On the electrodeposition of nickel–zinc alloys from a eutectic-based ionic liquid
电沉积法制备碱性电解水镍基析氧电极的研究进展
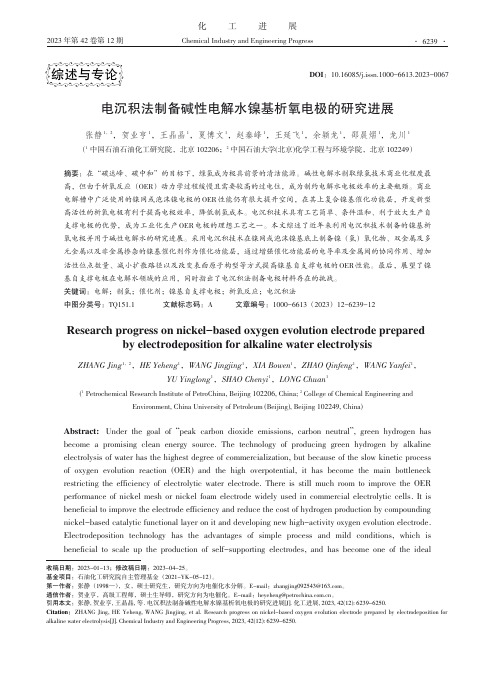
化工进展Chemical Industry and Engineering Progress2023 年第 42 卷第 12 期电沉积法制备碱性电解水镍基析氧电极的研究进展张静1,2,贺业亨1,王晶晶1,夏博文1,赵秦峰1,王延飞1,余颖龙1,邵晨熠1,龙川1(1 中国石油石油化工研究院,北京 102206;2 中国石油大学(北京)化学工程与环境学院,北京 102249)摘要:在“碳达峰、碳中和”的目标下,绿氢成为极具前景的清洁能源。
碱性电解水制取绿氢技术商业化程度最高,但由于析氧反应(OER )动力学过程缓慢且需要较高的过电位,成为制约电解水电极效率的主要瓶颈。
商业电解槽中广泛使用的镍网或泡沫镍电极的OER 性能仍有很大提升空间,在其上复合镍基催化功能层,开发新型高活性的析氧电极有利于提高电极效率,降低制氢成本。
电沉积技术具有工艺简单、条件温和、利于放大生产自支撑电极的优势,成为工业化生产OER 电极的理想工艺之一。
本文综述了近年来利用电沉积技术制备的镍基析氧电极并用于碱性电解水的研究进展。
采用电沉积技术在镍网或泡沫镍基底上制备镍(氢)氧化物、双金属及多元金属以及非金属掺杂的镍基催化剂作为催化功能层,通过增强催化功能层的电导率及金属间的协同作用、增加活性位点数量、减小扩散路径以及改变表面原子构型等方式提高镍基自支撑电极的OER 性能。
最后,展望了镍基自支撑电极在电解水领域的应用,同时指出了电沉积法制备电极材料存在的挑战。
关键词:电解;制氢;催化剂;镍基自支撑电极;析氧反应;电沉积法中图分类号:TQ151.1 文献标志码:A 文章编号:1000-6613(2023)12-6239-12Research progress on nickel-based oxygen evolution electrode preparedby electrodeposition for alkaline water electrolysisZHANG Jing 1,2,HE Yeheng 1,WANG Jingjing 1,XIA Bowen 1,ZHAO Qinfeng 1,WANG Yanfei 1,YU Yinglong 1,SHAO Chenyi 1,LONG Chuan 1(1 Petrochemical Research Institute of PetroChina, Beijing 102206, China; 2 College of Chemical Engineering andEnvironment, China University of Petroleum (Beijing), Beijing 102249, China)Abstract: Under the goal of “peak carbon dioxide emissions, carbon neutral ”, green hydrogen has become a promising clean energy source. The technology of producing green hydrogen by alkaline electrolysis of water has the highest degree of commercialization, but because of the slow kinetic process of oxygen evolution reaction (OER) and the high overpotential, it has become the main bottleneck restricting the efficiency of electrolytic water electrode. There is still much room to improve the OER performance of nickel mesh or nickel foam electrode widely used in commercial electrolytic cells. It is beneficial to improve the electrode efficiency and reduce the cost of hydrogen production by compounding nickel-based catalytic functional layer on it and developing new high-activity oxygen evolution electrode. Electrodeposition technology has the advantages of simple process and mild conditions, which is beneficial to scale up the production of self-supporting electrodes, and has become one of the ideal综述与专论DOI :10.16085/j.issn.1000-6613.2023-0067收稿日期:2023-01-13;修改稿日期:2023-04-25。
NiSe2_NF 溶剂热硒化泡沫镍
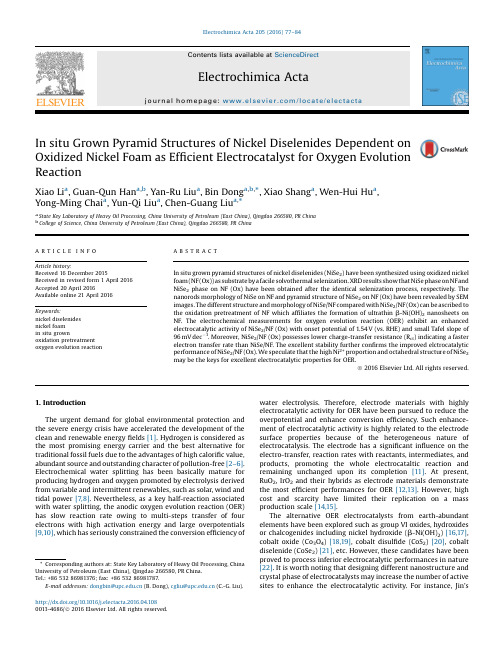
In situ Grown Pyramid Structures of Nickel Diselenides Dependent on Oxidized Nickel Foam as Ef ficient Electrocatalyst for Oxygen Evolution ReactionXiao Li a ,Guan-Qun Han a ,b ,Yan-Ru Liu a ,Bin Dong a ,b ,*,Xiao Shang a ,Wen-Hui Hu a ,Yong-Ming Chai a ,Yun-Qi Liu a ,Chen-Guang Liu a ,*a State Key Laboratory of Heavy Oil Processing,China University of Petroleum (East China),Qingdao 266580,PR China bCollege of Science,China University of Petroleum (East China),Qingdao 266580,PR ChinaA R T I C L E I N F OArticle history:Received 16December 2015Received in revised form 1April 2016Accepted 20April 2016Available online 21April 2016Keywords:nickel diselenides nickel foam in situ grownoxidation pretreatment oxygen evolution reactionA B S T R A C TIn situ grown pyramid structures of nickel diselenides (NiSe 2)have been synthesized using oxidized nickel foam (NF(Ox))assubstrate bya facile solvothermal selenization.XRD results show that NiSe phaseon NFand NiSe 2phase on NF (Ox)have been obtained after the identical selenization process,respectively.The nanorods morphology of NiSe on NF and pyramid structure of NiSe 2on NF (Ox)have been revealed by SEM images.The different structure and morphology of NiSe/NF compared with NiSe 2/NF (Ox)can be ascribed to the oxidation pretreatment of NF which af filiates the formation of ultrathin b -Ni(OH)2nanosheets on NF.The electrochemical measurements for oxygen evolution reaction (OER)exhibit an enhanced electrocatalytic activity of NiSe 2/NF (Ox)with onset potential of 1.54V (vs.RHE)and small Tafel slope of 96mV dec À1.Moreover,NiSe 2/NF (Ox)possesses lower charge-transfer resistance (R ct )indicating a faster electron transfer rate than NiSe/NF.The excellent stability further con firms the improved elctrocatalytic performance of NiSe 2/NF (Ox).We speculate that the high Ni 2+proportion and octahedral structure of NiSe 2may be the keys for excellent electrocatalytic properties for OER.ã2016Elsevier Ltd.All rights reserved.1.IntroductionThe urgent demand for global environmental protection and the severe energy crisis have accelerated the development of the clean and renewable energy fields [1].Hydrogen is considered as the most promising energy carrier and the best alternative for traditional fossil fuels due to the advantages of high calori fic value,abundant source and outstanding character of pollution-free [2–6].Electrochemical water splitting has been basically mature for producing hydrogen and oxygen promoted by electrolysis derived from variable and intermittent renewables,such as solar,wind and tidal power [7,8].Nevertheless,as a key half-reaction associated with water splitting,the anodic oxygen evolution reaction (OER)has slow reaction rate owing to multi-steps transfer of four electrons with high activation energy and large overpotentials [9,10],which has seriously constrained the conversion ef ficiency ofwater electrolysis.Therefore,electrode materials with highly electrocatalytic activity for OER have been pursued to reduce the overpotential and enhance conversion ef ficiency.Such enhance-ment of electrocatalytic activity is highly related to the electrode surface properties because of the heterogeneous nature of electrocatalysis.The electrode has a signi ficant in fluence on the electro-transfer,reaction rates with reactants,intermediates,and products,promoting the whole electrocataltic reaction and remaining unchanged upon its completion [11].At present,RuO 2,IrO 2and their hybrids as electrode materials demonstrate the most ef ficient performances for OER [12,13].However,high cost and scarcity have limited their replication on a mass production scale [14,15].The alternative OER electrocatalysts from earth-abundant elements have been explored such as group VI oxides,hydroxides or chalcogenides including nickel hydroxide (b -Ni(OH)2)[16,17],cobalt oxide (Co 3O 4)[18,19],cobalt disul fide (CoS 2)[20],cobalt diselenide (CoSe 2)[21],etc.However,these candidates have been proved to process inferior electrocatalytic performances in nature [22].It is worth noting that designing different nanostructure and crystal phase of electrocatalysts may increase the number of active sites to enhance the electrocatalytic activity.For instance,Jin ’s*Corresponding authors at:State Key Laboratory of Heavy Oil Processing,China University of Petroleum (East China),Qingdao 266580,PR China.Tel.:+8653286981376;fax:+8653286981787.E-mail addresses:dongbin@ (B.Dong),cgliu@ (C.-G.Liu)./10.1016/j.electacta.2016.04.1080013-4686/ã2016Elsevier Ltd.All rights reserved.Electrochimica Acta 205(2016)77–84Contents lists available at ScienceDirectElectrochimica Actaj o u r n a l h o m e p a g e :w w w.e l s e v i e r.c o m /l o c a t e /e l e c t a c tagroup has recently prepared novel porous b-Ni(OH)2nanosheets with excellent and stable elctrocatalytic activity for OER[23]using layered double hydroxide(LDH)nanoplates as precursors.Sun’s group reported NiSe nanowirefilm supported on three dimen-sional(3D)nickel foam(NF)with enhanced electrocatalytic activity and stability for OER[24].3D architectures of NF have been proved to offer more active sites and enhanced electro-catalytic activity and stability for OER[25].The above researches have suggested that novel nanostructuring may be the key to obtain the excellent OER electrocatalysts.Herein,we synthesized in situ grown pyramid structures of nickel diselenides(NiSe2)based on oxidized nickel foam(NF (Ox))for thefirst time,referred to as NiSe2/NF(Ox).The oxidation pretreatment of NF will provide not only3D skeleton structure but also ultrathin b-Ni(OH)2nanosheets on the surface of NF[24],which may decide the crystal phase and morphology of Ni x Se y during selenization.XRD and SEM results show the crystalline structure of synthesized Ni x Se y has surprisingly varied from hexagonal NiSe based on bare NF to cubic pyrite-type NiSe2based on NF(Ox)with the morphology changing from short nanorods to evenly distributed pyramids structure.The electrochemical measurements of NiSe2/NF(Ox) indicate prominent improvements of OER activity and electrical conductivity compared to NiSe/NF,and also revealing a long-term stability in basic media.The enhanced mechanisms of OER activity have been discussed.2.Experimental2.1.Materials and CharacterizationAll of the reagents were of analytical grade and used as obtained without further purification.NF with thickness of1.0mm,surface density of350g mÀ2was purchased from Shenzhen Poxon Machinery Technology Co.,Ltd.The phase analysis of samples was conducted by X-ray diffraction(XRD,X’Pert PRO MPD,Cu KR).The valence states of elements were examined by X-ray photoelectron spectroscopy (XPS,VG ESCALABMK II,Al K a(1486.6eV)).And the morphology and structure of samples were characterized by scanning electron microscopy(SEM,Hitachi,S-4800)and transmission electron microscopy(TEM,FEI Tecnai G2).2.2.Preparation of NF(Ox)SamplesThe similar chemical oxidation method that has been reported [26]was used to prepare NF(Ox)as a precursor.Firstly,NF was cut into pieces of1Â2cm2and then ultrasonically washed before use with0.1M H2SO4,acetone,ethanol and water for20min, respectively.Secondly,the wet pieces of NF were sealed into a glass vials for24h.Afterwards,above pieces of NF were taken out and immersed in a mixed solution containing30mL,3M NaOH and 15mL,1M(NH4)2S2O8and sealed for6h at room temperature. Finally,NF(Ox)samples were rinsed with ethanol and deionized water for several times and dried at150 C for6h.Fig.1.(a)XRD patterns of NF(Ox),NiSe/NF and NiSe2/NF(Ox).Crystal structure of(b)hexagonal phase NiSe and(c)cubic phase NiSe2. 78X.Li et al./Electrochimica Acta205(2016)77–842.3.Preparation of NiSe 2/NF (Ox)and NiSe/NF SamplesA facile solvothermal selenization process has been conducted using Se powder and ethanol to prepare in situ grown nickel selenides on NF substrate [24].In a typical process,NiSe 2/NF (Ox)samples were prepared as following.0.118g Se powder was added into 2mL deionized water containing 0.13g NaHB 4.A clear NaHSe solution was obtained after moderate stirring.Meanwhile,N 2was purged into 60mL ethanol for 30min to eliminate the dissolved oxygen.The fresh prepared NaHSe solution was quickly added into above ethanol under N 2flow.After that,the solution was transferredinto a 100mL Te flon-lined stainless steel autoclave with three pieces of NF (Ox)samples as substrates.The hydrothermal reaction was maintained in an electric oven at 140 C for 12h.Following the autoclave cooled down at room temperature,the samples were rinsed with ethanol and deionized water for several times and dried at 60 C for 8h.For comparison,NiSe/NF samples were prepared by the same selenization method on the bare NF without chemical oxidation pretreatment.To investigate the growth of NiSe 2/NF (Ox)during selenization,NiSe 2/NF (Ox)-4h and NiSe 2/NF (Ox)-8h samples are also synthesized by controlling the selenization time for 4h and 8h,respectively.Fig.2.(a)XPS survey spectra for NiSe 2/NF (Ox)in the (c)Ni 2p,(e)Se 3d regions.(b)XPS survey spectra for NiSe/NF in the (d)Ni 2p,(f)Se 3d regions.X.Li et al./Electrochimica Acta 205(2016)77–84792.4.Electrochemical MeasurementsThe electrochemical measurements were performed on an electrochemical workstation(Gamry Reference600Instrument, USA)with a three-electrode system in a1M KOH aqueous solution (pH=$14)using a sample NF as the working electrode,Pt foil as the counter electrode and a saturated calomel electrode(SCE)as the reference electrode.O2was purged into the electrolyte for30min to saturate the electrolyte prior to each electrochemical measure-ment.The polarization curve was obtained by consecutive linear sweep voltammetry(LSV)from0to0.8V(vs.SCE)with a scan rate of20mV sÀ1until there is no evident variation.Electric impedance spectroscopy(EIS)was carried out from105Hz to0.1Hz at an overpotential of0.45V(vs.SCE).Stability is tested by cyclic voltammetry(CV)at a sweep rate of100mV sÀ1for500cycles.3.Result and discussionFig.1a shows XRD patterns of NF(Ox),NiSe/NF and NiSe2/NF (Ox).The obviously sharp diffraction peaks of the three samples at around43.94 and51.34 may arise from the metallic NF substrate (PDF No.03-065-0380).And the peaks at around21.83 belong to the amorphous glass slide.The main peaks of NiSe/NF including (101),(102),(110)and(202)planes can be exactly indexed to that of NiSe(PDF No.03-065-6014),and no impurity can be detected. Similarly,the main planes of NiSe2/NF(Ox)such as(200),(210), (211),(311),(023),(321)and(421)are also well-matched with that of NiSe2(PDF No.03-065-5016).Obviously,the oxidation pretreatment of NF brings the change of the crystal structure from hexagonal phase NiSe(in Fig.1b)into distinct cubic phase NiSe2with a pyrite-type octahedral structure(in Fig.1c).While the presence of b-Ni(OH)2on NF(Ox)is not confirmed by the XRD analysis,which probably owes to the tiny amount not enough for detection,it can be further confirmed by SEM.Fig.2shows XPS survey spectra for NiSe2/NF(Ox)and NiSe/NF. As shown in Fig.2a and2b,the characteristic peaks of Ni and Se can be clearly observed in both NiSe2/NF(Ox)and NiSe/NF.In addition,the peaks of C1s and O1s may derive from contamina-tion and surface oxidation[27].Considering that the solvother-mal reaction,drying step or chemical oxidation pretreatment inevitably causes the surface oxidation of NF substrate,the emergencies of O1s signals may represent the existences of nickel oxides[24].In Fig.2c and2d,the comparison of Ni2p peaks from NiSe2/NF(Ox)and NiSe/NF is clearly presented,respectively. For both of the two samples,the peaks at872.9and855.4eV correspond to Ni2+[28,29]which is regarded as one kind of unusual valence states Ni playing important roles in improving OER catalytic performance[30].However,Ni3+centered at 874.4and856.5eV[29]derived from surface oxidation may be inactive for OER owing to the high valence states and difficulties in further oxidation to active sites.Therefore,the higher proportion of Ni2+in NiSe2/NF(Ox)may predict a better OER performance.In fact,for the two samples,the ratio of Ni2+to Ni3+ can be elucidated by calculations of Ni2p peak area with a result of5.7:1in NiSe2/NF(Ox)and3.5:1in NiSe/NF,which implies the better electrocatalytic activity of NiSe2/NF(Ox)for OER. Meanwhile,the peaks at852.8and870.2eV belong to metallic Ni from NF substrate[28].Fig.2e and f show the Se3d region where the splitting peaks of3d3/2and3d5/2representsÀ2valence of Se,and the relative lower and broad peak near58.6eV indicates the surface oxidation state of Se species[31].Finally,XPS spectra for as-prepared NiSe2/NF(Ox)and NiSe/NF also reveal the about 1:2and1:1Ni:Se ratio corresponding with the crystal phase analysis in XRD.Fig.3presents SEM images of the bare NF and NF(Ox).In Fig.3a, the macroscopic3D skeleton of bare NF can be observed.And the smooth surface with no impurities forms the substrate of anode electrode material(in Fig.3b).The unique3D structure and high surface area of NF are advantages for ideal substrate.Fig.3c shows that b-Ni(OH)2film homogeneously covers on the surface of3D NF after oxidation pretreatment.Under higher magnification(as shown in Fig.3d),b-Ni(OH)2film is composed of manynanosheets Fig.3.Low(a)and high(b)magnification SEM images of the bare NF;low(c)and high(d)magnification SEM images of NF(Ox).80X.Li et al./Electrochimica Acta205(2016)77–84with a partly cross-linked structure grown on the surface of 3D NF [26].Fig.4shows SEM images of different morphologies of NiSe/NF and NiSe 2/NF (Ox).Fig.4a exhibits a network-like film of NiSe grown on the 3D NF.Under higher magni fication,the network-like film is composed of many nanorods and a few nanowires (as shown in Fig.4b and c).With further TEM analysis of NiSe scratched off NiSe/NF samples (see in Fig.S1),it can be clearly observed that the diameter of NiSe nanorods is about 70nm and the average length is around 1m m.The small amount of nanowires with the length ranging from 2to 4m m may be the intermediates during the growth process of nanorods.Fig.4d and e indicate that a homogeneous film entirely covers on the skeleton of NF (Ox).There look like many pyramids on the surface of the film under higher magni fication (as shown in Fig.4f).The morphology of distributed NiSe 2pyramids on NiSe 2/NF (Ox)is evidently different from the morphology of NiSe/NF nanorods.The pyramid structures of NiSe 2may belong to octahedron con figuration of cubic system consistent with XRD results.Therefore,the oxidation pretreatment of NF is responsible for the different structure and morphologybetween NiSe 2pyramids and NiSe nanorods.To clearly observe the growth of NiSe 2pyramids,SEM images of NiSe 2/NF (Ox)-4h and NiSe 2/NF (Ox)-8h at different times during the growth of NiSe 2are further revealed in Fig.5.It can be seen that NiSe 2pyramids increases gradually and distributes densely with the prolonging of selenization process.Meanwhile,a large amount of irregularly little cubes,which can be assigned to the intermediates of standard NiSe 2pyramids,emerge on NiSe 2/NF (Ox)-8h (in