精馏原理3s
化工原理精馏知识点总结
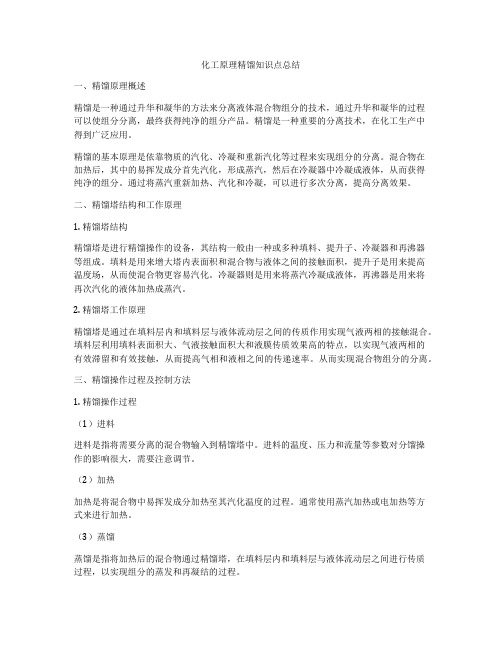
化工原理精馏知识点总结一、精馏原理概述精馏是一种通过升华和凝华的方法来分离液体混合物组分的技术,通过升华和凝华的过程可以使组分分离,最终获得纯净的组分产品。
精馏是一种重要的分离技术,在化工生产中得到广泛应用。
精馏的基本原理是依靠物质的汽化、冷凝和重新汽化等过程来实现组分的分离。
混合物在加热后,其中的易挥发成分首先汽化,形成蒸汽,然后在冷凝器中冷凝成液体,从而获得纯净的组分。
通过将蒸汽重新加热、汽化和冷凝,可以进行多次分离,提高分离效果。
二、精馏塔结构和工作原理1. 精馏塔结构精馏塔是进行精馏操作的设备,其结构一般由一种或多种填料、提升子、冷凝器和再沸器等组成。
填料是用来增大塔内表面积和混合物与液体之间的接触面积,提升子是用来提高温度场,从而使混合物更容易汽化。
冷凝器则是用来将蒸汽冷凝成液体,再沸器是用来将再次汽化的液体加热成蒸汽。
2. 精馏塔工作原理精馏塔是通过在填料层内和填料层与液体流动层之间的传质作用实现气液两相的接触混合。
填料层利用填料表面积大、气液接触面积大和液膜传质效果高的特点,以实现气液两相的有效滞留和有效接触,从而提高气相和液相之间的传递速率。
从而实现混合物组分的分离。
三、精馏操作过程及控制方法1. 精馏操作过程(1)进料进料是指将需要分离的混合物输入到精馏塔中。
进料的温度、压力和流量等参数对分馏操作的影响很大,需要注意调节。
(2)加热加热是将混合物中易挥发成分加热至其汽化温度的过程。
通常使用蒸汽加热或电加热等方式来进行加热。
(3)蒸馏蒸馏是指将加热后的混合物通过精馏塔,在填料层内和填料层与液体流动层之间进行传质过程,以实现组分的蒸发和再凝结的过程。
(4)冷凝冷凝是指将产生的蒸汽通过冷凝器使之冷却成液体,从而得到纯净的组分。
冷凝器通常采用水冷或风冷等方式来进行冷却。
2. 精馏操作控制方法(1)温度控制保持适当的加热温度是进行精馏操作的关键,通过合理控制加热温度,可以使易挥发组分蒸发,而留下不易挥发组分。
精馏操作原理

精馏操作原理
精馏操作原理是利用物质间沸点或挥发度的不同,通过加热、蒸发、冷凝等物理手段实现混合物的分离。
具体来说,精馏过程包括汽化、冷凝、回流等步骤,通过控制加热温度、冷凝温度和操作压力等条件,使混合物中各组分得到分离和纯化。
精馏操作中,首先将原料加热汽化,使其中的轻组分和重组分分别向汽相和液相分布。
汽相通过多次冷凝和再沸,各组分逐次富集,最后得到高纯度的轻组分产品。
液相则通过多次蒸发和冷凝,各组分逐次贫化,最后得到高纯度的重组分产品。
精馏操作的关键在于控制加热温度、冷凝温度和操作压力等条件,使各组分得到充分的分离和纯化。
同时,还需考虑设备的效率、能耗、稳定性等方面的问题。
精馏操作在石油、化工、轻工等领域得到广泛应用,是工业上实现液体混合物分离的重要技术之一。
蒸馏或精馏的基本原理

蒸馏或精馏的基本原理
蒸馏和精馏是常用的分离技术,其基本原理在化工生产和实验室中被广泛应用。
