4 金刚石刀具切削加工
四大材料刀具的性能与选择
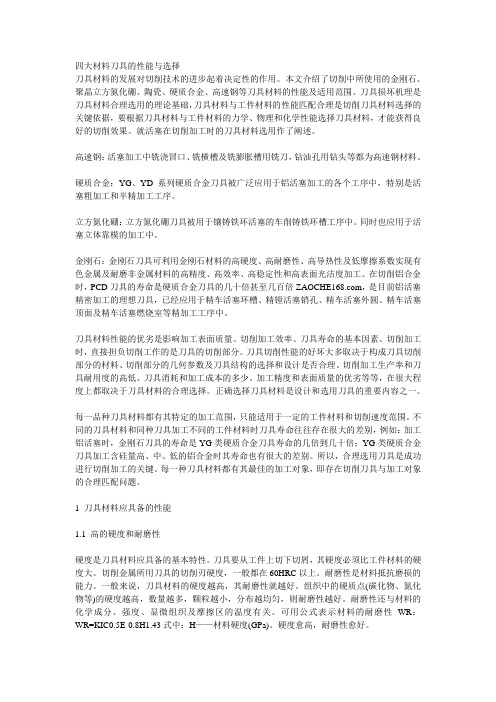
四大材料刀具的性能与选择刀具材料的发展对切削技术的进步起着决定性的作用。
本文介绍了切削中所使用的金刚石、聚晶立方氮化硼、陶瓷、硬质合金、高速钢等刀具材料的性能及适用范围。
刀具损坏机理是刀具材料合理选用的理论基础,刀具材料与工件材料的性能匹配合理是切削刀具材料选择的关键依据,要根据刀具材料与工件材料的力学、物理和化学性能选择刀具材料,才能获得良好的切削效果。
就活塞在切削加工时的刀具材料选用作了阐述。
高速钢:活塞加工中铣浇冒口、铣横槽及铣膨胀槽用铣刀,钻油孔用钻头等都为高速钢材料。
硬质合金:YG、YD系列硬质合金刀具被广泛应用于铝活塞加工的各个工序中,特别是活塞粗加工和半精加工工序。
立方氮化硼:立方氮化硼刀具被用于镶铸铁环活塞的车削铸铁环槽工序中。
同时也应用于活塞立体靠模的加工中。
金刚石:金刚石刀具可利用金刚石材料的高硬度、高耐磨性、高导热性及低摩擦系数实现有色金属及耐磨非金属材料的高精度、高效率、高稳定性和高表面光洁度加工。
在切削铝合金时,PCD刀具的寿命是硬质合金刀具的几十倍甚至几百倍,是目前铝活塞精密加工的理想刀具,已经应用于精车活塞环槽、精镗活塞销孔、精车活塞外圆、精车活塞顶面及精车活塞燃烧室等精加工工序中。
刀具材料性能的优劣是影响加工表面质量、切削加工效率、刀具寿命的基本因素。
切削加工时,直接担负切削工作的是刀具的切削部分。
刀具切削性能的好坏大多取决于构成刀具切削部分的材料、切削部分的几何参数及刀具结构的选择和设计是否合理。
切削加工生产率和刀具耐用度的高低、刀具消耗和加工成本的多少、加工精度和表面质量的优劣等等,在很大程度上都取决于刀具材料的合理选择。
正确选择刀具材料是设计和选用刀具的重要内容之一。
每一品种刀具材料都有其特定的加工范围,只能适用于一定的工件材料和切削速度范围。
不同的刀具材料和同种刀具加工不同的工件材料时刀具寿命往往存在很大的差别,例如:加工铝活塞时,金刚石刀具的寿命是YG类硬质合金刀具寿命的几倍到几十倍;YG类硬质合金刀具加工含硅量高、中、低的铝合金时其寿命也有很大的差别。
金刚石刀具生产工艺
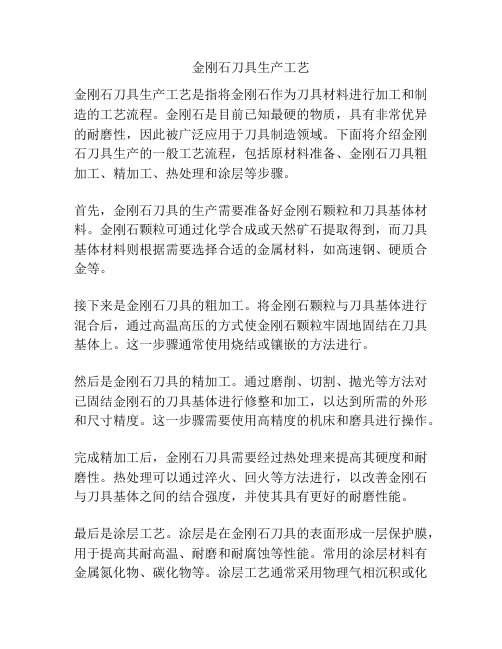
金刚石刀具生产工艺
金刚石刀具生产工艺是指将金刚石作为刀具材料进行加工和制造的工艺流程。
金刚石是目前已知最硬的物质,具有非常优异的耐磨性,因此被广泛应用于刀具制造领域。
下面将介绍金刚石刀具生产的一般工艺流程,包括原材料准备、金刚石刀具粗加工、精加工、热处理和涂层等步骤。
首先,金刚石刀具的生产需要准备好金刚石颗粒和刀具基体材料。
金刚石颗粒可通过化学合成或天然矿石提取得到,而刀具基体材料则根据需要选择合适的金属材料,如高速钢、硬质合金等。
接下来是金刚石刀具的粗加工。
将金刚石颗粒与刀具基体进行混合后,通过高温高压的方式使金刚石颗粒牢固地固结在刀具基体上。
这一步骤通常使用烧结或镶嵌的方法进行。
然后是金刚石刀具的精加工。
