挤出吹膜-重点难点.
挤出吹膜技术讲座4

第一章挤出吹塑薄膜成型工艺1、挤出成型工艺参数1)挤出机部位工艺参数挤出机工艺参数主要指料筒温度、螺杆转速、运行电流等。
a、料筒温度温度是挤出成型工艺要素中的第一要素。
挤出机的加热一般都是电加热,通常采用铸铝电阻加热器。
控制采用热电偶温度传感器、辐射高温测量仪、电阻温度传感器、数字温度控制仪表料筒温控模式:从加料口到料筒末端,温度逐渐升高。
靠近加料口的第一段应低于原料的软化温度;料筒出口处温度应低于原料的分解温度;中间段温度逐渐升高;b、料筒压力一般不用控制,当熔料进入机头,测定机头压力;c、料筒内料流阻力的大小通过螺杆扭矩即力矩显示;塑料熔体黏度大,力矩大;一旦扭矩过大,有可能折断螺杆;d、螺杆转速的选择直接影响制品产量;过低,降低了产量;过快,则会影响塑化质量;开始启动转速应先慢后快;2)辅机工艺参数a、吹胀比:是指吹胀后管泡的直径与机头口模直径(薄膜的规格与机头大小)之比。
通常设定为1.5-3;恒定的吹胀比要求压缩空气必须保持稳定;b、拉伸比(牵引比):是指牵引速率(牵引辊的表面线速度)与挤出速率(熔体离开口模的线速度)之比。
牵引比通常控制在4-10;c、模口间隙:是指口模缝隙的宽度。
通常设定为0.8-1.2mm;关系:牵引比=模口间隙/(薄膜厚度×吹胀比)在实际生产中三种参数相互关联,应做综合调整3)环境工艺参数挤出生产线的环境要求如下:a、周围介质温度不超过40℃,不低于-20 ℃;b、空气相对湿度不大于85%;c、没有导电尘埃及破坏金属绝缘的腐蚀性气体;d、避免振动和颠簸;e、车间空气流通均匀;f、环境清洁,无虫蝇;第二章吹膜质量标准1、外观要求:塑化良好,无明显“水纹”和“云雾”;表面应当平整光滑,无皱折或仅有少量的活褶;不允许有气泡、穿孔及破裂现象;不允许有严重的挂料线和丝纹存在;不允许出现表面划痕和污染;色母料分布均匀,遮光率好;鱼眼和僵块(个/㎡) >2mm(不允许) 0.6-2mm(≤15)分散度(个/10cm×10cm) ≤5;杂质(个/㎡) >0.6mm (不允许) 0.3-0.6mm (≤4)分散度(个/10cm×10cm) ≤2;2、规格尺寸要求:1)宽度偏差:极限偏差≤±5mm;2)厚度偏差:极限偏差%≤±8,平均偏差% ≤±6;3、电晕要求:复合面电晕处理值≥38达因,整卷一致、无缺失;4、标注要求:采用有色胶带,并在端面夹放明显标记,注明原因;5、标示要求:严格执行质量跟踪卡,如实记录生产班组、生产日期、米数、厚度、宽度、电晕处理面、重量、次品位置、次品长度与原因。