蒸馏和精馏是通过液相和气相之间的分馏作用实现的,本文将详细介绍这两种技术的基本原理及其区别。
蒸馏的基本原理
蒸馏是将液体混合物在受热的装置中加热,使其转变为气态,然后再将气态物
质冷凝并收集的分离方法。
其基本原理是利用不同物质的沸点差异来实现分离。
在蒸馏过程中,混合物中沸点较低的物质首先蒸发,然后冷凝成为液体,从而实现物质的分离。
蒸馏通常分为简单蒸馏和精馏两种类型。
简单蒸馏适用于沸点差异较大的混合物,而精馏则适用于沸点差异较小的混合物。
精馏的基本原理
精馏是蒸馏的一种改良方法,用于分离沸点接近的液体混合物。
与简单蒸馏不同,精馏在蒸馏过程中通过多次蒸馏操作来提高纯度,实现更精确的分离。
在精馏过程中,混合物经过加热蒸发、冷凝以及收集凝结液体的多个循环,从而逐渐提高目标物质的纯度。
精馏的基本原理是利用混合物中各组分的沸点差异来不断分离混合物,通过多
次蒸馏操作使得目标物质逐渐富集在收集液体中。
精馏可以更有效地提高混合物的纯度,广泛应用于化工生产、制药和食品工业中。
总结
蒸馏和精馏是重要的分离技术,通过利用不同物质的沸点差异来实现混合物的
分离。
蒸馏适用于沸点差异较大的混合物,而精馏则适用于沸点差异较小的混合物。
精馏通过多次蒸馏操作提高纯度,广泛应用于化工生产和实验室分离技术中。
在实际应用中,根据需要选择合适的蒸馏或精馏方法来实现目标物质的分离。
(化工原理)精馏原理

精馏的原理和过程
原理
基于物质的沸点不同,通过加热和冷凝的方法,将不同沸点的物 质分离出来。
过程
将液体混合物加热至沸腾,产生的蒸汽在冷凝器中冷凝,再通过 回流装置将冷凝液返回精馏塔中,重复进行加热和冷凝的过程, 直至达到分离目的。
操作温度应根据进料组成 和产品要求进行选择,以
实现最佳分离效果。
操作压力应根据进料组成 和产品要求进行选择,以
实现最佳分离效果。
操作条件的优化
实验法
通过实验方法测定不同操作条件下的分离效果,找 出最优的操作条件。
模拟法
利用计算机模拟软件对精馏过程进行模拟,通过优 化算法找出最优的操作条件。
经济分析法
石油化工原料的制备
通过精馏技术可以制备石油化 工原料,如乙烯、丙烯等,这 些原料是生产塑料、合成橡胶 等材料的重要基础。
精馏在其他领域的应用
01
02
03
食品工业
精馏技术可用于食品工业 中,如分离果汁中的果糖 和乙醇饮料中的酒精等。
制药工业
精馏技术可用于药品的生 产和提纯,如分离抗生素、 维生素等。
精馏的分类
02
01
03
根据操作方式的不同,精馏可以分为连续精馏和间歇 精馏。
根据进料位置的不同,精馏可以分为侧线精馏、塔顶 精馏和塔底精馏。
根据操作压力的不同,精馏可以分为常压精馏、加压 精馏和减压精馏。
02
精馏塔的构造和工作原理
精馏塔的结构
塔体
进料板
塔板
溢流管
冷凝器
精馏塔的主要部分,用于 容纳待分离的液体混合物 和进行传热传质过程。
精馏原理和流程

1-4精馏原理和流程1.掌握的内容:精馏分离过程原理及分析2.重点:精馏原理、精馏装置作用3.难点:精馏原理,部分气化和部分冷凝在实际精馏操作中有机结合的过程。
