轴承钢管生产工艺
钢管分类大全 钢管生产工艺大全

钢管分类大全钢管生产工艺大全钢管分类大全钢管生产工艺大全钢管分类大全.钢管生产工艺大全钢管按生产方法可以分成两大类:无缝钢管和存有缠钢管。
1.无缝钢管按生产方法可分为:热轧无缝管、冷拔管、精密钢管、热扩管、冷旋压管和挤压管等。
无缝钢管用优质碳素钢或合金钢做成,存有钢材、钢(忽)之分后。
2.焊接钢管因其焊接工艺不同而分为炉焊管、电焊(电阻焊)管和自动电弧焊管,因其焊接形式的不同分为直缝焊管和螺旋焊管两种,因其端部形状又分为圆形焊管和异型(方、扁等)焊管。
冲压钢管就是由卷曲管形的钢板以对缝或螺旋缠冲压而变成,在生产方法上,又分成扰动流体运送用冲压钢管、螺旋缠电焊钢管、轻易卷焊接钢管、电焊管及等。
无缝钢管可以用作各种行业的液体气压管道和气体管道等。
冲压管道可以用作输水管道、煤气管道、暖气管道、电器管道等。
钢管按制管材质(即钢种)可分为:碳素管和合金管、不锈钢管等。
碳素管及又可以分成普通碳素钢管及和优质碳素结构管。
合金管又可分为:低合金管、合金结构管、高合金管、高强度管。
轴承管、耐热耐酸不锈管、精密合金(如可伐合金)管以及高温合金管等。
按相连接方式分类钢管按管端联接方式可分为:光管(管端不带螺纹)和车丝管(管端带有螺纹)。
车丝管又分为:普通车丝管和管端加厚车丝管。
加厚车丝管还可以分成:外加厚(拎外螺纹)、内加厚(拎内螺纹)和内外加厚(拎内外螺纹)等地车丝管。
车丝管若按螺纹型式也可分为:普通圆柱或圆锥螺纹和特殊螺纹等地车丝管。
另外,根据用户需要,车丝管一般均配有管接头交货。
按镀涂特征分类钢管按表面镀涂特征可分为:黑管(不镀涂)和镀涂层管。
镀层管存有镀锌管、镀铝管、镀铬管、滤渣铝管以及其他合金层得钢管。
涂层管有外涂层管、内涂层管、内外涂层管。
通常采用的涂料有塑料、环氧树脂、煤焦油环氧树脂以及各种玻璃型的防腐涂层料。
镀锌管又分为kbg管,jdg管,螺纹管等不锈钢管分类按生产方式分类不锈钢管按生产方式分为无缝管和焊管两大类,无缝钢管又可分为热轧管,冷轧管、冷拔管和挤压管等,冷拔、冷轧是钢管的二次加工;焊管分为直缝焊管和螺旋焊管等。
轴承制造专业术语

气体环境: 一个有限的空间如熔炉里的空气的组成成分。
ATMOSPHERE CONTROLLED FURNACE: Furnace which uses endothermic base atmosphere
which is formed by the partial reaction of a mixture of fuel, gas, and air in an
80% ANNEAL: Tempering operation; process of heating product to remove hydrogen
from railroad product so the product does not crack.
80% 退火:回火操作;加热去氢以达到用于铁路的产品不易碎裂的目的。
the production of high quality alloy steel.
