浅谈轻量化铝合金地铁车辆组装工艺设计
地铁车辆铝合金车体的铆接工艺

地铁车辆铝合金车体的铆接工艺随着城市化进程的加速,地铁作为城市公共交通工具的重要组成部分,扮演着连接城市各个角落的重要角色。
而地铁车辆的制造与维护则显得尤为重要。
在地铁车辆的制造中,铝合金车体的铆接工艺是其中的重要部分之一。
本文将对地铁车辆铝合金车体的铆接工艺进行介绍。
一、铝合金车体的特点铝合金车体由于其重量轻、耐腐蚀性高、表面处理方便等优点,成为地铁车辆制造的首选材料之一。
它不仅可以有效地提高车辆的装载能力,同时还可以降低车辆的整体重量。
铝合金材料还具有很好的可塑性,便于制造各种形状的车体结构。
但是铝合金车体在制造和装配过程中,需要进行大量的铆接工艺,以确保车体的整体稳定性和安全性。
1. 防腐蚀处理铝合金车体在使用过程中极易受到氧化腐蚀的影响,因此在铆接之前,需要对铝合金材料进行防腐蚀处理。
一般来说,先将铝合金表面进行清洗和除漆处理,然后进行化学氧化处理,最后再进行喷漆处理。
这样可以有效地提高铝合金材料的抗腐蚀能力,延长其使用寿命。
2. 铆接工艺铆接是在连接两个或多个金属构件时,采用钉状铆钉或铆钉组的一种连接方式。
在铝合金车体的制造中,铆接工艺是不可或缺的一部分。
在进行铆接工艺时,需要注意以下几点:(1)钣金准备:在进行铆接之前,需要对车体的钣金部件进行准备工作。
包括清洗、打磨和调整钣金部件的形状和尺寸,确保其平整度和尺寸精确度。
(2)铆接工具选择:在进行铆接工艺时,需要选择适合的铆接工具。
通常使用的铆接工具包括气动铆接枪、液压铆接枪和手动铆接枪等。
根据具体的铆接要求和工件形状,选择合适的铆接工具进行铆接。
(3)铆接技术要求:在进行铆接工艺时,需要掌握一定的铆接技术。
包括铆接点的选择、铆接过程的控制和铆接质量的检查等。
特别是在进行车体的角部和弧形结构的铆接时,需要更加注意铆接的技术要求。
(4)质量控制:在进行铆接工艺时,需要对铆接质量进行严格的控制。
包括铆接点的平整度、铆接强度和铆接密封性等方面的检测和控制,确保铆接质量符合要求。
浅谈铝合金在轨道交通中的应用

浅谈铝合金在轨道交通中的应用铝合金在轨道交通领域的应用是一项长期受到关注的技术。
它在轨道交通中的广泛应用,包括高铁、地铁、有轨电车等,都展现了其独特的优势和价值。
本文将就铝合金在轨道交通中的应用进行探讨,着重介绍其优势、现状和未来发展趋势。
一、铝合金在轨道交通中的应用优势轻量化: 铝合金具有较低的密度和良好的强度,因此在轨道交通中可以大幅减轻车辆自重,有利于降低能耗和减少磨损,同时提高运行效率和安全性。
耐腐蚀: 铝合金具有良好的耐腐蚀性能,可以在恶劣的环境下保持长期稳定的性能,这使其在地铁、高铁等密闭环境下的应用更为适宜。
成型加工性能好: 铝合金易于成型加工,可以适应各种车辆结构需求,提高车辆设计的灵活性和多样性。
节能减排: 利用铝合金替代传统材料,如钢材,车辆重量减轻可带来降低动力消耗、减少排放的效果,有助于节能减排。
二、铝合金在高铁领域的应用铝合金在高铁领域得到了广泛的应用。
高铁列车以高速、大载客量、运行稳定著称,而铝合金正是其“减重”之选。
高铁车体及部分结构件采用铝合金制造,不仅减轻了车辆自重,提高了运行速度和载客量,还增强了车辆的整体抗腐蚀和使用寿命。