1.4.1 精馏原理精馏原理是根据图1-7所示的t-x-y图,在一定的压力下,通过多次部分气化和多次部分冷凝使混合液得以分离,以分别获得接近纯态的组分。
理论上多次部分气化在液相中可获得高纯度的难挥发组分,多次部分冷凝在气相中可获得高纯度的易挥发组分,但因产生大量中间组分而使产品量极少,且设备庞大。
工业生产中的精馏过程是在精馏塔中将部分气化过程和部分冷凝过程有机结合而实现操作的。
1.4.2 精馏装置流程一、精馏装置流程典型的精馏设备是连续精馏装置,包括精馏塔、冷凝器、再沸器等,如图1-8所示。
用于精馏的塔设备有两种,即板式塔和填料塔,但常采用的是板式塔。
连续精馏操作中,原料液连续送入精馏塔内,同时从塔顶和塔底连续得到产品(馏出液、釜残液),所以是一种定态操作过程。
二、精馏装置的作用精馏塔以加料板为界分为两段,精馏段和提馏段。
1.精馏段的作用加料板以上的塔段为精馏段,其作用是逐板增浓上升气相中易挥发组分的浓度。
2.提馏段的作用包括加料板在内的以下塔板为提馏段,其作用逐板提取下降的液相中易挥发组分。
3.塔板的作用塔板是供气液两相进行传质和传热的场所。
每一块塔板上气液两相进行双向传质,只要有足够的塔板数,就可以将混合液分离成两个较纯净的组分。
4.再沸器的作用其作用是提供一定流量的上升蒸气流。
5.冷凝器的作用其作用是提供塔顶液相产品并保证有适当的液相回流。
回流主要补充塔板上易挥发组分的浓度,是精馏连续定态进行的必要条件。
精馏是一种利用回流使混合液得到高纯度分离的蒸馏方法。
1-5两组分连续精馏的计算1.掌握的内容:(1)精馏塔物料衡算的应用。
(2)操作线方程和q线方程及其在x-y图上的作法和应用。
(3)理论板和实际板数的确定(逐板计算法和图解法)、塔高和塔径的计算。
精馏的基本知识

精馏的基本知识
精馏是一种物质分离的方法,通过对混合物进行加热,使其中的成分以不同的沸点蒸发,然后再冷凝成液体。
这样,就可以利用不同成分之间的沸点差异来进行分离。
精馏的基本原理是利用混合物中不同成分的沸点差异,使液体成分蒸发后冷凝回流,分离出纯净的组分。
具体步骤如下:
1. 加热混合物:将混合物加热至其中的成分开始蒸发。
加热的方式可以是直接加热或通过加热器。
2. 蒸汽冷凝:将蒸发的气体通过冷凝器冷却,使其变为液态。
冷凝可以采用冷水或其他冷却介质进行。
3. 分离纯净成分:冷凝后的液体被收集并用于分离纯净成分。
分离可以通过收集液体的不同组分,或者通过进一步加热蒸发、冷凝的循环操作来提高纯度。
值得注意的是,精馏的有效性取决于混合物中各组分之间的沸点差异。
如果沸点差异较小,可能需要采用多次精馏或者配合其他分离方法。
此外,精馏还需考虑各组分的物化性质、操作压力等因素。
精馏的原理是什么
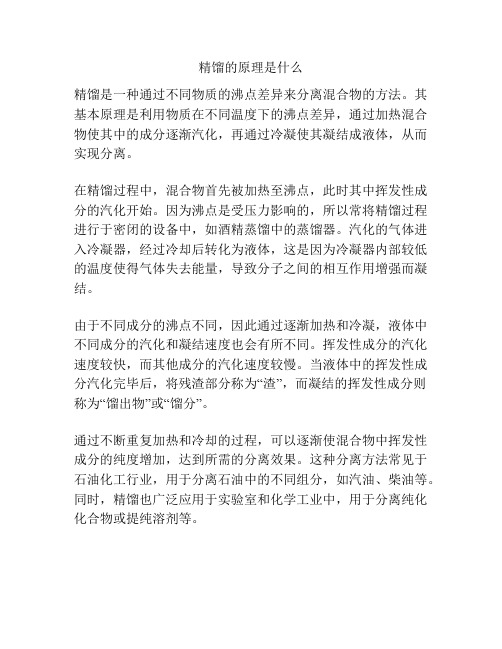
精馏的原理是什么
精馏是一种通过不同物质的沸点差异来分离混合物的方法。