Fig.5d),however,there still exists large area of exposed Ni (Ox)surface suggesting the incomplete of selenization process for 8h.For NiSe 2growing on NiSe 2/NF (Ox)after selenization for 12h (in Fig.4f),the thick layer of densely distributed NiSe 2pyramids and intermediates has already formed.Accordingly,that some parts of surface morphol-ogy do not look exactly standard pyramid structures may owe to the large amount of NiSe 2pyramids or their intermediates with different sizes strongly overlaying each other.The growth mechanisms of the different types of Ni x Se y grown on bare NF or NF (Ox)could be explained by the following putative chemical equations.2NaHSe +O 2!2Se #+2NaOH(1)Fig.4.Low (a)and high (b and c)magni fication SEM images of NiSe 2/NF (Ox);low (d)and high (e and f)magni fication SEM images of NiSe/NF.X.Li et al./Electrochimica Acta 205(2016)77–84816Ni(OH)2+13Se +Se 2À!6NiSe 2#+2SeO 3À+6H 2O(2)Ni ðOH Þ2!Ni2þþ2OH Àð3À1Þ3Se þ6OH À!2Se 2ÀþSeO 3Àþ3H 2Oð3À2ÞNi +2CH 3CH 2OH +Se 2À!NiSe #+2CH 3CH 2O À+H 2"(4)The prepared NaHSe solution tends to be easily oxidized into amorphous red Se even under N 2atmosphere (Equation (1)),which facilitates the growth of NiSe 2described as Equation (2).The detailed growth mechanisms are as follows:(1)The b -Ni(OH)2layer on NF (Ox)gradually decomposes into Ni 2+and OH À(Equation (3-1))with increasing temperature of solvothermal reaction,which creates a relative much stronger basic environ-ment and a large quantity of Ni 2+;(2)The disproportionation of Se with excess OH Àcan provide more Se 2À(Equation (3-2))which is the key to synthesize NiSe 2.Therefore,the high density of Se 2Àaggregating around Ni 2+af filiates the formation of NiSe 2crystal nucleus whose octahedron skeleton are composed of 6Se atoms located at the corners with 1Ni atom in the central position (Fig.1c).For the growth process of NiSe/NF,there ’s no existing Ni 2+participating the reaction with Se 2Àowing to the absence of Ni (OH)2.Besides,the alkalinity of solution is not strong enough to promote more Se 2Àby the disproportionation of Se.Therefore,only NiSe,whose formation needs less Se 2À,emerges instead of NiSe 2(Equation (4)).Summing up the above growth mechanisms of NiSe 2and NiSe,the oxidation pretreatment of NF plays a dominant role in the transformation of crystal phases.The ir-corrected electrocatalytic performances for OER based on projected geometry area of NiSe 2/NF (Ox),NiSe/NF,NF (Ox)and bare NF electrodes are shown in Fig.6.Fig.6a presents their polarization curves on the reversible hydrogen electrode (RHE)scale in 1M KOH electrolyte.As is evident from the enhancement of current density and the earliest onset potential (1.54V vs.RHE)of OER,NiSe 2/NF (Ox)demonstrates much superior electro-catalytic activity than NiSe/NF,NF (Ox)and bare NF samples.However,the obvious oxidation peaks at around 1.4V (vs.RHE)are observed for NiSe 2/NF (Ox),NiSe/NF and NF (Ox),which can be assigned to the surface reactions from Ni 2+to active Ni 3+species (Equation (5),(6)and (7))[32–35].The obtained active Ni 3+species including NiSe 2(OH),NiSe(OH)and NiO(OH)have been speculated to be the real active sites for OER [30],[32],however,different types of transformations from Ni 2+to active sites may differ signi ficantly in their ease of reactions leading to the different amount of active sites.Such distinction may be resulted from the disparities of unique crystal structures between NiSe 2and NiSe.As shown in Fig.1c,the central Ni atom is octahedrally bonded to adjacent 6Se atoms composing a pyrite-type crystal structure in NiSe 2,whereas 1Ni atom is attached to only 3Se atoms in NiSe (in Fig.1b).The much higher density of Se atoms in NiSe 2compared with NiSe means the stronger electronegativity atmosphere.Thus,the shell electrons of Ni 2+in NiSe 2can be more easily attracted by Se atoms to facilitate the oxidation reaction into more Ni 3+as active sites for OER.Accordingly,NiSe 2demonstrates enhanced activity for OER during anodic polariza-tion compared with NiSe.As for Ni (Ox),the inferior OER performance may owe much to the smaller amount of active sites generated by ultrathin b -Ni(OH)2nanosheets on Ni (Ox)as shown in SEM images of Fig.3d.NiSe 2+OH À!NiSe 2(OH)+e À(5)Fig.5.Low (a)and high (b)magni fication SEM images of NiSe 2/NF (Ox)–4h prepared by solvothermal reaction for 4h;low (c)and high (d)magni fication SEM images of NiSe 2/NF (Ox)–8h prepared by solvothermal reaction for 8h.82X.Li et al./Electrochimica Acta 205(2016)77–84NiSe +OH À!NiSe(OH)+e À(6)Ni(OH)2+OH À!NiO(OH)+H 2O +eÀ(7)Fig.6b shows the Tafel plots of NiSe 2/NF (Ox),NiSe/NF,NF (Ox)and bare NF.It can be observed that Tafel slope has been signi ficantly reduced from 153mV dec À1of NiSe/NF to 96mV dec À1of NiSe 2/NF (Ox),which indicates a higher OER rate for NiSe 2/NF (Ox)and is in agreement with the polarization curves.As shown in Fig.6c,the electrochemical impedances spectra (EIS)of NiSe 2/NF (Ox),NiSe/NF and NF (Ox)under 0.45V (vs.SCE)are compared and the mesured EIS data have been fitted and analyzed using Zview software.It can be seen that the simulated results are in good agreement with the experimental data.The insert equivalent circuit obtained from fitting spectra is further attached with the related electrochemical parameters of equivalent circuit:solution resistance (R s ),charge-transfer resistance (R ct )and constant phaseelement (CPE).Estimates of these circuit parameters are presented in Table ing CPE to replace capacitance is due to the high degree of roughness and inhomogeneity of the electrode and it hardly exhibits pure capacitance in real electrochemical process [36,37].In comparison of the simulated R ct of samples,NiSe 2/NF (Ox)with smallest R ct value means a best overall catalytic activity according to that R ct is proportional to the number of active sites and the site activity on the electrode material [38].The analysis of EIS data reinforce the highest OER activity of NiSe 2/NF (Ox)as con firmed in LSV results.To finally investigate the stability of synthesized NiSe 2/NF (Ox),500cycles of CV tests are conducted with a satisfying result as shown in Fig.6d.The current density and onset potential of polarization curve remain almost unchanged after stability tests.The enlargement of oxidation peak may be attributed to the arrival to a steady state with a certain content of active Ni 3+on the electrode as CV measurements continues.The signi ficantly enhanced activity for OER can be ascribed to the composition and unique crystal structure of NiSe 2/NF (Ox).On the one hand,the higher proportion of Ni 2+in NiSe 2/NF (Ox)compared with NiSe/NF as shown in XPS spectra of Ni 2p region (Fig.2c and d)would provide more active Ni 3+,representing the better activity as expected.On the other hand,the octahedral structure of NiSe 2accelerates the oxidation tendency of Ni 2+into Ni 3+which can enhance the amount of active sites improving the OER performance of NiSe 2/NF (Ox)as discussed above.In summary,the higher Ni 2+proportion and octahedralstructureFig.6.Electrocatalytic performances for OER of NiSe 2/NF (Ox),NiSe/NF,NF (Ox)and NF.(a)Polarization curves based on RHE in 1M KOH electrolyte;(b)Tafel plots extracted from (a);(c)EIS plots of NiSe 2/NF (Ox),NiSe/NF,NF (Ox)at 0.45V (vs.SCE)from 105Hz to 0.1Hz;(d)Polarization curves of NiSe 2/NF (Ox)before and after 500cycles used for stability tests.Table 1Simulated parameters of the elements in equivalent circuits for OER of NiSe 2/NF (Ox),NiSe/NF and NF (Ox)at 0.45V (vs.SCE)in O 2saturated 1.0M KOH.R s (V cm 2)R ct (V cm 2)CPE-T (F cm À2)CPE-P (F cm À2)NiSe 2/NF (Ox) 2.154 6.4840.3370.417NiSe/NF 2.24618.3260.2940.428NF (Ox)3.762146.0200.0230.481X.Li et al./Electrochimica Acta 205(2016)77–8483of NiSe2could synergistically increase the amount of active Ni3+ and lead to a significantly enhanced OER performance.4.ConclusionThe oxidized NF was utilized to in situ prepare novel NiSe2 pyramid structures by a facile solvothermal selenization.The ultrathin b-Ni(OH)2nanosheets grown on NF after oxidation pretreatment may be responsible for the formation of NiSe2 pyramids rather than NiSe nanorods.The electrochemical meas-urements for OER activity demonstrate that NiSe2/NF(Ox)has the enhanced electrocatalytic activity including the smaller over-potential,Tafel slope and charge-transfer resistance in comparison with NiSe/NF,which may be due to the high content of Ni2+and inherently octahedral structure of NiSe2.Therefore,designing novel nanostructures based on oxidized NF may provide a choice for preparing OER eletrocatalysts with excellent performances.AcknowledgementsThis work isfinancially supported by the National Natural Science Foundation of China(U1162203and21106185)and the Fundamental Research Funds for the Central Universities (15CX05031A).Appendix A.Supplementary dataSupplementary data associated with this article can be found,in the online version,at /10.1016/j. electacta.2016.04.108.References[1]D.G.Vlachos,S.Caratzoulas,The roles of catalysis and reaction engineering inovercoming the energy and the environment crisis,Chem.Eng.Sci.65(2010)18.[2]G.W.Crabtree,M.-S.Dresselhaus,M.V.Buchanan,The hydrogen economy,Phys.Today57(2004)39.[3]M.S.Dresselhaus,I.L.Thomas,Alternative energy technologies,Nature414(2001)332.[4]P.Jiang,Q.Liu,Y.Liang,J.Tian,A.M.Asiri,X.Sun,A Cost-Effective3D HydrogenEvolution Cathode with High Catalytic Activity:FeP Nanowire Array as the Active Phase,Angew.Chem.Int.Ed.53(2014)12855.[5]Z.Pu,Q.Liu,A.M.Asiri,Y.Luo,X.Sun,Y.He,3D macroporous MoS2thinfilm:insitu hydrothermal preparation and application as a highly active hydrogen evolution electrocatalyst at all pH values,Electrochim.Acta168(2015)133.[6]J.Guo,F.Li,Y.Sun,X.Zhang,L.Tang,Oxygen-incorporated MoS2ultrathinnanosheets grown on graphene for efficient electrochemical hydrogenevolution,J.Power Sources291(2015)195.[7]J.A.Turner,Sustainable hydrogen production,Science305(2004)972.[8]J.D.Holladay,J.Hu,D.L.King,Y.Wang,An overview of hydrogen productiontechnologies,Catal.Today139(2009)244.[9]H.Dau,C.Limberg,T.Reier,M.Risch,S.Roggan,P.Strasser,The mechanism ofwater oxidation:from electrolysis via homogeneous to biological catalysis, ChemCatChem2(2010)724.[10]J.O.M.Bockris,Kinetics of activation controlled consecutive electrochemicalreactions:anodic evolution of oxygen,J.Chem.Phys.24(1956)817.[11]S.B.Strbac,R.R.Adzic,in:G.Kreysa(Ed.),et al.,Electrocatalysis,Fundamentals-Electron Transfer Process;Current-Potential Relationship;Volcano Plots,Encyclopedia of Applied Electrochemistry,Springer,New York,2014,pp.417–423.[12]R.G.González-Huerta,G.Ramos-Sánchez,P.B.Balbuena,Oxygen evolution inCo-doped RuO2and IrO2:Experimental and theoretical insights to diminish electrolysis overpotential,J.Power Sources268(2014)69.[13]F.Kong,J.Liu,A.Ling,Z.Xu,H.Wang,Q.Kong,Preparation of IrO2nanoparticleswith SBA-15template and its supported Pt nanocomposite as bifunctional oxygen catalyst,J.Power Sources299(2015)170.[14]T.R.Cook,D.K.Dogutan,S.Y.Reece,Y.Surendranath,T.S.Teets,D.G.Nocera,Solar energy supply and storage for the legacy and nonlegacy worlds,Chem.Rev.110(2010)6474.[15]M.G.Walter,E.L.Warren,J.R.McKone,S.W.Boettcher,Q.Mi,E.A.Santori,Solarwater splitting cells,Chem.Rev.110(2010)6446.[16]M.E.G.Lyons,M.P.Brandon,The oxygen evolution reaction on passive oxidecovered transition metal electrodes in aqueous alkaline solution.Part1-Nickel, Int.J.Electrochem.Sci.3(2008)1386.[17]X.Wang,H.Luo,H.Yang,P.J.Sebastian,S.A.Gamboa,Oxygen catalyticevolution reaction on nickel hydroxide electrode modified by electrolesscobalt coating,Int.J.Hydrogen Energy29(2004)967.[18]S.Palmas,F.Ferrara,A.Vacca,M.Mascia,A.M.Polcaro,Behavior of cobalt oxideelectrodes during oxidative processes in alkaline medium,Electrochim.Acta 53(2007)400.[19]M.E.G.Lyons,M.P.Brandon,A comparative study of the oxygen evolutionreaction on oxidised nickel,cobalt and iron electrodes in base,J.Electroanal.Chem.641(2010)119.[20]W.Fang,D.Liu,Q.Lu,X.Sun,A.M.Asiri,Nickel promoted cobalt disulfidenanowires array supported on carbon cloth:An efficient and stablebifunctional electrocatalyst for full water splitting,mun.63 (2016)60.[21]M.Gao,Y.Xu,J.Jiang,Y.Zheng,S.Yu,Water oxidation electrocatalyzed by anefficient Mn3O4/CoSe2nanocomposite,J.Am.Chem.Soc.134(2012)2930. [22]I.C.Man,H.Su,F.Calle-Vallejo,H.A.Hansen,J.I.Martínez,N.G.Inoglu,J.Kitchin,T.F.Jaramillo,J.K.Nørskov,J.Rossmeisl,Universality in oxygen evolutionelectrocatalysis on oxide surfaces,ChemCatChem3(2011)1159.[23]H.Liang,L.Li,F.Meng,L.Dang,J.Zhuo,A.Forticaux,Z.Wang,S.Jin,Porous Two-Dimensional Nanosheets Converted from Layered Double Hydroxides and Their Applications in Electrocatalytic Water Splitting,Chem.Mater.27(2015) 5702.[24]C.Tang,N.Cheng,Z.Pu,W.Xing,X.Sun,NiSe Nanowire Film Supported onNickel Foam:An Efficient and Stable3D Bifunctional Electrode for Full Water Splitting,Angew.Chem.Int.Ed.54(2015)9351.[25]Y.Liang,Q.Liu,A.M.Asiri,X.Sun,Enhanced electrooxidation of urea usingNiMoO4ÁxH2O nanosheet arrays on Ni foam as anode,Electrochim.Acta153 (2015)456.[26]X.Xiong,D.Ding,D.Chen,G.Waller,Y.Bu,Z.Wang,M.Liu,Three-dimensionalultrathin Ni(OH)2nanosheets grown on nickel foam for high-performance supercapacitors,Nano Energy11(2015)154.[27]A.Panneerselvam,M.A.Malik,M.Afzaal,P.O0Brien,M.Helliwell,The chemicalvapor deposition of nickel phosphide or selenide thinfilms from a single precursor,J.Am.Chem.Soc.130(2008)2420.[28]P.Prieto,V.Nistor,K.Nouneh,M.Oyama,M.Abd-lefdil,R.Díaz,XPS study ofsilver,nickel and bimetallic silver–nickel nanoparticles prepared by seed-mediated growth,Appl.Surf.Sci.258(2012)8807.[29]W.Hu,R.Chen,W.Xie,L.Zou,N.Qin,D.Bao,CoNi2S4Nanosheet ArraysSupported on Nickel Foams with Ultrahigh Capacitance for AqueousAsymmetric Supercapacitor Applications,ACS Appl.Mater.Interfaces6(2014) 19318.[30]W.Zhou,X.Wu,X.Cao,X.Huang,C.Tan,J.Tian,H.Liu,J.Wang,H.Zhang,Ni3S2nanorods/Ni foam composite electrode with low overpotential forelectrocatalytic oxygen evolution,Energy Environ.Sci.6(2013)2921. [31]S.Huang,Q.He,W.Chen,Q.Qiao,J.Zai,X.Qian,Ultrathin FeSe2Nanosheets:Controlled Synthesis and Application as a Heterogeneous Catalyst in Dye-Sensitized Solar Cells,Chem.Eur.J.21(2015)4085.[32]M.W.Louie,A.T.Bell,An investigation of thin-film Ni–Fe oxide catalysts for theelectrochemical evolution of oxygen,J.Am.Chem.Soc.135(2013)12329. [33]H.H.Huo,Y.Q.Zhao,C.L.Xu,3D Ni3S2nanosheet arrays supported on Ni foamfor high-performance supercapacitor and non-enzymatic glucose detection,J.Mater.Chem.A2(2014)15111.[34]T.Zhu,Z.Wang,S.Ding,J.S.Chen,X.W.Lou,Hierarchical nickel sulfide hollowspheres for high performance supercapacitors,RSC Adv.1(2011)397. [35]M.S.Burke,M.G.Kast,L.Trotochaud,A.M.Smith,S.W.Boettcher,Cobalt–Iron(Oxy)hydroxide Oxygen Evolution Electrocatalysts:The Role of Structure and Composition on Activity,Stability,and Mechanism,J.Am.Chem.Soc.137(2015)3638.[36]Cl.Bohnke,O.Bohnke,B.Vuillemin,Constant phase angle behavior of SnO2/WO3thinfilm electrodes in anhydrous LiClO4–propylene carbonateelectrolyte,Electrochim.Acta38(1993)1935.[37]U.Rammelt,G.Reinhard,Impedance analysis of conversion layers on iron,Electrochim.Acta40(1995)505.[38]Y.L.Lo,B.J.Hwang,Characterization of the electroless Ni-Mo-P/SnO2/Tielectrodes with heat-treatment for oxygen evolution in alkaline solution,J.Electrochem.Soc.143(1996)2158.84X.Li et al./Electrochimica Acta205(2016)77–84。
英语原文
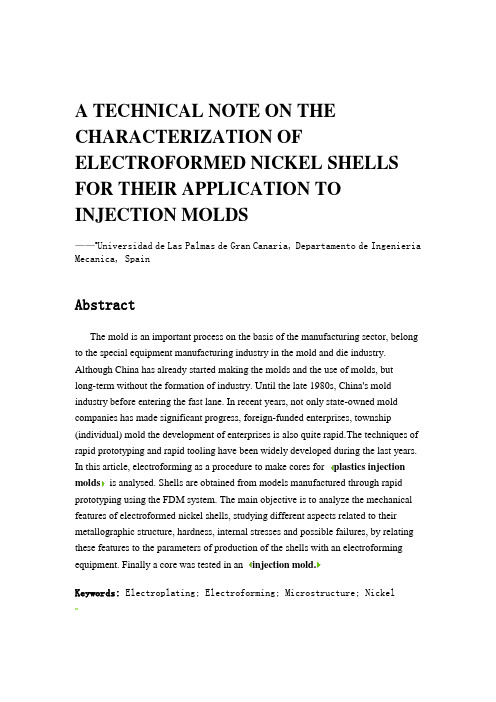