通过磨削、切割、抛光等方法对已固结金刚石的刀具基体进行修整和加工,以达到所需的外形和尺寸精度。
这一步骤需要使用高精度的机床和磨具进行操作。
完成精加工后,金刚石刀具需要经过热处理来提高其硬度和耐磨性。
热处理可以通过淬火、回火等方法进行,以改善金刚石与刀具基体之间的结合强度,并使其具有更好的耐磨性能。
最后是涂层工艺。
涂层是在金刚石刀具的表面形成一层保护膜,用于提高其耐高温、耐磨和耐腐蚀等性能。
常用的涂层材料有金属氮化物、碳化物等。
涂层工艺通常采用物理气相沉积或化
学气相沉积等方法进行。
综上所述,金刚石刀具的生产工艺包括原材料准备、金刚石刀具粗加工、精加工、热处理和涂层等步骤。
通过这些工艺流程,可以制造出耐磨耐用的金刚石刀具,用于各种切削加工和磨削工艺中。
第二章 特种加工 金刚石切削原理
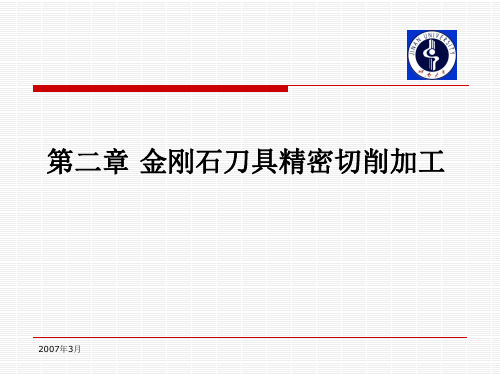
2007年3月
4、微量进给装置
设计要求: 1)精微进给和粗进给分开 2)运动部分必须是低摩擦和高稳定性 3)末端传动元件必须有很高的刚度 4)内部连接必须可靠 5)工艺性好 6)具有好的动特性 7)能实现微进给的自动控制
2007年3月
(1)压电和电致伸缩微进给装置:
2007年3月
(2)摩擦驱动装置:
2007年3月
基本要求: ★高精度 ★高刚度 ★高稳定性 ★高自动化
2007年3月
2、FG—001超精密机床
2007年3月
3、 Cranfield公司的OAGM2500大型超精密机床
◆ 研制时间:1991年 ◆ 工件: 2500X2500X610 mm大型曲面反射镜 ◆ 特点: 立式主轴结构; 龙门结构; 三轴数控联动; X、Y向采用液体 静压导轨,Z向采用空 气轴承 人造花岗岩填充床 身;附带坐标测量。
2007年3月
通用金刚石车刀--2
2007年3月
车刀的刀尖形状
2007年3月
三、金刚石刀具上金刚石的固定方法
(1)机械夹固
2007年3月
(2)用粉末冶金法固定
(3)使用粘结或钎焊固定
2007年3月
金刚石刀具研磨机结构原理图
粗磨的目的:去除余量 (研磨方向、研磨速度、 压力、金刚石微粉粒度) 精研的目的:获得高质量 (金刚石微粉粒度、研磨 盘质量、研磨方向等)
2007年3月
-- 热稳定性: 在700℃以上温度,金刚石易与铁族 金属产生化学作用而形成碳化物,造成化学 磨损。
因此,金刚石单晶的热稳定性较低, 其刀具一般不适合切削钢铁材料。
2007年3月
四、金刚石晶体各晶面的刃磨方向
2007年3月
精密加工技术(第三讲)

课堂作业
1,分析该金刚石刀 具的前角,后角,主 偏角,副偏角和修光 刃模式。
2,解释何为位错密度,表面残余应力,刀具的锋锐度?请 说明金刚石刀具的锋锐度对表面质量的影响。
பைடு நூலகம்
金刚石刀具的主切削刃和副切削刃之间采用 过渡刃对加工表面起修光作用。 国内:多采用直线修光刃,修光刃长度一般 取0.1~0.2mm 国外:多采用圆弧修光刃,圆弧半径 R=0.5~3mm。 金刚石刀具的主偏角用得较多的是45度。
2.4 金刚石刀具使用
1、金刚石刀具切削部分的几何形状
(2)前角和后角
