结构设计规范
结构工程师-结构设计要求规范
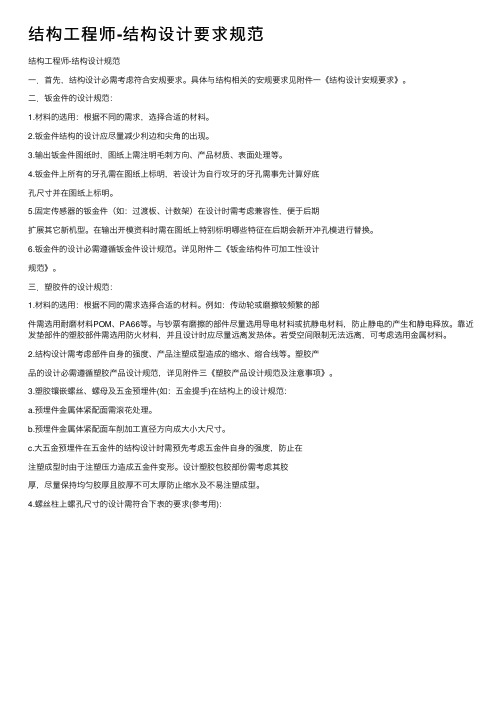
结构⼯程师-结构设计要求规范结构⼯程师-结构设计规范⼀.⾸先,结构设计必需考虑符合安规要求。
具体与结构相关的安规要求见附件⼀《结构设计安规要求》。
⼆.钣⾦件的设计规范:1.材料的选⽤:根据不同的需求,选择合适的材料。
2.钣⾦件结构的设计应尽量减少利边和尖⾓的出现。
3.输出钣⾦件图纸时,图纸上需注明⽑刺⽅向、产品材质、表⾯处理等。
4.钣⾦件上所有的⽛孔需在图纸上标明,若设计为⾃⾏攻⽛的⽛孔需事先计算好底孔尺⼨并在图纸上标明。
5.固定传感器的钣⾦件(如:过渡板、计数架)在设计时需考虑兼容性,便于后期扩展其它新机型。
在输出开模资料时需在图纸上特别标明哪些特征在后期会新开冲孔模进⾏替换。
6.钣⾦件的设计必需遵循钣⾦件设计规范。
详见附件⼆《钣⾦结构件可加⼯性设计规范》。
三.塑胶件的设计规范:1.材料的选⽤:根据不同的需求选择合适的材料。
例如:传动轮或磨擦较频繁的部件需选⽤耐磨材料POM、PA66等。
与钞票有磨擦的部件尽量选⽤导电材料或抗静电材料,防⽌静电的产⽣和静电释放。
靠近发垫部件的塑胶部件需选⽤防⽕材料,并且设计时应尽量远离发热体。
若受空间限制⽆法远离,可考虑选⽤⾦属材料。
2.结构设计需考虑部件⾃⾝的强度、产品注塑成型造成的缩⽔、熔合线等。
塑胶产品的设计必需遵循塑胶产品设计规范,详见附件三《塑胶产品设计规范及注意事项》。
3.塑胶镶嵌螺丝、螺母及五⾦预埋件(如:五⾦提⼿)在结构上的设计规范:a.预埋件⾦属体紧配⾯需滚花处理。
b.预埋件⾦属体紧配⾯车削加⼯直径⽅向成⼤⼩⼤尺⼨。
c.⼤五⾦预埋件在五⾦件的结构设计时需预先考虑五⾦件⾃⾝的强度,防⽌在注塑成型时由于注塑压⼒造成五⾦件变形。
设计塑胶包胶部份需考虑其胶厚,尽量保持均匀胶厚且胶厚不可太厚防⽌缩⽔及不易注塑成型。
4.螺丝柱上螺孔尺⼨的设计需符合下表的要求(参考⽤):螺丝柱的直径必需根据螺丝柱底孔尺⼨来设计,⼀般需保证有1.5mm的壁厚。
防⽌外观缩⽔螺丝柱底部需掏⽕⼭⼝。
《混凝土结构设计规范》GB50010-2010
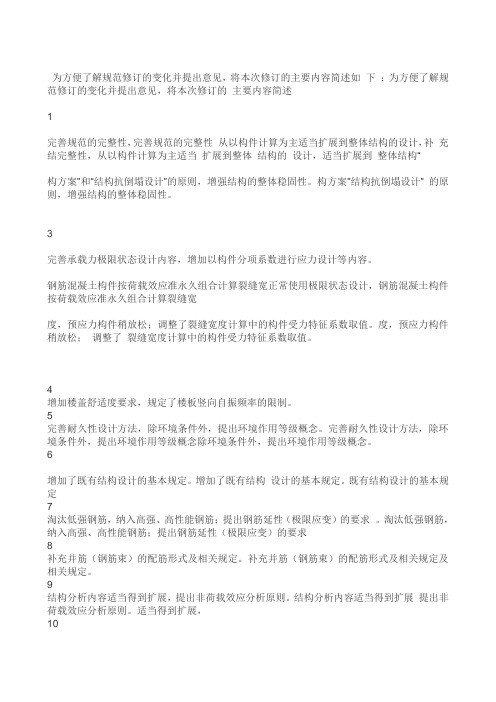
为方便了解规范修订的变化并提出意见,将本次修订的主要内容简述如下:为方便了解规范修订的变化并提出意见,将本次修订的主要内容简述1完善规范的完整性,完善规范的完整性从以构件计算为主适当扩展到整体结构的设计,补充结完整性,从以构件计算为主适当扩展到整体结构的设计,适当扩展到整体结构“构方案”和“结构抗倒塌设计”的原则,增强结构的整体稳固性。
构方案”结构抗倒塌设计” 的原则,增强结构的整体稳固性。
3完善承载力极限状态设计内容,增加以构件分项系数进行应力设计等内容。
钢筋混凝土构件按荷载效应准永久组合计算裂缝宽正常使用极限状态设计,钢筋混凝土构件按荷载效应准永久组合计算裂缝宽度,预应力构件稍放松;调整了裂缝宽度计算中的构件受力特征系数取值。
度,预应力构件稍放松;调整了裂缝宽度计算中的构件受力特征系数取值。
4增加楼盖舒适度要求,规定了楼板竖向自振频率的限制。
5完善耐久性设计方法,除环境条件外,提出环境作用等级概念。
完善耐久性设计方法,除环境条件外,提出环境作用等级概念除环境条件外,提出环境作用等级概念。
6增加了既有结构设计的基本规定。
增加了既有结构设计的基本规定。
既有结构设计的基本规定7淘汰低强钢筋,纳入高强、高性能钢筋;提出钢筋延性(极限应变)的要求。
