GM RT2149 Iss 1 Kinematic Gauging Requirements for Railway Vehicles
EAO 紧急停止开关白皮书说明书

Emergency stop switches, generally referred to as E-Stops, ensure the safety of persons and machinery and provide consistent, predictable, failsafe control response. A wide range of electrical machinery must have these specialized switch controls for emergency shutdown to meet workplace safety and established international and U.S. regulatory requirements. E-Stops – critical human machine interface (HMI) devices – differ from simple stop switches (that merely turn equipment off) in that they offer “foolproof” equipment shutdown. This is accomplished through advanced switch design that requires a twist, pull, or key to release electrical contacts to allow machinery restart.E-Stops are generally designed for failsafe operation so the stop command has priority over the sustaining function. This has led to innovative switch designs that prevent “blocking” (wanton or accidental obstruction of the actuator with foreign objects) and “teasing” (which could result in premature or unreliable action). Switch companies also are developing new solutions to problems that arise when contact block and actuator are improperly installed or separated because of vibration or other malfunction. Safe Emergency StoppingAccording to international standards, the emergency stop function must be initiated by a single human action using a manually actuated control device. The E-Stop function mustbe operational at all times and designed to stop the machine without creating additional hazards.Resetting the electrical system can only be done by first releasing the E-Stop that was originally activated. If E-Stops were activated at multiple locations, all must be released before machinery restart. It should be noted that resetting E-Stops does not in itself restart the machinery; it only permits restarting through normal procedures appropriate for the machinery involved. Ergonomic, electrical, mechanical, and color requirements for E-Stops are quite specific. The E-Stop control, commonly a distinctive pushbutton switch or “mushroom type” pushbutton (although wires, ropes, bars, handles, or foot pedals are sometimes employed), must use direct mechanical actionwith mechanical latching. When the E-Stop is activated (pushed), it permanently opens the electrical contacts through a latching mechanism. To close the electrical contacts and allow machinery restart, the E-Stop actuator must be manually unlatched with a twist or a key release. Some E-Stop actuators can simply be pulled to close the electrical contacts.This approach may be less desirable from a safety standpoint than a twist or key release, which requires a more deliberate action by an operator.Designers should be aware of international and U.S. standards and regulations that impact the design and use of E-Stops.Emergency Stop SwitchesJoseph Torzillo, VP Sales, HMI ComponentsLance A. Scott, President, EAO Switch CorporationPicture Picture(grayscale)E-Stops are critical to the human machine interface (HMI).Selecting the Right E-Stopfor Your ApplicationBecause of the confusing array ofE-Stops available, it is important to understand the design basics that contribute to high-quality, ergonomic switch design. EAO is a leader in HMI Components and Systems, including innovative, rugged, reliable, and affordable E-Stops that meet or exceed international and U.S. standards. One of the first steps is determiningwhere the E-Stop fits within your machine control system and whether your particular application requires Category 0 or Category 1 type emergency shutdown. The intended application often determines the placement, size, electrical specifications, mechanical characteristics, ergonomics, color/legends, and number of E-Stops required. So a thorough understanding of the machinery and associated control systems is key to making the right E-Stop choice.A second, and equally important step, is determining what international and U.S. standards, performance ratings, and codes apply for your application. Requirements vary by industry segment, so standards for E-Stops used on transportation vehicles may differ significantly from those used on process machinery or medical equipment and will be governed by different regulatory bodies specific to those segments. Regulatory bodies may also specify size, color, legend, contact terminals, etc.It is then useful to construct or consultan existing E-Stop series selector chart (often supplied by vendors). For example, EAO provides a chart that allows easy comparison of key design factors(see Figure 2). You can select panel opening size, type of actuator, type andnumber of contact blocks, connectors,colors, and maximum electrical rating tocome up with one or more appropriatemodels.Like many vendors, EAO provides specialenclosures, switch guards, palm guards,custom labeling, and other accessories tocomplete virtually any E-Stop application.Some accessories may be specified byindustry standards, such as the SEMIstandards for semiconductor fabricationequipment that mandate the use of palmguards. EAO and other vendors also offerservices to assist customers in the design,engineering, and production of HMISystems, integrating E-Stops.Designed for rough dutyRobust, heavy-duty construction is thehallmark of the original 22.5 mm switches.Many, like the EAO Series 04 E-Stops,have stackable contact blocks, optionalkey release actuators, and mountingoptions for 22.5 mm panel openings. ThisEAO series is rated at up to 10 A, 600VAC, has silver contacts with availablegold over silver or silver over palladiumcontacts, and silver-plated screw terminalswith available quick-connect terminals.Smaller mounting footprintModern applications often demanda slimmed down E-Stop with 16 mmmounting. Innovative products, like theEAO Series 61, are now available with anactuator shape that prevents blockagefrom foreign objects, a black indicatorring visible from long distances, andavailable key release actuators. This EAOseries is rated at 5 A, 250 VAC, and has achoice of silver or gold contacts, screw orsolder quick-connect terminals.An E-Stop must be initiated by a single human action using a manual control device.A 22.5 mm switch must be durable and rugged.T oday’s applications often require a slimmer footprint.12345Figure 1 – Parts of an E-StopShort behind-panel depthNewer electronic applications are requiring E-Stops with shorter behind-panel depth. EAO’s Series 84 E-Stop,for example, features a very short behind-panel depth (18 mm maximum), single “mono-block” construction, 22.5 mm mounting, and available LED illumination that is visible from the side as well as front of the actuator. This series is rated at 3 A, 120 VAC and 1.5 A, 240 VAC, has gold contacts, quick-connect/solder printed circuit board terminals, and ribbon cable terminals.ApplicationsVirtually all industry segments – from machinery, instrumentation, medical treatment and diagnostic, lifting/ moving, and transportation – mandateE-Stops for safe operation. Designers need to have a thorough knowledge ofE-Stop fundamentals, E-Stop switch characteristics and capabilities, and the international and U.S. standards and compliance requirements that apply to their application areas.E-Stops are required on all machinery independent of the type of energy used to control the function, except for ma-chines in which an E-Stop function would not lessen the risk. An E-Stop switch is intended to be one part of a compre-hensive safety system, so the equip-ment designer must also consider safetyfunctions, such as reversal or limitationof motion, deflection, shielding, braking,or disconnecting, that are not specificallyaddressed in this paper. Primary applica-tion areas where electrical machineryis safeguarded with E-Stop technologyinclude:MetalworkingWood productionTextile productionFood processingPrintingMedical laser & x-ray equipmentPackaging equipmentSemi-fab equipmentPumpingLifting/moving equipmentPlastics & rubber processingMaterials handlingElectronic production equipmentPaper & cardboard productionInspection/testing equipmentCompressorsLaundry/dry cleaning facilitiesTransportationConstruction/building materialsX-ray EquipmentCabinet x-ray systems used fordiagnostic and therapeutic medicalapplications, industrial non-destructiveinspection and thickness gauging,security inspection of baggage, andother imaging are closely regulated foroperational safety. E-Stops are coveredby standards and regulations of theFDA Department of Health and HumanServices. The key document is CFR Title21, Part 1020 – Performance Standardsfor Ionizing Radiation Emitting Products,section 40, which requires accessibleemergency stop switches and keyedlock-out switches to disable the system.Semiconductor ManufacturingSemiconductor chips used in electricaland electronic devices are fabricatedthrough a sequence of photographicand chemical processing steps. Theprocess includes lithography, steppers,etching, and deposition equipment. Thecomplex process is governed by specificoperational and safety guidelines setdown by SEMI, a trade organization ofsuppliers of equipment and materialsused in the fabrication of semiconductordevices. SEMI S2-93 makes a cleardistinction between emergency off (EMO)switches and E-Stops, requiring the latterto be clearly distinguishable from EMOsthrough the use of color (red), actuatorshape (extended not mushroom), andlabeling (“Emergency Stop”). It alsospecifies that E-Stops should stop allhazardous mechanical motion at theequipment interface, but not shut offMedical imaging E-Stops are closely regulated.In semiconductor manufacturing, there are strictguidelines set by the SEMI trade organization.E-Stops may require shorter behind-panel depth.associated equipment.Overhead and Gantry CranesThese large lifting and moving devices may have a gantry mounted cab which includes an E-Stop on the operator console. Smaller overhead cranes usually