某涡轴发动机离心叶轮低循环疲劳试验研究
基于低周热疲劳试验条件的活塞寿命预测研究
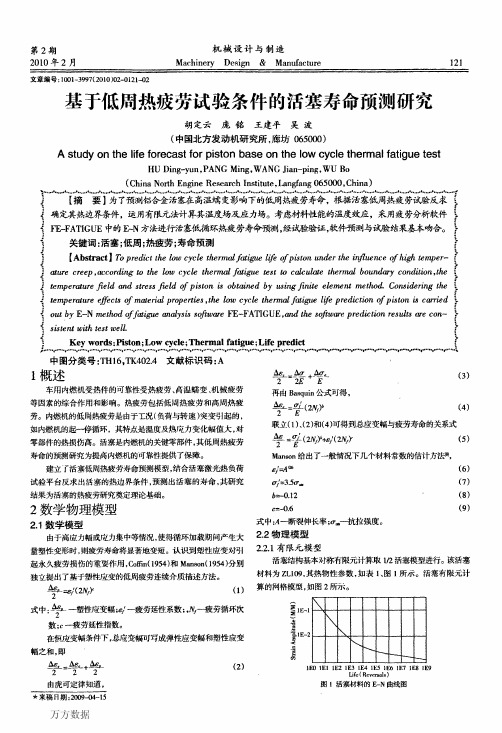
万方数据122胡定云等:基于低周热疲劳试验条件的活塞寿命预测研究第2期表1活塞材料热属性图2活塞的网格2.2,2边界条件活塞的低周热疲劳试验,是通过激光把活塞加热到特定的温度分布,激光卸载时配合通水、通气强制冷却方式加速活塞的热疲劳。
三个环形区域为激光加载区域,如图3所示。
预热时Ⅸ域1—3的热流密度分别为203.1啪,m2、2.52W/m2,687,9w^n2,以后每次加热的热流密度为预热时的1.5倍,试验中活塞区域3的加热预设温度为300。
C,冷却预设温度为170"C,加热时间为210s,强制冷却时间为lOs。
活塞有限无数值仿真寿命预测与活塞激光热负荷的热边界条件一致,为了量化其边界条件,采用有限元迭代反求方法闭,求出各边界的具体热物性参数,如表2所示。
图3激光加载位鼍示意图表2活塞热边界条件3模拟结果和讨论活塞顶面激光加载区域3内某特征点的温度变化,如图4所示。
冷却过程中,该点温度在通水通气条件下迅速冷却,下降速率是先快后慢(下凹分布);加热过程中,其温度上升,上升速率是先快后慢(上凸分布),这与试验结果(如图7)及文献1"31的观点一致。
活塞内腔某特征点的Von-mise应力变化,如图5所示。
其应力在冷却过程中急剧变化,应力先增大后减小,极值约为240MPa;在加热过程中应力先减小至冷却前的状态并保持至加热结束,最终应力约为20MPa。
将有限元计算结果导入到FE—Fatigue软件中使用其E—N法计算出活塞寿命分布,寿命分布,如图6所示。
活塞破坏位置在冷却油道与活塞内腔过渡圆角处,循环寿命为18.2次。
£300.芒§250.盘200.150.50.100.150.200.Time(s)图4特征点温度变化曲线Time(s)图5特征点Von—raise应力变化曲线图6活器疲劳寿命分布4试验验证采用和数值模拟相同的热边界条件在激光热负荷试验台上做活塞低周热疲劳试验,监测点温度变化,如图7所示。
航空发动机涡轮叶片疲劳损伤诊断研究

航空发动机涡轮叶片疲劳损伤诊断研究航空发动机的安全运行是保障航空安全的重要因素之一,而涡轮叶片是其核心部件之一。
然而,随着使用时间的延长,涡轮叶片会出现疲劳损伤。
因此,建立涡轮叶片疲劳损伤诊断的方法,对航空发动机的安全运行具有重要的意义。
一、涡轮叶片疲劳损伤的原因和类型涡轮叶片疲劳损伤通常是由于复杂的工作条件下引起的,工作温度、压力、振动等因素会导致材料内部的裂纹和损伤,严重时会导致叶片断裂。
而涡轮叶片的疲劳损伤种类主要有以下几种:1. 喀啦声疲劳损伤:在高温和高压力环境下,涡轮叶片表面会出现微小裂纹,随着使用时间的增加,这些裂纹会扩大并形成类似于喀啦声的频繁断裂。
2. 振动疲劳损伤:涡轮叶片在高速旋转时,会产生振动,振动强度过大时会导致叶片失效。
3. 粘合疲劳损伤:涡轮叶片的表面涂覆保护材料后,残留应力和热膨胀效应会导致粘合点的断裂和剥离。
以上三种疲劳损伤均会影响涡轮叶片的性能和寿命,在航空发动机领域,这些疲劳损伤的诊断和修复显得尤为重要。
二、涡轮叶片疲劳损伤的诊断技术涡轮叶片疲劳损伤的诊断技术主要有两种,其中一种是磁粉探伤技术,另一种是电化学腐蚀技术。
这两种技术各有优缺点,具体情况应根据实际情况选择。
1. 磁粉探伤技术:磁粉探伤技术是一种通过磁粉颗粒的吸附和积聚来检测涡轮叶片表面的裂纹和损伤的无损检测技术。
该技术具有检测速度快、检测效率高、成本低等优点,但检测结果易受外部因素干扰,同时对样品的加工和处理要求高。
2. 电化学腐蚀技术:电化学腐蚀技术是将涂有一定电解液的涡轮叶片浸泡在电化学池中,通过电化学反应来腐蚀叶片表面,并通过对腐蚀后的叶片表面形貌进行分析来检测裂纹和损伤。
该技术具有检测灵敏度高、检测结果准确等优点,但操作步骤较复杂,检测时间较长,且有一定的安全隐患。
三、涡轮叶片疲劳损伤的修复技术涡轮叶片疲劳损伤修复技术主要有三种,分别是加料焊补、熔覆修复和替换修复。
1. 加料焊补:加料焊补是一种通过在叶片表面上进行焊接,并将焊接后的材料加入到焊缝中来修复涡轮叶片损伤的工艺。
某燃气轮机涡轮叶片维修周期方案设计

