第七章 挤出成型(2)
合集下载
第七章 高分子材料的成型加工技术PPT课件

物料在压力推动下通过口模而成为连续 型材
b.挤出过程
熔融:外部加热和内部摩擦热作用下, 逐渐熔化成熔体
成型:通过口模时在压力下成为与口模 相似的连续体
定型:在外部冷却下连续体被凝固定型
图 18-2 单 螺 杆 挤 出 机 基 本 结构 示 意 图
c.特点及应用 生产效率高,可自动化连续生产;
酚醛树脂(PF) 环氧树脂(EP) 2.工程塑料的成型基础 成型性能:成型物料对各种成型工艺和模具结构
的适应能力 (1)塑料熔体的流变行为 流变 流动与变形 粘度 流变性的主要表现
粘度及其变化是塑料成型中最主要的参数 影响粘度的因素
a.聚合物分子量 分子量越大,粘度越大 不同成型方法对粘度要求不同 可通过添加低分子物质(如增塑剂)降低分子量 b.温度
(3)特点与应用 原料是已成型的片材或板材,属二次加工
适应性强,设备投资少,模具制造简便
要求板、片材在加工提哦案件下有较好的延展 性
主要适宜于热塑性塑料,如ABS、PMMA、 PVC、PP、PA、PC、PET等
(8)浇注成型
在室温或稍高温度下是液体的树脂,在加入固 化剂或催化剂与其它添加剂后,可在液态下浇 入模腔,通过化学反应硬化成形
(1)分类 按热行为:热塑性、热固性 按产量用途:通用塑料、工程塑料、功能塑料 (2)常用塑料 聚乙烯(PE) 聚氯乙烯(PVC) 聚丙烯(PP)
聚苯乙烯(PS) 聚甲基丙烯酸甲酯(PMMA) 氟塑料 聚酰胺(PA) 尼龙 聚碳酸酯(PC)
ABS 聚脂树脂
不饱和聚脂(UP) 饱和聚脂:PET、PBT
第七章 高分子材料的成型加工技术
1.高分子材料:以高聚物为主并加入多种添加剂 形成的材料
按用途 :塑料、橡胶、合成纤维 按热行为:热塑性、热固性 2.高分子材料生产过程
b.挤出过程
熔融:外部加热和内部摩擦热作用下, 逐渐熔化成熔体
成型:通过口模时在压力下成为与口模 相似的连续体
定型:在外部冷却下连续体被凝固定型
图 18-2 单 螺 杆 挤 出 机 基 本 结构 示 意 图
c.特点及应用 生产效率高,可自动化连续生产;
酚醛树脂(PF) 环氧树脂(EP) 2.工程塑料的成型基础 成型性能:成型物料对各种成型工艺和模具结构
的适应能力 (1)塑料熔体的流变行为 流变 流动与变形 粘度 流变性的主要表现
粘度及其变化是塑料成型中最主要的参数 影响粘度的因素
a.聚合物分子量 分子量越大,粘度越大 不同成型方法对粘度要求不同 可通过添加低分子物质(如增塑剂)降低分子量 b.温度
(3)特点与应用 原料是已成型的片材或板材,属二次加工
适应性强,设备投资少,模具制造简便
要求板、片材在加工提哦案件下有较好的延展 性
主要适宜于热塑性塑料,如ABS、PMMA、 PVC、PP、PA、PC、PET等
(8)浇注成型
在室温或稍高温度下是液体的树脂,在加入固 化剂或催化剂与其它添加剂后,可在液态下浇 入模腔,通过化学反应硬化成形
(1)分类 按热行为:热塑性、热固性 按产量用途:通用塑料、工程塑料、功能塑料 (2)常用塑料 聚乙烯(PE) 聚氯乙烯(PVC) 聚丙烯(PP)
聚苯乙烯(PS) 聚甲基丙烯酸甲酯(PMMA) 氟塑料 聚酰胺(PA) 尼龙 聚碳酸酯(PC)
ABS 聚脂树脂
不饱和聚脂(UP) 饱和聚脂:PET、PBT
第七章 高分子材料的成型加工技术
1.高分子材料:以高聚物为主并加入多种添加剂 形成的材料