吹膜工艺及常问题的分析解决
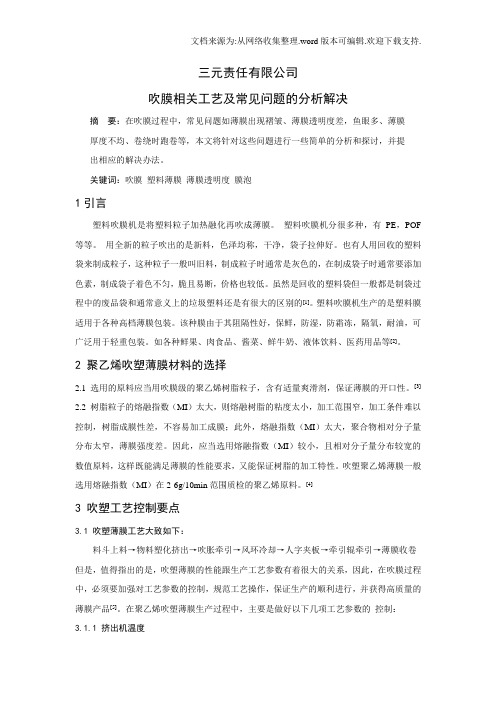
三元责任有限公司吹膜相关工艺及常见问题的分析解决摘要:在吹膜过程中,常见问题如薄膜出现褶皱、薄膜透明度差,鱼眼多、薄膜厚度不均、卷绕时跑卷等,本文将针对这些问题进行一些简单的分析和探讨,并提出相应的解决办法。
关键词:吹膜塑料薄膜薄膜透明度膜泡1引言塑料吹膜机是将塑料粒子加热融化再吹成薄膜。
塑料吹膜机分很多种,有PE,POF 等等。
用全新的粒子吹出的是新料,色泽均称,干净,袋子拉伸好。
也有人用回收的塑料袋来制成粒子,这种粒子一般叫旧料,制成粒子时通常是灰色的,在制成袋子时通常要添加色素,制成袋子着色不匀,脆且易断,价格也较低。
虽然是回收的塑料袋但一般都是制袋过程中的废品袋和通常意义上的垃圾塑料还是有很大的区别的[1]。
塑料吹膜机生产的是塑料膜适用于各种高档薄膜包装。
该种膜由于其阻隔性好,保鲜,防湿,防霜冻,隔氧,耐油,可广泛用于轻重包装。
如各种鲜果、肉食品、酱菜、鲜牛奶、液体饮料、医药用品等[2]。
2 聚乙烯吹塑薄膜材料的选择2.1 选用的原料应当用吹膜级的聚乙烯树脂粒子,含有适量爽滑剂,保证薄膜的开口性。
[3] 2.2 树脂粒子的熔融指数(MI)太大,则熔融树脂的粘度太小,加工范围窄,加工条件难以控制,树脂成膜性差,不容易加工成膜;此外,熔融指数(MI)太大,聚合物相对分子量分布太窄,薄膜强度差。
因此,应当选用熔融指数(MI)较小,且相对分子量分布较宽的数值原料,这样既能满足薄膜的性能要求,又能保证树脂的加工特性。
吹塑聚乙烯薄膜一般选用熔融指数(MI)在2-6g/10min范围质检的聚乙烯原料。
[4]3 吹塑工艺控制要点3.1 吹塑薄膜工艺大致如下:料斗上料→物料塑化挤出→吹胀牵引→风环冷却→人字夹板→牵引辊牵引→薄膜收卷但是,值得指出的是,吹塑薄膜的性能跟生产工艺参数有着很大的关系,因此,在吹膜过程中,必须要加强对工艺参数的控制,规范工艺操作,保证生产的顺利进行,并获得高质量的薄膜产品[5]。
挤出成型—吹塑薄膜挤出工艺实例(高分子成型课件)

八、挤出吹塑薄膜成型实例
(三)吹塑薄膜主要设备 4 牵引装置——起稳泡,展平,冷却,牵引作用
(1)人字板
夹板式
①使吹胀的膜管稳定地导入牵引辊; ②逐渐将圆筒形的薄膜折叠成平面状; ③导辊式人字板进一步冷却薄膜作用。 人字板夹角可用螺钉调节,一般为10-40度
(2)牵引辊(装置)
