机械事件仿真及其分析实例
工程施工机械事故案例

工程施工机械事故案例分析一、事故概况2020年某月,我国某城市建设施工现场发生了一起严重的工程施工机械事故。
事故发生在某栋高层建筑的施工现场,当时正在进行楼面混凝土浇筑作业。
事故导致1人死亡,3人受伤,直接经济损失约100万元。
二、事故经过事故发生时,施工现场一台混凝土泵车正在作业。
浇筑过程中,泵车输送混凝土的管道突然断裂,导致混凝土浆液喷溅。
正在附近作业的工人躲闪不及,被喷溅的混凝土浆液击中头部,当场倒地不起。
另外3名工人也被不同程度地喷溅受伤。
三、事故原因1. 设备老化:经过调查发现,事故发生的混凝土泵车存在严重的老化现象,输送管道接口处存在裂纹,导致了事故的发生。
2. 检修不规范:施工单位对泵车的检修维护工作不规范,没有严格按照厂家要求进行保养,导致设备性能不稳定。
3. 现场管理不善:施工现场的安全管理不到位,对机械设备的安全检查不够严格,没有及时发现并排除安全隐患。
四、事故教训及预防措施1. 加强设备管理:施工单位应加强对工程施工机械设备的管理,定期进行检修和维护,确保设备性能稳定。
2. 定期培训:对施工现场的作业人员进行定期安全培训,提高他们的安全意识和操作技能,避免因操作不当导致的事故发生。
3. 强化现场安全管理:施工现场应加强对机械设备的安全检查,及时发现并排除安全隐患。
同时,设置明显的安全警示标志,提醒作业人员注意安全。
4. 制定应急预案:针对可能发生的机械事故,施工单位应制定应急预案,确保在事故发生时能够迅速有效地进行处置,减少损失。
五、结论通过此次工程施工机械事故的调查分析,暴露出施工现场在设备管理、人员培训、现场安全管理等方面存在不足。
为了确保工程施工的顺利进行,施工单位应认真吸取事故教训,加强施工现场的安全管理,确保工程施工机械设备的安全运行。
机械安全事故案例分析

机械安全事故案例分析机械安全事故是生产过程中经常发生的问题,对企业和员工的安全带来极大的威胁。
本篇文章通过对一些典型的机械安全事故案例进行分析,以提高大家对机械安全问题的认识,并找出防止类似事故发生的措施。
案例一:机械伤害某工厂的一名工人在操作一台冲压机时,不慎将手卷入机器中,造成严重伤害。
经过调查分析,事故发生的原因有以下几点:1.工人未按照操作规程操作,伸手进入危险区域。
2.冲压机缺少必要的防护装置,如防护栏、警示标志等。
3.工厂对员工的安全培训不足,导致员工对安全风险认识不足。
案例二:物体打击在某建筑工地上,一名工人在操作塔吊时,吊装的货物突然脱落,将地面上的一名工人击中,导致重伤。
事故原因分析如下:1.工人操作塔吊时,未对货物进行稳固,导致货物脱落。
2.塔吊的监控系统不完备,无法实时监控货物状态。
3.现场安全管理不到位,缺乏对作业现场的安全监督。
案例三:触电事故一家电器生产厂家的员工在维修一台电动机时,未切断电源,直接进行维修,导致触电事故发生。
事故原因分析如下:1.员工在进行设备维修时,未按照操作规程切断电源。
2.企业对设备维修的安全管理不严格,未对员工进行充分的安全教育。
3.设备本身存在缺陷,如缺乏漏电保护装置等。
通过对以上三个案例的分析,我们可以总结出一些防止机械安全事故发生的措施:1.加强员工的安全培训,提高员工的安全意识,使员工熟练掌握安全操作规程。
2.企业应完善设备的安全防护设施,如防护栏、警示标志、漏电保护装置等。
3.企业应建立健全的安全管理制度,加强对作业现场的安全监督,确保各项安全措施得到有效执行。
4.加强设备的日常维护和检修,确保设备处于良好的工作状态。
以上是本文对机械安全事故案例的分析,希望对大家有所启示。
在今后的生产过程中,我们要时刻警惕机械安全风险,确保企业和员工的安全。
案例四:火灾爆炸在某化工厂,由于操作人员未严格遵守操作规程,在搬运易燃物品时引发了火灾,火势蔓延导致爆炸事故。
