锂基润滑脂生产工艺条件选择对润滑脂的影响
2号极压锂基润滑脂密度
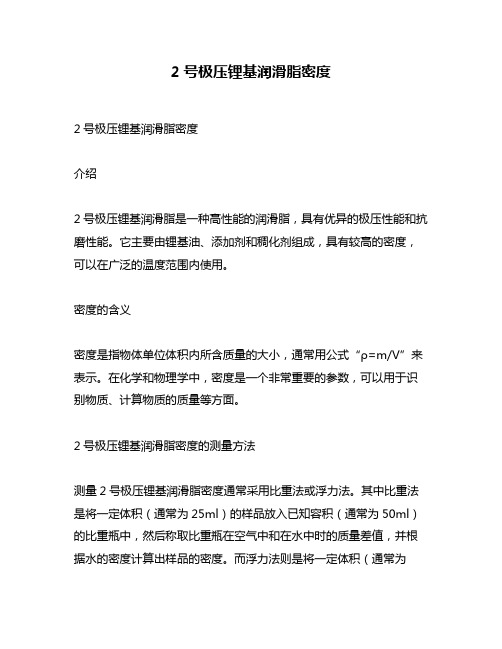
2号极压锂基润滑脂密度2号极压锂基润滑脂密度介绍2号极压锂基润滑脂是一种高性能的润滑脂,具有优异的极压性能和抗磨性能。
它主要由锂基油、添加剂和稠化剂组成,具有较高的密度,可以在广泛的温度范围内使用。
密度的含义密度是指物体单位体积内所含质量的大小,通常用公式“ρ=m/V”来表示。
在化学和物理学中,密度是一个非常重要的参数,可以用于识别物质、计算物质的质量等方面。
2号极压锂基润滑脂密度的测量方法测量2号极压锂基润滑脂密度通常采用比重法或浮力法。
其中比重法是将一定体积(通常为25ml)的样品放入已知容积(通常为50ml)的比重瓶中,然后称取比重瓶在空气中和在水中时的质量差值,并根据水的密度计算出样品的密度。
而浮力法则是将一定体积(通常为100ml)的样品放入已知容积(通常为250ml)的密度瓶中,然后称取密度瓶在空气中和在水中时的质量差值,并根据水的密度计算出样品的密度。
2号极压锂基润滑脂密度的影响因素2号极压锂基润滑脂密度受多种因素影响,主要包括以下几个方面:1. 温度:温度越高,2号极压锂基润滑脂的密度通常会降低。
2. 压力:当压力增加时,2号极压锂基润滑脂的密度也会相应增加。
3. 成分:不同成分的添加剂和稠化剂会对2号极压锂基润滑脂的密度产生影响。
4. 生产工艺:不同生产工艺也会对2号极压锂基润滑脂的密度产生影响。
应用领域由于其优异的性能,2号极压锂基润滑脂广泛应用于各种机械设备、汽车、船舶等领域。
具体包括以下几个方面:1. 工业设备:如轴承、齿轮、链条等机械设备。
2. 汽车:如发动机、变速器、制动系统等。
3. 船舶:如主机、辅机、推进器等。
4. 其他领域:如航空、军工等。
总结2号极压锂基润滑脂密度是其重要的性能指标之一,可以反映其质量和使用性能。
测量2号极压锂基润滑脂密度通常采用比重法或浮力法,受温度、压力、成分和生产工艺等因素的影响。
在各种机械设备、汽车、船舶等领域都有广泛应用。
复合锂基润滑脂生产

复合锂基润滑脂生产
复合锂基润滑脂是一种高性能润滑材料,广泛用于机械设备、汽车、航空航天、工业制造等领域。
其生产包括原材料选用、工艺流程、制备工艺等多个环节。
首先,原材料的选择十分重要。
复合锂基润滑脂的主要成分包括基础油、稠化剂、添加剂等。
其中,基础油应具备良好的润滑、抗氧化、抗磨损等性能;稠化剂应能够使基础油成膏状,提高润滑脂的黏度和极压性能;添加剂包括抗氧化剂、抗磨剂、极压剂、防锈剂等,能够增强润滑脂的性能。
其次,复合锂基润滑脂的制备工艺一般包括混合、加热、冷却、过滤等环节。
具体地,首先将基础油、稠化剂、添加剂等原材料混合均匀,然后加热至一定温度,使稠化剂溶解形成膏状润滑脂。
随后,将润滑脂冷却至室温,并进行过滤,以去除其中的杂质。
复合锂基润滑脂生产中还需要注意一些关键技术,例如加热温度、混合时间、过滤精度等。
