TSFF5210_08中文资料
DLT 5210
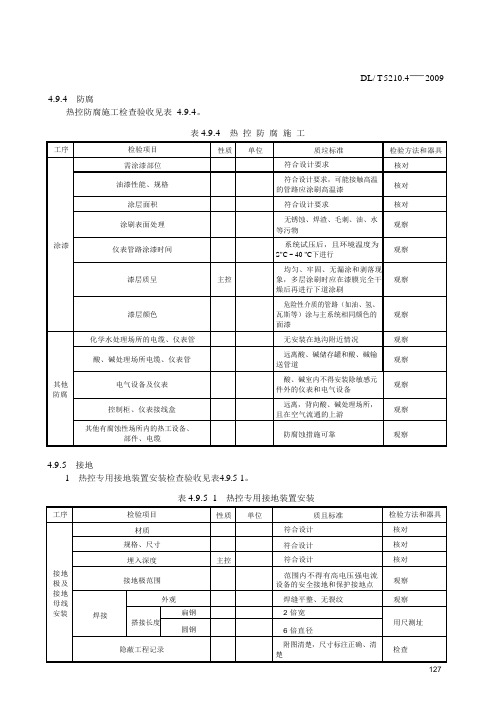
断偶保护
符合检定规程要求
冷端温度补偿
·c
比较法,二等水银温度计
调校
零点迁移
符合检定规程要求
输入信号检查
示值误差
主控
%
符合检定规程要求
输入信号检查
回程误差
主控
·c
符合检定规程要求
输入信号检查
4流拢测蜇仪表检定
各种流量测量仪表检定见表4.10.2-9表4.10.2-15。
表4.10.2- 9转 子 流 量 计 检 定
清楚
观察
调校
液柱修正
正确
观察
示值误差
主控
%
符合检定规程要求
比较法,压力、真空校验台和标
准仪表
回程误差
主控
Pa
符合检定规程要求
轻敲变动址
Pa
符合检定规程要求
观察
指针在全程中运动
符合检定规程要求
观察
表4.10.2- 4(续)
。
3传感器和变送器调校
各种传感器和变送器调校见表4.10.2-5表4.10.2-8。
工序
检验项目
性质
单位
质品标准
检验方法和器具
检查
电源电压
极性
正、负极性正确
使用数字电压表测泣
幅值
符合制造厂负载特性曲线要求
严密性
无渗漏
按制造厂要求进行压力试验
调校
压力变送器液柱修正
正确
输入压力或差压检查
示值误差
主控
%
符合检定规程要求
回程误差
主控
%
符合检定规程要求
输入压力或差压检查
端基一致性
%
MIL-DTL-5015H-2008

MIL-DTL-5015HAMSC N/A FSC 5935DETAIL SPECIFICATIONCONNECTORS, ELECTRICAL, CIRCULAR THREADED, AN TYPE,GENERAL SPECIFICATION FORThis specification is approved for use by all Departments and Agencies of the Department of Defense.1. SCOPE1.1 Scope. This specification covers circular threaded electrical connectors with solder or removable crimp contacts (both front and rear release). These connectors are for use in electronic, electrical power, and control circuits (see 6.1).1.2 Classification. Electrical connectors covered by this specification are divided into the following classes, series, and receptacle styles.1.2.1 Classes. The classes of electrical connectors are as follows:Class A - Solid shell solder contact connectorsClass B - Split shell solder contact connectorsClass C - Solder contact connectors for use with pressurized equipmentClass D - Crimp and solder contact connectors for use in high-impact shock conditions Class DJ - Crimp contact connectors with backshell connector assembly for use in high impact shock conditionsComments, suggestions, or questions on this document should be addressed to the Naval Air Systems Command (Commander, Naval Air Warfare Center Aircraft Division, Code4L8000B120-3, Highway 547, Lakehurst, NJ 08733-5100) or by e-mail to***********************. Since contact information can change, you may want to verify the currency of this address information using the ASSIST online database at .w/AMENDMENT 12Class E - Environment resistant solder contact connectorsClass F - Environment resistant solder contact connectors, with clampClass H - Hermetic solder contact connectorsClass K - Crimp and solder firewall connectorsClass L - Fluid resistant crimp contact connectorsClass P - Environment resistant potted solder contact connectorsClass R - Crimp and solder contact connector with grommet seal without clamp Class U - Fluid resistant crimp contact connectorsClass W - General purpose crimp contact connectors1.2.2 Series. The series of electrical connectors are as follows:Series I - Solder contact connectorsSeries II - Front release, crimp contact connectorsSeries III - Rear release, crimp contact connectorsSeries IV - Connector accessories1.2.3 Receptacle styles. The receptacle styles of electrical connectors are as follows:Flange (box or wall)Jam nutCable connectingSolder mounting2. APPLICABLE DOCUMENTS2.1 General. The documents listed in this section are specified in sections 3 and 4 of this specification. This section does not include documents cited in other sections of thisspecification or recommended for additional information or as examples. While every effort has been made to ensure the completeness of this list, document users are cautioned that they must meet all specified requirements documents cited in sections 3 and 4 of this specification, whether or not they are listed.2.2 Government documents.2.2.1 Specifications and standards. The following specifications and standards form a part of this document to the extent specified herein. Unless otherwise specified, the issues of these documents are those listed in the issue of the Department of Defense Index of Specifications and Standards (DoDISS) and supplement thereto, cited in the solicitation (see 6.2).w/AMENDMENT 1SPECIFICATIONSFEDERALL-P-410 - Plastic, Polyamide (Nylon), Rigid, Rods, Tubes, Flats,Molded and Cast Parts.QQ-S-365 - DELETEDQQ-P-416 - DELETEDDEPARTMENT OF DEFENSEMIL-S-901 - Shock Tests H.I. (High-Impact) Shipboard Machinery,Equipment, and Systems, Requirements for.MIL-C-915 - Cable and Cord, Electrical, for Shipboard Use, GeneralSpecification for.MIL-H-5606 - Hydraulic Fluid, Petroleum Base; Aircraft, Missile, andOrdnance. (Inactive for new design)MIL-S-7742 - Screw Threads, Standard, Optimum Selected Series:General Specification for. (Inactive for new design) MIL-PRF-7808 - Lubricating Oil, Aircraft Turbine Engine, Synthetic Base.MIL-PRF-8516 - Sealing Compound, Synthetic Rubber, Electric Connectorsand Electric Systems, Chemically Cured.MIL-W-16878 - Wire, Electrical, Insulated, General Specification for.MIL-DTL-22520 - Crimping Tools, Terminal, General Specification for.MIL-W-22759 - DELETEDMIL-PRF-23586 - Sealing Compound (With Accelerator), Silicone Rubber,Electrical.MIL-W-25038 - Wire, Electrical, High Temperature, Fire Resistant, andFlight Critical, General Specification for.MIL-C-39029 - DELETEDMIL-C-39029/29 - DELETEDMIL-C-39029/30 - DELETEDMIL-C-39029/44 - DELETEDMIL-C-39029/45 - DELETEDMIL-DTL-81381 - Wire, Electric, Polyamide-Insulated, Copper or CopperAlloy.MIL-I-81969/14 - Installing and Removal Tools, Connector, Electrical Contact,Type III, Class 2, Composition B.MIL-I-81969/15 - Installing and Removal Tools, Connector, Electrical Contact,Type II, Class 2, Composition A.MIL-I-81969/17 - Installing and Removal Tools, Connectors, ElectricalContact, Type 1, Composition C.3w/AMENDMENT 1MIL-I-81969/19 - Installing and Removal Tools, Connector, Electrical Contact,Type II, Class 1, Composition C.MIL-C-85049 - DELETEDMIL-C-85049/11 - DELETEDMIL-C-85049/52 - DELETED(See supplement 1 for list of MS sheets.)STANDARDSFEDERALFED-STD-H28 - Screw-Thread Standards for Federal Services.DEPARTMENT OF DEFENSEMIL-STD-167-1 - Mechanical Vibrations of Shipboard Equipment (Type I-Environmental and Type II-Internally Excited).MIL-STD-1285 - Marking of Electrical and Electronic Parts.MIL-STD-1344 - DELETEDMIL-STD-1651 - Insert Arrangements for MIL-C-5015, MIL-C-22992(Classes C, J, and R), and MIL-C-83723 (Series II) ElectricalConnectors.(Unless otherwise indicated, copies of the above specifications and standards are available from the Standardization Document Order Desk, 700 Robbins Avenue, Building 4D, Philadelphia, PA 19111-5094.)2.3 Non-Government publications. The following documents form a part of this document to the extent specified herein. Unless otherwise specified, the issues of the documents which are DoD adopted are those listed in the issue of the DoDISS cited in the solicitation. Unless otherwise specified, the issues of the documents not listed in the DoDISS are the issues of the documents cited in the solicitation (see 6.2).AMERICAN NATIONAL STANDARDS INSTITUTEANSI-Z540.1 - Laboratories, Calibration, and Measuring and TestEquipment. (DoD adopted)(Application for copies should be addressed to American National Standards Institute,11 West 42nd Street, New York, NY 10036.)4w/AMENDMENT 1AMERICAN SOCIETY FOR TESTING AND MATERIALS (ASTM)ASTM-B85 - Aluminum-Alloy Die Castings. (DoD adopted)ASTM-A342 - Materials, Feebly Magnetic, Permeability of. (DoD adopted)ASTM-B488 - Gold for Engineering Uses, Electrodeposited Coatings of.(DoD adopted)ASTM-A582 - Free-Machining Stainless and Heat Resisting Steel Bars.(DoD adopted)ASTM-B700 - Standard Specification for Electrodeposited Silver forEngineering Use.ASTM-B733 - Metals, Autocatalytic Electroless Nickel-PhosphorusCoating On. (DoD adopted)(Application for copies should be addressed to the American Society for Testing and Materials, 100 Barr Harbor Drive, West Conshohocken, PA 19428-2959.)ELECTRONIC COMPONENTS ASSOCIATIONEIA-364-02 - Air Leakage Test Procedure for Electrical Connectors.(DoD adopted)EIA-364-03 - Altitude Immersion Test Procedure for ElectricalConnectors. (DoD adopted)EIA-364-05 - Contact Insertion, Release and Removal Force TestProcedure for Electrical Connectors. (DoD adopted) EIA-364-06 - Contact Resistance Test Procedure for ElectricalConnectors. (DoD adopted)EIA-364-09 - Durability Test Procedure for Electrical Connectorsand Contacts. (DoD adopted)EIA-364-010 - Fluid Immersion Test Procedure for Electrical Connectors.(DoD adopted)EIA-364-020 - Withstanding Voltage Test Procedure for ElectricalConnectors, Sockets and Coaxial Contacts. (DoD adopted) EIA-364-021 - Insulation Resistance Test Procedure for ElectricalConnectors, Sockets, and Coaxial Contacts. (DoD adopted) EIA-364-025 - Probe Damage Test Procedure for Electrical Connectors.