第五章__挤出成型解析
挤出成型
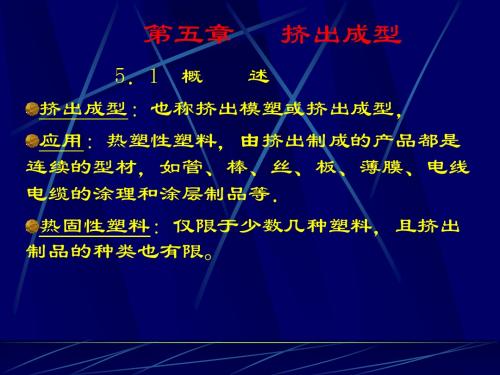
从输出工艺角度来考虑,关键是控制送料 段料筒和螺杆的温度,因为摩擦系数是随 温度而变化的,一些塑料对钢的摩擦系数 与温度的关系如图5—5所示。
如果物料与螺杆之间的摩擦力是如此之大, 以致物料抱住螺杆,此时挤出量Qs和移动速度 均为零,因为φ=0。这时物料不能向前进行, 这就是常说的“不进料”的情况。如果物料与 螺杆之间的摩擦力很小,甚至可略而不计,面 对料筒的摩擦力很大,这时物料即以很大的移 动速度前进,即φ=900。如果料在筒内开有纵 向沟槽,迫使物料沿令φ=900方向前进,这是 固体输送速率的理论上限。一般情况即是在00 <φ<900范围。在挤出过程中,如果不能控制 物料与螺杆和料筒的摩擦力为恒定值,势必引 起移动角变化,最后造成产率波动。
5.3 单螺杆挤出原理
挤出机达到稳定的产量和质量,一方面, 沿螺槽方向任一截面上的质量流率必须保持恒 定且等于产量,另一方面,熔体的输送速率应 等于物料的熔化速率。 因此,从理论上阐明挤出机中固体输送、熔化 和熔体输送与操作条件、塑料性能和螺杆的几 何结构之间的关系,无疑是有重要意义的。
5.3.1 固体输送理论 目前理论推导最为简单的是以固体对固体 的摩擦力静平衡为基础的。 基本假设: (1)物料与螺槽和料筒内壁所有边紧密接触, 形成固体塞或固体床,并以恒定的速率移动; (2)略去螺翅与料筒的间隙、物料重力和密度变 化等的影响; (3)蝶槽深度是恒定的,压力只是螺槽长度的函 数,摩擦系数与压力无关; (4)螺槽中固体物料像弹性固体塞一样移动。
图5—7所示螺槽截面上熔体膜和固体床内温 度分布情况; 熔体膜内的温度(T)分 布画数在边界条件y=o、 T=Tm和y=δ、T=Tb 时可表为:
从熔体膜进入单位界面的热量为:
固体床内的温度分布可在边界条件y=o、T=Tm和y Ts时推得为 :
挤出成型工艺—挤出成型原理(塑料成型加工课件)
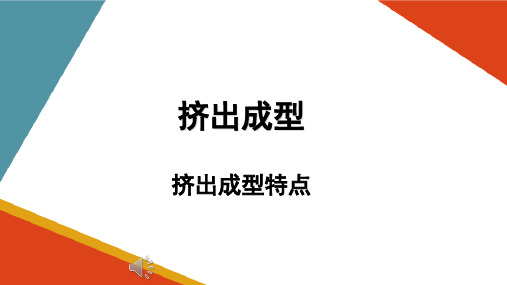
二、挤出成型过程
既有混合过 程,也有成 型过程
树脂原料 加热黏流 塑料熔体
助剂
混合过程
加压 挤出连续体
一定规格的 制品
切割 成型连续体
冷却定型
成型过程
以 管 材 挤 出 原料 成型为例
挤出连续体
熔体
定型连续体
制品
三、挤出成型特点
1. 可以连续化生产,生产效率高。 2. 设备自动化程度高,劳动强度低。 3. 生产操作简单,工艺控制容易。 4. 原料适应性强,适用大多数热塑性树脂和少数热固性 树脂。 5. 可生产的产品广泛,同一台挤出机,只要更换不同的 辅机,就可以生产不同的制品。
挤出成型
挤出成型特点
一、挤出成概述
