常见金属表面处理的种类
金属表面处理方法6种
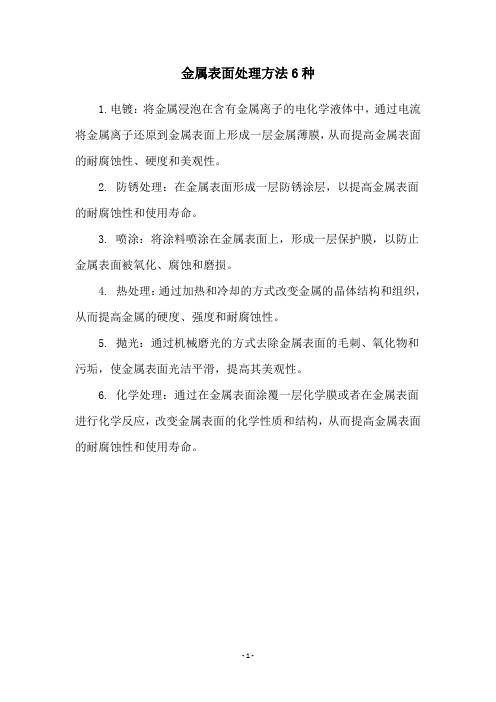
金属表面处理方法6种
1.电镀:将金属浸泡在含有金属离子的电化学液体中,通过电流将金属离子还原到金属表面上形成一层金属薄膜,从而提高金属表面的耐腐蚀性、硬度和美观性。
2. 防锈处理:在金属表面形成一层防锈涂层,以提高金属表面的耐腐蚀性和使用寿命。
3. 喷涂:将涂料喷涂在金属表面上,形成一层保护膜,以防止金属表面被氧化、腐蚀和磨损。
4. 热处理:通过加热和冷却的方式改变金属的晶体结构和组织,从而提高金属的硬度、强度和耐腐蚀性。
5. 抛光:通过机械磨光的方式去除金属表面的毛刺、氧化物和污垢,使金属表面光洁平滑,提高其美观性。
6. 化学处理:通过在金属表面涂覆一层化学膜或者在金属表面进行化学反应,改变金属表面的化学性质和结构,从而提高金属表面的耐腐蚀性和使用寿命。
- 1 -。
几种常见的金属表面处理方法

此法适宜于含铜较高的铸造铝合金。
[方法 8]
喷砂或打磨后,在下述溶液中阳极化:
氧化铬 100 硫酸 0.2 氯化钠 0.2
在 40°C 下于 10min 内将电压从 0 V 升至 10V ,保持 20min ,再在 5min 内从 10V 升
至 50V ,保持 5min ,然后水洗,700C 下干燥。注意:游离氧化铬浓度不得超过 30-35g/l 。
然后在 20°C 的冷水中洗 5min ,再在下述溶液中浸亮:
重铬酸钠 5 浓硫酸 10 水 85
然后在冷水中洗净,浸入氢氧化铵(d=0.85 )10min ,再用冷水洗 5min ,蒸馏水洗
净,在 40°C 下干燥。此法用于黄铜和青铜处理。
[方法 8]
在下述溶液中氧化:
过硫酸钾 1.5 氢氧化钠 5 水 100
氢氟酸(浓) 84 盐酸(37%) 8.9 磷酸(85%) 4.3
经水冲洗,蒸馏水洗净,在 93°C 下干燥。
[方法 4]
脱脂后,用碱性水溶液洗涤,然后在下述溶液中于室温下处理 4-6min:
硝酸(70%) 5 氟化铵 3 水 92
经水洗,在下述溶液中于室温下处理 2min:
磷酸三钠 5
氟化钠 1 氢氟酸 1.5
浓硫酸 30
重铬酸钠 7.5 水 62.5
在室温下浸渍 1min ,水洗,干燥。
二、镁及镁合金表面处理方法
[方法 1]
脱脂处理。常用溶剂为:三氯乙烯、丙酮、醋酸乙酯和丁酮等。
[方法 2]
脱脂后在下述溶液中于 70-75°C 下浸渍 5min :
氢氧化钠 12
水 100
用冷水冲洗,再于下述溶液中在 20°C 浸渍 5min :
常见金属表面处理的种类及工艺、作用

金属表面处理的种类及工艺1、表面处理工艺简介:利用现代物理、化学、金属学和热处理等学科的技术来改变零件表面的状况和性质,使之与心部材料作优化组合,以达到预定性能要求的工艺方法,称为表面处理工艺。
表面处理的作用:提高表面耐蚀性和耐磨性,减缓、消除和修复材料表面的变化及损伤;使普通材料获得具有特殊功能的表面;节约能源、降低成本、改善环境。
