors Corporation 通用汽车公司2.Ford Motor Co.福特汽车公司3.Chrysler Motors Corporation 克莱斯勒汽车公司4.Toyota Motor Corporation 丰田汽车公司5.Nissan Motor Co. Ltd.日产汽车公司6.Honda Motor Co. Ltd.本田汽车公司7.Mitsubishi Motors Corporation 三菱汽车公司8.Mercedes-Benz AG梅赛德斯-奔驰汽车公司9.BMW AG宝马汽车公司10.Volkswagen AG群众汽车公司11.Audi AG奥迪汽车公司12.Suzuki Motor Corporation 铃木汽车公司13.Isuzu Motors Ltd.五十铃汽车公司14.Mazda Motor Corporation 马自达汽车公司15.Volvo Car Corporation 沃尔沃轿车公司16.Volvo Bus Corporation 沃尔沃巴士公司17.Porsche AG保时捷汽车公司//. Translate the following English names of cars into Chinese:1.Chevrolet Corvette; Buick Century; Cadillac Deville 雪佛兰克尔维特;别克世纪;凯迪拉克德维尔2.Ford Mustang; Ford Mendeo; Lincoln Town Car 福特野马;福特蒙迪欧;林肯城市3.Dodge Caravan; Jeep Grand Cherokee; New Yorker 道奇捷龙;吉普大切诺基;纽约人ndcruiser; Camry; Crown; Lexus陆地巡洋舰;凯美瑞;皇冠;雷克萨斯1.What are the advantages of continuously variable transmission?Because there are no gears to tie a given road speed directly to a given engine speed, the CVT can vary the engine speed as needed to access maximum power as well as maximum fuel efficiency. This allows the CVT to provide quicker acceleration than a conventional automatic or manual transmission while delivering superior fuel economy.2.What are the main components of automated manual transmission?Transmission control ECU, clutch activator, transmission actuator, operators, and sensorsII. Translate the following paragraph into Chinese :The basic technical criteria for continuously variable transmissions are size, weight, transmission-ratio range, transfer efficiency, noise emissions and installation possibilities. With regard to these aspects, mechanical continuously variable transmissions, in the form of chain-driven transmission, have provided the best results so far.评判无级变速器的基本技术标准是尺寸、重量、传动比范围、传动效率、噪声排放和安装可能性。
1215控制器接线图

M I C R O P R O C E S S O RM O T O R S P E E D C O N T R O L L E R S A P P L I C A T I O NThe Curtis PMC 1214/1215/1219 controllers are ide-ally suited for larger electric vehicle applications, such as walkie/rider pallet trucks, personnel carriers, stackers, reach trucks, fork lifts and other series or compound motorapplications.D E S C R I P T I O NCurtis PMC 1214/1215/1219 series of motor speed controllers feature a microprocessor based logic section combined with a proven MOSFET power section.The 1214/1215/1219 series controllers are efficient, cost effective and easy to install.F E A T U R E S• Compact size.• Environmental protection provided by a sealed package.• Advanced high frequency power section utilizing custom power MOSFETs provides high efficiency, silent operation and reduced motor and battery losses.• Power connections made by solid copper busses with polarized Molex connector for control signals.• Thermal protection and compensation circuitry provideunder temperature cutback, constant current limit over the operating range and linear rollback in over temperature. No sudden loss of power under any thermal conditions.• Over voltage and under voltage protection.• Fully compatible with 1311, 1314, and 1307Programmers for full parametric adjustment, tuning, test and diagnostics.• Complete diagnostics of the controller can also be accomplished with the built-in status LED.• Meets or exceeds EEC fault detection requirements withcircuitry and software to detect faults in the throttle circuit, MOSFET drive circuits, MOSFET transistors, contactor drivers and contactors.• Input sequencing options include neutral start (HPD) and static return to off (SRO).• True arcless contactor switching with microprocessor controlled contactor sequencing.• Throttle position variable or fixed plugging current options.• Neutral braking option provides for automatic plug braking in neutral.• MultiMode™ option for programmable two mode (current limit, speed, acceleration) operation.• Emergency reverse function (belly button) provides fullfunction with a single input. Additional output provides for an emergency reverse circuit continuity check.• Anti-rollback (ramp start) function gives full power for starting on ramps.• Simple contactor and switch wiring. Coil drivers are monitored for short and open circuit for fail-safe operation.• Flexible throttle circuitry accepts a variety of throttletypes including: 5k-0, 0-5k, 0-5v, 0-10v and three wire potentiometer.CURTIS INSTRUMENTS, (UK) LTD.5 UPPER PRIORY STREETNORTHAMPTON NN1 2PTENGLANDTEL 44 (0) 1604-629755FAX 44 (0) 1604-629876CURTIS INSTRUMENTS INDIAPRIVATE LTD.1199, GHOLE ROAD PUNE 411004, INDIA TEL 91 (0) 20-5531288 FAX 91 (0) 20-5539192CURTIS INSTRUMENTS, INC.200 KISCO AVENUE 235 EAST AIRWAY BLVD. MT. KISCO, NY 10549 LIVERM O RE, CA 94551 USA USA TEL (914) 666-2971 TEL (925) 961-1088 FAX (914) 666-2188 FAX (925) 961-10992 MIN TYP . VOLTAGE UNDERVOLTAGECURTIS PMC VOLTAGE CURRENT RATING DROP @ 100A CUTBACK MO DELS(volts)(amps)(amps) (volts)(volts)1214-8XXX 24-36 400 400 <0.20 16 1214-8XXX 36-48 350 350 <0.30 21 1215-8XXX 24-36 500 500 <0.16 16 1215-8XXX 36-48 500 500 <0.20 21 1219-8XXX 24-36 600 600 <0.12 16 1219-8XXX36-48600600<0.1521M O D E L C H A R TT Y P I C A L W I R I N G D I A G R A MD I ME N S I O N SSpecifications subject to change without notice50069 REV B 4/06©2006 Curtis Instruments, Inc.W A R R A N T Y Two year limited warranty from time of delivery.is a trademark of Curtis Instruments, Inc.(0.22)26.4×20.6×2.3 (1.04×0.81×0.09);[6 plcs in 1219]BRAKE/SEA TMODE SELECT EMERG.REVFORWARD REVERSE REVCONT ACTORSMAINFWD KEYSWITCH SWITCHESSWITCHES24-pin detailEMERGENCY REVERSE BRAKE or SEAT SWITCHREVERSE (walkies only)2-WIRE FORWARD。
Robust Control and Estimation
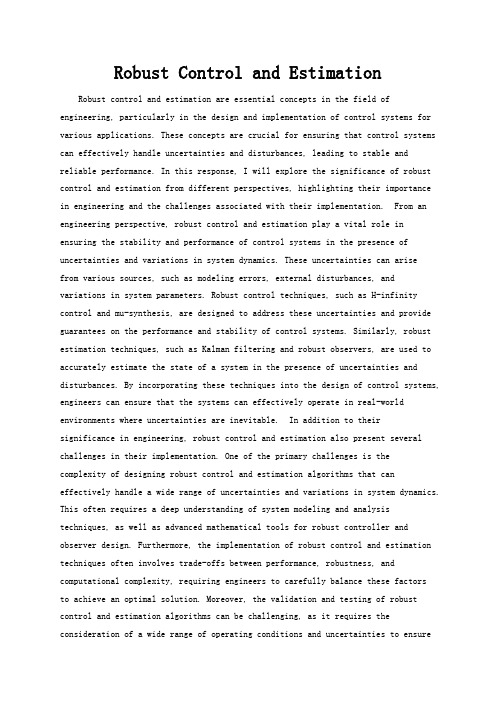
Robust Control and Estimation Robust control and estimation are essential concepts in the field of engineering, particularly in the design and implementation of control systems for various applications. These concepts are crucial for ensuring that control systems can effectively handle uncertainties and disturbances, leading to stable and reliable performance. In this response, I will explore the significance of robust control and estimation from different perspectives, highlighting their importancein engineering and the challenges associated with their implementation. From an engineering perspective, robust control and estimation play a vital role in ensuring the stability and performance of control systems in the presence of uncertainties and variations in system dynamics. These uncertainties can arisefrom various sources, such as modeling errors, external disturbances, andvariations in system parameters. Robust control techniques, such as H-infinity control and mu-synthesis, are designed to address these uncertainties and provide guarantees on the performance and stability of control systems. Similarly, robust estimation techniques, such as Kalman filtering and robust observers, are used to accurately estimate the state of a system in the presence of uncertainties and disturbances. By incorporating these techniques into the design of control systems, engineers can ensure that the systems can effectively operate in real-world environments where uncertainties are inevitable. In addition to theirsignificance in engineering, robust control and estimation also present several challenges in their implementation. One of the primary challenges is thecomplexity of designing robust control and estimation algorithms that can effectively handle a wide range of uncertainties and variations in system dynamics. This often requires a deep understanding of system modeling and analysis techniques, as well as advanced mathematical tools for robust controller and observer design. Furthermore, the implementation of robust control and estimation techniques often involves trade-offs between performance, robustness, and computational complexity, requiring engineers to carefully balance these factorsto achieve an optimal solution. Moreover, the validation and testing of robust control and estimation algorithms can be challenging, as it requires the consideration of a wide range of operating conditions and uncertainties to ensurethe robustness and reliability of the designed control systems. From a practical perspective, the significance of robust control and estimation becomes evident in various engineering applications, such as aerospace, automotive, robotics, and process control. In these applications, the ability to effectively handle uncertainties and disturbances is crucial for ensuring the safety, reliability, and performance of control systems. For example, in aerospace applications, robust control techniques are used to design flight control systems that can operate in the presence of aerodynamic uncertainties and external disturbances. Similarly, in automotive applications, robust estimation techniques are used for state estimation in vehicle navigation and control systems, where uncertainties in sensor measurements and environmental conditions can affect the system's performance. By incorporating robust control and estimation techniques into these applications, engineers can ensure that the control systems can operate safely and effectively in real-world scenarios. Furthermore, the significance of robust control and estimation extends beyond engineering applications, as these concepts also have