机械设计中的模拟与仿真技术应用案例

机械设计中的模拟与仿真技术应用案例摘要:机械设计中的模拟与仿真技术被广泛应用于产品设计、工艺优化、可靠性验证等方面。
本文选取了几个典型的应用案例,分别涉及结构分析、动力学仿真和流体力学仿真等方面,以展示模拟与仿真技术在机械设计中的应用效果和优势。
一、结构分析结构分析是机械设计中常见的一项任务,用于评估和优化产品的结构强度和刚度。
通过模拟和仿真技术,可以在产品设计的早期阶段就预测结构的行为,并进行有针对性的改进。
在一家汽车制造公司的案例中,他们面临着一个问题,即如何增加某款轿车的车身刚度,以提高车辆的稳定性。
他们使用了有限元分析(FEA)技术来对车身进行结构分析。
通过改变车身结构中的一些零部件的材料和尺寸,他们通过模拟和仿真确定了最佳的设计方案,最终成功地增加了车辆的刚度,提高了稳定性。
二、动力学仿真动力学仿真是模拟机械系统运动的一种方法,可以精确预测和分析机械系统在不同工况下的运行情况。
在产品设计和优化中,动力学仿真可以帮助设计师评估系统的性能、研究系统的稳定性和响应时间等。
在某家航空航天公司的案例中,他们面临着一个问题,即飞机发动机启动过程中的振动问题。
他们使用了多体动力学仿真技术来分析发动机启动时可能出现的振动,并设计了一种新的结构来减少振动。
通过模拟和仿真技术,他们验证了新结构在减少振动方面的有效性,并成功地解决了该问题。
三、流体力学仿真流体力学仿真是研究流体力学问题的一种方法,可以模拟流体在不同条件下的运动和变化,对于优化机械产品的设计和性能分析具有重要意义。
在一家水泵制造公司的案例中,他们需要提高水泵的效率和降低能耗。
他们使用了计算流体力学(CFD)仿真技术来研究水泵内部流体的行为,并优化了水泵的设计。
通过模拟和仿真技术,他们成功地减少了废弃能量的损失,并提高了水泵的效率。
结论:机械设计中的模拟与仿真技术应用案例表明,模拟与仿真技术在结构分析、动力学仿真和流体力学仿真等方面的应用都能提供高效、准确的分析结果。
机械伤害事故案例分析
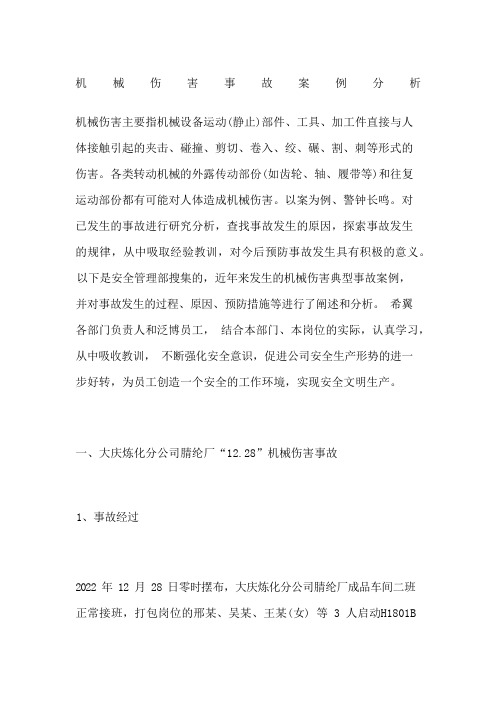
机械伤害事故案例分析机械伤害主要指机械设备运动(静止)部件、工具、加工件直接与人体接触引起的夹击、碰撞、剪切、卷入、绞、碾、割、刺等形式的伤害。
各类转动机械的外露传动部份(如齿轮、轴、履带等)和往复运动部份都有可能对人体造成机械伤害。
以案为例、警钟长鸣。
对已发生的事故进行研究分析,查找事故发生的原因,探索事故发生的规律,从中吸取经验教训,对今后预防事故发生具有积极的意义。
以下是安全管理部搜集的,近年来发生的机械伤害典型事故案例,并对事故发生的过程、原因、预防措施等进行了阐述和分析。
希翼各部门负责人和泛博员工,结合本部门、本岗位的实际,认真学习,从中吸收教训,不断强化安全意识,促进公司安全生产形势的进一步好转,为员工创造一个安全的工作环境,实现安全文明生产。
一、大庆炼化分公司腈纶厂“12.28”机械伤害事故1、事故经过2022 年 12 月 28 日零时摆布,大庆炼化分公司腈纶厂成品车间二班正常接班,打包岗位的邢某、吴某、王某(女) 等 3 人启动H1801B打包机进行打包作业。
在启动打包机过程中,排料门发阻塞,机器浮现故障报警。
班长刘某赶到现场指挥处理故障,刘某安排邢某在操作盘,自己到打包机的二层位置处理故障。
故障排除后,刘某指示邢某进行预压操作,在预压头下降过程中阻塞卡死,打包机再次停机。
零时 30 分摆布,班长刘某联系的肇某推着手推电瓶车到达现场并将监视窗打开,刘某与邢某二人交替站在高为 1.7 米的手推电瓶车上进行清理阻塞物的作业,由另一位打包工吴某负责监护操作盘。
