辊道窑温度分布式智能控制系统的研究及应用
辊道窑窑炉智能控制系统的应用

辊道窑窑炉智能控制系统的应用江竹亭;杨芸;罗明照【摘要】“辊道窑智能控制系统”集节能与管理功能融为一体、将模糊逻辑、专家系统、自适应和最优控制、运筹学等多项技术综合的先进的控制系统;“辊道窑智能控制系统”可以对采集的数据进行全面、系统的分析处理,根据给定的任务要求,在可能的处理措施中选择最合适的控制参数和方法,改变控制策略去适应对象的复杂性和不确定性,以最优的方案,实现控制目标;解决了传统控制无法很好的适应多变复杂对象的难题;在燃料发热值和窑炉压力等频繁波动的情况下,实现自适应控制;它以模糊数学控制理论做为理论基础,以对窑炉当时测定参数为依据,通过计算机程序控制,实现自动改变风机变频频率来达到符合当时工况的最佳空燃比,实现合理燃烧,从而达到节能减排的目的.【期刊名称】《中国陶瓷工业》【年(卷),期】2013(020)006【总页数】4页(P44-47)【关键词】辊道窑;智能控制;节能;管理【作者】江竹亭;杨芸;罗明照【作者单位】景德镇陶瓷学院,江西景德镇333001;江西陶瓷工艺美术职业技术学院,江西景德镇333001;佛山市华夏建筑陶瓷研究开发中心,广东佛山528061【正文语种】中文【中图分类】TQ174.530 概述“辊道窑智能控制系统”是集节能与管理功能融为一体、将模糊逻辑、专家系统、自适应和最优控制、运筹学等多项技术综合的先进控制系统。
目前,在陶瓷行业属首创的辊道窑控制系统。
该系统软件核心部分采用国内工业炉窑控制专家40余年专业经验,并结合诸多国内外企业和专家提供的资料、数据构成了专家系统。
“ICPower辊道窑智能控制系统”可以对采集的数据进行全面、系统地分析处理,根据给定的任务要求,在可能的处理措施中选择最合适的控制参数和方法,改变控制策略去适应对象的复杂性和不确定性,以最优的方案,达到控制目标,解决了传统控制无法很好地适应多变复杂对象的难题;能在燃料发热值和压力等频繁波动的情况下,实现自适应控制,将老式的手动操作的炉窑,经过智能控制技术改造,一步到位变成自动、高效率的自动化炉窑,节能5%以上。
基于PLC的陶瓷辊道窑烧成段温度串级控制系统设计
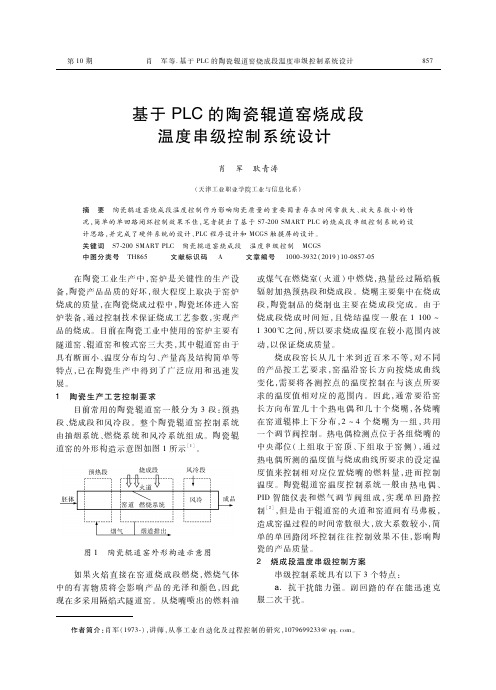
图 1 陶瓷辊道窑外形构造示意图
如 果 火 焰 直 接 在 窑 道 烧 成 段 燃 烧,燃 烧 气 体 中的有害物质 将 会 影 响 产 品 的 光 泽 和 颜 色,因 此 现在多采用隔焰式隧道窑。从烧嘴喷出的燃料油
输 入 信 号 的 特 性 ,这 种 特 性 存 在 于 副 回 路 中 ,由 于 副回路是随动 控 制 系 统,因 而 能 够 很 好 地 跟 踪 负 载与操作条件 的 变 化,使 系 统 即 使 处 在 条 件 变 化 比较频繁的环 境 中,其 输 出 值 也 可 以 很 好 地 跟 踪 期望值。串级控制系统控制原理如图 2所示。
串级控制系统具有以下 3个特点: a.抗干扰能 力 强。 副 回 路 的 存 在 能 迅 速 克 服二次干扰。
