Modeling_12052012
Design and Implementation of a Bionic Robotic Hand
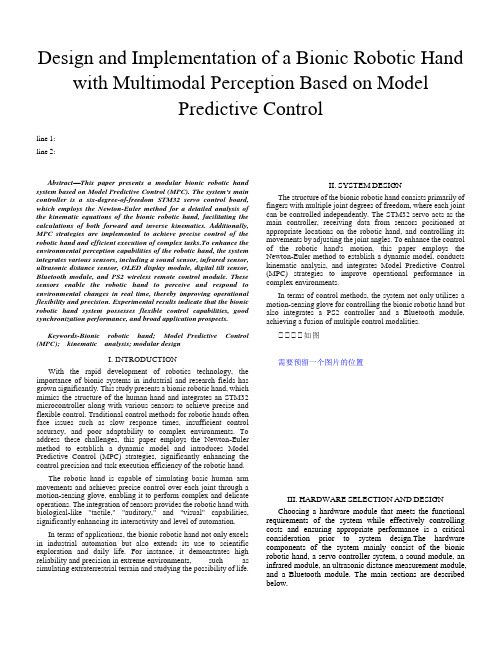
Design and Implementation of a Bionic Robotic Hand with Multimodal Perception Based on ModelPredictive Controlline 1:line 2:Abstract—This paper presents a modular bionic robotic hand system based on Model Predictive Control (MPC). The system's main controller is a six-degree-of-freedom STM32 servo control board, which employs the Newton-Euler method for a detailed analysis of the kinematic equations of the bionic robotic hand, facilitating the calculations of both forward and inverse kinematics. Additionally, MPC strategies are implemented to achieve precise control of the robotic hand and efficient execution of complex tasks.To enhance the environmental perception capabilities of the robotic hand, the system integrates various sensors, including a sound sensor, infrared sensor, ultrasonic distance sensor, OLED display module, digital tilt sensor, Bluetooth module, and PS2 wireless remote control module. These sensors enable the robotic hand to perceive and respond to environmental changes in real time, thereby improving operational flexibility and precision. Experimental results indicate that the bionic robotic hand system possesses flexible control capabilities, good synchronization performance, and broad application prospects.Keywords-Bionic robotic hand; Model Predictive Control (MPC); kinematic analysis; modular designI. INTRODUCTIONWith the rapid development of robotics technology, the importance of bionic systems in industrial and research fields has grown significantly. This study presents a bionic robotic hand, which mimics the structure of the human hand and integrates an STM32 microcontroller along with various sensors to achieve precise and flexible control. Traditional control methods for robotic hands often face issues such as slow response times, insufficient control accuracy, and poor adaptability to complex environments. To address these challenges, this paper employs the Newton-Euler method to establish a dynamic model and introduces Model Predictive Control (MPC) strategies, significantly enhancing the control precision and task execution efficiency of the robotic hand.The robotic hand is capable of simulating basic human arm movements and achieves precise control over each joint through a motion-sensing glove, enabling it to perform complex and delicate operations. The integration of sensors provides the robotic hand with biological-like "tactile," "auditory," and "visual" capabilities, significantly enhancing its interactivity and level of automation.In terms of applications, the bionic robotic hand not only excels in industrial automation but also extends its use to scientific exploration and daily life. For instance, it demonstrates high reliability and precision in extreme environments, such as simulating extraterrestrial terrain and studying the possibility of life.II.SYSTEM DESIGNThe structure of the bionic robotic hand consists primarily of fingers with multiple joint degrees of freedom, where each joint can be controlled independently. The STM32 servo acts as the main controller, receiving data from sensors positioned at appropriate locations on the robotic hand, and controlling its movements by adjusting the joint angles. To enhance the control of the robotic hand's motion, this paper employs the Newton-Euler method to establish a dynamic model, conducts kinematic analysis, and integrates Model Predictive Control (MPC) strategies to improve operational performance in complex environments.In terms of control methods, the system not only utilizes a motion-sensing glove for controlling the bionic robotic hand but also integrates a PS2 controller and a Bluetooth module, achieving a fusion of multiple control modalities.整整整整如图需要预留一个图片的位置III.HARDWARE SELECTION AND DESIGN Choosing a hardware module that meets the functional requirements of the system while effectively controlling costs and ensuring appropriate performance is a critical consideration prior to system design.The hardware components of the system mainly consist of the bionic robotic hand, a servo controller system, a sound module, an infrared module, an ultrasonic distance measurement module, and a Bluetooth module. The main sections are described below.A.Bionic Mechanical StructureThe robotic hand consists of a rotating base and five articulated fingers, forming a six-degree-of-freedom motion structure. The six degrees of freedom enable the system to meet complex motion requirements while maintaining high efficiency and response speed. The workflow primarily involves outputting different PWM signals from a microcontroller to ensure that the six degrees of freedom of the robotic hand can independently control the movements of each joint.B.Controller and Servo SystemThe control system requires a variety of serial interfaces. To achieve efficient control, a combination of the STM32 microcontroller and Arduino control board is utilized, leveraging the advantages of both. The STM32 microcontroller serves as the servo controller, while the Arduino control board provides extensive interfaces and sensor support, facilitating simplified programming and application processes. This integration ensures rapid and precise control of the robotic hand and promotes efficient development.C.Bluetooth ModuleThe HC-05 Bluetooth module supports full-duplex serial communication at distances of up to 10 meters and offers various operational modes. In the automatic connection mode, the module transmits data according to a preset program. Additionally, it can receive AT commands in command-response mode, allowing users to configure control parameters or issue control commands. The level control of external pins enables dynamic state transitions, making the module suitable for a variety of control scenarios.D.Ultrasonic Distance Measurement ModuleThe US-016 ultrasonic distance measurement module provides non-contact distance measurement capabilities of up to 3 meters and supports various operating modes. In continuous measurement mode, the module continuously emits ultrasonic waves and receives reflected signals to calculate the distance to an object in real-time. Additionally, the module can adjust the measurement range or sensitivity through configuration response mode, allowing users to set distance measurement parameters or modify the measurement frequency as needed. The output signal can dynamically reflect the measurement results via level control of external pins, making it suitable for a variety of distance sensing and automatic control applications.IV. DESIGN AND IMPLEMENTATION OF SYSTEMSOFTWAREA.Kinematic Analysis and MPC StrategiesThe control research of the robotic hand is primarily based on a mathematical model, and a reliable mathematical model is essential for studying the controllability of the system. The Denavit-Hartenberg (D-H) method is employed to model the kinematics of the bionic robotic hand, assigning a local coordinate system to each joint. The Z-axis is aligned with the joint's rotation axis, while the X-axis is defined as the shortest distance between adjacent Z-axes, thereby establishing the coordinate system for the robotic hand.By determining the Denavit-Hartenberg (D-H) parameters for each joint, including joint angles, link offsets, link lengths, and twist angles, the transformation matrix for each joint is derived, and the overall transformation matrix from the base to the fingertip is computed. This matrix encapsulates the positional and orientational information of the fingers in space, enabling precise forward and inverse kinematic analyses. The accuracy of the model is validated through simulations, confirming the correct positioning of the fingertip actuator. Additionally, Model Predictive Control (MPC) strategies are introduced to efficiently control the robotic hand and achieve trajectory tracking by predicting system states and optimizing control inputs.Taking the index finger as an example, the Denavit-Hartenberg (D-H) parameter table is established.The data table is shown in Table ITABLE I. DATA SHEETjoints, both the forward kinematic solution and the inverse kinematic solution are derived, resulting in the kinematic model of the ing the same approach, the kinematic models for all other fingers can be obtained.The movement space of the index finger tip is shownin Figure 1.Fig. 1.Fig. 1.The movement space at the end of the index finger Mathematical Model of the Bionic Robotic Hand Based on the Newton-Euler Method. According to the design, each joint of the bionic robotic hand has a specified degree of freedom.For each joint i, the angle is defined as θi, the angular velocity asθi, and the angular acceleration as θi.The dynamics equation for each joint can be expressed as:τi=I iθi+w i(I i w i)whereτi is the joint torque, I i is the joint inertia matrix, and w i and θi represent the joint angular velocity and acceleration, respectively.The control input is generated by the motor driver (servo), with the output being torque. Assuming the motor input for each joint is u i, the joint torque τi can be mapped through the motor's torque constant as:τi=kτ∙u iThe system dynamics equation can be described as:I iθi+b iθi+c iθi=τi−τext,iwhere b i is the damping coefficient, c i is the spring constant (accounting for joint elasticity), and τext,i represents external torques acting on the joint i, such as gravity and friction.The primary control objective is to ensure that the end-effector of the robotic hand (e.g., fingertip) can accurately track a predefined trajectory. Let the desired trajectory be denoted as y d(t)and the actual trajectory as y(t)The tracking error can be expressed as:e(t)=y d(t)−y(t)The goal of MPC is to minimize the cumulative tracking error, which is typically achieved through the following objective function:J=∑[e(k)T Q e e(k)]N−1k=0where Q e is the error weight matrix, N is the prediction horizon length.Mechanical constraints require that the joint angles and velocities must remain within the physically permissible range. Assuming the angle range of the i-th joint is[θi min,θi max]and the velocity range is [θi min,θi max]。
