铸造工艺常见的缺陷及质量控制措施
铸造工艺流程中的铸件缺陷分析与改进策略

铸造工艺流程中的铸件缺陷分析与改进策略铸造工艺是一种重要的金属加工方法,用于制造各种形状的金属件。
然而,在铸造过程中,铸件缺陷是一个常见的问题,它会影响到铸件的质量和性能。
因此,对于铸造工艺流程中的铸件缺陷进行深入分析,并提出改进策略,对于提高铸件质量和工艺效率具有重要意义。
一、铸件缺陷的分类与原因分析在铸造工艺中,铸件缺陷可以分为表面缺陷和内部缺陷两类。
常见的表面缺陷包括气孔、砂眼、砂洞等;内部缺陷主要有夹杂物、孔洞、收缩系数不均匀等。
1.1 气孔气孔是铸造工艺中最常见的表面缺陷之一。
其形成的原因通常有两个方面,一是液态金属中溶解气体含量过高,二是在金属凝固过程中,气体生成而未能有效排除。
造成气孔的常见因素包括砂芯质量不佳、浇注温度过高、浇注速度过快等。
1.2 砂眼和砂洞砂眼是指铸件表面局部凹陷的缺陷,而砂洞是指铸件内部或边缘凹陷的缺陷。
主要原因包括模具缺陷、浇注系统设计不合理、浇注金属温度过低等。
1.3 夹杂物夹杂物是指铸件中存在的杂质,如炉渣、油污等。
其主要原因包括铁水净化不彻底、砂芯质量不佳等。
1.4 孔洞孔洞是指铸件内部存在的封闭空腔。
常见的孔洞形式包括气孔和收缩孔。
造成孔洞的原因主要有铁水中含气量高、铸型泥浆含水量高等。
1.5 收缩系数不均匀收缩系数不均匀是指铸件不同部位的收缩量不一致。
这可能会引起铸件的内部应力集中,从而导致开裂和变形。
收缩系数不均匀的原因包括铸造合金的特性、浇注温度的控制等。
二、改进策略为了减少铸件缺陷,提高铸件质量和工艺效率,以下是一些改进策略的具体措施:2.1 优化模具设计模具设计是影响铸件质量的关键因素之一。
通过优化模具结构、提高模具材料质量和表面光洁度,可以减少砂眼、砂洞等表面缺陷的产生。
2.2 控制浇注温度和速度浇注温度和速度对铸件质量有着直接的影响。
合理控制浇注温度和速度,可以降低气孔和夹杂物等缺陷的产生。
2.3 改进铸型材料和工艺选择合适的铸型材料,对铸件质量和工艺效率的提高至关重要。
铸造工艺流程的质量控制方法
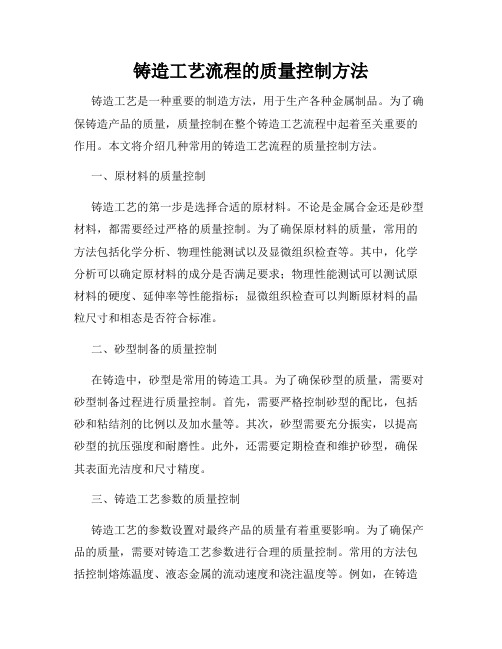
铸造工艺流程的质量控制方法铸造工艺是一种重要的制造方法,用于生产各种金属制品。
为了确保铸造产品的质量,质量控制在整个铸造工艺流程中起着至关重要的作用。
本文将介绍几种常用的铸造工艺流程的质量控制方法。
一、原材料的质量控制铸造工艺的第一步是选择合适的原材料。
不论是金属合金还是砂型材料,都需要经过严格的质量控制。
为了确保原材料的质量,常用的方法包括化学分析、物理性能测试以及显微组织检查等。
其中,化学分析可以确定原材料的成分是否满足要求;物理性能测试可以测试原材料的硬度、延伸率等性能指标;显微组织检查可以判断原材料的晶粒尺寸和相态是否符合标准。