作 者 简 介 :肖 军 (1973),讲 师 ,从 事 工 业 自 动 化 及 过 程 控 制 的 研 究 ,1079699233@ qq.com。
858
化 工 自 动 化 及 仪 表 第 46卷
值来自于主控 制 器 的 输 出,而 主 控 制 器 的 输 出 是
可 知 ,副 控 制 器 选 择 反 作 用 。
随时间化的。
当操纵变量燃 料 油 量 增 加 时,主 变 量 窑 道 温
在本设计中,选取火道温度为副变量、窑道温 度增加,副 变 量 火 道 温 度 也 增 加,主 对 象 为 正 作
在 陶 瓷 工 业 生 产 中,窑 炉 是 关 键 性 的 生 产 设 备 ,陶 瓷 产 品 品 质 的 好 坏 ,很 大 程 度 上 取 决 于 窑 炉 烧 成 的 质 量 ,在 陶 瓷 烧 成 过 程 中 ,陶 瓷 坯 体 进 入 窑 炉 装 备 ,通 过 控 制 技 术 保 证 烧 成 工 艺 参 数 ,实 现 产 品的烧成。目前在陶瓷工业中使用的窑炉主要有 隧 道 窑 、辊 道 窑 和 梭 式 窑 三 大 类 ,其 中 辊 道 窑 由 于 具 有 断 面 小 、温 度 分 布 均 匀 、产 量 高 及 结 构 简 单 等 特点,已在陶瓷 生 产 中 得 到 了 广 泛 应 用 和 迅 速 发 展。 1 陶 瓷 生 产 工 艺 控 制 要 求
一种陶瓷辊道窑温度自动控制系统设计

传统的陶瓷辊道窑生产中,当出现异常情况时,会导致窑炉空窑,这就需要窑炉操作员及时对窑炉温度进行监控并结合产品在窑炉内空窑的位置进行手动调节。
由于原料配方或者设备故障原因等客观存在的因素导致出现空窑,对异常问题的处理高度依赖个人经验。
本文设计的方案主要是通过获取各段窑炉的传动线速度并监控进砖信号开发对窑炉内产品位置进行实时动态仿真模拟控件,从而获取产品在窑炉内的位置状态信息,根据这些信息系统利用算法进行智能分析出窑炉内哪个位置存在空窑或稀窑,然后根据用户设定的温度控制参数,系统将自动进行温度调节,从而实现窑内温度自动调节到生产需求。
空窑温度控制系统的投入使用将大大降低窑炉操作人员的工作强度,提升温度控制的及时度及精度,同时也在节约能源方面发挥着举足轻重的作用。
窑炉空窑温度自动控制系统硬件设计主要包括传动数据采集系统、进砖信号采集系统、温度控制系统三个部分,系统硬件结构图如图1所示。
整个系统基于计算机系统实现功能,通过PLC 采集进砖信号实现砖块位置传输给计算机,通过通讯模式实现对传动速度的采集和温度的采集,汇总给计算机通过算法实现窑炉空窑温度自动控制的功能。
整个系统运行的最终目的是:当窑炉空窑或稀窑时,系统可以控制窑炉降低温度,当空窑结束时,控制窑炉恢复生产温度,从而达到在不影响产品质量的情况下节能的目的。
计算机获取窑炉的速度,主要是通过采集变频器的频率,通过电机和辊棒之间线性关系换算成窑炉速度(如图2)。
龙威舜,蓝万聪(佛山市科达机电有限公司,佛山528000),辊道窑炉的烧成温度稳定对产品烧成质量起决定性的作用,辊道窑是一种连续性生产模式,这种模式决定了温度的自动控制要求比较高。