合金钢:指钢中含有铁,碳,以及镍、铬、钼等一种或多种其他的合金元素。Timken 公司是全球领先的高质量合金钢的生产商。
AMERICAN NATIONAL STANDARDS INSTITUTE - ANSI: An agency that develops standards
tempering or stabilizing process. (Also called Shotblasting)
磨料喷砂法:热处理之后磨削之前去除产品表面氧化皮的工序;把工件放进滚筒里,用高速金属磨料喷击表面。这道工序也起到回火或退火处理的作用。(也叫喷丸处理)
ABRASIVE WEARING: Damage to bearing parts caused by fine foreign particles which
GCr15轴承钢管快速球化退火工艺研究

编号 为 K1 K , , 9 , 2 … K 。其 主 要化 学 成分 ( 量百 分 质
含 量 ) 别 为 W( ) 09 % , Mn= . % , S) 分 C = .9 W( ) 03 0 W(i=
0 1 %, ( r 1 4 .9 w C) . %。 =4
间 长 达 l~ 8 。 2 1h
在不 改 变 工艺 流 程 的情 况 下 , 热 轧穿 孔后 的 对
年 快 速球 化退 火工 艺成 为研 究 的热点 。
毛管 进 行取 样 。任 意抽 取 一 根 穿孑 后 雾冷 的毛管 . L 其 规格  ̄4 mmx m 距 毛 管 端 部 2 0 1 4 m, 0 mm 处 , 砂 用
基 金 项 目 : 庆 科 技 学 院 横 向科 研 项 目( 1— 0 )重 庆 科 技 学 院 大 学生 科 技 创 新 项 目 重 19 0 1 ; 作 者 简 介 : 蜀 焱 (9 3 )男 , 川南 部 人 , 士 , 师 , 任 17 一 , 四 硕 讲 研究 方 向 为材 料 加 工 。
铁 素 体 通 过 碳 的扩 散 向奥 氏体 基 体 生 长 形 成 等 轴 状 晶粒 。 因此 , 现 离 异 共 析 转 变 的 关 键 是 在 基 体 实 中保 持 足 够 的 弥 散 的未 溶 碳 化 物粒 子 作 为后 续 的
8 0C;保 温 1 ~ 0 n后 随 炉 冷 10 i ,冷 却 到 1 ̄ 0 2 mi 2 mn
摘
要 : 据快 速球 化 退 火 原 理 , 生 产现 场切 取 G r5轴 承 钢 管 试 样 , 照 不 同 的 快 速 球化 退 火 方 案 试 验 。 察 其 根 从 Cl 按 观
轴承钢的冶炼
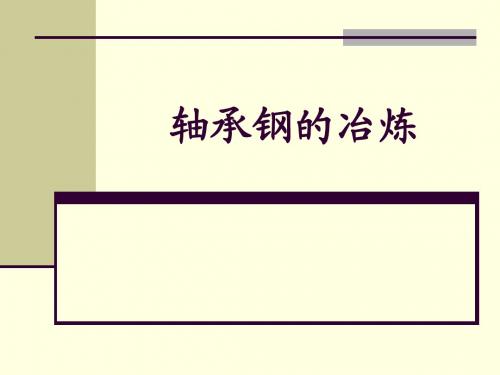
于废钢;
采用铁水预处理,进一步提高铁水的纯净度; 转炉终点碳控制水平高,钢渣反应比电炉更趋
于平衡;
转炉钢气体含量低;
连铸和炉外精炼和工艺水平与电炉相当。
日本和德国采用不同的生产工艺,区别——炼
钢终点碳的控制;