其基本原理是利用物质在不同温度下的沸点差异,通过加热混合物使其中的成分逐渐汽化,再通过冷凝使其凝结成液体,从而实现分离。
在精馏过程中,混合物首先被加热至沸点,此时其中挥发性成分的汽化开始。
因为沸点是受压力影响的,所以常将精馏过程进行于密闭的设备中,如酒精蒸馏中的蒸馏器。
汽化的气体进入冷凝器,经过冷却后转化为液体,这是因为冷凝器内部较低的温度使得气体失去能量,导致分子之间的相互作用增强而凝结。
由于不同成分的沸点不同,因此通过逐渐加热和冷凝,液体中不同成分的汽化和凝结速度也会有所不同。
挥发性成分的汽化速度较快,而其他成分的汽化速度较慢。
当液体中的挥发性成分汽化完毕后,将残渣部分称为“渣”,而凝结的挥发性成分则称为“馏出物”或“馏分”。
通过不断重复加热和冷却的过程,可以逐渐使混合物中挥发性成分的纯度增加,达到所需的分离效果。
这种分离方法常见于石油化工行业,用于分离石油中的不同组分,如汽油、柴油等。
同时,精馏也广泛应用于实验室和化学工业中,用于分离纯化化合物或提纯溶剂等。
精馏原理
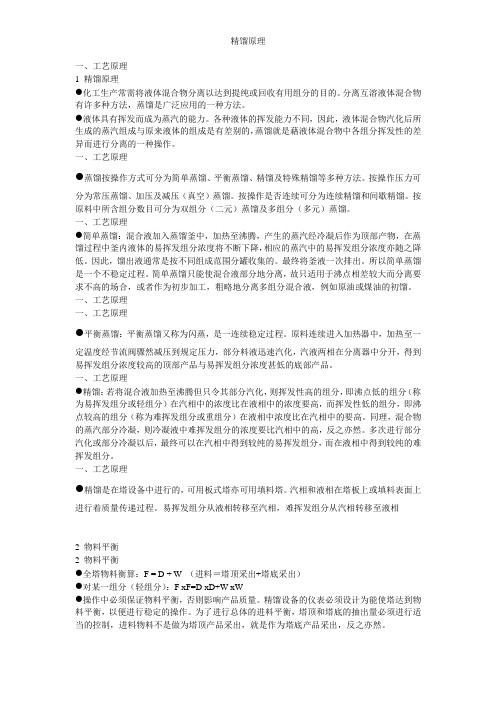
一、工艺原理1 精馏原理●化工生产常需将液体混合物分离以达到提纯或回收有用组分的目的。
分离互溶液体混合物有许多种方法,蒸馏是广泛应用的一种方法。
●液体具有挥发而成为蒸汽的能力。
各种液体的挥发能力不同,因此,液体混合物汽化后所生成的蒸汽组成与原来液体的组成是有差别的,蒸馏就是藉液体混合物中各组分挥发性的差异而进行分离的一种操作。
一、工艺原理●蒸馏按操作方式可分为简单蒸馏、平衡蒸馏、精馏及特殊精馏等多种方法。
按操作压力可分为常压蒸馏、加压及减压(真空)蒸馏。
按操作是否连续可分为连续精馏和间歇精馏。
按原料中所含组分数目可分为双组分(二元)蒸馏及多组分(多元)蒸馏。
一、工艺原理●简单蒸馏:混合液加入蒸馏釜中,加热至沸腾,产生的蒸汽经冷凝后作为顶部产物,在蒸馏过程中釜内液体的易挥发组分浓度将不断下降,相应的蒸汽中的易挥发组分浓度亦随之降低。
因此,馏出液通常是按不同组成范围分罐收集的。
最终将釜液一次排出。
所以简单蒸馏是一个不稳定过程。
简单蒸馏只能使混合液部分地分离,故只适用于沸点相差较大而分离要求不高的场合,或者作为初步加工,粗略地分离多组分混合液,例如原油或煤油的初馏。
一、工艺原理一、工艺原理●平衡蒸馏:平衡蒸馏又称为闪蒸,是一连续稳定过程。
原料连续进入加热器中,加热至一定温度经节流阀骤然减压到规定压力,部分料液迅速汽化,汽液两相在分离器中分开,得到易挥发组分浓度较高的顶部产品与易挥发组分浓度甚低的底部产品。
一、工艺原理●精馏:若将混合液加热至沸腾但只令其部分汽化,则挥发性高的组分,即沸点低的组分(称为易挥发组分或轻组分)在汽相中的浓度比在液相中的浓度要高,而挥发性低的组分,即沸点较高的组分(称为难挥发组分或重组分)在液相中浓度比在汽相中的要高。
同理,混合物的蒸汽部分冷凝,则冷凝液中难挥发组分的浓度要比汽相中的高,反之亦然。
多次进行部分汽化或部分冷凝以后,最终可以在汽相中得到较纯的易挥发组分,而在液相中得到较纯的难挥发组分。
