PVC管件分层,什么原因,怎么办?
PVC生产中的常见问题及解决方法
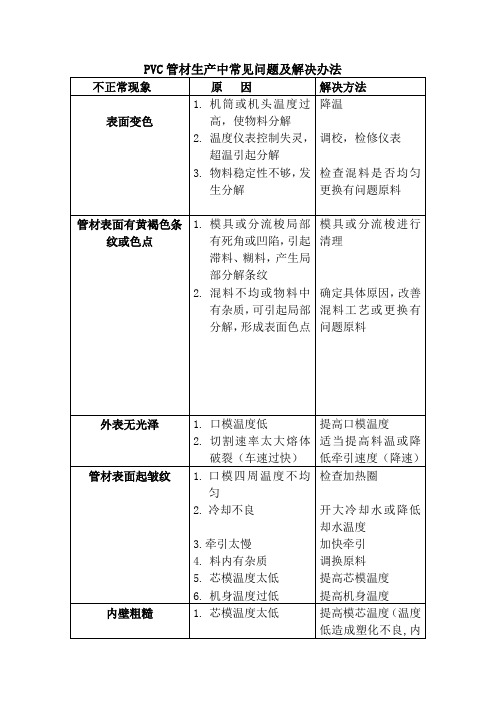
模具或分流梭进行清理
确定具体原因,改善混料工艺或更换有问题原料
外表无光泽
1.口模温度低
2.切割速率太大熔体破裂(车速过快)
提高口模温度
适当提高料温或降低牵引速度(降速)
管材表面起皱纹
1.口模四周温度不均匀
2.冷却不良
3.牵引太慢
4.料内有杂质
5.芯模温度太低
PVC管材生产中常见问题及解决办法
不正常现象
原 因
解决方法
表面变色
1.机筒或机头温度过高,使物料分解
2.温度仪表控制失灵,超温引起分解
3.物料稳定性不够,发生分解
降温
调校,检பைடு நூலகம்仪表
检查混料是否均匀更换有问题原料
管材表面有黄褐色条纹或色点
1.模具或分流梭局部有死角或凹陷,引起滞料、糊料,产生局部分解条纹
1.口模内壁不光滑,沾有析出物
2.定型模真空度不够,管材贴模不紧
3.温度太低,塑化不良
4.挤出速度过快,塑化不良
清理口模
提高真空度
提温或增加ACR加工助剂
降速
管材有明显的熔结线(合模线)
1.温度太低,塑化不良
2.挤出速度快,物料塑化不良
提高温度
降速
制作人;张忠诚
6.机身温度过低
检查加热圈
开大冷却水或降低却水温度
加快牵引
调换原料
提高芯模温度
提高机身温度
内壁粗糙
1.芯模温度太低
2.机筒温度过低,塑化不良
3.螺杆温度太高(给料转速与主机转速不合理;给料电机转速过快)
提高模芯温度(温度低造成塑化不良,内壁在模头处难以升温,故产生粗糙现象)
PVC管材生产中常见问题及解决办法
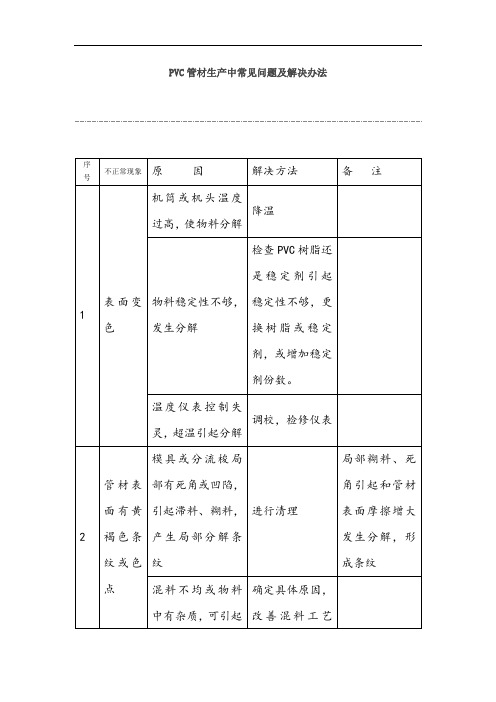
PVC管材生产中常见问题及解决办法PVC型材生产中常见问题及解决办法pvc管材变色问题2010-08-08 17:53型材在加工时就发现色泽不统一(如色泽有轻微偏差是允许的);(2)加热变形后型材明显黄变;(3)加热后状态良好,但型材制成门窗时间不长就变灰。
型材正常生产中不发黄,而在后来的成窗制品时发黄。
在型材生产过程中,当原料及模具等基本条件无变化时,如果将其塑化段及均化段的温度提高5℃左右,所产生的型材发生黄变倾向,也说明其热稳定效率不足,应增加热稳定剂的加入量,尤其是配方中加入荧光增白剂等增白助剂时,热稳定剂不足,增白效果不明显。
PVC分子结构与颜色的关系(1)因PVC树脂是一种热敏性塑料,其光稳定性较差,在热和光的作用下,支链发生脱HCI反应、多烯结构分子,当主链出现共扼双键数量不太多时产生微量色差,氯化氢首先会与周围潜在的对酸活性的物质发生反应,而共扼双键成为PVC分子链内新的活性位置,被光引发成大分子游离基后,PVC就容易遭受氧化,产生色变。
(2)PVC树脂中存在一定数量偏低低分子量组分,降低了聚合物的热稳定性,PVC分解的机理有游离基机理、离子机理、单分子机理等,PVC分解除稳定剂外还有可能受到PVC树脂本身质量的影响,如PVC树脂内是否存有残留过多的引发剂。
(3)聚合物中如存在某种杂质,例如在聚合过程中加人的引发剂、催化剂、酸、碱等去除不尽,或在储运过程中吸收水分,都会降低聚合物的稳定性。