implications for broader societal and economic challenges. For instance, in the context of autonomous systems and artificial intelligence, robust control and estimation are essential for ensuring the safety and reliability of autonomous vehicles, drones, and robotic systems. The ability to effectively handle uncertainties and disturbances is critical for the widespread adoption of these technologies, as it directly impacts their ability to operate safely in dynamic and unpredictable environments. Moreover, in the context of industrial automation and process control, robust control and estimation techniques are essential for optimizing the performance and efficiency of manufacturing processes, leading to economic benefits and environmental sustainability. In conclusion, robust control and estimation are essential concepts in the field of engineering, withsignificant implications for various applications and societal challenges. Despite the challenges associated with their implementation, these concepts play a crucial role in ensuring the stability, reliability, and performance of control systems in the presence of uncertainties and disturbances. By addressing these challenges and incorporating robust control and estimation techniques into engineering applications, engineers can ensure the safe and effective operation of controlsystems in real-world environments, leading to technological advancements and societal benefits.。
SAE J2602-2 2005 LIN Network for Vehicle Applications Conformance Test

E-mailing, copying and internet posting are prohibited VEHICLERECOSAE Technical Standards Board Rules provide that: “This report is published by SAE to advance the state of technical and engineering sciences. The use of this report is entirely voluntary, and its applicability and suitability for any particular use, including any patent infringement arising therefrom, is the sole responsibility of the user.”SAE reviews each technical report at least every five years at which time it may be reaffirmed, revised, or cancelled. SAE invites your written comments and suggestions. Copyright © 2005 SAE InternationalAll rights reserved. No part of this publication may be reproduced, stored in a retrieval system or transmitted, in any form or by any means, electronic, mechanical, photocopying, recording, or otherwise, without the prior written permission of SAE.SAE J2602-2 Issued SEP20055.7 Mandatory Node Configuration Requests (ref. LIN 2.0 Diag and Config Specification) (14)5.7.1General Configuration Requirements (14)5.7.2NAD and Message ID Assignment (15)5.7.3Targeted Reset (21)5.7.4Broadcast Reset Slave Response (21)5.8 Master and Slave Message Format (23)5.8.1Checksum (ref. Section 2.1.5, LIN 2.0 Protocol Specification) (23)5.8.2Signal Consistency (ref. Section 1.2, LIN 2.0 Protocol Specification) (23)5.8.3Signal Encoding Types (ref. Section 1.1, LIN 2.0 Protocol Specification) (23)5.8.4Signal Management (23)5.8.5Unused Bits in the Data Field (ref. Section 2.3, LIN 2.0 Protocol Specification) (23)5.8.6J2602 Slave Status Byte (23)Types (23)5.9 Message5.9.1Availability of Unconditional Frames (ref Section 2.3.1, LIN 2.0 Protocol Specification) (23)5.9.2Event Triggered Frames (ref. Section 2.3.2, LIN 2.0 Protocol Specification) (23)5.9.3Identifier Assignment (J2602-1 Requirement resulting from Event Triggered FrameAnomaly) (23)6.J2602 API Requirements (24)6.1 Master Node Configuration API (24)6.2 Diagnostic Transport Layer API (24)7.J2602 Bus Operation (24)7.1 Normal Communication Mode and Transmission Rate (24)7.1.1Master Node Bit Time Measurement (24)7.1.2Slave Node Bit Time Measurement (26)7.2 Sleep/Wake Mode in Master and Slave (28)7.2.1Wake-up of Master and Slave (ref. Section 5.1, LIN 2.0 Protocol Specification) (29)7.2.2Go To Sleep (ref. Section 5.2, LIN 2.0 Protocol Specification) (30)7.3 LIN Controller Clock Tolerance (30)7.4 Bus Electrical Parameters (31)7.4.1LIN Bus Signals and Loading Requirements (31)7.5 Master / Slave LIN Data Link (UART) Requirements (40)7.5.1Sample Point (40)7.5.2Synchronization (44)7.5.3Transmit Message Buffering (44)7.6 LIN ECU Requirements (44)7.6.1ECU Circuit Requirements (44)7.6.2Board Layout Requirements (45)Topology (45)7.7 Network7.7.1Loss of ECU Ground at Master or Slave Node (45)7.7.2Loss of ECU Battery (46)7.7.3Bus Electrical Load Distribution (46)7.7.4Bus Wiring Topology Configurations (47)7.7.5Bus Wiring Constraints (47)7.7.6Bus Wiring Practices to Improve EMC Performance (47)7.7.7Bus Wiring Harness and ECU Connectors (47)7.8 Master / Slave ESD Immunity (47)7.9 Master / Slave EMC Testing Requirements (47)SAE J2602-2 Issued SEP2005Modes (47)7.10 FaultTolerant7.10.1ECU Power Loss – Master / Slave (48)7.10.2Bus Wiring Short to Ground – Master / Slave (49)7.10.3Bus Wiring Short to Battery (50)7.10.4Short / Open in Other Circuits (52)7.11 Ground Offset Voltage (52)7.12 Operating Battery Power Voltage Range (52)7.12.1Normal Battery Voltage Power Operation (52)7.12.2Battery Power Over-Voltage Operation (54)7.12.3Low Battery Voltage Operation (55)7.12.4Battery Offset Voltage (56)7.12.5Reverse Battery Blocking Diode (56)7.13 EnvironmentalRequirements (56)7.13.1Transmit Operating Conditions (56)ForewordThe objective of this document is to define a standard conformance test for J2602-1 devices.The goal of this document is to define a basic conformance test for J2602-1 Master and Slave nodes that can be used to determine the suitability of devices for use. This is not a complete Qualification test. This does not replace the individual suppliers’ IC and/or module qualification.1.ScopeThis document covers the tests to be performed on all J2602-1 defined Master and Slave nodes. Tests described in this document will ensure a minimum standard level of performance to which all compatible ECUs and media shall be designed. This will assure full serial data communication among all connected devices regardless of supplier.The goal of SAE J2602-2 is to improve the interoperability and interchangeability of LIN devices within a network by verifying the devices pass a minimum set of tests.To allow for easy cross-reference, this document is arranged such that the conformance test for a given section in J2602-1 is in the same section in J2602-2.This document is to be referenced by the particular vehicle OEM component technical specification that describes any given EC U in which the LIN data link controller and physical layer interface is located. Primarily, the performance of the physical layer is specified in this document. ECU environmental and other requirements, when provided in the component technical specification, shall supercede the requirements of this document.The intended audience includes, but is not limited to, EC U suppliers, LIN controller suppliers, LIN transceiver suppliers, component release engineers and vehicle system engineers.SAE J2602-2 Issued SEP20051.1Mission/ThemeThis serial data link network is intended for use in applications where high data rate is not required and a lower data rate can achieve cost reductions in both the physical media components and in the microprocessor and/or dedicated logic devices (ASICs) which use the network.1.2OverviewLIN is a single wire, low cost, C lass A communication protocol. LIN is a master-slave protocol, and utilizes the basic functionality of most Universal Asynchronous Receiver Transmitter (UART) or Serial Communication Interface (SCI) devices as the protocol controllers in both Master and Slave devices. To meet the target of “Lower cost than either an OEM proprietary communications link or CAN link” for low speed data transfer requirements, a single wire transmission media based on the ISO 9141 specification was chosen. The protocol is implemented around a UART/SCI capability set, because the silicon footprint is small (lower cost). Many small microprocessors are equipped with either a UART or SC I interface (lower cost), and the software interface to these devices is relatively simple to implement (lower software cost). Finally, the relatively simplistic nature of the protocol controller (UART/SCI) and the nature of state-based operation, enable the creation of Application Specific Integrated C ircuits (ASIC s) to perform as input sensor gathering and actuator output controlling devices, in the vein of Mechatronics.All message traffic on the bus is initiated by the Master device. Slave devices receive commands and respond to requests from the Master. Since the Master initiates all bus traffic, it follows that the Slaves cannot communicate unless requested by the Master. However, Slave devices can generate a bus wakeup, if their inherent functionality requires this feature.The “LIN Consortium” developed the set of LIN specifications. The Consortium is a group of automotive OEMs, semiconductor manufacturers, and communication software and tool developers. The LIN specification set is “released” by the LIN Steering C ommittee, a closed subset of the members. Associate Consortium members contribute to the formation of the specifications through participation in LIN Work Groups; however, the direction of the Work Groups and the final released content of the specifications is the responsibility of the LIN Steering