have a wired or wireless pendant control operated from ground level. The pendant includes an E-Stop. The chief regulating body for these massive devices is the Occupational Safety and Health Administration. OSHA 29 CFR 1910.179 (a)(59) defines “emergency stop switch” as a manually or automatically operated electric switch to cut off electric power independent of the regular operating controls. Another section, 9 CFR 1910.179(a)(61) defines “main switch”as a device controlling the entire power supply to the crane.U.S. Standards for E-Stops Occupational Safety and Health Administration (OSHA) – Standards –29 CFR (Code of Federal Regulations); OSHA 1910American National Standards Institute (ANSI) – B11, Electrical and Mechanical Equipment GuidelinesANSI/NFPA (National Fire Protection Association) – 79, Electrical Standardsfor Industrial MachineryUnderwriters Laboratories Inc. (UL) –Category NISD, Emergency Stop DeviceFood and Drug Administration,Department of Health and HumanServices, Subchapter J – RadiologicalHealth: CRF Title 21, Part 1020,Performance Standards for IonizingRadiation Emitting ProductsOther Complianceand Rating BodiesMost quality E-Stop switches, includingthose made by EAO, are RoHS andREACH compliant, meet cUL (CanadianUL) requirements, and TÜV (TechnischerÜberwachungsverein, a German safetymonitoring agency), SEV (a Swissdesignation) and CE (European Union)approvals.Depending on design and applicationrequirements, many E-Stops are listedas UL category NISD emergencystop devices. This rating covers twocategories of E-Stop function as definedin ANSI/NFPA 79, Electrical Standardsfor Industrial Machinery (ANSI is theAmerican National Standards Instituteand NFPA is the National Fire ProtectionAssociation):1. Stop Category 0 – Immediate removalof power to the machine or mechanicaldisconnection (de-clutching) of hazardouselements.2. Stop Category 1 – Controlled stopwith power available to stop the machinefollowed by removal of power when thestop is achieved.The emergency stop actuator providedin these devices must be a self-latchingtype. E-Stops with this rating have beenreviewed for their functionality in additionto fire and electric shock safety.ISO 13850 (formerly EN418)Max rating: 5 A/250 VACMax rating: 3 A/250 VACE-Stops can be mounted on a console or on awireless pendant.Figure 3 – International standards that apply to Emergency Stops vs. Stop SwitchesFuture of the TechnologyThe pace of change in E-Stop technology is steady, not revolutionary. By their nature, these devices must be recognizable, reliable, and rugged. They have a straightforward function: instantly shut down equipment witha simple push of a (usually) bright red actuator. For safety, reactivation of the switch requires twisting or pulling the actuator by hand or, for even more security, unlocking it with a key beforemachinery can be restarted. Established standards, function, and familiarity dictate a certain beneficial inertia in new E-Stop developments.Many advances are driven by norm changes for E-Stops, such as DIN EN ISO 13850: 2008 that now requires mechanical latching and manual resetting of E-Stops. Most researchand development is aimed at improving the safety and reliability of the switches themselves and expanding their roles as lockout devices in some worker safety applications.One area of current interest is making sure that the E-Stop itself will “failsafe” should the actuator and contact block be separated. The contact block has normally closed contacts that allow power to flow to the machinery. Pushingan E-Stop separates the spring-loadedcontacts, and mechanical latching keepsthem open, stopping the machinery. Butwhat happens if the actuator separatesfrom the contact block or the latchingmechanism fails?Separation of the contact block from theactuator renders an E-Stop ineffective.Current solutions include mono-blockor unibody switches with a one-pieceactuator/contact block, as well asswitches with failsafe contact blocks thatautomatically cause machinery shutdownif the actuator and contact block areseparated.Other advances are application-driven.EAO’s Series 84 E-Stops, for example,were developed for hand-held enclosureswith slim behind-panel depth for roboticsapplications. These versatile E-Stopsalso are used in pendant controls forlifting and moving machinery. Applicationrequirements have also created a widevariety of available optional features andaccessories for most E-Stop products –illumination, protective rings, enclosures,guards, legend plates, etc. – that addto the functionality and safety of E-Stopinstallations.E-Stops will continue to evolve to meetnew standards and new applications.For designers, the most importantconsiderations in making the right designdecisions are a thorough understandingof E-Stop function; a grounding in thestandards, codes, and compliancesinvolved; proper selection of devicesthat meet or exceed the applicationrequirements.Once you understand the E-Stop function and relevant standards, codes, and compliances you candetermine the appropriate device.Emergency Stop Switches J. T orzillo, L. ScottEAO Switch Corporation98 Washington StreetMilford CT 06460T: (203) 877 4577F: (203) 877 3694E-mail:*******************Member of the EAO Group。
Extreme Networks SLX 9640高性能固定路由器商品介绍说明书
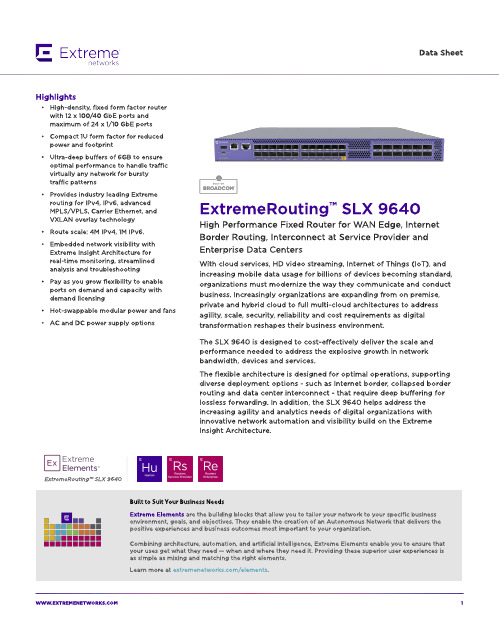
ExtremeRouting? SLX 9640
Built to Suit Your Business Needs Ext rem e Elem ent s are t he b uild ing b locks t hat allow you t o t ailor your net w ork t o your sp ecific b usiness environm ent , g oals, and ob ject ives. They enab le t he creat ion of an A ut onom ous Net w ork t hat d elivers t he p osit ive exp eriences and b usiness out com es m ost im p ort ant t o your org anizat ion.
W W W.EXTREMENETW
1
Flexib le Bo rd er Ro ut ing w it h Int ernet Scale, Ult ra-Deep Buffers,
MPLS and EVPN
The SLX 964 0 is a very p ow erful com p act d eep b uffer Int ernet b ord er rout er, p rovid ing a cost -efficient solut ion t hat is p urp ose-b uilt for t he m ost d em and ing service p rovid er and ent erp rise d at a cent ers and MA N/ WA N ap p licat ions. The rob ust syst em archit ect ure sup p ort ed by SLX-OS and a versat ile feat ure set includ ing IPv4 , IPv6, and MPLS/ VPLS w it h Carrier Et hernet 2.0 and OA M cap ab ilit ies t o p rovid e d ep loym ent flexib ilit y.
无线网络技术在医院信息化建设中的应用

I G I T C W技术 应用Technology Application116DIGITCW2024.011 无线网络技术在医院信息化建设中应 用的重要性无线网络技术在医院信息化建设中的重要性主要体现在以下几个方面。
首先,无线网络技术可以大大提升医院的信息化水平。
传统的有线网络虽然稳定性较高,但需要铺设大量的网络线路,且线路的管理、维护成本较高。
而采用无线网络技术则不需要铺设大量的网络线路,便于网络的搭建和管理,可以更快速地推进医院信息化建设。
无线网络技术可以支持医院各种信息化应用,如电子病历、医疗影像、医院管理等。
这些信息化应用的实现将大大提高医院工作的效率和精确度,从而为医疗服务提供更好保障[1]。
其次,无线网络技术可以提高医院服务的质量。
医院中需要各类医疗设备进行监测和数据传输,这些医疗设备如果能够实现无线联网,便可以大大提高数据传输的效率和准确性。
此外,无线网络技术还可以支持远程医疗服务,如远程会诊、远程监护等。
这些服务的实现将大大方便患者就医,缓解患者看病难、看病贵等问题,同时也可以使医生更加高效地为患者服务,提高医院的服务质量和声誉。
最后,无线网络技术可以降低医院信息化建设的成本。
医院信息化建设需要大量的投资,无线网络技术的采用可以减少网络线路的铺设,降低网络建设的成本。
同时,无线网络技术还可以实现设备的远程监测和管理,大大降低设备的管理成本。
此外,无线网络技术可以支持医院各类移动办公,如移动护士站、移动护理等,可以更加灵活地为患者提供服务,并降低医院建设和管理的成本。
总之,无线网络技术在医院信息化建设中的应用是非常重要的。
它可以提升医院的信息化水平、提高医院的服务质量、降低医院信息化建设的成本,为医院信息化建设和医疗卫生事业的发展做出重要的贡献。
因此,要在实际的医院信息化建设中,大力推广无线网络技术,将其应于医院的各项业务,以有效提升医院无线网络技术在医院信息化建设中的应用林 虹1,许艺南2(1.厦门大学附属第一医院,福建 厦门 361001;2.智业软件股份有限公司,福建 厦门 361001)摘要:随着无线网络技术的不断发展,我国各大医院正在逐步推进信息化建设。
SIGALARM Model 210 MicroGuard 414 MicroGuard 414错误
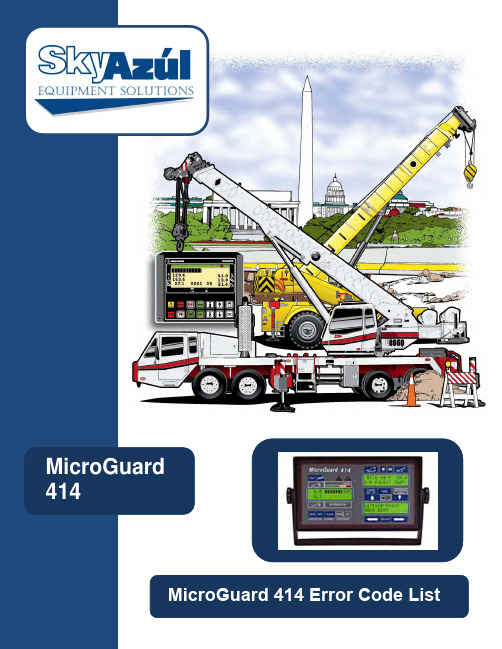
SkyAzúl, Equipment Solutions301-371-61261FAULT REPORTING AND FAULT CODESSystem Fault Codes provide one of the most important ways to quickly locate and assess problems in your MicroGuard ®System. Please review this section carefully.FAULT DIAGNOSTIC PROCEDURESEach time the System is turned on, it goes through a self-testing process lasting two to three seconds that automatically detects any Faults in the System. During normal operation, a Self-Test can be initiated at any time by pressing the TEST button on the Display Console. Fault conditions in external sensors are detected without a System Self-Test.Faults detected in the System during Self-Test, are indicated on the Display Console in the following way:•The word FAULT will appear in the information area of the left Display.•The RED LAMP will illuminate and the AUDIBLE ALARM will sound.Diagnosis of a Fault is obtained by PRESSING and HOLDING the TEST button. The System will then go through a Self-Test followed by the appearance of a Fault Code screen. The Fault Code screen will remain visible as long as the TEST button is pressed. Information will be displayed on the screen in the four groups shown in Figure 5.0.Note: Always repair Analog Sensor Faults (AAA) prior to investigating other faults. A complete listing of all possible Fault Codes and the description of each is listed on the following pages.000 NO FAULTS001TX.0PISTON PRESSURE SENSOR002 TX.1 ROD PRESSURE SENSOR 004 AIN2 EXTENSION SENSOR 008 AIN3 BOOM ANGLE SENSOR 016 AIN4 S’STRUCTURE ANGLE SENSOR 032 AIN5 SWING POTENTIOMETER “A” 064AIN6SWING POTENTIOMETER “B”Group AAA Analog Sensors0 NO FAULTS1 1 DIGITAL INPUT AND OUTPUT2 2 ANALOG INPUT AND OUTPUT44DISPLAY UNITGROUP B IO FAULTS00 NO FAULTS 01 1 PROGRAM ROM 02 2 DUTY ROM 04 4 SCRATCHPAD RAM 088PERSONALITY ROMGROUP CC MEMORY FAULTS00 NO FAULTS 01 1 NO DUTY FOUND 022CURRENT DUTY BADGROUP DD GENERAL FAULTSFIGURE 5.0 FAULT CODES2SkyAzúl, Equipment Solutions 301-371-61263018 Fault 002 & 016 019 Fault 001, 002, & 016 020 Fault 004 & 016 021 Fault 001, 004, & 016 022 Fault 002, 004, & 016023 Fault 001, 002, 004, &016 024 Fault 008, & 016025 Fault 001, 008, & 016026 Fault 002, 008, & 016027 Fault 001, 002, 008, &016028 Fault 004, 008, & 016 029 Fault 001, 004, 008, &016 030 Fault 002, 004, 008, &016 031 Fault 001, 002, 004,008, & 016 032 Swing Pot “A” 033 Fault 001, & 032 034 Faults 002, & 032035Faults 001, 002, &AAA Fault Codes continuedFAULT No . DESCRIPTION036 Faults 004 & 32 037 Faults 001, 004, &032 038 Faults 002, 004, &032 039 Faults 001, 002, 004, & 032 040Faults 008, & 032 041 Faults 001 008, &032 