FEM Analysis On A Rear Axle Housing Oil-Leakage Prediction Of Four-Wheel Farm Transporters On COSMOS
Analysis of the axle fracture of the bucket wheel excavator

Analysis of the axle fracture of the bucket wheel excavatorMile Savkovic´a ,⇑,Milomir Gašic ´a ,Miodrag Arsic ´b ,Radovan Petrovic ´a aUniversity of Kragujevac,Faculty of Mechanical Engineering Kraljevo,Dositejeva 19,36000Kraljevo,Serbia b Institute for Testing Materials IMS,Bulevar Vojvode Mišic´a 43,11000Belgrade,Serbia a r t i c l e i n f o Article history:Received 4May 2010Received in revised form 27September 2010Accepted 28September 2010Available online 27October 2010Keywords:Bucket wheel excavator Bucket wheel axle Failure analysis Experimental testinga b s t r a c tThe common design of the bucket wheel drive mechanism in some bucket wheel excava-tors (BWE)consists of a gearbox and a hollow shaft,while the bucket wheel is supported bythe axle passing through the hollow shaft.Improper maintenance and inadequate elimina-tion of axis misalignment of the hollow shaft and the bucket wheel axle are the maincauses of excavator failure and axle fracture.The paper examines the causes of bucketwheel axle fractures.Experimental testing of the chemical composition and mechanical properties of thematerial used to make the bucket wheel axle and metallographic inspections of the frac-ture surfaces in the bucket wheel axle by means of electronic and light microscope carriedout in the first part of the paper have shown that there are no significant inhomogeneitiesand errors in the material of the axle.The second part of the paper presents the FEM analysis of influences of disturbances onthe manner of support of the bucket wheel axle on the fracture.It shows that the negativeinfluences of support of the axle reflected through the increase in the stress concentrationand occurence of the initial crack are the main causes of the axle fracture.Ó2010Elsevier Ltd.All rights reserved.1.IntroductionDigging and depositing of layers of materials in open pit mines are most frequently performed by bucket wheel excava-tors (BWE).BWE SRs 2000.32/5.0+VR92(Fig.1a)is used in the open pit mine in ‘‘Kolubara”–Serbia.After more than 40,000h of exploitation of the BWE SRs 2000.32/5.0+VR92(Fig.1a)during a period of ten years,there occurred a fracture of the bucket wheel axle (Fig.1b and c),which caused the failure of the BWE.Since the digging drive in the BWE represents a subsystem of vital importance for the reliability in operation and stability of the BWE,research into the cause of the fracture of the bucket wheel axle is of particular significance [1].For the mentioned BWE,the largest diameter of the axle is 550mm,the length is 4500mm,the mass is 5934kg and the frequency of rotation is 4.394min À1.The bucket wheel axle was made by forging.The gearbox of the mass ffi51,000kg is connected to the bucket wheel by means of the hollow shaft.Additional support of the gearbox on the bucket wheel axle through the hollow shaft is accomplished through the sliding bushing (Fig.2).After the BWE had been exploited for more than 10years,at the end of 2006there occurred pronounced misalignment between the hollow shaft and the bucket wheel axle,which was most noticeable in the zone of the hollow shaft ending.Without prior analysis of the cause of misalignment between the hollow shaft and the bucket wheel axle,the user,wishing to solve the problem that had arisen,inserted a split bronze bushing in the zone of the hollow shaft ending (Fig.2).1350-6307/$-see front matter Ó2010Elsevier Ltd.All rights reserved.doi:10.1016/j.engfailanal.2010.09.031⇑Corresponding author.Tel.:+38136383392;fax:+38136383380.E-mail address:savkovic.m@mfkv.kg.ac.rs (M.Savkovic´).2.Examination of the causes of fracture of the bucket wheel axleAfter more than 8500h of exploitation of the BWE,there occurred a fracture of the bucket wheel axle.For the purpose of investigating the causes of the fracture,an experimental procedure was carried out and it covered the examination of the chemical composition and mechanical properties of the material [2],visual and metallographic inspection of the fracture surface on the axle as well as the analysis of the stress state of the bucket wheel axle.2.1.Experimental procedureAccording to the manufacturer’s data,the bucket wheel axle is made of steel 30CrMoV9V.Samples for analysis of the chemical composition and preparation of test pieces for examination of the mechanical properties of the bucket wheel axle were taken from the points presented in Fig.3b.The results of examination of the chemical composition of the samples taken at the point of fracture are shown in Table 1.The test results of the mechanical properties of the bucket wheel axle are shown in Table 2.The hardness of the material of the axle is appropriate,in compliance with the requirements for the mentioned type of steel,i.e.259–260HB 5/750.The measured hardness at the point of fracture in the longitudinal and lateral directions shows that there is no significant scattering and that it is uniform for all samples taken at the points marked in Fig.3b.excavator SRs 2000.32/5.0+VR92:(a)outlook of BWE,(b)bucket wheel axle before the failure and (c)bucket2.2.Visual and metallographic examinationFor the purpose of obtaining as realistic a picture of the fracture surface on the bucket wheel axle as possible,besides visual examination,stereoscopy was performed.Metallographic examination was made using Axiovert25,ZEISS.Fracto-graphic examinations were made using SEM JOEL JSM-5800.The fatigue fracture initiation on the bucket wheel axle of the BWE SRs 2000.32/5.0+VR92is shown in Fig.4.The en-larged initial crack is shown in Fig.5,and the structure of the material in the longitudinal section in the polished and etched states with non-metallic inclusions,in the zone of fatigue failure,is presented in Fig.6.The enlarged crack in the material in the zone of plastic fracture is shown in Fig.7,and the structure of the material of the longitudinal section in the polished and etched states with fractures in the zone of plastic fracture is shown in Fig.8.2.3.Discussion of the results of the examinationThe results of examination of the samples taken at the point of the bucket wheel axle fracture have shown that the chem-ical composition and mechanical properties correspond to the quality of steel 30CrMoV9V (according to DIN 17200;1987).The external appearance of the fracture surface (Figs.3and 4)indicates the fracture was due to material fatigue in which characteristic signs of tearing can be seen [3–5].The fatigue fracture initiation can also be clearly seen (Fig.4).The state of the structure of material of the bucket wheel axle is improved.The analysis of the microstructure of the material of the bucket wheel axle in the lateral and longitudinal sections has shown that there is slight anisotropy,i.e.the inclusions shown are slightly elongated.By examining the micro strength in the cross section on the sample surface,it was established that there was no decarburization according to ASTM 381standard.The performed experimental procedure of testing the chemical composition and mechanical properties of the material,as well as the visual and metallographic examination of the fracture surface on the axle,show that the fracture did not occur due to an error in the material.3.Calculation of the stress stateThe analysis of the stress state of the bucket wheel axle was carried out by applying the FEM method [6–8].By the