同时,铝合金的可回收再利用特性也符合高铁领域可持续发展的要求。
三、铝合金在地铁领域的应用在地铁领域,铝合金同样发挥着重要作用。
地铁车辆需要应对密闭环境、潮湿腐蚀等问题,而铝合金的优异耐腐蚀性能使其成为地铁车辆的理想选择。
通过采用铝合金材料,地铁车辆的自重得以降低,利于提高整体运行效率和降低能耗,同时也能够提高车辆的整体安全性。
四、铝合金在有轨电车领域的应用在有轨电车领域,铝合金的应用也日益普及。
相比于传统的钢制车辆,铝合金车辆在减轻自重的同时,也可提高车辆的运行速度和舒适性。
此外,铝合金具有优异的导电性能,有利于电车的性能提升和整车电气系统的稳定运行。
五、未来展望随着轨道交通行业的不断发展和技术进步,铝合金在该领域的应用前景依然广阔。
未来,随着铝合金材料制造工艺的不断完善和成本的进一步降低,铝合金在轨道交通领域的应用将进一步扩大,有望实现更多创新和突破。
浅谈轻量化铝合金地铁车辆组装工艺设计

3 结束语
在螺栓联接中产生与保持足够大的预紧力 . 是保 证螺栓联接疲劳 强度 的重要手段之一。 综合本文以上分析讨 论结果 。 对钢制标准螺栓 , 在不超过螺栓联接 的螺杆 . 螺纹与联接件 的静强度的前提之 下 . 对 一 个给定 的螺栓联接设计 . 可以认为是预 紧力 越大 . 其有效疲 劳强度也 则在螺栓联接 中产 其中A 为螺杆 的有效受力面积。以上公式可以证 明 . 由于预 紧力 就越大 。如果不需要考虑撤卸后螺栓 的重复使用 , ● 过低产生螺栓联接分离对疲劳强度的降低 . 远 大于预紧力适度增加 时 生 的预紧力可以接近甚至达 到螺杆 的屈服应力 。 对疲劳强度的影响 【 参考文献】 根据公式( 9 ) , 预紧力为零时 , 螺栓联接 的持久极限疲劳强度安全 系数为最小 。当外力作用使螺栓联接产 生分离时 . 预紧力 的增大能提 高螺栓联接 的疲劳强度。 螺栓联接 的疲劳强度安全系数随预紧力增加 而变大 。 而如果外力作用下在整个疲劳加载过程中都不会使螺栓联接 产生分离 , 由公式 ( 5 ) 得到的结果则是预紧力越大 , 螺栓联接 的疲劳强 度就变得越小 。 而且 , 如果 预紧力可 以很大 . 计算得到的螺栓 联接疲劳 强度 可以变得非常小 以上 的分析似乎也表明 . 一个适 当的预 紧力对螺栓联接持久极 限 疲劳强度 的最大化非常重要。 但是 , 通过对下面两个因素的讨论 . 实 际 结论 却是在正常条件下 , 预 紧力越 大 . 螺栓联接 的有效疲 劳强度也越
利用螺栓联接的古德曼法则公式 ( 5 ) 来计算给定外力作用下螺栓 联接 的疲劳强度安全系数 时. 外力作用不能大于使螺栓联接产生联接 分离 的作用力 P 。 在外力使螺栓联接产生分离的条件下 , 螺栓联接 的 疲劳强度可能会大幅降低 。 如果外力使螺 栓联 接产生分离 . 螺 栓联接的疲劳强度 安全系数 n 可 以通过 P / P 来 定义 , 其中 P 是外力作用幅值 , P | 是加载曲线 口 与疲劳强度 曲线 — S m 的交点对 应的外 力作用 。很容易证明 . 此时 的疲劳强度安全系数 n 可通过下面公式来计算 :
浅析城轨车辆铝合金车体焊接工艺

