机械加工表面加工质量
机械制造工艺学 第四节 机械加工表面质量
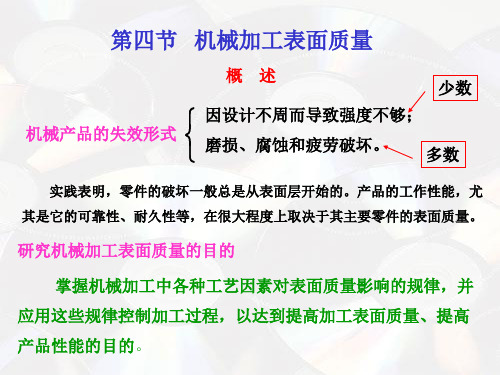
2)砂轮的粒度和砂轮的修整对表面粗糙度的影响
砂轮的粒度
磨粒间的距离
磨粒的大小
砂轮的粒度号越大, 磨粒和磨粒间离越小
砂轮的粒度号↑ ,参与磨削的磨粒↑ ,粗糙度↓ ;
修整砂轮时,纵向进给量对表面粗糙度的影响甚大; 纵向进给量↓ ,砂轮表面的等高性越好 ,粗糙度 ↓ ;
(2)金属表面层的塑性变形 在磨削过程中,由于磨粒大多具有很大的负前角,很不锋 利,所以大多数磨粒在磨削时只是对表面产生挤压作用而使表 面出现塑性变形,磨削时的高温更加剧了塑性变形,增大了表 面粗糙度值。
表面层的加工硬化对疲劳强度影响 适当的加工硬化能阻碍已有裂纹的继续扩大和新裂纹的产生,有助于 提高疲劳强度。但加工硬化程度过大,反而易产生裂纹,故加工硬化程度 应控制在一定范围内。
拉应力加剧疲劳裂纹的产生和扩展;
3.表面质量对零件耐腐蚀性的影响 表面粗糙 表面粗糙度值越大,越容易积聚腐蚀性物质; 度的影响 波谷越深,渗透与腐蚀作用越强烈。 零件的耐腐蚀性在很大程度上取决于表面粗糙度 表面残余应力对零件耐腐蚀性影响
(二)、表面层的残余应力 l、表面层残余应力及其产生的原因 表面层残余应力 外部载荷去除后,工件表面层及其与
基体材料的交界处仍残存的互相平衡的应力。
表面层残余应 力产生的原因
(1)冷态塑性变形引起的残余应力 (2)热态塑性变形引起的残余应力 (3)金相组织变化引起的残余应力
(1)冷态塑性变形引起的残余应力
其中: H——加工后表面层的显微硬度
H0——材料原有的显微硬度
(2)表面层金相组织变化
指的是加工中,由于切削热的作用引起表层金属金相组织 发生变化的现象。如磨削时常发生的磨削烧伤,大大降低表面 层的物理机械性能。 (3)表面层产生残余应力 指的是加工中,由于切削变形 和切削热的作用,工件表层及其基 体材料的交界处产生相互平衡的弹 性应力的现象。残余应力超过材料
机械加工精度与加工表面质量

机械加工精度与加工表面质量机械加工精度和加工表面质量是衡量机械加工工艺质量的两个重要指标。
机械加工精度是指加工件在尺寸、形状、位置和几何特征等方面的精确度,而加工表面质量则是指加工件表面的光洁度、粗糙度以及表面缺陷等特征。
这两个指标在现代制造业中具有重要的意义,直接关系到产品的质量和性能。
1. 机械加工精度机械加工精度通常表示加工件与其设计尺寸之间的误差。
机械加工精度的高低直接影响着加工件的装配性能和使用寿命。
常见的机械加工精度包括以下几个方面:1.1 尺寸精度尺寸精度是指加工件的几何尺寸与其设计尺寸之间的偏差。
尺寸精度可以通过测量加工件的长度、直径、角度等几何参数来评估。
通常,尺寸精度可以分为直线度、平行度、圆度、圆柱度、角度度等几个方面。
1.2 形状精度形状精度是指加工件的形状与设计形状之间的误差。
形状精度通常包括圆度、平面度、圆锥度、曲率半径等方面。
1.3 位置精度位置精度是指加工件上各个特征点的位置与设计位置之间的误差。
位置精度可以通过测量加工件上的特征点坐标来评估。
常见的位置精度指标有平行度、垂直度、位置误差等。
2. 加工表面质量加工表面质量是指加工件表面的光洁度、粗糙度以及表面缺陷等特征。
加工表面质量直接影响着摩擦、磨损、润滑等性能,同时也会影响产品的外观质量。
常见的加工表面质量指标包括以下几个方面:2.1 光洁度光洁度是指加工件表面的光亮程度。
