基于快速成形技术的汽车覆盖件金属模具制造
浅谈汽车车身覆盖件现状及制造工艺发展

浅谈汽车车身覆盖件现状及制造工艺发展摘要:为了满足人们对未来汽车车身越来越高的品质追求,同时达到轻量化目的和降低车身生产成本。
对汽车车身覆盖件在外形、轻量化、成形工艺、加工工艺、模具共性问题等方面进行现状梳理和概述。
通过对车身覆盖件现状的概述和制造技术的梳理,提出汽车车身覆盖件向一体化、低成本和轻量化方向的发展趋势。
关键词:汽车车身;车身件生产技术;现状;制造工艺;发展;轻量化引言当前在我国汽车生产总量逐年增加的同时,汽车销量也多年稳居全球汽车销量第一。
汽车在人们日常生活中出现频次的增加,也使得各行各业对汽车成本以及汽车质量的考核越来越重视。
纵观汽车制造行业,从前期市场调研,产品定位、研发到后期生产制造全线,汽车车身质量在整个汽车的总质量中占比约40%~50%。
从汽车外形来看,车身在面积上基本覆盖了整个汽车。
基于此就足以看出,车身在汽车质量方面以及在汽车覆盖面积方面举足轻重的影响力,所以,无论在汽车研发过程中对车身的研发还是在汽车车身生产过程中都需要大量人力物力以及能源的投入与消耗,因此,在汽车车身生产技术传承的基础上,车身技术的发展需要加快新技术的突破。
1车身覆盖件发展现状1.1覆盖件造型汽车车身覆盖件是汽车与空气接触面积最大的部分,车身覆盖件造型的敲定也决定了整车的造型,所以,车身覆盖件的设计不仅要让汽车外形更加贴合空气动力学,让汽车外形更具有科技感,同时也需要迎合大众审美。
在汽车行业中,如果要上一款新车,造型设计前需要做大量的调研和模拟论证工作,比如市场调研、对标车型确定、客户群确定等等。
比如,一辆跑车要设计一种特殊造型的汽车尾翼,可通过 CFD 模拟验证该尾翼在汽车行驶过程中产生下压力的效果,先做出了性能评价,再通过对现有跑车外形进行三维建模和对模型进行空气动力学仿真,结合仿真模拟结果对局部造型进行优化来达到了降低空气阻力的目的,使得尾翼的设计更合理,进而整车造型更完美。
1.2轻量化在2016年10月中国汽车工程学会年会上发布的《节能与新能源汽车技术路线图》中显示,到2030年要大幅度增加高强度钢的应用,单车用铝合金超过350 kg ,碳纤维超过总质量的5%。
汽车覆盖件模具设计

覆盖件冲压工艺方案制定又称工法设计,简称DL设计。工法图也称DL图。
覆盖件的主要冲压工序有: 落料、拉延、整形、修边、切断、翻边、冲孔等,其中最关键的工序是拉延
工序。绝大多数覆盖件通过拉延工序得到全部或部分形状。确定拉延工艺方案是 覆盖件冲压分析的第一步。
汽车覆盖件模具设计 ppt 课件
工艺分析的概念
绝大多数覆盖件由3到5套模具冲压得到,即3到5道冲压工序 ,以下是常见 的几种工序排布方案:
1、拉延(DR)→修边冲孔(TR+PI)→整形(RST) 2、拉延(DR) →修边冲孔(TR+PI) →整形(翻边)(RST)→整形 (侧整、侧修、侧修)(RST+CTR+CPI) 3、落料(BL)→拉延(DR) →修边冲孔(TR+PI) →整形)(RST) → 整形)(RST)
