样品出货跟踪记录表
出货检验作业流程

出货检验作业流程1.准备:检验员需要了解产品的规格和要求,并准备所有必要的检验设备和工具,如测量工具、测试设备、检验记录表等。
2.取样:从要发货的产品批次中随机抽取样品。
取样的数量要根据订单要求和出货批次的大小进行确定。
确保样品的代表性,避免选择异常样品。
3.外观检验:首先对样品进行外观检查。
检验员应仔细观察产品的外观,包括颜色、形状、表面缺陷、划痕等。
根据产品要求,判断外观是否符合标准。
4.尺寸测量:对产品的尺寸进行测量。
根据产品规格书和要求,使用合适的测量工具测量产品的长度、宽度、高度、厚度等尺寸。
将测量结果与产品要求进行比较,确定产品尺寸是否合格。
5.功能测试:对产品的功能进行测试。
使用合适的测试设备和方法,对产品进行各项功能测试,如电气性能、机械性能、工作稳定性等。
确保产品能够正常工作,并满足客户的要求。
7.检验记录:将检验结果记录在检验记录表中。
记录包括样品编号、检验时间、检验员、外观、尺寸、功能等项。
如发现不合格的产品,需详细描述不合格原因和具体情况。
8.判定:根据检验结果,对产品进行判定。
如果产品的外观、尺寸、功能等符合要求,则判定为合格产品,可以进行发货。
如果产品不符合要求,则判定为不合格产品,需进行处理,如重新生产、修复、退货等。
9.决策:根据检验结果和判定,制定相应的决策。
如果产品合格,可以进行发货,并将相应的检验记录和报告发送给客户。
如果产品不合格,需要与客户协商处理方式,并根据客户的要求和协议进行处理。
10.追踪和改进:对检验作业进行追踪和改进。
记录和分析每次的检验结果,发现问题并采取纠正措施,以提高检验作业的效率和准确性,提升产品质量。
综上所述,出货检验作业流程是一个非常重要的环节,可以确保产品质量符合客户要求,并保证产品在运输和使用过程中的安全和可靠性。
通过合理执行和完善流程,可以提高质量管理水平,达到项目的成功交付。
客户打样订单生产流程
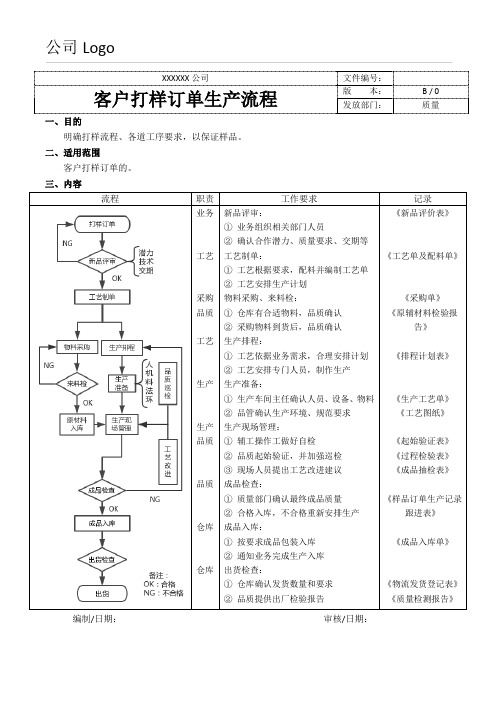
生产排程:
①工艺依据业务需求,合理安排计划
②工艺安排专门人员,制作生产
生产准备:
①生产车间主任确认人员、设备、物料
②品管确认生产环境、规范要求
生产现场管理:
①辅工操作工做好自检
②品质起始验证,并加强巡检
③现场人员提出工艺改进建议
成品检查:
①质量部门确认最终成品质量
②合格入库,不合格重新安排生产
一、目的
明确打样流程、各道工序要求,以保证样品。
二、适用范围
客户打样订单的。
三、内容
流程
职责
工作要求
记录
业务
工艺
采购
品质
工艺
生产
生产
品质
品质
仓库
仓库
新品评审:
①业务组织相关部门人员
②确认合作潜力、质量要并编制工艺单
②工艺安排生产计划
物料采购、来料检:
①仓库有合适物料,品质确认
成品入库:
①按要求成品包装入库
②通知业务完成生产入库
出货检查:
①仓库确认发货数量和要求
②品质提供出厂检验报告
《新品评价表》
《工艺单及配料单》
《采购单》
《原辅材料检验报告》
《排程计划表》
《生产工艺单》
《工艺图纸》
《起始验证表》
《过程检验表》
《成品抽检表》
《样品订单生产记录跟进表》
《成品入库单》
《物流发货登记表》
《质量检测报告》
编制/日期:审核/日期:
出货检验控制程序(含表格)