Committee.The LIN C onformance Test Specification contains tests for the Physical Layer, Data Link Layer, Node Configuration and Network Management, and EMC.1.3Relationship to the LIN Conformance Test SpecificationThe LIN C onformance Test Specification Package, version 1.0 dated August 1, 2004, consists of four documents:1.3.1LIN OSI L AYER 1–P HYSICAL L AYERThe LIN OSI Layer 1 – Physical Layer Test Specification describes the tests to be performed on the physical layer characteristics, including operating voltage range, signal threshold values, slope control, propagation delay, power and ground voltage shifts, fault conditions, etc.SAE J2602-2 Issued SEP20055.8Master and Slave Message Format5.8.1C HECKSUM (REF.S ECTION 2.1.5,LIN2.0P ROTOCOL S PECIFICATION)If this is not correct, no other messaging would work correctly. The tool shall check the checksum in every message sent by the DUT. If the checksum is not correct an error shall be logged.5.8.2S IGNAL C ONSISTENCY (REF.S ECTION 1.2,LIN2.0P ROTOCOL S PECIFICATION)Not a requirement.5.8.3S IGNAL E NCODING T YPES (REF.S ECTION 1.1,LIN2.0P ROTOCOL S PECIFICATION)Recommended messaging, not verifiable.5.8.4S IGNAL M ANAGEMENTVerified by review of the applicable NCF (Slave ECU) or LDF (Master ECU).5.8.5U NUSED B ITS IN THE D ATA F IELD (REF.S ECTION 2.3,LIN2.0P ROTOCOL S PECIFICATION) Informational, not a requirement.5.8.6J2602S LAVE S TATUS B YTE5.8.6.1Error Field DefinitionVerified proper use of Error Field Definition in Section 5.4.1.5.8.6.2Application Information FieldVerified by component/system level testing by the OEM/Tier 1 Supplier.5.9Message Types5.9.1A VAILABILITY OF U NCONDITIONAL F RAMES (REF S ECTION 2.3.1,LIN2.0P ROTOCOL S PECIFICATION) This is a guideline.5.9.2E VENT T RIGGERED F RAMES (REF.S ECTION 2.3.2,LIN2.0P ROTOCOL S PECIFICATION)Verified by component/system level testing by the OEM/Tier 1 Supplier.5.9.2.1Identifier Assignment (J2602-1 Requirement Resulting from Event Triggered Frame Anomaly) Verified by component/system level testing by the OEM/Tier 1 Supplier.SAE J2602-2 Issued SEP20055.9.3S PORADIC F RAME (REF.S ECTION 2.3.3,LIN2.0P ROTOCOL S PECIFICATION)Verified by component/system level testing by the OEM/Tier 1 Supplier.6.J2602 API Requirements6.1Master Node Configuration APINot externally verifiable, requires a software review.6.2Diagnostic Transport Layer APINot a requirement.6.3Additional API RequirementsNot externally verifiable, requires a software review.7.J2602 Bus OperationThe physical layer is responsible for providing a method of transferring digital data symbols (1’s and 0’s) to the communication medium. The physical layer interface is a single wire, vehicle battery referenced bus, with low side voltage drive.7.1Normal Communication Mode and Transmission Rate7.1.1M ASTER N ODE B IT T IME M EASUREMENTThis test verifies the bit time of the Master DUT is within the specified range under maximum and minimum bus loading conditions.SAE J2602-2 Issued SEP2005Section 3.5.3 Test:1. The DUT is made to send a wake-up request.2. The LIN tool sends TST_FRAME_2 after the first wake-up request. After that TST_FRAME_6 is sentby the LIN tool.Section 3.5.3 Verification:1. The DUT must send the Wake Up Request according to Section 5.1, LIN2.0 Protocol Specification.2. The DUT must stop transmission of the wake-up request and must answer TST_FRAME_6.7.2.2G O T O S LEEP (REF.S ECTION 5.2,LIN2.0P ROTOCOL S PECIFICATION)Test according to LIN C onformance Test Specification Node C onfiguration / Network Management Version 1.0 of August 1, 2004 Section 3.1.Verification:1. The DUT(Master) must send the frame without failure and the first data byte must be 0x00.2. The DUT must not send any more messages. Observe the DUT for one complete message tablecycle time or 1 second, whichever is longer.7.2.2.1Slave Node SleepTest according to LIN C onformance Test Specification Node C onfiguration / Network Management Version 1.0 of August 1, 2004 Sections 3.2 and 3.6.Section 3.2 Verification:1. The DUT (Slave) current draw must decrease to the quiescent level as specified in the componentspec within 10 seconds unless otherwise specified in the component spec.Section 3.6 Verification:1. After a minimum of 4 seconds without any message traffic, the DUT (Slave) current draw mustdecrease to the quiescent level as specified in the component spec within 60 seconds if the default operation is the sleep state. Otherwise, the component may continue to activate outputs, etc. as defined by the component spec.2. In addition, the tool shall send TST_FRAME_2 followed by TST_FRAME_6 followed by the Header ofTST_FRAME_2. The slave shall have the same behavior as described above.3. Additionally, the tool shall send TST_FRAME_2 followed by TST_FRAME_6 followed by the Headerof TST_FRAME_2 and the first data byte. The slave shall have the same behavior as described above.7.3LIN Controller Clock ToleranceSee data sheet and clock divide error.FIGURE 14—LOGIC LEVEL VOLTAGE MEASUREMENT DESCRIPTIONSlave Node V oh and V ol Levels MeasurementSAE J2602-2 Issued SEP20057.7.4B US W IRING T OPOLOGY C ONFIGURATIONSFYI.7.7.5B US WIRING CONSTRAINTSGuaranteed by system design.7.7.6B US W IRING P RACTICES TO I MPROVE EMC P ERFORMANCEGuaranteed by system design.7.7.7B US W IRING H ARNESS AND ECU CONNECTORSShall be guaranteed by the connector supplier.7.8Master / Slave ESD ImmunityDUT circuit should be as specified in J2602-1 Figure 3 (Slave) or Figure 4 (Master).The ECU LIN Bus I/O pin shall withstand the following electrostatic discharges without any damage to the ECU when subjected to the Ford EMC Test – Electrostatic Discharge Immunity test (Section 19). Use the requirements in Table 8 of J2602-1 unless otherwise specified in the CTS.7.9Master / Slave EMC Testing RequirementsDUT circuit should be as specified in J2602-1 Figure 3 (Slave) or Figure 4 (Master).Testing using the below listed Ford EMC series of tests shall be used to assess the EMC performance ofa LIN physical layer design. Required testing methods include the following EMC test specifications.1. Test per Section 7.0 Radiated RF Emissions: RE3102. Test per Section 10.3 RF Immunity Requirements 1 – 400 MHz: RI112, level 1.3. Test per Section 10.4 RF Immunity Requirements 400 – 3100 MHz: RI114, level 1.7.10Fault Tolerant ModesThe Network shall meet the requirements as defined per the following failure modes:。
汽车电子毕设设计外文文献翻译(适用于毕业论文外文翻译+中英文对照)

Ultrasonic ranging system designPublication title: Sensor Review. Bradford: 1993.Vol.ABSTRACT: Ultrasonic ranging technology has wide using worth in many fields, such as the industrial locale, vehicle navigation and sonar engineering. Now it has been used in level measurement, self-guided autonomous vehicles, fieldwork robots automotive navigation, air and underwater target detection, identification, location and so on. So there is an important practicing meaning to learn the ranging theory and ways deeply. To improve the precision of the ultrasonic ranging system in hand, satisfy the request of the engineering personnel for the ranging precision, the bound and the usage, a portable ultrasonic ranging system based on the single chip processor was developed.Keywords: Ultrasound, Ranging System, Single Chip Processor1. IntroductiveWith the development of science and technology, the improvement of people’s standard of living, speeding up the development and construction of the city. Urban drainage system have greatly developed their situation is construction improving. However, due to historical reasons many unpredictable factors in the synthesis of her time, the city drainage system. In particular drainage system often lags behind urban construction. Therefore, there are often good building excavation has been building facilities to upgrade the drainage system phenomenon. It brought to the city sewage, and it is clear to the city sewage and drainage culvert in the sewage treatment system.Co mfort is very important to people’s lives. Mobile robots designed to clear the drainage culvert and the automatic control system Free sewage culvert clear guarantee robots, the robot is designed to clear the culvert sewage to the core. Control system is the core component of the development of ultrasonic range finder. Therefore, it is very important to design a good ultrasonic range finder.2. A principle of ultrasonic distance measurementThe application of AT89C51:SCM is a major piece of computer components are integrated into the chip micro-computer. It is a multi-interface and counting on the micro-controller integration, and intelligence products are widely used in industrial automation. and MCS-51 microcontroller is a typical and representative.Microcontrollers are used in a multitude of commercial applications such as modems, motor-control systems, air conditioner control systems, automotive engine and among others. The high processing speed and enhanced peripheral set of these microcontrollers make them suitable for such high-speed event-based applications. However, these critical application domains also require that these microcontrollers are highly reliable. The high reliability and low market risks can be ensured by a robust testing process and a proper tools