此外,生产过程中需要严格控制产品质量,确保润滑脂符合相关标准和要求。
总之,复合锂基润滑脂的生产需要选用优质原材料、采用适当的制备工艺和关键技术,以保证产品的高性能和稳定品质。
- 1 -。
极压锂基润滑脂技术档案

极压锂基润滑脂随着我国对新能源汽车的不断重视,锂基电动汽车成为了市场上的宠儿,同时锂基锂油也是目前最有市场前景的高性能锂基润滑脂之一。
随着锂电池技术不断发展和成熟,其电池性能在逐渐提高。
在新能源汽车用锂基润滑脂方面,由于其使用环境与传统锂蓄电池有很大不同,因此对于高性能锂基润滑脂的要求也是在不断提高。
极压锂基润滑脂(LiFeCore)就是为满足这样一种特殊要求而研制出来的一种新型润滑油。
LiFeCore是由高质量石墨制成的高性能脂状物,其润滑性、热稳定性、导电率等性能均优于传统润滑脂。
极压锂基润滑脂具有较好的粘附性、较低的热分解温度,更高工作温度下不发生凝胶现象,使其使用寿命长达3~5年。
在车辆、电梯等汽车关键设备上得到了广泛应用。
•1.高粘度、高粘度指数和高耐磨性,可在高速运转的齿轮处使用;•LiFeCore最大的优点是不会与金属或其它材料产生反应,因此它在齿轮润滑方面具有非常出色的耐磨性和较低的摩擦系数。
特别是其可在低温下操作,这对齿轮来说是至关重要的。
此外, LiFeCore耐高温,同时具有优良的润滑性能和机械特性,从而能够在恶劣环境中安全、可靠地工作。
LiFeCore是采用石墨为主要原料制成的高性能脂类轴承润滑油,它既有与金属相同的耐高温、低摩擦系数和耐磨性;又具有较好的粘度指数(EI)和高润滑性。
这使得LiFeCore适用于高速运转时轴承传动装置中,例如滚珠丝杠摩擦装置、滚动轴承、螺钉传动装置等。
由于LiFeCore具有良好的润滑性能而且有出色的耐高温性能和极高的力学性能。
它已在高速齿轮传动装置、大型齿轮转子式联轴器中得到了广泛使用。
此外LiFeCore 还可用于滑动轴承中。
••2.良好的粘附性;•LiFeCore采用特殊配方设计,使其具有较好的粘附性。
摩擦系数通过不同的稠度也可以达到相同甚至更高。
LiFeCore粘度越高,粘附性能越好。
LiFeCore与普通润滑脂相比具有如下优点:粘附性大大优于一般润滑脂;LiFeCore具有良好的润滑性,即使油量不足或不流动也不会产生分离;良好的粘附性有助于将油泥等粘附到零部件上去;即使油被密封在润滑剂中也不会发生分离。
影响锂基润滑脂的注脂因素

锂基润滑脂用于机械的摩擦部分,起润滑和密封作用,也用于金属表面,起填充空隙和防锈作用。
以上的知识简单的介绍是为了让大家更好的了解影响该产品的注脂因素的知识。
1、集中润滑:基础油粘度适当、稠度低的锂基润滑脂。
2、温度:产品的滴点应高于设备的工作温度30~50℃。
3、负荷:负荷大时采用基础油粘度大、稠度小的极压产品。
4、滑动轴承用润滑脂:圆周速度小于2m/s,间歇运动和要求对污染物和水分有密封作用,选用特勃仕润滑脂考虑的因素。
