TPS在广汽丰田物流系统的应用及借鉴意义
【物流规划】-广汽丰田物流模式探究

【物流规划】-广汽丰田物流模式探究广汽丰田汽车的物流充分运用了丰田生产方式(TPS)的准时化(JIT)和働自动化理念,以实现最佳物流品质、最低物流成本为目标,践行准时化物流和TPS的持续改善,致力于追求世界第一的物流模式,特别是借助于股东方日本丰田的经验优势,这些理念和目标已深深融入到汽车物流运作的每一个环节,形成明显的特色。
丰田目前基本上专注于对汽车的研发、设计、制造、销售及售后服务等领域,而物流业务都是采取外包的方式,委托物流供应商来实现。
“丰田为了控制成本,实现平准化生产,在供应链管理中实行‘零库存’方式。
所谓的‘零库存’当然不是完全没有库存,而是指没有多余的不必要的库存,设定的库存是可以维持生产需要的最少量的库存。
丰田通过有效地降低物流过程的库存,很好地控制了各环节的成本。
”这种JIT物流方式和现在广州本田和东风日产等汽车厂家的模式有所不同。
在零部件物流方面,广汽丰田为满足顾客需求,实现市场动向、工厂生产和零部件采购的同期化管理,全面采用了同步物流和循环取货的零部件物流模式。
“同步物流,是生产和供应之间的最短连接,快速高效,库存最小,体现了精益物流的精髓——消除一切浪费。
广汽丰田在项目规划时,就将50%以上货量的零部件布局在工厂周边,建立同步物流体系。
同步物流的信息,由生产线控制系统直接传送,就是说,我们将周边供应商完全纳入厂内工程系统。
可以说,运用最新的理念,进行前瞻性的规划布局,是广汽丰田物流成功的起点。
”“循环取货的特点是高效、准确、灵活,是供应链物流最有效的运输模式,也是中国汽车零部件物流发展的方向。
广汽丰田是中国汽车物流业‘循环取货’的先行者,也是其理论和方法的集大成者。
早在2006年,广汽丰田第一款车‘凯美瑞’投产时,就以丰田全球样板工厂的定位,导入了‘循环取货’的物流模式。
而丰田式的‘循环取货’最大的特色,是每个环节融入丰田生产方式的JIT理念,作‘平准化’的物流供应。
比如物流中转仓(Cross Dock),除了进度吸收,更重要的功能是进行与生产同步的平准化作业,这是一个操作过程,而非单纯的仓储功能。
TPS在广汽丰田零部件厂内物流系统中的应用
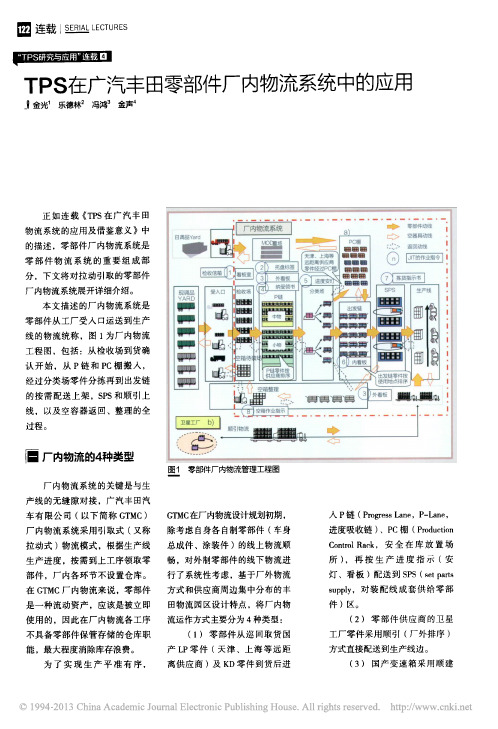
使 用状态
分割 进度 数进一 步细
化 就 是平 准 化 水 平 的 进 一 步 提
子
再 到 SP 区 ( 或 生 产线 ) S
广州地 区以外 因为运输周 期较长
( 如无 对策则 对应 生产计 划变更 的 响应 周期 长 ), 零 部件 出厂时 对应 的生产顺 序 尚未确定 , 这些 课 题都需 要在 厂 内物 流环节逐 一
产 线 出现 异 常, G M C 停 止 向供 T 应 商下达取 货指令使包 括空 器具 返 回的物流 停止 , 后续 恢复生产
四 连 互 生 CT E 载渔旦 LE U尺 二 S
在不同 的 P 链
表1 不同线路供应商取货便数及对应p 链数
. . 睡藏 差. . . . . 跪泣自. 口且四 到 . . 目画回 参曰
部件 几乎完全相同
生 产指示 在供 应商完 成排序 ( 分
类 ) 再 进 行 JI 引取 配送 T 对于 物 流距 离较远 (卫星工厂之外的 ,
使用, 则分割进度数> P 链数,
2加9 年再 次分 割进 度 数 二 ( 日 6 3 取货便数可为 l 2 3 4 6 9