environment for the validation of these microcontrollers both at the component and at the system level. Intel Plaform Engineering department developed an object-oriented multi-threaded test environment for the validation of its AT89C51 automotive microcontrollers. The goals of this environment was not only to provide a robust testing environment for the AT89C51 automotive microcontrollers, but to develop an environment which can be easily extended and reused for the validation of several other future microcontrollers. The environment was developed in conjunction with Microsoft Foundation Classes(AT89C51).1.1 Features* Compatible with MCS-51 Products* 2Kbytes of Reprogrammable Flash MemoryEndurance: 1,000Write/Erase Cycles* 2.7V to 6V Operating Range* Fully Static operation: 0Hz to 24MHz* Two-level program memory lock* 128x8-bit internal RAM* 15programmable I/O lines* Two 16-bit timer/counters* Six interrupt sources*Programmable serial UART channel* Direct LED drive output* On-chip analog comparator* Low power idle and power down modes1.2 DescriptionThe AT89C2051 is a low-voltage, high-performance CMOS 8-bit microcomputer with 2Kbytes of flash programmable and erasable read only memory (PEROM). The device is manufactured using Atmel’s high density nonvolatile memory technology and is compatible with the industry standard MCS-51 instruction set and pinout. By combining a versatile 8-bit CPU with flash on a monolithic chip, the Atmel AT89C2051 is a powerful microcomputer which provides a highly flexible and cost effective solution to many embedded control applications.The AT89C2051 provides the following standard features: 2Kbytes of flash,128bytes of RAM, 15 I/O lines, two 16-bit timer/counters, a five vector two-level interrupt architecture, a full duplex serial port, a precision analog comparator, on-chip oscillator and clock circuitry. In addition, the AT89C2051 is designed with static logicfor operation down to zero frequency and supports two software selectable power saving modes. The idle mode stops the CPU while allowing the RAM, timer/counters, serial port and interrupt system to continue functioning. The power down mode saves the RAM contents but freezer the oscillator disabling all other chip functions until the next hardware reset.1.3 Pin Configuration1.4 Pin DescriptionVCC Supply voltage.GND Ground.Prot 1Prot 1 is an 8-bit bidirectional I/O port. Port pins P1.2 to P1.7 provide internal pullups. P1.0 and P1.1 require external pullups. P1.0 and P1.1 also serve as the positive input (AIN0) and the negative input (AIN1), respectively, of the on-chip precision analog comparator. The port 1 output buffers can sink 20mA and can drive LED displays directly. When 1s are written to port 1 pins, they can be used as inputs. When pins P1.2 to P1.7 are used as input and are externally pulled low, they will source current (IIL) because of the internal pullups.Port 3Port 3 pins P3.0 to P3.5, P3.7 are seven bidirectional I/O pins with internal pullups. P3.6 is hard-wired as an input to the output of the on-chip comparator and is not accessible as a general purpose I/O pin. The port 3 output buffers can sink 20mA. When 1s are written to port 3 pins they are pulled high by the internal pullups and can be used as inputs. As inputs, port 3 pins that are externally being pulled low will source current (IIL) because of the pullups.Port 3 also serves the functions of various special features of the AT89C2051 as listed below.1.5 Programming the FlashThe AT89C2051 is shipped with the 2 Kbytes of on-chip PEROM code memory array in the erased state (i.e., contents=FFH) and ready to be programmed. The code memory array is programmed one byte at a time. Once the array is programmed, to re-program any non-blank byte, the entire memory array needs to be erased electrically.Internal address counter: the AT89C2051 contains an internal PEROM address counter which is always reset to 000H on the rising edge of RST and is advanced applying a positive going pulse to pin XTAL1.Programming algorithm: to program the AT89C2051, the following sequence is recommended.1. power-up sequence:Apply power between VCC and GND pins Set RST and XTAL1 to GNDWith all other pins floating , wait for greater than 10 milliseconds2. Set pin RST to ‘H’ set pin P3.2 to ‘H’3. Apply the appropriate combination of ‘H’ or ‘L’ logic to pins P3.3, P3.4, P3.5,P3.7 to select one of the programming operations shown in the PEROM programming modes table.To program and Verify the Array:4. Apply data for code byte at location 000H to P1.0 to P1.7.5.Raise RST to 12V to enable programming.5. Pulse P3.2 once to program a byte in the PEROM array or the lock bits. The byte-write cycle is self-timed and typically takes 1.2ms.6. To verify the programmed data, lower RST from 12V to logic ‘H’ level and set pins P3.3 to P3.7 to the appropriate levels. Output data can be read at the port P1 pins.7. To program a byte at the next address location, pulse XTAL1 pin once to advance the internal address counter. Apply new data to the port P1 pins.8. Repeat steps 5 through 8, changing data and advancing the address counter for the entire 2 Kbytes array or until the end of the object file is reached.9. Power-off sequence: set XTAL1 to ‘L’ set RST to ‘L’Float all other I/O pins Turn VCC power off2.1 The principle of piezoelectric ultrasonic generatorPiezoelectric ultrasonic generator is the use of piezoelectric crystal resonators to work. Ultrasonic generator, the internal structure as shown, it has two piezoelectric chip and a resonance plate. When it’s two plus pulse signal, the frequency equal to the intrinsic piezoelectric oscillation frequency chip, the chip will happen piezoelectric resonance, and promote the development of plate vibration resonance, ultrasound is generated. Conversely, it will be for vibration suppression of piezoelectric chip, the mechanical energy is converted to electrical signals, then it becomes the ultrasonic receiver.The traditional way to determine the moment of the echo’s arrival is based on thresholding the received signal with a fixed reference. The threshold is chosen well above the noise level, whereas the moment of arrival of an echo is defined as the first moment the echo signal surpasses that threshold. The intensity of an echo reflecting from an object strongly depends on the object’s nature, size and distance from the sensor. Further, the time interval from the echo’s starting point to the moment when it surpasses the threshold changes with the intensity of the echo. As a consequence, a considerable error may occur even two echoes with different intensities arriving exactly at the same time will surpass the threshold at different moments. The stronger one will surpass the threshold earlier than the weaker, so it will be considered as belonging to a nearer object.2.2 The principle of ultrasonic distance measurementUltrasonic transmitter in a direction to launch ultrasound, in the moment to launch the beginning of time at the same time, the spread of ultrasound in the air, obstacles on his way to return immediately, the ultrasonic reflected wave received by the receiverimmediately stop the clock. Ultrasound in the air as the propagation velocity of 340m/s, according to the timer records the time t, we can calculate the distance between the launch distance barrier(s), that is: s=340t / 23. Ultrasonic Ranging System for the Second Circuit DesignSystem is characterized by single-chip microcomputer to control the use of ultrasonic transmitter and ultrasonic receiver since the launch from time to time, single-chip selection of 875, economic-to-use, and the chip has 4K of ROM, to facilitate programming.3.1 40 kHz ultrasonic pulse generated with the launchRanging system using the ultrasonic sensor of piezoelectric ceramic sensorsUCM40, its operating voltage of the pulse signal is 40kHz, which by the single-chip implementation of the following procedures to generate.puzel: mov 14h, # 12h; ultrasonic firing continued 200msHere: cpl p1.0; output 40kHz square wavenop;nop;nop;djnz 14h, here;retRanging in front of single-chip termination circuit P1.0 input port, single chip implementation of the above procedure, the P1.0 port in a 40kHz pulse output signal, after amplification transistor T, the drive to launch the first ultrasonic UCM40T, issued 40kHz ultrasonic pulse, and the continued launch of 200ms. Ranging the right and the left side of the circuit, respectively, then input port P1.1 and P1.2, the working principle and circuit in front of the same location.3.2 Reception and processing of ultrasonicUsed to receive the first launch of the first pair UCM40R, the ultrasonic pulse modulation signal into an alternating voltage, the op-amp amplification IC1A and after polarization IC1B to IC2. IC2 is locked loop with audio decoder chip LM567, internal voltage-controlled oscillator center frequency of f0=1/1.1R8C3, capacitor C4 determinetheir target bandwidth. R8-conditioning in the launch of the high jump 8 feet into a low-level, as interrupt request signals to the single-chip processing.Ranging in front of single-chip termination circuit output port INT0 interrupt the highest priority, right or left location of the output circuit