•增加刀刃的强度考虑: 采用较大的刀具楔角,也就是刀具的前角、后角都取得 较小。 后角: a0 50 ~ 80 前角根据加工材料,切铝、铜合金前角取 0 0 ~ 5 0 。 •减小表面摩擦考虑:
2.4 金刚石刀具使用
1、普通车刀几何形状
前角:在正交平面 内,基面与前刀面 之间的夹角。
o
后角:在正交平面内, 切削平面与主后刀面 之间的夹角。
正交平面参考系
2.4金刚石刀具使用
1、普通车刀几何形状
后 角
前 角
正交平面参考系 主偏角 副偏角
2.4 金刚石刀具使用
2、金刚石刀具几何形状
(1)刀头形式
2.5 刀刃锋锐度对切削变形和加工表面质量的影响
四、刀刃锋锐度对加工表面残留应力的影响
1)刃口半径越小,残留应力越低; 2)背吃刀量越小,残留应力越小,但当背吃刀量减小 到临界值时,背吃刀量减小,残留应力增大。
三、表面层残余应力 定义:去除外力和热源作用后,零件内部自身 平衡的应力,称残余应力。 残余应力的成因: (一)局部温升过高引起的热应力 *材料在高温下,处于塑性状态,因温度升高 体积膨胀而发生塑性流动; *材料在低温下,处于弹性状态,因温度降低 体积减小而发生收缩,受下层材料的限制, 发生弹性变形,形成残余应力。
金刚石刀具

金刚石刀具金刚石刀具具有极高的硬度和耐磨性、低摩擦系数、高弹性模量、高热导、低热膨胀系数,以及与非铁金属亲和力小等优点。
可以用于非金属硬脆材料如石墨、高耐磨材料、复合材料、高硅铝合金及其它韧性有色金属材料的精密加工。
金刚石刀具类型繁多,性能差异显著,不同类型金刚石刀具的结构、制备方法和应用领域有较大区别。
天然金刚石刀具目前主要用于紫铜及铜合金和金、银、铑等贵重有色金属,以及特殊零件的超精密镜面加工,如录相机磁盘、光学平面镜、多面镜和二次曲面镜等。
但其结晶各向异性,刀具价格昂贵。
PCD的性能取决于金刚石晶粒及钴的含量,刀具寿命为硬质合金(WC基体)刀具的10~500倍。
主要用于车削加工各种有色金属如铝、铜、镁及其合金、硬质合金和耐磨性极强的纤维增塑材料、金属基复合材料、木材等非金属材料。
切削加工时切削速度、进给速度和切削深度加工条件取决于工件材料以及硬度。
人造聚晶金刚石复合片(PDC)性能和应用接近PCD刀具,主要用在有色金属、硬质合金、陶瓷、非金属材料(塑料、硬质橡胶、碳棒、木材、水泥制品等)、复合材料等切削加工,逐渐替代硬质合金刀具。
由于金刚石颗粒问有部分残余粘结金属和石墨,其中粘结金属以聚结态或呈叶脉状分布会减低刀具耐磨性和寿命。
此外存在溶媒金属残留量,溶媒金属与金刚石表面直接接触。
降低(PDC)的抗氧化能力和刀具耐热温度,故刀具切削性能不够稳定。
金刚石厚膜刀具制备过程复杂,因金刚石与低熔点金属及其合金之间具有很高的界面能。
金刚石很难被一般的低熔点焊料合金所浸润。
可焊性极差,难以制作复杂几何形状刀具,故TDF焊接刀具不能应用在高速铣削中。
金刚石涂层刀具可以应用于高速加工,原因是除了金刚石涂层刀具具有优良的机械性能外,金刚石涂层工艺能够制备任意复杂形状铣刀,用于高速加工如铝钛合金航空材料和难加工非金属材料如石墨电极等。
显示为纯金刚石。
ND是目前已知矿物中最硬的物质,主要用于制备刀具车刀。