淘汰低强钢筋,纳入高强、高性能钢筋;提出钢筋延性(极限应变)的要求8补充并筋(钢筋束)的配筋形式及相关规定。
补充并筋(钢筋束)的配筋形式及相关规定及相关规定。
9结构分析内容适当得到扩展,提出非荷载效应分析原则。
结构分析内容适当得到扩展提出非荷载效应分析原则。
适当得到扩展,10对结构侧移二阶效应,提出有限元分析及增大系数的简化方法。
侧移二阶效应,提出有限元分析及增大系数的简化10 对结构侧移二阶效应,提出有限元分析及增大系数的简化方法。
11 完善了连续梁、连续板考虑塑性内力重分布进行内力调幅的设计方法。
12 补充、完善材料本构关系及混凝土多轴强度准则的内容。
“ 任意截面”“ 简化计算”13 构件正截面承载力计算:任意截面”移至正文,简化计算”移至附录。
组合结构设计规范jgj138-2016
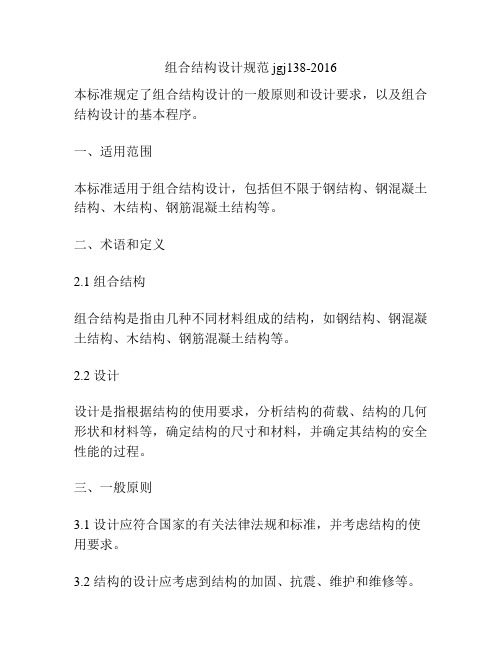
组合结构设计规范jgj138-2016
本标准规定了组合结构设计的一般原则和设计要求,以及组合结构设计的基本程序。
一、适用范围
本标准适用于组合结构设计,包括但不限于钢结构、钢混凝土结构、木结构、钢筋混凝土结构等。
二、术语和定义
2.1 组合结构
组合结构是指由几种不同材料组成的结构,如钢结构、钢混凝土结构、木结构、钢筋混凝土结构等。
2.2 设计
设计是指根据结构的使用要求,分析结构的荷载、结构的几何形状和材料等,确定结构的尺寸和材料,并确定其结构的安全性能的过程。
三、一般原则
3.1 设计应符合国家的有关法律法规和标准,并考虑结构的使用要求。
3.2 结构的设计应考虑到结构的加固、抗震、维护和维修等。
3.3 结构的设计应考虑到材料的性能、施工工艺和施工环境等。
3.4 结构的设计应考虑到结构的经济性、安全性、美观性和环
境友好性等。
四、设计要求
4.1 结构的设计应符合国家的有关法律法规和标准,并考虑结
构的使用要求。
4.2 结构的设计应考虑到结构的加固、抗震、维护和维修等。
4.3 结构的设计应考虑到材料的性能、施工工艺和施工环境等。
4.4 结构的设计应考。
混凝土结构设计规范GB50010-2010
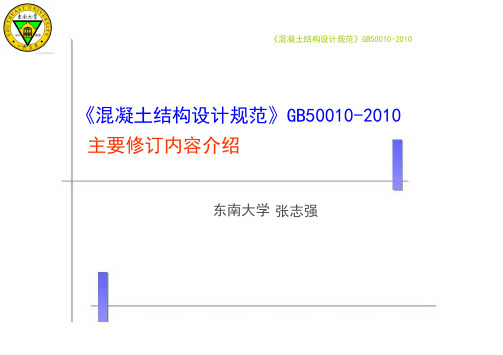
3.2.3 结构构件连接应符合下列要求: 1 连接部位的承载力不应小于被连接构件的承载力,并应保证被连接构 件之间的传力性能; 2 当混凝土构件与其他材料构件连接时,应采取可靠的连接措施; 3 应考虑构件变形对连接节点及相邻结构或构件造成的影响。 3.2.4 混凝土结构设计应符合节省材料、方便施工、降低能耗与保护环境 的要求。
3.3.4 (新增)偶然作用下承载力极限状态设计时的计算规定。 作用效应设计值S按偶然组合计算 结构重要性系数γ0取不小于1.0的数值 材料强度取标准值 3.3.5(新增)既有结构承载力极限状态设计时的计算规定
3.4 正常使用极限状态验算
1. 混凝土结构构件正常使用极限状态的验算应包括下 列内容: a. 对需要控制变形的构件,应进行变形验算; b. 对使用上限制出现裂缝的构件,应进行混凝土拉 应力验算; c. 对允许出现裂缝的构件,应进行受力裂缝宽度验 算; d. 对有舒适度要求的楼盖结构,应进行竖向自振频 率验算(新增内容)。