2、金属表面处理工艺分类:总共可以分为4大类:表面改性技术、表面合金化技术、表面转化膜技术和表面覆膜技术。
一、表面改性技术1、表面淬火表面淬火是指在不改变钢的化学成分及心部组织情况下,利用快速加热将表层奥氏体化后进行淬火以强化零件表面的热处理方法。
表面淬火的主要方法有火焰淬火和感应加热,常用的热源有氧乙炔或氧丙烷等火焰等。
2、激光表面强化激光表面强化是用聚焦的激光束射向工件表面,在极短时间内将工件表层极薄的材料加热到相变温度或熔点以上的温度,又在极短时间内冷却,使工件表面淬硬强化。
激光表面强化可以分为激光相变强化处理、激光表面合金化处理和激光熔覆处理等。
激光表面强化的热影响区小,变形小,操作方便,主要用于局部强化的零件,如冲裁模、曲轴、凸轮、凸轮轴、花键轴、精密仪器导轨、高速钢刀具、齿轮及内燃机缸套等。
3、喷丸喷丸强化是将大量高速运动的弹丸喷射到零件表面上,犹如无数个小锤锤击金属表面,使零件表层和次表层发生一定的塑性变形而实现强化的一种技术。
作用:提高零件机械强度以及耐磨性、抗疲劳和耐蚀性等;用于表面消光、去氧化皮;消除铸、锻、焊件的残余应力等。
4、滚压滚压是在常温下用硬质滚柱或滚轮施压于旋转的工件表面,并沿母线方向移动,使工件表面塑性变形、硬化,以获得准确、光洁和强化的表面或者特定花纹的表面处理工艺。
应用:圆柱面、锥面、平面等形状比较简单的零件。
5、拉丝拉丝是指在外力作用下使金属强行通过模具,金属横截面积被压缩,并获得所要求的横截面积形状和尺寸的表面处理方法称为金属拉丝工艺。
金属表面处理有哪些方式

表面处理属于最古老的技术,自从地球上有人类,表面处理就是人类最早掌握的一种技术。
原始人类的生活极其艰苦,过着群居的生活,为了生存,他们制造石器工具,应用研磨技术使石器具有锋利刃口,产生“尖劈”效果。
到了新石器时代,原始人使用的石器通体经过研磨,表面细腻光滑,注重装饰效果,已成为时代主流。
表面处理常见的方式有以下四种:
1、机械表面处理:喷砂、抛丸、磨光、滚光、抛光、刷光、喷涂、刷漆、抹油等。
2、化学表面处理:发蓝发黑、磷化、酸洗、化学镀各种金属与合金、TD 处理、QPQ处理、化学氧化等。
3、电化学表面处理:阳极氧化、电化学抛光、电镀等。
4、现代表面处理:化学气相沉积CVD、物理气相沉积PVD、离子注入、离子镀、激光表面处理等。
表面处理的目的是满足产品的耐蚀性、耐磨性、装饰或其他特种功能要求。
详情可以咨询焦作汇鑫恒机械制造有限公司。
金属表面处理常见种类
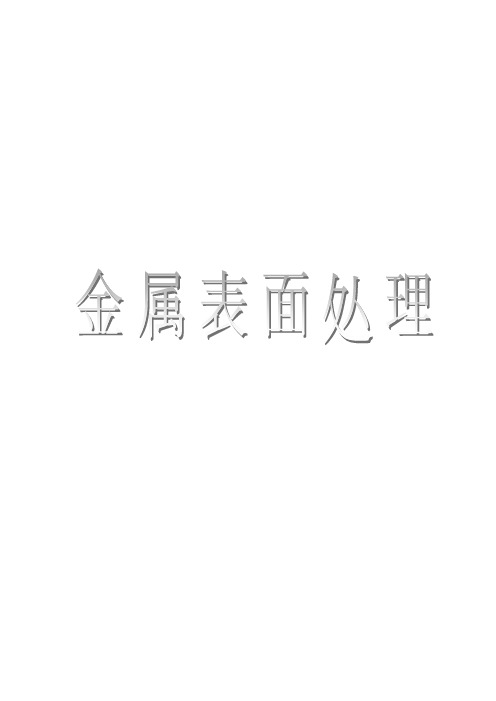
表面处理处理种类表面处理即是通过一定的方法在工件表面形成覆盖层的过程,其目的是赋以制品表面美观、防腐蚀的效果,进行的表面处理方法都归结于以下常用几种方法:1、镀(Plating)电镀(Electroplating) :将接受电镀的部件浸于含有被沉积金属化合物的水溶液中,以电流通过镀液,使电镀金属析出并沉积在部件上。
一般电镀有镀锌、铜、镍、铬、铜镍合金等,有时把煮黑(发蓝)、磷化等也包括其中。
2、热浸镀锌:通过将碳钢部件浸没温度约为510℃的溶化锌的镀槽内完成。