因为这些物质能引起分子-离子降解反应,CPE 中含有较多Cl2、HCl等低分子物,易加速树脂热分解。
因此对稳定不好的PVC+CPE体系,通过增加稳定剂用量也可消除一些型材泛黄问题。
(4)硬PVC结构型材,它是由PVC作连续相的多相聚合物与混合物捏合热稳定剂、光稳定剂润滑剂、填充剂与颜料构成的混合体系,当PVC异型材曝露在自然环境时,一旦PVC组分脱氯化氢后,碳酸钙原组分会转化成氯化钙新组分,它分散在氧化降解物层内,并形成潜在的吸水位置,这是户外型材发黄的原因之一。
PVC管材生产中常见问题及解决办法要点
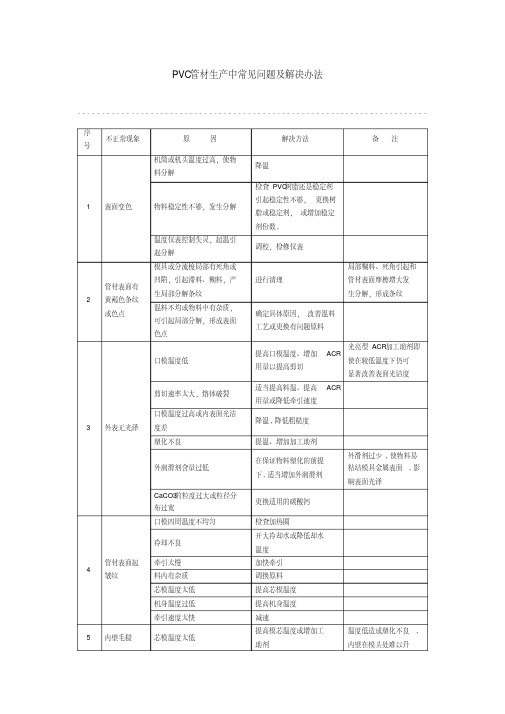
塑化不良 , 拉伸强度降低 PVC树脂质量不好 , 聚合度 低或分子量分布过宽 , 或分 子结构有缺陷
改性剂抗拉强度低 , 从而降 低了管材的抗拉强度
11 条中诸因素 , 同样会引起 管材抗拉强度低 , 使液压试 验不合格
塑化不良
配方中弹性橡胶体等高回缩 率物质组份过高,如 CPE 挤出速度与索引速度不匹 配,牵引速度过快 冷却不良 机头温度过高
得不到排除
型材表面粗
口模内壁不光滑,沾有析出
5
糙,光泽差, 物
解决办法 调整定型模具、牵引机的 位置 调节或修整模具 调整冷却水量或冷却水发 布 调整温度
降低挤出速度
降低牵引速度 检查是否有漏气或真空泵 系统有无堵塞 调节定型模与机头之间的 距离 调整定型模上下位置 加强冷却效果 清理机头 清理定型模
加工温度低
原铺料质量差
背压低
配方不良 加工温度高 ( 塑化 , 过度或 有分解 ) 使用 CPE抗冲改性时 , 螺杆 转速太快 , 剪切率过高使 CPE分散不均 , 呈堆集状态 , 搞抗冲作用下降
提高温度
加强螺杆冷却 干燥 检查泵工作状况 , 管路有 无堵塞 ( 抽粉子引起 ) 降低温度 调模 检查加热圈 , 检查螺杆有 无脉动现象 检查维修牵引机 检查真空泵及其管路 降螺杆温度
调校,检修仪表
进行清理
局部糊料、死角引起和 管材表面摩擦增大发 生分解,形成条纹
确定具体原因, 改善混料 工艺或更换有问题原料
提高口模温度、增加 用量以提高剪切
光亮型 ACR加工助剂即 ACR
使在较低温度下仍可
显著改善表面光洁度
适当提高料温、提高 ACR
pvc变形原因范文

pvc变形原因范文PVC是一种常见的塑料材料,由聚氯乙烯制成。
尽管在市场上广泛应用,但它也存在着变形的问题。
PVC变形的原因可以归结为材料结构、热膨胀性、机械应力和化学反应四个方面。
首先,PVC变形的原因之一是材料结构。
聚氯乙烯是由氯乙烯分子单体聚合而成的高分子聚合物,它的分子链结构比较松散,分子间力较弱。
因此,在温度升高或外力作用下,PVC分子链容易发生位移或转动,导致材料整体变形。
其次,热膨胀性也是导致PVC变形的原因之一、PVC材料的热膨胀系数较大,即在温度升高时,材料体积会相应增大。
当PVC受热膨胀后与周围环境无法有效补偿,就会发生变形。
这种变形可表现为材料膨胀、扭曲以及与其他材料之间的胶合层断裂等。