anal-ysis ANSYS program was used [9].According to the project documentation (case 1),the axle support was realized through bearings A and B with the existence of contact between the axle and the hollow shaft through the sliding bushing C (Figs.2Fig.2.Position of the bucket wheel axle within the bucket wheel drive.and 9a ).The user having inserted the split bronze bushing,the new additional contact D between the axle and the hollow shaft was formed (Fig.9b).By synthesis of 3D models of all structural parts,a 3D model of the bucket wheel axle was built (Fig.10).The model represents a continuum discretized by 10-node tetrahedral elements [6]for the purpose of creating an FEM model (45124nodes,25016elements).surface on the bucket wheel axle:(a)general look and point of transition from plastic fracture into the zone of brittle for examination.Table 1The results of examination of the chemical composition of the samples taken at the point of fracture.Elements (%)C Si S P Mn Cr Mo V Prescribed values 30CrMoV9V DIN17200;1987from 0.28max max max 0.40 2.300.150.10to 0.350.400.0300.0350.70 2.700.250.20Values obtained by testing 0.290.230.0160.0150.59 2.350.230.19Table 2The test results of the mechanical properties of the bucket wheel axle.Elements (%)R p 0,2(N/mm 2)R m (N/mm 2)A 5(%)K (J)Prescribed values 30CrMoV9V DIN17201;1987from min 800min min to 5909501435Values obtained by testing 60280117.544In compliance with the norms defined by the German code[10],the analysis of the bucket wheel axle was carried out for static(H1a)and variable(H1b)loads.The variability of digging resistance is the source of variable loads,which leads to the occurrence of dynamic inter-actions and impacts at the point of contact between the bucket wheel axle and the hollow shaft relized through the bushing.The uniaxial stressfield,according to the Huber-Hencky-von Mises hypothesis[11–13],for case1of the load,is presented in Fig.11.The maximum value of the uniaxial stress was obtained for case2,in the zone of support,Fig.12.3.1.Discussion about the results of the FEM analysisOn the basis of the FEM results,it can be concluded that:The stress state for case2is considerably more unfavourable.Due to the additional support,there occurs the stress con-centration in the zone of contact between the axle and the hollow shaft by means of the bushing.The level of the stress state in the zone of axle fracture for the case of additional support of the hollow shaft on the bucket wheel axle is very high.The values of uniaxial stresses,at the point of support are3.1times higher than the stresses for the basic case of load.The degree of safety of the axle in the characteristic section for case1of support is S¼r yr eq;max;I ¼613114¼5:4,while for case2S¼r yr eq;max;II ¼613498¼1:23.of fatigue fracture initiation on the bucketFig.7.The enlarged crack in the material in the zone of plastic fracture.longitudinal section in the polished and etched states with cracks,in9.Model of supports of the bucket wheel axle:(a)case1and(b)caseM.Savkovic´et al./Engineering Failure Analysis18(2011)433–441441 4.ConclusionOn the basis of the presented research results,the following conclusions can be made:The chemical composition and mechanical properties of the material from which the bucket wheel axle is made are within the prescribed limits for steel30CrMoV9V(according to DIN17200;1987).The metallographic examination of the fracture surface show that the fracture did not occur due to any errors in the material.Elimination of the misalignment between the bucket wheel axle and the hollow shaft of the gearbox,realized through the additional split bronze bushing,resulted in considerable increase in uniaxial stresses in the bucket wheel axle.That increase is3.1times higher than the stress without any additional supports,where the degree of safety of the axle at that point decreased from5.4to1.23,which is the main cause of the bucket wheel axle fracture.The bucket wheel axle fracture is caused by improper elimination of axis misalignment of the bucket wheel axle and the hollow shaft which resulted in:-An increased stress concentration in the bucket wheel axle,-A triple increase of uniaxial stresses in the axle,-A quadruple decrease of the degree of safety of the axle.References[1]Kowalczyk M,Czmochowski J,Rusinski E.Construction of diagnostic models of the states of developing fault for working parts of the multi-bucketexcavator.Maint Reliab2009;2(42):17–24[In Polish].[2]Rusinski E,Czmochowski J,Iluk A,Kowalczyk M.An analysis of the causes of a BWE counterweight boom support fracture.Eng Fail Anal2010;17:179–91.[3]Failure analysis and prevention.ASM handbook,vol.11.Metals park,Ohio:ASM International;2002.[4]Brooks RC.Metallurgical failure analysis.New York:McGraw-Hill;1993.[5]Fry PR.Loads and stresses–the real cause of failures in surface mining machinery.J Fail Anal Prev2003;3(2):7–14.[6]Rusinski E,Harnatkiewicz P,Kowalczyk M,Moczko P.Examination of the causes of a bucket wheel fracture in a bucket wheel excavator.Eng Fail Anal2010;17:1300–12.[7]Rusinski E,Czmochowski J,Moczko P.Failure reasons investigations of dumping conveyor breakdown.J Achieve Mater Manuf Eng2007;23(1):75–8.[8]Yin Y,Grondin GY,Obaia KH,Elwi AE.Fatigue life prediction of heavy mining equipment.Part2:behaviour of corner crack in steel welded box sectionand remaining fatique life determination.J Constr Steel Res2008;64:62–71.[9]Göksenli A,Eryürek IB.Failure analysis of an elevator drive shaft.Eng Fail Anal2009;16:1011–9.[10]Design fundamentals of large-scale equipment in open pit mine(Berechnungsgrundlagen für Großgeräte in Tagebauen).Düsseldorf:Der Minister fürWirtschaft und Verkehr des Landes Nordhein-Wesstfalen;1960.[11]Bošnjak S,Zrnic´N,Simonovic´A,Momcˇilovic´D.Failure analysis of the end eye connection of the bucket wheel excavator portal tie-rod support.Eng FailAnal2009;16:740–50.[12]Rusinski E,Czmochowski J,Moczko P.Half-shaft undercarriage systems-designing and operating problems.J Achieve Mater Manuf Eng2009;33(1):62–9.[13]Rusinski E,Harnatkiewicz P,Bobyr B,Yakhno B.Caterpillar drive shaft damage causes analysis.Arch Civ Mech Eng2008;VIII(3):117–29.。
霍尼韦尔 全自动流量分析仪说明手册说明书

THE NEEDSEvides Waterbedrijf required measurement of turbidity and flow to monitor water quality in the distribution network and manage the network. Until recently, this data had been recorded manually and analysed with outdated equipment. This process no longer fitted with the strategic pillar “digitising primary processes” which was an important aim of the Netherlands water provider. Evides Waterbedrijf developed an all-in-one measuring device which allowed them to make all distribution network measurements. During the measurement process, turbidity, flow and GPS location were all recorded and logged in real-time from the field. This data could be used to determine water quality of the distribution network, assess the effectiveness of previously implemented drainage actions and continue to optimise drainage plans. The process being largely automated. The flow meter was part of the total standpipe solution which was lightweight and easy to dismantle in the field.THE SOLUTIONTo support the needs of EvidesWaterbedrijf, Honeywell Smart Energyoffered their Q4000 electromagneticmeter as part of the standpipe solution.Featuring high quality design andengineering, Honeywell’s Q4000electromagnetic water meter is builtfor maintaining highly accurateperformance and lasting durabilityin demanding environments.With an unrestricted flow tube with nomoving parts and a 10-year batterylife, the Q4000 offers unrivalledperformance for an electromagneticwater meter. Delivering consistentaccuracy over a wide flow-ratemeasuring range, the meter can beadapted to suit either predominantlyhigh or low flow rates, and is ideal fordistribution network applications.The Q4000 is a high-performingelectromagnetic meter, ideal for networkmanagement and leakage monitoring.HON EYWELL’SW A TER M ETERCase StudySupports Accurate Real-Time Distribution Network AnalysisGood quality water supply is provided for the entire population in the Netherlands. Water consumption is one of the lowest in developed countries at 128 litres per capita per day and water leakage in the distribution network is one of the lowest in the world at only 6%.The Q4000 water meter forms part of the total standpipe solution.The Q4000 from Honeywell Smart Energy is a high-performing electromagnetic meter, ideal for bulk flow metering applications such as network management and leakage monitoring.