其结果是钢件表面上的铁锌合金渐渐变成产品外表面上的钝化锌。
热浸镀铝是一个类似的过程。
3、机械镀:通过镀层金属的微粒来冲击产品表面,并将涂层冷焊到产品的表面上。
一般螺丝多采用电镀方式,但用在电力、高速公路等室外的六角木螺钉等用热浸锌;电镀的成本一般每公斤为0.6——0.8元,热浸锌一般为1.5——2元/公斤,成本较高。
电镀的效果:电镀的质量以其耐腐蚀能力为主要衡量标准,其次是外观。
耐腐蚀能力即是模仿产品工作环境,设置为试验条件,对其加以腐蚀试验。
电镀产品的质量从以下方面加以控制:1、外观:制品表面不允许有局部无镀层、烧焦、粗糙、灰暗、起皮、结皮状况和明显条纹,不允许有针孔麻点、黑色镀渣、钝化膜疏松、龟裂、脱落和严重的钝化痕迹。
2、镀层厚度:紧固件在腐蚀性大气中的作业寿命与它的镀层厚度成正比。
一般建议的经济电镀镀层厚度为0.00015in~0.0005 in(4~12um).热浸镀锌:标准的平均厚度为54 um(称呼径≤3/8为43 um),最小厚度为43 um(称呼径≤3/8为37 um)。
3、镀层分布:采用不同的沉积方法,镀层在紧固件表面上的聚集方式也不同。
电镀时镀层金属不是均匀地沉积在外周边缘上,转角处获得较厚镀层。
在紧固件的螺纹部分,最厚的镀层位于螺纹牙顶,沿着螺纹侧面渐渐变薄,在牙底处沉积最薄,而热浸镀锌正好相反,较厚的镀层沉积在内转角和螺纹底部,机械镀的镀层金属沉积倾向与热浸镀相同,但是更为光滑而且在整个表面上厚度要均匀得多。
金属表面处理的方法有哪些
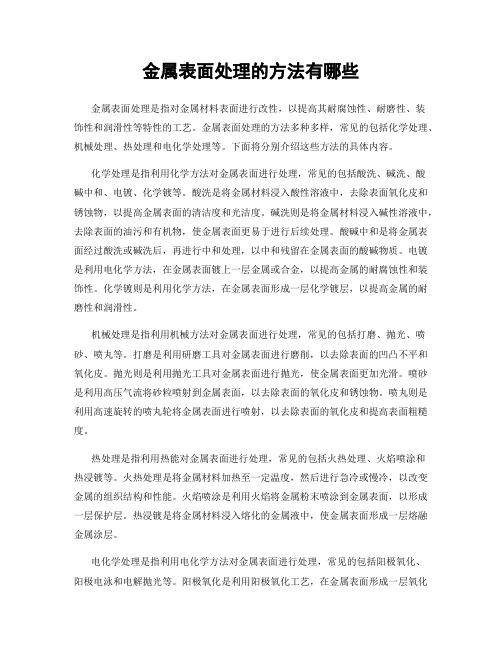
金属表面处理的方法有哪些金属表面处理是指对金属材料表面进行改性,以提高其耐腐蚀性、耐磨性、装饰性和润滑性等特性的工艺。
金属表面处理的方法多种多样,常见的包括化学处理、机械处理、热处理和电化学处理等。
下面将分别介绍这些方法的具体内容。
化学处理是指利用化学方法对金属表面进行处理,常见的包括酸洗、碱洗、酸碱中和、电镀、化学镀等。
酸洗是将金属材料浸入酸性溶液中,去除表面氧化皮和锈蚀物,以提高金属表面的清洁度和光洁度。
碱洗则是将金属材料浸入碱性溶液中,去除表面的油污和有机物,使金属表面更易于进行后续处理。
酸碱中和是将金属表面经过酸洗或碱洗后,再进行中和处理,以中和残留在金属表面的酸碱物质。
电镀是利用电化学方法,在金属表面镀上一层金属或合金,以提高金属的耐腐蚀性和装饰性。
化学镀则是利用化学方法,在金属表面形成一层化学镀层,以提高金属的耐磨性和润滑性。
机械处理是指利用机械方法对金属表面进行处理,常见的包括打磨、抛光、喷砂、喷丸等。
打磨是利用研磨工具对金属表面进行磨削,以去除表面的凹凸不平和氧化皮。
抛光则是利用抛光工具对金属表面进行抛光,使金属表面更加光滑。
喷砂是利用高压气流将砂粒喷射到金属表面,以去除表面的氧化皮和锈蚀物。
喷丸则是利用高速旋转的喷丸轮将金属表面进行喷射,以去除表面的氧化皮和提高表面粗糙度。
热处理是指利用热能对金属表面进行处理,常见的包括火热处理、火焰喷涂和热浸镀等。
