钻镗两用组合机床液压系统设计
卧式钻镗两用组合机床的液压系统设计精选文档

卧式钻镗两用组合机床的液压系统设计精选文档TTMS system office room 【TTMS16H-TTMS2A-TTMS8Q8-兰州工业学院毕业设计(论文)题目:卧式钻镗两用组合机床的液压系统设计系别机械工程系专业机电一体化班级姓名学号指导教师(职称)朱琪(副教授)日期兰州工业学院毕业设计(论文)任务书机械工程系 2013 届机电一体化技术专业毕业设计(论文)任务书毕业设计(论文)题目卧式钻镗两用组合机床液压系统设计课题内容性质理论研究/实验研究 /工程技术研究/软件开发课题来源性质结合教师科研课题/教师收集的结合生产实际的课设计/论文题/学生自立课题校内(外)指导职称工作单位及部门联系方式教师朱琪副教授兰州工业学院机械工程系一、题目说明(目的和意义):毕业设计是学生在校结束了全部理论课程和相应实践教学环节后进行的一项大型综合性实践教学环节,是学生在能将所学理论知识全面应用并结合理解实际问题的工程实践过程中不可或缺的、较系统的工程化训练,是完成工程师初步训练的重要步骤。
通过毕业设计,学生应达到以下基本要求:1、具有综合应用所学理论知识和实践技能,初步解决本专业范围内的工程技术问题的能力,善于应用新技术、新工艺、新材料。
2、具有查阅科技文献资料、使用各种标准、手册以及独立工作、创新的能力。
3、深刻认识理解联系实际的工作作风对技术人员的重要性。
二、设计(论文)要求(工作量、内容):设计一台卧式钻镗两用组合机床液压系统,完成8个Φ14mm孔的加工进给传动。
该系统工作循环为:快速前进→工作进给→快速退回→原位停止。
原始数据:⑴快进快退速度约为s;⑵工进速度可在~s范围内无极调速;⑶最大行程为400mm,工进行程为180mm;⑷最大切削力为18KN;运动部件自重为25KN;⑸启动换向时间为;⑹采用平导轨,静摩擦系数,动摩擦系数。
主要要求:要求根据系统的工作要求,进行工况分析和计算,拟定方案,确定液压传动系统,计算和选择液压元件,并进行系统的验算,确定合理的液压系统结构,绘制相关工作图并编制技术文件。
钻镗两用组合机床液压系统的设计
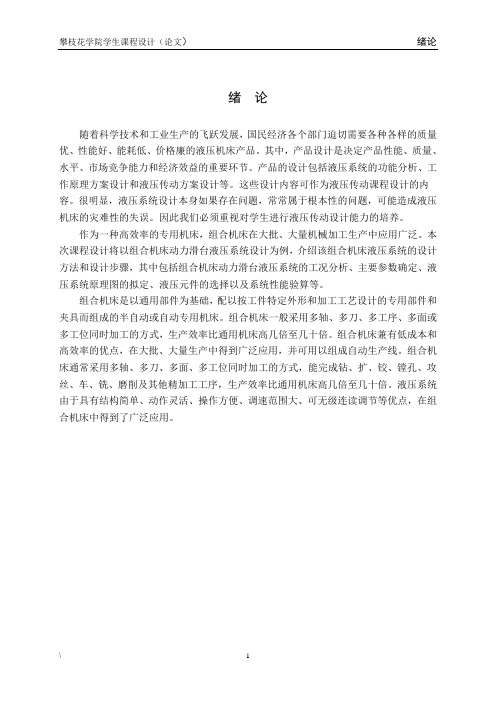
攀枝花学院学生课程设计(论文)绪论绪论随着科学技术和工业生产的飞跃发展,国民经济各个部门迫切需要各种各样的质量优、性能好、能耗低、价格廉的液压机床产品。
其中,产品设计是决定产品性能、质量、水平、市场竞争能力和经济效益的重要环节。
产品的设计包括液压系统的功能分析、工作原理方案设计和液压传动方案设计等。
这些设计内容可作为液压传动课程设计的内容。
很明显,液压系统设计本身如果存在问题,常常属于根本性的问题,可能造成液压机床的灾难性的失误。
因此我们必须重视对学生进行液压传动设计能力的培养。
作为一种高效率的专用机床,组合机床在大批、大量机械加工生产中应用广泛。
本次课程设计将以组合机床动力滑台液压系统设计为例,介绍该组合机床液压系统的设计方法和设计步骤,其中包括组合机床动力滑台液压系统的工况分析、主要参数确定、液压系统原理图的拟定、液压元件的选择以及系统性能验算等。
组合机床是以通用部件为基础,配以按工件特定外形和加工工艺设计的专用部件和夹具而组成的半自动或自动专用机床。
组合机床一般采用多轴、多刀、多工序、多面或多工位同时加工的方式,生产效率比通用机床高几倍至几十倍。
组合机床兼有低成本和高效率的优点,在大批、大量生产中得到广泛应用,并可用以组成自动生产线。
组合机床通常采用多轴、多刀、多面、多工位同时加工的方式,能完成钻、扩、铰、镗孔、攻丝、车、铣、磨削及其他精加工工序,生产效率比通用机床高几倍至几十倍。
液压系统由于具有结构简单、动作灵活、操作方便、调速范围大、可无级连读调节等优点,在组合机床中得到了广泛应用。
