表面处理技术在模具中的应用和发展_王平
表面技术在模具中的应用

在 现代生 产 中, 模 具是各 种工 业产 品生产 的重 要工艺 装备 。 随着 尖端 科学
技术和 现 代工业 的 发展 , 人们对 模具 工艺 提 出的要求 越来越 高 , 因为它们 直接
有高 硬度 、 高 耐学 f 生以及 高的抗蚀 陛等优异 陛能 。 硬 化膜沉积技 术 目前较成 熟的 是C V D、 P VD 法, 为 了增 加 膜层 工件 表面 的结 合强 度 , 现在 发展 了多种 增 强型 C V D、 P V D 技术 。 硬 化膜沉积 技术最早在工 具( 刀具、 刃具 、 量具 等) 上应用 , 效果极 佳, 多种 刀具 已将涂 覆硬化膜 作为标 准工 艺。 到 目前为止 , 硬 化膜沉 积技术 的成
[ K e y w o r d s ] mo u l d ; s u r f a c e t r e a t i n g; Ha r d e n e d衄m d e p o s i t i o n
中图分类 号 : T D5 3
1 . 引言 :
文献标 识码 : A
文章 编号 : 1 0 0 9 - 9 1 4 X( 2 0 1 4 ) 4 3 - 0 2 8 6 - 0 1 也 是应 用最广 泛 的模 具表 面处 理技 术 。 硬化膜 沉积是 利用物理 或化学 方法在 固体表 面生成 固态 沉积物 , 使工 件具
[ A b s t r a c t ] E f e c t o f s u r f a c e t r e a t i n g t e c h n o l o g y i n i mp r o v ng i t h e q u a l i t y o f mo u l d wa s
面技术 是提 高表 面性 能常 用的工 艺方法 , 是降低 成本 、 提 高模 具质量 和使 用寿 命 的最 有 效途径 , 对 于 充分 发挥 模具材 料 的潜 能都 具有 非凡 意义 。 2 . 模 具表 面 处理 技术
分析模具制造中的表面处理技术的发展趋势和应用
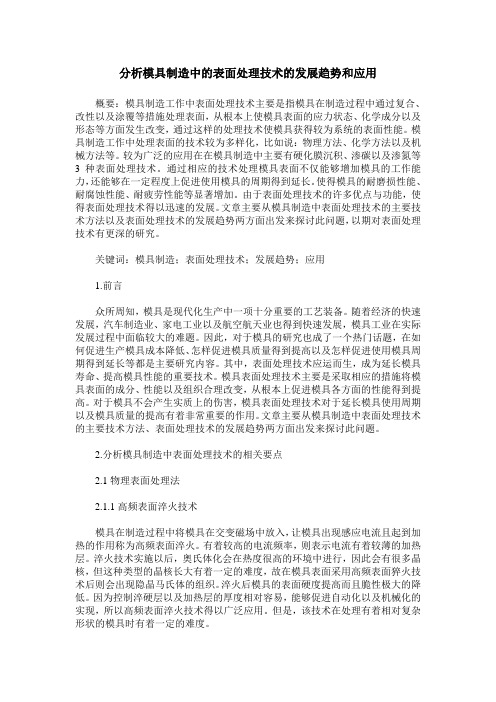
分析模具制造中的表面处理技术的发展趋势和应用概要:模具制造工作中表面处理技术主要是指模具在制造过程中通过复合、改性以及涂覆等措施处理表面,从根本上使模具表面的应力状态、化学成分以及形态等方面发生改变,通过这样的处理技术使模具获得较为系统的表面性能。
模具制造工作中处理表面的技术较为多样化,比如说:物理方法、化学方法以及机械方法等。
较为广泛的应用在在模具制造中主要有硬化膜沉积、渗碳以及渗氮等3种表面处理技术。
通过相应的技术处理模具表面不仅能够增加模具的工作能力,还能够在一定程度上促进使用模具的周期得到延长。
使得模具的耐磨损性能、耐腐蚀性能、耐疲劳性能等显著增加。
由于表面处理技术的许多优点与功能,使得表面处理技术得以迅速的发展。
文章主要从模具制造中表面处理技术的主要技术方法以及表面处理技术的发展趋势两方面出发来探讨此问题,以期对表面处理技术有更深的研究。
关键词:模具制造;表面处理技术;发展趋势;应用1.前言众所周知,模具是现代化生产中一项十分重要的工艺装备。
随着经济的快速发展,汽车制造业、家电工业以及航空航天业也得到快速发展,模具工业在实际发展过程中面临较大的难题。