5、非集中润滑:基础油粘度不限、稠度大的润滑脂。
6、环境:锂基润滑脂的抗水性及附着性等。
7、轴承材质:轴套为有色金属时,要求润滑脂不能含有S、Cl等活性元素。
在以上的内容介绍中可以得知锂基润滑脂的密封作用和保护作用都比普通的产品好,其大多是半固体状的物质,具有独特的流动性,是大家值得选择的产品。
锂基润滑脂 kdlfedfwe7。
通用锂基润滑脂标准

通用锂基润滑脂标准
通用锂基润滑脂是一种常见的润滑脂,广泛应用于工业设备、汽车、机械设备
等领域。
为了确保通用锂基润滑脂的质量和性能,制定了一系列的标准,以便对其进行评价和监控。
首先,通用锂基润滑脂的标准主要包括以下几个方面,外观、工作稠度、滴点、防水性能、氧化安定性、抗腐蚀性能等。
这些标准旨在确保通用锂基润滑脂在不同工况下能够发挥出良好的润滑作用,延长设备的使用寿命,提高设备的运行效率。
其次,通用锂基润滑脂的外观标准要求其呈现出均匀的光滑质地,无明显的异
物和机械杂质。
这有利于减少摩擦和磨损,保护设备的零部件。
同时,工作稠度标准则规定了在不同温度下的黏度范围,以确保通用锂基润滑脂在各种环境下都能够保持稳定的润滑性能。
此外,通用锂基润滑脂的滴点标准也是非常重要的。
滴点是指润滑脂在加热过
程中,其变稀并开始滴落的温度。
滴点高低直接影响到润滑脂的使用温度范围,因此滴点的标准也是制定通用锂基润滑脂标准的重要内容之一。
除此之外,防水性能、氧化安定性、抗腐蚀性能等标准也是通用锂基润滑脂标
准的重要内容。
这些性能直接关系到通用锂基润滑脂在潮湿、高温、高压等恶劣环境下的稳定性和持久性,对设备的保护起着至关重要的作用。
总的来说,通用锂基润滑脂标准的制定是为了保证其质量和性能,确保其在各
种工况下都能够发挥出良好的润滑效果,从而保护设备,延长设备的使用寿命,提高设备的运行效率。
只有严格按照标准生产和使用通用锂基润滑脂,才能够更好地发挥其作用,为各行各业的生产和运营提供可靠的保障。
润滑脂生产工艺

润滑脂生产工艺一、润滑脂的概述润滑脂是一种常见的润滑剂,广泛应用于工业生产和机械设备维护中。
它主要由基础油、增稠剂和添加剂组成,具有润滑、密封、防腐和减震等功能。
润滑脂生产工艺包括基础油的选择、增稠剂的加工、添加剂的调配和混合、产品包装等环节。
二、基础油的选择基础油是润滑脂的主要成分,其选择对润滑脂的性能有重要影响。
基础油通常采用矿物油、合成油或二者的混合物。
矿物油具有良好的润滑性能和稳定性,但其耐高温、抗氧化和抗腐蚀性能较差。
合成油则具有较高的耐高温性能和抗氧化性能,但成本较高。
在实际生产中,可以根据使用环境和要求选择适当的基础油。
三、增稠剂的加工增稠剂是润滑脂的重要组成部分,用于增加润滑脂的黏度和稠度。
常用的增稠剂有锂基、钠基、钙基、铝基等。
增稠剂的加工过程包括原料的筛选、研磨、混合和加热等环节。
其中研磨是关键步骤,通过研磨可以使增稠剂颗粒细小均匀,提高润滑脂的稳定性和使用寿命。
四、添加剂的调配和混合添加剂是润滑脂的功能性成分,用于改善润滑脂的性能和特性。