按用途 :塑料、橡胶、合成纤维 按热行为:热塑性、热固性 2.高分子材料生产过程
挤出成型工艺及模具设计_课件
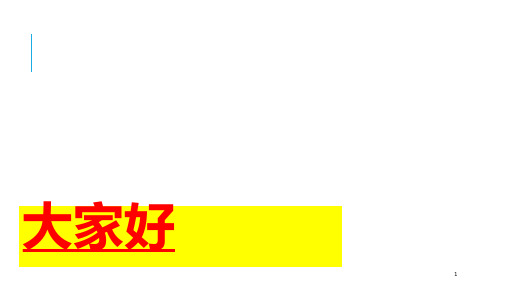
9
二、挤出成型机头概述
1. 挤出机头的作用 使熔融塑料由螺旋运动变为直线运动; 产生必要的成型压力,保证制品密实; 使塑料通过机头得到进一步塑化; 通过机头口模以获得截面形状相同、连续的塑料制品。
10
2. 机头的分类
按机头的几何形状分类 圆环机头:管材机头、棒材机头、造粒机头等 平板状机头:平模机头、板材机头、异型材机头等
内装置电热器时导入导线。
38
2. 管材的定径和冷却
为了使管材获得较低的表面粗糙值、准确的尺寸和几何 形状,管材离开口模时,必须立即进行定径和冷却,由定 径套来完成。
有两种方法: ❖ 外径定型 ❖ 内径定型
我国塑料管材标 准大多规定外径为基 本尺寸,故国内较常 用外径定型法。
39
(1)外径定型 适用于管材外径尺寸精度要求高、外表面粗糙度要求低的
按机头进出料方向分类 水平直通式机头 直角式机头
按机头的用途分类 吹膜机头、管材机头、板材机头、棒材机头、异型材 机 头等。
11
3.挤出机头的组成(以直通式管材机头为例)
口模 芯棒 分流器和分流器支架 机头体 过滤网和过滤板 连接部分 定径套
12
① 口模和芯棒 ② 挤出模的主要成型零件,口模用来成型塑件的外表
41
(2)内径定型
通过定径套内的循环水冷却定型 特点:保证管材内孔圆度,操作方便;宜用于直角式挤管机头
和旁侧式挤管机头。
适用:内径尺寸要求准确、圆度要求高的情况。
1-管材 2-定径芯模 3-芯棒 4-回水流道
5-进水管 6-排水管 7-进水嘴
42
定径芯长度:与管材壁厚及牵引速度有关,一般取80~ 300mm,牵引速度和壁厚大时,取大值。反之,取小值。 定径芯直径:一般比管材内径直径大2%~4%,始端比终端 直径大,锥度为0.6:100~1.0:100。
二、挤出成型机头概述
1. 挤出机头的作用 使熔融塑料由螺旋运动变为直线运动; 产生必要的成型压力,保证制品密实; 使塑料通过机头得到进一步塑化; 通过机头口模以获得截面形状相同、连续的塑料制品。
10
2. 机头的分类
按机头的几何形状分类 圆环机头:管材机头、棒材机头、造粒机头等 平板状机头:平模机头、板材机头、异型材机头等
内装置电热器时导入导线。
38
2. 管材的定径和冷却
为了使管材获得较低的表面粗糙值、准确的尺寸和几何 形状,管材离开口模时,必须立即进行定径和冷却,由定 径套来完成。
有两种方法: ❖ 外径定型 ❖ 内径定型
我国塑料管材标 准大多规定外径为基 本尺寸,故国内较常 用外径定型法。
39
(1)外径定型 适用于管材外径尺寸精度要求高、外表面粗糙度要求低的
按机头进出料方向分类 水平直通式机头 直角式机头
按机头的用途分类 吹膜机头、管材机头、板材机头、棒材机头、异型材 机 头等。
11
3.挤出机头的组成(以直通式管材机头为例)
口模 芯棒 分流器和分流器支架 机头体 过滤网和过滤板 连接部分 定径套
12
① 口模和芯棒 ② 挤出模的主要成型零件,口模用来成型塑件的外表
41
(2)内径定型
通过定径套内的循环水冷却定型 特点:保证管材内孔圆度,操作方便;宜用于直角式挤管机头
和旁侧式挤管机头。
适用:内径尺寸要求准确、圆度要求高的情况。
1-管材 2-定径芯模 3-芯棒 4-回水流道
5-进水管 6-排水管 7-进水嘴
42