挤出成型又叫挤出模塑,是利用加热使塑料熔融塑化成 为流动状态,然后在机械力(螺杆或柱塞的挤压)的作用下, 使熔融塑料通过一定形状的口模制成具有恒定截面连续的制 品,适用于绝大部分热塑性树脂和部分热固性树脂。
除了用于挤出造粒、染色、树脂掺和等共混改性,还可用于塑 料薄膜、网材、带包覆层的产品、截面一定、长度连续的管材、板 材、片材、棒材、打包带、单丝和异型材等塑料制品的生产。
料表面接近或达到黏流温度,表面发黏。
要求:输送能力要稍高于熔融段和均化段。
2. 压缩段 (熔融段)
位置:螺杆中部一段。 作用:输送物料,使物料受到热和剪切作用熔 融塑化,并进一步压实和排出气体。 特点:物料逐渐由玻璃态转变为粘流态,在熔 融段末端物料为粘流态。 要求:螺杆结构逐渐紧密,使物料进一步压实。
(3)横流(环流) 由垂直于螺棱方向的分速
度引起的使物料在螺槽内产生翻 转运动。对生产能力没有影响, 但能促进物料的混合和热交换。
(4)漏流 由机筒与螺棱间隙处形成的
第五章挤出成型(六讲)精品PPT课件
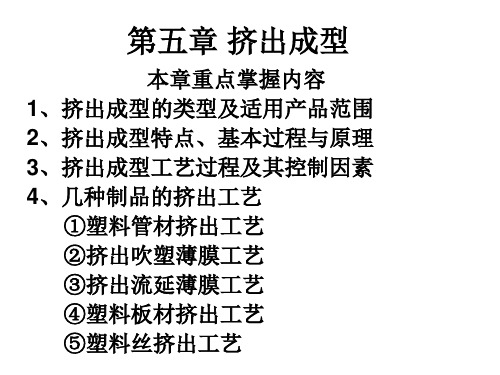
• (1)管材的挤出(P101 图 5-8)
挤出成型的主要原料有: PVC 、 PE 、 PP 、 ABS 、 PA 、 PC 等。
1、管材挤出过程
挤管成模型前头准有备: 直通式
机筒预热
加热塑化
挤出成型
偏移式(转定角径式)所用挤水出槽机冷,却应根据管材直牵引径和所需切割挤或收卷
直角式管材一般出不量需、后原处料品理种确定。同时考虑扩大再 2、挤出设备及生装产置的需要。
T ↓ , η↑ ,机头压力 ↑ ,制品致密,形状稳定, 易出现离模膨胀效应,
T ↓↓ ,塑化差,质量差。 转速 n ↑ ,剪切 ↑ ,利于塑化, η↓ ,但料筒中物 料的压力 ↑ 。
3 、定型和冷却 (同时进行)
• 管材、异型材 —— 独立的定型装置 板材、片材——压辊定型 薄膜、单丝、线缆包覆 —— 无需定型装置,直接冷却定 型。 定型方法: 管材:定径套(外径定型、内径定型) 原理:管坯内外形成压力差。使管外紧贴于套内壁冷却。 冷却速度: 硬质塑料:慢些,以避免内应力。软质塑料、结晶塑料: 快些。 (熔体粘度低)
和干燥。
干燥要求加:热器
热 风
一般塑料:水份
<
热
0.5%风
热
干燥高温下易鼓水风解机 的塑料,干燥如尼龙(
系
统纶(
PET )等:水份 过滤器
< 系统
0.03%
预热和干燥的方式:
PA
)、风 烘涤
料 斗
烘箱、烘房,可抽真空干燥,热风干燥。
热风除湿系统
加热系统
2 、塑化挤出
Байду номын сангаас• 挤出成型是连续成型工艺,关键是初期的 调整,要调整到正常挤出。 主要调整:
塑料成型工艺学课件第五章挤出成型
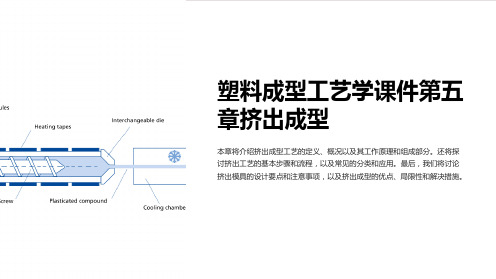
3
冷却和定型
挤出产生的热量通过冷却和定型系统使塑料固化,形成所需产品。
常见的挤出成型工艺塑料制品的生 产,如塑料管材、板材和 型材等。