with output gate IC3A access INT1 port single-chip, while single-chip P1.3 and P1.4 received input IC3A, interrupted by the process to identify the source of inquiry to deal with, interrupt priority level for the first left right after. Part of the source code is as follows:Receivel: push pswpush accclr ex1; related external interrupt 1jnb p1.1, right; P1.1 pin to 0, ranging from right to interrupt service routine circuitjnb p1.2, left; P1.2 pin to 0, to the left ranging circuit interrupt service routinereturn: SETB EX1; open external interrupt 1pop accpop pswretiright: …; right location entrance circuit interrupt service routineAjmp Returnleft: …; left ranging entrance circuit interrupt service routineAjmp Return3.3 The calculation of ultrasonic propagation timeWhen you start firing at the same time start the single-chip circuitry within the timer T0, the use of timer counting function records the time and the launch of ultrasonic reflected wave received time. When you receive the ultrasonic reflected wave, the receiver circuit output a negative jump in the end of INT0 or INT1 interrupt request generates a signal, single-chip microcomputer in response to external interrupt request, the implementation of the external interrupt service subroutine, read the time difference, calculating the distance. Some of its source code is as follows:RECEIVE0: PUSH PSWPUSH ACCCLR EX0; related external interrupt 0MOV R7, TH0; read the time valueMOV R6, TL0CLR CMOV A, R6SUBB A, #0BBH; calculate the time differenceMOV 31H, A; storage resultsMOV A, R7SUBB A, # 3CHMOV 30H, ASETB EX0; open external interrupt 0\POP ACCPOP PSWRETIFor a flat target, a distance measurement consists of two phases: a coarse measurement and a fine measurement:Step 1: Transmission of one pulse train to produce a simple ultrasonic wave.Step 2: Changing the gain of both echo amplifiers according to equation, until the echo is detected.Step 3: Detection of the amplitudes and zero-crossing times of both echoes.Step 4: Setting the gains of both echo amplifiers to normalize the output at, say 3 volts. Setting the period of the next pulses according to the: period of echoes. Setting the time window according to the data of step 2.Step 5: Sending two pulse trains to produce an interfered wave. Testing the zero-crossing times and amplitudes of the echoes. If phase inversion occurs in the echo, determine to otherwise calculate to by interpolation using the amplitudes near the trough. Derive t sub m1 and t sub m2.Step 6: Calculation of the distance y using equation.4、The ultrasonic ranging system software designSoftware is divided into two parts, the main program and interrupt service routine. Completion of the work of the main program is initialized, each sequence of ultrasonic transmitting and receiving control.Interrupt service routines from time to time to complete three of the rotation direction of ultrasonic launch, the main external interrupt service subroutine to read the value of completion time, distance calculation, the results of the output and so on.5、ConclusionsRequired measuring range of 30cm-200cm objects inside the plane to do a number of measurements found that the maximum error is 0.5cm, and good reproducibility. Single-chip design can be seen on the ultrasonic ranging system has a hardware structure is simple, reliable, small features such as measurement error. Therefore, it can be used not only for mobile robot can be used in other detection system.Thoughts: As for why the receiver do not have the transistor amplifier circuit, because the magnification well, integrated amplifier, but also with automatic gain control level, magnification to 76dB, the center frequency is 38k to 40k, is exactly resonant ultrasonic sensors frequency.6、Parking sensor6.1 Parking sensor introductionReversing radar, full name is "reversing the anti-collision radar, also known as" parking assist device, car parking or reversing the safety of assistive devices, ultrasonic sensors(commonly known as probes), controls and displays (or buzzer)and other components. To inform the driver around the obstacle to the sound or a moreintuitive display to lift the driver parking, reversing and start the vehicle around tovisit the distress caused by, and to help the driver to remove the vision deadends and blurred vision defects and improve driving safety.6.2 Reversing radar detection principleReversing radar, according to high-speed flight of the bats in thenight, not collided with any obstacle principles of design anddevelopment. Probe mounted on the rear bumper, according to different price and brand, the probe only ranging from two, three, four, six, eight,respectively, pipe around. The probe radiation, 45-degree angle up and downabout the search target. The greatest advantage is to explore lower than the bumper of the driver from the rear window is difficult to see obstacles, and the police, suchas flower beds, children playing in the squatting on the car.Display parking sensor installed in the rear view mirror, it constantlyremind drivers to car distance behindthe object distance to the dangerous distance, the buzzer starts singing, allow the driver to stop. When the gear lever linked into reverse gear, reversing radar, auto-start the work, the working range of 0.3 to 2.0 meters, so stop when the driver was very practical. Reversing radar is equivalent to an ultrasound probe for ultrasonic probe can be divided into two categories: First, Electrical, ultrasonic, the second is to use mechanical means to produce ultrasound, in view of the more commonly used piezoelectric ultrasonic generator, it has two power chips and a soundingboard, plus apulse signal when the poles, its frequency equal to the intrinsic oscillation frequency of the piezoelectric pressure chip will be resonant and drivenby the vibration of the sounding board, the mechanical energy into electrical signal, which became the ultrasonic probe works. In order to better study Ultrasonic and use up, people have to design and manufacture of ultrasonic sound, the ultrasonic probe tobe used in the use of car parking sensor. With this principle in a non-contactdetection technology for distance measurement is simple, convenient and rapid, easyto do real-time control, distance accuracy of practical industrial requirements. Parking sensor for ranging send out ultrasonic signal at a givenmoment, and shot in the face of the measured object back to the signal wave, reversing radar receiver to use statistics in the ultrasonic signal from the transmitter to receive echo signals calculate the propagation velocity in the medium, which can calculate the distance of the probe and to detect objects.6.3 Reversing radar functionality and performanceParking sensor can be divided into the LCD distance display, audible alarm, and azimuth directions, voice prompts, automatic probe detection function is complete, reversing radar distance, audible alarm, position-indicating function. A good performance reversing radar, its main properties include: (1) sensitivity, whether theresponse fast enough when there is an obstacle. (2) the existence of blind spots. (3) detection distance range.6.4 Each part of the roleReversing radar has the following effects: (1) ultrasonic sensor: used tolaunch and receive ultrasonic signals, ultrasonic sensors canmeasure distance. (2) host: after the launch of the sine wave pulse to the ultrasonic sensors, and process the received signal, to calculate the distance value, the data and monitor communication. (3) display or abuzzer: the receivinghost from the data, and display the distance value and provide differentlevels according to the distance from the alarm sound.6.5 Cautions1, the installation height: general ground: car before the installation of 45 ~55: 50 ~ 65cmcar after installation. 2, regular cleaningof the probe to prevent the fill. 3, do not use the hardstuff the probe surface cover will produce false positives or ranging allowed toprobe surface coverage, such as mud. 4, winter to avoid freezing. 5, 6 / 8 probe reversing radar before and after the probe is not free to swap may cause the ChangMing false positive problem. 6, note that the probe mounting orientation, in accordance with UP installation upward. 7, the probe is not recommended to install sheetmetal, sheet metal vibration will cause the probe resonance, resulting in false positives.超声测距系统设计原文出处:传感器文摘布拉福德:1993年超声测距技术在工业现场、车辆导航、水声工程等领域具有广泛的应用价值,目前已应用于物位测量、机器人自动导航以及空气中与水下的目标探测、识别、定位等场合。
- 1、下载文档前请自行甄别文档内容的完整性,平台不提供额外的编辑、内容补充、找答案等附加服务。
- 2、"仅部分预览"的文档,不可在线预览部分如存在完整性等问题,可反馈申请退款(可完整预览的文档不适用该条件!)。
- 3、如文档侵犯您的权益,请联系客服反馈,我们会尽快为您处理(人工客服工作时间:9:00-18:30)。