将压扁的薄膜压紧并送至卷取设备,防止膜管内空气漏 出,保证膜泡形状尺寸稳定。
八、挤出吹塑薄膜成型实例
(四)LDPE吹塑操作规程及工艺要点
1 操作规程
①加热:加热到规定的温度并保温一段时间; ②加料及挤出:启动挤出机,并让螺杆维持低速转动; ③提料:将通过机头的熔融物料汇集在一起,并将其提起,同 时通入少量的空气,以防相互粘结; ④喂辊:慢速将提起的管泡喂入压辊(牵引辊),再依次通过 导辊送至卷取装置; ⑤充气:向管泡充入压缩空气,直至膜泡直径达到要求为止; ⑥调整:可通过调节口模间隙、冷却风环的风量、牵引速度来 调整膜的厚薄公差;薄膜的幅宽公差主要通过充气吹胀的大小 来调节。
中心进料的“十字型” 旋转式机头
八、挤出吹塑薄膜成型实例
(三)吹塑薄膜主要设备 3 冷却装置
对风环的有关要求:
ü距机头30~100mm,直径增加时选 大值;
ü内径比口模大150~300mm,口径大 选大值;
ü气流以均匀的速度吹向管泡;不均匀 的出风量导致管泡冷却快慢不一并造 成薄膜厚度不均;
ü风环出风口的间隙为1~4 mm并可 调节风量;
八、挤出吹塑薄膜成型实例
(五)吹膜质量常见问题分析解决
3 薄膜鱼眼多 (1)鱼眼的形成原因
鱼眼主要是原料中的添加剂、低分子量树脂及粉尘等,在加工中 凝结在口模上,累积一定数量后被膜不断带走,从而在膜上形成 鱼眼。
吹膜常见问题
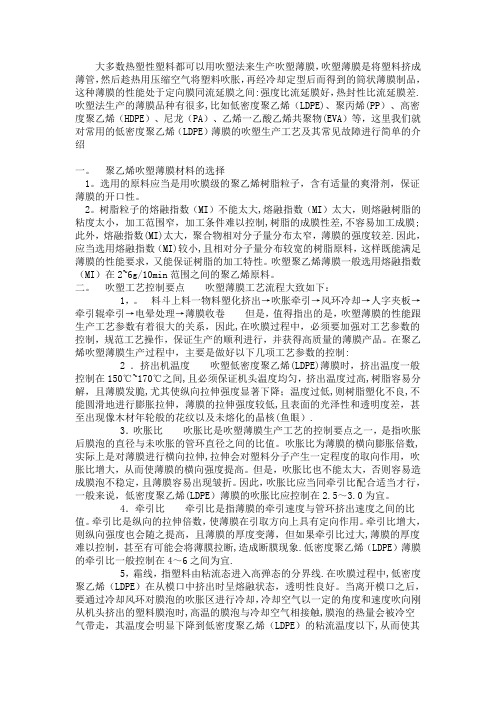
大多数热塑性塑料都可以用吹塑法来生产吹塑薄膜,吹塑薄膜是将塑料挤成薄管,然后趁热用压缩空气将塑料吹胀,再经冷却定型后而得到的筒状薄膜制品,这种薄膜的性能处于定向膜同流延膜之间:强度比流延膜好,热封性比流延膜差.吹塑法生产的薄膜品种有很多,比如低密度聚乙烯(LDPE)、聚丙烯(PP)、高密度聚乙烯(HDPE)、尼龙(PA)、乙烯一乙酸乙烯共聚物(EVA)等,这里我们就对常用的低密度聚乙烯(LDPE)薄膜的吹塑生产工艺及其常见故障进行简单的介绍一。
聚乙烯吹塑薄膜材料的选择1。
选用的原料应当是用吹膜级的聚乙烯树脂粒子,含有适量的爽滑剂,保证薄膜的开口性。
2。
树脂粒子的熔融指数(MI)不能太大,熔融指数(MI)太大,则熔融树脂的粘度太小,加工范围窄,加工条件难以控制,树脂的成膜性差,不容易加工成膜;此外,熔融指数(MI)太大,聚合物相对分子量分布太窄,薄膜的强度较差.因此,应当选用熔融指数(MI)较小,且相对分子量分布较宽的树脂原料,这样既能满足薄膜的性能要求,又能保证树脂的加工特性。