日本——“三脱”预处理,少渣冶炼高碳钢技
大容量初炼炉,保证钢水低磷,成份温度合格,
实现无渣出钢;
具备加热、真空、合金微调的精炼装置,最大限
度脱除氧、氢等气体。保护浇铸防二次氧化;
采用多极组合电磁搅拌和轻压下技术,保证钢坯
的中心质量,减少中心偏析;
轧机均为无扭无张力高速轧机轧制,保证轧材尺
寸精度和表面质量。
国产轴承钢精炼比已经达到 100% ,平均氧含
调整钢液成分、调整精炼渣成分、吹氩搅拌;
快速造碱性渣——脱氧脱硫;
底吹氩控制 —— 过大,钢渣反应过分激烈和钢液
对耐火材料冲刷严重,氧化物和钛化物进入钢液; 过小钢液温度、成分以及钢渣反应都不均匀,不
充分,脱氧产物不能充分上浮;
合适的底吹氩制度:精炼前期以较大的氩气压力
搅拌;后期以较小的氩气压力搅拌 ——使钛含量
/模铸(410mm×560mm),棒线材;
日本新日铁:高炉——转炉——LD转炉——LF
钢包精炼——RH——连铸,生产Ø19-120mm棒 线材;
日本爱知制钢:EAF——钢包精炼——RH——
连铸,生产Ø16-100mm棒线材;
德国克虏伯:110t UHP- EAF——钢包冶金——
连铸(6流260mm×330mm),生产Ø28-80mm
浇注过程中夹杂物的控制
常见汽车级机床用零件机加热处理工艺路线
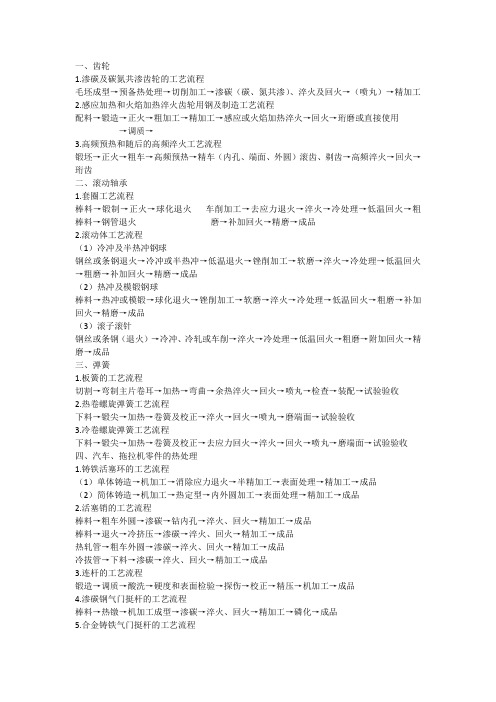
一、齿轮1.渗碳及碳氮共渗齿轮的工艺流程毛坯成型→预备热处理→切削加工→渗碳(碳、氮共渗)、淬火及回火→(喷丸)→精加工2.感应加热和火焰加热淬火齿轮用钢及制造工艺流程配料→锻造→正火→粗加工→精加工→感应或火焰加热淬火→回火→珩磨或直接使用→调质→3.高频预热和随后的高频淬火工艺流程锻坯→正火→粗车→高频预热→精车(内孔、端面、外圆)滚齿、剃齿→高频淬火→回火→珩齿二、滚动轴承1.套圈工艺流程棒料→锻制→正火→球化退火车削加工→去应力退火→淬火→冷处理→低温回火→粗棒料→钢管退火磨→补加回火→精磨→成品2.滚动体工艺流程(1)冷冲及半热冲钢球钢丝或条钢退火→冷冲或半热冲→低温退火→锉削加工→软磨→淬火→冷处理→低温回火→粗磨→补加回火→精磨→成品(2)热冲及模锻钢球棒料→热冲或模锻→球化退火→锉削加工→软磨→淬火→冷处理→低温回火→粗磨→补加回火→精磨→成品(3)滚子滚针钢丝或条钢(退火)→冷冲、冷轧或车削→淬火→冷处理→低温回火→粗磨→附加回火→精磨→成品三、弹簧1.板簧的工艺流程切割→弯制主片卷耳→加热→弯曲→余热淬火→回火→喷丸→检查→装配→试验验收2.热卷螺旋弹簧工艺流程下料→锻尖→加热→卷簧及校正→淬火→回火→喷丸→磨端面→试验验收3.冷卷螺旋弹簧工艺流程下料→锻尖→加热→卷簧及校正→去应力回火→淬火→回火→喷丸→磨端面→试验验收四、汽车、拖拉机零件的热处理1.铸铁活塞环的工艺流程(1)单体铸造→机加工→消除应力退火→半精加工→表面处理→精加工→成品(2)简体铸造→机加工→热定型→内外圆加工→表面处理→精加工→成品2.