Vehicle Applications ofController Area NetworkKarl Henrik Johansson,1, Martin T¨o rngren,2, Lars Nielsen31Department of Signals,Sensors and Systems,Royal Institute of Technology, Stockholm,Sweden,kallej@s3.kth.se2Department of Machine Design,Royal Institute of Technology,Stockholm, Sweden,martin@damek.kth.se3Department of Electrical Engineering,Link¨o ping University,Sweden,lars@isy.liu.se1IntroductionThe Controller Area Network(CAN)is a serial bus communications proto-col developed by Bosch in the early1980s.It defines a standard for efficient and reliable communication between sensor,actuator,controller,and other nodes in real-time applications.CAN is the de facto standard in a large vari-ety of networked embedded control systems.The early CAN development was mainly supported by the vehicle industry:CAN is found in a variety of passen-ger cars,trucks,boats,spacecraft,and other types of vehicles.The protocol is also widely used today in industrial automation and other areas of networked embedded control,with applications in diverse products such as production machinery,medical equipment,building automation,weaving machines,and wheelchairs.In the automotive industry,embedded control has grown from stand-alone systems to highly integrated and networked control systems[11,7].By net-working electro-mechanical subsystems,it becomes possible to modularize functionalities and hardware,which facilitates reuse and adds capabilities. Fig.1shows an example of an electronic control unit(ECU)mounted on a diesel engine of a Scania truck.The ECU handles the control of engine,turbo, fan,etc.but also the CAN bining networks and mecha-tronic modules makes it possible to reduce both the cabling and the number The work of K.H.Johansson was partially supported by the European Com-mission through the ARTIST2Network of Excellence on Embedded Systems Design, by the Swedish Research Council,and by the Swedish Foundation for Strategic Re-search through an Individual Grant for the Advancement of Research Leaders.The work of M.T¨o rngren was partially supported by the European Commission through ARTIST2and by the Swedish Foundation for Strategic Research through the project SAVE.2K.H.Johansson,M.T¨o rngren,L.NielsenFig.1.An ECU mounted directly on a diesel engine of a Scania truck.The arrows indicate the ECU connectors,which are interfaces to the CAN.(Courtesy of Scania AB.)of connectors,which facilitates production and increases reliability.Introduc-ing networks in vehicles also makes it possible to more efficiently carry out diagnostics and to coordinate the operation of the separate subsystems.The CAN protocol standardizes the physical and data link layers,which are the two lowest layers of the open systems interconnect(OSI)communica-tion model(see Fig.2).For most systems,higher-layer protocols are needed to enable efficient development and operation.Such protocols are needed for defining how the CAN protocol should be used in applications,for example, how to refer to the configuration of identifiers with respect to application mes-sages,how to package application messages into frames,and how to deal with start-up and fault handling.Note that in many cases only a few of the OSI layers are required.Note also that real-time issues and redundancy manage-ment are not covered by the OSI model.The adoption of CAN in a variety of applicationfields has led to the development of several higher-layer proto-cols,including SAE J1939,CANopen,DeviceNet,and CAN Kingdom.Their characteristics reflect differences in requirements and traditions of application areas.An example is the adoption of certain communication models,such as either the client-server model or the distributed data-flow model[13].The progress and success of CAN are due to a number of factors.The evolution of microelectronics paved the way for introducing distributed con-trol in vehicles.In the early1980s there was,however,a lack of low-cost and standardized protocols suitable for real-time control systems.Therefore,in 1983Kiencke started the development of a new serial bus system at Bosch,Vehicle Applications of Controller Area Network3ApplicationCAN Physical Data linkNetworkTransportSessionPresentationFig.2.The CAN protocol defines the lowest two layers of the OSI model.There exist several CAN-based higher-layer protocols that are standardized.The user choice depends on the application.Fig.3.The number of CAN nodes sold per year is currently about 400million.(Data from the association CAN in Automation [3].)which was presented as CAN in 1986at the SAE congress in Detroit [8].The CAN protocol was internationally standardized in 1993as ISO 11898-1.The development of CAN was mainly motivated by the need for new functionality,but it also reduced the need for wiring.The use of CAN in the automotive industry has caused mass production of CAN controllers.Today,CAN con-trollers are integrated on many microcontrollers and available at a low cost.Fig.3shows the number of CAN nodes that were sold during 1999–2003.4K.H.Johansson,M.T¨o rngren,L.NielsenBusFig.4.Three nodes connected through a CAN bus The purpose of this chapter is to give an introduction to CAN and some of its vehicle applications.The outline is as follows.Section2describes the CAN protocol,including its message formats and error handling.The section is concluded by a brief history of CAN.Examples of vehicle application ar-chitectures based on CAN are given in Section3.A few specific control loops closed over CAN buses are discussed in Section4.The paper is concluded with some perspectives in Section5,where current research issues such as x-by-wire and standardized software architectures are considered.The exam-ples are described in more detail in[14].A detailed description of CAN is given in the textbook[6].Another good resource for further information is the homepage of the organization CAN-in-Automation(CiA)[3].The use of CAN as a basis for distributed control systems is discussed in[13].2Controller Area NetworkThe Controller Area Network(CAN)is a serial communications protocol suited for networking sensors,actuators,and other nodes in real-time sys-tems.In this section,wefirst give a general description of CAN including its message formats,principle of bus arbitration,and error-handling mechanisms. Extensions of CAN,such as application-oriented higher-layer protocols and time-triggered CAN,are described,followed by a brief history of CAN.2.1DescriptionA CAN bus with three nodes is depicted in Fig.4.The CAN specification[4] defines the protocols for the physical and the data link layers,which enable the communication between the network nodes.The application process of a node,e.g.,a temperature sensor,decides when it should request the trans-mission of a message frame.The frame consists of a datafield and overhead, such as identifier and controlfields.Since the application processes in gen-eral are asynchronous,the bus has a mechanism for resolving conflicts.For CAN,it is based on a non-destructive arbitration process.The CAN protocol therefore belongs to the class of protocols denoted as carrier sense multiple access/collision avoidance(CSMA/CA),which means that the protocol listensVehicle Applications of Controller Area Network5SOF Identifier RTR ControlData ACKCRC EOFFig.5.CAN message frameto the network in order to avoid collisions.CSMA/CD protocols like Ether-net have instead a mechanism to deal with collisions once they are detected. CAN also includes various methods for error detection and error handling. The communication rate of a network based on CAN depends on the physical distances between the nodes.If the distance is less than40m,the rate can be up to1Mbps.Message formatsCAN distinguishes four message formats:data,remote,error,and overload frames.Here we limit the discussion to the data frame,shown in Fig.5.A data frame begins with the start-of-frame(SOF)bit.It is followed by an eleven-bit identifier and the remote transmission request(RTR)bit.The identifier and the RTR bit form the arbitrationfield.The controlfield consists of six bits and indicates how many bytes of data follow in the datafield.The datafield can be zero to eight bytes.The datafield is followed by the cyclic redundancy checksum(CRC)field,which enables the receiver to check if the received bit sequence was corrupted.The two-bit acknowledgment(ACK)field is used by the transmitter to receive an acknowledgment of a valid frame from any receiver.The end of a message frame is signaled through a seven-bit end-of-frame(EOF).There is also an extended data frame with a twenty-nine-bit identifier(instead of eleven bits).ArbitrationArbitration is the mechanism that handles bus access conflicts.Whenever the CAN bus is free,any unit can start to transmit a message.Possible conflicts, due to more than one unit starting to transmit simultaneously,are resolved by bit-wise arbitration using the identifier of each unit.During the arbitration phase,each transmitting unit transmits its identifier and compares it with the level monitored on the bus.If these levels are equal,the unit continues to transmit.If the unit detects a dominant level on the bus,while it was trying to transmit a recessive level,then it quits transmitting(and becomes a receiver). The arbitration phase is performed over the whole arbitrationfield.When it is over,there is only one transmitter left on the bus.The arbitration is illustrated by the following example with three nodes (see Fig.6).Let the recessive level correspond to“1”and the dominant level to“0”,and suppose the three nodes have identifiers I i,i=1,2,3,equal to6K.H.Johansson,M.T¨o rngren,L.NielsenFig.6.Example illustrating CAN arbitration when three nodes start transmitting their SOF bits simultaneously.Nodes1and2stop transmitting as soon as they transmit