12 13 18 36 ), P 链 数 二 , 29
参考
TPS
在广汽 丰 田物 流系统 的应 用及借 鉴 意义 (上 ) 中装车顺序图 ( 图
) 3 和本 文图 2 , 厂内运输链最多 可 容纳 16 个托 盘 , G M C 提 前 0 T 60 分钟 向供应商下 达进度需求 , 供 应 商 厂 内排 序 需要 1 分 钟 , 0 座椅 运 输 车 辆 在 供 应 商 装 车 一
内物流 , 图 2 是座椅 配送 的工 程
图
在库
供应商 没有空托 盘时 也会
全面认识丰田生产方式TPS
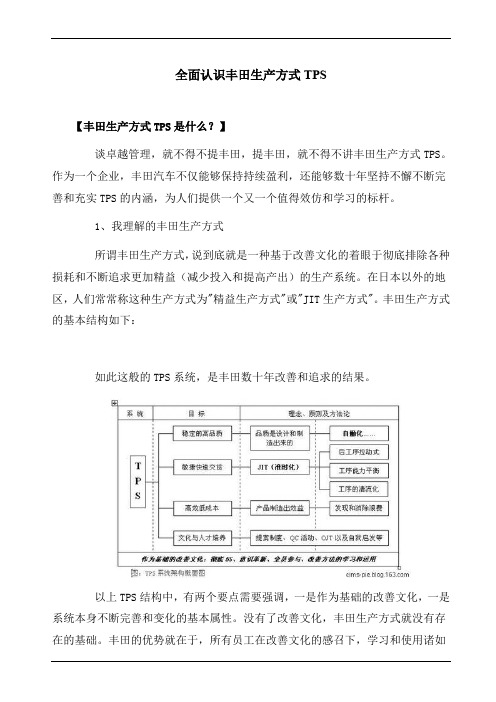
全面认识丰田生产方式TPS【丰田生产方式TPS是什么?】谈卓越管理,就不得不提丰田,提丰田,就不得不讲丰田生产方式TPS。
作为一个企业,丰田汽车不仅能够保持持续盈利,还能够数十年坚持不懈不断完善和充实TPS的内涵,为人们提供一个又一个值得效仿和学习的标杆。
1、我理解的丰田生产方式所谓丰田生产方式,说到底就是一种基于改善文化的着眼于彻底排除各种损耗和不断追求更加精益(减少投入和提高产出)的生产系统。
在日本以外的地区,人们常常称这种生产方式为"精益生产方式"或"JIT生产方式"。
丰田生产方式的基本结构如下:如此这般的TPS系统,是丰田数十年改善和追求的结果。
以上TPS结构中,有两个要点需要强调,一是作为基础的改善文化,一是系统本身不断完善和变化的基本属性。
没有了改善文化,丰田生产方式就没有存在的基础。
丰田的优势就在于,所有员工在改善文化的感召下,学习和使用诸如5S、TPM、TPI、QCC、TQM等各种有效的管理改善工具,进行持续不断的改善实践,让既有的生产系统不断走向更具精益的境界。
2、思想和实践的结合再好的思想、理念,如果缺少落地的办法,没有加踏实地的实践,就将成为空谈。
在我看来,丰田的卓越之处就在于,每提出一个理念都有有效落地的方法和员工持续改善实践的配合。
以下就几个核心理念及其实践进行简单的说明。
【误区阻碍我们前进】丰田生产方式听上去耳熟能详,但是对丰田生产方式,人们还存在着许多认识误区。
这些误区阻碍我们前进。
1、误区一:TPS仅仅是一套系统或方法在我的《卓越制造管理》课程中,会讲到A企业500吨注塑机"9分钟换模"的实战案例(基本上是"走钢丝"的水平),让学员们羡慕不已。
有学员提出,让笔者帮助他把公司近百台注塑机改造成9分钟换模(每年可以节省数百万),顾问费好谈!可见,这位学员认为"9分钟换模"只是一套可复制的方法。
广汽丰田物流详解

一、GTMC物流概述1、GTMC物流的背景(TPS)丰田生产方式(Toyota Production System,简称“TPS”)是TOYOTA 在长期的实践中逐步建立和完善的一套理论体系。
它以企业获得最大利润、服务社会、创造美好生活、培养优秀员工为根本目的,以彻底杜绝浪费为基本思想,在持续改善的基础上追求制造产品合理性品质至上的一种生产方式。
准时生产制:(Just in Time,简称“JIT”)和自働化是丰田生产方式的两大支柱。
1).JIT(准时生产制)➢JIT(准时生产制)要求在所需要的时间按所需要的数量生产所需要的品种,尽可能消除一切浪费;➢为了实现准时生产,丰田在整个物流过程中(从供应商到生产线)努力实现持续的小批量高频率平稳的部品运送。