2 双螺杆挤出
适用于工程塑料和特殊塑 料制品的生产,如塑料薄 壁制品和复合材料等。
3 共挤出
用于制备多层结构的复合 型材,如隔热管、隔音板 等。
常见的挤出成型缺陷及其解决措施
气泡
调整挤出机、模具和材料的参数,提高材料的 熔体温度和排气能力。
熔体中断
检查挤出机和模具的磨损和堵塞问题,确保材 料的连续供给。
螺纹纹理
调整挤出机和模具的温度、速度和压力,改善 模具的设计和制造。
尺寸不合格
优化挤出工艺参数,检查挤出机和模具的精度, 控制材料的品质。
挤出机的工作原理和组成部分
工作原理
挤出机通过将塑料材料加热、熔化、压缩和挤出, 形成连续的塑料型材或薄壁制品。
组成部分
挤出机主要由进料系统、加热和熔融系统、挤出系 统以及冷却和定型系统等组成。
挤出工艺的基本步骤和流程
1
进料和预热
塑料料粒经过熔融预热系统加热和软化,准备挤出。
2
熔融和挤出
熔化塑料通过螺杆在挤出机筒内熔融,然后被挤出模具形成型材。
挤出模具的设计要点和注意事项
挤出模具的设计需要考虑材料流动性、产品形状和尺寸、模具结构等因素。合理设计模具可以提高挤出成型的 质量和效率。
优点和局限性:挤出成型工艺的优势和限制
优点
高生产效率、产品外观光滑、成型质量稳定、无需 二次加工等。
局限性
对于某些复杂形状的产品来说,挤出成型可能无法 满足要求。
塑料成型工艺学课件第五 章挤出成型
本章将介绍挤出成型工艺的定义、概况以及其工作原理和组成部分。还将探 讨挤出工艺的基本步骤和流程,以及常见的分类和应用。最后,我们将讨论 挤出模具的设计要点和注意事项,以及挤出成型的优点、局限性和解决措施。
挤出成型原理
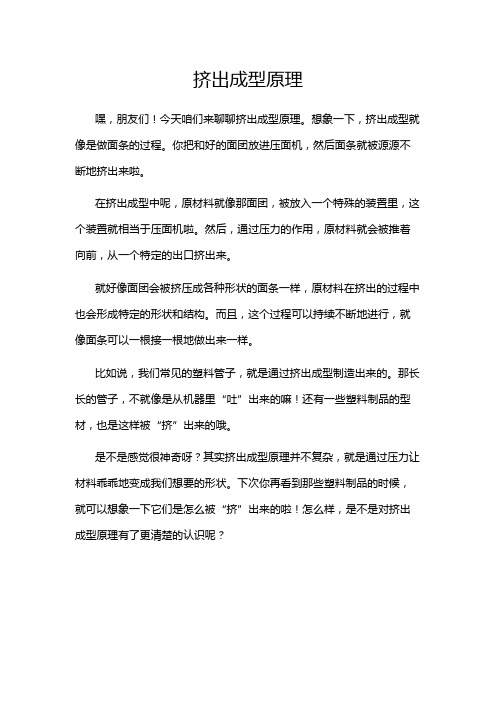
挤出成型原理
嘿,朋友们!今天咱们来聊聊挤出成型原理。
想象一下,挤出成型就像是做面条的过程。
你把和好的面团放进压面机,然后面条就被源源不断地挤出来啦。
在挤出成型中呢,原材料就像那面团,被放入一个特殊的装置里,这个装置就相当于压面机啦。
然后,通过压力的作用,原材料就会被推着向前,从一个特定的出口挤出来。
就好像面团会被挤压成各种形状的面条一样,原材料在挤出的过程中也会形成特定的形状和结构。
而且,这个过程可以持续不断地进行,就像面条可以一根接一根地做出来一样。
比如说,我们常见的塑料管子,就是通过挤出成型制造出来的。
那长长的管子,不就像是从机器里“吐”出来的嘛!还有一些塑料制品的型材,也是这样被“挤”出来的哦。
是不是感觉很神奇呀?其实挤出成型原理并不复杂,就是通过压力让材料乖乖地变成我们想要的形状。
下次你再看到那些塑料制品的时候,就可以想象一下它们是怎么被“挤”出来的啦!怎么样,是不是对挤出成型原理有了更清楚的认识呢?。
挤出成型工艺与模具结构讲解
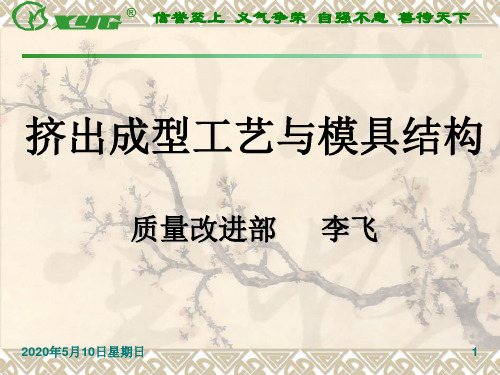
