常用金属表面处理要求(201006)
金属构件的表面处理方法及要求
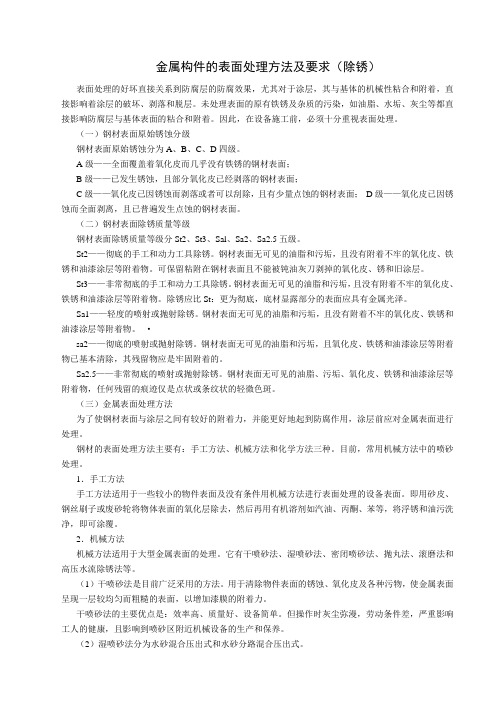
金属构件的表面处理方法及要求(除锈)表面处理的好坏直接关系到防腐层的防腐效果,尤其对于涂层,其与基体的机械性粘合和附着,直接影响着涂层的破坏、剥落和脱层。
未处理表面的原有铁锈及杂质的污染,如油脂、水垢、灰尘等都直接影响防腐层与基体表面的粘合和附着。
因此,在设备施工前,必须十分重视表面处理。
(一)钢材表面原始锈蚀分级钢材表面原始锈蚀分为A、B、C、D四级。
A级——全面覆盖着氧化皮而几乎没有铁锈的钢材表面;B级——已发生锈蚀,且部分氧化皮已经剥落的钢材表面;C级——氧化皮已因锈蚀而剥落或者可以刮除,且有少量点蚀的钢材表面;D级——氧化皮已因锈蚀而全面剥离,且已普遍发生点蚀的钢材表面。
(二)钢材表面除锈质量等级钢材表面除锈质量等级分St2、St3、Sal、Sa2、Sa2.5五级。
St2——彻底的手工和动力工具除锈。
钢材表面无可见的油脂和污垢,且没有附着不牢的氧化皮、铁锈和油漆涂层等附着物。
可保留粘附在钢材表面且不能被钝油灰刀剥掉的氧化皮、锈和旧涂层。
St3——非常彻底的手工和动力工具除锈。
钢材表面无可见的油脂和污垢,且没有附着不牢的氧化皮、铁锈和油漆涂层等附着物。
除锈应比St:更为彻底,底材显露部分的表面应具有金属光泽。
Sa1——轻度的喷射或抛射除锈。
钢材表面无可见的油脂和污垢,且没有附着不牢的氧化皮、铁锈和油漆涂层等附着物。
·sa2——彻底的喷射或抛射除锈。
钢材表面无可见的油脂和污垢,且氧化皮、铁锈和油漆涂层等附着物已基本清除,其残留物应是牢固附着的。
Sa2.5——非常彻底的喷射或抛射除锈。
钢材表面无可见的油脂、污垢、氧化皮、铁锈和油漆涂层等附着物,任何残留的痕迹仅是点状或条纹状的轻微色斑。
(三)金属表面处理方法为了使钢材表面与涂层之间有较好的附着力,并能更好地起到防腐作用,涂层前应对金属表面进行处理。
钢材的表面处理方法主要有:手工方法、机械方法和化学方法三种。
目前,常用机械方法中的喷砂处理。
不锈钢表面处理方法及要求

不锈钢表面处理方法及要求
不锈钢表面处理分为打磨和抛光两部分。
首先要对上道转入打磨工序的工件进行目测检验,如焊缝是否有漏焊,焊穿,焊点深浅不均匀,偏离接缝太远,局部凹陷,对接不齐,是否有较深划痕,碰伤,严重变形等在本工序无法补救的缺陷,如果有上述缺陷应返回上道工序修整。
如无上述缺陷,进入打磨工序。
不锈钢焊接打磨的主要目标是去掉焊点,为抛光做准备,打磨分粗磨和精磨两部分。
粗磨,本工序用80#百叶轮打磨,目标是去掉工件焊接留下的焊点,以及在上道工序出现的碰伤,达到焊口圆角初步成型,水平面和垂直面基本无大划痕,无碰伤,此步工序后工件表面的粗糙度应能达到R0.8mm。
一般来说以与被抛面成一条直线比较适中!
