简述胶印过程印迹变浅的原因
印刷过程中整体墨色变浅的原因解析
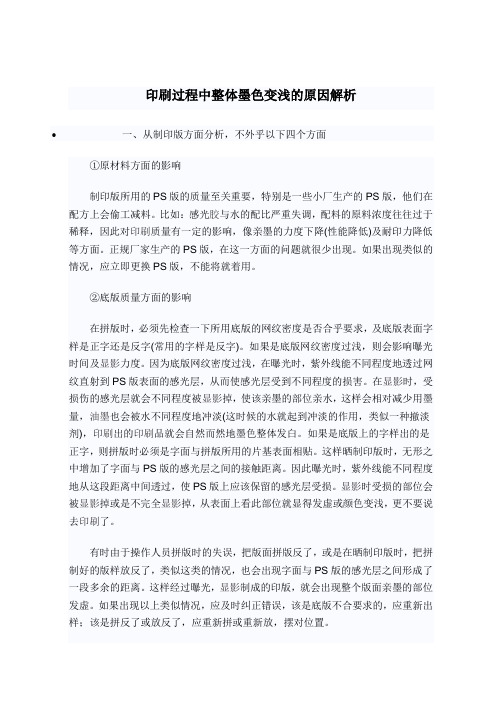
印刷过程中整体墨色变浅的原因解析一、从制印版方面分析,不外乎以下四个方面①原材料方面的影响制印版所用的PS版的质量至关重要,特别是一些小厂生产的PS版,他们在配方上会偷工减料。
比如:感光胶与水的配比严重失调,配料的原料浓度往往过于稀释,因此对印刷质量有一定的影响,像亲墨的力度下降(性能降低)及耐印力降低等方面。
正规厂家生产的PS版,在这一方面的问题就很少出现。
如果出现类似的情况,应立即更换PS版,不能将就着用。
②底版质量方面的影响在拼版时,必须先检查一下所用底版的网纹密度是否合乎要求,及底版表面字样是正字还是反字(常用的字样是反字)。
如果是底版网纹密度过浅,则会影响曝光时间及显影力度。
因为底版网纹密度过浅,在曝光时,紫外线能不同程度地透过网纹直射到PS版表面的感光层,从而使感光层受到不同程度的损害。
在显影时,受损伤的感光层就会不同程度被显影掉,使该亲墨的部位亲水,这样会相对减少用墨量,油墨也会被水不同程度地冲淡(这时候的水就起到冲淡的作用,类似一种撤淡剂),印刷出的印刷品就会自然而然地墨色整体发白。
如果是底版上的字样出的是正字,则拼版时必须是字面与拼版所用的片基表面相贴。
这样晒制印版时,无形之中增加了字面与PS版的感光层之间的接触距离。
因此曝光时,紫外线能不同程度地从这段距离中间透过,使PS版上应该保留的感光层受损。
显影时受损的部位会被显影掉或是不完全显影掉,从表面上看此部位就显得发虚或颜色变浅,更不要说去印刷了。
有时由于操作人员拼版时的失误,把版面拼版反了,或是在晒制印版时,把拼制好的版样放反了,类似这类的情况,也会出现字面与PS版的感光层之间形成了一段多余的距离。
这样经过曝光,显影制成的印版,就会出现整个版面亲墨的部位发虚。
如果出现以上类似情况,应及时纠正错误,该是底版不合要求的,应重新出样;该是拼反了或放反了,应重新拼或重新放,摆对位置。
③实际操作方面的影响在PS版曝光显影时,操作人员应根据实际情况酌情处理,不能千篇一律。
不干胶印刷品色彩变化问题的解决

不干胶印刷品色彩变化问题的解决
不干胶标签纸印刷品在印刷过程中出现色相、明度、饱和度会出现变化,深浅也可能出现变化。
是什么原因造成的呢?
主要有两个原因,作为印刷用的油墨在太阳的光线下,油墨的质量发生变化,光泽会变差,颜色会变浅,甚至褪色,有些质量更差的油墨甚至会产生变色的效果,使图案颜色完全变了。
如何避免或者减少这印刷上的变化,是客户满意呢?