(DoD adopted)EIA-364-026 - Salt Spray Test Procedure for Electrical Connectors,Contacts and Sockets. (DoD adopted)EIA-364-027 - Mechanical Shock (Specified Pulse) Test Procedure forElectrical Connectors. (DoD adopted)5w/AMENDMENT 1EIA-364-028 - Vibration Test Procedure for Electrical Connectors andSockets. (DoD adopted)EIA-364-031 - Humidity Test Procedure for Electrical Connectors andSockets. (DoD adopted)EIA-364-032 - Thermal Shock (Temperature Cycling) Test Procedure forElectrical Connectors and Sockets. (DoD adopted) EIA-364-035 - Insert Retention Test Procedure for Electrical Connectors.(DoD adopted)EIA-364-037 - Contact Engagement and Separation Force Test Procedurefor Electrical Connectors. (DoD adopted) EIA-364-045 - Firewall Flame Test Procedure for Electrical Connectors.(DoD adopted)EIA-364-083 - Shell-to-Shell and Shell-to-Bulkhead Resistance TestProcedure for Electrical Connectors. (DoD adopted) (Copies of these documents are available from or Electronic Components Association, 2500 Wilson Boulevard, Arlington, VA 22201-3834.) THE INSTITUTE FOR INTERCONNECTING AND PACKAGING ELECTRONICCIRCUITSJ-STD-001 - Requirements for Soldered Electrical and ElectronicAssemblies.J-STD-006 - Electronic Grade Solder Alloys and Fluxed andNon-Fluxed Solid Solders for Electronic SolderingApplications Requirements For.(Application for copies should be addressed to the Institute for Interconnecting and Packaging Electronic Circuits (IPC, Inc), 2215 Sanders Road, Suite 200 South, Northbrook,IL 60062-6126.)SOCIETY OF AUTOMOTIVE ENGINEERS (SAE) INTERNATIONALSAE-AMS-QQ-P-416 - Plating, Cadmium (Electrodeposited). (DoD adopted) SAE-AIR1351 - Aerospace Electrical and Electronic Wiring Devices andAccessories, Manufacturers’ Identification of.(DoD adopted)SAE-AMS-QQ-S-763 Steel Bars, Wire, Shapes, and Forgings; CorrosionResistant. (DoD adopted)SAE-AS22759 - Wire, Electrical, Fluoropolymer-insulated, Copper orCopper Alloy. (DoD adopted)6w/AMENDMENT 1SAE-AS31091 - Boots, Heat-Shrinkable, Strain-Relief Straight.(DoD adopted)SAE-AS31971 - Pin, Gage for Socket Contact Engagement Test.(DoD adopted)SAE-AS34021 - Connector, Receptacle, Electric, Box Mounting, FrontRelease, Crimp Contact, AN Type with. (DoD adopted) SAE-AS34121 - Connectors, Receptacle, Electric, Wall Mounting, FrontRelease, Crimp Contact, AN Type-with AccessoryThreads. (DoD adopted)SAE-AS34591 - Connectors, Plug, Electrical, Self-Locking, Coupling Nut,Rear Release, Crimp Contact, AN Type. (DoD adopted) SAE-AS39029 - Contacts, Electrical Connector, General Specification for.(DoD adopted)SAE-AS39029/29 - Contacts, Electrical Connector, Pin, Crimp Removable,(for MIL-C-5015 Series MS3450 and MIL-C-83723Series 2 Connectors). (DoD adopted)SAE-AS39029/30 - Contacts, Electrical Connector, Socket, CrimpRemovable (for AS50151 Series, AS34501 andMIL-DTL-83723 Series 2 Connectors). (DoD Adopted) SAE-AS39029/44 - Contacts, Electrical Connector, Pin, Crimp Removable(for MIL-C-5015 Series MS3400 Connectors). (DoDadopted)SAE-AS39029/45 - Contacts, Electrical Connector, Socket, CrimpRemovable (for MIL-C-5015 Series MS3400Connectors). (DoD adopted)SAE-AS85049 - Connector Accessories, Electrical, General Specificationfor. (DoD adopted)SAE-AS85049/11 - Connector Accessories, Electrical, Backshell,Environmental, Cable Sealing, Straight, Category 1A(for MIL-C-5015 Crimp, MIL-C-26482 Series 2,MIL-C-81703 Series 3, and MIL-C-83723 Series IIIConnectors). (DoD adopted)SAE-AS85049/52 - Connector Accessories, Electrical, Strain Relief,Nonenvironmental, Self-Locking and Non Self-Locking,Straight, Category 4B (for MIL-C-5015 Crimp,MIL-C-26482 Series 2, MIL-C-81703 Series 3, andMIL-C-81723 Series III Connectors). (DoD adopted) (Application for copies should be addressed to Society of Automotive Engineers International, 400 Commonwealth Drive, Warrendale, PA 15096 or .)7w/AMENDMENT 12.4 Order of precedence. In the event of a conflict between the text of this document and the references cited herein (except for related associated specifications, or MS sheets), the text of this document shall take precedence. Nothing in this document, however, supersedes applicable laws and regulations unless a specific exemption has been obtained.3. REQUIREMENTS3.1 MS sheets. The individual item requirements shall be as specified herein and in accordance with the applicable MS sheets. In the event of any conflict between the requirements of this specification and the MS sheets, the latter shall govern.3.2 Qualification. The connectors furnished under this specification shall be products that are authorized by the qualifying activity for listing on the applicable qualified products list before contract award (see4.3 and 6.14).3.3 Materials.3.3.1 Dissimilar metals. When dissimilar metals are employed in contact with each other ina connector or in a mated pair of connectors, protection against galvanic corrosion shall be provided (see 6.17).3.3.2 Nonmagnetic materials (except class H and K connectors). All parts shall be made of materials which are classed as nonmagnetic except for classes H and K connectors (see 1.2 and 3.6).3.3.3 Contacts.3.3.3.1 Contact materials. Contacts shall be made of conductive materials. Thermocouple contacts shall be made of a material compatible with the thermocouple wire to which attachment is intended (see 6.16).3.3.3.2 Contact plating.3.3.3.2.1 Contact plating (solder type, except class H). Contacts shall be silver plated in accordance with ASTM-B700 or gold plated in accordance with ASTM-B488 over silver plating in accordance with ASTM-B700. The resultant minimum thickness of contact plating shall be 100 microinches. Accessory members of the socket contacts need not be plated but shall meet the requirements for dissimilar metals specified in 3.3.1.3.3.3.2.2 Contact plating (class H connectors). Contacts shall be gold plated to a thickness of not less than 50 microinches in accordance with ASTM-B488, type 3, code C, over an underplate approved by the qualifying activity (see 6.14). A silver underplate shall not be used.8w/AMENDMENT 13.3.3.2.3 Contact plating (thermocouple). Thermocouple contacts shall be cadmium plated in accordance with SAE-AMS-QQ-P-416, or otherwise protected from corrosion. Accessory members of the socket contacts need not be plated, but shall meet the requirements for dissimilar metals (see 3.3.1).3.3.4 Dielectric materials.3.3.4.1 Insert and grommet. Insert and grommet materials shall be dielectric having hardness, electrical, and mechanical characteristics capable of meeting the requirements of this specification.3.3.4.1.1 Connectors (except solder contact class A, B, C, H, K, and P). The mating faces of pin inserts of solder contact connectors shall be a resilient material within a Shore A Durometer range of 60 to 85. On crimp contact front release connectors and rear release style P connectors the Shore A Durometer range shall be 35 to 85 with a thickness of not less then 0.090 inch.3.3.4.1.2 Class H. The hermetic sealing of class H connectors shall be accomplished by the use of vitreous material. The mating faces of pin inserts shall be resilient material within a ShoreA Durometer range of 35 to 55.3.3.5 Potting molds. Potting molds shall be made of polyamide conforming to L-P-410. The molds shall incorporate a means for attachment to the connector and shall accept and bond to MIL-PRF-8516 or MIL-PRF-23586 potting material without treatment by the user.3.3.6 Shells, coupling rings, and backshells.a. Connector shells and coupling rings, except for class D, H, and K, shall be madeof aluminum alloys. Die castings, if used, shall conform to ASTM-B85, composition number GPASC84B.b. Class D shells and coupling rings shall be made of a heat treated wrought aluminum alloy meeting the requirements of this specification.c. Class H and K shells and coupling rings shall be made of ferrous alloy.d. Class H, K, L, and U shells and coupling rings shall be made of non-magnetic corrosion-resistant steel in accordance with SAE-AMS-QQ-S-763, 300 series, or ASTM-A582, type XM-1 or 303. Class D and DJ shells and coupling rings shall be made of non-magnetic corrosion resistant steel in accordance with SAE-AMS-QQ-S-763, series 316 class.9w/AMENDMENT 110e. Backshells shall be fabricated and finished with the same materials as the connectors.3.3.6.1 Finish. The resultant finish on all connectors shall be electrically