042Faults 002, 008, &032 043Faults 001, 002, 008, & 032 044Faults 004, 008, &032 045Faults 001, 004, 008, & 032 046 Faults 002, 004, 008, & 032 047 Faults 001, 002, 004, 008, & 32048 Faults 016 & 032 049Faults 001, 016, &032 050 Faults 002, 016, &032 051 Faults 001, 002, 016, & 032 052Faults 004, 016, &AAA Fault CodesFAULT No. DESCRIPTIONFigure 5.2 AAA Analog Sensor Fault CodesNumbers 1-127 continuedSkyAzúl, Equipment Solutions 301-371-61264053 Faults 001, 004, 016,& 32 054 Faults 002, 004, 016,& 32 055 Faults 001, 002, 004,016, & 32 056 Faults 008, 016, &032 057 Faults 001, 008, 016,& 032 058 Faults 002, 008, 016,& 032 059 Faults 001, 002, 008,016, & 032 060 Faults 004, 008, 016,& 032 061 Faults 001, 004, 008,016, & 032 062 Faults 002, 004, 008,016, & 032 063 Faults 001, 002, 004, 008, 016, & 032 064 SWING POT “B” 065 Faults 001 & 064 066 Faults 002 & 064 067 Faults 001, 002, &064 068 Faults 004 & 064 069 Faults 001, 004, &064 070 Faults 002, 004, &064 071Faults 001, 002, 004,AAA Fault Codes continuedFAULT No . DESCRIPTION072 Faults 008, & 64 073 Faults 001, 008, & 64 074 Faults 002, 008, &064 075 Faults 001, 002, 008,& 064 076 Faults 004, 008, &064 077 Faults 001, 004, 008,& 064 078 Faults 002, 004, 008,& 064 079 Faults 001, 002, 004,008, & 064 080 Faults 016 & 064 081 Faults 001, 016 & 064 082 Faults 002, 016 & 064 083 Faults 001, 002, 016& 064 084 Faults 004, 016, &064085 Faults 001, 004, 016,& 064 086 Faults 002, 004, 016,& 064 087 Faults 001, 002, 004,016, & 064 088 Faults 008, 016, &064 089 Faults 001, 008, 016,& 064 090Faults 002, 008, 016,AAA Fault Codes continuedFAULT No . DESCRIPTIONFigure 5.2 AAA Analog Sensor Fault CodesNumbers 1-127 continuedSkyAzúl, Equipment Solutions301-371-61265091 Faults 001, 002, 008,016, & 064 092 Faults 004, 008, 016,& 064 093 Faults 001, 004, 008,016, & 064 094 Faults 002, 004, 008,016, & 064 095 Faults 001, 002, 004, 008, 016, & 064 096 Faults 032, & 064 097 Faults 001, 032, &064 098 Faults 002, 032, &064 099 Faults 001, 002, 032,& 064 100 Faults 004, 032, &064 101 Faults 001, 004, 032,& 064 102 Faults 002, 004, 032,& 064 103 Faults 001, 002, 004,032, & 064 104 Faults 008, 032, &064 105 Faults 001, 008, 032,& 064 106 Faults 002, 008, 032,& 064 107 Faults 001, 002, 008,032, & 064 108 Faults 004, 008, 032,& 064 109Faults 001, 004, 008,AAA Fault Codes continuedFAULT No . DESCRIPTION110 Faults 002, 004, 008,032, & 064 111 Faults 001, 002, 004, 008, 032, & 064 112 Faults 016, 032, &064 113 Faults 001, 016, 032,& 064 114 Faults 002, 016, 032,& 064 115 Faults 001, 002, 016,032, & 064 116 Faults 004, 016, 032,& 064 117 Faults 001, 004, 016,032, & 064 118 Faults 002, 004, 016,032, & 064 119 Faults 001, 002, 004, 016, 032, & 064 120 Faults 008, 016, 032,& 064121 Faults 001, 008, 016,032, & 064 122 Faults 002, 008, 016,032, & 064 123 Faults 001, 002, 008, 016, 032, & 064 124 Faults 004, 008, 016,032, & 064 125 Faults 001, 004, 008, 016, 032, & 064 126 Faults 002, 004, 008, 016, 032, & 064 127Faults 001, 002, 004,AAA Fault Codes continuedFAULT No . DESCRIPTIONFigure 5.2 AAA Analog Sensor Fault CodesNumbers 1-127 continuedSkyAzúl, Equipment Solutions 301-371-612660 No Faults1Digital Input and 2 Analog Input andOutput 3 Faults 1 & 2 4 Display Unit 5 Faults 1 & 4 6 Faults 2 & 47Faults 1, 2, & 4FAULT No .DESCRIPTION 00 No Faults01 Program ROM 02 Duty ROM 03 Faults 01 & 02 04 Scratchpad RAM 05 Faults 02 & 03 06 Faults 02 & 04 07 Faults 01, 02, & 04 08 Personality ROM 09Faults 01, & 08 10Faults 02 & 08 11Faults 01, 02, & 08 12Faults 04 & 08 13Faults 01, 04, & 08 14 Faults 02, 04, & 0815Faults 01, 02, 04, &FAULT No .DESCRIPTION 0No Faults01No Duty02 Current Duty Bad03Faults 01 & 02FAULT No .DESCRIPTIONFigure 5.3 B IO Fault CodesFigure 5.5 DD General Fault CodesFigure 5.4 CC Memory Fault Codes。
MXconfig系列工业网络配置工具说明书
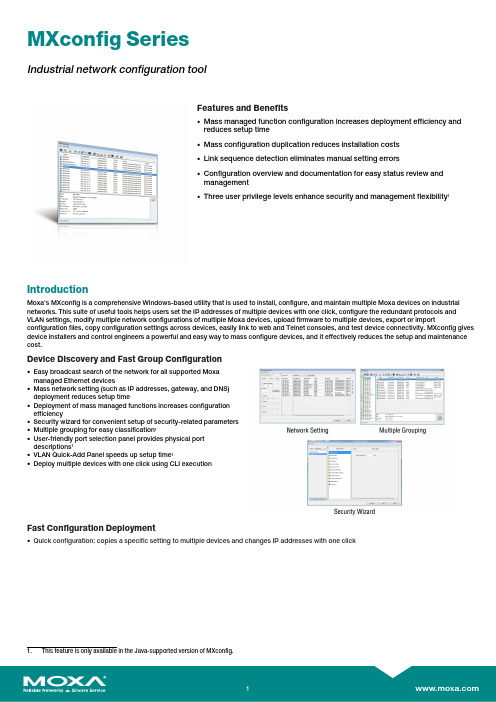
MXconfig SeriesIndustrial network configuration toolFeatures and Benefits•Mass managed function configuration increases deployment efficiency andreduces setup time•Mass configuration duplication reduces installation costs•Link sequence detection eliminates manual setting errors•Configuration overview and documentation for easy status review andmanagement•Three user privilege levels enhance security and management flexibility1IntroductionMoxa’s MXconfig is a comprehensive Windows-based utility that is used to install,configure,and maintain multiple Moxa devices on industrial networks.This suite of useful tools helps users set the IP addresses of multiple devices with one click,configure the redundant protocols and VLAN settings,modify multiple network configurations of multiple Moxa devices,upload firmware to multiple devices,export or import configuration files,copy configuration settings across devices,easily link to web and Telnet consoles,and test device connectivity.MXconfig gives device installers and control engineers a powerful and easy way to mass configure devices,and it effectively reduces the setup and maintenance cost.Device Discovery and Fast Group Configuration•Easy broadcast search of the network for all supported Moxamanaged Ethernet devices•Mass network setting(such as IP addresses,gateway,and DNS)deployment reduces setup time•Deployment of mass managed functions increases configurationefficiency•Security wizard for convenient setup of security-related parameters•Multiple grouping for easy classification1•User-friendly port selection panel provides physical portdescriptions1•VLAN Quick-Add Panel speeds up setup time1•Deploy multiple devices with one click using CLI executionFast Configuration Deployment•Quick configuration:copies a specific setting to multiple devices and changes IP addresses with one clickLink Sequence Detection•Link sequence detection eliminates manual configuration errorsand avoids disconnections,especially when configuringredundancy protocols,VLAN settings,or firmware upgrades for anetwork in a daisy-chain topology (line topology).•Link Sequence IP setting (LSIP)prioritizes devices and configuresIP addresses by link sequence to enhance deployment efficiency,especially in a daisy-chain topology (linetopology).Unlock Devices and User Privileges•Mass device unlocking and password file export for quick unlocks.•Three user privilege levels to enhance management flexibility and security:Admin,Supervisor,and Operator.2Configuration Overview and Documentation•Useful mass status overview and configuration check for eachmanaged function.•Generate reports on each managed function for multiple devices inthe network.2•Export multiple configuration files with flexible filenames and import multiple configuration files to multiple devices.•Export device list for easy backup,and import device list for quick searching2SpecificationsHardware RequirementsRAM2GB Hardware Disk Space10GB OSWindows 7(32/64-bit),Windows 10(32-64-bit),Windows Server 2012(32/64-bit)CPU 2GHz or faster dual-core CPUSupported DevicesAWK Products MXconfig Java Version:AWK-1121Series(v1.4or higher)AWK-1127Series(v1.4or higher)AWK-1131A Series(v1.11or higher)AWK-1137C Series(v1.3or higher)AWK-3121Series(v1.10or higher)AWK-3121-SSC-RTG Series(v1.4or higher)AWK-3121-M12-RTG Series(v1.4or higher)AWK-3131Series(v1.2or higher)AWK-3131-M12-RCC Series(v1.0or higher)AWK-3131A Series(v1.3or higher)AWK-3131A-RTG Series(v1.8or higher)AWK-4121Series(v1.10or higher)AWK-4131Series(v1.2or higher)AWK-4131A Series(v1.3or higher)AWK-5222Series(v1.7or higher)AWK-5232Series(v1.3or higher)AWK-6222Series(v1.7or higher)AWK-6232Series(v1.3or higher)EDR Products MXconfig Java Version:EDR-810Series(v3.2or higher)EDR-G902Series(v4.2or higher)EDR-G903Series(v4.2or higher)MXconfig Non-Java Version:EDR-810Series(v3.2or higher)EDR-G902Series(v4.2or higher)EDR-G903Series(v4.2or higher)EDR-G9010Series(v1.0or higher)EDS Products MXconfig Java Version:EDS-405A/408A Series(v3.1or higher)EDS-405A/408A-EIP Series(v3.1or higher)EDS-405A/408A-PN Series(v3.1or higher)EDS-405A-PTP Series(v3.3or higher)EDS-505A/508A/516A Series(v3.1or higher)EDS-510A Series(v3.1or higher)EDS-518A Series(v3.1or higher)EDS-510E/518E Series(v4.0or higher)EDS-528E Series(v5.0or higher)EDS-G508E/G512E/G516E Series(v4.0or higher)EDS-G512E-8PoE Series(v4.0or higher)EDS-608/611/616/619Series(v3.1or higher)EDS-728Series(v3.1or higher)EDS-828Series(v3.1or higher)EDS-G509Series(v3.1or higher)EDS-P510Series(v3.1or higher)EDS-P510A-8PoE Series(v3.1or higher)EDS-P506A-4PoE Series(v3.1or higher)EDS-P506E-4PoE Series(v5.5or higher)MXconfig Non-Java Version:EDS-405A/408A Series(v3.1or higher)EDS-405A/408A-EIP Series(v3.1or higher)EDS-405A/408A-PN Series(v3.1or higher)EDS-405A-PTP Series(v3.3or higher)EDS-505A/508A/516A Series(v3.1or higher)EDS-510A Series(v3.1or higher)EDS-518A Series(v3.1or higher)EDS-510E/518E Series(v4.0or higher)EDS-528E Series(v5.0or higher)EDS-G508E/G512E/G516E Series(v4.0or higher)EDS-G512E-8PoE Series(v4.0or higher)EDS-608/611/616/619Series(v3.1or higher)EDS-728Series(v3.1or higher)EDS-828Series(v3.1or higher)EDS-G509Series(v3.1or higher)EDS-P510Series(v3.1or higher)EDS-P510A-8PoE Series(v3.1or higher)EDS-P506A-4PoE Series(v3.1or higher)EDS-P506E-4PoE Series(v5.5or higher)ICS Products MXconfig Java Version:ICS-G7526/G7528Series(v3.1or higher)ICS-G7826/G7828Series(v3.1or higher)ICS-G7748/G7750/G7752Series(v3.1or higher)ICS-G7848/G7850/G7852Series(v3.1or higher)ICS-G7526A/G7528A Series(v4.0or higher)ICS-G7826A/G7828A Series(v4.0or higher)ICS-G7748A/G7750A/G7752A Series(v4.0or higher)ICS-G7848A/G7850A/G7852A Series(v4.0or higher)MXconfig Non-Java Version:ICS-G7826/G7828Series(v3.1or higher)ICS-G7748/G7750/G7752Series(v3.1or higher)ICS-G7848/G7850/G7852Series(v3.1or higher)ICS-G7526A/G7528A Series(v4.0or higher)ICS-G7826A/G7828A Series(v4.0or higher)ICS-G7748A/G7750A/G7752A Series(v4.0or higher)ICS-G7848A/G7850A/G7852A Series(v4.0or higher) IEX Products MXconfig Java Version:IEX-402Series(v1.0or higher)IEX-408E Series(v4.0or higher)MXconfig Non-Java Version:IEX-402Series(v1.0or