3.2.2 混凝土结构中结构缝的设计应符合下列要求: 1 应根据结构受力特点及建筑尺度、形状、使用功能,合理确定结构 缝的位置和构造形式; 2 宜控制结构缝的数量,并应采取有效措施减少设缝的不利影响; 3 可根据需要设置施工阶段的临时性结构缝。 结构缝的类型: 伸缩缝:减小混凝土收缩、温度变化引起的胀—缩变形的不利影响; 沉降缝:减小基础不均匀沉降的不利影响; 防震缝:防止地震时相邻结构互相撞击破坏; 构造缝:防止结构局部应力集中的不利影响; 体形缝:避免结构刚度及质量突变引起的不利影响; 分割缝:防止结构连续倒塌,控制倒塌范围; 临时缝(施工接槎和后浇带等):消除某些暂时性(早期收缩)的不 利影响; 控制缝:预留薄弱截面,利用混凝土收缩在指定部位按需的形式开裂, 并预先采取措施,消除设缝的不利影响。
结构设计评审规范
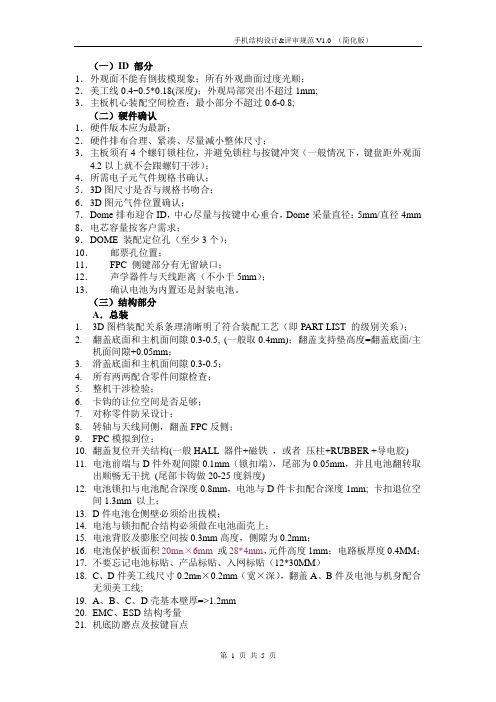
(一)ID 部分1.外观面不能有倒拔模现象;所有外观曲面过度光顺;2.美工线0.4~0.5*0.18(深度);外观局部突出不超过1mm;3.主板机心装配空间检查;最小部分不超过0.6-0.8;(二)硬件确认1.硬件版本应为最新;2.硬件排布合理、紧凑、尽量减小整体尺寸;3.主板须有4个螺钉锁柱位,并避免锁柱与按键冲突(一般情况下,键盘距外观面4.2以上就不会跟螺钉干涉);4.所需电子元气件规格书确认;5.3D图尺寸是否与规格书吻合;6.3D图元气件位置确认;7.D ome排布迎合ID,中心尽量与按键中心重合,Dome采量直径:5mm/直径4mm 8.电芯容量按客户需求;9.D OME 装配定位孔(至少3个);10.邮票孔位置;11.FPC 侧键部分有无留缺口;12.声学器件与天线距离(不小于5mm);13.确认电池为内置还是封装电池。
(三)结构部分A.总装1.3D图档装配关系条理清晰明了符合装配工艺(即PART LIST 的级别关系);2.翻盖底面和主机面间隙0.3-0.5, (一般取0.4mm);翻盖支持垫高度=翻盖底面/主机面间隙+0.05mm;3.滑盖底面和主机面间隙0.3-0.5;4.所有两两配合零件间隙检查;5.整机干涉检验;6.卡钩的让位空间是否足够;7.对称零件防呆设计;8.转轴与天线同侧,翻盖FPC反侧;9.FPC模拟到位;10.翻盖复位开关结构(一般HALL 器件+磁铁,或者压柱+RUBBER +导电胶)11.电池前端与D件外观间隙0.1mm(锁扣端),尾部为0.05mm,并且电池翻转取出顺畅无干扰(尾部卡钩做20-25度斜度)12.电池锁扣与电池配合深度0.8mm,电池与D件卡扣配合深度1mm; 卡扣退位空间1.3mm 以上;13.D件电池仓侧壁必须给出拔模;14.电池与锁扣配合结构必须做在电池面壳上;15.电池背胶及膨胀空间按0.3mm高度,侧隙为0.2mm;16.电池保护板面积20m m×6mm或28*4mm,元件高度1mm;电路板厚度0.4MM;17.不要忘记电池标贴、产品标贴、入网标贴(12*30MM)18.C、D件美工线尺寸0.2m m×0.2mm(宽×深),翻盖A、B件及电池与机身配合无须美工线;19.A、B、C、D壳基本壁厚=>1.2mm20.EMC、ESD结构考量21.机底防磨点及按键盲点B.功能性项目1.转轴翻盖转轴闭合预压25-26度(轴径和重量由选用LCD大小、翻盖重量决定),打开状态预压4-7度(一般取5度);角度方向正确;SPEC 确认;胶壳在转轴处壁厚1.2mm;止转要可靠、避免撞击而过快掉漆;固定可靠,无轴向串动;装拆有无空间?转轴与另一端的支撑必须同心转轴中心应尽量与外形中心重合2.镜片及相关设计大屏Lens一般采用为非塑加工(即切割加工),厚度0.85mm;小屏Lens尽量采用切割加工,厚度0.65-0.85mm;如采用IML,厚度1.2mm, 局部不小于0.8 mm; 且背面尽量不要有大的壁厚变化, ;如采用普通注塑+背面丝印,厚度>=1.0mm, 背面必须为大平面或大弧面。