因此,对于模具的研究也成了一个热门话题,在如何促进生产模具成本降低、怎样促进模具质量得到提高以及怎样促进使用模具周期得到延长等都是主要研究内容。
其中,表面处理技术应运而生,成为延长模具寿命、提高模具性能的重要技术。
模具表面处理技术主要是采取相应的措施将模具表面的成分、性能以及组织合理改变,从根本上促进模具各方面的性能得到提高。
对于模具不会产生实质上的伤害,模具表面处理技术对于延长模具使用周期以及模具质量的提高有着非常重要的作用。
文章主要从模具制造中表面处理技术的主要技术方法、表面处理技术的发展趋势两方面出发来探讨此问题。
2.分析模具制造中表面处理技术的相关要点2.1物理表面处理法2.1.1高频表面淬火技术模具在制造过程中将模具在交变磁场中放入,让模具出现感应电流且起到加热的作用称为高频表面淬火。
材料科学中表面处理技术及应用前景展望

材料科学中表面处理技术及应用前景展望表面处理技术在材料科学领域中具有重要的地位和广泛的应用前景。
随着科技的不断进步和材料需求的多样化,不同表面处理技术的发展与应用也日益增多,为各行各业的材料需求提供了多种解决方案。
本文将重点介绍表面处理技术的基础知识、常见的表面处理技术和其应用前景展望。
首先,我们来了解一下表面处理技术的基本概念和原理。
表面处理技术是指对物体表面进行物理、化学或机械处理,以改变其表面性质、形态或者实现特定的功能。
表面处理技术主要通过改变材料表面的化学成分、组织结构或形貌等方式来达到预期的目的。
其基本原理是通过增加表面层的相关组成、改变材料的物理性质,从而在一定程度上改变材料整体的性能。
在表面处理技术中,最常见的方法之一是化学处理。
化学处理一般是通过在材料表面形成一层化学膜或改变材料的化学成分来实现。
例如,阳极氧化是一种常用的化学处理方法,可以在金属表面形成一层致密的氧化膜,提高金属的耐腐蚀性、耐磨性和硬度。
此外,化学镀、电镀和浸渍等方法也常用于表面处理,使材料具有一定的防腐蚀、导电、绝缘等功能。
除了化学处理,物理处理也是表面处理技术的重要手段之一。
电子束熔凝、电弧喷涂和激光熔凝等物理处理方法可以通过高能量束的作用,改变材料表面的内部结构和形貌,提高材料的硬度、强度和耐磨性。
物理气相沉积(PVD)和化学气相沉积(CVD)也是常见的物理处理方法,通过在材料表面沉积一层薄膜来改变其表面性质,如陶瓷涂层、纳米薄膜等。
随着科技的发展,表面处理技术在科学研究和工业生产中得到了广泛应用。
在航空航天领域,表面处理技术可以提高材料的抗氧化、耐热和耐高温等性能,用于制造高温合金和热防护涂层等。
在电子信息领域,表面处理技术可以制备导电性好、抗氧化和耐蚀的电子元件,如金属薄膜电阻器、集成电路和光纤等。
此外,在能源领域、环境保护领域和生物医学领域,表面处理技术也具有广阔的应用前景。
在能源领域,表面处理技术可以提高太阳能电池板的光吸收效率和光电转化效率,同时降低材料的成本和环境污染。
表面处理技术在模具之应用及发展

表面處理技術在模具之應用及發展金屬工業研究發展中心一、前言近年來由於加工環境自動化及高速化之發展,對於模具壽命的要求日益提高。
影響模具壽命的因素包括材料、加工、熱處理、表面處理及使用條件等,各因素間往往相互影響,而其中表面處理製程在適當的選擇及應用下,可以在最短時程內,獲致壽命明顯的改善。
本文即針對國內已可工業應用之表面處理技術,如物理蒸鍍(PVD)、化學蒸鍍(CVD)、熱反應擴散被覆(TRD)製程之技術發展及應用現況加以說明。