浅析城轨车辆铝合金车体焊接工艺城轨车辆的车体是由铝合金材质焊接而成,本文对城轨车辆铝合金车体的焊接工艺、工装进行分析,探讨了铝合金车体焊接工艺的发展趋势。
标签:城轨车辆;焊接;铝合金;分析为了保证城轨车辆的高速行驶,城轨车辆采用的是轻量化的设计,车身采用铝合金的结构,降低整辆车的重量,减少了对轮轨的冲击。
但是铝合金的膨胀系数是钢的2倍,凝固的时候体积收缩也很大,因此,在焊接的过程中很容易变形。
特别是对于薄壁型的铝合金材质,不光焊接变形量大,而且在焊接的时候还会产生气孔、裂纹等现象,因此要提高铝合金的焊接工艺水平,尽量减少焊接过程中出现的问题,提高车体焊接的质量,就需要用专用的工装来保证车体焊接成型后的尺寸,为制造出高质量的城轨车辆奠定基础。
1 城轨车辆铝合金车体焊接的特点1.1 焊接方法和速度的选择铝合金的焊接方法有多种,包括惰性气体的保护焊(MIG)、钨极惰性气体的保护焊(TIG)两种焊接方法。
在焊接的时候,对于较厚夹板的焊接,为了能够保证焊接的质量要使焊缝从分均匀地融合,而且使焊缝中的气体顺畅溢出,采用较慢的环节速度和较大的电流配合焊接;对于较薄板的焊接,为了避免焊缝太热,在焊接的过程中要采用较快的焊接速度和较小的电流配合,从而确保焊接的质量,尽量避免气孔的形成[1]。
1.2 气孔的形成铝合金表面氧化膜有很强的吸水性,当环境湿度很大时,吸收了很多水的氧化膜在电弧的作用下水分解出氢,而氢气在熔池中没有时间排除就形成了气孔[2]。
2 铝合金车体的焊接工艺2.1 铝合金车体的焊接工艺流程车体预组、焊接前尺寸的调整、焊接前的清理、自动焊接、焊接后的打磨。
组装过程中所有零部件的误差及变形全部汇集在一起,通过车体组焊来消化,如果要控制铝合金车体的焊接质量就要在焊接前定好尺寸,通过焊接前的尺寸调整对铝合金车体的变形进行预先估测,做好合理工艺放量。
加强焊接过程的控制,通过组焊工装及辅助撑拉杆减小车体在焊接时的变形程度,提高焊接质量[3]。
浅析铝合金地铁车总组成装配工艺

浅析铝合金地铁车总组成装配工艺摘要:随着公司生产能力的日益增加,精益求精的装配工艺已经深入到我们每一位城铁员工的心中,合理的装配工艺可以有效地提高我们的工作效率和降低劳动强度。
技艺也是要在不断的摸索中来自我提升,为了能保质保量的完成每一台车的生产,我们要在工作中积累经验,在实践中小改小革大胆创新,真正做到“一次做好,永不返工”,以此来追求精益求精的生产需要。
本文将以广州地铁2 号线车体为例,讨论总组成装配工艺应如何进行。
全文主要分析了车体结构及制造工艺的流程以及难点,并针对这些难点提出了切实有效的工艺方案,为本项目生产和后续相同车型的制造提供了参考标准。
关键词:铝合金车体结构制造工艺装配结构尺寸一、车体结构介绍:广州地铁 2 号线车体结构主要由四个部分组成,分别是底架、车顶、侧墙以及端墙四部分。
而车体应该具有足够的强度以保证乘客的安全,同时还应该具有隔音、保温、防雨、通风等,以保证乘客能够有舒适的乘车环境。
而车体的结构主要由型腔式的铝合金结构。
而对于总组成来说需要消化各部位带来的公差。
二、车体结构的装配流程:1.底架铝结构装配将底架落入总组成组焊胎位,利用工装上底架边梁顶紧装置调整底架,使底架纵向中心与工装纵向中心重合,其后利用工装的拉紧装置将底架枕梁、边梁下平面与工装定位面拉严,无间隙。
