材料の成形条件
主要材料之成形标准条件

HDPE 190~200 PP PVC PS AS ABS 200~220 150~190 190~210 200~230 180~230
Acrylic 220~240 EVA PC PA 150~180 260~280 240~250
0.2~0.8 70~80 4~6HR 0.7~2 40~50 2~4HR 120 80 3~6HR 水份0.03%以下 4-8HR 水份0.03%以下
2-4HR 水份0.03%以下 6.含纖材料可比一般稍高溫度設計 3~5HR 水份0.02%以下 4HR 2003.1.25 乾燥溫度相同即可
320 290 工 業 有 限 公 司
主要材料之標準成形條件
4 螺桿轉速,最高能力之60%~80%
1000~1200 0.6~0.8 500~1000 0.6~2
ABS+PC 200~250 POM 190~210
600~1000 0.45~.0.7 90~100 3~5HR 500~900 1.5~3.5 80~90 3-6HR NYLON簡稱 4 螺桿轉速,最高能力之60%~80% 5 螺桿回轉時間稍短於冷卻時間
變性PPO 260~280 PBT PET PSF 230~260 240~270 330~360
60~100 1200~1300 0.7~0.8 100~120 2-4HR 60~70 70~80 95~100 300~1200 500~1500 700~1000 0.5~2 0.5~2 0.7 120 120 135
主要材料之標準成形條件
文件編號: QI- 751-01 成形 材料 LDPE 料管溫度 NH 180~210 190 190 210 190 200 220 220 220 150 280 240 230 190 260 230 240 330 料管溫度設定例 H1 190 190 210 190 200 220 220 220 150 280 240 240 190 260 240 250 330 H2 180 180 200 180 190 210 210 210 140 270 230 235 180 250 220 230 射出壓力 H3 模具溫度 (kg/cm2) 160 160 180 160 170 190 190 190 120 250 210 230 160 230 200 220 40~50 40~60 50~60 50~70 50~60 50~70 50~70 50~60 30~40 70~90 50~70 40~65 80~90 360~500 300~1000 500~800 600~1500 500~800 700~900 500~900 500~900 600~800 成形 收縮率 1.5~5 1.5~5 0.8~2.5 0.1~5 0.2~0.6 0.2~0.6 70~80 4~6HR 0.4~0.8 80~90 3~6HR 70~85 2~3HR 乾燥條例 溫度 一 時間 備考 補充及注意事項 1.NH:噴嘴(NOZZLE)溫度 H1:料管前區 H2:料管中區 H3:料管後區(料桶下) NH=H1>H2>H3 H2=H1-10 H3=H2-20 2.成形品的回水溫度 (Anealing)要在熱變形 溫度之下10左右 3.保持壓力約射壓之60%~80%