定径芯长度:与管材壁厚及牵引速度有关,一般取80~ 300mm,牵引速度和壁厚大时,取大值。反之,取小值。 定径芯直径:一般比管材内径直径大2%~4%,始端比终端 直径大,锥度为0.6:100~1.0:100。
第七课 挤出成型

按照加压方式的不同, 按照加压方式的不同,挤出工艺又可分为连续和间歇两 种。前一种所用设备为螺杆式挤出机;后一种为柱塞式挤出 前一种所用设备为螺杆式挤出机; 机。 螺杆式挤出机又可分为单螺杆挤出机和多螺杆挤出机。 螺杆式挤出机又可分为单螺杆挤出机和多螺杆挤出机。 螺杆式挤出机是借助于螺杆旋转产生的压力和剪切力, 螺杆式挤出机是借助于螺杆旋转产生的压力和剪切力, 使物料充分塑化和均匀混合,通过型腔(口模)的成型; 使物料充分塑化和均匀混合,通过型腔(口模)的成型;因而 使用一台挤出机就能完成混合、塑化和成型等一系列工序, 使用一台挤出机就能完成混合、塑化和成型等一系列工序, 进行连续生产。 进行连续生产。 柱塞式挤出机主要是借助拄塞压力, 柱塞式挤出机主要是借助拄塞压力,将事先塑化好的物 料挤出口模而成型。料筒内物料挤完后柱塞退回, 料挤出口模而成型。料筒内物料挤完后柱塞退回,待加入新 的塑化料后再进行下一次操作,生产是不连续的.而且对物 的塑化料后再进行下一次操作,生产是不连续的. 料不能充分搅拌、混合,还得预先塑化, 料不能充分搅拌、混合,还得预先塑化,故一般已不采用此 法,仅用于粘度特别大、流动性较差的塑料,如硝酸纤维素 仅用于粘度特别大、流动性较差的塑料, 塑料等成型。
压缩段(迁移段)的作用是压实物料, 压缩段(迁移段)的作用是压实物料,使物料由固体转化为熔融 并排除物料中的空气;为适应将物料中气体推回至加料段、 体,并排除物料中的空气;为适应将物料中气体推回至加料段、压 实物料和物料熔化时体积减小的特点, 实物料和物料熔化时体积减小的特点,本段螺杆应对塑料产生较大 的剪切作用和压缩。为此,通常是使螺槽容积逐渐缩减, 的剪切作用和压缩。为此,通常是使螺槽容积逐渐缩减,缩减的程 度由塑料的压缩率(制品的比重/塑料的表观比重)决定。 度由塑料的压缩率(制品的比重/塑料的表观比重)决定。压缩比除 与塑料的压缩率有关外还与塑料的形态有关,粉料比重小, 与塑料的压缩率有关外还与塑料的形态有关,粉料比重小,夹带的 空气多,需较大的压缩比(可达4—5),而粒料仅2.5—3。 5), 空气多,需较大的压缩比(可达4 5) 而粒料仅2 3 压缩段的长度主要和塑料的熔点等性能有关。 压缩段的长度主要和塑料的熔点等性能有关。熔化温度范围宽 的塑料,如聚氯乙烯150℃以上开始熔化,压缩段最长, 的塑料,如聚氯乙烯150℃以上开始熔化,压缩段最长,可达螺杆全 150℃以上开始熔化 100% 渐变型) 熔化温度范围窄的聚乙烯(低密度聚乙烯105 105— 长100%(渐变型),熔化温度范围窄的聚乙烯(低密度聚乙烯105 120℃,高密度聚乙烯125—135℃) 45—50 120℃,高密度聚乙烯125 135℃)等,压缩段为螺杆全长的45 50 125 135℃)等 压缩段为螺杆全长的45 %;熔化温度范围很窄的大多数聚合物如聚酰胺等, %;熔化温度范围很窄的大多数聚合物如聚酰胺等,压缩段甚至只 熔化温度范围很窄的大多数聚合物如聚酰胺等 有一个螺距的长度。 有一个螺距的长度。
挤出成型—挤出理论(高分子成型课件)

塔莫尔(Tadmor)研究结果: 计算出熔融区长度,但与实际值有一定差距。
四、挤出机的挤出理论
3 熔体输送理论 流动流动状态:
①正流Qd:沿正轴向口模/机头方向流动。由旋转螺杆挤压造成。 ②逆流Qp:沿正方向相反,由机头压力引起。 ③横流Qt:环流。不影响总流量。但对熔体的混合、塑化、热交换起重要 作用。 ④漏流Qc 物料在螺杆与机筒之间间隙向加料口方向回流,可降低挤出量 。一般情况下漏流Qc很小,但磨损严重时,漏流Qc增加急剧增加。
p在挤出过程中,由于螺杆 和料筒机构、机头、过滤 网以及过滤板的阻力,使 塑料内部存在压力。
p压力可以提高挤出熔体的混合均匀性和稳定性,提高产品致密 度, 是塑料变为均匀熔体并得到致密塑件的重要条件之一。 p螺杆转速的变化,加热、冷却系统的不稳定都对产生压力波动 产生影响,对制品质量产生不利影响。 p为保证制品质量,应尽可能减少压力的波动。
六、挤出工艺的影响因素
3 挤出速率
p挤出速率因素影响较多(机头阻力、螺杆与料筒结构、螺杆转速、 加热冷却系统和塑料特性等)但主要与螺杆转速有关,提高转速,可 提高挤出产量,但塑化质量不高,因而挤出速率要大小合适。 p挤出速率在生产过程中也存在波动现象,挤出速率的波动影响制品 几何形状和尺寸。生产中应保证挤出速率的稳定。
LDPE 15~20 3~4 90~100 100~140 140~160 140~160
PP
22~25 2.5~4 140~160 165~185 180~200 160~185
PC
16~25 2.5~3 200~240 240~250 230~255 200~22100
六、挤出工艺的影响因素
2 压力
tan tanb
四、挤出机的挤出理论
四、挤出机的挤出理论
3 熔体输送理论 流动流动状态:
①正流Qd:沿正轴向口模/机头方向流动。由旋转螺杆挤压造成。 ②逆流Qp:沿正方向相反,由机头压力引起。 ③横流Qt:环流。不影响总流量。但对熔体的混合、塑化、热交换起重要 作用。 ④漏流Qc 物料在螺杆与机筒之间间隙向加料口方向回流,可降低挤出量 。一般情况下漏流Qc很小,但磨损严重时,漏流Qc增加急剧增加。
p在挤出过程中,由于螺杆 和料筒机构、机头、过滤 网以及过滤板的阻力,使 塑料内部存在压力。
p压力可以提高挤出熔体的混合均匀性和稳定性,提高产品致密 度, 是塑料变为均匀熔体并得到致密塑件的重要条件之一。 p螺杆转速的变化,加热、冷却系统的不稳定都对产生压力波动 产生影响,对制品质量产生不利影响。 p为保证制品质量,应尽可能减少压力的波动。
六、挤出工艺的影响因素
3 挤出速率
p挤出速率因素影响较多(机头阻力、螺杆与料筒结构、螺杆转速、 加热冷却系统和塑料特性等)但主要与螺杆转速有关,提高转速,可 提高挤出产量,但塑化质量不高,因而挤出速率要大小合适。 p挤出速率在生产过程中也存在波动现象,挤出速率的波动影响制品 几何形状和尺寸。生产中应保证挤出速率的稳定。
LDPE 15~20 3~4 90~100 100~140 140~160 140~160
PP
22~25 2.5~4 140~160 165~185 180~200 160~185
PC
16~25 2.5~3 200~240 240~250 230~255 200~22100
六、挤出工艺的影响因素
2 压力
tan tanb
四、挤出机的挤出理论
第七章 挤出成型

而汇集于熔池。
同时,固体床又 以一定的速度沿Y方
向移向分界面,加以
补充形成新的熔膜, 以保证状态稳定。
(2)相迁移面 熔化区内固体相和熔体相的界面称为相迁移面。熔
化发生在相迁移面上。