-It has a fast continuous sampling rate, providing highly accurate and reliable measurement.-The Q4000’s extremely tough stainless steel constructionensures a long working life, while its lightweight body makes storage, transportation and installation both simpler and safer.-With an unrestricted flow tube, the Q4000 ensures minimal pressureABOUT EVIDES WATERBEDRIJFEvides Waterbedrijf supplies safe and clean drinking water 24 hours a day, 365 days a year to 2.5 millioncustomers and the business community in Zeeland, in the South West of Holland and the Brabantse Wal.Additionally, Evides Waterbedrijf offers tailor-made industrial water services to large industrial customers in the Netherlands, Belgium and Germany.THE BENEFITSloss, even at the highest flowrates, resulting in reduced network system pressures, helping to prevent leakage from burst pipes. -A large, bright and easy-to-read LCD, showing volume and instantaneous flow rate, is ideal for real-time network control and water management. -With the Q4000’s 10-yearcontinuous battery life and no need for calibration, expensive regular maintenance is a thing of the past. -With bi-directional pulse outputs, the Q4000 provides dependable connectivity to critical water management systems including AMR and data logging devices.All rights reserved.The company’s policy is one of continuous product improvement and the right is reserved to modify the specifications contained herein without notice. These products have been manufactured with current technology and in accordance with the applicable referenced standards.SS-20-2 ENG | 02/20© 2020 Honeywell International Inc.For more informationElster Water Metering Ltd130 Camford Way Sundon Park, Luton Bedfordshire, LU3 3AN United Kingdom T +44 1582 846400F +44 1582 564728*************************。
ross elementary analysis 2ed solution -回复

ross elementary analysis 2ed solution -回复Ross Elementary Analysis 2nd Edition SolutionIntroduction:Elementary Analysis is a branch of mathematics that deals with the study of real numbers and functions. The Ross Elementary Analysis 2nd Edition Solution is a comprehensive guide to the study of this important subject. In this article, we will explore the main topics covered in the Ross Elementary Analysis 2nd Edition Solution and provide a step-by-step guide to solve the problems that are found in the book.Chapter 1: The Real NumbersThe first chapter of the Ross Elementary Analysis 2nd Edition Solution covers the basics of the real numbers. It includes topics such as the properties of the real numbers, the Archimedean property, and the density of the rational numbers in the real numbers. The following are some of the problems found in this chapter.Problem 1: Prove that if x and y are positive real numbers, then x + y > 2 √xy.Solution:Let x and y be positive real numbers. Then, by the AM-GM inequality we have,x + y > 2 √(xy)Thus, x + y > 2 √xy, as required.Problem 2: Prove that if a and b are positive real numbers, then (a + b)²> 4ab.Solution:Let a and b be positive real numbers. Then,(a + b)²= a²+ 2ab + b²By the AM-GM inequality, we have,(a²+ b²)/2 ≥√(a²b²)a²+ b²≥2abThus,a²+ 2ab + b²> 4ab(a + b)²> 4abChapter 2: SequencesThe second chapter of the Ross Elementary Analysis 2nd Edition Solution covers the study of sequences. It includes topics such as the convergence and divergence of sequences, the Cauchy criterion, sub-sequences, and the monotone convergence theorem. The following are some of the problems found in this chapter.Problem 1: Determine whether the sequence {an} = (−1)n/n converges or diverges.Solution:The sequence {an} = (−1)n/n diverges because the limit of the absolute values of the terms is equal to lim an = lim 1/n = 0, which is not equal to zero.Problem 2: Determine whether the sequence {an} = (5n −3)/(3n + 7) converges or diverges.Solution:The sequence {an} = (5n −3)/(3n + 7) converges. To see this, we can divide the numerator and denominator of the sequence by n, and we get{an} = (5 −3/n)/(3/n + 7/n)Since both the numerator and denominator converge to 5/3 as n →∞, the original sequence {an} also converges to 5/3.Chapter 3: Limits and ContinuityThe third chapter of the Ross Elementary Analysis 2nd Edition Solution covers the study of limits and continuity. It includes topics such as the definition of limits, one-sided limits, continuity, and the intermediate value theorem. The following are some of the problems found in this chapter.Problem 1: Find the limit of the function f(x) = (x²−3x + 2)/(x −2) as x approaches 2.Solution:If we try to use direct substitution to find the limit, we get an indeterminate form of 0/0. However, we can factor the numerator to getf(x) = ((x −2)(x −1))/(x −2)Then, we can cancel out the (x −2) terms to getf(x) = x −1Therefore, the limit of f(x) as x approaches 2 is 1.Problem 2: Prove that the function f(x) = x²cos(1/x) is not continuous at the point x = 0.Solution:To prove that the function f(x) = x²cos(1/x) is not continuous at x = 0, we need to show that there exists an ε> 0 such that for any δ> 0, there exists an x in the interval (0, δ) or in the interval (−δ, 0) such that f(x) −f(0) > ε.Choose ε= 1 and consider any δ> 0. Let x = 1/(2nπ), where n is a positive integer. Then,f(x) −f(0) = x²cos(1/x) −0 = 1/(4n²π²)cos(2nπ) = 1/(4n²π²)As n →∞, f(x) −f(0) →0, which implies that there exists no δ> 0 such that for any x in the interval (0, δ) or in the interval (−δ, 0), f(x) −f(0) > 1. Therefore, f(x) is not continuous at x = 0.Conclusion:The Ross Elementary Analysis 2nd Edition Solution is an excellent resource for anyone interested in learning about elementary analysis. By studying the topics covered in this book and working through the problems, one can gain a deep understanding of the concepts of real numbers, sequences, limits, and continuity. With a clear understanding of these fundamental concepts, one can then move on to more advanced topics in mathematics.。
某型重卡平衡悬架结构综合优化设计

某型重卡平衡悬架结构综合优化设计冯琦;王宗彦;王凡;陆春月【摘要】针对某型重卡平衡悬架结构存在V型推力杆安装困难和结构冗余、质量大的问题,根据企业需求,改铆接横梁为整体铸造式横梁并且不改变原有平衡轴支架铸造工艺的前提下,对其结构进行综合优化设计.为满足制造工艺和装配工艺要求,先确定了其基础结构模型;以此为优化对象,在极限工况下,以降低结构总质量为目标,以结构强度为约束条件,对平衡悬架系统进行拓扑优化设计;根据拓扑结果,应用形状和尺寸优化方法并结合铸造工艺和设计经验对其结构进行详细设计,得到了最终的综合优化设计结果.优化后结构,在符合企业工艺要求的同时解决了实际装配问题;在满足强度的前提下,达到了轻量化目标,这对平衡悬架的结构改进有重要的参考价值.【期刊名称】《机械设计与制造》【年(卷),期】2016(000)001【总页数】4页(P258-261)【关键词】平衡悬架;横梁;拓扑优化;综合优化;轻量化【作者】冯琦;王宗彦;王凡;陆春月【作者单位】中北大学机械与动力工程学院,山西太原030051;中北大学机械与动力工程学院,山西太原030051;中北大学机械与动力工程学院,山西太原030051;中北大学机械与动力工程学院,山西太原030051【正文语种】中文【中图分类】TH16平衡悬架是重型卡车底盘系统中重要的承载部件,其结构对重卡载重量有至关重要的影响;同时,其装配工艺性能对重卡的综合使用及维修保养有着重要的影响。