A TECHNICAL NOTE ON THE CHARACTERIZATION OF ELECTROFORMED NICKEL SHELLS FOR THEIR APPLICATION TO INJECTION MOLDS——a Universidad de Las Palmas de Gran Canaria, Departamento de Ingenieria Mecanica, SpainAbstractThe mold is an important process on the basis of the manufacturing sector, belong to the special equipment manufacturing industry in the mold and die industry. Although China has already started making the molds and the use of molds, but long-term without the formation of industry. Until the late 1980s, China's mold industry before entering the fast lane. In recent years, not only state-owned mold companies has made significant progress, foreign-funded enterprises, township (individual) mold the development of enterprises is also quite rapid.The techniques of rapid prototyping and rapid tooling have been widely developed during the last years. In this article, electroforming as a procedure to make cores for plastics injection molds is analysed. Shells are obtained from models manufactured through rapid prototyping using the FDM system. The main objective is to analyze the mechanical features of electroformed nickel shells, studying different aspects related to their metallographic structure, hardness, internal stresses and possible failures, by relating these features to the parameters of production of the shells with an electroforming equipment. Finally a core was tested in an injection mold.Keywords: Electroplating; Electroforming; Microstructure; Nickel1. IntroductionOne of the most important challenges with which modern industry comes across is to offer the consumer better products with outstanding variety and time variability (new designs). For this reason, modern industry must be more and more competitive and it has to produce with acceptable costs. There is no doubt that combining the time variable and the quality variable is not easy because they frequently condition one another; the technological advances in the productive systems are going to permit that combination to be more efficient and feasible in a way that, for example, if it is observed the evolution of the systems and techniques of plastics injection, we arrive at the conclusion that, in fact, it takes less and less time to put a new product on the market and with higher levels of quality. The manufacturing technology of rapid tooling is, in this field, one of those technological advances that makes possible the improvements in the processes of designing and manufacturing injected parts. Rapid tooling techniques are basically composed of a collection of procedures that are going to allow us to obtain a mold of plastic parts, in small or medium series, in a short period of time and with acceptable accuracy levels. Their application is not only included in the field of making plastic injected pieces [1], [2] and [3], however, it is true that it is where they have developed more and where they find the highest output.This paper is included within a wider research line where it attempts to study, define, analyze, test and propose, at an industrial level, the possibility of creating cores for injection molds starting from obtaining electroformed nickel shells, taking as an initial model a prototype made in a FDM rapid prototyping equipment.It also would have to say beforehand that the electroforming technique is not something new because its applications in the industry are countless [3], but this research work has tried to investigate to what extent and under which parameters the use of this technique in the production of rapid molds is technically feasible. All made inan accurate and systematized way of use and proposing a working method.2. Manufacturing process of an injection moldThe core is formed by a thin nickel shell that is obtained through the electroforming process, and that is filled with an epoxic resin with metallic charge during the integration in the core plate [4] This mold (Fig. 1) permits the direct manufacturing by injection of a type a multiple use specimen, as they are defined by the UNE-EN ISO 3167 standard. The purpose of this specimen is to determine the mechanical properties of a collection of materials representative industry, injected in these tools and its coMParison with the properties obtained by conventional tools.Fig. 1. Manufactured injection mold with electroformed core.The stages to obtain a core [4], according to the methodology researched in this work, are the following:(a) Design in CAD system of the desired object.(b) Model manufacturing in a rapid prototyping equipment (FDM system). The material used will be an ABS plastic.(c) Manufacturing of a nickel electroformed shell starting from the previous model that has been coated with a conductive paint beforehand (it must have electrical conductivity).(d) Removal of the shell from the model.(e) Production of the core by filling the back of the shell with epoxy resin resistant to high temperatures and with the refrigerating ducts made with copper tubes.The injection mold had two cavities, one of them was the electroformed core and the other was directly machined in the moving platen. Thus, it was obtained, with the same tool and in the same process conditions, to inject simultaneously two specimens in cavities manufactured with different technologies.Plastic Injection Molding is the world’s most common method of producing complexcommercial plastic parts with excellent dimensional tolerance. According to theC-mold designguide, 32% by weight of all plastics processed go through Injection Molding machines, making.Plastic Injection Molding one of the most important manufacturing processes2. It is seen that thefinal molded part quality is chiefly dependent on the type of material, mold design and themolding process settings. Once the material and the mold to be used are specified, the partquality basically depends on the molding process. The molding process is quite complexinvolving many variable process parameters like pressure, temperature and time settings. Thesprocess parameters have to be optimally set in order to improve part quality and maximize the production capacity of the Injection Molding machine. Educated and experienced individualsare required to set up and optimize such a complex process. These individuals control themolding process on a trial and error basis, which is usually time consuming. This method ofcontrolling the molding process relies heavily on operator intuition anda few “rules of thumb,”which the operator develops over a period of time while working with different materials,pressures, temperatures and time settings.The plastics industry is one of the world's fastest growing industry, belongs to a small number of hundreds of millions of dollars in industry. Almost all the supplies in their daily lives are inseparable from the plastic and most can use plastic injection mold production. Injection molding injection molding process to take advantage of low-cost production of a variety of shapes and complex geometric patterns known [2].Injection molding injection molding process is a cyclic process. Can be divided into four key stages of packing, injection, cooling, demoulding. Plastic injection molding process begins to fill in the resin and the amount of additives to the hopper into the heating of the injection molding machine or injection system. Grain filling stage in injection temperature, the hot plastic melt into the mold cavity. The cavity is filled, the amount of molten plastic in the plastic solidification shrinkage caused by a higher compensation under the pressure of added. Followed by a cooling phase, the mold was cooled to a sufficient rigidity extrusion mold. Finally, the stripping stage, that is, open the mold and then the top part, and then together on the mold start the next cycle. The design and manufacture of injection molded plastic products with the expectedperformance is to rely on the experience of control of an expensive process, including the actual modification of the cover embossed. In mold design, design mold supplementary geometry, usually in the side of the core, including the complex projection and groove.Mold design must take into account many important design factor. These factors are the number and layout of the size of the mold cavity, runner system, gate systems, mold release systems, and shrinkage.Thermal analysis of the mold, the main objective is to analyze the role of the residual thermal stress or pressure injection of product diameter direction. Heat flux density enhancements in the cooling phase of the molded parts, mainly because of its low thermal conductivity and the temperature difference between the melting resin and mold. During cooling near the mold cavity will be non-uniform temperature region. During cooling, cooling channels near the area than the area far from the cooling channels to cool faster. This temperature difference will cause uneven shrinkage of the material to heat stress. The strong thermal stresses can cause warping problem. Therefore, it is an imitation of the important stage in the molded parts during the cooling area of the thermal residual stress. Understand the characteristics of the thermal stress, causing deformation of pre-simulation.In this article, the injection mold is designed to produce warping of test samples and perform the thermal analysis presented in the mold on the role of the residual thermal stress.After the completion of the mold design and manufacture of, tryout injection warp specimens there are many defects. Including a short shot, splash and warping. The solution of a short shot by milling out the additional pores to drain the trapped air in the corner of the cavity. At the same time, reducing the injection pressure can reduce the occurrence of splashing. Warpage control can be controlled by many factors, such as injection time, injection temperature and dissolved material temperature.After these trimming, mold can produce low-cost high-quality warp specimens, these specimens need to go through a simple polishing.3. Obtaining an electroformed shell: the equipmentElectrodeposition [5] and [6] is an electrochemical process in which a chemical change has its origin within an electrolyte when passing an electric current through it.The electrolytic bath is formed by metal salts with two submerged electrodes, an anode (nickel) and a cathode (model), through which it is made to pass an intensity coming from a DC current. When the current flows through the circuit, the metal ions present in the solution are transformed into atoms that are settled on the cathode creating a more or less uniform deposit layer.The plating bath used in this work is formed by nickel sulfamate [7] and [8] at a concentration of 400 ml/l, nickel chloride (10 g/l), boric acid (50 g/l), Allbrite SLA (30 cc/l) and Allbrite 703 (2 cc/l). The selection of this composition is mainly due to the type of application we intend, that is to say, injection molds, even when the injection is made with fibreglass. Nickel sulfamate allows us to obtain an acceptable level of internal stresses in the shell (the tests gave results, for different process conditions, not superior to 50 MPa and for optimum conditions around 2 MPa). Nevertheless, such level of internal pressure is also a consequence of using as an additive Allbrite SLA, which is a stress reducer constituted by derivatives of toluenesulfonamide and by formaldehyde in aqueous solution. Such additive also favours the increase of the resistance of the shell when permitting a smaller grain. Allbrite 703 is an aqueous solution of biodegradable surface-acting agents that has been utilized to reduce the risk of pitting. Nickel chloride, in spite of being harmful for the internal stresses, is added to enhance the conductivity of the solution and to favour the uniformity in the metallic distribution in the cathode. The boric acid acts as a pH buffer.The equipment used to manufacture the nickel shells tested has been as follows:• Polypropylene tank: 600 mm × 400 mm × 500 mm in size.• Three teflon resistors, each one with 800 W.• Mechanical stirring system of the cathode.• System for recirculation and filtration of the bath formed by a pump and a polypropylene filter.• Charging rectifier. Maximum intensity in continuous 50 A and continuous current voltage between 0 and 16 V.• Titanium basket with nickel anodes (Inco S-Rounds Electrolytic Nickel) with a purity of 99%.• Gases aspiration system.Once the bath has been defined, the operative parameters that have been altered for testing different conditions of the process have been the current density (between 1 and 22 A/dm2), the temperature (between 35 and 55 °C) and the pH, partially modifying the bath composition.4. Obtained hardnessOne of the most interesting conclusions obtained during the tests has been that the level of hardness of the different electroformed shells has remained at rather high and stable values. In Fig. 2, it can be observed the way in which for current density values between 2.5 and 22 A/dm2, the hardness values range from 540 and 580 HV, at pH4 ± 0.2 and with a temperature of 45 °C. If the pH of the bath is reduced at 3.5 and the temperature is 55 °C those values are above 520 HV and below 560 HV. This feature makes the tested bath different from other conventional ones composed by nickel sulfamate, allowing to operate with a wider range of values; nevertheless, such operativity will be limited depending on other factors, such as internal stress because its variability may condition the work at certain values of pH, current density or temperature. On the other hand, the hardness of a conventional sulfamate bath is between 200–250 HV, much lower than the one obtained in the tests. It is necessary to take into account that, for an injection mold, the hardness is acceptable starting from 300 HV. Among the most usual materials for injection molds it is possible to find steel for improvement (290 HV), steel for integral hardening (520–595 HV), casehardened steel (760–800 HV), etc., in such a way that it can be observed that the hardness levels of the nickel shells would be within the medium–high range of the materials for injection molds. The objection to the low ductility of the shell is compensated in such a way with the epoxy resin filling that would follow it because this is the one responsible for holding inwardly the pressure charges of the processes of plastics injection; this is the reason why it is necessary for the shell to have a thickness as homogeneous as possible (above a minimum value) and with absence of important failures such as pitting.Fig. 2. Hardness variation with current density. pH 4 ± 0.2, T = 45 °C.5. Metallographic structureIn order to analyze the metallographic structure, the values of current density and temperature were mainly modified. The samples were analyzed in frontal section and in transversal section (perpendicular to the deposition). For achieving a convenient preparation, they were conveniently encapsulated in resin, polished and etched in different stages with a mixture of acetic acid and nitric acid. The etches are carried out at intervals of 15, 25, 40 and 50 s, after being polished again, in order to be observed afterwards in a metallographic microscope Olympus PME3-ADL 3.3×/10×.Before going on to comment the photographs shown in this article, it is necessary to say that the models used to manufacture the shells were made in a FDM rapid prototyping machine where the molten plastic material (ABS), that later solidifies, is settled layer by layer. In each layer, the extruder die leaves a thread approximately 0.15 mm in diameter which is compacted horizontal and vertically with the thread settled inmediately after. Thus, in the surface it can be observed thin lines that indicate the roads followed by the head of the machine. These lines are going to act as a reference to indicate the reproducibility level of the nickel settled. The reproducibility of the model is going to be a fundamental element to evaluate a basic aspect of injection molds: the surface texture.The tested series are indicated in Table 1.Table 1.Tested seriesSeries pH Temperature (°C)Current density (A/dm2)1 4.2 ± 0.255 2.222 3.9 ± 0.245 5.563 4.0 ± 0.24510.004 4.0 ± 0.24522.22Fig. 3 illustrates the surface of a sample of the series after the first etch. It shows the roads originated by the FDM machine, that is to say that there is a good reproducibility. It cannot be still noticed the rounded grain structure. In Fig. 4, series 2, after a second etch, it can be observed a line of the road in a way less clear than in the previous case. In Fig. 5, series 3 and 2° etch it begins to appear the rounded grain structure although it is very difficult to check the roads at this time. Besides, the most darkened areas indicate the presence of pitting by inadequate conditions of process and bath composition.Fig. 3. Series 1 (×150), etch 1.Fig. 4. Series 2 (×300), etch 2.Fig. 5. Series 3 (×300), etch 2.This behavior indicates that, working at a low current density and a high temperature, shells with a good reproducibility of the model and with a small grain size are obtained, that is, adequate for the required application.If the analysis is carried out in a plane transversal to the deposition, it can be tested in all the samples and for all the conditions that the growth structure of the deposit is laminar (Fig. 6), what is very satisfactory to obtain a high mechanical resistance although at the expense of a low ductibility. This quality is due, above all, to the presence of the additives used because a nickel sulfamate bath without additives normally creates a fibrous and non-laminar structure [9]. The modification until a nearly null value of the wetting agent gave as a result that the laminar structure was maintained in any case, that matter demonstrated that the determinant for such structure was the stress reducer (Allbrite SLA). On the other hand, it was also tested that the laminar structure varies according to the thickness of the layer in terms of the current density.Fig. 6. Plane transversal of series 2 (×600), etch 2.6. Internal stressesOne of the main characteristic that a shell should have for its application like an insert is to have a low level of internal stresses. Different tests at different bath temperatures and current densities were done and a measure system rested on cathode flexural tensiometer method was used. A steel testing control was used with a side fixed and the other free (160 mm length, 12.7 mm width and thickness 0.3 mm). Because the metallic deposition is only in one side the testing control has a mechanical strain(tensile or compressive stress) that allows to calculate the internal stresses. Stoney model [10] was applied and was supposed that nickel substratum thickness is enough small (3 μm) to influence, in an elastic point of view, to the strained steel part. In all the tested cases the most value of internal stress was under 50 MPa for extreme conditions and 2 MPa for optimal conditions, an acceptable value for the required application. The conclusion is that the electrolitic bath allows to work at different conditions and parameters without a significant variation of internal stresses.7. Test of the injection moldTests have been carried out with various representative thermoplastic materials such as PP, PA, HDPE and PC, and it has been analysed the properties of the injected parts such as dimensions, weight, resistance, rigidity and ductility. Mechanical properties were tested by tensile destructive tests and analysis by photoelasticity. About 