蠕变---高温强度与断裂
第8章 金属高温下的变形与断裂
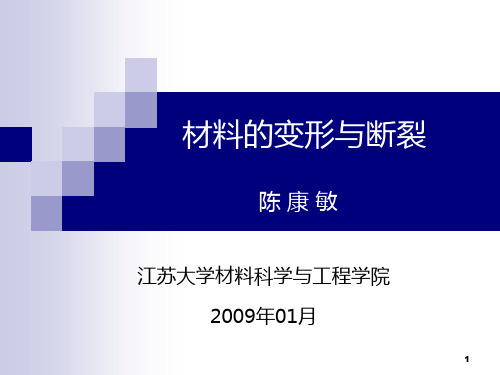
8
9
典型的蠕变曲线
金属蠕变过程用蠕变曲线来描述。 金属蠕变过程用蠕变曲线来描述。典型的蠕变曲线如图。 (1)Oa线段:是试样在t 温度下承受恒定拉应力σ时所产 线段: 线段 生的起始伸长率δq。 若应力超过金属在该温度下的屈服强度,则δq包括弹性伸长 弹性伸长 塑性伸长率两部分。 率和塑性伸长率 塑性伸长率 此应变还不算蠕变 应变还不算蠕变,而是由外载荷引起的一般变形过程。 应变还不算蠕变
20
(二)扩散蠕变
(二)扩散蠕变 扩散蠕变: 扩散蠕变:是在较高温度(约比温度(T/Tm)远超过0.5)下的 ( 一种蠕变变形机理。 它是在高温下大量原子和空位定向移动造成的 高温下大量原子和空位定向移动造成的。 高温下大量原子和空位定向移动造成的 在不受外力情况下,原子和空位的移动无方向性,因而宏观 上不显示塑性变形。 但当受拉应力σ作用时,在多晶体内产生不均匀的应力场 产生不均匀的应力场。 产生不均匀的应力场
17
刃位错攀移克服障碍的几种模型: 刃位错攀移克服障碍的几种模型: 可见,塞积在某种障碍前的位错通过热激活可以在新的滑移 面上运动(a),或与异号位错相遇而对消(b),或形成亚 晶界(c),或被晶界所吸收(d)。
18
当塞积群中某一个位错被激活而发生攀移时,位错源便可能 再次开动而放出一个位错,从而形成动态回复过程 动态回复过程。 动态回复过程 这一过程不断进行,蠕变得以不断发展。
7
本章介绍内容: 本章介绍内容: 阐述金属材料在高温长时载荷作用下的蠕变现象 蠕变现象。 蠕变现象 讨论蠕变变形和断裂的机理 蠕变变形和断裂的机理。 蠕变变形和断裂的机理 介绍高温力学性能指标及影响因素。 为正确选用高温金属材料和合理制定其热处理工艺提供基础 知识。
第1章第5节蠕变

28
48.2 45.1 41.8 38.2 34.3 30.3 26 21.5 16.7 11.7 6.6
表 1-2 叶片各截面σm 值
根据叶片的工作温度和应力选用温度为 550℃和应力为 98.07MN/m2 的蠕变曲线,其蠕 变速度 Vcr=1.2×10-7h-1,如图 1-20。 由已知各截面的应力值 σ ,计算各截面的σm 值,列入表 1-10 中,应用数值积分法得 到
550 1 × 10
0 − 5
= 90 MN/m2,是指当温度为 550℃时,蠕变速度为 1×10-5%/h 所对应
的应力为 90MN/m2。 表明材料高温强度特性的另一个重要指标时持久强度极限。 在一定温度下, 经过一定的 时间间隔后引起试件断裂(相当于图 1- 19 上的 D 点)的应力叫做持久强度极限。例如 Cr11MoV 的持久强度极限为 σ
Ω(t ) 2 =
Vcr 1.2 × 10 −7 t = × 105 = 7.97 ×10 −8 ( MN / m 2 ) − m σm (98.07) 2.6
1 0
∆l2 = Ω(t ) 2 ∫ σ m dx = 7.97 × 10 −8 × 10.3 × 10 2 = 0.82 × 10 − 4 m
550 10 5
0
= 160 MN / m
2
,它表示温度为 550℃时,经过 105
小时造成断裂的应力为 160MN/m2。 为了进行蠕变计算,需要将蠕变引起的变形( ε c⋅r = Vc⋅r t )与有关因素的关系列为数学 表达式。从大量试验结果归纳出来的重要经验公式是