顶盖前横梁没有翻边,形状不复杂,不需要整形。其有两处翻孔,翻孔的工 艺应考虑为先冲孔再翻孔。综上所述,顶盖前横梁应有三道工序:拉延→修边冲 孔→翻孔。考虑到冲孔较多,如果在第二序修边时冲完所有的孔,模具设计有困 难,上模没有足够的空间来布置弹簧、导板、限位螺栓等,模具强度弱,所以应 移一部分孔到3/3工序。
中文 废料 基准侧 公差 CAD数据 刃口间隙 让空 冲压 粗加工 下模重量 上模重量 总重量 冲压方向 送料行程 双凸轮 水平凸轮
英文 UPPER DIE BASE MATCH FACE TRIM STEEL FL UP FL DOWN MATERIAL FINISH CONCAVE CONVEX DIE HEIGHT FEED LEVEL PUNCH RETAINER START POINT PART DRAWING CHECKING FIXTURE
汽车覆盖件模具设计TR+PI+BL报告

汽车覆盖件模具设计TR+PI+BL报告汽车覆盖件模具设计TR+PI+BL报告一、概述汽车覆盖件是汽车外部装饰件的统称,如车身、车门、前后保险杠、轮毂罩等。
这些部件的设计与制造需要使用模具。
本报告介绍了汽车覆盖件模具的设计方法,并以TR覆盖件为例,详细介绍了PI和BL两种模具的设计。
二、TR覆盖件TR覆盖件是一种车身外部覆盖件,通常由塑料或复合材料制成。
它的设计需要考虑材料的性质、外观的美观、工艺的复杂度和成本等因素。
TR覆盖件的制造通常分为三个阶段:模具制造、注塑成型和后处理。
三、PI模具设计PI模具是一种用于制造TR覆盖件的模具,它由多个部件组成,包括模板、进口、出口、针嘴和膜片等。
PI模具的设计需要考虑以下因素:1.材料选择:PI模具需要承受高温和高压,因此需要选择耐热耐压的材料。
2.模块设计:PI模具通常由多个模块组成,每个模块的设计需要考虑到装配的方便性、精度和易于维护。
3.注塑系统设计:注塑系统包括进口、出口、针嘴和膜片等。
每个部件的位置和尺寸需要按照TR覆盖件的设计要求精确定位,以确保注塑的质量。
4.冷却系统设计:冷却系统可以帮助加快注塑周期和减少成本。
因此,冷却系统的设计需要考虑到冷却效果和均匀性。
四、BL模具设计BL模具是一种用于制造TR覆盖件的模具,它由钢和铜制成。
BL模具的设计需要考虑以下因素:1.材料选择:BL模具需要承受高温和高压,因此需要选择高强度、耐磨损、耐热的材料。
2.模块设计:BL模具也通常由多个模块组成。
模块的设计需要考虑到装配的方便性、精度和易于维护。
3.冷却系统设计:冷却系统对于BL模具的制造非常重要。
因为铜的热传导性能好,而钢的热传导性能较差,所以冷却系统需要确保模具的各个部分均匀受冷却。
4.工艺参数:制造BL模具需要控制一系列的工艺参数,如冷却时间、加热时间、加热温度、压力等。
这些参数需要根据不同的材料和模具的特性来确定,以确保制造出高质量的TR 覆盖件。
汽车覆盖件冲压模具制造工艺特点
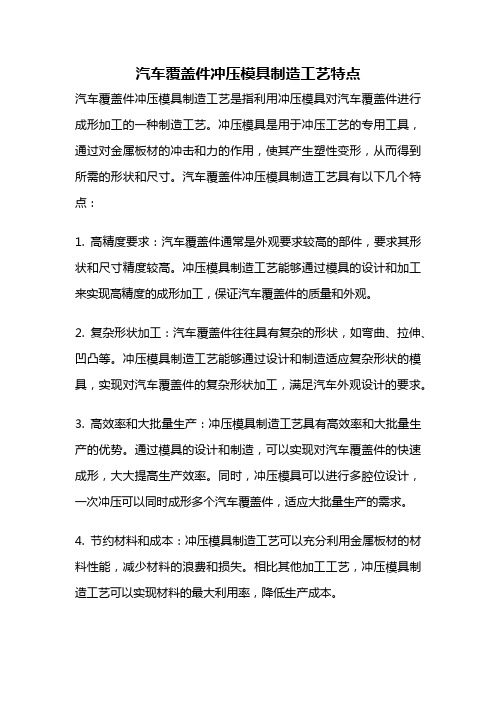
汽车覆盖件冲压模具制造工艺特点汽车覆盖件冲压模具制造工艺是指利用冲压模具对汽车覆盖件进行成形加工的一种制造工艺。
冲压模具是用于冲压工艺的专用工具,通过对金属板材的冲击和力的作用,使其产生塑性变形,从而得到所需的形状和尺寸。
