机加来料表面处理要求
机械加工表面质量控制详述
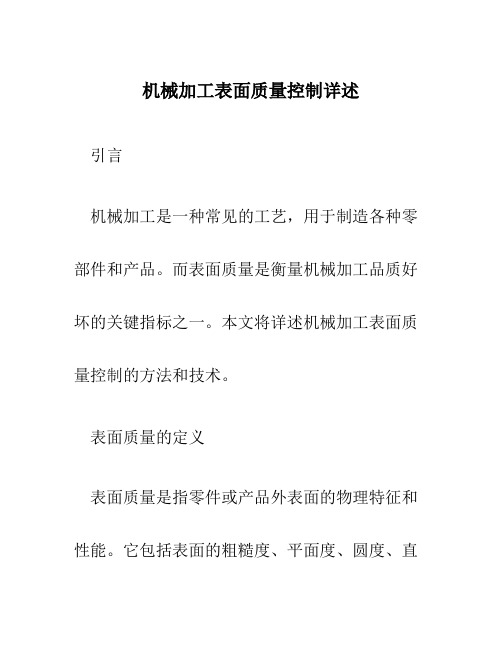
机械加工表面质量控制详述引言机械加工是一种常见的工艺,用于制造各种零部件和产品。
而表面质量是衡量机械加工品质好坏的关键指标之一。
本文将详述机械加工表面质量控制的方法和技术。
表面质量的定义表面质量是指零件或产品外表面的物理特征和性能。
它包括表面的粗糙度、平面度、圆度、直线度、平行度、垂直度等参数。
高质量的表面质量对于提高零件的性能、延长使用寿命和确保装配质量至关重要。
表面质量的评价指标常见的表面质量评价指标包括:1.粗糙度:表面的起伏程度,通常用Ra值(平均粗糙度)或Rz值(最大峰值与最小谷值之差)来表示。
2.平面度:表面在一个平面上的偏差程度。
3.圆度:表面的偏差程度,使其成为一个理想的圆形。
4.直线度:表面在一条直线上的偏差程度。
5.平行度:表面与参考面平行的程度。
6.垂直度:表面与参考面垂直的程度。
表面质量控制的方法预加工表面处理在进行机械加工前,通常需要对工件的表面进行预加工处理。
常见的预加工表面处理方法包括去除氧化层、清除污垢和毛刺、进行平整和硬化处理等。
这些表面处理的目的是为了提前解决一些表面质量问题,使机械加工过程更加顺利。
机床和刀具的选择机械加工过程中,选择适当的机床和刀具也对表面质量的控制起着很大的作用。
不同的机床和刀具具有不同的切削精度和稳定性,因此在选择时需要根据具体的加工要求进行选择。
同时,机床和刀具的定期维护和保养也是保证表面质量的重要环节。
加工参数的优化机械加工过程中的参数选择对表面质量有着直接影响。
例如,切削速度、进给速度、切削深度等参数的选择都会对表面质量产生影响。
根据不同的材料和加工方式,需要进行参数的优化选择,以实现最佳的表面质量。
加工过程的监控与调整在机械加工过程中,通过实时监测切削力、振动和温度等参数,可以及时发现并调整加工中的问题,以确保表面质量的稳定性和一致性。
表面质量的检测方法为了评估机械加工的表面质量,需要使用相应的检测方法。
常见的表面质量检测方法包括:1.视觉检测:通过肉眼观察表面是否有缺陷或异常。
自动化设备机械加工件来料检验标准

形位公差的检测方法按照GB/T1958-1980进行,必要时可检测工具进行检测。
7.5性能:
7.5.1镀锌、镀镍、镀铬等镀层附着力检验:新供应商导入时需做检测,用百格刀(或介刀)在供应商提供的60×90×1mm3的样板(同批表面处理)或同批试样工件表面划1mm×1mm格子100个,格子深度以见到基材为准,把3M透明胶纸贴在格子上,用手指抚压10个来回,使胶纸充分贴紧,以45°方向向上快速拉起,在同一个位置上重复做10次,每次用的胶纸要更新,格子不应有脱落。
6.螺纹规、环7.针规8.大理石平台9.万用表/兆欧表10.色板
6.术语及定义
外观面定义:A级表面:在使用过程中经常被客户看见且被关注的部分(如:作业平台,操作面板等)。
C级表面:在使用过程中不会被客户看到的表面部分(如:结合部位)。此表面的外观缺陷应合理而且不至于给客户觉得该产品质量不佳。