higher)IEX-408E Series(v4.0or higher)IKS Products MXconfig Java Version:IKS-6726/6728Series(v3.1or higher)IKS-G6524Series(v3.1or higher)IKS-G6824Series(v3.1or higher)IKS-6728-8PoE Series(v3.1or higher)IKS-6726A/6728A Series(v4.0or higher)IKS-G6524A Series(v4.0or higher)IKS-G6824A Series(v4.0or higher)IKS-6728A-8PoE Series(v4.0or higher)MXconfig Non-Java Version:IKS-6726/6728Series(v3.1or higher)IKS-G6524Series(v3.1or higher)IKS-G6824Series(v3.1or higher)IKS-6728-8PoE Series(v3.1or higher)IKS-6726A/6728A Series(v4.0or higher)IKS-G6524A Series(v4.0or higher)IKS-G6824A Series(v4.0or higher)IKS-6728A-8PoE Series(v4.0or higher)ioLogik Products MXconfig Java Version:ioLogik E1200Series(v3.2or higher)ioThinx Products MXconfig Java Version:ioThinx4510Series(v1.3or higher)MDS Products MXconfig Java Version:MDS-G4012Series(v1.1or higher)MDS-G4020Series(v1.1or higher)MDS-G4028Series(v1.1or higher)MXconfig Non-Java Version:MDS-G4012Series(v1.1or higher)MDS-G4020Series(v1.1or higher)MDS-G4028Series(v1.1or higher)MDS-G4012-L3Series(v2.0or higher)MDS-G4020-L3Series(v2.0or higher)MDS-G4028-L3Series(v2.0or higher)MGate Products MXconfig Java Version:MGate MB3170/MB3270Series(v4.2or higher)MGate MB3180Series(v2.2or higher)MGate MB3280Series(v4.1or higher)MGate MB3480Series(v3.2or higher)MGate MB3660Series(v2.5or higher)MGate EIP3270Series(v2.0or higher)MGate5101-PBM-MN Series(v2.2or higher)MGate5102-PBM-PN Series(v2.3or higher)MGate5103Series(v2.2or higher)MGate5105-MB-EIP Series(v4.3or higher)MGate5108Series(v2.4or higher)MGate5208Series(v2.4or higher)MGate5109Series(v2.3or higher)MGate5111Series(v1.3or higher)MGate5114Series(v1.3or higher)MGate5118Series(v2.2or higher)MGate5217Series(v1.0or higher)NPort Products MXconfig Java Version:NPort S8000Series(v1.3or higher)NPort S9000Series(v1.0or higher)NPort5110Series(v3.8or higher)NPort5130/5150Series(v3.8or higher)NPort5000AI-M12Series(v1.4or higher)NPort5200Series(v2.10or higher)NPort5400Series(v3.13or higher)NPort5600Series(v3.9or higher)NPort5100A Series(v1.5or higher)NPort5200A Series(v1.5or higher)NPort5610-8-DT/5610-8-DT-J/5650-8-DT/5650I-8-DT/5650-8-DT-J Series(v2.6orhigher)NPort5610-8-DTL/5650-8-DTL/5650I-8-DTL Series(v1.5or higher)NPort IA5000Series(v1.6or higher)NPort IA5150A/IA5150AI/IA5250A/IA5250AI Series(v1.4or higher)NPort IA5450A/IA5450AI Series(v1.6or higher)NPort6000Series(v1.21or higher)PT Products MXconfig Java Version:PT-7528Series(v3.1or higher)PT-7710Series(v3.1or higher)PT-7728Series(v3.1or higher)PT-7828/7828-PTP Series(v3.1or higher)PT-G7509Series(v3.1or higher)PT-508/510Series(v3.1or higher)PT-G7728Series(v5.4or higher)PT-G7828Series(v5.4or higher)MXconfig Non-Java Version:PT-7528Series(v3.1or higher)PT-7710Series(v3.1or higher)PT-7728Series(v3.1or higher)PT-7828/7828-PTP Series(v3.1or higher)PT-G7509Series(v3.1or higher)PT-508/510Series(v3.1or higher)PT-G7728Series(v5.4or higher)PT-G7828Series(v5.4or higher)TAP Products MXconfig Java Version:TAP-213Series(v1.2or higher)TAP-323Series(v1.8or higher)TN Products MXconfig Java Version:TN-4500A Series(v3.5or higher)TN-5508/5510Series(v3.1or higher)TN-5516/5518Series(v3.1or higher)TN-5916Series(v1.2or higher)MXconfig Non-Java Version:TN-4500A Series(v3.5or higher)TN-4908Series(v1.0or higher)TN-5508/5510Series(v3.1or higher)TN-5516/5518Series(v3.1or higher)TN-5916Series(v1.2or higher)TN-G6500Series(v5.0or higher)VPort Products MXconfig Java Version:VPort26A-1MP Series(v1.2or higher)VPort36-1MP Series(v1.1or higher)VPort P06-1MP-M12Series(v2.2or higher)WAC Products MXconfig Java Version:WAC-1001Series(v2.1or higher)WAC-2004Series(v1.6or higher)©Moxa Inc.All rights reserved.Updated Jul30,2021.This document and any portion thereof may not be reproduced or used in any manner whatsoever without the express written permission of Moxa Inc.Product specifications subject to change without notice.Visit our website for the most up-to-date product information.。
摩托罗拉 accessories 编程软件说明书

Motorola Accessory Programming SoftwareTable of Contents1.Introduction2.What's New in this Release3.Requirements4.Installation and Removal5.Open Issues Summary6.Legal Notice7.Publicly Available Software Legal Notices1. IntroductionThe Accessory Programming Software provides organizations with the ability to upgrade and manage the accessory devices.The Accessory Programming Software application contains an upgrade tool that can be used to upgrade one or multiple accessory devices at a time and a retrieve log tool to retrieve the device logs.2. What's New in this ReleaseVersion Notes1.0Initial release allows a user to upgrade their Mission critical and Operations critical wirelessaccessory devices.2.0This release allows a user to upgrade their XE RSM accessory devices.2.8This release allows a user to upgrade their GPS RSM as well as wireless devices.APS R2.8must beused for firmware upgrade to Mission Critical Wireless R01.04.00and Operations Critical WirelessR01.03.01or later firmware.3.0This release allows a user to upgrade their WRSM accessory devices4.0This release allows a user to recognize the name for Long Range OCW Wireless RSM as OCWWRSM.4.1This release allows a user to upgrade and manage their XE500Model1and Model1.5accessorydevices4.2This release allows a user to set codeplug to enable channel knob position broadcast duringpower up for their accessory devices.4.3This release allows a user to set Volume Channel codeplug for their XE500accessory devices.4.4This release allows a user to set Kodiak Device Operation Mode for their OCW WRSM accessorydevices.4.5This release allows a user to set Kodiak Device Operation Mode for their OCW WPOD accessorydevices.4.6This release allows a user to set the Radio,Wave and Kodiak Device Operation Mode for theirWRSM accessory devices.4.7This release allows a user to set the Send Channel Control Powerup for XVE500,XVP850andVolume Control Feature codeplug for XVE500,XVE NO KNOB,XVP850/830,XVN500RSMaccessory devices for FDNY support.4.8This release allows a user to upgrade XV RSM(PMMN4123A and PMMN4145A)accessorydevices.4.9This release fixes the XE500Model1volume configuration missing in version4.8and allows auser to disable over temperature reporting status for XVN500RSM accessory devices.4.10This release allows a user to set Volume and Channel codeplug for their XVE DIV1accessorydevices.4.11This release allows a user to set Extra Loud Earpiece Compatible codeplug for their WM800accessory devices.3. RequirementsOperating Systems●Microsoft®Windows®7Home/Professional Edition●Microsoft®Windows®8.1Home/Professional Edition●Microsoft®Windows®10Home/Professional EditionNote●Please see the application help file for information on how to use the Accessory Programming Software4. Installation and RemovalInstallationAdministrative rights on the PC in which the software is to be installed are required.To download the Accessory Programming Software,please visit the Motorola Solutions MOL website.After downloading the software,please refer to the“APS User Guide.pdf”for instructions to install the software.If a previous version of Accessory Programming Software has already been installed,please remove the software first and install the new software.RemovalIn the Control Panel,select the"Programs and Features"option.Select the Accessory ProgrammingSoftware item from the list of programs and click the Uninstall button.5. Open Issues SummaryOn rare occasion,after completion of the firmware upgrade user may get the following WARNING:"The device has been upgraded successfully but fails to reset.Please disconnect and reconnect the USB cable to reset the device."User can IGNORE this warning since the device was upgraded successfully.6. Legal NoticeMotorola Solutions is a registered trademark of Motorola Solutions,IncMicrosoft®and Windows®are registered trademarks of Microsoft Inc.7. Publicly Available Software Legal NoticesThis media,or Motorola Solutions Product,may include Motorola Solutions Software,Commercial Third Party Software,and Publicly Available Software.The Motorola Solutions Software that may be included on this media,or included in the Motorola Solutions Product,is Copyright(c)by Motorola Solutions,Inc.,and its use is subject to the licenses,terms and conditions of the agreement in force between the purchaser of the Motorola Solutions Product and Motorola Solutions,Inc.The Commercial Third Party Software that may be included on this media,or included in the Motorola Solutions Product,is subject to the licenses,terms and conditions of the agreement in force between the purchaser of the Motorola Solutions Product and Motorola Solutions,Inc.,unless a separate Commercial Third Party Software License is included,in which case,your use of the Commercial Third Party Software will then be governed by the separate Commercial Third Party License.The Publicly Available Software that may be included on this media,or in the Motorola Solutions Product,is listed below.The use of the listed Publicly Available Software is subject to the licenses,terms and conditions of the agreement in force between the purchaser of the Motorola Solutions Product and Motorola Solutions,Inc.,as wellas,the terms and conditions of the license of each Publicly Available Software package.Copies of the licenses for the listed Publicly Available Software,as well as,all attributions,acknowledgements,and software information details,are included below.Motorola Solutions is required to reproduce the software licenses,acknowledgments and copyright notices as provided by the Authors and Owners,thus,all such information is provided in its native language form,without modification or translation.For instructions on how to obtain a copy of any source code being made publicly available by Motorola Solutions related to software used in this Motorola Solutions Product you may send your request in writing to:Motorola Solutions,INC.Government&Public Safety BusinessPublicly Available Software Management1301E.Algonquin RoadSchaumburg,IL60196USA.In