由于各种原因,导致辊道窑很难持续满窑生产,会出现不间断的空窑现象。
在传统窑炉的温度控制中,往往需要人工根据经验针对空窑的情况进行手动调节温度,这样无形中增加了很大的操作难度,同时容易产生不良品。
本文设计了一套窑炉空窑温度自动控制系统,当出现空窑时,根据空窑位置及设定的温度控制参数进行自动调节,进而保持窑炉内部的温度稳定。
电热辊道窑在大规模陶瓷制造中的应用前景展望

电热辊道窑在大规模陶瓷制造中的应用前景展望随着社会发展和科技进步,陶瓷制造业也在不断进化和创新。
作为一种重要的陶瓷生产设备,电热辊道窑在大规模陶瓷制造中具有广阔的应用前景。
本文将对电热辊道窑的特点、优势以及目前的应用情况进行分析,并展望其在未来的发展趋势。
电热辊道窑是一种采用电加热方式的陶瓷生产设备,其主要原理是通过电能将辊道窑内的辊道加热,从而将窑膛内的温度升高到所需的生产温度。
与传统的燃气辊道窑相比,电热辊道窑具有以下几个显著特点。
首先,电热辊道窑不需要燃烧燃料,减少了对环境的污染。
传统的燃气辊道窑在燃烧过程中会产生大量的废气和废水,对环境造成较大的压力。
而电热辊道窑采用电加热方式,完全避免了这一问题,符合现代社会对于环保的要求。
其次,电热辊道窑的加热效果更为均匀稳定。
由于电能的加热方式可以精确控制温度和加热时间,所以电热辊道窑在生产过程中能够实现温度的精确控制,在制造陶瓷产品的质量和稳定性方面具备明显的优势。
再次,电热辊道窑具有自动化程度较高的特点。
电热辊道窑可以与控制系统相连,通过对温度、速度、压力等参数的自动控制和监测,实现对生产过程的全面管理和控制。
这种自动化程度的提高不仅可以提高生产效率,降低人力成本,还可以提升产品质量的稳定性和一致性。
目前,电热辊道窑已经在一些大规模陶瓷制造企业中得到了广泛应用。
特别是在建筑陶瓷、卫生陶瓷、工业陶瓷等领域,电热辊道窑已经成为生产工艺的主流选择。
在这些领域,电热辊道窑的特点和优势得到了充分的发挥,其可以满足快速、高效、稳定的生产要求。
然而,电热辊道窑在大规模陶瓷制造中仍然面临一些挑战和发展空间。
首先,电热辊道窑的投资成本相对较高。
由于其自动化程度较高,需要配备先进的控制系统和电加热设备,导致其价格较传统辊道窑更昂贵。
这使得一些中小企业难以承担升级换代的费用,限制了电热辊道窑的普及率。
其次,电热辊道窑的设备维护和保养对操作人员的要求较高。
相比于传统的燃气辊道窑来说,电热辊道窑在设备维护和保养方面更加复杂,对操作人员的技术水平要求较高。
辊道窑炉多功能触摸屏全自动温度控制系统
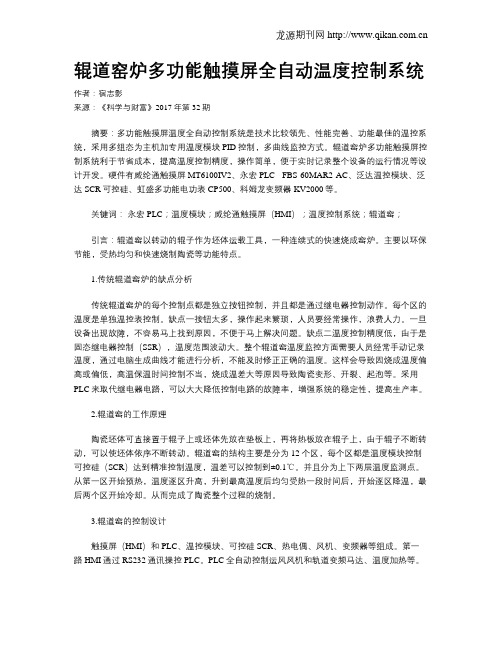
辊道窑炉多功能触摸屏全自动温度控制系统作者:宿志影来源:《科学与财富》2017年第32期摘要:多功能触摸屏温度全自动控制系统是技术比较领先、性能完善、功能最佳的温控系统,采用多组态为主机加专用温度模块PID控制,多曲线监控方式。
辊道窑炉多功能触摸屏控制系统利于节省成本,提高温度控制精度,操作简单,便于实时记录整个设备的运行情况等设计开发。
