表面制造加工 v5
CATIA V5 功能模块简介
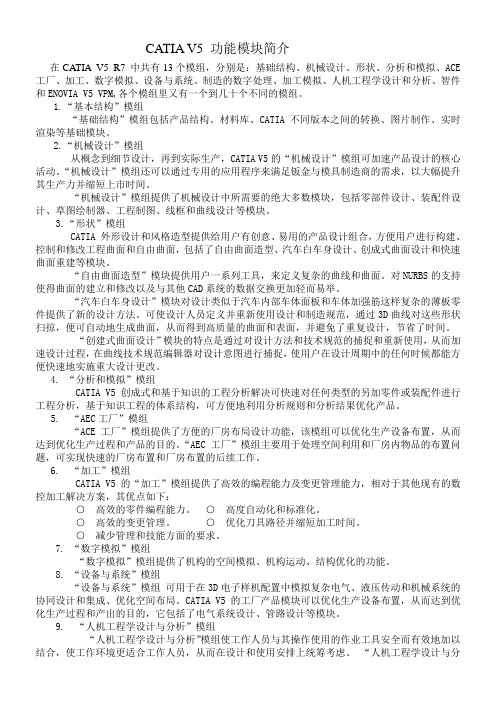
CATIA V5 功能模块简介在CATIA V5 R7 中共有13个模组,分别是:基础结构、机械设计、形状、分析和模拟、ACE 工厂、加工、数字模拟、设备与系统、制造的数字处理、加工模拟、人机工程学设计和分析、智件和ENOVIA V5 VPM,各个模组里又有一个到几十个不同的模组。
1.“基本结构”模组“基础结构”模组包括产品结构、材料库、CATIA 不同版本之间的转换、图片制作、实时渲染等基础模块。
2.“机械设计”模组从概念到细节设计,再到实际生产,CATIA V5的“机械设计”模组可加速产品设计的核心活动。
“机械设计”模组还可以通过专用的应用程序来满足钣金与模具制造商的需求,以大幅提升其生产力并缩短上市时间。
“机械设计”模组提供了机械设计中所需要的绝大多数模块,包括零部件设计、装配件设计、草图绘制器、工程制图、线框和曲线设计等模块。
3.“形状”模组CATIA 外形设计和风格造型提供给用户有创意、易用的产品设计组合,方便用户进行构建、控制和修改工程曲面和自由曲面,包括了自由曲面造型、汽车白车身设计、创成式曲面设计和快速曲面重建等模块。
“自由曲面造型”模块提供用户一系列工具,来定义复杂的曲线和曲面。
对NURBS的支持使得曲面的建立和修改以及与其他CAD系统的数据交换更加轻而易举。
“汽车白车身设计”模块对设计类似于汽车内部车体面板和车体加强筋这样复杂的薄板零件提供了新的设计方法。
可使设计人员定义并重新使用设计和制造规范,通过3D曲线对这些形状扫掠,便可自动地生成曲面,从而得到高质量的曲面和表面,并避免了重复设计,节省了时间。
“创建式曲面设计”模块的特点是通过对设计方法和技术规范的捕捉和重新使用,从而加速设计过程,在曲线技术规范编辑器对设计意图进行捕捉,使用户在设计周期中的任何时候都能方便快速地实施重大设计更改。
4. “分析和模拟”模组CATIA V5 创成式和基于知识的工程分析解决可快速对任何类型的另加零件或装配件进行工程分析,基于知识工程的体系结构,可方便地利用分析规则和分析结果优化产品。
加工表面质量名词解释

加工表面质量名词解释
加工表面质量是指通过加工制造过程中对零件表面的加工精度、表面形状、表面光洁度等方面的要求。
下面是一些常见的加工表面质量名词解释:
1. 光洁度:表面光滑程度的度量,通常使用Ra值表示。
Ra值越小,表面越光滑。
2. 平面度:平面与某个基准面之间的最大距离差,通常使用mm或μm表示。
3. 圆度:圆形轮廓与理论圆形之间的最大距离差,通常使用mm或μm表示。
4. 残余毛刺:加工后留在零件表面的微小凸起,通常使用μm 表示。
5. 毛坯余量:零件加工后与最终尺寸之间的距离差,通常使用mm或μm表示。
6. 粗糙度:表面的不规则程度,通常使用Rz、Rmax、Rt值表示。
Rz值越小,表面越光滑。
这些参数通常用于描述零件表面的质量要求,以确保零件能够达到其设计要求并且具有所需的性能和可靠性。