常用的添加剂有抗氧化剂、抗腐蚀剂、抗磨剂、极压剂等。
添加剂的调配和混合过程包括原料的称量、加热、搅拌和过滤等环节。
调配时需要根据产品配方和要求,精确控制添加剂的加入量和混合时间,确保产品的质量。
五、产品包装润滑脂生产完成后,需要进行产品包装。
常见的包装方式有胶管、桶装、盒装等。
在包装过程中,需要注意卫生和防止杂质的混入,以确保产品的质量。
包装后的润滑脂需要进行质检,检查产品的外观、黏度、稳定性等指标是否符合要求。
合格的产品可以进行标识和储存,待出厂或销售使用。
六、质量控制润滑脂生产过程中需要进行严格的质量控制,以确保产品的质量稳定。
质量控制包括原辅料的检验、生产过程的监控和产品的质检。
原辅料的检验需要对基础油、增稠剂和添加剂进行化验分析,确定其质量和性能是否符合要求。
生产过程的监控需要对各个环节进行严格控制,确保产品的配比和工艺参数准确可靠。
极压锂基润滑脂执行标准

极压锂基润滑脂执行标准极压锂基润滑脂是一种常用的润滑脂,其执行标准是指对其生产、性能、质量、使用等方面的规定和要求。
以下是关于极压锂基润滑脂执行标准的详细介绍。
一、极压锂基润滑脂的定义和分类极压锂基润滑脂是以锂基油为基础油,加入适量的增稠剂、极压剂、抗氧剂等添加剂制成的一种多功能润滑脂。
根据其用途和性能特点的不同,极压锂基润滑脂可以分为通用型、高温型、低温型和特殊型等多个子类。
二、极压锂基润滑脂的生产标准1.原材料的选择和检验:生产极压锂基润滑脂使用的原材料必须符合国家相关标准,特别是基础油、增稠剂和添加剂的质量和性能指标必须满足要求。
在生产过程中,对原材料进行必要的检验和测试,确保其符合标准要求。
2.生产工艺和设备:极压锂基润滑脂的生产过程需要采用适当的工艺和设备,以确保产品质量稳定。
生产中应注意加热、混合、均质等各个环节的操作参数和工艺要求,避免因生产操作不当导致产品质量问题。
3.检验和测试:在生产过程中,对生产中间产物和最终产品进行必要的检验和测试,以确保产品质量符合标准要求。
对于质量较好的极压锂基润滑脂,还可以进行额外的性能测试,以进一步确认其性能指标。
三、极压锂基润滑脂的性能要求1.抗磨性能:极压锂基润滑脂的抗磨性能是其最基本的性能要求之一。
它应具有良好的润滑性和降低磨损的能力,以提高机械设备的使用寿命。
2.极压性能:极压锂基润滑脂的极压性能是其特色之一。
它应具有良好的负荷承载能力,能在高负荷和冲击负荷下保持润滑性能,以减少设备的磨损和故障。
3.耐温性能:极压锂基润滑脂应具有良好的耐高温和耐低温性能。
在高温环境下,它不应融化和流失,而在低温环境下,它应具有良好的流动性和润滑性能。
4.氧化安定性:极压锂基润滑脂应具有良好的氧化安定性,能在长期使用和高温环境下稳定性能,不会产生过多的沉淀物和酸性物质,以保护设备免受氧化损害。
5.腐蚀防护性能:极压锂基润滑脂应具有良好的腐蚀防护性能,能有效防止设备受到湿度、酸碱和其他有害物质的侵蚀,保护设备表面和内部零部件免受腐蚀。