7.检验步骤:
7.3.3对机加件的表面缺陷具体标准参考下表:
外观缺
陷类型
缺陷所处
表面类型
允许范围
A级表面
B级表面
C级表面
基材花斑
金属表面
目视可见不允许
不允许
S总≤被测面积的5%
浅划痕
所有表面
目视可见不允许
L≤50×0.4,P≤2,N≥50
P≤5,N≥50
深划痕
所有表面
目视可见不允许
不允许
不允许
凹坑
非拉丝和喷砂面
目视可见不允许
7.6.3必须将产品的各检验特性都检验完毕后,方可进行综合判定。
7.6.4当本标准与实际效果不符且有争议时,以研发及品质部确认结果为准;
7.6.5标准里未体现的缺陷以我司品质部的判定标准为准。
机加工件表面处理的方法

机加工件表面处理的方法嘿,你知道吗,机加工件表面处理那可是相当重要的呀!这就好比给一个物品穿上一件合适的外衣,能让它变得更加完美。
那机加工件表面处理都有哪些方法呢?首先就是电镀啦!电镀的时候要先把工件清洗干净,这一步可不能马虎,不然就会影响电镀的效果哦!然后把工件放入电镀液中,通过电流的作用让金属离子附着在工件表面。
这里要注意电流的大小和时间的控制,要是没把握好,那可就糟糕啦!还有阳极氧化,这个过程要控制好氧化的时间和温度,不然也达不到理想的效果呢!另外还有喷涂,得把涂料调配好,均匀地喷在工件上,可别喷得厚一块薄一块的呀!这些方法在操作的时候都要特别小心谨慎,稍有不慎就可能前功尽弃呢!在这个过程中,安全性和稳定性那是绝对不能忽视的呀!就像走钢丝一样,稍有偏差可能就会出大问题。
比如说电镀过程中用到的化学药品,要是不小心接触到皮肤或者进入眼睛,那可不得了。
还有那些设备,得经常检查维护,不然突然出故障了咋办?所以呀,一定要严格按照操作规程来,千万不能马虎大意。
那这些表面处理方法都有啥应用场景和优势呢?哎呀呀,那可多了去了!电镀可以让工件变得更加美观,还能提高耐腐蚀性呢,多棒呀!阳极氧化可以让铝合金工件变得更坚硬,更耐磨。
喷涂就更不用说啦,各种颜色各种效果都能实现,让工件变得与众不同。
这些优势不就像是给机加工件加上了一双翅膀,让它们能在各种领域大展身手吗?给你讲个实际案例吧!有一次一个客户要求我们给一批零件做表面处理,我们就根据零件的材质和使用环境,选择了合适的方法。
最后做出来的零件那叫一个漂亮,客户超级满意呢!你说这效果好不好?总之,机加工件表面处理真的是太重要啦!它能让我们的工件变得更加完美,更加出色!我们一定要重视起来,好好利用这些方法,让我们的产品更上一层楼!。
机械加工零件表面质量控制措施
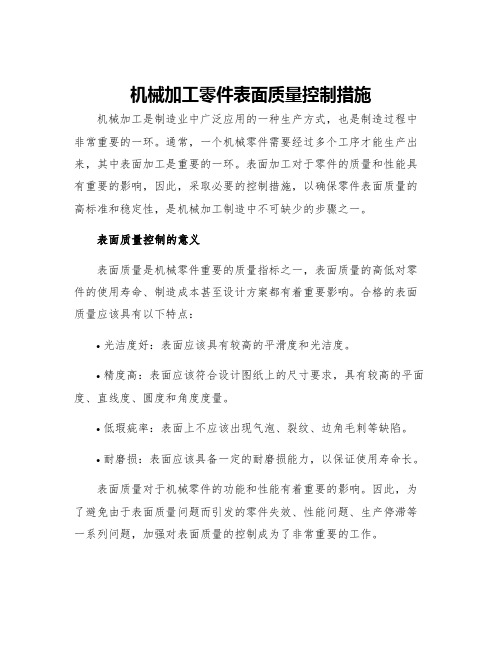
机械加工零件表面质量控制措施机械加工是制造业中广泛应用的一种生产方式,也是制造过程中非常重要的一环。
通常,一个机械零件需要经过多个工序才能生产出来,其中表面加工是重要的一环。
表面加工对于零件的质量和性能具有重要的影响,因此,采取必要的控制措施,以确保零件表面质量的高标准和稳定性,是机械加工制造中不可缺少的步骤之一。
表面质量控制的意义表面质量是机械零件重要的质量指标之一,表面质量的高低对零件的使用寿命、制造成本甚至设计方案都有着重要影响。