火热处理是将金属材料加热至一定温度,然后进行急冷或慢冷,以改变金属的组织结构和性能。
火焰喷涂是利用火焰将金属粉末喷涂到金属表面,以形成一层保护层。
热浸镀是将金属材料浸入熔化的金属液中,使金属表面形成一层熔融金属涂层。
电化学处理是指利用电化学方法对金属表面进行处理,常见的包括阳极氧化、阳极电泳和电解抛光等。
阳极氧化是利用阳极氧化工艺,在金属表面形成一层氧化膜,以提高金属的耐腐蚀性和耐磨性。
阳极电泳是利用电泳工艺,在金属表面形成一层有机涂层,以提高金属的装饰性和涂层均匀性。
常见金属材料表面处理工艺

常见金属材料表面处理工艺
1.喷砂:通过喷射高速砂粒,去除金属表面的氧化皮和污垢,同时增
加表面粗糙度,便于表面涂装和附着。
2.酸洗:将金属材料浸泡在酸性溶液中,去除表面氧化膜、锈斑等不
良物质,使表面变得光洁,便于表面涂装。
3.电镀:通过电解的方式,在金属表面形成一层金属或非金属的镀层,起到美化、防腐、增加硬度或改善耐磨性的作用。
4.电火花加工:利用电火花放电的高温和高压力,削除金属表面微小
毛刺和粗糙度,提高表面平整度和精度。
5.磨光:通过机械磨光,使金属表面光洁度和平整度更高,适用于精
密机械配件和光学器件等领域。
6.喷涂:利用压缩空气将涂料喷洒到金属表面,达到防锈、美化、增
加硬度或改善耐磨性的作用。
7.氧化:将金属材料置于高温维氧气氛中,使金属表面形成一层氧化层,起到增加耐蚀性和装饰作用。
8.拉伸加工:将金属材料经过拉伸变形,使其表面平整度和精度更高,适用于金属薄板和管材加工。
金属的表面处理

金属外表处理金属外表处理一般包含哪几类?金属外表处理有:电镀、涂装、化学处理层。
电镀包括〔镀锌、铜、铬、铅、银、金、镍、锡、镉等〕;涂装包括〔油漆涂装、静电喷粉、喷塑工艺〕;化学处理包括〔发黑处理、磷化处理〕。
另一方面是金属的外表改性,也称外表优化,现代先进的外表改性技术主要有物理气相沉积〔简称PVD〕、化学气相沉积〔简称CVD〕、等离子体化学气相沉积〔简称PCVD〕、离子注入和离子束沉积。
什么是电镀?电镀(electroplating)被定义为一种电沈积过程(electrodepos- ition process),是利用电极(electrode)通过电流,使金属附着于物体外表上,其目的是在改变物体外表之特性或尺寸。
目前较常遇见的电镀方式:水溶液电镀(滚镀、挂镀、连续镀)、化学电镀。
电镀的目的是什么?电镀的目的是在基材上镀上金属镀层(deposit),改变基材外表性质或尺寸。
例如赋予金属光泽美观、物品的防锈、防止磨耗;提高导电度、润滑性、强度、耐热性、耐候性;热处理之防止渗碳、氮化、尺寸错误或磨耗之另件之修补。
电镀的基本流程是什么?前处理(研磨→预备洗净→水洗→电解脱脂→水洗→酸浸渍及活性化→水洗)中和→洗水→电镀(打底) →水洗→中和→水洗→电镀(表层) →水洗→纯水→脱水→烘干前处理不完全所造成的镀层缺陷有以下几点:(1)镀层的剥离、气胀。
(2)污点、无光等光泽不均的现象。
(3)镀层的小孔、不平。
(4)针孔的发生而降低制品的耐蚀性。