锂基润滑脂
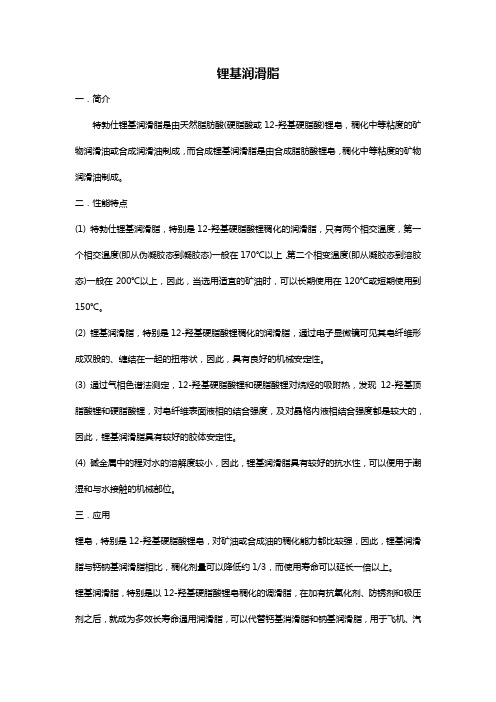
锂基润滑脂一.简介特勃仕锂基润滑脂是由天然脂肪酸(硬脂酸或12-羟基硬脂酸)锂皂,稠化中等粘度的矿物润滑油或合成润滑油制成,而合成锂基润滑脂是由合成脂肪酸锂皂,稠化中等粘度的矿物润滑油制成。
二.性能特点(1) 特勃仕锂基润滑脂,特别是12-羟基硬脂酸锂稠化的润滑脂,只有两个相交温度,第一个相交温度(即从伪凝胶态到凝胶态)一般在170℃以上,第二个相变温度(即从凝胶态到溶胶态)一般在200℃以上,因此,当选用适宜的矿油时,可以长期使用在120℃或短期使用到150℃。
(2) 锂基润滑脂,特别是12-羟基硬脂酸锂稠化的润滑脂,通过电子显微镜可见其皂纤维形成双股的、缠结在一起的扭带状,因此,具有良好的机械安定性。
(3) 通过气相色谱法测定,12-羟基硬脂酸锂和硬脂酸锂对烷烃的吸附热,发现12-羟基顶脂酸锂和硬脂酸锂,对皂纤维表面液相的结合强度,及对晶格内液相结合强度都是较大的,因此,锂基润滑脂具有较好的胶体安定性。
(4) 碱金属中的程对水的溶解度较小,因此,锂基润滑脂具有较好的抗水性,可以便用于潮湿和与水接触的机械部位。
三.应用锂皂,特别是12-羟基硬脂酸锂皂,对矿油或合成油的稠化能力都比较强,因此,锂基润滑脂与钙钠基润滑脂相比,稠化剂量可以降低约1/3,而使用寿命可以延长一倍以上。
锂基润滑脂,特别是以12-羟基硬脂酸锂皂稠化的调滑脂,在加有抗氧化剂、防锈剂和极压剂之后,就成为多效长寿命通用润滑脂,可以代替钙基消滑脂和钠基润滑脂,用于飞机、汽车、坦克、机床和各种机械设备的轴承润滑。
(Ⅰ)通用锂基润滑脂1.简介特勃仕通用锂基脂是由12-羟基硬脂肪酸锂皂稠化中等粘度矿物油,井加人抗氧防锈添加剂制成,按其锥人度分为l、2、3三个牌号。
深圳市特润宝润滑材料有限公司。
2.性能(l)良好的抗水、防锈性能。
可以在潮湿和与水接触的机械部件上使用。
(2)良好的帆械安定性和胶体安定性。
在高速运转的机械剪切作用下,润滑脂不会变稀或流失。
- 1、下载文档前请自行甄别文档内容的完整性,平台不提供额外的编辑、内容补充、找答案等附加服务。
- 2、"仅部分预览"的文档,不可在线预览部分如存在完整性等问题,可反馈申请退款(可完整预览的文档不适用该条件!)。
- 3、如文档侵犯您的权益,请联系客服反馈,我们会尽快为您处理(人工客服工作时间:9:00-18:30)。
锂基润滑脂生产工艺条件选择对润滑脂的影响(一)皂化反应时间的影响在常压釜生产润滑脂的过程中,影响皂化反应效果的因素很多,如反应温度、反应物的浓度、反应时间、投料顺序、反应物相互间接触的情况、机械搅拌的速度、碱类物质的浓度、脂肪或脂肪酸的组成以及基础油的组成等。
由于常压制脂工艺条件的局限性,皂化反应几乎总是不完全的,转化率最高也不超过98%,一般采用延长反应时间来提高反应的转化率,采用压力皂化釜进行皂化反应,皂化转化率可达到99.5%以上。