硬件有威纶通触摸屏MT6100IV2、永宏PLC - FBS-60MAR2-AC、泛达温控模块、泛达SCR可控硅、虹盛多功能电功表CP500、科姆龙变频器KV2000等。
关键词:永宏PLC;温度模块;威纶通触摸屏(HMI);温度控制系统;辊道窑;引言:辊道窑以转动的辊子作为坯体运载工具,一种连续式的快速烧成窑炉。
主要以环保节能,受热均匀和快速烧制陶瓷等功能特点。
1.传统辊道窑炉的缺点分析传统辊道窑炉的每个控制点都是独立按钮控制,并且都是通过继电器控制动作。
每个区的温度是单独温控表控制。
缺点一按钮太多,操作起来繁琐,人员要经常操作,浪费人力。
一旦设备出现故障,不容易马上找到原因,不便于马上解决问题。
缺点二温度控制精度低,由于是固态继电器控制(SSR),温度范围波动大。
整个辊道窑温度监控方面需要人员经常手动记录温度,通过电脑生成曲线才能进行分析,不能及时修正正确的温度。
这样会导致因烧成温度偏高或偏低,高温保温时间控制不当,烧成温差大等原因导致陶瓷变形、开裂、起泡等。
采用PLC来取代继电器电路,可以大大降低控制电路的故障率,增强系统的稳定性,提高生产率。
2.辊道窑的工作原理陶瓷坯体可直接置于辊子上或坯体先放在垫板上,再将热板放在辊子上,由于辊子不断转动,可以使坯体依序不断转动。
辊道窑的结构主要是分为12个区,每个区都是温度模块控制可控硅(SCR)达到精准控制温度,温差可以控制到±0.1℃。
并且分为上下两层温度监测点。
从第一区开始预热,温度逐区升高,升到最高温度后均匀受热一段时间后,开始逐区降温,最后两个区开始冷却。
辊道窑现场总线计算机控制系统

⑥上网点的逻辑查找只能在某个已打开的DPU 逻辑中进行,不能直接查找出引用该点的所有的DPU 号,另外DPU引用该上网点时查找不出来。
⑦A、B小机在转速大于4000r/m in时,两个测速通道偏差较大,转速大于5000r/m in时,测量误差大。
⑧ETS保护的切投状态与保护切投操作应增加历史记录功能。
⑨SCS控制的所有设备所处的手动/自动状态应增加历史记录功能,便于故障查询和事故分析。
一些重要的程控应有模拟试验功能。
收稿日期:2003-01-22。
作者高启繁,男,1964年生,1987年毕业于福州大学,工程师。
辊道窑现场总线计算机控制系统F ield Bus Co mputerized Control Syste m of Roller Conveyer Stove王 嵩 吴 刚 薛美盛 张培仁 孙德敏(中国科学技术大学自动化系,合肥 230027)0 引言在陶瓷制造工艺过程中烧成是最重要的工序,与产品质量密切相关,占用总能耗的60%~70%。
陶瓷的烧成是将成形后的生坯在一定条件下进行热处理,经过一系列物理化学变化,得到具有一定矿物组成和显微结构、达到所要求的理化性能指标的成坯。
烧成对温度高低、温度变化快慢、不同阶段的气氛等都有严格的要求。
烧成设备为窑炉,辊道窑代表了当前窑炉的先进水平,广泛应用于建筑、卫生和日用陶瓷行业。
辊道窑是一种连续窑,具有工艺先进、设计合理、易操作、易维修等优点,它用许多平行排列的不停转动的辊棒构成辊道,陶瓷坯件在辊道上被带动从窑头通过窑炉炉体至窑尾,经过预热、烧成、冷却,最后出窑。