做结构设计要用的规范
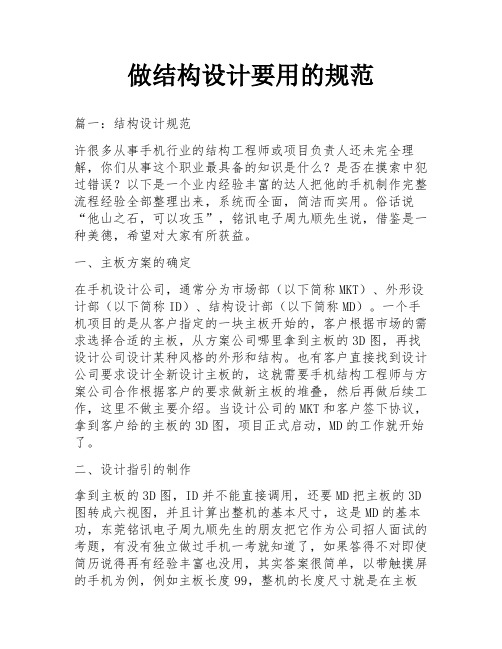
做结构设计要用的规范篇一:结构设计规范许很多从事手机行业的结构工程师或项目负责人还未完全理解,你们从事这个职业最具备的知识是什么?是否在摸索中犯过错误?以下是一个业内经验丰富的达人把他的手机制作完整流程经验全部整理出来,系统而全面,简洁而实用。
俗话说“他山之石,可以攻玉”,铭讯电子周九顺先生说,借鉴是一种美德,希望对大家有所获益。
一、主板方案的确定在手机设计公司,通常分为市场部(以下简称MKT)、外形设计部(以下简称ID)、结构设计部(以下简称MD)。
一个手机项目的是从客户指定的一块主板开始的,客户根据市场的需求选择合适的主板,从方案公司哪里拿到主板的3D图,再找设计公司设计某种风格的外形和结构。
也有客户直接找到设计公司要求设计全新设计主板的,这就需要手机结构工程师与方案公司合作根据客户的要求做新主板的堆叠,然后再做后续工作,这里不做主要介绍。
当设计公司的MKT和客户签下协议,拿到客户给的主板的3D图,项目正式启动,MD的工作就开始了。
二、设计指引的制作拿到主板的3D图,ID并不能直接调用,还要MD把主板的3D 图转成六视图,并且计算出整机的基本尺寸,这是MD的基本功,东莞铭讯电子周九顺先生的朋友把它作为公司招人面试的考题,有没有独立做过手机一考就知道了,如果答得不对即使简历说得再有经验丰富也没用,其实答案很简单,以带触摸屏的手机为例,例如主板长度99,整机的长度尺寸就是在主板的两端各加上2.5,整机长度可做到99+2.5+2.5=104,例如主板宽度37.6,整机的宽度尺寸就是在主板的两侧各加上2.5,整机宽度可做到37.6+2.5+2.5=42.6,例如主板厚度13.3,整机的厚度尺寸就是在主板的上面加上1.2(包含0.9的上壳厚度和0.3的泡棉厚度),在主板的下面加上1.1(包含1。
0的电池盖厚度和0.1的电池装配间隙),整机厚度可做到13.3+1.2+1.1=15.6,答案并不唯一,只要能说明计算的方法就行。
结构设计规范
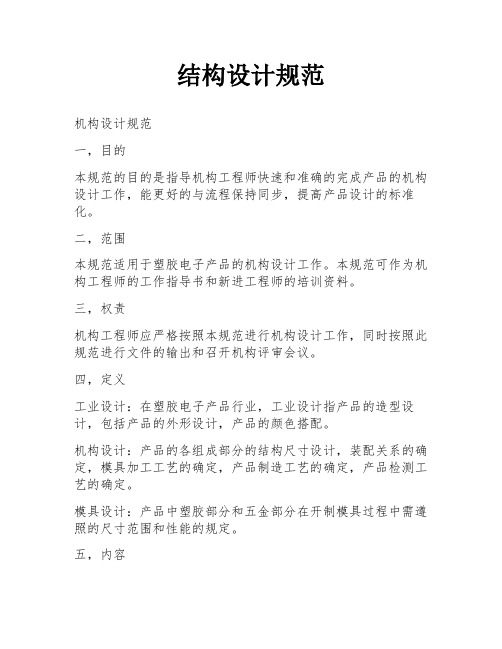
结构设计规范机构设计规范一,目的本规范的目的是指导机构工程师快速和准确的完成产品的机构设计工作,能更好的与流程保持同步,提高产品设计的标准化。
二,范围本规范适用于塑胶电子产品的机构设计工作。
本规范可作为机构工程师的工作指导书和新进工程师的培训资料。
三,权责机构工程师应严格按照本规范进行机构设计工作,同时按照此规范进行文件的输出和召开机构评审会议。
四,定义工业设计:在塑胶电子产品行业,工业设计指产品的造型设计,包括产品的外形设计,产品的颜色搭配。
机构设计:产品的各组成部分的结构尺寸设计,装配关系的确定,模具加工工艺的确定,产品制造工艺的确定,产品检测工艺的确定。
模具设计:产品中塑胶部分和五金部分在开制模具过程中需遵照的尺寸范围和性能的规定。
五,内容1,产品机构设计在开发工作中的作用产品开发的工作一般分为;产品的工业设计,产品的机构设计,产品的电路设计,产品工艺设计,产品的包装设计。
具体见附表1-产品的开发流程表。
产品开发工作的细化要求各个部门之间要有良好的协作关系。