第三,机械应力也是导致PVC变形的原因之一、由于PVC的分子链较为脆弱,当外力施加于PVC材料上时,分子链会受到拉伸、扭曲或剪切等影响。
若应力超过PVC的抵抗极限,就会导致材料发生变形。
这种变形可能是弹性变形,一旦去除外力则能恢复;也可能是塑性变形,即永久性的形状改变。
最后,化学反应也是导致PVC变形的原因之一、PVC材料容易与一些化学物质发生反应,如氧化剂、溶剂、酸碱等。
这些化学物质可能引起PVC材料的蠕变、变色、腐蚀等问题,从而导致其变形。
为了最大限度地减少PVC材料的变形,可以采取以下措施:首先,通过改善PVC的结构,提高材料的分子间力,可以增加材料的强度和刚度,从而减少变形的发生。
这可以通过添加填充剂、增塑剂等方法实现。
其次,可以通过改变PVC的配方,选择具有低热膨胀性的配方,以减少材料受热膨胀引起的变形。
同时,也可以考虑在设计中留出足够的空间,让PVC材料有足够的膨胀空间,从而减少变形的发生。
第三,应避免在PVC材料表面施加过大的机械应力,或提前进行预处理,如热处理、冷却等,以提高材料的抵抗力和强度。
最后,应避免PVC材料与可能引起化学反应的物质接触,尽量选择与PVC材料相容性较好的材料进行接合或封装。
PVC管道常见故障与排除方法

PVC管道常见故障与排除方法故障:1、管道断裂原因:1、管材质量不好造成的管道断裂预防措施:要严把进货关,确保管材质量。
2、不良地基原因造成的管道断裂预防措施:对不良的地基进行基础处理,如夯实、换填及设置混凝土或钢筋混凝土基础等;要清除干净管下石块、硬物,岩石地基的管下需铺15厘米的砂垫层。
3、温度应力造成的管道断裂预防措施:管道应覆土在最大冻深20厘米以下,并注意侧向及管下的土深;冬季施工要注意及时回填,水压试验后及时将水放掉;必须避免夏季高温施工,应尽量安装伸缩节,避免管道过水收缩。
4、施工中造成的管道断裂无消除预防措施:必须加强施工管理,特别是在管沟开挖、地基处理、铺设安装、管道试压、管沟回填等几道工序上要严格按规范进行。
排除方法:挖出回填土,开挖的沟长要大于断裂管长2.0米左右,截去断裂部分,用100目的砂布将沟内管口的外侧打毛,长度在5~10厘米左右。
采用扩口管代替裂管,扩口管的内径等于沟内管的外径,用砂布把扩口管的内壁打毛,长度在6—11厘米左右,涂上粘合剂。
抬起沟内管,用扩口管套住沟内管,左右旋转扩口管,使其粘合均匀。
故障:2、真空破坏原因:管道系统运行时突然停机,出现负压(真空),将管道吸扁预防措施:在管道系统中设计排气阀,顺坡时安装在管道的首端,逆坡时设计安装在管道的尾端或安装在地形变化较大处。
排除方法:更换被破坏的管材,根据地形安装进排气阀。
故障:3、气阻破坏原因:输水管道的起伏段,没有安装进排气阀,产生气阻爆管。
预防措施:必须在山岭管段或谷底管段设进排气阀。
排除方法:更换被破坏的管材,根据地形安装排气阀故障:4、接口渗漏原因:1、管头发生裂纹引起漏水2、管头搭接长度偏短或接头不牢固而漏水3、管件漏水排除方法:1、可用粘合剂在漏水处缠好,或把裂纹处用100目砂布打毛,涂上粘合剂,再选一块比裂纹稍长稍宽的塑料管片,用100目砂布打毛,涂上粘合剂,把管片贴在裂纹处,并左右移动一下,稍等片刻即可。