㊀收稿日期:2020 ̄03 ̄27㊀㊀㊀㊀㊀㊀基金项目:杭州市科学技术委员会重大科技创新专项«先进50MW等级燃气轮机数字样机设计»ꎬ«DesignofAdvanced50MWGasTurbineDig ̄italPrototype»ꎬ项目编号:20172011A02ꎮ㊀作者简介:车㊀明(1962 ̄)ꎬ男ꎬ浙江杭州人ꎬ机械工程师ꎮ主要从事汽轮机和燃气轮机现场技术服务工作ꎮ某燃气轮机涡轮叶片维修周期方案设计车㊀明1ꎬ宋洁琼1ꎬ魏佳明2ꎬ蓝吉兵2ꎬ余沛坰2(1杭州汽轮机股份有限公司ꎬ杭州310000ꎻ2杭州汽轮动力集团有限公司ꎬ杭州310000)摘要:以某型燃气轮机机组为例ꎬ对其涡轮叶片维修周期制定方法进行研究ꎮ基于准三维方法获得涡轮叶片运行各时刻温度场分布ꎬ通过有限元分析获得涡轮叶片应力/应变场分布ꎬ并计算6只叶片的低循环疲劳和蠕变寿命ꎬ根据线性累积损伤法则获得6只叶片的疲劳/蠕变交互曲线ꎮ结合该机组的实际运行工况以及涡轮叶片的疲劳/蠕变交互曲线ꎬ并采用西门子等效运行小时方法ꎬ对比了4种不同的维修周期方案对机组运行可靠性和维修经济性的影响ꎬ结果表明ꎬ每隔24000EOH或750Cycles进行涡轮叶片维修的方案为最佳ꎮ关键词:准三维分析ꎻ疲劳-蠕变交互ꎻ等效运行小时ꎻ维修周期分类号:TK478㊀㊀㊀文献标识码:A㊀㊀㊀文章编号:1001 ̄5884(2020)06 ̄0451 ̄04MaintenanceSchemesDesignofGasTurbineBladesCHEMing1ꎬSONGJie ̄qiong1ꎬWEIJia ̄ming2ꎬLANJi ̄bing2ꎬYUPei ̄jiong2(1HangzhouSteamTurbineCompanyLimitedꎬHangzhou310000ꎬChinaꎻ2HangzhouSteamTurbinePowerGroupCompanyLimitedꎬHangzhou310000ꎬChina)Abstract:Takingagasturbineunitasanexampleꎬthemethodofdeterminingthemaintenancecycleofturbinebladesisstudied.Basedonthequasithree ̄dimensionalmethodꎬthetemperaturefielddistributionoftheturbinebladeateachtimeofoperationisobtainedꎬandthestress/strainfielddistributionoftheturbinebladeisobtainedthroughthefiniteelementanalysis.Thelowcyclefatigueandcreeplifeofsixbladesarecalculatedꎬandthefatigue ̄creepinteractioncurveofsixbladesisobtainedaccordingtothelinearcumulativedamagelaw.Combinedwiththeactualoperationmodeoftheunitandthefatigue ̄creepinteractioncurveofturbinebladesꎬandusingtheSiemensequivalentoperationhourmethodꎬtheinfluenceoffourdifferentmaintenanceschemesontheoperationreliabilityandmaintenanceeconomyoftheunitiscompared.Theresultsshowthatthemaintenancescheme24000EOHor750Cyclesisthebest.Keywords:quasithree ̄dimensionalanalysisꎻfatigue ̄creepinteractionꎻequivalentoperationhoursꎻmaintenanceperiod0㊀前㊀言涡轮叶片是燃气轮机的主要部件之一ꎬ准确预估涡轮叶片寿命ꎬ同时制定合理的涡轮叶片维修周期ꎬ是保证燃气轮机机组可靠运行及减少维修成本的重要途径之一ꎮ燃气轮机涡轮叶片寿命主要受稳态蠕变㊁热疲劳㊁涂层氧化及机组其它运行特点引起的损伤的影响ꎮ稳态蠕变㊁热疲劳对涡轮叶片运行寿命的影响的研究比较普遍和广泛ꎮ目前广泛采用数值模拟方法以及统计法进行寿命预测ꎮGE[1]采用流体力学和有限元分析手段对7FA+和9FA+燃气轮机第1级涡轮静叶进行分析ꎬ其中最大径向应力出现在尾缘根部喷射冷却气流孔处ꎬ此预测与实际情况一致ꎮCESI[2]建立了透平叶片基材的热疲劳失效模型㊁叶片蠕变失效模型㊁涂层氧化失效模型ꎬ并采用有限元数值计算ꎬ预测到第一级动叶根部平台的吸力面侧边缘首先出现热疲劳裂纹ꎬ实测表明该预测结果完全正确ꎮ文献[3]搜集了日本的E级燃气轮机第一级静叶运行中出现的210000条裂纹的数据ꎬ归纳为11种代表性的裂纹模式ꎬ统计数据表明ꎬ裂纹扩展速度基本上与运行小时数和启动次数成正比ꎮ燃气轮机涡轮叶片的维修周期与燃气轮机的运行模式有关[4]ꎬ每个燃气轮机电厂都必须针