精磨,用120#百叶轮对前面工序出现的接缝进行修正及对粗磨后产生的印痕进行进一步的细磨,对前面工序留下的印痕要反复磨削,接缝基本消失,达到工件表面无划痕,表面变亮,本工序的粗糙度应能达到R0.2mm。
抛光分打蜡和擦亮两步,进入抛光工序前先目测上部工序是否有漏磨,打磨不均匀的地方等各种抛光阶段无法修复的问题,若存在这样的问题需返回重新打磨或者修补。
如若没有可开始用抛光轮,配合抛光蜡按照前面的方法进行抛光
擦亮,是抛光的最后一道工序,用干净的棉布对工件表面进行擦拭,使工件表面经打磨和抛光处理后留下的赃污擦拭干净。
拉丝是采用拉丝布或拉丝轮往复运动,在工件表面来回摩擦使工
件表面光洁度提高,表面的纹理呈直线状。
表面拉丝的加工方式,要根据拉丝效果的要求、不同的工件表面的大小和形状选择不同的加工方法。
金属材料表面处理技术的使用方法与注意事项
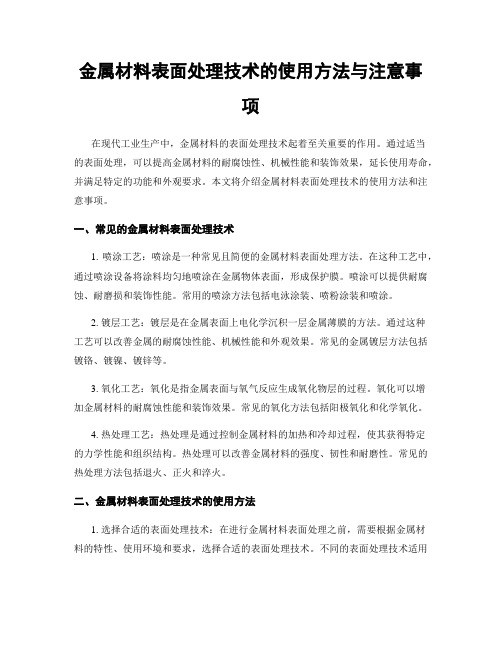
金属材料表面处理技术的使用方法与注意事项在现代工业生产中,金属材料的表面处理技术起着至关重要的作用。
通过适当的表面处理,可以提高金属材料的耐腐蚀性、机械性能和装饰效果,延长使用寿命,并满足特定的功能和外观要求。
本文将介绍金属材料表面处理技术的使用方法和注意事项。
一、常见的金属材料表面处理技术1. 喷涂工艺:喷涂是一种常见且简便的金属材料表面处理方法。
在这种工艺中,通过喷涂设备将涂料均匀地喷涂在金属物体表面,形成保护膜。
喷涂可以提供耐腐蚀、耐磨损和装饰性能。
常用的喷涂方法包括电泳涂装、喷粉涂装和喷涂。
2. 镀层工艺:镀层是在金属表面上电化学沉积一层金属薄膜的方法。
通过这种工艺可以改善金属的耐腐蚀性能、机械性能和外观效果。
常见的金属镀层方法包括镀铬、镀镍、镀锌等。
3. 氧化工艺:氧化是指金属表面与氧气反应生成氧化物层的过程。
氧化可以增加金属材料的耐腐蚀性能和装饰效果。
常见的氧化方法包括阳极氧化和化学氧化。
4. 热处理工艺:热处理是通过控制金属材料的加热和冷却过程,使其获得特定的力学性能和组织结构。
热处理可以改善金属材料的强度、韧性和耐磨性。
常见的热处理方法包括退火、正火和淬火。
二、金属材料表面处理技术的使用方法1. 选择合适的表面处理技术:在进行金属材料表面处理之前,需要根据金属材料的特性、使用环境和要求,选择合适的表面处理技术。
不同的表面处理技术适用于不同的金属材料和应用场景,例如,喷涂适用于大面积物体,而镀层适用于需要改善耐腐蚀性能的材料。
2. 准备工作:在进行金属材料表面处理之前,需要做好准备工作。
首先,要对金属材料进行清洗,去除表面的油污、杂质和氧化物。
然后,进行必要的预处理,如蚀刻、激活和除锈等,以提高表面处理效果。
3. 控制处理参数:在进行金属材料表面处理时,需要控制好处理参数,如处理时间、温度、涂料涂布量等。
不同的处理参数会对金属材料的性能产生不同的影响。
因此,在实际操作中需要根据具体情况进行优化和调整。
金属表面处理操作规程

金属表面处理操作规程金属表面处理是一种常见的工艺,旨在增强金属材料的耐腐蚀性、耐磨损性和粘附性,从而提高其使用寿命和性能。