辊道窑控制系统的发展,历经了20世纪60年代模拟仪表时期、80年代数字仪表时期以及90年代的DCS时期。
国内现有辊道窑大多控制水平低,产品类型少,质量波动大,生产能耗高,经济效益差。
引入先进控制技术可以降低成本,保证质量,提高经济效益。
1 工艺简介广东某陶瓷总厂7车间3号窑为燃油辊道窑,上世纪90年代初从意大利引进,用于烧800mm×800mm 或更小尺寸的地砖,氧化气氛烧成,烧成点1220℃左右。
电热辊道窑的智能化控制系统研究

电热辊道窑的智能化控制系统研究随着科技的进步和工业自动化的不断发展,智能化控制系统在各个行业中起到了至关重要的作用。
作为一种常见的工业设备,电热辊道窑在陶瓷、玻璃、建材等行业中扮演着重要角色。
本文将针对电热辊道窑的智能化控制系统进行研究,旨在提高其生产效率、降低运营成本,并提供更加可靠和安全的工作环境。
一、智能化控制系统的概述智能化控制系统是使用计算机和先进的软硬件技术来实现设备的自动化、集成化和智能化。
对于电热辊道窑来说,智能化控制系统可以包括以下几个方面的功能:1. 温度控制:通过精确的温度传感器和先进的控制算法,实时监测和控制窑内的温度变化,以确保产品的质量和生产的稳定性。
2. 运行状态监测:通过传感器和数据采集系统,对电热辊道窑的运行状态进行实时监测,如转速、电流、振动等参数,以及窑内的燃烧状态和气体排放情况,从而及时发现故障和异常,并做出相应的处理和调整。
3. 自动化控制:通过编程和智能算法,实现电热辊道窑的自动化控制,包括启动、停止、加热、冷却等操作,同时结合运行状态监测和温度控制功能,实现窑内温度的自动调节和产品的自动转运。
4. 数据分析和优化:通过对采集的数据进行分析和处理,获取关键指标和性能参数,为生产管理和工艺优化提供科学依据,从而提高电热辊道窑的生产效率和产品质量。
二、智能化控制系统的关键技术1. 传感器技术:合理选择和布置温度传感器、压力传感器、振动传感器、气体传感器等,确保准确采集窑内各项参数。
2. 数据采集与处理技术:使用高速数据采集系统和强大的计算能力,对采集的传感器数据进行实时处理和分析,并将处理后的数据传输给控制系统。
3. 控制算法和模型建立技术:采用先进的控制算法,如模糊控制、PID控制等,通过与温度传感器反馈信息的实时对比和调整,实现对电热辊道窑温度的精确控制。
4. 人机交互界面技术:设计直观、友好的人机交互界面,方便操作人员进行设备监控、参数调整和故障处理,同时也提供运行状态数据的可视化展示,为管理者提供生产决策的参考依据。
辊道窑窑内温度场变化研究

能 有 效 地 改 善 窑 内 ( 其 是 横 断 面 ) 度 的 均 匀 性 , 少 尤 温 减 制 品变 形 、 差 等 缺 陷 。温 度 均 匀 器 如 何 能 达 到 改 善 窑 内 色
物 理 结构 模 型及 网格 划 分
温 度 的 均 匀 性 ?了解 这 一 点 , 合 理 操 作 温 度 均 匀 器 很 有 21 物理结构模型 的简化 对 .