one(recessive level),and Node3is transmitting zero(dominant level).At these instances,Nodes1and2enter the receiver mode,indicated in grey.When the identifier has been transmitted,the bus belongs to Node3which thus continues transmitting its controlfield,datafield,etc.I1=11001101010,I2=11001011011,I3=11001011001.If the nodes start transmitting simultaneously,the arbitration process illus-trated in thefigure takes place.First all three nodes send their SOF bit.Then, they start transmitting their identifiers and all of them continue as long as they are equal.The sixth bit of I1is at the recessive level,while the corre-sponding bits are at the dominant level of I2and I3.Therefore,Node1stops transmitting immediately and continues only listening to the bus.This listen-ing phase is indicated in Fig.6with the greyfield.Since the tenth bit of I2 is at the recessive level while it is dominant for I3,Node3is the transmitter that has access to the bus after the arbitration phase and thus continues with the transmission of the control and datafields,etc.There is no notion of message destination addresses in CAN.Instead each node picks up all traffic on the bus.Hence,every node needs tofilter out the interesting messages on the bus.The arbitration mechanism of CAN is an effective way to resolve bus conflicts.Note that a minimum amount of address data is transmitted and that no extra bus control information has to be transmitted.A consequence of the arbitration mechanism,however,is that units with low priority may experience large latency if high-priority units are very active.Error handlingError detection and error handling are important for the performance of CAN. Because of complementary error detection mechanisms,the probability of hav-ing an undetected error is very small.Error detection is done infive differentVehicle Applications of Controller Area Network7 ways in CAN:bit monitoring and bit stuffing,as well as frame check,ACK check,and CRC.Bit monitoring simply means that each transmitter monitors the bus level,and signals a bit error if the level does not agree with the trans-mitted signal.(Bit monitoring is not done during the arbitration phase.)After having transmittedfive identical bits,a node will always transmit the oppo-site bit.This extra bit is neglected by the receiver.The procedure is called bit stuffing,and it can be used to detect errors.The frame check consists of checking that thefixed bits of the frame have the values they are supposed to have,e.g.,EOF consists of seven recessive bits.During the ACK in the message frame,all receivers are supposed to send a dominant level.If the transmitter,which transmits a recessive level,does not detect the dominant level,then an error is signaled by the ACK check mechanism.Finally,the CRC is that every receiver calculates a checksum based on the message and compares it with the CRCfield of the message.Every receiver node obviously tries to detect errors within each message.If an error is detected,it leads to an immediate and automatic retransmission of the incorrect message.In comparison to other network protocols,this mech-anism leads to a high data integrity and a short error recovery time.CAN thus provides elaborate procedures for error handling,including retransmis-sion and reinitialization.The procedures have to be studied carefully for each application to ensure that the automated error handling is in line with the system requirements.2.2Protocol extensionsCAN provides the basic functionality described above.In many situations, it is desirable to use standardized protocols that define the communication layers on top of the CAN.Such higher-layer protocols are described below to-gether with CAN gateways and the time-triggered extension of CAN denoted TTCAN,which allows periodic access to the communication bus with a high degree of certainty.Higher-layer protocolsThe CAN protocol defines the lowest two layers of the OSI model in Fig.2. In order to use CAN,protocols are needed to define the other layers.Field-bus protocols usually do not define the session and presentation layers,since they are not needed in these applications.The users may either decide to define their own software for handling the higher layers,or they may use a standardized protocol.Existing higher-layer protocols are often tuned to a certain application domain.Examples of such protocols include SAE J1939, CANopen,and DeviceNet.It is only SAE J1939that is specially developed for vehicle applications.Recently,attempts have been made to interface CAN and Ethernet,which is the dominant technology for local area networks and widely applied for connecting to the Internet.8K.H.Johansson,M.T¨o rngren,L.NielsenSAE J1939is a protocol that defines the higher-layer communication con-trol.It was developed by the American Society of Automotive Engineers (SAE)and is thus targeted to the automotive industry.The advantage of having a standard is considerable,since it enables independent development of the individual networked components,which also allows vehicle manufac-turers to use components from different suppliers.SAE J1939specifies,e.g., how to read and write data,but also how to calibrate certain subsystems. The data rate of SAE J1939is about250kbps,which gives up to about1850 messages per second[6].Applications of SAE J1939include truck-and-trailer communication,vehicles in agriculture and forestry,as well as navigation sys-tems in marine applications.CANopen is a standardized application defined on top of CAN and widely used in Europe for the application of CAN in distributed industrial automa-tion.It is a standard of the organization CAN in Automation(CiA)[3]. CANopen specifies communication profiles and device profiles,which enable an application-independent use of CAN.The communication profile defines the underlying communication mechanism.Device profiles exist for the most common devices in industrial automation,such as digital and analog I/O components,encoders,and controllers.The device can be configured through CANopen independent of its manufacturer.CANopen distinguishes real-time data exchange and less critical data exchange.It provides standardized com-munication objects for real-time data,configuration data,network manage-ment data,and certain special functions(e.g.,time stamp and synchronization messages).DeviceNet is another standardized application defined on top of CAN for distributed industrial automation.It is mainly used in the U.S.A.and Asia and was originally developed by Rockwell Automation.DeviceNet,Control-Net,and transmission control protocol/Internet protocol(TCP/IP)are open network technologies that share upper layers of the communication protocol, but are based on lower layers:DeviceNet is built on CAN,ControlNet on a token-passing bus protocol,and TCP/IP on Ethernet.CANKingdom is a high-layer protocol used for motion control systems. It is also used in the maritime industry,as described in a boat example in Section3.CANKingdom allows the changing of network behavior at any time, including while the system is running.For example,CANKingdom allows the system troubleshooter to turn offindividual nodes.The CAN node identifiers and the triggering conditions for sending messages can be changed while the system is running.One instance when real-time network reconfiguration is used is during failure conditions.An example is a loss of a radio link ECU in a maritime application.The network monitor,also known as the King, in that casefirst shuts offthe radio node to keep it from sending any more commands,and then tells the appropriate nodes to get data from the King. This operation eliminates the problem of a node receiving two simultaneous but conflicting commands.It also eliminates the problem of two nodes sending the same CAN id.Vehicle Applications of Controller Area Network9 The high-level protocols described above have been developed with differ-ent applications and traditions in mind,which is reflected,for example,in their support for real-time control.Although SAE J1939is used for implementing control algorithms,it does not provide explicit support for time-constrained messaging.In contrast,such functionalities are provided by CANKingdom and CANopen,which handle explicit support for inter-node synchronization. CANKingdom and CANopen allow static and dynamic configuration of the network,whereas SAE J1939provides littleflexibility.CAN gatewaysGateways and bridges enable CAN-based networks to be linked together or linked to networks with other protocols.A gateway between a CAN and another communication network maps the protocols of the individual net-works.There exist many different types of CAN gateways,e.g.,CAN-RS232 and CAN-TCP/IP gateways.The latter can provide remote access to a CAN through the Internet,which allows worldwide monitoring and maintenance. The networks connected through a gateway or a bridge are disconnected in terms of their real-time behavior,so obviously the timing and performance of the complex inter-connected network can be hard to predict even if the individual networks are predictable.Ethernet(or rather Ethernet/IP)is quite a different communication proto-col compared to CAN,but is still of growing importance in