五轴后处理设计思路
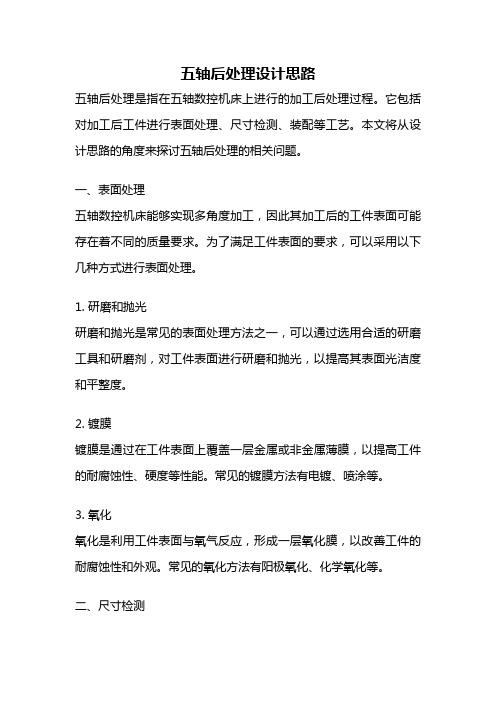
五轴后处理设计思路五轴后处理是指在五轴数控机床上进行的加工后处理过程。
它包括对加工后工件进行表面处理、尺寸检测、装配等工艺。
本文将从设计思路的角度来探讨五轴后处理的相关问题。
一、表面处理五轴数控机床能够实现多角度加工,因此其加工后的工件表面可能存在着不同的质量要求。
为了满足工件表面的要求,可以采用以下几种方式进行表面处理。
1. 研磨和抛光研磨和抛光是常见的表面处理方法之一,可以通过选用合适的研磨工具和研磨剂,对工件表面进行研磨和抛光,以提高其表面光洁度和平整度。
2. 镀膜镀膜是通过在工件表面上覆盖一层金属或非金属薄膜,以提高工件的耐腐蚀性、硬度等性能。
常见的镀膜方法有电镀、喷涂等。
3. 氧化氧化是利用工件表面与氧气反应,形成一层氧化膜,以改善工件的耐腐蚀性和外观。
常见的氧化方法有阳极氧化、化学氧化等。
二、尺寸检测尺寸检测是五轴后处理中必不可少的一环。
通过对工件的尺寸进行检测,可以确保工件的几何形状和尺寸精度符合设计要求。
1. 三坐标测量三坐标测量是一种高精度的尺寸检测方法,可以通过测量工件表面上的多个点,来获取工件的三维坐标数据,并与设计数据进行比较,以评估工件的尺寸精度。
2. 光学测量光学测量是利用光学原理进行尺寸检测的方法,它可以通过光学传感器或相机来获取工件表面的形貌信息,并进行尺寸测量和分析。
3. 探针测量探针测量是一种常用的尺寸检测方法,它通过将探针接触到工件表面上的点,测量出工件表面的高度、距离等信息,以评估工件的尺寸精度。
三、装配装配是五轴后处理的最后一步,它将加工好的零件按照设计要求进行组装,形成最终的产品。
1. 零件装配零件装配是将加工好的零件按照设计要求进行组装的过程。
在装配过程中,需要注意零件之间的配合精度和间隙,确保装配的准确性和稳定性。
2. 动力系统装配动力系统装配是指将动力系统(如电机、传动装置等)与零件进行组装,形成完整的动力传动系统。
3. 控制系统装配控制系统装配是将控制设备(如PLC、数控系统等)与零件进行组装,形成完整的控制系统。
5微米铜箔 -回复

5微米铜箔-回复什么是5微米铜箔?为什么它重要?如何制备5微米铜箔?以及它有什么应用领域?5微米铜箔是一种非常薄的铜箔材料。
微米(um)是长度单位,相当于千分之一毫米。
5微米即为0.005毫米,非常薄。
铜箔是以纯铜为原料制成的薄片,具有良好的导电性和导热性,是一种重要的电子材料。
为什么5微米铜箔如此重要呢?首先,由于其极薄的厚度,5微米铜箔可以实现较高的柔韧性和可塑性。
相比较较厚的铜箔,5微米铜箔可以更容易地弯曲和形成复杂的形状,从而方便应用于多种场合。
其次,5微米铜箔具有出色的导电性能,这使得它成为电子行业中的重要材料。
铜箔广泛应用于电子电路板、太阳能电池、LED封装、光纤传感器等领域。
那么,如何制备5微米铜箔呢?通常,铜箔的制备过程主要包括以下几个步骤。
首先,选择高纯度的铜金属作为原料。
然后,将铜金属通过加热、熔化和连续轧制的方式制成铜板。
