FMEA产品风险评估程序
空调系统风险评估(FMEA五分制法)

空调系统质量风险识别及控制规程一、目的1、为降低和控制车间洁净区空调系统相关的风险,建立有效的洁净区空调系统质量控制体系,提咼产品质量提供风险分析参考。
2、为设计单位提供风险分析参槪便设计单位采取适当设计措施以规避或将风险控制在可以接受的范围内,更好地设计出符合生产工艺和要求的空调系统,减少可能的设计缺陷。
3、为车间洁净区空调系统的验证确认活动提供风险分析参考。
4、为车间洁净区空调系统日常运行和产品的质量控制提供风险分析参考。
二、适用范围,空调系统的设计,安装,使用,验证过程。
三、定义:风险:是危害发生的可能性及其危害程度的综合体。
风险管理:即系统性的应用管理方针、程序实现对任标的风险分析、评价和控制。
风险分析:即运用有用的信息和工具,对危险进行识别、评价。
风险控制:即制定减小风险的计划和对风险减少计划的执行,及执行后结果的评价。
四、风险识别内容4・1、风险评估风险由两方面因素构万风险评估是基于对危害发生的频次和危害程度这两方面考虑而得出的综合结论。
4.1.1风险产生的后果即危害的严重程度(S)严重程度第1级:可忽略第2级微小第3级:中等第4级严重第5级毁灭性4.1.2风险发生的概率(0)第1级:稀少(发生频次小于每十年一次第2级:不太可能发生发生频次为每十年一次第3级:可能发生发生频次为每五年一次第4级:很可能发生发生频次为每一年一次第5级:经常发生几乎每次都可能发生4.1.2风险发生时的可预知性(D)第1级:不可能预知第2级:不太可能预知第3级:可能预知第4级:很可能预知第5级:完全可预知4・2风险识别第版制定日期:执行日期:3/9五、风险控制规程:5.1降低风险的计划5.11.在验证的准备阶段,对所有相关的文件均进行了一次核查,以确保文件的准确性5.12对相关的操作人员进行了岗位操作规程的培以确保全部验证过程能按文件规定执行理安排工时避免人员过度疲劳。
5.13.在设备的选型阶段就对设备的生产能力进行了评现用设备完全可以满足生产需求。
fmea风险评估三要素及计算公式

fmea风险评估三要素及计算公式
fmea的三要素:风险量化评估、列出原因/机理、寻找预防/改
善措施。
风险量化评估是指,在风险事件发生之前或之后(但还没有结束),该事件给人们的生活、生命、财产等各个方面造成的影响和损失的可能性进行量化评估的工作。
即,风险评估就是量化测评某一事件或事物带来的影响或损失的可能程度。
严重度(S)、频度(O)、不易探测度(D);因为这三个参数决定最终的RPN值。
如果想有效管理fmea,最好上线专业fmea软件,有消息称:上海通用已经明确要求,DFMEA需要专业系统管理FMEA风险系数,RPN Risk Priority Number.是严重度,发生率,探测度的乘积。
RPN=S×O×DS ---严重度1-10,数字越大,严重度
级别越高;O---频度1-10数字越大,越容易发生;D--探测度1-10
数字越大,越容易探测;RPN分值越高,风险系数越大,RPN的高低
并不是唯一判断FMEA的风险大小、实施相应对策的评价标准。
需要综合考虑S、O、D的先后顺序,以及对此三种影响着风险大小的理解与评估。
FMEA控制程序文件

FMEA控制程序文件一、目的FMEA(失效模式及影响分析)控制程序文件的目的在于规范和指导组织内进行有效的 FMEA 活动,以提前识别潜在的失效模式、评估其影响和风险,并制定相应的预防和控制措施,从而提高产品和过程的质量、可靠性和安全性,减少故障和损失,增强客户满意度。
二、适用范围本程序适用于组织内所有新产品开发、过程改进、现有产品和过程的变更等活动中涉及的 FMEA 应用。
三、术语和定义1、失效模式(Failure Mode):指产品或过程可能出现的不符合预期的方式。
2、失效影响(Failure Effect):指失效模式对产品功能、性能、顾客满意度等方面产生的后果。
3、失效原因(Failure Cause):指导致失效模式发生的根本原因。