天然金刚石刀具精细研磨后刃口半径可达0.01~0.002µm。
第二章 金刚石刀具精密切削加工

复习晶体结构
晶格模型
面心结构
晶体结构指晶体内部原子规则排列的方式.晶体结构不同, 其性能往往相差很大。为了便于分析研究各种晶体中原子 或分子的排列情况,通常把原子抽象为几何点,并用许多 假想的直线连接起来,这样得到的三维空间几何格架称为 晶格。
晶胞
Z
晶胞
c
b Y
a
X
晶格常数 a , b, c
人造单晶金刚石刀具 金刚石刀具 PCD刀具
多晶金刚石刀具
CVD金刚石薄膜涂层刀具
CVD金刚石刀具 金刚石厚度膜焊接刀具
金刚石刀具的性能特点
极高的硬度和耐磨性:硬度达HV10000,是自然界最硬的物质, 具有极高的耐磨性,天然金刚石耐磨性为硬质合金80-120倍,人 造金刚石耐磨性为硬质合金60-80倍。 各向异性能:单晶金刚石晶体不同晶面及晶向的硬度、耐磨性能 、微观强度、研磨加工的难易程度以及与工件材料之间的摩擦系 数等相差很大,因此,设计和制造单晶金刚石刀具时,必须进行 晶体定向。
二、典型机床简介
Pneumo 公司的MSG-325超精密车床
采用T形布局,机床空气主轴的径向圆跳动和轴向 跳动均小于等于0.05μm。床身溜板用花岗岩制造,导 轨为气浮导轨;机床用滚珠丝杠和分辨率为0.01μm的 双坐标精密数控系统驱动,用HP5501A双频激光干涉仪 精密检测位移。
DTM-3大型超精密车床
分为:液体静压和空气静压
供油压力恒定的液体静压轴承
主轴始终悬浮 在高压油膜上
液体静压轴承与气压轴承
1、液体静压轴承主轴
优点
回转稳定性好 刚度高 无振动
缺点
回转运动有温升 回油时有空气进入油源 注:空气静压轴承原理与静
2.4金刚石刀具解析

金刚石晶体的面网及原子排列形式
晶体内部分布有原子的面叫作晶面,也称面网
面网上原子排列形式、原子排列密度及面网间的 距离不同将造成晶体的不同晶向性能差异甚大。 三个重要晶面的原子排列形式—最小单元
金刚石晶体的面网密度及面网距
面网的单位面积上的原子数称为面网密度
三个晶面的面网密度之比为 : (100)(110)面网的分布是均匀的, (111)面网间 距一宽一窄交替看成加厚面网,宽间距即 (111)面间距 (100):(110):(111)=1:1.414:1.154
金刚石刀具结构
常把金刚石固定在小刀头上,小刀头用螺钉压板固定
在刀杆上,也有将金刚石直接固定在车刀刀杆上。
金刚石在刀头上的固定方法
1.较大颗粒的金刚石上下面磨平用压板固定在小刀头上 2.粉末冶金法固定 3.粘接或钎焊固定 金刚石放在合金粉末中,加压真空 粘接剂固定强度不高,金刚石易掉, 烧结,使金刚石固定在小刀头内。应用较多价格较高 钎焊法固定较好,钎料配方及工艺处于研究阶段。
5.金刚石刀具设计的主要问题
优选切削部分的几何形状
前后刀面选择最佳晶面
确定刀具结构及金刚石的固定方法
金刚石刀具切削部分的几何形状
国内多用 直线修光 刃,制造 容易,但
要求对刀
良好,修 光刃应严
格与进给
方向一致
金刚石刀具切削部分的几何形状
国外多用圆弧修光刃,对刀容易使用方便,但