500 injections were carried out on this core, remaining under conditions of withstanding many more.In general terms, important differences were not noticed between the behavior of the specimens obtained in the core and the ones from the machined cavity, for the set of the analysed materials. However in the analysis by photoelasticiy (Fig. 7) it was noticed a different tensional state between both types of specimens, basically due to differences in the heat transference and rigidity of the respective mold cavities. This difference explains the ductility variations more outstanding in the partially crystalline materials such as HDPE and PA 6.Fig. 7. Analysis by photoelasticity of injected specimens.For the case of HDPE in all the analysed tested tubes it was noticed a lower ductility in the specimens obtained in the nickel core, quantified about 30%. In the case of PA 6 this value was around 50%.First, the mold design based on the selection of the injection molding machine platen size. The largest area of the plate depends on the two-line distance between the rods, this is a limit for the injection molding machine.Used injection molding machine Tied a distance of 254mm. Therefore, the maximum width of the mold plate can not exceed this distance. In addition, there is a 4mm space to stay tied and mold to mold disassembly. This allows the die size of 250mm, can be the standard mold base. Staples in the upper right and lower-left corner of the mold substrate is fixed on the platen.Mold together with the folder pressure design allows the clamping force than the cavity forces the higher force (reaction force) in order to avoid the occurrence of plastic splash.According to the size of the standard mold, the public template width and height of 200mm and 250mm respectively. These dimensions make the level was placed on the public templates have enough space to design dual-mode cavity, the mother template simply left the space of fixed gate in order to inject molten plastic. Therefore, in the surface of the product will only leave the trace of a parting line. Products and flow in the mold parting surface at the same time off.The mold gate in the form of a standard gate or side gate. The gate is located between the flow channel and products. The bottom of the gate is designed to only 0.5mm thick and 20 ° inclination is to more easily injected into the plastic. The other end of the gate which is melting the plastic injected into the side 4mm wide and 0.5mm thick. The design of the mold, the choice of the flow cross-section of the parabolic form, can only facilitate the public template processing. However, this form of the flow channel with a circular flow channel have more heat loss and waste. This may make the molten plastic cools too fast. So should be designed so that the flow is relatively short at least 6mm radial dimensions.Materials or molten plastic the same temperature under the same pressure at the same time be sent to the cavity for the flow channel design is a very important point. For this reason, the layout of the cavity are generally symmetrical.In addition, the pores are also designed in the mold design, an important aspect. Public templates and the parent template with the surface of the high machining accuracy in order to prevent the occurrence of leaks in the injection molding. However, This will cause the air is enclosed in a closed mold cavity resulting in a short shot or incomplete parts. Suitable starting the stomatal design allows air to be released does not appear incomplete parts of the phenomenon.The cooling system is the level of holes played along the length direction of the cavity in the mold, since only the cooling effect. In the turbulent case, the waterline can be fully cooled mold.In this design, the mold release systems of only putting the fixed plate, gate sets and push the board. The intersection of sets in the center of the public mode, its role is not only a product fixed at the right location, is also played the role of product out of the cavity in the mold. Because the product is very thin, typically 1mm, so there is no need to design additional putter. Putting in the cavity but may broken holes in the mold release when introduced in the part.Finally, we need to stay under the shrinkage of the material sufficient tolerance compensation.8. ConclusionsAfter consecutive tests and in different conditions it has been checked that the nickel sulfamate bath, with the utilized additives has allowed to obtain nickel shells with some mechanical properties acceptable for the required application, injection molds, that is to say, good reproducibility, high level of hardness and good mechanical resistance in terms of the resultant laminar structure. The mechanical deficiencies of the nickel shell will be partially replaced by the epoxy resin that finishes shaping the core for the injection mold, allowing to inject medium series of plastic parts with acceptable quality levels.References[1] A.E.W. Rennie, C.E. Bocking and G.R. Bennet, Electroforming of rapid prototyping mandrels for electro discharge machining electrodes, J. Mater. Process. Technol.110 (2001), pp. 186–196.[2] P.K.D.V. Yarlagadda, I.P. Ilyas and P. Chrstodoulou, Development of rapid tooling for sheet metal drawing using nickel electroforming and stereo lithography processes, J. Mater. Process. Technol.111 (2001), pp. 286–294.[3] J. Hart, A. Watson, Electroforming: A largely unrecognised but expanding vital industry, Interfinish 96, 14 World Congress, Birmingham, UK, 1996.[4] M. Monzón et al., Aplicación del electroconformado en la fabricación rápida de moldes de inyección, Revista de Plásticos Modernos.84 (2002), p. 557.[5] L.F. Hamilton et al., Cálculos de Química Analítica, McGraw Hill (1989).[6] E. Julve, Electrodeposición de metales, 2000 (E.J.S.).[7] A. Watson, Nickel Sulphamate Solutions, Nickel Development Institute (1989).[8] A. Watson, Additions to Sulphamate Nickel Solutions, Nickel Development Institute (1989).[9] J. Dini, Electrodeposition Materials Science of Coating and Substrates, Noyes Publications (1993).[10] J.W. Judy, Magnetic microactuators with polysilicon flexures, Masters Report, Department of EECS, University of California, Berkeley, 1994. (cap′. 3).。
Development of High Performance Nickel Metal Hydride Batteries for Electric Vehicles

Development of High Performance Nickel Metal Hydride Batteries for Electric VehiclesSoo-Whan Kim, Ki-Chun Lee, Sung-Keun Lee, Tai-Ho Yang, San Cheon and Tae-Won L im, Hyundai Motor Company, Advanced Research & Development Center,San 1-1, Mabook-Ri, Kusung-Myun, Yongin-Shi, Kyunggi-Do, 449-910, KoreaPhone / Fax : 82-331-289-5598 / 82-331-289-5582E-mail : soowhan@, kichun@, dot@AbstractHyundai Motor Company (HMC) has long paid intensive attention to developing Zero Emission Vehicles (ZEV) as one of the major auto makers in the world. As the results, HMC, with its Acc ent EV, subcompact, equipped with Ni-MH battery, earned the world’s 5th certificate for an electr ic vehicle(EV) from California Air Resources Board (CARB) in 1997.Three kinds of Ni-MH batteries (80Ah, 90Ah, 105Ah) with over 70 Wh/kg and 195 W/kg have been developed in pilot scale since 1994. Modified cell design improved specific energy and pow er to 80 Wh/kg and 257 W/kg respectively in laboratory efforts, which lead to a better vehicle p erformance and a longer battery life.In addition, the efforts to reduce manufacturing costs of Ni-MH batteries have been made in term s of developing automation process of assembly and recycling technology.KeywordsNickel metal hydride, Specific energy, Specific power, Electrode, Recycling, Battery1. IntroductionAmong the several candidates of battery for EVs, Ni-MH battery has been considered as one of t he most promising in a near future, because it has many advantages such as high performance, hi gh energy density, proven safety and availability.[1]The performance of EV with Ni-MH battery is reasonably satisfactory for mass production, howe ver, its high cost and limited cruising range are acting as a main barrier against its wide applicati on. Therefore, the battery manufacturers are focussing their efforts on improvement of battery per formances as well as the cost reduction by automatic assembly process and recycling.In this paper, it is our intent to introduce our current status of development of Ni-MH battery inc luding automatic assembly process, recycling process and the improvement of battery performanc es such as specific energy and specific power.2. Development of Cells and Modules in Pilot ScaleNi-MH batteries with 80Ah, 90Ah and 105Ah capacity have been developed since 1994. The cell is composed of the pasted positive electrodes and sintered negative electrodes enveloped by non woven polyolefin separators. The positive electrode is made by mechanical impregnation of the p aste, which consists of nickel hydroxide, cobalt conductive material and binder, into a three dime nsional substrate such as nickel foam or fiber. The MH alloy powder of the negative electrode is prepared by crushing and grinding the ingot, which consists of V, Ti, Zr, Ni, Cr, Co, and Mn in some composition. The negative electrode is manufactured by compaction process of MH alloy powder onto two-dimensional current collector such as nickel-expanded metal and followed by si ntering process.The characteristics of HM series battery are shown in Figure 1 and Table 1.HM-80 and HM-90 modules have the same footprint with different heights. Also HM-105 modul e having the different footprint has been recently developed to be mounted on our new EV mode l which will be shown in the market soon.As shown in Figure 2, the available capacity of C/3 is 109Ah. The capacity decreases with incre asing discharging rate, however, more than 90% of the rated capacity can be available at 2.5C (262.5A) high rate. Figure 3 shows that over 104Ah is available in Dynamic Stress Test (DST) mo de.The available peak power during 30s at each DOD is shown in Figure 4. Over 2.5 kW is availab le from DOD 0% to 90% under the condition that maximum current is 300A and voltage is mor e than 2/3 OCV. In our electric vehicle system of 312V operated in constraint of maximum curre nt limit and minimum voltage limit, the battery pack can deliver more than 66kw through DOD 90. Also, the cycle life test of HM-105 is under way.Figure 1 HM-80 Ni-MH ModuleTable 1 Module Specification of HM SeriesItem HM-80HM-90HM-105Capacity(Ah)8090105Voltage(V)13.213.212Weight(kg)1618.518.6L 414414424W 100100100Dimension (mm)H168178173Specific Energy ( Wh/kg )707272.5Specific Power (W/kg 80% 30s)195195195Cycle life (cycles)>600>600Under TestThe specific power of HM-105 is 195W/kg, which meets 150W/kg of the mid-term goal of USA BC. In the specific energy, a further improvement is still in need to meet the mid-term goal.1234578910111213141516V o l t a g e (V )Time(hr)Figure 3. DST 120 Discharge characteristics of HM-105Module in ambient Temperature10203040506070809010089101112131415Discharging Capacity (Ah% / 105Ah)V o l t a g e (V )2030405060Battery Temperature (o C)Figure 2. Discharge characteristics of HM-105 Module at various discharge currents in Ambient Temperature3. Improvement of Cell Performances in Laboratory ScalePower and energy characteristics are improved by means of new electrode materials and new cell design.3.1. Improvement of specific energySpecific energy can be improved by enhancing efficiencies of electrode materials and minimizi ng the weight of other components such as case, current collectors and so on. The results are summarized in Table 2. The 80 Wh/kg cell is obtained via lighter current collector than that of control A, maintaining the same specific power. Also even if the amount of cobalt in the positive electrode is decreased, battery performance still shows the same as that of control, which results in cost reduction of materials. Further enhancement will be made to meet the m id-term goal of USABC in module basis via more efficient electrode materials.Table 2 Specific Energy improvement of prototype cellModificationControl Current CollectorElectrode MaterialsItemsAB D Weight(kg)1.61 1.58 1.59Dimension (mm)(W×H×L)97×178×36ßßAvailable Capacity(Ah)9910299Specific Energy(wh/kg)768076.5Specific Power(w/kg 30s)20420420510203040506070809010089101112131415D O D (%)V o l t a g e (V )01234Module Discharging Power(kW)102030405060708090100Pack Power(kW)Figure 4. Pulse Discharging (300A 30s) characteristics of HM-105 Module at each DOD in ambient Temperature3.2. Improvement of power capabilityDynamic characteristics of EVs, such as acceleration and a hill climbing are fully dependent on t he motor power and battery power capability. Therefore, the battery should supply enough power to the motor through EV Life. Battery power is degraded with repeated charge-discharge cycle, which is ascribed to increase of internal resistance. The degradation of power and capacity of the Ni-MH battery along the cycle life is attributed to the electrolyte dry-out of separator, oxidation of the negative electrodes and swelling of positive electrodes and so on. Accordingly, the initial p ower of battery should be improved to prolong the battery life.[2, 3]The factors affecting the internal resistance of HM series cells were studied by monitoring polari zation behaviors of each electrode during 60 second constant current pulse, as shown in Figure 5. From the polarization behaviors, it was found that the initial voltage drop (1s) was about 70% o f the voltage drop after 30s and, moreover, the drop in the negative electrode including separator s and electrolyte was ca 70% of the initial drop of the cell.In this development, the initial voltage drop was reduced with modified tab designs and new sub strates. In addition, thinner electrodes was used to increase the surface area of the positive and n egative electrodes and thus to reduce the reaction resistance. The results are shown in Table 3 an d Figure 6.The new negative substrate of cell B enhanced the specific power to 217 W/kg with compared to control A without expense of specific energy. Further improvements were obtained with modifie d tab design and thinner electrodes to 231 W/kg and 257 W/kg, respectively, in HM-80 cell. But they could be possible via sacrificing the specific energy by 5% and 17% respectively. Above i mprovements are due to the internal resistance reduction and mainly reduction of the initial cell r esistance. To improve the cruising range, dynamic characteristics and life of EV, our efforts to en102030405060V o l t a g e D r o p (V o c - V 100A )time(s)Figure 5. Voltage Drop of positive and negative electrodes in 100A pulse discharging at DOD 80% in ambient Temperathance both power capability and specific energy even further than now will be made.4. Cost Reduction4.1. Automation of cell assembly lineThe automatic assembly process plays a very important role in the cost reduction of battery. TherTable 3 Specific power improvement of prototype cellModificationControlCurrent Coll ector Tab DesignElectrode Thickness ItemsAC BDE Type HM-90HM-80HM-90HM-80HM-80Weight(kg) 1.61 1.42 1.61 1.38 1.42W x L 97 x 36ßßßßDimension (mm)H178158178158158Available Capacity(Ah)9986988270Specific Energy(wh/kg)7673.27672.560.8Specific Power(w/kg 30s)204208218231257Figure 6. Resistance comparison of 1s and 30s inproto cellsABCDE0.000.250.500.751.001.251.50Control HM-80Control HM-90Proto CellC e l l R e s i s t a n c e (m O h m )efore, our unique automatic cell assembly line has been developed from 1996. Last year, the cont inuous assembly line was successfully installed in our pilot plant, which results in reduction of m anufacturing labor cost.4.2. Development of Recycling ProcessThe recycling technology of Ni-MH battery has been developed to reduce the raw material cost s ince 1996. Our recycling technology consists of two parts. One is that the negative scrap and use d negative electrodes are re-melted to be reused in MH alloy. The other is that the nickel and co balt element in the positive scraps and used positive electrodes are recovered into cobalt powder, cobalt oxide powder and nickel oxide powder by leaching them in acid solutions.The raw material cost is reduced by 5% than before by reuse of the negative scraps via remeltin g. For further cost reduction, the remelting process of used negative electrodes has to be develop ed.In case of the positive scrap and used positive electrodes, they are dissolved in acid, and then co balt and nickel is recovered from solvent extraction method. Separated cobalt and nickel solution was made into cobalt powder, cobalt oxide powder and nickel oxide powder that may be used as positive materials. Now among them, recycled cobalt powder was identified as the same perform ance as the new material. The other materials are reused in other applications. As a result, we id entified 5% cost reduction of raw materials.5. Development of EVsHMC has been developing EVs since 1992 with Pb-Acid batteries and Ni/MH batteries mounted onto. Accent EV, subcompact, equipped with HM-90 Ni-MH batteries in 1996, and Atoz EVs wit h HM-80 batteries in 1998 were developed. These passenger EVs are converted from their own c ommercialized ICE-base models and are shown in Figures 6 and 7, respectively.Accent EV was certified as a ZEV by CARB in April 1997 and Hyundai Motor Company becam e the 5th of car makers in the world which have EVs to satisfy various and strict CARB require ments. Accent EV drove more than 100 miles in the city mode per single charge and 132 miles at 40 mph constant speed. Accent EVs and Atoz EVs are now under field operation to be tuned to real world.6. Future wor k1) Further improvements of the cell performances will be made via enhancing efficiencies o f electrode materials.2) In near future, Hybrid Electric Vehicle (HEV) will need powerful cylindrical D-cell to be developed through optimum cell design.7. SummaryPilot Scale Production1) 80, 90,105Ah Ni-MH Batteries have been developed successfully to satisfy the performance of 70 Wh/kg specific energy and 195 W/kg specific power. The performances of the 90Ah battery were proven to equip them with subcompact EV, Accent.Current Laboratory Efforts1) It was possible to obtain the 80Wh/kg cell by using the light current collector without a ny expense of specific power.2) 257w/kg specific power was obtained via reducing the electric resistance and increasing the reaction surface area.Figure 6 Accent EV with HM-90 PackFigure 7Atoz EV with HM-80 Pack8. References[1]P. Gifford,V. Hellmann and J. Adams, “Development of GM Ovonic nickel metal hydride batteries for electric vehicles and hybrid electric vehicle applications”, Proc. of EVS 96, Osaka (October 1996)[2]N. Fujioka, M. Ikoma, " Nickel Metal-Hydride Batteries for Pure Electric Vehicle", Proc. of EVS98,Bellgium(October, 98)[3]N. Ito, H. Inoue, K. Sato, N. Morishita and M. Ikoma, “Development of Sealed-Type Nickel/Metal-hydride Battery for Electric Vehicle”, Proc. of EVS 96, Osaka (October 1996)9. AcknowledgementThis work has been partially supported by the Korean Ministry of Commerce, Industry and Energy(MCIE). The authors are grateful to cordial cooperation of Mr. In-Joong Kim, Mr. Jin-Hun Jo and Mr. Ho-Yeon Ki m in Kyungwon Battery Co., Ltd.。