活塞销的工艺流程棒料→粗车外圆→渗碳→钻内孔→淬火、回火→精加工→成品棒料→退火→冷挤压→渗碳→淬火、回火→精加工→成品热轧管→粗车外圆→渗碳→淬火、回火→精加工→成品冷拔管→下料→渗碳→淬火、回火→精加工→成品3.连杆的工艺流程锻造→调质→酸洗→硬度和表面检验→探伤→校正→精压→机加工→成品4.渗碳钢气门挺杆的工艺流程棒料→热镦→机加工成型→渗碳→淬火、回火→精加工→磷化→成品5.合金铸铁气门挺杆的工艺流程合金铸铁整体铸造(间接端部冷激)→机械加工→淬火、回火→精加工→表面处理→成品合金铸铁整体铸造(端部冷激)→机械加工→消除应力退火→精加工→表面处理→成品钢制杆体→堆焊端部(冷激)→回火→精加工→成品钢制杆体→对焊→热处理→精加工→表面处理→成品6.马氏体型耐热钢排气阀的工艺流程马氏体耐热钢棒料→锻造成型→调质→校直→机加工→尾部淬火→抛光→成品7.半马氏体半奥氏体型耐热钢(Gr13Ni7Si2)排气阀的工艺流程棒料→顶锻→精压→热处理→精加工→成品8.奥氏体耐热钢排气阀的工艺流程棒料→顶锻→精压→阀面和尾部堆焊耐热合金→热处理→杆部滚压或软氮化→精加工→成品9.半轴调质的工艺流程合金结构钢棒料→锻造成形→正火或退火→机械加工→调质→校直→精加工→成品10.半轴的表面淬火的工艺流程棒料→锻造成形→预先热处理→校直→机械加工→表面淬火→校直→精加工→成品11.柱塞副和喷油嘴偶件的工艺流程热扎退火棒料→自动机加工成型→热处理→精加工→时效→成品12.拖拉机履带板(1)40SiMn2履带板的热处理热轧成形→下料→机加工→热处理→成品(2)ZGMn13履带板的热处理铸造成型→热处理→成品五、金属切削机床零件的热处理1.机床导轨(1)MM7125平面磨床立柱镶钢导轨锻造→正火→机加工→消除应力退火→机加工→淬火→回火→磨(2)M9025工具曲线磨床镶钢导轨锻造→退火→机加工→淬火→回火→磨(3)S788轴承磨床镶钢导轨机加工→消除应力退火→机加工→渗碳→淬火→回火→磨→时效(4)MZ208轴承磨床镶钢导轨锻造→退火→机加工→消除应力退火→机加工→淬火→冰冷处理→回火→磨→时效2.机床主轴(1)CA6104车窗主轴(45钢)下料→粗加工→正火→机加工→高频淬火→回火→磨(2)T68、T611镗床的镗杆及MGB132磨床的主轴(35CrMoAlA钢)下料→粗车→调质→精车→消除应力处理→粗磨→渗氮→粗磨(3)SGC630精密丝杠车床主轴(12CrNi3A)锻造→正火→机加工→渗碳→正火→校直→消除应力→机加工→头部淬火→颈部淬火→回火→磨→时效(4)X62W万能升降台铣床主轴(球墨铸铁QT60-2)铸造→机加工→淬火→回火(5)M1040无心磨床主轴(球墨铸铁QT60-2)铸造→机加工→正火→机加工3.