二、製程介紹及應用1.物理蒸鍍製程(physical vapor deposition)物理蒸鍍處理屬於原子類型的被覆技術,基本特點是蒸鍍材料以原子、離子、分子和離子團等原子級尺寸的顆粒形態於工作表面沈積,形成一層緻密的被覆層。
物理蒸鍍處理可分為:真空蒸鍍、濺射、離子蒸鍍三大類,表1為真空蒸鍍、濺射及離子蒸鍍之比較。
針對模具及刀具要求,底材與被覆層間須有優越射著性的物理蒸鍍處理技術首推離子蒸鍍。
(1)離子蒸鍍基本原理:真空環境下藉由電氣方式使蒸鍍材料蒸發,經過輝光放電區使蒸鍍材料與通入之反應氣體離子化,形成由帶電離子、電子.原子、分子等的電漿,此電漿作用於工件表面,工件表面與電漿中的活性原子與離子起反應,使表面狀態發生改變而獲得被覆層。
離子蒸技術將真空室中的輝光放電電漿技術及真空蒸鍍膜技術結合在一起,不僅明顯提高鍍層的各種性能且大大擴充應用範圍。
(2)離子蒸鍍的特點:附著力強─由於離子轟擊對工作表面產生清潔、蝕刻、加熱、注入、擴散等作用,增強被覆層與工作表面的附著強度。
繞附性好─蒸鍍材料在電漿區被解離為正離子,這些正離子將沿電場的電力線運動,凡是電力線分佈之處均可到達,而工作表面帶負電壓,因此工作的正面及背面都處於電場之中,使得蒸鍍材料的帶電原子能到達工件的所有表面而沈積鍍層,其次氣體的散射效應亦促使工作所有表面均能被被覆。
鍍層緻密─離子蒸鍍過程在真空條件下進行,具有輝光放電及離子轟擊作用,因此鍍層組織緻密,針孔氣泡少。
表面处理技术在模具中的应用和发展

2物 理 表 面 处理 法 2 . 1高频淬火
在现代 生产 中,模 具作 为一种重 要的工艺设备 ,对于各种工业 产 品生产至关重要 。伴随着市场经济 的快速发展 ,各行业 也都有 了 突飞猛进 的发展 ,在模具应用较为广泛和深入 的诸 多行业 ,如航 空 航天 、家 电工业和汽车制造行业等 ,对 于模具 工艺作 出了更为严格 的要求 。因此 ,降低生产成本 、提高模具质量水平 ,延长其使用寿 命成为行业 内亟待解决 的重要 问题 。在模具工 艺中,表面 处理技术 对于模具生产成本 的降低 、质量水平 的提高和使用寿 命的延 长有着 极为重要 的意义 。在模具表面处理工艺 中,可 以通过 各种表面 处理 技术 的运用 ,使模具表层性能 、成分与 组织得 以改变 ,进 而实现模 具表面性能 的大幅改善与优化 ,例如模具 的隔热性 能、脱模 性能和 摩擦性能 的增强 ,耐磨性 、硬度 、抗咬合性 能得 以增 强,型腔表面 抗擦伤能力和高温抗氧化性能 、耐腐蚀 性能 的提 高等 等。使模 具使 用寿命得 以大幅度提 高。模具生产成本及质量控制等 方面得 到极大 的优化 ,同时也促进 了生产效率 的提高 ,模 具材料 的潜能 也得 以充 分发挥 。模 具表面处理工 艺中,笔者在 本文 中针对集 中常用的处理 技术展开分析与探讨。 1化 学表层 处理法 所谓化 学表层 处理法 ,是指 为达 到技术要 求、使模具表 层性能 得 以提高 ,用指定温度 的活性介质对模具实施保温效 果,同时将 多 种或单一 的元素渗入模具表层 ,使模具表层 的化 学组 织与成分 发生 改变 的一种模具 处理工艺 。以表层渗入 的¨ 元 素类别对 化学表层 处理 法进行 区分 ,通常有渗硼 、渗氮 、渗碳 、氮碳共渗 、渗钒 、渗铝等
表面处理技术在汽车覆盖件模具零件中的应用
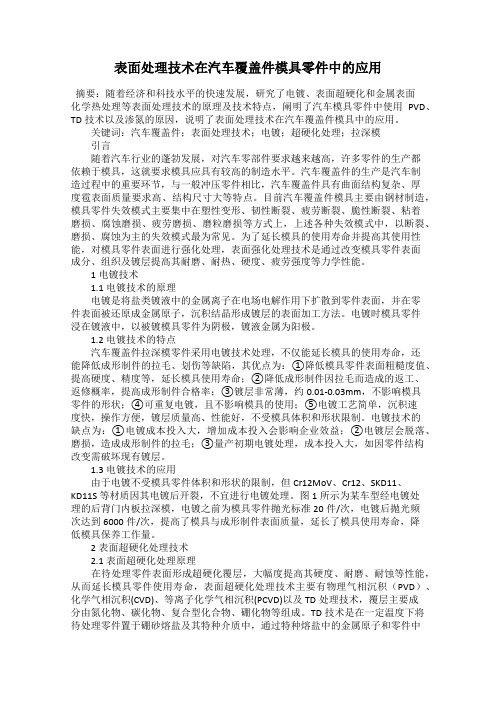