而平准化和看板的运用则是实现准时生产的重要途径。
平准化平准化是实现JIT 的大前提,其含义是将生产或供给的物品的种类和数量进行平均化。
在生产和供应的过程中如果没有实现平准化,将会造成自工序完成品不足或为防止缺品而准备库存,也会造成人员、器材必须以浮动的最大值准备,造成不必要的浪费。
在物流工程中,平准化具有重要的意义,右图就是在物流中未实施平准化的例子,可以明显的看出没有实施平准化所造成工时和物流器材的增加。
2 )看板JIT 是一种拉动式的管理方法,它需要从最后一道工序通过信息流向上一道工序传递信息,这种传递信息的载体就是看板。
没有看板,JIT 是无法进行的。
看板分为引取看板和生产看板两种,记载着生产和运送的数量、时间、目的地、放置场所、搬运工具等信息,从装配工序逐次向前工序追溯。
在装配线将所使用的部品上所带的看板取下,以此再去前一道工序领取。
前工序则只生产被这些看板所领走的量,“后工序领取”及“适时适量生产”就是通过这些看板来实现的。
看板具有以下作用和规则:①引取情报(前工程按后工程看板后补充生产);②生产指示情报(前工程按看板数生产);③防止生产过程搬运过多(无看板,不生产、不搬运);④问题明显化,可调节库存。
丰田汽车的TPS管理模式概要

浅议丰田汽车的TPS 管理模式(Ⅰ文◎杨永清摘要:文章就丰田管理的沿革、理念、内涵、举措和效应等方面进行了简析,认为丰田的管理模式及其TPS 管理系统是企业产业核心竞争的源泉,值得借鉴。
关键词:TPS 管理模式;丰田汽车公司;生产管理系统0前言巨大董事长曾经说过“如果不是当年用心学TPS ,就不可能有今天的巨大。
”他进而提出“以TPS 为师,植入改善的基因。
”可见丰田管理不仅在汽车业界令人刮目相看,同样在自行车行业亦有借鉴发扬光大之效。
本文就丰田管理的沿革、理念、内涵、举措和效应等进行简述与浅议。
20世纪80年代,电视广告语打出“有路必有丰田车”,当时觉得有点夸大其词,后有机会境外公干,从号称“汽车王国”的美国到发展中国家的泰国,以及宝岛台湾等等,Toyota 汽车广告满目琳琅,比比皆是,这才深信无疑。
纵观丰田汽车的成长历程,再看《丰田的秘密》的记叙,对该企业的发展沿革,方有所了解和感悟。
1沿革1933年,丰田喜一郎(Ki-ichiro Toyoda 在丰田纺织机械厂内设立汽车部,介入汽车产业,先后引进销量极好的通用公司的雪佛兰(Chevrolet 和德国迪克瓦公司的“DKW ”牌轿车作为样车,模仿制造。
后又购买美国福特(Fort 汽车作研发参考。
此时,从散件组装起步,化油器、速度表、火花塞等全部进口,谈不上自制率。
1937年8月,“丰田汽车工业株式会社”正式成立。
由于侵略战争的需要,纳入军工生产,汽车销量大增。
当年,共生产汽车4.1万辆,其中小车577辆。
截止1945年日本无条件投降,丰田汽车公司共产93293辆。
1950年,按银行要求,成立丰田汽车销售公司,实现产销分离。
当年,朝鲜战争爆发,美军46亿日元的巨额订货,给丰田带来了丰厚的利润,丰田从而大展宏图。
以产品为龙头,1955年5月1日丰田极力精心打造的皇冠(Crown 轿车下线,其魅力使德国大众甲壳虫相形逊色,受到美国消费者的青睐,风靡全球。
全面认识丰田生产方式TPS
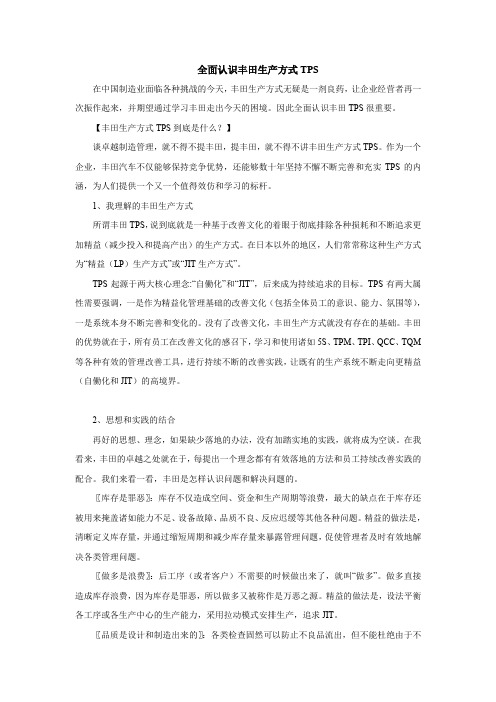