吹塑聚乙烯薄膜一般选用熔融指数(MI)在2~6g/10min范围之间的聚乙烯原料。
二。
吹塑工艺控制要点吹塑薄膜工艺流程大致如下:1,。
料斗上料一物料塑化挤出→吹胀牵引→风环冷却→人字夹板→牵引辊牵引→电晕处理→薄膜收卷但是,值得指出的是,吹塑薄膜的性能跟生产工艺参数有着很大的关系,因此,在吹膜过程中,必须要加强对工艺参数的控制,规范工艺操作,保证生产的顺利进行,并获得高质量的薄膜产品。
在聚乙烯吹塑薄膜生产过程中,主要是做好以下几项工艺参数的控制:2 .挤出机温度吹塑低密度聚乙烯(LDPE)薄膜时,挤出温度一般控制在150℃~170℃之间,且必须保证机头温度均匀,挤出温度过高,树脂容易分解,且薄膜发脆,尤其使纵向拉伸强度显著下降;温度过低,则树脂塑化不良,不能圆滑地进行膨胀拉伸,薄膜的拉伸强度较低,且表面的光泽性和透明度差,甚至出现像木材年轮般的花纹以及未熔化的晶核(鱼眼).3.吹胀比吹胀比是吹塑薄膜生产工艺的控制要点之一,是指吹胀后膜泡的直径与未吹胀的管环直径之间的比值。
(整理)聚乙烯LDPE吹塑薄膜生产过程中的问题和解决方法
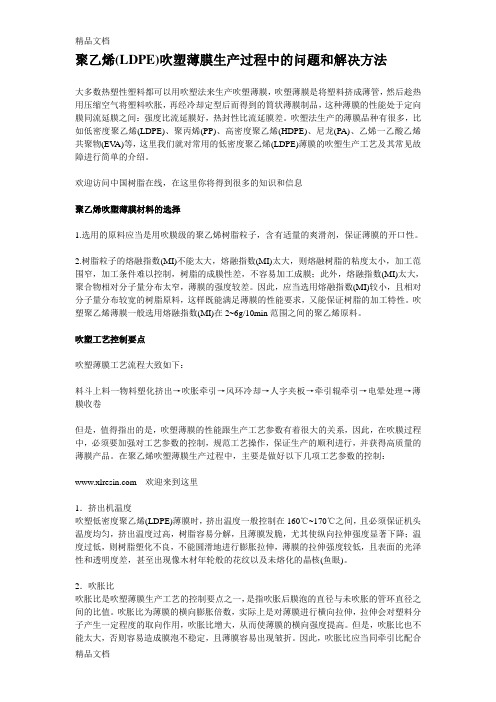
7.薄膜的厚度偏薄
故障原因:
①模口间隙偏小,阻力太大,因此薄膜厚度偏薄;
②冷却风环的风量太小,薄膜冷却太慢;
③牵引速度太快,薄膜拉伸过度,从而使厚度变薄。
解决办法:
①调整模口间隙;
②适当增大风环的风量,加快薄膜的冷却;
中国树脂在线永远是公益的网站!
③适当降低牵引速度。
8.薄膜的热封性差
吹塑工艺控制要点
吹塑薄膜工艺流程大致如下:
料斗上料一物料塑化挤出→吹胀牵引→风环冷却→人字夹板→牵引辊牵引→电晕处理→薄膜收卷
但是,值得指出的是,吹塑薄膜的性能跟生产工艺参数有着很大的关系,因此,在吹膜过程中,必须要加强对工艺参数的控制,规范工艺操作,保证生产的顺利进行,并获得高质量的薄膜产品。在聚乙烯吹塑薄膜生产过程中,主要是做好以下几项工艺参数的控制:
低密度聚乙烯(LDPE)吹塑薄膜常见故障及解决方法
1.薄膜太粘,开口性差
故障原因:
①树脂原料型号不对,不是吹膜级的低密度聚乙烯树脂粒子,其中不含开口剂或者开口剂的含量偏低;
②熔融树脂的温度太高,流动性太大;
③吹胀比太大,造成薄膜的开口性变差;
④冷却速度太慢,薄膜冷却不足,在牵引辊压力的作用下发生相互粘结;
基本性能的技术要求
1.规格及偏差
聚乙烯薄膜的宽度、厚度应当符合要求,薄膜薄厚均匀,横、纵向的厚度偏差小,且偏差分布比较均匀。