4 时 10 分摆布,预压头上部积累的短纤维基本清除,班长刘某在操作盘上进行开机操作,但未能升起预压头,此时邢某站在监视窗前方的叉车上观察,刘某告诉邢某不要动,他去打包机二层关闭风线阀门,切断打包机动力源,就在他转身上楼时,蓦地听到邢某的喊声,回头看邢某已经被升起的预压头带入打包机内,班长刘某即将返回到操作盘前,急忙按下“预压启动”按钮,将预压头降下来,在闻声赶来的班组其他成员的匡助下,将邢某从监视窗中救出,邢某终因伤势过重,抢救无效于当日死亡。
汽车机械制造中的模拟与仿真技术案例分析

汽车机械制造中的模拟与仿真技术案例分析在当今汽车行业中,模拟与仿真技术成为了不可或缺的一部分。
通过模拟与仿真技术,汽车制造商能够有效地进行产品开发、测试和优化,提高车辆的性能、安全性和可靠性。
本文将通过分析几个实际案例,探讨汽车机械制造中模拟与仿真技术的应用。
案例一:车辆碰撞仿真在汽车设计过程中,理解车辆在碰撞中的表现至关重要。
通过模拟与仿真技术,汽车制造商可以预测车辆在不同碰撞情况下的响应,并进行相应的设计调整。
例如,在碰撞测试中,模拟与仿真技术可以被用来评估车辆结构的刚性和安全性能,从而指导设计师进行优化。
此外,模拟与仿真还可以模拟不同角度和速度的碰撞实验,从而为车辆的碰撞安全设计提供重要参考。
案例二:发动机燃烧仿真发动机燃烧过程对汽车性能的影响非常大。
模拟与仿真技术可以模拟发动机燃烧过程中的燃烧效率、排放和噪音特性。
通过对发动机燃烧过程的模拟与仿真,汽车制造商可以提前预测发动机在不同负荷下的性能,并进行相应的优化。
这不仅提高了发动机的效率和可靠性,还降低了开发过程中的时间和成本。
案例三:悬挂系统动力学仿真悬挂系统是保证汽车行驶平稳性的重要组成部分。
通过模拟与仿真技术,汽车制造商可以评估不同悬挂系统设计方案的动力学表现。
传统方法中,测试和优化需要大量时间和实验成本,而模拟与仿真技术通过模拟悬挂系统的运动学和动力学,可以更快速、更经济地验证设计。
这有助于提高悬挂系统的性能和稳定性,同时降低了开发和测试的时间和成本。
案例四:车辆流体力学仿真车辆的气动特性对其燃油经济性和稳定性有着重要影响。
通过模拟与仿真技术,汽车制造商可以预测车辆在不同速度下的阻力、升力和气动稳定性。
这使得设计师能够评估不同外观设计和车身结构对车辆气动性能的影响,并进行优化。
模拟与仿真技术还可以模拟不同气候条件下的气动特性,从而为全球市场的汽车设计提供准确的数据支持。
综上所述,模拟与仿真技术在汽车机械制造中具有重要的应用价值。
通过分析碰撞仿真、发动机燃烧仿真、悬挂系统动力学仿真和车辆流体力学仿真等案例,我们可以看到这些技术如何帮助汽车制造商提高产品性能、安全性和可靠性。
机械伤害事故案例分析

机械伤害事故案例分析机械伤害事故是在工业生产过程中,由于机器的故障或者操作不当而引发的一种伤害事故。
这种事故往往会对工人的生命和健康带来很大的威胁,因此在生产过程中,必须采取有效措施来降低机械伤害事故的发生率。
下面,我们来看一起机械伤害事故案例,以此为启示制定更好的安全管理和措施,提高工作人员的安全意识。
案例描述:某厂家在印刷厂加工印刷品时,工人在机器上进行操作。
由于这台机器开启的时间太长,加工质量增加的同时,机器也开始发生故障。
机器操作人员为了达到生产要求,往往会忽略机器的维护和保养工作。
一天,机器在加工一些排版时出现故障,机器操作人员开始拆卸机器进行修理。
由于过于匆忙和急躁,工人没有关好机器的安全装置,在进行维护的过程中,不慎被机器卡住。
由于机器的运转速度非常快,工人受到的伤害非常严重。
工人被卡在了机器上,等到其他员工发现后,他已经失去了意识。
随后,救援人员及时赶到,将工人送往医院,经过治疗,生命得以保住。
案例分析:这起事故的发生是由于操作员冲动和机器未得到及时维护导致的。
作为员工,安全意识非常重要。
如果工人在维护机器时更加小心谨慎,遵循工作流程规范,遵循安全注意事项,他就不会在操作过程中受伤。
此外,机器设备使用的时间太长,也会影响其性能和使用寿命,导致故障发生的可能性增加。