全面认识丰田生产方式TPS在中国制造业面临各种挑战的今天,丰田生产方式无疑是一剂良药,让企业经营者再一次振作起来,并期望通过学习丰田走出今天的困境。
因此全面认识丰田TPS很重要。
【丰田生产方式TPS到底是什么?】谈卓越制造管理,就不得不提丰田,提丰田,就不得不讲丰田生产方式TPS。
作为一个企业,丰田汽车不仅能够保持竞争优势,还能够数十年坚持不懈不断完善和充实TPS的内涵,为人们提供一个又一个值得效仿和学习的标杆。
1、我理解的丰田生产方式所谓丰田TPS,说到底就是一种基于改善文化的着眼于彻底排除各种损耗和不断追求更加精益(减少投入和提高产出)的生产方式。
在日本以外的地区,人们常常称这种生产方式为“精益(LP)生产方式”或“JIT生产方式”。
TPS起源于两大核心理念:“自働化”和“JIT”,后来成为持续追求的目标。
TPS有两大属性需要强调,一是作为精益化管理基础的改善文化(包括全体员工的意识、能力、氛围等),一是系统本身不断完善和变化的。
没有了改善文化,丰田生产方式就没有存在的基础。
丰田的优势就在于,所有员工在改善文化的感召下,学习和使用诸如5S、TPM、TPI、QCC、TQM 等各种有效的管理改善工具,进行持续不断的改善实践,让既有的生产系统不断走向更精益(自働化和JIT)的高境界。
2、思想和实践的结合再好的思想、理念,如果缺少落地的办法,没有加踏实地的实践,就将成为空谈。
在我看来,丰田的卓越之处就在于,每提出一个理念都有有效落地的方法和员工持续改善实践的配合。
我们来看一看,丰田是怎样认识问题和解决问题的。
〖库存是罪恶〗:库存不仅造成空间、资金和生产周期等浪费,最大的缺点在于库存还被用来掩盖诸如能力不足、设备故障、品质不良、反应迟缓等其他各种问题。
精益的做法是,清晰定义库存量,并通过缩短周期和减少库存量来暴露管理问题,促使管理者及时有效地解决各类管理问题。
〖做多是浪费〗:后工序(或者客户)不需要的时候做出来了,就叫“做多”。
广汽丰田物流运输详解

一、GTMC物流概述1、GTMC物流的背景(TPS)丰田生产方式(Toyota Production System,简称“TPS”)是TOYOTA 在长期的实践中逐步建立和完善的一套理论体系。
它以企业获得最大利润、服务社会、创造美好生活、培养优秀员工为根本目的,以彻底杜绝浪费为基本思想,在持续改善的基础上追求制造产品合理性品质至上的一种生产方式。
准时生产制:(Just in Time,简称“JIT”)和自働化是丰田生产方式的两大支柱。
1).JIT(准时生产制)JIT(准时生产制)要求在所需要的时间按所需要的数量生产所需要的品种,尽可能消除一切浪费;为了实现准时生产,丰田在整个物流过程中(从供应商到生产线)努力实现持续的小批量高频率平稳的部品运送。
而平准化和看板的运用则是实现准时生产的重要途径。
平准化平准化是实现JIT 的大前提,其含义是将生产或供给的物品的种类和数量进行平均化。
在生产和供应的过程中如果没有实现平准化,将会造成自工序完成品不足或为防止缺品而准备库存,也会造成人员、器材必须以浮动的最大值准备,造成不必要的浪费。
在物流工程中,平准化具有重要的意义,右图就是在物流中未实施平准化的例子,可以明显的看出没有实施平准化所造成工时和物流器材的增加。
2 )看板JIT 是一种拉动式的管理方法,它需要从最后一道工序通过信息流向上一道工序传递信息,这种传递信息的载体就是看板。
没有看板,JIT 是无法进行的。