在产品开发初期,项目经理对产品可行性作大量的工作,如产品的市场前情的调查,样品的试制,性能的测试和成本的核算等。
产品的设计工作主要是将成功的试验室产品转化成可量产化产品的过程,即实现产品设计和检测的电子化,产品制造的流水线化的过程。
在产品开发中,无论何种电子产品,无论机构部分占主导,还是电路部分占主导,机构设计应该是主要部分,结构设计的好坏直接决定产品是否能够成功实现预期的目标,产品开发的工作是否按期完成,电路设计的空间是否得到充分保障,空间位置是否得到优化,生产工艺是否合理,生产效率是否得到保证,这些将决定产品开发的成功与否。
2.机构设计流程2.1.开发的工作应该以产品质量为目标进行的产品设计过程。
在国际上,产品开发已经被列入质量考核的一项内容。
如ISO9000,APQP,六西格马等。
在各个行业中,为了统一产品的质量标准,行业标准同样规范了产品的开发标准。
钢筋混凝土结构设计规范
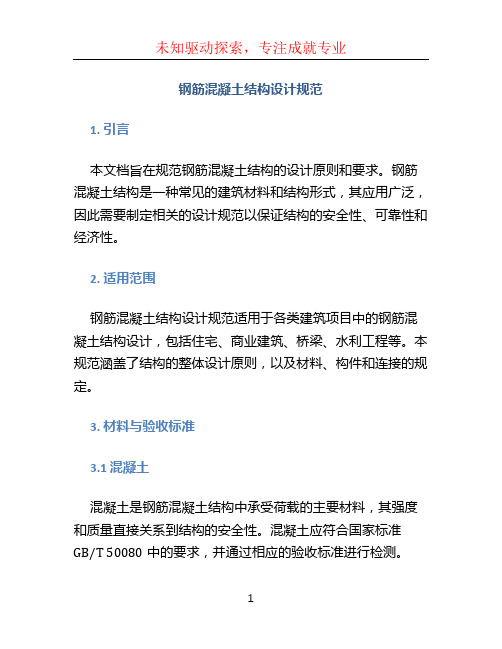
钢筋混凝土结构设计规范1. 引言本文档旨在规范钢筋混凝土结构的设计原则和要求。
钢筋混凝土结构是一种常见的建筑材料和结构形式,其应用广泛,因此需要制定相关的设计规范以保证结构的安全性、可靠性和经济性。
2. 适用范围钢筋混凝土结构设计规范适用于各类建筑项目中的钢筋混凝土结构设计,包括住宅、商业建筑、桥梁、水利工程等。
本规范涵盖了结构的整体设计原则,以及材料、构件和连接的规定。
3. 材料与验收标准3.1 混凝土混凝土是钢筋混凝土结构中承受荷载的主要材料,其强度和质量直接关系到结构的安全性。
混凝土应符合国家标准GB/T 50080中的要求,并通过相应的验收标准进行检测。
3.2 钢筋钢筋是钢筋混凝土结构中起到增强混凝土抗拉强度和承载能力的材料。
钢筋应符合国家标准GB/T 1499.2中的要求,并经过验收标准检测。
3.3 其他材料除混凝土和钢筋外,还包括其他辅助材料,如砂浆、抗裂剂等。
这些材料的选用应符合相关国家标准,并经过相应的验收标准检测。
4. 结构设计原则4.1 安全性原则钢筋混凝土结构的设计应满足结构强度和稳定性的要求,以确保结构在正常使用和极限状态下的安全。
4.2 可靠性原则结构设计应考虑结构材料和构件的可靠性,能够保证结构在设计寿命内具有良好的使用性能,并满足耐久性要求。
4.3 经济性原则结构设计应在满足安全和可靠性的前提下,尽量节约材料和成本,提高结构的经济效益。
5. 结构设计方法5.1 荷载分析结构设计应充分考虑结构所承受的荷载,包括重力荷载、风荷载、地震荷载等。
5.2 风荷载计算对于高层建筑和横跨较大跨度的结构,应按照国家标准GB 50009中的要求进行风荷载计算。
5.3 结构计算根据荷载分析的结果,进行结构的强度和稳定性计算,满足设计原则中的安全性和可靠性要求。
5.4 构件设计根据结构计算的结果和相关规范,进行构件尺寸和钢筋布置的设计,满足结构的强度和稳定性要求。
6. 结构施工与验收6.1 施工流程根据结构设计图纸,组织施工队伍进行施工,包括基础施工、结构构件的浇筑、钢筋的安装等。
- 1、下载文档前请自行甄别文档内容的完整性,平台不提供额外的编辑、内容补充、找答案等附加服务。
- 2、"仅部分预览"的文档,不可在线预览部分如存在完整性等问题,可反馈申请退款(可完整预览的文档不适用该条件!)。
- 3、如文档侵犯您的权益,请联系客服反馈,我们会尽快为您处理(人工客服工作时间:9:00-18:30)。
产品结构设计规范说明:图示:所有产品结构设计,都应在品质至上的基础上,以简单实用、生产(装配)容易、符合客户要求为主。