平衡悬架主要由平衡轴支架、横梁、中后桥、板簧组件和上下推力杆等组成[1],整个系统通过平衡轴支架固定在底盘车架上,推力杆传递车辆的制动力和驱动力,悬架系统整体承载着来自车身以及地面的复杂力,平衡悬架对整车的稳定性和安全性等主要性能起到重要的作用[2-4]。
因此,对平衡悬架整体结构进行综合优化,以简化装配工艺、减少整体悬架质量以及增强结构中横梁支撑的稳定性,有利于提高重卡车身载重量,提升使用性能,同时达到轻量化目的。
职称英语《理工A》阅读理解练习题及答案(2)

职称英语《理工A》阅读理解练习题及答案(2)2017职称英语《理工A》阅读理解练习题及答案参考答案36.C。
推理题。
题干:从第一段可以推断出欧洲的每个大城市都__________。
利用题干关键词可以定位到文章的第一段,该处对欧洲大城市中心区的共同点作了一个概述。
它们是否都有大广场、是否都有许多摩天大楼、是否有让旅游者和自己的配偶见面的中心,这些都没有提到。
但文章提到了当地居民和旅游者共同创造了一种令人兴奋的大都市氛围,由此可以推断,这些城市每年都吸引了大量的旅游者。
37.D。
细节题。
题干:下列有关Covent Garden表述,哪+项是不对的?利用题干关键词或者选项关键词可以定位到第三段中间,该处讲到了位手伦敦的Covent Garden。
选项A、B、C的内容在这段都可以找到,但D的内容找不到。
38.D。
细节题。
题干:为什么人们认为Venice是伟大的?利用题干关键词可以定位到第四段,即社会历史学家Joel Garreau在接受美国一本杂志采访时所说的话:“The reason people think Venice is so great is you don’t see all the mistakes…Those have all been removed.”39.B。
细节题。
题干:Parisian以什么而著名?利用题干关键词可以定位到文章的倒数第二段,首先讲了咖啡文化对保持这些城市的活力所具有的.重要性,然后说了巴黎正是如此。
巴黎市民是出了名的热衷于聊天的(famous enthusiastib conversationalists),他们喜欢边喝咖啡边聊天。
故答案为B。
40.A。
细节题。
题干:最后一段引用Duomo的例子说明。
利用题干关键词可以定位到最后一段第四句,可见作者把the Duomo作为一个例子来说明教会和社会之间的密切关系。
part CLiving on WaterDesperately short of living space and dangerously prone toflooding, the Netherlands plans to start building homes, businesses and even roads on water.With nearly a third of the country already covered by water and half of its land mass below sea level and constantly under threat from rising waters, the authorities believe that floating communities may well be the future.Six prototype wooden and aluminum floating houses are already attached to something off Amsterdam, and at least a further 100 are planned on the same estate, called Ijburg."Everybody asks why didn't we do this kind of thing before," said Gijsbert Van der Woerdt,director of the firm responsible for promoting the concept. "After Bangladesh we're the most densely populated country in the world. Building space is scarce and government studies show that we'll need to double the space available to us in the coming years to meet all our needs."Before being placed on the water and moved into position by tugboats (拖船), the houses are built on land atop concrete flat-bottomed boats, which encase giant lumps of polystyrene (聚苯乙烯) reinforced with steel. The flat-bottomed boats are said to be unsinkable and are anchored by underwater cables. The floating roads apply the same technology.The concept is proving popular with the Dutch. "The waiting list for such homes, which will cost between euros 200,000, 500,000 to buy, runs to 5,000 names," claims Van der Woerdt.With much of the country given over to market gardening and the intensive cultivation of flowers, planners have also come up with designs for floating greenhouses designed so that the water beneath them irrigates the plants and controls the temperature inside.A pilot project, covering 50 hectares of flooded land nearAmsterdam's Schiphol airport, is planned for 2005.The opportunities for innovative developers look promising. "We have 10 projects in the pipeline --floating villages and cities complete with offices, shops and restaurants," Van der Woerdt said.41. The Netherlands plans to start building floating communities on water becauseA. most parts of the country are covered by water.B. the country is constantly threatened by floods.C. it will promote the cultivation of flowers.D, people think it better to live on water.42. By citing "Everyone asks why didn't we do this kind of thing before", the author wants to tell us thatA. building floating communities is a very good idea.B. the director of the finn didn't want to answer the question.C. the Netherlands should follow the example of Bangladesh.D. people are not satisfied with the government's work.43. The floating houses will beA. reinforced with steel.B. made of concrete.C. constructed in water.D. built on boats.44. According to the author, the floating communities on waterA. can promote market gardening.B. are beyond the reach of most Dutch people.C. will increase the cost of gardening.D. will be very popular by the year of 2005.45. "10 projects in the pipeline" in the last paragraph meansA. 10 pipelines to provide gas.B. 10 companies to lay the pipelines.C. 10 floating houses to be built on water.D. 10 building projects planned and started.参考答案41.B。
洗劫机器的空气流场分析说明书

Simulation Analysis on Airflow Field of Plot Harvester Yingchun Xiao 1, a , Shuang Wang 1, Min Liao 1, Jian Liang 1 Junfu Zhang 21School of Mechanical Engineering, Xihua University, Chengdu 610039, China2Key Laboratory of Fluid and Power Machinery, Ministry of Education, Xihua University, Chengdu610039, Chinaa ****************Keywords: Plot harvester, Air-and-screen, Airflow field, CFD Simulation analysis, Fisheye sieve.Abstract . Airflow field play an important role on the cleaning performance of the air-and-screen cleaning device of the plot harvester, and an unreasonable airflow field can lead to poor cleaning quality. In order to understand the cleaning chamber airflow distribution and improve the cleaning quality of the cleaning device, the orthogonal experiment method is used for the numerical simulation on the plot harvester. The workbench is utilized to extract geometric model flow and mesh division on condition that the original shape and size of the fisheye sieve are kept. By means of CFD software FLUENT, the plot harvester airflow field is simulated and analyzed by changing the cross flow fan angle, the clear inclination of sieve and the cross flow fan speed . Test results show that the effective separation parameter is: the cross flow fan speed is 12m/s, the cross flow fan angle is 20°, and cleaning sieve angle is 6°. 1. IntroductionThe cleaning room is used as the screening environment to separate the impurity and grain, and the cleaning quality is directly related to the distribution of the airflow field in the chamber. For the plot harvester, in addition to the requirements of the low loss rate of cleaning and high cleaning rate of grain, the plot harvester with excellent performance is also required to keep a low grain residue. A lot of researches have been carried out about the main influence factors-vibration amplitude and frequency, eccentric wheel speed, scaly sieve angle etc.[1, 2] The CFD software has been used to analyze the airflow field of the cleaning device. [3, 4] But at present the airflow field simulation on fisheye sieve is scarce, and fisheye sieve, compared with other kinds of sieves (scaly sieve, plane punching sieve, knitting sieve) differs greatly. In recent years, CFD software FLUENT has been widely used in the field of agricultural equipment research, and has been recognized by researchers at home and abroad. [5-7] By means of the airflow field simulation in place of the testing device, the research and development cycle can be shortened, the cost saved, and thus manpower and material resources reduced. Therefore, the plot harvester airflow field was simulated by the software FLUENT. The airflow field analyzed with different structure parameters by orthogonal test method, the distribution and the effective separation parameters are obtained. 2. Airflow field mathematical modelGas dynamics differential control equations[8]: Continuity equation:()0i iu t x ρρ∂∂+=∂∂ (1) Navier-Stokes equation:''()()()i i i j i j i i i i ju p u u u u u S t x x x x ρρμρ∂∂∂∂∂+=-+-+∂∂∂∂∂ (2) International Conference on Mechatronics Engineering and Information Technology (ICMEIT 2016)In order to close (1), (2) equation, the RNG k ε- turbulent model control equation is adopted. The RNG k ε-turbulence model is more suitable for large eddy current field, which can reflect the complex flow field distribution more clearly.