二、砂型制备的质量控制在铸造中,砂型是常用的铸造工具。
为了确保砂型的质量,需要对砂型制备过程进行质量控制。
首先,需要严格控制砂型的配比,包括砂和粘结剂的比例以及加水量等。
其次,砂型需要充分振实,以提高砂型的抗压强度和耐磨性。
此外,还需要定期检查和维护砂型,确保其表面光洁度和尺寸精度。
三、铸造工艺参数的质量控制铸造工艺的参数设置对最终产品的质量有着重要影响。
为了确保产品的质量,需要对铸造工艺参数进行合理的质量控制。
常用的方法包括控制熔炼温度、液态金属的流动速度和浇注温度等。
例如,在铸造过程中,如果熔炼温度过高,易导致铸件内部存在气孔和夹杂物;如果浇注温度过低,易导致铸件的收缩缺陷。
因此,合理控制这些参数可以有效提高铸件的质量。
四、铸造产品的检测与测试在铸造工艺流程中,对铸造产品进行质量检测和测试是不可或缺的环节。
常用的方法包括无损检测、机械性能测试以及尺寸测量等。
其中,无损检测可以通过X射线、超声波等方法检测产品是否存在缺陷;机械性能测试可以测试产品的抗拉强度、硬度等力学性能;尺寸测量则可以验证产品的尺寸精度是否符合要求。
五、质量记录与反馈为了总结经验并改进铸造工艺流程,需要对质量进行记录和反馈。
对于每个铸造批次,应该记录原材料、砂型、工艺参数以及产品质量等关键信息。
常见铸造缺陷的产生原因及其预防措施
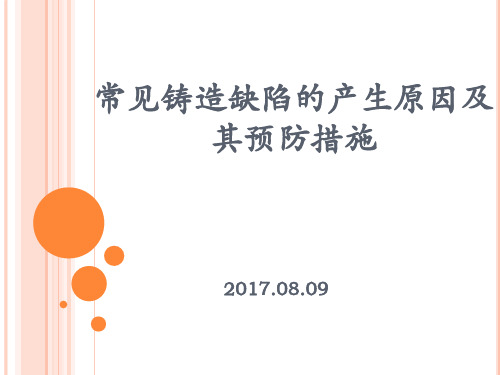
多肉产生的原因:
1、模具原因。 2、砂(芯)型起破。 3、砂(芯)型损坏 4、砂芯和砂型相接 表面不吻合
5、冷铁和模具不吻 合。
6、砂(芯)局部部 位未充满。
冷铁和模具不吻 合引起的铸件多
肉
多肉类缺陷的预防措施
(1) 提高铸型紧实度(下箱型砂的紧实度应高于 上箱的紧实度),避免局部过松;
(2)调整混砂工艺、控制水分,提高型砂强度; (3) 降低浇包的位置、降低浇注速度; (4) 铸型的分型面多压坭条或石棉绳; (5) 坭芯间的可见披缝尽量补死; (6) 需放置直接外冷铁时,外冷铁与铸件的接
根据GB/T 5611-1988《铸造术语》规定,将铸造缺陷 分为八大类。
① 多肉类缺陷 ② 孔洞类缺陷 ③ 裂纹、冷隔类缺陷 ④ 表面缺陷 ⑤ 残缺类缺陷 ⑥ 形状及重量差错类缺陷 ⑦ 夹杂类缺陷 ⑧ 性能、成分、组织不合格
分类(1)
大 类
序 号
缺陷名称
特征
1
飞翅(飞边、 产生在铸件分型面、坭芯间隙处、坭芯与
裂处金属表皮不氧化。
在铸件表面有未完全融合的缝隙或 洼坑,其交接边缘是光滑的。
热裂和冷裂(1) 热裂
图6-1 铸钢件的外热裂
冷裂
热裂和冷裂(2)
冷隔(1)
局 部 放 大
叶片机座 冷隔缺陷
冷隔(2)
典型的冷隔特 征
裂纹冷隔类缺陷的预防措施
(1) 严格按照化学成分的要求,控制钢水中的 S、 P含量;