- 1、下载文档前请自行甄别文档内容的完整性,平台不提供额外的编辑、内容补充、找答案等附加服务。
- 2、"仅部分预览"的文档,不可在线预览部分如存在完整性等问题,可反馈申请退款(可完整预览的文档不适用该条件!)。
- 3、如文档侵犯您的权益,请联系客服反馈,我们会尽快为您处理(人工客服工作时间:9:00-18:30)。
三元溶液节流节流后蒸气及液体的组成
• 方法一:图解 • 方法二:试算
张祉佑上册 蒸气量R" = Rα R , 组分为y1R" , y2 " R 液体量R' = R(1 − α R ), 组分为x1R ' , x2 '
操作线方程式 操作线截距 斜率
yI = yI =
(1 − α ) L N 2 V N 2 − αL N 2
xI +
N N VN2 y N2 − LN2 x N2
V N 2 − αL N 2
N N VN 2 y N2 − LN2 x N2
V N 2 − αL N 2
(1 − α ) LN 2 LI tga I = = V I V N 2 − αL N 2
VII = VI − α K LK = VN 2 − αVN 2 − α K LK
4.4 三元系精馏过程的计算
液空进料口位置
•
选择液空进料口位置的原则是在保证产品数量和纯度 的条件下,使所要求的理论塔板数最少。 当从液空进料口以上的塔段向下计算,如果出现增加 塔板数而在液相或气相中氧的浓度增加不明显、且氩 浓度开始下降时就需安排液空进料。但具体安排在哪 一块塔板最合适,尚需通过试算确定。液空进料后, 氧浓度会迅速增加,氩浓度也能增加,而后达到收 敛。
•
由于氩的沸点处于氧、氮沸点之间,在空分塔中将产 生氩的浓缩积聚现象。在上塔的上部,氩沸点比氮 高,气相中氩易被冷凝到液相中,随回流液向下流。 而在上塔的下部,氩的沸点比氧低,液相中氩易被蒸 发到气相,随塔内蒸气而上升,这样,在塔的中部便 会形成氩的富集区。 据实验,上塔中部含氩量可达10%左右,有些部位甚至 在10%以上。在这些部位如果仍按氮、氧分离进行计 算,必然会产生较大的误差。 在空分塔设计中一般多按三元系进行计算;尤其在设 计制取高纯氮的精馏塔时,必须按三元系进行计算。
4.3 二元系精馏过程的计算
下塔理论塔板数的确定
VK + L = V + LK
V, y L, x
VK y
K N2
+ Lx = Lk x
K N2
+ Vy
如果进塔空气是饱和状态
K Vk , yN2
Vk = V
Lk , x
K N2
则
Lk = L
LK LK K K y= x + ( yN2 − xN 2 ) VK VK
•
•
4.4 三元系精馏过程的计算
三元系精馏过程的计算步骤 三元逐板计算中,所作假设与二元系相同 逐板计算步骤: • 首先按稳定流动物料平衡规律求出塔中各物流 数量和浓度关系; • 确定各塔段的操作线; • 利用三元组分相平衡图,用逐板计算法确定理 论塔板数。
4.4 三元系精馏过程的计算
三元系精馏过程的计算分段
液氮节流后气化率α
LI = (1 − α ) LN 2