出货检验控制程序(ISO9001-2015)1.0目的:确保交付给客户的产品符合客户品质要求。
2.0范围:凡本公司所销售之产品均属之。
3.0定义:无。
4.0权责:4.1品保部:产品出货前的检验工作。
4.2制造/仓储:出货产品的包装和搬运,交货工作。
4.3生管:制订出货计划和出货交付运输安排。
5.0作业内容:5.1生管课依据客户订单交期或排程做出生产出货计划表以E-MAIL或PAPER 档的形式通知到品保、仓储、制造等各相关单位。
5.2制程产品在入库前需经过OQC检验,仓储根据出货需求,把待出货之产品移置到“OQC待检区”。
5.3OQC依据《SIP》、承认样本及限度样品的要求对出货前的产品进行抽样检验,并把检验结果记录在《制程巡检/抽检品质记录表》及《出货检验报告单》中。
5.4抽检时OQC按每个栈板为一个批次或小件以不超过1000PCS为一个批次,按照《ISO2859抽样计划》正常单次抽样,AQL:MA为0.4,Mi为0.65。
出现客诉问题需重点检查,无客诉问题产品则以出货前的查核为主。
如有客户要求,则按客户要求标准进行。
5.5OQC检验判定合格:5.5.1OQC依据《检试验管理程序》的要求在《产品标识单》上盖“OQCPASS”章。
5.5.2制造依据《产品标示单》OQC的标识进行入库。
5.6OQC检验判定不合格:5.6.1OQC把不合格现象或不合格样品呈报上级主管后,确认为异常,则发出《品质异常联络单》给相关责任单位处理与改善,并要求相关责任单位在《品质异常联络单》背面会签。
具体依照《品质异常处理流程》执行。
不合格批,每一栈板朝外的最上层的左上角贴《不良品标示单》,注明相关不良现象等内容。
具体依照《检试验管理程序》执行。
5.6.2经OQC判定的不合格品依据《不合格管理程序》进行处理;相关单位评审是否采取纠正措施或预防措施,如需采取纠正措施或预防措施则依据《纠正与预防措施管理程序》执行。
如果不采取纠正措施,因出货紧急,在不影响功能的情况下,由生管或业务提出特采申请,具体依照《特采作业流程》执行。
样品出货详细流程

样品出货详细流程
项目部各项目负责人
样品送至成品仓库指定位置
成品仓库王锐连&史德胜
需物资出厂单,保安签字和财务盖章
营销部各业务员
快递公司
详细说明:
项目部把样品送至成品仓库指定位置,仓库接收后填写物资出厂单,列明样品详情,保安核实无误后在物资出厂单上签字,仓库再交财务盖章,以上手续完成之后业务员才可领取样品交由快递公司出样。
以后业务员不得私自在项目部直接领取样品,为了保证业务员能及时拿到样品,烦请项目部提早把样品交至仓库以满足出样的及时率。
谢谢配合!
通知自今日起开始实行!
2008-06-09。
出货检验报告范文
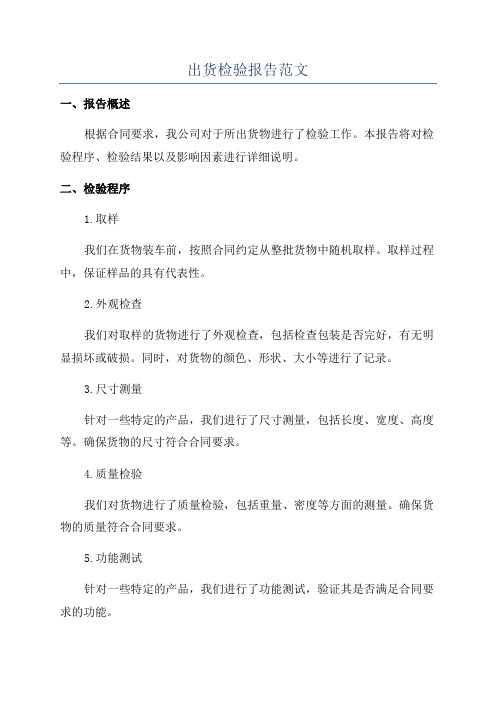
出货检验报告范文一、报告概述根据合同要求,我公司对于所出货物进行了检验工作。
本报告将对检验程序、检验结果以及影响因素进行详细说明。
二、检验程序1.取样我们在货物装车前,按照合同约定从整批货物中随机取样。
取样过程中,保证样品的具有代表性。
2.外观检查我们对取样的货物进行了外观检查,包括检查包装是否完好,有无明显损坏或破损。
同时,对货物的颜色、形状、大小等进行了记录。
3.尺寸测量针对一些特定的产品,我们进行了尺寸测量,包括长度、宽度、高度等。