conductive.a. The finish of class A, B, C, E, F, P, and R connectors with aluminum alloy shells,coupling rings, and external screws shall be cadmium plated in accordance with SAE-AMS-QQ-P-416, type II, class 3. A preliminary plating of another metal is permissible. The resultant finish on cadmium plated connectors shall be olive drab (light to dark). Stainless steel in accordance with SAE-AMS-QQ-S-763 is an acceptable alternative for external screws.b. The finish of class D connectors with wrought aluminum shells and coupling rings, class W connectors with aluminum alloy shells and coupling rings, and external screws for these classes shall be cadmium plated in accordance with SAE-AMS-QQ-P-416, type II, class 3 over nickel. The resultant finish on cadmium plated connectors shall be olive drab (light to dark). Stainless steel in accordance with SAE-AMS-QQ-S-763 is an acceptable alternative for external screws.c. The finish of class H connectors with ferrous alloy shells and coupling rings, series II and series III class K connectors with ferrous alloy shells and coupling rings, and external screws shall be electroless nickel in accordance with ASTM-B733, class 3 or 4. A preliminary plating of another metal is permissible. Stainless steel in accordance with SAE-AMS-QQ-S-763 is an acceptable alternative for external screws.d. The finish of series I class K connectors with ferrous alloy shells and coupling rings, series II and III class KT connectors with ferrous alloy shells and coupling rings, and external screws for these classes shall be cadmium plated in accordance with SAE-AMS-QQ-P-416, type II, class 3. The resultant finish on cadmium plated connectors shall be olive drab (light to dark). Stainless steel in accordance with SAE-AMS-QQ-S-763 is an acceptable alternate plating for external screws.e. The finish of class DS connectors with corrosion-resistant steel shells and coupling rings shall be cadmium plated in accordance with SAE-AMS-QQ-P-416, type II, class 3, color - black. All other classes of connectors with corrosion-resistant steel shells and coupling rings shall be passivated.f. The finish of class HT connectors with ferrous alloy shells and coupling rings, and external screws shall be electrically conductive fused tin. Stainless steel in accordance with SAE-AMS-QQ-S-763 is an acceptable alternate plating for external screws.g. The finish of class L and U connectors with aluminum alloy shells and coupling rings, and external screws shall be electroless nickel in accordance with ASTM-B733, class 3 or 4. Stainless steel in accordance with SAE-AMS-QQ-S-763 is an acceptable alternative for externalscrews.w/AMENDMENT 1113.4 Design and construction. Connectors and accessories shall be designed and constructed to withstand handling incident to installation and maintenance in service. The connectors and accessories shall conform to the following: Crimp contact connectors, back end figure 1 configuration except MS3402, MS3412, MS3452, SAE-AS34021, and SAE-AS34121 Connector, front release, series II figures 2 and 3 interface dimensions Connector, rear release series III, and figures 4, 5, and 6 hermetic, interface dimensions Connector solder contact (pin and socket) series I figure 7 configuration Accessories to be used with series II and SAE-AS85049 series III connectors 3.4.1 Contacts. Contacts shall conform to SAE-AS39029 except as otherwise required herein for solder contact connectors. Contacts shall be designed so that neither the pin nor socket contacts are damaged during mating of counterpart connectors. The quantity of crimp contacts required for the connector plus one spare contact for connector arrangements having 26 contacts or less and two spare contacts for arrangements over 26 contacts shall be included in the unit package. No spares shall be supplied with sizes 8, 4, and 0 contacts. For other than direct shipments to the Government, crimp contact connectors are permitted to be ordered without contacts (see 6.2). 3.4.1.1 Solder contacts. Solder contacts shall conform to figure 7. 3.4.1.1.1 Mating end. The entering end of socket contacts shall be rounded or chamfered to allow for misalignment of the entering pin. The socket contacts shall provide the spring action for maintaining the contacting pressure between the pin and the socket. Size 12 and 16 socket contacts shall be designed to exclude the entrance of a pin 0.005 inch larger than the allowable maximum diameter of a mating pin. Size 16 contacts shall pass the resistance probe damage test (see 4.6.22). Use of designs for solder type pin and socket contacts sizes 0, 4, and 8 which allow contacts to be readily removable from their inserts for soldering to their conductors is permitted.w/AMENDMENT 13.4.1.1.2 Solder cups. Solder cups shall be designed so that during soldering no components are damaged and no liquid solder escapes. The solder cups shall be as indicated on figure 7. The solder cups of sizes 0, 4, and 8 shall be provided with a venthole or with other provisions to prevent trapping of air during soldering. The interior surface of solder cups for sizes 16 and 12, except thermocouple contacts, shall be completely tinned over 100 percent of the full circle portion and for at least 50 percent of the remainder of the solder well area. For sizes 0, 4, and 8 the interiors shall be completely tinned with solder conforming to J-STD-006, composition Sn60 or better commercial grade. If flux is used, flux residues and contaminants shall be completely removed without effecting the components. No excess solder shall be on the exterior of the solder cup.1213w/AMENDMENT 114Shell sizeV Thread class 2AEE DiaF Dia of any exposed portion of the grommetGG +0.000 -0.010HH ±0.005S +0.005W Min perf thread WW Min 1/ 8S .500-20 UNF 0.426/0.419 0.275/0.305 0.500 0.368 10S, 10SL .625-24 UNEF 0.562/0.555 0.380/0.405 0.625 0.502 12S, 12 .750-20 UNEF 0.679/0.672 0.516/0.549 0.750 0.618 14, 14S .875-20 UNEF 0.804/0.797 0.590/0.665 0.875 0.743 16, 16S 1.000-20 UNEF0.929/0.9220.715/0.7901.0000.8680.065 0.290 0.310 18 1.0625-18 UNEF 0.984/0.977 0.794/0.869 1.062 0.924 20 1.1875-18 UNEF 1.109/1.102 0.919/0.994 1.187 1.049 22 1.3125-18 UNEF 1.234/1.227 1.044/1.119 1.312 1.174 24 1.4375-18 UNEF 1.359/1.352 1.159/1.244 1.437 1.299 28 1.750-18 UNS 1.613/1.603 1.394/1.465 1.750 1.520 32 2.000-18 UNS 1.863/1.853 1.640/1.715 2.000 1.77036 2.250-16 UN 2.113/2.103 1.855/1.930 2.250 1.985 0.095 0.467 0.487 40 2.500-16 UN 2.363/2.353 2.070/2.145 2.500 2.200 44 2.750-16 UN 2.613/2.603 2.325/2.400 2.750 2.455 483.000-16 UN2.858/2.848 2.575/2.6503.000 2.7051/ Length to accommodate accessoriesFIGURE 1. Crimp contact connectors back end configuration except MS3402, MS3412, MS3452, SAE-AS34021 and SAE-AS34121. - Continuedw/AMENDMENT 115FIGURE 2. Connector, plug, front release, series II, interface dimensions.w/AMENDMENT 116Shell sizeA Thread class 2B B Dia+0.000 -0.062 E Dia +0.000 -0.010 1/F Dia +0.015 -0.000 1/I +0.000 -0.020J ±0.005 JJ ±0.015 8S .500-28 UNEF0.365 0.252 0.25010S .625-24 UNEF 0.414 0.440 0.323 0.320 0.570 0.501 10SL0.446 0.398 0.397 12S.750-20 UNEF0.5550.4500.44812 0.664 0.757 0.68914S.875-20 UNEF 0.414 0.675 0.526 0.525 0.570 0.50114 0.664 0.757 0.68916S1.000-20 UNEF 0.414 0.805 0.651 0.650 0.570 0.50116 18 1.125-18 UNEF 0.930 0.776 0.770 20 1.250-18 UNEF 1.050 0.932 0.925 22 1.375-18 UNEF 1.175 1.026 1.020 24 1.500-18 UNEF1.300 1.151 1.14528 1.750-18 UNS 0.664 1.520 1.370 1.365 0.757 0.689 32 2.000-18 UNS 1.770 1.620 1.615 36 2.250-16 UN 1.980 1.838 1.830 40 2.500-16 UN 2.230 2.057 2.045 44 2.750-16 UN 2.485 2.310 2.300 483.000-16 UN2.735 2.560 2.5501/ On shell size 10SL “E” dia tolerance is + 0.000, - 0.006 and “F” diameter tolerance is + 0.006, - 0.000.FIGURE 2. Connector, plug, front release, series II interface dimensions - Continued.w/AMENDMENT 117NOTES:1. Dimensions are in inches.2. For contact cavity insert interface dimensions see figure 6.FIGURE 3. Connector, receptacle, front release, series II interface dimensions.w/AMENDMENT 118Shell sizeA Thread class 2AB Min thread D Dia +0.015 -0.000I Dia +0.000 -0.020J ±0.005 JJ ±0.015P +0.010 -0.0008S .500-28 UNEF0.370 0.2500.13010S .625-24 UNEF 0.375 0.448 0.320 0.536 0.543 0.165 10SL 0.397 12.750-20 UNEF0.625 0.558 0.448 0.7240.7310.22412S 0.3750.536 0.54314 .875-20 UNEF 0.625 0.678 0.525 0.724 0.731 0.263 14S0.3750.536 0.54316 1.000-20 UNEF 0.625 0.808 0.650 0.724 0.731 0.325 16S0.3750.536 0.543 18 1.125-18 UNEF 0.933 