1.加热阶段
经过炼胶处理的胶料原料由挤出机料斗加入料 筒后,在料筒温度和螺杆旋转、压实及混合作用下, 由固态的粒状或粉状转变为具有一定流动性的均匀 熔体。
2019年6月9日星期日
5
® 信誉至上 义气争荣 自强不息 善待天下
挤出成型的工艺过程
2.挤出成型阶段
均匀加热的胶料熔体随螺杆的旋转向料筒前端移动, 在螺杆的旋转挤压作用下,通过一定形状的口模而 获得与口模形状一致的型材。
影响挤出速度的因素有很多,如料筒的结构、 螺杆转速、加热冷却系统的结构和塑料的性能等。 在挤出机结构和胶料品种及胶条类型确定的情况下, 挤出速度与螺杆转速有关,因此调整螺杆转速是控 制挤出速度的主要措施。
2019年6月9日星期日
11
® 信誉至上 义气争荣 自强不息 善待天下
挤出成型工艺参数
4.牵引速度
通过牵引的胶条可根据使用要求在切割装置上 裁剪或在卷取8
® 信誉至上 义气争荣 自强不息 善待天下
挤出成型工艺参数
1.温度
温度是挤出成型中的重要参数之一。严格地说, 挤出成型温度应该是指料筒中的胶料熔体温度,但 是该温度在很大程度上取决于料筒和螺杆的温度, 所以,在实际生产中为了检测方便,经常用料筒温 度近似表示成型温度。
挤出成型胶条的截面形状均取决于挤出模具, 所以,挤出模具设计的合理性,是保证良好的挤出 成型工艺和挤出成型质量的决定因素。
2019年6月9日星期日
13
® 信誉至上 义气争荣 自强不息 善待天下
挤出成型模具的结构组成
1.机头
机头是挤出塑料制件成型的主要部件,它的作 用是将来自挤出机的熔融塑料由螺旋运动转变为直 线运动,并进一步塑化,产生必要的成型压力,保 证塑件密实,从而获得截面与口模形状相似的型材。 下面以典型的管材挤出成型机头为例,介绍机头的 结构组成。
第5章+挤出成型2
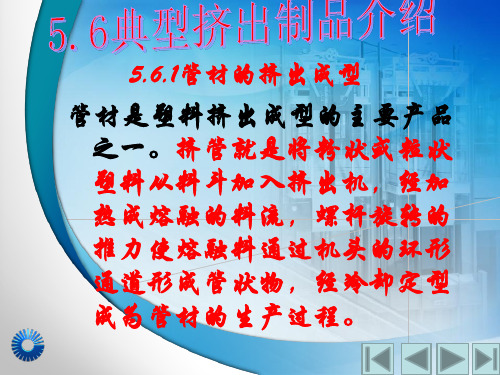
1.2挤出过程之牵引
牵引装置
4.牵引装置
橡胶带式:适合50-150mm管 滚轮式:<100m管 履带式:二履带、三履带、四履带和六履带,适合各种管。
5.6.1.2挤出过程之牵引
履带式牵引排列方式
履带的排列
a-六条履带 b-二条履带 c-三条履带 1-履带 2-塑料管材
挤出过程之牵引 履带式牵引机实物照片
5.6.1管材的挤出设备
机头附件:
分流器(鱼雷头)将圆柱形料流变为薄环状并 便于进一步加热塑化。大型分流器内设加热器, 支架用以支承分流器及芯棒,同时使料流分束 以加强搅拌,小型分流器与芯棒做为一体
5.6.1管材机头种类
(直通式、直角式、旁侧式和筛孔板式) 1)直通式 熔体在机头中流动方向与螺杆轴向一致,结 构简单易制造;适于PVC,PE,PA