分件及装配,先从生产角度构思。
尽可能减少生产工序及零件,以提高生产量降低成本,提升其市场竟争力。
图1-1图1-21. 产品壁厚 塑胶件的设计尽可能做到一次完成。
对于难以保证的位置,应考虑到产品加胶容易,减胶难。
预留些加胶的空间。
产品壳体厚度:产品的的壁厚大小取决於产品需要承受的外力、体积大小、功能要求以及材料不同。
一般的热塑性塑料壁厚设计应以4mm 为上限。
通常在满足所需要求情况下,尽可能的减少产品壁厚。
) 1) A 类:塑件外形高低小于150mm ,如MP3、MP4、GPS 、遥控器等(ABS).壁厚度一般为1.20mm ~2.0mm 。
2)B 类: 塑件外形高低150~250mm ,如座式电话机(ABS),壁厚度一般为1.8m m ~2.5mm 。
3)C 类: 塑件外形高低250mm 以上,如电饭煲(PP),器械外罩(ABS)。
壁厚度一般为2.5mm ~3.0mm 。
4)D 类:对于对壳体有特别要求的产品,如音箱(壁厚对音响效果影象较大),壁厚由3.0mm ~4.0mm 不等。
5)产品的壁厚直接影响到其寿命及成本,过薄可能会造成制品强度和刚度不足,受力后容易翘曲变形。
成型时流动阻力大,大型复杂的零件难以成形,使用过程容易变形破裂。
过厚则增加材料的成本,成型周期加长,降低生产率,产品表面产生缩水、气泡等不良现象。
6)在产品壁厚设计时应充分考虑其体积大小、材质、使用场合。
参考客户意见等资料。
如果在使用过程中表面受外加力或气压水压等,更须作出适当计算。
7) A 类产品通常会有小装饰件,装饰件壁厚为0.8~1.2 。
8)不建议使用大件的塑胶装饰件,大装饰件可改用厚为0.6~1.0的不锈钢件。
9)IML 件壁厚要求1.2以上,局部壁厚不小于0.8,凹陷的深度不大于0.3。
10) 尽可能的保持塑件有均一的壁厚,若是无可避免地产生厚薄胶的渐变,塑件的局部壁厚不小于平均壁厚的一半,而且要求做平缓的过度面加大的导圆角(过度面与局部壁厚3:1)。
(图1-1)11)塑件转角位置用圆角过渡(图1-2)。
尖锐的圆角位通常会导致部件有缺陷及应力集中,尖角的位置亦常在电镀过程後引起不希望的物料聚积。
集中应力的地方会在受负载或撞击的时候破裂。
较大的圆角提供了这种缺点的解决方法,不但减低应力集中的因素,且令流动的塑料流得更畅顺和成品脱模时更容易。
圆角是壁厚的0.2~0.6,理想数值是壁厚的0.5。
2.止口:止口在产品的组合中起到相互之间的定位、加固装配和调整接合线(夹口)的平整的作用。
常用的有单止口和双止口(见图2-1)。
1)大部分产品使用的都是单止口,凸止口宽一般来为壁厚的0.45倍。
高为宽度的1~1.5倍。
(常用高度有0.8mm,1.0mm,1.2mm,1.5mm,2.0mm。
体积大的产品还有3.0mm,4.0mm)。
2)双止口的使用相对会少。
一般用于防水或比较密封和须要用打胶方式固定的产品。
还有胶位厚的产品也常用。
3)凹凸止口的间隙通常单边为0.05mm~0.2mm(常用有0.05mm,0.08mm,0.10mm,0.15mm)。
4)止口的宽度设计要求不小于0.70m m 。
要注意凹止口底面到产品外表面距离过于单薄而产不良痕迹。
(如图2-2)5)A类产品侧壁厚要求1.8mm以上,凸止口为0.8x1.0(宽x长)或1.0x1.0。
凹凸止口的间隙为0.05,加3·的拔摸角。
B类产品侧壁厚要求2.3mm以上,凸止口为1.0x1.0或1.2x1.5。