4 0 mm 2 0 m 0 0 x 30 m。由于温度 均匀器装 置 中除辊 棒外 , 其
他 部 件 对 研 究 窑 内气 体 流场 没 有 任 何 影 响 .故 模 型 中其 他 部 件 可 忽 略 。 均 匀 器 辊 棒 结 构 尺 寸 为 :长 × 径m。经合理 简化后 , 加入 温度均匀 器后的窑
罔 2 窑体 模 型 结 构 简化 示 意 图
存 耗 费 不 大 且 计 算 精 度 又 能 保 证 的 P l 射 模 型 ,其 模 — 辐
型方程如 方程( : 7)
2 网格划分 . 2
模 型计 算 区 域 采 用 四面 体 非 结 构 网格 。窑 内 烟 气 经 过 温 度 均 匀 器 的辊 棒 时 会 发 生 绕 流 , 附 近 烟 气 速 度 场 较 大 变 化 会 导 致 温 度 场 的 变 化 。为 了更 合 理 地 模 拟 放 置 温 度 均 匀 器 后 烟 气 的温 度 场 ,先 对 两 辊 棒 四个 圆 端 面 的 圆 周 曲 线 生 成 线 网 格 , 后 再 生 成 体 网 格 , 现 对 辊 棒 周 围 然 实 的 网 格 局 部 加 密 , 后 生 成 的 网格 总 数 为 1 12 最 7 0 9个 。
必要 。
本 文 主要 是 研 究 辊 道 窑 烧 成 带 内垂 直 放 置 温 度 均 匀
- 1、下载文档前请自行甄别文档内容的完整性,平台不提供额外的编辑、内容补充、找答案等附加服务。
- 2、"仅部分预览"的文档,不可在线预览部分如存在完整性等问题,可反馈申请退款(可完整预览的文档不适用该条件!)。
- 3、如文档侵犯您的权益,请联系客服反馈,我们会尽快为您处理(人工客服工作时间:9:00-18:30)。
辊道窑温度分布式智能控制系统的研究及应用
2008-11-7 11:19:00黄义新,方怡冰供稿
摘要:根据辊道窑的特点及常规PID控制器的局限性,采用基于继电反馈的整定方法确定PID控制参数,在此基础上,采用模糊控制理论,根据系统运行过程中的偏差绝对值及偏差的积累绝对值,对PID参数进行实时校正,当参数或工况发生变化时,逐步调整PID参数值,使系统控制性能处于最优状态,实现对PID参数的在线智能校正,并以RS-485串行通信方式组成分布式智能控制系统对辊道窑温度进行集中监控。
该系统已在现场长期连续运行,性能稳定,可靠性高,具有良好的控制性能。
关键词:分布式控制系统;智能控制;PID参数自整定;辊道窑。
1 引言
陶瓷生产是一门古老、历史悠久的传统工业,陶瓷辊道窑的生产过程均采用传统的手工操作,炉温波动幅度大,造成瓷砖质量不高,甚至出现产品不合格的情况,再加上现场环境条件差,工人的劳动强度大,操作员工增加,对企业的经济效益影响较大。
为了提高陶瓷生产水平,根据企业的实际需求和工厂提出的工艺要求,我们研制了一套分布式智能控制系统对辊道窑炉温度进行集中监控,保证炉温的误差在工艺要求之内,从而提高瓷砖的质量与产量,改善工人的劳动条件,提高生产效率。
2 辊道窑温度分布式控制系统的组成及原理
该系统由上位机与下位机两大部分组成,上位机与下位机通过RS-485通讯协议完成信息的传递,上位机由586微机加RS232C/RS485转换器构成,位于集中控制室,完成向下位机(现场控制器)发送命令、接收现场控制器数据及数据分析、存储、报表打印、显示等功能。