(3)熔化长度 从熔化开始到固体床的 宽度降到零为止的螺槽总长。 熔化速度越高,熔化长度越 短。
(4)模型假设 ▲ 挤出过程是稳定的。 ▲ 固体床是均匀的连续体。
螺杆的直径D 螺杆的压缩比A 螺杆角 θ 螺杆与料筒的间隙
螺杆的长径比L/Ds 螺槽深度H 螺纹棱部宽度E
▲ 螺杆的直径D
代表挤出机的规格。D ,挤出机的生产能力 。 ▲ 螺杆的长径比L/Ds (15~25)
影响挤出机的产量和挤出质量(衡量塑化效率)。
L/Ds ,塑料的停留时间 ,混合塑化效果 。 ▲ 螺杆的压缩比A (2~5) A=螺杆第一螺槽的容积/螺杆最后螺槽的容积 A的获得:等距变深,等深变距,变深变距。
直角式机头
偏移式机头
挤薄膜、线缆包复物、吹塑制品。
共挤薄膜、共挤型材、共挤吹塑。
五、传动系统
包括带动螺杆转动的电机和机械传动部件。
六、附属设备
▲ 塑料的输送、预热、干燥等预处理装置。
▲ 挤出后制品的定型、冷却装置。 ▲ 牵引装置。 ▲ 卷绕或切割装置。 ▲ 控制设备等。
另外,附属设备因制品的不同而不同。 如:挤出-吹塑。
第七章 挤出成型
一、概述 挤出成型在高分子材料加工领域中,是一个变化众多,
用途最广,比重最大的成型工艺。
挤出过程是使高分子材料的熔体在挤出机的螺杆挤压 作用下,通过具有一定形状的口模而连续成型,所得制品 为恒定截面的连续型材。 挤出成型制品 三大合成材料的挤出,没有本质上的区别,所用设备加 工原理大同小异。挤出理论、工艺以塑料为多,故本节主要 讨论塑料的挤出成型。
挤出成型和注射成型PPT课件

43
塑料工艺
螺杆头部结构
• 要注意防止出现 熔融塑料积存、 回流现象。
• 一般η大的塑料, 用锥行尖头;η小 的塑料,必须装 止逆环以防回流。
44
塑料工艺
• 作用:
–保持较高注射压 力和速度,使物 料进一步塑化.
• 类型:
–直通式、自锁式、 杠杆针阀式等。 物料粘度大,热 稳性差,用大口 径直通式;粘度 小,用自锁式和 杠杆针阀式。
34
塑料工艺
注射成型产品示例
35
塑料工艺
二、注射成型原理
36
塑料工艺
注射机的分类
根据塑化方式不同分为: 柱塞式注射机 螺杆式注射机
37
塑料工艺
• 螺杆式注射机
38
塑料工艺
• 柱塞式注射机特点: – 结构简单、但压力损失大、塑化不均匀以, 不适合热敏性塑料。
• 实际应用: – 目前工厂中广泛使用的是螺杆式注射机, 60g以下的小型制件多用柱塞式。
波动, 由于熔融过程的不稳定性产生低频波动, 温控系统的稳定性差或环境因素的变化引起的 波动。 3. 混合效果差
不能很好适应一些特殊塑料的加工或混炼、 着色工艺过程。
20
四、新型螺杆
塑料工艺
1、排气式螺杆 用于含水和易产生挥发组分的物料 排气原理:物料到排气段时已基本塑化,由于该段 螺槽突然加深,压力骤降,气体从熔体中逸处,从 排气口排出。
17
塑料工艺
熔体输送能力的分析
• 熔体的输送 Q = Qd - Qp - Ql, 实际的流动形式为:熔 体沿螺槽螺旋前进。类似弹簧缠绕在螺槽内。
• 忽略Ql,经计算熔体输送能力为:
① 机头阻力加大P↑,Q↓产量下降。 ② 转速N↑,Q↑提高。 ③ 螺杆直径增加D↑,Q↑↑产量明显增加。所以要得 到
塑料工艺
螺杆头部结构
• 要注意防止出现 熔融塑料积存、 回流现象。
• 一般η大的塑料, 用锥行尖头;η小 的塑料,必须装 止逆环以防回流。
44
塑料工艺
• 作用:
–保持较高注射压 力和速度,使物 料进一步塑化.