光洁度往往是使用表面粗糙度指标来评估的,一般可通过光学显微镜、表面形貌仪等设备进行测量。
2.2 粗糙度粗糙度是指加工件表面的不规则程度。
表面粗糙度通常用Ra值表示,Ra值越小代表表面越光滑。
可以通过表面粗糙度仪进行测量,也可以使用触摸法、光学法等方法。
2.3 表面缺陷表面缺陷是指加工件表面的瑕疵、裂纹、划痕等缺陷。
表面缺陷会降低产品的整体质量和可靠性,因此正常加工过程中要尽量避免表面缺陷的产生。
3. 如何提高机械加工精度和加工表面质量为了提高机械加工精度和加工表面质量,可以从以下几个方面入手:3.1 选择合适的机床和刀具机床和刀具是机械加工的基础设备,选择合适的机床和刀具对于提高加工精度和表面质量非常重要。
机械加工表面质量
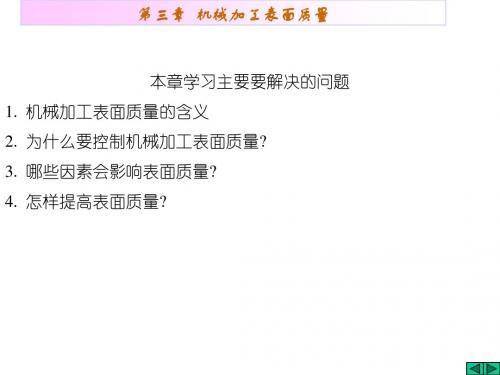
2.表面层物理 力学、化学性能
(1)表面粗糙度 (2)表面波度 (3)纹理方向 (4)伤痕——表面上一些个别位置 上出现的缺陷
(1)表面层加工硬化(冷作硬化)。 (2)表面层金相组织变化。
(3)表面层产生残余应力。
第一节 加工表面质量及其对使用性能的影响
第一节 加工表面质量及其对使用性能的影响
影响表层残余应力的因素
三、表层金属的残余应力——拉应力或者压应力
(一)残余应力产生的原因 1)冷塑性变形——使表层产生压缩残余应力,里层产生拉伸 残余应力。
原因:加工表面受刀具或砂轮磨粒的挤压和摩擦,产生拉伸塑性变形 ,此 时里层金属处于弹性变形状态,切削后里层金属趋于弹性恢复,但受 到已产生塑性变形的表层金属牵制
第三章 机械加工表面质量
本章学习主要要解决的问题 1. 机械加工表面质量的含义 2. 为什么要控制机械加工表面质量? 3. 哪些因素会影响表面质量? 4. 怎样提高表面质量?
第三章 机械加工表面质量
第一节 加工表面质量及其对使用性能的影响
一、机械加工表面质量的含义
1.表面的几何特征
2)热塑性变形——表层产生拉伸残余应力,里层产生压缩残 余应力。
原因:切削和磨削过程中,表层的温度比里层高,表层的热膨胀较大;加 工后零件冷却至室温时,表层金属体积的收缩受到里层的牵制。
影响表层残余应力的因素
3)相变引起的体积变化 金相组织的变化引起表层金属的比容增大,则表层金属将产生 压缩残余应力,而里层金属产生拉伸残余应力; 金相组织的变化引起表层金属的比容减小,则表层金属产生拉 伸残余应力,而里层金属产生压缩残余应力 。
• 提高砂轮速度,降低工件转速,减小纵向进给速度——增大单位面 积的磨粒数
影响机械加工表面质量的因素及采取的措施

影响机械加工表面质量的因素及采取的措
施
机械加工表面质量受到多种因素的影响,以下是一些常见因素及采取的措施:
1. 切削参数:
- 切削速度:过高的切削速度可能导致表面粗糙度增加,应根据工件材料和刀具选择适当的切削速度。
- 进给速度:过高的进给速度会增加切削力,可能导致振动和不稳定,影响表面质量,应选择适当的进给速度。
- 切削深度:过大的切削深度可能导致切削力增加和刀具失稳,影响表面质量,应选择适当的切削深度。
2. 刀具选择:
- 刀具材料和涂层:选择适当的刀具材料和涂层,能够提供更好的切削性能和寿命,有利于提高表面质量。
- 刀具尺寸和几何形状:选择合适的刀具尺寸和几何形状,以确保切削稳定性和表面质量。
3. 工件夹持和支撑:
- 夹持方式:选择适当的夹持方式和夹具,确保工件固定稳定,避免振动和变形,有利于提高表面质量。