丝杠(1)7级或7级精度一下的一般丝杠(45钢)下料→正火或调质→校直→消除应力处理→机加工(2)6级或6级以上精密不淬硬丝杠(T10或T12钢)球化退火→机加工→消除应力处理→机加工→时效→精加工(3)中大型精密淬硬丝杠(CrWMn)锻造→球化退火→机加工→消除应力→机加工→消除应力→机加工→淬火、回火→冰冷处理→回火→探伤→机加工→时效→精加工→时效→精加工(4)中小型精密淬硬丝杠(9Mn2V)锻造→球化退火→机加工→消除应力→机加工→淬硬淬火→回火→冰冷处理→回火、探伤→机加工→时效→精加工→时效→精加工(5)滚珠丝杠(GCr15,GCr15SiMn)4.弹簧卡头(1)卧式多轴自动车床夹料卡头(9SiCr)锻造→退火→机加工→淬火→回火→机加工→磨开口→胀大定型(2)卧式多轴自动车床送料卡头(T8A钢)锻造→退火→机加工→淬火→回火→磨(3)仪表机床小型专用卡头(60Si2)退火→机加工→淬火→回火→磨(4)磨阀辨机床专用卡头(65Mn)锻造→正火→高温→回火→机加工→淬火→回火→机加工5.摩擦片(1)X62W万能升降台铣床摩擦片(A3)机加工→渗碳→淬火→回火→机加工→回火(2)DLMO电磁离合器摩擦片(65Mn)冲片→淬火→回火→磨(3)电磁离合器摩擦片(6SiMnV)锻造→退火→切片→淬火→回火→磨6.FW250万能分度头主轴(45)锻造→正火→机加工→淬火→回火→机加工7.万能分度头蜗杆(20Cr)正火→机加工→渗碳→机加工→淬火→回火→机加工8.三爪卡盘卡爪(45)正火→机加工→淬火→回火→高频淬火→回火→法蓝→磨加工9.三爪卡盘丝(45)锻造→正火→机加工→淬火→回火→法蓝→磨六、活塞1.20CrMnMo钢制活塞的热处理锻造→正火→检验→机加工→渗碳→检验→正火→淬火→清洗→回火→检验→喷砂→磨削2.钒钢活塞的热处理下料→锻造→检验→预先淬火→球化退火→检验→机加工→淬火→回火→检验→磨削七、凿岩机钎尾锻造→退火→检验→渗碳→检验→淬火→回火→清洗→检验→磨削。
轴类零件加工工艺
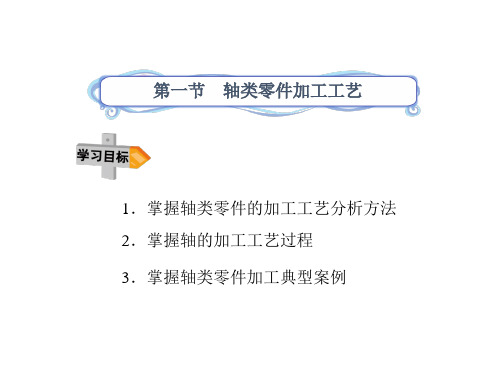
• 一、箱体零件的功用、结构及技术要求
1.功用、结构
功用:将机器中有关部件的轴、套、齿轮等相关零件连接成 一个整体,使这些零件保持正确的相对位置,并按一定的传动关 系协调地工作。
结构:形状复杂,壁薄且不均匀,内部呈腔形,既有精度要求 较高的孔系和平面,也有许多精度要求较低的紧固孔。
a)
b)
a)齿轮油泵箱体 b)齿轮减速箱箱体
Hale Waihona Puke 2.防止套类零件变形的工艺措施套类零件一般都存在壁较薄、径向刚度较差、容易变形等缺点。
套类零件变形的原因及工艺措施
导致变形的因素
工艺措施
夹紧力
(1)使夹紧力均匀分布,如图a所示 (2)变径向夹紧为轴向夹紧,如图b所示 (3)增加套筒毛坯的刚度,如图c所示
外力
切削力
重力 离心力
(1)增大刀具的主偏角 (2)内、外表面同时加工,如图c所示 (3)粗、精加工分开进行 增加辅助支承 配重
套类零件的毛坯类型与所用材料、结构形状和尺寸大小有关, 常采用型材、锻件或铸件。