()()[()]t i k b M k i j k jk k ku G G Y S t x x x μρρμρεσ∂∂∂∂+=+++--+∂∂∂∂ (3) 2132()()[()]()t i k b i j j u C G C G C S Re t x x x k kεεεεεμεεερερεμρσ∂∂∂∂+=+++-+-∂∂∂∂ (4)Where,(1)13203C Re kημρηηεβη-=+,()2j i it k t j i ju u u k C G x x x μμρμε∂∂∂==+∂∂∂ ,22t b iM t t iTG g Y M Pr x μβρε∂==∂Where,t μ-Turbulent viscosity; k G -Turbulent kinetic energy induced by the mean velocity gradient; b G -Turbulent kinetic energy induced by the buoyancy effect; M Y -Effect of compressible turbulent expansion on the total dissipation rate; k σ-Turbulent kinetic energy corresponding to the Prandtl number; εσ-Dissipation rate corresponding to the Prandtl number; ,,i k S S S ε-Source term; β-Thermal expansion coefficients; t M -Mach number. 3. Physical model and calculation modelAs shown in figure 1, it’s the plot harvester separating cleanin g system structure diagram, where α is cross flow fan angle and β is cleaning sieve angle. The cleaning device is composed of several parts, including grain rod roller, concave beater, straw shaker, cleaning sieve, air deflector, grain collector, oscillating grain pan, cross flow fan, conveyer belt and concave grate. After crops threshing through grain rod roller threshing device, most of the wheat grains and draft stem fall on the conveyor belt and are conveyed to the cleaning sieve by oscillating grain pan. However, long straw and a small number of wheat grains are thrown by the concave beater to the straw shaker. By reciprocating motion of the oscillating grain pan, it can effectively separate the wheat grains and the broken ears from the long straws. The wheat grains and the broken ears, through the fisheye sieve hole, fall down to the cleaning sieve after the oscillations of straw shaker while the long straws are thrown to the outside. Meanwhile, the broken ears are blown away with the help of the cross flow fan, and the wheat grains and slight impurities fall to the grain collector. Because of the complexity of the clearing room, considering that the straw shaker is responsible for the long straw throwing work mostly, and the requirement of airflow between the cavity and straw shaker is low in the cavity. According to the characteristics of the axial uniform distribution of the cross flow fan air outlet,[9] when the consistency between the computation domain and the actual flow field is guaranteed the calculation domain model is simplified. The cleaning chamber cavity region along the axial width of the cross flow fan is reduced, at the same time, the region between the straw shaker and wall was canceled. As shown in Figure 2, A, B, C three points respectively represent the fisheye sieve hole center which is located in a certain section. CREO software is used to create geometric model, and workbench to extract geometric model flow and mesh division. The simplified model of the chamber cavity model is created. In order to vividly simulate airflow through fisheye sieve as much as possible, the original shape and size are retained, where height is 12mm, and length is 25 mm.[10]1. Grain rod roller2.Concave beater3.Straw shaker4. Cleaning sieve5. Air deflector6. Grain collector7.Oscillating grain pan8.Cross flow fan9.Conveyer belt 10.Concave grateFig. 1 The plot harvester separating cleaning system structure diagramFig. 2 Computational domain model of the clearing room4. Solution algorithm and initial boundary conditionThe solution is based on the pressure-based of the SIMPLEC separation algorithm, meanwhile, in order to get higher accuracy and less numerical value, second order upwind discretization scheme is adopted. Working environment is set as a standard atmospheric pressure; external boundary conditions: The air outlet of the cross flow fan is defined as the velocity inlet boundary, cleaning sieve tail export is defined as the outflow boundary, other settings are retained default values.[11] 5. Analysis on airflow field in the cleaning chamber5.1 Test principleAccording to the theory of air cleaning, we make use of the difference of the aerodynamic characteristics of the grain mixture to separate. When the updraft speed of fisheye sieve exceeds the floating speed of impurities, and less than the floating speed of grain, it can separate the grain from the mixture effectively. As shown in figure 3, the inclined airflow with velocity v is acting on the material at θ angle with the sieve surface, the material floating speed v l needs to be overcome by vertical upward flow velocity v y , satisfied v y =vsinθ, v y >v l .According to the floating speed of several different of materials in Table 1, if we want to be able to separate the impurities effectively, we need to ensure 6m/s < v y < 8.9m/s. In the process ofA pointC pointB point12346 25 αβ78910moving on the sieve surface, the grain mixture is changed from thick to thin, so, it is important to ensure the sieve surface front airflow velocity 7~8 m/s, central airflow velocity of 5~6 m/s and the rear airflow velocity of 1~2 m/s.[10]Fig. 3 Vector diagram of airflow velocityTable 1 Floating speed of several different materialsCategory F loating speed /m•s-1D ensity /g•cm-3Wheat 8.9~11.5 1.22Light weed 4.5~5.6 1.02Rice wheat husk 0.6~5 0.4Short stalk 5~6Threshed ear of wheat 3.5~55.2 Design and results of orthogonal experimentIn order to investigate the sieve surface along the length direction of fisheye sieve center airflow velocity on A point, B point and C point. The cross flow fan speed, the cross flow fan angle and the cleaning sieve angle three parameters are selected as influencing factors and orthogonal experiment are carried out with three factors and three levels. [12]The orthogonal experiment table is shown in Table 2.Table 2 Factors and levels of orthogonal experimentLevelsfactorsCross flow fan speed Cross flow fan angle Cleaning sieve angle X/ m•s-1Y/(°) Z/(°)1 10 15 22 12 20 43 15 25 6According to the L9 (34) orthogonal experiment table, 9 groups of representative combinations are arranged to carry out simulation tests in the fluent, the test groups and results are shown in table 3.Table 3 Groups and result of simulationTest numberFactors A pointairflowvelocityB point airflowvelocityC point airflowvelocity Cross flowfan speedCross flowfan angleCleaning sieveangleX/ m•s-1Y/(°) Z/(°) / m•s-1/ m•s-1/ m•s-11 10 152 5.11 5.38 1.952 10 20 4 5.73 6.32 1.683 10 25 6 5.86 7.02 1.324 12 15 4 5.91 7.15 1.955 12 206 7.25 8.14 1.536 12 25 2 5.96 6.78 2.507 15 15 6 9.39 10.20 2.018 15 20 2 7.32 8.09 2.929 15 25 4 7.91 9.33 2.305.3 Test data analysisAs shown in figure 4~6, according to the results of simulation, the speed of A, B, C three points are expressed as the change of the three factor and three level with the chart.It can be seen from Figure 4 that the airflow velocity change of the cross flow fan has obvious influence on the airflow velocity of A, B and C three points. With the airflow velocity increasing, the velocity of the cross flow fan presents an upward trend.As shown in figure 5, the influence of the cleaning sieve angle on the airflow velocity of each point is different.The airflow velocity of A and B have an upward trend with the increase of the sieve surface inclination, however, the airflow velocity of C has a decreasing trend.As shown in