首先,要选择优质的油墨,有些要求不高的生产商,为了以低价抢占市场,不惜采用低价油墨,这样不但可能导致客户投诉,甚至失去客户,造成巨大损失。
其次,是纸张的选择,质量好的纸张表面平滑度好,密度高。
能承受较大的压力,使油墨的墨粘度、流动性、墨层厚度保持一定的良好的量产生最好的印刷效果。
反之,印刷出来的不干胶标签纸可能效果大打折扣。
另外纸张的吸水性及渗透性也会对不干胶标签纸印刷色彩产生影响。
纸张厚一点跟薄一点是有区别的。
最后,是生产环境跟存放环境,是否足够干燥不那么潮湿,自然可以让不干胶标签纸,印刷效果保存得更好。
其他的不干胶标签纸的堆放,及纸张的含碱性也要注意。
纸张PH值7,呈中性的纸张是最理想的。
每个不干胶标签纸印刷厂家需要从每个环节上去精益求精,才能生产出最优质的标签纸。
胶印墨色不匀的原因分析

胶印墨色不匀的原因分析胶印经常碰到的印刷质量问题之一印刷的墨色不均匀,实地表面为颜色深浅不一,网点处表现为同层次的网点还原程度不一样。
产生的原因很多,就常见的分析如下。
一、设备问题。
由于设备安装不合理,机械部件精度不高或磨损,可能造成运转不稳定,上墨不均匀,都会出现有规律的墨色不一致现象。
二、水墨平衡不好。
水墨平衡受影响的因素较多。
设备操作不当引起的,如墨辊、水辊的压力不恰当等,造成墨量、水量控制难,容易出现水墨不平衡;油墨、润版液质量不好,如乳化性能不恰当,对掌握水墨平衡困难,乳化作用太过,导致糊版,太小则会造成水溃印。
三、印刷压力不一。
印刷油墨的转移,油墨在压力下,油墨被压入承印物表面的孔隙中,油墨粘附于其表面,转移的油墨通过渗透、氧化等作用干燥。
油墨转移到表面的量与印刷压力、表面的吸附作用关系很大,纸面的不同部位受到的压力不同、纸表面吸附作用强弱不同,都会造成油墨转移量的不一致,产品的墨色就不均匀。
压力大小不一产生的原因分两类:1、印刷方面的原因。
例如橡皮布安装不平整。
2、纸张厚度不一、凹凸不平。
当印刷压力小时,会因纸张受到的压力不一,纸张厚或凸出的地方墨色深,薄或凹进的地方墨色浅。
四、纸张吸墨不匀造成的墨色不匀。
1、由于纸板匀度差,而压光压力太大特别是使用硬压光,造成纸面受压不一,以致表面光泽不一,孔隙差别大,对油墨的吸附不一样。
2、造纸毛毯使用时间长或受伤,表面的毛磨损脱落,基布的形状压印到湿纸上,造成纸板表面的毯印,压光后形成有规则光泽条痕。
3、压光、后加工故障,造成的光泽斑、光泽条痕。
4、纸面的水滴印、霉斑等。
5、由于纸张的COBB值和K&N控制不当易产生湿排斥,K&N过低,吸墨亦产生不匀。
墨色不一致的原因除上述以外还有其它的,要正确分析,有时并不容易。
要判别这些问题的原因一般可采用以下方法。
1、从出现位置的规律、出现的频率来判断。
印刷设备问题,出现的规律很强,几乎在一个位置。
印刷前淡后深咬口那偏浅版尾偏深什么原因

印刷前淡后深咬口那偏浅版尾偏深什么原因印刷前淡后深咬口是指在印刷过程中,印刷品的前半部分颜色较浅,后半部分颜色较深。
偏浅版尾偏深则表示整个版面上的颜色在版尾(即文章的末尾)有偏浅的现象,而在其他地方则偏深。
以下是可能导致这些现象出现的原因:1.墨水的用量不均匀:印刷机上的墨水供应系统可能存在问题,导致墨水的分布不平均。
例如,前半部分的墨水供应较多,而后半部分的墨水供应较少,从而导致前半部分的颜色较深,而后半部分的颜色较浅。
2.印版的老化:印版使用时间较长或者存储条件不好,可能会导致版面上的图文信息出现不均匀的印刷效果。