0.770 0.385 20 1.250-18 UNEF 1.053 0.925 0.463 22 1.375-18 UNEF 1.178 1.020 0.510 24 1.500-18 UNEF1.303 1.1450.57328 1.750-18 UNS 0.625 1.523 1.365 0.724 0.731 0.683 32 2.000-18 UNS 1.773 1.615 0.808 36 2.250-16 UN 1.985 1.830 0.915 40 2.500-16 UN 2.237 2.045 1.023 44 2.750-16 UN 2.492 2.300 1.150 48 3.000-16 UN2.742 2.5501.275FIGURE 3. Connector, receptacle, front release, series II interface dimensions - Continued.w/AMENDMENT 119NOTES:1. Dimensions are in inches.2. For contact insert interface dimensions see figure 6.3. Noted dimensions apply with contact fully seated back against contact retaining device.FIGURE 4. Connector, plug, rear release, series III, interface dimensions.w/AMENDMENT 120Shell sizeA Thread class 2BB Dia +0.000 -0.062 E 1/ Dia +0.000 -0.010F 1/ Dia +0.015 -0.000I Dia +0.000 -0.020J ±0.005JJ ±0.011 8S .500-28 UNEF 0.365 0.252 0.25010S .625-24 UNEF 0.414 0.4400.323 0.320 0.570 0.51010SL 0.446 0.398 0.397 12S.750-20 UNEF0.555 0.450 0.448120.6640.757 0.69814S .875-20 UNEF 0.414 0.675 0.526 0.525 0.570 0.510 140.6640.757 0.69816S 1.000-20 UNEF 0.414 0.805 0.651 0.650 0.570 0.501 1618 1.125-18 UNEF 0.930 0.776 0.770 20 1.250-18 UNEF 1.050 0.932 0.925 22 1.375-18 UNEF 1.175 1.026 1.020 24 1.500-18 UNEF 1.300 1.151 1.14528 1.750-18 UNS 0.664 1.5201.370 1.365 0.757 0.69832 2.000-18 UNS 1.770 1.620 1.615 36 2.250-16 UN 1.980 1.838 1.830 40 2.500-16 UN 2.230 2.057 2.045 44 2.750-16 UN 2.485 2.310 2.30048 3.000-16 UN 2.735 2.560 2.5501/ On shell size 10SL “E” dia tolerance is + 0.000, - 0.006 and “F” diameter tolerance is + 0.006, -0.000.FIGURE 4. Connector, plug, rear release, series III interface dimensions - Continued.。
IRF5210S中文资料

IRF5210S中文资料IRF5210S/LHEXFET ? Power MOSFETPD - 91405ClAdvanced Process Technology l Surface Mount (IRF5210S) l Low-profile through-hole (IRF5210L)l 175°C Operating Temperature l Fast Switching l P-Channell Fully Avalanche Rated5/13/98Absolute Maximum RatingsFifth Generation HEXFETs from International Rectifier utilize advanced processing techniques to achieve extremely low on-resistance per silicon area. This benefit, combined with the fast switching speed and ruggedized device design that HEXFET Power MOSFETs are well known for, provides the designer with an extremely efficient and reliable device for use in a wide varietyof applications.The D 2Pak is a surface mount power package capable of accommodating die sizes up to HEX-4. It provides the highest power capability and the lowest possible on-resistance in any existing surface mount package. The D 2Pak is suitable for high current applications because of its low internal connection resistance and can dissipate up to 2.0W in a typical surface mount application.The through-hole version (IRF5210L) is available for low-profile applications.Description2 D PakT O -262ParameterTyp.Max.UnitsR θJC Junction-to-Case–––0.75R θJAJunction-to-Ambient ( PCB Mounted,steady-state)**–––40Thermal Resistance°C/WParameterMax.UnitsI D @ T C = 25°C Continuous Drain Current, V GS @ -10V -40I D @ T C = 100°C Continuous Drain Current, V GS @ -10V -29A I DMPulsed Drain Current -140P D @T A = 25°C Power Dissipation 3.8W P D @T C = 25°C Power Dissipation 200W Linear Derating Factor 1.3W/°C V GS Gate-to-Source Voltage± 20V E AS Single Pulse Avalanche Energy 780mJ I AR Avalanche Current-21A E AR Repetitive Avalanche Energy 20mJ dv/dt Peak Diode Recovery dv/dt -5.0V/ns T J Operating Junction and-55 to + 175T STGStorage Temperature RangeSoldering Temperature, for 10 seconds300 (1.6mm from case )°CIRF5210S/LIRF5210S/LIRF5210S/LIRF5210S/LIRF5210S/LIRF5210S/LIRF5210S/LIRF5210S/LIRF5210S/L。
PTH08T210W资料

FEATURESAPPLICATIONSDESCRIPTIONPTH08T210WSLTS262D–OCTOBER2005–REVISED OCTOBER200630-A,5.5-V to14-V INPUT,NON-ISOLATED,WIDE OUTPUT ADJUST,POWER MODULE w/TurboTrans™•Up to30-A Output Current•TurboTrans™Technology• 5.5-V to14-V Input Voltage•Designed to meet Ultra-Fast TransientRequirements up to300A/µs•Wide-Output Voltage Adjust(0.7V to3.6V)•Auto-Track™Sequencing•Efficiencies up to96%•Multi-Phase,Switch-Mode Topology•±1.5%Total Output Voltage Variation•On/Off Inhibit•Differential Output Voltage Remote Sense•Complex Multi-Voltage Systems •Adjustable Undervoltage Lockout•Microprocessors•Output Overcurrent Protection•Bus Drivers(Nonlatching,Auto-Reset)•Operating Temperature:–40°C to85°C•Safety Agency Approvals:(Pending)–UL1950,CSA22.2950,EN60950VDEThe PTH08T210W is a high-performance30-A rated,non-isolated power module which utilizes a multi-phase, switch-mode topology.This module represents the2nd generation of the PTH series power modules which include a reduced footprint and improved features.Operating from an input voltage range of5.5V to14V,the PTH08T210W requires a single resistor to set the output voltage to any value over the range,0.7V to 3.6V.The wide input voltage range makes the PTH08T210W particularly suitable for advanced computing and server applications that uses a loosely regulated 8-V to12-V intermediate distribution bus.The module uses double-sided surface mount construction to provide a low profile and compact footprint.Package options include both through-hole and surface mount configurations that are lead(Pb)–free and RoHS compatible.A new feature included in this2nd generation of PTH and PTV modules is TurboTrans™technology(patent pending).TurboTrans allows the transient response of the regulator to be optimized externally,resulting in a reduction of output voltage deviation following a load transient and a reduction in required output capacitance. This feature also offers enhanced stability when used with ultra-low ESR output capacitors.The PTH08T210W incorporates a comprehensive list of standard features.They include on/off inhibit,a differential remote output voltage sense which ensures tight load regulation,and an output overcurrent and overtemperature shutdown to protect against load faults.A programmable undervoltage lockout allows the turn-on voltage threshold to be customized.AutoTrack™sequencing is a feature which simplifies the simultaneous power-up and power-down of multiple modules in a power system by allowing the outputs to track a common voltage.Please be aware that an important notice concerning availability,standard warranty,and use in critical applications of TexasInstruments semiconductor products and disclaimers thereto appears at the end of this data sheet.TurboTrans,AutoTrack,TMS320are trademarks of Texas Instruments.PRODUCTION DATA information is current as of publication date.Copyright©2005–2006,Texas Instruments Incorporated Products conform to specifications per the terms of the TexasInstruments standard warranty.Production processing does notnecessarily include testing of all parameters.UDG−05097 PTH08T210WSLTS262D–OCTOBER2005–REVISED OCTOBER2006These devices have limited built-in ESD protection.The leads should be shorted together or the device placed in conductive foam during storage or handling to prevent electrostatic damage to the MOS gates.A.R SET is required to set the output voltage higher than0.7V.See the Electrical Characteristics table.ORDERING INFORMATIONFor the most current package and ordering information,see the Package Option Addendum at the end of this datasheet,or see the TI website at .2Submit Documentation FeedbackDATASHEET TABLE OF CONTENTS ENVIRONMENTAL AND ABSOLUTE MAXIMUM RATINGS PTH08T210WSLTS262D–OCTOBER2005–REVISED OCTOBER2006DATASHEET SECTION PAGE NUMBER ENVIRONMENTAL AND ABSOLUTE MAXIMUM RATINGS3ELECTRICAL CHARACTERISTICS TABLE(PTH08T210W)4TERMINAL FUNCTIONS6TYPICAL CHARACTERISTICS(V I=12V)7TYPICAL CHARACTERISTICS(V I=8V)8INPUT&OUTPUT CAPACITOR RECOMMENDATIONS9TURBOTRANS™INFORMATION13ADJUSTING THE OUTPUT VOLTAGE18 UNDERVOLTAGE LOCKOUT(UVLO)20SOFT-START POWER-UP21REMOTE SENSE21OUTPUT INHIBIT22OVER-CURRENT PROTECTION22OVER-TEMPERATURE PROTECTION23AUTO-TRACK SEQUENCING23TAPE&REEL AND TRAY DRAWINGS26(Voltages are with respect to GND)UNIT UNIT Signal input voltage Track control(pin14)–0.3to V I+0.3VT A Operating temperature range Over V I range–40to85Surface temperature of module body or pinsT wave Wave soldering temperature PTH08T210WAD260(20seconds)°CPTH08T210WAS235(1)Surface temperature of module body or pinsT reflow Solder reflow temperature(20seconds)PTH08T210WAZ260(1)T stg Storage temperature–40to125(2) Mechanical shock Per Mil-STD-883D,Method2002.31msec,½sine,mounted250G Mechanical vibration Mil-STD-883D,Method2007.220-2000Hz15Weight8.5grams Flammability Meets UL94V-O(1)During reflow of surface mount package version do not elevate peak temperature of the module,pins or internal components above thestated maximum.