当吹塑材料为结晶塑料薄膜时管膜刚离开模头时是透明的至一定的高度由于冷却而结晶固化变得不透明浑浊浑浊与透明的交界线被称1适当提高或降低加工温度对固体输送率没有影响2机头压力大小对单螺杆挤出机的单位时间产量无关3在异向旋转双螺杆中物料是以正位移原理向前强制输送与螺杆与物料的摩擦系数无关因此输送效率是极4由于同向平行双螺杆转动而反复强迫物料转向使物料受到较好的剪切混合效果这种螺杆具有很好的自洁作用一般用于混料造粒
管材挤出成型常见故障的排查
拉破或拉断 故障分析及排除方法: 如果牵引过程中,管壁上产生小洞,主要是由于冷却定 型环的供水太少。应适当增加供水量。 若管壁上拉出大洞,主要是由于压缩空气供气量太 大。应合理调节压缩空气供给量。 若牵引太快,管材容易拉断。应合理控制牵引速度。
5.6.1管材的挤出成型流程实物图
牵引 切割 挤出机
5.6.1管材的挤出设备(机头、 1 机头:
挤出成型的基本原理

挤出成型的基本原理
挤出加工是一种常见的塑料加工方法,通过这种方法可以将塑料熔化后挤压成所需的形状。
其基本原理是利用挤出机将塑料加热到熔化状态后,通过螺杆的旋转将熔融塑料推送至模具中,最终形成所需的产品。
挤出成型有很广泛的应用,可以用于生产管材、板材、型材等各种各样的塑料制品。
在挤出加工过程中,首先需要将塑料原料加入到挤出机的供料口,随后通过加热系统将原料加热到熔点以上,使其变成熔融状。
挤出机内部的螺杆会旋转推动熔融的塑料向前挤压,同时增加一定的压力,使得塑料通过机筒中的螺旋槽顺利地进行挤出。
螺杆的设计和转速会影响挤出速度和压力,不同的产品需要不同参数的螺杆来实现最佳挤出效果。
在向前挤压的过程中,熔融的塑料会经过模头并通过模具的形状渐渐固化,最终在模具的出口处成型。
模具的设计决定了最终产品的形状和尺寸,通过更换不同的模具可以生产出多样化的产品。
挤出成型是一种连续生产的工艺,可以实现高效率的生产,适用于大批量的产品加工。
在挤出加工中,还可以通过添加不同的填料、颜色或添加剂来改变塑料的性质,以实现不同特性的塑料制品。
这种方法可以有效地提高塑料制品的功能性和美观性,满足不同客户的需求。
同时,挤出成型相对于其他成型方法来说成本较低,能够快速地进行生产,具有较高的经济效益。
总的来说,挤出成型作为一种常见的塑料加工方法,具有简单易行、高效快速、成本低廉等优点,广泛应用于塑料制品的生产领域。
通过合理的设计和控制,挤出加工可以满足各种不同形状和性能要求的塑料制品的生产需求,为塑料行业的发展提供了重要的技术支持。
1。
- 1、下载文档前请自行甄别文档内容的完整性,平台不提供额外的编辑、内容补充、找答案等附加服务。
- 2、"仅部分预览"的文档,不可在线预览部分如存在完整性等问题,可反馈申请退款(可完整预览的文档不适用该条件!)。
- 3、如文档侵犯您的权益,请联系客服反馈,我们会尽快为您处理(人工客服工作时间:9:00-18:30)。
✓料筒:包裹在螺杆外部的装置,起到受热受压 的作用,物料的塑化和加热、加压都在其中进 行,大部分都有冷却装置(风、水冷);