老化的印版可能会有颜料积存或者磨损的现象,导致印刷品在一些区域的墨水的密度较高,而在其他区域较低。
3.异常的印刷机调整:印刷机上的传动系统或者调整机构可能存在故障,如压印机构的压力不均匀,压力过大或过小等问题。
这些异常可能会导致墨水的压力不均匀,从而造成前后半部颜色不同的问题。
4.印刷品的纸张问题:印刷品所使用的纸张可能存在原材料不均匀、质量差或者受潮等问题,这也会导致墨水的吸收不均匀。
例如,一些纸张的前半部分由于与纸张边缘接触更久,吸湿更多,而后半部分则较为干燥,这会导致前后部分墨水的表现不同。
5.印刷品的设计问题:一些设计上的因素也可能导致印刷品前后半部分的颜色不同。
例如,在设计中,前半部分可能使用了较浓烈的色彩,而后半部分使用了较淡的色彩。
这种设计效果能够在展示一些特定信息时产生视觉冲击,但印刷时可能导致前后半部分的颜色不一致。
综上所述,印刷前淡后深咬口和偏浅版尾偏深可能由于多种因素导致。
在印刷过程中,需要确保印刷机、印版、墨水和纸张的质量均达到要求,并进行相应的调试和调整,以确保印刷品的质量和一致性。
此外,在设计时也需要考虑印刷的特点和限制,避免出现颜色不均的问题。
胶印工艺中色偏与混色故障现象原因

胶印工艺中色偏与混色故障现象原因胶印印刷工艺过程中,时常发生印品与打样样张色彩不相符的偏红、偏黄或偏青的现象,或者图案画面叠印后混色故障,轻者影响产品质量,严重的会使整批产品报废,使企业遭受严重经济损失。
本文就这一问题结合自己多年从事胶印工艺工作的体会,总结整理出自己的见解,以期与同行商榷。
印品色偏和混色故障大致可归纳为4个方面的原因:(1)制版操作不规范引起的黄、品红、青某一色印版网点过深或过浅;(2)油墨色彩调配不当或三原色油墨不相匹配;(3)印刷色序安排不合理;(4)印刷纸张本身存在较严重的色偏现象。
1、印版网点深浅故障引起的色偏印版晒制过程中,晒版光源强度、光谱同印版感光胶感光特性不匹配,或曝光时间不当;显影液pH值以及显影时间长短掌握不恰当等,都可能造成印版网点过深或过浅。
这样的印版上机印刷,其画面色偏就不可避免了。
故此,印版在上机前必须先对其质量进行鉴别,对印版网点的鉴别可借助放大镜分别对照黄、品红、青、黑各色原版胶片,仔细察看相对应印版图案同一部位的亮调、中调、暗调区域网点显现情况,即亮调部位2%的小网点,印版上应能同等晒得出,印刷品上3%的网点应能印得出来。
若印版上2%的小网点晒不出来,则说明印版晒浅了,不适用。
用鉴别印版同胶片亮调部位2%小网点的方法,鉴别印版上同原版胶片同一部位暗调97%的网点。
若印版上的这部位网点并糊,则说明这块印版晒深了;若这部位网点间空白区域面积扩大了,则说明印版晒浅了,就应重新晒制。
当然,在有条件的情况下,采用布鲁纳尔信号条来控制晒版质量,就能准确而便于操作。
鉴别方法是借助高倍放大镜,观察印版上的布鲁纳尔信号条的第5块50%的细网测试块中的各12个阴阳网点,其阴阳网点面积由大到小顺序都应各出齐6个;第6块的6个小格内2%的小网点要晒出来,若晒出的印版3%的网点存在,而2%的网点消失了,说明印版晒浅了。
反之,不仅2%的网点存在,而且1%的小网点也存在,则说明印版过深。
印刷前淡后深咬口那偏浅版尾偏深什么原因

印刷前淡后深咬口那偏浅版尾偏深什么原因1.印版问题:印版的密度不均匀,特别是在咬口和版尾位置。
可能是由于印版制作过程中的问题,如画面细节线条未完全密封,或者版面的压力不均匀等。
2.印刷机问题:印刷机的压力分布不均匀,特别是在咬口和版尾位置。