这一步骤需要先将大块的铜金属通过高温加热熔化,然后将熔化的铜金属注入到成型机中,在连续轧制的过程中,使得铜板的厚度逐渐减薄,最终制得所需的薄板。
接着,通过化学或机械方法将铜板进行表面处理,以去除表面的污垢和氧化物。
最后,将铜板进行切割和平整处理,得到所需的5微米铜箔。
5微米铜箔在众多应用领域有着广泛的应用。
首先,它在电子行业中被广泛应用于电路板的制造。
由于其良好的导电性能和柔韧性,5微米铜箔可以用于制作高密度的印制电路板,使电子设备的性能更加稳定和可靠。
其次,5微米铜箔也广泛应用于太阳能电池的制造。
太阳能电池需要在表面涂覆一层导电材料,以收集电能。
铜箔作为导电层,能够高效地收集太阳能电池板上发出的电能,进一步提高太阳能电池的转换效率。
此外,5微米铜箔还可以用于电子封装材料、光纤传感器、导电胶带等领域。
综上所述,5微米铜箔是一种非常薄的铜箔材料,具有良好的导电性能和柔韧性,为电子行业以及其他领域的发展做出了重要贡献。
通过特定的制备工艺,可以获得所需厚度的5微米铜箔,随后应用于电路板、太阳能电池、LED封装等众多领域。
表面粗糙度等级对照表

N4 1.6 0.2 不可辨加工痕迹的方向N3 0.8 0.1 最光面暗光泽面
精磨、研磨、抛光、超精磨、
镜面磨削等 N2 0.4 0.05
亮光泽面
N1 0.2 0.025 镜状光泽面
0.1 0.012 雾状镜面
0.05
镜面
表面特征表面粗糙度(Ra)数值加工方法举例
明显可见刀痕 Ra100、Ra50、Ra25、粗车、粗刨、粗铣、钻孔
微见刀痕 Ra12.5、Ra6.3、Ra3.2、精车、精刨、精铣、粗铰、粗磨
看不见加工痕迹,微辩加工方向 Ra1.6、Ra0.8、Ra0.4、精车、精磨、精铰、研磨暗光泽面 Ra0.2、Ra0.1、Ra0.05、研磨、珩磨、超精磨、抛光
镜面0.006微米
雾状镜面0.012 镜状光泽面0.025 亮光泽面
0.05 暗光泽面0.1 不可见加工痕迹的方向0.2 可见加工痕迹方向0.8 微见加工痕迹方向0.4 看不清加工痕迹方向 1.6 微见加工痕迹方向
3.2 可见加工痕迹方向 6.3 微见刀痕12.5 可见刀痕
25 明显可见刀痕50。
Re-YOLOv5

pecially牞comparedtothebaselinemodelYOLOv5s牞itachievesa6%improvement.Thereasoningtimeofasingleimageisonly8.9ms牞whichmeetsthereal timerequirementsofindustrialproduction.Inaddition牞themodeloccupieslessmemoryandiseasytobetransplantedtoindustrialequipment.Keywords牶structuralre parameterization牷YOLOv5牷RepVGG牷steeldefectdetection 目前国内的制造业发展迅速,但部分行业的技术并不先进,例如钢材生产行业。