下面是金属表面处理操作规程的一般步骤和注意事项,供参考。
一、表面清洁处理1. 在进行任何金属表面处理之前,首先要对金属表面进行彻底的清洁。
可以使用热水和洗涤剂进行清洗,也可以使用化学清洗剂进行清洗。
2. 清洁时要注意避免使用过多的清洗剂,以免对环境造成污染。
3. 清洁完毕后,应该用清水彻底冲洗干净金属表面,并确保金属表面完全干燥。
二、除锈处理1. 如果金属表面有锈蚀情况,需要进行除锈处理。
可以使用机械除锈(如打磨、切削等)或化学除锈(如酸洗)的方法进行除锈。
2. 在进行除锈处理时,需要采取安全措施,如佩戴防护眼镜、手套和口罩,以防化学溅入眼睛、皮肤或呼吸道。
三、酸洗处理1. 酸洗是常用的金属表面处理方法之一,可以去除金属表面的氧化物和其他不良物质。
2. 在进行酸洗处理时,应该选择适合的酸洗液,并按照使用说明正确配制酸液的浓度。
3. 在酸洗处理之前,应该将金属表面彻底清洁,并确保金属表面没有油脂、污垢等杂质。
4. 酸洗处理时,需要注意酸液的浓度和温度,以免对金属材料造成腐蚀和变形。
四、电镀处理1. 电镀是一种在金属表面上镀上一层金属或合金的方法,以增加金属的耐腐蚀性和美观性。
2. 在进行电镀处理之前,需要将金属表面进行清洁和除锈处理,并确保金属表面平整和光滑。
3. 在进行电镀处理时,应该选择适合的电镀液,并按照使用说明正确配制电镀液的浓度和温度。
4. 在电镀处理时,需要注意电流密度和镀层的厚度,以获得理想的镀层质量。
五、涂装处理1. 涂装是一种在金属表面上涂上一层涂料或烤漆的方法,以增加金属的耐腐蚀性、耐磨损性和美观性。
2. 在进行涂装处理之前,需要将金属表面进行清洁和除锈处理,并确保金属表面平整和光滑。
3. 在进行涂装处理时,应该选择适合的涂料或烤漆,并按照使用说明正确涂装和烘烤。
常用金属板表面处理参考资料
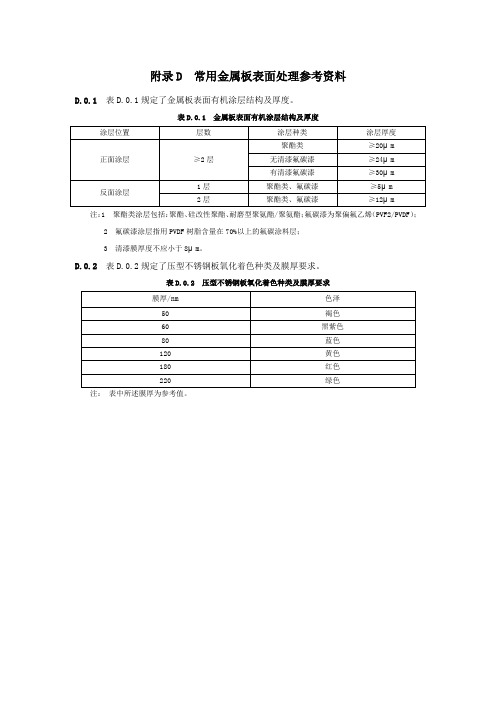
表D.0.2压型不锈钢板氧化着色种类及膜厚要求
膜厚/nm
色泽
50
褐色
60
黑紫色
80
蓝色
120
黄色
180
红色
220
绿色
注: 表中所述膜厚为参考值。
附录D
D.0.1表D.0.1规定了金属板表面有机涂层结构及厚度。
表D.0.1金属板表面有机涂层结构及厚度
涂层位置
层数
涂层种类
涂层厚度
正面涂层
≥2层
聚酯类
≥20μm
无清漆氟碳漆
≥24μm
有清漆氟碳漆
≥30μm
反面涂层
1层
聚酯类、氟碳漆
≥5μm
2层
聚酯类、氟碳漆
≥12μm
注:1聚酯类涂层包括:聚酯、硅改性聚酯、耐磨型聚氨酯/聚氨酯;氟碳漆为聚偏氟乙烯(PVF2/PVDF);
金属表面处理标准

金属表面处理标准金属表面处理标准是确保金属制品在使用过程中能够有良好的耐腐蚀性、耐久性和美观度的重要环节。
本文将围绕金属表面处理的相关内容展开,包括常见的金属表面处理方法、金属表面处理的目的与意义、金属表面处理的标准以及金属表面处理过程中需要注意的事项等。
通过对金属表面处理标准的介绍,希望能够提高金属制品的质量和使用寿命。