看板分为引取看板和生产看板两种,记载着生产和运送的数量、时间、目的地、放置场所、搬运工具等信息,从装配工序逐次向前工序追溯。
在装配线将所使用的部品上所带的看板取下,以此再去前一道工序领取。
前工序则只生产被这些看板所领走的量,“后工序领取”及“适时适量生产”就是通过这些看板来实现的。
看板具有以下作用和规则:①引取情报(前工程按后工程看板后补充生产);②生产指示情报(前工程按看板数生产);③防止生产过程搬运过多(无看板,不生产、不搬运);④问题明显化,可调节库存。
tps计划

tps计划TPS是一种以提高效率和简化流程为目标的管理方法,它源于日本的汽车制造行业,后来被广泛应用于各行各业。
TPS的全称为“Toyota Production System”,也被称为丰田生产方式或丰田生产系统。
TPS的核心思想是通过消除浪费、精益生产和持续改善来实现高效率和高质量的生产。
这一方法的成功在很大程度上得益于对员工的培养和参与,以及对优化整个价值流的不断追求。
本文将从TPS的起源和发展、基本原则、核心方法以及应用案例等方面进行阐述。
一、TPS的起源和发展TPS起源于丰田汽车公司,在20世纪50年代由一位丰田汽车公司的高级经理——福田康夫所创立。
福田康夫在观察丰田汽车公司生产线时,发现存在许多浪费,如库存过多、生产过程中的等待等。
为了解决这些问题,并提高生产效率,福田康夫开始试验并引进一些新的管理方法。
通过不断试错和改进,他最终发展出了TPS这一高效率的管理模式。
随着丰田汽车公司的快速发展和TPS的成功应用,TPS逐渐被其他企业所关注和借鉴,成为现代管理领域的重要理论之一。
二、TPS的基本原则TPS的基本原则包括“精确指导”的原则、“生产者视角”的原则、“员工培养”的原则以及“改善体系”的原则。
1. 精确指导的原则:TPS要求首先明确目标,并制定相应的计划。
精确的指导能够确保实施过程中能够保持目标的一致性和明确性,以避免浪费和无效的行动。
2. 生产者视角的原则:TPS鼓励员工始终以顾客需求为导向,并将自己视为价值链的一部分。
这种思维方式能够促使员工更加关注产品质量和客户满意度,并通过不断改进来提高生产效率和降低成本。
3. 员工培养的原则:TPS强调员工的培养和发展,认为员工是企业的核心竞争力。
通过培养员工的技能和知识,提高他们的参与度和责任心,以及激发他们的创造力和创新能力,能够有效地实现生产流程的优化和改善。
4. 改善体系的原则:TPS强调持续改善和追求卓越。
通过制定改善计划、明确改善目标、收集并分析数据、制定改善措施、进行实施和验证等步骤,不断推动流程的改善和创新,提高效率和质量。
- 1、下载文档前请自行甄别文档内容的完整性,平台不提供额外的编辑、内容补充、找答案等附加服务。
- 2、"仅部分预览"的文档,不可在线预览部分如存在完整性等问题,可反馈申请退款(可完整预览的文档不适用该条件!)。
- 3、如文档侵犯您的权益,请联系客服反馈,我们会尽快为您处理(人工客服工作时间:9:00-18:30)。
TPS在广汽丰田物流系统的应用及借鉴意义摘要:丰田汽车公司源于物流平准化的持续改善凝结成TPS,TPS在丰田汽车公司的全面应用使其得到快速发展,全球掀起学习TPS的浪潮。
TPS在广汽丰田物流系统的成功运用,使生产得到有效保障,现场运行有条不紊,做到了安全、质量、环境保护、5S和成本等各方面的精益,有着非常值得学习的地方。