对自身的运行模式制定相应的维修计划ꎬ减少非计划停机时间ꎬ降低备品备件消耗ꎬ提升电厂效益ꎬ因此ꎬ必须制定合理的维修周期ꎮ国外燃气轮机厂商都开展关于热部件维修周期制定方法的研究ꎮ文献[5]指出ꎬ三菱M701F热部件的维修周期建立在EOH(等效运行小时)的基础上ꎬ其中EOH=(AOH+AˑE)ˑFꎬAOH为实际运行小时ꎬA为正常停机㊁甩负荷㊁跳闸和快速负荷变化的校正系数ꎬE为正常停机㊁甩负荷㊁跳闸和快速负荷变化的等效次数ꎬF为燃料系数ꎬ根据热通道部件的预期寿命ꎬ提前安排维修计划ꎮ文献[6]指出ꎬ西门子公司为V94.3A设计了等效运行小时teq的寿命估算方法ꎬ确定热通第62卷第6期汽㊀轮㊀机㊀技㊀术Vol.62No.62020年12月TURBINETECHNOLOGYDec.2020道部件寿命ꎬ并根据teq数值来制定检修计划ꎬ其中teq=a1n1+ðni=1ti+fwb1t1ꎮ文献[7]指出ꎬGE公司为9F.03制定了维修间隔ꎬ维修因子=当量运行小时/实际运行小时ꎬ维修间隔期=24000/维修因子ꎮ本文首先采用数值模拟方法预测了3级涡轮叶片寿命ꎮ同时ꎬ根据机组的实际运行模式以及涡轮叶片的疲劳/蠕变交互曲线ꎬ并结合西门子等效运行小时的方法制定了针对本机组的维修周期ꎬ具体流程如图1所示ꎮ图1㊀研究流程图1㊀涡轮叶片寿命预估对3级涡轮动/静叶片的寿命进行分析ꎬ以第1级涡轮动叶为例进行详细分析ꎮ首先进行准三维温度场分析ꎬ获得运行各时刻动/静叶温度场分布ꎬ然后基于双线性随动强化-Norton本构模型得到涡轮叶片应力/应变场ꎬ根据塑性应变大小确定叶片考核区域ꎬ分别计算了考核区域的低循环疲劳寿命和蠕变疲劳寿命ꎬ并基于线性累积损伤法则获得叶片疲劳/蠕变交互曲线ꎮ1.1㊀叶片温度场分析采用准三维方法计算获得叶片基本负荷工况温度场ꎬ然后以此为基准计算其它工况温度场ꎮ叶片稳态温度场分布如图2所示ꎮ图2㊀叶片稳态温度场1.2㊀叶片强度分析第1级动叶材料为IN738LCꎬ金属表面有粘结层MCrAlY和热障涂层TBCꎮ采用带中间节点的四面体网格进行网格划分ꎮ将温度场结果赋给叶片节点ꎬ对叶片整体施加转速ꎬ加载过程如图3所示ꎬ同时约束叶根接触面位移ꎮ采用Norton方程来模拟蠕变行为ꎬ塑性屈服条件为VonMises屈服准则ꎬ与其相关联的流动法则选取Prandlt-Reuss关系ꎬ并采图3㊀动叶载荷示意图用双线性随动强化模型ꎮ通过弹塑性有限元分析得到叶片应力/应变场ꎬ由塑性应变的大小确定叶片尾缘为考核区ꎬ叶片尾缘的塑性应变㊁蠕变应变云图如图4所示ꎬS1㊁S3㊁等效应力云图如图5所示ꎮ图4㊀应变云图图5㊀应力云图1.3㊀叶片寿命分析采用带符号的等效应力和机械应变[8]ꎬ对考核点的应力/应变进行处理ꎬ获得循环应力/应变曲线ꎬ如图6所示ꎬ得到启停时考核点的应变幅值Δε=0.0033ꎬ考核点温度为750ħꎬ通过插值ε-Nꎬ获得低循环疲劳寿命N=1837cyclesꎬ如图6所示ꎮ提取了考核区域的蠕变应变随时间变化曲线ꎬ如图7所示ꎮ认为当蠕变应变为1%时叶片失效ꎬ此时第1级涡轮动叶寿命为340000hꎮ254汽㊀轮㊀机㊀技㊀术㊀㊀第62卷图6㊀低循环疲劳寿命图7㊀蠕变时间1.4㊀其余叶片疲劳/蠕变寿命分析采用相同的分析方法ꎬ计算得到其余各只叶片的低循环疲劳寿命n和蠕变寿命tꎬ见表1ꎮ根据线性累积损伤法则[9]ꎬD=nN+tTr<1ꎬ将叶片总损伤绘制在N ̄Tr图上ꎬ如图8所示ꎮ图8㊀N-Tr图㊀㊀表1各只叶片寿命叶㊀片低循环寿命nꎬcycles蠕变寿命tꎬh第1级动叶1837340000第1级静叶1090300000第2级动叶2000360000第2级静叶1875160000第3级动叶2800410000第3级静叶30723800002㊀维修周期方案对比分析研究了不同运行模式对涡轮叶片寿命的影响ꎬ同时调研了电厂运行情况ꎬ统计了本机组的运行模式ꎮ基于西门子等效运行小时维修方法制定了不同的维修周期方案ꎬ并分析了不同的维修周期方案对机组的可靠性和维修经济性的影响ꎮ2.1㊀运行模式对叶片寿命的影响以第3级动叶片为例ꎬ得到不同的运行模式对叶片损伤的影响ꎬ见表2ꎮ定义参数t/nꎬ其中ꎬt为燃机在额定工况运行时间ꎬn为燃机启停次数ꎬt/n的值代表不同运行模式ꎮ以基本负荷(t/n=400)为例ꎬ当Dtotal=0.9996ꎬ即失效ꎮ以日起停负荷(t/n=12)为例ꎬ当Dtotal=0.966ꎬ即失效ꎮ㊀㊀表2不同运行模式对叶片寿命的影响工㊀况DcreepDLCFDtotal基本负荷(t/n=400)0.07320.02680.10000.21950.08040.29990.29270.10710.39980.36590.13390.49980.43900.16070.59970.51220.18750.69970.58540