毛坯内孔直径小于φ20mm时大多选用棒料,孔径较大、长度 较长的零件常用无缝钢管或带孔的铸、锻件。
• 三、套类零件的加工工艺分析
1.保证相互位置精度的工艺措施
轴承套毛坯采用“4件合一”的方 式加工:指棒料按四个轴承套零件尺 寸下料,四件同时加工
传动轴是轴类零件中使 用最多、结构最为典型的一 种阶梯轴,所示。该轴为小 批量生产,材料选择45钢, 淬火硬度40~45HRC。试分 析其加工工艺过程。
1.结构分析
主要结构要素有内外圆柱面、螺纹、键槽等,该轴为典型的 阶梯轴结构,有两个支承轴颈。
2.技术要求
两端轴颈的尺寸精度为IT7,表面粗糙度Ra值为0.8μm; 用于安装齿轮的轴颈的尺寸精度主IT7,表面粗糙度Ra值为 1.6μm; 右端轴颈外圆上规定了圆柱度为0.02mm; 左端轴颈外圆上规定了圆柱度为0.02mm; 轴上各配合面对两端轴颈的公共轴线的径向跳动为0.02mm, 可保证齿轮平稳传动。
钢管加工工艺
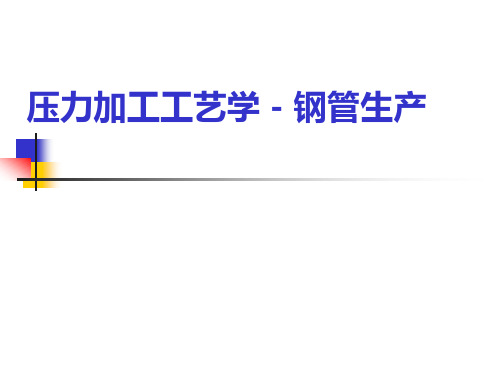
热轧无缝管:实心管坯→穿孔→延伸 →定(减)径→冷却→精整。
焊管:板带坯料→成型(管筒状) →焊 接成管→精整。
1.3 钢管的技术要求与发展趋势
⑴ 对多种腐蚀介质的高抗蚀性、对高温强度 和低温韧性的要求越来越高,使得管材产品的 化学成分不断变化,冶炼、加工工艺不断改进;
⑵ 管材产品尺寸(壁厚精度)、形状精度的要 求促使在线检测、自动控制技术不断进步;
(2)做结构件:在同样重量下,钢管相 对于其他钢材具有更大的截面模数,也 就是说它具有更大的抗弯、抗扭能力, 属于经济断面钢材、高效钢材。
二、钢管的分类
1 按生产方式分类
(1)热加工管(无缝钢管):热轧穿孔、 挤压、P.P.M(压力穿孔)、冲压法;
(2)焊管(有缝钢管):包括直缝钢管 与螺旋焊管;
压力加工工艺学-钢管生产
1 概述
1.1 钢管的特性与分类: 一、钢管的概念与用途 钢管的概念:凡是两端开口并具有中空封 闭型断面,且长度与断面周长成较大比例 的钢材,统称为钢管。而比值较小的钢材 称为管段或管件。
钢管的用途:
(1)输送流体:具有封闭的中空几何形 状,可以作为液、气体及固体的输送管 道;
(4)加热温度考虑工艺条件
a)GCr15 1%C(高碳钢),1.5%Cr(硬、耐磨),在 允许温度范围内取下限,防止脱碳;
b)硅钢希望脱碳,加热温度可提高;
(1)连铸圆坯:是目前国际上应用较多的坯料,也是衡量一 个国家钢管生产技术水平的标志之一。其具有成本低、 能耗少、组织性能稳定等特点,是管坯发展的主流,也 是钢管实现连轧的首要条件。
(2)轧坯:一般为圆坯,生产中也经常使用。 (3)铸(锭)坯:主要有方(锭)坯,用于P.P.M轧制方式(或压
力穿孔)。 (4)锻坯:用于穿孔性能较差的合金钢与高合金钢管的生产。
钢管生产流程

钢管生产流程
钢管是一种常见的金属制品,广泛应用于建筑、机械、化工等
领域。
它的生产流程经过多道工序,需要经过严格的控制和监测,