确保货物的尺寸符合合同要求。
4.质量检验我们对货物进行了质量检验,包括重量、密度等方面的测量。
确保货物的质量符合合同要求。
5.功能测试针对一些特定的产品,我们进行了功能测试,验证其是否满足合同要求的功能。
6.其他检验根据合同约定,我们可能进行了其他特殊的检验项目,如化学成分分析、物理性能测试等。
三、检验结果根据上述检验程序,我们得出了以下检验结果:1.外观检查:货物包装完好,无损坏或破损。
2.尺寸测量:货物尺寸符合合同要求,长度为X cm,宽度为Y cm,高度为Z cm。
3.质量检验:货物的重量符合合同要求,密度为D g/cm³,满足质量标准。
4.功能测试:货物的功能正常,满足合同要求的要求。
5.其他检验:经过化学成分分析和物理性能测试,货物的化学成分符合标准要求,物理性能正常。
四、影响因素尽管我们尽力保证检验结果的准确性,但以下因素可能对检验结果产生影响:1.样品取样过程中的人为误差,可能导致样品的不完全代表性。
2.检验设备的准确度和精度可能存在误差,可能对测量结果产生一定的影响。
3.货物在运输过程中可能出现损坏,影响货物的外观和质量。
4.在功能测试中,可能因为测试设备的问题导致测试结果不准确。
五、结论与建议根据上述检验结果,我们认为所出货物符合合同规定的质量和功能要求。
同时,我们建议在收到货物后,进行再次检验以确认货物的完好和质量。
总之,基于以上检验程序和结果,我们可以确认所出货物的质量和功能满足合同要求。
产品出货检验报告(模板)

包装 2.规格,数量,制造日期,以及料号,客户名称,订单号必须标示清楚;不可混料,内外包装箱不可破损 检查 。
3.外包装标示是否齐全?是否贴附到最小包装单位?
检测工具
目视
不良率
判定
NG
OK
OK
OK
OK
OK
OK
OK
1.依据《外观检验标准书》,RING高光面不可存在振纹、划伤、异色、白点、毛刺等不良;裙边上 下不可存在毛刺,凸台位置不可存在毛刺等;
OK
外观
检查 2.依据颜色留样品和颜色矩阵比对是否符合产品要求?
OK
3.比对留样或样品确认产品结构,不可多料,少料
OK
实配 1.根据客提供TP屏实际组装确认,产品装配满足客户要求。
/
标准尺寸/公差
实测尺寸(mm)
(mm)
1
2
3
4
5
6
测量工具
卡尺
OK
尺
寸
测
量
0 0
备注
类型
测试项目/判定
RCA纸带耐 低温储存 磨测试 测试
高温储存 测试
恒温恒湿 储存测试
冷热冲击
盐雾测试
按压测试
/
/பைடு நூலகம்
/
/
/
/
/
相关 测试
汗液测试 1.可靠性测
试 /
耐化妆品 测试
/
紫外线老 化测试
/
钢球跌落 测试
/
百格测试 /
水煮试验 /
酒精摩擦试验 /
橡皮摩擦 铅笔硬度 抗化学试
试验
试验
剂试验
/
/
/
xx测试 2.功能测试
出货检验(OQC) 作业指导书,流程
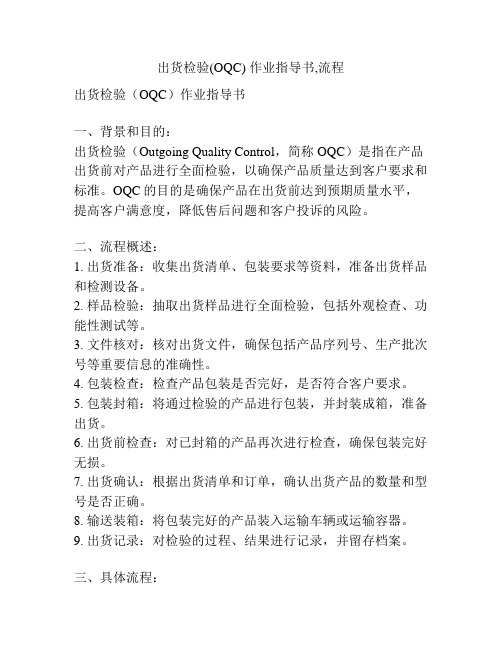
出货检验(OQC) 作业指导书,流程出货检验(OQC)作业指导书一、背景和目的:出货检验(Outgoing Quality Control,简称OQC)是指在产品出货前对产品进行全面检验,以确保产品质量达到客户要求和标准。
OQC的目的是确保产品在出货前达到预期质量水平,提高客户满意度,降低售后问题和客户投诉的风险。