.21430.79970.65850.24110.89960.73170.26790.9996日起停负荷(t/n=12)0.0240.2980.3220.0490.5950.6440.0730.8930.9660.0981.1901.288㊀㊀表中ꎬDcreep=tTrꎻDLCF=nNꎻDtotal=Dcreep+DLCFꎮ调研了电厂燃机运行模式ꎬ并进行了数据统计ꎬ本文所研究的燃气轮机主要用于调峰ꎬ取t/n=40[10]ꎮ2.2㊀4种维修周期方案对比研究本文采用西门子等效运行小时方法来制定涡轮叶片维修周期:teq=a1n1+ðni=1ti+fw(b1t1+b2t2)(1)式中ꎬn1为启动次数ꎻa1为启动系数ꎬa1=10ꎻti为由于温度快速变化产生的等效运行小时ꎻn为快速温度变化次数ꎻt1为达到基本负荷的运行小时数ꎻb1为基本负荷系数ꎻt2为在基本负荷和尖峰负荷之间的运行小时数ꎻb2为尖峰负荷系数ꎻf为燃料加权系数ꎻw为喷水的加权系数ꎮ354第6期车㊀明等:某燃气轮机涡轮叶片维修周期方案设计㊀㊀假设机组运行时都是基本载荷ꎬ燃料为天然气ꎬ无注水ꎬ所以f=w=b1=1ꎮ不考虑温度快速变化ꎬ所以ðti=0ꎬb2=0ꎬ故式(1)可化简为teq=10n+tꎮ同时ꎬ以启停次数n作为另外一种限制条件ꎬ等效运行小时或启停次数无论哪个先到达ꎬ即进行一次维修ꎮ参考国外同等级燃气轮机维修周期[5ꎬ11]ꎬ确定了以下4种不同的维修周期方案ꎬ具体数值见表3ꎮ㊀㊀表34种维修方案方案等效运行小时ꎬh启停次数ꎬcycles方案124000600方案224000750方案333000600方案433000750㊀㊀将运行模式曲线t/n绘制在叶片N-Tr图上ꎬ并以等效运行小时及启停次数为限制ꎬ采用不同的维修方案时ꎬ每只涡轮叶片所对应的最大维修间隔见表4ꎮ如采用方案1时ꎬ即每隔24000h或者600cycles进行一次维修ꎬ第1级动叶的最大维修间隔为3ꎬ即在第3次大修时需要更换第1级动叶ꎻ而第1级静叶的最大维修间隔为2ꎬ即在第2次大修时就需要更换第1级静叶ꎮ每次大修时需要更换叶片ꎬ就需要准备新备件ꎬ同时ꎬ对于调峰机组ꎬ希望其具有较高的启停次数ꎬ因此统计了不同方案所需的备件数和对应的启停次数ꎬ结果见表5ꎮ㊀㊀表4㊀不同维修方案对应每只叶片的最大维修间隔叶㊀片最大维修间隔方案1方案2方案3方案4第1级动叶3322第1级静叶2211第2级动叶3322第2级静叶2222第3级动叶4443第3级静叶4444㊀㊀表54种方案优劣对比方案100000h内最大启停次数100000h内需要替换的备件数方案124008方案230008方案318006方案422507㊀㊀对表5进行分析ꎬ可得到以下结论:(1)方案1需要8套新叶片备件ꎮ(2)方案2在100000h内允许启停次数最多ꎬ需要8套新叶片备件ꎮ(3)方案3在100000h内允许启停次数最少ꎬ需要6套新叶片备件ꎮ(4)方案4在100000h内需要7套新叶片备件ꎮ综合考虑ꎬ方案2从机组的可靠性和维修经济性上最佳ꎮ原因如下:(1)调峰机组需要有更多的启停次数ꎮ(2)在100000h内新备件的数量较少ꎬ减小维修费用ꎮ3㊀结束语本文采用准三维方法获得叶片运行各时刻温度场分布ꎬ同时采用双线性随动强化-Norton本构模型获得叶片应力/应变场分布ꎬ并计算得到各只叶片的低循环疲劳寿命和蠕变寿命ꎮ同时ꎬ根据机组的实际运行模式以及涡轮叶片的疲劳/蠕变交互曲线ꎬ并结合西门子等效运行小时方法ꎬ对比分析不同的维修周期方案的优缺点ꎬ得到以下结论: (1)通过弹塑性蠕变分析ꎬ并根据塑性应变大小ꎬ确定第1级动叶危险区域位于叶片尾缘区域ꎮ(2)分析获得各只叶片低循环疲劳寿命和蠕变寿命ꎬ并通过线性累积损伤法则得到3级叶片的N-Tr图ꎮ(3)对比分析4种维修周期方案ꎬ其中采用每隔24000h或者750次循环进行维修周期的方案为最佳ꎮ在下一阶段ꎬ本研究将根据机组外场运行数据反馈ꎬ对寿命计算进行修正ꎮ同时ꎬ在制定维修计划时ꎬ需要考虑由于快速启停或者其它因素对寿命的影响ꎬ从而调整维修周期方案ꎮ参考文献[1]㊀E.WanꎬP.Crimiꎬet.al.CombustionTurbineF-ClassLifeMan ̄agementof1stStageTurbineBlades[R].ASMEGT2002-30301.[2]㊀C.RidaldiꎬV.BicegoandP.Colomgbo.ValidationofCESIBladeLifeManagementSystembyCaseHistoriesꎬonLineMeasurementandinSiteNDT[R].ASMEGT2004-54217.