2.端墙铝结构装配将端墙落入底架位置,调整贯通道门口高度,按照 1953(0 ,+2) mm 进行调整,调整贯通道门口宽度,按照 1640(-1,+1) mm 组对,以底架端梁中心为中心,调整端墙位置,使贯通道门中心与底架中心重合。
安装端墙车内撑杆,调整端墙延车长方向垂直度,端墙向车外倾斜 5mm。
调整贯通道门口宽度,保证端角柱外侧与底架边梁外侧无错口。
通过端墙外侧顶紧装置,保证端墙与底架端梁外表面组对后无错口。
如端墙在落入底架后,发现有超过 1mm 的缝隙存在的话,可以使用手拉葫芦配合吊带将端墙缝隙拉严。
3.侧墙铝结构装配利用天车配合 2 根 10 吨 6 米吊带吊装侧墙。
b型铝合金地铁车辆车体制造工艺
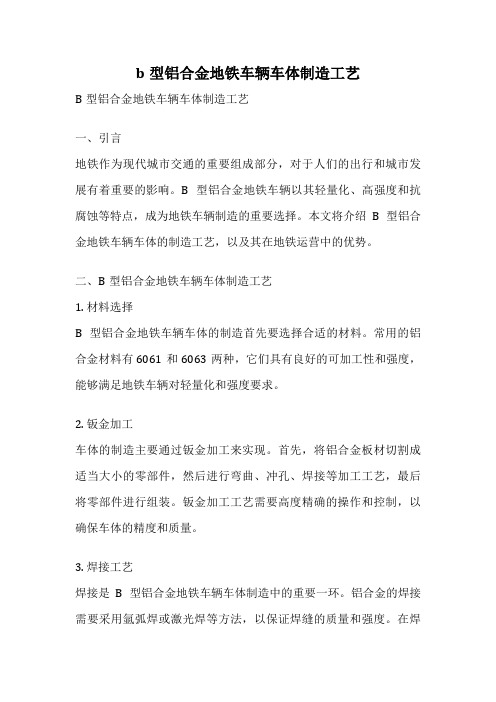
b型铝合金地铁车辆车体制造工艺B型铝合金地铁车辆车体制造工艺一、引言地铁作为现代城市交通的重要组成部分,对于人们的出行和城市发展有着重要的影响。
B型铝合金地铁车辆以其轻量化、高强度和抗腐蚀等特点,成为地铁车辆制造的重要选择。
本文将介绍B型铝合金地铁车辆车体的制造工艺,以及其在地铁运营中的优势。
二、B型铝合金地铁车辆车体制造工艺1. 材料选择B型铝合金地铁车辆车体的制造首先要选择合适的材料。
常用的铝合金材料有6061和6063两种,它们具有良好的可加工性和强度,能够满足地铁车辆对轻量化和强度要求。
2. 钣金加工车体的制造主要通过钣金加工来实现。
首先,将铝合金板材切割成适当大小的零部件,然后进行弯曲、冲孔、焊接等加工工艺,最后将零部件进行组装。
钣金加工工艺需要高度精确的操作和控制,以确保车体的精度和质量。
3. 焊接工艺焊接是B型铝合金地铁车辆车体制造中的重要一环。
铝合金的焊接需要采用氩弧焊或激光焊等方法,以保证焊缝的质量和强度。
在焊接过程中,还需要注意控制焊接温度和速度,避免产生焊接变形和应力集中。
4. 表面处理车体的表面处理主要包括除油、除氧化和喷涂等工艺。
除油和除氧化可以去除车体表面的污染物和氧化层,保证喷涂的附着力和耐腐蚀性。
喷涂工艺可以采用静电喷涂或涂装等方法,使车体表面呈现出美观且耐用的涂层。
5. 质量检测地铁车辆的制造过程中需要进行严格的质量检测。
包括对材料、零部件和车体整体的尺寸、强度、密封性等性能进行检测。
通过质量检测,可以确保地铁车辆在使用过程中的安全和可靠性。
三、B型铝合金地铁车辆的优势1. 轻量化相比传统的钢铁车体,B型铝合金地铁车辆车体重量更轻,能够降低车辆的能耗和运营成本,同时减少地铁线路的磨损和振动。
2. 高强度B型铝合金具有优异的强度和刚度,能够有效抵抗外部冲击和振动,保证乘客的安全和舒适。
3. 抗腐蚀铝合金具有良好的耐腐蚀性,能够在潮湿和腐蚀环境中长期使用,并减少维护和修复成本。
浅析城轨车辆铝合金车体焊接工艺

浅析城轨车辆铝合金车体焊接工艺摘要:进入21世纪,由于人们的生活节奏日益加快,对生活品质要求也逐渐提高。
为了保证人员流动的便利性,提供便利的交通是必不可少的,城轨车辆作为大城市的主要交通工具具有速度快便捷且承载能力大的特点,因此可见,城轨车辆拥有较为广阔的市场。