金属表面处理方法有很多种,常用的包括电镀、喷涂、热处理和机械加工等。
其中,电镀是一种利用电解作用使金属表面形成一层防护层的方法,可以提高金属制品的耐腐蚀性和外观质量;喷涂是一种将涂料均匀地喷涂在金属表面上的方法,可以实现防腐、防氧化和装饰等效果;热处理是一种利用金属材料的热稳定性和相变性质来改变其物理和化学性质的方法,可以提高金属制品的硬度和强度;机械加工是一种通过机械方法对金属表面进行切削、打磨和抛光等处理的方法,可以提高金属制品的尺寸精度和表面光洁度。
而金属表面处理的主要目的是提高金属制品的耐腐蚀性、耐久性和美观度。
首先,金属制品在使用过程中容易受到腐蚀的影响,因此需要进行表面处理以形成一层防护层,防止金属与外界环境的接触,延长使用寿命。
其次,金属表面处理还能够改善金属制品的物理和化学性质,提高其硬度、强度和耐磨性,增加使用安全性。
同时,金属表面处理还能够改善金属制品的外观质量,使其具有光亮、平滑和美观的特点,提升产品的市场竞争力。
对于金属表面处理标准来说,首先需要明确指定金属表面处理的方法和要求。
例如,对于电镀来说,需要明确电镀材料的种类、电镀层的厚度和电镀温度等具体参数。
其次,金属表面处理标准还需要规定金属制品的质量检测方法和标准,以确保金属制品符合相关的标准要求。
这些质量检测方法可以包括金属表面形貌检测、表面化学成分检测和物理性能检测等。
最后,金属表面处理标准还需要注重金属制品的环境保护和安全性问题,确保表面处理过程符合相关的环保法规和安全操作规范,减少对环境的影响和对人体的危害。
废旧物资堆放及处理规定201006
废旧物资堆放及处理规定
为了规范废旧物资的回收、堆放及处理,特制定以下规定:
一、废旧物资堆放要求:
1、废旧物资必须堆放到指定地点,不得随处乱扔;
2、废旧物资必须分三类堆放:
1)金属件,包括废钢废铁、有色金属;
2)非金属件,如塑料地板、凳等;
3)有可维修价值的总成件,如门泵、电机、马达、刹车总泵及分泵等;
3、废旧物资必须与生活、生产垃圾分开堆放;
4、废旧物资必须与发外整修的旧件分开堆放。
二、废旧物资处理:
1、职责
物资公司负责集团公司各部门及所属单位的各类废旧物资的回收及处理,其它部门或单位不得擅自处理。
2、废旧物资的回收
物资公司各仓库要严格执行以旧换新制度,负责做好各分公司、修理厂的废旧物资的回收工作,并分类堆放到指定地点。
运输班定期到各分公司将废旧物资拉到物资公司集中堆放,并按照废钢废铁、有色金属、总成件及非金属件四类分开堆放。
旧电瓶、报废轮胎、废机油由各回收公司直接到各分公司场地收购,各公司凭物资公司开具的发票给回收单位开出门证。
3、废旧物资销售
废旧物资通过比价销售,销售价格不得低于市场价,销售利润一律上交集团公司财务处。
附:
各分公司废旧物资堆放情况表。
金属表面处理标准
金属表面处理标准金属表面处理是一种通过改变金属表面的物理、化学性质,以提高其耐腐蚀性、机械性能、外观和其他特性的工艺。
标准化的金属表面处理有助于确保产品质量、提高工业生产效率,并满足各种应用领域的需求。