• 类型:
–直通式、自锁式、 杠杆针阀式等。 物料粘度大,热 稳性差,用大口 径直通式;粘度 小,用自锁式和 杠杆针阀式。
34
塑料工艺
注射成型产品示例
35
塑料工艺
二、注射成型原理
36
塑料工艺
注射机的分类
根据塑化方式不同分为: 柱塞式注射机 螺杆式注射机
37
塑料工艺
• 螺杆式注射机
38
塑料工艺
• 柱塞式注射机特点: – 结构简单、但压力损失大、塑化不均匀以, 不适合热敏性塑料。
• 实际应用: – 目前工厂中广泛使用的是螺杆式注射机, 60g以下的小型制件多用柱塞式。
波动, 由于熔融过程的不稳定性产生低频波动, 温控系统的稳定性差或环境因素的变化引起的 波动。 3. 混合效果差
不能很好适应一些特殊塑料的加工或混炼、 着色工艺过程。
20
四、新型螺杆
塑料工艺
1、排气式螺杆 用于含水和易产生挥发组分的物料 排气原理:物料到排气段时已基本塑化,由于该段 螺槽突然加深,压力骤降,气体从熔体中逸处,从 排气口排出。
17
塑料工艺
熔体输送能力的分析
• 熔体的输送 Q = Qd - Qp - Ql, 实际的流动形式为:熔 体沿螺槽螺旋前进。类似弹簧缠绕在螺槽内。
• 忽略Ql,经计算熔体输送能力为:
① 机头阻力加大P↑,Q↓产量下降。 ② 转速N↑,Q↑提高。 ③ 螺杆直径增加D↑,Q↑↑产量明显增加。所以要得 到
挤出成型工艺学习培训资料(课件)

决定塑料的塑化及挤出效率
小:剪切速率高,利于传热和塑化,但挤出生产效率低
热敏性塑料——深槽螺杆 热稳定性较高、熔体粘度低——浅槽螺杆 H1≥0.1 DS H3=0.02-0.06 DS
(5)螺旋角 θ=10°-30°
定义:螺纹与螺杆横截面之间的夹角 θ大,挤出机的生产能力提高,但螺杆对塑料的剪切
我国各塑料机械厂生产之挤出机料筒壁厚
我国生产的挤出机的料筒壁厚
螺杆直径:30 45 60 90 120 150 200 料筒壁厚:20—25 20~25 30-45
40—45 40-50 40一50 50—60
锥形双孔机筒
三. 螺杆
作用:输送、挤压、剪切 用耐热、耐腐蚀、高强度的合金钢制作 表面高硬度、高光洁度 转速10-120 rpm、无级变速
用于挤出塑料制品,如管材、板材、棒材、片材、 薄膜。各种异型材以及塑料和其它材料的复合物等, 也常用于塑料的着色、混炼、塑化、造粒及塑料的 共混改性等。
橡胶挤出——压出 合成纤维——螺杆挤出纺丝 塑料挤出——主要以热塑性塑料为主
2 挤出成型的特点
操作简单,工艺易控,可连续化、工业化、自动化生产, 生产效率高
第一节 单螺杆挤出机基本结构及作用
传动系统 挤出系统——挤出成型系统的关键部分
加料装置、料筒、螺杆、机头、口模 加热系统:采用电阻丝加热,也可电感应加热,
蒸汽或油加热。 冷却系统:空冷或水冷,其作用是防止进料口处
的物料过热发粘,出现搭桥现象,使 物料供料不足。另外在紧急停车时, 避免物料过热降解。
应用范围广,广泛应用于塑料、橡胶、合成纤维的成型 加工,也常用于塑料的着色、混炼、塑化、造粒及塑料 的共混改性等。
挤出—吹塑成型,中空吹塑制品 挤出—拉幅成型,双轴拉伸薄膜
小:剪切速率高,利于传热和塑化,但挤出生产效率低
热敏性塑料——深槽螺杆 热稳定性较高、熔体粘度低——浅槽螺杆 H1≥0.1 DS H3=0.02-0.06 DS