凹凸止口的间隙为0.08,加3·的拔摸角。
C类产品侧壁厚要求 3.0以上,止口为 1.5x1.5或1.5x2.0。
凹凸止口的间隙为0.15,加3·的拔摸角。
图2-1 图2-23.装饰线(美观线):产品的配合装饰线间隙(高)尺寸因其体积的大小而不一。
设计时应考虑装饰线与产品整体的协调。
通常有(0.30mm,0.50mm,0.8mm,1.0mm。
)宽度通常有(0.30mm,0.50mm,1.0mm)。
A类产品装饰线为0.3x0.3 。
B类产品装饰线为0.5x0.5 。
C类产品装饰线为0.8x0.8 。
装饰线与凹凸止口的间隙关系设计如(图3-1)。
图3-14.拔模:1)产品在其出模方向所有与模穴有磨擦的面积都应有拔模角,在结构设计前要详细检查表面有没有无法出模现象。
拔模角在产外观与结构允许的情况下尽可能加大,以方便产品加工生产。
2)对于外部有蚀纹工艺要求产品,跟据蚀纹的粗细和深度拔模角也相应不同(准确数据可参考相应的纹板)。
通常用的为0.5~5度。
特别对于较粗蚀纹,如果角度不够表面可能产生拖花现像。
常用为5~8度,最大的要达10多度。
3)对于表面透明或要求光洁度很好的产品,为防拖花角度通常加大到2~5度。
4)产品某些较单独或较细、容易变形位置,如喇叭网罩、装饰边框、较密集的喇叭孔等。
由于单薄或区域磨擦力集中,脱模时容易粘连前模,使产品拉断或变形。
拔模角通常要加大到5~7度。
(图4-1)5)如果产品垂直高度比较大表面(表面无蚀纹)或比较高的筋、螺丝柱,为避免拔模后胶过厚表面产生缩水。
其拔模规则为拔模后壁厚比拔模前单边落差不小于0.20mm。
(图4-2)6)塑件精度要求高,应采用较小的拔摸角。
塑件较高较大,应采用较小的拔摸角,即按落差计算。
塑件形状复杂,不易脱模,应采用较大的拔摸角。
塑件收缩率较大,应采用较大的拔摸角。
塑件壁较厚,收缩也增大,应采用较大的拔摸角。
7)产品表面如果有侧面行位开摸,则行位位置拔摸角可忽略。
图4-1 图4-25.倒圆角:1)产品的所有外形棱线必须要导圆角。
特别注意电铸件或电铸按键的棱线2)倒圆角应不小于R 0,30m m,小于R 0.30mm会被视为工艺角。
3)壳体的螺丝头沉孔边要加0.3以上的圆角。
4)特别注意电铸件或电铸按键的棱线防后期产生掉漆要加0.2以上的导圆角。
5)零件的所有转角尽可能的设计成圆角或用圆弧过渡。
(如图1-2)以减少应力的集中、提高强度和利于模具填充、脱模。
6)矩形通孔,要在四个拐角处留0.3-0.5的小圆角,避免出模时,由于应力集中,会有拉白拉裂等现象。
6.按钮设计:1)按钮壁厚通常为 1.0m m~1.5.0mm ,裙边1.0mmX1.0mm(高)、1.5mmX1.2mm。
(图6-1)2)按键的设计应考虑其加工和安装的方便性,高度不宜太高,通常体积不大的不高于15.0mm。
3)按键按其色彩、材料、工艺等尽可能的用弹簧筋等方式设计成组合体。
如:电镀按键为一组,喷漆的为一组,透明的为一组等。
(图6-2)图6-14)按键弹簧筋尺寸:宽度:1.2~2.5高度:0.8~1.05)按钮上下行程由所采用的PCB板元件决定。
通常有:0.30mm、0.5mm、1.0mm。
导电硅胶行程为1.0~1.50mm6)按键与壳体装配通常以壳体上的围筋压住按键裙边的方式来固定,外形若为圆形或椭圆形,要加定位筋。
定位筋高度为按钮行程2倍。
图6-24)螺丝柱加强筋(火箭脚)高度不应与螺丝柱面相平,通常是为螺丝柱的0.9。