这可能是由于印刷机的调整不当,导致压印力不均匀,从而影响了印刷品的颜色均匀度。
3.墨水问题:墨水的颜色浓度不均匀,特别是在印刷品的前半部分和底部区域。
这可能是由于墨水的配方不当,或者是在印刷过程中墨水的供应不均匀等原因导致的。
4.纸张问题:使用不均匀的纸张质量也可能导致印刷前淡后深咬口和偏浅的版尾。
纸张的吸墨性和光泽度可能存在差异,从而导致印刷品在不同区域的颜色表现不一致。
5.印刷过程控制问题:印刷过程中,操作人员对于压力、墨水供给量和速度等参数的控制不当,也可能导致印刷品的色彩不均匀。
解决这种问题的方法可以包括:1.正确调整印版和印刷机:确保印版的质量良好,制作过程中注意细节线条的完全密封,并调整印刷机的压力分布均匀,以提高印刷品的色彩均匀度。
2.选择合适的墨水:使用质量稳定的墨水,并确保墨水的颜色浓度均匀,避免在印刷过程中墨水供给不均匀的情况。
3.选择质量稳定的纸张:确保使用质量稳定、吸墨性和光泽度均匀的纸张,从而提高印刷品的颜色均匀度。
4.加强印刷过程的控制:对印刷过程的参数进行精确的控制,如压力、墨水供给量和速度等,确保色彩分布的均匀性。
总之,印刷前淡后深咬口和偏浅的版尾是印刷过程中常见的问题,可能由印版、印刷机、墨水、纸张和印刷过程控制等多个方面的原因导致。
解决这些问题需要从制版、调整印刷机参数、选择合适的墨水和纸张等方面入手,确保印刷品的颜色均匀度和质量。
影响印刷颜色的一些因素

影响印刷颜色的一些因素(广州怡彩印刷罗家宝)在胶印中颜色的控制是最为重要的,颜色变化的主要因素有以下几点:1.网点的变化胶印中网点的扩大、变形、角度错位等都会影响色彩的变化。
图文的精度、菲林的线数、角度的不同、网点的百分比都跟色彩变化有关。
2.油墨的色浓度和色相等油墨的色浓度有高有低,在印刷中,色浓度低的油墨印实地时,需要印很厚很深的一层墨才能达到样稿的要求,但旁边的网点部分则由于油墨太厚造成网点扩大,而产生颜色比样稿深。
油墨的色相:油墨都存在不同程度的色偏,如透明黄有偏兰,有偏红的油墨,品红有偏黄、有偏兰的等。
3.承印物(纸张)纸张的光泽度、平滑度、密度、表面白度、以及伸缩性都与印刷的色彩有关,光泽度不好的纸张印出来的东西其亮度就差对不上样稿(表面偏暗),平滑度不够的纸张会使网点变形而影响颜色,密度差的纸张偏软造成网点还原差、变形,表面白度与样稿不同颜色自然就跟不上原样,伸缩性会影响套色,进而影响颜色。
4.印刷工艺A:印刷色序因为现代的胶印大多数是多色印刷,属于湿叠湿印刷,色序不同每个颜色经过叠压的次数也不同,其网点扩大程度也不同,故而颜色变化不一样。
油墨的粘性、透明度、纸张的吸墨性等的差别都会影响印刷颜色。
一般来说,印刷色序的合理安排:应符合油墨的透明度和墨层厚度依次递增、粘度依次递减的原则。
B.水墨平衡在胶印中,控制水墨平衡是至关重要的,水过大,则产生油墨严重乳化,印品花白、印迹发虚、墨色深浅不一,且纸张的变形量增大,造成天气套印不准,水过小,容易脏版、糊版。
把握水墨平衡的一个总原则是:在一定的印刷压力和印刷速度下,形成乳化的油墨乳浊液中,润湿液的体积比应控制在15-26%之间,要尽可能以最小的水份与油墨达到平衡。
C.印刷压力在印刷的各种条件一定时。
油墨转移率与印刷压力的关系:印刷压力过低,油墨与纸张不能充分接触,使印张发虚,印刷压力适中,油墨转移率最好,印刷压力过大,会使网点扩大,印迹模糊,严重时还会发生滑移、摩擦等问题,造成套印不准。
胶印生产中印刷品前深后浅故障分析