[3]㊀T.FujiiandT.Takahashi.DevelopmentofaCrackGrowthPredic ̄tionSystemforfirstStageNozzleofGasTurbine[R].ASMEGT2001-0470.[4]㊀I.KhanꎬA.HamiltonandR.L.Lewellyn.TechnicalꎬFinancialandEngineeringManagementofCCGTOverhaulsInnogyOneApproachatDidcotB[R].ASMEGT2003-38874.[5]㊀毛㊀丹ꎬ诸粤珊.三菱M701F型燃气轮机维修理念分析[J].燃气轮机技术ꎬ2010ꎬ23(3):53-57.[6]㊀何㊀磊ꎬ刘明昊ꎬ崔耀欣ꎬ等.西门子SGT5-2000E燃气轮机的维护和检修[J].热力透平ꎬ2008ꎬ(1):63-67. [7]㊀DavidBalevicꎬRobertBurgerꎬDavidForry.Heavy-DutyGasTurbineOperatingandMaintenanceConsiderations.GEEnergy[R].GER-3620Kꎬ2015.[8]㊀E.VacchieriꎬS.R.HoldsworthꎬE.Poggioꎬet.al.Service-likeTMFtestsforthevalidationandassessmentofacreep-fatiguelifeproceduredevelopedforGTbladesandvanes[J].InternationalJournalofFatigueꎬ2016:S0142112316303449.[9]㊀陈立杰ꎬ江铁强ꎬ等.涡轮叶片蠕变-疲劳交互作用下寿命预测方法综述[J].航空制造技术ꎬ2004ꎬ(12):61-64ꎬ84. [10]㊀王登银ꎬ等.燃气轮机热端部件寿命的等效运行时间分析[J].技术与市场ꎬ2017ꎬ24(7):109-110.[11]㊀徐㊀刚ꎬ王㊀鑫.V94.3A型燃气轮机寿命估算方法及应用[J].发电设备ꎬ2011ꎬ23(6):381-383.454汽㊀轮㊀机㊀技㊀术㊀㊀第62卷。
航空发动机涡轮叶片疲劳特性研究

航空发动机涡轮叶片疲劳特性研究航空发动机是现代航空业的核心设备,其性能直接关乎航空运输的安全和效率。
涡轮叶片则是航空发动机中的重要部分,直接制约其性能和寿命。
因此,研究航空发动机涡轮叶片的疲劳特性成为一项热门研究课题。
一、涡轮叶片的疲劳特性涡轮叶片在长时间高速旋转的过程中,会受到高温高压的环境和离心力、惯性力等多种载荷的作用,长期使用后会出现裂纹、剥落等现象,最终导致发动机失效。
因此,研究涡轮叶片的疲劳特性十分重要。
涡轮叶片的疲劳特性受到多个因素的影响,包括环境温度、高温氧化、冷却方式等。
其中,高温氧化对涡轮叶片寿命影响最大。
在高温氧化的环境下,叶片表面会形成氧化层,减缓了疲劳成裂纹的扩展速度,但同时也导致了叶片失效后的断裂更加严重。
同时,涡轮叶片设计的合理性也会对其疲劳特性产生重要影响。
设计合理的涡轮叶片应该采用合适数量的叶片,以减轻每个叶片的载荷,同时要保证叶片的强度和刚度。
此外,正确的涡轮叶片材料选择和强度分析也是保证涡轮叶片寿命的重要因素之一。
二、涡轮叶片疲劳研究的方法涡轮叶片疲劳研究是从飞行中实际应用中的疲劳实验开始的。
在疲劳实验中,研究人员将涡轮叶片加工成标准试样,然后在不同的温度和载荷下进行测试,以研究叶片的寿命和疲劳特性。
随着科技的发展,涡轮叶片疲劳研究方法也在不断创新。
目前,主要的研究方法包括数值模拟、疲劳实验和断裂分析。
数值模拟是在计算机上模拟涡轮叶片受力情况、疲劳寿命等,对涡轮叶片的设计、材料选择、工艺参数等方面做出分析和改善。
疲劳实验可以在某些特定条件下,对涡轮叶片进行实际疲劳测试,以验证数值模拟的结果。
断裂分析则可以通过对失效叶片进行分析,研究其失效原因和方式,为涡轮叶片的设计和改进提供重要参考。
三、涡轮叶片疲劳研究的意义涡轮叶片疲劳研究的意义不仅仅是为了提高航空发动机的安全性和寿命,还可以推动材料、工艺和设计等方面的技术进步。
当前,随着人们环保意识的提高,越来越多的航空公司关注航空运输的能耗和排放。
航空发动机涡轮叶片疲劳寿命及可靠性分析
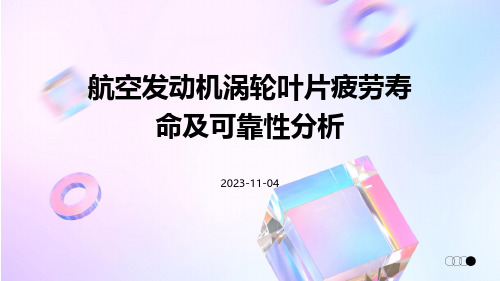
2023-11-04•引言•航空发动机涡轮叶片概述•航空发动机涡轮叶片疲劳寿命分析•航空发动机涡轮叶片可靠性分析•航空发动机涡轮叶片可靠性验证与实验目•研究结论与展望录01引言研究背景与意义航空发动机涡轮叶片是发动机的核心部件,其性能直接影响到发动机的性能和安全性。
涡轮叶片的疲劳寿命及可靠性是评估其性能的重要指标,对于保证发动机的安全运行具有重要意义。
随着航空发动机技术的不断发展,对于涡轮叶片的疲劳寿命及可靠性的要求也越来越高,因此需要进行深入的研究。