(二)最高炼制温度的影响如果说皂化反应是制造润滑脂最基本的条件,则最高炼制温度就是制造润滑脂最关键的条件。
润滑脂在炼制过程中纤维结构发生几次相转变过程,特别是在最高炼制温度下皂纤维处于熔融状态,熔融状态的皂纤维基本形成了皂与油的溶胶状态。
在此状态下可采取不同的急冷方式来实现产品不同的性能要求,如果最高炼制温度偏低,则难以实现上述目的;最高炼制温度偏高,虽可实现各种性能要求,但釜内基础油轻组分会大量挥发,而且急剧氧化,影响脂的外观和润滑脂产品质量,同时抗氧剂也易因挥发变质而失去作用。
因此应注意在生产过程中,一方面加快升温速率,以便尽快达到最高炼制温度,同时又要求在达到最高炼制温度后,迅急进入冷却调和工序,使釜内物在最高炼制温度下停留时间尽可能地短。
在锂基润滑脂生产过程中,当温度达到155~175℃时,制脂釜内混合物即由开始加热皂化至熔融,基本上形成了皂与油的溶胶状态。
有些生产厂在此温度下即加急冷油,同时用齿轮泵通过剪切阀打循环使其冷却。
这种工艺所制备的锂基润滑脂的性能较差。
正确的方法是继续升温至最高炼制温度205~210℃左右,使制脂釜内皂一油体系完全呈真溶液状态。
然后进入冷却工序,通过控制冷却速率和方式,以获得最佳锂基润滑脂的皂纤维结构,从而生产出性能优良的锂基润滑脂产品。
为了制备性能优良的锂基润滑脂产品,在生产工艺条件上,采用预留30%一50%的基础油作急冷混合油,使制脂釜内物的温度由最高炼制温度205~210℃降至150~160℃,然后经循环剪切或研磨处理。
这种工艺与常规的操作方法相比,可节省脂肪酸原料。
例如,生产3号锂基润滑脂,含皂量只需要8%~10%,而且产品的机械安定性好,十万次剪切试验的锥入度变化值在25个单位左右。
关键词:润滑,影响,选择,条件,工艺,生产,温度,反应,最高,状态,(三)脂肪材料的影响生产锂基润滑脂时,对脂肪材料的要求比生产其他皂基润滑脂更为严格。
虽然各种脂肪或脂肪酸都可以用来制造锂基润滑脂,但脂肪或脂肪酸的碳链长度与锂基润滑脂的性质(如锂基润滑脂的稠度和胶体安定性)有着密切的关系。
对于正构碳链脂肪酸来说,用短链脂肪酸制备的锂基脂所得的产品析油量大,过长链的脂肪酸制备的锂基脂析油量虽小,但稠化能力很低。
一般认为用十八碳和十六碳的混合酸以及以十八碳为主的12一羟基硬脂酸、氢化蓖麻油作为锂基润滑脂的脂肪原料最为适宜。
单独使用硬脂酸生产锂基润滑脂时,硬脂酸的质量对成品锂基润滑脂性质有很大影响。
当硬脂酸的碘值(脂肪酸饱和程度小)增大时,锂基润滑脂的色泽加深;当硬脂酸内含油酸量较多时,制备的锂皂稠化能力较低,润滑脂的机械安定性较差。
但微量不饱和酸的存在,可使成品润滑脂氧化安定性和胶体安定性稍好。
单独使用氢化蓖麻油锂皂生产锂基润滑脂时,稠化能力较低,制得的成品锂基润滑脂的滴点较低,胶体安定性和防护性较差。
因而目前一般不用它作锂基润滑脂的脂肪原料。
单独使用12一羟基硬脂酸锂皂生产锂基润滑脂时,锂皂的稠化能力较强,其机械安定性要比单独用硬脂酸的制品好得多,但胶体安定性较差。