以下是关于金属表面处理标准的一些主要方面,包括涂层、清洗、镀层和防腐措施等。
1、表面清洗标准:目的:清洗是金属表面处理的首要步骤,旨在去除油脂、污垢、氧化物等不良物质,为后续处理提供清洁的表面。
标准:根据不同金属和应用领域的需求,清洗标准可能包括溶剂清洗、酸洗、碱洗等具体的清洗工艺和条件。
2、防腐涂层标准:目的:防腐涂层用于保护金属表面免受大气、水分、化学品等腐蚀因素的侵蚀。
标准:根据环境条件和要求,涂层标准可能包括涂层材料的选择、涂层厚度、附着力、耐腐蚀性能等方面的规定。
3、阳极氧化标准:目的:阳极氧化是一种常用的表面处理方法,通过电化学反应在金属表面形成氧化膜,提高其耐腐蚀性和硬度。
标准:包括氧化膜的颜色、厚度、密度等要求,以及操作条件和检测方法等。
4、镀层标准:目的:镀层可以改变金属表面的外观、耐腐蚀性、导电性等性质,常见的镀层包括镀铬、镀镍、镀锌等。
标准:包括镀层的成分、厚度、均匀性、附着力等方面的要求,确保镀层质量符合标准。
5、喷涂涂层标准:目的:喷涂是一种常见的涂层方法,用于在金属表面形成保护性的、美观的涂层。
标准:包括喷涂材料的选择、涂层厚度、涂层外观、耐腐蚀性等方面的规定。
6、钝化标准:目的:钝化是通过在金属表面形成一层氧化物膜来提高其耐腐蚀性的处理方法。
标准:包括钝化工艺、膜的性质、厚度等方面的规定。
7、金属表面检测标准:目的:通过检测确保金属表面处理的质量符合标准要求。
标准:包括各种检测方法,如膜厚测量、附着力测试、耐腐蚀性能检测等。
8、环保标准:目的:考虑到环保要求,金属表面处理标准可能包括对涂料、溶剂、废水等的环保规定。
标准:鼓励使用环保材料和工艺,降低环境污染。
结束语:综合而言,金属表面处理标准涉及到多个方面,从清洗到涂层,从防腐到检测,都需要符合一系列明确的标准。
金属表面涂装的预处理要求
涂装金属表面预处理要求1表面预处理及除锈方法(最初表面预处理)(1) 表面预处理及除锈方法和分类应根据下表1表1 原始表面预处理标准(2) 在采用酸洗法的情况下,要清洗的材料应保证浸在硫酸,盐酸或磷酸的溶液中,然后用碱中和,并用热水(约80C)清洗并干燥,此后应立即用临时防锈剂涂刷。
(3) 对于精加工的表面,就不能采用喷丸及酸洗等会影响表面粗糙度的清洗方法。
(4) 对于铸件表面,应采用喷砂或喷丸来清除铸件飞边或型砂,然后用干燥的压缩空气去除生铁灰尘及砂粒,也可以用砂轮面来清除光整粗糙的铸件表面。
(5) 对于钢板及框架包括焊接结构件等要油漆的表面,通常应采用喷砂处理,在没有条件的情况下,可以采用电动刷来清理•如果焊接件有焊渣及氧化皮,则应将其彻底清除。
(6) 工作台大梁及齿轮箱的内表面在喷丸或喷砂处理后应立即涂上耐油漆,此后就不必再进行预处理。
(7) 在可能发生氢脆的情况下,则不应采用酸洗进行处理。
(8) 第二次表面处理:这种处理是指修补或修复油漆表面生锈的部分及由于焊接漆膜被烧坏的部分,并按下述表2进行。
表2 第二次表面预处理标准注1:上表中从第一级至第五级清理的级别均根据表 1.2清洗如在机件的表面上粘有由肉眼可见的如锈迹,灰尘及残留油脂,手指印,水珠及碱等外来物, 会使机件在运输和储存过程中产生锈迹, 因此清洗工作应彻底进行。