基于非线性建模与拟合的永磁同步电机转子初始位置精确估计方法

第28卷㊀第2期2024年2月㊀电㊀机㊀与㊀控㊀制㊀学㊀报Electri c ㊀Machines ㊀and ㊀Control㊀Vol.28No.2Feb.2024㊀㊀㊀㊀㊀㊀基于非线性建模与拟合的永磁同步电机转子初始位置精确估计方法姚培煜1,㊀冯国栋1,㊀吴轩2,㊀彭卫文1,㊀丁北辰3(1.中山大学智能工程学院,广东深圳518107;2.湖南大学电气与信息工程学院,湖南长沙410082;3.中山大学先进制造学院,广东深圳518107)摘㊀要:针对永磁同步电机转子初始位置估计的精度与收敛速度受限问题,提出一种基于高频信号注入的非线性建模与拟合实现的初始位置估计方法㊂首先,建立初始位置与高频信号响应的关联模型,表明高频响应可用于直接计算初始位置,但直接计算结果在大部分转子位置易受测量噪声的影响㊂为此,提出基于多项式模型建立位置估计非线性模型,选取合适的模型参数,利用少量测试点拟合该模型,即可实现初始位置的快速精确估计,有效提高了估计精度与系统抗干扰能力㊂实验与仿真结果表明,相比现有方法,提出的方法易于实现,无需复杂滤波器与观测器设计,仅需要选取少量测试点即可快速估计精确转子初始位置,在保证估计精度的同时改进了传统估计方法收敛速度慢问题㊂关键词:永磁同步电机;高频信号注入;转子初始位置估计;多项式模型;非线性模型DOI :10.15938/j.emc.2024.02.014中图分类号:TM351文献标志码:A文章编号:1007-449X(2024)02-0142-10㊀㊀㊀㊀㊀㊀㊀㊀㊀㊀㊀㊀㊀㊀㊀㊀㊀㊀㊀㊀㊀㊀㊀㊀㊀㊀㊀㊀㊀㊀㊀㊀㊀㊀㊀㊀㊀㊀㊀㊀㊀㊀㊀㊀㊀㊀㊀㊀㊀㊀㊀㊀㊀㊀㊀㊀㊀㊀㊀㊀㊀㊀㊀㊀㊀㊀㊀㊀㊀㊀㊀㊀㊀㊀㊀㊀㊀㊀㊀㊀㊀㊀㊀㊀㊀㊀㊀㊀㊀㊀㊀㊀㊀㊀㊀㊀㊀㊀㊀㊀㊀㊀㊀㊀㊀㊀㊀㊀㊀㊀㊀㊀㊀㊀收稿日期:2022-09-24基金项目:国家自然科学基金(52105079,62103455)作者简介:姚培煜(1999 ),男,硕士研究生,研究方向为永磁同步电机无位置传感控制;冯国栋(1988 ),男,博士,副教授,硕士生导师,研究方向为新能源汽车电机系统控制关键技术;吴㊀轩(1983 ),男,博士,副教授,研究方向为电力电子与电力传动㊁大型风力发电技术㊁特种车辆电驱动技术;彭卫文(1987 ),男,博士,副教授,研究方向为系统可靠性㊁智能系统的状态监测㊁故障预测与健康管理;丁北辰(1990 ),男,博士,副教授,研究方向为机器人控制与新能源汽车动力系统控制㊂通信作者:丁北辰High precision initial rotor position estimation method for permanent magnet synchronous motor based on nonlinear modeling and fittingYAO Peiyu 1,㊀FENG Guodong 1,㊀WU Xuan 2,㊀PENG Weiwen 1,㊀DING Beichen 3(1.School of Intelligent Systems Engineering,Sun Yat-sen University,Shenzhen 518107,China;2.College of Electrical and Information Engineering,Hunan University,Changsha 410082,China;3.School of Advanced Manufacturing,Sun Yat-sen University,Shenzhen 518107,China)Abstract :Aiming at the problem that the accuracy and convergence speed of rotor initial position estima-tion of permanent magnet synchronous motor are limited,a nonlinear modeling and fitting method basedon high-frequency signal injection was proposed.Firstly,the correlation model between the initial posi-tion and the high-frequency signal response was established,which shows that the high-frequency re-sponse can be used to calculate the initial position directly,but the direct calculation results are vulnera-ble to the measurement noise in most rotor positions.To solve this issue,a polynomial model was used toestablish the nonlinear model of location estimation,suitable model parameters were selected and a few oftest points were used to fit the polynomial model to achieve rapid and accurate calculation of the initialposition,which effectively improves the estimation accuracy and anti-interference ability of the system. The experimental and simulation results show that compared with the existing methods,in the proposed method it is easy to implement,complex filter and observer design is not needed,and only a few test points need to be selected to quickly estimate the initial position of the precise rotor,which ensures the estimation accuracy and improves the problem of slow convergence of the traditional estimation methods. Keywords:permanent magnet synchronous motor;high frequency signal injection;initial rotor position es-timation;polynomial model;nonlinear model0㊀引㊀言永磁同步电机(permanent magnet synchronous motor,PMSM)因其结构简单,高效率,高能量密度等优点而被广泛应用于新能源汽车等多个领域[1-3]㊂对于永磁同步电机伺服系统,转子初始位置是保证电机启动性能的重要参数㊂具体而言,精确的初始位置能够提高电机控制性能,若初始位置误差过大,会降低启动性能,甚至会导致电机反转与启动失败[4-6]㊂转子位置可通过光电编码器,旋转变压器等获取,但增加了系统成本和体积,在低成本应用如家用电器以及超高速电机应用中,无位置传感控制技术被广泛应用㊂初始位置估计是无位置传感控制的重要环节,可有效地提高系统启动与控制的可靠性㊂因此,转子初始位置估计对永磁同步电机伺服系统十分关键㊂转子初始位置估计在文献中已有广泛研究㊂其中,利用电感饱和效应是近年来解决转子初始位置估计的重要手段,可分为脉冲电压法[7-10],高频信号注入法[11-23]㊂脉冲电压法通过注入一系列脉冲电压矢量,利用电流响应估计转子位置㊂然而,脉冲电压注入可导致转子转动,且过程耗时长㊂高频信号注入法实现简单,无需电机参数和额外硬件,可分高频旋转电压注入[11-16]和高频脉振电压注入[17-23]㊂高频旋转电压注入法依赖于转子凸极效应,且需要通过坐标变换和滤波器提取转子位置㊂文献[11]对高频电流响应进行低通滤波,根据电流幅值随转子位置变化实现转子位置估计㊂文献[14]对三相高频电流正㊁负序分量分离,利用任意一相正负序相角差估计转子位置㊂文献[15]分析了旋转高频注入方法受采样㊁滤波器的影响,并提出一种补偿算法提高位置观测精度㊂高频脉振电压注入法对凸极性要求不高,适用于表贴式电机㊂文献[17]针对相移问题,改用交直轴响应电流解调去除高频分量㊂文献[18]通过对虚拟直轴施加高频电压产生一系列振动信号实现初始位置估计㊂但该方法需要振动传感器,且在转动惯量较大的应用中,需要较大电流诱导转子振动㊂文献[20]在脉振注入基础上引入载波频率成分法判断磁极极性,避免二次信号注入,简化了实现步骤㊂现有高频信号注入估计方法大多通过滤波环节分离高频信号,再通过观测器估计转子初始位置㊂但滤波器对高频信号的幅值和相位产生影响,限制了系统带宽,无法同时保证转子位置的辨识精度和辨识速度㊂同时,观测器的设计也依赖高频信号响应和电机参数㊂针对以上问题,本文提出一种基于高频信号注入的非线性建模与拟合方法,实现转子初始位置估计㊂在虚拟直轴注入高频信号,解调高频电流响应即可获得初始位置,但易受转子所在位置的影响㊂在此基础上,提出基于非线性建模的初始位置估计方法,利用少数测试对非线性模型辨识,实现对转子位置的精确估计㊂此方法无需复杂滤波器和观测器设计,避免相位偏移和收敛速度慢等问题㊂此外,采用测试点快速拟合估计模型有效提高初始位置估计精度和收敛速度㊂仿真与实验结果验证提出方法的有效性㊂1㊀高频信号注入建模永磁同步电机d-q轴电压方程可表示为:u d=Ri d+L dd i dd t-ωL q i q;u q=Ri q+L qd i qd t+ωL d i d+ωλ0㊂üþýïïïï(1)式中:u d/q㊁i d/q和L d/q分别表示d-q轴电压㊁电流和电感;λ0是永磁磁链;R是绕组电阻;ω是电角速度㊂对应的高频信号注入模型可表示为:u dh=R h i dh+L dhd i dhd t;u qh=R h i qh+L qhd i qhd t㊂üþýïïïï(2)341第2期姚培煜等:基于非线性建模与拟合的永磁同步电机转子初始位置精确估计方法式中下标h 表示高频分量㊂例如L dh /qh 表示高频电感,R h 表示高频电阻,初始转速为0㊂不失一般性,假设电机转子的初始位置为θ0㊂定义一个虚拟d -q 轴,其虚拟d 轴的位置为θv ,而θ0和θv 间的误差定义为Δθ=θv -θ0,虚拟d -q 轴与真实d -q 轴的关系如图1所示㊂图1㊀虚拟d -q 轴与真实d -q 轴的关系Fig.1㊀Relationship between virtual and actualdq-axis为估计初始位置θ0,将高频电压信号注入虚拟d 轴,可表达为u dh,v =V dh cos(ωh t )㊂(3)式中:u dh,v 表示高频电压;V dh 为幅值;ωh 为频率㊂基于旋转变换可得注入实际d 轴的高频电压信号为:u dh =u dh,v cosΔθ;u qh =u dh,vsinΔθ㊂}(4)式中u dh 和u qh 为注入到真实d -q 轴的高频电压㊂将式(3)和式(4)代入式(2)可得d -q 与α-β轴下的高频电流响应为:㊀i dh =I dd sin(ωh t -φd )cosΔθ;i qh=I dqsin(ωht -φq)sinΔθ㊂}(5)㊀i αh =I dd sin(ωh t +φd )cosΔθcos θ0-I dq sin(ωh t +φq )sinΔθsin θ0;i βh =I dd sin(ωh t +φd )cosΔθsin θ0+I dqsin(ωht +φq)sinΔθcos θ0㊂üþýïïïï(6)㊀I dd =V dh Z dh ;I dq =V dh Z qh;Z 2dh =R 2h +ω2h L 2dh ;Z 2qh =R 2h +ω2h L 2qh ;tan φd =R h ωh L dh ;tan φq =R h ωh L qh㊂üþýïïïïïï(7)式中i αh 和i βh 可由abc 相电流计算获取㊂对α-β轴高频电流进行如下运算,即:M αs ≜avg(i αh sin ωh t )=I 1cosΔθcos θ0-I 2sinΔθsin θ0;M βs≜avg(i βhsin ωht )=I 1cosΔθsin θ0+I 2sinΔθcos θ0㊂}(8)式中: avg(x ) 表示x 在一个或多个周期内的平均值(例如信号x 的5个周期),I 1和I 2表示如下:I 1=0.5I dd cos φd ;I 2=0.5I dq cos φq ㊂}(9)2㊀转子初始位置直接计算2.1㊀高频注入直接计算法原理式(8)存在3个未知数,至少需要两组数据确定θ0㊂为此,将高频信号分别注入2个虚拟d 轴,对应位置分别为θv0和θv1,其中:1)将V dh0cos(ωh0)注入虚拟d 轴θv0,得到i αh0和i βh0;2)将V dh1cos(ωh1)注入虚拟d 轴θv1,得到i αh1和i βh1㊂基于式(8)以及i αh i 和i βh i ,i =0㊁1,可得:M αs0=I 1cos(θv0-θ0)cos θ0-I 2sin(θv0-θ0)sin θ0;M βs0=I 1cos(θv0-θ0)sin θ0+I 2sin(θv0-θ0)cos θ0;M αs1=I 1cos(θv1-θ0)cos θ0-I 2sin(θv1-θ0)sin θ0;M βs1=I 1cos(θv1-θ0)sin θ0+I 2sin(θv1-θ0)cos θ0㊂üþýïïïï(10)不难看出,基于式(10)可直接计算转子初始位置,定义计算出的位置为θr ㊂特别地,当选择虚拟位置满足θv0=0和θv1=π/2时,θr 可表示为:2θr =arccos(cos2θ0),sin2θ0ȡ0;2π-arccos(cos2θ0),sin2θ<0㊂{(11)其中:sin2θ0=B2C -A 2;cos2θ0=DA 2C -A 2㊂üþýïïïï(12)A =M αs0+M βs1=I 1+I 2;B =2M αs1=(I 1-I 2)sin2θ0;C =M 2αs0+M 2βs1+2M 2αs1=I 21+I 22;D =M 2αs0-M 2βs1=(I 21-I 22)cos2θ0㊂üþýïïïïï(13)图2给出了直接计算法的实施流程,高频信号依次注入得到α-β轴高频电流响应,通过式(10)~式(13)计算出转子初始位置的估计值θr ,最后使用短脉冲注入方法辨识转子磁极极性[24]㊂2.2㊀直接计算法估计误差分析不难看出直接计算法的估计误差与高频信号注入的虚拟位置θv0与θv1相关㊂定义直接计算法的估计误差为Δθe =θr -θ0㊂本节研究θv0与θv1的选择与441电㊀机㊀与㊀控㊀制㊀学㊀报㊀㊀㊀㊀㊀㊀㊀㊀㊀㊀㊀㊀㊀第28卷㊀估计误差Δθe 的关系,指导θv0与θv1的选择㊂图2㊀直接计算法框图Fig.2㊀Block diagram of direct calculation method2.2.1㊀虚拟位置θv0和θv1选择与误差Δθe 的关系直接计算法是将式(3)中的高频信号分别注入虚拟位置θv0和θv1,获得α-β轴高频响应,对其进一步处理得方程组(10),包含3个未知量,利用数值计算可获得估计结果㊂图3为分别在2个转子初始位置θ0下选择任意不同θv0和θv1时,直接计算法估计误差的分布图,图中每个误差点都是在噪声强度为30dB 仿真环境下2000次随机试验的平均值㊂下文若无特别说明,仿真环境中的噪声强度统一为30dB㊂不难看出,当θv0和θv1越接近,Δθe 越大;当θv0=θv1时,式(10)中的方程式个数变为2个,方程组无解;当θv0和θv1的差值越大,估计误差受噪声影响越小㊂θv0和θv1分别取0和π/2时估计误差相对最小㊂图3㊀不同θv0和θv1的估计误差分布Fig.3㊀Estimation error distributions of different θv0and θv12.2.2㊀不同转子位置的误差Δθe 分析本节探讨转子在不同初始位置直接计算法的估计误差㊂图4给出了不同转子位置的估计误差㊂其中,虚拟位置设置为θv0=0和θv1=π/2;每个误差点都是对同一位置2000次随机试验的平均值㊂可以看出θ0在[0,π]上的估计误差Δθe 呈现三角函数规律变化,在θ0=0㊁π/2㊁π/4附近时θr 的误差Δθe 较小,最小误差约为0.01rad,而在θ0=π/4㊁3π/4附近时θ0的误差Δθe 非常大,最大误差为0.063rad,最大误差是最小误差的6倍以上㊂导致误差呈三角函数规律变化的原因如下:在式(10)中噪声来源于M αs 和M βs ,而在使用式(10)求解θr 时,对cos2θ0进行反三角变化求解θr ㊂对式(10)等式右边变换拆解,提取含有cos2θ0的部分为:S αs =0.5(cos θv (I 1-I 2)cos2θ0)M αs ;S βs =0.5(sin θv (I 1-I 2)cos2θ0)M βs㊂üþýïïïï(14)式中:S αs 和S βs 可以近似表示信号与噪声的比例,即信噪比(signal to noise ratio,SNR)㊂当θ0接近π/4㊁3π/4时,cos2θ0趋于0,S αs 和S βs 趋于0㊂θ0趋于0㊁π/2㊁π时,cos2θ0趋于1,S αs 和S βs 远大于0㊂即Δθe 随着cos2θ0变化而波动㊂不难发现,由于测量噪声的存在,基于式(10)的直接计算法的估计误差在不同转子位置的波动非常大,特别是转子位置在π/4㊁3π/4附近的估计误差比最小误差增加了6倍㊂因此,本文提出基于非线性建模与拟合的方法估计初始位置,提高估计精度和降低估计误差的波动㊂图4㊀直接计算法在不同转子位置的误差变化Fig.4㊀Error variation of direct calculation method atdifferent rotor positions3㊀基于非线性建模与拟合的初始转子位置估计3.1㊀基于多项式建模与曲线拟合的估计方法基于式(8),定义M s ≜M 2αs +M 2βs =I 22+(I 21-I 22)cos 2(θv -θ0)㊂(15)541第2期姚培煜等:基于非线性建模与拟合的永磁同步电机转子初始位置精确估计方法式中M s 以虚拟d 轴位置θv 为自变量的函数,且M s在θv 满足下式时取最大值:Δθ=θv -θ0=0or π㊂(16)如图5所示,考虑在一个周期内,函数M s (θv )在θv <θ0时递增,在此处后递减,这表明转子初始位置θ0可在函数曲线M s (θv )的最大值处得到㊂图5㊀θ0=π/2时M s (θv )曲线Fig.5㊀Curve of M s (θv )at θ0=π/2考虑到直接计算法受测量噪声影响较大,本文提出利用多项式函数对M s (θv )建模,进而在M s (θv )的最大值处确定初始位置θ0㊂不失一般性,本文使用k 阶多项式对M s (θv )建模,即M s (θv )=a k θk v +a k -1θk -1v+ +a 1θv +a 0㊂(17)式中a 0, ,a k -1,a k 为k 阶多项式的系数,可通过曲线拟合估计㊂当a 0, ,a k -1,a k 确定,初始位置θ0可以通过求解下式获得:d M s (θv )d θv =ka k θk -1v +(k -1)a k -1θk -2v+ +2a 2θv +a 1=0㊂(18)当k =2或3时,θ0的估计为:θ0=-a 12a 2,k =2;-a 2ʃa 22-3a 3a 13a 3ɪ[0,π2],k =3㊂ìîíïïïï(19)综上,基于提出的初始位置估计分为两步:第一步:设置N 个虚拟d 轴位置,注入高频测试信号并采集数据用于拟合M s (θv );第二步:基于最小二乘估计a 0, ,a k -1,a k ,并用式(19)计算初始位置θr ㊂图6给出了第一步的图解,假设N 个虚拟d 轴位置为{θv1,θv2, ,θv N },通过电流计算获得{M s1,M s2, ,M s N }㊂基于上述数据与最小二乘法拟合的多项式系数可表示为a =(ϕT ϕ)-1ϕT M ㊂(20)式中:a =[a 0,a 1, ,a k ]T ;ϕ=θk v1θk -1v1θv11θk v2θk -1v2 θv21︙︙︙︙θk v N θk -1v N θv N 1éëêêêêêêùûúúúúúú;M =[M s1,M s2, ,M s N ]T ㊂üþýïïïïïïïïï(21)图6㊀第一步的步骤图Fig.6㊀Diagram of the first step图7给出了此方法的实施框图㊂定义测试点固定间距为θL ,高频电压信号依次注入d 轴虚拟位置θv i =θv i -1+θL ,i =1, ,N ㊂采集α-β轴电流响应,利用式(15)计算M s (θv )用于建模与拟合,利用式(19)计算初始位置θ0㊂图7㊀拟合估计法框图Fig.7㊀Block diagram of fitting estimation method3.2㊀多项式模型参数选择首先,讨论如何选择合适的参数k ㊂一般选择k =2~4可满足估计精度要求㊂考虑到实际环境中的测量噪声,图8为使用不同阶次的多项式拟合M s (θv )㊂从表1不难发现,曲线拟合误差随着k 的增加而越小,但在θ0附近使用二阶多项式拟合即可实现较好的拟合精度㊂641电㊀机㊀与㊀控㊀制㊀学㊀报㊀㊀㊀㊀㊀㊀㊀㊀㊀㊀㊀㊀㊀第28卷㊀表1㊀不同阶次多项式的拟合精度比较Table 1㊀Comparison of fitting precision between differentorder polynomials参数转子位置/rad 拟合误差/rad真实位置θ00.7854 二阶多项式0.83080.0454三阶多项式0.82730.0419四阶多项式0.82560.0402图8㊀不同阶次多项式拟合M s (θv )Fig.8㊀Fitting M s (θv )with different order polynomials拟合k 次多项式最少需要k +1个拟合点,即N ȡk +1㊂其次,研究如何选取合适的虚拟位置{θv1,θv2, ,θv N },保证初始位置估计精度㊂图9给出了选择k =2㊁N =3㊁4㊁5时的估计误差㊂从图9中不难发现拟合点数量N =5较N =4拟合精度提升并不明显,但需要增加测试点;而N =4较于N =3估计精度有显著提高,且N =4对应的估计精度已满足应用需求㊂综合实现复杂度与估计精度要求,本文选择N =4个拟合点实现多项式模型的拟合㊂图9㊀不同拟合点数量的估计误差Fig.9㊀Estimation error between different number offitting points直接计算法估计的θr 可用于确定一个θ0的粗略分布区域㊂假定θ0=π/4㊁k =2㊁N =4㊂分别在区间R 1=[0,π/2]㊁R 2=[π/8,3π/8]和R 3=[3π/16,5π/16]内随机选取拟合点进行曲线拟合估计,表2是进行2000次随机实验的平均误差,表明通过θr 确定一个合适的区间可以有效地提高估计精度㊂表2㊀不同拟合点选取区间的拟合精度比较Table 2㊀Comparison of fitting precision between differentselection interval of fitting points参数转子位置/rad 拟合误差/rad 真实位置θ00.7854R 10.95280.1674R 20.95680.1714R 30.89680.1114M s (θv )曲线在峰值附近以峰值为中心左右对称,因此在两侧对称选取拟合点能有效提高拟合效果㊂考虑到估计的θr 接近峰值位置,因此本文选择在θr 左右对称地选取拟合点㊂具体而言,首先确定左侧第一个拟合点,其次在当前位置叠加θL 确定下一拟合点位置,该过程可表示为θ2=θ1+θL , ,θN =θN -1+θL ㊂(22)式中θL 对拟合结果有显著影响㊂假定θ0=π/4㊁k =2㊁N =4,图10给出了选择不同θL 时估计误差的变化曲线㊂不难看出,选择θL =0.558rad 估计误差最小㊂综上,本文选择二阶多项式四点拟合,其中拟合点以直接计算值θr 左右对称等间距θL =0.558rad 选取㊂图10㊀不同拟合点间距的估计误差Fig.10㊀Estimation error under different θL3.3㊀多项式曲线拟合法仿真实验本节通过仿真结果验证提出方法的有效性㊂上文分析得出k 阶多项式参数k =2㊁N =4以及拟合点741第2期姚培煜等:基于非线性建模与拟合的永磁同步电机转子初始位置精确估计方法间距选择θL =0.558rad,具有较高的估计精度,下文仿真实验都将使用此模型参数㊂图11是假定初始位置θ0=π/4时,分别使用直接计算法和拟合估计法进行2000次随机实验的估计误差分布㊂不难发现,相比于直接计算法,曲线拟合估计法在同一转子位置上的估计误差和误差波动都更小㊂图11㊀2000次随机实验的估计误差分布Fig.11㊀Estimated error distributions for 2000randomized tests图12为使用高频注入直接计算法和曲线拟合估计法在不同转子位置上的估计误差比较,图12(a)㊁(b)分别为30dB 和40dB 测量噪声下的结果㊂图中每点都是进行了2000次实验的平均估计误差㊂可以发现在θ0=π/4㊁3π/4附近的大部分区域,拟合误差远小于直接计算误差,差值最大的位置拟合误差较直接计算误差减小了0.0352rad,减小了56%㊂另外,对比不同噪声强度环境可以发现,曲线拟合估计法在不同噪声强度下都能够保持较大幅度的估计精度提升㊂曲线拟合法在超过80%的转子位置上估计误差小于直接计算法,在一些位置误差能减小50%以上㊂但在θ0=0㊁π/2㊁π附近其余20%的位置上,因信噪比较大,直接计算法估计误差小于曲线拟合法㊂因此在一个电角度周期内,可以采用两种方法混合估计,当θ0在0㊁π/2㊁π附近小部分区域时令θr 为最终估计结果,否则进一步实施拟合方法估计初始位置,如表3所示㊂图12㊀不同转子位置上估计误差对比Fig.12㊀Comparison of estimated errors between differ-ent rotor positions表3㊀不同转子位置上3种方法的区别Table 3㊀Difference of three methods between differentrotor positions方法θ0在0㊁π/2㊁π附近其他位置直接计算法直接计算直接计算拟合估计法拟合估计拟合估计混合估计法直接计算拟合估计在所有位置上,θr 的平均误差为0.0432rad,拟合θ0的平均误差为0.0268rad,混合估计法可使平均误差进一步减小到0.0248rad㊂整体估计精度提高40%,且拟合估计值的误差波动更小㊁更平稳㊂4㊀实验验证在图13所示的PMSM 样机实验平台上验证本文所提出的方法㊂实验电机的设计参数如表4所示㊂测试电机配备高分辨率光学编码器,单转脉冲数(PPR)为2500㊂从该编码器测量的转子位置将被用来评估提出估计方法的性能,不参与实际控制㊂在实验平台验证方法过程中,电机的转速与转矩都为0㊂注入高频信号的参数为:注入信号频率ωh =150Hz,注入信号幅值V dh =20V㊂选择的非线性模型参数为:k =2㊁N =4㊁θL =0.558rad㊂图14出了使用此参数对M s (θv )进行建模估计θ0的例子㊂841电㊀机㊀与㊀控㊀制㊀学㊀报㊀㊀㊀㊀㊀㊀㊀㊀㊀㊀㊀㊀㊀第28卷㊀图13㊀实验装置Fig.13㊀Experimental device 表4㊀实验电机的设计参数Table 4㊀Design parameters of experimental motor图14㊀实验验证的拟合估计法例子Fig.14㊀Examples of fitting estimation method verifiedby experiment首先,实验一在不同转子位置进行实验以评估提出估计方法的效果㊂图15(a)给出了电机一个电角度周期内8个位置的估计结果,不难发现估计结果与真实位置十分接近,具体误差分布见图15(b)㊂从图15可以看出,一个电角度周期内,最大拟合误差0.0412rad,最小拟合误差0.0035rad,平均拟合误差约为0.018rad㊂结果表明,曲线拟合估计法能精确估计转子初始位置㊂其次,实验二对比直接计算法与拟合估计法的实验结果㊂直接计算法从α-β轴高频响应电流计算转子初始位置,曲线拟合估计法采用二阶多项式四点非线性建模与拟合估计转子位置㊂估计结果对比如图16(a)所示,2种方法的估计误差对比如图16(b)所示㊂可以看出,直接计算法的平均估计误差为0.034rad,最大估计误差0.114rad,拟合估计的平均拟合误差为0.016rad,最大拟合误差0.042rad㊂实验证明提出的方法相比于传统高频注入法大幅提升了估计精度,降低了误差波动㊂图15㊀实验一的转子初始位置估计结果Fig.15㊀Rotor initial position estimation results inexperiment 1图16㊀实验二的转子初始位置估计结果比较Fig.16㊀Comparison of rotor initial position estimationresults in experiment 25㊀结㊀论本文提出一种基于高频注入的非线性建模与拟合的转子初始位置估计方法,并通过仿真和实验验941第2期姚培煜等:基于非线性建模与拟合的永磁同步电机转子初始位置精确估计方法证提出方法的有效性㊂提出的方法利用少数测试点对位置估计非线性模型快速拟合,实现简单,不依赖电机参数,无需复杂滤波器和观测器的设计㊂实验结果表明,最大误差小于0.05rad,平均误差小于0.02rad㊂与现有方法相比,提出的方法具有估计精度高,收敛速度快,易于实现等优势,工程实用价值高㊂此外,该方法同样在无位置传感器控制技术上有潜在的应用前景㊂参考文献:[1]㊀SHOU W,KANG J,DEGANO M,et al.An accurate wide-speedrange control method of IPMSM considering resistive voltage drop and magnetic saturation[J].IEEE Transactions on Industrial E-lectronics,2020,67(4):2630.[2]㊀朱元,肖明康,陆科,等.电动汽车永磁同步电机转子温度估计[J].电机与控制学报,2021,25(6):72.ZHU Yuan,XIAO Mingkang,LU Ke,et al.Rotor temperature estimation for permanent magnet synchronous motors in electric ve-hicles[J].Electric Machines and Control,2021,25(6):72. [3]㊀王晓远,刘铭鑫,陈学永,等.电动汽车用ANGN带滤波补偿三阶滑模自抗扰控制[J].电机与控制学报,2021,25(11):25.WANG Xiaoyuan,LIU Mingxin,CHENG Xueyong,et al.Third-order sliding mode active disturbance rejection control of PMSM with filter compensation for electric vehicle[J].Electric Machines and Control,2021,25(11):25.[4]㊀BRIZ F,DEGNER M.Rotor position estimation[J].IEEE Indus-trial Electronics Magazine,2011,5(2):24.[5]㊀YEH H,YANG S.Phase inductance and rotor position estimationfor sensorless permanent magnet synchronous machine drives at standstill[J].IEEE Access,2021(9):32897.[6]㊀贾洪平,贺益康.基于高频注入法的永磁同步电动机转子初始位置检测研究[J].中国电机工程学报,2007,27(15):15.JIA Hongping,HE Yikang.Study on inspection of the initial rotor position of a PMSM based on high-frequency signal injection[J].Proceedings of the CSEE,2007,27(15):15.[7]㊀张树林,康劲松,母思远.基于等宽电压脉冲注入的永磁同步电机转子初始位置检测方法[J].中国电机工程学报,2020,40(19):6085.ZHANG Shulin,KANG Jinsong,MU Siyuan.Initial rotor position detection for permanent magnet synchronous motor based on identi-cal width voltage pulse injection[J].Proceedings of the CSEE, 2020,40(19):6085.[8]㊀王宾,彭皆彩,于水娟.一种电流合成的PMSM转子初始位置检测方法[J].电机与控制学报,2020,24(8):67.WANGBin,PENG Jiecai,YU Shuijuan.Method to detect the ini-tial rotor position of PMSM based on current synthesis[J].Elec-tric Machines and Control,2020,24(8):67.[9]㊀孟高军,余海涛,黄磊,等.一种基于线电感变化特征的永磁同步电机转子初始位置检测新方法[J].电工技术学报, 2015,30(20):1.MENG Gaojun,YU Haitao,HUANG Lei,et al.A novel initial rotor position estimation method for PMSM based on variation be-havior of line inductances[J].Transactions of China Electrotech-nical Society,2015,30(20):1.[10]㊀WU X,LU Z,LING Z,et al.An improved pulse voltage injec-tion based initial rotor position estimation method for PMSM[J].IEEE Access,2021(9):121906.[11]㊀鲁家栋,刘景林,卫丽超.永磁同步电机转子初始位置检测方法[J].电工技术学报,2015,30(7):105.LU Jiadong,LIU Jinglin,WEI Lichao.Estimation of the initialrotor position for permanent magnet synchronous motors[J].Transactions of China Electrotechnical Society,2015,30(7):105.[12]㊀JIN X,NI R,CHEN W,et al.High-frequency voltage-injectionmethods and observer design for initial position detection of per-manent magnet synchronous machines[J].IEEE Transactions onPower Electronics,2018,33(9):7971.[13]㊀王华斌,施金良,陈国荣,等.内嵌式永磁同步电机转子初始位置检测[J].电机与控制学报,2011,15(3):40.WANG Huabin,SHI Jinliang,CHEN Guorong,et al.Initial ro-tor position detection of IPMSM[J].Electric Machines and Con-trol,2011,15(3):40.[14]㊀刘景林,鲁家栋.基于相电流正负序分量相角差的高精度内置式永磁同步电机转子初始位置检测方法[J].电工技术学报,2016,31(23):63.LIU Jinglin,LU Jiadong.High-precision estimation method of in-itial rotor position for IPMSM based on phase difference of posi-tive and negative sequence current component[J].Transactionsof China Electrotechnical Society,2016,31(23):63. [15]㊀杨健,杨淑英,李浩源,等.基于旋转高频电压注入的永磁同步电机转子初始位置辨识方法[J].电工技术学报,2018,33(15):3547.YANG Jian,YANG Shuying,LI Haoyuan,et al.Initial rotor po-sition estimation for IPMSM based on high frequency rotating volt-age injection[J].Transactions of China Electrotechnical Society,2018,33(15):3547.[16]㊀SHUANG B,ZHU Z.A novel sensorless initial position estima-tion and startup method[J].IEEE Transactions on Industrial E-lectronics,2021,68(4):2964.[17]㊀于安博,刘利,阚志忠,等.高频脉振信号注入永磁同步电机无滤波器初始位置辨识方法[J].电工技术学报,2021,36(4):801.YU Anbo,LIU Li,KAN Zhizhong,et al.Initial position identi-051电㊀机㊀与㊀控㊀制㊀学㊀报㊀㊀㊀㊀㊀㊀㊀㊀㊀㊀㊀㊀㊀第28卷㊀fication of PMSM with filterless high frequency pulse signal injec-tion method[J].Transactions of China Electrotechnical Society,2021,36(4):801.[18]㊀FU X,XU Y,HE H,et al.Initial rotor position estimation bydetecting vibration of permanent magnet synchronous machine[J].IEEE Transactions on Industrial Electronics,2021,68(8):6595.[19]㊀ZHANG X,LI H,YANG S,et al.Improved initial rotor positionestimation for PMSM drives based on HF pulsating voltage signalinjection[J].IEEE Transactions on Industrial Electronics,2018,65(6):4702.[20]㊀李洁,周波,刘兵,等.表贴式永磁同步电机无位置传感器起动新方法[J].中国电机工程学报,2016,36(9):2513.LI Jie,ZHOU Bo,LIU Bing,et al.A novel starting strategy ofsensorless control for surface mounted permanent magnet synchro-nous machines[J].Proceedings of the CSEE,2016,36(9):2513.[21]㊀TANG Q,SHEN A,LUO X,et al.PMSM sensorless control byinjecting hf pulsating carrier signal into ABC frame[J].IEEETransactions on Power Electronics,2017,32(5):3767. [22]㊀吕德刚,姜国威,纪堂龙.永磁同步电机低速域改进高频脉振注入控制[J].哈尔滨理工大学学报,2022,27(6):32.LÜDegang,JIANG Guowei,JI Tanglong.Improved high fre-quency pulse injection control inlow speed domain of permanentmagnet synchronous motor[J].Journal of Harbin University ofScience and Technology,2022,27(6):32.[23]㊀WU T,LUO D,HUANG S,et al.A fast estimation of initial ro-tor position for low-speed free-running IPMSM[J].IEEE Trans-actions on Power Electronics,2020,35(7):7664. [24]㊀XUAN W,YAO F,XIAO L,et al.Initial rotor position detec-tion for sensorless interior PMSM with square-wave voltage injec-tion[J].IEEE Transactions on Magnetics,2017,53(11):1.(编辑:刘琳琳)151第2期姚培煜等:基于非线性建模与拟合的永磁同步电机转子初始位置精确估计方法。