合格的表面质量应该具有以下特点:•光洁度好:表面应该具有较高的平滑度和光洁度。
•精度高:表面应该符合设计图纸上的尺寸要求,具有较高的平面度、直线度、圆度和角度度量。
•低瑕疵率:表面上不应该出现气泡、裂纹、边角毛刺等缺陷。
•耐磨损:表面应该具备一定的耐磨损能力,以保证使用寿命长。
表面质量对于机械零件的功能和性能有着重要的影响。
因此,为了避免由于表面质量问题而引发的零件失效、性能问题、生产停滞等一系列问题,加强对表面质量的控制成为了非常重要的工作。
表面质量控制的措施表面质量控制的核心是通过对表面加工过程的精细控制,来确保表面质量能够满足设计要求。
这里我们列出了一些常见的表面质量控制措施。
合理的工艺参数选择在机械加工中,工艺参数是十分重要的因素之一,对表面质量有着很大的影响。
选择合理的工艺参数,可以有效的提高零件的表面质量。
合理的工艺参数包括:•切削速度(n):切削速度对切削力、热量等因素都有影响。
切削速度过高时,会导致热量集中,表面温度过高,易产生毛刺、烧伤等不良现象;切削速度过低,则会导致表面粗糙度大,表面质量不合格。
选定切削速度时要综合考虑材料、刀具、加工精度等因素。
•给进量(f):也就是每刀切深。
如果给进量太大,就会造成刀具磨损过快、容易产生毛刺等现象。
较小的给进量可以保证表面光洁度和尺寸精度。
•转速(v):表面转速不宜过高,否则会引起机床本身的振动,造成表面质量损害。
表面处理检验规范
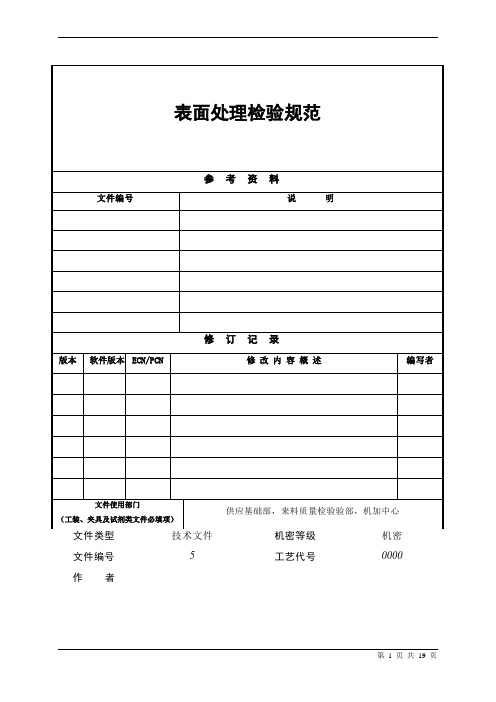
文件编号5工艺代号0000作者第 1 页共19 页表面处理检验规范1适用范围本规范适用于电镀、氧化、化学处理、喷塑、喷漆、喷砂、拉丝等金属表面处理的检验。
2术语和定义2.1 A级表面:在使用过程中总能被客户看见的部分(如:面壳的正面和顶面,后壳的顶面,手柄,透镜,按键及键盘正面,探头整个表面等)。
2.2 B级表面:在使用过程中常常被客户看见的部分(如:面壳的左右侧面,底壳或后壳的左右侧面及背面等)。
这些表面允许有轻微不良,但是不致引起挑剔客户不购买产品。
2.3 C级表面:在使用过程中很少被客户注意到的表面部分(如:面壳的底面,底壳或后壳的底面,内部零件表面)。
此表面的外观缺陷应合理而且不至于给客户觉得该产品质量不佳。
2.4 金属表面:包括电镀、氧化、钝化等表现为金属质感的表面,非喷涂表面。
2.5 基材花斑:电抛光、电镀或氧化前因基体材料腐蚀、或者材料中的杂质、材料微孔等原因所造成的、与周围材质表面不同光泽或粗糙度的斑块状花纹外观。
2.6 抛光区:对基材上的腐蚀、划伤、焊接区、铆接区等部位进行机械打磨抛光后表现出的局部高光泽、光亮区域。
2.7 浅划痕:镀(膜/塑/漆)层表面划伤,但未伤及底层(即底层未暴露);对其它无镀(膜/塑/漆)层表面则为:目测不明显、手指甲触摸无凹凸感、未伤及材料本体的伤痕。
数控冲床加工中机床台面对板材的摩擦产生的轻微痕迹属于此类划痕。
2.8 深划痕:镀(膜/塑/漆)层表面划伤,且已伤至底层(即底层已暴露出来);对其它无镀(膜/塑/漆)层表面则为:目测明显、手指甲触摸有凹凸感、伤及材料本体的伤痕。