4、风险优先数(Risk Priority Number,RPN):通过严重度(S)、发生度(O)和探测度(D)的乘积计算得出,用于评估失效模式的风险程度。
四、职责分工1、项目经理:负责组织和协调 FMEA 团队的工作,确保 FMEA 活动按时完成,并对 FMEA 结果进行审核和批准。
2、FMEA 团队成员:包括设计工程师、工艺工程师、质量工程师、生产人员等,负责收集相关信息,进行失效模式的分析和评估,提出预防和控制措施。
3、质量部门:负责监督 FMEA 活动的执行情况,对 FMEA 报告进行存档和管理,并跟踪措施的实施效果。
五、FMEA 流程1、策划和准备确定 FMEA 的范围和目标,包括产品或过程的名称、型号、适用范围等。
组建 FMEA 团队,明确团队成员的职责和分工。
收集相关的技术文件、标准、规范、以往的经验教训等资料。
2、结构分析绘制产品或过程的结构框图,明确各组成部分之间的关系。
确定分析的层次和边界,将产品或过程分解为子系统、组件、零件等。
3、功能分析描述每个组成部分的功能和要求,确定其预期的输出和性能指标。
分析功能之间的交互作用和依赖关系。
4、失效模式分析针对每个功能,识别可能出现的失效模式,包括完全失效、部分失效、间歇失效等。
FMEA产品风险评估及管控程序
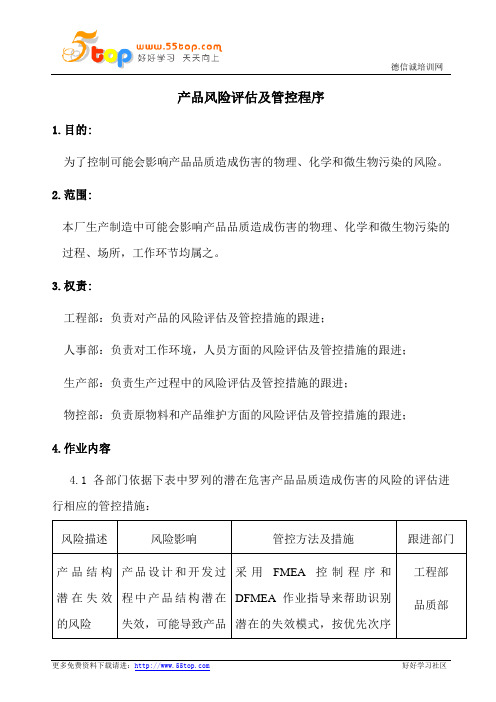
德信诚培训网
更多免费资料下载请进: 好好学习社区 产品风险评估及管控程序
1.目的:
为了控制可能会影响产品品质造成伤害的物理、化学和微生物污染的风险。
2.范围:
本厂生产制造中可能会影响产品品质造成伤害的物理、化学和微生物污染的过程、场所,工作环节均属之。
3.权责:
工程部:负责对产品的风险评估及管控措施的跟进;
人事部:负责对工作环境,人员方面的风险评估及管控措施的跟进;
生产部:负责生产过程中的风险评估及管控措施的跟进;
物控部:负责原物料和产品维护方面的风险评估及管控措施的跟进;
4.作业内容
4.1各部门依据下表中罗列的潜在危害产品品质造成伤害的风险的评估进行相应的管控措施: 风险描述 风险影响 管控方法及措施 跟进部门
产品结构潜在失效的风险 产品设计和开发过程中产品结构潜在失效,可能导致产品采用FMEA 控制程序和DFMEA 作业指导来帮助识别
潜在的失效模式,按优先次序
工程部
品质部。
产品风险评估与控制管理工作程序
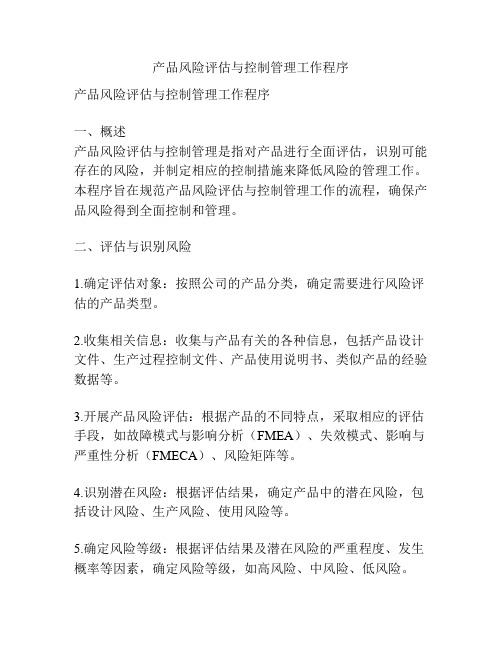
产品风险评估与控制管理工作程序产品风险评估与控制管理工作程序一、概述产品风险评估与控制管理是指对产品进行全面评估,识别可能存在的风险,并制定相应的控制措施来降低风险的管理工作。
本程序旨在规范产品风险评估与控制管理工作的流程,确保产品风险得到全面控制和管理。
二、评估与识别风险1.确定评估对象:按照公司的产品分类,确定需要进行风险评估的产品类型。
2.收集相关信息:收集与产品有关的各种信息,包括产品设计文件、生产过程控制文件、产品使用说明书、类似产品的经验数据等。
3.开展产品风险评估:根据产品的不同特点,采取相应的评估手段,如故障模式与影响分析(FMEA)、失效模式、影响与严重性分析(FMECA)、风险矩阵等。
4.识别潜在风险:根据评估结果,确定产品中的潜在风险,包括设计风险、生产风险、使用风险等。
5.确定风险等级:根据评估结果及潜在风险的严重程度、发生概率等因素,确定风险等级,如高风险、中风险、低风险。
三、制定控制措施1.确定控制目标:根据风险评估结果,确定控制目标,即希望通过控制措施达到何种效果,如降低风险等级、减少风险发生概率等。
2.制定控制措施:根据潜在风险的具体情况,制定相应的控制措施。
如对设计风险进行改进、完善生产过程控制、提供明确的产品使用说明等。
3.确定责任部门与人员:确定每项控制措施的责任部门和具体负责人,明确各个环节的职责和任务。
四、控制措施的实施与监控1.实施控制措施:按照制定的控制措施要求,由相应责任部门和人员进行实施,并确保实施的有效性。