攀枝花学院学生课程设计(论文) 1 钻镗液压机床的设计1 钻镗液压机床的设计1.1机床的设计要求设计一台钻镗两用组合机床的液压系统。
钻镗系统的工作循环时快进→工进→快退→停止。
液压系统的主要参数与性能要求如下:最大切削力18000N,移动部件总重量27000N;最大行程434mm(其中工进行程184mm);快进、快退的速度为5.85m/min,工进速度应在(20~120)mm/min范围内无级调速;启动换向时间△t=0.05s,采用水平放置的导轨,静摩擦系数fs=0.2;动摩擦系数fd=0.1。
设计一台钻镗两用组合机床的液压系统
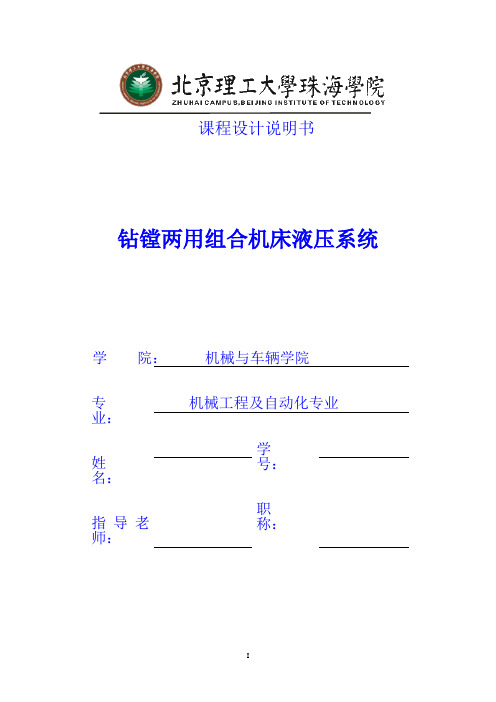
课程设计说明书钻镗两用组合机床液压系统学院:机械与车辆学院专业:姓名:指导老师:机械工程及自动化专业学号:职称:中国·珠海二○一二年五月北京理工大学珠海学院课程设计任务书学生姓名:专业班级:机械工程及自动化指导教师:工作部门:机械与车辆学院一、课程设计题目设计一台钻、镗两用组合机床的液压系统,要求液压系统完成“快进→工进→快退→停止”的工作循环及工件的定位与夹紧。
已知:最大切削力为12000N,运动部件自重为18000N,工作台快进行程为200mm,工进行程为200mm,快进、快退速度为5m/min,工进速度为20—100mm/min,加、减速时间为0.2s,导轨为平导轨,静摩擦系数为0.2,动摩擦系数为0.1。
工件所需夹紧力不得超过6000N,最小不低于3330N,由松开到夹紧的时间为1s,夹紧缸的行程为40mm。
二、课程设计内容液压传动课程设计一般包括以下内容:(1) 明确设计要求进行工况分析;(2) 确定液压系统主要参数;(3) 拟定液压系统原理图;(4) 计算和选择液压元件;(5) 验算液压系统性能;(6) 结构设计及绘制零部件工作图;(7) 编制技术文件。
三、进度安排四、基本要求(1) 液压传动课程设计是一项全面的设计训练,它不仅可以巩固所学的理论知识,也可以为以后的设计工作打好基础。
在设计过程中必须严肃认真,刻苦钻研,一丝不苟,精益求精。
(2) 液压传动课程设计应在教师指导下独立完成。
教师的指导作用是指明设计思路,启发学生独立思考,解答疑难问题,按设计进度进行阶段审查,学生必须发挥主观能动性,积极思考问题,而不应被动地依赖教师查资料、给数据、定方案。
(3) 设计中要正确处理参考已有资料与创新的关系。
任何设计都不能凭空想象出来,利用已有资料可以避免许多重复工作,加快设计进程,同时也是提高设计质量的保证。
另外任何新的设计任务又总有其特定的设计要求和具体工作条件,因而不能盲目地抄袭资料,必须具体分析,创造性地设计。
钻镗两用组合机床液压系统设计

目录一.工况分析........................................................................ ...............................................二.绘制液压缸的负载图和速度图........................................................................ ...........三.拟订液压系统原理图........................................................................ ............................四.确定执行元件主要参数........................................................................ .......................五.