材料成形原理

名词解释1、凝固:是物质由液相转变为固相的过程,是液态成形技术的核心问题,也是材料研究和新材料开发领域共同关注的问题。
2、均质形核:形核前液相金属或合金中无外来固相质点而从液相自身发生形核的过程,所以也称“自发形核” 。
非均质形核:依靠外来质点或型壁界面提供的衬底进行生核过程,亦称“异质形核”或“非自发形核”。
3、粗糙界面:界面固相一侧的点阵位置只有约50%被固相原子所占据,形成坑坑洼洼、凹凸不平的界面结构。
大多数金属界面属于这种结构。
光滑界面:界面固相一侧的点阵位置几乎全部为固相原子所占满,只留下少数空位或台阶,从而形成整体上平整光滑的界面结构。
非金属及化合物大多属于这种。
4、外生生长:晶体自型壁生核,然后由外向内单向延伸的生长方式。
内生生长:等轴枝晶在熔体内部自由生长的方式5、沉淀脱氧:是指溶解于液态金属中的脱氧剂直接和熔池中的[FeO]起作用,使其转化为不溶于液态金属的氧化物,并脱溶沉淀转入熔渣中的一种脱氧方式扩散脱氧:在熔池尾部,随着温度的下降,液态金属中过饱和的氧化铁会向熔渣中扩散6、裂纹:在应力与致脆因素的共同作用下,使材料的原子结合遭到破坏,在形成新界面时产生的缝隙裂纹热裂:是铸件处于高温状态时形成的裂纹类缺陷。
凝固裂纹(结晶裂纹):金属凝固结晶末期,在固相线附近发生的晶间开裂现象冷裂纹:是指金属经焊接或铸造成形后冷却到较低温度时产生的裂纹7、塑性:材料受力破坏前可承受最大塑性变形的能力。
塑性指标:1、拉伸试验(断后伸长率和断面收缩率越大说明塑性越好)2、压缩试验3、扭转试验。
8、主平面:切应力为零的平面;主应力:主平面上的正应力:主方向:主平面的法线方向,亦即主应力的方向;主切应力平面:使切应力达到极大值的平面称为主切应力平面;主切应力:主切应力平面上所作用的切应力称为主切应力9、屈服准则(也称塑性条件或塑性方程):质点进入塑性状态时,各应力分量之间满足的关系屈雷斯加(T resca)屈服准则(又称最大剪应力准则):材料(质点)中的最大剪应力达到某一临界值时,材料发生屈服,该临界值取决于材料在变形条件下的性质,而与应力状态无关密塞斯(mises)屈服准则:当受力物体内质点应力偏张量的第2不变量I2 达到某一临界值时,材料发生屈服,该临界值取决于材料在变形条件下的性质,而与应力状态无关。
塑料成型质量要求

塑料成型质量要求
塑料成型质量要求如下:
1.塑料材料需符合成型要求,满足产品的使用环境条件和性能标准。
2.塑料材料应具有一定的强度、硬度、耐热性、耐腐蚀性等特性。
3.塑料材料应具有良好的加工性能,易于进行挤出、注射、吹塑等成型加
工。
4.塑料材料应具有较低的吸湿性,避免在加工过程中出现气泡、裂纹等缺