国内外对于航空发动机涡轮叶片疲劳寿命及可靠性的研究已经开展了多年,取得了一定的研究成果。
目前的研究主要集中在材料选用、结构设计、表面处理等方面,以提高涡轮叶片的疲劳寿命及可靠性。
随着计算机技术和数值模拟技术的发展,对于涡轮叶片的疲劳寿命及可靠性的分析已经越来越精确,对于发动机的设计和优化具有重要意义。
研究现状与发展02航空发动机涡轮叶片概述涡轮叶片的结构涡轮叶片由叶身、叶根和榫头等组成,叶身是工作部分,叶根是连接部分,榫头是定位部分。
涡轮叶片的功能涡轮叶片是航空发动机的关键部件之一,负责将高温高压的气体转化为机械能,为飞机提供动力。
涡轮叶片的结构与功能涡轮叶片的工作环境涡轮叶片需要在高温、高压、高转速的恶劣环境下工作,最高温度可达1000℃以上,最高转速可达每分钟数万转。
涡轮叶片的工作工况涡轮叶片需要承受周期性变化的应力、应变,以及气动力、热力等多种复杂因素的影响。
涡轮叶片的工作环境与工况涡轮叶片一般采用高温合金、钛合金等高性能材料制造。
涡轮叶片的材料涡轮叶片的制造工艺主要包括铸造、锻造、热处理、表面处理等环节,其中精密铸造和等温锻造是关键环节。
涡轮叶片的制造工艺涡轮叶片的材料与制造工艺03航空发动机涡轮叶片疲劳寿命分析03基于有限元分析的预测模型利用有限元分析软件,对涡轮叶片进行应力分析,预测不同工况下的疲劳寿命。
疲劳寿命预测模型01基于材料性能参数的预测模型考虑材料性能参数,如弹性模量、屈服强度、抗拉强度等,建立疲劳寿命与材料性能之间的数学关系。
某发动机静子叶片疲劳极限试验研究

《某发动机静子叶片疲劳极限试验研究》1.引言在航空航天领域发动机是至关重要的部件之一,而静子叶片作为发动机中的重要部分,其疲劳性能一直备受关注。
针对某发动机静子叶片的疲劳极限试验研究,我们将深入探讨该主题并给出全面评估。
2.静子叶片的工作原理及重要性静子叶片作为发动机的重要部件,主要负责引导气流,起到多种重要作用。
其疲劳性能直接关系到发动机的稳定性和可靠性,因此研究静子叶片的疲劳极限显得尤为重要。
3.静子叶片疲劳极限试验研究的必要性静子叶片在发动机工作过程中受到较大的振动和负载,因此疲劳极限试验研究对于评估其使用寿命和耐久性具有重要意义。
通过试验研究,可以更好地了解静子叶片在不同工况下的疲劳行为和性能表现。
4.研究方法及流程在静子叶片疲劳极限试验研究中,我们采用了一系列先进的实验设备和方法。
通过模拟不同的工作条件,并对静子叶片进行加速寿命试验和疲劳破坏分析,以获取准确可靠的试验数据。
5.试验结果及数据分析我们通过试验获得了大量的数据和结果,并对其进行了深入分析和解读。
在不同工况下,静子叶片的疲劳寿命和破坏特点都得到了全面的评估,并为进一步改进设计和使用提供了有力的依据。
6.个人观点及总结通过某发动机静子叶片疲劳极限试验研究,我们深刻认识到了其重要性和必要性,也增加了对于静子叶片疲劳行为的理解。
未来,我们将继续致力于静子叶片疲劳性能的研究和改进,为航空航天领域的发展做出更大的贡献。
通过对“某发动机静子叶片疲劳极限试验研究”的文章撰写,我希望您能对该主题有更深入的了解和领悟。
文章的撰写遵循了从简到繁、由浅入深的逻辑顺序,希望您能获得全面、深刻和灵活的知识体验。
在静子叶片的疲劳极限试验研究中,我们使用了先进的数字化技术和计算模拟方法,以更加准确地模拟静子叶片在不同工作条件下的疲劳受力情况。
我们在试验中使用了先进的材料测试设备和振动台,以模拟真实工作条件下的振动和负载情况。
通过这些试验设备和方法,我们成功地获取了静子叶片在不同工况下的疲劳性能数据,并对其进行了深入分析。
涡轮叶片高低周疲劳分析方法总结论文综述

本次毕业设计论文的内容是涡轮叶片高低周疲劳分析方法的总结与对比。
涡轮叶片是航空发动机工作环境最恶劣 ,结构最复杂的零件之一 ,也是发动机断裂故障多发件之一。
由于发动机工作时涡轮叶片始终在高温下承受复合载荷的作用,因此它的高周疲劳寿命和低周疲劳寿命的计算至关重要。
高周疲劳是指破坏循环数大于104~105的疲劳,高周疲劳的情况下,其应力水平低于弹性极限,没有明显的宏观塑性变形,应力与应变呈线性关系。
低周疲劳是指破坏循环数小于104~105的疲劳,低周疲劳的情况下,其应力水平高于弹性极限,有明显的宏观塑性变形,应力与应变呈非线性关系。
在《高周疲劳和低周疲劳统一的能量表征方法研究》一文中,对高周疲劳和低周疲劳预测模型进行了研究,提出了一种能够将高周疲劳和低周疲劳统一表征的能量形式参量。
用统一的能量形式表征参量对高温合金GH141的760摄氏度高周疲劳和低周疲劳数据进行处理,得到理想的能量-寿命方程。