汽车覆盖件冲压模具制造工艺具有以下几个特点:1. 高精度要求:汽车覆盖件通常是外观要求较高的部件,要求其形状和尺寸精度较高。
冲压模具制造工艺能够通过模具的设计和加工来实现高精度的成形加工,保证汽车覆盖件的质量和外观。
2. 复杂形状加工:汽车覆盖件往往具有复杂的形状,如弯曲、拉伸、凹凸等。
冲压模具制造工艺能够通过设计和制造适应复杂形状的模具,实现对汽车覆盖件的复杂形状加工,满足汽车外观设计的要求。
3. 高效率和大批量生产:冲压模具制造工艺具有高效率和大批量生产的优势。
通过模具的设计和制造,可以实现对汽车覆盖件的快速成形,大大提高生产效率。
同时,冲压模具可以进行多腔位设计,一次冲压可以同时成形多个汽车覆盖件,适应大批量生产的需求。
4. 节约材料和成本:冲压模具制造工艺可以充分利用金属板材的材料性能,减少材料的浪费和损失。
相比其他加工工艺,冲压模具制造工艺可以实现材料的最大利用率,降低生产成本。
5. 适用性广泛:冲压模具制造工艺适用于不同类型的汽车覆盖件,包括钣金、外壳、罩等。
无论是小型车、中型车还是大型车,冲压模具制造工艺都能够满足其覆盖件的成形需求。
在汽车覆盖件冲压模具制造工艺中,需要通过以下几个步骤来完成整个制造过程:1. 模具设计:根据汽车覆盖件的形状和尺寸要求,进行模具的设计。
模具设计需要考虑到材料的可用性、成形工艺的要求以及模具的使用寿命等因素。
2. 模具制造:根据模具设计的要求,进行模具的制造。
模具制造包括材料的选择、加工工艺的确定以及模具的装配和调试等环节。
3. 冲压成形:将制造好的模具安装在冲压机上,将金属板材放置在模具上,并施加一定的压力,使其产生塑性变形,最终得到所需的汽车覆盖件。
汽车覆盖件冲压工艺及模具设计技术研究
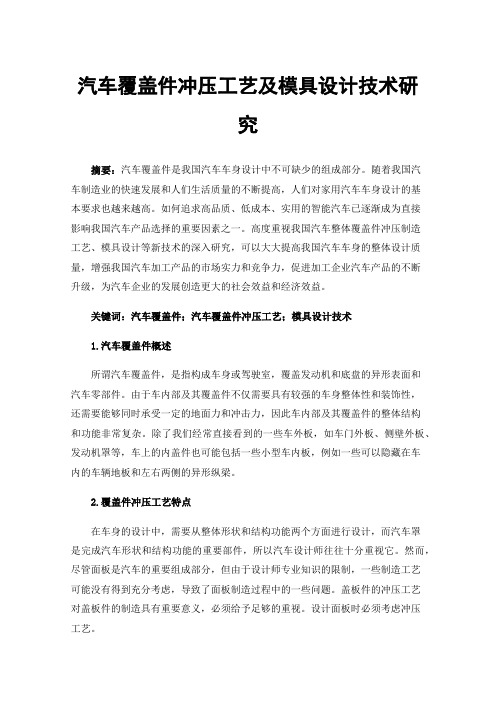
汽车覆盖件冲压工艺及模具设计技术研究摘要:汽车覆盖件是我国汽车车身设计中不可缺少的组成部分。
随着我国汽车制造业的快速发展和人们生活质量的不断提高,人们对家用汽车车身设计的基本要求也越来越高。
如何追求高品质、低成本、实用的智能汽车已逐渐成为直接影响我国汽车产品选择的重要因素之一。
高度重视我国汽车整体覆盖件冲压制造工艺、模具设计等新技术的深入研究,可以大大提高我国汽车车身的整体设计质量,增强我国汽车加工产品的市场实力和竞争力,促进加工企业汽车产品的不断升级,为汽车企业的发展创造更大的社会效益和经济效益。
关键词:汽车覆盖件;汽车覆盖件冲压工艺;模具设计技术1.汽车覆盖件概述所谓汽车覆盖件,是指构成车身或驾驶室,覆盖发动机和底盘的异形表面和汽车零部件。
由于车内部及其覆盖件不仅需要具有较强的车身整体性和装饰性,还需要能够同时承受一定的地面力和冲击力,因此车内部及其覆盖件的整体结构和功能非常复杂。
除了我们经常直接看到的一些车外板,如车门外板、侧壁外板、发动机罩等,车上的内盖件也可能包括一些小型车内板,例如一些可以隐藏在车内的车辆地板和左右两侧的异形纵梁。
2.覆盖件冲压工艺特点在车身的设计中,需要从整体形状和结构功能两个方面进行设计,而汽车罩是完成汽车形状和结构功能的重要部件,所以汽车设计师往往十分重视它。
然而,尽管面板是汽车的重要组成部分,但由于设计师专业知识的限制,一些制造工艺可能没有得到充分考虑,导致了面板制造过程中的一些问题。