Nickel zinc electrochemical cell incorporating den

专利名称:Nickel zinc electrochemical cellincorporating dendrite blocking ionicallyconductive separator发明人:Muguo Chen,Fuyuan Ma,JenniferLeveille,Tsepin Tsai,Anu Eapen,BenLewis,Liang Liang,Xuejun Cao,AlexElien,Octavia Elien申请号:US10445271申请日:20030523公开号:US20050112471A1公开日:20050526专利内容由知识产权出版社提供专利附图:摘要:A nickel-zinc electrochemical cell is disclosed using a polymer matrix separator. The polymer matrix separator includes a polymerization product of one or more monomers selected from the group of water-soluble, ethylenically-unsaturated acids and acid derivatives, and a crosslinking agent, and serves as a primary or supplemental source of electrolyte ionic species for the electrochemistry. Ionic species is contained as a solution phase within the polymer matrix membrane, allowing it to behave as a liquid electrolyte without the disadvantages. In secondary batteries (i.e., rechargeable), polymer matrix membranes are particularly useful as both an electrolyte reservoir and as a dendrite resistant separator between the charging electrode and the zinc electrode. The polymer matrix membrane protects the electrodes from corrosion and prevents zinc oxidation product from the zinc electrode to contaminate the electrolyte.申请人:Muguo Chen,Fuyuan Ma,Jennifer Leveille,Tsepin Tsai,Anu Eapen,BenLewis,Liang Liang,Xuejun Cao,Alex Elien,Octavia Elien地址:South Salem NY US,Yorktown NY US,Brewster NY US,Chappaqua NY US,NewCity NY US,Yonkers NY US,Yorktown Heights NY US,Nanuet NY US,Bronx NY US,Bronx NYUS国籍:US,US,US,US,US,US,US,US,US,US 更多信息请下载全文后查看。
非晶态镍磷合金微管的制备及其催化加氢性能

•30 •非晶态镍磷合金微管的制备及其催化加氢性能刘连川1,卢小萍1,李强1,王桂雪1,谢广文1, *,王荣生2(1.青岛科技大学材料科学与工程学院,山东 青岛 266042; 2.山东电力集团公司青岛供电公司,山东 青岛 266002)摘要:以蜘蛛丝作模板,采用化学镀法在模板表面沉积得到均匀的非晶态Ni–P 合金镀层,用碱液溶解法去除内部的蜘蛛丝模板,制得非晶态Ni–P 合金微管。
分别采用能谱仪、扫描电镜、X 射线衍射法对产物进行表征。
以硝基苯液相加氢为探针反应,考察了非晶态Ni–P 合金微管的催化加氢性能,结果表明,非晶态Ni–P 合金微管具有良好的催化活性和循环使用性能。
关键词:镍–磷合金;化学镀;微管;模板;催化加氢 文章编号:1004 – 227X (2011) 10 – 0030 – 03 中图分类号:TQ 153.2文献标志码:APreparation and catalytic hydrogenation property of amorphous nickel–phosphorus alloy microtubes // LIU Lian-chuan, LU Xiao-ping, LI Qiang, WANG Gui-xue, XIE Guang-wen*, WANG Rong-shengAbstract: Amorphous Ni–P alloy microtubes were prepared via electroless plating with spider silk as template followed by removal of the template by dissolving in alkaline liquor. The products were characterized by energy-dispersive spectroscopy, scanning electron microscopy and X-ray diffraction technique. The catalytic hydrogenation property of the prepared amorphous Ni–P alloy microtubes were studied by liquid-phase hydrogenation of nitrobenzene. The results showed that the amorphous Ni–P alloy microtubes exhibit good catalytic activity for hydrogenation and cyclic use performance.Keywords: nickel–phosphorus alloy; electroless plating; microtube; template; catalytic hydrogenationFirst-author’s address: College of Material Science and Engineering, Qingdao University of Science and Technology, Qingdao 266042, China1 前言近年来,具有管状结构的纳微材料引起了人们的广泛关注。
物理学专业英语
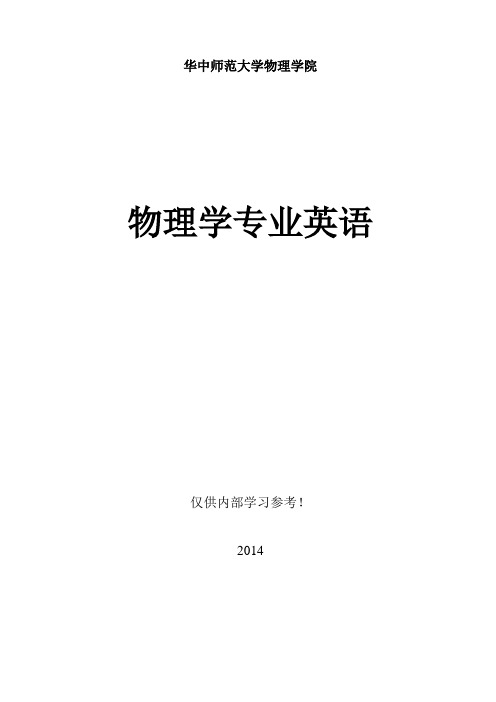
华中师范大学物理学院物理学专业英语仅供内部学习参考!2014一、课程的任务和教学目的通过学习《物理学专业英语》,学生将掌握物理学领域使用频率较高的专业词汇和表达方法,进而具备基本的阅读理解物理学专业文献的能力。
通过分析《物理学专业英语》课程教材中的范文,学生还将从英语角度理解物理学中个学科的研究内容和主要思想,提高学生的专业英语能力和了解物理学研究前沿的能力。
培养专业英语阅读能力,了解科技英语的特点,提高专业外语的阅读质量和阅读速度;掌握一定量的本专业英文词汇,基本达到能够独立完成一般性本专业外文资料的阅读;达到一定的笔译水平。
要求译文通顺、准确和专业化。
要求译文通顺、准确和专业化。
二、课程内容课程内容包括以下章节:物理学、经典力学、热力学、电磁学、光学、原子物理、统计力学、量子力学和狭义相对论三、基本要求1.充分利用课内时间保证充足的阅读量(约1200~1500词/学时),要求正确理解原文。
2.泛读适量课外相关英文读物,要求基本理解原文主要内容。
3.掌握基本专业词汇(不少于200词)。
4.应具有流利阅读、翻译及赏析专业英语文献,并能简单地进行写作的能力。
四、参考书目录1 Physics 物理学 (1)Introduction to physics (1)Classical and modern physics (2)Research fields (4)V ocabulary (7)2 Classical mechanics 经典力学 (10)Introduction (10)Description of classical mechanics (10)Momentum and collisions (14)Angular momentum (15)V ocabulary (16)3 Thermodynamics 热力学 (18)Introduction (18)Laws of thermodynamics (21)System models (22)Thermodynamic processes (27)Scope of thermodynamics (29)V ocabulary (30)4 Electromagnetism 电磁学 (33)Introduction (33)Electrostatics (33)Magnetostatics (35)Electromagnetic induction (40)V ocabulary (43)5 Optics 光学 (45)Introduction (45)Geometrical optics (45)Physical optics (47)Polarization (50)V ocabulary (51)6 Atomic physics 原子物理 (52)Introduction (52)Electronic configuration (52)Excitation and ionization (56)V ocabulary (59)7 Statistical mechanics 统计力学 (60)Overview (60)Fundamentals (60)Statistical ensembles (63)V ocabulary (65)8 Quantum mechanics 量子力学 (67)Introduction (67)Mathematical formulations (68)Quantization (71)Wave-particle duality (72)Quantum entanglement (75)V ocabulary (77)9 Special relativity 狭义相对论 (79)Introduction (79)Relativity of simultaneity (80)Lorentz transformations (80)Time dilation and length contraction (81)Mass-energy equivalence (82)Relativistic energy-momentum relation (86)V ocabulary (89)正文标记说明:蓝色Arial字体(例如energy):已知的专业词汇蓝色Arial字体加下划线(例如electromagnetism):新学的专业词汇黑色Times New Roman字体加下划线(例如postulate):新学的普通词汇1 Physics 物理学1 Physics 物理学Introduction to physicsPhysics is a part of natural philosophy and a natural science that involves the study of matter and its motion through space and time, along with related concepts such as energy and force. More broadly, it is the general analysis of nature, conducted in order to understand how the universe behaves.Physics is one of the oldest academic disciplines, perhaps the oldest through its inclusion of astronomy. Over the last two millennia, physics was a part of natural philosophy along with chemistry, certain branches of mathematics, and biology, but during the Scientific Revolution in the 17th century, the natural sciences emerged as unique research programs in their own right. Physics intersects with many interdisciplinary areas of research, such as biophysics and quantum chemistry,and the boundaries of physics are not rigidly defined. New ideas in physics often explain the fundamental mechanisms of other sciences, while opening new avenues of research in areas such as mathematics and philosophy.Physics also makes significant contributions through advances in new technologies that arise from theoretical breakthroughs. For example, advances in the understanding of electromagnetism or nuclear physics led directly to the development of new products which have dramatically transformed modern-day society, such as television, computers, domestic appliances, and nuclear weapons; advances in thermodynamics led to the development of industrialization; and advances in mechanics inspired the development of calculus.Core theoriesThough physics deals with a wide variety of systems, certain theories are used by all physicists. Each of these theories were experimentally tested numerous times and found correct as an approximation of nature (within a certain domain of validity).For instance, the theory of classical mechanics accurately describes the motion of objects, provided they are much larger than atoms and moving at much less than the speed of light. These theories continue to be areas of active research, and a remarkable aspect of classical mechanics known as chaos was discovered in the 20th century, three centuries after the original formulation of classical mechanics by Isaac Newton (1642–1727) 【艾萨克·牛顿】.University PhysicsThese central theories are important tools for research into more specialized topics, and any physicist, regardless of his or her specialization, is expected to be literate in them. These include classical mechanics, quantum mechanics, thermodynamics and statistical mechanics, electromagnetism, and special relativity.Classical and modern physicsClassical mechanicsClassical physics includes the traditional branches and topics that were recognized and well-developed before the beginning of the 20th century—classical mechanics, acoustics, optics, thermodynamics, and electromagnetism.Classical mechanics is concerned with bodies acted on by forces and bodies in motion and may be divided into statics (study of the forces on a body or bodies at rest), kinematics (study of motion without regard to its causes), and dynamics (study of motion and the forces that affect it); mechanics may also be divided into solid mechanics and fluid mechanics (known together as continuum mechanics), the latter including such branches as hydrostatics, hydrodynamics, aerodynamics, and pneumatics.Acoustics is the study of how sound is produced, controlled, transmitted and received. Important modern branches of acoustics include ultrasonics, the study of sound waves of very high frequency beyond the range of human hearing; bioacoustics the physics of animal calls and hearing, and electroacoustics, the manipulation of audible sound waves using electronics.Optics, the study of light, is concerned not only with visible light but also with infrared and ultraviolet radiation, which exhibit all of the phenomena of visible light except visibility, e.g., reflection, refraction, interference, diffraction, dispersion, and polarization of light.Heat is a form of energy, the internal energy possessed by the particles of which a substance is composed; thermodynamics deals with the relationships between heat and other forms of energy.Electricity and magnetism have been studied as a single branch of physics since the intimate connection between them was discovered in the early 19th century; an electric current gives rise to a magnetic field and a changing magnetic field induces an electric current. Electrostatics deals with electric charges at rest, electrodynamics with moving charges, and magnetostatics with magnetic poles at rest.Modern PhysicsClassical physics is generally concerned with matter and energy on the normal scale of1 Physics 物理学observation, while much of modern physics is concerned with the behavior of matter and energy under extreme conditions or on the very large or very small scale.For example, atomic and nuclear physics studies matter on the smallest scale at which chemical elements can be identified.The physics of elementary particles is on an even smaller scale, as it is concerned with the most basic units of matter; this branch of physics is also known as high-energy physics because of the extremely high energies necessary to produce many types of particles in large particle accelerators. On this scale, ordinary, commonsense notions of space, time, matter, and energy are no longer valid.The two chief theories of modern physics present a different picture of the concepts of space, time, and matter from that presented by classical physics.Quantum theory is concerned with the discrete, rather than continuous, nature of many phenomena at the atomic and subatomic level, and with the complementary aspects of particles and waves in the description of such phenomena.The theory of relativity is concerned with the description of phenomena that take place in a frame of reference that is in motion with respect to an observer; the special theory of relativity is concerned with relative uniform motion in a straight line and the general theory of relativity with accelerated motion and its connection with gravitation.Both quantum theory and the theory of relativity find applications in all areas of modern physics.Difference between classical and modern physicsWhile physics aims to discover universal laws, its theories lie in explicit domains of applicability. Loosely speaking, the laws of classical physics accurately describe systems whose important length scales are greater than the atomic scale and whose motions are much slower than the speed of light. Outside of this domain, observations do not match their predictions.Albert Einstein【阿尔伯特·爱因斯坦】contributed the framework of special relativity, which replaced notions of absolute time and space with space-time and allowed an accurate description of systems whose components have speeds approaching the speed of light.Max Planck【普朗克】, Erwin Schrödinger【薛定谔】, and others introduced quantum mechanics, a probabilistic notion of particles and interactions that allowed an accurate description of atomic and subatomic scales.Later, quantum field theory unified quantum mechanics and special relativity.General relativity allowed for a dynamical, curved space-time, with which highly massiveUniversity Physicssystems and the large-scale structure of the universe can be well-described. General relativity has not yet been unified with the other fundamental descriptions; several candidate theories of quantum gravity are being developed.Research fieldsContemporary research in physics can be broadly divided into condensed matter physics; atomic, molecular, and optical physics; particle physics; astrophysics; geophysics and biophysics. Some physics departments also support research in Physics education.Since the 20th century, the individual fields of physics have become increasingly specialized, and today most physicists work in a single field for their entire careers. "Universalists" such as Albert Einstein (1879–1955) and Lev Landau (1908–1968)【列夫·朗道】, who worked in multiple fields of physics, are now very rare.Condensed matter physicsCondensed matter physics is the field of physics that deals with the macroscopic physical properties of matter. In particular, it is concerned with the "condensed" phases that appear whenever the number of particles in a system is extremely large and the interactions between them are strong.The most familiar examples of condensed phases are solids and liquids, which arise from the bonding by way of the electromagnetic force between atoms. More exotic condensed phases include the super-fluid and the Bose–Einstein condensate found in certain atomic systems at very low temperature, the superconducting phase exhibited by conduction electrons in certain materials,and the ferromagnetic and antiferromagnetic phases of spins on atomic lattices.Condensed matter physics is by far the largest field of contemporary physics.Historically, condensed matter physics grew out of solid-state physics, which is now considered one of its main subfields. The term condensed matter physics was apparently coined by Philip Anderson when he renamed his research group—previously solid-state theory—in 1967. In 1978, the Division of Solid State Physics of the American Physical Society was renamed as the Division of Condensed Matter Physics.Condensed matter physics has a large overlap with chemistry, materials science, nanotechnology and engineering.Atomic, molecular and optical physicsAtomic, molecular, and optical physics (AMO) is the study of matter–matter and light–matter interactions on the scale of single atoms and molecules.1 Physics 物理学The three areas are grouped together because of their interrelationships, the similarity of methods used, and the commonality of the energy scales that are relevant. All three areas include both classical, semi-classical and quantum treatments; they can treat their subject from a microscopic view (in contrast to a macroscopic view).Atomic physics studies the electron shells of atoms. Current research focuses on activities in quantum control, cooling and trapping of atoms and ions, low-temperature collision dynamics and the effects of electron correlation on structure and dynamics. Atomic physics is influenced by the nucleus (see, e.g., hyperfine splitting), but intra-nuclear phenomena such as fission and fusion are considered part of high-energy physics.Molecular physics focuses on multi-atomic structures and their internal and external interactions with matter and light.Optical physics is distinct from optics in that it tends to focus not on the control of classical light fields by macroscopic objects, but on the fundamental properties of optical fields and their interactions with matter in the microscopic realm.High-energy physics (particle physics) and nuclear physicsParticle physics is the study of the elementary constituents of matter and energy, and the interactions between them.In addition, particle physicists design and develop the high energy accelerators,detectors, and computer programs necessary for this research. The field is also called "high-energy physics" because many elementary particles do not occur naturally, but are created only during high-energy collisions of other particles.Currently, the interactions of elementary particles and fields are described by the Standard Model.