(5)镀层皮膜的脆化。
镀锌电镀锌有哪几类?(1)酸性镀锌(acid zinc plating) (2)碱性非氰化物镀锌(alkaline plating )(3)氰化物镀锌(cyanide zinc plating )各有什么优缺点?1.1 酸性镀锌形状简单镀件和做油漆底层用的较多,其优缺点如下:优点(1)可得光泽,平滑,镀锌层相似的镀层(2)可直接镀在碳化,氮化的钢铁上和铸铁上(3)电流效率较高(4)废液处理容易,只需用高ph值将锌沉淀(5)导电性佳,节省电原(6)产生氢脆性小(7)可在较高温下得到光泽镀层(8)镀浴安定,毒性小,成本低缺点(1)镀浴腐蚀性强,镀槽及附属设备需加衬(2)焊接及组合镀件不宜,会有渗流(bleadout)(3)厚镀层延性差(4)结晶粗糙(5)均一性差(6) 需要有过滤,冷却管及冷冻设备碱性非氰化物镀锌(Alkaline Non-Cyanide Zinc Plating)优点(1)毒性小(2)废液处理容易,只需将锌沉淀(3)成本低(4)均一性好(5)可用刚镀槽缺点(1)镀浴成份需严格控制,每天要分析(2)前处理要求质量高(3)锌含量少时,电流效率降低(4)对金属杂质及硬水杂质敏感(5)镀层校氰化镀锌脆(6)需要添加剂,否则黑暗镀层出现(7)添加剂特殊,非一般性原料,需由厂商提供1.3 光泽氰化镀锌优点(1)使用历史悠久,经验较丰富(2)前处理要求比较不严格(3)被覆性优良(4)浴成份的分析及控制比较容易(5)镀层延性好(6)镀浴腐蚀性小缺点(1)镀浴毒性强,须做氰化物废物处理(2)热处理及铸铁零件不能镀(3)需较高温度操作,否则得不到光泽镀层,其温度必须在105F以上(4)镀浴导电性差(5)高电流密度下,电流效率剧降镀锌有哪些特征?良品特征1.锌镀层应是稍带湛蓝色调的银白色2.钝化的锌镀层是带有绿色、黄色和紫色色彩的彩虹色3.五酸钝化的锌镀层应是均一的草绿色4.氧化的锌镀层应是均一的蓝黑色5.磷化的锌镀层应是细晶结构的浅灰色不良品特征1.镀层粗糙、烧焦、麻点、黑点、起泡、脱落2.树枝状、海绵状和条纹状的镀层3.局部无镀层4.可擦去的疏松钝化膜或呈深黄色、棕色和裼色的钝化膜5.成片的淡白色钝化膜6.五酸钝化膜呈深灰色、彩色或淡黄色7.未洗净的盐类痕迹镀镍镀镍有哪几类?通过电解或化学方法在金属或某些非金属上镀上一层镍的方法,称为镀镍。
- 1、下载文档前请自行甄别文档内容的完整性,平台不提供额外的编辑、内容补充、找答案等附加服务。
- 2、"仅部分预览"的文档,不可在线预览部分如存在完整性等问题,可反馈申请退款(可完整预览的文档不适用该条件!)。
- 3、如文档侵犯您的权益,请联系客服反馈,我们会尽快为您处理(人工客服工作时间:9:00-18:30)。
金属表面处理的种类电镀镀层金属或其他不溶性材料做阳极,待镀的工件做阴极,镀层金属的阳离子在待镀工件表面被还原形成镀层。
为排除其它阳离子的干扰,且使镀层均匀、牢固,需用含镀层金属阳离子的溶液做电镀液,以保持镀层金属阳离子的浓度不变。
电镀的目的是在基材上镀上金属镀层,改变基材表面性质或尺寸。