表面处理技术在汽车覆盖件模具零件中的应用摘要:随着经济和科技水平的快速发展,研究了电镀、表面超硬化和金属表面化学热处理等表面处理技术的原理及技术特点,阐明了汽车模具零件中使用PVD、TD技术以及渗氮的原因,说明了表面处理技术在汽车覆盖件模具中的应用。
关键词:汽车覆盖件;表面处理技术;电镀;超硬化处理;拉深模引言随着汽车行业的蓬勃发展,对汽车零部件要求越来越高,许多零件的生产都依赖于模具,这就要求模具应具有较高的制造水平。
汽车覆盖件的生产是汽车制造过程中的重要环节,与一般冲压零件相比,汽车覆盖件具有曲面结构复杂、厚度雹表面质量要求高、结构尺寸大等特点。
目前汽车覆盖件模具主要由钢材制造,模具零件失效模式主要集中在塑性变形、韧性断裂、疲劳断裂、脆性断裂、粘着磨损、腐蚀磨损、疲劳磨损、磨粒磨损等方式上,上述各种失效模式中,以断裂、磨损、腐蚀为主的失效模式最为常见。
为了延长模具的使用寿命并提高其使用性能,对模具零件表面进行强化处理,表面强化处理技术是通过改变模具零件表面成分、组织及镀层提高其耐磨、耐热、硬度、疲劳强度等力学性能。
1电镀技术1.1电镀技术的原理电镀是将盐类镀液中的金属离子在电场电解作用下扩散到零件表面,并在零件表面被还原成金属原子,沉积结晶形成镀层的表面加工方法。
电镀时模具零件浸在镀液中,以被镀模具零件为阴极,镀液金属为阳极。
1.2电镀技术的特点汽车覆盖件拉深模零件采用电镀技术处理,不仅能延长模具的使用寿命,还能降低成形制件的拉毛、划伤等缺陷,其优点为:①降低模具零件表面粗糙度值、提高硬度、精度等,延长模具使用寿命;②降低成形制件因拉毛而造成的返工、返修概率,提高成形制件合格率;③镀层非常薄,约0.01-0.03mm,不影响模具零件的形状;④可重复电镀,且不影响模具的使用;⑤电镀工艺简单,沉积速度快,操作方便,镀层质量高、性能好,不受模具体积和形状限制。
电镀技术的缺点为:①电镀成本投入大,增加成本投入会影响企业效益;②电镀层会脱落、磨损,造成成形制件的拉毛;③量产初期电镀处理,成本投入大,如因零件结构改变需破坏现有镀层。
表面处理技术在模具中的应用和发展

表面处理技术在模具中的应用和发展【摘要】表面处理技术的应用极大地推动了模具发展。
本文对于保证模具质量水平所应用的表面处理技术进行概述,并分别从化学表面处理法、物理表面处理法和表面覆层处理法等方面就模具表面处理技术进行分析与探讨。
【关键词】模具;发展;表面处理技术前言在现代生产中,模具作为一种重要的工艺设备,对于各种工业产品生产至关重要。
伴随着市场经济的快速发展,各行业也都有了突飞猛进的发展,在模具应用较为广泛和深入的诸多行业,如航空航天、家电工业和汽车制造行业等,对于模具工艺作出了更为严格的要求。
因此,降低生产成本、提高模具质量水平,延长其使用寿命成为行业内亟待解决的重要问题。
在模具工艺中,表面处理技术对于模具生产成本的降低、质量水平的提高和使用寿命的延长有着极为重要的意义。
在模具表面处理工艺中,可以通过各种表面处理技术的运用,使模具表层性能、成分与组织得以改变,进而实现模具表面性能的大幅改善与优化,例如模具的隔热性能、脱模性能和摩擦性能的增强,耐磨性、硬度、抗咬合性能得以增强,型腔表面抗擦伤能力和高温抗氧化性能、耐腐蚀性能的提高等等。
使模具使用寿命得以大幅度提高。
模具生产成本及质量控制等方面得到极大的优化,同时也促进了生产效率的提高,模具材料的潜能也得以充分发挥。