总结管件生产过程中的常见问题及解决方案
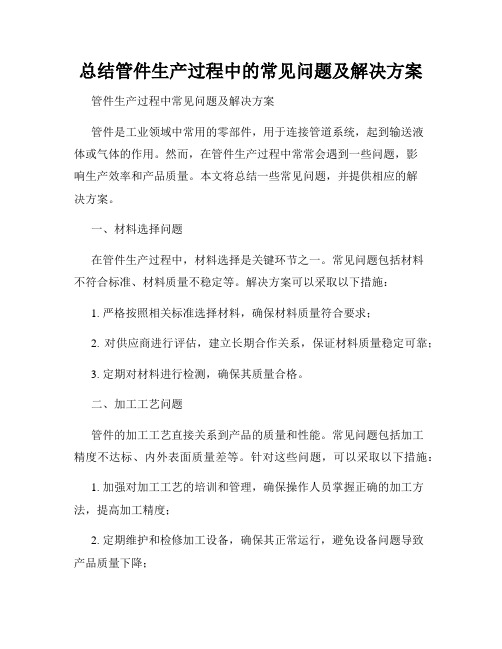
总结管件生产过程中的常见问题及解决方案管件生产过程中常见问题及解决方案管件是工业领域中常用的零部件,用于连接管道系统,起到输送液体或气体的作用。
然而,在管件生产过程中常常会遇到一些问题,影响生产效率和产品质量。
本文将总结一些常见问题,并提供相应的解决方案。
一、材料选择问题在管件生产过程中,材料选择是关键环节之一。
常见问题包括材料不符合标准、材料质量不稳定等。
解决方案可以采取以下措施:1. 严格按照相关标准选择材料,确保材料质量符合要求;2. 对供应商进行评估,建立长期合作关系,保证材料质量稳定可靠;3. 定期对材料进行检测,确保其质量合格。
二、加工工艺问题管件的加工工艺直接关系到产品的质量和性能。
常见问题包括加工精度不达标、内外表面质量差等。
针对这些问题,可以采取以下措施:1. 加强对加工工艺的培训和管理,确保操作人员掌握正确的加工方法,提高加工精度;2. 定期维护和检修加工设备,确保其正常运行,避免设备问题导致产品质量下降;3. 引进先进的生产设备和技术,提高加工效率和产品质量。
三、焊接问题焊接是管件生产过程中常用的连接方法之一,然而焊接质量直接影响到管件的强度和密封性。
常见问题包括焊接接头强度不达标、焊缝气孔等。
针对这些问题,可以采取以下措施:1. 建立严格的焊接工艺规程,明确焊接参数和操作步骤;2. 进行焊工培训,提高焊接操作人员的技术水平;3. 加强焊接质量检测,对焊接接头进行超声波检测等非破坏性检测,确保焊接接头强度合格;4. 加强焊接设备和材料的管理,确保其质量和性能稳定。
四、表面处理问题管件的表面处理主要是为了增加其耐腐蚀性能和装饰效果。
常见问题包括表面处理层不牢固、外观质量不达标等。
解决方案可以采取以下措施:1. 严格按照表面处理工艺要求进行操作,确保每道工序的质量;2. 建立表面处理质量检测制度,对表面处理层进行厚度和附着力测试;3. 引进先进的表面处理设备和技术,提高表面处理效果和质量。
PVC注塑问题的改善措施(大全五篇)

PVC注塑问题的改善措施(大全五篇)第一篇:PVC注塑问题的改善措施PVC注塑件问题的改善措施(一)解決PVC件的牛屎紋和夾水紋問題,首先是必須降低熔膠射進型腔的速度,防止產生折疊波浪形或螺旋形射膠和分流等不平穩的充型。
但是,有時會因模具型腔过于寬大的原故,當射膠速度已經降到螺杆几乎都不能前进時,牛屎紋和夾水紋問題仍然未能解決,這种情況在生產中時常出现。
如果在靠近入水口前的流道上,增加一個阻水針或者加一個緩沖包,可以起到帮助降低熔膠進入型腔之速度的作用,从而能夠达到減輕注塑件的牛屎紋和夾水紋程度的目的。
對于牛屎紋和夾水紋不是特別嚴重的情況,使用這种方法再配合調機技巧,牛屎紋和夾水紋問題是可以解決的。
但是如果問題比较嚴重,就需要再配合更多的解決措施了解決PVC注塑件的牛屎紋和夾水紋難題,需要用到非常慢的射膠速度進行一級射膠。