触面一定要打磨平整; (7) 合箱后,注意保证上、下箱连接位置的紧固,
需放置压铁时上、下箱之间要用冷铁尖死。
分类(2-1)
大 类
序 号
缺陷名称
特征
孔 洞
铸钢件常见铸造缺陷及预防措施
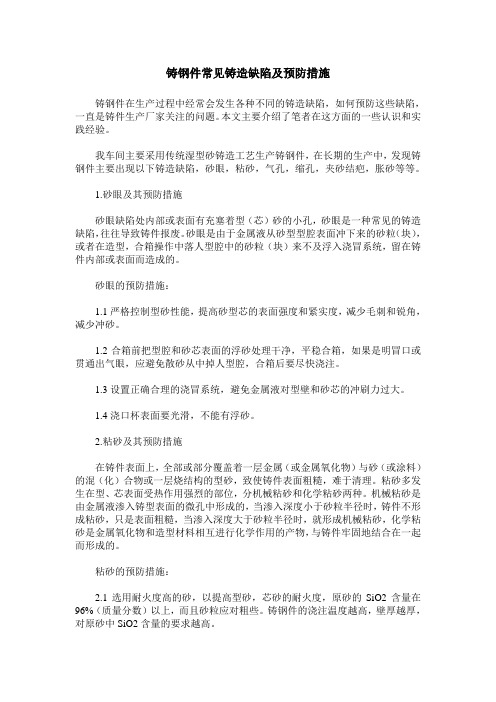
铸钢件常见铸造缺陷及预防措施铸钢件在生产过程中经常会发生各种不同的铸造缺陷,如何预防这些缺陷,一直是铸件生产厂家关注的问题。
本文主要介绍了笔者在这方面的一些认识和实践经验。
我车间主要采用传统湿型砂铸造工艺生产铸钢件,在长期的生产中,发现铸钢件主要出现以下铸造缺陷,砂眼,粘砂,气孔,缩孔,夹砂结疤,胀砂等等。
1.砂眼及其预防措施砂眼缺陷处内部或表面有充塞着型(芯)砂的小孔,砂眼是一种常见的铸造缺陷,往往导致铸件报废。
砂眼是由于金属液从砂型型腔表面冲下来的砂粒(块),或者在造型,合箱操作中落人型腔中的砂粒(块)来不及浮入浇冒系统,留在铸件内部或表面而造成的。
砂眼的预防措施:1.1严格控制型砂性能,提高砂型芯的表面强度和紧实度,减少毛刺和锐角,减少冲砂。
1.2合箱前把型腔和砂芯表面的浮砂处理干净,平稳合箱,如果是明冒口或贯通出气眼,应避免散砂从中掉人型腔,合箱后要尽快浇注。
1.3设置正确合理的浇冒系统,避免金属液对型壁和砂芯的冲刷力过大。
1.4浇口杯表面要光滑,不能有浮砂。
2.粘砂及其预防措施在铸件表面上,全部或部分覆盖着一层金属(或金属氧化物)与砂(或涂料)的混(化)合物或一层烧结构的型砂,致使铸件表面粗糙,难于清理。
粘砂多发生在型、芯表面受热作用强烈的部位,分机械粘砂和化学粘砂两种。
机械粘砂是由金属液渗入铸型表面的微孔中形成的,当渗入深度小于砂粒半径时,铸件不形成粘砂,只是表面粗糙,当渗入深度大于砂粒半径时,就形成机械粘砂,化学粘砂是金属氧化物和造型材料相互进行化学作用的产物,与铸件牢固地结合在一起而形成的。
粘砂的预防措施:2.1选用耐火度高的砂,以提高型砂,芯砂的耐火度,原砂的SiO2含量在96%(质量分数)以上,而且砂粒应对粗些。
铸钢件的浇注温度越高,壁厚越厚,对原砂中SiO2含量的要求越高。
2.2适当降低浇注温度和提高浇注速度,减轻金属液对砂型的热力学和物理化学作用。
2.3砂型紧实度要高(通常大于85)且均匀,减少砂粒间隙;型、芯修补到位,不能有局部疏松。
铸造工艺常见的缺陷及质量控制措施
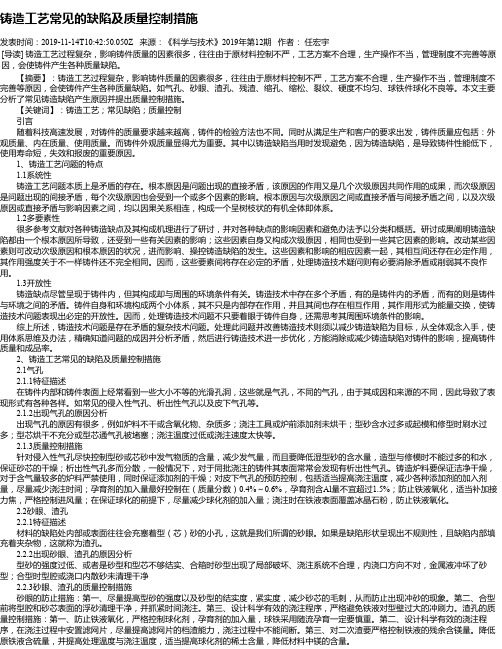
铸造工艺常见的缺陷及质量控制措施发表时间:2019-11-14T10:42:50.050Z 来源:《科学与技术》2019年第12期作者:任宏宇[导读] 铸造工艺过程复杂,影响铸件质量的因素很多,往往由于原材料控制不严,工艺方案不合理,生产操作不当,管理制度不完善等原因,会使铸件产生各种质量缺陷。