(1) 石油溶剂清洗法在初步清洗后, 将机器零件局部或完全浸入如汽油, 粗汽油及煤油等石油溶剂中, 接着用刷子或棉布擦洗干净或溶化处理,第二步清洗即将机器零件全部浸入另一种干净溶剂内进行处理.尽管石油溶剂对于油及油脂的可溶性较高, 也应采用其溶点尽可能高的溶剂, 主要考虑其可燃性.且在有可燃的情况下, 可以采用不可燃的三氯化物溶剂( 三氯乙烯), 这种溶液对于油脂及焊剂的溶解性是高的.(2) 碱清洗法(表面活性剂)将机器零件浸在苛性钠, 纯碱, 硅酸氢钠等清洗剂的水溶液内,或者将上述碱溶液中的一种喷射在机器零件的表面, 然后用热水彻底清洗机器零件的表面. 加入少量活性剂(正离子, 负离子, 无离子及偶极离子)至碱溶液中可以减少碱溶剂的用量, 且能增强清洗的效果. 通常,只要加入0.1~0.5%的非离子活性剂就可以清洗由矿物油形成的污垢。
常用的金属表面处理方法
常用的金属表面处理方法“哇,这把小勺子好漂亮啊!”我看着妈妈新买的不锈钢勺子,忍不住发出感叹。
妈妈笑着说:“这是经过金属表面处理的哦。
”啥是金属表面处理呢?嘿嘿,今天我就来给大家讲讲常用的金属表面处理方法。
咱先说说电镀吧。
电镀就像给金属穿上一件漂亮的外衣。
步骤呢,就是把金属制品放到一个装满溶液的大桶里,然后通上电,溶液里的一些物质就会跑到金属表面,形成一层亮亮的膜。
注意事项可不少呢!要小心溶液别溅到身上,那可不得了。
电镀的应用场景可多啦,像咱们平时用的水龙头、自行车的零件很多都是电镀过的。
为啥要用电镀呢?因为电镀后的金属不仅好看,还能防锈呢!就好比给金属穿上了一层铠甲,厉害吧?我记得有一次去参观工厂,看到那些正在进行电镀的零件,闪闪发光的,可漂亮啦!再讲讲喷涂。
喷涂就像是给金属化个妆。
把油漆用喷枪喷到金属表面。
这可得注意喷枪的使用方法,别喷得太厚也别太薄。
喷涂可以让金属有各种不同的颜色,可酷啦!比如一些户外的栏杆,很多都是喷涂过的,这样既美观又能保护金属不被腐蚀。
这不就像给金属涂了一层防晒霜嘛!有一次我在公园里看到那些彩色的栏杆,我就想,这要是没有喷涂,得多难看呀!还有一种叫氧化。
氧化就像是让金属经历一场奇妙的变化。
把金属放在特定的环境里,让它表面自然形成一层氧化膜。
这个过程要注意环境的控制哦。
氧化后的金属会有一种独特的质感,像那些复古的铜制品很多都是氧化处理过的。
这就好像金属变成了一个有故事的老人,充满了魅力。
我在博物馆里看到过一些氧化的青铜器,哇,那真的是太震撼啦!总之,这些金属表面处理方法都超厉害的。
它们让我们的生活变得更加丰富多彩,也让金属更加耐用。
大家说是不是呀?。
- 1、下载文档前请自行甄别文档内容的完整性,平台不提供额外的编辑、内容补充、找答案等附加服务。
- 2、"仅部分预览"的文档,不可在线预览部分如存在完整性等问题,可反馈申请退款(可完整预览的文档不适用该条件!)。
- 3、如文档侵犯您的权益,请联系客服反馈,我们会尽快为您处理(人工客服工作时间:9:00-18:30)。
17