同步逆变器并离网切换策略研究

2021年7期科技创新与应用Technology Innovation and Application方法创新同步逆变器并离网切换策略研究张钦臻,朱鹏鹏(上海电力大学电子与信息工程学院,上海201306)1概述随着全球化石燃料的不断消耗及环境问题的日益加重,推动了微电网及可再生分布式能源发电技术在电网中的应用[1]。
然而大量的可再生分布式发电单元通过电力电子接口接入电网,传统的同步发电机所具有的阻尼及惯性不足以维持电网稳定、高效的运行[2],亟需一种友好的并网设备连接微电网与电网。
虚拟同步机是将电力电子变流器控制成具有传统同步机内部阻尼、惯量特性和外部下垂特性的方法[3]。
其中作为虚拟同步机的一种实现方式———同步逆变器将同步机的数学结构模型转化为电压参考指令,引入到逆变器的控制中,并根据需要在逆变器直流侧配备充足的储能单元即可为系统提供惯量支撑,提升系统运行的稳定性。
文献[4]提出了虚拟同步发电机的并离网切换策略,但没有考虑并网时无功功率对微电网带来的冲击。
文献[5]基于虚拟同步发电机技术的无缝切换策略,可以很好的进行离/并网切换,但是结构相对复杂。
本文在研究同步逆变器结构、控制原理的基础上,针对微电网并网、离网的两种工作状态,提出了采用同步逆变器技术的微电网无缝切换策略。
在Matlab/Simulink中搭建了仿真模型,验证了所提出无缝切换策略的有效性。
2同步逆变器的原理2.1同步逆变器的控制原理同步逆变器由物理结构和控制结构两部分构成。
物理结构上,由图1所示,同步逆变器由直流侧电源、三相全桥拓扑、LC滤波器、并/离网切换装置构成。
图中U dc为直流侧电压,e abc为三相全桥拓扑桥臂处的电压可等效为同步机的内电势,C为滤波电容、L为滤波电感模拟同步机的定子电感,L的等效电阻及功率器件的寄生电阻模拟同步机的定子电阻,U Cabc为LC滤波器中电容电压等效为同步发电机机端电压。
进而同步逆变器的电磁方程表示为:L di abc dt=e abc-U Cabc-Ri abc(1)式中:i abc为同步逆变器滤波电感中的电流,R为同步逆变器电阻。
基于BP_神经网络的切削ZL114A_铝合金表面粗糙度预测
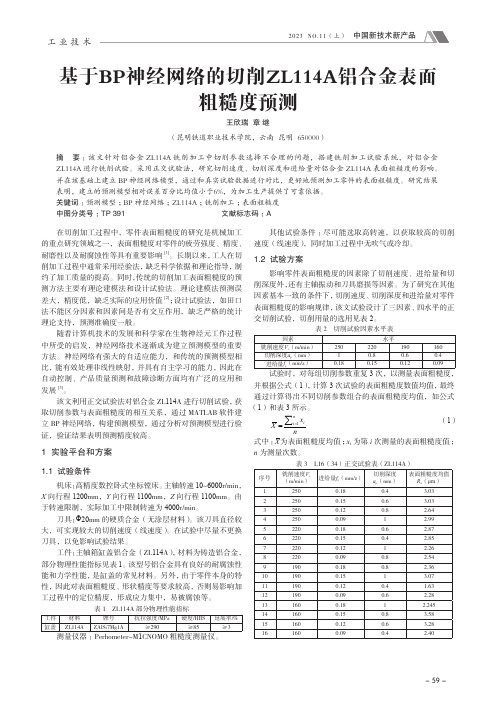
100
net.trainParam.mc=0.4;% 设置动量因子
net=train(net,inputn,outputn);% 训练函数
预测流程如图 2 所示。
最佳验证性能是第1571轮的0.030627
训练 验证 最佳 目标
均方误差(mse)
3 预测和误差分析
10-2
在 MATLAB 中根据流程编写程序,设置目标误
1 实验平台和方案
1.2 试验方案
影响零件表面粗糙度的因素除了切削速度、进给量和切
削深度外,还有主轴振动和刀具磨损等因素。为了研究在其他
因素基本一致的条件下,切削速度、切削深度和进给量对零件
表面粗糙度的影响规律,该文试验设计了三因素、四水平的正
交切削试验,切削用量的选用见表 2。
表 2 切削试验因素水平表
分别为第 k+1 次的权值和阈值的改变量 ;gw(k) 和 gb(k)为当前性能函数对权值和阈值的梯度 ; ak 为学习率;mc 为动量因子(动量系数),取值范 围为 [0,1] ;∆w(k-1)和 ∆b(k-1)为第 k-1 次
输入层
隐含层
输出层
的权值和阈值的该变量。
图 1 BP 神经网络结构图
- 60 -
工业技术
2023 NO.11(上) 中国新技术新产品
基于BP神经网络的切削ZL114A铝合金表面
粗糙度预测
王欣瑞 章 继 (昆明铁道职业技术学院,云南 昆明 650000)
摘 要 :该文针对铝合金 ZL114A 铣削加工中切削参数选择不合理的问题,搭建铣削加工试验系统,对铝合金
ZL114A 进行铣削试验。采用正交试验法,研究切削速度、切削深度和进给量对铝合金 ZL114A 表面粗糙度的影响。
半潜式支持平台系泊系统的设计方法及应用
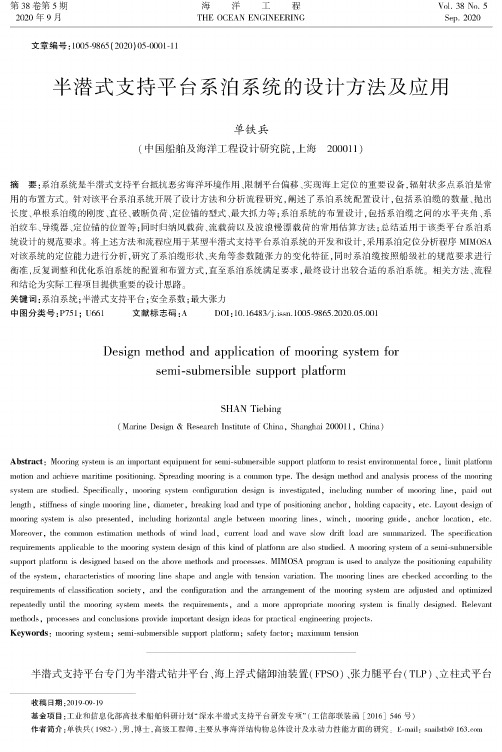
第38卷第5期海洋工程Vol.38No.5 2020年9月THE OCEAN ENGINEERING Sep.2020文章编号:1005-9865(2020)05-0001-11半潜式支持平台系泊系统的设计方法及应用单铁兵(中国船舶及海洋工程设计研究院,上海200011)摘要:系泊系统是半潜式支持平台抵抗恶劣海洋环境作用、限制平台偏移、实现海上定位的重要设备,辐射状多点系泊是常用的布置方式。
针对该平台系泊系统开展了设计方法和分析流程研究,阐述了系泊系统配置设计,包括系泊缆的数量、抛岀长度、单根系泊缆的刚度、直径、破断负荷、定位锚的型式、最大抓力等;系泊系统的布置设计,包括系泊缆之间的水平夹角、系泊绞车、导缆器、定位锚的位置等;同时归纳风载荷、流载荷以及波浪慢漂载荷的常用估算方法;总结适用于该类平台系泊系统设计的规范要求。
将上述方法和流程应用于某型半潜式支持平台系泊系统的开发和设计,采用系泊定位分析程序MIMOSA 对该系统的定位能力进行分析,研究了系泊缆形状、夹角等参数随张力的变化特征,同时系泊缆按照船级社的规范要求进行衡准,反复调整和优化系泊系统的配置和布置方式,直至系泊系统满足要求,最终设计岀较合适的系泊系统。
相关方法、流程和结论为实际工程项目提供重要的设计思路。
关键词:系泊系统;半潜式支持平台;安全系数;最大张力中图分类号:P751;U661文献标志码:A D0I:10.16483/j.issn.1005-9865.2020.05.001Design method and application of mooring system forsemi-submersible support platformSHAN Tiebing(Marine Design&Research Institute of China,Shanghai200011,China)Abstract:Mooring system is an important equipment for semi-submersible support platform to resist environmental force,limit platform motion and achieve maritime positioning.Spreading mooring is a common type.The design method and analysis process of the mooring system are studied.Specifically,mooring system configuration design is investigated,including number of mooring line,paid out length,stiffness of single mooring line,diameter,breaking load and type of positioning anchor,holding capacity,yout design of mooring system is also presented,including horizontal angle between mooring lines,winch,mooring guide,anchor location,etc. Moreover,the common estimation methods of wind load,current load and wave slow drift load are summarized.The specification requirements applicable to the mooring system design of this kind of platform are also studied.A mooring system of a semi-submersible support platform is designed based on the above methods and processes.MIMOSA program is used to analyze the positioning capability of the system,characteristics of mooring line shape and angle with tension variation.The mooring lines are checked according to the requirements of classification society,and the configuration and the arrangement of the mooring system are adjusted and optimized repeatedly until the mooring system meets the requirements,and a more appropriate mooring system is finally designed.Relevant methods,processes and conclusions provide important design ideas for practical engineering projects.Keywords:mooring system;semi-submersible support platform;safety factor;maximum tension半潜式支持平台专门为半潜式钻井平台、海上浮式储卸油装置(FPSO)、张力腿平台(TLP)、立柱式平台收稿日期:2019-09-19基金项目:工业和信息化部高技术船舶科研计划“深水半潜式支持平台研发专项”(工信部联装函[2016]546号)作者简介:单铁兵(1982-),男,博士,高级工程师,主要从事海洋结构物总体设计及水动力性能方面的研究二E-mail:snailstb@2海洋工程第38卷(SPAR)以及半潜式生产平台等海上油气勘探、处理平台提供人员居住、娱乐、物资补给和工程辅助等作业支持,不仅可为平台上工作人员提供一个舒适的居住坏境,在紧急情况下还能作为紧急避难场所以保证人员安全。
基于AMESim、MATLAB_与LabVIEW_的联合仿真虚拟平台技术

第 22卷第 10期2023年 10月Vol.22 No.10Oct.2023软件导刊Software Guide基于AMESim、MATLAB与LabVIEW的联合仿真虚拟平台技术董壮壮,王兆强,孙令涛,陆阳钧(上海工程技术大学机械与汽车工程学院,上海 201620)摘要:针对AMESim和MATLAB/Simulink的机电液系统联合仿真过程中参数设置较为繁琐、仿真结果可视化效果不够直观等问题,基于FMI标准化接口和ActiveX技术,利用LabVIEW进行人机交互界面设计与数据交互,研究了一种可定制化、参数设置集中化且仿真结果可视化的仿真虚拟平台技术。
初步应用实验结果表明,该虚拟平台可简便地对联合仿真模型进行参数设置与数据交互,结果准确、仿真效果直观,且仿真报告可自动化输出,有利于提高工作效率。
关键词:联合仿真;人机交互;多物理域;虚拟平台;数据交互DOI:10.11907/rjdk.231493开放科学(资源服务)标识码(OSID):中图分类号:TP391.9 文献标识码:A文章编号:1672-7800(2023)010-0042-07Joint Simulation Virtual Platform Technology Based on AMESim,MATLAB and LabVIEWDONG Zhuangzhuang, WANG Zhaoqiang, SUN Lingtao, LU Yangjun(School of Mechanical and Automotive Engineering, Shanghai University of Engineering Science, Shanghai 201620, China)Abstract:In response to the problem of cumbersome parameter settings and insufficient visualization of simulation results in the joint simu⁃lation process of AMESim and MATLAB/Simulink electromechanical hydraulic systems,a customizable,centralized parameter settings,and visualized simulation results simulation virtual platform technology was studied using LabVIEW based on the standardized interface of FMI (Functional Mock up Interface) and ActiveX technology for human-machine interaction interface design and data exchange. The pre⁃liminary application experimental results showed that the virtual platform can easily set parameters and interact with data for joint simula⁃tion models, with accurate results and intuitive simulation effects. The simulation report can be automatically output, which is conducive to improving work efficiency.Key Words:joint simulation; human-computer interaction; multi-physical domain; virtual platform; data interaction0 引言目前,国内外仿真软件种类越来越多,仿真技术已经广泛地应用于汽车制造[1-4]、工程机械[5]、航空航天[6-7]等领域。
基于特征模型的永磁同步直线电机自适应控制
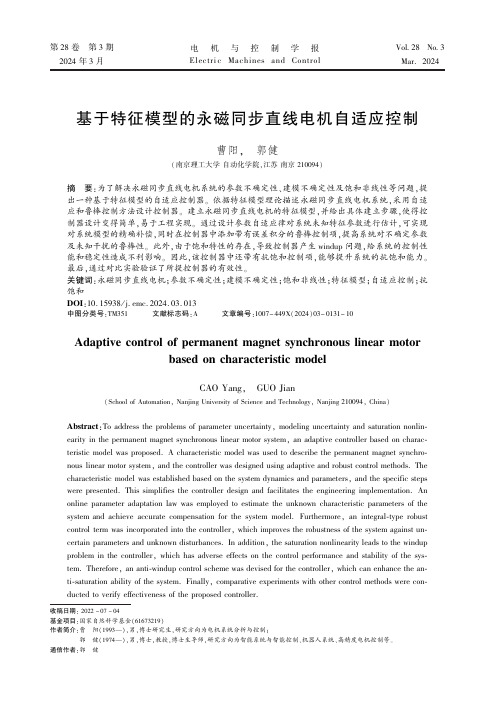
第28卷㊀第3期2024年3月㊀电㊀机㊀与㊀控㊀制㊀学㊀报Electri c ㊀Machines ㊀and ㊀Control㊀Vol.28No.3Mar.2024㊀㊀㊀㊀㊀㊀基于特征模型的永磁同步直线电机自适应控制曹阳,㊀郭健(南京理工大学自动化学院,江苏南京210094)摘㊀要:为了解决永磁同步直线电机系统的参数不确定性㊁建模不确定性及饱和非线性等问题,提出一种基于特征模型的自适应控制器㊂依据特征模型理论描述永磁同步直线电机系统,采用自适应和鲁棒控制方法设计控制器㊂建立永磁同步直线电机的特征模型,并给出具体建立步骤,使得控制器设计变得简单,易于工程实现㊂通过设计参数自适应律对系统未知特征参数进行估计,可实现对系统模型的精确补偿,同时在控制器中添加带有误差积分的鲁棒控制项,提高系统对不确定参数及未知干扰的鲁棒性㊂此外,由于饱和特性的存在,导致控制器产生windup 问题,给系统的控制性能和稳定性造成不利影响㊂因此,该控制器中还带有抗饱和控制项,能够提升系统的抗饱和能力㊂最后,通过对比实验验证了所提控制器的有效性㊂关键词:永磁同步直线电机;参数不确定性;建模不确定性;饱和非线性;特征模型;自适应控制;抗饱和DOI :10.15938/j.emc.2024.03.013中图分类号:TM351文献标志码:A文章编号:1007-449X(2024)03-0131-10㊀㊀㊀㊀㊀㊀㊀㊀㊀㊀㊀㊀㊀㊀㊀㊀㊀㊀㊀㊀㊀㊀㊀㊀㊀㊀㊀㊀㊀㊀㊀㊀㊀㊀㊀㊀㊀㊀㊀㊀㊀㊀㊀㊀㊀㊀㊀㊀㊀㊀㊀㊀㊀㊀㊀㊀㊀㊀㊀㊀㊀㊀㊀㊀㊀㊀㊀㊀㊀㊀㊀㊀㊀㊀㊀㊀㊀㊀㊀㊀㊀㊀㊀㊀㊀㊀㊀㊀㊀㊀㊀㊀㊀㊀㊀㊀㊀㊀㊀㊀㊀㊀㊀㊀㊀㊀收稿日期:2022-07-04基金项目:国家自然科学基金(61673219)作者简介:曹㊀阳(1993 ),男,博士研究生,研究方向为电机系统分析与控制;郭㊀健(1974 ),男,博士,教授,博士生导师,研究方向为智能系统与智能控制㊁机器人系统㊁高精度电机控制等㊂通信作者:郭㊀健Adaptive control of permanent magnet synchronous linear motorbased on characteristic modelCAO Yang,㊀GUO Jian(School of Automation,Nanjing University of Science and Technology,Nanjing 210094,China)Abstract :To address the problems of parameter uncertainty,modeling uncertainty and saturation nonlin-earity in the permanent magnet synchronous linear motor system,an adaptive controller based on charac-teristic model was proposed.A characteristic model was used to describe the permanent magnet synchro-nous linear motor system,and the controller was designed using adaptive and robust control methods.The characteristic model was established based on the system dynamics and parameters,and the specific steps were presented.This simplifies the controller design and facilitates the engineering implementation.An online parameter adaptation law was employed to estimate the unknown characteristic parameters of the system and achieve accurate compensation for the system model.Furthermore,an integral-type robust control term was incorporated into the controller,which improves the robustness of the system against un-certain parameters and unknown disturbances.In addition,the saturation nonlinearity leads to the windup problem in the controller,which has adverse effects on the control performance and stability of the sys-tem.Therefore,an anti-windup control scheme was devised for the controller,which can enhance the an-ti-saturation ability of the system.Finally,comparative experiments with other control methods were con-ducted to verify effectiveness of the proposed controller.Keywords:permanent magnet synchronous linear motor;friction nonlinearity;saturation nonlinearity;ar-mature mass variation;characteristic model;adaptive control;anti-windup0㊀引㊀言相比于旋转同步电机,永磁同步直线电机(per-manent