your request,please include the Motorola Solutions Product Name and Version,along with the Publicly Available Software specifics,such as the Publicly Available Software Name and Version.Note,the source code for the Publicly Available Software may be resident on the Motorola Solutions Product Installation Media,or on supplemental Motorola Solutions Product Media.Please reference and review the entire Motorola Solutions Publicly Available Software Notifications/EULA for the details on location of the source code.Note,dependent on the license terms of the Publicly Available Software,source code may not be provided.Please reference and review the entire Motorola Solutions Publicly Available Software Notifications/EULA for identifying which Publicly Available Software Packages will have source code provided.To view additional information regarding licenses,acknowledgments and required copyright notices for Publicly Available Software used in this Motorola Solutions Product,please select Legal Notices display from the GUI(if applicable),or review the Notifications/EULA File/ReadMe,on the Motorola Solutions Install Media,or resident in the Motorola Solutions Product.Motorola Solutions and the Stylized M logo are registered in the US Patent and Trademark Office.All other trademarks,logos,and service marks("Marks")are the property of the respective third party owners.You are not permitted to use the Marks without the prior written consent of Motorola Solutions or such third party which may own the Marks.===========================================================================PUBLICLY AVAILABLE SOFTWARE LIST===========================================================================Name:Microsoft WPF ToolkitVersion: 3.5.40619.1Description:The WPF Toolkit is a collection of WPF features and components that are being made available outside of the Framework ship cycle.The WPF Toolkit not only allows users to get new functionality more quickly,but allows an efficient means for giving feedback to the product team. Many of the features will be released with full source code as well.SoftwareSite:/wpfSourceNo Source Distribution Obligations.Code:License:Microsoft Public License(Ms-PL)Microsoft Public License(Ms-PL)This license governs use of the accompanying software.If you use the software,you accept this license.If you do not accept the license,do not use the software.1.DefinitionsThe terms"reproduce,""reproduction,""derivative works,"and"distribution"have the same meaning here as under U.S.copyright law.A"contribution"is the original software or any additions or changes to the software.A"contributor"is any person that distributes its contribution under this license."Licensed patents"are a contributor's patent claims that read directly on its contribution.2.Grant of Rights(A)Copyright Grant-Subject to the terms of this license,including the license conditions and limitations in section 3,each contributor grants you a non-exclusive,worldwide,royalty-free copyright license to reproduce its contribution,prepare derivative works of its contribution,and distribute its contribution or any derivative works that you create.(B)Patent Grant-Subject to the terms of this license,including the license conditions and limitations in section3, each contributor grants you a non-exclusive,worldwide,royalty-free license under its licensed patents to make, have made,use,sell,offer for sale,import,and/or otherwise dispose of its contribution in the software or derivative works of the contribution in the software.3.Conditions and Limitations(A)No Trademark License-This license does not grant you rights to use any contributors'name,logo,or trademarks.(B)If you bring a patent claim against any contributor over patents that you claim are infringed by the software, your patent license from such contributor to the software ends automatically.(C)If you distribute any portion of the software,you must retain all copyright,patent,trademark,and attribution notices that are present in the software.(D)If you distribute any portion of the software in source code form,you may do so only under this license by including a complete copy of this license with your distribution.If you distribute any portion of the software in compiled or object code form,you may only do so under a license that complies with this license.(E)The software is licensed"as-is."You bear the risk of using it.The contributors give no express warranties, guarantees or conditions.You may have additional consumer rights under your local laws which this license cannotchange.To the extent permitted under your local laws,the contributors exclude the implied warranties of merchantability,fitness for a particular purpose and non-infringement.。
Transition Networks SISTG1040-2x2-LRT 产品说明书

SISTG1040-2x2-LRT Quick Start GuideIntroductionTransition Networks’ SISTG1040-242-LRT and SISTG1040--282-LRT are Industrial Unmanaged GbESwitches suitable for industrial Ethernet applications. See the SISTG1040-2x2-LRT Install Guide forimportant Cautions, Warnings, Features, Specifications, Front & Back Panel, LEDs, RESET button,Installation, Package Contents, and Troubleshooting, Warranty, Support & Compliance information.Unpack and Install1.Check package contents: verify that you have received the Switch, Quick Start Guide, Terminal Block, and Mountingkit. Two optional Power Supply models are available (sold separately).2.Unpack the contents in install location, and continue with Desktop, DIN Rail, or Wall mounting; see the Install Guide.3.Review the front panel description the Install Guide. Use the front panel grounding screw as required; see chapter 3of the Install Guide.4.Install SFP modules. Refer to the specific SFP manual for cautions and warnings. Note: The SFP ports should use ULListed Optional Transceiver product, Rated 3.3Vdc, Laser Class 1.5.Connect to Network / Devices: the switches provide eight or four 10M/100M/1G RJ45 ports. Use Cat 5e or betterunshielded twisted pair (UTP) cable terminated with an RJ-45 connector.6.Connect to 12-48V DC Power. Caution: Before applying power from an AC outlet, insert terminal connectors into theSISTG1040-2x2-LRT switch and verify all connections. Plugging in power connection after energizing power supply(s) may damage the switch. a) Connect the wires between the +P1 and –P1 terminals on the switch terminal block and the +V and -V terminals on the power supply. Optionally, connect the wires between the +P2 and –P2 terminals on the switch terminal block and the +V and -V terminals on the power supply if redundant power is to be used.b) Use a small Phillips screwdriver to tighten the wire-clamp screws. c) Connect the three wires (e.g., green, black,white) of the power cord to the Ground (), N, and L clamp connections respectively. Use a small Phillipsscrewdriver to tighten the wire-clamp screws. d) Connect the plug end of the power cord into a live AC outlet.e) Verify that the Power Supply front panel DC OK LED is lit. See the Install Guide for more details.7.Check the SYS LED. If it is lit, the power connection is correct. If not, see the Install Guide.LED Descriptions: three front panel LEDs allow switch status checking and monitoring:•Power LEDs indicate if the switch is powered up correctly.•System LED indicates if the system is ready.•Port Status LEDs indicates the current status of each port. Check these LEDs to understand the port status.RESET ButtonPress the RESET button to reboot the switch. The front panel LEDs flash and the switch is reset.Front PanelsSISTG1040-242-LRT SISTG1040-282-LRT LED SummaryLED Color FunctionSYS (System) Green On = the switch is ready. Of = the switch is not ready.P1 (Power 1) Green Input Power source 1 supplying power. P2 (Power 2) Green Input Power source 2 supplying power.Link/Act/Speed Green/AmberLight off: port disconnected or link failed.Green Light on: 1G Link Present, No Activity.Amber Light on: 100M/10M Link Present, No Activity.Green Blinking: 1G Activity. Port is sending or receiving data.Amber Blinking: 100M/10M Activity. Port is sending or receiving data.Link/Act/Speed Green/AmberLNK: Amber/Green (Two Color)Light off: port disconnected or link failedAmber Light on: link-up (100M)Green Light on: link-up (1G)Blinking: activity (receiving or transmitting data)Contact UsFor Transition Networks Drivers, Firmware, etc. go to the Product Support webpage (logon required).For Manuals, Application Notes, Brochures, Data Sheets, Specifications, etc. go to the Support Library (no logon required).Transition Networks | 10900 Red Circle Drive | Minnetonka, MN 55343, U.S.A.Technical Support: Technical support is available 24-hours a day. US and Canada: 1-800-260-1312;International: 00-1-952-941-7600. | tel: +1.952.941.7600 | toll free: 1.800.526.9267 | fax: 952.941.2322 ******************** | ************************** | ******************************。
Netra 1290服务器设置指南说明书