2.外观
要求聚乙烯薄膜塑化良好,无明显的"水纹"和"云雾";薄膜的表面应当平整光滑,无皱折或仅有少量的活褶;不允许有气泡、穿孔及破裂现象;无明显的黑点、杂质,晶点和僵块;不允许有严重的挂料线和丝纹存在。
②模口温度分布不均匀,有高有低,从而使吹塑后的薄膜薄厚不均;
吹膜常见问题

大多数热塑性塑料都可以用吹塑法来生产吹塑薄膜,吹塑薄膜是将塑料挤成薄管,然后趁热用压缩空气将塑料吹胀,再经冷却定型后而得到的筒状薄膜制品,这种薄膜的性能处于定向膜同流延膜之间:强度比流延膜好,热封性比流延膜差。
吹塑法生产的薄膜品种有很多,比如低密度聚乙烯(LDPE)、聚丙烯(PP)、高密度聚乙烯(HDPE)、尼龙(PA)、乙烯一乙酸乙烯共聚物(EVA)等,这里我们就对常用的低密度聚乙烯(LDPE)薄膜的吹塑生产工艺及其常见故障进行简单的介绍一。
聚乙烯吹塑薄膜材料的选择??1.选用的原料应当是用吹膜级的聚乙烯树脂粒子,含有适量的爽滑剂,保证薄膜的开口性。
2.指数二。
→在 2 之345在从模口中挤出时呈熔融状态,透明性良好。
当离开模口之后,要通过冷却风环对膜泡的吹胀区进行冷却,冷却空气以一定的角度和速度吹向刚从机头挤出的塑料膜泡时,高温的膜泡与冷却空气相接触,膜泡的热量会被冷空气带走,其温度会明显下降到低密度聚乙烯(LDPE)的粘流温度以下,从而使其冷却固化且变得模糊不清了。
在吹塑膜泡上我们可以看到一条透明和模糊之间的分界线,这就是霜线。
在吹膜过程中,霜线的高低对薄膜性能有一定的影响。
如果霜线高,位于吹胀后的膜泡的上方,则薄膜的吹胀是在液态下进行的,吹胀仅使薄膜变薄,而分子不受到拉伸取向,这时的吹胀膜性能接近于流延膜。
相反,如果霜线比较低,则吹胀是在固态下进行的,此时塑料处于高弹态下,吹胀就如同横向拉伸一样,使分子发生取向作用,从而使吹胀膜的性能接近于定向膜。
三。
基本性能的技术要求1.规格及偏差聚乙烯薄膜的宽度、厚度应当符合要求,薄膜薄厚均匀,横、纵向的厚度偏差小,且偏差分布比较均匀。
2.外观要求聚乙烯薄膜塑化良好,无明显的水纹和云雾;;薄膜的表面应当平整光滑,无皱折或仅有少量的活褶;不允许有气泡、穿孔及破裂现象;无明显的黑点、杂质,晶点和僵块;不允许有严重的挂料线和丝纹存在。
3.物理机械性能由于吹塑后的聚乙烯薄膜用于印刷或者复合加工工艺时,要受到机械力的作用,因此,要求聚乙烯薄膜的物理机械性能应当优良,主要包括拉伸强度、断裂伸长率、撕裂强度等几项指标应当符合标准。
吹膜挤出技术故障诊断!如果你做薄膜,这些必须懂!