模具表面处理工艺中,笔者在本文中针对集中常用的处理技术展开分析与探讨。
1化学表层处理法所谓化学表层处理法,是指为达到技术要求、使模具表层性能得以提高,用指定温度的活性介质对模具实施保温效果,同时将多种或单一的元素渗入模具表层,使模具表层的化学组织与成分发生改变的一种模具处理工艺。
以表层渗入的元素类别对化学表层处理法进行区分,通常有渗硼、渗氮、渗碳、氮碳共渗、渗钒、渗铝等等。
模具表面的耐腐蚀性、耐磨性、抗氧化性和抗疲劳强度均可通过化学表层处理法得到大幅提高。
1.1渗硼渗硼方法分为多种,如盐浴渗硼、固体渗硼和气体渗硼等。
国际上的处理方法以固体渗硼和盐浴渗硼较为常见。
表面工程技术在模具制造中的应用

表面工程技术在模具制造中的应用作为一门科学与技术,表面工程能够有效的改善电子电器元件、机械零件等基质材料表面的性能。
如今,表面工程中的各项表面技术已经被广泛的应用到各类机电产品当中,显然已经成为了现代制造技术的重要组成部分,是当前维修、再制造环节中是基本手段。
文章首先对模具表面的主要处理技术进行了详细的阐述,其次对表面工程技术在模具制造中的应用进行了系统的分析与探讨。
标签:模具制造;表面工程技术;应用作为模具工业的基础,模具材料随着模具工业的迅猛发展,其不但需要具备较高的韧性、强度之外,还需要具有良好的综合性能。
通过表面工程技术的应用,不仅能让模具表面的各种性能得到相应的提高,并且模具内部也将保持着足够的强韧性。
显然,它的应用对于模具综合性能的改善、材料潜力的发挥、成本的降低、合金元素的节约以及模具新材料的进一步利用来说,都十分有效。
1 模具表面的主要处理技术1.1 硬化膜沉积技术物理气相沉积技术、化学气相沉积(CVD)是目前较为成熟的硬化膜沉积技术。
硬化膜沉积技术在最早出现的时候,通常都是应用在刀具、量具等工具上,有着极佳的效果。
并且,很多刀具都已经将涂覆硬化膜当做成最为标准的工艺。
在目前的实际应用过程中,我们不难发现,硬化膜沉积技术的成本是较高的,尤其体现在设备的成本上。
同时,硬化膜沉积技术依旧只应用于一些较精密且具有长寿命的模具上,如果通过建立热处理中心的方式来对其应用,必定会大大降低涂覆硬化膜的成本。
显然,在硬化膜沉积技术的应用下,整个模具制造的水平将得到实质性的提高。
1.2 滲氮技术在整个渗氮工艺中,具有离子渗氮、液体渗氮、气体渗氮等多种方式,而每一种不同的渗氮方式中都具有诸多不同的渗氮技术,这些不同的技术能够有效的适应不同工件、不同钢种的实际要求。
另外,由于渗氮技术能够有效的形成性能较为优良的表面,并且渗氮的温度较低,在渗氮后并不需要激烈的冷却,而模具的变形也很小,加之渗氮工艺和模具钢淬火工艺之间具有良好的协调性。
- 1、下载文档前请自行甄别文档内容的完整性,平台不提供额外的编辑、内容补充、找答案等附加服务。
- 2、"仅部分预览"的文档,不可在线预览部分如存在完整性等问题,可反馈申请退款(可完整预览的文档不适用该条件!)。
- 3、如文档侵犯您的权益,请联系客服反馈,我们会尽快为您处理(人工客服工作时间:9:00-18:30)。
文章编号:1001-4934(2007)05-0058-05表面处理技术在模具中的应用和发展王 平1,魏晓伟2,杨 军1( .西南石油大学 材料科学与工程学院,四川 南充 63700 ) .西华大学 材料科学与工程学院,四川 成都 6 0039)摘 要:简要地概述了表面处理技术在提高模具质量中的作用,按物理表面处理法、化学表面处理法和表面覆层处理法对模具表面处理技术进行了综述。