确定液压泵的规格和电动机功率及型号................................................................六..验算液压系统性能........................................................................ ...............................七. 参考书目........................................................................ ............................................设计一台钻镗两用组合机床的液压系统。
该系统的工作循环时快进→工进→快退→停止。
液压系统的主要参数与性能要求如下:最大切削力18000N,移动部件总重量25000N;最大行程400mm(其中工进行程180mm);快进、快退的速度为4.5m/min,工进速度应在(20~120)mm/min范围内无级调速;启动换向时间△t=0.05s,采用水平放置的导轨,静摩擦系数f s =0.2;动摩擦系数f d=0.1。
钻镗两用组合机床的液压控制系统及电气控制系统设计

目录摘要 (1)Abstract (2)1、绪论 (1)1.1、课题的背景 (1)1.2、组合机床概述 (1)1.3、专用组合机床的介绍 (3)1.4、 PLC简介 (4)1.4.1 PLC的定义 (5)1.4.2 PLC的基础知识 (6)1.4.3 PLC的用途 (8)2、钻镗两用组合机床控制概述 (9)2.1、钻镗两用组合机床主电路原理图 (10)2.2、钻镗两用组合机床的工作流程图 (11)2.3、钻镗两用组合机床的控制过程 (11)2.3.1各电磁阀动作状态 (12)2.3.2专用组合机床的总控制过程 (12)3、钻镗两用组合机床的液压系统设计 (12)3.1、确定系统方案 (13)3.2、拟定液压系统图 (14)3.3、液压缸的设计计算 (14)3.3.1液压缸的类型及结构形式 (15)3.3.2液压缸的工作压力 (15)3.3.3计算液压缸的尺寸 (16)3.3.4液压缸各工作阶段的压力、流量和功率计算 (17)3.4、液压缸工况图 (18)3.5、液压缸推力的计算 (19)3.6、液压系统的压力损失计算 (19)4、专用钻孔机床的PLC设计 (19)4.1、输入输出点分配 (21)4.2 、PLC的选择 (22)4.3、专用组合机床PLC控制系统接线图 (23)5、钻镗两用组合机床PLC控制程序 (24)结论 (25)致谢 (26)参考文献 (27)摘要钻镗两用组合机床,属于机械加工用机床。
它由工作台、安装在工作台两端及一侧的导轨,导轨与工作台的边缘平行,钻架通过吊铁和锁紧螺钉安装在导轨上;导轨上设有燕尾,钻架可在导轨上水平移动;钻架包括溜板、溜板上装有传动机构,溜板底面上设有与导轨上的燕尾相配合的燕尾槽,机械滑台上装有主支撑架,主支撑架上装有纵向机械滑台及控制系统,控制系统连接一控制活动按钮站,纵向机械滑台上装有附属支撑架,附属支撑架上通过机械滑台装有水平方向的钻削动力头。
它解决了现有的钻床加工大型零部件特别是回转体直径较大时操作不方便、加工困难等技术问题。
钻、镗两用组合机床液压系统的设计(二)毕业设计

钻、镗两用组合机床液压系统的设计(二)毕业设计
2.液压系统组成
液压系统主要由以下组成部分构成:液压泵、液压缸、液压阀、压力表等。
在这些部
件中,液压泵是液压系统的重要原件,其主要作用是将机床所需的液体压力转换为动能,
供液压系统的其他部件使用。
液压缸是液压系统中的执行部件,其主要功能是根据系统的
压力变化,控制机床设备的运动、位置、速度等参数。
液压阀则是液压系统中的控制部件,其主要用途是根据操作员的指令,调节系统的压力、流量等参数,以控制液压缸的运动状态。
3.液压系统设计原则