2.监控控制措施:建立相应的监控机制,定期对控制措施的执行情况进行检查和评估,及时发现并纠正可能存在的问题。
3.风险评估更新:根据产品的使用情况和相关数据的反馈,定期对产品进行风险评估的更新,并相应调整控制措施。
五、事故应急处理1.建立应急预案:针对可能发生的风险事故,制定相应的应急处理预案,明确各个环节的应急处理措施和责任人员。
2.应急演练:定期进行应急演练,检验应急预案的有效性,并对相应的应急处理流程进行改进。
过程FMEA程序-第五版

1.0 目的:/purpose:评估产品/过程中失效的潜在技术风险,分析失效的起因和影响,记录预防和探测措施,针对降低风险的措施提出建议,FMEA形成文件并跟踪这些措施的实施情况,以降低风险。
并介定后续维护中的提出、制订、执行及随后监察其有效性的责任。
Evaluate the potential techincal risks of failure of a product or process,analyze the causes and effects of those failures,document preventive and detection actions,recommend actions to reduce risk,the FMEA documents and tracks actions that are taket to reduce risk, It also defines the responsibilities for the subsequent maintenance of the proposal, formulation, implementation and subsequent monitoring of its effectiveness. 2.0 范围:/Scope:适用于制作流程的检查与预防。
Applicable to the production process of the inspection and prevention.注:根据APQP要求,并针对下述来源所发现的潜在缺陷,应采取相应的预防及纠正行动。
Note:according to the requirements of APQP, and according to the following sources found potential defects, the corresponding preventive and corrective action should be taken. 以前产品认可时发出的偏差纠正;Deviation from the previously approved products when correcting;因设计、标准、物料更改导致产品变化;Product changes caused by design, standard, material changes;使用新指示或物料;Using the new instructions or material;使用新的或优化的工具,包括生产和客户提供的工具;Use new or optimization tools, including production and provide the tools;对原有工具和设备进行过翻新和重新布置;The original tools and equipment for renovation and redecorating生产流程、方法、组装、物流过程发生变动;Production process, method, assembly, logistics process change;工具和设备位置迁移;Tools and equipment location migration;部件、物料或服务的外发加工商变更;Outward processing business changes of parts, materials or services;工具停用一年后再次使用;。
新版fmea七步法案例