Shipping Kit ContentsYour shipping kit should contain the following items:■Netra 1290Server Getting Started Guide (this document)■Rackmount kit:■Slide assemblies with mounting brackets (2)■No.10-32UNF screws with washers (8)■M6screws with washers (8)■Cable management arm (CMA-800)■Lite cable management arm (CMA-Lite)■Ethernet/serial cables (4)■Antistatic wrist strap and snap-on converter ■RJ-45to DB-25male adapter ■RJ-45to DB-9female adapter ■Unpacking tools:■13mm wrench■8mm wrenchSetting Up the Netra 1290ServerThe following list summarizes the tasks to set up your Netra 1290server:1.Verify power,air conditioning,and floor area requirements.2.Set up the Sun™Rack and connect the power cables.Refer to the Sun Rack Installation Guide.3.Unpack the Netra 1290server and install it into the rack.Refer to the Netra 1290Server Installation Guide ,819-4372.4.Power on the Sun Rack.Refer to the Sun Rack Installation Guide.5.Connect an administrative console to access the system controller and power on the Netra 1290server.Refer to the Netra 1290Server Installation Guide ,819-4372.6.Allow the server to run through POST and ensure there are no errors,then power off the server.Refer to the Netra 1290Server System Administration Guide ,819-4374,if there are errors.7.(Optional)Install options and storage devices.Refer to the Netra 1290Server Service Manual ,819-4373,and documentation that came with the option or storage device for details.8.Power on the Netra 1290server,and configure the system.Refer to the Netra 1290Server System Administration Guide ,819-43749.(Optional)Create additional domains.Refer to the Netra 1290Server System Administration Guide ,819-4374.a.Install the Solaris™software on each domain.Refer to the Solaris Installation Guide.b.Boot the Solaris software on each domain.Refer to the Netra 1290Server System Administration Guide ,ra ™ 1290 Server Getting Started GuidePart No. 819-4378-10, Rev. A May 2006Sun Microsystems, Accessing Netra 1290Server DocumentationThe Netra 1290server documentation is available online at the following URL:/documentationContacting Sun Technical SupportIf you have technical questions about this product that are not answered in the Netra 1290server documentation,go to:/service/contactingSun Welcomes Your CommentsSun is interested in improving its documentation and welcomes your comments and suggestions.You can submit your comments by going to:/hwdocs/feedbackPlease include the title and part number of your document with your feedback:Netra 1290Server Getting Started Guide ,part number 819-4378-10.Copyright 2006Sun Microsystems,Inc.All rights e is subject to license terms.Third-party software,including font technology,is copyrighted and licensed from Sun suppliers.Portions may be derived from Berkeley BSD systems,licensed from U.of CA.Sun,Sun Microsystems,the Sun logo,Netra,and Solaris are trademarks or registered trademarks of Sun Microsystems,Inc.in the U.S.and in other countries.All SPARC trademarks are used under license and are trademarks or registered trademarks of SPARC International,Inc.in the U.S.and in other countries.ernment Rights—Commercial ernment users are subject to the Sun Microsystems,Inc.standard license agreement and applicable provisions of the FAR and its supplements.Copyright 2006Sun Microsystems,Inc.Tous droits réservés.Distribuépar des licences qui en restreignent l’utilisation.Le logiciel détenu par des tiers,et qui comprend la technologie relative aux polices de caractères,est protégépar un copyright et licenciépar des fournisseurs de Sun.Des parties de ce produit pourront être dérivées des systèmes Berkeley BSD licenciés par l’Universitéde Californie.Sun,Sun Microsystems,le logo Sun,Netra,et Solaris sont des marques de fabrique ou des marques déposées de Sun Microsystems,Inc.aux Etats-Unis et dans d’autres pays.Toutes les marques SPARC sont utilisées sous licence et sont des marques de fabrique ou des marques déposées de SPARC International,Inc.aux Etats-Unis et dans d’autres pays.。
- 1、下载文档前请自行甄别文档内容的完整性,平台不提供额外的编辑、内容补充、找答案等附加服务。
- 2、"仅部分预览"的文档,不可在线预览部分如存在完整性等问题,可反馈申请退款(可完整预览的文档不适用该条件!)。
- 3、如文档侵犯您的权益,请联系客服反馈,我们会尽快为您处理(人工客服工作时间:9:00-18:30)。
way Group StandardRailway Group StandardGM/RT 2149Issue OneDate August 1994Kinematic Gauging Requirements for Railway VehiclesSynopsisThis standard prescribesmaximum permissible vehicle dimensions for traction and rolling stock and for on-track machines, to ensure that safe and adequate clearances are provided and maintained between vehicles and track infrastructure and between vehicles passing each other.This document is the property of Railtrack. It shall not be reproduced in whole or in part without the written permission of the Controller, Safety Standards.Published bySafety & Standards Directorate RailtrackRailway Technical Centre London Road Derby©Copyright 1994 RailtrackWithdrawn DocumentUncontrolled When PrintedApproved ByApproved ByWithdrawn DocumentUncontrolled When PrintedThis page is intentionally blank.Railway Group Standardsue Date August 1994Standard2149for Railway Vehicles C o n tentsSection DescriptionPagePart A Issue record 2Responsibilities and distribution 2 Implementation 2 Disclaimer 2 Supply2Part B1 Purpose 32 Scope3 3 Definitions3 4 General Requirements 5 5 Vehicle Swept Gauge 6 6 Vehicle Swept Envelope 7 7 Specific Requirements for Vehicle Equipment 8 8 Verification and Records 9Appendices A CI Gauge for Passenger Vehicles 10 B CI Appendix A Gauge for Passenger Vehicles 11 C Locomotive Gauge 12 D W5 Gauge for Freight Vehicles 13 E Gauge Width Reduction Formulae for Curves 14 F W6/W6A Gauges for Freight Vehicles 16 G W6/W6A Exception Gauges for Containers 19 H W6A/SBI-C Gauge for Demountable Loads 21 I Swept Envelope for Shoegear 27 J Location of AWS Receiver 28 K Location of APC Receiver 29 L Location of Tripcock 30References 31Withdrawn Document Uncontrolled When Printedumcode|GM/RT 2149************************2******************************************************************************************************************************************************************************************************************Part AIssue recordThis Standard will be updated when necessary by distribution of a complete replacement.Amended or additional parts of revised pages will be marked by a vertical black line in the adjacent margin.Issue Date Comments 1 Aug 94 Original document (draft was numberedGM/TT0268)Responsibilities and This standard applies to Train Operators that operate or propose to distributionoperate railway vehicles on Railtrack lines. Train Operators shall ensure that the provisions of the standard are communicated to all associated organisations and persons with responsibilities for vehicles and kinematic gauging in the fields of technical specification, design, development, procurement, testing, maintenance and Engineering Change.Implementation The provisions of this standard are mandatory. The standard shallapplyfrom 1 November 1994 to all new procurement contracts for new vehicles and to all new programmes involving Engineering Change to existing vehicles.Disclaimer The Safety & Standards Directorate (S&SD) shall use its bestendeavours to ensure that the content, layout and text of its standards are accurate, complete and in line with current best practice insofar as is reasonably practicable. It makes nowarranties, express or implied, that compliance with all or any of its standards shall be sufficient to ensure safe systems of work or operation. The S&SD will not be liable to pay compensation in respect to the content or subsequent use of its standards, except where it can be shown to have acted in bad faith or there has been wilful default.Supply Controlled and uncontrolled copies of this standard must be obtainedfrom the TDCC Manager, Document Services, Railway Technical Centre, London Road, Derby, DE24 8UP.Withdrawn Document Uncontrolled When Printed***************************************************************************************************************************************************************3******************************3***********************3***Part B1 PurposeThe purpose of this standard is to prescribe the maximumdimensions of vehicles and component equipments to ensure that, when likely suspension movements are allowed for, the clearances between vehicles and infrastructure and between vehicles when passing each other are sufficient to avoid risk of collisions and will ensure operational safety on Railtrack lines.2 ScopeThe requirements of this standard apply to traction and rolling stock vehicles, and also to on-track machines. The requirements apply to all new vehicles. They also apply to existing vehicles which aresubject to engineering change or are proposed for redeployment on routes for which permission to operate has not been received.This standard does not cover the requirements for out-of-gauge vehicles, such as independent snow-ploughs, for which special operating arrangements apply.3 DefinitionsBalancing SpeedThe vehicle running speed on curved and canted track at which the centrifugal force and gravitational force components acting parallel to the plane of the track exactly balance. It is the speed which equates to zero Cant Deficiency.Cant DeficiencyThe difference between (i) the angle to which the track would have to be canted on a curve to just counterbalance the centrifugal forces acting on a vehicle, and (ii) the actual cant angle of the track. Cant ExcessThe extent by which the angle of cant on curved track exceeds that just required to counterbalance the centrifugal forces acting on a vehicle. It equates to a negative value of Cant Deficiency. Curve OverthrowThe extent to which a transverse cross-section of a vehicle is displaced inwards or outwards from the track centreline on a perfectly aligned curve.Engineering ChangeAny alteration or modification to the design of a vehicle that affects its technical performance, particularly where it influences vehicle dimensions and suspension performance.Withdrawn Document Uncontrolled When Printedumcode|GM/RT 2149************************4*****************************************************************************************************************************************************************************3******************************3***Equivalent CantA measure of the total lateral acceleration field acting on a vehicle, comprising the actual Cant Deficiency (or Cant Excess), the cross-level error in the track, and the dynamic lateral acceleration of the vehicle in response to track irregularities. It is the track cant angle which would produce the same total lateral acceleration field on the vehicle when stationary .Infrastructure ManagerThe technical manager responsible for the provision, maintenance and safety of track and associated infrastructure for a line of route. Kinematic EnvelopeThe envelope described by the vehicle cross-sectional profile at any position along a vehicle, together with all Kinematic