设计一个合理稳定的液压系统,需要遵循以下原则:
(1)在设计过程中,需根据机床的工艺特点,合理选择液压泵、液压缸等液压装置的型号、规格。
(2)在进行设计时,需要对液压管路的长度、直径、弯曲处的变形程度等进行考虑,以确保系统的流通性与稳定性。
(3)需要根据液压系统的工作压力与流量,确定合适的液压阀的类型、规格、数量。
(4)在液压系统设计后,需要进行系统试验,以检验其稳定性、运行正常性、各部件的适用性等。
5.结论
本文通过对钻、镗两用组合机床液压系统的设计研究,得出了一系列液压系统方案和
设计原则。
在液压系统方案选择过程中,应结合机床的工艺特点、液压泵的选型、液压管
路的布置、液压阀的安装、液压油的使用等因素,并严格遵循相关液压系统设计标准,以
确保长期稳定、可靠的机床工作状态。
钻镗两用组合机床机液压系统设计
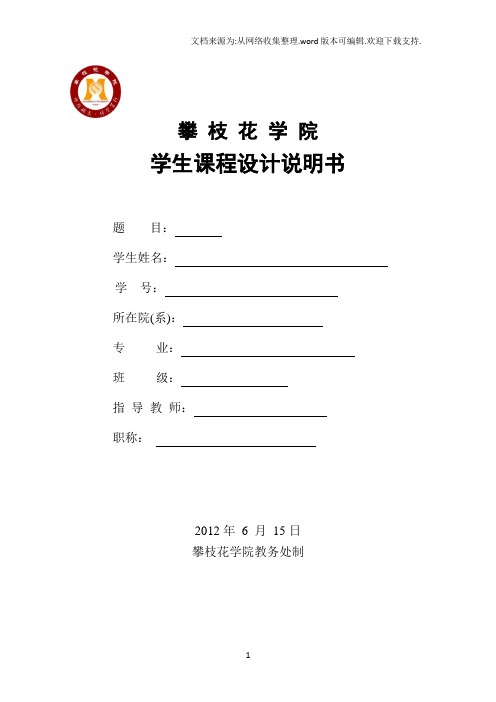
符合本专业相关规范或规定要求;规范化符合本 文件第五条要求。
综述简练完整,有见解;立论正确,论述充分, 结论严谨合理;实验正确,分析处理科学。
45% 11 创新
10
对前人工作有改进或突破,或有独特见解。
成绩
指 导 教 师 评 语
指导教师签名: 3
年月日
摘要
钻镗组合机床是机械、电气、液压三者紧密联系,结合的一个综合体。液 压传动与机械传动、电气传动并列为三大传统形式,液压传动系统的设计在现代 机械的设计工作中占有重要的地位。因此,《液压传动》课程是工科机械类各专 业都开设的一门重要课程。它既是一门理论课,也与生产实际有着密切的联系。 为了学好这样一门重要课程,除了在教学中系统讲授以外,还应设置课程设计教 学环节,使学生理论联系实际,掌握液压传动系统设计的技能和方法。
课程设计(论文)指导教师成绩评定表
题目名称
评分项目
分得 值分
评价内涵
工 01 学习态度 作 表 02 科学实践、调研 现 20% 03 课题工作量
6
遵守各项纪律,工作刻苦努力,具有良好的科学 工作态度。
7
通过实验、试验、查阅文献、深入生产实践等渠 道获取与课程设计有关的材料。
7
按期圆满完成规定的任务,工作量饱满。
3 何玉林,沈荣辉,贺元成.主编.机械制图. 重庆大学出版社.2000.8
4 路甬祥主编.液压气动技术手册.北京.机械工业出版社.2002
5 雷天觉主编.液压工程手册.北京.机械工业出版社.1990
4、课程设计工作进度计划
内容
学时
明确机床对液压系统的要求,进行工作过程分析
6
初步确定液压系统的参数,进行工况分析和负载图的编制
钻镗两用组合机床液压系统的设计

毕业设计(论文)钻、镗两用组合机床液压系统的设计Drilling and boring amphibious combination machine tools hydraulicsystem design系名:专业班级:学生姓名:学号:指导教师姓名:指导教师职称:二〇**年六月任务书目录引言 (5)第一章设计任务 (7)1.1要求 (7)1.2功能分析、需求设计 (7)第二章工况分析 (8)2.1运动参数分析 (8)2.2动力参数分析 (8)第三章计算液压缸尺寸和所需流量 (10)3.1工作压力的确定 (10)3.2计算液压缸的尺寸 (10)3.3确定液压缸所需的流量 (12)3.4夹紧缸的有效工作面积、工作压力和流量的确定 (12)第四章液压系统图的拟定 (14)4.1确定执行元件的类型 (14)4.2换向方式确定 (14)4.3调速方式的选择 (14)4.4快进转工进的控制方式的选择 (14)4.5终点转换控制方式的选择 (14)4.6实现快速运动的供油部分设计 (15)4.7夹紧回路的确定 (15)第五章选择液压元件 (17)5.1选择液压泵 (17)5.2选择阀类元件 (18)5.3 确定油管尺寸 (18)5.4确定邮箱容量 (19)第六章计算压力损失和压力阀的调整值 (21)6.1沿程压力损失 (21)6.2局部压力损失 (21)6.3总的压力损失 (22)结论 (23)致谢 (24)参考文献 (25)钻、镗两用组合机床液压系统的设计摘要液压传动是以液压油为工作介质,通过动力元件将原动机的机械能变为液压油的压力能,再通过控制元件,然后借助执行元件将压力能转换成机械能,驱动负载实现直线或回转运动。