因钢铁的生产流程非常复杂,工序多,其现代化生产模式尚未完全普及,大部分工厂都还未实现完全的机械化,生产的方法也相对简单,这就导致钢铁的表面可能存在很多的缺陷,如裂纹(Crazing,Cr)、夹杂物(Inclusion,In)、斑块(Pat ches,Pa)、麻点(PittedSurface,Ps)、氧化铁皮(Rolled inScale,Rs)和划痕(Scratches,Sc)。
在上述各种缺陷中,裂纹的形状比较复杂多样,大部分是鱼鳞状,其产生的主要原因是温度加热不均。
Cr对钢材的性能破坏极大,若未被及时发现和处理,其会造成钢材的破损和开裂;In是钢材表面出现的深灰色或棕色斑块,一般是在钢材生产的过程中混入了其他的非金属,其很容易导致钢材的开裂;Pa是钢材表面出现的参差不齐的形状,产生的主要原因是在冷却过程中没有均匀吸收冷却液,其会影响钢材的结构稳定性,缩短钢材的使用寿命;Ps是参差不齐的粗糙面,加热过程中产生的氧化物没有得到完全清除时,就会产生麻点,麻点对钢材的性能影响不大,但是会造成一定程度的厚度误差,从而影响精度;Rs是在加热时间过长时钢材表面产生的黑色或红棕色氧化物,如未及时清理,会在轧制过程中被压入钢材表面,降低钢材性能;Sc是6种缺陷里最常见的,其性状是明亮的细长白条,主要是因钢材生产或搬运过程中与坚硬的物体非正常接触造成的,划痕会降低钢材的强度,影响使用寿命。
PCB加工V-CUT说明
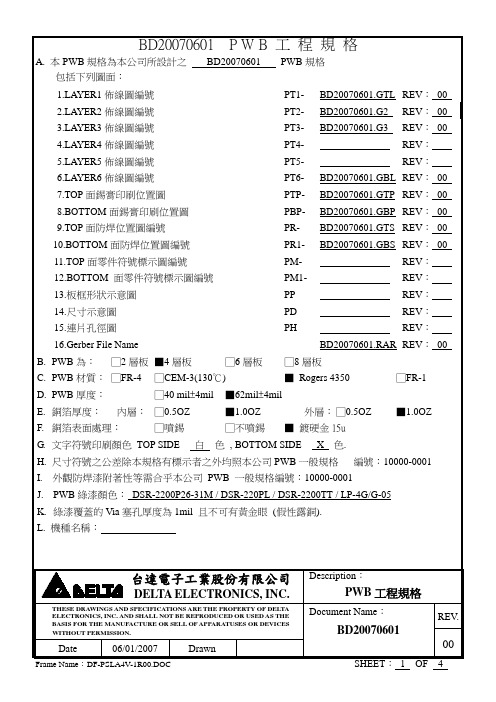
K. 綠漆覆蓋的 Via 塞孔厚度為 1mil 且不可有黃金眼 (假性露銅).
L. 機種名稱:
台達電子工業股份有限公司
DELTA ELECTRONICS, INC.
THESE DRAWINGS AND SPECIFICATIONS ARE THE PROPERTY OF DELTA ELECTRONICS, INC. AND SHALL NOT BE REPRODUCED OR USED AS THE BASIS FOR THE MANUFACTURE OR SELL OF APPARATUSES OR DEVICES
MODEL: □:RE-LAYOUT □:MINOR CHANGE □:PD □:PM □:PM-1 □:PH
□:PP
REV:00 □:PT □:PR
CODE:00 □:PR-1
ITEM
COMPONENTS
HOLES PITCHS
1
2
3
4
5
6
7
8
10
ITEM 1 2 3 4 5
OTHERS
台達電子工業股份有限公司
7. ■ CAM 加上日期
8. ■ CAM 加上防火等級
9. ■ CAM 加上廠商安規等級
10. □ CAM 於四角加上蝕刻監測 Track;L:400mil、W:10mil
11. ■ 蝕刻後走線寬度誤差不得超過 20%
12. ■ PWB 鑽孔偏移量加板層對位偏移量不得超過 5mil
13. □ Each Layout Offset 不得超過 3mil
WITHOUT PERMISSION.