吹膜挤出技术故障诊断!如果你做薄膜,这些必须懂!挤出问题这一篇探讨排除吹膜过程中常遇到的各种故障的方法。
这部分内容主要针对挤出机进行探讨。
挤出机问题对于挤出效益,制品尺寸及质量的影响是重大的,值得深入研究。
干货集中,文字比较多。
请耐心看~如果觉得有用,请点赞转发。
NO1、挤出波动挤出波动是指熔体经过模头挤出的质量流率随时间变化过大,姑且说是挤出波动。
这种情况下可以观察到料筒前端压力即网前压力有比较大的快速的波动。
有时候也能观察到电机电流的瞬时波动很大。
熔体压力波动可以达到±15%甚至更大,而且是随机的。
压力波动上下限出现的周期在几秒到几十秒不等。
挤出波动区别于螺杆跳动。
螺杆跳动造成的模头压力波动通常小于±10%且与螺杆转动周期相匹配。
螺杆跳动产生的挤出脉冲会受到多孔板和模头背压的平抑。
挤出波动带来的是薄膜纵向厚薄偏差。
挤出波动有两个主要的原因:喂料不稳定和熔融不稳定。
喂料不稳定产生的波动沿着螺杆进入模头进行传递。
在一个有效的挤出系统内,固体颗粒与机筒摩擦较大并受到螺棱推动往前输送,与螺槽底部相对滑动。
固体输送的关键因素是固体料与机筒内壁摩擦系数与螺杆摩擦系数之比。
比值越大,固体输送越高效。
如果螺杆温度高,表面未清理干净或者有损伤,则使得物料容易粘附在螺杆上从而增大螺杆摩擦系数。
另外,固体形态差异大,比如固体原料含有粉状物料,会导致其熔融速率差异较大,颗粒小的原料较早熔融并粘附在螺杆上从而增大螺杆摩擦系数。
不管什么原因,只要有原料粘附在螺杆上,其输送就会暂停直到粘附的物料后端产生足够大的压力推动其运动进入螺槽前端。
对于吹膜挤出,尤其是聚乙烯,解决喂料量不稳定问题的最好办法是使用开槽机筒。
这项技术极大提高了料筒与原料的摩擦,提高喂料稳定性并提高了挤出机整体的挤出量。
另一个使喂料稳定的方法是保持螺杆表面光滑并使用颗粒形状一致的原料。
螺杆表面干净不黏料,如果进行抛光电镀降低摩擦系数,那效果就更好了。
塑料薄膜的挤出吹塑成型 薄膜平挤上吹成型工艺控制要点
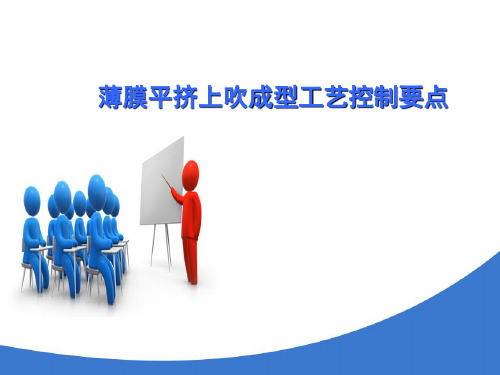
吹胀比越大,薄膜的光学性能
越好,这是因为在熔融树脂中,包 括那些塑化较差的不规则料流可以 纵横延伸,使薄膜平滑所致。图示 意表示吹胀比对薄膜雾度的影响。 吹胀比的增加,还可以提高冲击强 度。
薄膜种类 PVC
吹胀比 2.0~ 3.0
LDPE
2பைடு நூலகம்0~ 3.0
LLDPE
1.5~ 2.0
HDPE(超 薄)
• (3)拉伸比 • 吹塑薄膜的拉伸比是薄膜牵引速度与管坯挤出速
度的比值,实际是薄膜在纵向被拉伸的倍数。拉 伸比使薄膜在引膜方向上具有取向作用,增大拉 伸比,薄膜的纵向强度随之提高。但拉伸比不能 太大,否则难以控制厚薄均匀度,甚至有可能将 薄膜拉断。一般拉伸比为4~6。 • 牵引速度即薄膜牵引辊的转动线速度。管坯挤出 速度可用单位时间挤出的树脂体积除以口模间隙 的截面积求得。 • 当加快牵引速度时,从模口出来的熔融树脂的不 规则料流,在冷却固化前,不能得到充分缓和, 故光学性能较差,如图所示。即使增加挤出速度, 也不能避免薄膜透明度的下降。
吹塑薄膜的挤出温度范围(℃)