以确保产品质量和性能。
下面将介绍钢管的生产流程。
首先,钢管的生产通常以原材料的准备开始。
原材料主要包括
钢板、钢坯等。
这些原材料需要经过切割、热处理等工艺,以满足
后续生产的要求。
接下来是钢管的成型工艺。
成型工艺通常分为冷拔和热轧两种
方式。
冷拔是将钢坯通过模具冷变形成型,适用于生产精密钢管;
热轧则是将钢坯加热至一定温度后通过轧制机械成型,适用于生产
一般钢管。
随后是焊接工艺。
对于一些需要焊接的钢管,会经过焊接工艺。
焊接工艺主要包括高频焊、埋弧焊等方式,通过将钢板或钢带经过
卷板、成型、焊接等工序,最终形成焊接钢管。
然后是钢管的表面处理。
表面处理是为了提高钢管的耐腐蚀性
能和美观度。
通常包括酸洗、磷化、镀锌等工艺,以确保钢管在使
用过程中不易生锈、耐腐蚀。
最后是检测和包装。
在生产完成后,钢管需要经过一系列的检测,包括外径、壁厚、长度、化学成分、力学性能等指标的检测。
合格后,钢管会进行包装,通常采用塑料薄膜包装或捆扎包装,以
确保产品的安全运输和存储。
总的来说,钢管的生产流程经过原材料准备、成型、焊接、表
面处理、检测和包装等多个环节。
每个环节都需要严格控制和监测,以确保最终产品的质量和性能。
同时,生产过程中也需要注重节能
减排和安全生产,促进钢管产业的可持续发展。
- 1、下载文档前请自行甄别文档内容的完整性,平台不提供额外的编辑、内容补充、找答案等附加服务。
- 2、"仅部分预览"的文档,不可在线预览部分如存在完整性等问题,可反馈申请退款(可完整预览的文档不适用该条件!)。
- 3、如文档侵犯您的权益,请联系客服反馈,我们会尽快为您处理(人工客服工作时间:9:00-18:30)。
轴承钢管生产工艺
轴承钢管生产工艺是指轴承钢管的生产过程和工艺流程。
下面将介绍轴承钢管的生产工艺流程和主要步骤。
首先,轴承钢管的生产需要选择高质量的轴承钢作为原料。
轴承钢具有高强度、高硬度和良好的纯净性能,能够满足轴承钢管对材质的要求。
其次,将选好的轴承钢加热到适当温度,进行热处理。
热处理过程包括淬火和回火两个步骤,淬火可以提高轴承钢的硬度和强度,回火则能够降低轴承钢的脆性,提高其韧性和冲击韧性。
接下来,对经过热处理的轴承钢进行锻造。
锻造是指将轴承钢加热到一定温度后,通过锻造机械的冲击力使其变形,加工成希望得到的形状和尺寸。
锻造可以提高轴承钢的整体强度和塑性。
然后,对锻造好的轴承钢进行精加工。
精加工是指将轴承钢通过车、铣、磨等加工工艺,加工成轴承钢管的标准尺寸和形状。
精加工过程需要严格控制加工精度,以确保轴承钢管的质量和性能。
最后,对精加工好的轴承钢管进行检验和测试。
检验和测试包括外观检查、尺寸测量、力学性能试验和检验等。
只有通过了检验和测试的轴承钢管才能出厂销售和应用。
轴承钢管生产工艺需要掌握高精度的加工技术和严格的质量控
制。
只有在合理的工艺流程和严格的质量控制下,才能生产出高质量的轴承钢管,满足工业领域对于轴承钢管的要求。