Date
06/01/2007
Drawn
Frame Name:DF-PSLA4V-1R00.DOC
316L不锈钢表面微织构激光加工工艺参数

第 3期
刘宇航,等:316L不锈钢表面微织构激光加工工艺参数
269
观察微织构全貌发现,沟槽呈火山口堆积状,且 两侧边缘出现不规则的凸起,此种形态与蚊子吸血 鼻器上的刚毛及具有不光滑外形的寄生虫产卵器相 似[11,15]。图 2可知,沟槽深度随扫描次数的增加而 增大,但加剧了沟槽附近的灼烧效应。当扫描次数 为 1和 2时,微织构表面较整洁,热影响区改性范围 小、颜色浅且无明显重熔溅射现象,微织构加工质量 较好。当扫描次数为 3时,微织构表面凹凸不平,热 影响区改性范围广、颜色深且沟槽两侧存在较多圆 球状熔渣,微织构加工质量低。当扫描次数为 4和 5时,激光熔融物对沟槽型腔的堵塞严重,微织构化 表面加工质量差。因此,扫描次数对沟槽深度及表 面灼烧程度影响很大。
对工件进行激光对焦,然后按照正交表的方案 设计顺序依次在 316L不锈钢方板上采用直线扫描 的方式加工微织构。加工直线段长度设为 20mm。 旋转微位移平台旋钮,使 316L不锈钢方板沿垂直于
268
烟台大学学报(自然科学与工程版)
第 34卷
激光束的扫描方向移动 05mm,进行下组实验方案 的便捷加工。重复上述过程,以完成所有预设实验 方案。
综上所述,综合考虑沟槽深度和微织构化表面 加工质量,激光的最佳扫描次数为 2次。 22 直线型微织构的宽度和深度分析
利用超景深光学显微镜测量 316L不锈钢方板 上沟槽的宽度和深度并记录。将基体表面到沟槽底 部的高度差作为测量沟槽深度的标准,以排除沟槽 凹凸不同边缘对深度的影响。计算沟槽宽度、深度 的平均值和极值,并填入表 4中。为更加直观分析 正交实验的 4种因素对沟槽宽度及深度的影响效 应,根据表 4中的数据,绘制图 3、4中的效应曲线。
!"#$
- 1、下载文档前请自行甄别文档内容的完整性,平台不提供额外的编辑、内容补充、找答案等附加服务。
- 2、"仅部分预览"的文档,不可在线预览部分如存在完整性等问题,可反馈申请退款(可完整预览的文档不适用该条件!)。
- 3、如文档侵犯您的权益,请联系客服反馈,我们会尽快为您处理(人工客服工作时间:9:00-18:30)。
概述:制一表面廠以普通面為主,以貝殼MOP面與油壓P面全為副貝殼MOP面需要先做塗裝,貼合,及拋光等工序,貝殼片易碎油壓P面比普通面多了設計/加工中心,油壓,車底,熱焊足,過爐等工序,P面比普通面要求高,工模部門:工模部門生產各種模具普通面/ 貝殼面/ P面模具製作組裝流程:1.審核:看清仕樣書瞭解作業內容,2.製作:使用各種加工設備將所需模具加工製出,標記分類a)鋸床:粗胚開料用,製作圓柱體b)車床:將圓柱體車出符合的模具外形c)銑床:銑模具的面,打點或鑽孔d)鑽床:鑽給線切割鋼絲通過的孔,e)攻絲機:製作螺絲孔f)線切割機+ 熱硬化:使用編程軟體CAXA●切割模具的外徑,中心孔,三角缺口,再經過熱處理硬化。
●模具都是先把孔打好,經過(工廠內)熱處理後再線切割。
●如果先線切割後再熱處理則模具會變形。
g)磨床:●模具安裝好後不平的地方將其磨平。
●熱處理後模具會很硬,所以如果上下模不密合就要用磨床將接觸面磨平,●一次最多只能磨10t以下。