新版FMEA七步法案例分析1. 背景介绍FMEA(Failure Mode and Effects Analysis)是一种常用的风险分析方法,旨在识别并评估系统或过程中的潜在故障模式、其对系统性能的影响以及采取的措施。
新版FMEA七步法是对传统FMEA方法的改进和完善,强调了风险预防和控制的重要性。
本文将以汽车制造业中的零部件生产过程为例,详细介绍新版FMEA七步法的应用过程和结果。
2. 案例背景假设某汽车制造公司生产某型号车辆的发动机零部件,该零部件在汽车性能中起到至关重要的作用。
公司决定采用新版FMEA七步法对该零部件生产过程进行风险分析,以提高产品质量和生产效率。
3. 案例过程步骤一:明确目标在这一步骤中,团队明确了目标:提高零部件生产过程的质量和效率。
同时,制定了详细的项目计划,明确每个步骤的时间和责任人。
步骤二:制定团队为了保证分析的全面性和准确性,公司组建了一个跨职能的团队,包括设计工程师、生产工程师、质量控制人员、供应商等。
每个团队成员都具备相关领域的专业知识和经验。
步骤三:定义过程在这一步骤中,团队对零部件生产过程进行了详细的定义和描述。
包括输入物料、工艺流程、设备使用等方面的信息。
同时,团队还明确了每个步骤的控制点和关键参数。
步骤四:风险分析团队根据零部件生产过程的定义,开始进行风险分析。
通过采用常用的风险评估工具,如故障模式与影响分析(FMEA)和故障树分析(FTA),对每个步骤的潜在故障模式和影响进行了评估和排名。
例如,在零部件生产过程中,一个潜在的故障模式是工艺参数设置错误,导致产品尺寸不合格。
该故障模式的影响包括:影响产品装配质量、增加产品退货率、增加维修成本等。
步骤五:制定改进措施在风险分析的基础上,团队制定了一系列改进措施,以减少潜在故障的发生概率和减轻故障影响。
这些改进措施包括:•设立更严格的工艺参数控制标准,确保每个步骤的参数设置正确;•引入自动化设备,减少人为操作错误的可能性;•加强员工培训,提高操作技能;•建立更严格的质量检查流程,确保产品质量符合要求。
成衣服产品PFMEA风险评估
保养清洁不当
2
每天设备日常保养
3
42
无
影响产品外观
5
设备参数不正 确
3
首件确认/过程巡 检
3
45
无
6
包装 拉QC100%检查, IPQC首件检验/巡 检 拉QC100%检查, IPQC首件检验/巡 检 拉QC100%检查, IPQC首件检验/巡 检 利器管理/玻璃易 碎品定期检查
数量少装
包装资料
影响客户销售
6
包装工误操作
2
3
36
无
包装方法
产品错装
包装资料
影响客户销售
6
包装工误操作
2
3
36
无
混装错误
包装资料
影响客户销售
6
包装工误操作
2
3
36
无 IPQC每2小时 QA部 巡查一次异物 完成日期: 管控 2014/09/01起
异物污染
利器/玻璃易碎品 利器/玻璃易碎品 混入产品伤害消 等异物污染 管理程序 费者
外观 熨烫
外观检验标准
影响产品外观
5
员工操作不当
3
首件确认/过程巡 检
3
45
无
5
外观
外观差
外观检验标准
影响产品外观
5
员工操作不当
3
首件确认/过程巡 检
3
45
无
審批: 劉蘭芳
編制:陳濤
2018/12/24
3/5
潜在失效模式及后果分析
Design FMEA设计 Product产品 产品类型: T-Shirt Subsystem子系统 Component部件 Process FMEA 过程 日期:2014/09/01 批准:Yang Sen 设计或过程责任:业务/工程/品 文件编号:P-FMEA-01 质部/生产部 编制: Ma Yayun
fmea探测度评级方法
fmea探测度评级方法
【一、FMEA概述】
FMEA(Failure Mode and Effects Analysis)是一种前瞻性的风险评估方法,旨在识别和评估系统、产品或过程中的潜在故障模式及其潜在影响。
这种方法通常在设计、生产和维护阶段进行,以便及时改进和降低风险。
【二、FMEA探测度评级方法介绍】
1.评级标准