VI = VN 2 − αLN 2
精馏段操作线方程式
yI = (1 − α ) LN 2 VN 2 − αLN 2 xI +
N N V N 2 y N 2 − LN 2 x N 2
V N 2 − α LN 2
4.3 二元系精馏过程的计算
上塔精馏段
II II O VII y2 = LII x2 − VO2 y2
LII II VO2 O y = x1 − y1 操作线 VII VII 方程组 LII II VO2 O II y2 x2 − y2 = VII VII
II 1
液空节流气化率αK
LII = LI + (1 − α K ) LK = (1 − α ) LN 2 + (1 − α K ) LK
( y1( 0) , y20 )
x1(1) ⎫ 操作线 ⎧ y1(1) ⎯⎯ →⎨ (1) ⎯ (1) ⎬ x2 ⎭ ⎩ y2
三元相图
( ( x11) ,x21) ( ( x12) ,x22)
( y1(1) , y21)
( y1( 2) , y22)
x1( 2) ⎫ 操作线 ⎧ y1( 2) ⎯⎯ →⎨ ( 2) ⎯ ( 2) ⎬ x2 ⎭ ⎩ y2 LL x1( n ) = x1K ⎫ (n) K⎬ x2 = x2 ⎭
I 1
LI I VN 2 N LN 2 N y = x2 + y2 − x2 VI VI VI
I 2
液氮节流气化率α
LI = (1 − α ) LN 2 VI = VN 2 − αLN 2
4.4 三元系精馏过程的计算
三元系精馏过程的计算 上塔提馏段
VII = LII − VO2
VII y1II = LII x1II − VO2 y1O
液空节流后气化率αK
LII = (1 − α ) LN 2 + (1 − α K ) LK
VII = VN 2 − αLN 2 − α K LK
提馏段操作线方程式
y II = (1 − α ) LN 2 + (1 − α K ) LK VN 2 − αLN 2 − α K LK xII −
O VO2 y N 2
1* 2* 3*
4.3 二元系精馏过程的计算
上塔理论塔板数的确定
上塔中以液空进料口 为界,以上为精馏 段,以下为提馏段, 分别建立物料平衡关 系式,由于两段的汽 液比不同,故其操作 线斜率不同
精馏段和提馏段理论 塔板数分别进行计算
4.3 二元系精馏过程的计算
上塔精馏段
物料衡算
N N LN 2 x N 2 + VI y I = VN 2 y N 2 + LI xI
Vk , y
K N2
已知液氮浓度,富氧液空浓 度,则可由上而下或由下而 上求得下塔理论塔板数 。
K Lk , xN2
三元系精馏过 程的计算
x x
(0) 1 (0) 2
⎫ 操作线 ⎧ y1( 0) =x ⎯ ⎬ ⎯⎯ →⎨ ( 0) =x ⎭ ⎩ y2
N 1 N 2
三元相图
( ( x10) ,x20)
•
膨胀空气进料口位置
根据经验,对于全低压制氧装置的精馏塔,一般在液空 进料口以下2~3块理论塔板处安排膨胀空气的入口。