【摘要】:铸造工艺过程复杂,影响铸件质量的因素很多,往往由于原材料控制不严,工艺方案不合理,生产操作不当,管理制度不完善等原因,会使铸件产生各种质量缺陷。
如气孔、砂眼、渣孔、残渣、缩孔、缩松、裂纹、硬度不均匀、球铁件球化不良等。
本文主要分析了常见铸造缺陷产生原因并提出质量控制措施。
【关键词】:铸造工艺;常见缺陷;质量控制引言随着科技高速发展,对铸件的质量要求越来越高,铸件的检验方法也不同。
同时从满足生产和客户的要求出发,铸件质量应包括:外观质量、内在质量、使用质量。
而铸件外观质量显得尤为重要。
其中以铸造缺陷当用时发现避免,因为铸造缺陷,是导致铸件性能低下,使用寿命短,失效和报废的重要原因。
1、铸造工艺问题的特点1.1系统性铸造工艺问题本质上是矛盾的存在。
根本原因是问题出现的直接矛盾,该原因的作用又是几个次级原因共同作用的成果,而次级原因是问题出现的间接矛盾,每个次级原因也会受到一个或多个因素的影响。
根本原因与次级原因之间或直接矛盾与间接矛盾之间,以及次级原因或直接矛盾与影响因素之间,均以因果关系相连,构成一个呈树枝状的有机全体即体系。
1.2多要素性很多参考文献对各种铸造缺点及其构成机理进行了研讨,并对各种缺点的影响因素和避免办法予以分类和概括。
研讨成果阐明铸造缺陷都由一个根本原因所导致,还受到一些有关因素的影响;这些因素自身又构成次级原因,相同也受到一些其它因素的影响。
改动某些因素则可改动次级原因和根本原因的状况,进而影响、操控铸造缺陷的发生。
这些因素和影响的相应因素一起,其相互间还存在必定作用,其作用强度关于不一样铸件还不完全相同。
铸造中常见缺陷及其处理方法
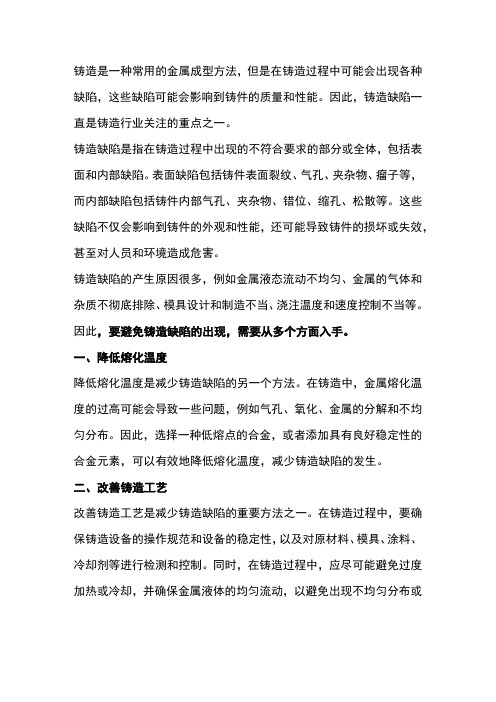
铸造是一种常用的金属成型方法,但是在铸造过程中可能会出现各种缺陷,这些缺陷可能会影响到铸件的质量和性能。
因此,铸造缺陷一直是铸造行业关注的重点之一。
铸造缺陷是指在铸造过程中出现的不符合要求的部分或全体,包括表面和内部缺陷。
表面缺陷包括铸件表面裂纹、气孔、夹杂物、瘤子等,而内部缺陷包括铸件内部气孔、夹杂物、错位、缩孔、松散等。
这些缺陷不仅会影响到铸件的外观和性能,还可能导致铸件的损坏或失效,甚至对人员和环境造成危害。
铸造缺陷的产生原因很多,例如金属液态流动不均匀、金属的气体和杂质不彻底排除、模具设计和制造不当、浇注温度和速度控制不当等。
因此,要避免铸造缺陷的出现,需要从多个方面入手。
一、降低熔化温度降低熔化温度是减少铸造缺陷的另一个方法。
在铸造中,金属熔化温度的过高可能会导致一些问题,例如气孔、氧化、金属的分解和不均匀分布。
因此,选择一种低熔点的合金,或者添加具有良好稳定性的合金元素,可以有效地降低熔化温度,减少铸造缺陷的发生。
二、改善铸造工艺改善铸造工艺是减少铸造缺陷的重要方法之一。