试验证明,用12一羟基硬脂酸和硬脂酸按一定比例(如8:2至6:4)混合生产的锂基润滑脂,则能兼顾到稠化能力、胶体安定性和机械安定性。
(四)基础油和添加剂的影响基础油的粘度对成品锂基润滑脂的性质影响较大。
用硬脂酸锂皂制备的锂基润滑脂,如采用石蜡基润滑油作基础油时,产品安定性较好;当采用环烷基润滑油作基础油时,产品的稠度大于石蜡基基础油制备的产品,胶体安定性也较好。
如若采用环烷基和石蜡基按一定比例混合的润滑油作基础油,制备的锂基润滑脂的理化性质更为满意。
一般来说,锂皂的稠化能力对于基础油的粘度有最佳值(一般落在中粘度范围)。
低于或高于此粘度最佳值时,所得润滑脂的稠度较小,滴点降低。
此外,低粘度基础油制备的锂基润滑脂容易分油。
与其他类型皂基润滑脂一样,锂皂是以皂纤维结构的形态分散在基础油内,随着生产工艺的不同,各种不同脂肪酸的锂基润滑脂皂纤维结构的形状和大小会发生改变。
通常,如采用不饱和脂肪酸为原料时(如油酸等),则得到长纤维结构的锂基润滑脂;当采用饱和脂肪酸(如硬脂酸)时,即得到短纤维结构锂基润滑脂;采用12一羟基硬脂酸时,锂基润滑脂的结构是扭带状纤维结构。
如将硬脂酸1.2%、12一羟基硬脂酸4.8%、氢氧化锂0.96%、二苯胺0.3%和10号汽油机油92.7%制成的锂基润滑脂,用电子显微镜观察,可以看到锂基润滑脂是一种扭带状纤维结构。
由于锂皂对基础油具有氧化催化作用,故生产锂基润滑脂时要选择合适的原料。
例如脂肪酸内的不饱和组分要越少越好,金属锂盐的纯度要高等。
如果锂盐内含铁,即使是痕迹,其氧化催化作用仍很明显,能加速基础油的氧化。
若含不纯物,如Na’、K’、s暖一、cl一等离子,会加速分油、降低锂基润滑脂稠度及抗水性。
润滑油的过度精制会减少天然抗氧组分,也是不利的。
由于上述原因,在生产锂基润滑脂时,必须添加抗氧剂,如苯二胺、二苯胺、苯基一。
一萘胺等,用量在0.1%~0.5%之间。
这些抗氧剂一般均为极性物质,加在润滑脂内均能起正或负的结构稳定剂作用。
在选择添加剂的种类和确定用量时,应考虑到对润滑脂胶体结构的影响。
为了提高锂基润滑脂的抗氧化性和防锈性,可添加防锈剂石油磺酸钡和亚硝酸钠以及抗氧剂苯基一a一萘胺0.5%和环烷酸2%。
制成的锂基润滑脂对黑色金属和有色金属都具有防锈性。
锂基润滑脂中加入防锈剂石油磺酸钡,会使稠化能力下降,但机械安定性较好。
若加入亚硝酸钠,易使锂基润滑脂的胶体安定性下降,分油增大。
当采用石蜡基原油生产的基础油制备锂基润滑脂时,在组成中添加少量环烷酸(一般为润滑脂的1.5%~2%)。
对其结构有明显改善作用,尤其对改善润滑脂的胶体安定性更有效果。
这是由于生成的环烷酸锂皂本身也有稠化剂作用,同时赋予基础油具有类似环烷基原油基础油那样的皂一油分散特性,除此以外,采用其他皂类作为结构改善剂(如添加硬脂酸铅皂)后,可增加稠化能力,这可能是由于锂皂和铅皂生成共晶体之故。