提高城轨车辆铝合金焊接工艺,保障人员流动安全是十分重要的。
关键词:城轨车辆;铝合金;焊接工艺【正文】城轨车辆大多数都是利用铝合金这种材料来制造的,利用这种材料能够更好的保障车辆的运行,使列车在高速运行的同时不受到损害。
另一方面它可以使列车更加轻便,相比较传统材料而言启动速度更快,冲击力更小。
但这种材料也有它的缺陷,例如它更易于膨胀变形。
尤其是薄款铝合金在焊接的时候产生气孔,所以放下最好的方式就是提高铝合金的生产质量,减轻其在制造业中的缺陷。
这篇文章主要分析了城轨车辆铝合金车体焊接的工艺,展望了这项工艺在未来发展的趋势,提出了几种提高焊接工艺的方法,以期城轨车辆为人们带来更多的便利,对未来的交通事业作出更多的贡献。
一、城轨车辆铝合金车体焊接的特征1.1焊接方式和焊接速度的选择铝合金做衣材料焊接的方式是多种多样的,有两种焊接方式分别为惰性气体和钨这惰性气体保护焊。
在焊接时要根据焊接物体的薄厚来确定焊接的方式,若对于较厚的板子来说,如果要使它的密封程度更好,让板子的空气能够排除,应该利用电流配合来进行焊接。
但若是一些比较薄的板子,为了焊接缝隙不会太热,就要利用较小的电流来进行工作。
这样一来就会学使气孔出现的机率变小。
1.2焊接时会经常产生气孔铝合金的表层上附着着一层吸水能力较强的氧化膜,如果实在较为潮湿的环境之下,氧化膜中的水分会变味氢气,而氢气无法在氧化膜中排解出来,气孔就由此生成。
二、铝合金焊接的过程和利用的技术2.1焊接车体的主要流程。
焊接之前首先要进行周密的计划,将焊接车体的大小测量好,焊接材料进行打磨和清理工作。
在在车辆焊接的过程中,难免会出现零件的误差,这时就需要将有误的零件整合在一起,通过焊接过程中的增补将有误的零件进行修理。
地铁车辆车体结构设计方案

地铁车辆车体结构设计方案一、引言地铁车辆作为城市轨道交通系统中的重要组成部分,其车体结构设计方案的合理性和可靠性对于确保列车运行的安全性和乘坐舒适性至关重要。
本文将分析和探讨地铁车辆车体结构设计方案的相关要素,并提供一个综合可行的设计方案。
二、车体材料选择地铁车辆车体材料的选择是保证车体结构强度和轻量化的关键。
一般而言,地铁车辆的车体由钢材、铝合金和复合材料构成。
钢材具有强度高、耐久性好的特点,但重量较大;铝合金具有轻量化、耐蚀性好的特点,但成本较高;复合材料具有轻量化、抗腐蚀性好的特点,但制造工艺复杂。
综合考虑成本、强度和轻量化等因素,建议使用铝合金作为地铁车辆车体的主要材料。
三、车体结构设计1.车体长度和宽度:根据地铁运营的需求和站台长度等因素,确定车体的长度和宽度。
一般而言,地铁车辆的长度应控制在100米左右,宽度约为3.2米。
2.车体强度设计:地铁车辆需要经受各种复杂的力学、热学和振动环境的考验,因此车体的强度设计至关重要。
在车体设计过程中,需要进行有限元分析,确定车体结构的各主要部位的受力状况,并通过材料选择、优化设计等手段确保车体强度满足要求。
3.车体外形设计:地铁车辆的外形设计既要满足美观的要求,又要考虑乘客上下车、站台对接等操作的便利性。
因此,车体外形应具备流线型,减少阻力;车门位置应合理设置,方便乘客进出和站台对接;车体表面颜色要与城市环境相协调,提高城市形象。