蠕变 PPT课件

服某些短程障碍,从而使变形不断产生。
位错热激活方式有多种,高温下热激活主要是刃位错的攀移。
28
蠕变第一阶段:由于蠕变变形逐渐产生应变硬化,使位错源 开动的阻力及位错滑移阻力增大,使蠕变速率不断降低。
线)可得到十万小时的持久强度极限值。 如:12Cr1MoV钢在580℃、100000h的持久强度极限为89MPa。
26
27
10.3 蠕变变形与蠕变断裂机理
一、蠕变变形机理 金属蠕变变形主要是通过位错滑移、原子扩散及晶界滑
动等机理进行的,且随温度及应力的变化而有所不同。
(一)位错滑移蠕变 在蠕变过程中,位错滑移仍然是一种重要的变形机理。 在常温下,若滑移面上位错运动受阻产生塞积,滑移便不能
在耐热合金中晶界上形成的空洞照片,如图。
36
以上两种形成裂纹方式,都有空洞萌生过程。
可见,晶界空洞对材料在高温使用温度范围和寿命是至关重 要的。裂纹形成后,进一步依靠晶界滑动、空位扩散和空洞 连接而扩展,最终导致沿晶断裂。
由于蠕变断裂主要在晶界上产生,因此,晶界的形态、晶界 上的析出物和杂质偏聚、晶粒大小及晶粒度的均匀性等对蠕 变断裂均会产生很大影响。
这就是说:要提高金属材料的高温力学性能,应控制晶内和 晶界的原子扩散过程。
这种扩散过程主要取决于:合金的化学成分、冶炼工艺、热 处理工艺等因素。
41
(一)合金化学成分的影响 位错越过障碍所需的激活能(蠕变激活能)越高的金属,越
难产生蠕变变形。 实验表明:纯金属蠕变激活能大体与其自扩散激活能相近。 因此,耐热钢及合金的基体材料一般选用熔点高、自扩散激活 能大或层错能低的金属及合金。
蠕变

图a-为晶界滑动与晶内滑移带在晶界上交割时形成的空洞。 图b-为晶界上存在第二相质点时,当晶界滑动受阻而形成 的空洞,空洞长大并连接,便形成裂纹。 在耐热合金中晶界上形成的空洞照片,如图。
36
以上两种形成裂纹方式,都有空洞萌生过程。 可见,晶界空洞对材料在高温使用温度范围和寿命是至关重 要的。裂纹形成后,进一步依靠晶界滑动、空位扩散和空洞 连接而扩展,最终导致沿晶断裂。 由于蠕变断裂主要在晶界上产生,因此,晶界的形态、晶界 上的析出物和杂质偏聚、晶粒大小及晶粒度的均匀性等对蠕 变断裂均会产生很大影响。
41
(一)合金化学成分的影响 位错越过障碍所需的激活能(蠕变激活能)越高的金属,越 难产生蠕变变形。 实验表明:纯金属蠕变激活能大体与其自扩散激活能相近。 因此,耐热钢及合金的基体材料一般选用熔点高、自扩散激活 能大或层错能低的金属及合金。 这是因为: 在一定温度下,熔点越高,自扩散激活能越大,其自扩散越 慢。 熔点相同,但晶体结构不同,则自扩散激活能越高,扩散越 慢。
700 例如, 110 30MPa
3
表示该合金在700℃、1000h的持久强度为30MPa。 试验时,规定持续时间是以机组的设计寿命为依据的。 例如,对于锅炉、汽轮机等,机组的设计寿命为数万以至数 十万小时,而航空喷气发动机则为一千或几百小时。
23
持久强度: 对于设计在高温运转过程中不考虑变形量大小,而只考虑在 承受给定应力下使用寿命的机件(如锅炉道热蒸气管)是极 其重要的性能指标。
典型的蠕变曲线
12
从a点开始随时间τ增长而产生的应变属于蠕变,abcd曲线 即为蠕变曲线。 蠕变曲线上任一点的斜率,表示该点的蠕变速率。 按照蠕变速率的变化情况,可将蠕变过程分为三个阶段:
耐热钢的高温力学性能

耐热钢的高温力学性能耐热钢的基本性能是它在高温下的力学性能和耐腐蚀性能,同时还有常温下的力学性能、工艺性能和物理性能等。
耐热钢的高温力学性能主要包括蠕变性能、持久强度、疲劳性能、松弛性能等。
1 蠕变性能耐热材料的蠕变是指温度高于0.5T下,材料所承受的应力远低熔点于屈服强度的应力时,随着加载时间的持续增加而产生的缓慢塑性变形现象。
通常用蠕变曲线来描述材料的蠕变规律。
在实践中通常使用条件蠕变极限来测定耐热钢的蠕变性能。
条件蠕变极限是指在获得一定变形速率,在规定时间内获得一定总变形量的应力。
一般用下列两种方式表示:表示;1) 以伸长率确定蠕变极限时,用σδτ/τ表示。
2) 以蠕变速率确定蠕变极限时,用σv在工程实践中常用规定的蠕变速率确定蠕变极限。
汽轮机、锅炉设备零部件的工作时间一般规定为105h。
用于汽轮机、锅炉设备的耐热钢,其条件蠕变极限的确定是以105h变形为1%时的应力来计算零部件的强度。
2 持久强度耐热材料的持久强度是指在给定的温度下和规定的时间内断裂时的强度,要求给出的只是此时所能承受的最大应力。
持久强度试验不仅反映材料在高温长期应力作用下的断裂应力,而且还表明断裂时的塑性(即持久塑性)。
耐热材料零部件在高温下工作的时间长达几百小时,几千小时,甚至几万小时,而持久强度试验不可能进行那么长时间,一般只做一些应力较高而时间较短的试验,然后根据这些试验数据利用外推法,得出更长时间的持久强度值。
但外推法所得持久强度值可能与实际值有差距,因此,重要的材料仍需进行长达数万小时的持久强度试验。
耐热材料零部件由于温度波动会加速蠕变过程,降低持久强度。
有些耐热钢有缺口敏感性。
缺口所造成的应力集中对持久强度的影响决定于试验温度、缺口的几何形状、钢的持久塑性、热处理工艺及钢的成分等因素。
3 疲劳性能高温下工作的材料,除经受机械疲劳之外,还经受热疲劳作用。
材料经多次反复热应力循环以后导致破坏的过程称为热疲劳。
航空发动机涡轮叶片、导向叶片、涡轮盘及汽轮机叶片等部件经常处于温度急剧交变情况下工作.使材料内部承受交变的热应力,同时伴随着弹性变形的循环,由此引起塑性变形逐渐积累损伤,最后导致材料破坏。
高温蠕变与疲劳

C % / h
(MPa)表示。
蠕变极限适用于失效方式为过量变形的那些高温零部件。
持久强度是材料抵抗蠕变断裂的能力。它是在
一定温度下,规定时间内使材料断裂的最大应力值,
以
表t C示。
对于锅炉、管道等构件。其主要破坏方式是断
裂而不是变形,设计这类构件就要采用持久强度指 标。
持久塑性是材料承受蠕变变形能力的大小,用 蠕变断裂时的相对伸长率和相对断面收缩率表示。
4、蠕变断裂机制图 晶间断裂是蠕变断裂的普遍形式,高温
低应力下情况更是如此。
晶间断裂有两种模型:一种是晶界滑动 和应力集中模型,另一种是空位聚集模型。
第一种模型:
图12.18 晶界滑动在三晶粒交界处形成楔形空间
第二种模型 :
图12.20 空位聚集形成空洞
断裂机制图 :
影响蠕变断裂机制的最重要因素是应力、 温度和加载速率,因此,断裂机制图的纵坐
标通常为规范化流变应力fl/E,横坐标为断
裂时间tf或相对温度T/Tm。
图12.21 Nimonic 80A合金断裂机制图
图12.22断裂机制图示意图
二、高温疲劳
高温疲劳涉及疲劳、蠕变和环境影响等几个与 时间有关的过程的交互作用,这些过程在高温疲劳 损伤中的相对作用随具体材料而异。