液压系统是液压设备的重要组成部分,它与设备主体的关系密切,两者的设计通常需要同时进行。
本次设计介绍了液压系统的设计过程,具体讲解了设计的步骤,分析了液压系统的功能设计、需求分析所达到的目的,介绍总体设计方案的拟定方法、液压系统原理图的拟定过程、液压元件的选择方法及液压系统性能验算方法。
- 1、下载文档前请自行甄别文档内容的完整性,平台不提供额外的编辑、内容补充、找答案等附加服务。
- 2、"仅部分预览"的文档,不可在线预览部分如存在完整性等问题,可反馈申请退款(可完整预览的文档不适用该条件!)。
- 3、如文档侵犯您的权益,请联系客服反馈,我们会尽快为您处理(人工客服工作时间:9:00-18:30)。
目录一.工况分析.......................................................................................................................二.绘制液压缸的负载图和速度图...................................................................................三.拟订液压系统原理图....................................................................................................四.确定执行元件主要参数...............................................................................................五.确定液压泵的规格和电动机功率及型号................................................................六..验算液压系统性能.......................................................................................................七. 参考书目....................................................................................................................设计一台钻镗两用组合机床的液压系统。
该系统的工作循环时快进→工进→快退→停止。
液压系统的主要参数与性能要求如下:最大切削力18000N,移动部件总重量25000N;最大行程400mm(其中工进行程180mm);快进、快退的速度为4.5m/min,工进速度应在(20~120)mm/min范围内无级调速;启动换向时间△t=0.05s,采用水平放置的导轨,静摩擦系数f s =0.2;动摩擦系数f d=0.1。
机械效率取0.9。