电镀能增强金属的抗腐蚀性(镀层金属多采用耐腐蚀的金属)、增加硬度、防止磨耗、提高导电性、润滑性、耐热性、和表面美观。
电泳电泳是电泳涂料在阴阳两极,施加于电压作用下,带电荷涂料离子移动到阴极,并与阴极表面所产生之碱性作用形成不溶解物,沉积于工件表面。
电泳表面处理工艺的特点:电泳漆膜具有涂层丰满、均匀、平整、光滑的优点,电泳漆膜的硬度、附着力、耐腐、冲击性能、渗透性能明显优于其它涂装工艺。
电泳工艺优于其他涂装工艺。
镀锌镀锌是指在金属、合金或者其它材料的表面镀一层锌以起美观、防锈等作用的表面处理技术。
现在主要采用的方法是热镀锌。
电镀与电泳的区别电镀就是利用电解原理在某些金属表面上镀上一薄层其它金属或合金的过程。
电泳:溶液中带电粒子(离子)在电场中移动的现象。
溶液中带电粒子(离子)在电场中移动的现象。
利用带电粒子在电场中移动速度不同而达到分离的技术称为电泳技术。
电泳又名——电着 (著),泳漆,电沉积。
发黑钢制件的表面发黑处理,也有被称之为发蓝的。
其原理是将钢铁制品表面迅速氧化,使之形成致密的氧化膜保护层,提高钢件的防锈能力。
发黑处理现在常用的方法有传统的碱性加温发黑和出现较晚的常温发黑两种。
但常温发黑工艺对于低碳钢的效果不太好。
A3钢用碱性发黑好一些。
在高温下(约550℃)氧化成的四氧化三铁呈天蓝色,故称发蓝处理。
在低温下(约3 50℃)形成的四氧化三铁呈暗黑色,故称发黑处理。
在兵器制造中,常用的是发蓝处理;在工业生产中,常用的是发黑处理。
采用碱性氧化法或酸性氧化法;使金属表面形成一层氧化膜,以防止金属表面被腐蚀,此处理过程称为“发蓝”。
黑色金属表面经“发蓝”处理后所形成的氧化膜,其外层主要是四氧化三铁,内层为氧化亚铁。
发蓝(发黑)的操作流程:工件装夹→去油→清洗→酸洗→清洗→氧化→清洗→皂化→热水煮洗→检查。
所谓皂化,是用肥皂水溶液在一定温度下浸泡工件。
目的是形成一层硬脂酸铁薄膜,以提高工件的抗腐蚀能力。
金属表面着色金属表面着色,顾名思义就是给金属表面“涂”上颜色,改变其单一的、冰冷的金属色泽,代之以五颜六色,满足不同行业的不同需求。
给金属着色后一般都增加了防腐能力,有的还增加了抗磨能力。
但表面彩色技术主要的应用还在装饰领域,即用来美化生活,美化社会。
抛丸抛丸的原理是用电动机带动叶轮体旋转(直接带动或用V型皮带传动),靠离心力的作用,将直径约在0.2~3.0的弹丸(有铸钢丸、钢丝切丸、不锈钢丸等不同类型)抛向工件的表面,使工件的表面达到一定的粗糙度,使工件变得美观,或者改变工件的焊接拉应力为压应力,提高工件的使用寿命。
通过提高工件表面的粗糙度,也提高了工件后续喷漆的漆膜附着力。
其寓意即为抛丸处理可以为喷漆工艺的前道工序。
喷砂喷砂是采用压缩空气为动力,以形成高速喷射束将喷料(铜矿砂、石英砂、金刚砂、铁砂、海南砂)高速喷射到需要处理的工件表面,使工件表面的外表面的外表或形状发生变化,由于磨料对工件表面的冲击和切削作用,使工件的表面获得一定的清洁度和不同的粗糙度,使工件表面的机械性能得到改善,因此提高了工件的抗疲劳性,增加了它和涂层之间的附着力,延长了涂膜的耐久性,也有利于涂料的流平和装饰。