制造研磨费事。推荐圆弧半径R=0.5~1.5mm
金刚石刀具的研磨加工
粗研
一颗单晶金刚石毛坯,要做成精密刀具,先 要晶体定向,确定前后刀面位置,确定需磨去的部分。
仔细检查内部有无缺陷。采用高速旋转铸铁盘加金刚
超精密切削加工与金刚石刀具(精密加工

2.5 切削刃锋锐度对切削变形、加工表面质量的影 响
三、切削刃锋锐度对切削变形和切削力的影响
2021/5/1
锋锐车刀切削变形系数明显低于 较钝的车刀。 刀刃锋锐度不同,切削力明显不 同。刃口半径增大,切削力增大, 即切削变形大。背吃刀量很小时, 切削力显著增大。因为背吃刀量很 小时,刃口半径造成的附加切削变 形已占总切削变形的很大比例,刃 口的微小变化将使切削变形产生很 大的变化。所以在背吃刀量很小的 精切时,应采用刃口半径很小的锋 锐金刚石车刀。
(FN ) Ff cos FP sin
A点为极限临界点,极限最小切削厚度 hDmin 应为
hDmin rn(1 cos ) rn1
2021/5/1
第2章 超精密切削与金刚石刀具
2.1超精密切削时刀具的切削速度、磨损和耐用度 2.2超精密切削时积屑瘤的生成规律 2.3切削参数变化对加工表面质量的影响 2.4刀刃锋锐度对切削变形和加工表面质量的影响 2.5超精密切削时的最小切削厚度 2.6金刚石刀具晶面选择对切削变形和加工表面质
2021/5/1
2.2 超精密切削时刀具的磨损和寿命
后刀面 前刀面
2021/5/1
图2-2:切削刃正常磨损;
图 2-3 : 图 a 是 刀 刃 磨 损 的 正常情况,图b是剧烈磨损 情况,可以看到磨损后成 层状,即刀具磨损为层状 微小剥落;
图2-4:图中所示沿切削速 度方向出现磨损沟槽,由 于金刚石和铁、镍的化学 和物理亲和性而产生的腐 蚀沟槽;
2.3 超精密切削时积屑瘤的生成规律
2、进给量f和背吃刀量 p的影响
• 由图2-7可以看出在进给量很小时,积屑瘤的高度很大,在 f=5μm/r时,h0值最小,f值再增大时,h0值稍有增加。
- 1、下载文档前请自行甄别文档内容的完整性,平台不提供额外的编辑、内容补充、找答案等附加服务。
- 2、"仅部分预览"的文档,不可在线预览部分如存在完整性等问题,可反馈申请退款(可完整预览的文档不适用该条件!)。
- 3、如文档侵犯您的权益,请联系客服反馈,我们会尽快为您处理(人工客服工作时间:9:00-18:30)。
为什么金刚石刀具中直线刃刀尖精度要高于圆弧刃刀具? 为什么金刚石刀具中直线刃刀尖精度要高于圆弧刃刀具? 关于刀尖的精度,一般认为直线刃比圆弧刃优越 ; 原因是刀头加工精度有所不同,直线刃是由平面合成的, 研磨条件好,刀头是在研磨机上涂以金刚石粉末进行研磨,平 面研磨是将被研磨面紧贴在研磨盘上进行;而圆弧面研磨是在 同样的研磨盘上,使圆弧上的一点边接触边移动进行研磨,磨 料游离使研磨条件变坏,造成圆弧面质量下降。另外,从加工 面的粗糙度来说,也是直线刃较好。 当进给量为13m/r时,用圆弧刃可得到Rmax0.01m, 用直线刃可得到Rmax0.004m。
PCD刀具材料的主要性能指标:
①PCD的硬度可达8000HV,为硬质合金的80~120倍; ②PCD的导热系数为700W/mK,为硬质合金的1.5~9倍,甚 至高于铜,因此PCD刀具热量传递迅速; ③PCD的摩擦系数一般仅为0.1~0.3(硬质合金的摩擦系数 为0.4~1),因此PCD刀具可显著减小切削力; ④PCD的热膨胀系数仅为0.9×10 -6~1.18×10 -6,仅相当 于硬质合金的1/5,因此PCD刀具热变形小,加工精度高; ⑤PCD刀具与有色金属和非金属材料间的亲和力很小,在加 工过程中切屑不易粘结在刀尖上形成积屑瘤。
刀具磨损对加工质量的影响
刀具的磨损形式在很大程度上取决于工件 工件 材料性质、金刚石特性的利用及其机床的动态 材料性质、金刚石特性的利用 机床的动态 特性。 特性 特别是金刚石的特性和磨损有很大的关系。 合理地使用金刚石刀具,可以在很长的时 间内保持较高的加工质量。
刀具的耐用度
1. 刀具磨损的影响: 刀具磨损到一定程度就不能继续使用, 否则将降低加工零件的尺寸精度和加工表面 质量,同时也增加了刀具的消耗、增加加工 成本。
2 刀具磨损过程
正常磨损情况下,刀具磨损量随切削时间增加而逐渐扩大。 正常磨损情况下,刀具磨损量随切削时间增加而逐渐扩大。若以后 刀面磨损为例,它的典型磨损过程如图所示,图中大致分三个阶段。 刀面磨损为例,它的典型磨损过程如图所示,图中大致分三个阶段。初 期磨损阶段(Ⅰ 、正常磨损阶段(Ⅱ 、急剧磨损阶段(Ⅲ 。 期磨损阶段 Ⅰ段)、正常磨损阶段 Ⅱ段)、急剧磨损阶段 Ⅲ段)。
裂纹
破损
当垂直于金刚石(111)晶面的拉力超过某特定值时,两相邻的(111)晶面分 离、产生解理劈开 解理劈开。 解理劈开 如果金刚石晶面方向选择不当,切削力容易引起金刚石的解理,使刀具寿命急 剧下降,尤其是在有冲击振动、切削不稳定的条件下,更容易产生解理。 最新研究表明,为了增加刀刃的微观强度,减小破损几率,应选用微观强度最 高的(110)晶面 ( )晶面作为金刚石刀具的前后刀面。 制作刀具时,尽可能与(111)面平行研磨并形成前刀面。 但与(111)面成平行的研磨会使加工成本过高,通常是以3左右的倾角进行 研磨以形成前刀面和锋利的切削刃。
金刚石刀头的形状
——条件是:不产生走刀痕迹的形状直线刃和圆弧刃
①直线刃刀头 安装很难,需要有高超的安装技术,有10角度误差就会影响精加工表面的质量, 但是这种刀头的加工表面精度最好。 ②圆弧刃刀头 安装容易,但加工表面精度稍差一点, 因此最好采用能微调安装角度的直线刃刀刀头。 但是加工曲率半径小的聚光反射镜等则必须采用四圆弧刃刀头。
(2)刀具的破损 )
产生刀具破损的原因: 裂纹 结构缺陷; 切屑流过刀具表面时,循环应力的作用; 刀具表面研磨应力 脆裂 解理 是指矿物被打击时,常沿一定方向有规则地裂开形成光滑平面的性质。 是指矿物被打击时 常沿一定方向有规则地裂开形成光滑平面的性质。 常沿一定方向有规则地裂开形成光滑平面的性质
4. 刀具的耐用度 刀具的耐用度是指刀具由开始切削到磨钝为止的总 切削时间。代表了刀具磨损的快慢程度。 切削时间。代表了刀具磨损的快慢程度。