(5)螺旋角 θ=10°-30°
定义:螺纹与螺杆横截面之间的夹角 θ大,挤出机的生产能力提高,但螺杆对塑料的剪切
我国各塑料机械厂生产之挤出机料筒壁厚
我国生产的挤出机的料筒壁厚
螺杆直径:30 45 60 90 120 150 200 料筒壁厚:20—25 20~25 30-45
40—45 40-50 40一50 50—60
锥形双孔机筒
三. 螺杆
作用:输送、挤压、剪切 用耐热、耐腐蚀、高强度的合金钢制作 表面高硬度、高光洁度 转速10-120 rpm、无级变速
用于挤出塑料制品,如管材、板材、棒材、片材、 薄膜。各种异型材以及塑料和其它材料的复合物等, 也常用于塑料的着色、混炼、塑化、造粒及塑料的 共混改性等。
橡胶挤出——压出 合成纤维——螺杆挤出纺丝 塑料挤出——主要以热塑性塑料为主
2 挤出成型的特点
操作简单,工艺易控,可连续化、工业化、自动化生产, 生产效率高
第一节 单螺杆挤出机基本结构及作用
传动系统 挤出系统——挤出成型系统的关键部分
加料装置、料筒、螺杆、机头、口模 加热系统:采用电阻丝加热,也可电感应加热,
蒸汽或油加热。 冷却系统:空冷或水冷,其作用是防止进料口处
的物料过热发粘,出现搭桥现象,使 物料供料不足。另外在紧急停车时, 避免物料过热降解。
应用范围广,广泛应用于塑料、橡胶、合成纤维的成型 加工,也常用于塑料的着色、混炼、塑化、造粒及塑料 的共混改性等。
挤出—吹塑成型,中空吹塑制品 挤出—拉幅成型,双轴拉伸薄膜
挤出成型 ppt课件

第一节 挤出成型概论
3. 挤出成型制品多
(1)管、棒、膜、丝、板、网、带等。 (2)各种异型材,如楼梯扶手、塑料门窗等。 (3)中空制品,如桶、灯笼、包装容器等。 (4)电线、电缆等。 (5)为压延成型喂料,造粒等。
第一节 挤出成型概论
三. 挤出成型的优点: 1.设备制造容易,成本低,塑料加工厂的投资少 2.可以连续化生产,生产效率高 3.设备的自动化程度高,劳动强度低 4 . 生产操作简单,工艺控制容易 5 . 挤出产品均匀、密室,质量高 6 . 原料的适应性强,大多数热塑性材料 ,少量热固性材
料 7 . 生产的产品广泛,可一机多用,同一台挤出机,只需更
换辅机,就 可以生产不同制品 8. 生产线占地面积小,且生产环境清洁 四. 挤出成型的缺点: 1.不能生产三维尺寸的制品 2.制品往往需要二次加工
• 五、挤出机的分类
• 挤出机的分类:随着挤出机用途的增加,出现了各种 挤出机,分类方法很多。
第一节 挤出成型概论
• 5、后处理(热处理和调湿处理) 在挤出成型大截面尺寸的管材、棒材和异型材时, 常出挤出物内外冷却降温速度相差较大而使制品 内具有较大的内应力。具有较大内应力的挤塑制 品在成型后应及时进行热处理以消除内应力,否 则存放过程中或机械加工时会出现裂纹,严重时 制品开裂。PA之类吸湿性强的挤出制品,在空气 中使用或存放的过程中因吸湿而明显膨胀,但这 种吸湿膨胀过程需要很长时间才能达到平衡,为 加速这类挤塑制品的吸湿平衡,常需在成型后进 行凋湿处理。
迁移面
塑料在挤出机中的状态及流动
• 熔体输送—计量段(均化段) 正流、逆流、漏流、横流
塑料熔体在螺槽中混合流动示意图
熔体在螺槽内的流速分布图
(1)正流(拖曳流动) :流体沿着螺槽向机头方