magnet synchronous linear motor,PMSLM)具有更高的推力密度和更快的动态响应,特别适用于对速度和精度要求较高的场合,已被广泛应用在高精密加工㊁轨道交通传输等现代工业领域[1-2]㊂但是由于采用直接驱动方式,PMSLM控制系统对参数摄动及扰动等因素变得更加敏感[3],这会严重影响系统的控制性能㊂因此,保证PMSLM系统的高精度跟踪性能与抗扰动能力十分重要,对提高机床加工精度㊁提升交通传输效率具有重要的意义㊂针对PMSLM系统的高精度跟踪问题,国内外已有众多学者对其进行了研究㊂文献[4]设计了一种带模型参考自适应观测器的预测电流控制策略,经过实验验证该控制策略可以实现对速度进行在线准确辨识,进而提高电流的跟踪性能㊂文献[5]利用扩张状态观测器和非线性状态误差反馈对PMSLM的自抗扰控制器进行优化,提高了系统的动态响应性能和抗干扰能力㊂文献[6]提出一种基于周期性扰动学习的自适应滑模控制方法,采用滑模控制确保PMSLM系统对不确定性因素具有较强的鲁棒性㊂文献[7]在系统模型反馈线性化的基础上,将Hɕ鲁棒控制方法与D-K迭代法相结合,提高了系统对不确定性因素影响的抑制能力㊂姚斌等[8]提出一种自适应鲁棒控制方法,所开发的控制器成功应用在多种控制系统中[9-11]㊂为了解决非光滑饱和非线性的影响,文献[12]构造了一种新的近似饱和模型,该模型能够以任意规定的精度平滑地逼近实际饱和㊂此外,通过添加积分器技术,使得控制器可以消除与表面误差和边界层误差有关的耦合项㊂但是该方法在控制器的设计中需要对虚拟控制量重复微分,如果系统模型阶数高,会增加设计的复杂性㊂文献[13]提出一种考虑LuGre 摩擦的自适应鲁棒控制方法,针对陀螺框架伺服系统未知惯量和阻尼系数㊁LuGre摩擦参数不确定性及未知外部干扰上界,设计参数更新律对其进行估计,该控制律提高了系统的跟踪精度并通过仿真结果验证了所提方法的有效性㊂但该方法需要被控对象的精确数学模型,另外估计的未知参数过多,多个自适应参数需要反复调试,增加了实际应用时的难度㊂自适应鲁棒控制可以估计系统未知参数,但如果系统模型复杂㊁未知参数多㊁某些状态不可测时,控制器的设计将面临巨大挑战㊂针对这些问题,吴宏鑫院士等[14-15]提出特征建模的思想,特征模型一般用一阶或二阶差分方程/微分方程来描述,有关信息都压缩到几个特征参数中,并不丢失原有的信息㊂特征模型建立的形式比原对象动力学方程简单,为实际复杂系统的建模问题提供了一条途径㊂文献[16]基于永磁同步电机的特征模型,设计一个以非线性黄金分割自适应控制为主的控制方案㊂通过安排过渡过程和特征模型参数的在线辨识,该控制方案实现了控制器参数的在线自适应调节㊂文献[17]将特征建模方法推广到具有惯性变化的齿轮传动伺服系统中,设计了一个自适应二阶离散终端滑模控制器,并实现了有限时间有界性㊂然而上述基于特征模型所设计的控制器没有进行抗饱和(anti-windup)研究㊂windup现象是指由于被控对象的输入限制,使得被控对象的实际输入与控制器的输出不等,引起系统闭环响应变差(如超调变大,调节时间变长,甚至使系统失去稳定)的现象㊂实际的PMSLM是个物理限制系统,转速控制器的输出必须限定在一定的范围内,使得实际电机的控制输入量不能大于一个预先设定值㊂当控制器输出受到饱和限制时,特别是含有积分项的控制信号仍然增加时,就会出现windup现象,使实际闭环系统的性能下降,因此对PMSLM系统设计抗饱和控制是有必要的[18-19]㊂基于上述分析,针对PMSLM系统存在的参数不确定性㊁建模不确定性及饱和非线性等问题,提出一种基于特征模型的抗饱和自适应鲁棒控制器(an-ti-windup adaptive robust control based on characteris-tic model,AARC)㊂利用特征模型简化PMSLM系统的描述,并对其进行验证㊂然后,设计一种基于参数投影的自适应律,实现对系统模型的在线补偿㊂同时,将系统的不确定参数和未知干扰视为集总的干231电㊀机㊀与㊀控㊀制㊀学㊀报㊀㊀㊀㊀㊀㊀㊀㊀㊀㊀㊀㊀㊀第28卷㊀扰项,引入误差积分的鲁棒控制项进行抑制㊂此外,为了解决积分环节可能引起的windup 现象,加入抗饱和控制项,提高系统的抗饱和能力㊂最后,基于Lyapunov 函数证明闭环系统的稳定性,并通过实验验证所提控制器的有效性和鲁棒性㊂1㊀PMSLM 的特征建模与验证1.1㊀PMSLM 模型PMSLM 的运动方程为m d y d t =3π2τn p i q [ψf+(L d -L q )i d ]-F fric (y )㊂(1)式中:m 为等效质量;ψf 为磁链;y 为动子速度;i d ㊁i q 分别为d㊁q 轴电流;τ为极距;n p 为极对数;L d ㊁L q 分别为d㊁q 轴电感;F fric (y )为摩擦力㊂由式(1)可得y ㊃㊃=1.5πn p mτ[ψf i ㊃q +(L d -L q )(i ㊃d i q +i ㊃q i d )]- F fric y㊃m y㊂(2)设PMSLM 的采样周期为T ,将式(2)离散化可得㊀y (k +1)-2y (k )+y (k -1)T 2=[1.5πmTτn p ψf +1.5n p (L d -L q )i d (k )mTτ]i q (k )-[1.5πmTτn p ψf +1.5n p (L d -L q )i d (k )mTτ]i q (k -1)+1.5πn p (L d -L q )i q (k )mTτ[i d (k )-i d (k -1)]-1mT F firc (y (k )-y (k -1))y ㊂(3)在式(3)两边同乘T 2,可以重新写为y (k +1)=[1.5πmτn p ψfT +1.5n p (L d -L q )i d (k )Tmτ]i q (k )+[2-1m F firc T v ]y (k )+[1m F firc T v-1]y (k -1)+[1.5n p (L d -L q )i d (k )T mτ-1.5πmτn p ψfT ]i q (k -1)+1.5πn p (L d -L q )i q (k )Tmτˑ[i d (k )-i d (k -1)]=β1(k )i q (k )+α1(k )y (k )+α2(k )y (k -1)+Δ(k )㊂(4)式中:y (k )为系统输出;i q (k )为系统输入;α1㊁α2㊁β1为系统的特征参数,定义为:α1(k )=[2-1m F firc Tv];α2(k )=[1m F firc Tv -1];β1(k )=[1.5πmτn p ψf T +1.5n p (L d -L q )i d (k )T mτ]㊂üþýïïïïïïï(5)Δ(k )表示集总未知非线性函数,包括建模误差和未知扰动,定义为Δ(k )=[1.5n p (L d -L q )i d (k )Tmτ-1.5πmτn p ψfT ]i q (k -1)+1.5πn p (L d -L q )i q (k )Tmτˑ[i d (k )-i d (k -1)]㊂(6)通过式(4)可以看出,特征模型是将模型结构的模型不确定性和参数摄动等不确定信息压缩成几个未知的特征参数,使其与实际模型等价而不是近似㊂使用特征建模不仅能简化控制器设计,而且更利于工程应用㊂1.2㊀特征模型验证特征模型验证过程如图1所示㊂首先,分别给予PMSLM 系统和特征模型相同的输入信号u ㊂然后,采样PMSLM 的输入输出信号,采用传统投影梯算法[16]在线辨识特征参数,并计算特征模型输出㊂最后,通过比较特征模型输出y ^与PMSLM 系统输出y ,得到误差e 0㊂将输入设为1sin(2.09t )A 的正弦信号,并且设PMSLM 的采样频率为80μs㊂特征模型验证结果如图2所示㊂实验结果表明,在相同的控制输入作用下,特性模型输出与实际系统输出的误差很小,说明特征模型可以很好地描述PMSLM 系统的输入输出特征,可以利用该特征模型来设计控制器㊂331第3期曹㊀阳等:基于特征模型的永磁同步直线电机自适应控制图1㊀特征模型验证Fig.1㊀Verification block diagram of characteristicmodel图2㊀特征模型验证结果Fig.2㊀Verification results of characteristic model2㊀非线性自适应控制器设计2.1㊀自适应控制设计针对PMSLM 系统中存在的参数不确定㊁饱和非线性以及外界干扰,设计基于特征模型的自适应鲁棒控制律,对系统的不确定性和干扰进行估计和补偿,实现PMSLM 的速度跟踪控制㊂设计的自适应控制结构如图3所示,控制器包括模型补偿项u a ㊁线性反馈项u s1㊁积分鲁棒控制律u s2和抗饱和控制律k cw η,i qmax =0.03㊁i qmin =-0.03为饱和限制上下界㊂图3㊀自适应抗饱和控制结构框图Fig.3㊀Structure diagram of adaptive anti-windupcontroller将特征模型写成如下二阶时变辨识模型:y (k +1)=φ(k )T θ(k )㊂(7)式中:φ(k )=[y (k )y (k -1)u (k )]T ;θ(k )=[α1(k )α2(k )β1(k )]T ㊂在下面的部分中,㊃j 表示向量㊃的第j 个分量,并且针对2个向量的运算 < 是根据向量的相应元素来执行的㊂用θ^表示θ的估计值,θ~表示估计误差(θ~=θ^-θ)㊂结合式(7),一种不连续投影可以定义为proj θ^j {㊃j }=0,if θ^j =θj max and㊃j >0;0,if θ^j =θj min and㊃j <0;㊃j ,otherwise㊂ìîíïïïï(8)式中:j =1,2,3;proj θ^j{㊃j }可以保证估计参数在有界凸闭集D s 内㊂为保证参数估计值的有界性,设计未知参数估计自适应律为:θn (k )=θ^(k -1)+Γτλ+φT(k -1)φ(k -1);θ^(k )=proj θ^(θn(k ))㊂}(9)式中:Γ>0,λ>0为待设计的可调参数;τ为待合成的自适应函数;θ^(k )为系统参数θ(k )的估计值,利用基于不连续投影的参数自适应律可以估计出未知的特征参数α1㊁α2㊁β1㊂特征模型式(4)可被重写为y (k +1)=[α^1(k )-α~1(k )]y (k )+[α^2(k )-α~2(k )]y (k -1)+[β^1(k )-β~1(k )]u (k )+β1η(k )+Δ(k )㊂(10)式中α~1(k )=α^1(k )-α1(k ),α~2(k )=α^2(k )-α2(k ),β~1(k )=β^1(k )-β1(k )为辨识误差㊂所以式(10)可以改写为431电㊀机㊀与㊀控㊀制㊀学㊀报㊀㊀㊀㊀㊀㊀㊀㊀㊀㊀㊀㊀㊀第28卷㊀y(k+1)=α^1(k)y(k)+α^2(k)y(k-1)+β^1(k)u(k)+β1η+Δ(k)-θ~(k)φ(k)㊂(11)其中θ~(k)φ(k)=α~1(k)y(k)+α~2(k)y(k)+β~1(k)u(k)表示模型估计误差㊂假设1:从工程实践中可知,对于稳定对象,参数不确定性和不确定非线性的程度已知,即θɪΩθ {θ:θminɤθɤθmax};ΔɪΩd {Δ:|Δ(k)-Δ(k-1)|ɤδd(k)}㊂}(12)式中:θmin=[θ1min, ,θ3min]T;θmax=[θ1max, ,θ3max]T;δd是已知的㊂控制目标是设计自适应控制器使得系统的输出y(k)跟踪期望输出y d(k),定义跟踪误差函数为e(k)=y(k)-y d(k)㊂(13)定义s(k)为s(k)=e(k)-k1e(k-1)㊂(14)其中0<k1<1为待设计的可调参数㊂所以有s(k+1)=e(k+1)-k1e(k)㊂(15)自适应抗饱和控制律可以设计为:u(k)=1β^1(k)[u a(k)+u s1(k)+u s2(k)];u a(k)=-α^1(k)y(k)-α^2(k)y(k-1)+ y d(k+1)+k1e(k)-k cwη;u s1(k)=k s s(k);u s2(k)=-E1(k)㊂üþýïïïïïïïï(16)式中:k cwȡ β1 max为抗饱和反馈增益;|k s|<1是待设计的可调参数;E1(k)表达式为E1(k)=E1(k-1)+k s k2s(k-1)+βsat(s(k-1))㊂(17)式中:k2>0为可调系数;sat(㊃)为饱和函数㊂设计参数自适应律τ=s(k)φ(k-1),将式(9)改写为:θn(k)=θ^(k-1)+Γs(k)φ(k-1)λ+φT(k-1)φ(k-1);θ^(k)=projθ^(θn(k))㊂üþýïïï(18) 2.2㊀稳定性分析定理1:对于特征模型式(10)所描述的PMSLM,所有信号都是有界的㊂采用自适应控制律式(16)和参数更新规律式(18),能使闭环系统的跟踪误差渐近收敛至0㊂证明:将式(16)代入式(10)中,并结合式(18)可得s(k+1)=[y(k+1)-y d(k+1)]-k1e(k)=α^1(k)y(k)+α^2(k)y(k-1)+β^1(k)u(k)-α~1(k)y(k)-α~2(k)y(k-1)-β~1(k)u(k)+Δ(k)=-θ~T(k)φ(k)+β1η(k)-k cwη(k)+k s s(k)-E1(k)+Δ(k)㊂(19)取k cwȡ β1 max,然后对式(19)进行差分可得s(k+1)-s(k)=-(θ~T(k)φ(k)-θ~T(k-1)φ(k-1))+k s(s(k)-s(k-1))-(E1(k)-E1(k-1))+Δ(k)-Δ(k-1)㊂(20)考虑到采样周期很小,通过线性外推法预测可知s(k+1)=2s(k)-s(k-1)㊂(21)构建Lyapunov函数为V(k)=s(k)λ+φT(k-1)φ(k-1)+θ~(k) 2Γ㊂(22)首先考虑式(22)的第2项,根据投影参数自适应律式(18)可得θ~(k) 2ɤ θn(k)-θ(k) 2= θ~(k-1) 2+2Γs(k)φT(k-1)θ~(k-1)λ+ φ(k-1)Tφ(k-1) +(Γs(k))2 φ(k-1) 2(λ+ φ(k-1) 2)2ɤ2Γs(k)φT(k-1)θ~(k-1)λ+ φ(k-1) 2+Γ2s2(k)λ+ φ(k-1) 2+ θ~(k-1) 2㊂(23)将式(16)㊁式(20)和式(21)代入式(23)可得 θ~(k) 2- θ~(k-1) 2ɤ2Γs(k)[-(s(k)-s(k-1))+k s(s(k-1)-s(k-2))]λ+ φ(k-1) 2+ 2Γs(k)[-θ~T(k-2)φ(k-2)+k s k2s(k-1)-βsign(s(k-1))]λ+ φ(k-1) 2+531第3期曹㊀阳等:基于特征模型的永磁同步直线电机自适应控制2Γs (k )[(Δ(k -1)-Δ(k -2)]λ+ φ(k -1) 2+Γ2s 2(k )λ+ φ(k -1) 2㊂(24)选取βȡ| θM φmax +δd |,进一步可得 θ~(k ) 2- θ~(k -1) 2ɤ2Γs (k )(k s -1)(s (k )-s (k -1))+2Γk s k 2s (k )s (k -1)λ+ φ(k -1) 2+Γ2s 2(k )λ+ φ(k -1) 2㊂(25)引理1[20]:(Young 不等式)假设a ㊁b 为非负实数,P >1,1p +1q =1,那么ab ɤa p p +b pq ,当且仅当a p=b q时,等号成立㊂根据引理1可得:2s (k )s (k -1)ɤ s (k ) 2+ s (k -1) 2; θ~(k ) 2- θ~(k -1) 2ɤ-Γ(3-3k s -k s k 2)s 2(k )λ+ φ(k -1) 2+Γ(k s +k s k 2-1)s 2(k -1)λ+ φT (k -1) 2㊂üþýïïïïïï(26)对Lyapunov 函数式(22)进行差分,并联立式(26)可得ΔV (k )=V (k )-V (k -1)ɤs 2(k )λ+ φT (k -1) 2-s 2(k -1)λ+ φT (k -2) 2+-(3-3k s -k s k 2)s 2(k )λ+ φ(k -1) 2+(k s +k s k 2-1)s 2(k -1)λ+ φT (k -1) 2+Γs 2(k )λ+ φT (k -1) 2ɤ-(2-3k s -k s k 2-Γ)s 2(k )λ+ φT (k -1) 2+(k s +k s k 2-1)s 2(k -1)λ+ φT (k -1) 2-s 2(k -1)λ+ φT (k -2) 2ɤ-As 2(k )-Bs 2(k -1)㊂(27)式中:A =2-3k s -k s k 2-Γλ+ φT (k -1) 2;B =1λ+ φT (k -2) 2-1-k s -k s k 2λ+ φT (k -1) 2㊂通过选取合适的参数k s ㊁k 2㊁Γ㊁λ使得A >0,B >0㊂根据式(27),对Δ(k )从1到k 求和可得ðki =1[As 2(k )+Bs 2(k -1)]ɤV (1)-V (k )ɤV (1)㊂(28)当k ңɕ时,As 2(k )+Bs 2(k -1)ȡ0,由于φ(k ) 有界,可知lim k ңɕ|s (k )|=0㊂(29)根据式(29)可知,∃N ,当k >N 时,有|s (k )|ɤ0㊂(30)由式(15)可得|e (k )|ɤ|k 1||e (k -1)|+|s (k )|ɤ|k 1|k -N|e (N )|+|k 1|k -N -1|s (N +1)|+ +s (k )ɤ|k 1|k -N|e (N )|+0㊂(31)因为|k s |<1,所以有lim k ңɕsup |e (k )|=0㊂(32)3㊀实验结果比较为了说明上述方法的可行性和有效性,在实验室建立一个验证平台如图4所示,PMSLM 的基本参数列于表1㊂该平台由MOSFET 三相逆变桥㊁磁栅尺㊁相电流采样电路㊁TMS320F28062(DSP)及外围电路㊁IR2181S 驱动电路㊁系统电源电路组成㊂此外,为了模拟不同的工作条件,对直线电机的动子进行了调整㊂通过直接在动子上安装标准化铁块,准确地改变其质量m ,以模拟不同的惯性效应㊂图4㊀PMSLM 实验平台Fig.4㊀PMSLM experimental platform631电㊀机㊀与㊀控㊀制㊀学㊀报㊀㊀㊀㊀㊀㊀㊀㊀㊀㊀㊀㊀㊀第28卷㊀表1㊀PMSLM 的基本参数Table 1㊀Parameters of PMSLM㊀㊀参数数值极对数n p7极距τ/mm(180ʎ)12d 轴电感L d /mH 8q 轴电感L q /mH 8永磁体磁链ψf /Wb0.61PMSLM 矢量控制系统框架如图5所示㊂它由PMSLM㊁空间矢量脉宽调制(space vector pulse widthmodulation,SVPWM)模块㊁Park 和Clark 坐标变换㊁电压源逆变器㊁电流调节器和速度控制器组成㊂本文设计一种速度控制器,电流控制器采用PI 控制㊂图5㊀矢量控制总体结构框图Fig.5㊀Overall structure diagram of vector control为了验证所提控制器的可行性和有效性,本文对以下3种控制器进行比较㊂1)AARC㊂本文设计的抗饱和自适应鲁棒控制器参数设置如下:k 1=0.15,k 2=0.0006,k s =0.1,β=0.04,k cw =0.1,Γ=0.05,λ=0.995,θ^(0)=[1.9,-0.9,0.00001]T ㊂2)抗饱和自适应控制器(anti-windup adaptivecontrol based on characteristic model,AAC)㊂未添加鲁棒项u s2的抗饱和自适应控制器,其他参数与AARC 一致㊂3)抗饱和PID 控制器(anti-windup proportional-integral-differential,APID)㊂控制器的增益设置为k p =150,k i =1,k d =0,k cw =0.1㊂此外,将使用跟踪误差的最大值㊁平均值和标准差来衡量每个控制算法的质量,定义如下:1)最大跟踪误差的绝对值为M e =max i =1, ,N{|e (i )|}㊂(33)2)平均跟踪误差定义为μ=1N ðNi =1|e (i )|㊂(34)3)跟踪误差的标准差为δ=1N ðNi =1[|e (i )|-μ]2㊂(35)其中N 是所记录的数字信号的个数㊂首先将给定速度设置为y d =0.56sin(3.14t)m/s㊂系统跟踪结果如图6所示,性能指标如表2所示㊂从这些实验结果可以看出,所提出的AARC 控制器在瞬态和最终跟踪误差方面优于其他两种控制器,因为AARC 采用了基于参数自适应的补偿和鲁棒控制项,可以同时处理参数和未建模不确定性㊂虽然AAC 中也包含参数自适应,但对于建模的不确定性和未知扰动的抑制效果不佳㊂通过表2可以看出,AARC 添加鲁棒项后各种误差指标会比AAC 小,验证了鲁棒控制项u s2的有效性㊂在3种控制器中,线性抗饱和PID 的误差指标最差,达到了AARC 的2倍以上,这说明基于非线性模型的控制器设计方法具有更大的优势㊂图6㊀无铁块情况下PMSLM 的跟踪结果Fig.6㊀Tracking results of PMSLM without iron表2㊀最后两个周期的性能指标Table 2㊀Performance indexes during the last two cycles控制方法M e /(m /s)μ/(m /s)δ/(m /s)APID 0.055420.013360.00971AAC0.026890.008100.00572AARC 0.025220.006000.00490731第3期曹㊀阳等:基于特征模型的永磁同步直线电机自适应控制为了进一步验证控制器对参数变化的自适应能力,设定了不同的动子质量来进行实验㊂给PMSLM 的动子上添加1.33kg 的铁块㊂系统跟踪结果如图7所示,表3列出了最后两个周期的性能指标㊂从图7可以看出,使用AARC 控制方法的控制系统,在面对动子质量变化时,其反应速度快,并且波动较小㊂从表3可知,APID 的最大跟踪误差没有增大,意味着APID 中存在大的积分增益对该扰动也有一定的抑制效果㊂但与上一个实验情况相比,APID 的μ和δ指标增大明显,仍然比其他2个控制器差㊂适当的参数自适应在一定程度上也可以削弱动子质量变化给系统带来的参数不确定性影响,就像AAC 那样㊂AARC 的各项误差指标是3个控制器中最好的,再次证明了该控制器的有效性㊂图7㊀铁块质量为1.33kg 时PMSLM 的跟踪结果Fig.7㊀Tracking results of PMSLM when iron massis 1.33kg表3㊀最后两个周期的性能指标Table 3㊀Performance indexes during the last two cycles控制方法M e /(m /s)μ/(m /s)δ/(m /s)APID 0.043890.015370.01061AAC0.029620.008440.00605AARC 0.025320.005980.00496最后将动子上的铁块增加到2.64kg,此时PMSLM 受到的摩擦非线性和扰动进一步增大,3个控制器的跟踪性能都有所变差㊂实验结果如图8所示,误差指标见表4㊂在这个测试用例中,APID 中的跟踪误差抖动变大,而AARC 的跟踪误差则相当平滑㊂APID 控制器表现出最差的跟踪性能,最大跟踪误差为0.094,表明APID 在该跟踪任务中已经达到了其局限性㊂另外,即使在增大动子质量情况下,所提出的AARC 控制器仍然可以对模型进行补偿并衰减未建模的扰动,从而在所有比较的控制器中达到最好的跟踪性能㊂图8㊀铁块质量增加到2.64kg 情况下PMSLM 的跟踪结果Fig.8㊀Tracking results of PMSLM when the mass ofiron is increased to 2.64kg 表4㊀最后两个周期的性能指标Table 4㊀Performance indexes during the last two cycles控制方法M e /(m /s)μ/(m /s)δ/(m /s)APID 0.093700.027090.01934AAC0.034620.008410.00643AARC 0.028870.005860.005054㊀结㊀论本文针对PMSLM 系统提出一种基于特征模型的自适应控制方法,该方法能够有效地解决PMSLM 系统的参数不确定性㊁建模误差和外部干扰等问题㊂首先利用二阶变差分方程对PMSLM 系统进行简化831电㊀机㊀与㊀控㊀制㊀学㊀报㊀㊀㊀㊀㊀㊀㊀㊀㊀㊀㊀㊀㊀第28卷㊀建模,然后设计了一种基于特征模型的自适应控制器,仅利用系统的输入和输出信号,实现了对PMSLM系统的精确速度跟踪控制㊂为了提高系统的鲁棒性和抗饱和能力,还引入了鲁棒补偿项和抗饱和控制项,并严格证明了闭环系统的稳定性㊂最后,通过实验结果验证了所提控制方法的有效性㊂本文控制器的参数是固定的,需要通过反复调试来确认㊂当实验条件和环境发生改变时,可能导致参数不一定是最优的㊂因此,在未来工作中将考虑进一步研究控制器参数的自动调整技术[21],采用自学习的方法来替代控制器中参数的人工调整部分㊂参考文献:[1]㊀龚夕霞,李焱鑫,卢琴芬.