喷砂工艺与其它清理工艺(如酸洗,工具清理)相比有以下特点:一、喷砂处理是最彻底、最通用、最迅速、效率最高的清理方法。
二、喷砂处理可以在不同粗糙度之间任意选择,而其它工艺是没办法实现这一点的。
手工打磨可以打出毛面但速度太慢,化学溶剂清理则清理表面过于光滑不利于涂层粘接。
喷丸的特点:1、清理的灵活性大。
容易清理复杂工件的内外表面和管件的内壁;并且不受场地的限制,可以将其移至到特大型工件附近进行清理。
2、设备结构简单,整机投资少,易损件少,维修费用低。
3、消耗能量大,必须配备大功率的空压站4、清理表面易有潮气,容易生绣。
5、清理效率低,操作人员多,劳动强度大。
抛丸的特点:1、灵活性差。
受场地的限制,清理工件有些盲目性,在工件内卫表面易产生清理不到的死角、2、不用压缩空气加速弹丸,不必设置大功率的空压站,3、清理表面不易有潮气,不容易生绣。
4、设备结构比较复杂,易损件多,特别是叶片等零件,维修工时多,费用高。
5、清理效率高,费用低,操作人员少,容易实现自动化控制,适用于大批量生产。
喷丸喷丸shot peening 。
用喷丸进行表面处理,打击力大,清理效果明显。
但喷丸对薄板工件的处理,容易使工件变形,且钢丸打击到工件表面(无论抛丸或喷丸)使金属基材产生变形,由于Fe3O4和Fe2O3没有塑性,破碎后剥离,而油膜与基材一同变形,所以对带有油污的工件,抛丸、喷丸无法彻底清除油污。
在现有的工件表面处理方法中,清理效果最佳的还数喷砂清理。
喷砂适用于工件表面要求较高的清理。
但是我国目前通用喷砂设备中多由铰龙、刮板、斗式提升机等原始笨重输砂机械组成。
喷丸与抛丸的区别喷丸使用高压风或压缩空气作动力,而抛丸一般为高速旋转的飞轮将钢砂高速抛射出去。
抛丸效率高,但会有死角,而喷丸比较灵活,但动力消耗大。
两种工艺虽喷射动力和方式不同,但都是高速冲击工件为目的,其效果也基本相同,相比而言,喷丸比较精细,容易控制精度,但效率不及抛丸之高,适形状复杂的小型工件,抛丸比较经济实用,容易控制效率和成本,可以控制丸料的粒度来控制喷射效果,但会有死角,适合于形面单一的工件批量加工.两种工艺的选用主要取决工件的形状和加工效率.喷丸与喷砂的区别喷丸与喷砂都是使用高压风或压缩空气作动力,将其高速的吹出去冲击工件表面达到清理效果,但选择的介质不同,效果也不相同.喷砂处理后,工件表面污物被清除掉,工件表面被微量破坏,表面积大幅增加,从而增加了工件与涂/镀层的结合强度.经过喷砂处理的工件表面为金属本色,但是由于表面为毛糙面,光线被折射掉,故没有金属光泽,为发暗表面.喷丸处理后,工件表面污物被清除掉,工件表面被微量而不被破坏,表面积有所增加.由于加工过程中,工件表面没有被破坏,加工时产生的多余能量就会引会工件基体的表面强化.经过喷丸处理的工件表面也为金属本色,但是由于表面为球状面,光线部分被折射掉,故工件加工为亚光效果.磷化磷化(phosphorization)是一种化学与电化学反应形成磷酸盐化学转化膜的过程,所形成的磷酸盐转化膜称之为磷化膜。