下位机由现场温度智能控制器、温度传感器,电动比例调节阀等组成,主要完成对辊道窑炉各点温度的测量、控制及向上位机发送有关数据等。
6个控制器通过电动比例调节阀调整喷油量达到分别控制窑炉内6点温度,从而保证窑炉烧成带温度的恒定,该系统特别适合于象辊道窑这样的小规模DCS系统。
3 智能温度控制器的设计
3.1 概述
常规PID控制器由于具有原理简单,稳定性好,易于实现等优点,因而在过程控制中得到广泛应用,但在辊道窑温度控制系统中,常规PID控制器也暴露出其局限性。
首先常规PID控制器的设计是基于对象的数学模型,而辊道窑炉难以用数学表达式描述,故系统达不到预期的控制品质。
其次当辊道窑的工况发生变化时(例如,油压波动,油的品质变化时),在某一工况下整定的PID参数不能满足性能指标要求。
为此,在PID控制器设计时,首先采用基于继电反馈的整定方法,确定PID调节器参数,再对PID参数实行实时Fuzzy 校正,使其具有自适应功能,从而满足系统变工况的要求。
3.2 温控器的控制策略
3.2.1 PID参数自整定
根据继电振荡原理,继电反馈系统框图如图1所示。
若继电器输出幅度为b,则根据非线性理论,继电器的描述函数为,其中误差信号的幅度为不断调整继电特性的幅值,使系统发生自振荡,然后测取振荡周期与幅度,便可得出临界增益与临界周期。
利用这两个参数,根据Ziegler-Nichols方法,可得出PID参数,,。
PID参数整定完毕后,此参数作为PID控制器Fuzzy校正的初值,并自动转入PID参数Fuzzy校正控制。
一般在系统初次投入时整定,并把整定值存入EEPROM中。
其中Kp为比例系数;Ti为积分时间常数;Td为微分时间常数。
3.2.2 PID参数实时Fuzzy校正
根据上述自整定得出的PID参数,当辊道窑炉参数或工况发生变化时,系统的性能将下降,甚至无法满足工艺要求,所以必须对PID参数进行在线调整。
目前较多地采用自校正PID算法,但这种方法是基于被控对象精确的数学模型,为此,我们采用模糊控制技术,根据系统运行过程中的偏差绝对值及偏差的积累绝对值,对PID参数进行实时校正,当参数或工况发生变化时,逐步调整值,使系统控制性能处于最优状态。
的修正规则如下:
(1)比例系数增大,系统响应速度加快,稳态误差减小,因此在偏差大的情况下,要增大值。
但是过大会使系统产生超调,甚至不稳定,因此在偏差小的情况下,要减小值。
将偏差绝对值的模糊子集取为很大(VB)、大(B)、中(M)、小(S)和很小(VS),的模糊子集取为PB、PS、O、NS、NB,则的修正量的Fuzzy控制规则如表1所示。
其中,的基本论域为[0,10],分为11个量化等级,即={0,1,2,3,4,5,6,7,8,9,10},的基本论域为[-0.5,+0.5],分为11个等级即={-0.5,-0.4,-0.3,-0.2,-0.1,0,0.1,0.2,0.3,0.4,0.5}。
(2)在PID控制器中,积分作用是为了消除稳态误差,加强积分作用(减小)有利于减小稳态误差,但过强的积分作用会引起积分饱和,使系统超调加大,甚至引起振荡。
因此,在调节过程中的初期,即误差的积累较小时,应减弱积分的作用(加大)。
而在调节过程的后期,即误差累积较大时,应加强积分作用(减小)。
将误差累积绝对值的模糊子集取为VB、B、M、S和VS,的模糊子集取为PB、PS、O、NS、NB,则的修正量的Fuzzy控制规则如表2所示。