谢 谢!
2012/1/31 18
11
摩擦系数要求: 带尾标T、G要求摩擦系数在0.13±0.03,批量监控要求平均值 ±3σ落在0.10-0.16区间内
12
பைடு நூலகம்
GMW4700-08
电镀锌合金,常用为锌镍合金(Zn-Ni) 生产方式为挂镀或滚镀 Type A 5.0-15.0% Ni含量,480h红锈 Type B 10.0-17.0%Ni含量,240h白锈,1000h红锈 厚度要求大于8μ,但一般不超过15μ 要求每批抽取至少10件监控厚度 注意高电流区域容易造成厚度和镍含量增高
15
GMW3359分为三个等级 Type A 12μ,240h/白锈不超过5%,720h/无红锈 Type B 12μ,144h/白锈不超过5% ,480h/无红锈 Type C 8μ,72h/白锈不超过5% ,240h/无红锈 螺栓头部最大厚度不超过25μ 每批至少抽10件检查厚度 如图纸无特别标注,缺省定义为Type B
10
氢脆检查按SAE/USCAR-7 方法:对螺栓 选取五件,测试断裂扭矩,计算平均断裂扭矩; 去氢过程,每一炉抽取一定数量的零件按80%断裂扭矩紧固在对 应工装,24h后,重新紧固至80%断裂扭矩,再经24h后,再次紧 固至80%断裂扭矩,然后卸载,检查零件是否有裂纹等破坏; 只要有一个零件试验失效,整炉报废,不得返工。
5
3.潮湿试验 144h/40 ℃ /100%,按GMW14729,外观无变化 4.碎石冲击 5.固化 6.耐机油、燃油、电瓶液、耐磨
6
GMW3044-05
镀锌要求 用于钣金件、铸件和紧固件,生产方式:挂镀或滚镀 注意图纸的标注要求 U表示不需钝化 K表示本色 B表示黑色 第一个数字是镀层最小厚度 字母后第一个数字表示出现红锈的盐雾试验时间 字母后第二个数字表示出现白锈的盐雾试验时间
2
标准按零件在整车的位置分为underhood和underbody Underhood表示发动机舱下部零件 Underbody表示车身下部零件 防腐试验要求不同: Underhood:循环腐蚀和腐蚀扩散评价 将零件按GMW15282划线后,按GMW14872 exposure B进行循 环腐蚀试验,评价腐蚀扩散,裸板和铸件基材小于6mm,其它基 材小于3mm underbody:碎石冲击和循环腐蚀 将零件按GMW14700,方法C进行碎石冲击,然后按GMW14872 exposure A进行循环腐蚀试验,按GMW15357进行评价,要求8以 上
13
盐雾试验、附着力试验、去氢要求、氢脆检查要求同GMW3044 循环腐蚀试验GMW14872 Type A EXT All, 4s, Method SH/SM/SL, Exposure D 红锈不超过10%,白锈不超过50% Type B UB All, 4s, Method SH/SM, Exposure D 无红锈,白锈不超过50% 带尾标G,要求摩擦系数,要求同GMW3044
3
注意图纸要求标注方法: 如“GMW14671 – A-U/B ”表示涂装类型为电泳,试验要求按 underbody 零件 如图纸未标注U/B或U/H,则零件要求按实际装车位置