3.組裝:●組裝上下模具,模具必須清潔乾淨●依仕樣書標示機芯及客戶要求尺寸找對中心沖頭,裝於中心座,調整高度及緊固4.調試:紙張測試調整模具,對角的撕紙力道相當即可。
P面油壓模具CNC製作流程:1.設計:根據客戶要求設計出P面圖紋,2.程式設計:使用MasterCam編譯CNC加工程式3.刀具處理:調整磨刀角度,將刀具的尖端磨到指定的尖銳程度4.上機:由P面工模做出模具外形,CNC加工中心雕刻出P面圖案,●清潔刀具,將刀具並固定於CNC機床●擺正與校準刀具與P面模具的相對位置及距離,刀具預熱●置入編譯器,檢查參數,開始雕刻加工5.熱處理:雕刻出的P面模具必須做(外加工)熱處理-硬化,6.測試/整修:表面硬化處理後清洗乾淨再到P面試模,修整P面模具修正披鋒,貝殼加工部門(貝殼廠):貝殼片對外採購,由貝殼部門(貝殼廠)加工半成品貝殼加工作業流程:1.審核:看清仕樣書了解作業內容2.來料檢驗:貝殼片按照等級分開A純白,B微彩,C特彩,有黑點和暗紋的不良品退回3.貝殼塗裝:(塗裝流程可參照表面)貝殼塗裝流程:1.清洗乾燥:噴塗前須用脫脂水,洗潔精,純水清洗貝殼片表面,離心乾燥2.貼保護膜:貝殼正面貼保護膜(貝殼片較粗糙的一面為背面要噴涂油漆)3.清潔烘烤:酒精擦拭貝殼片表面,烘烤溫度110C,時間10分鐘4.調油噴塗:調油,貝殼面背面噴塗油漆,烘烤溫度110C,時間20分鐘5.撕保護膜:貝殼正面撕保護膜,檢驗有無黑點6.返修:貝殼塗裝不良品可做表面洗油返修(先留一個做樣,防止產品搞混)未烘烤過的塗裝貝殼片可直接洗天拿水已烘烤過的塗裝貝殼片可浸泡強力脫漆劑4.貝殼貼合:●貼合時要掌握膠量的多寡,正面不能溢膠,噴塗不乾膠需等一小時再貼合●搪瓷貝殼須留意銅胚變形問題●拼湊貝殼烘烤溫度80C,時間60分鐘●河貝殼貼合時需留意紋路方向5.貝殼刮面刮底:●刮面時要將面上的溢出的油漆和膠水刮乾淨,用新刀片要避免刮傷貝殼●刮底時要將底部的突起刮除,順便測量銅胚有無變形6.外觀檢測:貝殼不良品如貝殼裂,脫層,偏貼,反貼等須挑出更換沖外徑部門:普通面沖一次外徑,沖外徑部門也沖秒圈上板。
如果仕樣書注明表面有網底,則銅板在發料前必須貼上保護膜防止刮花。
貝殼面沖外徑前要把模具磨細磨光滑,避免貝殼面被壓裂貝殼面沖外徑前需檢查表面上的膠水有無殘留,面有無劃傷或裂痕P面沖外徑一般要沖兩次,第一次沖外徑在油壓前,而且要沖出二個耳朵狀的定位。
第二次沖外徑在油壓後,油壓後沖的外徑才是產品的外徑,有網底的面必須貼保護膜。
銅板加厚度是P面部門根據網底的高度來決定的。
普通面/ P面/ 貝殼面沖外徑作業流程:1.審核:看清仕樣書瞭解作業內容,2.剪料:根據生產訂單跟仕樣書的要求,用剪床將外購來的銅板切割成需要的長寬,3.選模:根據仕樣書選擇板材和厚度,找出相對應的外徑模具4.檢查:檢查機器是否正常5.安裝:安裝外徑模具到沖床上,6.調試:調試外徑模具●如發現沖出的外徑尺寸不符或中心偏移,請立即返回對應的工模部門重調●中孔直徑公差±1t,中孔要圓,不可有毛邊,●貝殼面中孔直徑加大5t●平面斜度±3t●普通面外徑±5t●搪瓷面外徑±1t●三角缺口深度25t,不可偏大7.沖外徑:●沖普通面或P面上模沖頭需要加上彈膠,沖貝殼面上模沖頭不需要彈膠,上模一般加大5t●沖普通面時,要根據仕樣書選擇板材和厚度,注意壓傷和變形●沖貝殼面時,特別用風槍將模具及貝殼胚吹乾淨(無灰塵),避免面壓傷●沖貝殼面時,不良問題如壓傷,孔印,邊裂,中孔裂等都需解決并改善●沖P面時,要看釘字/紋路/三眼圈的高度,高度太高的需要在下模墊膠並挖空避開。