在铸造过程中,要确保铸造设备的操作规范和设备的稳定性,以及对原材料、模具、涂料、冷却剂等进行检测和控制。
同时,在铸造过程中,应尽可能避免过度加热或冷却,并确保金属液体的均匀流动,以避免出现不均匀分布或过热的情况,从而减少铸造缺陷的发生。
三、质量检测和控制质量检测和控制是减少铸造缺陷的关键步骤之一。
在铸造完成后,应对铸件进行全面的检测和控制包括X射线检测、超声波检测、金相分析、硬度测试等。
通过这些检测和控制方法,可以及时发现铸造缺陷,及时采取措施进行修复或重新铸造,从而保证铸件的质量和稳定性。
四、培养专业人才铸造行业的专业人才对于减少铸造缺陷的重要性不言而喻。
铸造行业需要拥有一批专业的技术人员和工人,他们能够理解和掌握铸造技术的各个方面,并能够在实践中灵活应对各种情况。
因此,铸造企业应该加强人才培养和引进工作,提高行业整体素质,从而减少铸造缺陷的发生。
再生铝合金铸造工艺中的铸造缺陷与缺陷控制技术

再生铝合金铸造工艺中的铸造缺陷与缺陷控制技术铸造工艺在现代工业生产中扮演着重要的角色,而铸造缺陷是不可避免的问题,尤其在再生铝合金铸造过程中更是如此。
因此,探索铸造缺陷的成因及相应的缺陷控制技术具有重要的理论意义和实践价值。
本文将分析再生铝合金铸造工艺中常见的缺陷,并探讨相应的解决方法。
首先,再生铝合金铸造工艺中常见的铸造缺陷之一是气孔。
气孔是由于铝合金液体在凝固过程中释放的气体未能完全逸出所形成的。
气孔不仅会降低铝合金件的强度和密封性,还会影响其外观品质。
针对气孔问题,工程师们往往采取增加浇注系统的压力、增加液态金属的保温时间和采用适当的浇注温度等措施,以促使气体逸出,从而减少气孔的产生。
其次,再生铝合金铸造工艺中常见的另一个缺陷是缩松。
缩松是铝合金凝固过程中由于体积收缩而形成的空洞或裂纹。
缩松缺陷会降低铝合金件的承载能力和韧性。
为了避免缩松,可以通过优化浇注系统设计,采用合适的冶炼工艺和浇注温度,以及合理控制凝固速率等方式进行控制。
此外,再生铝合金铸造工艺中还存在着夹杂物的产生。
夹杂物是指杂质或其他金属的颗粒在铝合金液体中未能被有效去除而造成的。
夹杂物会降低铝合金的强度和塑性,同时也会对铝合金件的外观造成影响。
为了解决夹杂物问题,工程师们通常采取净化熔体、增加浇注速度、优化浇注系统设计以及采用合适的过滤器等技术手段。
最后,再生铝合金铸造工艺中还需关注晶粒度的控制。
晶粒度是指铝合金凝固过程中晶粒的大小,对铝合金件的力学性能和耐磨性能有着重要影响。
通常情况下,大晶粒度会导致铝合金件的塑性下降,而小晶粒度则会影响铝合金件的强度。
为了控制晶粒度,可以通过合适的铸造参数、合金元素添加和合理的工艺操作等方法进行调控。
再生铝合金铸造工艺中的铸造缺陷控制技术是一个复杂而关键的问题。
工程师们需要深入研究缺陷产生的机理,结合实际情况,寻找最佳的解决方案。