industrial automa-tion either in constellations with CAN or on its own.Traditionally,Ethernet is used in office automation and multimedia applications,while CAN domi-nates in vehicles and in certain industrial automation systems.The strength of Ethernet is the ability to quickly move large amounts of data over long distances and that the number of nodes in the network can be large.CAN,on the other hand,is optimized for transmitting small messages over relatively short distances.A drawback with a network based on the Ethernet protocol is that the nodes need to be quite powerful and complex(and therefore more expensive)in order to handle the communication control.Another drawback with Ethernet is that during network traffic congestion the delay jitter can be severe and unpredictable,although at low network load Ethernet gives almost no delay.Time-triggered communication on CANTraditional CAN communication is event based:asynchronous events are trig-gered by node applications that initialize each transmission session.In many cases,this strategy is an efficient way to share the network resource.There are a variety of applications,however,that require a guaranteed access to the communication bus with afixed periodic rate.This constraint is typical for sampled-data feedback control systems.In the automotive industry,x-by-wire10K.H.Johansson,M.T¨o rngren,L.Nielsensystems are examples of such control systems with deterministic communica-tion behavior during regular operation.By introducing the notion of global network time,the standard ISO11898-4defines the extension Time-triggered communication on CAN(TTCAN). It is built on top of the traditional event-triggered CAN protocol and en-ables existing CAN nodes to work in parallel with TTCAN nodes.The global clock requires hardware implementation;otherwise,TTCAN is a pure soft-ware extension of CAN.The synchronization in TTCAN takes place through a periodic reference message,which all TTCAN nodes recognize and use to synchronize their clocks.The nodes are configured to know when to send their message after the reference message.The period time of the transmission of a periodic node should be a multiple of the reference period.Traditional CAN nodes(or event-based TTCAN nodes)compete for the access of the free win-dows between the reference messages,along the line of the conventional CAN protocol.This mechanism is thus the reason why time-triggered and event-triggered scheduling is possible simultaneously in TTCAN.The sender of the reference message is obviously a crucial node in TTCAN to guarantee clock synchronization.Therefore,an automatic procedure is pro-vided for letting another node take over if the reference sender fails,and taking the reference back when the original clock master recovers.It is possible to use an external clock,for example,from the global positioning system(GPS).2.3A brief historyThe evolution of microelectronics paved the way for introducing distributed control systems in vehicles.In the early1980s there was,however,no low-cost and standardized protocol that was suitable for real-time control systems. Therefore,as we stated before,in1983Kiencke started the development of a new serial bus system at Bosch,which was presented as CAN in1986at the SAE congress in Detroit[8].The development of CAN was mainly motivated by the need for new functionalities,but it also substantially reduced the need for wiring.The Bosch CAN Specification2.0was published in1991and then two years later the CAN protocol was internationally standardized as ISO 11898-1.The need for higher-layer protocols was recognized early.In1991, CAN Kingdom was introduced by Kvaser.DeviceNet,another higher-layer protocol,was introduced by Allen-Bradley in1994,and CANopen by CAN in Automation(CiA)in1995.CiA is an international users and manufacturers group,which was founded in1992.Mercedes-Benz has been using CAN in its passenger cars since1992.Originally,CAN was used only for engine control, but today there are a variety of CAN nodes not only for powertrain and chassis control but also for body electronics and infotainment systems.Many other car manufacturers base their control architecture on CAN,including BMW,Fiat, Renault,SAAB,Volkswagen,and Volvo.The CAN architecture for a Volvo passenger car is described in the next section.The notion of time-triggered protocols for real-time systems was introduced by Kopetz and co-workers[10].Time-triggered extensions of CAN were discussed in the late1990s and early 2000s.This led to the standardization of TTCAN as ISO11897-4in2004. Currently,there are intensive activities on utilizing TTCAN in a variety of vehicle applications.3ArchitecturesIn this section,four vehicular examples of distributed control architectures based on CAN are presented.The architectures are implemented in a passen-ger car,a truck,a boat,and a spacecraft.3.1Volvo passenger carIn the automotive industry,there has been a remarkable evolution over the last few years in which embedded control systems have grown from stand-alone control systems to highly integrated and networked control systems. Originally motivated by reduced cabling and the specific addition of function-alities with sensor sharing and diagnostics,there are currently several new x-by-wire systems under development that involve distributed coordination of many subsystems.Fig.7shows the distributed control architecture of the Volvo XC90.The blocks represent ECUs and the thick lines represent networks.The actual lo-cation of an ECU in the car is approximately indicated by its location in the block diagram.There are three classes of ECUs:powertrain and chassis,info-tainment,and body electronics.Many of the ECU acronyms are defined in the figure.Several networks are used to connect the ECUs and the subsystems. There are two CAN buses.The leftmost network in the diagram is a CAN for power train and chassis subsystems.It connects for example engine and brake control(TCM,ECM,BCM,etc.)and has a communication rate of500kbps. The other CAN connects body electronics such as door and climate control (DDM,PDM,CCM,etc.)and has a communication rate of125kbps.The central electronic module(CEM)is an ECU that acts as a gateway between the two CAN buses.A media oriented system transport(MOST)network de-fines networking for infotainment and telematics subsystems.It consequently connects ECUs for multimedia,phone,and antenna.Finally,local intercon-nect networks(LINs)are used to connect slave nodes into a subsystem and are denoted by dashed lines in the block diagram.The maximum configuration for the vehicle contains about40ECUs[7].3.2Scania truckThere are several similarities between the control architecture in passenger cars and trucks.There are also many important differences,some of whichPowertrain and chassis Body electronics TCM Transmission control module CEM Central electronic moduleECM Engine control module SWM Steering wheel moduleBCM Brake control module DDM Driver door moduleBSC Body sensor cluster REM Rear electronic moduleSAS Steering angle sensor SWM Steering wheel moduleSUM Suspension module DDM Driver door moduleAUD Audio module PDM Passenger door moduleREM Rear electronic moduleInfotainment/Telematics CCM Climate control module MP1,2Media players1and2ICM Infotainment controlPHM Phone module UEM Upper electronic moduleMMM Multimedia module DIM Driver information moduleSUB Subwoofer AEM Auxiliary electronicATM Antenna tuner moduleFig.7.Distributed control architecture for the Volvo XC90.Two CAN buses and some other networks connect up to about40ECUs.(Courtesy of Volvo Car Corpo-ration.)are due to the fact that trucks are configured in a large number of physical variants and have longer expected life times.These characteristics impose requirements onflexibility with respect to connecting,adding,and removing equipments and trailers.The control architecture for a Scania truck is shown in Fig.8.It consists of three CAN buses,denoted green,yellow,and red by Scania due to their relative importance.The leftmost(vertical)CAN contains less critical ECUs such as the audio system and the climate control.The middle(vertical)CAN handles the communication for important subsystems that are not directly involved in the engine and brake management.For example,connected to thisGreen bus Yellow busAUS Audio system LAS Locking and alarm systemCSS Crash safety system AWD All wheel drive systemACC Automatic climate control ICL Instrument cluster systemWTA Auxiliary heater water-to-air TCO Tachograph systemATA Auxiliary heater air-to-air VIS Visibility systemCTS Clock and timer system APS Air processing systemRTG Road transport info gateway BWS Body work systemRTI Road transport info system BCS Body chassis systemRed busGMS Gearbox management system COO Coordinator systemACS Articulation control systemEMS Engine management systemEEC Exhaust emission controlBMS Brake management systemSMS Suspension management systemSMD Suspension management dollyFig.8.Distributed control architecture for a Scania truck.Three CAN buses(de-noted green,yellow,and red due to their relative criticality)connect up to more than twenty ECUs.The coordinator system ECU(COO)is a gateway between thethree CAN buses.(Courtesy of Scania AB.)。