●The model accounts for the 12 known particles of matter (quarks and leptons) thatinteract via the strong, weak, and electromagnetic fundamental forces.●Dynamics are described in terms of matter particles exchanging gauge bosons (gluons,W and Z bosons, and photons, respectively).●The Standard Model also predicts a particle known as the Higgs boson. In July 2012CERN, the European laboratory for particle physics, announced the detection of a particle consistent with the Higgs boson.Nuclear Physics is the field of physics that studies the constituents and interactions of atomic nuclei. The most commonly known applications of nuclear physics are nuclear power generation and nuclear weapons technology, but the research has provided application in many fields, including those in nuclear medicine and magnetic resonance imaging, ion implantation in materials engineering, and radiocarbon dating in geology and archaeology.University PhysicsAstrophysics and Physical CosmologyAstrophysics and astronomy are the application of the theories and methods of physics to the study of stellar structure, stellar evolution, the origin of the solar system, and related problems of cosmology. Because astrophysics is a broad subject, astrophysicists typically apply many disciplines of physics, including mechanics, electromagnetism, statistical mechanics, thermodynamics, quantum mechanics, relativity, nuclear and particle physics, and atomic and molecular physics.The discovery by Karl Jansky in 1931 that radio signals were emitted by celestial bodies initiated the science of radio astronomy. Most recently, the frontiers of astronomy have been expanded by space exploration. Perturbations and interference from the earth's atmosphere make space-based observations necessary for infrared, ultraviolet, gamma-ray, and X-ray astronomy.Physical cosmology is the study of the formation and evolution of the universe on its largest scales. Albert Einstein's theory of relativity plays a central role in all modern cosmological theories. In the early 20th century, Hubble's discovery that the universe was expanding, as shown by the Hubble diagram, prompted rival explanations known as the steady state universe and the Big Bang.The Big Bang was confirmed by the success of Big Bang nucleo-synthesis and the discovery of the cosmic microwave background in 1964. The Big Bang model rests on two theoretical pillars: Albert Einstein's general relativity and the cosmological principle (On a sufficiently large scale, the properties of the Universe are the same for all observers). Cosmologists have recently established the ΛCDM model (the standard model of Big Bang cosmology) of the evolution of the universe, which includes cosmic inflation, dark energy and dark matter.Current research frontiersIn condensed matter physics, an important unsolved theoretical problem is that of high-temperature superconductivity. Many condensed matter experiments are aiming to fabricate workable spintronics and quantum computers.In particle physics, the first pieces of experimental evidence for physics beyond the Standard Model have begun to appear. Foremost among these are indications that neutrinos have non-zero mass. These experimental results appear to have solved the long-standing solar neutrino problem, and the physics of massive neutrinos remains an area of active theoretical and experimental research. Particle accelerators have begun probing energy scales in the TeV range, in which experimentalists are hoping to find evidence for the super-symmetric particles, after discovery of the Higgs boson.Theoretical attempts to unify quantum mechanics and general relativity into a single theory1 Physics 物理学of quantum gravity, a program ongoing for over half a century, have not yet been decisively resolved. The current leading candidates are M-theory, superstring theory and loop quantum gravity.Many astronomical and cosmological phenomena have yet to be satisfactorily explained, including the existence of ultra-high energy cosmic rays, the baryon asymmetry, the acceleration of the universe and the anomalous rotation rates of galaxies.Although much progress has been made in high-energy, quantum, and astronomical physics, many everyday phenomena involving complexity, chaos, or turbulence are still poorly understood. Complex problems that seem like they could be solved by a clever application of dynamics and mechanics remain unsolved; examples include the formation of sand-piles, nodes in trickling water, the shape of water droplets, mechanisms of surface tension catastrophes, and self-sorting in shaken heterogeneous collections.These complex phenomena have received growing attention since the 1970s for several reasons, including the availability of modern mathematical methods and computers, which enabled complex systems to be modeled in new ways. Complex physics has become part of increasingly interdisciplinary research, as exemplified by the study of turbulence in aerodynamics and the observation of pattern formation in biological systems.Vocabulary★natural science 自然科学academic disciplines 学科astronomy 天文学in their own right 凭他们本身的实力intersects相交,交叉interdisciplinary交叉学科的,跨学科的★quantum 量子的theoretical breakthroughs 理论突破★electromagnetism 电磁学dramatically显著地★thermodynamics热力学★calculus微积分validity★classical mechanics 经典力学chaos 混沌literate 学者★quantum mechanics量子力学★thermodynamics and statistical mechanics热力学与统计物理★special relativity狭义相对论is concerned with 关注,讨论,考虑acoustics 声学★optics 光学statics静力学at rest 静息kinematics运动学★dynamics动力学ultrasonics超声学manipulation 操作,处理,使用University Physicsinfrared红外ultraviolet紫外radiation辐射reflection 反射refraction 折射★interference 干涉★diffraction 衍射dispersion散射★polarization 极化,偏振internal energy 内能Electricity电性Magnetism 磁性intimate 亲密的induces 诱导,感应scale尺度★elementary particles基本粒子★high-energy physics 高能物理particle accelerators 粒子加速器valid 有效的,正当的★discrete离散的continuous 连续的complementary 互补的★frame of reference 参照系★the special theory of relativity 狭义相对论★general theory of relativity 广义相对论gravitation 重力,万有引力explicit 详细的,清楚的★quantum field theory 量子场论★condensed matter physics凝聚态物理astrophysics天体物理geophysics地球物理Universalist博学多才者★Macroscopic宏观Exotic奇异的★Superconducting 超导Ferromagnetic铁磁质Antiferromagnetic 反铁磁质★Spin自旋Lattice 晶格,点阵,网格★Society社会,学会★microscopic微观的hyperfine splitting超精细分裂fission分裂,裂变fusion熔合,聚变constituents成分,组分accelerators加速器detectors 检测器★quarks夸克lepton 轻子gauge bosons规范玻色子gluons胶子★Higgs boson希格斯玻色子CERN欧洲核子研究中心★Magnetic Resonance Imaging磁共振成像,核磁共振ion implantation 离子注入radiocarbon dating放射性碳年代测定法geology地质学archaeology考古学stellar 恒星cosmology宇宙论celestial bodies 天体Hubble diagram 哈勃图Rival竞争的★Big Bang大爆炸nucleo-synthesis核聚合,核合成pillar支柱cosmological principle宇宙学原理ΛCDM modelΛ-冷暗物质模型cosmic inflation宇宙膨胀1 Physics 物理学fabricate制造,建造spintronics自旋电子元件,自旋电子学★neutrinos 中微子superstring 超弦baryon重子turbulence湍流,扰动,骚动catastrophes突变,灾变,灾难heterogeneous collections异质性集合pattern formation模式形成University Physics2 Classical mechanics 经典力学IntroductionIn physics, classical mechanics is one of the two major sub-fields of mechanics, which is concerned with the set of physical laws describing the motion of bodies under the action of a system of forces. The study of the motion of bodies is an ancient one, making classical mechanics one of the oldest and largest subjects in science, engineering and technology.Classical mechanics describes the motion of macroscopic objects, from projectiles to parts of machinery, as well as astronomical objects, such as spacecraft, planets, stars, and galaxies. Besides this, many specializations within the subject deal with gases, liquids, solids, and other specific sub-topics.Classical mechanics provides extremely accurate results as long as the domain of study is restricted to large objects and the speeds involved do not approach the speed of light. When the objects being dealt with become sufficiently small, it becomes necessary to introduce the other major sub-field of mechanics, quantum mechanics, which reconciles the macroscopic laws of physics with the atomic nature of matter and handles the wave–particle duality of atoms and molecules. In the case of high velocity objects approaching the speed of light, classical mechanics is enhanced by special relativity. General relativity unifies special relativity with Newton's law of universal gravitation, allowing physicists to handle gravitation at a deeper level.The initial stage in the development of classical mechanics is often referred to as Newtonian mechanics, and is associated with the physical concepts employed by and the mathematical methods invented by Newton himself, in parallel with Leibniz【莱布尼兹】, and others.Later, more abstract and general methods were developed, leading to reformulations of classical mechanics known as Lagrangian mechanics and Hamiltonian mechanics. These advances were largely made in the 18th and 19th centuries, and they extend substantially beyond Newton's work, particularly through their use of analytical mechanics. Ultimately, the mathematics developed for these were central to the creation of quantum mechanics.Description of classical mechanicsThe following introduces the basic concepts of classical mechanics. For simplicity, it often2 Classical mechanics 经典力学models real-world objects as point particles, objects with negligible size. The motion of a point particle is characterized by a small number of parameters: its position, mass, and the forces applied to it.In reality, the kind of objects that classical mechanics can describe always have a non-zero size. (The physics of very small particles, such as the electron, is more accurately described by quantum mechanics). Objects with non-zero size have more complicated behavior than hypothetical point particles, because of the additional degrees of freedom—for example, a baseball can spin while it is moving. However, the results for point particles can be used to study such objects by treating them as composite objects, made up of a large number of interacting point particles. The center of mass of a composite object behaves like a point particle.Classical mechanics uses common-sense notions of how matter and forces exist and interact. It assumes that matter and energy have definite, knowable attributes such as where an object is in space and its speed. It also assumes that objects may be directly influenced only by their immediate surroundings, known as the principle of locality.In quantum mechanics objects may have unknowable position or velocity, or instantaneously interact with other objects at a distance.Position and its derivativesThe position of a point particle is defined with respect to an arbitrary fixed reference point, O, in space, usually accompanied by a coordinate system, with the reference point located at the origin of the coordinate system. It is defined as the vector r from O to the particle.In general, the point particle need not be stationary relative to O, so r is a function of t, the time elapsed since an arbitrary initial time.In pre-Einstein relativity (known as Galilean relativity), time is considered an absolute, i.e., the time interval between any given pair of events is the same for all observers. In addition to relying on absolute time, classical mechanics assumes Euclidean geometry for the structure of space.Velocity and speedThe velocity, or the rate of change of position with time, is defined as the derivative of the position with respect to time. In classical mechanics, velocities are directly additive and subtractive as vector quantities; they must be dealt with using vector analysis.When both objects are moving in the same direction, the difference can be given in terms of speed only by ignoring direction.University PhysicsAccelerationThe acceleration , or rate of change of velocity, is the derivative of the velocity with respect to time (the second derivative of the position with respect to time).Acceleration can arise from a change with time of the magnitude of the velocity or of the direction of the velocity or both . If only the magnitude v of the velocity decreases, this is sometimes referred to as deceleration , but generally any change in the velocity with time, including deceleration, is simply referred to as acceleration.Inertial frames of referenceWhile the position and velocity and acceleration of a particle can be referred to any observer in any state of motion, classical mechanics assumes the existence of a special family of reference frames in terms of which the mechanical laws of nature take a comparatively simple form. These special reference frames are called inertial frames .An inertial frame is such that when an object without any force interactions (an idealized situation) is viewed from it, it appears either to be at rest or in a state of uniform motion in a straight line. This is the fundamental definition of an inertial frame. They are characterized by the requirement that all forces entering the observer's physical laws originate in identifiable sources (charges, gravitational bodies, and so forth).A non-inertial reference frame is one accelerating with respect to an inertial one, and in such a non-inertial frame a particle is subject to acceleration by fictitious forces that enter the equations of motion solely as a result of its accelerated motion, and do not originate in identifiable sources. These fictitious forces are in addition to the real forces recognized in an inertial frame.A key concept of inertial frames is the method for identifying them. For practical purposes, reference frames that are un-accelerated with respect to the distant stars are regarded as good approximations to inertial frames.Forces; Newton's second lawNewton was the first to mathematically express the relationship between force and momentum . Some physicists interpret Newton's second law of motion as a definition of force and mass, while others consider it a fundamental postulate, a law of nature. Either interpretation has the same mathematical consequences, historically known as "Newton's Second Law":a m t v m t p F ===d )(d d dThe quantity m v is called the (canonical ) momentum . The net force on a particle is thus equal to rate of change of momentum of the particle with time.So long as the force acting on a particle is known, Newton's second law is sufficient to。
从碱性NH4OHNH4Cl缓冲溶液中电沉积镍