盖板件的冲压工艺对盖板件的制造具有重要意义,必须给予足够的重视。
设计面板时必须考虑冲压工艺。
3汽车覆盖件冲压工艺与设计方案本文主要以某汽车生产公司的一辆小型货车的后门为分析对象。
后门内板尺寸大,形状多样,是典型的汽车覆盖件。
3.1汽车覆盖件冲压工艺分析汽车后门内板分为后窗内板和后门外板。
后车门的内板和外板通过内板的焊接边缘和冲压工艺相互连接,形成汽车的后车门,后车门直接安装在汽车的行李箱上。
汽车冲压覆盖件的原理
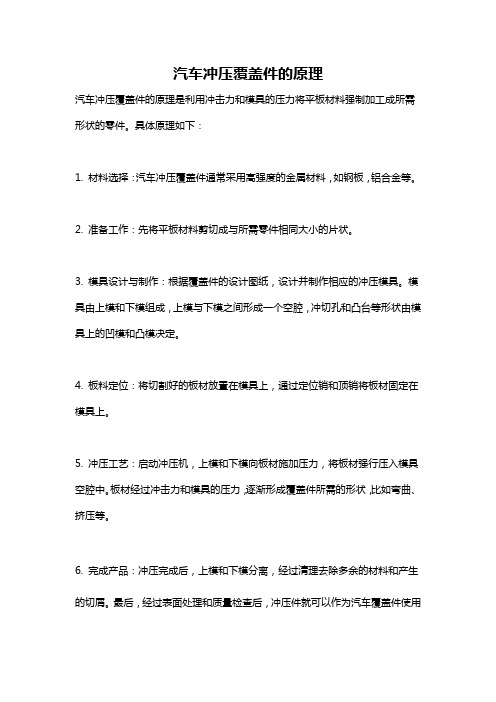
汽车冲压覆盖件的原理
汽车冲压覆盖件的原理是利用冲击力和模具的压力将平板材料强制加工成所需形状的零件。
具体原理如下:
1. 材料选择:汽车冲压覆盖件通常采用高强度的金属材料,如钢板,铝合金等。
2. 准备工作:先将平板材料剪切成与所需零件相同大小的片状。
3. 模具设计与制作:根据覆盖件的设计图纸,设计并制作相应的冲压模具。
模具由上模和下模组成,上模与下模之间形成一个空腔,冲切孔和凸台等形状由模具上的凹模和凸模决定。
4. 板料定位:将切割好的板材放置在模具上,通过定位销和顶销将板材固定在模具上。
5. 冲压工艺:启动冲压机,上模和下模向板材施加压力,将板材强行压入模具空腔中。
板材经过冲击力和模具的压力,逐渐形成覆盖件所需的形状,比如弯曲、挤压等。
6. 完成产品:冲压完成后,上模和下模分离,经过清理去除多余的材料和产生的切屑。
最后,经过表面处理和质量检查后,冲压件就可以作为汽车覆盖件使用
了。
浅谈汽车覆盖件冲压成形模具中锻造技术和铸造技术

浅谈汽车覆盖件冲压成形模具中锻造技术和铸造技术作者:刘毅来源:《中国新技术新产品》2013年第09期摘要:汽车覆盖件冲压理论和技术的发展将带来汽车工业的发展和相关领域的发展。
汽车覆盖件冲压理论和技术的发展将带来汽车工业的发展和相关领域的发展。
关键词:汽车;覆盖件;冲压;汽车工业中图分类号:X734.2 文献标识码:A汽车覆盖件冲压理论和技术的发展将带来汽车工业的发展和相关领域的发展。
1 汽车锻造模具技术1.1 概述锻造模具的主要技术发展方向是提高模具设计水平,采用新型模具材料,使用高效高精度加工手段,以期在模具高寿命的状态下实现锻件高精度。
1.2 未来市场需求及产品锻造技术在汽车工业中应用最为广泛,在铁路、航空、航天、船舶等工业领域的应用也在逐渐增加。
预计未来国内汽车工业和其他行业仍将保持持续快速发展的态势,锻造工业也将随之持续发展,与此相伴,锻造模具的需求将会逐渐增加。
1.3 关键技术1.3.1 锻造模具CAD/CAM/CAE 一体化技术及信息化技术(1)现状。
CAD/CAM技术已广泛应用,CAD/CAM/CAE 一体化技术应用还较少,锻造模具信息化技术鲜有使用。
(2)挑战。
CAD/CAM/CAE软件大部分来自国外,价格昂贵,使用不便。
成形过程数值模拟技术尚需突破。
(3)目标。
普遍采用CAD/CAM/CAE一体化技术,精确化数值模拟替代传统工艺调试,开发出具有自主知识产权的锻造模具CAD/CAM/CAE软件,促进集成PDM、ERP、 MIS系统与Internet平台的锻造模具信息化网络技术广泛使用。