陷。
5.塑料材料应具有较高的热稳定性,避免在加工过程中出现降解、变色等缺
陷。
6.塑料材料应具有较低的熔体粘度,以便于进行注射、挤出等加工操作。
7.塑料材料应具有较高的熔体强度,避免在加工过程中出现断裂、变形等缺
陷。
8.塑料材料应具有良好的耐候性,避免在户外使用时出现老化、龟裂等缺
陷。
成型条件的五大要素
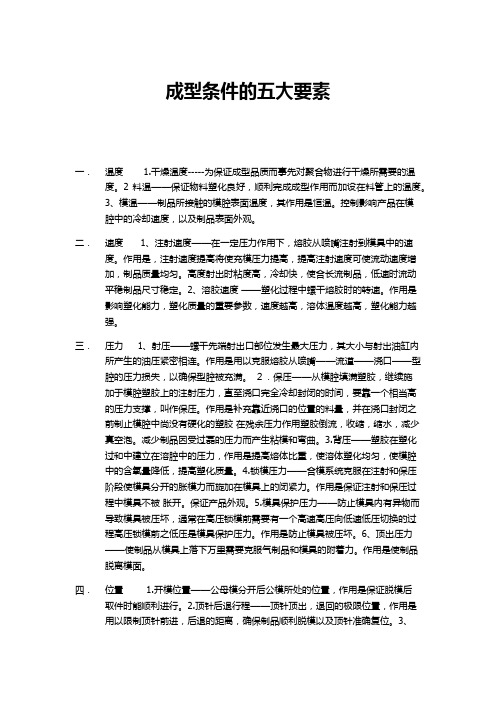
成型条件的五大要素一.温度 1.干燥温度-----为保证成型品质而事先对聚合物进行干燥所需要的温度。
2料温——保证物料塑化良好,顺利完成成型作用而加设在料管上的温度。
3、模温——制品所接触的模腔表面温度,其作用是恒温。
控制影响产品在模腔中的冷却速度,以及制品表面外观。
二.速度 1、注射速度——在一定压力作用下,熔胶从喷嘴注射到模具中的速度。
作用是,注射速度提高将使充模压力提高,提高注射速度可使流动速度增加,制品质量均匀。
高度射出时粘度高,冷却快,使合长流制品,低速时流动平稳制品尺寸稳定。
2、溶胶速度——塑化过程中螺干熔胶时的转速。
作用是影响塑化能力,塑化质量的重要参数,速度越高,溶体温度越高,塑化能力越强。
三.压力 1、射压——螺干先端射出口部位发生最大压力,其大小与射出油缸内所产生的油压紧密相连。
作用是用以克服熔胶从喷嘴——流道——浇口——型腔的压力损失,以确保型腔被充满。
2.保压——从模腔填满塑胶,继续施加于模腔塑胶上的注射压力,直至浇口完全冷却封闭的时间,要靠一个相当高的压力支撑,叫作保压。
作用是补充靠近浇口的位置的料量,并在浇口封闭之前制止模腔中尚没有硬化的塑胶在残余压力作用塑胶倒流,收缩,缩水,减少真空泡。
减少制品因受过磊的压力而产生粘模和弯曲。
3.背压——塑胶在塑化过和中建立在溶腔中的压力,作用是提高熔体比重,使溶体塑化均匀,使模腔中的含氧量降低,提高塑化质量。
4.锁模压力——合模系统克服在注射和保压阶段使模具分开的胀模力而旋加在模具上的闭紧力。
作用是保证注射和保压过程中模具不被胀开。
保证产品外观。
5.模具保护压力——防止模具内有异物而导致模具被压坏,通常在高压锁模前需要有一个高速高压向低速低压切换的过程高压锁模前之低压是模具保护压力。
作用是防止模具被压坏。
6、顶出压力——使制品从模具上落下万里需要克服气制品和模具的附着力。
作用是使制品脱离模面。
四.位置 1.开模位置——公母模分开后公模所处的位置,作用是保证脱模后取件时能顺利进行。
材料成形三要素材料成形发展
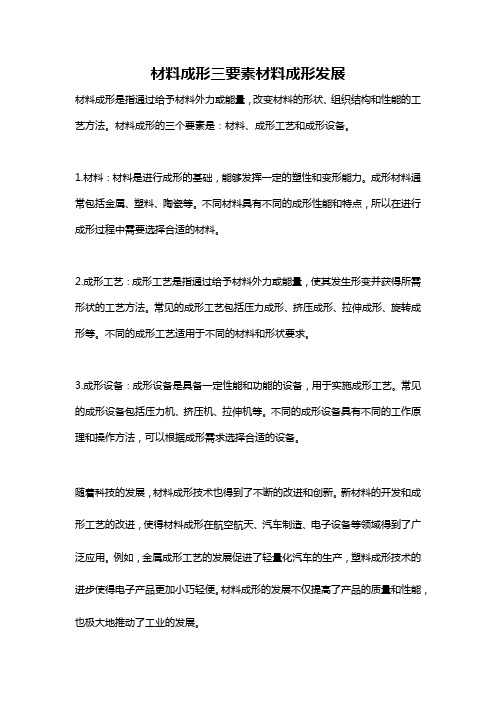
材料成形三要素材料成形发展
材料成形是指通过给予材料外力或能量,改变材料的形状、组织结构和性能的工艺方法。
材料成形的三个要素是:材料、成形工艺和成形设备。
1.材料:材料是进行成形的基础,能够发挥一定的塑性和变形能力。
成形材料通常包括金属、塑料、陶瓷等。
不同材料具有不同的成形性能和特点,所以在进行成形过程中需要选择合适的材料。