模块化永磁直线同步电机考虑制造公差的推力鲁棒性优化[J].电工技术学报,2024,39(2):465.GONG Xixia,LI Yanxin,LU Qinfen.Thrust robustness optimiza-tion of modular permanent magnet linear synchronous motor ac-counting for manufacture tolerance[J].Transactions of China Electrotechnical Society,2024,39(2):465.[2]㊀张春雷,张辉,叶佩青.高霍尔位置检测精度的圆筒型永磁同步直线电机设计[J].电工技术学报,2022,37(10):2481.ZHANG Chunlei,ZHANG Hui,YE Peiqing.Design of tubular permanent magnet synchronous linear motor by reliability-based ro-bust design optimization[J].Transactions of China Electrotechni-cal Society,2022,37(10):2481.[3]㊀缪仲翠,苏乙,张磊,等.梯形Halbach交替极无铁心永磁同步直线电机特性分析与优化设计[J].电机与控制学报, 2024,28(1):164.MIAO Zhongcui,SU Yi,ZHANG Lei,et al.Characteristic analy-sis and optimization design of air-core permanent magnet linear synchronous motor with trapezoidal Halbach array consequent-pole [J].Electric Machines and Control,2024,28(1):164. [4]㊀李争,安金峰,肖宇,等.基于自适应观测器的永磁同步直线电机模型预测控制系统设计[J].电工技术学报,2021,36(6):1190.LI Zheng,AN Jinfeng,XIAO Yu,et al.Design of model predic-tive control system for permanent magnet synchronous linear motor based on adaptive observer[J].Transactions of China Electrotech-nical Society,2021,36(6):1190.[5]㊀李争,张梓豪,王康涛,等.基于无模型的PMLSM改进自适应滑模自抗扰控制[J].电机与控制学报,2024,28(1):142.LI Zheng,ZHANG Zihao,WANG Kangtao,et al.Improved adap-tive sliding mode active disturbance rejection control for PMLSM based on model-free theory[J].Electric Machines and Control, 2024,28(1):142.[6]㊀张康,王丽梅.基于周期性扰动学习的永磁直线电机自适应滑模位置控制[J].电机与控制学报,2021,25(8):132.ZHANG Kang,WANG Limei.Adaptive sliding mode position con-trol for permanent magnet linear motor based on periodic disturb-ance learning[J].Electric Machines and Control,2021,25(8): 132.[7]㊀孙宜标,毛爽,夏加宽.直线电机悬浮平台的μ-Hɕ鲁棒控制[J].沈阳工业大学学报,2014,36(1):7.SUN Yibiao,MAO Shuang,XIA Jiakuan.μ-Hɕrobust control for linear motor levitation platform[J].Journal of Shenyang Uni-versity of Technology,2014,36(1):7.[8]㊀YAO B,BU F,REEDY J,et al.Adaptive robust control of sin-glerod hydraulic actuators:theory and experiments[J].IEEE/ ASME Transactions on Mechatronics,2000,5(1):79. [9]㊀CHEN S,CHEN Z,YAO B,et al.Adaptive robust cascade forcecontrol of1-DOF hydraulic exoskeleton for human performance augmentation[J].IEEE/ASME Transactions on Mechatronics, 2017,22(2):589.[10]㊀HELIAN B,CHEN Z,YAO B.Adaptive robust motion control ofa pump direct drive electro-hydraulic system with meter-out pres-sure regulation[J].IFAC-Papers OnLine,2020,53(2):9005.[11]㊀HAN J,YANG S,XIA L,et al.Deterministic adaptive robustcontrol with a novel optimal gain design approach for a fuzzy2doflower limb exoskeleton robot system[J].IEEE Transactions onFuzzy Systems,2020,29(8):2373.[12]㊀LIU Y.Saturated robust adaptive control for uncertain nonlinearsystems using a new approximate model[J].IET Control Theoryand Applications,2017,11(6):870.[13]㊀王璐,郭毓,钟晨星,等.控制力矩陀螺框架伺服系统期望补偿自适应鲁棒控制[J].控制理论与应用,2017,34(9):1143.WANG Lu,GUO Yu,ZHONG Chenxing,et al.Desired com-pensation adaptive robust control for control moment gyroscopesgimbal servo system[J].Control Theory and Applications,2017,34(9):1143.[14]㊀CHANG Y,JIANG T,PU Z.Adaptive control of hypersonic ve-hicles based on characteristic models with fuzzy neural networkestimators[J].Aerospace Science and Technology,2017,68:475.[15]㊀常亚菲.一类不确定非线性系统基于特征模型的复合自适应控制[J].控制理论与应用,2019,36(7):1137.CHANG Yafei.Characteristic model-based composite adaptivecontrol for a class of uncertain nonlinear systems[J].ControlTheory and Applications,2019,36(7):1137. [16]㊀王永,窦晓华,方浩,等.永磁同步电机非线性黄金分割自适应转速控制[J].电机与控制学报,2017,21(10):23.WANG Yong,DOU Xiaohua,FANG Hao,et al.Nonlineargolden-section adaptive speed control of permanent magnet syn-chronous motor[J].Electric Machines and Control,2017,21(10):23.931第3期曹㊀阳等:基于特征模型的永磁同步直线电机自适应控制[17]㊀WANG X,WU Y,ZHANG E,et al.Adaptive terminal sliding-mode controller based on characteristic model for gear transmis-sion servo systems[J].Transactions of the Institute of Measure-ment and Control,2019,41(1):219.[18]㊀QI L,BAO S,SHI H.Permanent-magnet synchronous motor ve-locity control based on second-order integral sliding mode controlalgorithm[J].Transactions of the Institute of Measurement andControl,2015,37(7):875.[19]㊀张兴华,姚丹.感应电机直接转矩控制系统的 抗饱和 控制器设计[J].电工技术学报,2014,29(5):181.ZHANG Xinghua,YAO Dan.Anti-windup speed controller de-sign for direct torque controlled induction motor drives[J].Trans-actions of China Electrotechnical Society,2014,29(5):181.[20]㊀IGHACHANE M A,AKKOUCHI M.Further refinements ofYoung's type inequality for positive linear maps[J].Revista de laReal Academia de Ciencias Exactas,Físicas y Naturales.SerieA.Matemáticas,2021,115(2):10.[21]㊀BENOSMAN M.Learning-based adaptive control for nonlinearsystems[C]//European Control Conference(ECC),June24-27,2014,Strasbourg,France.2014:920-925.(编辑:邱赫男)041电㊀机㊀与㊀控㊀制㊀学㊀报㊀㊀㊀㊀㊀㊀㊀㊀㊀㊀㊀㊀㊀第28卷㊀。
高速永磁同步电动机变系数铁耗计算模型

第27卷㊀第7期2023年7月㊀电㊀机㊀与㊀控㊀制㊀学㊀报Electri c ㊀Machines ㊀and ㊀Control㊀Vol.27No.7Jul.2023㊀㊀㊀㊀㊀㊀高速永磁同步电动机变系数铁耗计算模型徐永明1,㊀庞松印2,㊀刘文辉2,㊀艾萌萌2(1.常州工学院电气信息工程学院,江苏常州213032;2.哈尔滨理工大学电气与电子工程学院,黑龙江哈尔滨150080)摘㊀要:高速永磁同步电机铁心损耗受磁场多因素影响,现有的计算模型难以准确计算㊂本文基于经典的Bertotti 三项常系数铁耗模型,综合考虑高次谐波㊁旋转磁化㊁集肤效应和小磁滞回环等因素对铁心损耗计算的影响,建立了包含磁滞损耗㊁涡流损耗和附加损耗补偿系数的铁耗计算模型㊂并以一台150kW ,30000r /min 高速永磁同步电动机为例,充分考虑补偿系数随磁密波形畸变率㊁幅值和频率的变化,对样机在不同转速下的铁耗进行计算,实验结果表明,与传统模型相比,该模型计算结果与实测值更加接近㊂之后进一步分析了各因素对铁耗的影响程度,发现影响程度由大到小依次是高次谐波㊁旋转磁化㊁磁滞回环和集肤效应㊂关键词:高速永磁同步电动机;铁心损耗;补偿系数;高次谐波;旋转磁化;影响程度DOI :10.15938/j.emc.2023.07.018中图分类号:TM351文献标志码:A文章编号:1007-449X(2023)07-0174-09㊀㊀㊀㊀㊀㊀㊀㊀㊀㊀㊀㊀㊀㊀㊀㊀㊀㊀㊀㊀㊀㊀㊀㊀㊀㊀㊀㊀㊀㊀㊀㊀㊀㊀㊀㊀㊀㊀㊀㊀㊀㊀㊀㊀㊀㊀㊀㊀㊀㊀㊀㊀㊀㊀㊀㊀㊀㊀㊀㊀㊀㊀㊀㊀㊀㊀㊀㊀㊀㊀㊀㊀㊀㊀㊀㊀㊀㊀㊀㊀㊀㊀㊀㊀㊀㊀㊀㊀㊀㊀㊀㊀㊀㊀㊀㊀㊀㊀㊀㊀㊀㊀㊀㊀㊀㊀㊀㊀㊀㊀㊀㊀收稿日期:2021-11-11基金项目:国家自然科学基金(52077047);黑龙江省自然科学基金(LH2020E092)作者简介:徐永明(1979 ),男,博士,教授,博士生导师,研究方向为电机设计及多物理场耦合计算;庞松印(1997 ),男,硕士,研究方向为永磁电机设计;刘文辉(1983 ),男,博士研究生,研究方向为特种电机设计;艾萌萌(1991 ),男,讲师,研究方向为电机优化设计㊂通信作者:徐永明Calculation model of core loss with variable coefficient ofhigh-speed permanent magnet synchronous motorsXU Yongming 1,㊀PANG Songyin 2,㊀LIU Wenhui 2,㊀AI Mengmeng 2(1.School of Electrical and Information Engineering,Changzhou Institute of Technology,Changzhou 213032,China;2.School of Electrical and Electronic Engineering,Harbin University of Science and Technology,Harbin 150080,China)Abstract :The core loss of high-speed permanent magnet synchronous motors is affected by multi-factor magnetic field,and it is difficult to calculate the existing calculation model accurately.Based on the clas-sical Bertotti model of core loss with three constant coefficients and considering the influence of high-order harmonics,rotational magnetization,skin effects,and a small hysteresis loop on the calculation of core loss,a calculation model of core loss with compensation coefficients for hysteresis loss,eddy current loss,and additional loss was established.Taking a 150kW,30000r /min high-speed permanent magnet syn-chronous motor as the research object,the core loss at different rotational speeds was calculated by fully considering the change in compensation coefficient with the waveform distortion rate,amplitude,and fre-quency of the flux density.The experimental results show that the calculated results of the model presen-ted are closer to the measured values than the traditional model.Then the influence degree of each factor on core loss was further analyzed,and it is found that the influence degree is in the order of high harmon-ic,rotational magnetization,hysteresis loop,and skin effect.Keywords :high-speed permanent magnet synchronous motor;core loss;compensation coefficient;high-order harmonic;rotational magnetization;influence degree0㊀引㊀言高速永磁同步电动机采用变频电源供电时,其电源谐波和电机内部磁场谐波共同作用使电机的定子铁耗大幅增加,如何准确计算及精细化分析其铁耗始终是高速电机领域的研究热点之一[1]㊂目前高速电机铁耗的计算多是在Bertotti提出的经典三项常系数模型的基础上进行修正㊂张洪亮等采用2个相互正交的交变磁化以等效考虑旋转磁化的影响,并通过样机实测证明铁耗计算中仅考虑交变磁场和基波磁通是不够的[2]㊂文献[3-4]在铁耗计算时考虑旋转磁场影响与不考虑时相比,计算模型和仿真实验结果更接近㊂文献[5]对不同磁化方式下的铁耗进行了计算,经实验验证了考虑旋转磁化影响时铁耗计算模型的有效性㊂文献[6]通过对硅钢片的损耗测试证明了铁耗计算时考虑旋转磁化的必要性㊂文献[7]引入涡流损耗㊁磁滞损耗和附加损耗补偿系数,考虑高次谐波对铁心损耗的影响,以48槽/8极内转子和36槽/48极外转子两台永磁电机为例进行计算并经实验验证了计算模型的有效性㊂文献[8]引入磁滞损耗附加磁密低次项和涡流损耗附加磁密高次项来考虑到高次谐波的影响,以补偿磁场谐波对铁耗的影响,实验证明了该方法的有效性㊂文献[9]考虑了逆变器输出电压谐波对电机铁耗的影响,将铁损表示成电压和速度的函数,以5.5kW和55kW两台变频感应电机为例对比分析了不同转速和负载条件下铁耗的计算值和实验值,验证了模型的准确性㊂文献[10-13]在铁耗的计算中考虑了高次谐波和旋转磁化的影响,并经有限元仿真验证了计算结果㊂当电机运行频率较高时,集肤效应作用会导致叠片厚度上涡流分布不均,对铁耗产生影响[14]㊂文献[15]考虑了高频下集肤效应的影响,构建了铁耗计算模型,并以实例计算和实验验证证明了模型的有效性㊂文献[16-17]铁耗计算时在高次谐波和旋转磁化影响的基础上,通过引入补偿函数考虑了集肤效应对铁耗的影响㊂随着电磁负荷和功率密度的增加,电机内磁场饱和程度逐渐增加,在铁心损耗的研究中还应考虑磁滞回线产生的磁滞回环的影响㊂文献[18]等在铁耗计算中,引入旋转磁化损耗系数来考虑旋转磁化致磁滞损耗的增加,并给出了该系数的确定方法㊂文献[19]在铁耗计算中引入磁滞损耗修正系数,考虑小磁滞回环的影响,并对多台样机的空载铁耗试验,验证了方法的有效性㊂文献[20]铁耗计算中在高次谐波的基础上进一步考虑了磁滞回环的影响,计算结果相比经典模型与实测值更接近㊂文献[21]考虑了旋转磁化㊁高次谐波和小磁滞回环等因素的影响,根据已有的实验数据,利用支持向量回归机(support