4.车体连接方式设计:地铁车辆的车体连接方式通常有焊接和螺栓连接两种。
焊接连接方式简单,但在生产和维修过程中较难进行拆卸和更换;螺栓连接方式方便拆卸和更换,但需要注意连接点的强度和稳定性。
在车体结构设计中,根据实际情况选择合适的连接方式。
四、车体附件设计地铁车辆的车体附件包括车门、车窗、座椅等。
这些附件的设计要考虑到乘客的安全和舒适性,同时也要满足车体结构的强度和重量要求。
车门应具备快速开闭和安全防夹功能;车窗应具备隔热、防眩光功能;座椅应具备舒适、耐久的特点。
- 1、下载文档前请自行甄别文档内容的完整性,平台不提供额外的编辑、内容补充、找答案等附加服务。
- 2、"仅部分预览"的文档,不可在线预览部分如存在完整性等问题,可反馈申请退款(可完整预览的文档不适用该条件!)。
- 3、如文档侵犯您的权益,请联系客服反馈,我们会尽快为您处理(人工客服工作时间:9:00-18:30)。
浅谈轻量化铝合金地铁车辆组装工艺设计
作者:王庆召
来源:《科技视界》2013年第23期
本文从设计的角度,讨论地铁车辆组装工艺和设备布置,以便其更优化、更合理的适应地铁车辆组装的要求。
1 铝合金地铁车辆工艺现状
国内地铁制造企业与国外西门子、阿尔斯通、庞巴迪等公司合作,引进铝合金地铁车辆焊接、涂装、组装、调试等技术。
先进、适用的制造工艺是轨道交通装备产品可靠性的重要保证。
目前国内铝合金地铁车辆车体既有从西门子引进的整体焊接结构,也有从阿尔斯通、庞巴
迪引进的模块化结构,然后采用特殊螺栓连接方式组合成铝合金车体。
车辆组装既有从西门子引进的台位固定、施工工序流动的作业方式,也有从阿尔斯通引进的施工工序固定、台位流动的作业方式。
无论是台位固定、施工工序流动的作业方式还是施工工序固定、台位流动的作业方式,铝合金地铁车辆的组装工序流程基本是相同的,主要是车体表面处理完成之后通过移车台将车体转换到组装的转换台位,通过转换台位运输至组装台位,在组装台位完成车内、车顶、车底设备的安装后,再进行落车调簧称重过限界试验。
组装工艺的流程如图1所示。
2 宁波城轨公司介绍
宁波城轨公司采用合资合作方式,南车株洲电力机车有限公司与宁波市政府作为合作伙伴,引入多元投资主体,实现强强联合,有效依托南车株机公司在城轨车辆研制技术与检修方面的丰富经验,以及质量保证、售后服务,结合宁波市地域资源优势及宁波城轨公司的项目运作管理能力和资金保障,建立先进的城轨车辆组装及修理基地。
3 组装工艺功能分区及设备配置
根据组装工艺流程,组装车间可分为架车转换区、组装区、落车区等组成。
3.1 架车转换区
架车转换区是表面处理后的车体通过移车台进入总装车间的第一步,车辆进入架车转换区后,利用转换台位架车机提升车辆。
架车转换区配备的主要设备为转换台位架车机。
车体从转换台位进入到组装台位根据工艺的不同有两种方式,一种是轨道式,一种是气垫运输式。
总装区采用48米大跨度厂房结构进行柔性生产,不采用大吨位行车进行吊运,并且地铁车辆大量的部件是安装在车底,需要将部件方便地运到车底,为适应地铁及城轨车辆的生产组织方式,设计采用气垫运输车进行车体以及车底部件的运输。
大吨位气垫运输车主要有两处使用:在转换台位上通过气垫车将车体转运到组装台位进行总装,总装完车体后通过气垫车送落车台位。