- 支撑结构:对于柔性或薄壁工件,提供适当的支撑结构,以减少振动和变形,有助于改善表面质量。
4. 切削润滑和冷却:
- 切削润滑剂:使用适当的切削润滑剂,可以减少摩擦和热量,改善切削过程,提高表面质量。
- 冷却剂:使用合适的冷却剂冷却切削区域,防止过热,减少切削力和刀具磨损,有利于提高表面质量。
5. 切削震动和振动控制:
- 刀具和工件的几何匹配:确保刀具和工件的几何匹配,减少切削震动和振动的发生,有助于提高表面质量。
- 切削参数的优化:通过调整切削参数,降低切削震动和振动的发生,有助于改善表面质量。
以上是一些常见的影响机械加工表面质量的因素和采取的措施。
在实际应用中,还需根据具体情况进行综合考虑和调整,以获得满足要求的表面质量。
机械加工表面质量

机械加工表面质量1. 简介机械加工表面质量是机械制造过程中一个重要的质量指标,其直接影响着制品的外观和性能,特别是在涉及到接触表面的机械零件中。
机械加工表面质量的好坏会直接影响到摩擦、磨损、润滑和密封等方面的性能。
因此,对于机械加工表面质量的控制和评估非常重要。
2. 常见的机械加工表面缺陷机械加工表面质量的主要缺陷包括以下几种:2.1 粗糙度粗糙度是表面峰谷的高低起伏程度的度量,它直接影响到接触面的摩擦性能和润滑性能。
通常,粗糙度越小,表面质量越好。
2.2 铁锈机械加工过程中,如果没有采取适当的防护措施,金属表面容易受到空气中的氧气和水蒸气的腐蚀而产生铁锈。
铁锈不仅会损坏表面的光洁度,还会降低金属的强度和耐腐蚀性能。
2.3 划痕和切削工艺痕迹在机械加工过程中,操作不当或切削刀具磨损会导致表面出现划痕和切削工艺痕迹。
这些痕迹会影响零件的密封性能和外观质量。
2.4 焊接瑕疵在焊接过程中,不完全熔化、气孔、裂纹等问题容易导致焊接瑕疵。
焊接瑕疵不仅会降低表面质量,还会影响焊接接头的强度和密封性能。
2.5 水渍机械加工过程中,如果不对工件进行适当的清洗,可能会在表面留下水渍。
水渍不仅会降低表面的光洁度,还会影响涂层的附着力和防腐性能。
3. 表面质量评估为了评估机械加工表面质量,常见的方法包括目测评估和仪器测量两种。
3.1 目测评估目测评估是通过肉眼观察和触摸来对表面质量进行评估。
一般来说,表面光洁度、缺陷的数量和大小以及表面的平整程度可以通过目测进行初步评估,但是目测评估存在主观性较强,缺乏量化数据的问题。
3.2 仪器测量仪器测量可以通过使用专业的测量仪器来获取表面质量的精确数据。
常用的仪器包括三坐标测量仪、表面粗糙度测量仪等。
这些仪器可以对表面的粗糙度、平整度、峰谷高度等参数进行测量,并生成相应的数据报告。
4. 改善机械加工表面质量的方法为了改善机械加工表面质量,可以采取以下几种方法:4.1 选择合适的切削刀具和工艺参数在机械加工中,选择合适的切削刀具和工艺参数是提高表面质量的关键。
机械加工表面质量

第三章机械加工表面质量第一节概述评价零件是否合格的质量指标除了机械加工精度外,还有机械加工表面质量。
机械加工表面质量是指零件经过机械加工后的表面层状态。
探讨和研究机械加工表面,掌握机械加工过程中各种工艺因素对表面质量的影响规律,对于保证和提高产品的质量具有十分重要的意义。
一机械加工表面质量的含义机械加工表面质量又称为表面完整性,其含义包括两个方面的内容:1.表面层的几何形状特征表面层的几何形状特征如图3-1所示,主要由以下几部分组成:⑴表面粗糙度它是指加工表面上较小间距和峰谷所组成的微观几何形状特征,即加工表面的微观几何形状误差,其评定参数主要有轮廓算术平均偏差R a或轮廓微观不平度十点平均高度R z;⑵表面波度它是介于宏观形状误差与微观表面粗糙度之间的周期性形状误差,它主要是由机械加工过程中低频振动引起的,应作为工艺缺陷设法消除。