2.成形工艺:成形工艺是指通过给予材料外力或能量,使其发生形变并获得所需形状的工艺方法。
常见的成形工艺包括压力成形、挤压成形、拉伸成形、旋转成形等。
不同的成形工艺适用于不同的材料和形状要求。
3.成形设备:成形设备是具备一定性能和功能的设备,用于实施成形工艺。
常见的成形设备包括压力机、挤压机、拉伸机等。
不同的成形设备具有不同的工作原理和操作方法,可以根据成形需求选择合适的设备。
随着科技的发展,材料成形技术也得到了不断的改进和创新。
新材料的开发和成形工艺的改进,使得材料成形在航空航天、汽车制造、电子设备等领域得到了广泛应用。
例如,金属成形工艺的发展促进了轻量化汽车的生产,塑料成形技术的进步使得电子产品更加小巧轻便。
材料成形的发展不仅提高了产品的质量和性能,也极大地推动了工业的发展。
材料成形原理

材料成形原理材料成形原理是指通过外部力或能量作用于材料,使其发生形状的变化,最终达到所需形态的过程。
材料成形原理主要包括塑性成形、热成形和复合成形三种。
塑性成形是指在一定温度范围内,材料受到外力作用后,经过一系列塑性变形,使材料的形状发生改变。
塑性成形主要包括锻造、挤压、拉伸、压力成形等方法。
在塑性成形过程中,材料中的晶体发生滑移、变形和晶粒疏化等过程。
滑移是指晶体原子沿晶体面壳滑动,在晶界形成位错。
材料中的位错会使晶体结构变得稀疏,从而使材料发生塑性变形。
塑性成形广泛应用于航空、汽车、机械等领域。
热成形是指通过加热材料到一定温度,使材料变得柔软,并通过外力进行变形。
在热成形过程中,材料的晶粒会发生再结晶现象,从而提高材料的塑性和韧性。
常见的热成形方法有热轧、热挤压、热拉伸等。
热成形广泛应用于冶金、造船、能源等行业。
复合成形是指通过多种成形工艺的组合使用,将不同材料进行结合形成复合材料的成形方法。
常见的复合成形方法有层积成形、注射成形、挤出成形等。
复合成形可以改善材料的机械性能、耐腐蚀性能、阻燃性能等,被广泛应用于航空航天、电子、建筑等领域。
材料成形原理的基础是塑性变形原理。
塑性变形是指材料在外力作用下,发生形状的改变,并保持新形态的能力。
塑性变形包括弹塑性和塑性。
弹塑性是指材料在外力作用下发生变形,当外力消失时,材料能够恢复原有形态。
塑性是指材料在外力作用下发生变形,即使外力消失,材料也不能恢复原有形态。
塑性变形的基础是晶体的位错理论和晶体结构的变形机制。
在材料成形原理中,还有一些重要的影响因素。
温度是影响材料成形的重要因素之一,不同温度下材料的塑性性能不同。
施加的外力大小和方向会影响材料的塑性变形。
材料的化学成分和物理性质也会对成形过程产生影响。
综上所述,材料成形原理是指通过外部力或能量作用于材料,使其发生形状的变化,最终达到所需形态的过程。
塑性成形、热成形和复合成形是常见的材料成形方法。
材料成形原理的基础是塑性变形原理,影响材料成形的因素有温度、外力、材料的化学成分和物理性质等。
材料的成型方法有哪些
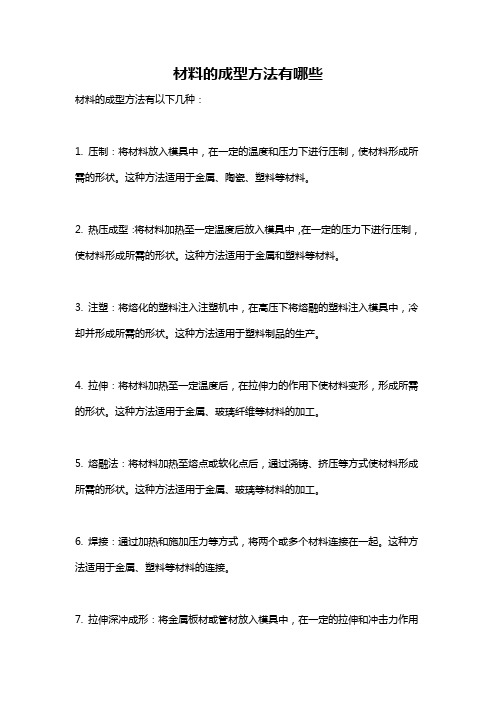