2.9 凹坑:由于基体材料缺陷,或在加工过程中操作不当等原因而在材料表面留下的小坑状痕迹。
2.10 凹凸痕:因基材受撞击或校形不良等而呈现出的明显变形、凹凸不平的现象,手摸时有不平感觉。
2.11 烧伤:拉丝、电抛光、电镀处理时因操作不当、造成零件表面过热而留下的烧蚀痕迹。
2.12 水印:电镀、氧化或电抛光后因清洗水未及时干燥或干燥不彻底所形成的斑纹、印迹。
机械加工中零件加工的要求有哪些

在进行机械加工的过程中,产品质量一直都是加工过程中十分重要的事情。
为了保证产品的质量符合标准,需要加工者对机械加工零件的要求提高重视。
本文就来具体介绍一下,零件在加工的过程中,需要注意哪些要求。
一、零件的轮廓处理1、未注形状公差应符合GB1184-80的要求。
2、未注长度尺寸允许偏差±0.5mm。
3、未注圆角半径R5。
4、未注倒角均为C2。
5、锐角倒钝。
6、锐边倒钝,去除毛刺飞边。
二、零件表面处理1、零件加工表面上,不应有划痕、擦伤等损伤零件表面的缺陷。
2、加工的螺纹表面不允许有黑皮、磕碰、乱扣和毛刺等缺陷。
所有需要进行涂装的钢铁制件表面在涂漆前,必须将铁锈、氧化皮、油脂、灰尘、泥土、盐和污物等除去。
3、除锈前,先用有机溶剂、碱液、乳化剂、蒸汽等除去钢铁制件表面的油脂、污垢。
4、经喷丸或手工除锈的待涂表面与涂底漆的时间间隔不得多于6h。
5、铆接件相互接触的表面,在连接前必须涂厚度为30~40μm防锈漆。
搭接边缘应用油漆、腻子或粘接剂封闭。
由于加工或焊接损坏的底漆,要重新涂装。
三、零件的热处理1、经调质处理,HRC50~55。
2、中碳钢:45 或40Cr 零件进行高频淬火,350~370℃回火,HRC40~45。
3、渗碳深度0.3mm。
4、进行高温时效处理。
四、精加工后技术要求1、精加工后的零件摆放时不得直接放在地面上,应采取必要的支撑、保护措施。
2、加工面不允许有锈蛀和影响性能、寿命或外观的磕碰、划伤等缺陷。
3、滚压精加工的表面,滚压后不得有脱皮现象。
4、最终工序热处理后的零件,表面不应有氧化皮。
经过精加工的配合面、齿面不应有退火五、零件的密封处理1、各密封件装配前必须浸透油。
2、组装前严格检查并清除零件加工时残留的锐角、毛刺和异物。
保证密封件装入时不被擦伤。
3、粘接后应清除流出的多余粘接剂。
浅谈机械加工零件表面的质量控制措施

浅谈机械加工零件表面的质量控制措施机械加工是指按照工作图纸要求对定制工件进行切削、加工、成型的加工方法,其中对表面质量的要求非常高。
机械加工零件表面的质量控制措施是确保产品不受缺陷影响,并保证产品质量稳定、可靠、高效的重要手段。
一、表面处理机械加工的表面处理方法主要有机械处理、化学处理、电化学处理等。
而在生产中,机械加工通常采取磨削方法来调整零件表面粗糙度和形状。
机械加工中,加工表面的状态直接影响着加工零件的品质,滑动区表面的质量决定着热效应、摩擦特性、疲劳强度等零件性能。
因此,在机械加工中,表面处理是关键,它能使零件表面平滑、美观有光泽,同时保证工件表面的精度和形状,从而提高零件的使用寿命和可靠性。