希望本文能为学习TPS的企业和个人有所给力。
1. 引言长期以来,丰田一直将物流管理、营销管理及财务管理等同视之为核心管理技术。
丰田物流企划部的员工自豪地说:“TPS(Toyota Production System,丰田生产体系)的发展史就是一部物流发展的历史。
”日本物流协会前会长、丰田前总经理、现董事长张富士夫(TPS的创始人大野耐一的弟子之一,曾参与创建TPS)曾担任丰田生产管理部物流管理室的第一任室长,由有物流管理从业背景的人出任企业最高管理者在世界汽车界也是绝无仅有的,足见丰田汽车公司对物流的重视和物流在TPS中的重要性。
本文描述的物流系统是指按照采购订单有组织地将零部件从供应商以多种物流服务方式输送至汽车生产工厂指定位置暂时停放及卸货,并有序、准确地向生产车间进行零部件上线,以及完成汽车生产后商品车运输管理的整个物流过程。
广汽丰田汽车有限公司(以下简称GTMC)的物流模式,是基于TPS思想构筑的物流管理体系,用计算机系统辅以人的智慧制定切实可行、精益的物流计划,用最简单和容易理解的方式在最恰当的时间把恰到好处的作业指令在最恰当的场所传递给每一个合格作业人员(即JIT的作业指令,或称恰到好处的作业指令),其形式上可以是指示牌、作业指示书等作业指令和附着在物品或器具上的看板或其他形式的管理道具,很多看板可以及时暴露问题。
当工作条件恰当,工作内容简单、易于执行可以及时发现不良,整个系统的每个人都知道什么时间干什么,工作时间被安排得有条不紊、忙而不乱时,全面彻底的包含各管理要素的标准作业(安全、质量、环境保护、5S和成本等)就能使各方面都做到最精益。
如物流系统的YARD、P链、PC棚、看板等都堪称TPS的经典运用。
在TPS思想的指导下,GTMC得以快速发展,现地(指中国本地)管理人员和员工也得到快速成长。
中外专家根据中国地大物博和消费现状率先开发出“销售·物流整合管理系统”(通称SLIM:Sales Logistics Integrated Management),SLIM旨在将制造物流与营销管理衔接起来,从生产计划到整车制造、下线在库、发车运输、到店交付、客户交车的全过程进行“可视化”管理,该系统正在向丰田全球其他企业进行推广。
现任丰田汽车公司总经理丰田章男将其称为21世纪的看板管理和新一代的TPS。
由此可见,TPS在中国不但可以生存,更可以发展,并为TPS添加新的元素。
2.TPS及其思想在物流系统的表现形式丰田汽车公司于1937年由丰田喜一郎创立,当时日本劳动生产率是美国的1/9,1945年8月15日(日本战败日)丰田喜一郎提出:“要三年赶上美国!否则,日本的汽车工业就建立不起来”。
大野耐一认为:并不是美国人付出了日本人十倍的体力,一定是日本人生产中存在着严重的浪费和不合理现象,需要彻底消除浪费。
他在工厂车间运用工业工程的手法发现很多问题,如原材料到货不均衡导致忙闲不均、不必要的库存、产品质量不合格等,这些问题造成了很多浪费。
通过推进拉动式生产并实施“根据生产计划,用看板及时、准确地下达作业指令,后工序在必要的时间去上工序取必要数量的产品”、“自働化”(绝对不能翻译成“自动化”,“働”原本是中文汉字,丰田赋予的含义见表一)等一系列措施,使问题可视化并得到及时改善,这一改善体系逐步被总结成TPS。
但在TPS使用范围扩大的过程中,因为思想冲突,丰田内部很多部门领导都不理解其思想,甚至到丰田喜一郎处强烈投诉这一管理体系。