(1)过于光滑老化的墨辊应及时更换,保证 墨辊良好的传墨性能和墨辊表面足够的储墨量, 使印刷所消耗的墨量与墨辊的储墨量之比尽可
能小,这样就能增强墨辊自身调整墨量的能力,
使印刷品墨色一致。
世间是循环的,人不可能永生为人。我也期待下辈子也许会
(2)掌握好油墨的流动性和黏度,因为油墨 的流动性与黏度直接影响油墨的传输速度和墨 辊的储墨量。
பைடு நூலகம்
世间是循环的,人不可能永生为人。我也期待下辈子也许会
着墨辊不断滚动上墨,墨辊上的墨量逐渐减少, 滚至印版拖梢部分时,着墨辊上墨量已经很少。 这就很容易引起墨色前深后浅。
2.墨辊排列的影响
输墨装置的墨辊一般分为上墨和收墨两组, 不同的机型,两组墨辊的排列情况又有不同。均 匀分配型墨辊排列的墨路是两路平分,4 根着墨
辊均匀着墨,针对这种墨辊排列方式,如果调节
不当,后两根着墨辊起不到补充上墨、匀墨和收
世间是循环的,人不可能永生为人。我也期待下辈子也许会
回多余墨层的作用,印刷品就极易出现前深后浅 的现象。而着墨辊前多后少着墨型,前 2 根着墨 辊占 90%,后 2 根为 10%,这样的分配一般不
会产生印刷品墨色前深后浅现象。 3.工艺上的补救及操作中的注意事项
(3)严格控制版面水分,防止油墨过量乳化, 保证油墨的正常传输与附着性能。
(4)针对均匀分配型墨路布局,调节靠版墨 辊压力时,前两根应重些,后两根应轻些,相互 间的接触宽度,从前至后一般调整为 6mm,6mm、
4mm、4mm。着墨辊与串墨辊之间的压力,应等于
着墨辊与印版表面的接触压力。因为着墨辊的转
单张纸胶印机在印刷图文面积比较大或实 地版的印刷品时,常会出现同一张印刷品墨色前 深后浅的现象,产生这种现象除了工艺操作和调
- 1、下载文档前请自行甄别文档内容的完整性,平台不提供额外的编辑、内容补充、找答案等附加服务。
- 2、"仅部分预览"的文档,不可在线预览部分如存在完整性等问题,可反馈申请退款(可完整预览的文档不适用该条件!)。
- 3、如文档侵犯您的权益,请联系客服反馈,我们会尽快为您处理(人工客服工作时间:9:00-18:30)。
简述胶印过程印迹变浅的原因
在胶印过程中,纸张、油墨和润版液之间相互作用产生变数,正如同机器部件和印刷材料一样,这些变数不仅影响胶印过程,而且也影响印刷质量。
因此,必须不断观察分析,才能使印刷过程正常进行。
本文就印刷过程印迹变浅因素进行分析。
一.橡皮布上纸张和油墨残留物的堆积
在胶印过程中,造成印迹变浅的原因很多,但主要原因是橡皮布上纸张和油墨残留物的堆积。
一般讲,洗后的橡皮布大约在开始印刷至1500张以后就会产生堆积现象,其堆积效应主要受以下几方面影响。
1.油墨的黏滞性对堆积的影响
油墨的黏滞性分干黏滞性和湿黏滞性,干黏滞性可理解为油墨中不含润版液成分时所表现的黏滞性;湿黏滞性可理解为印刷过程中油墨含润版液后所表现的黏滞性。
黏滞性在批量印刷过程中是有变化的,当油墨黏滞性低于纸版掉毛极限时,在整个印刷中印迹既不满也不崭,不容易产生纸毛堆积现象;当油墨的黏滞性高于纸张掉毛极限时,印迹在印刷过程中会越来越崭。
由于油墨的黏滞性高,许多小纸毛从纸张表面被拔下来,促使纸毛堆积在橡皮布上。
另外,纸张表面有少许松散的小颗粒(纸粉),小颗粒也很容易脱离纸张被黏附在橡皮布的着墨部分,形成堆积。
在印刷开始时,也就是洗完橡皮布不久,正常的润版液量情况下,图文部分(网点、线条、实地)油墨量被100%转移到纸上。
而当印刷至1500张之后或在润滑液不正常情况下,橡皮布上的墨迹回会产生堆积现象,通过高倍显微照片观察更明显。