二、表面加工表面加工主要是针对加工后表面缺陷的修补,以保证零件表面完整和规范。
正确的表面加工对机械加工零件的表面质量控制具有重要意义。
表面加工主要包括打磨、研磨、抛光、刻字等,其中手工打磨、研磨和抛光工艺是经济、实用的方法,但是需要有专业技能的工匠进行操作,因为加工所得表面质量直接决定产品的质量。
三、质检控制机械加工零件的表面质量控制需要对制品进行分析、测试和评价。
质量控制采用非接触式设备,例如研磨计算机模拟软件、机器视觉系统等,能够实时检测表面的平整度、粗糙度、几何形状等指标。
在质量控制中,需要对工艺参数参数进行监控和随时调整,以保证生产的稳定性和准确性。
四、治理措施在机械加工质量发生问题时,应立即采取治理措施。
如工艺流程的问题,及时调整流程;机床的并轴度、高度校准等问题,需要检修或调整;材料问题,则要选择合适的材料或改进材料;而系统的问题,则需要对系统进行检测和调整,确保系统正常运行。
治理措施需要针对具体问题具体分析,采取不同的方式去进行治理,并时刻关注整个制造过程中的质量问题。
总之,对机械加工中零件表面质量进行控制是确保产品质量的重要手段,机械加工表面的处理、加工、质检和治理措施都需要充分考虑并在生产过程中实施。
《机加件常用材料和表面处理加工规范A1》

三、 表面处理(一) 铝件的氧化处理1、 普通阳极氧化处理 类型:(1)黑色阳极氧化(默认为亮黑,可选哑黑,需要时请注明)(2)黑色喷砂阳极氧化(默认为亮黑,可选哑黑,需要时请注明) (3)本色阳极氧化(默认为亮银,可选哑光,需要时请注明) (4)本色喷沙阳极氧化(默认为亮银,可选哑光,需要时请注明) 规定:(1)铝件表面处理首选:本色喷砂阳极氧化; (2)激光模组内铝件首选:黑色阳极氧化; (3)膜厚要求:10-15μm ;(4)氧化膜硬度要求:HV300±202、 硬质氧化处理 类型:黑色硬质氧化 规定:(1)有耐磨等特殊要求时,选择黑色硬质氧化;(2)一般件只做黑色硬质氧化,不做其他颜色(防止材料颜色误差); (3)膜厚要求:30 -40μm ;(4)氧化膜硬度要求:HV500±20(5)所有铝件做“本色硬质氧化”统一为“黑色硬质氧化”。
注:由于本色硬质氧化色差较大,不推荐使用。
3、 辊类的表面处理 规定:(1)辊类做特殊硬质氧化以及表面硬化处理; (2)膜厚要求:60 -100μm ;(3)氧化膜硬度要求:HV800以上(4)砂纸带抛光,最终表面粗糙度Ra0.4以下。
○1一般过辊 材料:A6063-T5类型:褐色硬质氧化+硬化处理 (镀氧化锆陶瓷) ○2CCD 过辊 材料:A6063-T5类型:黑色硬质氧化+硬化处理 (镀氧化锆陶瓷) ○3抚平小辊(收卷抚平辊、) 材料:A6061-T6类型:本色硬质氧化 (颜色呈灰色和6061阳极颜色接近)管控事项更改事项: 1. 规范各类表面处理的检验要求。
修订 审核 批准 喷沙阳极亮银喷沙阳极哑光13.透明亚克力14.黑色亚克力19.优力胶A50。
- 1、下载文档前请自行甄别文档内容的完整性,平台不提供额外的编辑、内容补充、找答案等附加服务。