因此,机器设备的维护和保养是非常重要的。
设备完好和使用规范对于减少机械伤害事故是非常有必要的。
结论:对于机械伤害事故的发生,我们必须认真对待。
为了保障安全及减少机械伤害事故的发生,我们需要在以下方面开展工作:1.加强员工安全意识教育,帮助员工了解安全的重要性和必要性。
2.及时维护和保养设备,检查设备的性能和质量,确保设备使用寿命的延长。
3.合理安排生产计划,确保员工的工作强度和操作时间不会过长。
4.完善员工培训体系,确保员工能够掌握使用和维护机器的方法技能。
重要的是要时刻关注和了解机器的性能和使用寿命。
通过完善的安全管理和生产计划,保障员工的安全,避免机械伤害事故的发生。
机械事故分析报告

机械事故分析报告1. 引言机械事故是指由于机械设备或系统故障导致的意外事件。
它们可能会对人员、设备和环境造成严重的损害。
本报告旨在对一起机械事故进行分析,以确定其原因并提出相应的解决方案,以避免类似事故再次发生。
2. 事故描述在某工厂的生产线上,一台自动化机械设备发生了故障。
据工厂工作人员描述,故障发生时,机械设备突然停止工作,并发出异常的噪音。
工作人员立即停止了生产线,并将故障设备隔离以确保安全。
3. 调查过程为了确定事故的原因,我们进行了详细的调查。
以下是我们的调查过程和结果:3.1 现场勘察我们首先对事故现场进行了勘察。
我们注意到机械设备的一部分零件出现了明显的磨损和断裂。
此外,我们还发现了一些润滑油的泄漏痕迹。
3.2 设备维护记录我们进一步调查了该设备的维护记录。
根据记录,该设备的维护一直按照规定进行,并定期更换润滑油和检查零部件的磨损情况。
3.3 人员采访我们与相关工厂工作人员和机械设备操作员进行了面对面的采访。
他们表示,在事故发生前,没有发现任何设备异常或操作问题。
3.4 专家意见为了得到更专业的意见,我们咨询了机械工程师。
根据他的意见,这种故障很可能是由于零部件磨损过度导致的。
他们建议进行更频繁的维护和更换耐磨损的零件。
4. 分析和结论综合以上调查结果,我们得出以下分析和结论:•机械设备的故障是由于零部件磨损过度导致的,这导致了设备的突然停止和异常噪音。
•尽管设备的维护记录表明已按规定进行维护,但可能需要增加维护频率和更换耐磨损零件的策略。
•润滑油的泄漏可能是零部件磨损的一个征兆,应更加注意检查和修复润滑系统。
5. 解决方案基于我们的分析和结论,我们提出以下解决方案以预防类似的机械事故发生:•增加设备的维护频率,特别是对易损耗的零件进行更频繁的检查和更换。
•提高工作人员的培训水平,使他们能够更早地发现设备异常,并采取相应的措施。
•加强润滑系统的监控和维护,确保其正常运行并及早发现泄漏问题。
工程机械故障分析案例分享经验

工程机械故障分析案例分享经验1. 案例一:液压系统故障在一次建筑工地的挖土机作业中,挖斗无法正常升降。
经过维修人员的检查,发现液压系统存在故障。
经过仔细分析,确定是液压泵的密封件磨损严重导致压力不稳定,进而影响了挖斗的升降功能。
解决该问题的方法是更换液压泵的密封件,并对液压系统进行全面检修,确保系统正常运行。
2. 案例二:电路系统故障某建筑工地的起重机在使用过程中突然失去了电源供应,无法正常运行。
经过检查,发现电路系统中的保险丝烧断,导致电流无法正常传导。
经过仔细分析,确认是电路系统中出现了过载情况,超出了保险丝的额定负荷。
解决该问题的方法是更换合适额定负荷的保险丝,并对电路系统进行全面检修,确保系统正常工作。
3. 案例三:机械结构故障在一次道路施工作业中,压路机的振动系统发生异常,振动力不稳定。
经过维修人员的检查,发现机械结构中的振动轴出现了严重的磨损,导致振动力的传递不稳定。
解决该问题的方法是更换新的振动轴,并对机械结构进行全面检修,确保振动系统正常工作。
4. 案例四:润滑系统故障一台挖掘机在使用过程中发现发动机温度过高,无法正常工作。