4
试验要求 1.划格试验,评分1或0 1.1供货状态 1.2 潮湿试验后(144h/40 ℃ /100%) 2.腐蚀试验 2.1 循环腐蚀按GMW14872 2.2 盐雾试验按GMW3286,336h,划线腐蚀扩散小于3mm,边缘 锈蚀不超过总长度的20%; 对镀锌板、锌合金板基材,不划线,240h,边缘白锈不超过总长 20%,红锈不超过5%,边缘腐蚀扩散宽度不超过8mm和零件宽 度的1/3
常用金属零件表面处理要求
------Zhang Chunping
1
GMW14671-09
底盘零件的涂装要求 分为A、B、C、D、E、F、G七种类型 A 表示电泳涂装,膜厚在16-22μ B 表示电泳涂装,膜厚在23-35μ C 表示浸涂涂装,膜厚大于35μ D 表示粉末涂装,膜厚大于40μ E 表示可选用A、B、C、D中的任何一种 F 表示膜厚在图纸上或材料标准中指定 G 表示喷涂溶剂型或水溶型的漆,膜厚大于40μ 注意图纸标注方法,如“GMW14671-A”表示选用A 类型
14
GMW3359-07
非电解富锌涂料 涂料中富含锌片、铝片 前处理可以使用脱脂水洗、抛丸或溶剂清洗 涂覆可以用浸涂、也可以用喷涂方式 颜色可以通过加不同的面涂实现,同时面涂可以调节摩擦系数 此工艺过程不产生氢,不会有氢脆问题(前处理使用酸洗除外) 这种涂层渗透性好,有少量吸氢可在涂料烘烤过程中析出 防腐性能可与镀锌镍合金相当,生产过程环保。
16
盐雾试验方法同GMW3044,每批至少取3件测试 循环腐蚀试验按GMW14872,仅批准时做此试验 Type A: EXT All, 4 s, Method SH/SM/SL, Exposure D. Type B: EXT All, 4 s, Method SH/SM/SL, Exposure C. Type C: UH All, 4 s, Method SH/SM, Exposure B 阴极保护试验 宽度0.5mm的划痕,划至基材,96h盐雾后,无红锈 涂层附着力试验,96h/40 ℃ ,100%湿度后,百格试验,大于99% 由于螺纹紧固件时,摩擦系数在0.13±0.03,批量监控要求平均 值±3σ落在0.10-0.16区间内
7
8
盐雾试验 必须在电镀后至少24h进行,如标注H,试验前须经1h/150 ℃处理 对紧固件,装配后外露面须被暴露在盐雾中,如螺栓摆放如图
9
镀层附着力试验 30min/220 ℃处理后,立即放入室温的水中,镀层没有起泡、裂纹 防氢脆处理 对表面硬度大于35HRC(HV332)或芯部硬度大于32HRC(HV306)的零 件,必须去氢 去氢处理按SAE/USCAR-5 硬度大于HV353(HRC37.2)时,4h/200 ℃去氢 硬度大于HV390(HRC40.8)时,8h/200 ℃去氢 热处理后,经过低于200回火的,8h/110去氢 注意:1.去氢在电镀后1h内进行,此过程在钝化之前; 2.去氢过程,烘炉不能开门再放入零件,去氢时间为零件温度 达到去氢温度开始计时