薄膜品种
料筒
连接器
机头
聚氯乙烯 (粉料)
高速吹膜 热收缩薄膜
160~175 170~185
170~180 180~190
185~190 190~195
聚乙烯
130~160 160~170 150~160
聚丙烯
190~250 240~250 230~240
复合薄膜
聚乙烯
120~170 210~220
薄膜平挤上吹成型工艺控制要点
薄膜平挤上吹成型工艺控制要点
一.温度控制 二.吹胀比 三.拉伸比 四.薄膜冷却
一. 温度控制
- 1、下载文档前请自行甄别文档内容的完整性,平台不提供额外的编辑、内容补充、找答案等附加服务。
- 2、"仅部分预览"的文档,不可在线预览部分如存在完整性等问题,可反馈申请退款(可完整预览的文档不适用该条件!)。
- 3、如文档侵犯您的权益,请联系客服反馈,我们会尽快为您处理(人工客服工作时间:9:00-18:30)。
序号
单元名称
重点
难点
1
挤出薄膜生产概况
塑料薄膜的性能要求:渗透性能、力学性能、卫生性能及其他性能,薄膜的后处理
塑料薄膜的生产方式与特点:挤出成型(挤出吹塑、流延、双向拉伸)、压延成型
吹塑薄膜的成型方法(平挤上吹、平挤下吹、平挤平吹)与适用场合
渗透性能、电晕、真空镀铝
2
吹塑薄膜机头结构
常见问题分析
成型工艺参数(温度、吹胀比与拉伸比、薄膜冷却)的控制,常见问题分析
5
聚乙烯吹塑膜
LDPE、LLDPE、HDPE吹塑薄膜的品种与原料选择
挤出机与口模结构
工艺条件控制,膜泡形状和冷却定型,
HDPE吹塑薄膜
工艺条件控制
6
共挤吹塑薄膜
多层复合薄膜的性能与用途
共挤吹塑薄膜的设备与工作原理:共挤机头、IBC内冷系统、旋转牵引系统
双向拉伸薄膜生产工艺流程,双向拉伸薄膜的原料性能和应用
双向拉伸薄膜生产线,纵向拉伸与横向拉伸机的组成
双向拉伸薄膜成型工艺,拉伸温度与拉伸比的控制
其它特殊薄膜
挤出厚片的冷却、预热、拉伸、热定型各段温度的控制
3
挤出吹塑薄膜辅机
挤出吹塑薄膜辅机的构成,
吹塑薄膜冷却装置(普通风环、双风口减压风环、自动风环,水环,内冷装置)、牵引装置(人字板、牵引)、卷取装置(中心卷取、表面卷取)的结构及对薄膜生产与薄膜质量的影响
双风口减压风环、自动风环、内冷装置的结构与工作原理
4
吹塑薄膜成型工艺控制
成型工艺流程与操作程序
成型工艺参数的控制:温度、吹胀比与拉伸比、薄膜冷却的控制
共挤吹膜成型工艺控制要点
共挤机头、IBC内冷系统、旋转牵引系统的结构
7ቤተ መጻሕፍቲ ባይዱ
流延薄膜
挤出流延薄膜的生产工艺过程,流延膜的性能
流延膜设备及工作原理:挤出机选择与安装要求,狭缝式机头结构,冷却装置,厚度调节装置
流延薄膜成型挤出温度、冷却辊温、气刀、牵引速度等对生产的影响
机头结构,成型工艺影响因素
8
双向拉伸薄膜
吹膜机头(芯棒式机头、中心进料式机头、螺旋机头、旋转机头)的结构、特点与适用场合
吹膜机头工艺参数(吹胀比、牵引比、口模缝隙宽度、口模、芯模定型部分的长度、缓冲槽尺寸、流道扩张角)的定义、对薄膜生产的影响
挤出机与吹膜机头的匹配
机头结构(读懂结构图,通过模具拆装实训熟悉机头)
吹膜机头工艺参数对薄膜规格尺寸、薄膜性能的影响