用1Cr11Ni2W2MoV 钢500摄氏度和粉末盘材料FGH95d 600摄氏度高温低周疲劳和高周疲劳数据对统一表征方法进行验证,验证结果表明,用能量形式的表征参量能够得到理想的能量-寿命方程。
疲劳试验通常可以通过控制应变或控制应力来进行。
按照控制方式可以将疲劳分为应力疲劳和应变疲劳。
材料发生了塑性变形进入屈服阶段后,小的应力变化将引起大的变形,此时进行疲劳试验时多采用应变控制,材料的疲劳寿命一般比较短,因此通常也叫低周疲劳而当材料在没有进入屈服阶段前,采用应力和采用应变都可以进行疲劳试验,通常控制应力来进行疲劳实验,材料的疲劳寿命一般比较长,因此,通常也叫高周疲劳。
三参数幂函数能量方法寿命预测模型:采用应力控制的方式进行高周疲劳实验,用应力参量来表征高周疲劳的寿命特征;采用应变控制的方式进行低周疲劳实验,用应变参量或能量参量来表征低周疲劳的寿命特征。
如果能够用能量参量来表征高周疲劳的寿命特征,那就可以将高周疲劳和低周疲劳统一起来用一个表征参量进行表征,从而就不需将疲劳划分为高周疲劳和低周疲劳,但能量表征同时需要应力和应变参量。
航空发动机涡轮叶片材料疲劳寿命模拟分析
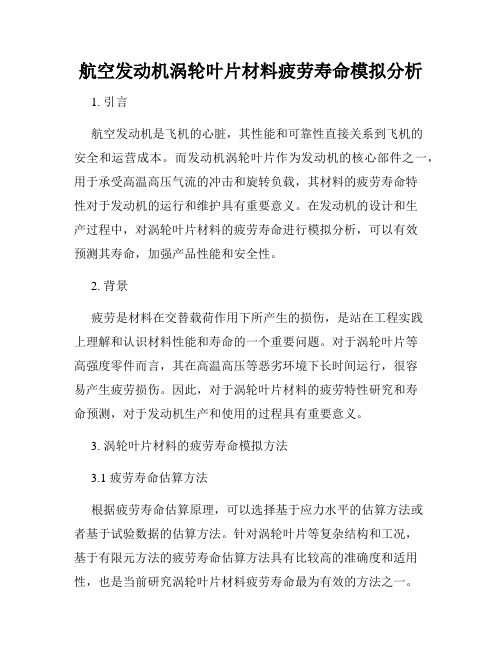
航空发动机涡轮叶片材料疲劳寿命模拟分析1. 引言航空发动机是飞机的心脏,其性能和可靠性直接关系到飞机的安全和运营成本。
而发动机涡轮叶片作为发动机的核心部件之一,用于承受高温高压气流的冲击和旋转负载,其材料的疲劳寿命特性对于发动机的运行和维护具有重要意义。
在发动机的设计和生产过程中,对涡轮叶片材料的疲劳寿命进行模拟分析,可以有效预测其寿命,加强产品性能和安全性。
2. 背景疲劳是材料在交替载荷作用下所产生的损伤,是站在工程实践上理解和认识材料性能和寿命的一个重要问题。
对于涡轮叶片等高强度零件而言,其在高温高压等恶劣环境下长时间运行,很容易产生疲劳损伤。
因此,对于涡轮叶片材料的疲劳特性研究和寿命预测,对于发动机生产和使用的过程具有重要意义。
3. 涡轮叶片材料的疲劳寿命模拟方法3.1 疲劳寿命估算方法根据疲劳寿命估算原理,可以选择基于应力水平的估算方法或者基于试验数据的估算方法。
针对涡轮叶片等复杂结构和工况,基于有限元方法的疲劳寿命估算方法具有比较高的准确度和适用性,也是当前研究涡轮叶片材料疲劳寿命最为有效的方法之一。
3.2 有限元分析方法有限元分析是目前最为广泛使用的计算机仿真分析方法之一,可以通过离散化、求解和后处理等过程,模拟大量工程问题的复杂物理场。
对于疲劳寿命分析而言,有限元分析方法可以直接基于实际工况模拟受力分布和变形情况,从而通过应力-循环寿命曲线和损伤积累特性,计算出涡轮叶片的疲劳寿命。
3.3 循环寿命分析循环寿命是材料在交替载荷作用下出现裂纹和断裂之前的循环次数。
在涡轮叶片材料疲劳寿命模拟中,通过循环寿命分析可以获取涡轮叶片材料的循环寿命,从而评估其使用寿命和寿命损伤程度。
4. 涡轮叶片疲劳寿命模拟分析实例为了更深入地了解涡轮叶片材料的疲劳特性和模拟分析过程,以下是一个典型的实例。
4.1 问题描述某型号涡轮叶片,材料为热压熔结镍基合金,叶片尺寸为长80毫米,宽22毫米,厚度3毫米。
叶片常温下的静态强度为1100MPa,材料的疲劳极限为310MPa。
- 1、下载文档前请自行甄别文档内容的完整性,平台不提供额外的编辑、内容补充、找答案等附加服务。
- 2、"仅部分预览"的文档,不可在线预览部分如存在完整性等问题,可反馈申请退款(可完整预览的文档不适用该条件!)。
- 3、如文档侵犯您的权益,请联系客服反馈,我们会尽快为您处理(人工客服工作时间:9:00-18:30)。
某涡轴发动机离心叶轮低循环疲劳试验研究作者:鲍冬冬艾书民
来源:《中国科技纵横》2020年第08期
摘要:本文针对某涡轴发动机的离心叶轮试验转接段进行试验方案设计,通过有限元分析和试验验证,对比了两种试验方案的结果,可以看出方案二的结构中压块所受应力较低,且疲劳寿命有了明显提升,说明方案二中的结构设计能满足使用需求,本项工作为涡轴发动机部件试验的研制提供了支持,并为今后转接段的设计工作提供了参考。
关键词:航空发动机;离心叶轮;低循环疲劳
中图分类号:V233 文獻标识码:A 文章编号:1671-2064(2020)08-0060-02
轮盘是航空发动机的旋转部件之一。
轮盘工作时承受着高温、高离心载荷等作用,轮盘的失效直接影响航空发动机的可靠性、使用性能和维护成本,甚至危及飞机和乘员的安全,导致灾难性的后果,因此,轮盘被列为发动机的关键件,对发动机工作的安全性、可靠性[1]、耐久性有重要影响,而低循环疲劳破坏是发动机轮盘寿命损耗的最大问题之一,据统计,航空发动机结构故障占总故障的60%~70%,疲劳破坏占发动机结构故障的80%~90%。