⑶表面加工纹理它是指表面切削加工刀纹的形状和方向,取决于表面形成过程中所采用的机加工方法及其切削运动的规律。
⑷伤痕它是指在加工表面个别位置上出现的缺陷,如砂眼、气孔、裂痕、划痕等,它们大多随机分布。
2.表面层的物理力学性能表面层的物理力学性能主要指以下三个方面的内容:⑴表面层的加工冷作硬化;⑵表面层金相组织的变化;⑶表面层的残余应力。
二表面质量对零件使用性能的影响1.表面质量对零件耐磨性的影响零件的耐磨性是零件的一项重要性能指标,当摩擦副的材料、润滑条件和加工精度确定之后,零件的表面质量对耐磨性将起着关键性的作用。
由于零件表面存在着表面粗糙度,当两个零件的表面开始接触时,接触部分集中在其波峰的顶部,因此实际接触面积远远小于名义接触面积,并且表面粗糙度越大,实际接触面积越小。
在外力作用下,波峰接触部分将产生很大的压应力。
当两个零件作相对运动时,开始阶段由于接触面积小、压应力大,在接触处的波峰会产生较大的弹性变形、塑性变形及剪切变形,波峰很快被磨平,即使有润滑油存在,也会因为接触点处压应力过大,油膜被破坏而形成干摩擦,导致零件接触表面的磨损加剧。
第七节 机械加工表面质量

3 表面层的残余应力
• 由于切削力和热的综合作用,表面层金属晶格 会发生不同程度的塑性变形或产生金相组织变 化,使表面层产生残余应力。
(三)表面质量的内容
表面粗糙度 表面微观几何 形状特征 表面波度
零件表面质量
表面物理力学 性能的变化 表面层冷作硬化 表面层残余应力 表面层金相组织的变化
二、表面质量对零件使用性能的影响
1.影响切削加工后表面粗糙度的因素
(c)刀尖圆弧半径
• 刀尖圆弧半径增加,从几何因素来看会减小表 面粗糙度值。但会增加切削过程中的挤压,塑 性变形增大,使表面粗糙度值增加。 •
(d)刃倾角
• 增大刃倾角,对降低表面粗糙度有利。因为刃 倾角增大,实际工作前角也随之增大,切削过 程中的金属塑性变形程度随之下降,这会显著 地减轻工艺系统的振动,从而使加工表面的粗 糙度下降。
2.影响磨削加工后表面粗糙度的因素
(4)砂轮材料
• 砂轮材料可分为氧化物系(刚玉)、碳 化物系(碳化硅、碳化硼)和高硬磨料 系(人造金刚石、立方氮化硼)。 • 氧化物系:适于磨削钢类零件 • 碳化物系:磨削铸铁、硬质合金等材料
• 高硬磨料:可获得极小的表面粗糙度值, 但加工成本很高。
2.影响磨削加工后表面粗糙度的因素
(5)砂轮的修整
• 修整工具有单颗粒金刚石笔和金刚石滚轮,也 可用白口铸铁或砂轮来修整,以单颗粒金刚石 笔修整的质量为最好。 • 修整砂轮的纵向进给量愈小,磨削的表面粗糙 度值愈小。
2.影响磨削加工后表面粗糙度的因素
(6)砂轮速度
• 砂轮速度越高,就有可能使表层金属塑性变形 的传播速度大于切削速度,工件材料来不及变 形,致使表层金属的塑性变形减小,磨削表面 的粗糙度值将明显减小。
影响机械加工表面质量的因素及改进措施

影响机械加工表面质量的因素及改进措施
一、影响机械加工表面质量的因素。
1.机床和刀具破损:机床体系及其附件的破损,会影响刀具的正常安
装及运行,从而产生肉眼可见的小硬斑、节肢及拉伤着痕等。
刀具的破损,也会影响机加工表面的质量,表现在高点、拉伤、刀印等方面,增大机加
工表面质量不稳定性及表面粗糙度。
2.刀具磨损:刀具工作经过一段时间,就会变得锋利变尖,从而影响