8.檢驗:●沖外徑要做首件檢驗,完全符合要求才可繼續生產●普通面50~100片自檢一次,檢查面是否有凹點,塵點,劃條●油壓面30~50片自檢一次,檢查面是否有凹點,塵點●貝殼面10~15片自檢一次,檢查面是否有凹點,塵點,毛邊,劃傷,裂痕●最後全片抽樣檢查P面過爐部門:開機後一般爐溫700~750 C,分解爐爐溫870 C無氧化光亮退火爐參數表:過爐作業流程:1.預熱:用布擦拭清潔傳輸帶,預熱轉動兩三圈的時間2.調試:●測試放入一兩片銅片,觀察銅片退火情況,顏色是否光亮●如過爐不良要調整爐溫至750 C,待良品為止再調回建議爐溫3.過爐:●批次放入銅片,觀察銅片是否正常輸送,●如有堵塞應立即暫停,將爐膛疏通後才繼續作業P面油壓部門:油壓前的表面需過爐做軟化處理後再壓,如果紋路較深一次未壓飽滿,則需要再過爐軟化後繼續壓,有的表面要油壓多次,直到壓出的字體與紋路完全飽和為止,最後一次壓最好能讓表面硬一點,以免太軟造成下一道工序加工時變形油壓作業流程:1.審核:看清仕樣書作業內容,2.選模:依仕樣書找對P面油壓模具,3.檢查:檢查機器是否正常,4.組裝:●將壓頭套入上部模架,模具鎖住頂緊●將模具墊塊套入下部模架孔內,墊塊高度需比下部模架底部及上端均高出3~4mm,螺絲鎖住頂緊●P面油壓模具套入模架保護套中,用手壓緊連模具帶套鎖入下模架的三個對應的螺絲孔,P面油壓模具底部墊一塊100t厚的銅片緩衝力道,以螺絲均勻擰緊為准5.安裝:安裝P面油壓模具到油壓機上6.調試:調試P面油壓模具,7.油壓:油壓時表面上面墊一層紙是為了增大衝壓效果,8.清潔:作業中清洗P面油壓模具,9.檢驗:首件檢驗,中間檢查,最後片檢查P面車底部門:油壓後的表面由於厚度超出要求,則必須要車底車底後須再次貼保護膜,再沖第二次外徑。
車底作業流程:1.審核:看清仕樣書作業內容,2.選模:依仕樣書找對車底模具,3.檢查:檢查機器是否正常,4.安裝:安裝車底模具上機,5.調試:調試車底模具,●車底時不同的面要用不同的車底模具,必須調平整,不平整則需要墊模●厚度由設備自帶的千分尺來調節,車出來的表面厚度一定要均勻6.車底:車底粗糙的原因:●車刀不良,請換刀修理重磨●走刀速度過快,請調整車削機的軌道運行速度7.檢驗:首件檢驗,中間檢查,最後片檢查8.貼膜:貼保護膜後,再沖第二次外徑沖24孔部門:沖孔模具由沖孔部門的CNC設計中心自行製作如果是貝殼面沖24孔,則需注意貝殼面易裂。
主要是沖釘孔,上下層板足位孔;沖針都是外購。
沖孔模具CNC製作流程:1.設計:●審查所有機芯,釘圖,上層板的數值與仕樣書的標注是否一致●查機芯圖的足位座標●查釘圖的釘腳距P值及釘腳座標●查上層板的足位座標2.程式設計:使用MasterCam編譯CNC加工程式3.刀具處理:選擇刀具,磨刀具,對準刀具,測試刀具4.上機:●沖釘孔模具由工模生產出外形,模具上的針孔位由沖孔部門車間的CNC加工鑽出來。
●正模:普通面,須車削的面,腐蝕凹6t以上的面正模如果是全CD車削面+腐蝕紋,下模要加大釘足位●反模:搪瓷面,貝殼面反模的中模要鑽出機芯足位,如果機芯足位和釘足位很近,要立刻反應並改善5.測試/整修:表面硬化處理後清洗乾淨再到沖孔部門試模,修整沖孔模具修正披鋒釘孔的數量根據釘的大小來決定,一般都是兩個釘孔,珠座只有一個釘孔,其他的則是膠水孔。