5)离壳边较近的螺丝柱加筋与壁相连起来,目的是加强支柱的强度及使胶料流动更顺畅。
(图9-1)6)孔加倒斜角,螺丝头沉台加围筋。
(如图5)7)通常螺丝柱的外径是内径的两倍。
但如果这种方式螺丝柱壁厚等於或超过胶料厚度而在表面产生缩水纹及高成型应力。
则螺丝柱的厚度应为胶料厚度的50-70%。
如因此螺丝柱不能提供足够强度,可以加加强筋,若柱位置接近边壁,则可用一条肋骨将边壁和柱相互连接来达到加强的效果。
常用的螺丝柱、螺丝头沉台孔、螺丝头孔螺丝螺丝柱外径螺丝柱内径沉台孔螺丝头孔3.50 6.50 3.00 3.70 6.703.00 5.20 2.40 3.20 6.02.60 4.50 2.20 2.80 5.202.30 4.20 1.90 2.50 4.602.00 4.00 1.70 2.20 4.201.70 3.20 1.302.003.501.40 3.00 1.00 1.602.601.002.60 0.70 1.20 2.508)丝头孔如果较深螺丝头孔应尽可能的加大以方便螺丝刀的操作。
9)A类产品常用螺丝为1.0~2.0 。
B类产品常用螺丝为1.7~3.0。
C类产品常用螺丝为2.6~4.0 。
10)螺丝柱尽可能的避免靠边,靠边柱容易造成表面缩水。
(图9-2)图9-1图9-210.螺丝盖1)螺丝盖要求做段差来定位高度如图10-1。
2)避免用大面配合如图10-1上面段有0.05的间隙。
尽量用筋骨做局部零配合,如图10-1的零配合面。
装入口要加C角作安装导入。
3)如果外表面是弧面必须有防呆设计。
图10-14)表面必须有拆卸槽。
(图10-2)5)螺丝盖的总高度不宜过高,通常是其直径的1.5倍。
图10-211.卡扣1)卡扣的设计主要是用在零件间的连接或组合,扣位的组合部份在生产成品的时候同时成型,装配时无须配合其他如螺丝、介子等紧锁配件,只要需组合的两边扣位互相配合扣上即可,提供了一种不但方便快捷而且经济的产品装配方法。
2)按功能来区分,扣位的设计可分为成永久型和可拆卸型两种。
永久型扣位的设计方便装上但不容易拆下,可拆卸型扣位的设计则装上、拆下均十分方便。
可拆卸型扣位的勾形伸出部份附有适当的导入角及导出角方便扣上及分离的动作,如滑动式的电池门扣。
永久型的扣位则只有导入角而没有导出角的设计,所以一经扣上,相接部份即形成自我锁上的状态,不容易拆下。
这是最常用的一些如组合卡扣。
卡扣效果完全取决于塑胶的弹性,设计中特别注意其强度和变形量。
3)卡扣的根部要加圆角以减少应力的集中,防止断裂。
4)卡扣常用的扣合量A类产品扣合量为0.5~0.8 ,预留加胶0.2以上。
B类产品装饰线为0.8~1.2。
预留加胶0.5以上。
5)扣位的设计时考虑斜顶的宽度和行程是否足够。
(宽度5.0以上,行程6.0以上。
)6)卡扣的常用设计数据(A类产品):①:公扣厚度,0.8以上,注意弹力和缩水。
②:公扣直身边,0.5以上。
③:公扣挂钩高度,1.5以上,如有空间尽量做强。
④:母扣挂钩高度,1.2以上。
如果公扣较高或强度不够可加加强筋。
公母扣必须要加导入C角。
(如图11-1)⑤:公母扣间隙,0.15以上。
⑥:公母扣扣合间隙,0.05~0.10。
⑦:母扣预留加胶空间,0.2以上,如有空间尽量加大。
⑧:母扣扣合量,0.6以上。
⑨:公母扣避空空间,如有空间尽量加大。
11-112.加强筋1)加强筋在塑胶部件上是不可或缺的功能部份,加强筋有效地增加产品的刚性和强度而无需大幅增加产品切面面积。
对一些经常受到压力、扭力、弯曲的塑胶产品尤其适用。