1.3.2 锻造模具延寿、快修及再制造技术(1)现状。
模具寿命较低,平均寿命热锻模6000件,温锻模4000件,冷锻模10000件,锻造模具快速修复及再制造技术刚刚起步。
(2)挑战。
国内模具材料技术水平还不高,热处理和表面处理技术重视程度不够,缺乏针对不同工艺条件下的模具润滑技术细致研究。
(3)目标。
汽车覆盖件冲压成形技术pdf

汽车覆盖件是指构成汽车车身或驾驶室、覆盖发动机和底盘的薄金属板料制成的异形体表面和内部零件。
汽车覆盖件冲压成形技术是一种用于制造汽车覆盖件的技术,它通常涉及使用冲压模具将金属板材成形为所需的形状。
汽车覆盖件冲压成形技术的主要优点包括:
1.生产效率高:可以在短时间内生产大量的覆盖件。
2.成本低:与其他制造方法相比,冲压成形技术的成本较低。
3.质量高:可以生产出高精度、高质量的覆盖件。
4.设计灵活:可以根据需要设计各种形状的覆盖件。
汽车覆盖件冲压成形技术的主要步骤包括:
1.设计:根据汽车的设计要求,设计出所需的覆盖件形状。
2.模具制造:根据设计制造出冲压模具。
3.板材准备:将金属板材切割成所需的大小和形状。
4.冲压成形:使用冲压模具将金属板材成形为所需的形状。
5.修整:对成形后的覆盖件进行修整,以确保其符合设计要求。
6.表面处理:对覆盖件进行表面处理,以提高其外观和耐久性。
总的来说,汽车覆盖件冲压成形技术是一种高效、低成本、高质量的制造技术,它在汽车制造中得到了广泛的应用。
- 1、下载文档前请自行甄别文档内容的完整性,平台不提供额外的编辑、内容补充、找答案等附加服务。
- 2、"仅部分预览"的文档,不可在线预览部分如存在完整性等问题,可反馈申请退款(可完整预览的文档不适用该条件!)。
- 3、如文档侵犯您的权益,请联系客服反馈,我们会尽快为您处理(人工客服工作时间:9:00-18:30)。
基于快速成形技术的汽车覆盖件金属模具制造
徐达宋玉华张人佶颜永年
文摘:为获得高质量的汽车覆盖件金属模具,提出了基于快速成形(RP-Rapid Prototyping)技术的快速金属模具制造技术。
分析了RP技术的离散/堆积成形原理,给出了采用RP技术制造非金属原型的工艺过程,介绍了基于并行处理技术的超大型LOM-1600快速成形系统。
该系统采用非线性有限元对凝固过程中铸件的尺寸精度进行数值模拟,通过动态信息反馈优化原型尺寸,详细介绍了无焙烧陶瓷型精密铸造技术的工艺及机理。
基于RP技术的汽车覆盖件金属模具制造系统是一种全新的闭环控制模具设计与制造系统,经实际生产验证,取得良好的效果。
关键词:快速成形;数值模拟;精密铸造;模具
目前我国汽车工业迅猛发展,正在开发自己的轿车车型,大型覆盖件金属模具的快速、低成本制造是决定轿车更新换代、参与竞争的最关键因素之一,而我国的模具制造业很难满足汽车工业发展的需要,尤其是轿车大型覆盖件金属模具几乎全部依靠进口,一个新车型覆盖件模具需要几百套,价值数亿元。
目前国内外流行的、比较先进的汽车大型覆盖件金属模具制造技术是建立在轻型数控铣、大型精密数控铣和消失模铸造技术基础之上的,初期投资巨大,生产周期长,费用高[1]。
基于快速成形RP技术的大型汽车覆盖件金属模具制造技术,是打破上述局面的很好出路,其成果还可以直接应用到其它制造领域。