机械加工表面质量,表现为断刃,切口拉伤等,给进程控制带来更多的困难,增加了失效率。
3.加工环境:通常条件下,温度、湿度、噪声及污染等外界环境因素,会影响机械加工表面质量,表现为减少刀具的硬度,使刀具失去钝化作用,从而影响机械加工表面的质量。
4.加工工艺:在机械加工过程中,不同的加工工艺选择,会影响机械
加工表面的质量,如使用过大的进给量或过长的切削时间,则会使刀具快
速磨损,影响加工表面质量。
二、改善措施。
1.检查机床及刀具:定期检查机床及刀具的破损情况,及时更换破损
的部件,使刀具能够正常工作。
2.控制刀具磨损:合理控制刀具的运行时间,根据不同材料选择合适
的刀具,以满足机械加工工艺要求,并减少刀具的损。
- 1、下载文档前请自行甄别文档内容的完整性,平台不提供额外的编辑、内容补充、找答案等附加服务。
- 2、"仅部分预览"的文档,不可在线预览部分如存在完整性等问题,可反馈申请退款(可完整预览的文档不适用该条件!)。
- 3、如文档侵犯您的权益,请联系客服反馈,我们会尽快为您处理(人工客服工作时间:9:00-18:30)。
由于切屑的崩碎而在加工表面留下许多麻点,使表 面粗糙。
机械加工表面加工质量
(2)切削速度的影响 (3)进给量的影响
加工塑性材料时,切削速度对
表面粗糙度的影响(对积屑瘤和鳞 刺的影响)见如图4-41所示。
此外,切削速度越高,塑性变 形越不充分,表面粗糙度值越小
(1)磨削用量
▪ 砂轮的转速↑ →材料塑性变形↓ → 表面粗
糙度值↓ ;
▪磨削深度↑、工件速度↑ → 塑性变形↑ →表
面粗糙度值↑ ; 为提高磨削效率,通常在开始磨削时采
用较大的径向进给量,而在磨削后期采用较 小的径向进给量或无进给量磨削,以减小表 面粗糙度值。
机械加工表面加工质量
(2)工件材料
•太硬易使磨粒磨钝 →Ra ↑ ; •太软容易堵塞砂轮→Ra ↑ ; •韧性太大,热导率差会使磨
影响显微硬度因素
•塑变引起的冷硬
•金相组织变化引起 的硬度变化
表面物理力学 性能
影响残余应力因素
•冷塑性变形 •热塑性变形 •金相组织变化
影响金相组织变化 因素
•切削热
机械加工表面加工质量
1. 表面层的冷作硬化
(1) 表面层加工硬化的产生
定义:机械加工时,工件表面层金属受到 切削力的作用产生强烈的塑性变形,使晶 格扭曲,晶粒间产生剪切滑移,晶粒被拉 长、纤维化甚至碎化,从而使表面层的强 度和硬度增加,这种现象称为加工硬化, 又称冷作硬化和强化。
机械加工表面加工质量
三、表面层金相组织变化与磨削烧伤
1.表面层金相组织变化与磨削烧伤的产生
切削加工中,由于切削热的作用,在工件的加 工区及其邻近区域产生了一定的温升。
定义:磨削加工时,表面层有很高的温度,当 温度达到相变临界点时,表层金属就发生金相组织 变化,强度和硬度降低、产生残余应力、甚至出现 微观裂纹。这种现象称为磨削烧伤。
机械加工表面加工质量
2.表面质量对零件疲劳强度的影响
(1)表面粗糙度对零件疲劳强度的影响 表面粗糙度越大,抗疲劳破坏的能力越差。 对承受交变载荷零件的疲劳强度影响很大。在交
变载荷作用下,表面粗糙度的凹谷部位容易引起应力 集中,产生疲劳裂纹。
表面粗糙度值越小,表面缺陷越少,工件耐疲劳 性越好;反之,加工表面越粗糙,表面的纹痕越深, 纹底半径越小,其抗疲劳破坏的能力越差。