4.4 三元系精馏过程的计算
三元溶液节流节流后蒸气及液体的组成
气化率可用 h-x图和T-x 图近似计算
c’
m' ' a ' b' = α= m a ' c'
a’ b’
4.4 三元系精馏过程的计算
VN 2 − αLN 2 − α K LK
4.3 二元系精馏过程的计算
上塔提馏段
操作线方程
y II = (1 − α ) LN 2 + (1 − α K ) LK VN 2 − αLN 2 − α K LK xII −
O VO2 y N 2
VN 2 − αLN 2 − α K LK
O xII = y N 2
• 在平衡曲线和操作线之间作阶梯线段,各塔段
形成的三角形数即代表该段的理论塔板数。
液气比对塔板数的影响
y 1*
液气比 沿塔下流的液体和 上升蒸气之比L/V
2* 3* 2 3 x= y
1
0
K xN 2
LN xN 2
x
液气比对塔板数的影响
上塔
当氧、氮纯度已定,精馏段和提 馏段两操作线的交点C的位置可 以随气液比的不同在C1和C2之间 移动。 当交点愈偏向C1点,说明精馏段 液气比愈小,塔板数则愈多,塔 的高度和沿塔的流动阻力都会增 加。 当交点愈偏向C1时,精馏段操作 线的斜率为最小值,要达到这种 工况,理论上需要无穷多块塔 ⎛L⎞ 板。 ⎜ ⎟
4.4 三元系精馏过程的计算
三元系精馏过程的计算 上塔精馏段
VI + LN 2 = LI + VN 2
VI y1I = LI x1I + VN 2 y1N − LN 2 x1N
I I N N VI y2 = LI x2 + VN 2 y2 − LN 2 x2
操作线方程组
LI I VN 2 N LN 2 N x1 y1 − y = x1 + VI VI VI
4.3 二元系精馏过程的计算
下塔理论塔板数的确定 y 理论塔板数
n = 2.5
V, y L, x
1* 2* 3* 2 3 x= y
1
K Vk , yN2
K Lk , xN2
0
K xN 2
LN xN 2
x
1点代表两股物流:(x1,y1) 1*点代表平衡物流(y1,x2) 2点代表不平衡物流(x2,y2)
4.3 二元系精馏过程的计算
下塔理论塔板数的确定
LK K LK K x + ( yN2 − xN 2 ) 下塔操作线方程 y = VK VK
操作线的截距(即x=0时)
y=y
K N2
LK K − xN 2 VK
下塔顶部的氮气浓度与冷凝的液 氮浓度相同,表示该截面气液组 分浓度的点在y=x线上。联立解 下塔操作线方程式和y=x可得其 交点的横坐标 。
K Vk , y N 2
进塔空气是饱和状态
K Lk , x N2
Lk = L Vk = V
x1 + x2 + x3 = 1, y1 + y2 + y3 = 1
4.4 三元系精馏过程的计算
三元系精馏过程的计算 下塔操作线方程
V, y L, x
L VK K LK K y1 = x1 + y1 − x1 V V V V K L K L y 2 = x2 + K y 2 − K x2 V V V
N N y N2 ≈ x N2