材料在高温下的疲劳行为,除了与循环应力有 关,还与材料的化学成分、显微组织和环境等因素 有很大关系。
金属材料的典型蠕变曲线如图12.16所示。
图12.16 典型蠕变曲线
oa线段是施加外载荷后试样的瞬时应变0,不 属于蠕变;
曲线abcd表明应变是随时间增长逐渐产生的, 称为蠕变;蠕变曲线上任一点的斜率表示该点的蠕
变速率,用 表示。
蠕变断裂

3.3 延缩性蠕变断裂
延缩性断裂主要发生在高温 (T > 0.6 Tm )条件下。这种断 裂过程总伴随着动态再结晶,在 晶粒内不断产生细小的新晶粒。 由于晶界面积不断增大,空位将 均匀分布,从而阻碍空洞的形成 和长大。因此,动态再结晶抑制 沿晶断裂。晶粒大小与应变量成 反比。如右图所示,在缩颈处晶 粒要细得多,缩颈可伴随动态再 结晶一直进行到截面积减小为零 时为止。
3.1 沿晶蠕变断裂 2)空洞在晶界上聚集形成裂纹
• 在垂直于拉应力的晶界上,当应力水平超过临界值时,通过空位聚集 的方式形成空洞。 • 空洞核心一旦形成,在拉应力作用下,空位由晶内或沿晶界继续向空 洞处扩散,使空洞长大并相互连接形成裂纹。
3.1 沿晶蠕变断裂 3)晶界空洞、裂纹的连接
3.2 穿晶蠕变断裂
s kT
A变模量;b -位错柏氏矢量;k -波尔兹 曼常数。
1.4 晶粒尺寸对蠕变速率的影响
蠕变变形主要由晶内变形和晶界滑动两部分组成。显然,晶粒越细, 晶界滑动对总变形量的贡献就越大。因此,对高温蠕变来说,晶粒细的 蠕变速度较大,随晶粒直径的增加,蠕变速度减小。但晶粒尺寸足够大 以致晶界滑动对总变形量贡献小到可以忽略时,蠕变速度将不依赖于晶 粒尺寸。
3)晶界滑动蠕变机理
晶界在外力作用下会发生相对滑 动。在常温下,可忽略不计,但在高 温下,晶界的相对滑动可以引起明显 的塑性变形,产生蠕变。
对于金属材料和陶瓷材料,晶界 滑动一般是由晶粒的纯弹性畸变和空 位的定向扩散引起的。但前者的贡献 不大,主要还是空位的定向扩散。
对于含有牛顿液态或似液态第二 相物质的陶瓷材料,由于第二相的粘 性流动也可引起蠕变。
材料性能_ 材料的高温蠕变性能_9-1高温蠕变_

刃型位错攀移克服障碍的几种模型
① 由于温度的升高,原子和空位热激活能增加,位错可 以克服某些障碍得以运动,继续产生塑性变形
② 由于塞积位错数量减少,对位错源的反作用力减少, 位错源可以重新开动,位错得以增殖,产生蠕变变形
低温大应力下,变形不能协调 c.当应力集中达到晶界的结合强度 时,发生开裂,形成楔形空洞
楔形空洞形成示意图
② 空位聚集形成晶界裂纹(高温低应力)
a.在垂直于拉应力的晶界,当 应力水平超过临界值时,通 过空位聚集的方式萌生空洞
b.在应力作用下,空位由晶内 和沿晶界继续向空洞处扩散
c.使空洞长大并互相连接形成 裂纹。
应力较低时,温度越高且晶粒度越小时,晶界滑 动对蠕变的作用越大。
晶界运动的两种方式:
晶界的滑动是由晶粒的纯弹性畸变和空位的定向 扩散引起,主要是空位的定向扩散引起。
晶界沿着法线方向迁移。
因此,对于高温蠕变来说,随着晶粒直径的增 加,蠕变速率减小。当晶粒尺寸足够大以致于晶界 滑动对总变形量贡献小到可以忽略,蠕变将不依赖 于晶界滑动。
高温长时应力作用下:蠕变、 应力松弛、持 久断裂、氧化和腐蚀及热疲劳损坏等一系列 高温失效现象。
蠕变:材料在一定温度和恒应力作用下,随时间的 增加发生缓慢塑性变形的现象 ,这种现象导致的 材料断裂称为蠕变断裂。