膠水孔的目的是為了點膠水進去,以便於固定釘。
沖24孔作業流程:1.審核:看清仕樣書瞭解作業內容●先沖孔(正常):普通面,腐蝕紋面,油壓面●後沖孔(特殊):搪瓷面,須車削的面,腐蝕凹6t以上的面●噴油,搪瓷,腐蝕凹面底下要墊紙防止刮花,墊紙要墊平,防止有油漆的中心孔掉漆,防止沒油漆的中心孔變形。
2.選模:根據生產訂單跟仕樣書的要求,找出相對應沖孔模具,注意是正模還是反模3.組裝:●選擇並安裝沖針(上模):●●上模和中模之間有一層彈膠和墊片,可緩衝沖孔的力道。
4.安裝:安裝沖孔模具到衝床上5.調試:調試沖孔模具,●將調模的面沖孔,找出對稱點,拉平行,●調一次就要用投影儀檢測一次,直到調出來的模具完全符合要求。
●調模標準:請遵守“24孔品質標準”6.沖孔:每沖一次孔需要空沖一次把銅屑沖掉,銅屑留在模具裡面容易斷針,沖針斷在表面裡產品報廢。
7.檢驗:●沖釘孔要做首件檢驗,完全符合要求才可繼續生產,●生產過程中每半小時必須檢查一次。
8.穴孔:●先(正面)沖孔,後(反面)穴孔,穴孔目的防止釘的脫落。
●穴喇叭孔是為了點膠水後裝針固定,釘孔要穴,膠水孔不用穴。
●釘的高度在250以上的才穴喇叭孔,喇叭孔都穴在背面,只裝真石的則在正面穴喇叭孔。
●喇叭孔的深度為0.20~0.25mm,Φ28的釘孔用Φ70的鑽頭來穴。
沖窗部門:P面比普通面沖窗多了一個拍平機,因為P面軟,中間加工過程中容易變形,所以在沖窗後有變形的表面都要拍平。
主要沖普通窗,絞窗及壓彎。
●普通窗直接根據仕樣書要求調試模具,調好模具後再開始批量沖窗。
●絞窗則先沖一個普通窗的形狀,再壓斜邊。
●有壓彎要求的表面則需要用模具來壓。
沖窗作業流程:1.審核:看清仕樣書瞭解作業內容,●先沖窗(正常):一般情況●後沖窗(特殊):搪瓷要植窗框的面,窗位背後要求車裡挽的面2.選模:根據生產訂單跟仕樣書的要求,找出相對應的沖窗模具3.組裝:●組裝上下沖窗模具,注意三角缺口和方向性,上下沖窗模具須密合對齊●沖窗模具的上模一定要裝一個具有彈性的橡膠棒,以保護正面外觀。
4.安裝:安裝沖窗模具到衝床上5.調試:調試沖窗模具,●將調模的面沖窗,必須符合仕樣書的位置和尺寸,●調一次就要用投影儀檢測一次,直到調出來的模具完全符合要求。
●日曆窗尺寸相差±2t●窗位,中心孔,三角缺口是否平行,●窗不可有大小邊,6.沖窗:●沖搪瓷面時,窗和中心孔不可掉油●沖貝殼面時,特別用風槍將模具及面吹乾淨(無灰塵),避免面壓傷和窗位裂痕●沖P面時,如果有紋路留平臺,請配合平臺作業,檢查窗位是否有變形,壓傷,走位7.檢驗:●沖窗要做首件檢驗,完全符合要求才可繼續生產●普通面50~100片自檢一次,檢查窗位有無變形,位置有無走位(三角缺口的鬆緊),●油壓面30~50片自檢一次,檢查窗位是否有變形,壓傷,走位,●貝殼面10~15片自檢一次,檢查面有無壓傷,窗位有無變形,壓傷,裂痕,走位●最後全片抽樣檢查8.拍平:●如表面有變形則需要拍平,●拍平機頂部的螺絲調節拍下的深度,●下模是可調節大小的凹形槽,衝擊頭是膠制的,並要用紙包住防止將面弄花,●每拍一個就用刮刀檢查平整度,不平則要繼續拍,直到完全平才可以。