转移到纸上的网点,其直径受损,而且网点中间呈现无墨的小白点,因此,网点显得浅淡,这表明转移到纸上的油墨量减少。
如果不勤洗橡皮布或对润版液量、墨量进行正确调整,橡皮布上堆积的纸毛、纸粉和油墨残留物会越来越多,印迹将会继续变浅,印在纸上网点中间无墨的部分还要进一步扩大,其中对网目调印品变浅趋势更明显。
2.润版液量对堆积现象的影响
(1)润版液量对油墨黏滞性的影响
从上述可知,油墨黏滞性分干黏滞性和湿黏滞性两种。
湿黏滞性比干黏滞性低,因为水分降低了油墨的黏滞性。
由此可知,润版液量对油墨的黏滞性有直接影响,即对堆积现象有直接影响。
一般情况下,油墨的黏滞性随着润版液量的增加而降低,但是受油墨种类、机型和墨辊的温度等诸多因素的影响,也有其他实验情况表明,油墨的湿黏滞性随着润版液量的增加而不一定总是降低。
因此我们必须注意观察和调整。
(2)润版液量除对堆积在橡皮布上的纸粉和油墨的影响外,纸粉、纸张涂料也能被润版液黏附和溶解,从而堆积在橡皮布上。
这种堆积现象多发生在易堆积性高的纸张上,并且堆积在橡皮布表面非图文部分。
当堆积量达到一定程度后,就会向印迹部分扩展。
在墨层厚度、油墨黏滞性、温度、湿度和实地密度等条件不变的情况下,只要润版液给足一些,橡皮布上就没有这种堆积物存在。
当然,这里所讲的把润版液给足一些,是在即使多用一些润版液印刷,也不会使印品出现水迹,并保证印品质量的前提下。
(3)有些胶印工教条地追求“水墨平衡”,印刷过程中不断地减少水量,而忽视了上述堆积效应对印迹变浅的的影响,结果使堆积现象加重,印迹继续变浅。
综上所述,在胶印过程中,由于堆积效应造成印刷质量显著变化——印迹不断变浅。
这种堆积是不可不可避免的,除了用勤洗橡皮布来保证印刷质量外,还必须调整油墨黏滞性,另外,当整批印件所用的润版液量都超过所印站特定的堆积极限值,洗橡皮布的间隔就会大大延长,这时对排除印迹变浅的故障,保证整批印件深浅一致有很大作用。
二.除了堆积原因外还有以下几种情况也会造成印迹变浅
1、一般情况下,当润版液量增加时,墨层厚度就会降低,这是操作人员能及时发现并调整,但有些油墨因吸水量大,印刷时情况却相反,再使用这类油墨印刷时操作人员常常会按常规做法减少润版用液量,想使印迹变深,反而印迹继续变浅。
2、胶印过程中油墨加放燥油太多。
停机后墨辊、墨斗辊上的墨层很快干固,使其吸附油墨的能力传墨性能减弱,重新开印时造成传墨量变少,使印迹突然变浅,有时印刷中途由于墨辊上墨层很薄也会逐渐干固,使印迹很快变浅(网目调试印刷易发生此现象)。
3、由于未勤观察墨斗,未及时发现墨斗内墨量水平面降低过多,或墨斗的油墨触变性过大,流动性过差,使油墨量减少,造成印迹变浅。
4、在整批印件印刷过程中,部分纸品的平滑度,吸墨性能突然变差,也会造成印迹变浅。
5、印刷过程中,印版的图文部分在着水辊、着墨辊、橡皮滚筒以及纸张上脱落下来的纸粉,纸毛的反复摩擦下,感光层逐渐被磨损、破坏,亲油性减弱,亲水性增强,有时印版的图文部分会逐渐变的着墨不良,使印迹变浅(用烤版处理的方法增强感光层抗磨损能力,可以延长印迹变浅时间)。
6、高速胶印机的滚筒直径较小,在滚压过程中压印的宽度也相应减少,印刷中途若突然较大的增加印刷速度而印刷压力没有相应增大,也会使印迹变浅,这是因为,当印刷速度提高时,必然使印版与橡皮布,橡皮布与印张之间互相对应的点所接触的时间相应的减少使印刷面之间不完全接触的可能性增大,引起图文转移不完整,网点不实,墨色灰淡。