Trans. Nonferrous Met. Soc. China 29(2019) 222−232Electrodeposition of nickel from alkaline NH4OH/NH4Cl buffer solutionsPiotr M. S KITAŁ, Przemysław T. S ANECKI, Dorota SALETNIK, Jan KALEMBKIEWICZFaculty of Chemistry, Rzeszów University of Technology, 35-959 Rzeszów, PolandReceived 2 March 2018; accepted 28 June 2018Abstract: The electrodeposition of nickel on steel and copper from alkaline NH4OH/NH4Cl buffer solutions was investigated by cyclic voltammetry (CV), chronopotentiometry (CP), chronoamperometry (CA) as well as an opto-digital microscope, glow-discharge optical emission spectroscopy (GD−OES), XRF, and SEM−EDS techniques. The aim was to obtain Ni coatings from weak alkaline solutions and to optimize the process. The electrolyte composition, pH, temperature as well as current and potential parameters of the process were optimized using the quality of Ni deposit as a criterion. The role of hydrogen evolution in the process was discussed. An influence of Co as an additive was also investigated. It was found that a small amount of Co catalyzes Ni deposition process and improves the quality and color of the deposit. Therefore, in the possible application, the Ni/Co codeposition should be seriously considered. It was also shown that for constant current deposition mode, the width of self-established potential range, revealed at the very beginning of the process by the chronopotentiometric E=f(t) curves, is related to the quality of the coating. Key words: nickel; cobalt; electrodeposition; ammonia buffer solution1 IntroductionNickel electrodeposition is a very important processdue to its widely practical application for technical,protective and decorative purposes. Generally, classicWatts type acidic baths at pH of 4.7−5, described inmany papers e.g. [1−6], are used for bright, semi-brightand matt nickel plating. Moreover, a number of papersdescribed the respective codeposition: Ni/Co [7−11],Ni/Zn [12,13], Ni/Fe [14], Ni/Cr [15], Ni/Al [16], Co/Ni/Fe [17], Ni/TiO2 [18] and Ni/TiN [19] codeposition. Thenickel deposition is connected with hydrogen evolutionsince the process is catalyzed by the presence of metallicnickel [9]. The presence of chloride anions is required tomaintain a constant concentration of Ni2+cations bymeans of nickel anode dissolution.The advantages of Watts type acidic baths probablymade a situation, where an alternative is rarely sought.Their problem is the hydrogen evolution and theassociated decrease in current efficiency and metalsurface hydrogenation [20]. Nevertheless, attempts toapply slightly alkaline solutions were described inRefs. [21−23] and the limitation of hydrogen evolutionwas raised as an advantage. In contrast to acidic baths,the application of alkali ones was the interest of a veryfew papers for Ni deposition alone [21−23] and Ni/Zncodeposition [24]. ZHENG et al [21] focused onobtaining black nickel on RuO2/Ti electrode. ZHENGet al [22] investigated testing of nickel electroplating in asolution containing ammonia and chloride withoutsulfate ions. The quality of the coatings and theirpossible usefulness were not investigated, and the focuswas to achieve high current efficiency. GRUJICIC andPESIC [23] focused on the examination of themechanism realized at vitreous carbon electrode bycyclic voltammerotry (CV) method and not on obtainingnickel coatings.Currently, there are no complete data to estimate thepossibility of mildly alkaline solutions industrialapplication. In respective patents [25−28], mainly theseries of brighteners for such mildly alkaline nickelplating solutions are described. Therefore, in the presentwork, to assess the value of nickel deposition processfrom ammonia alkaline solutions, the process wasinvestigated and optimized by the selection of bathcomposition, pH, current density, potential, temperatureas well as the codeposition with cobalt. The properties ofobtained deposits were compared with those obtained byusing classical Watts baths.Corresponding author:Przemysław T. SANECKI; Tel: +48-17-8651261; E-mail: psanecki@.plDOI:10.1016/S1003-6326(18)64931-3Piotr M. SKITAŁ, et al/Trans. Nonferrous Met. Soc. China 29(2019) 222−232 2232 Experimental2.1 ApparatusThe (chronopotentiometry) (CP), cyclic volta- mmetry CV, chronoamperometry (CA) experiments were carried out by means of PGSTAT100 potentiostat/ galvanostat with high current module BOOSTER10A (AUTOLAB). All potentials are related to SCE (saturated calomel electrode) reference electrode. The reference electrode was placed in the investigated solution. Its temperature was the same as that of the bath. The potential of the SCE at 40 °C, in which most experiments were done, was assumed as a standard (0.234 V). The potential of SCE at other temperatures (20, 30, 50 and 60 °C) was recalculated to this standard. The difference of 20 °C corresponds to potential value of 13.4 mV (−0.67 mV/°C). Microscopic images, as well as the surface roughness of the samples, were recorded by means of DSX500i opto-digital microscope (OLYMPUS).The samples with deposited Ni and Ni/Co coatings were investigated by GD−OES technique with the use of GDS GD PROFILER HR spectrometer and by XRF technique with the use of ARL ADVANT′XP Sequential XRF X-ray spectrometer. Electronic scanning microscope (Hitachi S−3400N) was also used in the following settings: high vacuum mode (HV), secondary electron beam detector (SE), 20 kV acceleration voltage, spot size <100 nm, magnification 5x to 300000x. Due to the high surface homogeneity, three areas were selected for each sample. Chemical composition analysis was performed by X-ray diffraction (EDS) analysis in the areas marked with a photo frame. The results of the EDS analysis are presented in the form of X-ray spectrum (qualitative analysis) and as a report of chemical element content (quantitative analysis).2.2 Experimental proceduresThe electrodeposition process was carried out by using baker-type electrolyzer with two Ni plate anodes and one cathode located mutually parallel. The total volume of the electrolyte was 100 mL. Electrode dimensions were 13.5 cm × 2.5 cm for both anodes and 12 cm ×2 cm for the cathode; working surface of the cathode was 14 cm2 (both sides) for CP, CA experiments and 8 cm2for CV experiment. Regardless of the electrolysis current, the process was carried out until it reached the same electric charge (Q=336 C); it corresponds to the theoretical Ni layer thickness of 8.2 μm. The process was carried out in the following temperature regimes: 20, 30, 40, 50 and 60 °C.Before deposition, steel samples were electro- polished for 10 min in solution: 600 mL 85% H3PO4, 370 mL 96% H2SO4, 30 mL H2O; current density 0.23 A/cm2; immersed surface of sample 24−28 cm2. The copper samples were electropolished for 10 min in solution: 700 mL 85% H3PO4, 350 mL H2O, current density 0.38 A/cm2; followed by immersing in 65% HNO3 (HNO3/H2O volume ratio of 1:1) solution for 1 s.2.3 Compositions of bathsSolution 1 for Ni deposition (S1) contained 0.5 mol/L NiSO4, 1 mol/L NH4OH, 0.9 mol/L (NH4)2SO4, 0.5 mol/L NH4Cl. Final pH=7.7, 8.4 or 9.4 was established with the use of NH4OH or H2SO4solution. Solution 2 for Ni deposition (S2) contained 0.5 mol/L NiSO4, 1 mol/L NH4OH, 0.9 mol/L (NH4)2SO4, 0.5 mol/L NH4Cl, 1×10−6, 10×10−6, 100×10−6, 1000×10−6 and 10000×10−6 C6H5SO3Na (SDS). Final pH of S2 was 8.4. Solution 3 for Ni and Co codeposition (S3) contained 0.5 mol/L NiSO4, 1 mol/L NH4OH, 0.9 mol/L (NH4)2SO4, 0.5 mol/L NH4Cl, 0.025 mol/L CoCl2·6H2O. Final pH of S3 was 8.2. The content of Ni2+ in the solutions used for deposition was controlled with the use of colorimetric method at λ=360 nm and 578 nm (Hitachi 5100). The results indicate that the constant level of Ni2+is maintained, provided that the hydrogen evolution is kept under 5% of current efficiency. If the evolution of hydrogen increases, the concentration of Ni2+ in the bath (2%−4%) slightly increases. During the preparation of mildly alkaline NH4OH/NH4Cl buffer solutions S1, S2 and S3 in the presence of NH4Cl, no nickel hydroxide precipitates unless pH is below 7.7. On the contrary, in the absence of NH4Cl, an addition of NH4OH into the Ni2+solution produces a precipitate which is soluble in the excess of reagent, although a small amount of Ni(OH)2 remains insoluble. The electrolyte composition was controlled by spectrophotometry of Ni2+ ions in solution (Ni2+concentration), pH (NH3concentration) and conductivity measurement. The evaporation of NH3 was not a problem since pH did not change during the course of the experiment. Solution 4 for electroless Ni deposition (S4) contained solution 4A (0.084 mol/L NiCl2·6H2O) and solution 4B (0.24 mol/L NaH2PO2·H2O, 0.12 mol/L CH3COONa, pH=7.3). Solutions 4A and 4B were mixed at a volume ratio of 1:1. The deposition process was carried out at 90−95 °C. Watts type solution contained 58.5 g NiSO4·6H2O, 7.5 g NiCl2·6H2O and 10 g H3BO3, refilled with water to 250 mL; it corresponded to 0.89 mol/L NiSO4·6H2O, 0.13 mol/L NiCl2·6H2O and 0.65 mol/L H3BO3.3 Results and discussion3.1 Results of constant current electrolysis (CCE)methodThe results of Ni deposition, in a form of images ofPiotr M. SKITAŁ, et al/Trans. Nonferrous Met. Soc. China 29(2019) 222−232 224the steel/Ni samples at pH=7.7, 8.4 and 9.4, are presented in Fig. 1.Fig. 1Deposition of nickel in alkaline ammonia solutions at different pH and current density values (CCE mode) (Optimization of pH and current density. Real photo of deposits obtained on Fe (steel) sample at pH=7.7, 8.4 and 9.4. At pH=7.7, a semi-bright but rough coating was obtained which was confirmed by microscopic images)The results in Fig. 1 give important information regarding the evolution of hydrogen and the quality of the coating. Current density and pH were applied as the input variables. At pH=9.4, visible spots of thinner nickel layer are obtained. Evidently, the slow evolution of hydrogen generates its standstill (anchored) bubbles on the surface which block the surface at these points. Moreover, for samples obtained with a current efficiency less than 96% (Fig. 1, pH=8.4), where hydrogen evolution is more intensive, the effect does not occur. Generally, at any pH value, hydrogen evolution should be kept intensively enough to obtain a good quality smooth deposit without spots which can be easily regulated by current density. The hydrogen evolution reaction (HER) process is tightly linked with current efficiency, determined from the mass of the deposited metal and respective charge exchange (Table 1). The current efficiency of the Ni deposition process with the simultaneously occurring HER was found to be relatively high in all cases including optimized conditions (pH=8.4, 3 A/dm2).Table 1 Current efficiencies at various pH values (Solution S1) pHCurrent efficiency/%2 A/dm23 A/dm24 A/dm27.7 92.1 93.2 93.88.4 98.5 97.0 95.19.4 98.0 97.0 96.3The microscopic images of the samples from Fig. 1 and Table 1 are presented in Fig. 2. The data of Fig. 1 and Table 1 allowed for the optimization of the hydrogen evolution process by setting the current density and pH. Increasing current efficiency to about 98% is associated with a decrease in the quality of the coating (Fig. 1, Table 1). Therefore, a slightly lower current efficiency had to be accepted in favor of the quality of the coating. Furthermore, Fig. 2 allowed for the evaluation of grain size and detection of possible cracks in the coating. The results also lead to the choice of pH=8.4 and current density 3 A/dm2. On the other hand, Figs. 2(c), (e), and (g) indicate the same quality of coating obtained at different pH and current density values.Further information about the process was obtained with the use of CP technique, equivalent to constant current electrolysis (CCE). The results in Fig. 1 and, more importantly, corresponding to data in Fig. 3 indicate that deposition potential should be less negative than −1.30 V to avoid a higher contribution of hydrogen evolution and more negative than −1.23 V to keep the effective process of nickel deposition. This range of potential maintains the hydrogen evolution on a proper level. The E=f(t) plots in Fig. 3 provide relevant data on the role of potential value in applied CCE technique. Figure 3 indicates that the deposition potential range from −1.23 to −1.30 V takes place for the curves 3, 5, and 7. For curve 7, the range is relatively wide (ΔE= 37 mV), which means that the consecutive layers were deposited at various potentials. In contrast, for curve 5 the whole layer was deposited in a narrow potential range (ΔE=13 mV), which corresponds to Figs. 1 and 2(e) at pH=8.4 and 3 A/dm2. Equally, curve 3 of Fig. 3 with ΔE=22 mV corresponds to Figs. 1 and Fig. 2(c) at pH=7.7 and 4 A/dm2.The potential shift of Ni deposition towards more negative values with the increase of pH value, observed in Fig. 3, should be interpreted. The current efficiency for the simultaneously occurring hydrogen evolutionPiotr M. SKITAŁ, et al/Trans. Nonferrous Met. Soc. China 29(2019) 222−232 225Fig. 2Microscopic images of samples from Fig. 1 showing comparison of various nickel layers deposited on steel at different current densities of 2 A/dm2 (a, d, g), 3 A/dm2 (b, e, h), and 4 A/dm2 (c, f, i) and different pH values of 7.7 (a, b, c), 8.4 (d, e, f), and 9.4 (g, h, i)Fig. 3 Nickel electrodeposition from alkaline solutions (CP responses at different current densities of 2, 3 and 4 A/dm2 and three applied pH values of 7.7, 8.4 and 9.4. All responses correspond to nine samples shown in Figs. 1 and 2. The areas matching with clear Ni coating (Figs. 2(c), (e), (g)) corresponded to the potential range from −1.23 to −1.30 V. For all curves, ΔE intervals were determined in the way shown for curve 1. The meaning of ΔE PL is also explained)Piotr M. SKITAŁ, et al/Trans. Nonferrous Met. Soc. China 29(2019) 222−232 226reaction (HER) is low in all cases (less than 8%); therefore, the influence of the HER can be neglected, at least at not very high current density. The observed trend points out the increasing complexation of Ni2+ ions in the solution. At pH values of 7.7, 8.4, and 9.4, the molar ratios of Ni/NH3are approximately 1:1, 1:2, and 1:6, respectively. Therefore, decreasing this molar ratio should lead to a decrease of Ni2+ions concentration. Simultaneously, a Nernstian negative pot ential shift ΔE PL (a shift of the current plateau) should occur, which is observed in practice. The conversion of ΔE PL parameter onto a decrease of Ni2+ions concentration is shown in Table 2. Approximate Ni2+concentration changes were calculated from ele ctrochemical data namely ΔE/ΔpH and the Nernst equation.On the other hand, the known values of stability constants β1, β2andβ6for nickel complexes make it possible to estimate the values of free Ni2+ion concentration. The calculation for solution S1 at pH values of 7.7, 8.4, and 9.4 gives the approximate free Ni2+ion concentration values of 1.8×10–3, 5.6×10–6 and 2.2×10–12, respectively. The Ni2+concentration, calculated from β1 and β2, decreased by a factor of 321. This is in consistency with the respective change calculated from electrochemical data (Table 2) where the Ni2+ concentration decreased by a factor of 251.A question arises, of which ammonia complex among possible NiL n, n=1−6 is the dominant form in the investigated solution. For this purpose, spectral UV−Vis studies of Ni complexes were performed for solutions with different molar ratios of Ni/NH3 (Figs. 4(a) and (b)). The results indicate that starting from the molar ratio of Ni/NH3 being 1:3 and above, the positions of absorption peaks at approximately 600 and 360 nm remain constant. The green color of the solution at molar ratios of Ni/NH3 being 1:0 and 1:0.5 corresponds to Ni2+aqua complex, blue color at molar ratios of Ni/NH3 being 1:1 and more corresponds to the ammonia complex. The molar ratio of Ni/NH3being 1:2, selected as optimization for deposit quality, corresponds mainly to NiL2complex since lg β1=2.75 and lg β2=4.95 [29].On the basis of the results obtained so far (Figs. 1−3), the optimum for Ni deposition on steel consists of the bath with pH=8.4, T=40 °C, current density 3 A/dm2, and the resulting current efficiency is 97%. The choice of temperature parameter should be also a result of the optimization process. The respective experimental data are presented in Fig. 5(a). The E=f(t) response of CP technique also depends on temperature (Fig. 5(b)).Data in Fig. 5 allow for temperature optimization and suggest that 40 °C is the best with the lowest grain size, which is in line with the early choice. Besides, the experimental results indicate that the best quality ofTable 2 Processing of data in Fig. 3Number of E=f(t) curve from Fig. 3 Current density/(A·dm−2)ΔpHΔE PL/mV (ΔE PL/ΔpH)/mVMean value of(ΔE PL/ΔpH)/mV(Δc Ni2+/ΔpH)/(mol·L−1)1−4 2 0.7 0.061 0.087 0.082 1154−7 2 1.0 0.078 0.078 0.082 4332−5 3 0.7 0.071 0.101 0.099 2515−8 3 1.0 0.097 0.097 0.099 19023−6 4 0.7 0.035 0.050 0.042 14.86−9 4 1.0 0.035 0.035 0.042 14.8Fig. 4 UV−Vis spectra of 0.5 mol/L Ni2+ in mol/L NH4Cl solution with different molar ratios of Ni2+/NH3 at different pH values (a) and optimized pH=8.4 (b)Piotr M. SKITAŁ, et al/Trans. Nonferrous Met. Soc. China 29(2019) 222−232227Fig. 5 Influence of temperature on quality of electrodeposited Ni (Deposit obtained at 20 °C shows cracks) (a) and influence of temperature on Ni electrodeposition process (CP responses were obtained in optimized solution (pH=8.4, 3 A/dm 2) at different temperatures; deposition technique: CCE (equivalent to CP)) (b)deposit (Fig. 5(a)) corresponds to the narrowest ΔE interval in E =f (t ), i.e. CP response at 40 °C (Fig. 5(b)). A cracked deposit occurs in cases when ΔE interval is wider (Fig. 5, 20 °C). A similar conclusion was derived from results in Fig. 3. The results in Figs. 3 and 5(b) are summarized as follows: the best quality of deposits corresponds to the narrowest ΔE interval in E =f (t ) response, revealed with the use of CP technique. This experimental fact suggests that a fast potential fixing in constant current technique promotes good quality of the coating.A comparison of Ni deposit on steel and copper is presented in Fig. 6. It is worth mentioning that the microscopic images of Ni deposit obtained on steel and copper are almost identical with that obtained by chemical electroless Ni deposition (results not shown).The same bath and conditions are optimum for Ni deposition on a copper surface (Fig. 6).The morphologies of the Ni coatings electro- deposited on steel and copper substrates under identical conditions are not identical (Fig. 6). Generally, in electroplating, the properties of a deposit depend on background kind, its properties, and structure.3.2 Results of constant potential electrolysis (CPE)methodFigure 7 shows nickel eletrodeposition from alkaline solutions by CPE at pH=8.4 and different deposition potentials and effect of potential on deposition process in solution S1 at pH=8.4. The results obtained by constant potential electrolysis (CPE), at optimized pH=8.4 (Fig. 7(b)), indicate that there exists a good relevance to the results obtained by means of constant current electrolysis (CCE). The potential value and the resulting current are responsible for the obtained structure. For small values of potential (−1.05 to −1.10 V), which correspond to low values of currentFig. 6 Comparison of Ni deposits on steel (a) and copper (b) at pH=8.4, 3 A/dm 2 in solution S1 with deposition technique of CCE(Fig. 7(a)), bright coatings are obtained (pictures a 1 and b 1 in Fig. 7(a)). An increase of negative potential results in matte coatings (pictures d 1, e 1 and f 1 in Fig. 7(a), E is from −1.23 to −1.30 V). A further shift of potential towards more intense hydrogen evolution leads to the destruction of the coatings by severe stresses and cracks (pictures g 1 and h 1 in Fig. 7(a); more negative thanPiotr M. SKITAŁ, et al/Trans. Nonferrous Met. Soc. China 29(2019) 222−232 228−1.30 V). The constant potential electrolysis results suggest the potential range of −1.23 to −1.30 V is optimal which remains in full compliance with the results obtained indirectly by CCE method, namely −1.23 to −1.30 V (Section 3.1, Figs. 2(c), (e) and (g)). 