(2)The shipping tray or tape&reel cannot be used to bake parts at temperatures higher than65°C.3Submit Documentation FeedbackELECTRICAL CHARACTERISTICSPTH08T210WSLTS262D–OCTOBER 2005–REVISED OCTOBER 2006T A =25°C,V I =12V,V O =3.3V,C I =470µF,C O =470µF OS-CON,and I O =I O max (unless otherwise stated)PARAMETERTEST CONDITIONSMIN TYP MAX UNIT 25°C,natural convection025I O Output current A 60°C,200LFM030V IInput voltage range Over I O range 5.514V Output adjust range Over I O range0.73.6V Set-point voltage tolerance±1(1)%V o Temperature variation –40°C <T A <85°C ±0.3%V o V OLine regulation Over V I range ±4mV Load regulation Over I O range±7mVTotal output variationIncludes set-point,line,load,–40°C ≤T A ≤85°C±1.5(1)%V oR SET =1.62k Ω,V O =3.3V 93%R SET =5.23k Ω,V O =2.5V 91%R SET =12.7k Ω,V O =1.8V89%ηEfficiencyI O =26AR SET =19.6k Ω,V O =1.5V 89%R SET =35.7k Ω,V O =1.2V 87%R SET =63.4k Ω,V O =1.0V84%Open,V O =0.7V80%V O Ripple (peak-to-peak)20-MHz bandwidth25mV PP I LIM Overcurrent thresholdReset,followed by auto-recovery55A t tr w/o TurboTrans Recovery time 50µs C O =470 µF∆V tr V O over/undershoot150mV t tr w/o TurboTransRecovery time 50µs 2.5A/µs load step Transient responseC O =940 µF,Type C 50to 100%I O max∆V tr V O over/undershoot125mV t trTT w/TurboTransRecovery time 50µs C O =940 µF,Type C∆V trTT V O over/undershoot85mV I ILTrack input current (pin 14)Pin to GND –130(2)µA dV track /dt Track slew rate capability C O ≤C O (max)1V/ms V I increasing 5 5.5Adjustable Undervoltage UVLO ADJPin 1openV lockout (pin 1)V I decreasing4.1Input high voltage (V IH )Open (3)V Inhibit control (pin 1)Input low voltage (V IL )-0.20.6Input low current (I IL )125µA I in Input standby current Inhibit (pin 1)to GND,Track (pin 14)open 3mA f s Switching frequency Over V I and I O ranges480kHz C IExternal input capacitance470(4)µF(1)The set-point voltage tolerance is affected by the tolerance and stability of R SET .The stated limit is unconditionally met if R SET has a tolerance of 1%with 100ppm/°C or better temperature stability.(2)A low-leakage (<100nA),open-drain device,such as MOSFET or voltage supervisor IC,is recommended to control pin 14.The open-circuit voltage is less than 5Vdc.(3)This control pin has an internal pullup.If it is left open-circuit,the module operates when input power is applied.A small,low-leakage (<100nA)MOSFET is recommended for control.The open-circuit voltage is less than 5Vdc.For additional information,see the related application note.(4)A 470µF electrolytic input capacitor is required for proper operation.The capacitor must be rated for a minimum of 500mA rms of ripple current.4Submit Documentation FeedbackPTH08T210W SLTS262D–OCTOBER2005–REVISED OCTOBER2006ELECTRICAL CHARACTERISTICS(continued)T A=25°C,V I=12V,V O=3.3V,C I=470µF,C O=470µF OS-CON,and I O=I O max(unless otherwise stated) PARAMETER TEST CONDITIONS MIN TYP MAX UNIT12,000Nonceramic470(5)Capacitance(6)µFValuew/out TurboTransCeramic5000External output Equivalent series resistance(nonceramic)3(7)mΩC OcapacitanceSee TT12,000Capacitance ValueµFchart(8)(9)w/TurboTrans10,000Capacitance×ESR product(C O×ESR)µF×mΩ(10)MTBF Reliability Per Bellcore TR-332,50%stress,T A=40°C,ground benign 3.6106Hr(5)A minimum value of external output capacitor is required for proper operation.Adding additional capacitance at the load further improvestransient response.See the Capacitor Application Information section for more guidance.(6)This is the calculated maximum.This value includes both ceramic and non-ceramic capacitors.The minimum ESR requirement oftenresults in a lower value.See the related Application Information for more guidance.(7)This is the minimum ESR for all the electrolytic(nonceramic)e5mΩas the minimum when using manufacturer'smax-ESR values to calculate.(8)Minimum capacitance will be determined by your transient deviation requirement.A corresponding resistor,R TT is required for properoperation.See the TurboTrans Selection section for guidance in selecting the capacitance and R TT value.(9)This is the calculated maximum.This value includes both ceramic and non-ceramic capacitors.(10)When calculating the Capacitance×ESR product use the capacitance and ESR values of a single capacitor.For an output capacitorbank of several capacitor types and values,calculate the C×ESR product using the values of the capacitor that makes up the majority of the capacitance.5Submit Documentation Feedback1131211432145678910PTH08T210WSLTS262D–OCTOBER 2005–REVISED OCTOBER 2006PTH08T210W (TOP VIEW)TERMINAL FUNCTIONSTERMINAL DESCRIPTIONNAME NO.V I 2,6The positive input voltage power node to the module,which is referenced to common GND.V O 5,9The regulated positive power output with respect to the GND.3,4This is the common ground connection for the V I and V O power connections.It is also the 0V dc reference for GND7,8the control inputs.The Inhibit pin is an open-collector/drain,negative logic input that is referenced to GND.Applying a low level ground signal to this input disables the module’s output and turns off the output voltage.When the Inhibit control is active,the input current drawn by the regulator is significantly reduced.If the Inhibit pin is left open-circuit,the module produces an output whenever a valid input source is applied.This input is not compatible with TTL logic Inhibit (1)/1devices and should not be tied to V I or any other voltage.UVLO adjustThis pin is also used for input undervoltage lockout (UVLO)programming.Connecting a resistor from this pin to GND (pin 3)allows the ON threshold of the UVLO to be adjusted higher than the default value.For more information,see the Application Information section.A 0.1W 1%resistor must be directly connected between this pin and pin 8(GND)to set the output voltage to a value higher than 0.7V.The temperature stability of the resistor should be 100ppm/°C (or better).The setpoint V o Adjust12range for the output voltage is from 0.7V to 3.6V.If left open circuit,the output voltage will default to its lowest value.For further information,on output voltage adjustment see the related application note.The specification table gives the preferred resistor values for a number of standard output voltages.The sense input allows the regulation circuit to compensate for voltage drop between the module and the load.+Sense 10For optimal voltage accuracy,+Sense must be connected to V O ,very close to the load.The sense input allows the regulation circuit to compensate for voltage drop between the module and the load.–Sense11For optimal voltage accuracy,–Sense must be connected to GND (pin 8),very close to the load.This is an analog control input that enables the output voltage to follow an external voltage.This pin becomes active typically 20ms after the input voltage has been applied,and allows direct control of the output voltage from 0V up to the nominal set-point voltage.Within this range the module's output voltage follows the voltage at the Track pin on a volt-for-volt basis.When the control voltage is raised above this range,the module regulates Track 14at its set-point voltage.The feature allows the output voltage to rise simultaneously with other modules powered from the same input bus.If unused,this input should be connected to V I .NOTE:Due to the undervoltage lockout feature,the output of the module cannot follow its own input voltage during power up.For more information,see the related application note.This input pin adjusts the transient response of the regulator.To activate the TurboTrans™feature,a 1%,50mW resistor must be connected between this pin and pin 10(+Sense)very close to the module.For a given value of output capacitance,a reduction in peak output voltage deviation is achieved by using this feature.If TurboTrans™13unused,this pin must be left open-circuit.External capacitance must never be connected to this pin.The resistance requirement can be selected from the TurboTrans™resistor table in the Application Information section.(1)Denotes negative logic:Open =Normal operation,Ground =Function active6Submit Documentation FeedbackTYPICAL CHARACTERISTICS (1)(2)CHARACTERISTIC DATA (V I =12V)I O − Output Current − A− P o w e r D i s s i p a t i o n − WP DE f f i c i e n c y − %I O− Output Current − AI O − Output Current − AV O − O u t p u t V o l t a g e R i p p l e −V P P m VT A −A m b i e n t T e m p e r a t u r e −Co I O −Output Current −AT A −A m b i e n t T e m p e r a t u r e −Co I O −Output Current −A PTH08T210WSLTS262D–OCTOBER 2005–REVISED OCTOBER 2006EFFICIENCYOUTPUT RIPPLEPOWER DISSIPATIONvsvsvsLOAD CURRENTLOAD CURRENTLOAD CURRENTFigure 1.Figure 2.Figure 3.AMBIENT CURRENTAMBIENT TEMPERATUREvsvsOUTPUT CURRENTOUTPUT CURRENTFigure 4.Figure 5.