通过优化工艺参数、改进铸造设备和引入先进的检测技术,可以有效地降低再生铝合金铸造工艺中的缺陷产生,提高铝合金件的质量和性能。
压力铸造缺陷、问题及对策实例集
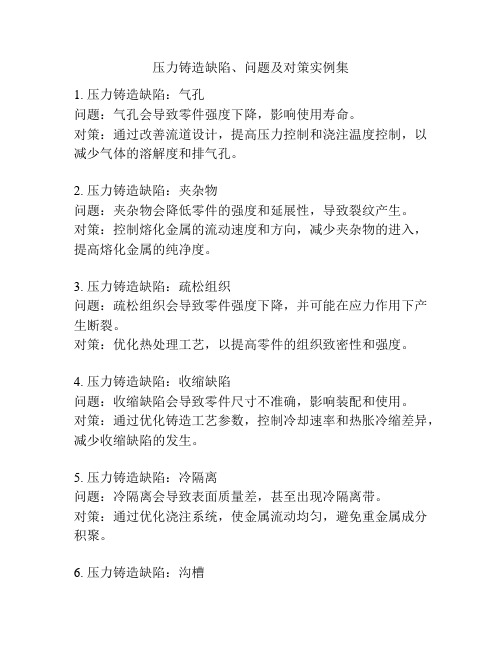
压力铸造缺陷、问题及对策实例集1. 压力铸造缺陷:气孔问题:气孔会导致零件强度下降,影响使用寿命。
对策:通过改善流道设计,提高压力控制和浇注温度控制,以减少气体的溶解度和排气孔。
2. 压力铸造缺陷:夹杂物问题:夹杂物会降低零件的强度和延展性,导致裂纹产生。
对策:控制熔化金属的流动速度和方向,减少夹杂物的进入,提高熔化金属的纯净度。
3. 压力铸造缺陷:疏松组织问题:疏松组织会导致零件强度下降,并可能在应力作用下产生断裂。
对策:优化热处理工艺,以提高零件的组织致密性和强度。
4. 压力铸造缺陷:收缩缺陷问题:收缩缺陷会导致零件尺寸不准确,影响装配和使用。
对策:通过优化铸造工艺参数,控制冷却速率和热胀冷缩差异,减少收缩缺陷的发生。
5. 压力铸造缺陷:冷隔离问题:冷隔离会导致表面质量差,甚至出现冷隔离带。
对策:通过优化浇注系统,使金属流动均匀,避免重金属成分积聚。
6. 压力铸造缺陷:沟槽问题:沟槽会导致零件表面不光滑,影响美观和功能。
对策:优化模具设计,控制浇注温度,避免金属流动速度过快导致沟槽产生。
7. 压力铸造缺陷:冷流痕问题:冷流痕会导致零件内部应力集中,容易产生裂纹。
对策:优化浇注系统,控制金属流动方向和速度,减少冷流痕的产生。
8. 压力铸造缺陷:灰斑问题:灰斑会降低零件的密度和强度。
对策:加强金属液的搅拌和过滤,减少灰斑产生。
9. 压力铸造缺陷:烧痕问题:烧痕会导致零件表面质量差,影响产品外观。
对策:控制铸模温度和冷却速度,避免金属液温度过高导致烧痕。
10. 压力铸造缺陷:渗透性差问题:渗透性差会导致零件内部孔隙和缺陷。
对策:加强模具密封和浇注压力控制,提高渗透性,减少缺陷的发生。
- 1、下载文档前请自行甄别文档内容的完整性,平台不提供额外的编辑、内容补充、找答案等附加服务。
- 2、"仅部分预览"的文档,不可在线预览部分如存在完整性等问题,可反馈申请退款(可完整预览的文档不适用该条件!)。
- 3、如文档侵犯您的权益,请联系客服反馈,我们会尽快为您处理(人工客服工作时间:9:00-18:30)。
力焦 , 严格 控制进 风量 。 在保 证球化 的前 提下, 尽量减 少球化 剂 的加 入 量, 浇注 时在铁液 表面覆盖 冰晶石粉 , 防止铁液 氧化。 2 , 砂眼 . 渣 孔 2 . 1 特征 描述 : 材料 的缺陷处 内部或 表面往往会充 塞着型 ( 芯) 砂的 t J , : t L , 这 就是我们 所谓 的砂眼 。 如果 是缺 陷形状 呈现 出不规 则性 , 且缺 陷内部填 充着夹杂物 , 这就 称为渣孔 。 