经过检查,发现是润滑系统中的油液不足,并未有效进行发动机部件的润滑。
解决该问题的方法是及时添加足够的润滑油,并对润滑系统进行全面检修,确保发动机正常工作。
5. 案例五:传动系统故障一辆装载机在使用过程中发现换挡困难,无法正常行驶。
经过检查,发现传动系统中的离合器磨损严重,无法有效传递动力。
解决该问题的方法是更换新的离合器,并对传动系统进行全面检修,确保装载机能够正常行驶。
通过以上案例的分析,我们可以得出以下经验:- 定期检查和维护工程机械的液压系统、电路系统、机械结构、润滑系统和传动系统,确保各个部件和系统正常运行。
- 注意机械设备的润滑和保养工作,及时添加润滑油,确保设备部件的正常润滑,防止因润滑不良导致的故障。
- 对于故障问题,要进行详细的分析和排查,找出问题的根源,然后采取相应的修复措施,确保设备恢复正常工作。
- 1、下载文档前请自行甄别文档内容的完整性,平台不提供额外的编辑、内容补充、找答案等附加服务。
- 2、"仅部分预览"的文档,不可在线预览部分如存在完整性等问题,可反馈申请退款(可完整预览的文档不适用该条件!)。
- 3、如文档侵犯您的权益,请联系客服反馈,我们会尽快为您处理(人工客服工作时间:9:00-18:30)。
2001年12月 沈阳工业学院学报 V o l.20N o.4第20卷第4期 JOU RNAL O F SH EN YAN G I N ST ITU T E O F T ECHNOLO GY D ec.2001文章编号:1003-1251(2001)04-0001-05机械事件仿真及其分析实例马星国1,安晓卫2,刘增龙2(11沈阳工业学院教务处,辽宁沈阳110016;21沈阳工业学院) 摘 要:机械事件仿真集成了运动学、柔体动力学和非线性应力分析理论,可以对一个事件的过程进行分析.本文简要介绍了其基本思想,并采用该方法对125穿甲弹在膛内运动这一事件进行了仿真分析.关键词:机械事件仿真;有限元;穿甲弹中图分类号:TB115 文献标识码:A1997年6月,美国工程师提出一种叫做虚拟工程分析(V irtual Engineering)的新方法.虚拟工程分析的提出是自25年前计算机应用于产品设计和研究以来,此领域的又一次伟大革命.虚拟工程分析将计算机仿真技术与计算机辅助工程分析有机结合,在虚拟的工程环境中对一个物理事件发生的过程进行研究和分析.例如,虚拟工程分析可以预测一座桥梁在地震时的响应状态,一个飞机零件在高温下是否会失效等,机械事件仿真(M echan ical Even t Si m u lati on)属于虚拟工程分析.以往的有限元分析,只能得到物体某一时刻受力的大小和位置,对下一时刻只能预测.真实世界中物体的一切变化(受力、变形)均处在一个过程中,对整个过程分析将是很有意义的.机械事件仿真提出一个过程的概念,本文利用该方法对穿甲弹弹带挤进过程受力、变形全过程进行了研究,得到了面向过程的弹带在膛内任意时刻的应力及变形云图等,对弹带的分析是全程的,比对某一时刻的分析更加全面、准确.1 机械事件仿真的基本理论机械事件仿真集成了运动学、柔体动力学和非线性应力分析理论.事件仿真通过在虚拟环境中模拟一个物理事件进行工程分析,用先进的计算机图象显示技术、后处理功能和有限元模型再现了物理事件发生进行的过程.提出了用规定位移代替外力作为分析的已知条件的概念.事件仿真可以用最少的假设来模拟一个物理事件的完整过程,特别在分析一个运动的受力物体时,不必再假设物体处在某一静止位置.一般地,认为应力是力的函数,即Ρ=f(F),并且变形和位移也是力的函数,即d=g(F).收稿日期:2001-09-10作者简介:马星国(1963—),男,辽宁昌图人,教授,工学硕士.2沈阳工业学院学报 2001年在虚拟工程分析中,认为力在运动中是变化的并且是同运动相关的,在特定的条件下,力和应力可以看作是位移和变形的函数,即F=f(d)和Ρ=g(d),位移和变形可以通过动力学方程求出.