(1)The electrical characteristic data has been developed from actual products tested at 25°C.This data is considered typical for the converter.Applies to Figure 1,Figure 2,and Figure 3.(2)The temperature at which internal components are at or below the manufacturer's maximum operating temperatures.Derating limits apply to modules soldered directly to a 100mm ×100mm double-sided PCB with 2oz.copper.Applies to Figure 5and Figure 4.7Submit Documentation FeedbackTYPICAL CHARACTERISTICS (1)(2)CHARACTERISTIC DATA (V I =8V)I O − Output Current − AV O − O u t p u t V o l t a g e R i p p l e −V P P m VI O − Output Current − A− P o w e r D i s s i p a t i o n − WPD E f f i c i e n c y − %I O − Output Current − AT A −A m b i e n t T e m p e r a t u r e −Co I O −Output Current −AT A −A m b i e n t T e m p e r a t u r e −Co I O −Output Current −APTH08T210WSLTS262D–OCTOBER 2005–REVISED OCTOBER 2006EFFICIENCYOUTPUT RIPPLEPOWER DISSIPATIONvsvsvsLOAD CURRENTLOAD CURRENTLOAD CURRENTFigure 6.Figure 7.Figure 8.AMBIENT TEMPERATUREAMBIENT TEMPERATUREvsvsOUTPUT CURRENTOUTPUT CURRENTFigure 9.Figure 10.(1)The electrical characteristic data has been developed from actual products tested at 25°C.This data is considered typical for the converter.Applies to Figure 6,Figure 7,and Figure 8.(2)The temperature at which internal components are at or below the manufacturer's maximum operating temperatures.Derating limits apply to modules soldered directly to a 100mm ×100mm double-sided PCB with 2oz.copper.Applies to Figure 9and Figure 10.8Submit Documentation FeedbackAPPLICATION INFORMATION CAPACITOR RECOMMENDATIONS FOR THE PTH08T210W POWER MODULE Input Capacitor(Required)TurboTrans Output CapacitorNon-TurboTrans Output Capacitor PTH08T210WSLTS262D–OCTOBER2005–REVISED OCTOBER2006 The size and value of the input capacitor is determined by the converter’s transient performance capability.Theminimum amount of required input capacitance is470µF,with an RMS ripple current rating of500mA.This minimum value assumes that the converter is supplied with a responsive,low inductance input source.This source should have ample capacitive decoupling,and be distributed to the converter via PCB power and groundplanes.For high-performance/transient applications,or wherever the input source performance is degraded,1000µF of input capacitance is recommended.The additional input capacitance above the minimum level insures an optimized performance.Ripple current(rms)rating,less than100mΩof equivalent series resistance(ESR),and temperature are the main considerations when selecting input capacitors.The ripple current reflected from the input of the PTH08T210W module is moderate to low.Therefore any good quality,computer-grade electrolytic capacitor will have an adequate ripple current rating.Regular tantalum capacitors are not recommended for the input bus.These capacitors require a recommended minimum voltage rating of2×(maximum dc voltage+ac ripple).This is standard practice to ensure reliability. No tantalum capacitors were found with a sufficient voltage rating to meet this requirement.When the operating temperature is below0°C,the ESR of aluminum electrolytic capacitors increases.For these applications, Os-Con,poly-aluminum,and polymer-tantalum types should be considered.Adding one or two ceramic capacitors to the input attenuates high-frequency reflected ripple current.The PTH08T210W requires a minimum output capacitance of470µF.The required capacitance above470µF will be determined by actual transient deviation requirements.TurboTrans allows the designer to optimize the capacitance load according to the system transient design requirement.High quality,ultra-low ESR capacitors are required to maximize TurboTrans effectiveness. Capacitors with a capacitance(µF)×ESR(mΩ)product of≤ 10,000 mΩ×µF are required.Working Example:A bank of6identical capacitors,each with a capacitance of680 µF and5 mΩ ESR,has a C × ESR product of 3400 µFxmΩ(680 µF×5 mΩ).Using TurboTrans in conjunction with the high quality capacitors(capacitance(µF)×ESR(mΩ))reduces the overall capacitance requirement while meeting the minimum transient amplitude level.Table1includes a preferred list of capacitors by type and vendor.See the Output Bus/TurboTrans column. Note:See the TurboTrans Technology Application Notes within this document for selection of specific capacitance.The PTH08T210W requires a minimum output capacitance of470 µF.Non-TurboTrans applications must observe minimum output capacitance ESR limits.A combination of200 µF of ceramic capacitors plus low ESR(15 mΩto30 mΩ)Os-Con electrolytic/tantalum type capacitors can be used.When using Polymer tantalum types,tantalum type,or Oscon types only,the capacitor ESR bank limit is3 mΩto5 mΩ.(Note:no ceramic capacitors are required).This is necessary for the stable operation of the regulator.Additional capacitance can be added to improve the module's performance to load transients.High quality computer-grade electrolytic capacitors are recommended.Aluminum electrolytic capacitors provide adequate decoupling over the frequency range,2kHz to150kHz,and are suitable when ambient temperatures are above-20°C.For operation below-20°C,tantalum,ceramic,or Os-Con type capacitors are necessary.9Submit Documentation FeedbackCeramic CapacitorsTantalum,Polymer-Tantalum CapacitorsCapacitor TableDesigning for Fast Load TransientsPTH08T210WSLTS262D–OCTOBER 2005–REVISED OCTOBER 2006APPLICATION INFORMATION (continued)When using a combination of one or more non-ceramic capacitors,the calculated equivalent ESR should be no lower than 2 m Ω(4 m Ωwhen calculating using the manufacturer’s maximum ESR values).A list of preferred low-ESR type capacitors,are identified in Table 1.Above 150kHz the performance of aluminum electrolytic capacitors is less effective.Multilayer ceramic capacitors have very low ESR and a resonant frequency higher than the bandwidth of the regulator.They can be used to reduce the reflected ripple current at the input as well as improve the transient response of the output.When used on the output their combined ESR is not critical as long as the total value of ceramic capacitors,with values between 10µF and 100µF,does not exceed 5000µF (non-TurboTrans).In TurboTrans applications,when ceramic capacitors are used on the output bus,total capacitance including bulk and ceramic types is not to exceed 12,000µF.Tantalum type capacitors are only used on the output bus,and are recommended for applications where the ambient operating temperature is less than 0°C.The AVX TPS series and Kemet capacitor series are suggested over many other tantalum types due to their higher rated surge,power dissipation,and ripple current capability.As a caution,many general-purpose tantalum capacitors have higher ESR,reduced power dissipation,and lower ripple current capability.These capacitors are also less reliable due to their reduced power dissipation and surge current ratings.Tantalum capacitors that have no stated ESR or surge current rating are not recommended for power applications.Table 1identifies the characteristics of capacitors from a number of vendors with acceptable ESR and ripple ratings.The recommended number of capacitors required at both the input and output buses is identified for each capacitor type.This is not an extensive capacitor list.Capacitors from other vendors are available with comparable specifications.Those listed are for guidance.The RMS ripple current rating and ESR (at 100kHz)are critical parameters necessary to ensure both optimum regulator performance and long capacitor life.The transient response of the dc/dc converter has been characterized using a load transient with a di/dt of 2.5 A/µs.The typical voltage deviation for this load transient is given in the Electrical Characteristics table using the minimum required value of output capacitance.As the di/dt of a transient is increased,the response of a converter’s regulation circuit ultimately depends on its output capacitor decoupling network.This is an inherent limitation with any dc/dc converter once the speed of the transient exceeds its bandwidth