FMEA探测度评级是根据潜在故障模式的发生概率和潜在影响的严重程度来进行评估的。
通常采用1-10分的评分标准,分数越高,表示风险越高。
2.评级步骤
(1)识别潜在故障模式:分析系统、产品或过程的各个环节,找出可能出现的故障模式。
(2)评估故障发生的概率:根据历史数据、行业标准和专家意见,评估故障发生的可能性。
(3)评估潜在影响:分析故障对系统、产品或过程的关键性影响,如安全性、可靠性、性能等。
(4)计算探测度评级:根据故障概率和潜在影响的评分,计算探测度评级。
3.评级结果分析与应用
根据探测度评级结果,对潜在故障模式进行优先级排序,针对高风险的项目进行改进和优化。
同时,定期进行FMEA复查,确保风险持续受控。
【三、FMEA探测度评级方法在实际案例中的应用】
在某汽车制造商的生产线中,通过FMEA探测度评级方法,发现了潜在的装配错误导致的车辆安全隐患。
针对这一高风险项目,企业进行了改进,提高了装配过程中的质量控制,有效降低了故障率。
【四、总结与展望】
FMEA探测度评级方法是一种有效的风险评估工具,可以帮助企业及时发现和解决潜在问题,提高产品质量和安全性。
设计FMEA第一步策划和准备的具体步骤
设计FMEA第一步策划和准备的具体步骤FMEA(故障模式与影响分析)是一种用于评估与预防产品或过程中的潜在故障模式和其对系统性能的影响的方法。
FMEA通常包括三个步骤:策划和准备、实施分析和采取行动。
策划和准备是FMEA过程的第一步,这是一个关键的阶段,需要明确FMEA的目标、确定团队成员、收集相关数据和准备工作文件。
以下是FMEA计划和准备的具体步骤:1.确定FMEA的目标:首先,需要明确FMEA的目标。
这可能是为了评估和预防潜在的故障模式,提高产品质量,降低风险等。
2.组建FMEA团队:组建一个跨部门的FMEA团队是至关重要的。
团队成员应代表各个领域,包括设计、工程、生产和质量等。
确保团队成员具备丰富的经验和专业知识来支持FMEA过程。
3.收集产品或过程信息:收集产品或过程的相关信息,包括技术规范、CAD图纸、设计文件、生产步骤、零部件清单等。
这些信息将帮助团队识别潜在的故障模式和潜在的影响。
4.确定FMEA工作范围:根据目标和可行性,定义FMEA的工作范围。
该范围可以是整个产品或过程,也可以是特定的子系统或阶段。
5.选择FMEA方法:选择适合项目的FMEA方法。
常见的FMEA方法包括设计FMEA(DFMEA)和过程FMEA(PFMEA)等。
DFMEA用于评估设计阶段的潜在故障模式和它们对产品性能的影响。
PFMEA用于评估生产过程中的潜在故障模式和它们对产品质量的影响。
6.准备FMEA模板:根据选择的FMEA方法和工作范围,准备FMEA模板。
模板通常包括故障模式、原因、后果、风险评估、预防措施和修正措施等字段。
7.制定FMEA时间表:制定一个具体的FMEA时间表,确保FMEA过程在预定的时间内完成。
时间表应包括各个阶段的开始和结束日期,以及预期的时间用于会议、讨论和文档准备。
8.建立FMEA数据库:建立一个FMEA数据库来存储和跟踪FMEA信息。
这个数据库可以是一个在线平台或一个本地服务器,它应该能够容纳所有FMEA文档、会议记录和相关数据。
- 1、下载文档前请自行甄别文档内容的完整性,平台不提供额外的编辑、内容补充、找答案等附加服务。
- 2、"仅部分预览"的文档,不可在线预览部分如存在完整性等问题,可反馈申请退款(可完整预览的文档不适用该条件!)。
- 3、如文档侵犯您的权益,请联系客服反馈,我们会尽快为您处理(人工客服工作时间:9:00-18:30)。
四、作业流程:
NO
流 程
权责单位
参考文件说明
使用表单
1
2
业务部
4.1.1 业务在收到客人的开发资讯/开发参考样品时,要注意收集客户的产品功能要求及产品的品质要求,出口地标准;给到工程部及品管部。
工程部
4.2.1 工程部在收到业务交的客人新产品资讯,依据客户的要求,参考工厂以往生产过程之品质状况及制程控制程序,结合出口地的安全标准,对产品进行产前风险,并将评估结果交业务.