二、流程概述:1. 出货准备:收集出货清单、包装要求等资料,准备出货样品和检测设备。
2. 样品检验:抽取出货样品进行全面检验,包括外观检查、功能性测试等。
3. 文件核对:核对出货文件,确保包括产品序列号、生产批次号等重要信息的准确性。
4. 包装检查:检查产品包装是否完好,是否符合客户要求。
5. 包装封箱:将通过检验的产品进行包装,并封装成箱,准备出货。
6. 出货前检查:对已封箱的产品再次进行检查,确保包装完好无损。
7. 出货确认:根据出货清单和订单,确认出货产品的数量和型号是否正确。
8. 输送装箱:将包装完好的产品装入运输车辆或运输容器。
9. 出货记录:对检验的过程、结果进行记录,并留存档案。
三、具体流程:1. 出货准备:a. 收集出货清单、包装要求等资料,并确认所需检测设备的可用性。
b. 准备出货样品,根据产品类型和规模,确定样品数量。
c. 准备检测设备和工具,确保能满足全面检验的要求。
2. 样品检验:a. 根据抽样标准,从待出货产品中抽取样品。
b. 进行外观检查,包括外包装完好性、产品外观是否无破损等。
c. 进行功能性测试,根据产品特性和标准,测试产品性能和功能是否符合要求。
3. 文件核对:a. 核对产品序列号、生产批次号等信息,确保准确无误。
b. 核对出货文件,包括合格证、检验报告等,确保文件齐全。
4. 包装检查:a. 检查产品包装是否完好,是否符合客户要求。
b. 检查包装材料是否符合防潮、防震、防尘等要求。
5. 包装封箱:a. 将通过检验的产品进行包装,确保包装方式正确无误。
b. 封装成箱,贴上标签,做好箱子标识。
供应商样品评估表
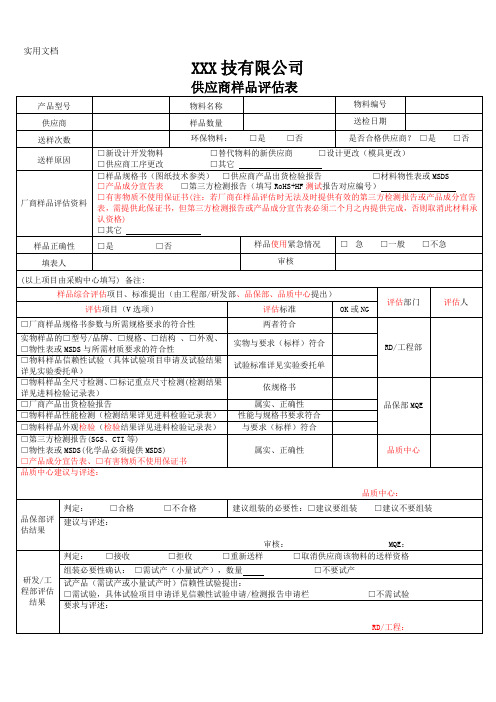
审核: MQE:
研发/工程部评估结果
判定: □接收 □拒收 □重新送样 □取消供应商该物料的送样资格
组装必要性确认: □需试产(小量试产),数量□不要试产
试产品(需试产或小量试产时)信赖性试验提出:
□需试验,具体试验项目申请详见信赖性试验申请/检测报告申请栏 □不需试验
要求与评述:
RD/工程:
□物料样品外观检验(检验结果详见进料检验记录表)
与要求(标样)符合
□第三方检测报告(SGS、CTI等)
□物性表或MSDS(化学品必须提供MSDS)
□产品成分宣告表、□有害物质不使用保证书
属实、正确性
品质中心
品质中心建议判定: □合格 □不合格
建议组装的必要性:□建议要组装 □建议不要组装
XXX技有限公司
供应商样品评估表
产品型号
物料名称
物料编号
供应商
样品数量
送检日期
送样次数
环保物料: □是□否
是否合格供应商?□是 □否
送样原因
□新设计开发物料 □替代物料的新供应商 □设计更改(模具更改)
□供应商工序更改 □其它
厂商样品评估资料
□样品规格书(图纸技术参类) □供应商产品出货检验报告□材料物性表或MSDS
□急 □一般 □不急
填表人
审核
(以上项目由采购中心填写) 备注:
样品综合评估项目、标准提出(由工程部/研发部、品保部、品质中心提出)
评估部门
评估人
评估项目(V选项)
评估标准
OK或NG
□厂商样品规格书参数与所需规格要求的符合性
两者符合
RD/工程部
实物样品的□型号/品牌、□规格、□结构 、□外观、□物性表或MSDS与所需材质要求的符合性