材料的成型方法有哪些
材料的成型方法有以下几种:
1. 压制:将材料放入模具中,在一定的温度和压力下进行压制,使材料形成所需的形状。
这种方法适用于金属、陶瓷、塑料等材料。
2. 热压成型:将材料加热至一定温度后放入模具中,在一定的压力下进行压制,使材料形成所需的形状。
这种方法适用于金属和塑料等材料。
3. 注塑:将熔化的塑料注入注塑机中,在高压下将熔融的塑料注入模具中,冷却并形成所需的形状。
这种方法适用于塑料制品的生产。
4. 拉伸:将材料加热至一定温度后,在拉伸力的作用下使材料变形,形成所需的形状。
这种方法适用于金属、玻璃纤维等材料的加工。
5. 熔融法:将材料加热至熔点或软化点后,通过浇铸、挤压等方式使材料形成所需的形状。
这种方法适用于金属、玻璃等材料的加工。
6. 焊接:通过加热和施加压力等方式,将两个或多个材料连接在一起。
这种方法适用于金属、塑料等材料的连接。
7. 拉伸深冲成形:将金属板材或管材放入模具中,在一定的拉伸和冲击力作用
下,使材料形成所需的形状。
这种方法适用于汽车制造、航空航天等行业。
8. 粘合:使用粘合剂将两个或多个材料黏合在一起。
这种方法适用于各种材料的连接和修补。
9. 3D打印:通过逐层堆叠材料的方式,使用计算机控制的机器制造出所需的形状。
这种方法适用于各种材料的快速原型制造和定制制作。
材料成形原理

材料成形原理
材料成形原理是指在材料加工过程中,通过施加外力和热力,使材料发生形状、尺寸和性能的变化,从而得到所需的工件或半成品的过程。
材料成形原理是材料加工工程中的重要基础理论,对于提高产品质量、降低生产成本、提高生产效率具有重要意义。
材料成形原理的基本原理是利用外力使材料发生塑性变形,从而获得所需形状
和尺寸的工件。
材料成形的基本方式包括压力成形、拉伸成形、弯曲成形、剪切成形等。
在这些成形过程中,材料会受到各种不同的力的作用,从而发生塑性变形,最终得到所需的工件。
在材料成形过程中,材料的塑性变形是通过应力和应变的作用来实现的。
应力
是单位面积上的力,而应变是材料单位长度上的变形量。
在材料成形过程中,通过施加外力,使材料受到应力作用,从而产生应变,最终实现材料的塑性变形。
材料成形原理的实现需要考虑材料的性能和成形工艺的匹配性。
材料的性能包
括硬度、韧性、塑性等,而成形工艺包括成形温度、成形速度、成形压力等。
只有在材料性能和成形工艺相互匹配的情况下,才能实现材料的有效成形。
材料成形原理在实际应用中具有广泛的意义。
在金属加工领域,通过材料成形
原理可以实现金属的锻造、冲压、拉伸等加工工艺,从而获得各种不同形状和尺寸的金属工件。
在塑料加工领域,材料成形原理可以实现塑料的注塑、挤压、吹塑等加工工艺,从而获得各种不同形状和尺寸的塑料制品。
总之,材料成形原理是材料加工工程中的重要理论基础,对于实现材料的有效
成形具有重要意义。
通过对材料成形原理的深入理解和研究,可以不断提高材料加工工艺的水平,实现产品质量的提高和生产效率的提升。