结合劳资纠纷等原因丰田喜一郎主动辞职承担了“高层干部的责任”,并承揽了针对大野耐一的指责使其能顺利展开工作。
直到1963年,借着丰田推进TQM的东风,时任副总经理的大野耐一才在工厂、经销商、供应商全面推行TPS,前后花了20年时间。
自上世纪七十年代起,日本经济长期处于低增长状态,但在全面应用TPS19年之后,1982年丰田汽车公司却取得了骄人的业绩,劳动生产率是通用的9.17倍,人均利润是通用的10倍。
此时TPS引起了全世界的关注,丰田因此成为日本制造业的标杆,引领日本经济快速发展,大野耐一在日本也被冠以“日本复活之父”、“生产管理的教父”等桂冠。
表1:丰田对TPS的定义丰田对自働化的解释:赋予机器人的智慧(带发现异常自动停止装置的机器)。
因为很多工作由人完成,笔者添加解释:赋予人机器的标准化能力。
(历史故事:丰田汽车公司的前身是丰田喜一郎的父亲丰田佐吉先生创立的丰田纺织公司,丰田佐吉先生为了解决其母亲手动织布的痛苦发明了自动织布机极大地提高了生产效率,但断纱没有及时发现会造成大量废品,因而发明了自动发现断纱并停机的装置。
该故事成为自働化和如同对待父母般对待顾客的原型)笔者对表1中“必要”的认识是“恰到好处”。
为了使文章简捷和连贯,以下保留“必要”的表述。
TPS 中Just In Time不仅仅包含时间上的恰到好处,还包括为了准时生产所需要的产品、数量、场所等要素的“恰到好处”。
笔者也把JIT解读为“如同锦囊妙计般完美的恰到好处”。
TPS思想的关键词在物流系统中的解读有如下几点:□顾客至上在GTMC中,上工序视下工序为顾客(简称“上工序、下工序”),即不仅消费者是顾客,销售店也是GTMC的顾客,甚至供应商、物流服务商也是顾客。
各部门、各级管理人员都要站在下级、下工序,最终站在作业人员能够有效工作的立场去思考、展开工作、培训作业人员并为作业人员创造必要的工作条件和下达JIT 的作业指令,像对待顾客一般服务于作业人员。
顾客至上的理念,在GTMC的生产、销售及物流系统以“上工序、下工序”的形式得到了充分的体现。
按照交付产品或服务的流程绘制的上、下工序很容易理解,供应商→GTMC→销售店→顾客,但各工序正常运作又必须有必要的前提条件,以信息传递流程为例,与前述流程正好相反:顾客→销售店→GTMC→供应商、物流服务商等,此时GTMC是供应商、物流服务商的上工序,要用“顾客至上”的理念服务于供应商、物流服务商。
GTMC要求每个物流单元在物流起始的时刻就做出可以清晰指导该物流单元所有下工序的物流作业看板。
如供应商的零部件装车前就要按照GTMC的要求,对每个EU箱做看板,指示以EU箱为物流单元全过程的物流活动,EU箱捆绑成托时即做出托看板,指示以托为物流单元全过程的物流活动,飞翼挂车以“便次号(便:卡车往返运输一趟,通常翻译成便)”的方式加以管理。
整车物流的物流单元是单台商品车,在物流开始即发行“物流管理票”(看板)与商品车的VIN一一对应,指导所有下工序进行必要的操作,直至到达销售店。
看板同时体现了“上工序、下工序”和“彻底消除浪费”的思想。
管理人员是直接作业人员的上工序,管理人员要用“顾客至上”的理念服务于作业人员,直接作业人员接受的作业指令必须是JIT的作业指令才能确保有序的作业和工作质量。
从此意义上讲,上级是下级的上工序,才不难理解“出了问题管理者先检讨”的思考方式。