4.7.1 产品实现过程的相关记录及各项分析根据责任主管确认及核准,以验证产品符合要求;并定期开检讨会使相关人员了解产品过程符合性及相关责任。
4.7.2 生产过程中各个检测点的记录参照, 《制程检验控制程序》。
4.7.3 储存及运输参照《储存与运输管制程序》。
4.7.3 相关记录的保存周期参照《记录管制程序》。
4.5.3 问题之处置对策,制作高风险工序检查控制点有异常时需要分析汇总,并做改善对策详细参考《矫正与预防措施作业程序》
4.5.4 各制程人员须严格依据《产品流程图》操作指引操作;关键工序严格依据相关参数标准及相关要求。
4.5.5 生产设备及工程夹具要定期检测以确保其准确性,实适性;如果生产设备及工程夹具部能满足生产工艺要求,PE组要负责跟进,至达到要求时期。
FMEA
一、 目的:为了减少产品在开发,生产制程,检验及交付储存等过程所产生的风险,从而保证产品质量能符合客户特定要求,特制定此程序。
二、 适用范围:本公司所有的产品之制作过程。
三、 定义:Biblioteka 1、产品风险评估(FMEA)-工程部
2、产品生产流程,工艺及生产设施的评估-工程部/生产部(PE组)。
3、产品质量标准及检验程序之制定-品管部。
4.5.6 生产各个单位须做好自检,若有异常及时通知品管及按《不合格品控制程序》执行。
PFMEA
6
工程部/品管部
4.6.1 采购及外发等工序严格依据《采购/外发控制程序》及《进料检验控制程序》;执行,如有异常《矫正与异常对策处理程序》
《(相关项目)测试记录表》《异常矫正预防对策处理单》
7
工程部/品管部
4.4.3 如产品的原物料存在可预见风险,建议客人更换物料,以降低原物料所产生的风险。
相关表单
5
工程部/品管部/生产部
4.5.1 制程作业之风险管理(参考产品艺流程图/操作指引/产品检验标准)。
4.5.2 QA在评估产品生产过程时发现产品存在高风险或不符合出口地相关法律法规时,必须要求工程部给出改善措施,必要时要与客户反映确保问题得以有效的解决方可出货。
NO
流 程
权责单位
参考文件与说明
使用表单
4
工程部
4.4.1 人员操作,通过人力资源规划及训练,根据生产流程图明确产品实现之各个需要的人力;由人力资源部给于协助招募,从而降低人员操作过程中所产生的风险。
4.4.2 产品结构;功能本身存在风险应及时向客户提出,并要求做出改善,以降低产品本身结构及功能所产生的风险指数。
FMEA
4.2.2 工程部依据客户样品或新产品开发资料及产品生产工艺,制作流程和风险评估;依据评估结果改良制作工艺与完善生产夹具,在现有的生产设备及检测仪器(或当生产量之需求超出现有的设备时,应有时间准备必要之设备)能力下,制定产品流程图及流程中各个过程之人力资源需求及作业标准,从而降低产品在制造过程中所产生的风险。
FMEA
工程部
4.3.1 产品本身是否存在安全隐患。
4.3.2 产品结果,功能是否合理。
4.3.3 产品各类原料是否能满足客户之质量要求。
4.3.4 产品是否符合出口国家的法规法例。
4.3.5 产品生产过程中可能会产生的产品风险指数。
4.3.6 人员、机器设备与夹具等因素肯能产生的产品风险指数。
FMEA
《会议记录》