。 2 . 2 出现砂 眼 渣孔 的原因分析: 型砂 的强度过低 、 或者是 砂型和 型 芯 不够结 实、 合 箱时砂 型出现 了局部 破 坏、 浇注 系统 不合理 , 内浇 I Z l 方 向不对 , 金 属液冲坏 了砂 型; 合型时 型腔或浇 口 内散砂未清 理干净 2 . 3 砂眼、 渣孔 的质 量控制措 施 : 砂眼的 防止措施 : 第一 、 尽量提高 型砂 的强度 以及砂 型的结 实度 , 紧实度 , 减 少砂芯的 毛 刺, 从 而防止 出 现 冲砂的现 象 。 第二 、 合型前 将型腔 和砂 芯表面 的浮砂 清理干净 , 并抓 紧 时间浇注 。 第 三、 设 计科学 有效 的浇注 程序 , 严 格避免 铁液对 型壁过 大 的冲刷 力。 渣孔 的质量 控制措施 : 第一、 防止铁 液氧化, 严格 控制球化 剂, 孕 育剂 的加 入量 , 球 铁 采用随 流孕 育一定 要慎重 。 第二、 设 计科 学 有 效的浇 注程 序, 在 浇注过 程中安置滤 网片, 尽量 提高滤 网片 的档渣 能 力, 浇注 过程 中不能间断 。 第三 、 对二 次渣要严格 控 制铁液 的残 余含 镁 量。 降低原铁 液含硫 量 , 并提高处 理温 度与浇注 温度 , 适 当提高 球化 剂 的稀 土含量 , 降低材 料 中镁的 含量。
铸造工艺常见的缺陷及质量控制措施
张振 中信戴卡股份有限公司 河北秦皇 岛 0 6 6 0 1 1
【 摘要】 铸 造工艺过程 复杂, 影响铸件质量的因素很多, 往往 由于原 结晶, 这 些孔洞 中较 大而且较 为密集的称 为缩孔 , 较小而 又分 散的孔 洞 材料控制不严, 工艺方案不合 理, 生产操作 不当, 管理制度 不完善 等 原 因, 称为缩松 。 会 使铸 件产生各 种质量缺 陷。如气孔、 砂眼、 渣孔 、 残渣 、 缩孔、缩松、裂 4 . 2 出现缩孔 、 缩 松缺 陷的原因分析 : 一旦金属液 遇冷凝 固时, 这个 纹、 硬度不 均匀 、 球 铁件球 化不良等。 本文主要 分析了 常见铸造缺 陷 产生原 过程 中产 生的 液态 收缩 和 凝固收 缩是 远远 超过 于固态收 缩 的, 而且 铸 因并提 出质 量控 制 措 施 。 件表面最后凝 固的地 方往往很 难得到应有 的金属液 。 4 . 3 缩孔, 缩松缺 陷的质 量控 制措施 : 【 关键词 】 铸造 ; 工艺; 缺 陷; 措施 第一 、 不 同的铸 件 , 壁厚 不 同, 相 应的 化学成 分不 同, 尽量 控制 好 镁 的含量 , 第二、 设计 科学 的浇注 系统 , 适 当降低 浇注 的温 度,尽量 使 1 . 气 孔 第三、 严 格控制 好炉前孕育剂 的含 1 . 1 特征 描述 : 在铸 件 件表面各处 都能得 到充分补缩 ; 一 般情况下, O . 3 %-0 . 