□彻底消除浪费物流系统的浪费涵盖人的浪费(不能充分发挥人的智力、能力和改善积极性)和现场的七种浪费【不良品的浪费、库存的浪费、动作的浪费、搬运的浪费、等待的浪费、制造过多(早)的浪费、加工的浪费】,要做到高品质的物流,并在物流系统彻底消除一切浪费,需要平准化的、周期短、循环往复、高效、可以灵活对应变化的简单标准作业,同时辅以JIT的作业指令,才能消除无效的工作并在有效工作时间内提高稼働率(稼働率=工作日有效工作时间/工作日时间,这里不但强调工作,更强调“品质·智慧”的有效工作),才能实现有质量的低成本。
可以看见的浪费容易消除,看不见的浪费是最可怕也是最难入手的,GTMC全面采用可视化管理,暴露各种问题并加以解决,是问题意识的完美体现[7]。
□自働化自働化也称之为自工序完结,物流系统的每一个工序都必须做到自工序完结,包含“良品条件”和“标准作业”两部分。
其中,“良品条件”是优化工作流程及工作的设计使工作简单化、为作业人员提供必要的标准作业培训和包含机器、物料、工作方法、环境等要素的工作条件,下达JIT的作业指令,自工序能够发现并消除不良;“标准作业”是通过良品条件、作业观察、激励等一系列活动,使所有过程的作业彻底标准化,人人都能在规定的时间完成确保安全、质量、5S等的作业。
在PDCA的任何阶段发现自工序完结的不足,都可以作为改善的切入点。
GTMC有着确保安全为前提品质最优先的基本方针,一系列自働化的措施确保了物流品质的稳定和无差错。
□准时生产(JIT)平准化的准时化生产是TPS最具有挑战性的内容之一,准时化生产的发展基础是物流系统的发展。
准时化生产的前提是高品质和平准化,平准化是使所有的工作平均分布,平均得越精益,越能体现其好处,月度工作平准化到每天,再将每天的工作拆分成恰当的单元,对于每个单元的工作在同一场地投入相同的设备和人员,在物流系统各环节实施JIT的信息传递和下达JIT的作业指令,均衡、不断重复地工作,提高人、设备和场地的使用效率,从而实现平准化的准时化生产。
物流全过程的自働化加上准时化生产,消除了物流质量不合格、忙闲不均的现象,同时消除了库存和作业等浪费,达到彻底消除浪费的目的,实现顾客至上的根本理念。
3.GTMC发展历程及物流系统概述GTMC成立于2004年9月1日,是由广州汽车集团股份有限公司和丰田汽车公司共同投资建设和经营的企业,2006年投产当年,创造了产销双双超过61000辆的佳绩,此后,产销额一直保持良好增势。
2011年8月4日迎来第100万辆整车,成为最快实现百万辆下线的企业之一。
可见,坚实的物流系统根基,为GTMC的快速发展提供了基础。
笔者认为,基于TPS思想确定物流系统的基本原则包括周期性、周期短、高效率、柔性。
物流系统的理想状态是:构筑满足顾客需求的体制,追求安全事故为零、无运输损坏、差错和延迟,遵守先进先出的原则,并追求环境保护和低成本。
构筑“JIT、可视化、简单化、循环往复”的物流作业体系,通过减少在库、少人化、少器材、少场地化、少物流动线、提高车辆装载率和运行效率等措施,达到降低成本的目的。
GTMC的物流系统由零部件物流系统和整车物流系统两大部分组成。
其中,零部件物流系统支撑着供应链的输入体系,整车物流系统构筑起供应链的输出体系。
零部件物流系统分为厂外物流系统与厂内物流系统两大领域。
厂外物流系统是指工厂受入口以外所有的零部件物流,包括供应商的集货和空箱返回、中继地的中转、中继地—YARD、YARD—工厂受入口的交付等。