磷化的目的主要是:给基体金属提供保护,在一定程度上防止金属被腐蚀;用于涂漆前打底,提高漆膜层的附着力与防腐蚀能力;在金属冷加工工艺中起减摩润滑使用。
钝化其钝化的机理可用薄膜理论来解释,即认为钝化是由于金属与氧化性质作用,作用时在金属表面生成一种非常薄的、致密的、覆盖性能良好的、牢固地吸附在金属表面上的钝化膜。
这层膜成独立相存在,通常是氧化金属的化合物。
它起着把金属与腐蚀介质完全隔开的作用,防止金属与腐蚀介质接触,从而使金属基本停止溶解形成钝态达到防腐蚀的作用。
钝化的优点1、与传统的物理封闭法相比,钝化处理后具有绝对不增加工件厚度和改变颜色的特点、提高了产品的精密度和附加值,使操作更方便;2、由于钝化的过程属于无反应状态进行,钝化剂可反复添加使用,因此寿命更长、成本更经济。
3、钝化促使金属表面形成的氧分子结构钝化膜、膜层致密、性能稳定,并且在空气中同时具有自行修复作用,因此与传统的涂防锈油的方法相比,钝化形成的钝化膜更稳定、更具耐蚀性。
金属或合金受一些因素影响,化学稳定性明显增强的现象,称为钝化。
由某些钝化剂(化学药品)所引起的金属钝化现象,称为化学钝化。
如浓HNO3、浓H2SO4、HClO3、K2Cr2O7、KMnO4等氧化剂都可使金属钝化。
金属钝化后,其电极电势向正方向移动,使其失去了原有的特性,如钝化了的铁在铜盐中不能将铜置换出。
此外,用电化学方法也可使金属钝化,如将Fe置于H2SO4溶液中作为阳极,用外加电流使阳极极化,采用一定仪器使铁电位升高一定程度,Fe就钝化了。
由阳极极化引起的金属钝化现象,叫阳极钝化或电化学钝化。
喷涂利用压力或静电力将油漆或粉末附着在工件表面,使工件有防腐和外观装饰作用.烤漆在基材上打上底漆、面漆,每上一遍漆,都送入无尘衡温烤房,烘烤。
浸渗是一种微孔(细缝)渗透密封工艺。
将密封介质(通常是低粘度液体)通过自然渗透(即微孔自吸)、抽真空和加压等方法渗入微孔(细缝)中,将缝隙填充满,然后通过自然(室温)、冷却或加热等方法将缝隙里的密封介质固化,达到密封缝隙的作用。
喷油将油漆喷在产品表面,自然风干的方式。
抛光利用柔性抛光工具和磨料颗粒或其他抛光介质对工件表面进行的修饰加工。
抛光不能提高工件的尺寸精度或几何形状精度,而是以得到光滑表面或镜面光泽为目的,有时也用以消除光泽(消光)。
通常以抛光轮作为抛光工具。
抛光轮一般用多层帆布、毛毡或皮革叠制而成,两侧用金属圆板夹紧,其轮缘涂敷由微粉磨料和油脂等均匀混合而成的抛光剂。
抛光时,高速旋转的抛光轮(圆周速度在20米/秒以上)压向工件,使磨料对工件表面产生滚压和微量切削,从而获得光亮的加工表面,表面粗糙度一般可达Ra0.63~0.01微米;当采用非油脂性的消光抛光剂时,可对光亮表面消光以改善外观。
对产品表面要求稍低时,常采用滚筒抛光的方法。
粗抛时将大量磨料和产品放在罐状滚筒中,滚筒转动时,使产品与磨料等在筒内随机地滚动碰撞以达到去除表面凸锋而减小表面粗糙度的目的。
超声波清洗是利用超声波在液体中的空化作用、加速度作用及直进流作用对液体和污物直接、间接的作用,使污物层被分散、乳化、剥离而达到清洗目的。