金刚石刀具用于精密切削加工时, 金刚石刀具用于精密切削加工时,其破损或磨损而不能继续使用的标志是 加工表面粗糙度超过规定值。 加工表面粗糙度超过规定值。 金刚石刀具的耐用度一般用切削路程的长度表示。 金刚石刀具的耐用度一般用切削路程的长度表示。 金刚石刀具拒绝振动和碰撞。 金刚石刀具拒绝振动和碰撞。
刀具磨损过程曲线
3. 磨钝标准 (1)工艺磨损限度 工 工艺磨损限度 工艺磨损限度 工艺磨损限度是根据工件表面粗糙度及尺寸精度的要 求而制定的,当刀具磨损到一定数值时,工件表面粗糙度 增大、尺寸精度下降,并有可能超出所要求的表面粗糙度 及其公差范围。精密加工都采用这种工艺磨损限度。 (2)合理磨损限度 合 合理磨损限度 合理磨损限度 这是合理使用刀具材料的观点出发而制定的磨损限度。 太大和太小都会浪费刀具材料,只有取正常磨损阶段终 了之前的磨损量作为磨损限度才能最经济地使用刀具。
L4 (100) ) L2 L3 (111) )
(110) ) a)4 次对称轴 和(100)晶面 b)2 次对称轴 和(110)晶面 图4-1 八面体的晶轴和镜晶面 c)3 次对称轴 和(111)晶面
金刚石晶体的面网距和解理现象 ◎金刚石晶体的(111)晶面面网密度最大,耐磨性最好。 ◎(100)与(110)面网的面间距分布均匀;(111)面网 的面间距一宽一窄(图4-21) ◎ 在 距 离 大 的 ( 111 ) 面之间,只需击破一个 共价键就可以劈开,而 在 距 离 小 的 ( 111 ) 面 之间,则需击破三个共 价键才能劈开。 ◎在两个相邻的加强 (111)面之间劈开, 可得到很平的劈开面, 称之为“解理”。
劈开面
图4-2 (111)面网C原子分布 和解理劈开面
(3) 硬度高 金刚石结晶原子间的结合力非常牢固,其显微硬度值比其 他物质高许多,耐磨性是刚玉磨料的140倍左右。 金刚石的最强结晶位置是(111)面,抛光后的抗拉强度 为400~1000kg/mm2之间。 制作刀具时,尽可能与(111)面平行研磨并形成前刀面。 但与(111)面成平行的研磨会使加工成本过高,通常是 以3左右的倾角进行研磨以形成前刀面和锋利的切削刃。
刀具磨损破损和耐用度
金刚石刀具的磨损、破损 刀具的磨损形式: 机械磨损、粘结磨损、相变磨损、扩散磨损、破损和碳化磨损 机械磨损、粘结磨损、相变磨损、扩散磨损、破损和碳化磨损。 金刚石刀具的磨损形式:机械磨损、破损和碳化磨损。最常见的磨损形式为 机械磨损、破损和碳化磨损 机械磨损 机械磨损、破损 碳化磨损 碳化磨损较少见。 机械磨损、破损,碳化磨损 (1)机械磨损 由于机械摩擦所造成的磨损。 后刀面一般情况是形成阶梯形磨损 阶梯形磨损。 阶梯形磨损 前刀面是由于切屑流过而引起的,产生凹槽形的磨损带 凹槽形的磨损带。 凹槽形的磨损带 金刚石刀具的机械磨损一般很小,磨损后的表面非常平滑,对加工一般不会 显著地影响加工表面质量。 这种机械磨损主要产生在金刚石刀具加工铝、铜尼龙等物质材料。但是在加 工过程中切削过程稳定、没有冲击振动。
热膨胀系数和化学惰性低。天然金刚石具有无与伦比的硬
度,是精密和超精密加工的一种最佳的切削刀具材料,现在天
然单晶金刚石已经成为精密超精密切削主要刀具。