figure 6, when the cross flow fan angle is changed,because of the air deflector and the sieve cleaning position has not changed, the airflow velocity of three points changes little.According to the test data obtained in table 3 and the requirement of three part airflow velocity of sieve, combined with the floating speed of grain, the combination of test parameters to meet the requirements of the cleaning is determined by X 2Y 2Z 3- the cross flow fan speed is 12m/s, the cross flow fan angle is 20°, the cleaning sieve angle is 6°. As shown in Figure 7, the airflow field velocity vector diagram for the parameter combination X 2Y 2Z 3.Fig. 7 Airflow field velocity vector diagram of the cleaning roomAs shown in figure 7, under the condition of parameter combination for X 2Y 2Z 3, the airflow field is relatively smooth, at this point, the A point at a speed of 7.25 m/s, B points at a speed of 8.14 m/s, C points at a speed of 1.53 m/s. Due to the change direction of the front of the sieve surface affected by the Oscillating grain pan. A point y direction of the velocity components is less than B point y direction of the velocity components, and B point speed is less than the floating speed of wheat grains, it can effectively separate the miscellaneous and wheat grains.C pointA pointB point246810246A pointB pointC pointa i r f l o w v e l o c i t y /m •s -1Fig.5 Effect of cleaning sieve angle on airflow velocitycleaning sieve angle /(°)6.Conclusion(1)Simulation on cleaning chamber flow field is carried out by means of CFD software FLUENT, and distribution of the whole cleaning room airflow field is conducted. The three flow velocity of the surface A, B, C is respectively calculated.(2)Orthogonal simulation experiment with three factors and three levels is utilized. The test results show that: the cross flow fan speed is12m/s, the cross flow fan angle is 20°, the cleaning sieve angle is 6°, which are the best parameter combination in the experiment.(3)The analysis focuses on cross flow fan speed, cross flow fan angle, cleaning sieve angle. Other factors that affect the distribution of the airflow field (such as the air deflector angle) are not analyzed, but the ideas and theoretical basis can be provided for the further design improvement. AcknowledgmentsThis work was financially supported by the Research Project of Application Basis of Sichuan Province (2014JY0055), the Science and Technology Support Project of Sichuan Province (2015NZ0055), the Research Project of Key Laboratory of Fluid and Power Machinery (Xihua University), Ministry of Education (JYBFX-YQ-1), the Innovation Fund of Postgraduated, Xihua University (ycjj2015079).References[1]. Yifeng Zhang, Shujuan Yi. Experiment research on multi factors of air-and-screen cleaningdevice of vertical axial flow[J]. Machinery Design & Manufacture, 2012(02):30-32.[2]. Wei Tian, Shujnan Yi, Li Zhang. Experimental Research on the Air-and-screen Cleaning DeviceParameters[J]. Journal of Heilongjiang Bayi Agricultural University, 2010, 22(04):77-79. [3]. Hua Li, Meina Zhang, Wenqing Yin, et al. Optimization of Airflow Field on Air-and-screenCleaning Device Based on CFD[J]. Transactions of the Chinese Society for Agricultural Machinery, 2013, 44(z2):12-16.[4]. Quan Zhou, Yaoming Li, Hongchang Li. Impact of the Main Structural Parameters on theAirflow Field the Air and Screen Cleaning Mechanism[J]. Journal of Agricultural Mechanization Research, 2012, 34(03):29-32.[5]. Gebrehiwot M G, Baerdemaeker J D, Baelmans M. Effect of a cross-flow opening on theperformance of a centrifugal fan in a combine harvester: Computational and experimental study[J]. Biosystems Engineering, 2010, 105(2):247-256.[6]. Hongchang Li, Yaoming Li, Fang Gao, et al. CFD–DEM simulation of material motion inair-and-screen cleaning device[J]. Computers & Electronics in Agriculture, 2012, 88(2):111-119.[7]. Panneerselvam R, Savithri S, Surender G D. CFD modeling of gas–liquid–solid mechanicallyagitated contactor[J]. Chemical Engineering Research & Design, 2008, 86(12):1331-1344. [8]. Fang Li, Yaoming Li. Optimization and Simulation Research of the Airway of Tangential - axialCombine Harvester Cleaning Room[J]. Journal of Agricultural Mechanization Research, 2015(02):75-78.[9]. Xiaoqiang Du, Menghua Xiao, Xiaoqin Hu, et al. Numerrical simulation and experiment ofgas-solid two-phase flow in cross-flow grain cleaning device[J]. Transactions of the Chinese Society of Agricultural Engineering, 2014(03):27-34.[10]. Chinese Academy of Agricultural Mechanization Sciences. Agricultural Machinery DesignManual (down) [M]. China Agricultural Science and Technology Press, 2007.[11]. Pengfei Li, Minyi Xu, Feifei Wang. FLUENT GAMBIT ICEM CFD Tecplot[M]. POSTS &TELECOM PRESS, 2011.[12] .Qiyi Tang, Mingguang Feng. DPS DATA PROCESSING SYSTEM-Experiment Design,Statistical Analysis and Data Mining[M]. Science Press, 2006.。
Finite Element Analysis (FEA)
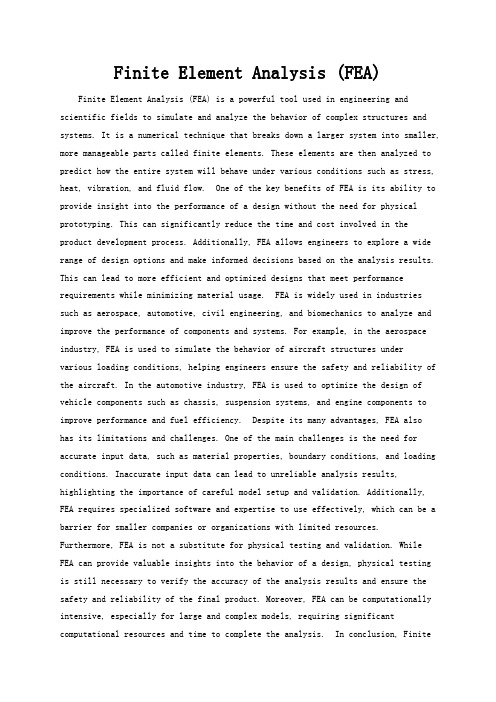
Finite Element Analysis (FEA) Finite Element Analysis (FEA) is a powerful tool used in engineering and scientific fields to simulate and analyze the behavior of complex structures and systems. It is a numerical technique that breaks down a larger system into smaller, more manageable parts called finite elements. These elements are then analyzed to predict how the entire system will behave under various conditions such as stress, heat, vibration, and fluid flow. One of the key benefits of FEA is its ability to provide insight into the performance of a design without the need for physical prototyping. This can significantly reduce the time and cost involved in the product development process. Additionally, FEA allows engineers to explore a wide range of design options and make informed decisions based on the analysis results. This can lead to more efficient and optimized designs that meet performance requirements while minimizing material usage. FEA is widely used in industries such as aerospace, automotive, civil engineering, and biomechanics to analyze and improve the performance of components and systems. For example, in the aerospace industry, FEA is used to simulate the behavior of aircraft structures undervarious loading conditions, helping engineers ensure the safety and reliability of the aircraft. In the automotive industry, FEA is used to optimize the design of vehicle components such as chassis, suspension systems, and engine components to improve performance and fuel efficiency. Despite its many advantages, FEA alsohas its limitations and challenges. One of the main challenges is the need for accurate input data, such as material properties, boundary conditions, and loading conditions. Inaccurate input data can lead to unreliable analysis results, highlighting the importance of careful model setup and validation. Additionally, FEA requires specialized software and expertise to use effectively, which can be a barrier for smaller companies or organizations with limited resources. Furthermore, FEA is not a substitute for physical testing and validation. While FEA can provide valuable insights into the behavior of a design, physical testingis still necessary to verify the accuracy of the analysis results and ensure the safety and reliability of the final product. Moreover, FEA can be computationally intensive, especially for large and complex models, requiring significant computational resources and time to complete the analysis. In conclusion, FiniteElement Analysis (FEA) is a valuable tool for engineers and scientists to simulate and analyze the behavior of complex structures and systems. It offers numerous benefits such as cost and time savings, design optimization, and insight into performance without physical prototyping. However, it also comes with its own set of challenges and limitations, such as the need for accurate input data, specialized software and expertise, and the necessity of physical testing for validation. Despite these challenges, FEA remains an essential tool in the modern engineering and scientific toolkit, enabling the development of safer, more efficient, and innovative designs.。