Sway displacements and vertical suspension displacements at a particular track location.Kinematic GaugingThe process by which the Swept Envelope of a vehicle is used to ensure that a vehicle can run safely along a section of track without coming unacceptably close to lineside structures or vehicles running on adjacent tracks.Kinematic SwayThe lateral and roll displacements of a vehicle body and its bogies on their suspension systems in response to:(a) track layouts, discrete features and irregularities; (b) vehicle speeds and cant deficiencies; (c) wind forces;(d) suspension performance and condition, (including tolerances, wear, and likely failure modes); (e) track position tolerances and wear of rails. K speed CoefficientA dynamic factor relating the magnitude of lateral body accelerations to track irregularities as a function of vehicle speed.On-track MachineA rail-mounted machine permitted by the Rule Book (BR 87109) to be moved, either self-propelled or in train formation, outside a possession.Pantograph SwayThe Kinematic Sway of the pantograph, excluding track positional tolerances and wear of rails.Reference Swept Envelope/GaugeA Swept Envelope/Gauge to which vehicles have been previously built and are known to have acceptable clearances on one or more specified routes.Standard Vehicle GaugeWithdrawn Document Uncontrolled When Printed***************************************************************************************************************************************************************5******************************5*** ********************5***An outline drawing or specification of a notional vehicle, whichprescribes maximum vehicle and loading dimensions, certain suspensiondisplacements, and certain Curve Overthrow limitations.Swept Envelope The combinations of Kinematic Envelopes and Curve Overthrows atall cross-sections along a vehicle as the vehicle moves along the track. This represents the bounds of the volume that the vehicle can sweep through in traversing a particular section of track.Swept Gauge The combinations of a Standard Vehicle Gauge and CurveOverthrows atall cross-sections along a vehicle as the vehicle moves along thetrack. This represents the bounds of the volume that the vehicle can sweep through in traversing a particular section of track.Technically Competent Authority A person or organisation with recognised professional expertise andexperience in Kinematic Gauging.4 General Requirements 4.1 Vehicles shall be designed and maintained so that they do notinfringe the minimum clearances required between vehicles and trackinfrastructure and between vehicles passing each other on adjacenttracks. Required clearances shall be maintained under all normal track andoperating conditions on those routes where the vehicles are permittedto operate.These requirements apply: (a) Over the full permissible range of operating speeds and cantdeficiencies at each site on the permitted routes of operation;(b) Over the appropriate range of track and rail configurations,features and associated tolerances, as defined in references [1] and [2] and by the Infrastructure Manager(s) for the routes concerned;(c) Over the range of normal wind speeds at each site on thepermitted routes of operation.4.2 Vehicles shall meet the requirements of this standard over thefull range of variations in vehicle condition that are likely to be experienced. Account shall be taken of tolerances in vehicle dimensions, mass distributions and wheel loadings, suspension characteristics, normal variations in vehicle maintenance condition and wear, and any other relevant variables.4.3 Vehicles shall be maintained so that the prescribed tolerancesfor components, assemblies and systems that influence swept envelopes are sustained over the lives of the vehicles. Withdrawn Document Uncontrolled When Printedumcode|GM/RT 2149************************6*****************************************************************************************************************************************************************************5******************************5***4.4 Where vehicles can be operated separately or in multiple, the vehicles shall meet the requirements of this standard both individually and when forming part of a train. Where vehicles must be joined together to form an operationally inseparable rake, the rake as a whole, and the rake as part of a train, shall meet the requirements of the standard.4.5 A vehicle shall satisfy at least one of the following requirements to be accepted for operation on a specified route. In each case, formal acceptance and clearance to operate must be obtained from the appropriate Infrastructure Manager.(a) the swept gauge of the vehicle shall not be greater than that prescribed in Section 5.(b) the swept envelope of the vehicle shall not be greater than that prescribed in Section 6.(c) for vehicles which fail to meet the requirements of both (a) and (b), special arrangements for kinematic gauging clearance shall be agreed and implemented.It should be noted that compliance with (a) may result in vehicles that are smaller than necessary. Compliance with (c) may require extensive investigations and costly modifications to the trackinfrastructure, and the imposition of additional operating restrictions.5 Vehicle Swept Gauge 5.1 The swept gauge for a candidate vehicle shall be comparedwith a Reference Swept Gauge to which vehicles have beenpreviously built and are known to have acceptable clearances on the proposed route or routes of operation. The swept gauge for the candidate vehicle shall not infringe the Reference Swept Gauge.The permitted Reference Swept Gauges are listed below. Vehicles of any type may be built to any of the Reference Swept Gauges providing they fully comply with the requirements of the chosen Reference Swept Gauge.(a) CI Gauge for Passenger Vehicles.Details shall be in accordance with reference [3].An extract of the principal details is included in Appendix A.(b) CI Appendix A Gauge for Passenger Vehicles. Details shall be in accordance with reference [4].An extract of the principal details is included in Appendix B.Withdrawn Document Uncontrolled When Printed***************************************************************************************************************************************************************7******************************7***********************7***(c) Locomotive Gauge.Details shall be in accordance with reference [5].An extract of the principal details is included in Appendix C.(d) W5, W6 and W6A Gauges for Freight Rolling Stock.Details shall be in accordance with references [6], [7] and [8]. Extracts of the principal details are included in Appendices D, F and G.(e) W6A/SBI-C Special Gauge for Demountable Loads. Details shall be in accordance with reference [9].Extracts of the principal details are included in Appendix H. 5.2 In applying a comparison with a Reference Swept Gauge, itshall be ensured that the comparison is valid, particularly in terms of any novelty in the candidate vehicle's configuration, its operating speeds and cant deficiencies, and its suspension characteristics. The factors listed in Section 6.2 (a) to (h) shall be considered.If there is doubt about the validity of the comparison, then clearanceto operate shall be sought in accordance with Section 4.5 (b) or (c).6 Vehicle Swept 6.1 The swept envelope for a candidate vehicle on a specified routeshallEnvelope be determined at all critical sites along the route. The envelope shallbe compared with a Reference Swept Envelope which has been determined by a similar calculation method and is known to provide acceptable clearances. The swept envelope for the candidate vehicle shall not infringe the Reference Swept Envelope.6.2 Swept envelopes shall be determined by calculations, dynamicsimulations, experiments and tests as appropriate, taking into account the following factors.(a) Quasi-static sway of the vehicle arising from steady-statecurving forces (cant deficiency and cant excess).(b) Dynamic sway of the vehicle in response to track irregularities. (c) Vehicle sway due to wind forces. (d) Static vertical displacements caused by payload variations,wheel wear, and suspension stiffness tolerances, etc.(e) Dynamic vertical suspension displacements in response to trackirregularities.(f) Vertical and sway displacements associated with likelysuspension failure modes and other relevant factors.(g) Vehicle speed. (h) Vehicle overthrows on curves, laterally and vertically.Withdrawn Document Uncontrolled When Printedumcode|GM/RT 2149************************8*****************************************************************************************************************************************************************************7******************************7***(i) Track positional tolerances in alignment, top and cross-level, as indicated in Section 4.1 (b).6.3 Kinematic envelope and swept envelope information shall be presented to the Infrastructure Manager(s), as required.7 Specific Requirements 7.1 PantographFor Vehicle Equipment Pantograph sway displacements shall not exceed the followingvalues at a height of 4.3 m above rail level:(a) + 130 mm when running at all speeds up to the maximumvehicle operating speed and at maximum cant deficiency in still air.(b) + 190mm when running at maximum vehicle operating speedand at maximum cant deficiency with a maximum wind speed of 35 m/s(126 km/h). Where contact wire heights are higher than 4.3 m above rail level,the pantograph sway displacements shall not be increased by more than+ 40mm for each metre increase in height above 4.3 m. 7.2 Shoegear Shoegear and associated equipment shall not infringe the limitingswept envelope prescribed in Appendix 1, when subject to the following two setsof conditions: Case A: Displacements Towards the Outside of a Curve:(a) The curve overthrows resulting from a 160 m radius simple curve.