最后指出了表面处理技术在模具发展中的重要作用。
关键词:模具;表面处理;发展中图分类号:TG156文献标识码:BAbstract : Effect of surface treating technology in improving the quality of mould was introduced in brief .The mould surface treating technology was introduced by classification of physics surface treating ,chemical surface treating and clad surface treating .Finally ,it was pointed out that surface treating technology acted as an important role in mould development .Keywords : mould ;surface treating ;development收稿日期: 007-03- 9作者简介:王 平( 98 -),男,硕士研究生。
0 引言模具在现代生产中是生产各种工业产品的重要工艺装备。
随着社会经济的发展,特别是汽车、家电工业、航空航天的迅猛发展,对模具工业提出了更高的要求。
如何提高模具的质量、使用寿命和降低生产成本成为当前迫切需要解决的问题。
表面处理在模具中的应用是提高模具质量和使用寿命,降低成本的最有效途径。
通过采用不同的表面处理技术,只改变模具表层的成分、组织、性能,从而大幅度地改善和提高模具的表面性能,如硬度、耐磨性、摩擦性能、脱模性能、隔热性能、耐腐蚀和高温抗氧化性能、提高型腔表面抗擦伤能力、脱模能力、抗咬合等特殊性能,数倍、几十倍地提高模具使用寿命。
这对于提高模具质量,大幅度降低生产成本,提高生产效率和充分发挥模具材料的潜能都具有重要意义[ ]。
在模具上使用的表面技术方法多达几十种,主要可以归纳为物理表面处理法、化学表面处理法和表面覆层处理法。
本文综述了模具表面处理中常用的部分表面处理技术。
1 物理表面处理法1.1 高频表面淬火[2]高频淬火是把模具置于一个交变磁场中,模具产生感应电流而被加热。
电流频率越高,电流加热层愈薄。
淬火以后,由于奥氏体化是在较大的过热度下进行的,因此晶核多,不易长大,淬火后组织为细隐晶马氏体。
表面硬度高,比一般淬火提高HRC -3,而且脆性较低。
显著提高模具的疲劳强度,小尺寸模具可以提高 - 倍,大件也可以提高 0 %-30 %。
加热温度和淬硬层厚度易控制,便于实现机械化和自动化,得到了广泛的应用。
但对于形状复杂的模具处理比较困难。
1.2 火焰表面淬火火焰表面淬火是用乙炔-氧或煤气-氧等火焰加热模具表面。
火焰温度很高(3 000 ℃以上),能将工件表面迅速加热到淬火温度。
然后空冷或立即用水喷射冷却。
调节加热时间和冷却速度可以调节淬硬层厚度和硬度。
和高频表面淬火相比,具有设备简单,成本低等优点,但是生产率低,模具表面存在不同程度的过热,质量控制比较困难。
因此主要适用于单件、小批量和质量要求不高的模具的表面处理。