2-3-习题(含解答)

2-3 习题(含解答)目录第1章编译原理概述 (1)第2章PL/O编译程序的实现 (4)第3章文法和语言 (4)第4章词法分析 (13)第5章自顶向下语法分析方法 (28)第6章自底向上优先分析 (39)第7章LR分析 (42)第8章语法制导翻译和中间代码生成 (60)第9章符号表 (67)第10章目标程序运行时的存储组织 (70)第11章代码优化 (73)第12章代码生成 (76)综合练习一 (79)综合练习二 (84)综合练习三 (90)综合练习四 (95)综合练习五 (101)综合练习六 (107)第1章编译原理概述一、选择题1.一个编译程序中,不仅包含词法分析,语法分析,中间代码生成,代码优化,目标代码生成等五个部分,还应包括 (1) 。
其中, (2) 和代码优化部分不是每个编译程序都必需的。
词法分析器用于识别 (3) ,语法分析器则可以发现源程序中的 (4) 。
(1) A.模拟执行器 B.解释器 C.表格处理和出错处理 D.符号执行器(2) A.语法分析 B.中间代码生成 C.词法分析 D.目标代码生成(3) A.字符串 B.语句 C.单词 D.标识符(4) A.语义错误 B.语法和语义错误 C.错误并校正 D.语法错误2.程序语言的语言处理程序是一种 (1) 。
(2) 是两类程序语言处理程序,他们的主要区别在于 (3) 。
(1) A.系统软件 B.应用软件 C.实时系统 D.分布式系统(2) A.高级语言程序和低级语言程序 B.解释程序和编译程序C.编译程序和操作系统D.系统程序和应用程序(3) A.单用户与多用户的差别 B.对用户程序的查错能力C.机器执行效率D.是否生成目标代码3.汇编程序是将翻译成,编译程序是将翻译成。
A.汇编语言程序B.机器语言程序C.高级语言程序D. A 或者BE. A 或者CF. B或者C4.下面关于解释程序的描述正确的是。
(1) 解释程序的特点是处理程序时不产生目标代码(2) 解释程序适用于COBOL 和 FORTRAN 语言(3) 解释程序是为打开编译程序技术的僵局而开发的A. (1)(2)B. (1)C. (1)(2)(3)D.(2)(3)5.高级语言的语言处理程序分为解释程序和编译程序两种。
- 1、下载文档前请自行甄别文档内容的完整性,平台不提供额外的编辑、内容补充、找答案等附加服务。
- 2、"仅部分预览"的文档,不可在线预览部分如存在完整性等问题,可反馈申请退款(可完整预览的文档不适用该条件!)。
- 3、如文档侵犯您的权益,请联系客服反馈,我们会尽快为您处理(人工客服工作时间:9:00-18:30)。
FEM Analysis On A Rear Axle Housing Oil-Leakage Prediction Of Four-Wheel Farm Transporters Based On COSMOS SenKai LU1, 2, a,Jianhuan Su1,Shude Liao1, Jiaqiang Su1, Bo Wang1,Liang Yu3,b, Yanli Jiang3,c and Shouhong Wen2,d1 Department of Physics and Electronic Technology, Hechi University, Hechi 546300, China2 Department of Physics and Information Technology, Guilin Normal College, Guilin 541001, China3 Key laboratory of new processing technology for nonferrous metals & Materials, Ministry ofEducation, Guilin University of Technology, Guilin 541004, Chinaa lusky3616@,b syyuiang@,c jiangyanli024@,d wenshouhong0773@Keywords: Finite Element Method, Rear Axle Housing, Oil Leakage, COSMOSAbstract. A finite element method (FEM) analysis based on COSMOS study with the aim to find the causes and effects of deformations in the interface between the rear axle housing and the central gear house of the four-wheel farm transporters during operation has been performed. The present design is analyzed with the aid of a mixed-fidelity, or mixed-grain, FE-model. Boundary conditions are defined on the bushings in front of the rear axle and on the air bellows behind the rear axle. The different load scenarios are represented by forces either on the wheels, the central gear or on the rear axle housing. The simulated results showed that with the worst combined load case for the different proposed design solutions suggested that modified design with a thicker flange and a removed stiffener would be significantly better than the present design; the simulated max displacement is about 0.5 mm and satisfied the design requirement. It indicated that the proposed method of finite element analysis was a good and efficient method predicts the oil leakage of rear axle housing, which can increased the knowledge of how oil leakage from the rear axle central gearbox can be controlled by design measures.IntroductionThe four-wheel farm vehicle transporter is one of the most vital subsystems in the vehicles, which is normally composed of the engine, clutch, gearbox, shafts, and a rear axle which integrates a central differential gearbox, hub reductions and disc/drum brakes [1]. The torques in the four-wheel farm vehicle transporter from the engine as well as from the rear axle brakes are focused at the differential mounted in the rear axle bridge [2]. Elastic deformations of the gear teeth, shafts, bearings, and the housing cause undesirable side-effects, such as a dynamic transmission error. It may also cause oil leakage in the gearbox housing and cap interface [3-5]. The oil leakage problem has been also observed in the screw-joint interface between the differential housing and cap [6]. The gearbox housing consists of two parts that are mounted with guides and connected with a screw joint shown in Fig. 1(a) and Fig. 1(b). Oil leakage has been observed at severe field operations, e.g. braking with full load on rough terrain [7]. The housing contains a large amount of oil, and there is a thin sealing gasket object between the two mating surfaces, which maybe causes oil leakage, but the problems have not been fully understood [8]. Researches have been developed to prevent the oil leakage, for example, silicon, o-ring (proposed), and thin paper gasket (presently favored) sealing solutions the silicon sealing [9-11]. But o-ring is rejected for manufacturing cost reasons [10], and a thin paper basket does not complete solve the leakage problem. Tobias Lööf, et al reported that a strive for perfection in the vehicle transporters design requires that the design parameters must be carefully tuned [11].The aim of the paper was to study the deformations in the rear axle housing of four-wheel farm vehicle transporters based on the finite element method (FEM) software COSMOS and to suggest design changes that would increase the sealing capability of the favored paper gasket interface.Fig. 3 Applied loads of the rear axle housing of four-wheel farm vehiclet t MethodThe explorative nature of the study close relation between shape and behavior of the studied components justified a simulation-driven approach based on the Solidworks 2006 for composing CAD model [12], and calculated by FEM simulating software COSMOS 2006 [13]. To analyze the distribution of the contact pressure and the occurrence and the location, size and shape properties of local clearances between the mating surfaces requires a highly detailed model of the interface region and the directly related components[1, 3] .The FE- model of the rear axle housing is shown in Fig. 1(c). To actual study the sealing performance of the interface, it was decided to study static load cases defined from elementary driving operations such as wheel braking, driveshaft (pinion) torque, motor braking, rolling, vertical bending, lateral loading, longitudinal loading, and combinations of these elem entary load cases [9, 10]. It is convenient to apply those loads directly to the driveshaft, wheels, and frame. Consequently, models of the load interacting components, such as the differential gearbox, rear wheels, and the suspension units were included in the systems model. A mixed-fidelity finite element representation of the studied system is shown in figure 2(b). The total size of the systems model is 20070 nodes and 67456 elements in contact.Of simulation performance reason, these “non-focused” components were modeled as simple as possible and as detailed as judged necessary[1, 5], which implies that systems modeling were a non-routine and iterative process.Fig.1 Model of the axle housing of four-wheel farm vehicle transporter(a) Geometry , (b) Cutaway view, (c) A mixed-fidelity FE- model of the rear axle housingTo study the sealing performance of the interface, it was