❖砂轮转速越高,单位时间内通过被磨表面的磨粒数越 多,表面粗糙度值就越小。 ❖工件转速对表面粗糙度值的影响刚好与砂轮转速的影 响相反。工件的转速增大,通过加工表面的磨粒数减少, 因此表面粗糙度值增大。 ❖砂轮的纵向进给量小于砂轮的宽度时,工件表面将被 重叠切削,而被磨次数越多,工件表面粗糙度值就越小。
对滑动零件,可降低其摩擦系数,从而减少发热和功率损
失。
机械加工表面加工质量
表面质量对零件使用性能的影响
对耐磨性影响
粗糙度太大、太小都不耐磨 适度冷硬能提高耐磨性
零件表面质量Байду номын сангаас
对疲劳强度的 影响
粗糙度越大,疲劳强度越差
适度冷硬、残余压应力能提高疲 劳强度
对工作精度的 影响
粗糙度越大、工作精度降低 残余应力越大,工作精度降低
粒早期崩落→Ra ↑ 。
(2)砂轮粒度与硬度
•磨粒太细,砂轮易被磨屑
堵塞,使表面粗糙度值增大, 若导热情况不好,还会烧伤 工件表面。
•砂轮太硬,使表面粗糙度增
大;
•砂轮选得太软,使表面粗糙
度值增大。
机械加工表面加工质量
影响磨削加工表面粗糙度的因素
影响磨削加工表面 粗糙度的因素
砂轮粒度 砂轮修正 砂轮硬度 磨削用量 工件材料性质
(1)砂轮的磨粒
磨粒在砂轮上的分布越 均匀、磨粒越细,刃口的等 高性越好。则砂轮单位面积 上参加磨削的磨粒越多,磨 削表面上的刻痕就越细密均 匀,表面粗糙度值就越小。
机械加工表面加工质量
(2)砂轮修整 (3)磨削用量
砂轮修整除了使砂轮具
有正确的几何形状外,更重 要的是使砂轮工作表面形成 排列整齐而又锐利的微刃 (图4-47)。因此,砂轮修 整的质量对磨削表面的粗糙 度影响很大。
•粒度↓→Ra↓
• 金刚石笔锋利↑,修正导程、
径向进给量↓→ Ra↓
•磨粒等高性↑→Ra↓
•硬度↑→钝化磨粒脱落↓→ Ra↑ •硬度↓→磨粒脱落↑→Ra↑ •硬度合适、自励性好↑→Ra↓
•砂轮V↑→ Ra↓ •ap、工件V↑→ 塑变↑→ Ra↑ •粗磨ap↑→生产率↑ •精磨ap↓→ Ra↓(ap=0光磨)
机械加工表面加工质量
图 切削热在表层金属产生残余拉应力的示意图
机械加工表面加工质量
(2)磨削裂纹的产生
磨削裂纹和残余应力有着十分密切的关系。在磨削 过程中,当工件表面层产生的残余应力超过工件材料的强 度极限时,工件表面就会产生裂纹。磨削裂纹常与烧伤同 时出现。
(3)影响表面残余应力的主要因素
机械加工后工件表面层的残余应力是冷态塑性变形、热 态塑性变形和金相组织变化的综合结果。切削加工时起主要 作用的往往是冷态塑性变形,表面层常产生残余压缩应力。 磨削加工时起主要作用的通常是热态塑性变形或金相组织变 化引起的体积变化,表面层常产生残余拉伸应力。
刀具材料、刃磨质量
•刀具材料强度↑→ Ra↓ •刃磨质量↑→ Ra↓ •冷却、润滑↑→ Ra↓
机械加工表面加工质量
(二)磨削加工表面粗糙度
1、 磨削中影响粗糙度的几何因素
工件的磨削表面是由砂轮上大量磨粒刻划出无数极细 的刻痕形成的,工件单位面积上通过的砂粒数越多,则刻 痕越多,刻痕的等高性越好,表面粗糙度值越小。
机械加工表面加工质量
(1)表面层残余应力的产生
1) 冷态塑变
工件表面受到挤压与摩擦,表层产生伸长塑 变,基体仍处于弹性变形状态。切削后,表层产 生残余压应力,而在里层产生残余拉伸应力。
2) 热态塑变
表层产生残余拉应力,里层产生产生残余压 应力(其原理见图)
3) 金相组织变化
比容大的组织→比容小的组织→体积收缩,产生 拉应力,反之,产生压应力。(密度小,比容大)
切削刃 rε↑、前角↓、后面磨损量VB↑ →表层金属的塑变加剧→冷硬↑
⑵切削用量的影响