1. 金刚石刀具的特性
(1) 金刚石的颜色和硬度 有红色 绿色等多种颜色。 红色和绿色 红色 绿色 硬度随颜色不同而不同。茶色最硬、无色和黄色次之。 金刚石还有很高的韧性(与矿物相比较):黄色天然金刚 石的韧性更好,不易崩刃。 要选用不易崩刃并且易于使用色泽的金刚石刀具。 结论:在难切削材料镜面加工中,几乎都是采用的茶色 茶色的金刚 茶色 石刀头。
一是金刚石晶体的晶面选择 晶面选择。 晶面选择 选择正确与否直接影响着各向异性的单晶金刚石刀具的使用寿命 二是金刚石刀具的刃口的锋利性,即刀尖圆弧半径 刀尖圆弧半径 影响切削加工的最小切削深度 最小切削深度 影响到微量切除能力和加工质量。
单晶金刚石刀具的刀刃钝圆半径可小到1nm(1nm= mm) 目前国内外金刚石刀具刀刃钝圆半径可以达到的状况: 美国可磨到5nm, 【日本可磨到10~20nm,日本大阪大学和美国LLL实验 室(Lawrence Livermore Labor-atory)合作研究超精密 切削厚度的最小极限,成功地实现了纳米级切削厚度 纳米级切削厚度的 纳米级切削厚度 稳定切削,使超精密切削水平达到新的高度。】 我国可磨到100nm,即0.1m。
(2).金刚石的晶体结构 (2).金刚石的晶体结构 金刚石的晶体结构:规整的单晶金刚石晶体有八面体、 金刚石的晶体结构:规整的单晶金刚石晶体有八面体、 十二面体和六面体,有三根4次对称轴,四根3 十二面体和六面体,有三根4次对称轴,四根3次对称轴和 六根2次对称轴( 六根2次对称轴(图7-20)。 20)
2.金刚石刀具的制造
(1)成形 天然金刚石的标准结晶形是正八面体,但通常多为斜 方十二面体。 由于形状千差万别,金刚石刀头很难加工,天然矿石的 加工成形多采用研磨加工 研磨加工方法,对研磨位置,研磨方向有严 研磨加工 格的限制,刀头通常由于平面组合成形。 近几年来,专用天然金刚石超精密研磨机的发展,使 得加工各种形状的刀形的刀头变得十分简单。
κr
(2)金刚石车刀切削部分 前角γ0=0; 后角α0=5~8; 主偏角Kr=45。
刃口圆角半径ρ 刃口圆角半径 0和后刀面光洁度对加工质量的影响
研究和试验表明: 刃口圆角半径ρ0和后刀面光洁度是影响工件表面质量的主 要因素。 ρ0=0.3m,加工铝合金的表面粗糙度Ra达0.025m; ρ0=0.1m,加工铝合金的表面粗糙度Ra达0.012m;
(3) 热传导率大 金刚石是由碳原子的共价结合而成的,其热传导率在矿物 中是最大的。 由于前刀面及刃口十分光滑,其摩擦系数比其他刀具材料 小,切屑脱落较好,所以切削加工时发热量非常小。且所产生 的热量能被金刚石迅速地导入刀体材料中 。
金刚石刀具必须解决的两个重要问题: 金刚石刀具必须解决的两个重要问题
1.2 PCD刀具的性能特点
金刚石刀具具有硬度高、抗压强度高、导 热性及耐磨性好等特性,可在高速切削中 获得很高的加工精度和加工效率。 由于聚晶金刚石(PCD)的结构是取向不 一的细晶粒金刚石烧结体,虽然加入了结 合剂,其硬度及耐磨性仍低于单晶金刚石。 但由于PCD烧结体表现为各向同性,因此 不易沿单一解理面裂开。