其中,的基本论域为[0,10],分为11个量化等级,即={0,1,2,3,4,5,6,7,8,9,10},的基本论域为[-5,+5],分为11个量化等级即={-5,-4,-3,-2,-1,0,1,2,3,4,5}。
(3)微分在PID控制中的作用主要是改善系统的动态性能,控制超调。
对于变工况且
不确定系统,在调节过程的初期,即误差的累积绝对值较小时,应加强微分的作用(即增大),而在调节过程的后期,即误差累积的绝对值较大时,应减弱微分的作用(即减小),将的模糊子集取为PB、PS、O、NS、NB,则的修正量的Fuzzy控制规则如表2所示。
其中,的的基本论域为[-1,1],分为11个量化等级即={-1,-0.8,-0.6,-0.4,-0.2,0,0.2,0.4,0.6,0.8,1}。
智能温度控制系统结构图如图2所示,当要整定参数时把开关打在T,参数整定完毕,切换到自动位置A,参数自调整控制器对控制对象进行调节。
4 智能控制器的实现
4.1 控制器的硬件系统
控制器的硬件主要由微处理机系统,输入通道,输出通道,键盘及显示等部分组成。
(1)微处理机系统:由8031单片机,2764 EPROM(用于存放监控及控制程序),2816EEPROM(用于存放自整定的参数及温度设定值),译码电路与锁存器等组成。
(2)输入通道:由热电偶冷端补偿电路,放大电路(OP07,741),V/F,光电耦合,计数器,定时器等组成。
热电偶冷端补偿电路利用PN结电压随温度上升而线性下降的特性进行补偿。
采用两级放大器可将毫伏级信号放大到需要幅度0~5V,由上V/F转换成频率量,再通过软件的定时,计数完成A/D转换工作。
(3)输出通道:由D/A转换器,V/I转换器,输出锁存器和光电隔离电路组成。
D/A 转换器将输出转换为0~5V的电压信号,经V/I转换器输出0~10mA标准电流信号。
(4)键盘及显示部分:由8279,4个键与4个LED组成。
4.2 控制器的软件设计
控制器的软件主要由监控软件与控制软件组成,其软件框图如图3所示
4.3 调度与应用
为了不影响窑炉的正常生产,在PID参数整定前,先手动调节炉温到正常工作点(1200℃)附近,并设定电动比例调节阀的开度在工作点附近±10% 范围内变化,使PID调节器参数整定时,炉温变化幅度较小,如图4所示,其中前10 min为参数整定时间。
温度的变化情况,采样周期t=15s。
该系统已在现场长期连续运行,性能稳定,可靠性高,采用温度智能控制后,在设定温度1200℃时,温度波动范围从原来手动控制时的℃降为℃,(见图4),说明该系统具有良好的控制性能。
5 结论
(1)由于采用分布式控制系统,上位机为586微机,软件资源丰富,可进行集中监控、画面显示、参数设定等工作,下位机能方便地与上位机交换信息,也可以单独运行,对现场进行实时控制,系统可靠性高,且价格低廉。
(2)温度控制器采用PID参数自整定技术,可以大大缩短现场调试时间,特别适合于缺乏自动化工程技术人员的工厂。
(3)对于无法确定精确数学模型及变工况(象燃油炉)控制对象,采用PID控制时,先采用自整定技术确定PID参数的初值,然后根据实时数据,对PID参数进行在线Fuzzy 调整,是一种非常实用且有效的控制策略。
文章来源:中国传动网
原文网址:/publish/tech/application/2008/11/tech_3_16_11747.html。