采用气垫技术有以下优点:搬运负载几乎没有摩擦力,可以全方位运动,具有准确定位和在狭窄区域的运动能力,具有非常小的组合高度和非常小的磨损,低运转费和低维修费。
3.2 组装区
组装区主要承担铝合金地铁车辆的总装任务,承担电器设备的配线与检查,制动管路的安装与检查,内墙装饰板、门窗、座椅、扶手杆的安装与检查,室内电器设备的安装以及电缆和制动管件的制作等,车底设备(含变流设备、制动设备、制动电阻柜)的安装,车顶空调、受电弓设备安装。
组装区推行以“台位”为基本单位的工艺设计模式。
根据厂房设计的生产纲领为年总装150辆地铁车辆,每台车辆的总装周期约为15天,设计采用12个组装台位,每边分布6个台位。
中间为气垫车运行通道。
组装方式主要有台位固定、施工工序流动的作业方式和施工工序固定、台位流动的作业方式,根据铝合金地铁车辆组装工艺流程以及地铁车辆自身的特点和产品批量,为提高台位利用率,减少倒车次数,组装方式采用台位固定、施工工序流动的作业方式。
总装区配备4台3t悬挂吊,用于起吊车顶和其他部分设备,车底和车端设备采用小吨位气垫运输车或搬运叉车进行运输安装。
3.3 落车区
落车区为15米跨,设置两股道,其中一股道为落车,另一股道为称重、限界,该轨道拉至通长,可存放转向架。
落车工艺采用的设备为城轨车辆架车称重调载试验系统,主要为车体调簧和转向架调簧,车体调簧即通过车体水平性试验进行,转向架调簧通过调整紧急弹簧进行。
该工艺通过水平性试验将车体加垫以及调整转向架紧急弹簧的工艺,使地铁车辆二系支承载荷优化分布,实现了自动快速精确的调簧,保证车体重量在轮载上的均匀分布,同时保证车体和转向架的互换性,提高地铁车辆质量。
转向架调簧是模拟车体的重量加载,这种模拟加载是一种理想情况,与落车时的现实情况并不完全一致。
因此,在转向架称重调簧完成落车后,使用车辆称重仪进行整车称重试验。
整车称重试验完成后,即通过限界设备完成车辆过限界试验。
4 工艺流程及布局
图2为组装车间工艺图,具体工艺流程如图所示,其中车间内物流人流通道如图所示。
该种方案采用气垫车移动车体,组装台位之间设有物料通道。
5 结语
本方案是笔者根据所了解的地铁组装工艺设计一般情况而进行的一次探讨,简洁方便。
组装工艺布局也可采用以下改进方式:组装台位之间可不设物料通道,各台位都相互连接,这样车下物料从台位下的空间进入,车上台位比较宽敞,能容下车内组装物料;或台位采用双层结构,上层台位方便进行车顶设备安装,如此布局,能确保作业安全;或将组装工序分为前装和后装工序。
前装工序主要负责车内地板、防寒棉、线缆、管道以及车下管道安装,后装工序主要负责内装、车下设备、车顶设备的安装;或组装车辆依靠气垫车移动的同时安装轨道,可以实现车辆在组装台位上的纵向移动。
【参考文献】
[1]曾海燕.地铁车辆的车体调簧工艺研究[J].电力机车与城轨车辆,2006(3).
[2]贾洪洋.地铁车辆大修称重调簧工艺浅析[J].铁道机车车辆工人,2009(9).
[3]李强.地铁车辆段检修厂房组合[J].铁道标准设计,1999(5).
[4]刘林.地铁车辆架修的工艺设计[J].科技信息,2012(8).
[责任编辑:曹明明]。