1.3 激光表面淬火[3]激光用于模具表面的处理方法包括激光相变硬化(LT H)、激光表面涂覆及合金化(LCS/LSA)、激光表面融化处理(LSM)、激光冲击(LSH)和激光非晶化等。
目前激光相变硬化和激光表面涂覆及合金化已被研究应用于提高模具寿命。
其中激光相变硬化应用较为广泛。
激光相变硬化(激光淬火)是利用激光辐照到金属表面,使其表面迅速升温达到相变温度而形成奥氏体,当激光束离开后,利用金属本身的热传导而发生“自淬火”,使金属表面发生马氏体转变。
与传统的淬火方法相比,激光淬火是在较高的温度梯度下进行的,在表面形成了一层硬度极高的特殊淬火组织。
淬火层的硬度比普通淬火的硬度还高 5 %- 0 %,淬硬层深度可达0. - .5 mm。
因此可以大幅度地提高模具的耐磨性和使用寿命。
如对T8A钢制冲头和Cr Mo钢制的凹模进行激光硬化处理后,由冲压 .5万件提高到 0万件。
喷丸强化和加工硬化也是模具表面处理常用的表面处理方法。
2 化学表面处理法化学表面处理法是将模具置于一定温度的活性介质中保温,使一种或几种元素渗入模具表面,改变模具表面的化学成分和组织,达到改进表面性能和满足技术要求。
按照表面渗入的元素不同,化学表面处理法可分为渗碳、渗氮、碳氮共渗、渗硼、渗铝、钒等金属。
化学表面处理能有效提高模具表面的耐磨性、疲劳强度、耐蚀性和抗氧化性能。
2.1 渗碳渗碳是使模具表面形成一层 - mm的含碳量为0.8 %- .05 %渗层。
经过适当淬火与回火处理,可提高模具表面的硬度、耐磨性及疲劳强度,使模具芯部仍保持良好的韧性和塑性。
因此渗碳主要用于同时受严重磨损和较大冲击载荷的模具。
由于渗碳温度较高,渗后还需热处理,模具变形较大,因此精度要求较高的模具不宜采用。
模具的渗碳工艺有固体渗碳、气体渗碳、真空渗碳和离子渗碳。
与传统渗碳相比,离子渗碳具有渗碳效率高、碳浓度梯度平缓、工件变形小、环境污染小以及狭缝和小孔都能处理的优点。
2.2 渗氮模具经过渗氮处理后,表面的耐磨性、抗疲劳作用、抗热、抗蚀、硬度和抗咬合性能都比渗碳处理后优越。
与渗碳相比,渗氮的温度较低(500 ℃-600 ℃),模具渗氮后变形小。
渗氮工艺复杂、时间长、成本高,一般用于耐磨性和精度或抗热都要求较高的模具。
随着软氮化、离子氮化等新工艺的发展,逐渐解决了普通渗氮时间长、功效低的缺点。
可通过调节气体组分来调节控制氮化组织、降低渗氮层的脆性,不易产生剥落和热疲劳。
W6Mo5Cr4V钢制冷挤凸模经过离子渗氮后,使用寿命可提高 -3倍:5CrMnMo钢热锻模离子氮化后,磨损量减到原来的 /4。
离子渗氮[4]在所有的模具处理中都有应用,但是对于形状复杂的模具,难以获得均匀的加热和渗层,同时渗层较浅。
2.3 碳氮共渗碳氮共渗就是同时向零件表面渗入碳和氮的化学处理工艺,也称氰化。
主要有液体和气体碳氮共渗两种。
液体碳氮共渗有毒,污染环境,劳动条件差,已很少应用。
共渗处理速度快,模具变形小,较高的耐磨性、抗粘着性,模具寿命可提高 -5倍。
2.4 渗硼、渗金属渗硼方法有固体渗硼、气体渗硼、盐浴渗硼等。
国内外应用较多的是盐浴渗硼和固体渗硼。
苏联将该法用于冷热加工模具上,对溶盐电解法研究的很多;日本发展了以硼砂溶盐为主的液体渗硼及其它元素的T D法,提高模具寿命4- 0倍;德国、美国[5]也都搞了很多硼与其它元素的共渗工艺。
通过渗铬后可显著提高模具使用寿命,尤其是对在热态工作或承受强烈磨损的模具。
适用于锤锻模、压铸模、塑料模、拉深模等冷热作模具,渗铬后使用寿命可提高几到数十倍。