1、基于RP技术的金属模具制造技术
基于RP技术的大型汽车覆盖件金属模具制造技术的实质是用先进的精密热加工代替冷加工,大型快速原型制造系统本身也是一种复杂的NC加工设备,它的出现大大改变了模具制造的现状。
该技术将NC加工技术从冷加工转移到热加工,以获得精密的“毛坯”即模具,这个概念是现代加工技术发展的趋势。
先进制造技术发展的事实证明精密热加工使得“毛坯”精化,甚至制造出精密的零件,从而减少了对冷加工的技术要求,提高了生产效率,降低了成本,具体工艺路线见图1。
图1基于RP技术的大型汽车覆盖件金属模具制造工艺2、关键技术研究
2.1快速成形技术
RP技术是先进制造技术的重要组成部分,是综合了计算机、数控、激光、新材料和CAD/CAM 等新技术而形成的一种基于离散/堆积成形原理的直接从CAD三维模型设计到实际原型/零
件加工的全新制造方法,是当代制造领域的前沿技术[2]。
RP技术的基本原理是离散/堆积成形原理,三维形体在离散过程中被沿1至3个方向分解,生成形体的各个截面、截线和截点,称之为离散面、离散线和离散点,将这些离散体(面、线和点)转换成实体,并将它们依照原先的顺序堆积还原成三维形体的实体形状。
RP技术的特点是通过离散获得材料堆积的路径、顺序和方式,在数控系统控制下将材料逐层“迭加”起来形成三维实体,实现数字化成形,其成形过程见图2:三维CAD电子模型被沿Z向离散,生成一系列二维层面数据,再将分层后的数据进行处理,加入加工参数,生成数控代码,数控系统以平面加工方式顺序加工出每个层片并使它们堆积、粘接成形,构成三维物理实体。
图2RP技术成形工艺2.2RP原型制作及设备
在众多的RP工艺中,以LOM工艺最为适于制作实心块体原型,为汽车大型覆盖件模具首选RP工艺。
超大型的LOM-1600分层实体制造系统是本技术的关键设备,目前我们已经完成设计、制造,并进入最后调试[3]。
该系统是基于并行工程的设计思想而实现的,其成形空间为1600mm×800mm×700mm。
采用双激光并行数控系统,将原型分成两个部分同时加工,提高了成形速度,自行研制的控制电路,其功率0~40W随切割速度实时匹配,关键零部件采用世界名牌产品:如数控系统采用美国Park公司产品;伺服电机及其驱动器采用日本三菱公司产品;丝杠和导轨采用日本THK公司产品;温控系统采用英国West公司产品。
2.3凝固过程尺寸精度模拟
凝固过程中铸件的尺寸精度是精密模具铸造的一个主要问题,我们开发出基于MARC非线性有限元分析软件的凝固过程尺寸精度模拟软件系统,能够对凝固过程中铸件的尺寸精度进行数值模拟,通过动态信息反馈提高精密铸件的尺寸精度,从而获得尺寸精度良好的模具。
尺寸精度模拟是一个复杂的热力耦合问题,在凝固过程中铸件与铸型之间有接触力产生,同时又发生不平衡热传导,我们采用弹塑性热力耦合分析方法对大型汽车覆盖件模具凝固过程进行三维非线性有限元分析,变形与温度场的耦合计算采用弱耦合模式,在每一增量步内的计算由传热计算和弹塑性变形计算两部分组成。
在传热计算时采用Fourier热传导微分方程,结合Fourier热传导微分方程以及热传导分析的边界条件,采用Galerkin法建立瞬态热传导的有限元格式