发生蠕变的温度可以是低温下,也可以是高温下, 但只有在约比温度高于0.3时才较显著,所以通常 又叫做高温蠕变。 约比温度(T/Tm) T—试验温度,Tm—材料熔点
3、蠕变断裂机理
一般在高温低应力下,晶内及晶界的强度都降 低,但晶界下降的快,因此蠕变断裂一般都是沿晶 蠕变断裂。
- 1、下载文档前请自行甄别文档内容的完整性,平台不提供额外的编辑、内容补充、找答案等附加服务。
- 2、"仅部分预览"的文档,不可在线预览部分如存在完整性等问题,可反馈申请退款(可完整预览的文档不适用该条件!)。
- 3、如文档侵犯您的权益,请联系客服反馈,我们会尽快为您处理(人工客服工作时间:9:00-18:30)。
5、层错能的影响
研究表明,许多fcc金属的蠕 变速度与层错能有关,可表示为:
s kT
A F
n
DGb
Gb G
式中,φ(γF/Gb)是关于层错能的函 数,可由实验得到。
Mohamed和Langdon分析整理了 25种fcc金属的蠕变数据和层错能 数据,得到右图所示的结果。可 见图中直线的斜率约等于3,说明 除少数固溶体外,大部分符合 φ(γF/Gb)=(γF/Gb)3的关系,因而有:
2、应力大小及温度对蠕变曲线的影响
• 当减小应力或降低温度时,蠕变第Ⅱ阶段延长,甚至不出 现第Ⅲ阶段; • 当增加应力或提高温度时,蠕变第Ⅱ阶段缩短,甚至消失, 试样经减速蠕变阶段后很快进入加速蠕变阶段而断裂。
3、温度及应力对蠕变速率的影响
1)温度的影响
大量实验表明,稳态蠕变速率对数与绝对温度的倒数呈线性关系。 因此,稳态蠕变速率与温度的关系可表示为如下的阿累尼乌斯关系:
s
A1
exp
Qc RT
式中,Qc -蠕变表观激活能。
注:表中Qsd为自扩散激活能,可见它与表观激活能很相近,说明蠕变和扩散过程 紧密相关。
2)应力的影响
大量实验表明,稳态蠕变速率与应力的双 对数呈线性关系,如右图所示。在较低的应力 下,可写为如下幂律蠕变形式:
s A2 n
式中,n-稳态蠕变速度应力指数。
第六章 材料的高温强度天 — 能源 — 化工
• 高温对材料力学性能影响的总体趋势
— 强度下降 — 塑性增加 — 时间效应
• 高温的含义
一般用“约比温度”(即 T / Tm )来描述。当T / Tm > 0.4 ~ 0.5 时为高温;反之则为低温。
第一节 高温蠕变性能
金属材料在蠕变过程中可发生不同形式的断裂,按照 断裂时塑性变形量大小的顺序,可将蠕变断裂分为如下三 个类型:
例如,在同素异构转变温 度下,γ-Fe(fcc)的蠕变速率 仅为α-Fe(bcc)的 1 / 200,这 个巨大的差别由γ-Fe 的扩散率 仅为α-Fe 的 1 / 350可直接得到 解释。
2、蠕变的微观过程
在温度高于 0.5Tm 条件下, 金属蠕变过程中可发生下列三种 微观结构的变化:
攀移绕过障碍
材料在长时间的恒温、恒载荷作用下缓慢地产生塑性变 形的现象称为蠕变,由这种变形而最后导致材料的断裂称为 蠕变断裂。
一、蠕变的一般规律
1、蠕变曲线
可由蠕变曲线描述,一 般分为三个阶段:
• 减速蠕变(过渡蠕变)
• 恒速蠕变(稳定蠕变)
• 加速蠕变(失稳蠕变)
蠕变量ε与时间 t 的关系为:
ε=ε0 + f (t) + D t +Φ(t)
空位在晶内扩散,蠕变速率为: 7Dyb3
kTd 2
式中,Dy-体积扩散系数。
Coble 蠕变