✓螺杆:利用它才能使料筒内的塑料向前移动, 得到加压和热量(摩擦热);
①螺杆的直径(D)和长径比(L/D),长径 比决定了体积容量以及塑化的均匀性。
※ 对机头结构的要求:
Ⅰ. 口模定型部分应有适当长度。 A. 使物料处于稳定流动; B.减小熔体弹性和出口膨胀; C. L长,产量提高; D.太长,笨重,阻力大,Q降低。 Ⅱ.机头中过渡部分应光滑,呈流线型。 原因:防止物料的停滞和分解。
Ⅲ. 应设置调节装置,改善周边的流率分布。(厚度均匀)
5.2.2 挤出机的辅助设备
5.1 挤出设备
• 由挤出机、机 头和口模、辅 机等组成。
主要设备
5.1.1 单螺杆挤出机的组成
单螺杆挤出机主要 由传动系统、加料 系统、塑化系统、 加热与冷却系统、 控制系统等组成。
挤出系统是最主要 的系统,它由料筒、 螺杆、多孔板和过 滤网组成。
单螺杆挤出机的结构
✓传动系统:是带动螺杆转动的部分,通常由电 机、减速机构以及轴承等组成;
※物料处理设备 主要指预热干燥等设备
※挤出物处理设备 主要指冷却、牵引、切割、卷取、检测设 备
※控制生产工艺的设备 主要指各种测控设备
5.2.2 挤出机的一般操作方法
※设备调试 ※安全 ※清洗
5.3 单螺杆挤出原理
学习目标:
掌握挤出理论中影响生产和产品质量的因素
5.3 单螺杆挤出工作原理
5.3.1 固体输送
稳定流动时,Fs= Fbz,则Asfs=Abfbcosφ
①Fs= Fbz=0,物料在料筒中不能发生任何流动。 ② Fs> Fbz,物料被夹带于螺杆中随螺杆转动不产生移动。 ③ Fs< Fbz,物料能在料筒与螺杆间生相对运动。
螺槽中固体输送的理想模型(a) 和固体塞移动速度的矢量图(b)
• 假设条件:
③螺旋角和螺棱宽度(e):螺旋角取决于料粒 的形状,例如30o对应粉状, 15o左右对应 方块状,17o左右对应球状和柱状,
④螺杆头部形状:一般呈锥形,以避免在螺 杆头部停留过久而导致分解出现。
5.1.2 双螺杆挤出机的结构
典型的双螺杆挤出机的螺杆:
Colombo螺杆; 锥型双螺杆; 组合型双螺杆;
螺杆的主要参数:
D:螺杆外径; d:螺杆根径; L:螺杆长度;
t:螺距;
W:螺槽宽度; ε:压缩比
e:螺纹宽度 ; h:螺槽深度; φ:螺旋角;
L/D:长径比。
② 螺杆形式和分段
最常用的是等距不等深螺杆
1-渐变型(等距不等深) 2-渐变型(等深不等距) 3-突变型 4-鱼雷头螺杆 Ⅰ-加料段(固体输送段) Ⅱ-压缩段(熔融段) Ⅲ-计量段(均化段)
5.2.2 机头和口模
※圆孔口模 主要用来生产棒材、单丝造粒,口模平直部
分长度和直径比小于10 ※扁平口模
一般用来生产厚度小于0.25mm的膜或板材 ※环形口模
一般用来生产管材、管状薄膜、吹塑用型胚以及 电线电缆 ※异形口模 主要用来挤出不同横截面的制品
※ 过滤板(网)的作用:
Ⅰ. 使物料由螺旋运动转变为平直运动。 Ⅱ. 过滤杂质和未熔化好的塑料颗粒。 Ⅲ. 使物料受到较大的剪切作用,以利于塑料塑化均匀。 Ⅳ. 使料筒和机头定位。
①物料与螺槽和料筒壁紧密接触形成固体塞(床),以 恒速移动;
②略去物料重力、密度变化的影响;
③磨擦系数恒定,压力是螺槽长度的函数;
④螺槽为矩形
• 经过分析可看出物料的运动类似螺母运动。 • 提高固体输送的措施
① 适当提高螺杆转数N和螺槽深度H; ② 采用锥形结构料筒;在加料段料筒内壁开设纵向沟槽
(提高fb);冷却进料段防止物料提前软化; ③小冷fs却)螺杆加料段(减小fs),增加螺杆表面光洁度(减
定义:挤出成型又叫挤塑、挤压、挤出模 塑。是借助螺杆或柱塞的挤压作用,使塑化 均匀的塑料强行通过口模而成为具有恒定 截面的连续制品。
挤出管材生产
管材挤出的辅助设备
挤出片材生产
挤出线缆包覆成型
挤出吹塑薄膜
挤出中空吹塑成型
塑料挤出成型工艺流程
• 挤出过程:
加料——在螺杆中熔融塑化——机头口模挤出— —定型——冷却——牵引——切割
加料段具有输送固体物料,兼有预压、预热 作用。 要使制品质量、产量稳定,须满足以下两 个条件:
1. 熔体的输送速率等于固态物料的熔化速率 2. 沿螺杆轴向任一截面物料的质量流率等于 挤出机生产率 目前对此理论的推导最为简单的是以固体对 固体的摩擦力静平衡为基础的。
物料在该段类似于“弹性固体塞”,固体 塞在螺槽内的运动就如螺帽在螺丝上的运 动一样。
挤出成型的特点:
① 连续化,效率高,质量稳定 ② 应用范围广
③ 设备简单,投资少,见效快 ④ 生产环境卫生,劳动强度低 ⑤ 适于大批量生产
适用的树脂材料:
绝大部分热塑性塑料及部分热固性塑料,如PVC、 PS、ABS、PC、PE、PP、PA、丙烯酸树脂、环氧树 脂、酚醛树脂及密胺树脂等
应用:
料薄膜、网材、带包覆层的产品、截面一定、长度 连续的管材、板材、片材、棒材、打包带、单丝和异 型材等等,还可用于粉末造粒、染色、树脂掺和等。
① 如旋转螺丝,而螺帽上无压力,则 螺帽跟着螺丝转动而不前移。
② 若在螺帽上加一定压力,再旋转螺 丝,则螺帽就会随螺丝旋转而前移。
成型时,塑料与螺杆的摩擦力应小于塑 料与料筒的摩擦力,也即螺杆的光洁度应 大于料筒的光洁度。否则,塑料只能抱着 螺杆空转打滑不能前移。
固体塞摩擦模型
受力分析
由上图知:Fb= PAbfb,Fs= PAsfs ,Fbz=AbfbPcosφ。
第五章 挤出成型
内容简介:
挤出成型是借助螺杆的挤压作用,使塑化均匀的塑 料强行通过机头(口模)而成为连续的制品,如管材、 板材、丝、薄膜、电线电缆等。挤出成型是塑料成型 加工的重要方法之一。根据对塑料的加压方式不同, 可分为连续式和间歇式;按塑料的塑化方式不同可分 为干法和湿法两种。
本章重点:
1.单螺杆挤出原理 2. 几种制品的挤出工艺:吹塑薄膜、管材、拉伸产品、 板与片、其它产品