机械事件仿真分析不单单得到一个静止的解,而是模拟整个事件过程.根据牛顿第二定律及虎克定律可得:m a+cv+kd=0(1) 用矩阵表示为M a+Cv+Kd=0(2) 这就是虚拟工程分析的基本方程,综合考虑了运动、阻尼和变形.该方程虽和有限元分析所用方程一样,但在处理问题的思路上有所不同.在事件过程中,任一时刻的应力可通过公式得出,Ρ=EΕ,这里应变向量Ε可由位移向量d求得.2 分析实例本文采用AL GOR公司的Superdraw 软件利用机械事件仿真分析方法对125穿甲弹在膛内(滑膛)的运动及受力进行分析.2.1 基本假设(1)弹带、弹托、弹芯是一完整的轴对称结构——由于弹芯的轴对称性、弹带的轴对称性以及弹托被完全紧固,可以将弹丸作为轴对称结构.(2)载荷具有轴对称性.(3)弹丸不旋转、不计重力;弹托和尾翼被省去,而以等效质量代替.(4)忽略温度应力场——由于挤进过程历时非常短,膛内温度的变化不可能在瞬时完成,所以温度应力场可不记;(5)不计阻尼和弹丸在直膛区的摩擦阻力.在挤进过程中弹丸和坡膛间的摩擦阻力已考虑在挤进阻力曲线中;而在直膛区弹丸和膛壁间的摩擦阻力很小,因此不计.根据以上假设,研究对象为轴对称结构,弹带镶嵌在弹托上,弹芯、弹托间以环槽相接触,这里以刚性连接,全弹在炮膛内只受载荷(弹底压力)和炮壁径向约束,其余方向完全自由.2.2 建模2.2.1 表面、层、组的应用在建模中充分利用表面、层、组,使较复杂的弹丸分体建模变得容易.此穿甲弹模型共分4个构件:弹芯、弹托、弹带和炮身,因此用了4个组表示4个构件.并且材料也用组来表示,每组只能用一种材料.2.2.2 材料弹带的材料为尼龙.在挤进过程中,弹带在短时间内发生较大变形,应变率比较高.弹芯的材料为钨合金,弹托的材料为硬铝,炮身材料为碳素钢,炮身的所有节点被全约束,实质上只作为参照物,不参与计算.2.2.3 弹带挤进——规定位移弹带的挤进过程十分复杂,由于弹带的挤进过程是在非常短的时间内完成,给实验测定造成困难,目前尚无此方面的实验数据,也无严格的理论分析.本文采用了在某些节点加“规定位移”的方法,弹带的径向位移是一定的,由于炮身内膛的口径为125mm ,弹带的外径在挤进前为12915mm ,在挤进后一定要变成125mm ,并且一开始为线接触,随着挤进的深入逐渐变为面接触,及至弹带全部挤进内径125mm 的炮膛.在此轴对称模型中弹带的径向规定位移为2125mm .2.2.4 模型参数和网格图图1为125穿甲弹的二维模型图.穿甲弹的有限元模型采用2维三角形和四边形混合单元.图1 125穿甲弹的二维模型2.3 边界条件和载荷整个穿甲弹模型为轴对称模型.对称轴只有轴向位移.在弹托的125mm 外径的径向定位处只有轴向位移.其余节点全为自由.载荷,即弹底压力曲线(P -T 曲线)由实验测得,穿甲弹在发射过程中挤进时还要受到挤进阻力的作用,挤进阻力可通过运动方程S (P d -R )=m a 求得,其中a 为穿甲弹的加速度,S 为穿甲弹的125直径处的横截面面积,P d 为弹底压力,因此挤进阻力R 为随时间变化的压力.2.4 事件分析及其结果弹丸在膛内受压力作用时间为0100595s ,由实验得出.步长为0100001s .所有参数都设定好后就可以进行分析了.在分析时,可直接通过后处理即时看模型的动态变化,也可以看模型的运动曲线.2.4.1 运动特性通过分析,可得出穿甲弹模型上的任一节点的运动参数,图2、图3为弹芯底部一点的速度和加速度曲线.3第4期 马星国等:机械事件仿真及其分析实例图2 速度曲线图3 加速度曲线根据速度曲线,弹丸的出炮口速度为1920m s ,而125穿甲弹的出炮口速度实验数值为1740m s ,相对误差为10135%,与实验数据基本吻合.