capability.If the target application specifies a higher di/dt or lower voltage deviation,the requirement can only be met with additional low ESR ceramic capacitor decoupling.Generally,with 50%load steps at >100 A/µs,adding multiple 10 µF ceramic capacitors,3225case size,plus 10 × 1 µF,including numerous high frequency ceramics (≤ 0.1 µF)are all that is required to soften the transient higher frequency edges.Special attention is essential with regards to location,types,and position of higher frequency ceramic and lower ESR bulk capacitors.DSP,FPGA and ASIC vendors identify types,location and capacitance required for optimum performance of the high frequency devices.The details regarding the PCB layout and capacitor/component placement are important at these high frequencies.Low impedance buses and unbroken PCB copper planes with components located as close to the high frequency processor are essential for optimizing transient performance.In many instances additional capacitors may be required to insure and minimize transient aberrations.10Submit Documentation FeedbackTable1.Input/Output Capacitors(1)Capacitor Characteristics QuantityMax Output BusMax.Capacitor Vendor,RippleWorking Value ESR Physical InputType Series(Style)TurboTransCurrent at Vendor Part No.NoVoltage(µF)at100Size(mm)Bus(Cap85°C TurboTranskHz Type)(2)(Irms)Panasonic25V10000.043Ω>1690mA16×151≥2(3)N/R(4)EEUFC1E102SFC(Radial)25V18000.029Ω2205mA16×201≥1(3)N/R(4)EEUFC1E182FC(SMD)25V22000.028Ω>2490mA18×21,51≥1(3)N/R(4)EEVFC1E222NFK(SMD)25V10000.060Ω1100mA12,5×13,51≥2(5)N/R(4)EEVFK1V102QUnited Chemi-ConPTB(SMD)Polymer 6.3V4700.025Ω2600mA7,3x4,3x N/R(6)≥2~≤4(3)C≥2(2)6PTB477MD8TERTantalum 2.8LXZ,Aluminum(Radial)25V6800.068Ω1050mA10×161≥1~≤3(3)N/R(4)LXZ25VB681M10X20LLPS,16V3300.014Ω5060mA10×12,52≥2~≤3B≥2(2)16PS330MJ12Poly-Aluminum(Radial)PXA,Poly-Aluminum16V3300.014Ω5050mA10×12,22≥2~≤3B≥2(2)PXA16VC331MJ12TP(SMD)PS, 6.3V6800.010Ω5500mA10×12,5N/R(6)≥1~≤2C≥1(2)6PS680MJ12Poly-Aluminum(Radial)PXA, 6.3V4700.012Ω4770mA8×12,2N/R(6)≥1~≤2C≥1(2)PXA6.3VC471MH12TPPoly-Aluminum(Radial)Nichicon,Aluminum25V4700.070Ω985mA12,5×151≥2(3)N/R(4)UPM1E471MHH6HD(Radial)25V4700.038Ω1430mA10×161≥2(3)N/R(4)UHD1E471MHRPM(Radial)35V5600.048Ω1360mA16×151≥2(3)N/R(4)UPM1V561MHH6Panasonic,7,3L×4,3Poly-Aluminum: 2.0V3900.005Ω4000mA W×4,2H N/R(6)N/R(6)B≥2(2)EEFSE0J391R(V O≤1.6V)(7) (1)Capacitor Supplier VerificationPlease verify availability of capacitors identified in this table.Capacitor suppliers may recommend alternative part numbers because of limited availability or obsolete products.In some instances,the capacitor product life cycle may be in decline and have short-term consideration for obsolescence.RoHS,Lead-free and Material DetailsSee the capacitor suppliers regarding material composition,RoHS status,lead-free status,and manufacturing process requirements.Component designators or part number deviations can occur when material composition or soldering requirements are updated.(2)Required capacitors with TurboTrans.See the TransTrans Application information for Capacitor SelectionCapacitor Type Groups by ESR(Equivalent Series Resistance):•Type A=(100<capacitance×ESR≤1000)•Type B=(1,000<capacitance×ESR≤5,000)•Type C=(5,001<capacitance×ESR≤10,000)(3)Total bulk nonceramic capacitors on the output bus with ESR of≥15mΩto≤30mΩrequires an additional≥200µF of ceramiccapacitor.(4)Aluminum Electrolytic capacitor not recommended for the TurboTrans due to higher ESR×capacitance products.Aluminum and higherESR capacitors can be used in conjunction with lower ESR capacitance.(5)Output bulk capacitor's maximum ESR is≥30mΩ.Additional ceramic capacitance of≥200µF is required.(6)N/R–Not recommended.The voltage rating does not meet the minimum operating limits.(7)The voltage rating of this capacitor only allows it to be used for output voltage that is equal to or less than80%of the working voltage.Table1.Input/Output Capacitors(continued)Capacitor Characteristics QuantityMax Output BusMax.Capacitor Vendor,RippleWorking Value ESR Physical InputType Series(Style)TurboTransCurrent at Vendor Part No.NoVoltage(µF)at100Size(mm)Bus(Cap85°C TurboTranskHz Type)(2)(Irms)SanyoTPE,Poscap(SMD) 6.3V4700.018Ω3500mA7,3×4,3N/R(8)≥1~≤3C≥1(9)6TPE470MITPE Poscap(SMD) 2.5V4700.007Ω4400mA7,3×4,3N/R(8)≥1≤2B≥2(9)2R5TPE470M7(V O≤1.8V)(10) TPD Poscap(SMD) 2.5V10000.005Ω6100mA7,3×4,3N/R(8)≤1B≥1(9)2R5TPD1000M5(V O≤1.8V)(10) SA,Os-Con(Radial)16V4700.020Ω>6080mA16×231≥1~≤4N/R(11)16SA470MSP Oscon(Radial)10V4700.015>4500mA10×11,5N/R(8)≥1~≤3C≥2(9)10SP470MSEPC,Os-Con(Radial)16V4700.010Ω>4700mA10×131≥1~≤2B≥1(9)16SEPC470MSVPA,Os-Con(SMD) 6.3V4700.020Ω4700mA10×10,3N/R(8)≥1~≤4(12)C≥1(9)(12)6SVPA470MAVX,Tantalum,Series III 6.3V6800.035Ω>2400mA7,3L N/R(8)≥2~≤7(12)N/R(11)TPSE477M010R0045TPM Multianode 6.3V4700.018Ω>3800mA×4,3W N/R(8)≥2~≤3(12)C≥2(9)(12)TPME687M006#0018×4,1HTPS Series III(SMD)4V10000.035Ω24057,3L×5,7N/R(8)≥2~≤7(12)N/R(11)TPSV108K004R0035W(V O≤2.2V)(10)Kemet,Poly-Tantalum 6.3V4700.018Ω2700mA4,3W N/R(8)≥1~≤3(12)C≥2(9)T520X477M06ASE018T520(SMD) 6.3V4700.010Ω>5200mA×7,3L N/R(8)≥1~≤2B≥1(9)T530X477M006ASE010T530(SMD) 6.3V4700.005Ω7300mA×4H N/R(8)≤1B≥1(9)T530X477M006ASE005T530(SMD) 2.5V10000.005Ω7300mA4,3w×N/R(8)≤1B≥1(9)T530X108M2R5ASE0057,3L(V O≤2.0V)(10)Vishay-Sprague594D,Tantalum(SMD) 6.3V10000.030Ω2890mA7,2L×5,7N/R(8)≥1~≤6N/R(11)594D108X06R3R2TR2TW×4,1H94SA,Os-con(Radial)16V10000.015Ω9740mA16×251≥1~≤3N/R(11)94SA108X0016HBP94SVP Os-Con(SMD)16V3300.017Ω>4500mA10×12,72≥2~≤3C≥1(9)94SVP827X06R3F12Kemet,Ceramic X5R16V100.002Ω–32251≥1(13)A(9)C1210C106M4PAC(SMD)6.3V470.002ΩN/R(8)≥1(13)A(9)C1210C476K9PACMurata,Ceramic X5R 6.3V1000.002Ω–3225N/R(8)≥1(13)A(9)GRM32ER60J107M(SMD)6.3V47N/R(8)≥1(13)A(9)GRM32ER60J476M25V221≥1(13)A(9)GRM32ER61E226K16V101≥1(13)A(9)GRM32DR61C106KTDK,Ceramic X5R(SMD) 6.3V1000.002Ω–3225N/R(8)≥1(13)A(9)C3225X5R0J107MT6.3V47N/R(8)≥1(13)A(9)C3225X5R0J476MT16V101≥1(13)A(9)C3225X5R1C106MT016V221≥1(13)A(9)C3225X5R1C226MT(8)N/R–Not recommended.The voltage rating does not meet the minimum operating limits.(9)Required capacitors with TurboTrans.See the TransTrans Application information for Capacitor SelectionCapacitor Type Groups by ESR(Equivalent Series Resistance):•Type A=(100<capacitance×ESR≤1000)•Type B=(1,000<capacitance×ESR≤5,000)•Type C=(5,001<capacitance×ESR≤10,000)(10)The voltage rating of this capacitor only allows it to be used for output voltage that is equal to or less than80%of the working voltage.(11)Aluminum Electrolytic capacitor not recommended for the TurboTrans due to higher ESR×capacitance products.Aluminum and higherESR capacitors can be used in conjunction with lower ESR capacitance.(12)Total bulk nonceramic capacitors on the output bus with ESR of≥15mΩto≤30mΩrequires an additional≥200µF of ceramiccapacitor.(13)Maximum ceramic capacitance on the output bus is≤3000µF.Any combination of the ceramic capacitor values is limited to3000µFfor non-TurboTrans applications.The total capacitance is limited to14,000µF which includes all ceramic and non-ceramic types.。
北京斯达峰控制技术有限公司SF-5210S-QG数控切割机系统说明书

使用系统前请认真阅读本手册使用注意事项:1.包装箱打开后,请检查系统在运输过程中有无破损,装箱单上所列内容与箱内物品是否符合。
2.本说明书适用于北京斯达峰控制技术有限公司生产的SF-5210S-QG数控切割机系统。
3.请检查电网电压是否正确。
在电网与系统之间要使用AC220V的隔离变压器,以确保系统可靠工作和人员的安全。
4.数控系统要求工作环境温度为 0℃~ +40℃,相对湿度为0~85% 。
如在高温、高湿和有腐蚀性气体的环境下工作,需要采取特殊的防护。
5.数控系统各部分接线要按要求正确连接,地线接触良好。
6.数控系统不允许带电插拔机箱后部的所有电缆插头,由此产生的后果,本公司拒绝保修。
7.数控系统后部输出端口的线,不允许和其他电源线短路,否则将烧毁数控。
8.在高粉尘环境下,整机需要做粉尘防护,并且需要定期清理灰尘,尽量保证数控系统的清洁。
9.数控系统应由专人管理,对操作人员应进行相关培训。
10.不允许将数控系统内部使用的交流/直流电源连接到其它外部电器上。
11.如遇问题,请与本公司联系。
切勿在不熟悉的情况下自行拆装、改造系统。
12.维护系统和机床,每班执行一次日常维护和检查;每月执行一次二级维护;每六个月执行一次一级维护。
13.数控系统设置的各项参数,要严格按照本说明书或订货时的补充说明的进行设置;如设置的参数超出规定范围,可能会使数控系统工作不正常,甚至损坏。
14.系统的液晶屏为易碎物品,使用过程中注意对液晶进行防护。
15.本系统技术指标如有变更,恕不另行通知。
16.注意:系统的USB口输出功率很小,只能供U盘使用,不能接其他的USB设备,以防损坏。
17.特殊声明:本产品的保修期、保修范围为自出厂之日起十二个月内,按使用说明允许的情况下所发生的故障。
保修期外和保修范围以外发生故障的处理为收费服务。
以下情况不在保修范围内:A:违反使用要求的人为损坏;B:不可抗力导致的损坏;不可抗力通常包括两种情况:一种:是自然原因引起的,如雷击、水灾、旱灾、暴风雪、地震等;另一种:是社会原因引起的,如战争、罢工、政府禁令等;C:未经许可,擅自拆卸、改装、修理等行为导致的损坏。
烽火设备基础资料

780BNMU单盘硬件
面板指示灯含义
指示灯 ACT
UA/NUA NET SBUS MBUS
DCC指示灯
指示灯状态
备注
长亮但不闪烁表示 NMU盘未得到正确的配置 或时间;正常工作时,均 匀闪烁。
★ MBS1 MBUS1口通讯状态指示.闪动表示该口收到数据,本设备对外有6个MBUS1
口并联使用,可将其它功能模块(框、架)纳入到本设备进行管理
★ MBS2 MBUS2口通讯状态指示 闪动表示该口收到数据
★ DCCw 西DCC接收指示
闪动表示该口收到数据
★ DCCe 东DCC接收指示
闪动表示该口收到数据
6 6 611 3 3 322
EEEEEE 111111 ︱︱︱︱︱︱
666666 333333
123
456789
00 01 02 03 04 05 06 0 0 09 0 0 0 0 0 0F
11
78
ABCDE
风扇及分纤单元
OO
TTAAO 0
OO
25 25
U U U U 15 15
25 25
00 00
★ SBUS BCT应答指示 均匀闪动表示BCT与EMU通讯正常,不闪动表示
EMU未收到BCT应答,闪动频度不均匀表示可能有BCT通讯不好