decided to study static load cases defined from elementary driving operations such as braking, driveshaft (pinion) torque, motor braking, rolling, vertical bending, lateral loading, longitudinal loading, and combinations of these elementary load cases [3]. Theforces defined for the elementary loading case rolling, i.e.a presentation of the centripetal forces that appear whenwe are driving in a curve shown in Fig.2. Anotherelementary load case is motor braking. In the model, braking is represented by force-pairs in the gearbox, as shown in the right portion of Fig.1 in Ref [11]. ResultsThe results can be classified into analyzed results that are clarifying the identified sealingproblem and solutions to the design problem, i.e. design proposals.a c pressur on screws case due to motor braking Rolling (left) andpinion torque (right) loadClarification of the sealing problem. Fig.3(a) shows the simulated contact pressure distribution in the targeted interface, when the screw joint is preloaded only, i.e. when there is no external loading of the system. The simulated interface clearance for a combined load case is presented in Fig.3(b). The clearance in the region identified in Fig.3(c) shows a large gradient in the radial direction of the interface. During field operations, some gasket creep resulting in a risk for oil leakage has-been observed [4] The values on screw and welded stiffener areas are 458 MPa, which are lower than that of the holding teeth.. If we compare the location of the observed gasket creep with the expected gearbox oil level and the computed clearance anomaly identified in Fig.3(b), a likely explanation of the leakage problem is that a conically shaped clearance may destroy the sealing capacity of the paper gasket at some complex driving operations [11]. It may be noted that the largest conical clearance in the identified problem region was obtained for a load case composed of rolling and 50 % of maximum drive shaft torque.Fig. 3 The simulated contact pressure distribution in the targeted interface,(a) no external loading ,(b)combined load , oil level (red line), and observed gasket creep, (c) large clearance gradientProposed design solutions. The FE-simulated displacements as a function of the applied longitudinal force, worst combined load case ,are presented in Fig.3. The observed problem is located close to a stiffened region. One proposed design solution is to reduce the influence of the stiffener by making it more slender, modifying it locally, or by removing it as shown in Fig.4(a). Examples of other proposed design solutions are to thicken the flange, or to locally alter the decrease the distance between the screws shown in Fig.4(b). Simulations with the worst combined load case for the different proposed design solutions suggested that the max displacement of rear housing, which is modified design with a thicker flange and a removed stiffener, is about 0.5 mm. It means design with a thicker flange and a removed stiffener it would be significantly better than the present design shown in Fig.4(c). An analysis of the simulated interface clearance and contact pressure results suggests that the interface gasket, and thus its sealing capacity, isdestroyed by extensive micro-sliding in interface regions where conically shaped clearances appear atcertain complex loading conditions. It means that by strengthening the central gear housings flange reduction of the conical openings can be achieved. The simulated result is conceptually similar with Ref [1,3]. However, the FEM results can only be validated with an independent method. If a rear axle housing system of farm vehicle transporter meets its specified requirements, it should be applied with physical testing. [9,11,14]. The results need to be compared with experimental results, which is also our suggestion for future work.Fig. 4 FE-simulated force-displacement relation.(a) reduced stiffness of the stiffener and increased interface stiffness, (b) thicken flange, (c) present design aagasket creepoil levelReducing siffener Max displacement 0.9~1.2 mm Present desing altered screws, Max displacement 1.0~1.5 mmlarge gradientThicken flange Max displacement0.4~0.5mmConclusions and discussionAn oil leakage problem has been observed during four-wheel farm vehicle transporter operation. The problem is located to the rear axle differential gearbox housing. An FE-based on COSMOS study with the aim to find the causes and effects of deformations in the interface between the rear axle housing and the central gear house during operation has been performed. The present design is analyzed with the aid of a mixed-fidelity FE-mode. The simulated results shown that when the rear axle housing is loaded with both interior and exterior forces it tends to locally open the interface between the rear axle housing and the central gear housing. Simulations with the worst combined load case for the different proposed design solutions suggested that the max displacement of rear housing, which is modified design with a thicker flange and a removed stiffener, is about 0.5 mm satisfied the design requirement. This design change will most likely minimize the leakage problem observed on the vehicle transporter.AcknowledgementsThis work was supported by the project named Dynamics Simulation and Experimental Research of Four-wheel farm vehicle stamping and welding-type rear axle(200911MS218), the Basic Research Fund for the Northeastern University (N090302005), the National Natural Science Foundation of China (No. 50902018, No. 50872018) and Province science and technology in the Guangxi offends pass item (1099043).References[1] Scania Home Page, , 2006.[2] T. Lööf, F.,Videll. “FEM-based design study of rear axle housing ADA1100 and central gear house R780 interface deformations”. (in Swedish), Master of Science Thesis MMK 2006:11[3] Sellgren, U., “Architecting models of technical systems for non-routine simulations”, Proc. International Conference on Engineering Design – ICED 03, Stockholm, Sweden, 2003.[4] N. Cong, J.Z. Shang, X. Chen, et al.: “International conference on measuring technology and mechatronics automation”, (2009), pp. 3–6.[5] O'Keefe, R.M., Balci, O., and Smith, E.P., Validating expert system performance, IEEE Expert, Vol.2(1987), pp. 81-90.[6] J. Schijve: Dordrecht, Netherlands: Kluwer Academic Publishers (2001), pp. 68–72.[7] S.K. Lu, J.H Su, S. D. Liao, et al., “Finite element analysis on Fatigue failure prediction of a rear axle housing of Vehicle based on Cosmos”,ICFMD,( 2011),Taiwan,(In press)[8]B.Y. Hea, S. X. Wang, and F. Gao, “Failure analysis of an automobile damper spring tower” .[9]R. Link , C. J. Deschamps,“Numerical modeling of startup and shutdown transients in reciprocating compressors”international journal of refrigeration ( 2011), pp. 1-17.(In press) [10] L.Yu, Y.L. Jiang, S. K Lu,“Numerical simulation of brake discs of CRH3 high-speed trains based on Ansys”, ICME,(2011),USA,(In press)[11] T. Lööf, F. Videll¸ and U. Sellgren, “A FEA-based design study to control run-time truck rear axle gearbox oil-leakage ”NAFEMS Seminar: Prediction and Modelling of Failure Using FEA“ May31–June 1, 2006 Copenhagen / Roskilde, Denmark[12] /sw/3d-cad-design-software.htm[13] /sw/products/10169_ENU_HTML.htm[14] M.W. Fu, H. Li, J. Lua, et al., “Numerical study on the deformation behaviors of the flexible die forming by using viscoplastic pressure-carrying medium”,Computational Materials Science Vol. 46 (2009) pp. 1058–1068.。