vactor regression,SVR)进行非线性回归得到磁滞损耗系数,但计算过程繁琐,且模型不能体现铁耗随磁密波形畸变率㊁磁密基波和谐波幅值的变化规律㊂上述研究成果,有效提升了电机铁耗计算的准确性,在Bertotti经典模型的基础上考虑了部分影响铁耗的磁场因素㊂有限元数值分析是将各单元的磁通密度幅值代入求解,无法将磁密的磁化轨迹和谐波分解的结果代入,考虑不到磁场磁化㊁谐波和小磁滞回环等磁场因素的影响,导致其结果相对较小㊂但实际上,在铁心损耗计算时,需要综合考虑高次谐波㊁旋转磁化㊁集肤效应和小磁滞回环等磁场多因素的影响,并深入分析各因素对铁耗的影响程度㊂针对这一情况,本文以一台150kW,30000r/min 曝气风机用高速永磁同步电动机为例,构建综合考虑磁场多因素影响的变系数铁心损耗计算模型,并研究磁场各因素对铁耗的影响程度,通过实验予以验证该模型的准确性㊂1㊀变系数铁耗计算模型变系数铁耗计算模型是在Bertotti经典铁耗计算模型的基础上,综合考虑高次谐波㊁旋转磁化㊁集肤效应和小磁滞回环等因素的影响,所构建的铁耗计算模型㊂经典的Bertotti铁耗计算模型为[22]p Fe=p h+p c+p e=k h fBαm+k c f2B2m+k e f1.5B1.5m㊂(1)式中:p Fe为单位质量铁耗,W/kg;p h为磁滞损耗, W/kg;p c为经典涡流损耗,W/kg;p e为附加涡流损耗,W/kg;k h㊁α为磁滞损耗系数;k c为经典涡流损耗系数;k e为附加损耗系数;f为磁场的变化频率, Hz;B m为磁密幅值,T㊂对于高速电机而言,任意磁场波形下产生的铁耗等于其基波和各次谐波分量产生的铁耗之和,考虑高次谐波影响的铁耗计算模型如下:p Fe=k hðn i=1f i Bαi+k cðn i=1f2i B2i+k eðn i=1f1.5i B1.5i㊂(2)571第7期徐永明等:高速永磁同步电动机变系数铁耗计算模型式中:i 为磁场谐波阶次,i =1,2,3, ,n ;f i 为电机第i 阶谐波频率;B i 为磁场第i 阶谐波磁密幅值㊂根据磁密基波和谐波之间的关系,以经典涡流损耗为例,推导计及磁波形畸变率㊁幅值和频率的补偿系数,即p c =k c f 21B 21+k c f 22B 22+k c f 23B 23+ =[f 1f 1()2(B 1B m )2(B m B 1)2+f 2f 1()2(B 2B m )2(B m B 1)2+ +f if 1()2(B iB m)2(B m B 1)2+ ]k c f 21B 21㊂(3)式中B m =ðni =1B 2i 为合成磁场的磁密幅值,则B2m B21=1+B 22B 21+B 23B 21+ +B 2n B21=1+B 2THD ,B THD 为磁密波形畸变率㊂则经典涡流损耗可表示为p c =ðni =1f if 1()2(Bi Bm)2(1+B 2THD)[]k c f 21B 21=k ᶄc (f i ,B i ,B THD )k c f 21B 21㊂(4)式中k 'c (f i ,B i ,B THD )为涡流损耗补偿系数㊂同理,磁滞损耗和附加损耗的补偿系数可表示为:k ᶄh(f i ,B i ,B THD )=ðni =1f i f 1(B i B m)α(1+B 2THD)α2;(5)k ᶄe(f i ,B i ,B THD )=ðni =1f if 1()1.5(B i B m)1.5(1+B 2THD )34㊂(6)此外,高速永磁电动机其供电频率是普通电机的几倍甚至几十倍,较高的频率使得硅钢片的集肤效应增大,导致硅钢片内部涡流分布不均匀,须引入涡流损耗修正系数,考虑集肤效应对铁耗的影响,即k c (f )=k c3D f sinh(D f )-sin(D f )cosh(D f )-cos(D f )㊂(7)式中:D =dπμσ,d 为硅钢片厚度;μ为硅钢片平均磁导率;σ为硅钢片电导率㊂电机定子铁心硅钢片与处于静止磁场的硅钢片相比,其磁化方式除了交变磁化以外,还含有旋转磁化㊂磁密在变化的过程中,存在局部非线性转折现象,即磁密反向变化,即形成小磁滞回环,会导致铁心中磁滞损耗的增加,需通过补偿系数加以考虑,有k B =1+k m ðNj =1ΔB mj B m()㊂(8)式中:k m 为常数,一般取0.65;B m 是磁密幅值;ΔB mj 是局部磁密的变化量;N 为一个电周期内局部磁密变化次数㊂为考虑旋转磁化的影响,将磁密分解成径向与切向两个正交方向,并以径向和切向的磁密幅值来替代经典铁耗计算模型中的磁密幅值㊂综合以上分析,考虑高次谐波㊁旋转磁化㊁集肤效应和磁滞回环等多因素的影响,得到变系数铁心损耗计算模型如下:p Fe =k Bðn i =1f i f 1(B i r B mr)α(1+B 2THD -r)α2[]k h f 1B α1r +ðni =1f if 1(Bi tBmt)α(1+B 2THD -t )α2[]k h f 1B α1t []+ðn i =1k c (f )fi f 1()2(B i r B mr)2(1+B 2THD -r )[]f 21B 21r +ðn i =1k c(f )f i f 1()2(Bi tBmt)2(1+B 2THD -t )[]f 21B 21t []+ðn i =1f i f 1()1.5(B i r B mr)1.5(1+B 2THD -r)34[]k e f 1.51B 1.51r +ðni =1f i f 1()1.5(B i t B mt)1.5(1+B 2THD -t)34[]k e f 1.51B 1.51t []㊂(9)式中:B i r ㊁B i t 分别为考虑旋转磁化后的径向和切向磁密第i 阶谐波幅值;B THD -r ,B THD -t 分别为考虑旋转磁化后的径向和切向磁密波形畸变率㊂2㊀高速永磁同步电动机的定子铁耗本文以一台额定输出功率为150kW 的4极24槽高速永磁同步电机为研究对象,其额定转速为30000r /min,采用SPWM 逆变器对其进行供电,同时为降低逆变器输出电压含有的大量谐波分量对电机磁场的影响,在供电电路中并联滤波电容㊂该电机的基本参数如表1所示,样机二维有限元仿真模型如图1所示㊂2.1㊀定子铁心内瞬态磁场分析根据区域化铁耗计算方法,将电机定子铁心划分为齿顶㊁齿中㊁齿根和轭中4部分,如图2所示,分别取A ㊁B ㊁C ㊁D 点磁密代表各自区域的磁密㊂671电㊀机㊀与㊀控㊀制㊀学㊀报㊀㊀㊀㊀㊀㊀㊀㊀㊀㊀㊀㊀㊀第27卷㊀表1㊀高速永磁同步电动机的基本参数Table1㊀Basic parameters of high-speed permanent magnet synchronous motors图1㊀高速永磁同步电动机仿真模型Fig.1㊀Simulation model ofhigh-speed permanent mag-net synchronous motor图2㊀定子铁心分区和取点示意图Fig.2㊀Schematic diagram of stator core partition andselection of points定子铁心磁密可以分解为径向磁密和切向磁密,其数学表达式如下:B r=B x cosθ+B y sinθ;B t=B x sinθ+B y cosθ㊂}(10)式中:B r为径向磁密;B t为切向磁密;B x为电机磁密的x轴分量;B y为其y轴分量;θ为柱坐标中x轴与径向夹角㊂采用二维磁场的时步有限元理论和式(10),可以得到在一个磁场变化周期内不同位置的磁密变化曲线,如图3~图6所示㊂图3㊀A点磁密分量Fig.3㊀Magnetic density component at point A图4㊀B点磁密分量Fig.4㊀Magnetic density component at point B图3为定子齿顶区域A点的磁密分量,在相同的电角度下,齿顶A点的径向磁密与切向磁密相差较大,磁密幅值主要由径向磁密构成,为0.901T,而切向磁密为0.303T,和旋转磁场相比,主要受交变磁场的影响㊂图4为齿中区域B点的磁密分量,在相同的电角度下,B点的径向磁密均远大于切向磁密,其幅值分别为1.195T和0.042T㊂可认为该区域的磁化771第7期徐永明等:高速永磁同步电动机变系数铁耗计算模型方式只受交变磁场的影响㊂图5㊀C 点磁密分量Fig.5㊀Magnetic density component at pointC图6㊀D 点磁密分量Fig.6㊀Magnetic density component at point D图5为齿根区域C 点的磁密分量,C 点介于定子齿部与轭部的分界处,径㊁切向磁密幅值相差不大,分别为0.848T 和0.632T,该区域磁化方式为旋转磁场和交变磁场二者影响均较大㊂图6为定子轭中区域D 点的磁密分量,在相同的电角度下,D 点大部分的切向磁密与径向磁密相差较大,其径㊁切向磁密幅值分别为0.202T 和1.034T,主要由切向磁密组成㊂因此和交变磁场相比,主要受旋转磁场的影响㊂由以上分析可知,在高速永磁同步电动机额定运行工况下,定子上各部分的磁化方式存在明显差异㊂对于磁密中存在的谐波分量,将各点的径向和切向磁密通傅里叶进行谐波分解,得到各点磁密的基波和各次谐波幅值变化情况,如图7所示㊂图7㊀各点磁密谐波分布图Fig.7㊀Magnetic density harmonic distribution diagram由图7可以看出,就径向磁密而言,定子齿中B871电㊀机㊀与㊀控㊀制㊀学㊀报㊀㊀㊀㊀㊀㊀㊀㊀㊀㊀㊀㊀㊀第27卷㊀点的磁密基波幅值比其他区域大,为1.131T;定子轭部D点的磁密基波幅值最小,为0.198T㊂而对切向磁密来说,定子轭部D点的磁密基波幅值最大,为0.979T;定子齿中B点的磁密基波幅值最小,为0.039T㊂此外,根据径向和切向磁密的傅里叶分解结果,从点A到点D由于旋转磁场的影响逐渐加大,相比于A㊁B两点,C㊁D两点处的切向磁密均显著增大,C点径向和切向磁密之间的基波幅值差距减小,分别为0.826T和0.529T㊂从上图可以看出谐波幅值随谐波次数的增加呈降低趋势㊂各点的低次谐波磁密含量较大,即3㊁5㊁7㊁9次谐波,但当谐波次数达到11次谐波以后,谐波含量变得很小,在铁耗计算时可忽略㊂计算各点磁密波形谐波畸变率,切向磁密波形畸变率B点最大,为27.8%;D点最小,为5.3%㊂而径向磁密波形畸变率D点最大,为25.1%;B点最小,为10.6%㊂2.2㊀定子铁心损耗计算在磁密分析的基础上,采用本文所提出的变系数模型计算样机在额定工况下的定子铁耗㊂表2给出了定子铁心不同区域的铁耗及其所占总铁耗的比重㊂表2㊀定子铁心不同区域铁耗分布Table2㊀Distribution of iron loss in different areas ofstator core㊀定子铁心参数齿顶齿中齿根轭中铁心体积/mm366.7124143290基波铁耗/W78244228458谐波铁耗/W29406453区域铁耗/W107284292511铁耗密度/(W/mm3) 1.6 2.29 2.04 1.76占总铁耗比例/%8.923.824.542.8由表2可见,定子齿顶区域铁心体积较小,其铁耗在4个区域中的比重最小,仅占总铁耗的8.9%㊂定子轭部所占的铁心区域体积最大,并且其磁密幅值大,故其铁耗所占比重最大,为42.8%㊂虽然定子齿中铁耗密度最大,但其铁心体积小,因此其铁耗不是最大,占定子总体的23.8%㊂定子齿根与轭部的交界处与定子齿中的面积和磁密幅值相差不大,其铁耗和定子齿中的铁耗较为接近,所占比重为24.5%㊂在额定运行工况下,定子铁心各区域铁心损耗分布由大到小依次为定子轭部㊁定子齿根㊁定子齿中和定子齿顶㊂此外,从谐波损耗可以看出,定子铁心各区域还存在一定的谐波铁耗㊂为进一步分析考虑磁场因素对铁耗计算的必要性,研究磁场频率对电机铁耗的影响,分别对不同转速下的定子铁耗进行计算,并和经典模型计算结果相比,如表3所示㊂表3㊀不同转速下定子铁耗计算结果Table3㊀Calculation results of stator iron loss at different speeds转速/(r/min)本文模型/W经典模型/W相对误差/% 1200034428221.99 1800058747922.55 2400087571123.07 300001194101717.40由表3的结果对比可以看出,本文模型的铁耗计算结果均明显高于经典模型,二者之间的相对误差在20%左右,主要是引入了考虑旋转磁化㊁集肤效应和小磁滞回环等磁场因素的补偿系数,使得计算结果更大㊂与经典模型相比,当电机在额定转速,即30000r/min时,铁耗增加最少,为17.40%;当电机转速为24000r/min时,铁耗增加最多,为23.07%㊂当电机转速从12000r/min到24000r/min,随着频率的增大,主要由磁场因素的影响程度加大,导致铁耗增加;尽管此时频率增加使集肤效应的影响变大,但因集肤效应引起的铁耗减小不明显,故相对误差呈先逐渐增大的趋势㊂随着频率的进一步增大,当转速为30000r/min时,集肤效应的影响逐渐变大,使得铁耗因其减小的效果开始明显,电机铁耗总体增加幅度减小,进而导致相对误差减小㊂本文模型的铁耗计算结果和有限元数值分析结果对比如图8所示㊂由图8可以看出,数值分析结果明显小于本文模型的计算结果,本文模型的计算结果平均要比其高出105W左右,这是因为数值分析过程是将各单元的磁通密度幅值代入求解,无法将磁密的磁化轨迹和谐波分解的结果代入,难以考虑磁场磁化㊁谐波和小磁滞回环等磁场因素的影响,导致其结果相对较小㊂因此,在计算电机铁耗时,计971第7期徐永明等:高速永磁同步电动机变系数铁耗计算模型及高次谐波㊁旋转磁化㊁小磁滞回环㊁集肤效应等因素的影响是很有必要的㊂图8㊀与数值分析铁耗计算结果对比Fig.8㊀Comparison with numerical analysis iron losscalculation results3㊀各因素对定子铁耗的影响为研究各因素对铁心损耗的影响程度,以经典模型为基础,分别建立仅考虑单一磁场因素的计算模型㊂仅考虑高次谐波影响的铁耗模型,即㊀p Fe =ðni =1f i f 1(B i B m)α(1+B 2THD )α2k h f 1B α1+ðni =1k c f if 1()2(B i B m)2(1+B 2THD )k c f 21B 21+ðni =1f i f 1()1.5(B i B m)1.5(1+B 2THD )34k e f 1.51B 1.51㊂(11)仅考虑小磁滞回环影响的铁耗模型为p Fe =k B ˑk h fB αm +k c f 2B 2m +k e fB 1.5m ㊂(12)仅考虑旋转磁化影响的铁耗模型为p Fe =k h f (B αr +B αt )+k c f 2(B 2r +B 2t )+k e f 1.5(B1.5r+B 1.5t )㊂(13)采用经典模型和上述3个模型分别计算样机在不同转速下的铁耗,以分析各因素对铁耗的影响程度㊂不同转速下各模型的单位质量铁耗计算结果对比如表4所示㊂从表4中可以看出,仅考虑高次谐波的影响,在表中四个转速时的单位质量铁耗,和经典模型相比,分别增加了8.61㊁18.09㊁27.74㊁42.02W,平均增加幅度约为17.14%㊂同理,仅考虑磁滞回环的影响,单位质量铁耗增加幅度很小,平均约为4.79%;而仅考虑旋转磁化的影响时,单位质量铁耗平均增加幅度约为9.49%㊂就铁耗增加幅度而言,高次谐波的影响程度最大,旋转磁化次之,磁滞回环最小㊂表4㊀样机各模型的单位质量铁耗对比Table 4㊀Comparison of core loss per unit mass of eachmodel for prototype转速/(r /min)经典模型/W 仅考虑高次谐波/W 仅考虑磁滞回环/W 仅考虑旋转磁化/W 1200061.3469.9564.3266.7218000104.04122.13109.17114.1824000155.38183.12162.41169.2230000217.87259.89228.40240.83电机运行频率越高,集肤效应对铁耗的影响就越明显㊂为了更加明显地分析集肤效应影响程度,本文在仅考虑高次谐波影响的铁耗模型的基础上,对集肤效应影响加以分析㊂不同转速下考虑集肤效应与否时单位质量铁耗计算结果如表5所示㊂表5㊀集肤效应考虑与否时单位质量铁耗对比Table 5㊀Comparison of core loss per unit mass of consider-ing skin effect or not转速/(r /min)仅考虑高次谐波/W考虑集肤效应/W1200069.9569.8818000122.13121.8324000183.12182.3130000259.89257.53由表5可知,考虑集肤效应影响后,铁耗有所减少,且随着转速的增加单位质量铁耗减少量逐渐加大,但整体铁耗的减少的量非常小㊂与仅考虑高次谐波的影响相比,在此基础上考虑集肤效应影响后铁耗平均降低幅度约为0.42%㊂可见,随着转速的升高,较高的频率使集肤效应变明显,导致电机硅钢片内部的涡流分布不均匀,使铁耗逐渐降低,但整体而言,集肤效应对铁耗的影响很小,可忽略不计㊂4㊀实验验证为进一步验证本文所提计算模型的准确性,对一台曝气风机用150kW,30000r /min 高速永磁同步电动机定子铁心损耗进行验证,试验设备主要由UPS㊁输入电抗器㊁滤波器㊁变频器㊁制动电阻㊁输出电抗器㊁磁悬浮轴承控制柜以及冷却风机等组成㊂样机实验平台如图9所示㊂081电㊀机㊀与㊀控㊀制㊀学㊀报㊀㊀㊀㊀㊀㊀㊀㊀㊀㊀㊀㊀㊀第27卷㊀图9㊀样机实验平台Fig.9㊀Prototype experiment platform由于风机压升较高,精确测试压升需要风机进口㊁出口均有较长的距离㊂而试验现场空间较小,实际压升通过压力表难以测量,最终使用测试水管高度的方式进行压升测试㊂电机带叶轮实验,按照以下三个过程实验:首先带叶轮㊁不带蜗壳升速至额定转速;之后带叶轮㊁蜗壳升速至额定转速;最后调节风机进出口阀门,进行风机性能测试㊂高速永磁电动机的定子铁耗由空载实验经损耗分离的方法得到㊂其中,电机的输入和输出功率可别通过功率分析仪器和转矩转速传感器测量得到;各转速下空载电流在5~7A之间,线电阻为0.0105Ω,由于铜耗很小,因此忽略不计;机械损耗由测功机在不同转速下拖动无永磁体转子的待测样机,由同轴连接在测功机与待测样机间的转速转矩传感器上的扭矩值计算得到,转速为12000㊁18000㊁24000和30000r/min时,机械损耗分别是58㊁130㊁220和362.5W㊂利用本文变系数铁耗模型和经典模型对样机在不同转速下的铁耗计算值与实验结果对比分析,如表6所示㊂由表6可知,在不同的转速下,经典铁耗模型结果和实验值相比相对误差较大,都在20%左右㊂而采用本文给出的变系数铁耗计算模型所得结果和实验值更为接近,相对误差较小,均在5%以内,验证了考虑多磁场因素后的本文模型对于铁耗计算有更高的准确性㊂但由于未考虑温度㊁应力和加工工艺等对电机的影响,使得本文计算结果小于实验结果㊂表6㊀样机不同转速下铁耗计算值与实验结果对比Table6㊀Iron loss comparison of calculation value and ex-perimental results of prototype at different speeds 转速/(r/min)计算值/W本文模型经典模型实验值/W相对误差/%本文模型经典模型12000344282355 3.1020.56 18000587479608 3.4521.22 24000875711913 4.1622.12 30000119410171241 3.7918.055㊀结㊀论本文给出一种综合考虑磁场内多因素影响的变系数铁耗计算模型,分析了不同因素对铁耗的影响程度,得到如下结论:1)在经典铁耗模型的基础上,引入在磁滞损耗,经典涡流损耗和附加损耗补偿系数,综合考虑高次谐波㊁旋转磁化㊁集肤效应和小磁滞回环等因素的影响,构建了综合考虑磁场多因素影响的变系数铁心损耗计算模型,且补偿系数随磁密幅值㊁频率和磁密畸变率变化,实验证明该模型计算结果更接近实验数据㊂2)由于变频电源中大量高次谐波成分和集肤效应的影响,使得定子区域各点的径向和切向磁密波形非正弦分布,在磁密增加或减小的过程中,存在着局部磁密反向的现象,且电机齿部位置的磁场波形畸变要高于轭部位置,定子各区域铁耗所占总铁耗的比例由大到小依次是轭中㊁齿根㊁齿中和齿顶㊂3)得到了磁场各因素对铁耗的影响程度,与经典模型计算结果相比,磁场因素对铁耗计算结果的影响程度由大到小依次是高次谐波㊁旋转磁化㊁磁滞回环,分别为17.14%㊁9.49%㊁4.79%;其中集肤效应的影响程度是在考虑高次谐波的基础上得到的,相对来说集肤效应对铁耗的影响最小,仅为0.42%,可忽略不计㊂参考文献:[1]㊀孔晓光,王凤翔,徐云龙,等.