一.工况分析液压缸负载主要包括:切削阻力,惯性阻力,重力等,即F= F W+F f+ F m式中:F W——工作负载,对于金属切削机床来说,即为活塞运动方向的切削力F W =18000NF f——导轨摩擦阻力负载,启动时为静摩擦阻力,启动后为动摩擦阻力,对于平导轨F f可由下式求得:)F f=f(G+Fn)G——运动部件重力Fn——垂直于导轨的工作负载,为零f ——导轨摩擦系数,静摩擦系数为0.2,动摩擦系数为0.1Ffs= 25000×0.2=5000 NFfd =25000×0.1=2500 NFm——运动部件速度变化时的惯性负载;Fm= G·Δv/(g·Δt)式中,g——重力加速度;Δt——加速或减速时间,Δt=0.05s;Fm= G·Δv/(g·Δt)=25000×4.5/(9.8×0.05×60)=3826N根据以上分析,计算出液压缸各动作中的负载表1:(单位:N,取η=0.9)m Array表1液压缸负载表二.绘制液压缸的负载图和速度图根据上表数值,绘制出液压缸的负载循环图如图1所示:根据任务书技术参数和设计要求,绘制速度循环图如图2所示:三.拟订液压系统原理图1.确定供油方式:由设计要求可知,工进时负载大速度较低,而快进、快退时负载较小,速度较高。
为节约能源减少发热。
油源宜采用双泵供油或变量泵供油。
选用双泵供油方式,在快进、快退时,双泵同时向系统供油,当转为共进时,大流量泵通过顺序阀卸荷,小流量泵单独向系统供油,小泵的供油压力由溢流阀来调定。
若采用限压变量泵叶片泵油源,此油源无溢流损失,一般可不装溢流阀,但有时为了保证液压安全,仍可在泵的出口处并联一个溢流阀起安全作用。
现采用压力反馈的限压式变量叶片泵。
2.调速方式的确定在中小型专用机床的液压系统中,进给速度控制一般采用节流阀或调速阀。
根据钻镗类专用机床工作时对低速性能和速度负载特性都有一定要求特点,决定采用限压式变量泵和调速阀组成的容积节流阀组成的容积节流调速。
这种调速回路具有效率高、发热小和速度刚性好的特点并且调速阀装在回路上,具有承受负切削力的能力。
3.速度换接方式的选择本系统采用电磁阀的快慢速换接回路,它的特点是结构简单、调节行程比较方便,阀的安装也比较容易,但速度换接的平稳型较差。
若要提高系统的换接平稳性,则可改用行程阀切换的速度换接回路。
4.换向回路的选择由速度图可知,快进时流量不大,运动部件的重量也较小,在换向方面又无特殊要求,所以可选择电磁阀控制的换向回路。
5.液压基本回路的组成将已选择的液压回路,组成符合设计要求的液压系统并绘制液压系统原理图。
此原理图除应用了回路原有的元件外,又增加了液压顺序阀和单向阀等,其目的是防止回路间干扰及连锁反应。
液压系统原理图如图3所示:图3 液压系统原理图1、滤油器2、双联叶片泵3、外控顺序阀4、单向阀5、溢流阀6、电液换向阀7、单向行程调速阀8、压力继电器9、主液压缸10、二位三通电磁换向阀11、背压阀 12、二位二通换向阀根据原理图中进行简要分析:A、快进过程中个工作元件的工作情况1YA通电,电液换向阀左位工作,大泵→单向阀5→→电液换向阀7→行程阀14→主液压缸无杆腔小泵2→单向阀5→→电液换向阀7→行程阀14→主液压缸无杆腔液压缸有杆腔→电磁阀11→电液换向阀7→单向行程调速阀8→油箱(差动换接)B、工进过程中个工作元件的工作情况3YA通电,切断差动油路,快进行程到位,挡铁压下行程阀8,切断快进油路,3YA通电,切断差动油路,快进转工进,液压系统工作压力升高到溢流阀5调定压力,进油路高压油切断单向阀5 供油路,打开外控顺序阀4,大泵卸荷,接通经背压阀12通油箱油路。
大泵→外控顺序阀4(卸荷阀)→油箱(大泵卸荷)小泵2→→电液换向阀7→单向行程调速阀8→主液压缸无杆腔主液压缸有杆腔→电磁阀11→电液换向阀7→背压阀12→油箱C、快退过程中个工作元件的工作情况1YA断电,2Y A、3Y A、4Y A通电工进结束,液压缸碰上死挡铁,压力升高到压力继电器调定压力,压力继电器发出信息,1YA断电,2Y A、3Y A、4Y A通电大泵→单向阀5→电液换向阀7→电磁阀11→主液压缸有杆腔小泵2→单向阀5→电液换向阀7→电磁阀11→主液压缸有杆腔主液压缸无杆腔→单向行程调速阀8→电液换向阀7→电磁阀13→油箱小泵2→单向行程调速阀8→电液换向阀7→电磁阀13→油箱主液压缸无杆腔快退到位碰行程开关,行程开关发信,6YA通电。