空位沿晶界扩散,蠕变速率为: 50Dg b4
kTd 3
式中,Dg-晶界扩散系数。
Nabarro-Herring 空位晶内扩散
Coble空位晶j界扩散
3)晶界滑动蠕变机理
晶界在外力作用下会发生相 对滑动。在常温下,可忽略不计, 但在高温下,晶界的相对滑动可 以引起明显的塑性变形,产生蠕 变。
•位错滑移和攀移
▪ 刃位错攀移(图a) ▪ 螺位错交滑移
不规整晶界滑动及晶 内位错运动协调变形
▪ 正、负位错互毁(图b)
•晶界滑动
▪ 位错协调(图c) ▪ 扩散协调(图d)
空位(或原子)沿晶 界或在晶内扩散
•原子(空位)扩散(图e)
异号刃型位错攀移互毁
晶界滑动及原子在三 晶粒交界处扩散
3、蠕变机理
在较高应力水平下,幂律蠕变规律失效, 此时可用指数函数来近似表示:
s A2 exp B
综合温度和应力的影响,有:
s
A3
n
exp
Qc RT
s kT
A
n
DGb G
式中,D-自扩散系数;G-切变模量;b -位错柏氏矢量;k -波尔兹曼常数。
4、晶粒尺寸对蠕变速率的影响
蠕变变形主要由晶内变形和晶界滑动两部分组成。显然, 晶粒越细,晶界滑动对总变形量的贡献就越大。因此,对高 温蠕变来说,晶粒细的蠕变速度较大,随晶粒直径的增加, 蠕变速度减小。但晶粒尺寸足够大以致晶界滑动对总变形量 贡献小到可以忽略时,蠕变速度将不依赖于晶粒尺寸。
总位错密度
在蠕变第一阶段,随着变形 量增加,总位错密度增加,亚结 构细化。在第二阶段达到稳态时, 位错结构也达到稳定,位错结构 不变化。
亚晶界(或胞壁)位错密度 亚结构内位错密度
二、蠕变变形机制
1、扩散对蠕变的影响
实验证明,在较低的温度 下,蠕变激活能和交滑移激活 能相近;当温度高于 0.5Tm 时, 蠕变激活能与自扩散激活能相 等(如右图所示)。这说明在 较高的温度下是自扩散控制了 蠕变速率。
位扩散成了蠕变的主要机制。如图所示,上下方晶界受拉应力,空位形成 能较低,空位浓度较高;两侧晶界由于侧向收缩而受压应力,空位浓度较 低。由于存在空位浓度梯度,上下晶界的空位将向两侧晶界扩散迁移,而 原子扩散方向恰好相反,造成晶粒沿拉伸方向伸长。
根据空位扩散路径不同,又可分为两种:
Nabarro-Herring 蠕变
对于金属材料和陶瓷材料, 晶界滑动一般是由晶粒的纯弹性 畸变和空位的定向扩散引起的。 但前者的贡献不大,主要还是空 位的定向扩散。
对于含有牛顿液态或似液态 第二相物质的陶瓷材料,由于第 二相的粘性流动也可引起蠕变。
5、蠕变机制图
蠕变机制图综合反映了在不同温度、应力区域内的主要 蠕变机制。
三、蠕变断裂机理
材料蠕变变形机理主要有位错滑移、原子扩散、晶界滑 动。对高分子材料,还有分子链段沿外力的舒展。
1)位错滑移蠕变机理
位错蠕变有加工硬 化和回复软化两种微观 结构变化趋势,其相互 作用的综合结果,主要 取决于位错的变化特征, 并决定了低温、低应力 条件下的蠕变特征。
2)扩散蠕变机理
在高温(扩散很快)、低应力(位错很少)的条件下,应力诱导的空
s kT
A F
3
n
DGb Gb G
6、蠕变中位错亚结构的变化
对纯金属和单相固溶体的观 察表明,经过仔细退火内部位错 密度很低的金属,在蠕变初期位 错密度迅速增加,很快形成位错 缠结并最终过渡到胞状结构,大 部分位错相互缠结形成胞壁而胞 内位错很少。当应力较大、蠕变 第一阶段变形量较大时,胞壁位 错逐渐整齐排列形成亚晶界,胞 状结构也就变成亚晶组织。