3 表面覆层处理法3.1 电镀、刷镀、化学镀电镀硬铬、硬镍是模具表面处理技术中的传统技术,通过利用电化学的方法在模具工作面上沉积薄层金属或合金的一种湿式镀覆。
电镀操作温度低,模具发生变形较小,模具本身的性能几乎不受影响,镀层的摩擦系数低,显微硬度可达800 H V,可以大大提高模具的耐磨性。
但是,镀层的孔隙较大,耐腐蚀性能不高,不适用于耐腐蚀性要求高的模具。
同时,由于电镀具有尖端效应,对于多孔、形状复杂的模具也不适用。
刷镀工艺简单,沉积速度快,操作方便,镀层质量和性能较好。
易于现场操作,不受模具大小和形状的限制,用在报废模具和大模具的修复上经济效益明显。
刷镀应用于热作模具,可提高模具寿命50 %- 00 %,主要原因是刷镀层有良好的红硬性、耐磨性和抗氧化能力。
刘元义[6]研究表明材料为3C r W8V的热冲模刷镀处理后表面硬度达750 H V,模具寿命提高 -3倍。
刷镀也可以大幅度提高冷作模具的寿命,这是因为刷镀层有高的硬度和良好的抗粘着性能。
北京内燃机总厂的连杆盖模3Cr W8V经刷镀处理后提高寿命54.5 %。
化学镀是利用还原剂把电解质溶液中的金属离子化学还原在呈活性催化的工件表面沉积出能与基体表面牢固结合的涂镀层。
化学镀没有电镀中因为电力分布不均而造成的深镀和分散能力差的问题。
它对于形状复杂、多孔洞、有棱边夹角的模具的处理最为有效,克服了电镀的缺点与不足。
在汽车用铸模、铝模具上化学镀镍,不仅可以提高脱模效果,还可提高模具50 %的使用寿命,且零部件的光洁度高。
如用45#钢加表面N i-P化学镀代替不锈钢制作塑料型材挤出模,不但降低模具制造成本,而且可以提高模具寿命,由于镀层改善了脱模性能,塑料成形周期缩短,型材表面质量显著改善。
在生产应用中对模具表面性能要求是多元的,因此单金属的镀层往往不能满足质量要求,这些促使了复合镀技术的发展。
现在复合镀技术的实施主要借助于电镀、刷镀、化学镀。
复合镀后膜层质量和性能提高显著,模具寿命更长。
在模具表面上复合电镀Ni-W-P、Ni-Fe-P、Co-W-P合金显著提高了汽车模具的耐磨性和使用寿命。
如Ni-PTFE、Al O3镀层可提高抗蚀性能;Ni-WC、SiC、SiO 、SiO 镀层可提高耐磨及抗蠕变性能;Ni-Mo 镀层可提高减磨自润性能;N i-C r镀层可提高高温强度。
3.2 热喷涂热喷涂大致可分为火焰喷涂、电弧喷涂、等离子喷涂、激光喷涂、电热热源喷涂以及“冷喷”。
在生产中应用的主要是等离子喷涂(48 %)和高速火焰喷涂( 5 %)。
在模具上采用热喷涂金属陶瓷涂层对其表面进行强化,可提高其硬度、抗黏着、抗冲击、耐磨和抗冷热疲劳等。
如不锈钢制品拉深模表面采用高速火焰喷涂工艺制备30-50 um厚的WC-Co涂层后,修模频率由原来的500件/次提高到7 000件/次,寿命也由原来的拉制3万件提高3-8倍,而且制品质量也得到改善[7]。
热喷涂也用于模具的制造,国外均采用火焰喷焊镍基自熔合金制造和修复玻璃模具,寿命成倍提高。
热喷涂技术在不断的发展之中,主要向以下几个方向发展[7]:( )向在较低温度下具有高速飞行速度的喷涂方向发展;( )向能在长时间大功率下稳定高效的工艺及设备发展;(3)向精密高效节能的工艺和设备发展;(4)采用喷涂法制备纳米结构涂层;(5)用热喷涂法部分替代电镀硬铬的工艺研究与应用;(6)新型热障涂层(TBC)的研制。