(五)冷却方式及条件的影响锂基润滑脂生产过程中的冷却方式及条件对锂基润滑脂性质的影响非常明显。
冷却条件不同,锂基润滑脂的皂纤维结构(皂纤维的形状及长径比)也不同,制备的润滑脂产品性质也会有所差异,因此,可以通过控制冷却方式和条件生产稠化能力高、胶体安定性和机械安定性都好的锂基润滑脂。
总的说来,当锂基润滑脂配方(组成)确定后,锂基润滑脂皂纤维的长宽比及形状决定了锂基润滑脂的某些性质。
具有较长纤维结构的锂基润滑脂,具有好的机械安定性能;较短纤维结构的锂基润滑脂,则具有好的胶体安定性能。
因此,除非增加皂量,否则要使润滑脂同时具有上述两种性能,是有一定矛盾的。
实际上,同时含有粗、细两种纤维结构的锂基润滑脂,其剪切安定性和胶体安定性大体上相当于二者的平均值。
关于这方面的研究已有报道,先分别取两种锂基润滑脂,一种是皂结晶处于安定状态的短纤维脂(纤维长度l~10um,长宽比17~26);另一种是皂结晶处于介安状态的微纤维脂(纤维长度小于lum,长宽比5—15)。
然后将二者混合,所得产品的机械安定性可优于混合前的二者,而胶体安定性几乎等于微纤维脂的产品。
上述两种脂在相状态方面的差别用显微镜不易发现,但用热差分析法是容易分辨出来的。
为了制取短纤维结构锂基润滑脂,可将l/3量的基础油与氢化蓖麻油混合。
再用当量氢氧化锂皂化后升温脱水,使皂完全溶解。
然后在相转变温度(182—205)下保持1h以上(最好2~3h),再加入剩余的2/3基础油。
同时,慢慢冷却至约94~135℃时进行研磨。
为了制备微细纤维结构的锂基润滑脂,将1/3量的基础油与12一羟基硬脂酸混合,与当量氢氧化锂皂化后升温脱水,当温度升至150度后,再加入其剩余的2/3的基础油,然后升温到193℃(最好205℃),使皂全部溶解,最后,使之快冷,最好在几秒钟内通过相转变温度而降至38~65℃,为此目的可采用冷却鼓。
然后经研磨均化、脱气得产品。
将制备的两种锂基润滑脂按1:3到3:l之间比例混合。
混合后,在65~93℃下慢慢搅拌约O.5h或更长时间。
再经研磨即得最终产品。
该产品具有较好的机械安定性和较好的胶体安定性。
此方法的优点是,仅用一般设备就可以进行生产。
由此可见,锂基润滑脂的胶体安定性及机械安定性不仅受皂含量的影响,而且也受锂皂纤维的形状和大小的影响。
这种皂纤维形状和大小的生成条件,是受制脂工艺中冷却速率控制的。
静置快速冷却,生成的皂纤维较小,比表面积大,因此润滑脂的稠度大,分油少,但机械安定性较差。
反之,慢冷则生成的皂纤维较大,比表面积小,润滑脂的稠度较小,分油量较大,而机械安定性较好。
所以,要获得胶体安定性和机械安定性都满意的产品,除了调节皂含量外,还应严格控制冷却条件。
(急冷混合温度低生成短纤维结构)(六)研磨条件对产品性质的影响研磨是润滑脂生产的最后加工工序,也是非常关键的工序。
润滑脂生产,特别是锂基润滑脂生产,不经研磨是不能直接使用的。
研磨不仅可以改善润滑脂的外观,更主要的是可以将胶体安定性和机械安定性稳定在最适宜程度上,使其具有理想的使用性能。