计算结果略大于实验数据主要是因为计算中忽略了阻尼、弹丸在运动过程中与炮膛膛壁之间的摩擦阻力而致.2.4.2 应力及应变模型的应力和应变为一动态过程,是随时间变化的.这里只截选二个瞬间,图4和图5分别为挤进过程中和最大膛压时的等应力云图.图4 125穿甲弹挤进过程中的等应力云图图5 125穿甲弹在最大膛压时的等应力云图图6 穿甲弹在运动过程中最大应力曲线最大应力曲线如图6.通过该曲线可看出穿甲弹的最大应力在010016s 到010038s 之间几乎不变,为弹芯进入塑性区.在本文的计算中认为坡膛为刚体、没有变形.这导致计算所得的应力偏大.2.4.3 运动过程本例共生成弹带的挤进过程及其受力、挤进过程中整个弹体的应力变化和变形情况、弹丸在膛内的整个运动过程三个动画文件,通过这三个动画演示了仿真分析结果.4沈阳工业学院学报 2001年3 结论(1)机械事件仿真集成了运动学、柔体动力学和非线性应力分析理论.通过在虚拟环境中模拟一个物理事件进行工程分析,用计算机图象显示技术和后处理功能用有限元模型再现了物理事件发生进行的全过程,并提出了用规定位移代替外力作为分析的已知条件的解题思路.(2)应用机械事件仿真方法分析穿甲弹在膛内的运动及受力,可以得到任意时刻、任意点的位移、速度、加速度及应力.(3)应用机械事件仿真方法分析穿甲弹在膛内的运动及受力,可得到弹带的挤进过程及其受力、挤进过程中整个弹体的应力变化和变形情况、弹丸在膛内的运动三个过程的动态仿真动画.从中可知穿甲弹所受应力的变化及屈服发生的时刻和区域,可分析出最大应力的变化规律.参考文献:[1]朱以文,韦庆如,顾伯达1微机有限元前后处理系统V izi CAD 及应用[M ]1北京:科学技术文献出版社,1993.[2]宁俊生1发射初期弹带材料对弹带及弹托中应力的影响[J ]1兵器材料科学与工程,1995,(5):39244.[3]李健1尾翼稳定脱壳穿甲弹在线膛炮膛内的运动分析[J ]1兵工学报弹箭分册,1992,(4):33241.[4]D 1R 1J 1欧文,E 1辛顿著1弹性力学有限元——理论与应用[M ]1曾国平等译1北京:兵器工业出版社,1989.M echan ica l Even t Si m ula tion and Its Appl ica tion i nAna lysis of Arm orp ierc i ng ShellM A X ing 2guo 1,AN X iao 2w ei 2,L I U Zeng 2long2(1.T he D ep t .of T each ing A ffairs ,Shenyang Institute of T echno logy ,Shenyang 110016,Ch ina ;2.Shenyang Institute of T echno logy )Abstract :M echan ical even t si m u lati on com b ines rigid flex ib le k inem atics 、non linear FE M together .It can analyses the w ho le p rocess of a m echan ical even t .In th is paper ,the basic theo ry of m echan ical even t si m u lati on is in troduced and si m u lati on of 1252ar m o rp iercing shell in cana fo r a k inetic p rocess is given .Key words :m echan ical even t si m u lati on ;FEA ;ar m o rp iercing shell5第4期 马星国等:机械事件仿真及其分析实例。