通常轮盘破坏会产生巨大的碎块功能,发动机无法包容,所以会产生很严重的后果,离心叶轮作为发动机的寿命关键件,通常需要通过低循环疲劳试验来进行寿命评估,而离心叶轮的低循环疲劳试验转接段是专门用于离心叶轮试验的转接装置,其作用是将试验件与试验器相连接,一般情况下为保证试验结果真实可靠,应当在条件允许的情况下尽可能模拟试验件在发动机上的连接形式,应通过对比分析计算,确认试验件的在试验条件下的受力状态与发动机使用条件下的受力状态相同,关键部位的装配应力及其分布,接近发动机条件下的装配应力,应避免由于变形协调情况不同和装配应力不同而产生附加载荷,所以转接段的设计应当考虑参考发动机的连接方式,并且转接段不应该对轮盘有明显的加强和削弱的作用。
1 试验方案设计
在试验方案设计的过程中,会考虑很多因素,为了解决试验转接段的动力学特性问题,同时综合考虑试验转接段与试验器的连接通用性,转接段与试验件的连接方式及加工等问题,对本次试验方案的设计重点在以下两个方面:(1)根据离心叶轮的应力分析,确定考核部位;(2)在保证与离心叶轮在发动机上连接方式的相同之余,优化试验转接段本身的动力学特性。
1.1 考核部位的确定
对离心叶轮进行了相关分析,采用UG建立计算用实体模型,采用ANSYS进行前后处理以及有限元分析。
对离心叶轮计算模型进行简化处理,去除花键及端齿等特征,简化后的离心叶轮结构和载荷均具有循环对称性,采用循环对称方法进行计算,取包含一对大小叶片在内的整个试验件的1/15循环对称段作为计算模型。
本次计算分析主要考虑了离心载荷、温度载荷、气动力、预紧力和腔压:离心载荷以转速的形式施加在整个计算模型上;温度载荷以节点温度的形式施加在所有节点上,详细应力计算结果见表1。
经计算发现,试验件在发动机工作状态下最大当量应力位置在轮盘上,而在此状态下轮盘的应力计算结果见表2。
可以发现轮心和前端齿的最大当量应力较大,故将轮心和前端齿确定为考核部位。
1.2 试验转接段结构的确定
根据试验件在发动机上连接方式,设计了两种结构的试验转接段,这两种结构主要区别在于压块结构的不同,分别见图1和图2所示。
试验方案一的思路主要是模拟了发动机上与离心叶轮相连接的二三级盘的结构,材料也与二三级盘相同,其目的是完全模拟离心叶轮在发动机上的受力状态和协调变形,二三级盘的结构见图3,可以看出第一种试验方案的压块与二三级盘的结构是完全相同的。
试验方案二的思路主要是模拟了发动机上与离心叶轮相连接的端齿结构,结构与二三级盘结构不同。
由于前端齿的应力较大,所以与之相连接的压块的结构对于试验的影响较大,在试验中体现得较为明显。
2 试验验证
2.1 试验结果对比
将离心叶轮分别与两种结构的转接段装配后,进行低速动平衡合格后与试验器连接后进行试验,试验载荷谱见图4。
方案一离心叶轮在完成了31605次试验循环后,转接段中的压块端齿部分产生了裂纹,见图5所示,经过理化分析可知,压块端齿薄壁部位可能是较早期的源区,而方案二则顺利完成试验。
结合两种方案的试验结果,可以看出方案二中的压块结构更加稳定。
2.2 试验转接段疲劳寿命对比分析
疲劳寿命计算过程如下:用Goodman曲线(见图6)把已知的工作循环(M点)转换到应力比R为0.1的循环(N点),按照以下三式联立求出应力比R为0.1时的最大应力,然后利用S-N曲线方程即可求出相应的循环次数。
式中:为应力幅; 为平均应力;R为应力比。
根据文献[2]:300℃下应力比R=0.1的轴向光滑疲劳S-N曲线:
lgNf=38.42139-11.6983×lg(中值)
450℃下应力比R=0.1的轴向光滑疲劳S-N曲线[3]:
lgNf=53.4037-17.148×lg(中值),试验转接段寿命[4]对比计算结果见表3。
经过模拟计算可以看出,两种结构都可以保证试验状态下的离心叶轮与发动机状态下的离心叶轮所受的应力状态相同,而方案一中压块结构所受应力比方案二中压块结构所受应力大,且寿命短,说明方案二中的压块不会发生比试验件更早出现疲劳裂纹的现象,与试验结果相符。
3 结论
针对两种试验方案的结果对比,得到结论:
(1)经过计算和试验结果可以表明:方案二中试验转接段的结构可以达到预期效果;
(2)在保证与原工作状态一致的情况下,试验转接段的结构不是必须要设计与连接件相同的结构;
(3)在保证应力状态不变的情况下,应该将转接段所受的当量应力降低,这样可以相应延长其疲劳寿命,从而达到考核试验件的目的。
参考文献
[1] 《中国航空材料手册》(第4卷)[M].北京:中国标准出版社,2001.
[2] 李钢.发动机设计用材料性能数据手册[D].株洲:第六〇八研究所,2010.
[3] 宋兆泓.航空燃气涡轮发动机强度设计[M].北京:北京航空学院出版社,1988.
[4] 曹凤梅.倒圆对产品质量的影响[J].论坛集萃,2012:56-57.。