电磁铁动作顺序表如表2所示:表2 电磁铁动作顺序表四.确定执行元件主要参数1.工作压力的确定工作压力可根据负载大小及设备类型来初步确定,见表1,根据工进负载F I=20500N,选P I=4MPa。
为防止加工结束动力头突然前冲, 设回油有背压阀或调速阀,取背压P2=0.8 MPa。
2.确定液压缸的内径D和活塞杆直径d取液压缸无杆腔有效面积等于有杆腔有效面积的2倍=P1A1- P2A2= A1(P1- P2 A2/ A1)F/m快进速度V=4500mm/min,工进速度V=100mm/min,相差很大,需进行差动换接,取k= A2/ A=0.5,则:1根据液压缸尺寸系列表,取液压缸筒标准值:D=104mm根据液压缸快进快退速度相近,取d/D=0.7,则活塞杆直径d=0.7×104mm=72.8mm,按活塞杆系列表取d=73mm 。
根据已取缸径和活塞竿内径,计算出液压缸实际有效工作面积,无竿腔面积A1和有竿腔面积A2分别为22156.849041mm D A ==π2222745.3812)(41mm d D A =-=π液压缸的实际计算工作压力为:MPa D F P 4.2104.014.3205004422=⨯⨯==π 则实际选取的工作压力P=4MP 满足要求 按最低工作速度验算液压缸的最小稳定速度23min min 1.260104.0100005.0cm v Q =⨯⨯⨯=-由于A>min min v Q ,所以能满足最小稳定速度的要求 3. 计算在各工作阶段液压缸所需的流量min)/(82.184/5.4073.014.34/d 22L v Q =⨯⨯==快进快进πmin)/(084.04/1.0*104.0*104.0*14.34/min 2min L v D Q ===工进工进π min)/(58.74/max 2max L v D Q ==工进工进πmin)/(38.194/5.4*)073.0*073.0104.0*104.0(14.34/)d D 22L v Q =-=-=快退快退(π4. 计算液压缸各运动阶段的压力,流量和功率根据上述所确定的液压缸的内径D 和活塞杆直径d ,以及差动快进时的压力损失时 ΔP=0.5MPa ,工进时的背压力ΔP=0.8MPa 快退时ΔP=0.5MPa ,则可以计算出液压缸各工作阶段的压力,流量和功率。
如表3所示:表3各工况下的主要参数值液压工况图如4所示:五. 确定液压泵的规格和电动机功率及型号1 计算液压泵的压力由于本设计采用双泵供油方式,根据液压系统的工况图,大流量液压泵只需在快进和快退阶段向液压缸供油,因此大流量泵工作压力较低。
小流量液压泵在快速运动和工进时都向液压缸供油,而液压缸在工进时工作压力最大,因此对大流量液压泵和小流量液压泵的工作压力分别进行计算。
根据液压泵的最大工作压力计算方法,液压泵的最大工作压力可表示为液压缸最大工作压力与液压泵到液压缸之间压力损失之和。
对于调速阀进口节流调速回路,选取进油路上的总压力损失p 0.8MPa ∑∆=,同时考虑到压力继电器的可靠动作要求压力继电器动作压力与最大工作压力的压差为0.5MPa ,则小流量泵的最高工作压力可估算为()P P P P a M p 7.3M 5.08.04.2P P a max 1=++=++=继电器损大流量泵只在快进和快退时向液压缸供油,快退时液压缸中的工作压力比快进时大,如取进油路上的压力损失为0.5MPa ,则大流量泵的最高工作压力为:()P P P P P a a M M p 76.15.026.112=+=+=损2.计算液压泵的流量 液压泵的最大流量q 泵应为: Qp ≥K L (∑Q)max式中:Qp----液压泵的最大流量;(∑Q)max----同时动作各液压缸所需流量之和的最大值。