(1)其中
(2)g为等参单元的形函数,q为热流密度,v为热对流速度,ρ为材料的密度,c为材料的比热,k为热传导系数,T为温度值,Q为由有塑性功及摩擦生热转化的内部热源。
在铸件凝固过程中,铸件在重力、摩擦力和热应力的作用下发生弹塑性变形,性能参数随温度变化,材料的弹塑性应力增量与应变增量的关系为
(3)
(4)
(5)其中:
(6)
(7)σ为应力张量,ε为应变张量,s为应力偏张量,σeq为等效应力,εeq为等效应变,σy为屈服应力,E为弹性模量,α为热膨胀系数。
采用接触力学的方法对凝固过程热力耦合分析中铸件与铸型间的接触问题进行处理。
采用修正的Lagrange乘子法对铸件的凝固过程进行描述,基于载荷控制的自适应时间步长,将位移判据作为收敛判据,得到铸件凝固过程的温度场分布、位移分布及变形状态图(图3~5)。
图3 凹模一半的三维有限元分析模型图4 凹模的温度场分布及变形状态图图5 凹模位移场分布及变形状态图2.4基于RP的无焙烧陶瓷型精密铸造工艺
陶瓷型精密铸造是以耐火度高、热膨胀系数小的耐火材料作为骨料,硅酸乙脂水解液作为粘结剂,配制成陶瓷浆料,在催化剂的作用下,经过灌浆、结胶、硬化、起模、焙烧等一系列工序制成表面光洁度和尺寸精度高的陶瓷铸型,浇铸出精密铸件[4]。
RP技术能够得到高精度的原型,陶瓷型精密铸造可以在保持原型精度和光洁度的基础上得到金属模具,同时由于对陶瓷型进行高温焙烧会产生裂纹及变形,对于超大尺寸模具需要大尺寸焙烧炉,又要求炉内温度均匀,技术难度很大,为此我们研究出基于RP的无焙烧陶瓷型精密铸造新技术,其工艺流程见图6。
图7为采用该技术制造的汽车上梁覆盖件凹模。
图6基于RP的无焙烧陶瓷型精密铸造工艺流程
图7汽车上梁覆盖件凹模无焙烧陶瓷型精密铸造的水解、胶凝的反应过程如下:四氯化硅与乙醇作用制得硅酸乙酯,反应方程式为SiCl4+4C2H5OH=(C2H5O)4Si+4HCl(8)
硅酸乙酯水解后成为硅酸胶体溶液,作为无焙烧陶瓷型的粘结剂,其中盐酸作为水解反应的催化剂,反应方程式为:
(9)
(10)
(11)
(12)硅酸乙酯水解液中分散的SiO2胶体作为一种吸附剂,把耐火材料吸附在一起,胶凝后形成网状无机硅聚合物,得到高强度陶瓷型。
3、结论
超大型LOM-1600快速成形系统是实现大型模具快速制造的前提和基础,它的开发成功填补了快速成形技术在制造大型原型方面的空白;凝固过程中尺寸精度模拟对于快速金属模具制造中优化原型尺寸,获得尺寸精度良好的模具有着重要的意义;基于RP的无焙烧陶瓷型精密铸造技术高效、实用、高精度地将RP非金属型转换为金属型,实现了金属模具的快速制造,较好地解决了对陶瓷型进行高温焙烧会产生裂纹、形变等影响陶瓷型铸件精度的问题,以及对于大型陶瓷型,需要大规模的焙烧炉,炉内温度场又要求均匀的技术难题;基于RP 技术的大型汽车覆盖件金属模具制造系统是包含了快速成形技术、凝固过程数值模拟和精密转换工艺的早期、多回路、快速信息反馈的闭环控制模具设计与制造系统,经实际生产验证,取得良好的效果。
它较好地解决了汽车工业中大型覆盖件模具的制造问题,对于提高我国模具制造的快速反应能力,提高设计水平,缩短研制周期,降低生产成本和提高制造柔性,具有十分重要的意义。