(b) The kinematic displacements when operating at the speedwhich produces maximum design cant deficiency with an installed track cant of 6°.(c) Track positional tolerances.Case B: Displacements Towards the Inside of a Curve:(a) The curve overthrows resulting from a 160 m radius simple curve.(b) The kinematic displacements when operating at a speed of 5km/h with an installed track cant of 6°.(c) Track positional tolerances.Withdrawn Document Uncontrolled When Printed***************************************************************************************************************************************************************9******************************9***********************9***7.3 Obstacle Deflectors, Snowploughs & Lifeguards Obstacle deflectors, snowploughs and lifeguards shall complygenerally with the requirements of Sections 5 and 6, except where their essential function of clearing obstructions from the path of the leading wheelset necessitates infringements of reference swept gauges or reference swept envelopes. In which cases, clearance to operate shall be arranged under Section 4.5 (c).7.4 Advanced Warning System (AWS) Receivers The profiles of AWS receivers shall be contained within the sweptenvelope prescribed in Appendix J.7.5 Automatic Power Control (APC) Receivers APC receivers, provided to interrupt and re-establish the supply of accurrent to pantographs before and after neutral sections, shall be contained within the swept envelope prescribed in Appendix K.7.6 Tripcocks Tripcocks, provided to initiate an emergency brake application in theevent of train over-runs in sub-surface terminal stations, shall be contained within the swept envelope prescribed in Appendix L.7.7 Other Equipments The permissible swept envelopes for other specific equipments notlisted in this Section and not covered by Sections 5 and 6, shall be agreed with the Infrastructure Manager(s) for the route(s) for which special clearance is required in accordance with Section 4.5 (c).8 Verification & Records 8.1 Compliance with the requirements of this standard shall beverified by calculations, by comparisons with other vehicles, by testing or by other appropriate means. The verification shall be commensurate with the level of complexity and innovation in the vehicle design.8.2 Where a vehicle incorporates active elements, or is otherwisenovel in design, the method and values used to describe the swept envelope shall be endorsed by a Technically Competent Authority.8.3 Auditable records shall be kept of drawings, calculations andtechnical information used to evaluate and describe the swept envelope of a vehicle.Withdrawn Document Uncontrolled When Printedumcode|GM/RT 2149************************10*****************************************************************************************************************************************************************************9******************************9***Appendix ACI Gauge for Passenger VehiclesApplication Notes for CI GaugeA.1 This gauge applies directly only to vehicles having the following dimensions:(a) 19,354 mm over headstocks and 14,173 mm between bogie centres giving overthrows of 25 mm on a1026 m radius curve at the vehicle centre and 25 mm on a 849 m radius curve at the vehicle ends.(b) 17,373 mm over headstocks and 12,192 mm between bogie centres giving overthrows of 25 mm on a 784m radius curve at the vehicle centre and 25 mm on a 724 m radius curve at the vehicle ends. A.2 This gauge must not be exceeded nor the defined lengths and bogie centres varied without the authority of the Infrastructure Manager.A3Underclearances and heights below 1118 mm above Rail Level (R.L) are minima after full drop due to wear etc. has occurred. Heights above 1118 mm above R.L must not be increased to compensate for any drop.A.4 The sloping doted profile is permitted only on bogie frames between wheelsets.A.5 Bolster movements and all mechanical lateral displacements in spring and axle assemblies at limits of permissible wear must not exceed a width of 2386 mm between 280 mm and 940 mm above R.L. A.6The above is an extract from Drawing CCE 891-61 Issue D. The actual drawing must be consulted for further details.Maximum Permisible Contour For Undergear Not Subject ToOverthrow On Curve.Withdrawn Document Uncontrolled When Printed********************************************************************************************************************** *****************************************11******************************11***********************11***Appendix BCI Appendix A Gauge for Passenger Vehicles Note:Withdrawn DocumentUncontrolled When Printedumcode|GM/RT 2149************************12*****************************************************************************************************************************************************************************11******************************11***Appendix CLocomotive GaugeApplication Notes forLocomotive GaugeC.1 Underclearancesare minima andare to be maintained under all conditions of loading and wear with the locomotive stationary.C.2 The curve displacement values (broken lines) show the boundaries which must not be exceeded by a locomotive when stationary.C.3 Optimum minimum negotiable curve is 70 m radius with or without gauge widening. C.4 Full line dimensions refer to the maximum building contour.Note that the full line represents the maximum widths to which a locomotive may be built on condition that any overthrow on the contour, or on any part of the locomotive of lesser width, must not exceed the broken line when on a 200 m radius curve.C.5 Broken line dimensions refer to the maximum overthrow contour.Note that the broken line represents the maximum permitted overthrow displacement on a 200 m curve. Where full and broken lines are coincident, the building line must be reduced accordingly where overthrow occurs.C.6 The sloping dotted profiles are permitted only on items which are not subject to overthrow on curves.C.7The above is an extract from Drawing L-AO-1806. The actual drawing must be consulted for further details.Withdrawn Document Uncontrolled When Printed***************************************************************************************************************************************************************13******************************13***********************13***Appendix D W5 Gauge For Freight VehiclesApplication Notes for W5 GaugeD.1 The gauge widths shown above incorporate allowances for lateral displacements of vehicle suspension systems,together with permissible limits for wear. Actual vehicle widths must therefore be reduced accordingly.D.2 Vehicle widths must satisfy gauge requirements for negotiating curves in accordance with the gauge widthreduction formulae defined in Appendix E. The following values shall be used for calculating gauge width reductions E i and E o : R = 200 m K = 0.075 m at body heights above 1.065 m ARL (Above Rail Level) K = 0.025 m at body heights below 1.065 m ARL.D.3 The under-clearances shown above are the minimum permissible. They must be maintained under allconditions of vehicle loading and wear.D.4 The broken line profiles are permitted only on items which are not subject to overthrow on curves.D.5 The above is an extra from Drawing RE/RA/G/I. The actual drawing must be consulted for further details.305 at 3965 A.R.L.1590 at 3750 A.R.L.2440 at 3430 A.R.L.2740 between 1065 and 3140 A.R.L.2640 between 280 and 1065 A.R.L.2210 between 180 and 280 A.R.L.2080 between 155 and 180 A.R.L.1350 at 100 A.R.L.See Note D.4All Dimensions in mmWithdrawn Document Uncontrolled When Printedumcode|GM/RT 2149************************14*****************************************************************************************************************************************************************************13******************************13***Appendix EGauge Width Reduction Formulae For CurvesE.1In applying Freight Vehicle Standard Gauges, gauge widths shall be reduced in accordance with the formulae below. These width reductions are derived by consideration of the plan-viewgeometry of a vehicle on a simple curve, as shown in Figure E1 below.E.2 Formula for Gauge Width ReductionsGauge width reductions E i and E o shall be calculated as follows:whereE i = Width reduction on each side of the Gauge at a vehiclecross-section situated inboard between bogie centres, or between axle centres of a two-axled vehicle.E o = Width reduction on each side of the Gauge at a vehiclecross-section situated outboard between bogie centres, or beyond axle centres of a two-axled vehicle.A = Distance between bogie centres, or the wheelbase of a two-axled vehicle.N i = Distance from a vehicle inboard cross-section to the nearestbogie centre, or to the nearest axle centre of a two-axled vehicle. N o = Distance from a vehicle outboard cross-section to thenearest bogie centre, or to the nearest axle centre of a two-axled vehicle.R = Curve radius for gauging assessmentK = Curve Overthrow threshold at which gauge width reductionsare required.Notes:(1) The calculated gauge width reductions shall be applied to allwidth coodinates of the gauge profile at the cross-section being considered.E A.N N 2RKE A.N N 2RKi i io o o 22=−−=+−Withdrawn Document Uncontrolled When Printed***************************************************************************************************************************************************************15******************************15***********************15***(2) Negative values of E i and E o indicate that gauge widthreductions are not necessary.(3) No increase in gauge widths are permissible even if lateraldisplacements on curves are less than those allowed in E.2.(4) With K = 0, E i and E o equate to the Curve Overthrowsinboard and outboard of the bogie centres, or of the axle centres of a two-axled vehicle.Figure E1 Diagram for Gauge Width Reduction FormulaeWithdrawn Document Uncontrolled When Printed。