切削速度v↑→塑变↓→冷硬↓ f↑→切削力↑→塑变↑→冷硬↑
⑶工件材料性能的影响
材料塑性↑→冷硬↑
机械加工表面加工质量
2. 表面层残余应力
定义: 机械加工中工件表面层组织发生 变化时,在表面层及其与基体材料的交 界处会产生互相平衡的弹性力。这种应 力即为表面层的残余应力。
机械加工表面加工质量
影响切削加工表面粗糙度的因
素
刀具几何形状
•残留面积↓ →Ra↓ •前角↑→ Ra↓ •后角↑→摩擦↓→Ra↓ •刃倾角会影响实际工作前角
影响切削加工表面 粗糙度的因素
切削用量
• v↑→ Ra↓
•f↑→ Ra↑ •ap对Ra影响不大,太小会 打滑,划伤已加工表面
工件材料
•材料塑性↑→ Ra↑ •同样材料晶粒组织大↑→ Ra↑ ,常用正火、调质处理
机械加工表面加工质量
图4-47 砂轮上的磨粒
机械加工表面加工质量
2、 磨削中影响粗糙度的物理因素
磨削速度比一般切削速度高得多,且磨粒大多数是负前角,切
削刃又不锐利,大多数磨粒在磨削过程中只是对被加工表面挤压, 没有切削作用。加工表面在多次挤压下出现沟槽与隆起,又由于磨 削时的高温更加剧了塑性变形,故表面粗糙度值增大。
淬火钢在磨削时,由于磨削条件不同,产生的 磨削烧伤有三种形式。
机械加工表面加工质量
2. 磨削烧伤的三种形式
(8-1) (8-2)
•刀尖圆弧半径rε •主偏角kr、副偏角kr′ •进给量f(图4-40)
机械加工表面加工质量
图4-40 车削、刨削时残留面积高度
机械加工表面加工质量
2、物理力学因素
(1)工件材料的影响
❖韧性材料:工件材料韧性愈好,金属塑性变形愈
大,加工表面愈粗糙。故对中碳钢和低碳钢材料的 工件,为改善切削性能,减小表面粗糙度,常在粗 加工或精加工前安排正火或调质处理。
#2 BORE Matrix
机械加工表面加工质量
缸体缸孔Honing加工表面发生的缺陷分析 (SEM)
#3BORE
机械加工表面加工质量
缸体缸孔Honing加工表面发生的缺陷分析 (SEM)
#4 BORE
机械加工表面加工质量
四、 影响表面层物理力学性能的 主要因素及其控制
影响表面层物理力学性能的主要因素
机械加工表面加工质量
图4-38 表面粗糙度与初期磨损量的关系
机械加工表面加工质量
(2)表面层的冷作硬化对零件耐磨性的影响
➢加工表面的冷作硬化,一般能提高零件的耐磨 性。因为它使磨擦副表面层金属的显微硬度提高, 塑性降低,减少了摩擦副接触部分的弹性变形和 塑性变形。 ➢并非冷作硬化程度越高,耐磨性就越高。这是 因为过分的冷作硬化,将引起金属组织过度“疏 松”,在相对运动中可能会产生金属剥落,在接 触面间形成小颗粒,使零件加速磨损。
机械加工表面加工质量
2020/11/18
机械加工表面加工质量
表面质量的含义(内容)
零件表面质量
表面微观几何 形状特征
表面物理力学 性能的变化
表面粗糙度 表面波度
表面层冷作硬化 表面层残余应力 表面层金相组织的变化
机械加工表面加工质量
二、表面质量对零件使用性能的影响
1.表面质量对零件耐磨性的影响
(1)表面粗糙度对零件耐磨性的影响 ❖ 表面粗糙度太大和太小都不耐磨。如图4-38所示。 ❖表面粗糙度太大,接触表面的实际压强增大,粗糙不平 的凸峰相互咬合、挤裂、切断,故磨损加剧; ❖表面粗糙度太小,也会导致磨损加剧。因为表面太光滑, 存不住润滑油,接触面间不易形成油膜,容易发生分子粘 结而加剧磨损。 ❖表面粗糙度的最佳值与机器零件的工作情况有关,载荷 加大时,磨损曲线向上、向右移动,最佳表面粗糙度值也 随之右移。