★ NET F口数据指示灯 该灯以一定的频率闪动表示F口有数据收发
★ DCC0~3 从CPU串行口1~4指示灯 闪动表示该口收到数据
GF155-03BEMU单盘说明
❖ 可对某站点的光/电分支设备进行管理,;
TS08 应用概述

Summarize for TS08 applicationRecommended final depth (thickness) of Dielectric : under 6 mm for PMMA推荐的最终绝缘介质层(面板)的厚度:PMMA 6MM以下。
For non-direct type application, choice of Dielectric material is important.对于非直接接触式的应用来说,绝缘介质材料的选择是很重要的。
Manufacturers have to select non-conducting material for Dielectric such as plastic, PC or ABS, acryl, glass and so on.同时,绝缘介质上的喷涂和附着材料也一定是绝缘的。
否则,在操作过程中触控感应将出现差错。
At this time, coating and painting material also must be non-conducting type.If not, there will be errors in sensing operation.同时,绝缘介质上的喷涂和附着材料也一定是绝缘的。
否则,在操作过程中触控感应将出现差错。
Sensing principal of TS08TS02感应的主要原理:When human has contact to Touch pad, electric charge in the human body will be accumulated through the Touch pad.当人体接触感应焊盘时,在人体里的电荷将被通过感应焊盘积累。
This change of capacitance value can be detected by TS08.TS08可以探测到电容量的这种变化。
IR5210LPBF资料

IRF5210S/LHEXFET ® Power MOSFETPD - 91405ClAdvanced Process Technology l Surface Mount (IRF5210S)l Low-profile through-hole (IRF5210L)l 175°C Operating Temperature l Fast Switching l P-Channell Fully Avalanche Rated5/13/98Absolute Maximum RatingsFifth Generation HEXFETs from International Rectifier utilize advanced processing techniques to achieve extremely low on-resistance per silicon area. This benefit, combined with the fast switching speed and ruggedized device design that HEXFET Power MOSFETs are well known for, provides the designer with an extremely efficient and reliable device for use in a wide variety of applications.The D 2Pak is a surface mount power package capable of accommodating die sizes up to HEX-4. It provides the highest power capability and the lowest possible on-resistance in any existing surface mount package. The D 2Pak is suitable for high current applications because of its low internal connection resistance and can dissipate up to 2.0W in a typical surface mount application.The through-hole version (IRF5210L) is available for low-profile applications.Description2 D PakT O -262ParameterTyp.Max.UnitsR θJC Junction-to-Case–––0.75R θJAJunction-to-Ambient ( PCB Mounted,steady-state)**–––40Thermal Resistance°C/WParameterMax.UnitsI D @ T C = 25°C Continuous Drain Current, V GS @ -10V -40I D @ T C = 100°C Continuous Drain Current, V GS @ -10V -29A I DMPulsed Drain Current -140P D @T A = 25°C Power Dissipation 3.8W P D @T C = 25°C Power Dissipation 200W Linear Derating Factor 1.3W/°C V GS Gate-to-Source Voltage± 20V E AS Single Pulse Avalanche Energy 780mJ I AR Avalanche Current-21A E AR Repetitive Avalanche Energy 20mJ dv/dt Peak Diode Recovery dv/dt -5.0V/ns T J Operating Junction and-55 to + 175T STGStorage Temperature RangeSoldering Temperature, for 10 seconds300 (1.6mm from case )°CIRF5210S/LIRF5210S/LIRF5210S/LIRF5210S/LIRF5210S/LIRF5210S/LIRF5210S/LIRF5210S/LIRF5210S/L元器件交易网Note: For the most current drawings please refer to the IR website at:/package/。
- 1、下载文档前请自行甄别文档内容的完整性,平台不提供额外的编辑、内容补充、找答案等附加服务。
- 2、"仅部分预览"的文档,不可在线预览部分如存在完整性等问题,可反馈申请退款(可完整预览的文档不适用该条件!)。
- 3、如文档侵犯您的权益,请联系客服反馈,我们会尽快为您处理(人工客服工作时间:9:00-18:30)。
Document Number: 81090For technical questions, contact: emittertechsupport@High Speed Infrared Emitting Diode, RoHS Compliant, 870 nm,GaAlAs Double HeteroTSFF5210Vishay SemiconductorsDESCRIPTIONTSFF5210 is an infrared, 870 nm emitting diode in GaAlAs double hetero (DH) technology with high radiant power and high speed, molded in a clear, untinted plastic package.FEATURES•Package type: leaded •Package form: T-1 3/4•Dimensions (in mm): ∅ 5•Leads with stand-off•Peak wavelength: λp = 870 nm •High reliability •High radiant power•High radiant intensity•Angle of half intensity: ϕ = ± 10°•Low forward voltage•Suitable for high pulse current operation•High modulation bandwidth: f c = 24 MHz •Good spectral matching with Si photodetectors•Lead (Pb)-free component in accordance with RoHS 2002/95/EC and WEEE 2002/96/ECAPPLICATIONS•Infrared video data transmission between camcorder and TV set•Free air data transmission systems with high modulation frequencies or high data transmission rate requirements •Smoke-automatic fire detectorsNoteTest conditions see table “Basic Characteristics”NoteMOQ: minimum order quantity94 8390PRODUCT SUMMARYCOMPONENT I e (mW/sr)ϕ (deg)λP (nm)t r (ns)TSFF5210180± 1087015ORDERING INFORMATIONORDERING CODE PACKAGINGREMARKSPACKAGE FORMTSFF5210BulkMOQ: 4000 pcs, 4000 pcs/bulkT-1¾ABSOLUTE MAXIMUM RATINGSPARAMETER TEST CONDITIONSYMBOLVALUE UNIT Reverse voltage V R 5V Forward current I F 100mA Peak forward current t p /T = 0.5, t p = 100 µsI FM 200mA Surge forward current t p = 100 µs I FSM 1A Power dissipationP V180mW For technical questions, contact: emittertechsupport@Document Number: 81090TSFF5210Vishay SemiconductorsHigh Speed Infrared Emitting Diode, RoHS Compliant, 870 nm, GaAlAs Double HeteroNoteT amb = 25 °C, unless otherwise specifiedFig. 1 - Power Dissipation Limit vs. Ambient Temperature Fig. 2 - Forward Current Limit vs. Ambient TemperatureNoteT amb = 25 °C, unless otherwise specifiedJunction temperature T j 100°C Operating temperature range T amb - 40 to + 85°C Storage temperature range T stg - 40 to + 100°C Soldering temperaturet ≤ 5 s, 2 mm from caseT sd 260°C Thermal resistance junction/ambient J-STD-051, leads 7 mm, soldered on PCBR thJA230K/WABSOLUTE MAXIMUM RATINGSPARAMETER TEST CONDITIONSYMBOLVALUEUNITBASIC CHARACTERISTICSPARAMETER TEST CONDITION SYMBOLMIN.TYP.MAX.UNIT Forward voltageI F = 100 mA, t p = 20 ms V F 1.5 1.8V I F = 1 A, t p = 100 µsV F 2.3 3.0V Temperature coefficient of V F I F = 1 mA TK VF - 1.8mV/K Reverse current V R = 5 VI R 10µA Junction capacitance V R = 0 V, f = 1 MHz, E = 0C j 125pF Radiant intensity I F = 100 mA, t p = 20 ms I e 120180360mW/sr I F = 1 A, t p = 100 µs I e 1800mW/sr Radiant powerI F = 100 mA, t p = 20 msφe 50mW Temperature coefficient of φe I F = 100 mATK φe - 0.35%/K Angle of half intensity ϕ± 10deg Peak wavelength I F = 100 mA λp 870nm Spectral bandwidthI F = 100 mA Δλ40nm Temperature coefficient of λp I F = 100 mA TK λp 0.25nm/K Rise time I F = 100 mA t r 15ns Fall time I F = 100 mAt f 15ns Cut-off frequency I DC = 70 mA, I AC = 30 mA ppf c 24MHz Virtual source diameterd3.7mmTSFF5210 High Speed Infrared Emitting Diode, RoHSCompliant, 870 nm, GaAlAs Double HeteroVishay SemiconductorsBASIC CHARACTERISTICST amb = 25°C, unless otherwise specifiedFig. 3 - Pulse Forward Current vs. Pulse Duration Fig. 4 - Forward Current vs. Forward Voltage Fig. 5 - Radiant Intensity vs. Forward CurrentFig. 6 - Relative Radiant Power vs. Wavelength Fig. 7 - Relative Radiant Intensity vs. Angular Displacement Fig. 8 - Attenuation vs. FrequencyDocument Number: 81090For technical questions, contact: emittertechsupport@ TSFF5210Vishay Semiconductors High Speed Infrared Emitting Diode, RoHSCompliant, 870 nm, GaAlAs Double Hetero For technical questions, contact: emittertechsupport@ Document Number: 81090Disclaimer Legal Disclaimer NoticeVishayAll product specifications and data are subject to change without notice.Vishay Intertechnology, Inc., its affiliates, agents, and employees, and all persons acting on its or their behalf (collectively, “Vishay”), disclaim any and all liability for any errors, inaccuracies or incompleteness contained herein or in any other disclosure relating to any product.Vishay disclaims any and all liability arising out of the use or application of any product described herein or of any information provided herein to the maximum extent permitted by law. The product specifications do not expand or otherwise modify Vishay’s terms and conditions of purchase, including but not limited to the warranty expressed therein, which apply to these products.No license, express or implied, by estoppel or otherwise, to any intellectual property rights is granted by this document or by any conduct of Vishay.The products shown herein are not designed for use in medical, life-saving, or life-sustaining applications unless otherwise expressly indicated. Customers using or selling Vishay products not expressly indicated for use in such applications do so entirely at their own risk and agree to fully indemnify Vishay for any damages arising or resulting from such use or sale. Please contact authorized Vishay personnel to obtain written terms and conditions regarding products designed for such applications.Product names and markings noted herein may be trademarks of their respective owners.元器件交易网Document Number: 。