高速永磁电机铁耗的分析和计算[J].电机与控制学报,2010,14(9):26.KONG Xiaoguang,WANG Fengxiang,XU Yunlong,et al.Analy-sis and calculation of iron loss of high-speed permanent magnet motors[J].Electric Machines and Control,2010,14(9):26.[2]㊀张洪亮,邹继斌.考虑旋转磁通的PMSM铁心损耗数值计算[J].电机与控制学报,2007,11(4):340.181第7期徐永明等:高速永磁同步电动机变系数铁耗计算模型ZHANG Hongliang,ZOU Jibin.Numerical calculation of PMSM core loss considering rotating magnetic flux[J].Electric Machines and Control,2007,11(4):340.[3]㊀KIM C W,KIM J M,SEO S W,et al.Core loss analysis of perma-nent magnet linear synchronous generator considering the3-D flux path[J].IEEE Transactions on Magnetics,2017,54(3):1.[4]㊀戈宝军,罗前通,王立坤,等.高速永磁同步电动机铁耗分析[J].电机与控制学报,2020,24(4):32.GE Baojun,LUO Qiantong,WANG Likun,et al.Iron loss analy-sis of high-speed permanent magnet synchronous motors[J].Elec-tric Machines and Control,2020,24(4):32.[5]㊀TAKBASH A,IBRAHIM M,MASISI L,et al.Core loss calcula-tion in a variable flux permanent magnet machine for electrified transportation[J].IEEE Transactions on Transportation Electrifi-cation,2018,4(4):857.[6]㊀LI Yongjian,CHENG Hao,LIN Zhiwei,et al.A modified charac-terization method for core loss calculation under rotational magneti-zation[J].IEEE Transactions on Magnetics,2021,57(2):1.[7]㊀揭丁爽,黄苏融,陈克慧,等.计及高次谐波影响的高密度永磁同步电机铁耗计算[J].电机与控制应用,2019,46(4):71.JIE Dingshuang,HUANG Surong,CHEN Kehui,et al.Calcula-tion of iron loss of high-density permanent magnet synchronous mo-tor considering the influence of higher harmonics[J].Electric Ma-chines and Control Application,2019,46(4):71. [8]㊀张冬冬,赵海森,王义龙,等.用于电机损耗精细化分析的分段变系数铁耗计算模型[J].电工技术学报,2016,31(15):16.ZHANG Dongdong,ZHAO Haisen,WANG Yilong,et al.A piecewise variable coefficient iron loss calculation model for refined analysis of motor loss[J].Transactions of China Electrotechnical Society,2016,31(15):16.[9]㊀ZHANG Dongdong,LIU Tianhao,ZHAO Haisen,et al.An ana-lytical iron loss calculation model of inverter-fed induction motors considering supply and slot harmonics[J].IEEE Transactions on Industrial Electronics,2019,66(12):9194.[10]㊀肖成东,赵海森,张冬冬,等.变频供电条件下异步电机空载磁场及损耗分布特点[J].电机与控制应用,2015,42(3):64.XIAO Chengdong,ZHAO Haisen,ZHANG Dongdong,et al.No-load magnetic field and loss distribution characteristics of a-synchronous motors under variable frequency power supply[J].Electric Machines and Control Application,2015,42(3):64.[11]㊀魏静微,于晓,黄全全.不同供电方式下永磁同步电动机铁耗计算与分析[J].微特电机,2018,46(3):64.WEI Jingwei,YU Xiao,HUANG Quanquan.Calculation and a-nalysis of different power supply on iron loss of permanent magnetsynchronous motor[J].Small&Special Electrical Machines2018,46(3):64.[12]㊀KIM C W,KOO MM,KIM J M,et al.Core loss analysis of per-manent magnet linear synchronous generator with slotless stator[J].IEEE Transactions on Applied Superconductivity,2018,28(3):1.[13]㊀ZHANG Chao,CHEN Lixiang,WANG Xiaoyu,et al.Loss cal-culation and thermal analysis for high-speed permanent magnetsynchronous machines[J].IEEE Access,2020,8:92627.[14]㊀XUE Shaoshen,FENG Jianghua,GUO Shuying,et al.Iron lossmodel for electrical machine fed by low switching frequency in-verter[J].IEEE Transactions on Magnetics,2017,53(11):1.[15]㊀JIA Wanying,LAN Xiao,WU Hongfei,et al.An improved core-loss calculation method for doubly salient electromagnetic motor[C]//2017IEEE Energy Conversion Congress and Exposition(ECCE),October1-5,2017,Cincinnati,OH,USA.2017:3125-3129.[16]㊀江善林,邹继斌,徐永向,等.考虑旋转磁通和趋肤效应的变系数铁耗计算模型[J].中国电机工程学报,2011,31(3):104.JIANG Shanlin,ZOU Jibin,XU Yongxiang,et al.Variable coef-ficient iron loss calculation model considering rotating magneticflux and skin effect[J].Proceedings of the CSEE,2011,31(3):104.[17]㊀IBRAHIM M.Core loss prediction in electrical machine lamina-tions considering skin effect and minor hysteresis loops[J].IEEETransactions on Industry Applications,2013,49(5):2061.[18]㊀赵海森,张冬冬,王义龙,等.变频供电条件下感应电机空载铁耗分布特点及其精细化分析[J].中国电机工程学报,2016,36(8):2260.ZHAO Haisen,ZHANG Dongdong,WANG Yilong,et al.Distri-bution characteristics and refined analysis of no-load iron loss ofinduction motors under variable frequency power supply[J].Pro-ceedings of the CSEE,2016,36(8):2260.[19]㊀佟文明,孙静阳,段庆亮,等.永磁同步电动机空载铁耗研究[J].电机与控制学报,2017,21(5):51.TONG Wenming,SUN Jingyang,DUAN Qingliang,et al.No-load iron loss of permanent magnet synchronous motors[J].Elec-tric Machines and Control,2017,21(5):51. [20]㊀TAITODA T,TAKAHASHI Y,FUJIWARA K.Iron loss estima-tion method for a general hysteresis loop with minor loops[J].IEEE Transactions on Magnetics,2015,51(11):1. [21]㊀靳荣华,师蔚.多因素影响下永磁电机定子铁耗计算[J].微特电机,2019,47(6):16.JIN Ronghua,SHI Wei.Calculation of stator iron loss of perma-nent magnet motor influenced by multi-factors[J].Small&Spe-cial Electrical Machines,2019,47(6):16.[22]㊀BERTOTTI G,FIORILLO F,MAZZETTI P,et al.Statisticalmodels of losses in soft magnetic materials[J].Journal of Mag-netism and Magnetic Materials,1984,46(1):68.(编辑:刘素菊)281电㊀机㊀与㊀控㊀制㊀学㊀报㊀㊀㊀㊀㊀㊀㊀㊀㊀㊀㊀㊀㊀第27卷㊀。
- 1、下载文档前请自行甄别文档内容的完整性,平台不提供额外的编辑、内容补充、找答案等附加服务。
- 2、"仅部分预览"的文档,不可在线预览部分如存在完整性等问题,可反馈申请退款(可完整预览的文档不适用该条件!)。
- 3、如文档侵犯您的权益,请联系客服反馈,我们会尽快为您处理(人工客服工作时间:9:00-18:30)。
ITRS Winter Public Conference, December3, Makuhari Messe, Japan
ITRS Winter Conference, December 5, 2012, Hsinchu, Taiwan
1
Modeling & Simulation SCOPE & SCALES Modeling Overall Goal • Support technology development and optimization
Lithography Simulation including EUV
• Complementary lithography • Simulation of defect inspection and characterization, influences/defect printing. Mask optimization including defect repair or compensation based on defect signature available from characterization. Multilayer defect propagation • Simulation of resolution enhancement techniques including combined mask/source optimization (OPC, PSM) and including EMF and resist effects, and extensions for inverse lithography • Models that bridge requirements of OPC (speed) and process development (predictive) including EMF effects, including high NA effects for EUV • Predictive and separable resist models (e.g., mesoscale models) including line-edge roughness, accurate profiles, topcoat and substrate (underlayer) interactions, etch resistance, adhesion, mechanical stability, leaching, swelling or slimming, and time-dependent effects in in single and multiple exposure • Resist model parameter calibration methodology (including kinetic transport and stochastic parameters) • Fast, predictive simulation of ebeam mask making (single-beam and multibeam) including short and long range proximity corrections • Simulation of directed self-assembly of sublithography patterns, esp. guiding pattern optimization and defect formation • Modeling lifetime effects of equipment and masks, including lens and mirror heating effects • Predictive coupled deposition-lithography-etch simulation (incl. double patterning, self-aligned patterning) • Modeling metrology equipment and data extraction for enhancing model calibration accuracy • Modeling of pellicle effects and pellicle defects simulation (incl. double patterning, self-aligned patterning)
• Reduce development times and costs Equipment related • Equipment/Feature scale Modeling • Lithography Modeling • • • • Numerical Methods Materials Modeling Reliability Modeling Modeling for Design Robustness, Manufacturing and Yield IC-scale • Circuit Elements Modeling • Package Simulation
ITRS Winter Public Conference, December3, Makuhari Messe, Japan
ITRS Winter Conference, December 5, 2012, Hsinchu, Taiwan
4
2012 Short-Term Difficult Challenges – changes from 2011 in blue
Modeling and Simulation ITWG
Jürgen Lorenz – Fraunhofer IISB, Germany – Chairperson M&S ITWG
ITWG/TWG Members
H. Jaouen, STM-F R. Minixhofer, austriamicrosystems W. Molzer, Intel Mobile Communications A. Benvenuti, Micron B. Huizing, NXP W. Lerch, centrotherm W. Demmerle, Synopsys Germany P. Pfäffli, Synopsys Switzerland J. Lorenz, Fraunhofer IISB (chairperson) A. De Keersgieter, IMEC J.-C. Barbe, LETI W. Grabinski, EPFL Lausanne M. Ciappa, ETH Zurich T. Grasser, TU Vienna S. Satoh, Fujitsu N. Aoki, Toshiba F. Benistant, Globalfoundries J. H. Choi, Hynix J.-K. Park, Samsung Y. Kwon, Samsung Y.S. Pang, MagnaChip H. Park, Synopsys Korea S. Han, SNU Y.M. Sheu, TSMC D. Chen, UMC I.C. Yang, Macronix M. Chang, Tsing-Hua Univ. V. Singh, INTEL C. Mouli, Micron D. Dunn, IBM S. Kincal, A. Nainani, Applied Materials R. Gafiteanu, MENTOR V. Moroz, Synopsys G. Klimeck, Purdue
ITRS Winter Conference, December 5, 2012, Hsinchu, Taiwan
2
Some Key Messages
Mission of Modeling and Simulation as cross-cut topic: Support areas covered by other ITWGs Continued in-depth analysis of M&S needs of other ITWGs, based on documents + inter-ITWG discussions Strong links with ALL ITWGs – see also crosscut texts in 2011 ITRS Modeling and simulation based on quantitative physical understanding of equipments/materials/processes/devices/circuits/systems tool for technology/device development & optimization and for training/education One of the few methods which can reduce development times and costs Delineation between M&S and ERD / ERM: Architectures to be addressed by M&S ITWG as soon as transferred from ERD/ERM to PIDS 2012 work: Update of M&S tables Prepare for new development time & cost reduction survey in 2013 Extended support to PIDS specs via new partner Purdue & others Continued trend to delay items observed: Necessary research could not be done due to lack of resources (research funding)