5 %的含量较佳 ; 第四、 避 免铁 液氧化 。 光 滑孔 洞 , 这 些就是 气孔, 不 同的气孔 , 由于其成 因和 来源的不 同, 因此 量 , 导 致了表 现形 式有各种各 样。 如常见的侵 入性气孔 、 析 出性 气孔以及 皮 5 、 裂 纹 5 . 1 裂 纹特征 描述 : 浇 注好 的铸 件表面一 般都 弯曲的裂 纹 。 裂纹 分 下气孔等 1 . 2 出现气孔 的原因分析: 出现气孔 的原 因有很多, 例如炉 料不干或 热 裂和冷 裂两种。 热裂 的裂 口 形 状不规 则, 端I Z l 表面 的颜 色往往 呈现 出 含 氧化物 、 杂质多, 浇 注工具 或炉前 添加 剂未烘 干; 型砂含 水过 多或 起 深 黑色 , 氧化现 象较 为 明显, 且 较为 曲折 。 而 冷裂 的裂 口和热 裂弯 曲不 模 和修 型时刷水过 多 , 型芯烘 干不充分或 型芯通气孔被 堵塞 , 浇注温 度 同, 裂口比较直 , 形 状较为规 则, 且铸件断 口表面 的氧化现 象比较轻微 , 发 出金 属光泽 。 过低或 浇注 速度太快 等。 1 . 3 质 量控制措 施 : 针对侵 入性 气孔尽快 控制 型砂 或芯砂 中发气物 5 . 2 产生裂纹的原因分析 : 铸 件遇冷凝 固收缩 , 在这个过程 中会产生 质的含 量 , 减少发 气量 , 而且要 降低湿 型砂 的含水 量 , 造型与修 模时不 内部应 力, 一旦应 力大于材料 的屈服 极限, 铸件救 出出现 裂纹现象 。 能 过多的和 水 , 保证砂 芯的干燥 ; 析 出性 气孔多而分 散 , 一 般情况下, 对 5 . 3 预防裂纹 的质 量控制措 施 : 第一 、 铁 液 的化学成 分 必须要 控制 于 同批 浇注 的 铸件 其表 面常常会 发现 有析 出性 气孔 。 铸 造炉 料要 保证 好。 其中硫的含 量能够影 响 “ 热脆性 ” 的产生, 在 灰铸铁 中, w( s ) 的含量 洁净干燥 , 对 于含气 量较多的炉料 严禁使 用, 同时保证 添加剂 的干燥 ; 不能低 于O . 1 1 %, 但 是也 不能 太高 , 过高 的话 会影 响孕育效 果 。 磷 的含 对皮下气孔的预 防控制 , 包括适 当提 高浇注 温度 , 减少各种 添加 剂的加 量 是影 响铸件发生 “ 冷脆性 ” 的因素 , 进 而产生冷裂缺 陷, 所以 , 灰铸铁 中w( P ) 最好 低于0 . 1 3 %; 第二 、 控 制铸 件各个 部位 的冷却 速度 , 防止局 入剂量 , 尽量减 少浇 注时 间, 孕育剂的加 入 量最好 控制在 ( 质量 分数 ) 第三、 当进行 完浇注 以后 , 不能过早 的开型, 只有当型 0 . 4 %~0 . 6 %, 孕育剂含A1 量不宜超 过 1 . 5 ‰ 防止铁液 氧化 , 适当补加接 部 产生过热 现象 ;