但是因為速度太慢,熔膠在流道中運行的時間過長,熱量散失將會很大,溫度下降得太多,熔膠的流動性會大大下降,充型將变得更加困難,這樣對解決問題极為不利。
升高熔膠溫度和模具溫度是解決問題的一个改善措施。
升高熔膠溫度,可以使慢速射膠有足夠的溫度來保証熔膠的流動性,但所調高的溫度以不使PVC燒膠為前提。
如果再增加一點背壓,效果就更好。
有時我們宁愿不調太高的熔胶溫度,而多增加一點背壓。
因為增加背壓不但可以使PVC熔膠溫度更加均勻,流動性更好,而且還有升溫的作用,所以比單獨升高溫度對改善流動性會更好。
既升高熔膠溫度又加大背壓PVC會很容易造成燒膠問題。
適當升高模具溫度,可以減慢熔膠散熱的速度,确保PVC長時間的慢速充型仍能保障足夠的流動性。
因此,在注塑件不產生縮水問題的情況下,應盡可能地多升高一點模具溫度,減小泠卻水的流量或是干脆不通冷却水注塑。
總之能夠提高流動性的措施都會對解決PVC夾水紋和牛屎紋問題有好處。
此外,減少水口料的含量,增加一點擴散油等等也都會對問題的解決有幫助。
新機和优质的注塑機的改善效果都會好过残机和普通机。
聚氯乙烯(PVC)出现这些问题,该如何解决

聚氯乙烯(PVC)出现这些问题,该如何解决一、聚氯乙烯注射成型常见故障的排查·欠注故障分析及排除方法:(1)熔料温度太低。
应适当提高成型温度。
(2)成型周期太短。
应适当延长。
(3)注射压力不足。
应适当提高。
(4)注射速度太慢。
应适当加快。
(5)供料不足。
应增加供料量。
(6)模具温度太低,应适当提高。
特别是要合理设置模具的冷却回路,保持模具温度均匀。
(7)塑件形体结构设计不合理或壁太薄。
应在可能变动的情况下进行调整。
(8)浇注系统结构尺寸偏小。
应适当放大浇口和流道截面。
(9)模具排气不良。
应增加排气孔,改善模具的排气性能。
(10)模具强度不足。
应尽量提高其刚性。
·缩痕故障分析及排除方法:(1)料筒温度太高。
应适当降低料筒温度。
(2)注射压力不足。
应适当提高。
(3)保压时间太短。
应适当延长。
(4)冷却时间太短。
应适当提高冷却效率或延长冷却时间。
(5)供料不足。
应增加供料量。
(6)模具温度不均匀。
应调整模具的冷却系统,合理设置冷却回路。
(7)塑件的形体结构设计不合理,或塑件壁太厚。
应在可能变动的情况下适当调整。
(8)浇口截面积太小。
应适当加大。
·熔接痕故障分析及排除方法:(1)熔料温度太低。
应适当提高成型温度。
(2)注射压力不足。
应适当提高。
(3)注射速度太慢。
应适当加快。
(4)模具温度太低,应适当提高。
(5)浇口截面积太小。
应适当加大。
(6)模具排气不良。
应增加排气孔,改善模具的排气性能。
(7)冷料穴结构尺寸太小或位置不当。
应合理调整。
(8)原料内混入杂质。
应彻底清除异物杂质或换用新料。
(9)脱模剂用量偏多。
应尽量减少其用量。
(10)镶件设置不合理。
应适当调整。
(11)原料着色不均匀。
应选用分散性较好的着色剂,以及延长混色的搅拌时间,使原料着色均匀。
·流料痕故障分析及排除方法:(1)熔料温度太低。
应适当提高成型温度。
(2)注射压力不足。
应适当提高。
(3)保压时间太短。