- 2、"仅部分预览"的文档,不可在线预览部分如存在完整性等问题,可反馈申请退款(可完整预览的文档不适用该条件!)。
- 3、如文档侵犯您的权益,请联系客服反馈,我们会尽快为您处理(人工客服工作时间:9:00-18:30)。
表面处 检验项目 理方式
检验方法及质量要求
人工照明时背景要求无光泽的黑色,灰色,不能用彩色背景。 通常要求本色氧化为银灰色,黑色阳极氧化需呈深黑色。氧化膜外观 1、外观 均匀、平整,表面不允许有色差、皱纹、裂纹、气泡、流痕、夹杂、 发粘、漆膜脱落等缺陷。 2、粗糙度 表面粗糙度应达到图纸设计要求。 除特别注明,镀层厚度通常要求≧10μ m。 阳极氧化 3、膜厚 方法:在试样镀层表面上,用切割刀具在水平和垂直方向各划11条间距为1mm的 4、结合度 平行线,深达基体金属,形成100个方格。用胶带紧密粘贴于划格部位,迅速垂 直拉起。要求划格部位无起皮、无脱落为合格。 5、耐化学 A、耐盐酸测试B、耐洗涤性C、耐腐水性 品性 呈深黑色,膜层结晶致密、均匀,产品无漏底,无明显色差发白异色,氧化膜不 1、外观 牢,锈斑。 2、耐蚀性 A、硫酸铜点滴法 B、盐雾试验 3、环保 无毒、无异味。 镀层为浅黄色泽的银白色,经抛光的应有镜面光泽,表面均匀、细致连续。不允 许表面明显可见的镀层缺陷,如气泡、起皮、粗糙、毛刺、针孔、烧焦、剥落、 1、外观 雾状、残留物及漏镀;镀层表面的人为磕碰、划痕、打磨痕也不允许。
发黑
2、粗糙度 表面粗糙度应达到图纸设计要求。 镀镍 2、厚度 特别注明外,通常镀层厚度要求10--15μ m。 方法:在试样镀层表面上,用切割刀具在水平和垂直方向各划11条间距为1mm的 3、镀层结 平行线,深达基体金属,形成100个方格。用胶带紧密粘贴于划格部位,迅速垂 合力 直拉起。要求划格部位无起皮、无脱落为合格。 4、耐蚀性 采用铜盐加醋酸盐雾试验(CASS试验)达到七级以上为合格。 镀层应光亮细致,不允许有气泡、空隙、粗糙、裂纹、烧焦和局部无镀层等。允 许有挂具接触点,但应选在非主要表面。黑色钝化膜呈深黑色,完整,不允许有 1、外观 疏松,脱落等缺陷。 除特别注明或另有规定,通常镀层厚度为8--15μ m。 2、厚度 镀黑锌 方法:在试样镀层表面上,用切割刀具在水平和垂直方向各划11条间距为1mm的 3、镀层结 平行线,深达基体金属,形成100个方格。用胶带紧密粘贴于划格部位,迅速垂 合力 直拉起。要求划格部位无起皮、无脱落为合格。 4、耐蚀性 采用铜盐加醋酸盐雾试验(CASS试验)达到七级以上为合格。 表面光亮有光泽,不允许麻点、气泡、剥落、裂纹或任何对表面有不良影响的其 1、外观 它缺陷。 2、粗糙度 表面粗糙度应达到图纸设计要求。 3、镀层结 方法:将用于实验的工件用钳子夹紧,反复向两面弯曲90度,直至断裂。要求: 镀鉻 合力 底层和基体、底层和鉻层之间不允许有任何分离与起层。 4、耐蚀性 采用铜盐加醋酸盐雾试验(CASS试验),达到七级以上为合格。 表明镀硬鉻时,镀层厚度应达到10--30μ m 5、厚度 6镀层硬度 除特别注明或另有规定,通常硬度值HV≧750.