3.3 Further optimization of Ni electrodepositionTo improve the quality of nickel coatings, WU et al [10] included Co as a co-deposited metal. The quoted authors reported, among others, that for 2.5% cobalt content in the coating, a silver-white layer can be obtained. The codeposition of Ni/Co alloys was also extensively investigated by VAZQUEZ-ARENAS et al [8,9]. Our results indicate that a small amount of Co ions in the bath (solution S3, 4.78% Co in the sum of Ni and Co inserted) give a brighter and smoother nickel coating. In turn, the content of Co in Ni/Co deposit, determined with the use of several spectral techniques, is 5.2%−5.8%. Current vs potential characteristics of Ni and Co are shifted relative to each other by about 160 mV at I=−0.4 A (Fig. 8). Figure 8 shows that Co catalyzes nickel deposition and indirectly reduces the hydrogen evolution. Cobalt codeposition also makes it possible to apply a higher current regime. It is worth mentioning that cyclic voltammetry (CV) deposition technique (CV electrolysis, CVE) was chosen as the best technique for the copper deposition [30,31].To show that the additives applied to Watts type baths can also be applied for the alkaline ones, a typical additive i.e. sodium benzenesulfonate (SDS) was checked. The results (Fig. 9) indicate that the brightening effect also appears in the alkaline solution. The optimum concentration of SDS was 1000×10−6 (mass fraction). The influence of SDS concentration is also visible in CP responses (Fig. 9). Figure 9 indicates both catalytic and inhibitory effects, characteristic for the adsorption of inert organic compounds on electrodes [32].The roughness of metallic deposit is an important parameter which was determined by using a specified option of the applied microscope. Figure 10 presents the representative results of such a determination. The roughness values of deposits were compared with those of steel and copper bases. The roughness differences between samples are significant but not high due to theFig. 7 Nickel electrodeposition from alkaline solutions by CPE at pH=8.4 and deposition potentials of −1.05 V (a1), −1.10 V (b1), −1.15 V (c1), −1.23 V (d1), −1.25 V (e1), −1.30 V (f1), −1.35 V (g1) and −1.40 V (h1) (a) and effect of potential on deposition process in solution S1 at pH=8.4 (b)Fig. 8Comparison of Ni and Ni/Co deposits obtained by CVE mode: (a, b) Deposits obtained on steel with their respective microscopic images for Ni (a) and Ni/Co (b); (c) CV responses (scan rate 0.01 V/s; 4 cycles scanned to obtain Q=336 C, reverse potential −1.6 V)Piotr M. SKITAŁ, et al/Trans. Nonferrous Met. Soc. China 29(2019) 222−232229Fig. 9 Effect of SDS concentration on microscopic image of Ni deposit (Deposition technique: CCE; solution S2; SDS concentration: 0−10000×10−6; current efficiency: 90%−91%) (a) and effect of SDS concentration on CP responses (Deposition technique: CCE; solution S2) (b)Fig. 10 Overview of roughness describing parameters for all experimentally obtained Ni and Ni/Co deposits (R a (μm) is roughness factor: Average profile height; R z (μm) is the biggest profile height. All data were obtained and processed by using Olympus microscope. Dotted lines: Results for electropolished Fe samples before deposition)fact that all samples were electropolished before deposition (samples 1 vs 2 and 3 vs 4) to obtain repetitive results. Moreover, the state of the metal surface also determines the quality of the coating. The results support the correctness of the presented optimization of the mildly alkaline bath since the lowest roughness results were obtained under the optimized conditions of the process (pH=8.4, J =3 A/dm 2, T =40 °C). It is visible for the pairs: samples 9 vs 6 and 12 (pH criterion choice); samples 9 vs 8 and 10 (J criterion choice); samples 21 vs 19, 20 and 22, 23 (T criterion choice).3.4 Composition and structure of optimized Ni andNi/Co coatingsThe compositions of Ni and Ni/Co coatings arepresented in Table 3. Three spectroscopic techniques (GD −OES, XRF, and SEM −EDS) were used to check the composition of the coatings. A confirmation of the composition was obtained for a pure Ni coating, where, depending on the technique, 100% or 96.8% Ni was determined (Table 3). The oxygen content was also determined to evaluate the degree of coating oxidation. In turn, the Ni/Co layer composition, mentioned in Section 3.3, depending on the technique, was determined as 5.2% and 5.6% of Co (GD −OES and XRF, respectively). The SEM −EDS method, based on a small surface sample, gave 7.4% of Co (Table 3). The Co content obtained by SEM −EDS method is higher in comparison to GD −OES method. The discrepancy can arise from the fact that Co peak is coupled with one ofPiotr M. SKITAŁ, et al/Trans. Nonferrous Met. Soc. China 29(2019) 222−232 230three Fe peaks. Therefore, the most reliable Co content in the coating is 5.2%−5.6% (Table 3). Since the participation of Co in optimized bath composition is 4.78% in the sum of Ni and Co, an enrichment of the layer in this component occurs. GD−OES technique determines not only the surface composition of the layer, but also the composition profiles along the entire deposited coating (Fig. 11). Figure 11 shows a comparisonTable 3 Compositions of Ni and Ni/Co coatings obtained by GD−OES, XRF and EDS methodsCoating Method Content/% Ni Co O FeNiGD−OES* at. 99.9 <0.1 −<0.1 XRF wt. 100 0 −−SEM−EDS**SEM−EDS**wt. 96.8±0.4 0 1.1±0.1 2.1±0.1at. 93.9±0.4 0 3.9±0.3 2.2±0.1Ni/CoGD−OES* at. 94.7 5.2±0.2 −<0.1 XRF wt. 94.2 5.6±0.2SEM−EDS**SEM−EDS**wt. 90.2±0.5 7.4±0.2 1.5±0.1 0.9±0.1at. 86.7±0.5 7.0±0.2 5.3±0.2 0.9±0.1* Measurements completed on surface of 19.6 mm2; ** measurements completed on surface of 0.1 mm2Fig. 11 SEM images of optimized Ni (a, a') and Ni/Co (b, b') coatings, and GD−OES content (at.%) profiles of optimized Ni (c, c') and Ni/Co (d, d') coatings (Logarithmic (c, d) and linear (c', d') scales were applied. Evaporation time (x-axis) is proportional to depth of metal layer)Piotr M. SKITAŁ, et al/Trans. Nonferrous Met. Soc. China 29(2019) 222−232 231of the surfaces of pure Ni and Ni/Co coatings and images were recorded with SEM.4 Conclusions(1) The optimized conditions for Ni plating in ammonia alkaline solution are as follows: composition of solutions S1 or S3; temperature 40 °C; potential from −1.23 to −1.30 V (vs SCE); current density 3−4 A/dm2; mode of the process: CCE, CPE as well as CVE repeated run after run. The small addition of cobalt ions catalyzes the deposition of nickel and improves the quality of the coating.(2) Even in mildly alkaline ammonia solution, the hydrogen evolution reaction (HER) due to the electrocatalytic effect of Ni deposit is present. Moreover, a noticeable contribution (up to 5%) of HER is necessary to obtain a good quality nickel deposit.(3) In alkaline ammonia solution, a small amount of cobalt ions improve the quality and color of the deposit, irrespective of the deposition technique used. The yellowish shine of the nickel coating disappears. Therefore, in the possible application, the nickel and cobalt codeposition should be considered. AcknowledgmentsThe authors are grateful to Dr. Eng. Wojciech Nowak for the realization of GD−OES and XRF spectral measurements and to Dr. Eng. M. Wierzbińska for the realization of SEM and EDS measurements. References[1]YEAGER J, CELS J P, YEAGER E, HOVORKA F. Theelectrochemistry of nickel. I: Codeposition of nickel and hydrogen from simple aqueous solution [J]. Journal of the Electrochemical Society, 1959, 106: 328−336.[2]EPELBOIN I, WIART R. Mechanism of electrocrystallization ofnickel and cobalt in acidic solution [J]. Journal of the Electrochemical Society, 1971, 118: 1577−1582.[3]KOLLIA C, SPYRELLYS N, AMBLARD J, FROMENT M,MAURIN G. Nickel plating by pulse electrolysis: Textural and microstructural modification due to adsorption/desorption phenomena [J]. Journal of Applied Electrochemistry, 1990, 20: 1025−1032.[4]XU W C, DAI P Q, WU X L. Deformation behaviour ofelectrodeposited nanocrystalline Ni with broad grain size distribution [J]. Materials Science and Technology, 2010, 26: 591−596.[5]V AZQUEZ-ARENAS J, ALTAMIRANO-GARCIA L, PRITZKERM, LUNA-SANCHEZ R, CABRERA-SIERRA R. Experimental and modeling study of nickel electrodeposition including H+and water reduction and homogeneous reactions [J]. Journal of the Electrochemical Society, 2011, 158: D33−D41.[6]ROSE I, WHITTINGTON C. Nickel plating handbook [M]. Brussels:Nickel Institute, 2014.[7]ZHOU Ke-chao, MA Li, LI Zhi-you. Oxidation behaviors ofelectrodeposited nickel−cobalt coatings in air at 960 °C [J].Transactions of Nonferrous Metals Society of China, 2011, 21: 1052−1060. [8]V AZQUEZ-ARENAS J, PRITZKER M. Steady-state model foranomalous Co−Ni electrodeposition in sulfate solutions [J].Electrochimica Acta, 2012, 66: 139−150.[9]V AZQUEZ-ARENAS J, ALTAMIRANO-GARCIA L, TREERA-TANAPHITAK T, PRITZKER M, LUNA-SANCHEZ R, CABRERA-SIERRA R. Co−Ni alloy electrodeposition under different conditions of pH, current and composition [J].Electrochimica Acta, 2012, 65: 234−243.[10]WU Z W, LEI Y P, WANG Y, FU H G. Effect of cobalt content onmicrostructure and property of electroplated nickel−cobalt alloy coatings [J]. Materials Science and Technology, 2013, 44: 593−600.[11]LIU Xue-wu, XU Yun-hua, QU Yi, SUN Li-long. Structure,morphology and wear resistance of electrodeposited Ni−Co alloy deposits [J]. Integrated Ferroelectrics, 2014, 152: 144−151.[12]LEWIS D B, LEHMBERG C E, MARSHALL G W. The structureand texture development of Ni alloy electrodeposits. III: Nickel−zinc electrodeposits [J]. Transactions of the Institute of Metal Finishing, 2004, 82: 64−70.[13]FASHU S, GU Chang-dong, ZHANG Jia-lei, HUANG Mei-ling,WANG Xiu-li, TU Jiang-ping. Effect of EDTA and NH4Cl additives on electrodeposition of Zn−Ni films from choline chloride-based ionic liquid [J]. Transactions of Nonferrous Metals Society of China, 2015, 25: 2054−2064.[14]MA Li, ZHANG Long, LI Xiao-bing, LI Zhi-you, ZHOU Ke-chao.Fabrication and characterization of electrodeposited nanocrystalline Ni−Fe alloys for NiFe2O4spinel coatings [J]. Transactions of Nonferrous Metals Society of China, 2015, 25: 146−153.[15]HE Mei-feng, WANG Hao, JIANG Hong, ZHAO Su, PAN Deng.Effect of hydrogen peroxide concentration on surface properties of Ni−Cr alloys [J]. Transactions of Nonferrous Metals Society of China, 2016, 26: 1353−1358.[16]ZHOU Yue-bo, ZHANG Hai-jun. Effect of annealing treatment oncyclic-oxidation of electrodeposited Ni−Al nanocomposite [J].Transactions of Nonferrous Metals Society of China, 2011, 21: 322−329.[17]LI Jian-mei, ZHANG Zhao, LI Jin-feng, XUE Min-zhao, LIUYan-gang. Effect of boron/phosphorus-containing additives on electrodeposited CoNiFe soft magnetic thin films [J]. Transactions of Nonferrous Metals Society of China, 2013, 23: 674−680.[18]NIU Te, CHEN Wei-wei, CHENG Huan-wu, WANG Lu. Graingrowth and thermal stability of nanocrystalline Ni−TiO2 composites [J]. Transactions of Nonferrous Metals Society of China, 2017, 27: 2300−2309.[19]ZHU Xu-bei, CAI Chao, ZHENG Guo-qu, ZHANG Zhao, LIJin-feng. Electrodeposition and corrosion behavior of nanostructured Ni−TiN composite films [J]. Transactions of Nonferrous Metals Society of China, 2011, 21: 2216−2224.[20]GABE D R. The role of hydrogen in metal electrodepositionprocesses [J]. Journal of Applied Electrochemistry, 1997, 27: 908−915.[21]ZHENG Guo-qu, ZHENG Li-feng, CAO Hua-zhen, GAO Zhi-feng,NI Si-yu, ZHANG Jiu-yuan. Nickel electrodeposition from leaching solution containing ammonia and chloride [J]. Transactions of Nonferrous Metals Society of China, 2003, 13: 217−220.[22]ZHENG Guo-qu, ZHENG Li-feng, CAO Hua-zhen. Formation ofblack nickel in leaching solution containing ammonia and chloride [J]. Transactions of Nonferrous Metals Society of China, 2005, 15: 165−170.[23]GRUJICIC D, PESIC B. Electrochemical and AFM study of nickelnucleation mechanisms on vitreous carbon from ammonium sulfate solutions [J]. Electrochimica Acta, 2006, 51: 2678−2690.[24]RODRIGUEZ-TORRES I, V ALENTIN G, LAPICQUE F.Electrodeposition of zinc−nickel alloys from ammonia-containing baths [J]. Journal of Applied Electrochemistry, 1999, 29: 1035−1044.。
- 1、下载文档前请自行甄别文档内容的完整性,平台不提供额外的编辑、内容补充、找答案等附加服务。
- 2、"仅部分预览"的文档,不可在线预览部分如存在完整性等问题,可反馈申请退款(可完整预览的文档不适用该条件!)。
- 3、如文档侵犯您的权益,请联系客服反馈,我们会尽快为您处理(人工客服工作时间:9:00-18:30)。
On the electrodeposition of nickel–zinc alloys from a eutectic-based ionic liquid
H.Y. Yang a,b,c, X,b, G.H. Wu a,b, W.J. Ding a,b, N. Birbilis c,d,∗
Electrodeposition of Ni–Zn alloys from aqueous plating baths is classified as an anomalous co-deposition, resulting in alloys with high Ni content being difficult to obtain. Alloys, with Ni content in the range of 5–20 wt.%, exhibit significantly better corrosion resistance than pure Zn in salt spray tests [28]. Many attempts were performed to rationalize the anomalous co-deposition and to increase Ni content in the deposition [29–31]. It is believed that anomalous co-deposition is related to hydrogen evolution at the
∗ Corresponding author at: ARC Centre of Excellence for Design in Light Metals, Monash University, Clayton, VIC. 3800, Australia. Tel.: +61 3 99054940; fax: +61 3 99054941.
article info
Article history: Received 31 August 2011 Received in revised form 15 December 2011 Accepted 17 December 2011 Available online 26 December 2011
© 2011 Elsevier Ltd. All rights reserved.
1. Introduction
Interest in Ni and its alloys for imparting corrosion resistance, electrocatalysis and magnetic properties, continues to grow. The electrodeposition of Ni alloys has been widely practiced in aqueous plating systems [1–8]. However, the hydrogen evolution reaction that occurs during electrodeposition has a profound effect on current efficiency and the final quality of the resultant Ni deposits, while in some instances the substrate is likely affected by hydrogen embrittlement. Thus, aprotic ionic liquids (ILs) provide, in a practical sense, an ideal alternative for the electrodeposition of Ni and its alloys since ILs usually provide wider electrochemical windows than aqueous solutions, a wide working temperature range, good conductivity for electrolysis, and free from hydrogen evolution owing to the absence of water [9–11]. To date, studies upon electrodeposition of Ni and its alloys have been focused on first generation ILs, i.e. chloroaluminate ILs [12–15]. However, the hygroscopic nature of these chloroaluminate ILs has delayed progress in their practical application [16–18], particularly for bulk components. The synthesis of air and water-stable ILs, which are considered the second generation of ILs, has attracted
Electrochimica Acta 63 (2012) 131–138
Contents lists available at SciVerse ScienceDirect
Electrochimica Acta
journal homepage: /locate/electacta
Keywords: Electrodeposition Ionic liquid Ni–Zn alloy Nucleation Corrosion resistance
abstract
The electrodeposition behavior of Ni–Zn alloys upon Cu was investigated in a choline chloride–urea (1:2 molar ratio) eutectic-based ionic liquid (1:2 ChCl–urea IL) bath containing 0.1 M NiCl2 and 0.4 M ZnCl2. Cyclic voltammetry reveals that the more noble metal, Ni, deposits preferentially to Zn. Ni–Zn co-deposition was achieved via deposition of Zn upon deposited Ni, at potentials more negative than that of Ni deposition, resulting in a Zn content always less than 50 at.%. Chronoamperometric investigations combined with SEM reveal the nucleation mechanism changes from three-dimensional progressive to instantaneous, followed diffusion-limited growth during Zn-codeposition. The Ni content of electrodeposits could be controlled by deposition potential and current density. Ni–Zn deposits were solid solutions, and deposits containing Ni > ∼87 at.% display best corrosion resistance due to a dense and crack-free structure.
a National Engineering Research Center of Light Alloy Net Forming, Shanghai Jiaotong University, Shanghai 200240, PR China b State Key Laboratory of Metal Matrix Composites, Shanghai Jiaotong University, Shanghai 200240, PR China c ARC Centre of Excellence for Design in Light Metals, Monash University, Clayton, VIC. 3800, Australia d CAST-CRC, Monash University, Clayton, VIC. 3800, Australia
great interest in various fields. However, in specific engineering applications, transition metal halides generally exhibit very low solubility in such ILs, due to the weak Lewis base nature of these anions [19,20]. With the exception of the dicyanamide (DCA−) anion based ILs which were reported to display appreciable solubility for several metal halides [21,22], a 1:2 ChCl–urea eutectic-based IL (otherwise known as a ‘deep eutectic solvent’) may be a promising candidate for the electrodeposition of the transition alloys owing to high solubility of metal halides and low cost [23–25]. In our previous work, we have shown that nanocrystalline Ni coatings could be successfully electrodeposited from 1:2 ChCl–urea eutectic-based IL, doped with nicotinic acid, yielding a current efficiency of ∼100% [26]. Additionally, Ni–Mo and Ni–Sn alloys have also been recently deposited from 1:2 ChCl–urea eutecticbased IL [27]. Given the promising nature of baths based on a ChCl–urea solvent, one obvious avenue is the electrodeposition of Ni–Zn alloys, which can potentially serve as a green alternative to hexavalent chromium and cadmium as corrosion resistant coating on aerospace, automotive and fastener components.